Toyota’s 80V Electric Pneumatic Forklift earns 2023 GOOD DESIGN Award
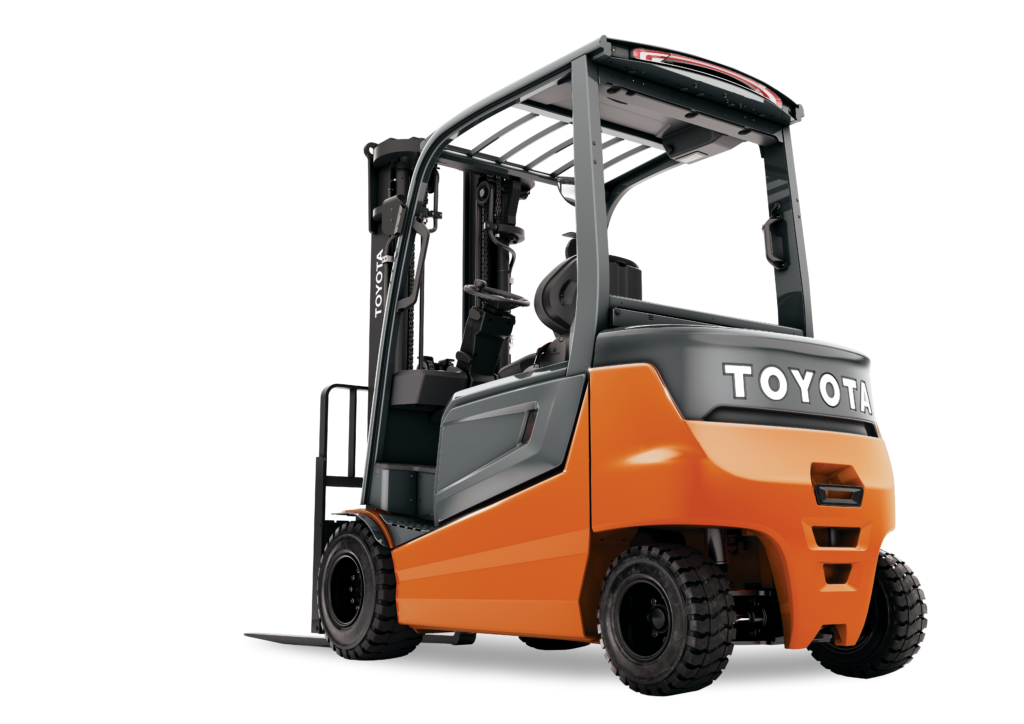
Toyota Material Handling receives the 2023 GOOD DESIGN Award as a testament to the engineering and design quality of the innovative, European-designed and built 80V Electric Pneumatic Forklift Toyota Material Handling’s innovative 80V Electric Pneumatic Forklift – designed and built in Europe – was named a 2023 GOOD DESIGN® Award recipient, giving testament to the product’s world-class engineering, aesthetics, durability, and performance. This model and the rest of Toyota’s advanced lineup of industry-leading forklifts reflect Toyota’s commitment to prioritizing customer needs, in alignment with the organization’s culture of Kaizen – or continuous improvement. “The Good Design Award not only expands awareness in the design community, but it also highlights the attention to quality, usability, aesthetics, and ergonomics in Toyota products around the world,” said Greg Smiley, Toyota Material Handling North America’s Head of Design. Recognition for this award-winning product is prompted by its unique and innovative features. The multifunction display system helps enhance efficiency by notifying the operator of battery capacity and operating time warnings while facilitating rapid diagnostics to prevent unplanned downtime. Toyota’s innovative System of Active Stability (SAS)™ engages instantly to stabilize the rear axle if the system senses the forklift is in a situation that could lead to instability. The forklift also provides ample comfort for operators with its full-floating cabin and full-suspension seat that helps minimize shock and vibration. Toyota’s Operator Presence Sensing System and the optional seatbelt interlock encourage operators to remain properly seated with the seatbelt buckled. Additionally, the cockpit-style operator compartment allows operators a clear line of sight and minimizes fatigue with its memory-tilt-steering technology, mini-lever controls, an armrest, and a low-height dashboard. The electric forklift is strategically engineered in alignment with Toyota’s sustainability initiative. With load capacities ranging from 4,000 to 17,500 pounds, the battery-powered forklift increases efficiency by combining the power and durability of non-electric models with its top-of-the-line AC drive motors, allowing operators a reliable material handling solution for indoor and outdoor environments. In addition, the forklift offers standard speed control and performance modes to allow operators to select power consumption, acceleration and regenerative braking. This contributes to maximized efficiency, performance and operating time. The 80V Electric Pneumatic also extends outdoor lifespan through preventative technology that limits water intrusion and corrosion. Learn more about Toyota Material Handling’s innovative material handling solutions at ToyotaForklift.com.
