Creform flow rack is ready to provide an organized flow of materials.
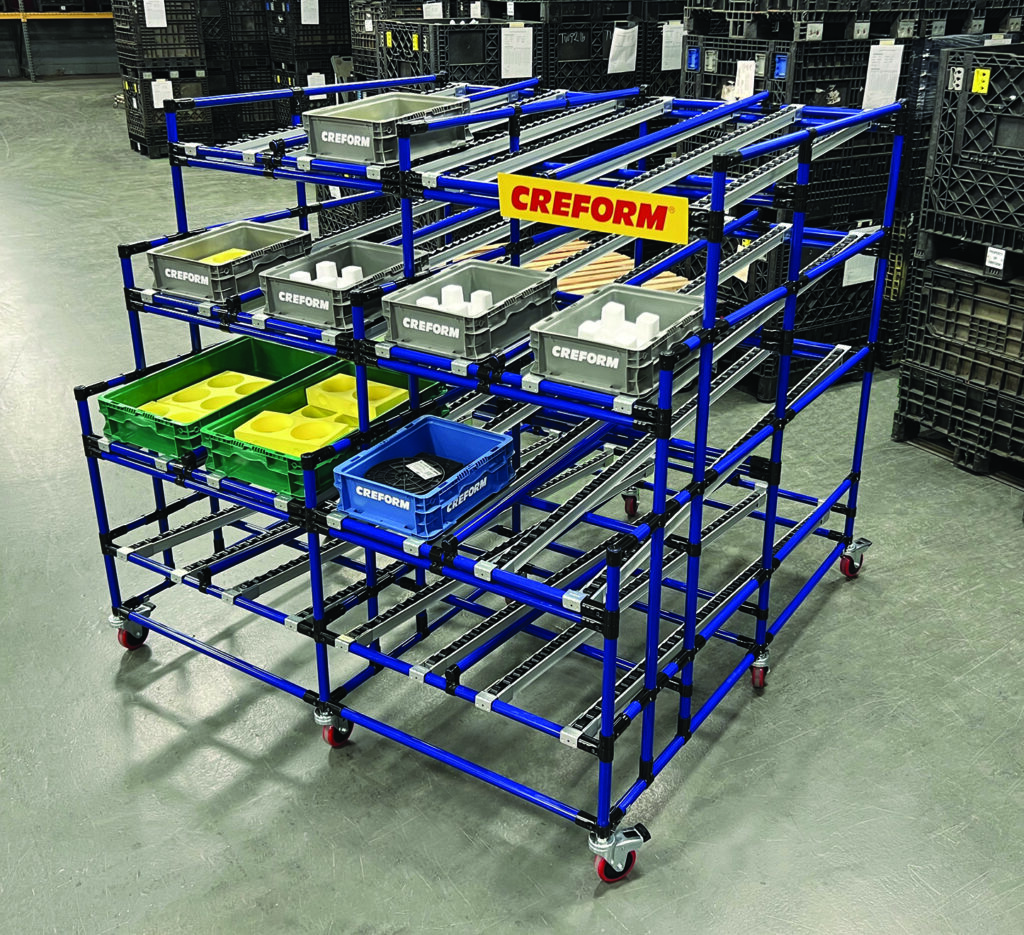
Creform Corporation, a manufacturer of unique products for material handling structures has designed and built a stair-stepped mobile flow rack to be used lineside by an automotive parts supplier. The flow rack enables lean manufacturing principles by providing a seamless and organized flow of materials and helps reduce waste while improving overall efficiency in the production process. The gravity flow rack assists in first-in, first-out (FIFO) inventory management. ensuring that materials are used in the order that they are received. The compact design allows for lineside placement, minimizing the need for excessive floor space. The pictured unit is 63″ T x 66″ D x 66″ W, can hold up to 1500 lb., and is built using Creform 28 mm pipe which provides flexibility and reusability for the user. Higher capacity and custom rack sizes and configurations are possible with Creform’s 42mm product line of pipe and joints. Further, the 42mm product line can integrate seamlessly with the 28mm system. The flow rack features three supply levels and one return level for product presentation in a stair-stepped setup. Each level has four lanes utilizing Creform skate wheel conveyors for shallow flow lane angles that are suitable for both plastic returnable totes as well as cardboard. Creform conveyors are sturdy and made with durable materials to ensure a robust and long-lasting flow rack. They are designed to withstand the demands of the toughest industrial environments. Lane dividers are located in the middle of each section of the rack and are used to organize the boxes into a specific lane. Each of the cart’s levels can be repositioned with only simple tools. With the stair step design, each level can be raised or lowered without changing the length of the conveyor. This greatly simplifies adjustment. The unit features six swivel-lock casters and three fixed in the center to allow for stability and ease of movement. Each caster can be locked in place when the need arises. The unit is built with blue pipe color, but as with all Creform flow racks, a wide variety of pipe colors are available, and accessories can include information sheet holders, label holders, tool storage, hooks to hang tools, and other supplies. As well as built with feet, rather than wheels. Creform Structures can be built for ESD for anti-static applications. Available as a kit or an assembled structure or in the component form for a complete DIY solution. The Creform System is used to create an array of material handling and efficiency-enhancing devices and is a proven component in continuous improvement and lean manufacturing programs. The company partners with customers in developing and implementing these programs.
Myers Industries completes acquisition of Signature Systems
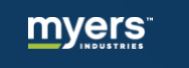
Myers Industries, Inc., a manufacturer and distributor of industrial products, has announced that it has completed its acquisition of Signature Systems, which was previously announced on January 2, 2024. “We are excited to welcome the Signature team to Myers with the closing of this transaction,” said Mike McGaugh, Chief Executive Officer of Myers Industries. “This acquisition strengthens our growing portfolio of market-leading brands, enhances our profitability profile, and demonstrates Myers’ capability as a platform for acquisitive growth. With a strong runway of future growth, due to increasing infrastructure investments over the next decade, we believe Signature’s sustainable competitive advantage, strong earnings growth, and free cashflow profile will help us accelerate EPS growth and achieve our long-term strategic objectives.” The cash transaction of $350 million was funded through an amendment and restatement of Myers’ existing loan agreement, which maintained a $250 million revolving credit facility and added a new $400 million 5-year senior secured term loan A (collectively, the “Loan Agreement”). The term loan A was increased by $50 million from the amount initially contemplated. These combined senior secured loan agreements enhance Myers’ overall liquidity profile and capacity for future potential acquisitions. Pro forma for the acquisition, the Company’s net leverage ratio is approximately 3.0x, which is within management’s target range. The financial results of Signature Systems are expected to be included within Myers’ Material Handling segment. Chief Financial Officer Grant Fitz commented, “As mentioned in January, this transaction is expected to be neutral to slightly dilutive to US GAAP EPS in fiscal year 2024, and we anticipate Signature will deliver EPS accretion of $0.20 to $0.30 in 2025 and $0.40 to $0.50 in 2026 with additional meaningful EPS accretion beyond 2026. We also expect annualized run-rate operational and cost synergies of $8 million to be fully captured by 2025 with additional synergies to be realized once Signature has an opportunity to leverage the Myers Business System. Excluding other potential opportunities that may come forward, we anticipate using the free cash flow generated from the combined Myers and Signature company to allow Myers to reduce the net leverage ratio below 2.0x within two years of the closing of this transaction.” Moelis & Company LLC served as the exclusive financial advisor to Myers concerning the transaction, while Vorys, Sater, Seymour, and Pease LLP and Davis Polk & Wardwell LLP provided legal counsel. William Blair & Company LLC served as exclusive financial advisor and Honigman LLP served as legal counsel to Signature. The Loan Agreement was led by J.P. Morgan Chase, U.S. Bank National, Wells Fargo Bank and KeyBank National.
