Optimizing the expansion of automation at MODEX 2024
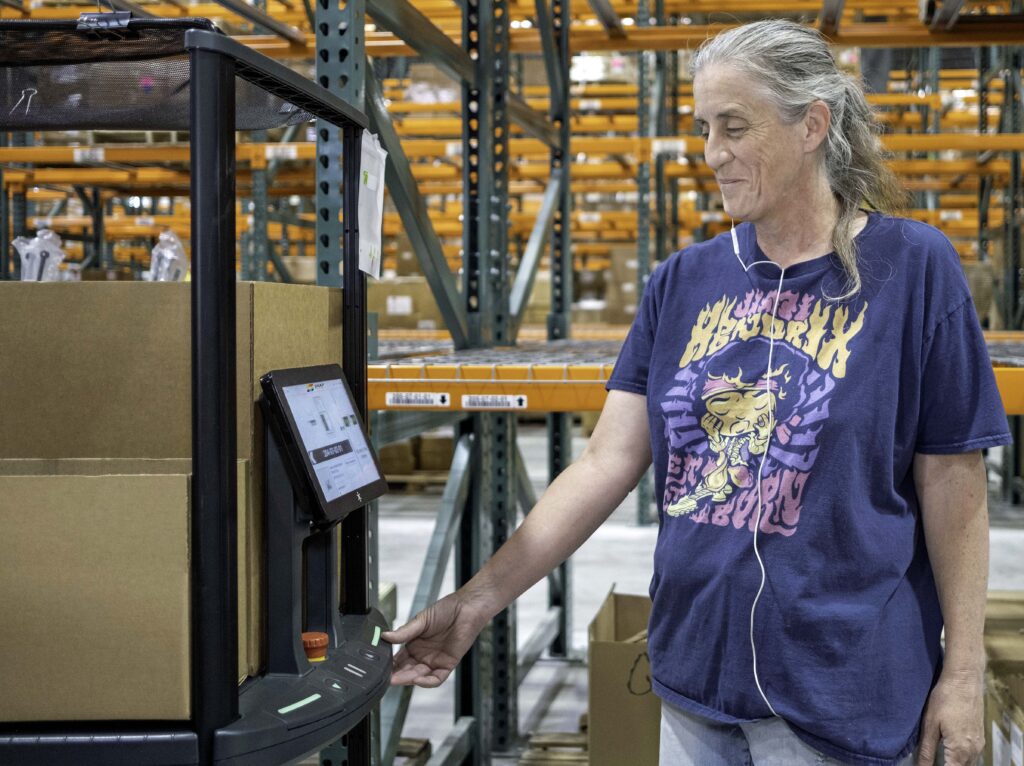
As warehouse logistics become increasingly automated with a mixed portfolio of devices, robots, and systems, the need to connect and orchestrate the various solutions is ever more urgent. The very latest multi-agent orchestration (MAO) technology, SnapControl, will be one of the main features at this year’s MODEX 2024 – at booth #A12509. Developed by warehouse management technology innovator, Synergy Logistics, SnapControl offers a device-agnostic and unified approach to automation, seamlessly connecting all warehouse devices and robots in real-time. It is suitable for both new (greenfield) and existing (brownfield) automated portfolios. Synergy Logistics’ Chief Product & Delivery Officer, Smitha Raphael, said: “We are excited to have the opportunity to highlight SnapControl to visitors at this year’s MODEX event. By uniquely interpreting bi-directional communication between machines and advanced WMS, SnapControl facilitates efficient and accurate decision-making, which are critical components of the second wave of automation recognized by leading industry analysts.” The virtues of SnapControl have already been tested rigorously by a rapidly expanding US online retailer, resulting in a sixfold increase in productivity over the first few months of implementation. Having invested in a new 300,000 sq. ft warehouse, featuring automated mobile robots (AMRs), carton right-sizing equipment, and automated packaging systems, the retailer required a MAO that could generate real-time data and make smart decisions from those integrations, with little or no human involvement. For this e-tailer, the return on investment (ROI) in automated resources has amounted to labor savings of over half a million dollars. On average, the company now saves over $40,000 per week, with an impressive investment payback period of just 23 weeks. Raphael added: “Not all MAOs are the same, because while most providers can integrate with a host of software and robotics vendors, a simple connection is as far as it goes. A true MAO platform, such as SnapControl, is the conductor of the orchestra. It provides the why and where, while connecting and controlling all devices at once, for a complete 360-degree picture of your operation.” Smitha and her colleagues are also offering practical 30-minute demonstrations at Booth #A12509 of the highly flexible and award-winning SnapFulfil WMS – showcasing how it can be changed or modified in minutes without custom code for quick and easy implementation and rapid response to evolving fulfillment demands.
Bobcat showcases the future of its material handling solutions at MODEX 2024
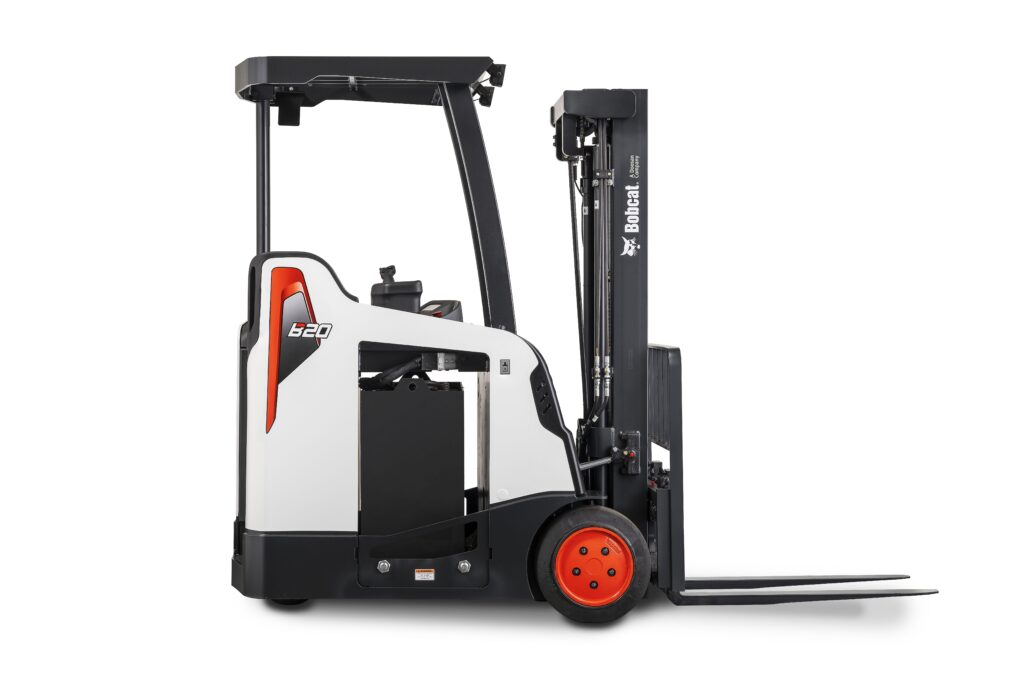
Booth features the company’s latest forklifts, including new hydrogen fuel cell prototypes From electric and internal combustion machines to new hydrogen prototypes, Bobcat Company is showcasing the future of its material handling solutions at MODEX 2024. Located in booth B2822 (Building ABC, Level 1), the Bobcat booth will feature solutions designed to handle various unique material handling challenges. Bobcat offers a full range of diesel, gas, liquid propane gas, and electric forklifts, with capacities ranging from 3,000 to 55,000 pounds. On display at MODEX 2024, Bobcat will feature: B20SU-9 Cushion Electric Stand-up Rider 3,000- to 4,000-pound capacity Stand-up configuration Guardian Stability System (GSS) 36-volt electric counterbalance Reliable all-AC power BR20SP-7 Plus Electric Pantograph Reach Truck 3,500- to 4,000-pound capacity Narrow-aisle specialty Guardian Stability System (GSS) All AC electric system BOP15S-9 Electric Order Picker 3,000-pound capacity Small chassis size perfect for narrow aisles Height and descent proximity sensors Available mast heights up to 300 inches 24-volt AC system D70S-9 Diesel Pneumatic Forklift 13,500- to 20,000-pound capacity Shift ProTek hot-shift transmission protector Bobcat will also showcase hydrogen fuel cell-powered forklift prototypes within the booth. Hydrogen fuel cell forklifts offer longer operating times and faster refueling, making them ideal for applications that require extended use and quick refueling turnaround. For warehouses operating multiple shifts, the hydrogen fuel cell forklift is a viable option to reduce carbon footprint while still meeting the operational needs to run longer hours with no charging required. Prototypes on display at MODEX include: B35X-7 Hydrogen Pneumatic Forklift Prototype This hydrogen forklift prototype would function similarly to the currently commercialized B35X-7 electric pneumatic forklift but powered by hydrogen rather than an electric battery. 7,000-pound capacity BER30S-9 Hydrogen Rider Pallet Jacks Forklift Prototype This hydrogen prototype would function similarly to the currently commercialized BER30-9 electric rider pallet jacks but powered by hydrogen rather than an electric battery. 6,000-pound capacity While still in the development phase, Bobcat is exploring hydrogen for use across its forklift range. More information on hydrogen fuel cell forklifts’ availability will be forthcoming. Bobcat forklifts and warehouse vehicles are new in their branding, but not in their legacy, as the product line transitioned to the Bobcat brand in early 2024 from its former brand of Doosan Industrial Vehicle.
