American Rental Association named Best Place to Work
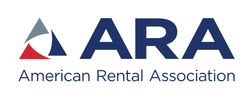
Quad City headquarters sets the standard for workforce culture The American Rental Association (ARA) has been honored as the Best Place to Work 2021 by the Quad City Times. The recognition is based on an employee nomination and employee voting. The ARA topped the list of Best Places to work in a region with a strong manufacturing legacy. The area is also a business hub with more than 150 companies on Fortune’s 500 and 1000 lists. The ARA consists of 64 employees with headquarters in Moline, Illinois. The central goal of the organization is to support the success of 11,000 members across 52 countries and advance the rental industry through strategic pillars that include education, technology, market intelligence, consumer awareness, and workforce development. The designation as a Best Place to Work showcases the ARA’s commitment to workforce development by modeling the culture and support for employees. The result is a strong sense of pride and drive to contribute to the goals of the association. “There is a positive vibe within the organization and a positive attitude shared by all our employees and staff. That comes through to our members and makes people proud to be a part of the ARA,” said Keith Pearson, Rental Industry Workforce Development Director. “When you have a strong belief in the industry that you are a part of, and a belief in supporting that industry, you take pride in what you do.” The ARA has been a staple in the Quad Cities community since 1955, which includes Davenport and Bettendorf, Iowa, and Moline and Rock Island, Illinois.
Women In Trucking Association names Lily Ley as 2021 Influential Woman in Trucking
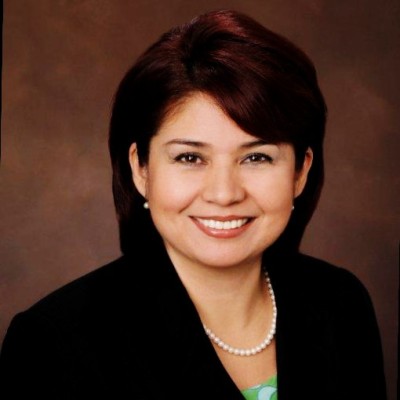
Women In Trucking Association (WIT) and Freightliner Trucks presented the 11th annual Influential Woman in Trucking award today to Lily Ley, Vice President and Chief Information Officer, PACCAR. The winner was announced during the WIT Accelerate! Conference & Expo in Dallas, Texas. The announcement came after the panel discussion “Inspiring Stories: How to Power Your Career.” The panel included all of the finalists for the 2021 Influential Woman in Trucking award and was facilitated by Elizabeth McManis, Manager, Brand Marketing, Daimler Trucks North America. The Influential Woman in Trucking award recognizes women in the trucking industry who make or influence key decisions, have a proven record of responsibility, and mentor and serve as a role model to other women. The award was developed in 2010 to honor female leaders in trucking and to attract and advance women within the industry. Finalists for the 2021 Influential Woman in Trucking award also included Eileen Dabrowski, Director of Learning, Development and Marketing, ReedTMS Logistics, and Amanda Schuier, Chief Operating Officer, Quality Transport Company. “After our conference in 2020 was virtual, it was refreshing to host the event live and listen to these outstanding finalists share their inspirational stories with the audience,” said Ellen Voie, WIT president and CEO. “This award is WIT’s way of highlighting Lily, Eileen, and Amanda for their commitment and service to the industry.” Lily Ley is an experienced Technology and IT executive, mentor to aspiring students, and passionate advocate for more inclusive workplaces for women. In her role as Vice President and CIO for PACCAR, a global automotive truck and engine company, Ley leads the Information Technology (IT) division and the modernization of IT for the Digital Age. She brings a customer-first mindset, a focus on applying innovation to deliver tangible business benefits, and a relentless pursuit of enhanced business efficiencies. Ley is a member of the MSIS Board of Advisors at the University of Washington. She is the Executive Sponsor for the PACCAR Women’s Association (PWA) where she advocates for the inclusion of women in the workplace. She is also involved in SeattleCIO, as an Advisory Board Member. In 2016, The Washington Diversity Council recognized her as “2016 Washington Most Powerful and Influential Women.” Ley has a Bachelor of Science in Computer Science and an MBA from CETYS University and has also completed the Executive Development Program at Stanford. She enjoys spending time with her husband German and two daughters and is passionate about travel and cooking.
Long Beach Harbor Commission appoints new Transportation Planning Director
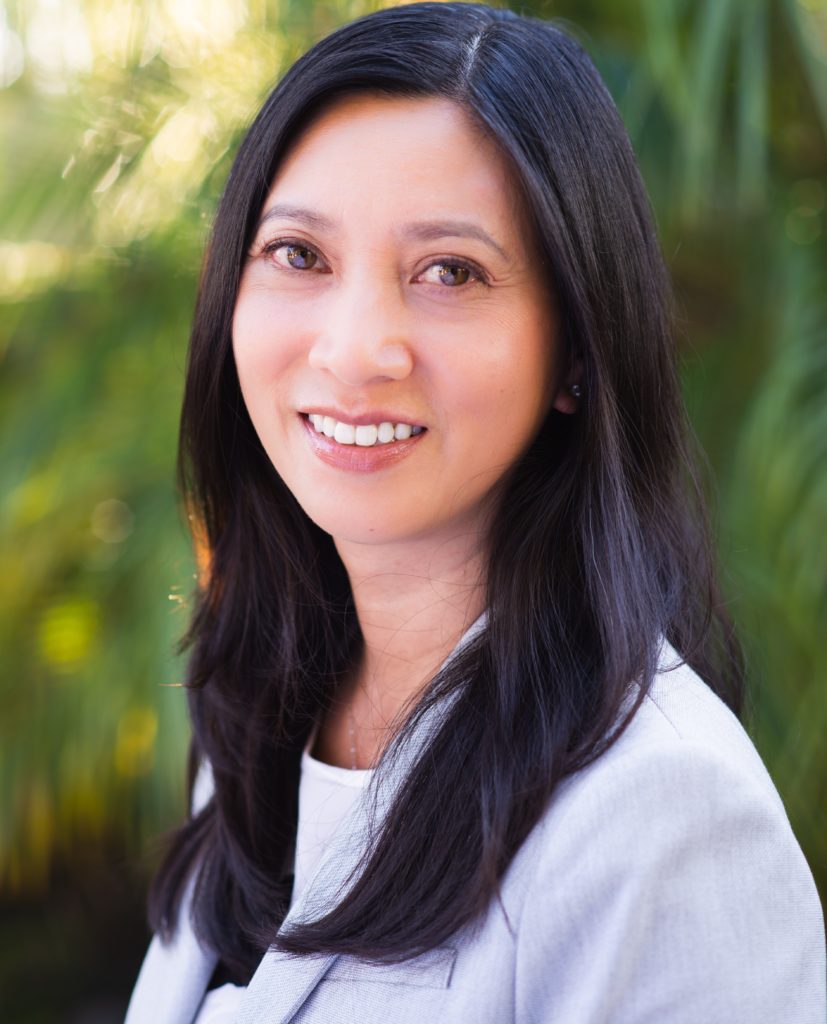
Dau-Ngo has served the Port of Long Beach since 2013 The Long Beach Board of Harbor Commissioners on Monday promoted Theresa Dau-Ngo to lead the Transportation Planning Division at the nation’s second-busiest seaport. Dau-Ngo started at the Port of Long Beach in 2013 as Manager of Transportation Development and was named Acting Director of the Transportation Planning Division in March 2021. The Director of Transportation Planning is responsible for guiding the analysis of the regional, state, and national transportation policies, regulations, and legislation; developing immediate and long-term transportation priorities; and assisting with managing Port-related traffic in support of supply chain optimization efforts. During her time at the Port, Dau-Ngo has received the Engineering Team Award presented to the Port Traffic Flow Task Force in 2017 and the 2016 Visionary Award for Women’s Leadership from the Port’s Women’s Leadership Circle. Prior to joining the Port, Dau-Ngo was a Supervising Planner with Los Angeles-based Parsons Brinckerhoff Inc., from 2000 to 2013. Earlier in her career, Dau-Ngo worked as a Transportation Planner with Wilbur Smith Associates Inc., San Francisco, and Meyer, Mohaddes Associates Inc., Seal Beach. She holds a Master of Science Degree in Civil and Environmental Engineering, and a Master of City Planning Degree from the University of California, Berkeley, along with a Bachelor of Science Degree in Planning and Development from the University of Southern California. She was also a 2019 participant in Leadership Long Beach. The appointment of Dau-Ngo is effective November 13, 2021.