KION Group starts solid with increases in revenue and earnings
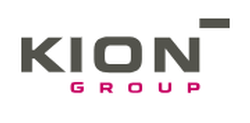
Revenue up by 2.8 percent to € 2.859 billion (Q1 2023: € 2.781 billion) Adj. EBIT improves to € 226.7 million (Q1 2023: € 156.0 million) Adj. EBIT margin of 7.9 percent (Q1 2023: 5.6 percent) Positive free cash flow of € 65.7 million (Q1 2023: € 104.9 million) Full-year 2024 outlook confirmed The KION Group started the financial year 2024 with revenue growth and improved profitability. The adjusted EBIT margin of 7.9 percent came in 2.3 percentage points higher year-on-year, with significant improvements in both operating segments. “KION Group had a solid start in 2024 substantially improving profitability at the Group level and in both segments in the first quarter,” says Rob Smith, CEO of KION GROUP AG. “Achieving the second-best quarterly adjusted EBIT on the KION Group level lays a strong foundation to deliver our full-year guidance.” Group revenue in the first quarter of 2024 grew by 2.8 percent to € 2.859 billion year-on-year (Q1 2023: € 2.781 billion). In the Industrial Trucks & Services segment, revenue increased by 7.4 percent to € 2.153 billion (Q1 2023: € 2.005 billion), mainly due to the positive geographic and product mix as well as higher production output and sales prices. The service business also grew. Revenue in the Supply Chain Solutions segment declined by 8.1 percent to € 718.9 million (Q1 2023: € 782.5 million) due to the lower project business order intake of the previous quarters. The Supply Chain Solutions segment benefited from increased demand from pure e-commerce providers, general merchandise, and food retailers, but order intake in the project business remained subdued in the first three months impacted by customers’ hesitancy to sign new contracts due to macroeconomic uncertainties. In addition, the order book contains a higher proportion of long-term projects, whose revenue realization will extend over a longer period. Service business achieved a significant increase in revenue in the reporting period. Adjusted EBIT at the Group level increased significantly to € 226.7 million (Q1 2023: € 156.0 million). The adjusted EBIT margin improved accordingly to 7.9 percent (Q1 2023: 5.6 percent). The Industrial Trucks & Services segment continued its positive development of the previous quarters and achieved a double-digit adjusted EBIT margin of 11.1 percent (Q1 2023: 8.8 percent) with an adjusted EBIT of € 239.7 million (Q1 2023: € 176.6 million). This was mainly due to the continued stability of material purchase prices, increased productivity as a result of improved material availability and revenue growth. In the Supply Chain Solutions segment, the adjusted EBIT margin increased to 2.6 percent (Q1 2023: 0.9 percent) with an adjusted EBIT of € 18.4 million (Q1 2023: € 7.1 million). Service business growth, improved project execution and the efficiency measures implemented contributed to the improvement in earnings and margins. At € 111.0 million, consolidated net income in the first quarter of 2024 was significantly higher year-on-year (Q1 2023: € 73.5 million). Free cash flow amounted to € 65.7 million (Q1 2023: € 104.9 million). KION Group Figures for the First Quarter 2024 in million € Q1/2024 Q1/2023 Diff. Revenue Industrial Trucks & Services Supply Chain Solutions 2,859 2,153 719 2,781 2,005 783 2.8% 7.4% -8.1% Adjusted EBIT [1] Industrial Trucks & Services Supply Chain Solutions 226.7 240 18 156.0 177 7 45.4% 35.7% > 100% Adjusted EBIT margin [1] Industrial Trucks & Services Supply Chain Solutions 7.9% 11.1% 2.6% 5.6% 8.8% 0.9% – – – Net income 111.0 73.5 50.9% Basic earnings per share (in €) [2] 0.83 0.55 50.9% Free cash flow [3] 65.7 104.9 -39.2 Order Intake [4] Industrial Trucks & Services Supply Chain Solutions 2,439 1,804 642 2,401 1,957 454 38 -152 187 Orderbook [4] Industrial Trucks & Services Supply Chain Solutions 5,588 2,877 2,778 6,045 3,197 2,921 -458 -320 -142 Employees [5] 42,566 42,325 241 [1] Adjusted for effects of purchase price allocations as well as non-recurring items. [2] Net income attributable to shareholders of KION GROUP AG: € 108.8 million (Q1/2023: € 72.1 million). EPS calculation is based on average number of shares of 131.1 million. [3] Free cash flow is defined as cash flow from ongoing business plus cash flow from investment activity. [4] Figures as of March 31, 2024, compared to balance sheet date Dec. 31, 2023. Prior-year figures for order intake and order book have been definition-related adjusted in the SCS segment. [5] Number of full-time equivalents incl. apprentices and trainees as of March 31, 2024, compared to balance sheet date Dec. 31, 2023. Outlook confirmed Due to the results in the first quarter of 2024, KION GROUP AG confirms the outlook published on February 29, 2024. Outlook 2024 KION Group Industrial Trucks & Services Supply Chain Solutions in million € 2023 Outlook 2024 2023 Outlook 2024 2023 Outlook 2024 Revenue1 11,433.7 11,200 – 12,000 8,479.6 8,500 – 9,000 2,997.0 2,700 – 3,000 Adjusted EBIT1 790.5 790 – 940 848.5 850 – 950 44.3 60 – 120 Free Cash Flow 715.2 550 – 670 – – – – ROCE 7.7% 7.4% – 8.8% – – – – 1 Disclosures for the Industrial Trucks & Services and Supply Chain Solutions segments also include intra-group cross-segment revenue and effects on EBIT.
National Safety Stand-Down to prevent falls is May 6-10
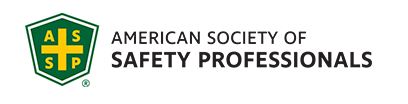
The American Society of Safety Professionals (ASSP) encourages safety professionals and employers to raise awareness and participate in the 11th annual National Safety Stand-Down to Prevent Falls in Construction on May 6-10. The observance is part of a year-round campaign led by the Occupational Safety and Health Administration (OSHA). Falls from height are the leading cause of death for construction workers, with more than 350 fatalities and 20,000 serious injuries occurring each year, according to the U.S. Bureau of Labor Statistics. Workers face risks on roofs, above floor openings and even at lower levels. “No matter the job, worker injuries and fatalities are preventable,” said fall protection expert Thom Kramer, P.E., CSP, vice president of finance on ASSP’s Board of Directors. “Companies can create safe environments by using prevention through design principles, providing the right equipment and training everyone involved. It’s also a great idea to implement a fall protection program that follows our recently updated Z359.2 consensus standard.” Construction companies can recognize the stand-down that week by briefly stopping work and giving a toolbox talk; performing a safety equipment inspection; conducting a rescue planning exercise; or discussing job-specific hazards. It’s important that all workers be outfitted with proper-fitting personal protective equipment (PPE). ASSP encourages the use of #StandDown4Safety in social media to share stories and recommendations during the weeklong observance, which coincides with National Construction Safety Week. It has helped train more than 10 million workers on fall prevention since its inception in 2014. Organizations of all sizes have participated over the years, including the U.S. military, highway construction companies, and residential contractors. OSHA offers several resources for conducting a safety stand-down, including infographics and articles about construction risks and fall protection; publications about ladder safety; fall protection videos; and hardhat stickers and hazard alert cards. Materials on working safely at height are available in English and Español. “Safety and health professionals should encourage their organizations to take an active role in the stand-down,” Kramer said. “And sharing how your company is participating may inspire others to get involved.” OSHA’s many partners in the stand-down include ASSP, the National Institute for Occupational Safety and Health (NIOSH), the National Occupational Research Agenda (NORA), the Center for Construction Research and Training (CPWR), and the National Safety Council.