ABCO Systems LLC aquires FastFetch
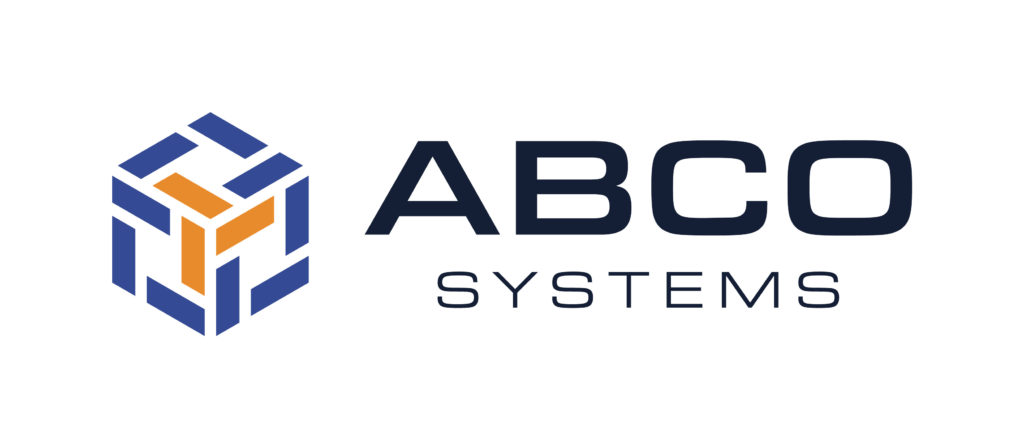
ABCO Systems LLC announced today its acquisition of FastFetch, known for its best-in-class order fulfillment technologies. This strategic move is set to expand ABCO ‘s reach within the Warehousing and Distribution industry by bringing faster, more accurate, and cost-effective technologies to a wider audience. FastFetch, renowned for its unique product group, offers a range of solutions that help E-Commerce distribution facilities significantly increase their pick rates by up to 5x in certain cases. This achievement in efficiency propels businesses to new heights of productivity and profitability. Additionally, FastFetch’s state-of-the-art cubing software empowers E-Commerce distribution centers to curtail shipping costs substantially by efficiently selecting the right-sized cartons for shipping. “We are thrilled to add the FastFetch product line to our offerings,” said Seth Weisberg, CEO of ABCO. “The acquisition aligns perfectly with our mission to provide innovative solutions that address the challenges faced by our clients in the Warehousing and Distribution industry.” The acquisition of FastFetch enables ABCO to seamlessly integrate its expertise with FastFetch’s cutting-edge technologies. Combined, they create a force to be reckoned with in revolutionizing the order fulfillment process. With this acquisition, ABCO solidifies its position as a leader in the industry, committed to delivering top-notch solutions that optimize warehouse operations. John (Jack) Peck, Founder of FastFetch, expressed his excitement about the acquisition, stating, “Joining forces with ABCO represents an incredible opportunity for us to further expand the reach of our solution and make a substantial impact on the Warehousing and Distribution community. We firmly believe that our innovative product line, coupled with ABCO’s strong industry presence, will lead to exceptional growth and success.” With the integration of FastFetch’s product line into ABCO ‘s offerings, the partnership aims to cater to the growing demand for enhanced efficiency and cost reduction in E-Commerce distribution facilities. Customers can expect unparalleled support and expertise as ABCO leverages its extensive knowledge and experience to deliver innovative solutions. Existing FastFetch customers will experience uninterrupted service, while the newly formed team will actively seek new opportunities to introduce the FastFetch product line to a broader market. This acquisition highlights ABCO ‘s unwavering commitment to staying at the forefront of industry advancements and continuously providing unparalleled solutions to its clients.
New fireboat stations dedicated at Port of Long Beach
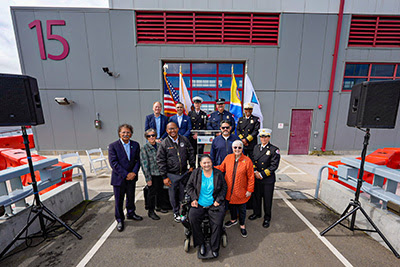
Facilities provide port-wide protection as part of a $109 million safety program Officials today dedicated two new Port of Long Beach fireboat stations that are greatly enhancing the Long Beach Fire Department’s waterside and landside emergency response capabilities, better safeguarding visiting ships, cargo, and waterfront workers. The facilities – Fireboat Station 15 and Fireboat Station 20 – are the products of a $109 million Port of Long Beach program to preserve business continuity, security, and economic interests. “These fireboat stations will provide an important and invaluable safety service to our Port,” said Long Beach Mayor Rex Richardson. “Our firefighters are now equipped with the most sophisticated facilities and emergency response capabilities to protect our Port, its valuable assets, and our waterfront workforce.” “This is a great day for the Port of Long Beach, as we celebrate the completion of a long-needed major revamping of fire safety facilities and equipment in the harbor,” said Port of Long Beach CEO Mario Cordero. “Fireboat Stations 15 and 20 and our fireboats vastly improve our preparedness and resilience in the face of emergencies.” “These new stations will have a lasting and positive impact on our ability to quickly respond to emergencies,” said Long Beach Harbor Commission President Bobby Olvera Jr. “We look forward to our continuing partnership with the Long Beach Fire Department to make the Port a safe place to work and do business.” “Our new fire stations are state-of-the-art public safety structures that will serve as bases of operations for any incident within the Port and throughout the region,” said Long Beach Fire Chief Dennis Buchanan. “Additionally, these stations have been designed with today’s workforce in mind, which means the assurance of workforce accommodations, such as separate sleeping quarters and restrooms.” Fireboat Station 15 is a single-level, 7,750-square-foot building in the Port’s outer harbor with living quarters, a garage for two firefighting apparatus trucks and a full wharf with a 16,311-square-foot boat bay enclosure that houses fireboat Vigilance. Construction started in April 2019 and the project was completed in September 2021. Fireboat Station 20, located in the Port’s inner harbor, is a two-level, 9,783-square-foot structure equipped with living quarters, a garage for two firefighting apparatus trucks and a 16,280-square-foot boat bay enclosure that houses fireboat Protector. Construction started in March 2021 and the project was completed in December 2023. Fireboat Protector entered service in 2016, followed a year later by its companion, Vigilance, heralding major advancements in harbor firefighting and emergency response capabilities at the Port of Long Beach. The fireboats are each equipped with 10 water cannons capable of sending up to 41,000 gallons per minute to a distance of up to 600 feet, or the length of two football fields. With an anticipated lifespan of 50 years, both stations were approved for construction in 2017 by the Long Beach Board of Harbor Commissioners and funded by Port revenues.
FANUC showcases latest Robotic and Automation technologies at MODEX 2024
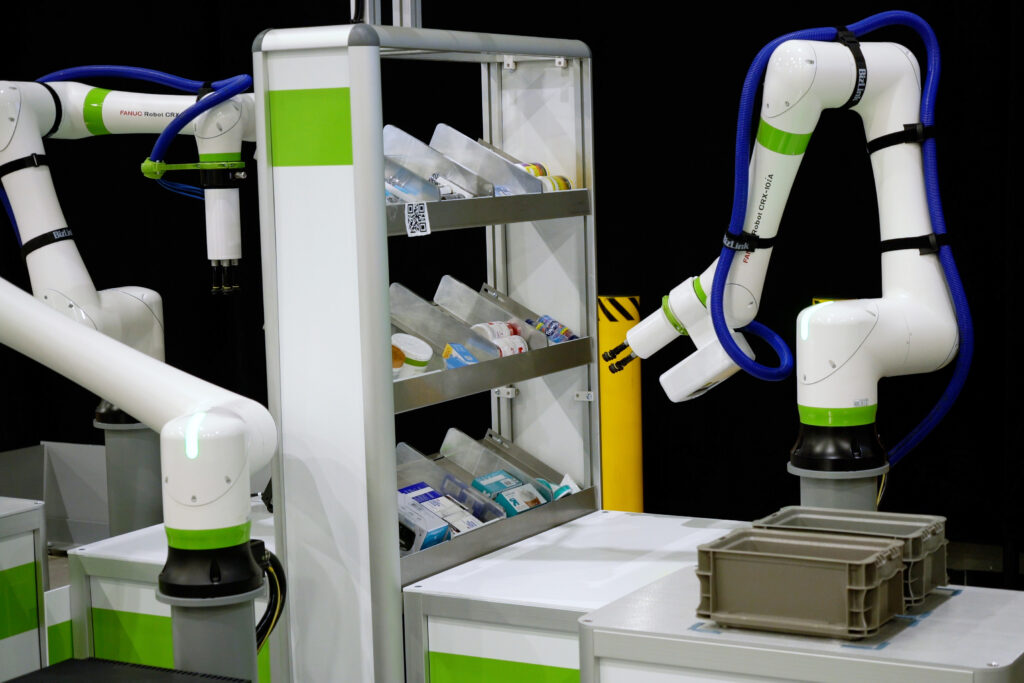
FANUC America, a supplier of CNCs, robotics, and ROBOMACHINE’s will showcase its automation solutions designed to help companies future-proof their supply chain at MODEX 2024 in Atlanta, March 11-14, booth #B-4026. CRX Cobot Demonstration – Order Fulfillment FANUC CRX cobots combined with Locus AMR and Vision technology will demonstrate a highly flexible autonomous solution for order fulfillment that can be easily scaled up or down. Visitors using a Tablet TP will select from a variety of consumer items to pick orders. One of two CRX-10iA cobots with an iRVision® 3DV/200 vision sensor mounted on its arm scans QR codes on a shelf to confirm that correct products are picked, and finds the items to transfer them to a bin on a table. Next, a CRX-20iA/L cobot also uses an iRVision 3DV/200 vision sensor to locate a full bin on the order table and place it on a Locus autonomous mobile robot (AMR). The cobot then finds an empty bin on the AMR and places it on the order table. The AMR moves from the order fulfillment area to the shelving side where the CRX-20iA/L picks an empty bin from the table and places it on the AMR and moves the full bin to a table. The CRX-20iA/L uses iRVision to scan QR codes on the bins and to locate the AMR. It also communicates with the AMR to let it know when it has finished swapping empty bins and full orders, and the AMR tells the CRX when it’s in the correct position. Finally, a second CRX-10iA with a fixed iRVision 3DV/600 vision sensor locates and picks products from the full bin, then scans each item according to its RFID tag and places it back on the correct shelf. The CRX-20iA/L can pick consumer items of varying sizes and shapes that weigh up to 20kg. The demonstration highlights its wide motion range and ability to handle small or large bins, relieving workers from physically demanding and repetitive jobs. CRX Cobot Demonstration – Vertical Put Wall FANUC’s Power Motion i Model A Plus (PMi-AP) will move a tool to random or user-specified locations on a put wall. Attendees can choose which bins to get items from and then the tool pulls the sequence of bins from the put wall and moves them to a conveyor belt for the CRX to access the bin. When a wall bin arrives at the access point, a FANUC CRX-10iA will pick an item and place it in an order fulfillment bin. An order is fulfilled once an item has been picked from each selected wall bin. Once an order has been fulfilled, the put wall system will bring the bins back to the CRX access point. The CRX then picks items from the order fulfillment bin and places them back into the appropriate put wall bins until each one has been restocked. Automated put walls are easy to deploy and scale, helping warehouses and distribution centers improve productivity by increasing order fulfillment, and decreasing labor costs. The PMi-A, which offers CNC-style moton control for automated assembly and other applicatons, integrates seamlessly into virtually any producton system using ethernet connecton for easy communicaton between robots and machines. Users who trust FANUC’s reliable control and servo technology along with overall support for machine tools, can expect the same performance and value in general purpose moton control. CRX Interactive A CRX-10iA demo showcases the cobot’s ease of use. Customers can program the robot and experience it firsthand. FANUC LR-10iA/10 Robot: Vision-Guided Retail Inducton A FANUC LR-10iA/10 robot guided by an iRVision 3DV/400 vision sensor mounted over the work cell will pick various bagged clothing items from a tote and drop them onto a conveyor belt to demonstrate retail inducton. The system demonstrates the speed and accuracy of robotcs in retail and logistics. Automated Palletzing/Depalletzing with FANUC M-710iD/50M The new FANUC M-710iD/50M, combined with two iRVision 3DV/1600 vision sensors and the FANUC iPC, will use the iPC’s AI Box Detecton sotware to locate boxes within stock carts. Once located, the M-710iD/50M will depalletze boxes from one cart and utlize PalletTool to palletze them on the opposite cart. Once a cart is empty, the process will be repeated by depalletzing and palletzing back to the original stock cart. The tall stock carts highlight the advantage provided by the M-710iD/50M’s curved arm. FANUC’s AI-driven iPC enables high-performance advanced picking in challenging lightng conditons to ensure seamless, reliable depalletzing. iPC is a major benefit for this demonstraton because the boxes have paterns that are difficult to segment and determine edge locatons. Built-in Intelligence FANUC offers application software for packaging and palletizing, integrated iRVision® and tracking features, ROBOGUIDE simulation, Dual Check Safety (DCS), and Zero Down Time (ZDT) to help customers monitor and manage their automation. Learn more about FANUC’s automaton soluton for fulfillment including: decant & de-case, mixed de-palletzing, piece picking, inducton, palletzing, sortaton and warehouse automaton.