Cimcorp joins MHI’s AS/RS Industry Group to further the development of Automated Warehousing Solutions
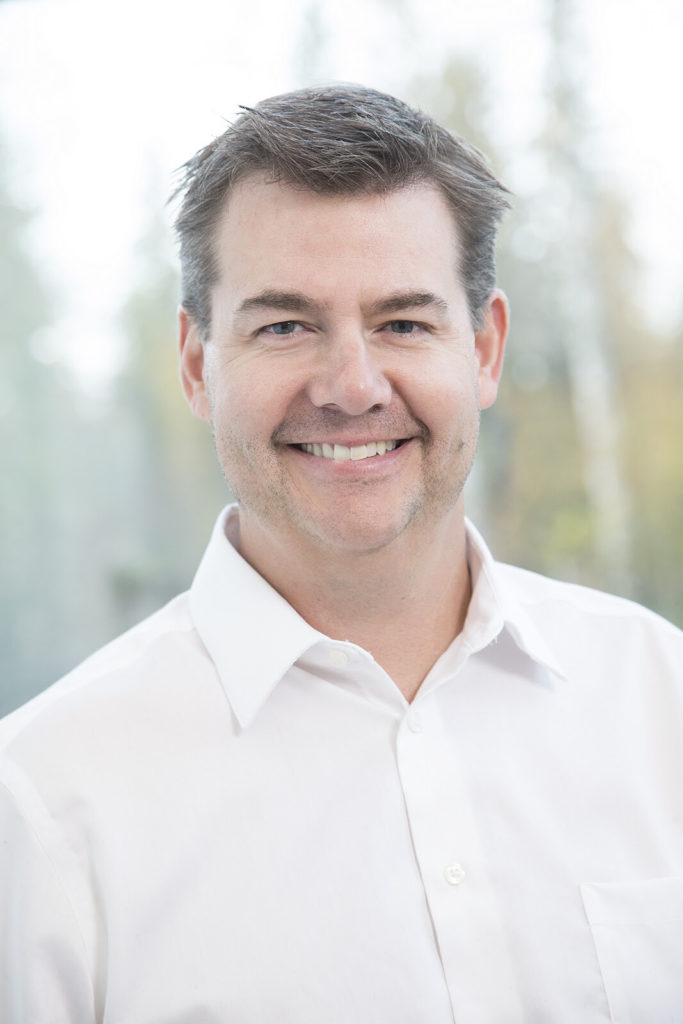
The Industry Group includes 25 of the world’s leading AS/RS suppliers who have installed thousands of systems worldwide, in virtually every manufacturing and distribution sector Cimcorp, a manufacturer and integrator of turnkey robotic order fulfillment and tire handling solutions, proudly announces it has joined MHI’s Automated Storage and Retrieval System (AS/RS) Industry Group, a collective of the world’s leading AS/RS suppliers that focuses on collaboratively growing and supporting the AS/RS market. As part of the Industry Group, Cimcorp will leverage its knowledge and expertise to help MHI members and customers discover efficient, safe, and innovative solutions to their most pressing material flow challenges. Incorporated in 1945, MHI is the nation’s largest material handling, logistics, and supply chain association that helps equipment and system manufacturers promote their solutions and advance the industry. It is an authoritative resource that offers education, networking, and solution sourcing for its 800+ members, its customers, and the industry at large. MHI includes 17 Industry Groups that represent the leading providers in several key equipment and system solution categories. The AS/RS Industry Group meets regularly to share and evaluate standards for the design, performance, and proper operation of AS/RS solutions. As a provider of intralogistics solutions, Cimcorp has installed automated systems in over 40 countries across six continents and is ready to lend its voice to further the AS/RS Industry Group’s mission. Cimcorp’s comprehensive portfolio of systems includes a variety of storage and retrieval solutions that uniquely solve critical challenges in warehousing and distribution. Cimcorp’s technology can handle a wide range of products with high speed and precision, making it ideal for industries such as retail, e-commerce, third-party logistics, and grocery—an industry in which Cimcorp has a wide breadth of experience. Notably, Cimcorp’s solutions have the flexibility to manage a distribution center’s entire operations or operate as an ‘island’ of automation within a manual facility. Derek Rickard, Director of Sales, Cimcorp Automation Ltd., commented, “We are excited to bring our insights and experiences to MHI’s members, as well as learn from fellow industry leaders! At Cimcorp, we know that implementing an AS/RS can have a big payout for warehouses and solve some of the biggest challenges in modern distribution—from labor shortages and safety concerns to SKU proliferation and shrinking storage space to rising customer demands for faster fulfillment speed. We also know that every organization’s warehousing needs are unique and that successful automation projects require so much more than technology. We bring extensive project management expertise to the table, and can help educate MHI members in best practices to reduce uncertainty, while ensuring safety and quality, during the implementation process.”
HNRY Logistics is renamed Yellow Logistics
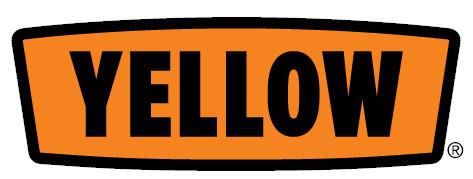
HNRY Logistics, the coast-to-coast logistics brokerage brand of the Yellow Corporation companies, is now Yellow Logistics. “We’re excited to announce this renaming and rebranding to Yellow Logistics, which aligns with the evolution of the LTL brands to one company, as Yellow,” said Jason Bergman, Yellow Chief Commercial Officer and Yellow Logistics President. “This milestone on our journey will make direct-to-carrier shipping easier than ever for our customers. Yellow Logistics has the technology, trucks, and talent to prioritize customers’ supply chains and deliver like never before.” Yellow Logistics offers custom logistics solutions as a one-stop shop for customers needing truckload, intermodal, residential, engineered solutions, retail/pool distribution, contract and reverse logistics or express direct services.
