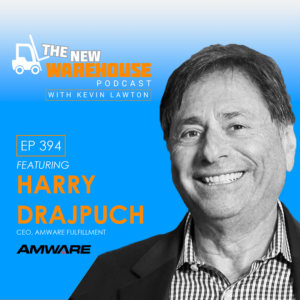
Episode 394: How Amware Fulfillment is driving success in the warehousing industry
Welcome to another exciting episode of The New Warehouse Podcast! In this episode, we had the privilege of speaking with
Welcome to another exciting episode of The New Warehouse Podcast! In this episode, we had the privilege of speaking with
Carton Cloud is on a mission to improve people’s lives in logistics. In this episode of the New Warehouse Podcast,
In this episode of the New Warehouse Podcast, we’re delighted to have Sneha Kumari, Head of Industry Trends at Circular
Welcome to a new episode of The New Warehouse Podcast! In today’s episode, Cliff Hardesty, the Marketing Director at Barcode
In the latest episode of The New Warehouse podcast, Kevin Lawton sits down with Guy Courtin, the VP of Industry
Welcome to a new episode of The New Warehouse! In this episode, we have the pleasure of hosting Connor McGuinness,
Welcome to the New Warehouse podcast. In this episode recorded at ProMat 2023, Kevin hosts Daniel Aguirre, Sales Manager at
In the latest episode of The New Warehouse Podcast, Saleh Elhattab, founder and CEO of Gravity, joins Kevin to discuss
The Impact of COVID-19 on Warehouse Real Estate The global pandemic has significantly affected the warehousing industry, with the need
In this episode of The New Warehouse Podcast, Kevin welcomes Jeff Lem, President and Founder of Portable Intelligence, to discuss
Live from ProMat 2023 Joel Thomas, Director of Intralogistics at Siemens, stops by the booth to discuss the future of
In this episode of the New Warehouse podcast, Corey Apirian, Davinci Micro Fulfillment’s founder, and CEO, sits down with Kevin
In a special panel episode of The New Warehouse, host Kevin Lawton welcomes industry experts to discuss Rajant’s revolutionary Kinetic
Ken Ramoutar, Chief Marketing Officer at Lucas Systems, joins The New Warehouse live from ProMat 2023. Lucas Systems is a
Welcome to The New Warehouse podcast! Tim Victor is the Project Lead for Electric Vehicles at Scale Microgrid, a company
Get ready to be inspired as Julio Diaz, the founder, and CEO of iLogistics USA, an e-commerce 3PL fulfillment company
CMO Dan Gilmore and CTO Mark Fralick of Softeon join The New Warehouse from ProMat 2023 to discuss the smart
For this episode of The New Warehouse, Nick D’Alessio, Senior Business Development Manager at Brother Mobile Solutions, joins Kevin live
Anil Varanasi, CEO and Co-Founder at Meter, joins The New Warehouse to discuss fast, secure, and reliable wireless connectivity for
In this episode of The New Warehouse, Kevin sat down with Matt Fain, CEO of Pop.Capacity. Pop.Capacity is a digital