TVH announces new VP of Sales-Americas
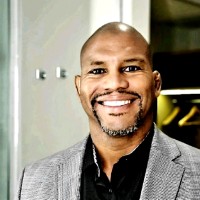
TVH Americas, a global provider of quality replacement parts and accessories for the material handling, industrial, and construction equipment industries, announced that Carnelius Cruz will be the new Vice President of Sales – Americas. Cruz will be responsible for the USA, Canada, and Mexico as well as the Latin America markets. The overall customer experience remains the top priority during Cruz’s integration along with continuing to execute the company’s commercial strategy and market growth. Cruz steps into this role with an extensive background in the automotive industry. In his most recent role as Vice President of Part Sales North America at Navistar Inc., he demonstrated exceptional leadership qualities overseeing Part Sales, National Accounts, and the Commercial Acceleration Program. With over a decade of experience managing sales portfolios exceeding a billion dollars, Cruz has consistently delivered exceptional results and valuable contributions to the applicable industry. TVH looks forward to adding another strong leader to its management team after the recent retirement of Cathy Diaz, former Director of USA Sales. Diaz began her career in the industry with System Material Handling Inc. (SMH) in 1984. Her wealth of experience and knowledge about parts and accessories proved vital during the SMH acquisition in 2003. A few years later in 2006, Diaz played an integral role in co-managing the IMC Holdings (Intrupa and LPM) acquisition. After a successful 40-year career, Diaz retired at the end of 2023 leaving the TVH USA customer base in the trusted hands of Ryan Walker, Director of USA Sales and Services.
Hy-Brid Lifts names new President and CEO
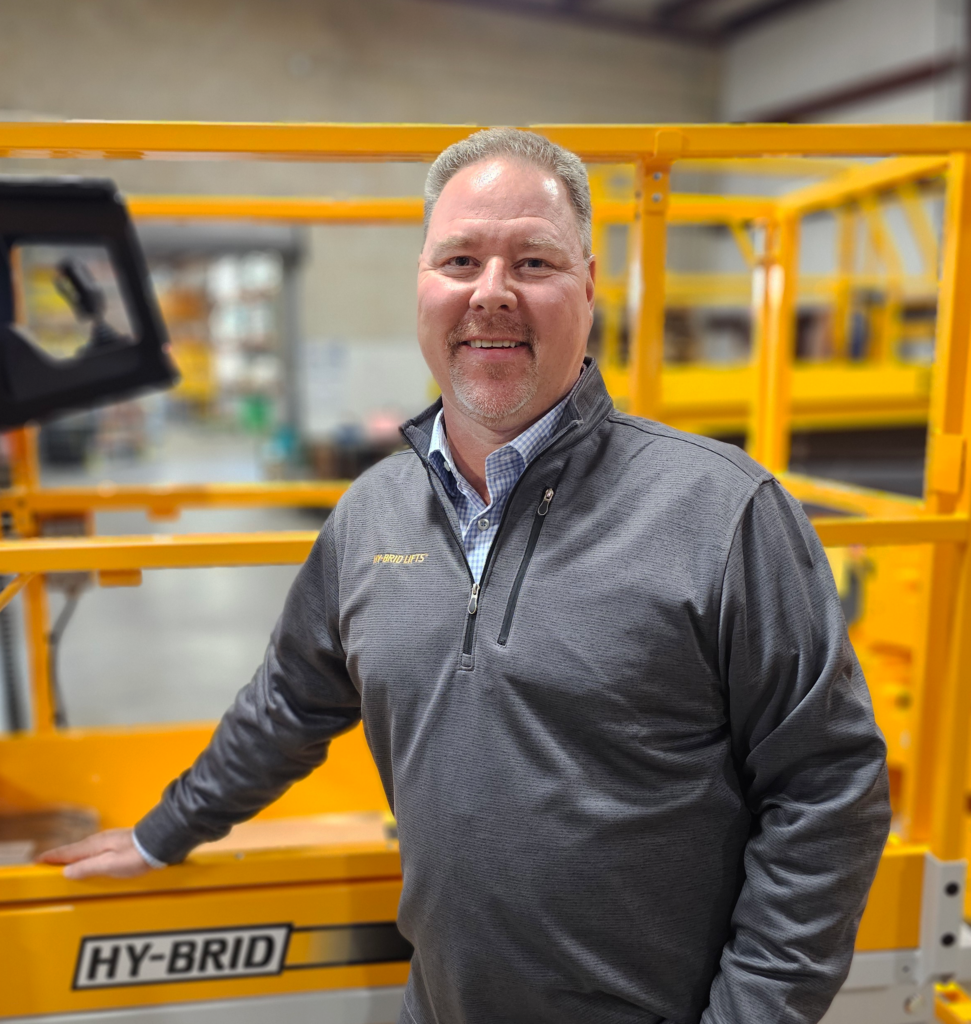
Hy-Brid Lifts by Custom Equipment, LLC appoints Eric Liner as its new President and CEO, effective February 5, 2024. He succeeds Jay Sugar, who successfully led the company for the past three years and is retiring on March 1, 2024. “We are extremely pleased to welcome Eric Liner as our new President and CEO,” said Steve Ellis, Custom Equipment, LLC Operating Manager of the Board. “Eric’s extensive background in the access and material handling industry is a perfect fit for our vision to expand our product portfolio under our new AXCS brand name and grow our market share in North America.” Liner is an industry veteran with more than 20 years of general management and executive experience in the access and material handling industry. His background encompasses a wide range of business disciplines including sales, product support, operations, finance, and new product development, which ensures the company will maintain a strong customer focus. His most recent position was President and CEO for LGMG North America, and previously the Executive Vice President, Americas at Skyjack. “On behalf of the board, we would also like to take this opportunity to thank Jay Sugar for his leadership over the past three years, having successfully navigated the company through an extremely challenging business environment,” said Ellis. “His vision and perseverance have the company poised to capitalize on significant new growth opportunities well into the future.” “I am excited for the opportunity to lead Hy-Brid Lifts into the future. The new partnership with ASKO, and their family of brands, creates a tremendous opportunity. It immediately expands our access equipment portfolio, quickly positions us to enter the North American telehandler market, and provides additional workforce and financial resources as we continue to grow,” Liner said. “The new products will be brought to the North American market under a newly formed brand name, AXCS. I am looking forward to working alongside our strong veteran leadership team as we establish ourselves as one of the industry’s premier equipment manufacturers.”
GRI appoints Barry Guildford as its Global Commercial Director
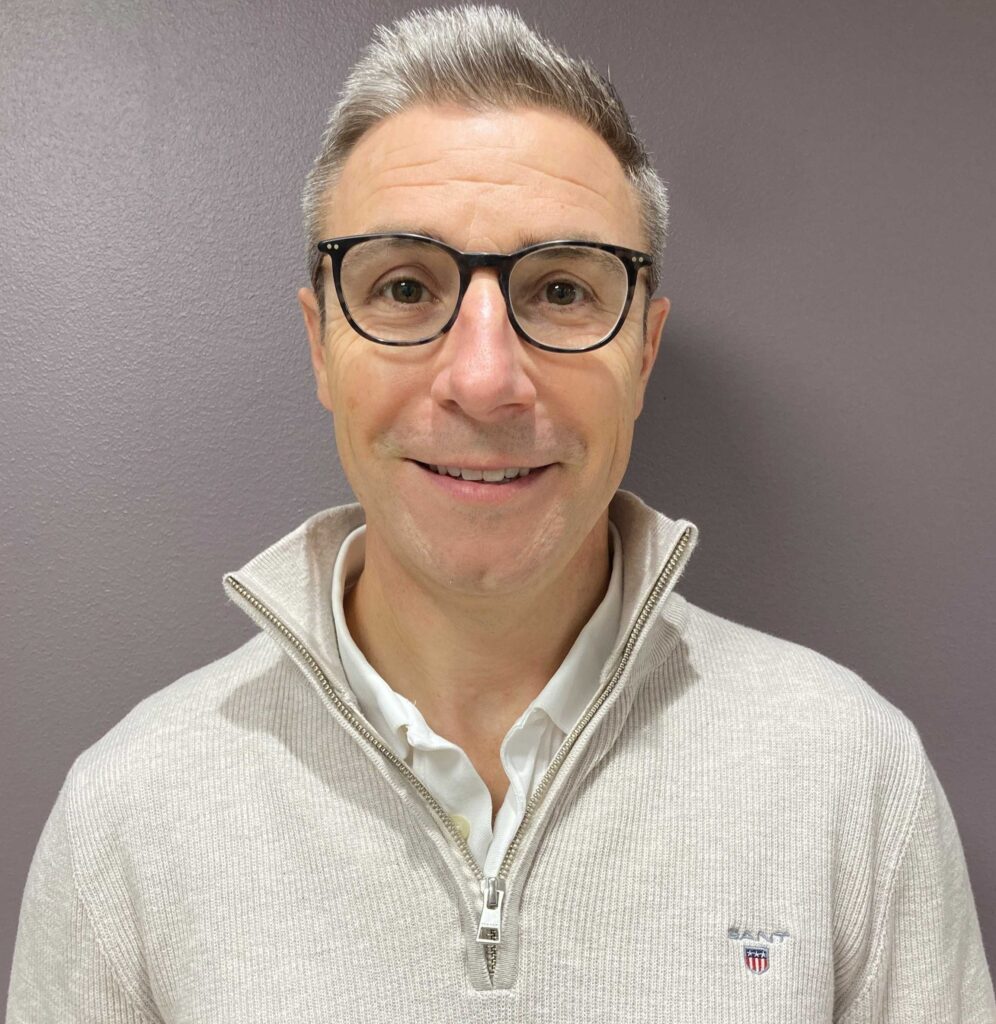
Global Rubber Industries or GRI, a specialty tire manufacturer, has appointed Barry Guildford as the Global Commercial Director (GCD), effective March 1, 2024. Guildford brings with him a wealth of experience and a proven track record of success in strategic leadership and sales management roles within the tire industry. As the GCD, Guilford will lead the global sales and marketing organization of GRI. Guildford’s tenure in the tire industry spans across distinguished positions, each marked by notable achievements and transformative initiatives. In his most recent role as the Head of Region Northeast Europe & Head of Sales ContiTrade at Continental, he orchestrated the overhaul of automotive retail networks across multiple countries. Notably, his initiatives in EV car service diversification, fleet business development, and digital fleet management solutions set new standards in the industry. Guildford’s expertise extends to marketing as well, as he crafted regional marketing strategies, launched digital business solutions, and orchestrated brand re-launch initiatives that resulted in significant growth, during his time at Continental. “Barry Guildford’s appointment as our Global Commercial Director is a testament to our commitment to excellence, business innovation, and growth. His extensive experience and proven leadership skills make him the ideal candidate to drive GRI’s commercial strategy forward,” remarked Prabhash Subasinghe, Managing Director of GRI. “Joining GRI as the Global Commercial Director presents an exciting opportunity to leverage my experience and drive meaningful impact for GRI in the global Specialty Tire market,” said Barry Guildford. “I am thrilled to be part of GRI’s journey, particularly as they are deeply committed to sustainability and green initiatives worldwide. I look forward to leading the commercial team towards new heights of success while advancing our environmental responsibility.” Under Guildford’s leadership, GRI is poised to capitalize on emerging opportunities, expand its market presence, and reinforce its commitment to delivering innovative specialty tire solutions to customers globally. His appointment marks a significant milestone in GRI’s journey toward continued success and reinforces the company’s dedication to fulfilling its customers’ aspirations worldwide.