Arbon Equipment acquires Minnesota-based Pugleasa Company, Inc.
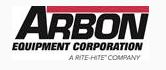
Milwaukee-based Arbon Equipment Corporation, a wholly-owned subsidiary of Rite-Hite, has acquired Pugleasa Company, Inc., a loading dock and industrial door sales and service organization headquartered in Arden Hills, Minnesota. Pugleasa Company has been in the material handling business for 65 years and has been the exclusive distributor of Rite-Hite products in Minnesota, the Dakotas, and parts of western Wisconsin and northern Iowa since the mid-1980s. Curt Moses has owned Pugleasa since 2008, during which the business grew thanks to a strong focus on employing good people, providing quality products, and excellent customer service. “Rite-Hite’s long and healthy partnership with Curt and the Pugleasa team made this acquisition a natural for our organization,” said Gerry Timms, president of Rite-Hite Company LLC, and Arbon Equipment Corporation. “And our customer-focused philosophy is right in-line with what the Pugleasa team has been doing since their founding.” The Pugleasa employees are now part of the Arbon Equipment organization and the work of serving customers continues uninterrupted. This new office is part of a growing network of Arbon Equipment sales and service providers with over 65 offices in the USA, Canada, and Australia.
Brown Machine Group is now BMG
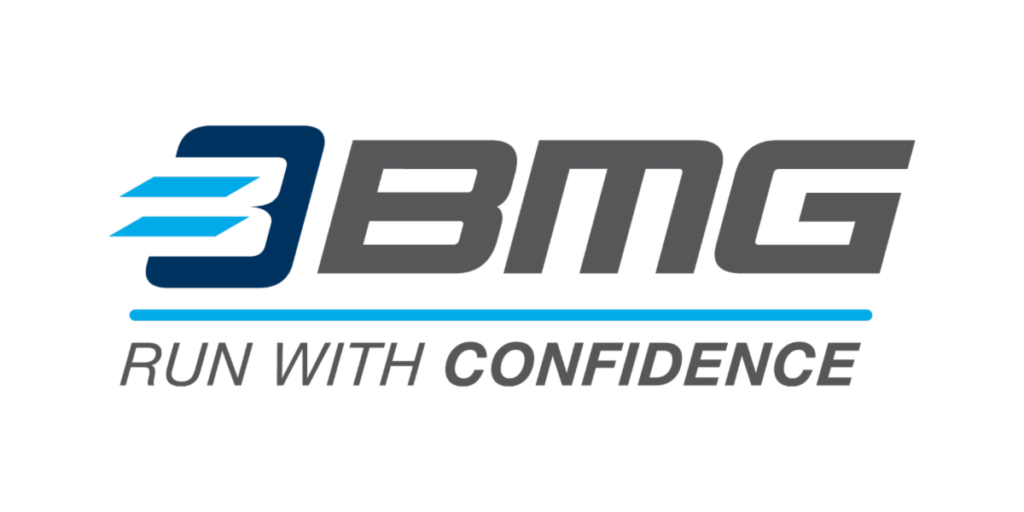
The new name reflects growth and integration into a complete turn-key solution provider in the plastic and paper industry Brown Machine Group, a provider of forming, tooling, and automation solutions for the global packaging industry, has announced that it is changing its name to BMG to reflect its growth and market position as a global turn-key solutions provider for the plastic and paper packaging industry. Brown Machine Group was originally created with the purpose of unifying a collection of industrial brands into one family. The company has grown steadily, including by recently acquiring GN Thermoforming. The company’s new branding as BMG brings together the companies already owned by Brown Machine Group under one consistent name. “BMG is Brown, Lyle, GN, Freeman, NAS and aXatronics. Brown Machine Group was already being shortened to BMG both externally and internally, and we believe the change is more inclusive to our family of brands and is easy for our customers to identify and remember,” explains Greg Wolf, BMG’s President and CEO. “BMG is our umbrella, and each brand can talk about solutions across the portfolio to fit customer needs. Together, BMG represents experience, innovation, and superior customer service, with a reputation for delivering solutions to improve consistency, productivity, and profitability. We look forward to building on BMG’s solid foundation in future growth through acquisition.” In conjunction with the name change, BMG has aligned its businesses into three core areas to serve its customers: BMG FORMING SOLUTIONS, which offers a wide variety of sizes and capabilities for thermoforming machines through the Brown, Lyle, and GN product offerings; BMG TOOLING SOLUTIONS, which offers forming, trim, form-fill-seal and contact heat tooling by Freeman and GN; BMG AUTOMATION SOLUTIONS, which offers robotic material handling and packaging automation by integrating NAS and Axatronics products
Global Shop Solutions names John Davis Chief Technology Officer
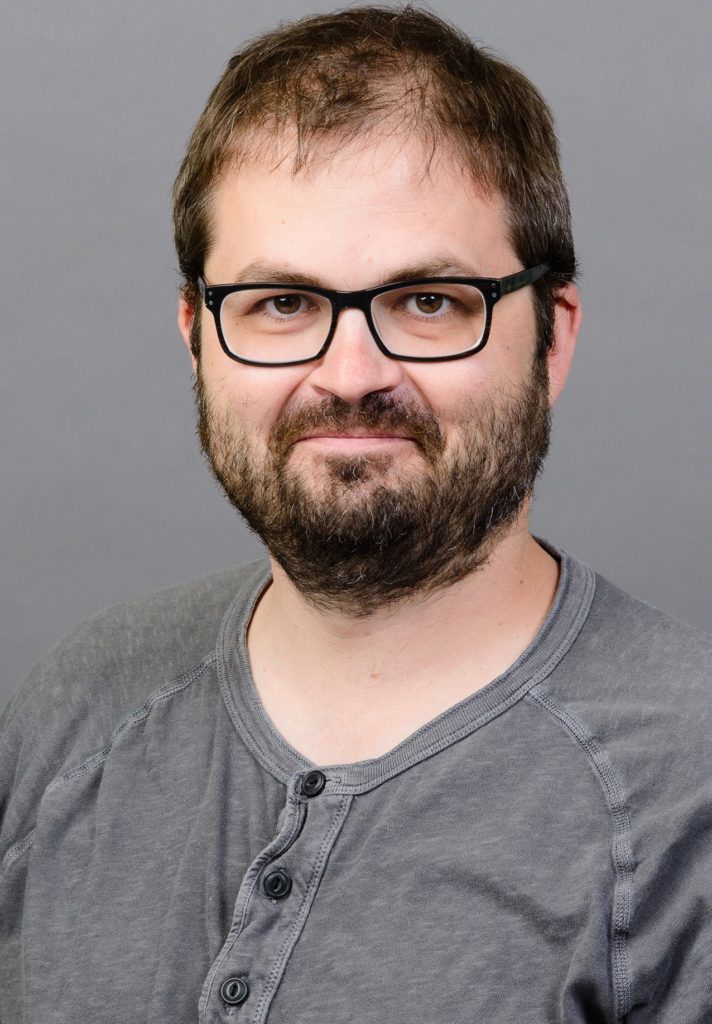
Global Shop Solutions, a developer of ERP software for manufacturers around the world, has named John Davis as Chief Technology Officer (CTO). Davis joined Global Shop Solutions in 2004, and over the past 17 years has served the company in many different capacities including analyst, programmer, and management. Most recently he led the R&D Infrastructure Team, and his excellent programming, networking, and all-around technical knowledge have played a critical role in shaping the company’s ERP software product. “John has been instrumental in leading Global Shop Solutions technical strategy so our customers can take advantage of the benefits IoT brings to the manufacturing industry,” says Erika Klein, VP of R&D. “As CTO he will define the standards for the technical excellence we hold ourselves to.” An experienced systems analyst in the computer software industry, Davis combines strong Visual Basic, Object-Oriented Design, SQL, Perl, and C++ skills with a background in Computer Resource and Instructional Planning. He received his degree in Interdisciplinary Studies with an emphasis in Computer Science, Business Information Systems, and Instructional Technology from Utah State University. “A great leader and coach for our developers, John will be responsible for raising the skill set of all our developers by mentoring and challenging them,” adds Klein. “He will determine which technologies drive our product and develop our feature roadmap for the years to come.”