stow Group presents a seamless collaboration of racking and robotics expertise at MODEX 2024
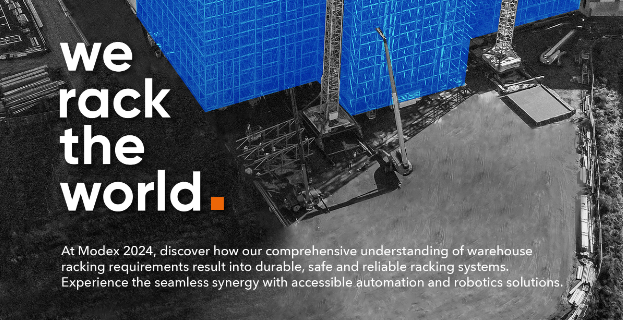
stow Group, a supplier of advanced racking systems and accessible automation and robotics solutions, is presenting its premier brands, stow and Movu Robotics, under one roof for the first time at MODEX 2024. Booth B6008 (in hall B) will be a vibrant showcase for stow Group, which will include live demonstrations of racking, automation and robotics systems. From bin storage via precise piece picking, to efficient pallet transport and strategic pallet storage, the exhibits will play out like a harmonious symphony of logistics expertise in both Racking and Robotics. In the dynamic world of warehouse operations, stow Group is the embodiment of long-term expertise, high quality, and reliability. MODEX 2024 is a significant milestone marking the next phase for the Group and, through spotlighting the power of expertise and innovation in action, it sets the stage for a promising future. Harmonizing the reliability of traditional racking systems with cutting-edge robotics automation, stow Group provides a ‘one-stop shop’ for autonomous sub-systems. By combining the best of racking and robotics, it creates successful and seamless integrated warehousing solutions for customers seeking efficient logistics operations. As a global leader in warehouse storage solutions, stow delivers innovative and reliable racking systems, ensuring easy and swift installation. Its global network of factories accelerates supply times and offers localized support for an unmatched storage experience. At its core, stow specializes in the development, manufacture, and installation of top-quality solutions. The company’s offering is a guarantee for performance and quality, which has been finely crafted over 40 years, and provides a precise, robust, and enduring foundation for all warehouse racking needs, setting the stage for seamless warehouse integration. At Modex 2024, the international scope and a strong portfolio of benchmark projects will be presented by a collection of showcases with customers in all industry sectors. Sharing the stand, stow Group’s new brand, Movu Robotics will present for the first time a unique technology showcase including the full portfolio. Movu throws the spotlight on democratizing automation and robotics by making it more accessible and possible in all kinds of warehouses. Going beyond offering a single robotics product, Movu produces cutting-edge sub-systems for automated storage and retrieval of bins and pallets as well as automating piece picking and internal transport to create a symphony of automated solutions. Providing flexibility and scalability, Movu’s easily adaptable cutting-edge robotics systems work in harmony with existing infrastructure, with its intelligent robots handling diverse loads for an efficient warehousing future. Visitors will be able to see how Movu software coordinates and monitors the shuttles and mobile robots, ensuring a smooth flow of materials with real-time visibility of the system. As demonstrated in the different material flow showcases on the stand, the solutions are a practical, accessible reality rather than a futuristic concept. Movu’s goal is to upgrade the world´s warehouses through the power of easier automation, ensuring that no warehouse – irrespective of its size, shape or use – is left behind. With stow providing excellence in established racking systems and Movu Robotics, pioneering accessible automation and robotics technologies, stow Group seamlessly merges the finest elements from the worlds of racking and robotics. Being a trusted partner with the gravitas of a global player and the agility of a start-up, the Group offers unparalleled reliability. Experts from both stow Group brands will be on hand to discuss how its solutions, which have improved efficiency for customers in a variety of sectors, can serve your requirements. Jos de Vuyst, CEO of stow Group commented: “We are excited to present for the first time both Group brands, stow and Movu Robotics, together on our booth at Modex 2024. We look forward to not only presenting the long-term experience and global footprint of our racking business but also showing visitors how they can access innovative and accessible warehouse automation solutions. The technology showcases will be outstanding performances of material flows, which will feature the entire robotics portfolio of Movu, for both bins and pallet transportation and storage. The stow Group brands integrate storage systems alongside autonomous sub-systems, with proven software interfaces. Such a fusion of strengths ensures that each element works in harmony, crafting a smooth and efficient orchestration of warehouse operations.”
LEEA sets date for #GLAD2024 and updates Logo
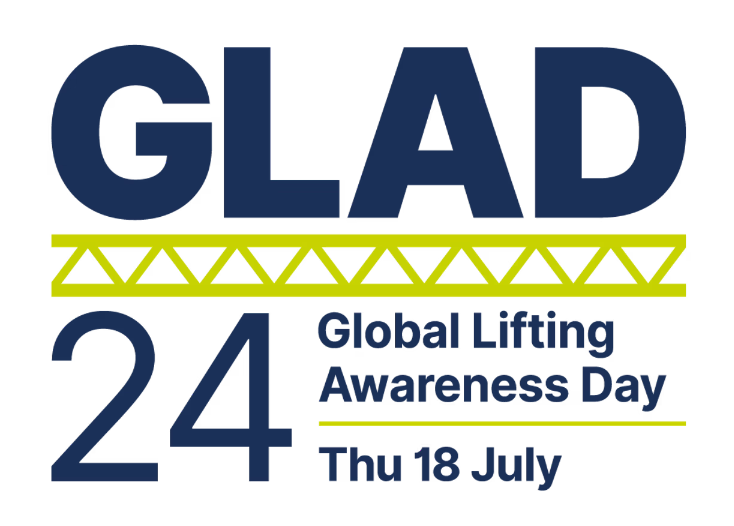
The fifth Global Lifting Awareness Day — #GLAD2024 — will take place on Thursday 18 July, represented by a new logo. Powered by the Lifting Equipment Engineers Association (LEEA) and supporting organizations, it is now a widely celebrated day where manufacturers, suppliers, and end users are among those that share material that promotes safe and high-quality load lifting. Social media posts, videos, articles, and in-person activity will again be bound together by the hashtag, #GLAD2024. Ross Moloney, CEO at LEEA, said: “GLAD is now positioned as a globally recognized concept and has achieved a brand-like status, perhaps ahead of schedule, following ongoing efforts from industry stakeholders to raise its profile. We’re looking to use its popularity to raise awareness of what our industry people do and what those outside of the sector need to do to become part of our world. This is why the themes LEEA will focus on this year are skills and employment.” The new logo captures this evolution, moving away from the previous version that centered on a hook, towards a graphic that focuses more on the title of the awareness event. The text is built around the gantry element of so many cranes and lifting technologies — instantly recognizable to industry representatives with the means to promote the sector. LEEA has consciously pivoted, putting the main focus on GLAD rather than a particular component or piece of equipment, reiterating that #GLAD2024 is for everyone. Moloney said: “The messaging has always been underpinned by raising awareness — a theme that endures. We are still raising awareness, but the difference will be that we will focus on attracting recruits and developing those already in the industry. Expect to see references to CPD [continual professional development] and training, as we showcase the abundance of opportunity our marketplace represents.” Use the hashtag As with previous years, LEEA is encouraging its members, end users, and everyone in between, to contribute by using the graphic and hashtag to celebrate their involvement with the industry and promote it as an interesting place to work, with skills and employment as suggested focal points of outreach efforts. It is a membership that understands the value of continually raising standards, with #GLAD2024 serving as a platform from which to convince a wider community to train and develop their staff while signposting pathways into lifting. Moloney added: “LEEA’s vision is to reduce all accidents, injuries, and fatalities within the lifting industry to zero, and we have various initiatives in place to achieve this. The fundamental tool in all these initiatives is knowledge transfer, enabling CPD, and raising standards of practice. The way by which LEEA provides access to and disseminates knowledge is through vehicles such as our online training platform, technical triage, Chatbot, guidance documents, and other resources.” Celebrate the lifting industry on Thursday 18 July — include the #GLAD2024 hashtag.
Flex-Line Automation, Inc. to shine on national television
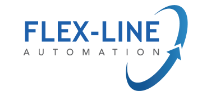
Flex-Line Automation, Inc., a family-owned business in southern Illinois, has been selected to feature on a national television program. For 17 years the World’s Greatest TV Show has been taking viewers on a fast-paced tour around the world, by providing behind-the- scenes footage and interviews of some of the most amazing and unique companies, products, services, technologies, people, and travel destinations the world has to offer. On 2/17/24 they will be showcasing the remarkable journey of Flex-Line Automation, Inc. and the legacy of excellence it has cultivated over the years. Flex-Line Automation, Inc. is an example of integrated innovation in the manufacturing industry and demonstrates unwavering commitment to customer service and creative thinking. Rhett Rinne founded Flex-Line Automation with his parents and wife Cathy in the early 1980’s when he saw an opportunity for his rural ingenuity to provide excellent material handling solutions for manufacturers. His daughter, Lauren, joined the company upon graduation. The company has become well-known in the industry for creative conveyor and robotic solutions. The segment on Flex-Line Automation, Inc. will provide an insightful look into the behind-the-scenes operations, the dedication of our employees, and our ongoing commitment to advancing innovation in rural America. “We are extremely honored and excited to be featured as one of the World’s Greatest!…,” said Cathy Rinne, president and majority owner of Flex-Line Automation, Inc. “Our selection is a testament to the hard work and creativity of our team. We are excited for this opportunity to represent the mission and values that make Flex-Line Automation stand out in our field.” The episode featuring Flex-Line Automation, Inc. is scheduled to air on Saturday February 17, 2024 at 1:00pm CST on BLOOMBURG TV. We encourage our suppliers, customers, collaborators, friends, and supporters to tune in and witness the remarkable story of our family business.
UniCarriers® Forklift unveils new brand campaign: A Brand You Can Trust

Reinforcing the brand’s commitment to providing reliable product development, prompting a future of innovation UniCarriers® Forklift, part of the Mitsubishi Logisnext Americas group (Logisnext), has launched its new brand campaign, A Brand You Can Trust, to celebrate more than 100 years of shaping a strong brand heritage focused on prioritizing customers, trustworthiness reliability, and innovation. UniCarriers Forklift has left a notable mark on businesses worldwide, offering unparalleled industry knowledge and expertise. The brand’s diverse range of forklifts has become an integral part of various industries, facilitating the seamless movement of goods and materials across warehouses, distribution centers, and manufacturing facilities around the world. Adapting to the dynamic needs of the industry, UniCarriers Forklift has evolved to meet customers changing needs, investing significantly in research and development. Dedicated to enhancing performance, efficiency and safety, UniCarriers Forklift has elevated productivity by gearing up for an electrification shift in North America, with the release of its advanced electric counterbalance product lineup in 2023. This includes: MXST and MXS Series: 3-wheel and 4-wheel electric pneumatics forklifts SCX N2 Series: Electric Stand-up Counterbalanced Lift Trucks MX2 and MXL Series: 80-Volt, 4-wheel electric pneumatic forklifts “We are proud of our strong counterbalance heritage, serving satisfied customers for more than a hundred years – a heritage that is unparalleled in the industry,” said Niels Tolboom, Director of North America Dealer Sales (Marengo) at Mitsubishi Logisnext Americas. “This heritage pushes our team to use their expertise to pave the way for a future full of innovation. UniCarriers Forklift continues to showcase advanced and reliable products that customers can trust to perform to the highest level.” UniCarriers Forklift Looks Ahead to the Future UniCarriers Forklift will continue being dependable, trustworthy, and at the forefront of the material handling industry as the brand looks ahead at a future concentrated on electric and internal combustion. Every Class I, IV, and V forklift manufactured by UniCarriers Forklift comes with the industry’s only 2 years/unlimited-hour warranty, reinforcing its confidence in the durability and performance of its products. The new UniCarriers electric lineup continues the tradition of reliability with key features, such as: Maximized Uptime: UniCarriers products are reliable forklifts with exceptional performance for customer operations, offering increased uptime and improved efficiency. Greater productivity: UniCarriers Forklift offers maximum productivity and ease of service through the use of innovative features that help improve visibility, handling, and performance while providing operator comfort and control. UniCarriers’ A Brand You Can Trust campaign will highlight customers’ continued success and further reinforce the brand’s commitment to its customers, reliability, dependability and excellence.