Women In Trucking Association announces its March 2024 Member of the Month
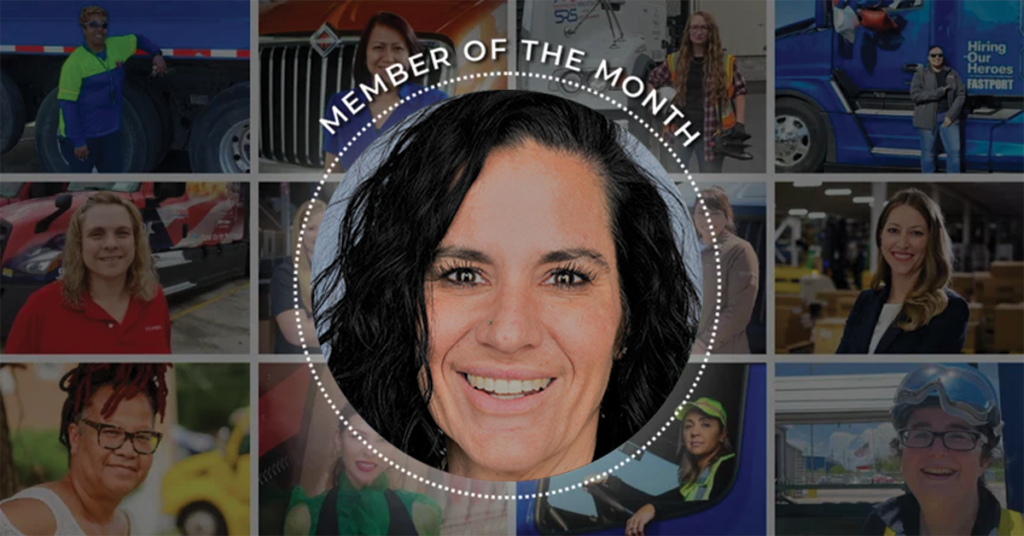
The Women In Trucking Association (WIT) has announced Tanya Miracle as its March 2024 Member of the Month. Miracle is the Director of OE Truck Channel at Bridgestone Americas. Even though Miracle has been involved in the trucking industry since she was in high school, she said that it was 100% by accident that she still finds herself in the trucking industry today. She lived in Ohio when she started her career as a dispatcher for Robert’s Express in 1993. From there, she worked for a tire mold company for a few years. She was married (and divorced) to an owner-operator who hauled oversize drop deck freight. She fully understands the sacrifices and challenges faced by the families of long-haul drivers. She knows how difficult it is when birthdays and holidays must be missed, or when the industry is experiencing a downturn and work is uncertain. She remembers those tough days but feels that it helped shape who she is today and helped build her resilience and courage. When Miracle decided to apply at Bridgestone, it was for the role of developing consumer tires, but the interviewers introduced her to the commercial truck group, and that is where she is today. Since then, she has fallen in love with the people, the industry, the weather in Nashville, and her work. She genuinely enjoys the interactions with the trucking industry. Working and meeting people at conferences and conventions, from truck drivers to CEOs, all interacting together, and sharing their knowledge and experience is part of the collaborative environment that keeps her in the industry. Everyone exchanges ideas and thoughts as equals, no matter what their title in their company may be. As Miracle says, “It is a great industry to be in.” The most unique aspect of Miracle’s role is how she goes about being in a predominantly male world – she promotes from within and continues to “break the bias” by breaking down the barriers for women in the industry. She creates pathways for women to succeed and ensures that everyone has the tools necessary to realize their full potential. Miracle has a progressive mindset and leverages her technical expertise as a previous design engineer to drive initiatives and innovative ideas to deliver solutions to her customers (OEMs and fleets). She selflessly shares information and contacts to make Bridgestone a great place to develop talent and preserve a culture of comradery. She is in her element when she can mentor and teach others in the industry. Outside of work, Miracle’s main interests are her children, family, and playing golf. She has nine children – three stepchildren, three of her own, and three adopted children. She loves being both a woman with an amazing career and a mom. Miracle won an internal Bridgestone America award for being part of the R213 team in 2020 and was further awarded as a top woman to watch in Bridgestone in 2022. As an inspiring and thoughtful leader, her biggest piece of advice is, “don’t be intimidated or come into the industry with a preconceived notion of what the trucking industry is; the societal stereotypes about ‘trucking’ are just not true.’” Miracle really believes that it is a shame that the trucking industry’s image is viewed as it is at times. She recognizes that the trucking industry is much more accepting and open than it is perceived to be. She feels that it is nice to see more diversity and that it will help to move the industry forward. With diversity comes innovative ideas, philosophies, and mindsets that will only help make the trucking industry even stronger in diverse ways. In the future, Miracle still sees herself in the trucking industry. She is a passionate person and wants to continue doing what she can to make the industry the best it can be. She would like to do whatever she can to continue to move the trucking industry forward. “This industry was created by hard-working, driven people who move the world around us into the future every day.”
LUCID showcases its latest 3D time-of-flight cameras at MODEX 2024
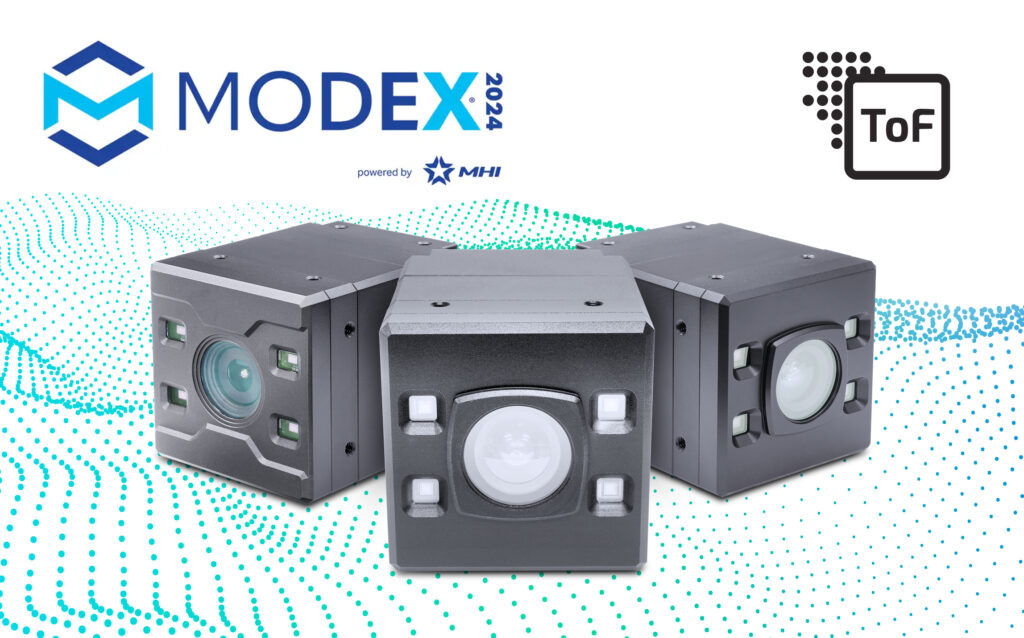
LUCID Vision Labs, Inc. is set to showcase its latest advancements at MODEX 2024, the nation’s premier material handling, logistics, and supply chain event taking place in Atlanta from March 11 to 14, 2024. Show Highlight: Helios2 Wide and Helios2+ 3D ToF Camera Family. One of the highlights of LUCID’s exhibit will include variants of the popular 3D Time-of-Flight camera family. The Helios2 Wide ToF camera integrates Sony’s DepthSense™ IMX556PLR back-illuminated image sensor paired with a wide-angle lens, providing an expansive 108º angle of view. Specifically designed for applications with a close working distance and large operational area, such as full-size palettizing applications, the camera delivers a depth resolution of 640 x 480 at up to an 8.3-meter working distance and operates at a frame rate of 30 fps. LUCID will demonstrate the Helios2+ Time-of-Flight camera, offering two on-camera depth processing modes: High Dynamic Range Mode (HDR) and High-Speed Mode. The HDR Mode combines multiple exposures in the phase domain, ensuring accurate depth information in high-contrast, complex scenes. The High-Speed Mode enables depth perception using a single-phase measurement, allowing for faster acquisition speed and higher frame rates suitable for moving object perception. More Industrial Cameras at Display. LUCID offers a wide range of industrial GigE Vision cameras tailored for applications in automation, robotics, autonomous vehicles, and emerging technologies. LUCID will showcase the flexible Phoenix GigE PoE camera module designed for easy OEM integration. Due to its small form factor and unique transformable design, the Phoenix camera can be easily configured for the ultimate custom fit. Visit us at MODEX 2024 from March 11 to 14, 2024, in Atlanta, at booth #C4771, and explore the latest in industrial vision technology.