The MHEFI Exceptional Contribution Award presented to Arlin Keck
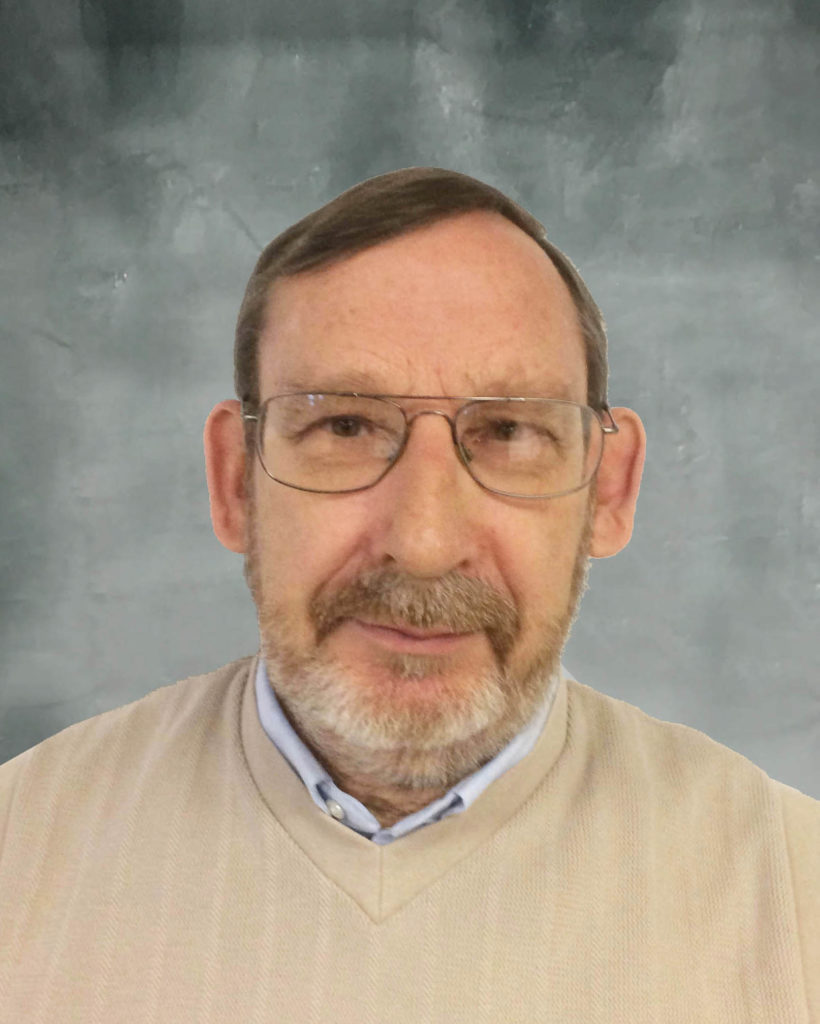
Steel King Industries, a manufacturer of storage rack and material handling products, is proud to announce Arlin Keck P.E., Steel King, Corporate R&D Engineer, has received the Material Handling Education Foundation, Inc. (MHEFI) Exceptional Contribution Award. The award is presented to individuals, organizations, or corporations who contribute to the material handling industry in extraordinary ways. Keck has worked in the material handling industry since 1973 and has been with Steel King since 2005. As an engineering leader and active member of the Storage Manufacturers Associations (SMA), Keck was chosen to receive this prestigious award for his extraordinary contributions to engineering standards for not only SMA but for storage materials throughout the industry. “We are privileged to have Arlin Keck as a key member of the Steel King engineering team for over sixteen years. In his service to Steel King, Arlin has facilitated the growth of Steel King’s capabilities beyond prior constraints and target market sectors. He has contributed greatly to our rapid growth,” stated Jay Anderson, president at Steel King Industries. Anderson continued, “Now in his fifth decade of engineering within the material handling industry, Arlin is a practical yet very creative engineer. In his many years as Engineering Committee Chairman for SMA, Arlin has led that group in raising the standards of design integrity and user safety for the entire universe of manufacturers and the larger user community. As Arlin transitions from a leadership role within SMA, on behalf of all Steel King team members, dealers, and end-users, I thank and salute him for his service to our industry. Well done, Arlin!” During his time as the SMA engineering committee chair, Keck led the group in raising design standards and user safety code excellence for the entire group of member companies and the larger user community. “Arlin’s positive energy drove the engineering committee to get things done. He always was willing to help, and his positive attitude made it easier to get through some dry information faster,” stated Kevin P. O’Neill, president, Steele Solutions and SMA Industry Group Chair. Take a moment to watch the video in which industry experts attest to the enormous, lasting contributions that Keck made to both the industrial storage equipment industry and the material handling industry as a whole.
