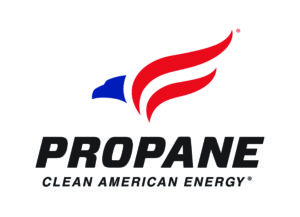
Fat Brain Toys thrives in competitive retail market with propane forklifts
NEBRASKA-BASED TOY STORE EXPEDITES SHIPPING WITH PROPANE EQUIPMENT Keeping pace in today’s retail world is no small undertaking. A company’s
NEBRASKA-BASED TOY STORE EXPEDITES SHIPPING WITH PROPANE EQUIPMENT Keeping pace in today’s retail world is no small undertaking. A company’s
Analysis shows risk of Surface Transportation Board’s renewed interest in aggressive regulation of U.S. freight rail industry Prior to the
Background: Independent pharmacies across the country rely on Rochester Drug Cooperative (RDC) for their daily shipments of prescription and over-the-counter
The lift chain is an important part of the lift truck that deserves a lot of attention. The lifespan and
Heineken and KHS are setting standards with the newest and one of the biggest breweries in Mexico on all counts:
Cedar Falls, Iowa-based AFE Crane has installed a 5-ton capacity ACCO explosion proof crane for lifting bulk container bags in a hazardous area at
Reliability, environmental friendliness and viability for the future are values held by KHS that Portuguese brewery Sociedade Central de Cervejas
Preventing your pallet truck from failing? Discover the points you can pay attention to in order to use your pallet
More locations mean more complexity, right? Wrong. While scaling can be complicated, especially when it is done through acquisition –
There are plenty of different types of brushes for industrial sweepers and floor scrubbers. What kind of brush or sweeper
“Honeywell Pro-Watch® solved our biggest problem: how to transition and replace our legacy security software that was no longer supported
Neglecting your scale can cost you profit The goal of any vehicle scale service program should be to ensure that
Systems supplier researches networking and line optimization The entire sector is talking about digitization and Industry 4.0 – but what
After developing a way to produce solar cells using materials previously considered too expensive for use on Earth, scientists at
As per a latest report, Rigid industrial packaging recorded a volume sales of ~1.85 billion units, equating a value of
As climate change continues, environmental sustainability remains a hot topic. So, it’s no surprise that sustainability is at the forefront
Storage solutions provider shares insight into the benefits, costs and return on investment of warehouse automation Westfalia Technologies, Inc. (Westfalia),
When is the optimal time to replace equipment? There are many factors to consider when making that decision, and it’s
According to the Gartner Digital Commerce Vendor Guide, 2018, “Digital commerce is a major component of a superior customer experience, with
White Paper: Innovative overhead crane manufacturer uses state-of-the-art wireless remote to grow business, increase productivity and improve operator safety supplied by Schneider