National Fleet Products’ FuelScoop has an aerodynamic design that reduces fuel consumption by more than 15 percent
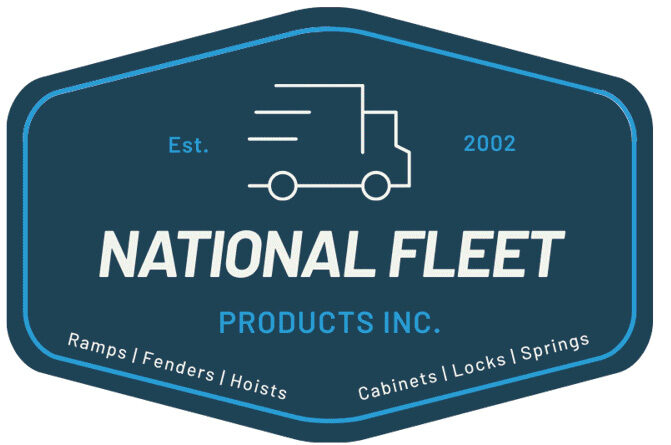
National Fleet Products’ FuelScoop cab fairing immediately saves fuel, improves vehicle stability, enhances vehicle handling, reduces driveline wear, significantly decreases CO2 emissions, and requires no drilling to install. National Fleet Products has announced that its FuelScoop aerodynamic rooftop and air-deflecting cab fairing will now be available for virtually all makes and models of medium-duty dry-freight box trucks. FuelScoop is lightweight yet strong uses factory mounting points when available, and is otherwise adhesively bonded, precisely matching a vehicle’s unique roof contours, so no drilling is required for installation. FuelScoop will be displayed to the industry during NTEA Work Truck Week 2024, March 5–8, 2024, in the National Fleet Products booth 6333. Many OEM cab fairings for medium-duty dry-freight box trucks require drilling through roof skins and the application of welded brackets to secure metal frames for structural support. Putting holes in cab roofs frequently causes leaks and corrosion. While the more primitive fairings’ rudimentary shapes help direct air up and over the cab, they do little or nothing to prevent turbulence and aerodynamic drag on either side of the vehicle. FuelScoop pairs with its intended roof contours exactly and is bonded with structural-grade adhesives often used in trailer body construction and in other heavy-duty applications worldwide. The design equally distributes FuelScoop’s weight across the entire roof surface, and the combination of precision fit and high-strength adhesion eliminates the need for drilling and is considered 100 percent reliable. “FuelScoop’s aerodynamic profile is superior to other fairings and addresses the side turbulence and drag associated with other styles,” Steven Peterson, president of National Fleet Products, said. “Its design includes a unique, signature configuration that not only directs airflow over the vehicle, but outward and around both sides. The resulting smooth, streamlined laminar airflow minimizes turbulence and drag, reducing driveline stress, while allowing the vehicle to move far more fuel efficiently.” Peterson said that FuelScoop can reduce a vehicle’s fuel consumption by more than 15 percent, while dramatically improving vehicle handling and stability. Users can typically expect to recoup the entire cost of the product within 12 months or less. “We see tires that advertise a few percentage points of fuel savings, and aerodynamic mudflaps and other devices that save one percent,” said Peterson. “With its more than 15 percent average fuel savings, FuelScoop offers users instant value that is both significant and easily measurable.” Peterson described what users can expect. “A vehicle driving 40,000 miles at 10 miles per gallon will use approximately 4,000 gallons of fuel. That 4,000 gallons will cost approximately $3.70 per gallon of diesel or roughly $14,800 of fuel per year,” he said, “With 15 percent savings from FuelScoop, users save $2,222 or 600 gallons of fuel per vehicle, so a fleet of 100 vehicles would save 60,000 gallons of fuel, netting it approximately $220,000 per year in savings. That’s $220,000 directly to a fleet’s bottom line,” said Peterson. Peterson also suggested that in an increasingly environmentally conscious and greening commercial vehicle landscape, FuelScoop can make a vehicle and a fleet greener overnight. He explained that every saved gallon of fuel prevents 20 pounds of CO2 from entering the atmosphere. So the 600 gallons of fuel saved by just one vehicle means a reduction of 12,000 pounds of CO2 and an overall reduction of 600 tons of CO2 for a fleet of 100. FuelScoop comes in a compact, palletized kit consisting of one base, one center panel, and two side panels. Assembling the lightweight FuelScoop takes just 30 minutes, and no special tools are required. Whether using factory roof mounts with Japanese model trucks, or an adhesive system for U.S. domestic model trucks, FuelScoop takes just 30 minutes to install. For those with refrigerated box trucks, National Fleet Products also offers its FridgeScoop, an aerodynamic fairing designed exclusively to accommodate vehicles with refrigeration units that overhang their cabs. The smaller-profile FridgeScoop offers many of the same advantages of FuelScoop, while still enabling easy access to refrigeration units. It also deflects insects away from refrigeration unit air intake manifolds. “With FuelScoop, we have had fuel reductions as high as 27 percent reported, so the opportunity for monumental savings is there for fleets and independent operators alike,” said Peterson. “FuelScoop is ideal for any vehicle that regularly travels at speeds over 30 to 35 mph, and as the speed increases so do the fuel savings, with trucks traveling at freeway speeds often saving more than 20 percent. It also provides a very large and visible surface for brand graphics.”
KION Group ends FY 2023 strong
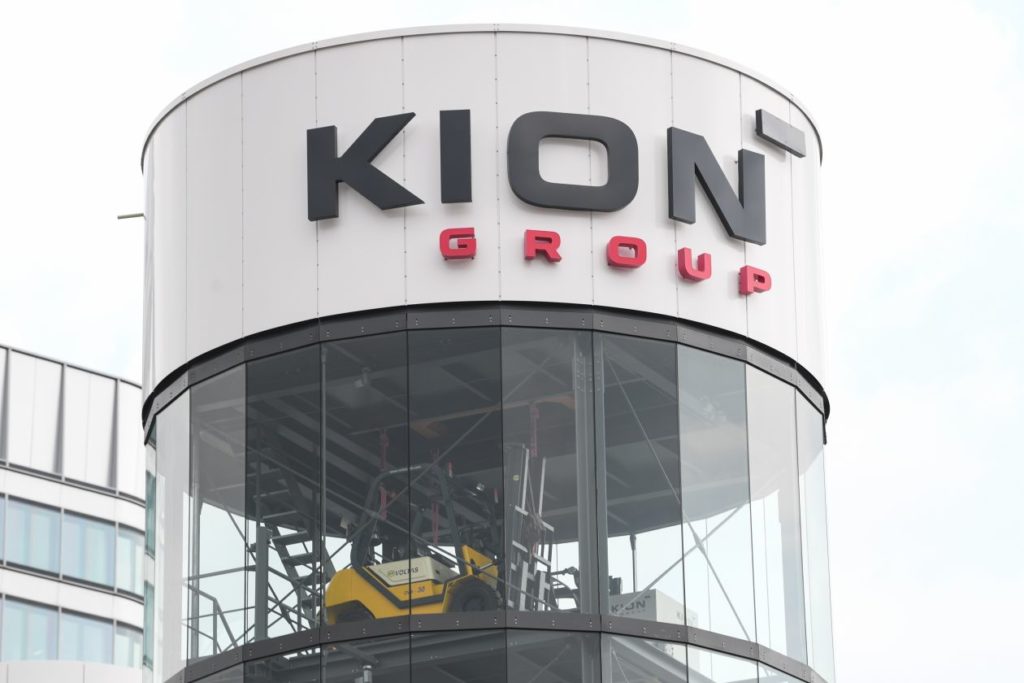
Strong financial year 2023: KION more than doubles adjusted EBIT and margin with outstanding free cash flow Record level revenue of € 11.434 billion (2022: € 11.136 billion) Adj. EBIT more than doubled to € 790.5 million (2022: € 292.4 million) Adj. EBIT margin of 6.9 percent (2022: 2.6 percent) Outstanding free cash flow of € 715.2 million (2022: € -715.6 million) Dividend proposal of € 0.70 per share (2022: € 0.19) KION Group significantly increased its profitability and free cash flow in 2023, closing the financial year with very good results in earnings – despite a decline in global demand for industrial trucks and supply chain solutions. The strong momentum was mainly driven by supply chain improvement measures in both segments, commercial actions in the Industrial Trucks & Services segment and project management process improvements in the Supply Chain Solutions segment. ”In 2023, the KION Group benefited from a year of delivering on our strategy as we took further significant steps along our path to sustainable and profitable growth,“ says Rob Smith, CEO of KION GROUP AG. ”We significantly improved profitability in both our business segments and for KION. The substantial progress in our results, the commercial and operational agility measures, and the changes of our organizational and leadership setup form a strong basis for our future business success.“ At € 11.434 billion, Group revenue grew slightly by 2.7 percent (2022: € 11.136 billion) and reached a record level. Revenue development differed across both operating segments. The Industrial Trucks & Services segment grew significantly by 15.3 percent to € 8.480 billion (2022: € 7.356 billion), mainly driven by higher production levels as well as price increases implemented in the previous year. The service business also grew. Revenue in the Supply Chain Solutions segment declined by 21.3 percent to € 2.997 billion (2022: € 3.807 billion), mainly driven by subdued customer demand in the project business (Business Solutions) over the previous quarters. The increased cost of capital had a negative impact on customers’ investment decisions for the construction of new warehouse space and therefore also on investments in warehouse automation. The stable and higher-margin service business (Customer Services) grew in the reporting period. Adjusted EBIT at Group level increased significantly and more than doubled to € 790.5 million (2022: € 292.4 million). The adjusted EBIT margin thus improved significantly to 6.9% (2022: 2.6 percent). The Industrial Trucks & Services segment again achieved a double-digit adjusted EBIT margin of 10.0 percent, corresponding to an adjusted EBIT of € 848.5 million (2022: € 420.5 million). Following a loss in the previous financial year, the Supply Chain Solutions segment achieved a positive adjusted EBIT margin of 1.5 percent with an adjusted EBIT of € 44.3 million (2022: € -45.6 million). Net income tripled to € 314.4 million (2022: € 105.8 million). Free cash flow reached a strong € 715.2 million (2022: € -715.6 million), due to overall good earnings and improved working capital management during the end of the year. KION shareholders will benefit from the strong financial year 2023: The Executive Board and Supervisory Board of KION GROUP AG will propose a dividend of € 0.70 (2022: € 0.19) per share for the 2023 