Ken’s Foods selects Westfalia Technologies to automate new Atlanta-Area warehouse
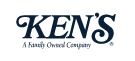
The warehouse will be the second Ken’s Food facility to install and streamline operations with Westfalia’s automated storage/retrieval and warehouse execution systems Westfalia Technologies, Inc., a provider of logistics solutions for manufacturers and distributors, announces its automation technology will be installed in the new Ken’s Foods, Inc. warehouse located in McDonough, GA. Westfalia’s automated storage/retrieval system (AS/RS) and Savanna.NET® Warehouse Execution System (WES) will fully automate the food manufacturing company’s 343K sq. ft. facility. This will be Ken’s Foods’ second location that incorporates Westfalia’s warehouse automation solutions. Ken’s Foods produces salad dressings, sauces, and marinades for a global network of customers. Westfalia’s technology will provide a reliable, temperature-controlled warehousing environment with a customized solution addressing all material handling, automatic layer picking, and integrated case picking requirements while delivering almost zero touches from receiving to shipping. The Savanna.NET® WES will streamline operations and provide seamless software integration between Ken’s Foods’ ERP system as well as all storage, order selection, and material flow automation. “Ken’s Foods Inc. has benefited greatly from the automation that Westfalia provided in our Massachusetts facility,” said Jim Bourne, Director of Transportation and Offsite Distribution at Ken’s Foods. “The system has allowed us to expand our operation in a smaller footprint and handle activities in an accurate and efficient manner. We look forward to putting a second system into our supply chain at the McDonough location as we continue to grow and meet our customer’s needs.” “Warehouse automation is critical for today’s food manufacturers to effectively keep up with high demand and a shrinking workforce,” said Dan Labell, President of Westfalia. “We are confident our automated warehousing system will optimize the McDonough location and operations for Ken’s Foods and are thrilled to continue our long-standing partnership with them.” The new warehouse will be built across the street from the existing Ken’s Foods manufacturing facility, further simplifying operations and taking more than 40 trucks off the highway each day.
Deane Nash joins Brown Machine Group as General Manager GN Thermoforming Equipment
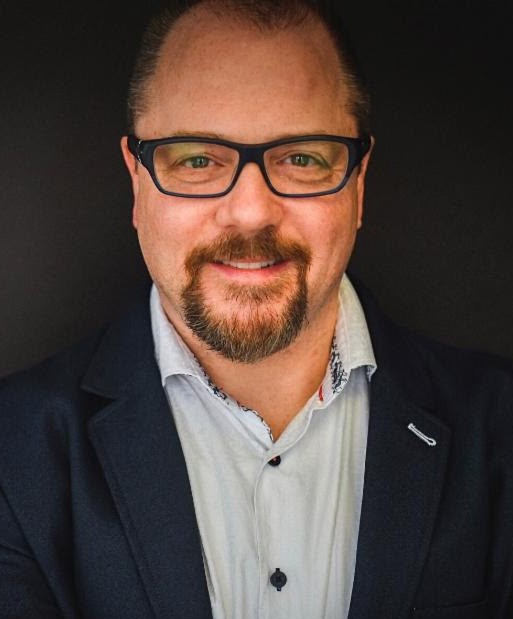
Skilled leader to focus on operations, tracking, and improving supply chain management BMG (Brown Machine Group) has announced the appointment of Deane Nash as General Manager of GN Thermoforming Equipment. Mr. Nash, an accomplished executive leader skilled in manufacturing management, brings more than 30 years of experience in plant startup, operations management, program launch management, and promoting business growth. He will be focusing on operations and developing superior tracking systems, as well as improving supply chain management and ensuring on-time delivery in light of pandemic-era constraints. Mr. Nash will also play a major role in supporting engineering teams and providing world-class technical sales and customer support. “I am extremely excited to join BMG, where I hope to drive performance with a strong focus on quality, service, on-time deliverables, and profitability,” said Nash. “My past success has been based on the power of effectively utilizing available resources and being a catalyst of change, with a clear and dynamic vision for future direction and goals. I look forward to using these skills to establish strong, mutually beneficial relationships with GN Thermoforming Equipment customers, suppliers, peers, and associates.” Mr. Nash is a highly self-motivated entrepreneur, with 33 years of experience in Tier 1 and Tier 2 automotive manufacturing organizations. He is known for his very shop floor-centric hands-on approach, which has resulted in great success for himself, his team, and his colleagues. Prior to joining GN, Mr. Nash spent 13 years at Precision Resource, a Tier 2 supplier of automotive, electronic, heavy industry, ordnance, and power-tool fine-blanked components and assemblies as Engineering Manager and previously was Operations Manager for China. He also served 16 years with Magna International, where he managed a highly automated CNC manufacturing plant as well as a high-pressure aluminum diecasting facility. “With his extensive manufacturing management experience in the automotive industry, Deane Nash is a great addition to our team,” said Jerome Romkey, President of GN Thermoforming Equipment Ltd. “He brings a great mix of general management, new factory construction, program management, continuous improvement, and sales to the table, as well as engineering, quality, and manufacturing skills that will help us in our quest for quality, on-time delivery, and ensuring a superior solution for our customers.”
Thomson Industries celebrates its 50th anniversary
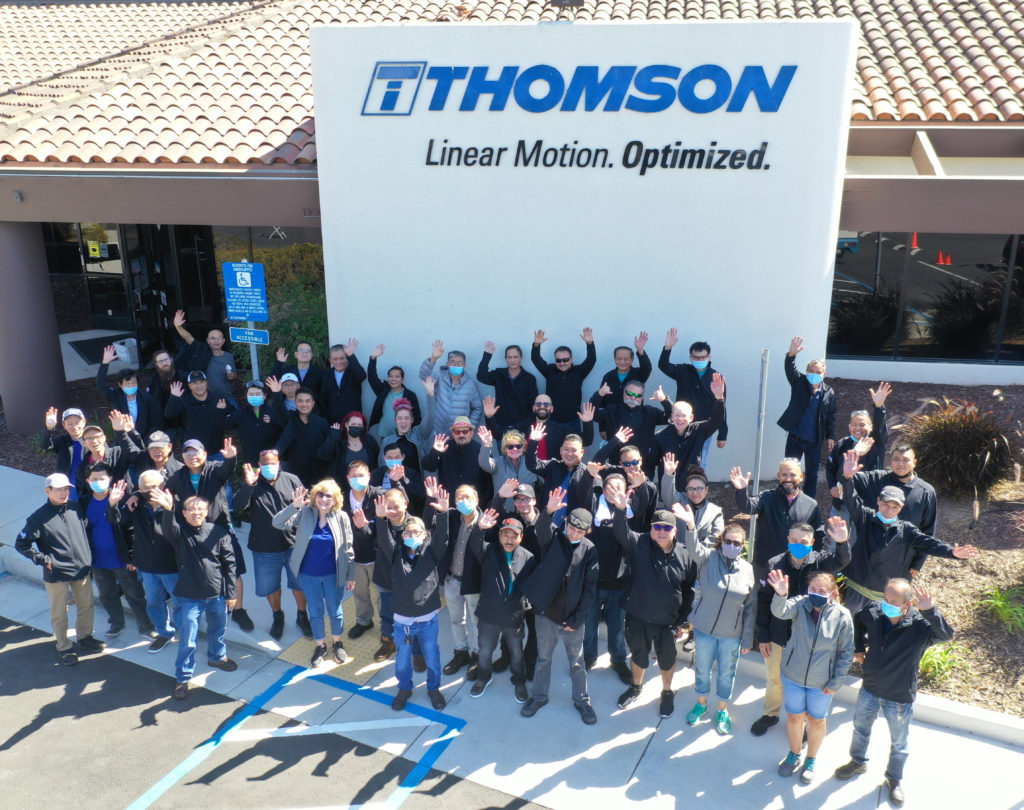
Thomson Industries, Inc., a manufacturer of linear motion control solutions, is celebrating the 50th anniversary of its legacy Ball Screws & Actuators Co. (BSA) business at its Fremont, California facility. The organization hosted a grand celebration to mark the occasion, highlighting its challenges and achievements, and reaffirming future goals. “The past 50 years have been an enjoyable and rewarding journey,” said Thomson President Scott Benigni. “We attribute this success to our hardworking and passionate employees, who work together toward the company’s objectives, and to our valued customers, whose faith in us has inspired our continued commitment to doing more and better things for them. We look forward to continued collaboration for the next 50 years and beyond.” The BSA business originated in 1971 when founder Scott Davis set out to machine ball screws for customers on the west coast of the United States. Initially, he sourced components from Thomson and other manufacturers but eventually developed his own components and patented his red Supernut® and ball screw product lines. These were well received by the semiconductor and medical product industries and, through various acquisitions and mergers, are now part of the Thomson catalog. The Fremont facility now produces Thomson lead screws and stepper motor linear actuators. The BSA acquisition was one of a series of acquisitions and mergers through which Thomson, now, as an operating company within Altra Industrial Motion, has evolved into a global provider in linear motion technology.
