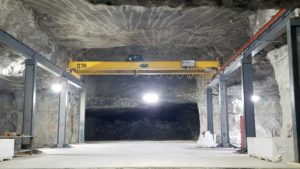
R&M Materials Handling Inc.installs underground 20-ton capacity overhead crane and hoist
A 20-ton capacity overhead crane and hoist from R&M Materials Handling Inc., sold by Harriman Material Handling (HMH), has been
A 20-ton capacity overhead crane and hoist from R&M Materials Handling Inc., sold by Harriman Material Handling (HMH), has been
If you’re reading this, you’re likely considering switching your fleet of forklifts and hand jacks to Lithium-Ion batteries. Or you
The Application Food Process Solutions (FPS) is a rapidly expanding company that specializes in the design and manufacture of large
Architecture & Engineering (A&E) firms provide professional services to support large industrial and infrastructure projects across a wide range of
Yale Materials Handling Corporation announces recognition on Supply & Demand Chain Executive’s annual list of 100 top supply chain projects.
As lithium-ion batteries continue to grow in popularity, lead-acid battery manufacturers are now offering thin plate pure lead batteries (TTPL)
Briggs & Stratton, a U.S. small engine manufacturer, made the switch to OneCharge lithium-ion batteries to achieve the highest performance
One of the leading US dairy producers made the switch to OneCharge Lithium-Ion batteries to ensure uninterrupted multishift warehouse forklift
Hyster Company has earned a spot on the Supply & Demand Chain Executive annual list of 100 top supply chain projects, for
The biggest impact of the ongoing pandemic, by far, has been the disruption in supply chains – from farm to
Audible and visible signals reduce risk of dangerous, costly accidents There are significant dangers to technicians, operators, and other workers
Automation brings unprecedented opportunities for the warehouses to improve operating efficiency and reduce costs. Among other innovations, Automated Guided Vehicles
BEUMER Group supports the start-up company Codept in developing a productive logistic platform BEUMER Group has declared digitization a top
Purchasing a forklift battery is an important investment. The question for many companies, however, is whether their choice is a
CDC Advice: Employee Health Protections Starting in January 2020, an outbreak of coronavirus (COVID-19) started in China and began to
Hy-Brid Lifts, the industry provider in high-quality, low-level access equipment, delivered the first order of ZT-1630 lifts to Advantage Rental
New Orleans, Louisiana-based Hoist & Crane Service Group (HCSG), a national provider for hoist and crane inspections, preventative maintenance, and
Products arrive in warehouses and distribution centers on any number of pallet types these days: two-way entry, four-way entry, skids,
Summary This is another example of a team effort that produced a great outcome for the customer. Papé Group / Pape Material
The war on packaging waste is fought on many fronts in the beverage industry – from the manufacturers of packaging