financial year at the Annual General Meeting on May 29, 2024. This corresponds to a total dividend payout of € 91.8 million. The payout ratio amounts to around 30 percent with earnings per share of € 2.33 for the 2023 financial year. It is within the targeted payout corridor of 25 percent to 40 percent. Sustainability remains in the focus In July 2023, the KION Group committed to the goals of the Science Based Targets initiative (SBTi) to make the measures and successes on the way to climate neutrality transparent. As of 2023, the KION Group received an MSCI ESG Rating of AAA. This is the first time that the KION Group has achieved the top score and ranks among the top 10 per cent in its industry (Construction & Farm Machinery & Heavy Trucks). As at December 22, 2023, the KION Group ranked 94th percentile in its industry (“IEQ Machinery and Electrical Equipment”) in the S&P Global Corporate Sustainability Assessment 2023. With the “A-” award in the CDP Climate Change Rating 2023, which was awarded in February 2024, the KION Group underpins its leading position in sustainability. Detailed information can be found in the Non-financial Report 2023 of KION GROUP AG, which will be published today. (https://www.kiongroup.com/en/About-us/Sustainability/) Outlook The KION Group predicts slight growth in the market for new industrial trucks in 2024 based on order numbers. This will be driven mainly by an anticipated upturn in the APAC and EMEA regions, whereas demand is expected to decrease in the Americas region. The size of the supply chain solutions market, as measured by revenue, will slightly increase in 2024 according to the KION Group and backed up by research from Interact Analysis. The continuing trend toward automation and the anticipated fall in the cost of capital over the course of the year are expected to make companies more likely to invest in warehouse automation. Meanwhile, the predicted sustained demand for mobile automation is set to boost the market for supply chain solutions. The KION Group believes that the positive medium- and long-term trends in the supply chain solutions market remain intact. For 2024, reflecting the midpoint of the performance range that has been projected, the Executive Board of KION GROUP AG expects the Group’s revenue to increase slightly and its adjusted EBIT to rise significantly compared with 2023. Return on Capital Employed (ROCE) is expected to be slightly higher than in the previous year. Free cash flow in 2024 will be in positive territory in line with the expected healthy financial performance but will be below the high free cash flow of the previous year. In the Industrial Trucks & Services segment, a slight increase in revenue to between € 8.5 billion and € 9.0 billion is expected for the 2024 financial year. This is based on the good order backlog, an expected modest increase in order numbers in new business due to
Workhound’s annual feedback trends report highlights State of Trucking in 2024
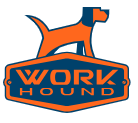
WorkHound, an employee feedback management for frontline workforce industries, unveiled its eagerly anticipated Annual Trends Report focused on top feedback trends in trucking for 2024. Based on nearly 100,000 anonymous frontline worker comments across 100+ logistics and trucking companies, the latest trends report dives deep into the workforce’s sentiments, concerns, and praises, spotlighting the most pressing issues and emerging trends across the industry. “2023 was a year with significant challenges in the trucking sector,” said Max Farrell, co-founder and CEO of WorkHound. “Despite facing a freight recession and new NLRB guidance, the industry demonstrated remarkable resilience. Federal initiatives began addressing the truck parking shortage, and the sector saw considerable mergers and acquisitions activity. Our latest workforce trend report leverages real-world feedback to illuminate the current state of the transportation industry, enabling employers to enhance the worker experience through a deeper understanding of their needs and concerns.” The report categorized driver comments into themes to simplify the data before measuring sentiment. The top theme of worker comments in 2023 was People, underscoring the crucial role of interpersonal connections in enhancing the work experience, particularly in roles where day-to-day interactions are not guaranteed. WorkHound’s sentiment analysis reveals positive relationships significantly boost morale and operational resilience. However, the breakdown of these connections leads to a ripple effect of dissatisfaction and challenges, emphasizing the profound impact of interpersonal dynamics on worker experiences. Key insights from the report: The top five feedback themes identified were People, Logistics, Equipment, Pay, and Praise, Some additional keywords identified were Raise, Weather, Sleep, Payroll, Breakdown, Planning, Lost, and Feeling. Praise theme aside, the majority of the themes featured comments with negative sentiments, and the report unveils some of the driving factors behind their dissatisfaction. Increased average comments per worker suggest a willingness – or need – among frontline employees to share their thoughts or concerns with employers. A 17% increase in mentions of “unions” from 2022 to 2023 and increased concerns about “pay” and “equipment reliability” reflect the evolving priorities and challenges faced by drivers. WorkHound’s commitment to leveraging AI for sentiment analysis and theme identification provides actionable insights for companies looking to improve retention, address employee concerns, and build a culture of trust and transparency. The findings serve as a roadmap for industry leaders to build a culture of trust and improvement, offering a clear view of the workforce’s evolving needs and priorities in real-time. “WorkHound remains dedicated to empowering companies to actively listen to their employees,” added Farrell. “Listening and communication are the keys to fostering better workplace environments and driving frontline industries toward a more inclusive, proactive, and positive future.” Click here to access the full WorkHound Annual Trends Report.
CVG presents “Contract Manufacturing Benefits to Your Process” Seminar at MODEX 2024
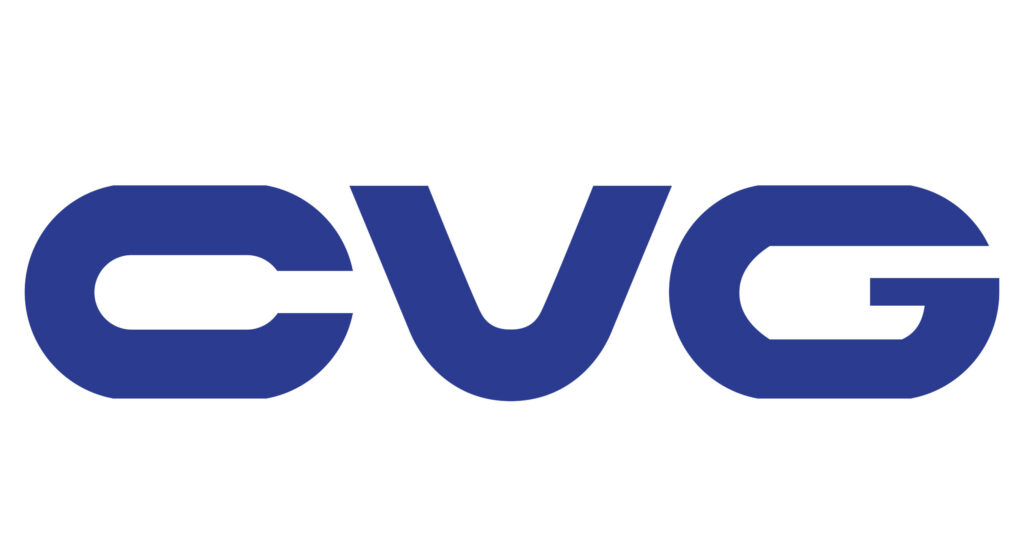
Join CVG at MODEX 2024 for an insightful seminar on “Contract Manufacturing Benefits to Your Process.” Hosted by Terry Shaw and Chris Quaglia, Senior Program Managers at CVG, this seminar will explore the transformative advantages of contract manufacturing for businesses seeking to optimize their processes. Seminar Details: Title: Contract Manufacturing Benefits to Your Process Presenters: Terry Shaw and Chris Quaglia, Senior Program Managers at CVG Date: Monday, March 11 Time: 1:30 – 2:15 PM Location: Theater G Commercial Vehicle Group (CVG) is a global leader in innovative solutions for the supply chain and material handling industries. With a focus on supply chain automation systems, CVG’s team of experts brings decades of experience in material handling equipment, operations management, sales, industrial engineering, and management. Attendees will gain valuable insights into the advantages of contract manufacturing, including significant cost savings, increased technical expertise, enhanced flexibility, scalability, end-to-end solutions, accurate cost estimates and deadlines, and faster time to market. With a focus on key takeaways such as highly experienced management, dedicated program management, emphasis on quality, flexible models, capacity for growth, highly trained personnel, and state-of-the-art facilities, this seminar promises to equip businesses with the knowledge and tools they need to thrive in today’s competitive landscape. Terry Shaw and Chris Quaglia bring a wealth of experience in supply chain automation systems, with strong backgrounds in material handling equipment, operations management, sales, industrial engineering, and management. As presenters of this seminar, Terry and Chris are dedicated to sharing their expertise and insights to help businesses unlock the full potential of contract manufacturing. For further inquiries, media requests, and live demonstrations regarding both the “Contract Manufacturing Benefits to Your Process” seminar and the new product launch of STACC to witness the Future of micro fulfillment, please contact CVG directly or visit in person at MODEX 2024 in booth C4489.
