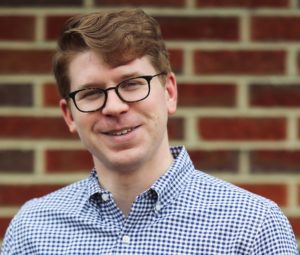
Episode 135 – RightHand Robotics
In this episode, I was joined by Vince Martinelli of RightHand Robotics. Vince is the Head of Product & Marketing
In this episode, I was joined by Vince Martinelli of RightHand Robotics. Vince is the Head of Product & Marketing
In this episode, I was joined by Josh Butler of Kinetic Eye. He is the Founder and CEO at Kinetic
In this episode, I was joined by Peter Christian who is an author, consultant, and teacher in the supply chain
In this episode, I was joined by John Conte who is the Founder and CEO at Conte Logistics Consulting. He
On this episode, I was joined by the Director of Business Development at Noviland, Francois Jaffres. Noviland is a cloud-based
In this episode, I was joined by Jen Ward of Peak-Ryzex where she is the offering manager. We discuss how
In this episode, I was joined by Jonathan Wright of IBM. Jonathan is the Global Head of Cognitive Process Reengineering
In this episode, I got a chance to speak with Tracy Hansen of ProGlove. Tracy is the president, North America
In this episode, I was joined by Dave Baiocchi for the December 2020 Material Handling Wholesaler cover story entitled “Factory
In this episode, I was joined by former guest Mark Wheeler of Zebra Technologies. Mark is the Director of Supply
In this episode, I was joined by the CEO of Wyebot, Roger Sands. Wyebot is the leader in AI-driven WiFi
In this episode, I was joined by Tim Wittig who is the General Manager of Motive Power Specialty at Enersys.
In this episode, I was joined by Brad Gossard who is the General Manager of Regal Conveying. You may remember
In this episode, I was joined by the CEO of SCI, Chris Galindo. SCI is one of the largest 3PL’s
In this episode, I was joined by Dr. Sankalp Arora of Gather AI who is their Chief Robotics Engineer. Gather
In this episode, I was joined by the president and CEO of PINC, Matt Yearling. You may remember PINC from
In this episode, I speak with Josh Cloer who is a Sales Director at Mobile Industrial Robot. This episode was
In this episode, I was joined by two guests for the November 2020 cover story of Material Handling Wholesaler. I
In this episode, I was joined by Ranga Bodla of NetSuite. Ranga is the VP of Field Engagement and Marketing
In this episode, I was joined by Art Eldred of VARGO Solutions. Art is the Client Executive of Systems Engineering