AMPURE appoints John Thomas as Global Head of EVSE Sales
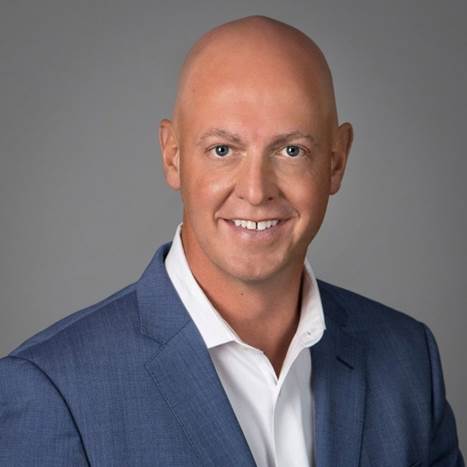
EV Industry veteran brings extensive experience in accelerating growth AMPURE, formerly Webasto Charging Systems, appoints John Thomas as Global Head of EVSE (Electric Vehicle Supply Equipment) Sales to grow its business. Transom Capital Group (Transom) recently acquired AMPURE as a portfolio company. John, former President and Chief Executive Officero of Webasto Charging Systems from 2017 – 2020, rejoins the AMPURE leadership ranks with the target of continuing the growth journey for its EVSE OEM (Original Equipment Manufacturer) and Aftermarket businesses. “John is the right person to lead our continued growth; he brings a wealth of industry knowledge, a strong reputation with the vehicle OEMs, and a unique ability to create partnerships across the entire energy ecosystem,” said Russ Roenick, co-founder and managing partner of Transom Capital Group. We are aggressively investing in people and products to continue positioning our portfolio company as a global leader in electric vehicle charging. John and his peers will pursue the international market, create strong partnerships, and accelerate our business.” Thomas brings over 30 years of global automotive, government relations, and transportation expertise, including more than seven years of leadership in the EV space. He recently served as Chief Operating Officer of a charging start-up, leading that organization’s transition to the North American stage, and was formerly President and Chief Executive Officer of Webasto Charging Systems from 2018-2020. “The electrification transformation is here to stay, and AMPURE brings the missing pieces to complete the puzzle with the industry’s most robust and reliable products. AMPURE is poised to lead the industry through this transition by combining automotive-grade hardware and user-friendly software, enabling our partners to operate their businesses seamlessly,” said Thomas. “AMPURE uses highly skilled engineering, a methodology of working directly with vehicle OEMs, market intelligence, and a focus on level 2 charging, which covers 90% of all EV charging applications. This unique mix allows our organization to design, develop, and manufacture high-quality, regulatory-compliant hardware and software for vehicles, homes, and commercial applications across the globe. I’m confident we possess the correct balance of phenomenal user experience and market-changing innovation that will complement the brand image of any customer or partner.”
Fairchild Equipment recognized as Hyster Dealer of Distinction
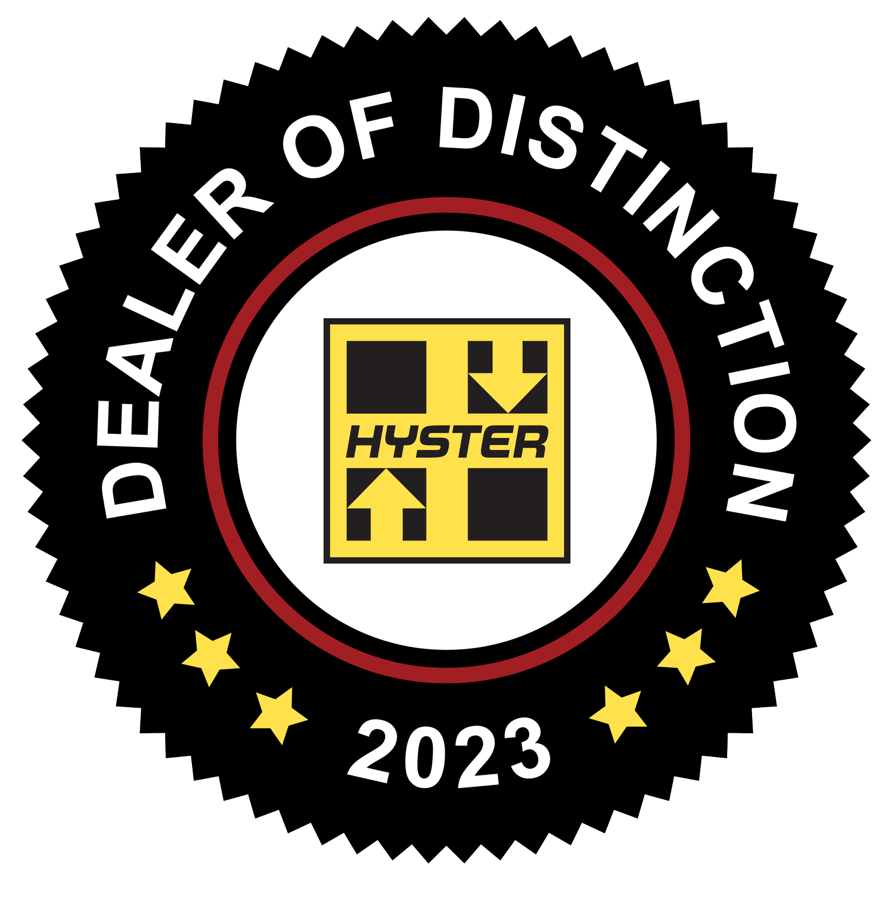
Fairchild Equipment has announced that for the eighth time, we have been recognized by Hyster Company with the 2023 Dealer of Distinction award. This annual award recognizes top-performing dealers across the country that drives their organizations to the highest level of sales and service performance. To be named a Hyster Dealer of Distinction, Hyster dealers must meet defined business practices and overall rigorous performance standards that are updated annually to keep pace with evolving customer expectations and industry dynamics. “Every year, Dealer of Distinction recipients demonstrate their willingness to enhance capabilities and commitment to the safety and well-being of their associates while meeting increasingly demanding recognition criteria,” says Bob Sattler, Vice President, Dealer Business Development. “Our dealers have the breadth of knowledge and experience to guide customers towards maximizing performance in every aspect of lift truck operation, from safety and evolving motive power options to maintenance and fleet management support.” “Receiving the Hyster Dealer of Distinction award for the eighth time is a true testament to our commitment to providing top-notch sales and service to our customers,” said Van Clarkson, President of Fairchild Equipment. “We are honored to be recognized among the best dealers in the country and will continue to strive for excellence in everything we do.” Fairchild Equipment was recognized along with the other Dealer of Distinction honorees at a special awards celebration last week.