Fairchild Equipment and IEWC Partner to support Feeding America Eastern Wisconsin with forklift donation
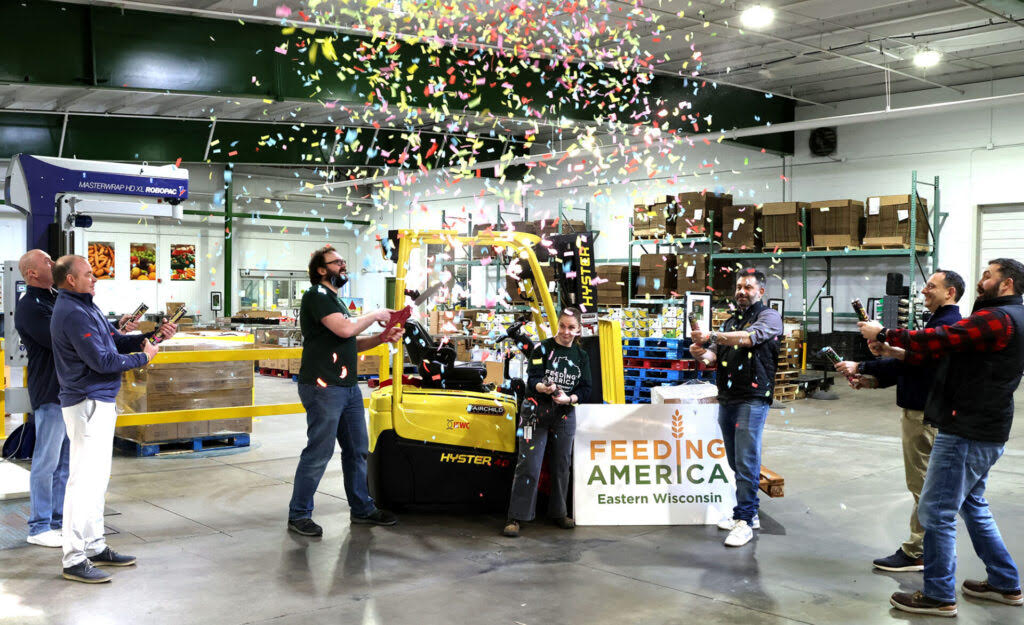
Fairchild Equipment, a provider of material handling equipment in the Upper Midwest, has announced its recent partnership with IEWC, a wire, cable, and wire management products, donate a Hyster forklift to Feeding America Eastern Wisconsin to help the organization fight hunger through its nationwide network of food banks. “As a company, we believe in being active in our communities and making a positive impact wherever we can. Donating this forklift to Feeding America is just one example of how we strive to live out our core values every day,” said Fairchild Equipment President Van Clarkson. “By donating this forklift, along with a collection of food items donated by our employees, to Feeding America, we hope to not only assist in their day-to-day operations but also contribute to their overall mission of fighting hunger in our community. We are proud to be able to support such a vital organization and hope that our donation will make a meaningful impact in their operations and the lives of those they serve,” Clarkson added. The initiative stemmed from a volunteer-day experience led by IEWC’s Chief Information and Digital Officer, Scot Stein, and his team. While volunteering at Feeding America Eastern Wisconsin, they identified a pressing need for a forklift to handle and distribute food donations efficiently. Moved by the organization’s mission and the immediate need, Stein connected with IEWC CEO Mike Veum and they reached out to Fairchild Equipment to partner on the initiative to find a solution. “When we witnessed the remarkable efforts of Feeding America firsthand and understood the logistical hurdles they overcome daily, we were inspired to lend a hand. Joining forces with Fairchild Equipment to refurbish and gift a forklift felt like a natural step in supporting this heartfelt mission,” Stein shared. “This gesture extends beyond a mere donation; it’s a commitment to helping countless individuals and families in our communities who depend on the vital support provided by Feeding America.” This donation is a powerful example of Fairchild Equipment’s and IEWC’s unwavering commitment to social responsibility and the betterment of their communities. By joining forces and utilizing their industry connections and resources, these two companies have significantly impacted Feeding America’s operations, underscoring the importance of private businesses working together to effect positive change in the communities where they operate. “We are thankful for the efforts of IEWC and Fairchild for making this forklift donation happen,” Feeding America Eastern Wisconsin Vice President of Development and Communications Scott Marshall said. “So much of what we do at Feeding America Eastern Wisconsin is affected by our logistics and machinery, and a forklift has been a very expensive need for us. This forklift will help to put thousands of meals on the table for Wisconsinites facing food insecurity. This is a prime example of the huge impact community partners can have on organizations like ours,” Marshall added.
PFlow Industries showcases its vertical material lifting solutions at MODEX 2024
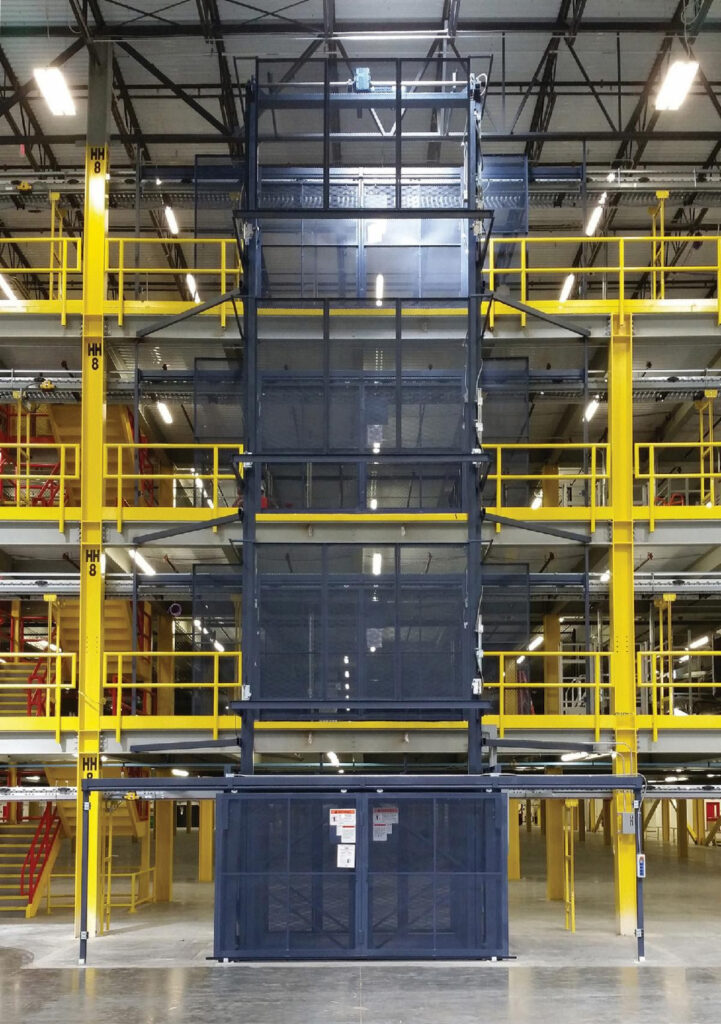
Visit Booth #B1019 to see how the Versatile VRCs Improve Efficiency and Worker Safety Join PFlow Industries, the founders of the vertical reciprocating conveyor (VRC) industry, at MODEX 2024, March 11-14, where they will be showcasing their vertical material lifting solution capabilities. Learn more about the versatility of PFlow VRCs, including the M Series 2-Post Mechanical Material Lifts that are ideal for almost any material lifting application. The PFlow M Series moves materials faster and more safely than forklifts, with a standard travel speed of 25 feet per minute (FPM), and up to 400 FPM available. With its ability to lift to 10,000 pounds, reach an unlimited number of floor levels, and perform under even the most demanding continuous-use applications, the M Series is a perfect lifting solution for high-speed / high-cycle and automated material handling applications. With quality construction, backed by a lifetime structural warranty, the M Series provides reliable, long-term performance, resulting in minimal downtime. Each M Series VRC conforms to ASME B20.1 and is equipped with advanced safety features, including limit switches that control carriage travel, shutting off the motor, and engaging the brake when tripped or power is lost. Additionally, chain sensors, certified safety cams, chain tensioners, and guides ensure safe operation by detecting chain tension loss and chain failure and preventing uncontrolled carriage descent. PFlow specializes in designing customized lifting solutions tailored to the specific requirements of each application, ranging from simple, two-level material lifting to complex integrations with automated systems. The versatile M Series VRC is available in both straddle and cantilever designs, each with its unique advantages. Straddle configurations provide increased lifting capacity and larger carriage platform sizes, making them ideal for applications with ample space. Conversely, cantilever configurations offer access to the carriage platform from three sides and can accommodate taller payloads, making them suitable for areas with limited space. Visit PFlow in booth B1019 where product experts will be available to discuss vertical material handling needs and provide customized solutions and best practices for accelerating business goals, including improving efficiency, increasing facility velocity/throughput, and enhancing worker safety.
NORD DRIVESYSTEMS will attend MODEX with dynamic solutions for intralogistics
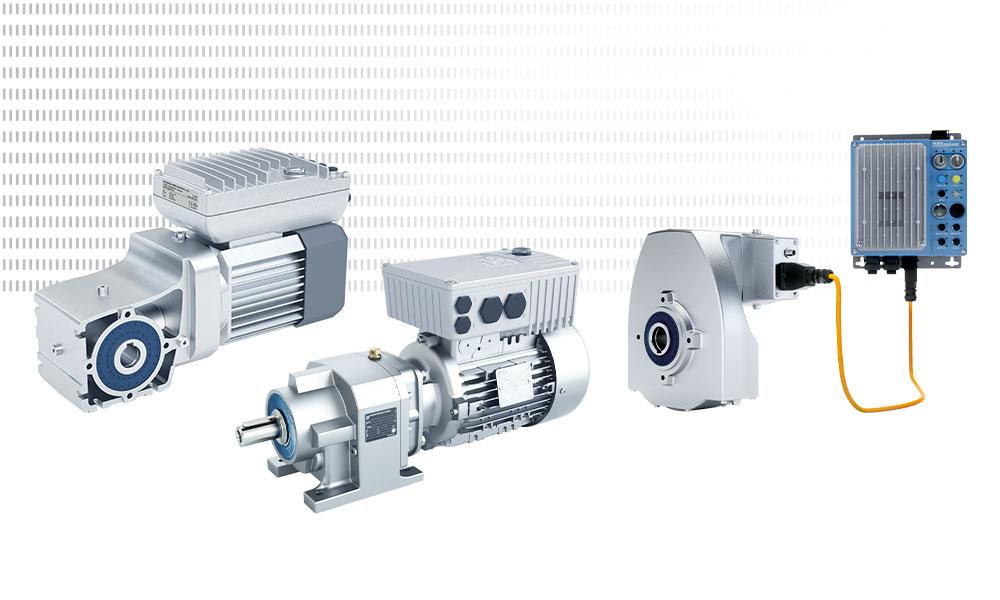
NORD’s drive solutions provide intralogistics systems with reliable operation, dynamic control, and long service life to effectively operate with greater system availability. NORD’s versatile modular product system offers highly configurable, energy-efficient, and reliable solutions to meet specific supply chain application requirements. The MODEX 2024 exhibition will be open March 11th – 14th at the Georgia World Congress Center in Atlanta, GA. Global drive solutions manufacturer, NORD DRIVESYSTEMS, will be in attendance to showcase their latest innovations for intralogistics applications. NORD has thousands of drives installed across the world and offers complete drive solutions specialized for intralogistics handling such as simple commissioning, Plug-and-Play capabilities, standardization, energy savings, and more. NORD DRIVESYSTEMS will be exhibiting at Booth C8066 with these industry-focused products: NORDAC ON/ON+ variable frequency drives were designed with the special requirements of horizontal conveyor technology in mind and have been optimized for use with IE3 motors (NORDAC ON) as well as IE5+ synchronous motors (NORDAC ON+). The electronic drives deliver a compact, dynamic solution for IIoT environments with their full Plug-and-Play capabilities, integrated multi-protocol Ethernet interface, and when operated with the NORDCON software tool, the drive can be controlled and programmed via PC. The drives offer additional flexibility with motor or wall mounting possible depending on installation space. NORD’s IE5+ synchronous motors help reduce system variants and operating costs thanks to their high efficiency and constant torque over a wide speed range. The ventilated design effectively dissipates heat to support high overload capacity in intralogistics. The motors are manufactured in-house for quick delivery times and fully match NORD’s modular system of gear units and variable frequency drives. When IE5+ motors are included in a drive system, there is a significant reduction in the Total Cost of Ownership (TCO) and a faster return on investment. The LogiDrive® solution from NORD is a complete drive solution that reduces planning and commissioning efforts through a cost-effective, standardized design. LogiDrive is ideal for post and parcel, warehouse, and airport systems and for each area, there are advanced versions utilizing IE5+ synchronous motors and a basic version with IE3 asynchronous motors. The advanced versions provide a solution focused on issues such as energy efficiency, version reduction, and TCO while the basic version’s main concentration is reduction of operational costs. NORDBLOC.1 two-stage helical bevel gear units are designed to optimize system performance, and efficiency, and reduce variants. The single-piece, UNICASE housing ensures an accurate alignment of all bearings, internal shafts, and gears for long service life with easy maintenance. Flexible installation options including various input and output options, solid and hollow shafts, and versatile mounting make the drives highly adaptable to a wide range of applications. For hygienic environments, a closed housing with a smooth surface is available. NORDBLOC.1 helical inline gear units offer high versatility for intralogistics applications with 16 compact case sizes to choose from and single, double, or triple gear reductions. They deliver quiet operation and reliable performance in a smooth, easy-to-clean design. These units also do not have installation openings, increasing the stability of the product and preventing material accumulation. NORDBLOC.1 helical inline gear units additionally offer a variety of options including keyless shaft designs with shrink disc and GRIPMAXXTM, foot or flange mounting, reinforced bearings, and more. Condition Monitoring for Predictive Maintenance, drive, and status data are recorded periodically or continuously to proactively maintain machines and optimize the efficiency of the entire plant. This status based maintenance in place of time-based maintenance enables early detection of undesired operating conditions, allowing for planned downtimes for maintenance – saving operating, service, and material costs as well as extending the operating life of components. Data collected from Condition Monitoring can even determine the optimal time to change oil, ensuring systems are always operating at their highest capacity.
