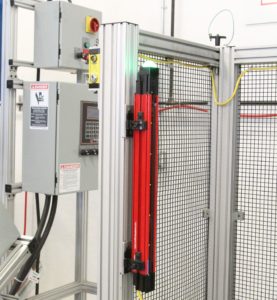
How Light Curtains brighten employee safety in industrial plants
At first glance, a simple beam of infrared light would seem ineffective protection against fast-moving, dangerous industrial machinery. After all,
At first glance, a simple beam of infrared light would seem ineffective protection against fast-moving, dangerous industrial machinery. After all,
mkhabur@onecharge.biz As the world recovers from the turbulent years of 2020 and 2021, we are seeing all sorts of repercussions
Selecting the right third-party logistics service provider can be a challenging experience for companies. After the coronavirus pandemic dismantled many supply chains,
Demand for industrial products has risen considerably over the past two decades — and with that, we’ve seen an increase
Bipolar Batteries: Little Gain for Lead-acid, Bright Future for Lithium As its name implies, “bipolar” battery technology uses an electrode
The Form, Design, and Chemistry of Lithium Forklift Battery Cells The diversity in forklift lithium battery cell design, chemistry composition,
When thinking of a modern distribution center, most people will picture a conveyor and sortation system. And while they are
When the coronavirus pandemic hit in early 2020, the e-commerce fulfillment landscape underwent a massive shift in response to spikes
Why are OSHA data statistics important? Ensuring employee safety in the workplace is a key challenge for all companies. Apart
Despite the growing trend towards electrification, propane continues to keep pace in the material handling space thanks to its reliable
Choosing industrial batteries can be complicated—there are just so many options that it can be difficult to decide which factors
Sri Lankan natural rubber is the key raw material used in GRI tires. Thus, natural rubber farmers are important stakeholders
The recent advances in lithium industrial batteries and their use in manufacturing are remarkable. So much so, that it may
Lithium-ion battery technology pairs well with the wine industry, like a good Cabernet with a lamb chop. The wine business
Logistics Drives Profitability in Food and Beverage Industry In the food and beverage industry, demand and growth are driven by
The impact of material handling on the recovery of the USA economy is monumental. Some segments were certainly hit harder
WITRON Logistic + Informatik Gmbh, (Parkstein, Germany) was tasked with reconfiguring UK health and beauty retail giant, Boots’ existing Nottingham
Recent independent degradation tests of commercial lithium batteries reveal a big surprise! Contrary to the claims of many NMC-based lithium
What does it mean for a specialist tire manufacturer to innovate? How can a company embed innovation into its DNA?
Fully automatic loading of bags on trucks The BEUMER autopac of the 2400 and 3000 construction series is a system