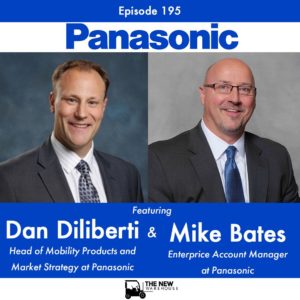
EP 195: TOUGHBOOK S1
On this episode, I was joined by two guests from Panasonic, Dan Diliberti and Mike Bates. We discuss the new
On this episode, I was joined by two guests from Panasonic, Dan Diliberti and Mike Bates. We discuss the new
On this episode, I was joined by A.K. Schultz the Co-Founder and CEO of SVT Robotics. A.K. and I connected
On this episode, I was joined by Vince Martinelli of RightHand Robotics at ProMatDX2021 . Vince has been on the
In this episode, I was joined by the president of B&C Logistics, Brian Severson. B&C Logistics is a 3PL that
On this episode, I was joined by Peter Schnorbach of Manhattan Associates. Peter is the Senior Director of Product Management
In this episode, I was joined by Rob Bussey of BWS Logistics. Rob is the National Account Manager at BWS
On this episode, I was joined by Dave Baiocchi of Resonant Dealer Services. We focused the discussion on something I
In this episode, I was joined by Jim Dempsey of Panasonic. Jim is the Director of US Business Development and
On this episode, I was joined by Jeff Christensen of Seegrid at ProMatDX 2021. Jeff is the VP of Product
In this episode, I was joined by John Slavik of Raymond. John is the Senior Sales Manager for Intelligent Warehouse
On this episode, I was joined by Sarah Swan of The FPI Consortium. Sarah is a Senior Code Specialist at
On this episode, I was joined by Darren Stratton of Camso, a non-marking tire company. Darren is the Product Management
On this episode, I was joined by the Co-Founder and CEO at SIERA.AI, Saurav Agarwal. I was very excited for
On this episode, I was joined by Sean Webb of Quadient at ProMatDX2021 . Sean is the Director of Automated
In this episode, I was joined by Jake Jakobson of Custom Industrial Products for the latest in our partnership with
On this episode, I was joined by the Director of Strategy at ProMatDX, Matt Cherewka. We have had Vecna on
On this episode, I was joined by Concentric’s VP of Marketing, Ryan Lynch. Concentric focuses on making sure you have
On this episode, I was joined by the VP of Product and Analytics at 6 River Systems, Gillan Hawkes. I
On this episode, I was joined by Avery Dennison’s Vice President of Identification Solutions, Ryan Yost. We discussed Avery Dennison’s
EP 176: CognitOps On this episode, I was joined by the Co-Founder & CEO at CognitOps, Alex Ramirez. CognitOps is