Alta Equipment Group appoints Sidhartha Nair as Director
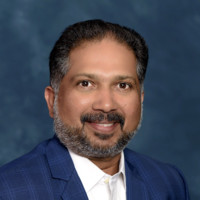
Alta Equipment Group Inc. has increased the size of the Board of Directors from five to six directors and subsequently appointed Sidhartha Nair to the Board, effective immediately. Sidhartha Nair is the Head of Strategy, Americas Region, for Mercedes-Benz Mobility and has led Strategic and Transformation activities in the U.S., Canada, and Mexico since December 2021. Mr. Nair first joined Daimler Financial Services in 2003 and has held roles of increasing responsibility during his tenure of more than 20 years in the U.S., Caribbean, and India business units. Before 2003, he held a previous role with McKinsey & Company as a consultant working on developing strategic solutions addressing growth, turnaround, and new market entry. Nair holds an MBA from the University of Michigan, Ross School of Business, and a Masters in Engineering from Purdue University. Nair brings global experience and knowledge of startups, new market entry, growth, and digital transformation of businesses at different periods in their life cycle. “Sid brings extensive business leadership experience as well as in-depth knowledge in digital transformation and business transformation in the automotive industry,” said Ryan Greenawalt, Chief Executive Officer and Chairman. “His expertise will be a significant boost to our ongoing initiatives. I look forward to the contributions he will make as part of the Alta family.” I am excited to join the Board of Alta and be part of its rapidly expanding growth and position in the market,” said Nair. “My experience should be beneficial to Alta’s diversified strategy to capitalize on the growth opportunities and cost-efficiency initiatives.”
Herc Rentals acquire MAC Equipment
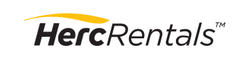
Herc Rentals has acquired MAC Equipment in Albany, NY from Rob and Janice Miller. MAC Equipment was founded in 2001 by Rob Miller who rented aerial, forklifts, and telehandlers. Janice Miller joined the business in 2005. Janice Miller, Owner and Managing Member of MAC Equipment, LLC was elected President of the Northeastern Subcontractors Association (NESCA) for the 2021-2022 term. As of July 1, Janice has been serving as the 49th president of the association. Following several years of service on NESCA’s Board of Directors, she previously served as NESCA’s vice president and treasurer. In 2012 Janice became the majority owner of MAC Equipment, a certified WBE and DBE in New York, Massachusetts, and Vermont as well as a WBE in New York City, the Port Authority, and the City of Albany.
Episode 465: Global E-Commerce Experts on taking your brand international
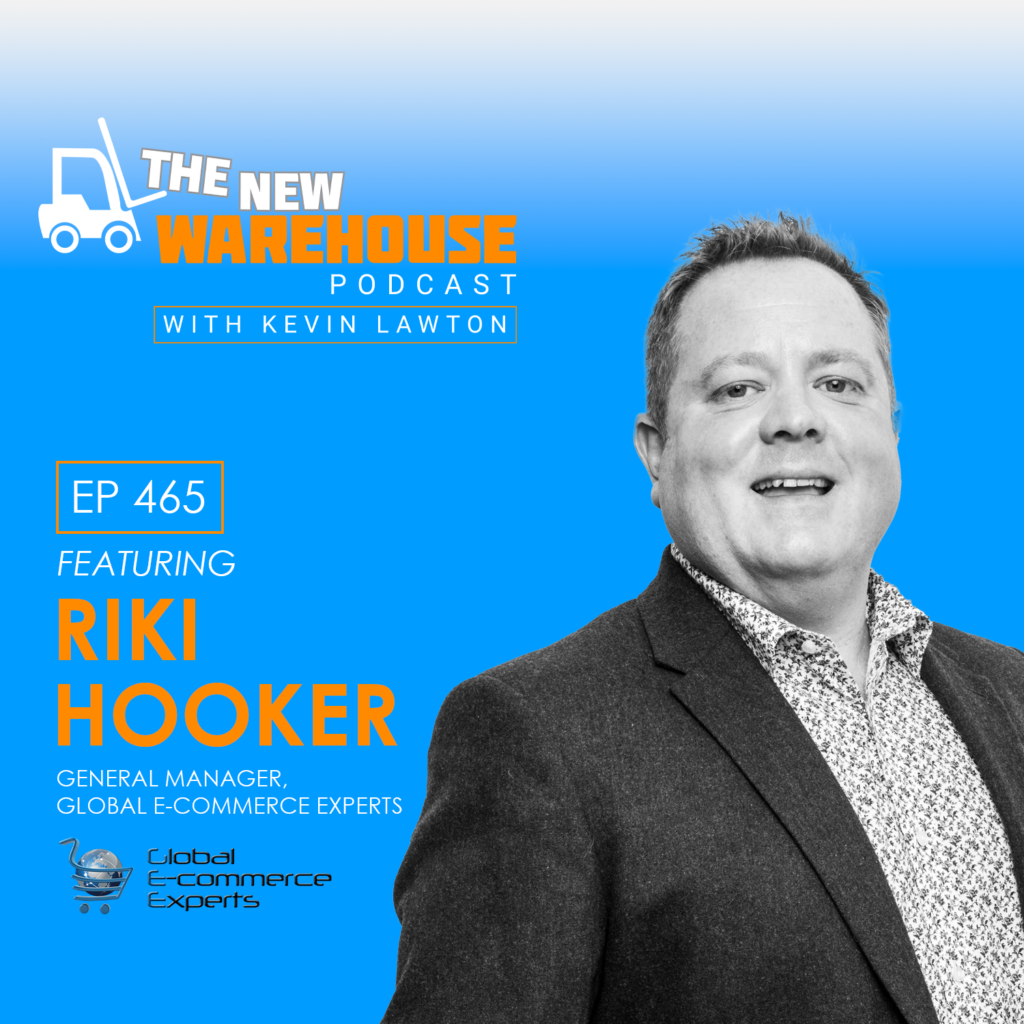
Get ready to dive into the intricacies of international e-commerce expansion with guest Riki Hooker, General Manager at Global E-commerce Experts. Global E-commerce Experts specializes in facilitating e-commerce through their portfolio of strategically placed 3PL warehouses. Offering insights on how brands can navigate and succeed in global markets, Hooker shares valuable strategies for brands looking to expand from the European market to the United States and vice versa. The Intricacies of Taking Your Brand International Navigating the journey of taking your brand international, particularly for e-commerce sellers, involves a blend of strategic planning and understanding the complexities of new markets. Hooker highlights the multifaceted approach required for American sellers, who are accustomed to platforms like Amazon, Walmart, and Shopify, to enter the European market successfully. From assessing the feasibility of your product’s success to navigating the complexities of compliance and logistics, each step is crucial for a smooth transition. Here’s a brief overview of the key steps involved: Feasibility Check – Assessing the product’s market potential, considering Europe’s vast e-commerce consumer base. Compliance Phase – Adhering to stringent European standards, including product labeling, ingredient regulations, and tax compliance. Logistics and Shipping – Overcoming the challenges of shipping to Europe for the first time and the importance of prior international selling experience. Omnichannel Presence – Adapting your online presence beyond Amazon, targeting regional platforms, and optimizing product listings for the European audience. Product Selection Strategy – Starting with a core product range to gradually build a presence as they adapt to the market. Hooker outlines the comprehensive services provided by Global E-commerce Experts, including compliance, logistics, and omnichannel growth. He emphasizes the importance of understanding market-specific regulations and consumer behaviors. “We handle the whole thing end-to-end…making them ready to sell in those markets,” explains Hooker, highlighting the necessity of a tailored approach for each new market. Navigating New Markets with Global E-commerce Experts Hooker reveals that European consumers, much like their American counterparts, demand swift delivery services, expecting prime next-day arrivals facilitated by Amazon’s extensive European distribution. The landscape in Europe offers a similar urgency, with platforms like Shopify achieving deliveries across the continent in just two to three days. This comparison underscores a universal e-commerce truth: speed reigns supreme in consumer expectations regardless of geography. For businesses venturing into new territories, navigating these expectations alongside stringent compliance requirements becomes a pivotal challenge. Hooker’s insights into the European e-commerce ecosystem, from the necessity of dual inventory for UK and EU markets to the strategic use of various shipping methods, highlight the complex yet rewarding journey of international expansion. As companies adapt to these global demands, the agility to balance swift delivery with operational compliance emerges as a key driver of e-commerce success. Key Takeaways: Global expansion requires a deep understanding of market-specific regulations and consumer preferences. Global e-commerce is pivotal in helping brands expand internationally by offering a platform to reach new markets with relative ease and efficiency. Strategic compliance and logistics planning are essential for entering new markets. The New Warehouse Podcast EP 465: Global E-Commerce Experts on Taking Your Brand International