Raymond’s Jim O’Brien accepted into Forbes Business Development Council
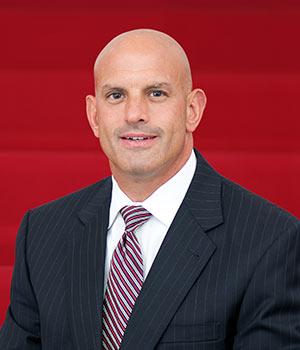
Forbes Business Development Council is an invitation-only community for Senior-Level Sales and Business Development Executives Jim O’Brien, Vice President of Sales at The Raymond Corporation, a global provider of best-in-class material handling products and intelligent intralogistics solutions, has been accepted into Forbes Business Development Council, an invitation-only community for senior-level sales and business development executives. O’Brien was vetted and selected by a review committee based on the depth and diversity of his experience. Criteria for acceptance include a track record of successfully impacting business growth metrics, as well as personal and professional achievements and honors. “We are honored to welcome Jim O’Brien into the community,” said Scott Gerber, founder of Forbes Councils, the collective that includes Forbes Business Development Council. “Our mission with Forbes Councils is to bring together proven leaders from every industry, creating a curated, social capital-driven network that helps every member grow professionally and make an even greater impact on the business world.” As an accepted member of the Council, Jim is invited to work with a professional editorial team to share his expert insights in original business articles on Forbes.com, and to contribute to published Q&A panels alongside other experts. “I am extremely excited to join the well-respected Forbes community,” said O’Brien. “I look forward to contributing to this network of business leaders and sharing my perspective on the future of the material handling and logistics industry.”
Cisco-Eagle has promoted Bryan Gauger to Vice President of Systems Integration
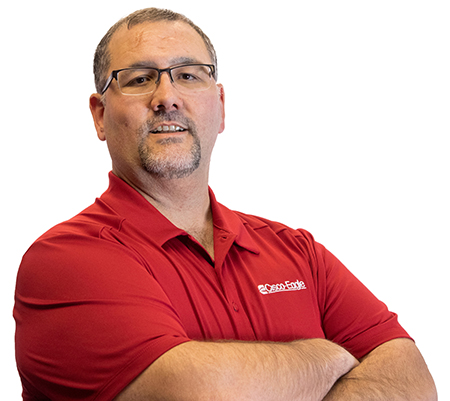
Cisco-Eagle has promoted Bryan Gauger to Vice President of Systems Integration according to Cisco-Eagle President Darein Gandall. Gauger brings decades of experience and a long list of accomplishments to the role. He started his material handling career as a CAD technician in 1996 and quickly rose to manage Cisco-Eagle’s CAD group. Gauger subsequently was promoted to work in various roles, including project management and application design positions. He became senior project manager before accepting the role of Director of Texas Systems Integration in 2018. In that position, Gauger was instrumental in the design and implementation of multiple large-scale material handling projects across the United States and in Texas. In his new role, Gauger will serve as part of Cisco-Eagle’s senior leadership team, where he will participate in strategic planning and other management decision-making. He will oversee the systems integration group, working with its teams on project design, integration, and implementation for a broad variety of material handling, conveyor, automation, and storage projects. Throughout his career, Gauger has worked Cisco-Eagle’s most significant customers and projects, designing and implementing automation concepts, sophisticated conveyor applications, advanced storage systems, and more. “Bryan is one of the best in the business,” said Gandall. “He has technical skills, experience, and knowledge, but what really sets him apart is his ideas. He’s got this way of seeing an operation and figuring out ways to improve it that is just flat out special.”