Vector Security Networks announces partnership with International Supply Chain Protection Organization (ISCPO)

Vector Security Networks to exhibit at Manifest 2024, an expo that brings together leaders and innovators in supply chain and logistics. Vector Security® Networks, a division of Vector Security®, Inc., and the single-source provider of physical security solutions and managed network services to multi-site businesses across North America, has been named a partner of the International Supply Chain Protection Organization (ISCPO). The partnership helps connect ISCPO members to solutions offered by Vector Security Networks that safeguard their supply chain operations while protecting people and products. As part of its Preferred Partner Program, ISCPO is dedicated to expanding its array of vendor solutions, harnessing proven products, and staying at the forefront of industry best practices. Additionally, Vector Security Networks will participate in Manifest 2024 in Las Vegas, February 5-7, at Caesars Forum. The company’s security experts will be on hand to discuss challenges, opportunities, and solutions for supply chain and logistics providers. The team will also be demonstrating EAIGLE automated vehicle access control and forklift camera solutions that not only can increase safety and security but can also provide insights to improve business operations. Look for Vector Security Networks at booth #1411.
Vacuum Interrupters introduces the new CBT-1203 circuit breaker timer test set
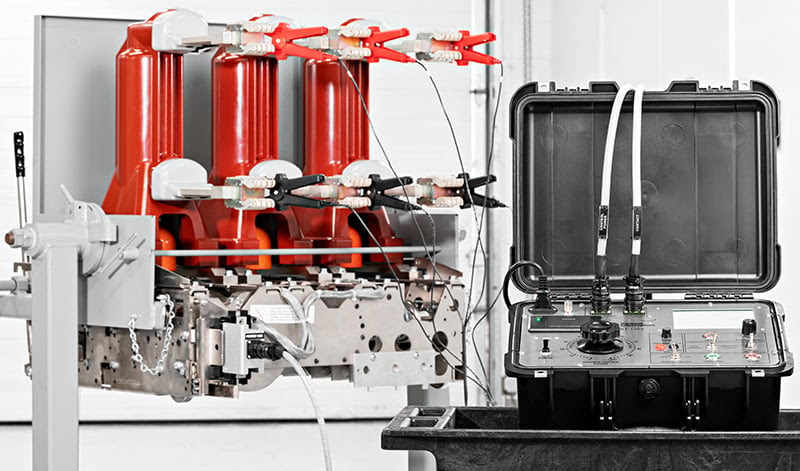
Vacuum Interrupters, a manufacturer of replacement vacuum interrupters, pole assemblies, parts, and components for medium-voltage vacuum circuit breakers and contactors, introduces the CBT-1203 circuit breaker timer test set. This accurate, portable, and easy-to-use tool confirms proper breaker speed and clearing times as part of a maintenance program or arc-flash validation study. The CBT-1203 performs three-phase timing tests, charges spring-charged circuit breakers, opens/trips and closes breakers, and captures and stores millisecond trip and close times and duration of contact bounce. With the integrated variable 120 VAC/125 VDC power supply, the CBT-1203 can operate breakers outside of cubicles. Breaker-switching controls and custom breaker-specific operation plugs allow users to quickly set up and operate the unit with all types of circuit breakers. The large back-lit LCD is viewable in sunlight and low-light conditions. The compact and lightweight unit measures 16.5 inches wide, 7 inches high, and 13.5 inches deep and weighs 19 pounds, making it ideal for use in the shop or field. The test set includes the circuit breaker timer, control power, and contact leads, a universal breaker operation cable, contact clamps, an input power cable, and a durable storage bag.
Cimcorp to feature end-to-end automation for fresh food distribution at MODEX 2024
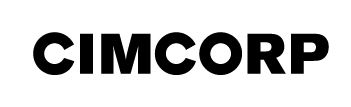
MODEX 2024 booth #B6019, attendees will discover how Cimcorp’s automation helps grocery retailers, bakeries, and dairies improve speed, sanitation, and sustainability Cimcorp, an intralogistics automation specializing in fresh food handling and tire-handling solutions, will exhibit at MODEX 2024 booth #B6019. The company will showcase its comprehensive range of automated storage and order-picking systems, specifically designed to optimize fresh and perishable food distribution for grocery retailers, bakeries, and dairies. MODEX attendees will have the opportunity to explore Cimcorp’s technology through interactive demonstrations and discussions with company experts. As a trusted automation partner, Cimcorp helps grocery retailers transform warehousing operations through efficient product handling. Cimcorp’s modular systems combine gantry robots, intelligent software, AS/RS, AGVs, conveyors, shuttles, palletizers, and more to optimize operations from end to end, boost productivity, and improve overall performance. Additionally, Cimcorp offers continuous maintenance through its Success Services—including spare parts, training, and 24/7 support—to help customers secure a lifecycle of 20 years or more for their automation technology. Throughout the show, MODEX attendees can meet with Cimcorp representatives to discuss their biggest operational challenges and explore how Cimcorp’s solutions: Modernize order fulfillment for fresh produce, dairy products, and baked goods Minimize lead times and maximize freshness for perishable foods Save costs and time by retrofitting existing facilities Support supply chain sustainability efforts Ensure 100-percent uptime, backed by lifetime support Notably, Cimcorp will highlight its flexible, modular solution for retrofitting existing distribution centers with automation. The solution enables rapid installation in any existing facility footprint and allows grocery retailers to introduce automation modules based on present needs, with the ability to scale as the business grows. “We’re excited to highlight our end-to-end automation at MODEX 2024! Automation is the future of fresh food distribution, and our unique solutions make it easier than ever to get started with automation in a way that is quick, cost-effective, scalable, and sustainable,” said Adam Gurga, National Manager of Grocery and Retail Partnerships, Cimcorp. “Equipped with Cimcorp technology and support, our clients can future-proof their operations and delight their customers with the freshest products for years to come.”
HWArobotics delivers advanced ASRS technology to Canadian e-commerce specialist Darwynn
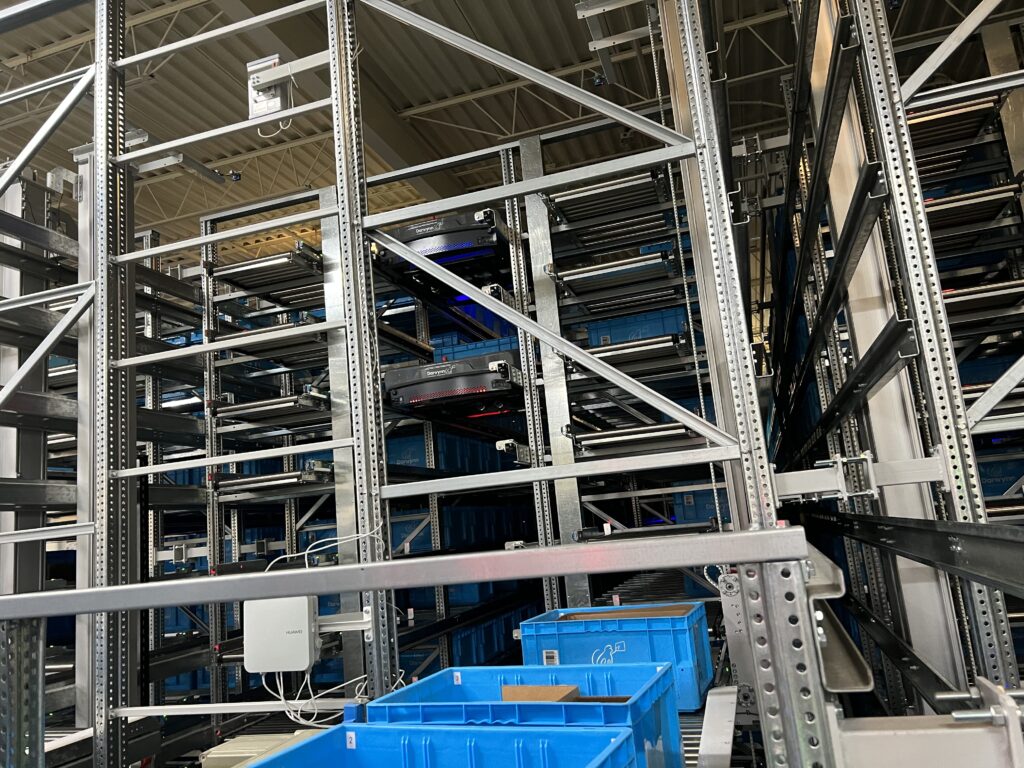
HWArobotics is making a splash in North America, supplying advanced shuttle ASRS technology to e-commerce logistics specialist Darwynn The North American warehouse automation market is undergoing rapid changes as it continues to expand and innovate. Shuttle systems pioneer HWArobotics is attracting attention in the region with the recent adoption of its technology by Canadian e-commerce fulfillment specialist Darwynn. Third-party logistics provider Darwynn, which prides itself on using cutting-edge warehousing solutions, turned to HWArobotics to streamline order fulfillment operations at its site in Toronto, Canada. Robotic automated storage and retrieval systems (Shuttle ASRS) technology from HWArobotics – comprising a multi-level shuttle system of 24 carts, 10,368 storage locations, and 6 goods lifts – was selected by Darwynn for its intelligent logistics center. Darwynn provides sellers with localized warehousing, logistics, and after-sales services through an integrated e-commerce platform, modularized intelligent warehouse, and seamless integration with multiple logistics platforms. It was looking to meet the demands of its business expansion as the number of SKUs within its facilities increased, in addition to enhancing service quality, efficiency, safety, and sustainable development capabilities. HWArobotics technology delivers immediate and future benefits With 20,000 individual SKUs handled by the new facility, the HWArobotics Shuttle ASRS “goods-to-person” system was able to increase throughput for Darwynn to 2,400 bins/hour. In the first phase of Darwynn’s