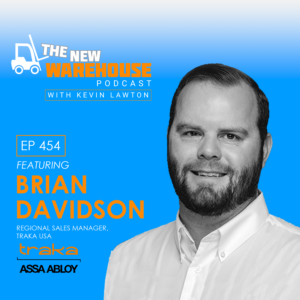
Episode 454: Innovating Asset Management in Warehousing with Traka
In this episode of The New Warehouse Podcast, Brian Davidson, Regional Sales Manager at Traka Americas, joins the show to
In this episode of The New Warehouse Podcast, Brian Davidson, Regional Sales Manager at Traka Americas, joins the show to
In this episode of The New Warehouse Podcast, Kevin speaks with Yong-Soo Chung, Founder and CEO of First Class Founders
In this episode of The New Warehouse Podcast, we’re diving into the intriguing world of returns with Spencer Kieboom, co-founder
Joe McIntyre, the founder and principal of Twelve48, joins this episode of The New Warehouse to discuss the logistics and
Michael Pytel is the co-founder and CTO of Fulfilld, a pioneering company introducing a new warehouse management system (WMS) to
In this episode of the New Warehouse Podcast, Anar Mammadov, the Technical Co-Founder of Senpex, shares how Senpex uses artificial
Episode 448 of The New Warehouse Podcast features an engaging conversation with Nick DiNatale, co-founder and CEO of ShipPlug. ShipPlug
In episode 447 of The New Warehouse podcast, Kevin is joined by Glynn LoPresti, the co-founder and CEO of Takt.
You don’t want to miss this feel-good episode featuring Chad Pregracke, CEO of Green Current Solutions. With a unique background
Steve Denton, CEO of Ware2Go, and Sara Mader, CEO of Palouse Brand, join episode 445 of The New Warehouse Podcast
In the latest episode of The New Warehouse Podcast, Robbie Cluett, Vice President of Business Development & Customer Success at
In this episode of The New Warehouse podcast, Kevin welcomes Nilay Parikh, the founder and CEO of Arvist. By leveraging
In episode 442 of The New Warehouse podcast, Kevin talks with Michael Walsh, CEO of Green Cubes Technology. The company,
In episode 441 of The New Warehouse podcast, Kevin is joined by Aaron Alpeter, founder of Izba. Izba, a multifaceted
In this episode of The New Warehouse Podcast, Kevin welcomes Jeremy Dang, Vice President of Business Development at Electrovaya, to
In this pre-Thanksgiving episode of The New Warehouse podcast, we welcome Jamie Callihan and Phil Denton from JLC Robotics. Jamie
The New Warehouse podcast recently welcomed Ryan Polakoff, the President of Nexterus, for a fascinating discussion on the evolution and
In this episode of The New Warehouse podcast, Jamie Dorland, a seasoned construction executive at Caddell Construction, joins the show.
In the latest episode of The New Warehouse podcast, Brendan Heegan, Founder and CEO of Boxzooka, joins the show. With
In the latest episode of The New Warehouse podcast, Kevin sits down with Gaurav Khandelwal, CEO and founder of Velostics,