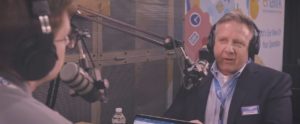
Episode 315: Sparck Technologies at MODEX 2022
Welcome to The New Warehouse podcast live from MODEX 2022! In today’s episode, Kevin talks with Sparck Technologies, a company
Welcome to The New Warehouse podcast live from MODEX 2022! In today’s episode, Kevin talks with Sparck Technologies, a company
Welcome to The New Warehouse podcast. In this episode, Kevin is joined by John Evans, Sr. Customer Success Manager/3PL Team
From the booth at MODEX 2022, Todd Boone, Director of Product Management Robotics and Automation at Zebra, joins Kevin for
Today’s guest is Aaron Smith, founder of U-Turn Transport and host of the Escape the Odds podcast. Aaron is on
The cannabis industry is growing at an unprecedented rate, and with that growth comes the need for innovative technology solutions.
Show favorite and CEO of Raymond, Mike Field, joins Kevin for a special episode of The New Warehouse Podcast as
Welcome to the New Warehouse Podcast! In this episode, Kevin is live from MODEX 2022. Craig Henry, U.S. Industry Manager
Joining Kevin from the booth at MODEX 2022 is Vince Martinelli, Head of Product and Marketing at RightHand Robotics. Unlike
Welcome to the New Warehouse podcast. In this episode, Kevin welcomes Paul Short, president of Combilift North America, as his
Coming to you from the booth at MODEX 2022, we welcome Jonathan Katz to this week’s episode of the New
No matter where your organization finds itself in its sustainability journey, you won’t want to miss this week’s episode of
Joining me from the booth at MODEX 2022 is Jay Jette, president, and CEO of GMR Safety. With a passion
In this week’s episode, we discuss the state of the warehousing labor market with Daniel Altman, Chief Economist at Instawork.
In this week’s episode of The New Warehouse, we are talking about an often overlooked aspect of warehousing, yard management
David Suarez joins me this week from the booth at MODEX 2022. David Suarez is the VP of Business Development
How fitting to have three guests join me for what is officially the 300th episode of The New Warehouse Podcast.
I’m excited to welcome back Seth Weisberg to the New Warehouse Podcast. Seth is the CEO of ABCO Systems which
Joining me this week from the booth at MODEX 2022 is Jake Heldenberg from Vanderlande. Jake is the senior manager
We are coming to you live from the Procensis Solution Center for this week’s episode of The New Warehouse. My
Joining me from the booth at MODEX 2022 for this week’s podcast is Brett Wood, the president, and CEO of