Staffing employment holds steady in April
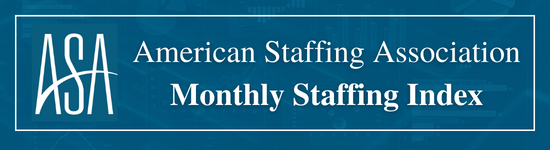
New Starts Down and Four-Week Average Down From Prior Week Staffing employment held steady during the week of April 8-14, with the ASA Staffing Index edging up just slightly to hold at a rounded value of 90. Staffing jobs were down 7.6% from the same period last year; and staffing firms cited school breaks and temporary-to-permanent conversions as factors that hindered further growth. New starts in the 15th week of the year decreased by 7.6% from the prior week. More than four in 10 staffing companies (42%) reported gains in new assignments week to week. The ASA Staffing Index four-week moving average decreased from the prior week to hold at a rounded value of 90, and temporary and contract staffing employment for the four weeks ending April 14 was 8.0% lower than the same period in 2023. “Further normalization in post-pandemic labor supply and demand has enabled staffing employment to reach a steady equilibrium, as evidenced by the ASA Staffing Index holding firm around a value of 90 for 10 consecutive weeks. However, there is still plenty of room for growth in 2024; tailwinds such as interest rate cuts by the Federal Reserve and further moderation in inflation have the potential to shake up the labor market,” said Noah Yosif, chief economist at ASA. This week will be used in the April monthly employment situation report scheduled to be issued by the U.S. Bureau of Labor Statistics on May 3. The ASA Staffing Index is reported nine days after each workweek, making it a near real-time measure of staffing employment trends. ASA Staffing Starts are the number of temporary and contract employees placed in new assignments during the reporting week. ASA research shows that staffing employment has historically been a coincident economic indicator.
U.S. Rail Traffic report for the Week Ending April 20, 2024
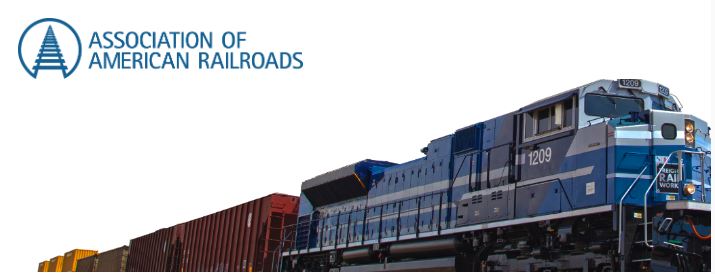
The Association of American Railroads (AAR) has reported U.S. rail traffic for the week ending April 20, 2024. For this week, total U.S. weekly rail traffic was 474,544 carloads and intermodal units, up 0.8 percent compared with the same week last year. Total carloads for the week ending April 20 were 216,945 carloads, down 6.7 percent compared with the same week in 2023, while U.S. weekly intermodal volume was 257,599 containers and trailers, up 8.2 percent compared to 2023. Seven of the 10 carload commodity groups posted an increase compared with the same week in 2023. They included motor vehicles and parts, up 2,236 carloads, to 16,877; petroleum and petroleum products, up 2,119 carloads, to 10,754; and forest products, up 686 carloads, to 8,427. Commodity groups that posted decreases compared with the same week in 2023 were coal, down 20,796 carloads, to 47,472; nonmetallic minerals, down 854 carloads, to 31,781; and metallic ores and metals, down 704 carloads, to 21,100. For the first 16 weeks of 2024, U.S. railroads reported a cumulative volume of 3,408,295 carloads, down 4.6 percent from the same point last year; and 4,025,328 intermodal units, up 9.1 percent from last year. Total combined U.S. traffic for the first 16 weeks of 2024 was 7,433,623 carloads and intermodal units, an increase of 2.3 percent compared to last year. North American rail volume for the week ending April 20, 2024, on 10 reporting U.S., Canadian and Mexican railroads totaled 330,830 carloads, down 4.1 percent compared with the same week last year, and 346,266 intermodal units, up 7.1 percent compared with last year. Total combined weekly rail traffic in North America was 677,096 carloads and intermodal units, up 1.3 percent. North American rail volume for the first 16 weeks of 2024 was 10,466,666 carloads and intermodal units, up 2.1 percent compared with 2023. Canadian railroads reported 96,737 carloads for the week, up 3.8 percent, and 75,954 intermodal units, up 6.0 percent compared with the same week in 2023. For the first 16 weeks of 2024, Canadian railroads reported a cumulative rail traffic volume of 2,556,647 carloads, containers, and trailers, up 0.3 percent. Mexican railroads reported 17,148 carloads for the week, down 11.2 percent compared with the same week last year, and 12,713 intermodal units, down 6.8 percent. Cumulative volume on Mexican railroads for the first 16 weeks of 2024 was 476,396 carloads and intermodal containers and trailers, up 9.0 percent from the same point last year. View the weekly rail traffic charts.
NORD offers optimum conveyor functionality with NORDAC ON/ON+ VFDs
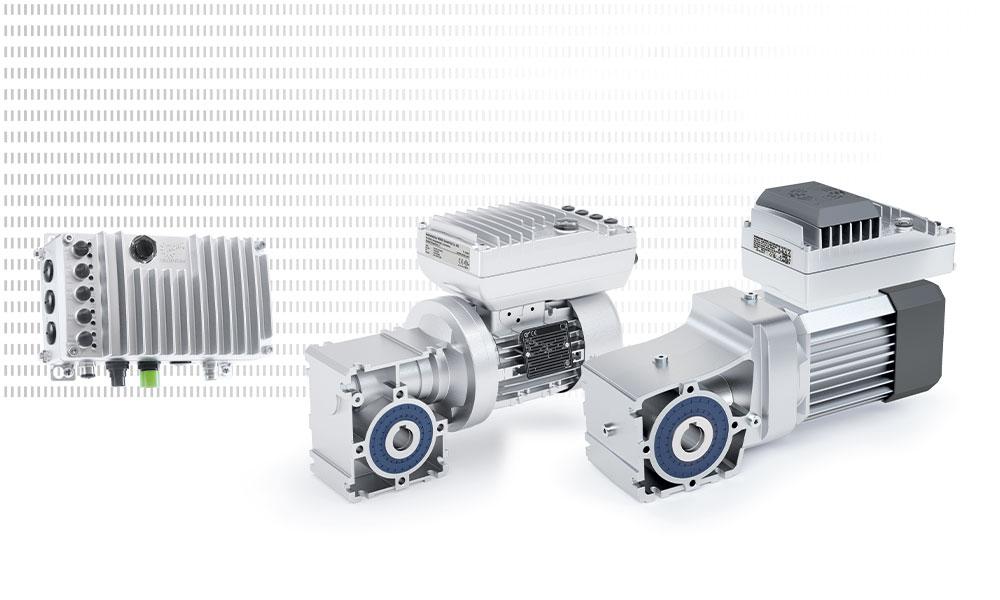
NORDAC ON/ON+ variable frequency drives deliver intelligent control of conveyor systems with an integrated multi-protocol Ethernet interface to improve efficiency, reduce system variants, and optimize performance. NORDAC ON/ON+ variable frequency drives are available in 3 frame sizes for scalable functionality NORDAC ON/ON+ decentralized variable frequency drives are the latest electronic control innovations to be produced by global manufacturer, NORD DRIVESYSTEMS. These VFDs have been engineered for the specific requirements of horizontal conveyor technology and feature integrated functions to optimize operation performance, an integrated Ethernet interface, full Plug-and-Play capability, and a compact design. NORDAC ON/ON+ variable frequency drives feature three frame sizes and two base versions: a version designed for combination with IE3 asynchronous motors and a version optimized for use with IE5+ synchronous