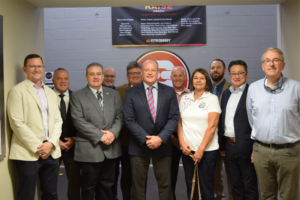
Kito Crosby announced significant investment in Peerless chain manufacturing equipment
Kito Crosby, a global leader in the lifting and securement industry, proudly announces the completion of a major investment at
Kito Crosby, a global leader in the lifting and securement industry, proudly announces the completion of a major investment at
Providing automotive-grade modular lithium battery systems that are transforming the material handling industry, BSL Battery – Industrial is at the forefront of innovation. With
Material-handling electric vehicles use two types of batteries: lithium-ion (Li-ion) and lead-acid batteries. The main deciding factors when choosing the right battery
Casper, Phillips & Associates Inc. (CP&A) has delivered a presentation to port authorities titled, ‘Peer Review of Container Cranes’, to
Vertical reciprocating conveyors (VRCs) act as the pivotal link between two major trends in warehouse operations that are dramatically increasing
Discover how HMS Networks’ wireless expertise and Anybus products took Mercedes-Benz’s Automated Guided Vehicle (AGV) installation to the next level.
The Transportation Intermediaries Association (TIA) released a new white paper titled Transforming Freight Logistics in the Era of Generative AI. The
Do you work in a paper or corrugated packaging plant? Are you looking for a solution that powers your workload?
By integrating Kardex Shuttles with ZOLLER TMS Tool Management Solutions Software, Intech Athens has taken a monumental leap in streamlining
The importance of accuracy has doubled in two years; drive to adopt new technology in the warehouse to improve accuracy
Identify hidden costs in two minutes with the total-cost-of-ownership-calculator How much do the printers you use on your production line
A large 7” vivid multi-touch display, with an integrated controller and expandable I/O, enables the new FT2J Series PLC+HMI to
Interest in and use of lithium-ion batteries in industrial trucks is growing. There are many advantages to this revolutionary technology,
Optimizing warehouse space is a critical endeavor for businesses looking to enhance efficiency and reduce operational costs. One innovative solution
Thomson Industries, Inc, a manufacturer of linear motion control solutions, has released a video: ‘Clean and Simple: The Electrification of
Movu Robotics is proud to spotlight their enduring partnership’s success through groundbreaking projects across Europe. Highlighting their successful long-term collaboration,
How to get personnel and material from ground level to mezzanine level quickly, safely, and efficiently Scissors lifts have been
The slimline infinite rotary units are suitable for the highly dynamic rotation of large workpieces and eccentric grippers as well
Hydraulic Dock Lifts have two advantages over other means of unloading trucks: Level unloading from the bed of a truck
From electrical equipment to environmental considerations, here are expert tips for smart selection What are filter fans? Filter fans protect electrical