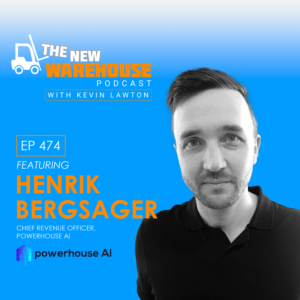
Episode 474: AI for warehousing with Powerhouse AI
In today’s episode of The New Warehouse Podcast, we are talking AI for Warehousing with Henrik Bergsager, Head of Strategic
In today’s episode of The New Warehouse Podcast, we are talking AI for Warehousing with Henrik Bergsager, Head of Strategic
In this episode of The New Warehouse, Kevin is joined by Read Egger, the Head of Growth Operations and Go-To-Market
This episode centers on the burgeoning trend of nearshoring. Mauricio de la Cerda, the Head of Growth at NowPorts, joins
This episode of The New Warehouse Podcast features Jerry Abiog, CEO of Standard Insights, discussing the pivotal role of AI
This episode of The New Warehouse Podcast features Dr. Mor Peretz, CEO of CaPow. CaPow, short for capacitive power, is
In this episode of The New Warehouse Podcast, Lee Rector, CEO of Embassy Data Logistics, joins Kevin for an informative
It’s an away game for The New Warehouse Podcast as Kevin visits the headquarters of Retail Reworks in Houston, Texas.
In this episode of The New Warehouse Podcast, we delve into the transformative power of automation in warehousing and logistics
In this captivating episode of the New Warehouse podcast, we discuss personalized 3PL services with Kate Terry, Chief Commercial Officer
Get ready to dive into the intricacies of international e-commerce expansion with guest Riki Hooker, General Manager at Global E-commerce
EnerSys® will premier its latest NexSys® charging innovations at MODEX 2024 – the NexSys® AIR wireless charger and the NexSys®+ Outdoor charger. Engineered
In this episode of The New Warehouse Podcast, Dennis Hoang, COO and Co-Founder of Patturn, delves into the innovative world
In this episode of The New Warehouse Podcast, we had the privilege of visiting Capacity’s headquarters in North Brunswick, New
In this episode of The New Warehouse podcast, we’re joined by Van Tucker, VP of Technology Partnerships at Harbor Lockers.
Welcome to the latest episode of The New Warehouse Podcast, where we sit down with Mark Harris, the visionary CEO
When is it good for things to be crawling around your warehouse? You’ll find out on this episode of The
In this episode of The New Warehouse Podcast features Courtney Folk, CEO and Co-Founder of Renewal Logistics. We delve into
Welcome to Episode 458 of The New Warehouse Podcast, featuring an in-depth discussion with Brendan Feeney, Director of Sales for
In this week’s episode of The New Warehouse Podcast, Justin Griffith, CTO at StayLinked, and David Krebs, EVP of Enterprise
In this episode of The New Warehouse Podcast, Jagan Reddy, the Managing Partner at NetLogistik US, joins the episode to