project, storage is configured as 3 double-deep aisles and 8 levels for the efficient parallel operation of multiple shuttle carts. The shuttle ASRS solution, with picking stations and WCS systems, was easily integrated into Darwynn’s end-to-end fulfillment operations via HWArobotics’ industry-leading speedy onboarding process. It has delivered a series of benefits for Darwynn and its customers, including: Optimized inventory management Enhanced operational efficiency Higher throughput Improved warehouse space utilization Expanded storage capacity Reduced overall business costs Lower error rates Reliability and ease of maintenance Complementing Darwynn’s real-time inventory tracking and e-commerce offering and meeting the demands of sellers and buyers, the new system is also future-proofed – with a total inventory capacity of 200,000 items, the capability to meet peak business needs, and the adaptability to match Darwynn’s growing demand. Commenting on the project, HWArobotics General Manager, Sky Chen, explains, “This project delivered an efficient, reliable, user-friendly and easily-maintained multi-level shuttle ASRS warehouse system. We are very pleased with the system performance so far and the potential the solution offers to Darwynn for further expansion. We look forward to continuing this successful partnership in the future.” HWArobotics plans to continue expansion in North America Darwynn is just one of many successful customer deployments by HWArobotics. Bringing its 20 years of rich industry experience in logistics automation to North America, the company has established a high-performance team in the region to provide extensive global after-sales service, with on-site engineers to assist post-sales. The company debuted its SLS600 four-directional tote shuttle robot at the ProMat 2023 trade expo in Chicago last March to gain momentum and seek further partnerships with North American system integrators. Sky Chen, adds, “Our tested and trusted ASRS solutions embody advanced design principles and are based on two decades of industry know-how, innovations, and outstanding R&D competence. Leveraging our extensive experience in supply chain efficiencies across the Asia-Pacific region, HWArobotics is an ideal partner for companies in North America, offering our full range of shuttle robot products. We are keen to bring our value proposition to U.S. system integration partners to achieve a win-win situation for the long term.” In addition to its expanding customer base in North America, HWArobotics also has successful deployments of its pioneering shuttle technology around the globe, with customers including Shein, Bosch UAES, SONY, Freshippo (Alibaba Group’s grocery retail chain), Hisense Hitachi, Faurecia (a subsidiary of global automotive technology giant FORVIA Group), JD.com, and Phoenix Media. In South Korea, the company has been a key part of consumer co-operative group iCOOP’s fresh food project, supplying a solution with 22 shuttle cars, 4,840 storage spaces, and 4 goods lifts. HWArobotics was recently nominated as a “Finalist” for the prestigious IFOY Award 2024. Run by German logistics prize group IFOY, the international industry prize this year features 15 companies from 6 countries. The winners are determined by an independent jury of international trade journalists and will be announced in June at a ceremony in Baden, near Vienna, Austria. Announcing the shortlist, Anita Würmser, Chairperson of the IFOY jury declared that the finalists “reflect the megatrends of our time”.
U.S. Rail Traffic for the week ending January and the week ending February 3, 2024
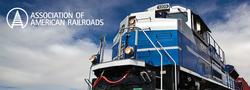
The Association of American Railroads (AAR) today reported U.S. rail traffic for the week ending February 3, 2024, as well as volumes for January 2024. U.S. railroads originated 1,025,168 carloads in January 2024, down 7.2 percent, or 79,725 carloads, from January 2023. U.S. railroads also originated 1,206,014 containers and trailers in January 2024, up 5.5 percent, or 63,195 units, from the same month last year. Combined U.S. carload and intermodal originations in January 2024 were 2,231,182, down 0.7 percent, or 16,530 carloads and intermodal units from January 2023. In January 2024, six of the 20 carload commodity categories tracked by the AAR each month saw carload gains compared with January 2023. These included: chemicals, up 4,298 carloads or 2.9 percent; petroleum & petroleum products, up 2,172 carloads or 4.5 percent; and primary metal products, up 1,447 carloads or 3.6 percent. Commodities that saw declines in January 2024 from January 2023 included: coal, down 40,542 carloads or 12.3 percent; crushed stone, sand & gravel, down 18,260 carloads or 19.5 percent; and grain, down 14,367 carloads or 12.8 percent. “In January, severe winter weather significantly disrupted railroad and rail customer operations in much of the country,” said AAR economist Dan Keen. “Moreover, uncertainty remains in the economy, especially in sectors that are important to railroads, like manufacturing. Because of these factors, January is not necessarily a harbinger of what’s to come for rail traffic in the months ahead.” Excluding coal, carloads were down 39,183 carloads, or 5.0 percent, to January 2024 from January 2023. Excluding coal and grain, carloads were down 24,816 carloads, or 3.7 percent. Week Ending February 3, 2024 Total U.S. weekly rail traffic was 491,697 carloads and intermodal units, up 11.6 percent compared with the same week last year. Total carloads for the week ending February 3 were 222,213 carloads, up 6.3 percent compared with the same week in 2023, while U.S. weekly intermodal volume was 269,484 containers and trailers, up 16.5 percent compared to 2023. All of the 10 carload commodity groups posted an increase compared with the same week in 2023. They included coal, up 4,641 carloads, to 62,779; motor vehicles and parts, up 2,297 carloads, to 15,455; and metallic ores and metals, up 1,096 carloads, to 19,457. North American rail volume for the week ending February 3, 2024, on 10 reporting U.S., Canadian and Mexican railroads totaled 328,148 carloads, up 4.7 percent compared with the same week last year, and 352,559 intermodal units, up 15.4 percent compared with last year. Total combined weekly rail traffic in North America was 680,707 carloads and intermodal units, up 10.0 percent. North American rail volume for the first five weeks of 2024 was 3,112,134 carloads and intermodal units, down 1.4 percent compared with 2023. Canadian railroads reported 91,685 carloads for the week, up 1.8 percent, and 72,643 intermodal units, up 12.7 percent compared with the same week in 2023. For the first five weeks of 2024, Canadian railroads reported a cumulative rail traffic volume of 743,641 carloads, containers, and trailers, down 5.8 percent. Mexican railroads reported 14,250 carloads for the week, up 0.4 percent compared with the same week last year, and 10,432 intermodal units, up 8.6 percent. Cumulative volume on Mexican railroads for the first five weeks of 2024 was 137,311 carloads and intermodal containers and trailers, up 16.1 percent from the same point last year. To view the Rail Traffic charts, click here.