motors (NORDAC ON+). Both versions offer compact frame sizes that can be motor- or wall-mounted based on the application and space requirements. The drives can be used over a wide speed range, enabling variant reduction for large intralogistics systems and streamlining operation. NORDAC ON supports a power range of 0.50 – 3.00 hp while NORDAC ON+ supports 0.50 – 4.00 hp. As with all NORD variable frequency drives, the NORDAC ON/ON+ is equipped with a dynamic internal PLC for drive-related functions. It can process data from connected sensors and actuators, initiate control sequences, and communicate drive and application data to the control center, networked components, or to cloud storage. For this purpose, the VFDs have an integrated multi-protocol Ethernet interface for easy integration into automation systems. Whether for ProfiNet, EtherCAT, or EtherNet/IP, the required protocol can be easily set via drive parameters. Firmware updates can also be implemented via Ethernet. In addition to simple configuration, NORDAC ON/ON+ VFDs offer quick installation and maintenance with full Plug-and-Play functionality. The 24 V DC supply for control and communication is integrated into the 3-phase 400 V supply connected to the drive via a 6-pole connector. A daisy chain connector can also be used to supply power to multiple drives, optimizing cable lengths and significantly reduce wiring efforts. NORDAC ON/ON+ VFDs include a variety of integrated functions to improve conveyor efficiency and integrate seamlessly with Industrial Internet of Things (IIoT) environments. These functions include integrated sensors via digital inputs, LED indicators for quick and simple diagnostics, an energy-saving function for optimized efficiency in partial load operation, and brake management for precise control of an electromagnetic holding brake for wear-free brake actuation. Optional functions such as Safe Torque Off (STO), Safe Stop (SS1-t), and internal braking resistors are also available for configuration. With their scalable functionality and dynamic control, NORDAC ON/ON+ variable frequency drives are suitable for a wide range of environments, particularly those in warehousing, post and parcel, airport technology, and other large-scale intralogistics applications.
Flux Power appoints Mark Leposky to Board of Directors
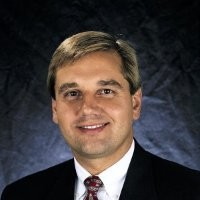
30-Year Global Supply Chain Executive at Fortune 500 Consumer Brands to Advance Company’s New Strategic Growth Initiatives Flux Power Holdings, Inc. has announced the appointment of Mark Leposky, a senior-level executive and entrepreneur, to its Board of Directors as an independent director, effective April 18, 2024. Leposky will also serve as a member of the Audit Committee, Compensation Committee, and Nominating Committee. Mark Leposky has over 30 years of experience leading, transforming, growing, and turning around consumer product and service companies. He currently serves as Executive Vice President and Chief Supply Chain Officer of Topgolf Callaway Brands Corp., an unrivaled tech-enabled golf company delivering leading golf equipment, apparel and entertainment, with a portfolio of global brands. He is responsible for sourcing, manufacturing, golf ball R&D, engineering, quality, program management, planning, purchasing, transportation, and logistics, the Ogio global brand, and the Wolfskin global brand. Before his work at Topgolf Callaway Brands, he served as the President & CEO of Gathering Storm, Chief Supply Chain Officer at Fisher Scientific, and Chief Operating Officer at TaylorMade Golf, among other roles at The Coca-Cola Company and United Parcel Service. Mr. Leposky also served in the U.S. Army for 16 years with roles including Infantry Officer, Platoon Leader, Executive Officer, Company Commander, Battalion and Brigade Logistics Officer. He retired from the Army with the rank of Major and received many awards and commendations including the Douglas MacArthur Leadership Award and The Illinois Medal of Merit. Mr. Leposky holds a Bachelor of Sciences degree in Industrial Technology from Southern Illinois University and an MBA from the Keller Graduate School of Management. “Mark brings deep and valuable business and product strategy experience with a strong track record of driving high growth revenue and profitability, and we welcome him to the Board,” said Ron Dutt, Chief Executive Officer of Flux Power. “He is a highly respected, purpose-driven leader who has a proven history of success throughout his career in a diverse set of industries as well as the U.S. military. His expertise in product development, engineering, program management, supply chain planning, manufacturing, procurement, transportation, logistics and sales operations will be invaluable in reaching sustained cash flow breakeven and continuing our upward margin trajectory, as well as the enhancement of long-term shareholder value.” Leposky added, “This is an exciting time to join Flux Power as it moves into 2024 with strategic growth initiatives, a strong group of sustaining Fortune 100 customers, and high potential new customer opportunities for its advanced lithium-ion energy storage solutions. I look forward to providing my experience in strategic supply chain and profitability improvement initiatives in the months and years to come.” The Company also announced that at the Annual Meeting of the Shareholders in 2024, Cheemin Bo-Linn will retire from the Board. After the 2024 Annual Meeting, Flux Power’s Board will consist of 5 members.