ProMach strengthens flexible Packaging Portfolio with acquisition of CL&D Graphics

The deal expands ProMach’s growing film and label converting capabilities for flexible and rigid packaging ProMach, a worldwide provider in packaging machinery solutions, announced today it has acquired CL&D Graphics and CL&D Digital. CL&D is a leading provider of high-quality flexographic and digital web packaging and converting solutions for consumer product companies. The addition of CL&D significantly expands ProMach’s portfolio of flexible and rigid packaging systems and strengthens its ability to provide complete machinery and material solutions for a broad range of packaging applications. CL&D Graphics offers roll-fed film and pressure-sensitive labels, shrink sleeves, pouches, lidding, and preprinted thermoform solutions to consumer packaged goods companies across North America. They provide complex, high-quality graphics for most unsupported film applications in the marketplace, along with research and development expertise in new product design as well as on-site technical support for packaging solutions to ensure consistent, attention-grabbing products in the marketplace. Additionally, CL&D Digital produces short-run, production quality prototypes and promotional samples to help bring products to market quickly with no minimum orders and rapid delivery for companies of all sizes. CL&D is GMP certified by the American Sanitation Institute to print both food contact packaging and non-food contact packaging and their innovations have earned numerous awards and certifications from the Flexible Packaging Association and Great Lakes Graphics Association. “We’re pleased to welcome the CL&D team to ProMach,” said Mark Anderson, ProMach president and CEO. “ProMach is always looking for new and unique ways to bring more value to our customers and CL&D changes that narrative for many of our clients in the flexible packaging space that has wanted a single-source partner who can provide a more complete and total solution including both materials and machinery. This proven model has served us well with our industry-leading brands like ID Technology and I’m confident this will be the case with our flexible packaging partners as we move forward. I am excited to work with the outstanding senior leadership team at CL&D as they continue helping ensure their customers’ products stand out on the store shelves and stand apart from the competition.” Brian Dowling founded CL&D Graphics in 1978 with Ed Flaherty and a single press in a small shop in Waukesha, Wisconsin. His vision of becoming a world-class flexographic printing company continued with his son Michael Dowling, current Chairman and owner. Under his tenure, CL&D has expanded over the last decade into a 24/7 operation, with four locations across Wisconsin and South Carolina operating numerous flexographic and digital presses. “For over forty years, we’ve worked to become the printer of choice for CPG companies across North America,” said Michael Dowling. “From our humble beginnings we’ve grown into one of the premier partners of customers from small businesses to Fortune 500 companies, I’m extremely grateful to our employees, without whom none of this would have been possible. From our locations in Hartland, Oconomowoc, and Rock Hill, our terrific team is the reason we’ve been able to help turn my father’s vision into a reality.” Hartland, Wisconsin-based CL&D and it’s over 280 employees are joining the ProMach team. Current CL&D president and CEO Mike Hokanson will join ProMach as Vice President and General Manager. “I’ve had the privilege of working with Mike for the last six-plus years and he has made a huge difference in our strategic vision and direction,” added Michael Dowling. “I look forward to helping support Mike as he leads CL&D forward as part of ProMach. With ProMach, we have a partner that has a strong and well-earned reputation in the packaging machinery marketplace, and they will help us expand our capabilities, accelerate our pace of innovation, and above all else help create additional value for our customers across the United States and Canada. We are looking forward to working with the entire ProMach team to continue this journey we embarked on so long ago.” “The CL&D team excels at helping build brands through packaging, and their strong customer focus and mentality of being easy to do business with is perfectly aligned with ProMach’s philosophy and approach of how we work with our over 55,000 customers across the world,” said Don Deubel, ProMach Senior Vice President, Flexibles & Trays. “CL&D complements a broad range of the ProMach portfolio, capable of partnering with our strong leading product brands like Matrix, Bartelt, FLtècnics, Modern, Axon, P.E. Labellers, Serpa, and more to provide a complete solution to the marketplace with film, labels, machinery, and a full range of support including parts and service. Constant innovation from CL&D and all ProMach product brands means we are able to meet our customers’ current needs as well as anticipate future needs to ensure we are there to support them every step of the way.”
Herc Holdings acquires New Hampshire-based Equipment Rental Business
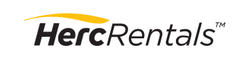
Herc Holdings Inc., a North American equipment rental supplier operating through Herc Rentals Inc., has announced that it has acquired substantially all the assets of Reliable Equipment, LLC, a New Hampshire-based equipment rental business with branch operations in Dover and Londonderry, NH. Terms were not disclosed. Reliable Equipment is a full-service provider of equipment rentals with a fleet that includes aerial, material handling, and earthmoving equipment, as well as specialty climate control and power generation equipment. Founded in 2010, the business has more than 50 employees and service coverage from Boston to Portland, ME. “The addition of Reliable Equipment expands our New England presence to eight physical locations, allowing us to serve existing and new customers with a larger fleet and improved responsiveness while also providing greater scale to operate more efficiently across the Northeast U.S.,” said Larry Silber, president and chief executive officer. “This transaction supports one of our key strategic initiatives to expand our presence in urban markets across North America. In particular, Reliable Equipment is well-positioned in the north Boston metropolitan area and to achieve growth in this dynamic market. “I am pleased to welcome the Reliable Equipment team to Team Herc. Our combined teams and resources position Herc Rentals to be a preeminent equipment rental partner throughout New England, serving a diverse mix of construction, industrial, and government customers.”
Cisco-Eagle promotes Eric Zuniga to Applications Specialist
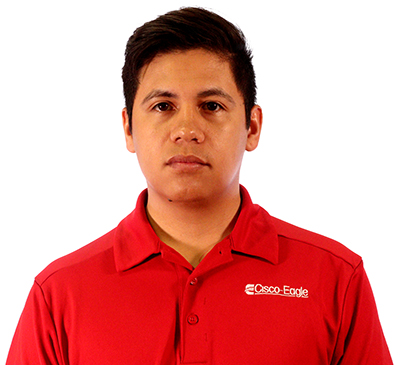
Cisco-Eagle has promoted Eric Zuniga to Applications Specialist according to Systems Integration Manager Bryan Gauger. Zuniga, who joined Cisco-Eagle’s systems integration group in 2018, will lead project design efforts for large-scale conveyor systems, warehouse layouts, automation, and other critical customer needs. He will help other designers and project managers during the design phase of projects, as well as oversee critical systems design and integration processes. “Eric is a big reason our customers succeed,” said Gauger. “His talent and work ethic will help us create better solutions for a broad range of customers. His new role gives him the ability to advise other designers and project managers across a wide number of projects. His ability to help customers at every step from concept to a realized system is a huge asset for us–and for our clients.” Zuniga will conceptualize and implement material handling solutions tailored to customer needs and objectives, utilizing a broad range of automation and conveyor solutions. Although his home office is in Dallas, Zuniga will work on projects in many other areas.
PLASTICS and ACC announce three new members to Elite Operation Clean Sweep blue Status
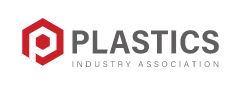
The Plastics Industry Association (PLASTICS) and American Chemistry Council (ACC) have announced the addition of three new members to Operation Clean Sweep blue. The elite status is achieved by exceeding rigorous standards set by Operation Clean Sweep® (OCS). OCS is an industry-led campaign dedicated to helping every plastic resin handling operation prevent plastic resin loss. New OCS blue Designees BASF (Florham Park, NJ) DuPont (Wilmington, DE) Eastman (Kingsport, TN) “Creating chemistry for a sustainable future is not just a tagline. We are proud to work with others along the value chain to drive a positive impact, which is why BASF signed on to OCS blue as a clear commitment to pellet loss prevention and protecting the environment,” said Gülay K. Serhatkulu, Senior Vice President, Performance Materials North America, BASF Corporation. “At DuPont, we are committed to a set of bold sustainability goals that are good for our communities and for our planet,” said Alexa Dembek, Chief Technology & Sustainability Officer, DuPont. “Joining Operation Clean Sweep blue underscores our commitment to best practices in facilities management and operation, including responsible resin handling and pellet containment processes.” “Eastman is committed to accelerating a more circular economy, and as that commitment stimulates product innovation at Eastman, it also inspires us to apply the same principles to our operations,” said Kellye Walker, Executive Vice President and Chief Legal Officer, Eastman. “By joining Operation Clean Sweep blue, we are underscoring our circularity efforts with our zero-incident mindset approach to safety, ethics, and compliance — driving continual improvement and creating a better circle.” “PLASTICS is proud of managing Operation Clean Sweep. Our industry recognizes the importance of ensuring that plastic is manufactured in a way that seeks to eliminate the loss of resin into the environment,” said Patrick Krieger, Senior Director of Materials and Sustainability at PLASTICS. “This requires coordination across the supply chain and dedication to sharing best practices and interventions. OCS blue reflects a commitment by these organizations to take this a step further seeking to become leaders in this mission. We welcome our newest members to the program and look forward to learning from and with them.” “America’s plastic makers congratulate the latest companies to achieve OCS blue status, and we encourage every company that makes or handles plastic pellets to do the same,” said Joshua Baca, ACC’s vice president of plastics. “Plastics are essential to a safer, cleaner, lower-carbon world – and all of us must work together to keep these advanced materials out of the environment.” The OCS blue achievement demonstrates these three companies’ commitment to preventing plastic from entering the environment or becoming marine debris. By achieving this elite status, these companies are held to a higher standard to eliminate plastic resin loss by conducting site audits, increasing employee awareness, and improving equipment, processes, and procedures at their facilities. For more than 25 years the plastics industry has promoted OCS, a campaign dedicated to helping every plastic resin handling operation prevent plastic resin loss. The Plastics Industry Association (PLASTICS) and the American Chemistry Council (ACC) strongly encourage companies to take their commitment – a pledge committing to OCS principles by plastics companies or plastics employees – to the next level.