Celebrating Success: Mitsubishi Logisnext Americas Group honors UniCarriers® Forklift’s Premier Club Winners for 2023
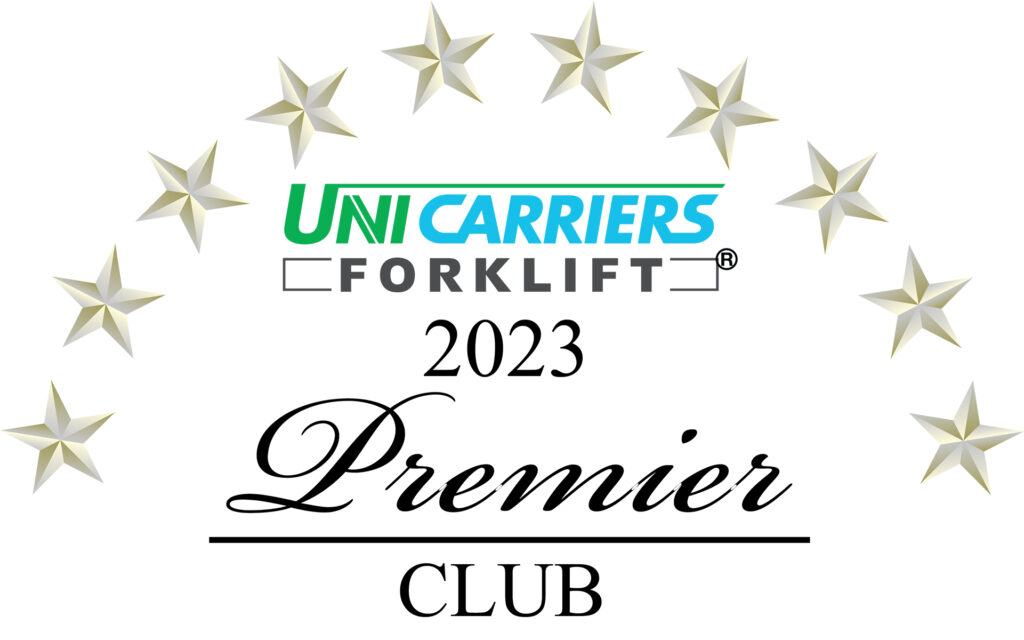
Mitsubishi Logisnext Americas, the exclusive manufacturer and provider of UniCarriers® Forklift across North, Central, and South America, revealed the winners of its Premier Club Awards for 2023. Each year, the Premier Club program identifies the top 10 UniCarriers Forklift dealers throughout the Americas that embody the brand’s core values. Award honorees set a benchmark for excellence, demonstrating remarkable standards that serve as an inspiration to all dealers. Beyond fostering a culture of reliability and professionalism, each awardee surpassed challenging targets, securing a place among the OEM’s premier dealerships. Overall, UniCarriers dealers were evaluated based on market penetration, aftermarket parts sales, new equipment sales and overall professionalism. “It is a privilege to support these honorees,” said Niels Tolboom, Director of North America Dealer Sales at Mitsubishi Logisnext Americas (Marengo). “We know this award is based on demanding metrics, so it is incredible to see exceptional dealers across the Americas rigorously commit and excel at representing the UniCarriers Forklift brand.” The following 10 dealers excelled in these fundamental areas and received the respected status as UniCarriers Premier Club winner for 2023: Dyna-Lift – Montgomery, AL J. M. Equipment Company, Inc. – Manteca, CA Lift Truck Service Center – Little Rock, AR MHS Lift, Inc. – Pennsauken, NJ Montacargas Truck S.A. De C.V. – Mexico City, MX Parkway Systems – San Antonio, TX Quality Forklift Sales & Services – Shakopee, MN Select Equipment Sales – Buena Park, CA Sunbelt Material Handling – Dallas, TX Vegusa Maquinaria – Leon, MX
Synergy Logistics announces dynamic new tech integration partnership
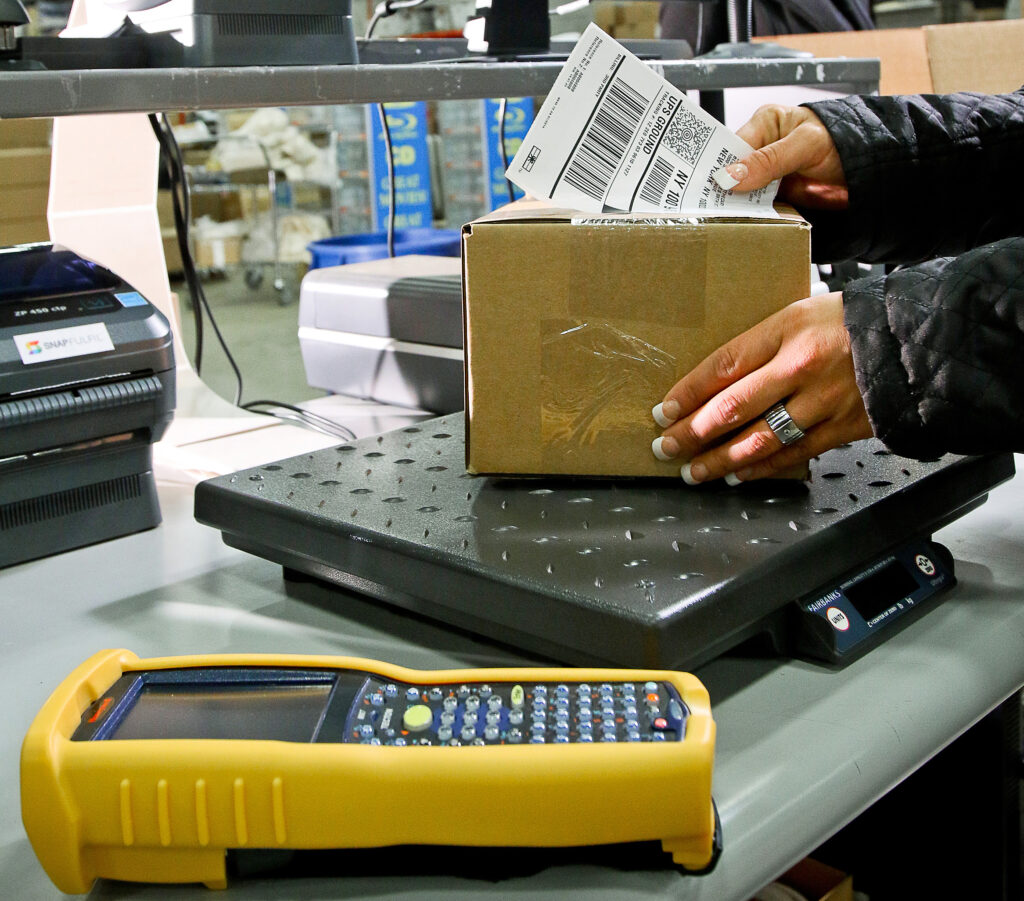
Warehouse technology innovator, Synergy Logistics, has partnered with leading connected fulfillment solutions specialist, Techdinamics, to provide customers with integrated rate shopping and transportation management capabilities. The alliance with Ontario-based Techdinamics is around their techSHIP solution, which dovetails seamlessly with Synergy’s advanced warehouse management system (WMS) SnapFulfil. Together, they create a fully connected workflow – order, WMS, pick, pack, ship – to get orders out the door faster and correctly, but with no additional labor and lower operating costs. TechSHIP is a powerful cloud-based application that quickly and easily integrates with multiple small parcels, Less-Than-Truckload (LTL), and Full Truckload Freight (FTL) carriers to generate shipping labels and custom documentation. It also provides lower cost or most appropriate services for customer product lines, depending on selection, shipping to addresses, and other preferences. The generated label and tracking information seamlessly populate SnapFulfil, providing users with a smooth end-to-end experience. This integrated process, known as the blackbox API, grants SnapFulfil operators access to comprehensive shipping software without the need to navigate between multiple screens. With connections to over 150+ carriers, techSHIP enhances order accuracy, accelerates order processing, ensures on-time delivery, and offers competitive shipping rates. Smitha Raphael, Chief Product & Delivery Officer for Synergy Logistics, says: “The techSHIP solution offers depth of integration, but also speed, as you can write your own, multiple management rules. It’s a quick and agile system like ours and customers can be configured and up-to-speed within 20-30 minutes for rapid efficiencies and return on investment.” The partnership is already working well for Utah-based online beauty retailer, Younique, as the integration with techSHIP has enabled them to not only onboard previously unavailable carriers like Purolator, but via SnapFulfil’s batch functionality print labels far more efficiently and quickly for high volume orders – decreasing the cost levels on their shipping for the first time. Reg Adams, President at Techdinamics, adds: “The partnership is a natural fit as SnapFulfil seamlessly integrates with techSHIP’s API, enabling users to stay within the WMS for order processing and label generation. Users can handle their orders in the WMS as usual and the system automatically communicates with techSHIP. This allows the full and dynamic utilization of techSHIP’s order management rules and rate shopping capabilities.” This strategic alignment with Techdinamics is the latest in Synergy’s rapidly expanding native integration and partnership network, which via real-time peer-to-peer transactions seeks to provide transparency across all critical business systems and sales routes – and is already 40+ companies strong across sectors like ERP, iPaaS, Marketplace, Robotics & MHE, Shipping, plus other channel partners.