Marketing shouldn’t always sell
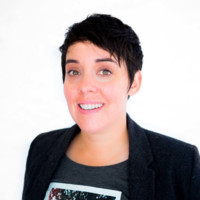
There’s been a recent push (most likely by the bean counters) to establish a direct ROI for marketing efforts. I can understand this thinking. Advertising and marketing are expensive. The adage of “half of all marketing spend is wasted, we just don’t know which half” makes sense, if you’re looking at waste in an immediate return sense. You spend $X on advertising and marketing this quarter and only get $Y in sales. As a numbers person, you’d want to invert that balance. But the problem is, that’s not the only purpose of marketing and advertising. For example, British Airways launched a new outdoor ad campaign, showing a child peering out the window of a plane in flight. The billboards don’t include a logo, QR code, tagline, or call to action. It doesn’t “sell” in the traditional sense. But that’s the point. In a world where executives sit around a board room, evaluating the marketing team’s concepts and stating, “Make the logo bigger”, “We need a call to action”, “Make the product image larger”, “Show the URL”, and “We need to list our features and benefits”, are those thinking about the beans – not how consumers operate and make decisions, or how to create perceptions or build trust and recognition. It comes across as a bit pompous. It’s like saying, “We need to talk as much about ourselves as possible”. A truly expert strategic marketer understands how a company needs to take a unique position and orientation and use marketing to capitalize on it. You see, British Airways isn’t oriented as the low-price leader. So advertising features, benefits, and other amenities would amplify the price narrative – in essence, we have more stuff, but we’re more expensive. So instead, the marketing strategy focused on shifting the narrative around their unique orientation – that experience is their differentiator, and it would be a step down to consider anything else. And they illustrated that experience rather than simply stating it in a bold, sans-serif font. Engaging consumers isn’t just about incessantly promoting features and benefits, but consistently reinforcing what makes you distinctly different in a way that connects with people. Over the last few decades, in the spirit of saving money, companies have continued to hire more and more junior staff, who see “cool” ads and simply try to replicate them, to little success. Remember, if someone knows how to use Canva, it doesn’t mean they are a designer, marketer, or strategist. Just like if someone knows how to use QuickBooks, it doesn’t mean they are a financial expert. It’s not about simply being cool, quirky, funny, or catchy. A unique orientation is inherent to a solid, well-thought-out foundation for a bigger strategy. Without it, the default is run-of-the-mill marketing that pushes features and benefits ad nauseum. Take Walmart, which sets the bar for low price expectations. So a competitor like Target instead focused on a better customer experience orientation. And their marketing focuses on reinforcing and shifting the narrative from “Is it worth paying more for Target?” to “I love Target. Do I want the hassle of going to Walmart?” Marketing strategy, just like a financial strategy, requires a level of experience and expertise that goes beyond the implementation of familiar tactics. And just like any good monetary strategy, returns can take time to manifest. Organizations need to start thinking about marketing less as a transactional sales tool and more as a mindset-changing, narrative-changing tool. Just like short-term versus long-term investing, you can make some quick gains from some lucky stock picks, but the people who make real money are focused on the long game. About the Author Andrea Belk Olson is a keynote speaker, author, differentiation strategist, behavioral scientist, and customer-centricity expert. As the CEO of Pragmadik, she helps organizations of all sizes, from small businesses to Fortune 500, and has served as an outside consultant for EY and McKinsey. Andrea is the author of three books, including her most recent, What To Ask: How To Learn What Customers Need but Don’t Tell You. She is a 4-time ADDY® award winner and host of the popular Customer Mission podcast. Her thoughts have been continually featured in news sources such as Chief Executive Magazine, Entrepreneur Magazine, Harvard Business Review, Rotman Magazine, World Economic Forum, and more. Andrea is a sought-after speaker at conferences and corporate events throughout the world. She is a visiting lecturer and startup coach at the University of Iowa, a TEDx presenter, and TEDx speaker coach. She is also an instructor at the University of Iowa Venture School.
Cabka demonstrates continued leadership in circular economy with 2023 Annual Report
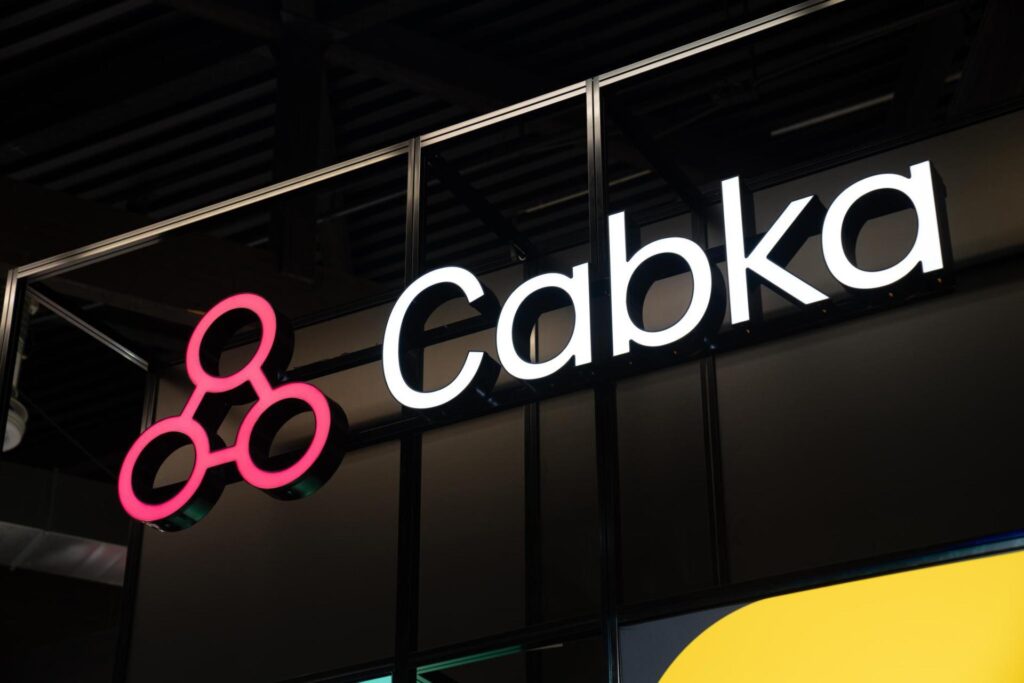
Cabka, the market leader in reusable transport packaging made of recycled plastic publishes its Annual Report 2023. It includes both the financial report for the accounts of Cabka N.V. and the company’s Environmental, Social, and Governance (ESG) report. Throughout 2023, Cabka remained steadfast in its commitment to sustainability, achieving significant milestones, which underscore its leadership in the circularity movement within the Reusable Transport Packaging (RTP) industry. Cabka’s dedication to sustainability is exemplified by its remarkable achievement of 89% of raw material originating in plastic material recovery. This means that the company was able to increase the already high proportion of recycled materials intake by a further 3% compared to the previous year. This accomplishment significantly surpasses the European average of 14% recycled plastics and the target to get to 33% by 2030. 1, highlighting Cabka's pioneering role in reshaping industry standards. Notably, all products are 100% reusable, with clauses for take- back and recycling, further supporting the circularity ethos. In recognition of its commitment to sustainability, Cabka attained “gold” status in the prestigious EcoVadis assessment for the first time in 2023. This underlines Cabka’s exceptional performance across various sustainability metrics, elevating the company to be within the top 6% of rated organizations, a leap from the top 25% in just one year. Moreover, Cabka’s engagement with the Carbon Disclosure Program (CDP) underscores its dedication to addressing climate impacts. With a commendable B score, Cabka aligns itself with the overall performance of European companies, demonstrating its proactive stance in combating climate change. Cabka's performance surpasses the sector’s average, being an average grade C across the plastic products manufacturing industry. Cabka’s commitment to low-carbon circular economy principles is evident in its product designs and material management strategies. By utilizing recycled materials and designing products for reuse and recyclability, Cabka minimizes waste and resource consumption throughout its product lifecycle. With its business model, Cabka avoids more greenhouse gases than those generated by its overall company carbon footprint of 226,000 tons CO 2 e (Scope 1, 2, and 3). In 2023, Cabka took in 140,000 tons of plastic waste. Inhouse waste processing and predominantly recycled material input therefore led to 309,000 tons CO 2 being avoided in 2023 2.