Underground Machinery Rental adds Merlo Telehandlers and Rotos to its fleet
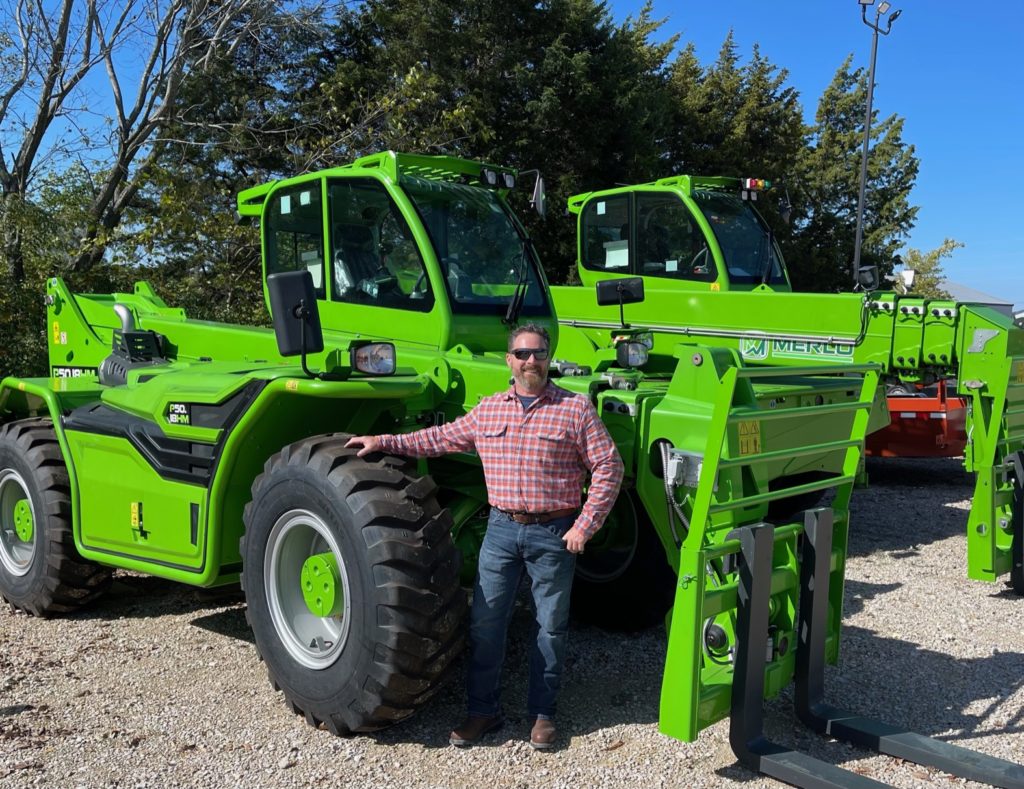
Underground Machinery Rental, headquartered in St. Louis, MO has added the Merlo line of telehandlers and Rotos to its fleet of specialized equipment utilized by the utility and construction markets across the USA. “Underground Machinery Rental was started in 2019 when we saw a need to fill the machinery gap that the utility and underground construction industry was experiencing,” said Justin Vermillion, Underground partner and VP of Sales and Operations. “Contractors need a reliable option for short or long-term underground machinery rentals to get projects completed on time and efficiently. This is what Underground Machinery Rentals delivers.” Underground Machinery Rental has developed a reputation for consistently supplying up-to-date and reliable equipment. Their current rental fleet includes DitichWitch®, fiber blowers and pullers, and their signature amphibious off-road industrial vehicle, the Fat Truck. After listening to customer requests, Vermillion and his team realized they needed to expand their offerings, and by extension, their market “to include a line of complementary equipment to sell as well as rent.” he said. “We became intrigued by Merlo telehandlers. We were looking for machines that delivered a broad range of operating capacities and capabilities.” “Underground Machinery has developed a laser-sharp focus on their industry,” said Bill Grundy, AMS-Merlo Territory manager. “They did their research and chose Merlo. These telehandlers fit their industry and product focus.” Recently, Underground took delivery of the Merlo High Capacity P50.18HM and the Roto 70.24 SPLUS with its 360° turret rotation. With just these two machines Underground has already expanded their customer base to include tree care and construction businesses in their area.“We like that these machines accept a broad range of attachments,” Vermillion said, “especially slewing platforms and the Woodcracker®. Both of these accessories fit the needs of our customer demographic. The Roto, with either attachment, makes powerline work cleaner and safer.” All Merlos are available for direct purchase and rent. See the full line of available Merlo telehandlers by visiting Uundergroundmachineryrental.com.
Exponential Power acquires Dry Creek Enterprises
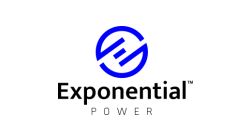
Exponential Power, Inc., a provider of stored power solutions, announced that it has joined forces with Bakersfield, California-based Dry Creek Enterprises. The acquisition enhances the company’s presence in the reserve power industry and supports its mission of delivering reliability, advancing technology, and providing an unmatched experience for its customers. Dry Creek Enterprises was founded in 1999 and quickly gained a strong reputation for outstanding service and commitment to excellence. Under previous leadership, the company developed a factory-trained service team servicing a variety of locations with critical power needs, including power plants, refineries, emergency response systems, and off-grid backup systems. “The partnership is a great addition to Exponential Power,” says CEO Jake Walker, “The team brings a solid track record and unwavering passion for delivering exceptional service to the reserve power industry.” He added that the acquisition “expands our West Coast service presence and supplements our existing businesses extremely well while aligning with our strategic vision.” The Exponential Power Stationary Service Team extends a warm welcome to Dry Creek Enterprises and looks forward to delivering quality work safely for every customer.