January 2024 Logistics Manager’s Index Report® LMI® at 55.6
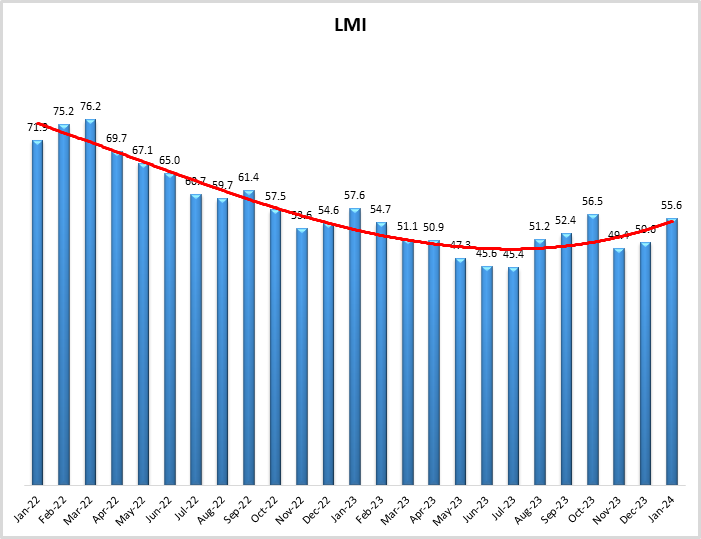
Growth is INCREASING AT AN INCREASING RATE for: Inventory Levels, Inventory Costs, Transportation Utilization and (making its first appearance in 20 months) Transportation Prices Growth is INCREASING AT A DECREASING RATE for: Warehousing Capacity, Warehousing Utilization, Warehousing Prices, and Transportation Capacity For the first time since September of 2019, every metric in the Logistics Managers’ Index is reading in expansion territory. The most significant move is the long-awaited return of Transportation Prices (+12.7) to expansion, its first appearance on the positive side of the ledger since June of 2022 at the start of the freight recession. This price increase is largely driven by movements by retailers to increase their Inventory Levels (+8.4) after a busy holiday season. This inventory rebuild also led to a considerable increase in the expansion of Inventory Costs (+11.0). This is a marked shift for Inventory Costs, which registered their lowest reading ever in January at 55.8. Our warehousing metrics continued their steady, sustainable rates of expansion, with all three growing at slightly slower rates (changes range from -1.0 to -1.5). We need to see a longer period of growth to call an official end to the freight recession. However, when taken together, January’s report does offer evidence that the logistics industry could be moving back into a period of growth after the long downturn that started in 2022. Researchers at Arizona State University, Colorado State University, Florida Atlantic University, Rutgers University, and the University of Nevada, Reno, in conjunction with the Council of Supply Chain Management Professionals (CSCMP) issued this report today. Results Overview The LMI score is a combination of eight unique components that make up the logistics industry, including: inventory levels and costs, warehousing capacity, utilization, and prices, and transportation capacity, utilization, and prices. The LMI is calculated using a diffusion index, in which any reading above 50.0 indicates that logistics is expanding; a reading below 50.0 is indicative of a shrinking logistics industry. The latest results of the LMI summarize the responses of supply chain professionals collected in January 2024. The LMI read in at 55.6 this month, up (+5.0) from December’s reading of 50.6. This is the fifth time in the last six months that the LMI has shown contraction. This growth is driven by an increase in the restocking of inventories – especially for retailers – after a busy holiday season as Americans are feeling better about the overall economy. Consumer sentiment spiked by 13.1% in January 2024 to a level of 79.0%. The combined 29% increase in sentiment from December to January is the biggest two-month jump since the end of the recession in 1991[1]. There are many reasons behind this improving sentiment. The U.S. continued to grow through the end of 2023 as GDP was up 3.3% in Q4. When taken together with the 4.9% growth in Q3, it is clear that the combination of federal spending, continued low unemployment and receding inflation have empowered U.S. consumers – whose spending increased 2.8% in Q4. On the inflation front, consumer prices only increased by 1.7% annually in Q4[2]. This has been greatly helped by moderating supply costs, which were only mildly inflationary (accounting for 0.38% inflation month-over-month for core PCE inflation) in December[3]. Additionally, this slowdown in inflation has not come at the employment cost that some economists had hypothesized would be necessary. Job growth remained robust in the U.S. as employers added 353,000 new positions in January – the most in a year. This included large increases in sectors like retail, manufacturing, and information technology[4]. Due to these improvements, in their January meeting the U.S. Federal Reserve formally changed their stance on interest rates to a more flexible position that would allow for the long-anticipated reductions in the interest rate. While rates currently remain between 5.25 and 5.5%, analysts are expecting as many as three rate cuts throughout 2024 and that the first such cut could come as early as the Spring[5]. This is good news for the freight markets as high interest rates have been the main factor holding back spending in the upstream portions of supply chains from which larger, bulkier shipments often originate. While the U.S. economy has looked strong to start the year, The recovery has not been consistent across the globe. While economies in the U.S. and India have been robust, the Euro-zone has been much more stagnant. The Eurozone registered 0% growth in Q4 – although this was up from contraction in Q3. This downturn may let up in late 2024 if the central bank begins cutting interest rates but will continue to face headwinds in the Ukraine-Russia war and a manufacturing slump in Germany[6]. There are also continued issues in China, where real estate firm Evergrande was ordered to liquidate by a judge in Hong Kong so that they can pay back their $300 billion debt. This closure will add a complication to China’s economic recovery as the government was deeply tied into Evergrande and their real estate holdings, and will need to make some creditors whole at a time when they need to appear to be a safe bet from foreign investors[7]. There are also issues in the links between the economic engines of the world. Ocean container shipping costs have more than doubled in the last month. This increase is largely due to the Houthi rebel attacks in the Red Sea that have caused Suez Canal traffic to dip 37% in January year-over-year[8]. Compounding this is the drought-related reduction in ships passing through the Panama Canal where low water levels have cut sailings in half[9]. While these issues are troubling, they have not yet caused supply shocks similar to what we saw during COVID. For some perspective, Drewry is currently estimating the cost of shipping a 40-foot container to be around $3,7008. During COVID, this number was closer to $20,000. That being said, the sooner these issues are resolved the better. Despite these global headwinds, the I.M.F. has joined the chorus of those recognizing the ongoing economic soft landing
Mitsubishi Logisnext Americas announces its 2024 Cat® Lift Trucks, Mitsubishi Forklift Trucks and Jungheinrich® Dealers of Excellence
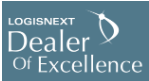
Mitsubishi Logisnext Americas, a manufacturer and provider of material handling, automation, and fleet solutions, has revealed the winners of its 2024 Dealers of Excellence program. Each year, the award program recognizes dealers representing Ca® lift trucks, Mitsubishi forklift trucks, and Jungheinrich® warehouse and automation products across North America. Dealers receiving this honor demonstrated best-in-class industry expertise and provided superior service to material handling industry customers. The 2024 winners were selected from among more than 90 Cat lift trucks, Mitsubishi forklift trucks, and Jungheinrich dealers within the Mitsubishi Logisnext Americas dealer network in North America. “We are excited to announce our exceptional and dedicated 2024 Dealers of Excellence recipients,” said Eric Gabriel, vice president of dealer sales Americas, Mitsubishi Logisnext Americas. “This award shines a spotlight on dealers, and we are so appreciative of their attentiveness to the material handling industry.” 2024 Dealers of Excellence Honorees Include: Darr Equipment Company (South) Equipment Depot Illinois Equipment Depot Kentucky Fallsway Equipment Company Fraza Holt of California Kelly Tractor MADISA MATCO Miami Industrial Trucks Morrison Industrial Equipment Prime Material Handling Quinn Lift Toromont Material Handling (Quebec) TRACSA Wiese USA (Atlantic) Wiese USA (Central) Wiese USA (East) Wiese USA (South)
Tompkins Solutions partners with Soft Robotics to deliver revolutionary AI-enabled technology to the logistics industry
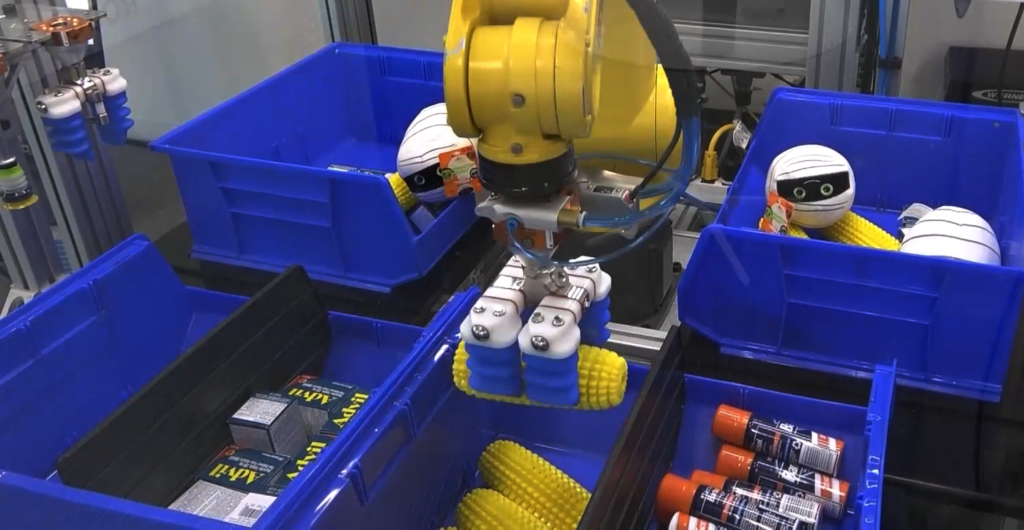
Tompkins Solutions, a leading supply chain consulting and material handling integration firm, has announced a partnership with Soft Robotics, a provider of innovative robotic automation solutions. This collaboration will deliver cutting-edge AI-powered robotics to logistics operations worldwide, enabling them to address ongoing supply chain issues and optimize order fulfillment. Initially introduced to the food industry, Soft Robotics’ mGripAI™ solution leverages AI-enabled 3D vision and soft grasping technologies to perform high-speed picking, sortation and packaging of a wide variety of items. This unique combination of advanced technologies enables industrial robots to replicate the sensory, cognitive and dexterous abilities of human workers, allowing warehouse operations to automate labor-intensive processes while increasing productivity and capacity. “We’re excited to team up with Soft Robotics to bring this proven technology to the logistics industry,” said David Latona, CEO of Tompkins Solutions. “As supply chains continue to face complex challenges and disruptions, AI-enabled solutions like mGripAI will play a critical role in helping companies increase efficiency, reduce costs and meet growing demands.” “After experiencing overwhelming success in the food industry, we’re now delighted to apply our no-code robotic picking and inspection solutions to applications across a variety of new industries,” said Mark Chiappetta, CEO of Soft Robotics. “We look forward to partnering with Tompkins Solutions to help organizations optimize their supply chain operations and gain a competitive advantage.” Tompkins Solutions will showcase mGripAI, along with other industry-leading warehouse automation and robotics systems, at its booth (#A11323) at MODEX 2024, March 11-14 at the Georgia World Congress Center in Atlanta.