DIEFFENBACHER mourns the death of Alfred H. Schenkmann

Schenkmann & Piel co-founder passed away at the age of 87 Alfred H. Schenkmann, founding partner and co-eponym of Schenkmann & Piel Verfahrenstechnik GmbH & Co. KG, passed away on April 12, 2024, at the age of 87. From its foundation in 1977 until his retirement on November 1, 2001, Schenkmann was Managing Director of Schenkmann & Piel Verfahrenstechnik in Leverkusen for 24 years. Even after the takeover by DIEFFENBACHER in 2003, he remained closely associated with the company and was always available to provide wise counsel. Schenkmann traveled to more than 80 countries during his career, making connections in the global wood-based panels industry and becoming an expert respected worldwide. In 1997, he was inducted into the Wood Composites Hall of Fame at Washington State University, an honor he shared with industry giants and wood-based panel pioneers such as Wilhelm Klauditz and Fred Fahrni. “In addition to his entrepreneurial and inventive spirit, Alfred Schenkmann was particularly valued by his employees for his knowledge and helpfulness as well as his tireless commitment to the company,” recalled Wolfgang Allerödder, Head of the Environmental Technology and Gluing Product Group at DIEFFENBACHER in Leverkusen, who worked under Alfred Schenkmann as a student. “To this day, I still benefit from the contacts I made through him,” Allerödder said. “Alfred Schenkmann was a cheerful Rhineland character and instantly popular with everyone. Wherever he went, he was always held in the highest esteem,” reminisced his long-time companion and former DIEFFENBACHER CEO Wolf-Gerd Dieffenbacher. “In Alfred H. Schenkmann, DIEFFENBACHER has lost a universally respected advisor, and the global wood-based panels industry has lost one of its pioneers. Our thoughts are with his family and friends, to whom I would like to express our deepest sympathy on behalf of the entire company.”
Revolutionizing industrial torque reaction solutions with carbon fiber
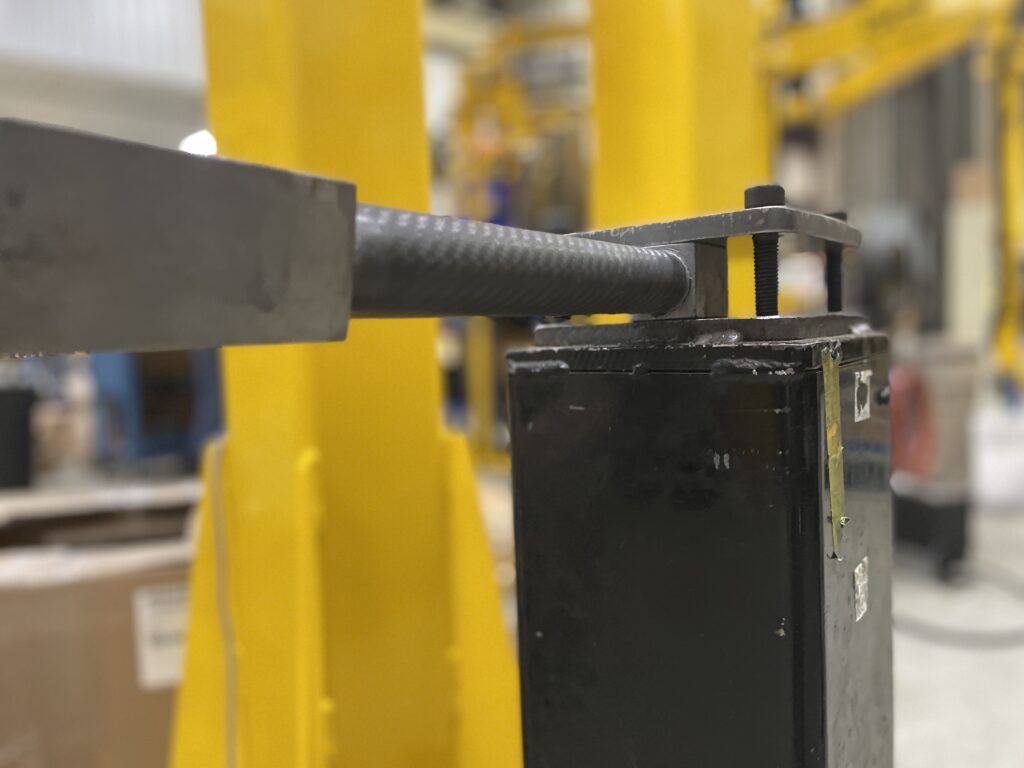
GCI Engineered Solutions is thrilled to unveil the groundbreaking carbon fiber torque tube, a pioneering advancement in industrial torque reaction technology. This innovative torque tube, crafted from carbon fiber, is the first of its kind capable of reacting both vertical and horizontal torque forces. Traditionally, torque tubes, also known as torque reaction tubes, have been vital components in manufacturing, offering versatility and coverage with overhead bridge cranes. However, the industry has long sought more efficient solutions to mitigate torque forces and alleviate operator fatigue. Conventional steel shafts, while functional, often pose ergonomic issues due to their weight, leading to discomfort and decreased productivity. Responding to these challenges, GCI has developed the carbon fiber torque tube, a lightweight composite solution weighing approximately one-third of its steel counterparts. This breakthrough material promises enhanced ergonomics and ease of use for operators. Research, design, and testing GCI’s engineering team spent countless hours testing different versions of carbon fiber tubes for torque reaction. With every limitation revealed from a test, an improvement was made to the new design. Eventually, a version was created that withstood all of the exploratory tests. To prepare the new carbon fiber torque for the market, extensive testing has been conducted to ensure performance and durability. Two key tests were undertaken: a durability test to examine fatigue and a max load test to determine the torque tube’s breaking point. The durability test involved running the tube through 100,000 vertical torque cycles, 50,000 horizontal torque cycles, and 50,000 cycles with a 30 lbs offset load. For the max load test, the applied load of a torque tool was continuously increased until the point of failure was reached, providing valuable insights into the torque tube’s true maximum capacity. How can you use a carbon fiber torque tube? The carbon fiber torque tube is the ideal solution for low torque application and applications that require torque tools to reach broad areas. Its compatibility with overhead bridge and jib crane systems allows for seamless integration and movement within work cells. The carbon fiber torque tube outshines traditional options and helps manufacturers improve the safety and ergonomics of repetitive processes. We are excited to be at the forefront of this groundbreaking new torque reaction technology, and we can’t wait to see how it will be implemented into your assembly lines. At GCI Engineered Solutions, we always aim to do better for our clients and partners; this new product is no exception.
