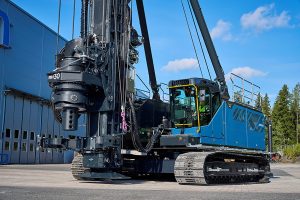
Junttan selects Volvo Penta as engine partner in next-generation equipment
Junttan has partnered with Volvo Penta to power its next-generation machines, starting with the new DR5 drilling rig uniting shared
Junttan has partnered with Volvo Penta to power its next-generation machines, starting with the new DR5 drilling rig uniting shared
FireLake Manufacturing of Hutchinson, MN, manufactures incinerators and crematoriums, serving the medical, veterinary, and law enforcement sectors. FireLake’s product line
When it comes to securing your products for shipment, selecting the right strapping materials is critical. This decision impacts not
When a landmark building in Nottingham required the replacement of its fabric tensile roof covering, the subcontractor tasked with this
Permanent lubrication system reduces maintenance costs A large beverage producer in Mexico invested in an automated system for packing and
The Plastics Industry Association (PLASTICS) has released a series of new videos as part of the Recycling is Real advocacy initiative. The
Versatile portable racks provide a wide range of flexible storage solutions for warehouse professionals Selective pallet racking is a versatile,
KHS technology boosts value creation in the production process at Schweppes Zimbabwe Limited A big step towards cutting greenhouse gas
When it comes to securing your products for shipment, selecting the right strapping materials is critical. This decision impacts not
R&M Materials Handling distributor, Specht Industries, has installed bridge cranes and hoists at a manufacturer of customized autoclave systems in
Gardiners is the UK’s leading distributor of global footwear and workwear brands to the retail trade. An award winning, family-run
Addressing labor challenges and enhancing operational efficiency are crucial priorities in manufacturing, warehousing, and logistics. Automating the palletized material workflow
In modern material handling, lithium-ion and lead-acid forklift batteries are popular choices for powering electric forklifts. When choosing the right
Learn how to create a safe, productive workplace JLG Industries, Inc., an Oshkosh Corporation business and a manufacturer of mobile
Material handling equipment has always been required to be efficient, reliable, and safe. However, as industries evolve, the focus on
CKF Systems was delighted to have been chosen by Primafruit to develop a new bespoke robotic de-palletising and re-palletising system
Learning how to identify and prevent these sins will reduce or eliminate unnecessary waste, improve efficiency and productivity, protect profitability
For businesses seeking optimal warehouse logistics management, Steel King Industries, an OEM with extensive expertise in designing and manufacturing high-quality
Market challenges post-Covid – including rising living costs, project delays and bottlenecks – will need to be overcome in order
The world’s largest producer of spirits is now benefiting from a turnkey package of three Italkrane ATEX-rated electric chain hoists