AGILOX North America to showcase their autonomous vehicles at MODEX Trade Show in Atlanta
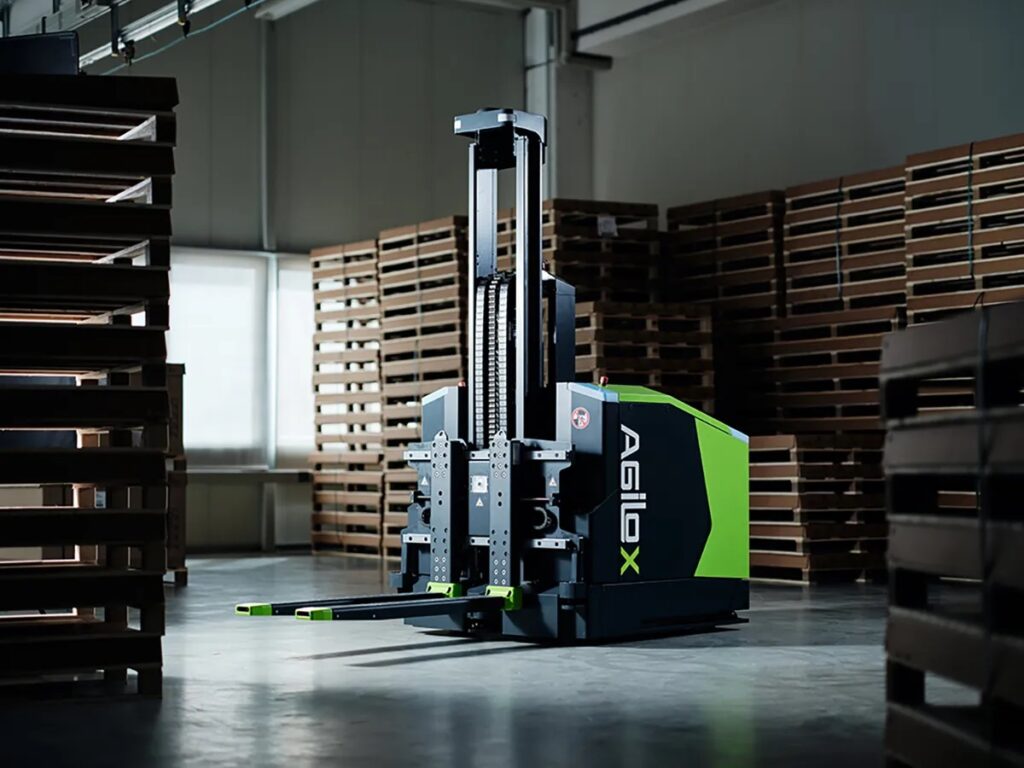
AGILOX North America has announced its participation in the upcoming MODEX 2024 in Atlanta Booth C7492. The company will exhibit its autonomous mobile robots, providing attendees with a firsthand look at the future of material handling and logistics. With a steadfast focus on customer success, AGILOX is set to unveil a new addition to its portfolio, demonstrating its continued dedication to supporting clients on an ever more integrated automation journey. The forthcoming product promises to showcase the latest advancements in technology, reinforcing AGILOX’s position as a leader in the industry. “We are excited to present our autonomous vehicles at MODEX, showcasing the latest advancements in material handling technology,” said Andreas Boedenauer, CEO at AGILOX North America. “Our goal is to offer solutions that enhance operational efficiency in logistics environments.” AGILOX’s fork-based vehicles revolutionize the world of AMRs, focusing on ease of use and scalability, allowing users to integrate AMRs and adjust workflows seamlessly. The vehicles comply with the UL 3100 standard, marking a milestone in safety and reliability. The certification underscores AGILOX’s commitment to meeting the highest industry standards for autonomous systems, ensuring safe and efficient operation in diverse industrial environments. To showcase the AGILOX AMRs and their capabilities, the company invites industry professionals to visit them at the upcoming MODEX show in Atlanta. The event will be an excellent opportunity for attendees to witness firsthand the advanced technology and safety features that set AGILOX apart in the autonomous robotics industry. MODEX 2024, Georgia World Congress Center, Atlanta. Booth C7492, MODEX 2024 March 11th – 14th, 2024. AGILOX representatives will be available at the booth to provide demonstrations, answer questions, and discuss how their certified AMRs can optimize material handling processes in various industries.
How to select a filter fan based on application conditions
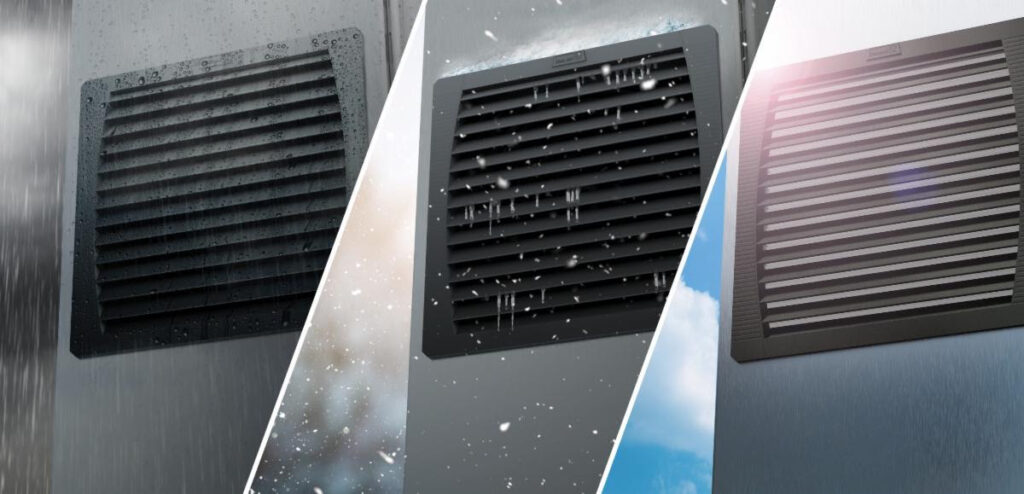
From electrical equipment to environmental considerations, here are expert tips for smart selection What are filter fans? Filter fans protect electrical enclosures from external environmental damage. From heat control to mitigating the ingress of liquid and solid objects, filter fans provide another layer of protection for the electrical equipment housed within enclosures. Filter fans protect critical equipment by reducing thermal load and filtering out airborne particles larger than 5 microns. The dual fan and filter composition keeps electrical equipment running at optimal temperatures while mitigating the amount of dust and other particulate matter from causing buildup and damage. When selecting a filter fan for an enclosure, it’s important to consider the application’s heat load, optimal temperature, and environmental conditions in which it will be operating. Environmental considerations are particularly important for outdoor enclosures, as rain, snow, ice, and sunlight all pose risks to electrical equipment. Challenges for outdoor applications Filter fans are necessary for a wide range of outdoor electrical equipment. Some applications, however, require intentionality and extra consideration when choosing the appropriate filter fan. These include irrigation pump panels, water, and wastewater, lighting control boxes for traffic signals or fields and stadiums, outdoor communication and information technology structures, energy storage and charging systems (such as in electric vehicles), and transportation systems, including bridges, toll stations, and electrical rail equipment. When properly designed and integrated, outdoor filter fans can provide an energy-efficient solution for heat load maintenance while also protecting enclosures from dust, ice, water, and sunlight. However, many filter fans on the market do not effectively protect critical electrical equipment. When improperly designed, filter fans can be subject to ice and dust buildup or damage from UV radiation and rainwater. These conditions can cause short-circuiting within the enclosure. While there are workarounds for water infiltration, such as adding a rain hood, these additional steps increase space requirements and initial investment costs. Tips for selecting the correct filter fan Given these challenges, there are some tips to keep in mind when selecting a filter fan for an outdoor electrical enclosure. Consider heat load and environment Selecting an outdoor filter fan begins with determining the application’s heat load and airflow requirements while considering environmental exposure. Electrical enclosures in dry, hot weather require different filter fan needs than those used in areas with snow, ice, and highly variable temperatures. For applications where environmental conditions cannot be determined ahead of time, a filter fan that can accommodate each of these possibilities is best. While determining application needs, it is beneficial to consult with an expert to help determine specific risk factors. An expert can help with considerations around which airborne particulates are present and if they are corrosive, as well as what ambient temperatures can be expected and how direct or indirect sunlight can affect operating temperatures. The Pfannenberg Outdoor Rated Filterfan® (NEMA 3R rated) is designed for outdoor weather where direct sunlight and extreme weather, like rain and ice formation, are important factors. This filter fan utilizes UV-resistant plastics to prevent premature degradation from direct sunlight. Additionally, the filter fan’s design protects against the ingress of falling dirt, rain, sleet, snow, and even external ice formation. Weigh maintenance needs Filter fans generally require little maintenance outside of regular filter replacement. However, it is crucial to change the filter as specified by the manufacturer as filter clogs reduce airflow, causing extra strain on the fan and increasing the potential for overheating. Well-designed filter inserts, including the filter for Pfannenberg’s Outdoor Rated Filterfan®, described above, provide longer service life. Pfannenberg’s fluted filter-mat enables longer mean time between maintenance, delivering three times longer service life than standard designs. It accomplishes this with its increased dust-holding capacity. As a result, the need for service is reduced, saving maintenance time, costs, and stress, which is especially helpful for electrical enclosures located in remote areas. Balance protection, airflow, and initial investment costs Filter fans for outdoor applications require a design that balances airflow optimization with low initial investment. A filter design that minimizes maintenance needs should also ensure unrestricted airflow throughout the fan’s service life. However, it must do so without compromising on water and dust protection capabilities. Combining a filter that fits these needs with a filter fan housing design that does not require metal rain hoods, achieves an excellent balance of protection, airflow management, and minimizing upfront costs. Conclusion Filter fans are critical for protecting electrical equipment from overheating, water, and airborne debris so the equipment can run safely and efficiently. In outdoor environments, this task is particularly challenging. Finding a filter fan suitable for outdoor environments without significant drawbacks requires careful research. By considering heatload, environmental conditions, and maintenance needs before selecting a filter fan, it is possible to keep costs low. In applications ranging from pump panels and lighting control boxes to communication technology and energy storage systems, well-designed filter fans keep outdoor electrical equipment functional and safe. By Lucas Faulkner, Solutions Engineer, Pfannenberg USA
Gebrüder Weiss announced acquisition of Salt Lake City based freight forwarding company Cargo-Link
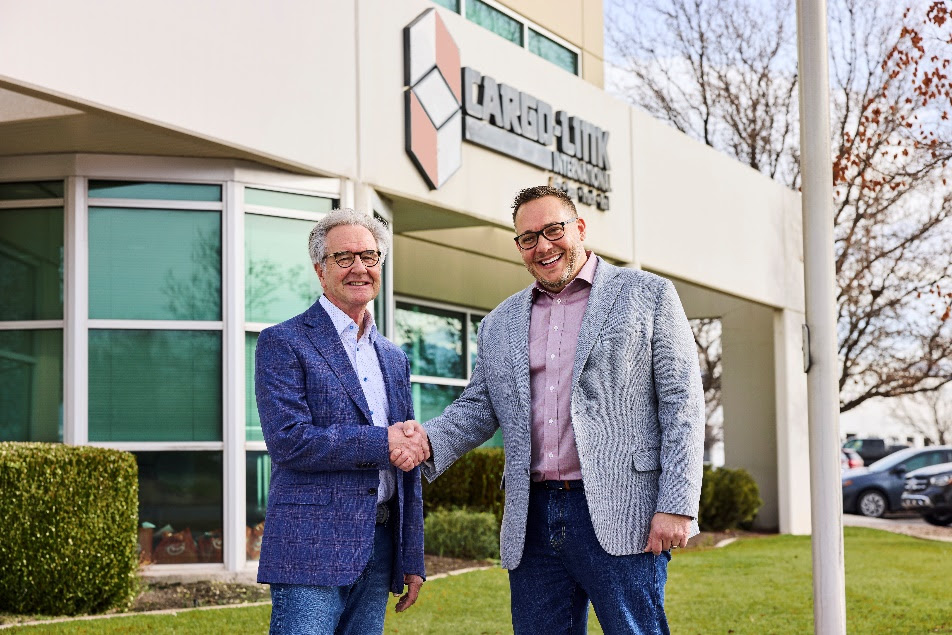
Gebrüder Weiss, a 500-year-old international transport and logistics company, has announced the acquisition of Cargo-Link, a fully family-owned, non-asset-based freight forwarding company based in Salt Lake City, Utah. Cargo-Link specializes in less-than-container load (LCL) shipping and imports from Asia to mid-west-based customers in the U.S. The acquisition is a component of the Gebrüder Weiss plans for continued growth in North America, including further development of LCL services in its Air & Sea division. With Cargo-Link, Gebrüder Weiss will offer specialized weekly LCL service from North and South China ports directly into Salt Lake City. Gebrüder Weiss, the North American division headquartered in Wood Dale, Illinois, will leverage Cargo-Link’s strategic location and its leadership team’s expertise to open new LCL routes to Asia and Europe. Salt Lake City is a fast-growing market that values local presence, and the acquisition provides a new regional market entrance. Gebrüder Weiss will retain Cargo-Link’s management team and integrate its employees into the newly merged organization. “We are thrilled to bring Cargo-Link under the Gebrüder Weiss umbrella,” says Mark McCullough, CEO of Gebrüder Weiss North America. “There are tremendous synergies between the two companies, and we mutually benefit from the agreement. We look forward to partnering with the Cargo-Link leadership team to enhance our customers’ LCL and Intermountain West-based opportunities.” Cargo-Link was founded in 1976 in Salt Lake City and grew to become a renowned freight forwarder and Customs House Brokerage (CHB) in a secondary market. Operationally, the majority of the business is comprised of sea freight imports, with air freight, domestic freight forwarding, and export business making up the remainder. CEO and Owner Scott Ogden has managed Cargo-Link since its inception and has developed an extensive network of client relationships and overseas partners. “This acquisition significantly upgrades our service potential and broadens customer access, seamlessly blending Cargo-Link’s expertise with the expansive capabilities of Gebrüder Weiss,” says Scott Ogden, CEO of Cargo-Link. “The two companies are a cultural fit as well as a business fit. Cargo-Link is a family-owned, family-focused company with a philanthropic culture, and we sought those same values in a corporate partner.” In addition to Gebrüder Weiss’ greater coverage in the Intermountain West geographic area and establishing Salt Lake City as its 15th North American location, the company also gains access to a 22,000-square-foot warehouse attached to the Cargo-Link office and optimally positioned near the Salt Lake City airport. Gebrüder Weiss North America has opened operations in all major U.S. markets and is now focusing on regional markets with location-specific experience and operations.
Unirope expands manufacturing in Ontario
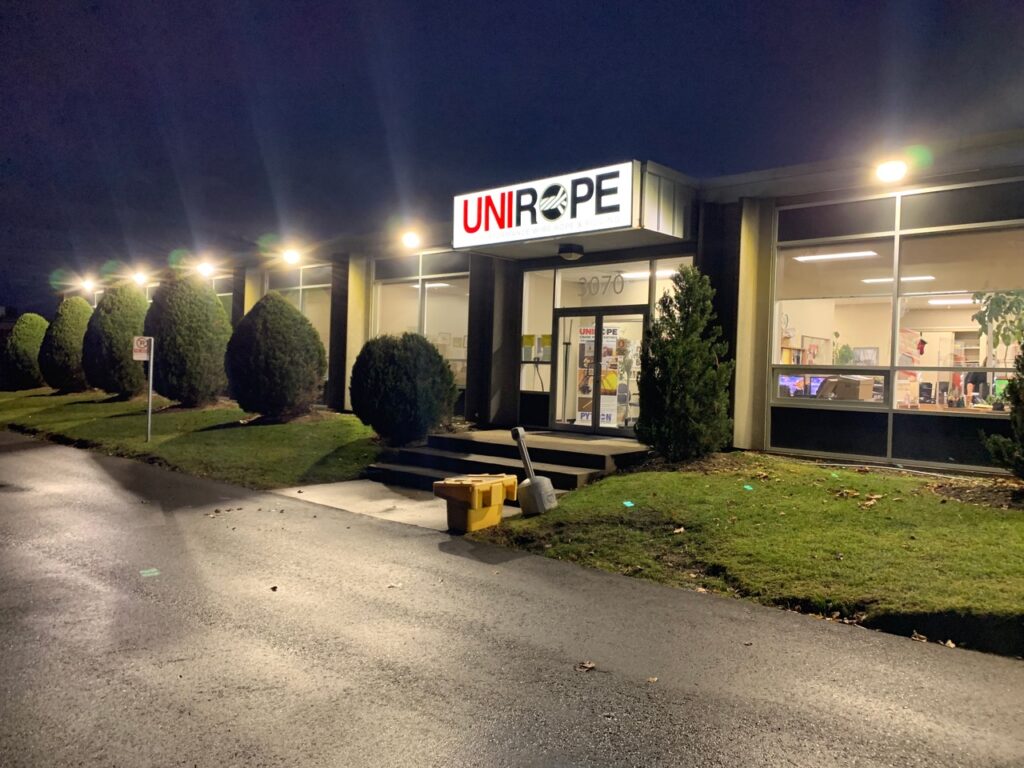
Mississauga, Ontario-based Unirope Limited has added 50,000 sq. ft. of manufacturing space to its headquarters, improving lead times by as much as 400% Unirope is a manufacturer, distributor, testing, certification, and inspection of high-performance wire rope and rigging products. It has additional facilities in Quebec and Alberta; the three sites combine to deliver service nationwide and to select customers in the U.S. and Europe. The expansion represents the completion of a journey that started in 2018, before ground-breaking two years later, and a major construction project that concluded in 2021. Since then, further investment has been committed to equipping the facility with state-of-the-art machining and fabrication equipment, centered on wire rope fabrication, synthetic sling manufacturing, and computer numerical control (CNC) technology. Justin Brown, president at Unirope, said: “At a minimum, we have cut lead times in half, and in the best case we have seen a 400% improvement. We are moving towards modernizing the traditional rigging shop model. The words ‘rigging shop’ and ‘modern’ are rarely mentioned in the same breath. Many of the products are heavy and lined with grease, and most factories are stuck in the 1980s with equipment from the 1960s. Not us.” He continued: “We have implemented material handling solutions to help with heavy lifting; installed modern machinery to make reeling, cutting, and fabrication easier; utilized technology to put work instructions at the fingertips of production workers; installed a full machine shop with modern [CNC] capabilities for custom wire rope end fittings; upgraded ventilation to keep the air clean; and fitted environmentally friendly plant lighting alongside fit-for-purpose test units.” The majority of Unirope’s work is on customized rigging products; an interesting statistic, for example, is that 90% of all chain slings that it manufactured in 2023 were unique, either in size, length, or configuration. The business can proof test up to 1.3 million pounds, and the highest single vertical sling capacity in the portfolio is 600,000 pounds. 68 years in the making Unirope already had two warehouses in Mississauga, but it was running out of space to store growing inventory, and the situation was starting to impede production. It would have been impossible to navigate an aggressive phase of growth without expanding and streamlining operations. Brown said: “With strategic machinery updates, we were able to eliminate certain labor-intensive tasks and ease the burden on production employees. The work is difficult, so anything we could do to make the jobs more efficient, eased the physical impact on our employees. Remember, unemployment is at an all-time low, so we have to optimize our workforce. The overall investment led to efficiencies that allowed us to eliminate bottlenecks, deliver faster, and increase our outputs.” An automatic wire rope cutting line, plus additional swaggers and upgraded annealing machines will be operated with an additional test bed and a third Twin-Path® machine. Additional warehouse space also meant that inventory could be increased across all product lines, including Python® high-performance wire rope, Grade 100 chain, and a range of Crosby rigging hardware. Python® wire rope is stocked in a wide variety of constructions for tower cranes, mobile and truck cranes, overhead cranes, and gantry cranes. These ropes are widely used in construction, automotive, and industrial applications. Unirope also stocks a variety of other standard and custom ropes, all meeting national and international standards. Brown added: “We have built a diversified customer base over the last 68 years and continue to build on that strategy. Our customers, without exception, are looking for professional and attentive service. They want our input and expertise; they are not looking for the cheapest and untested; they want reliability and quality.”