Chorus of diverse voices, railroads urge EPA denial of California Locomotive Authorization
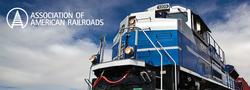
The Association of American Railroads (AAR) this week filed comments (EPA-HQ-2023-0574) with the U.S. Environmental Protection Agency (EPA), calling on the agency to reject an authorization request from the California Air Resources Board (CARB) to implement a locomotive regulation that was finalized last year. The rule bans the operation of any locomotive that is 23 years or older from operating in California starting in 2030 — prematurely retiring viable locomotives that help make rail the most fuel-efficient way to move goods over land. Starting in 2030 for switch, industrial, and passenger locomotives — and 2035 for line haul locomotives — new locomotives can only operate in the state if they are “zero-emissions locomotives.” AAR argues the regulation is infeasible and will yield counterproductive environmental results while disrupting the interconnected nature of the national freight rail network. “Railroads continue to invest billions to reduce their environmental impact, a major reason why carriers contribute less than one percent of all U.S. greenhouse gas (GHG) emissions,” said Ian Jefferies, President and CEO of the Association of American Railroads. “Yet California insists on using unreasonable, flawed assumptions to support a rule that will not result in emissions reductions. AAR and its members present a clear and compelling set of facts to the EPA, and we are joined by a wide range of our customers and other critical stakeholders who underscore the myriad negative impacts associated with the rule. We urge the Biden administration to heed these calls and make the right choice, putting rail on a better and more logical path to continued emissions reductions.” AAR’s comments include these key arguments: Complying with the regulation’s timeline is impossible given the current state of research and development into zero emissions locomotive technology. Because of the interstate nature of railroad operations, California’s regulation amounts to a national rule. For critical reasons, including protection of the healthy and efficient flow of national commerce, regulation of the national rail network is a federal matter, and no single state should set policy for the entire nation. Both the Clean Air Act and the Interstate Commerce Commission Termination Act of 1995 bar California from taking this action. A review of the public comments currently available reflect that a wide range of industries, legislators and experts also oppose the authorization request: Organized labor, such as ironworkers, pipe trades, engineers and conductors documented the negative effect on jobs and the economy. A coalition of more than 25 national agricultural organizations and more than 50 state agricultural groups from across the country, representing all portions of production — from fertilizers to commodities — discussed the effect on rail service and getting goods to market. The U.S. Chamber of Commerce and more than 130 state and local chambers stressed economic harm. Additionally, 206 state-based business organizations signed a letter filed by the Illinois Manufacturers Association. A group of major U.S. industries, led by the National Association of Manufacturers and representing the gamut of the economy — trucking, retailers, builders, contractors, beer, wholesalers, food companies, warehousing, lumber, paper, wood, plastics, fuel providers, fuel stations and a range of energy sources — argued the rule would hurt millions of Americans. The Rail Customer Coalition (RCC), representing industries tied closely to the viability of reliable rail transportation, filed on behalf of roughly 75 national and state organizations. Industries represented included manufacturing, agricultural, and energy — including the cross-section of chemical companies responsible for U.S. energy dominance. The “Joint Associations” — some of the largest users of freight rail — including the Private Railcar Food and Beverage Association, American Forest and Paper Association, Consumer Brands Association, Freight Rail Customer Alliance, National Coal Transportation Association, National Industrial Transportation League, and Western Coal Traffic League —voiced grave concern. Leaders from states across the country, including Ohio, California, Utah, Kentucky, New York, Missouri, Minnesota, Arizona, Illinois, Mississippi, Florida, Wisconsin, Georgia, Michigan, Oklahoma, North Carolina, West Virginia, Oregon, New Jersey, Virginia, Tennessee, Nevada, Louisiana, Texas, Pennsylvania, Washington and Indiana, also weighed in. Downstream, county advocates — through representation in Washington, D.C. — argued that the regulation will divert freight to strained highway systems while running afoul of a more appropriate approach coordinated between federal, state and local governments. Individual subject matter experts at institutions such as the American Enterprise Institute, Center for Regulatory Freedom, George Washington University, Heritage Foundation and Reason Foundation offered analysis. While a large coalition of policy organizations filed collectively at the EPA. Environmental advocates at the American Conservation Coalition, C3 Solutions and ConservAmerica argued that the rule will have counterproductive results in terms of emissions reductions. At the same time, consumer advocates argued the rule would raise costs by picking winners and losers and fail to meet long-term consumer needs. And, industries such as defense, rail suppliers, fuel and petrochemical manufacturers, and biofuels outlined the negative effects to their critical sectors. Critically, policymakers have also weighed in. This includes a letter from U.S. Senators Pete Ricketts (R-NE), Shelley Moore Capito (R-WV), Joe Manchin (D-WV), John Boozman (R-AR), Mike Braun (R-IN), Kevin Cramer (R-ND), Joni Ernst (R-IA), Deb Fischer (R-NE), John Hoeven (R-ND), Cynthia Lummis (R-WY), Roger Marshall (R-KS), and Roger Wicker (R-MS). Most recently, the majority of the House Transportation & Infrastructure Committee asserted their authority in this area. Additionally, the U.S Small Business Administration Office of Advocacy emphasized the disproportionate harm the CARB rule would have on short line railroads, including the ability to put many out of business. “Taken together, the public record reflects wide-reaching opposition to this misguided California rule,” added Jefferies. “We look forward to future discussions with the EPA to reinforce our public comments.” The rule remains the subject of litigation in California. The EPA is not obligated to rule on the authorization request and is not bound by a deadline. Additional comments filed at the EPA should appear publicly in the future.
Millwood’s growth leads to expansion
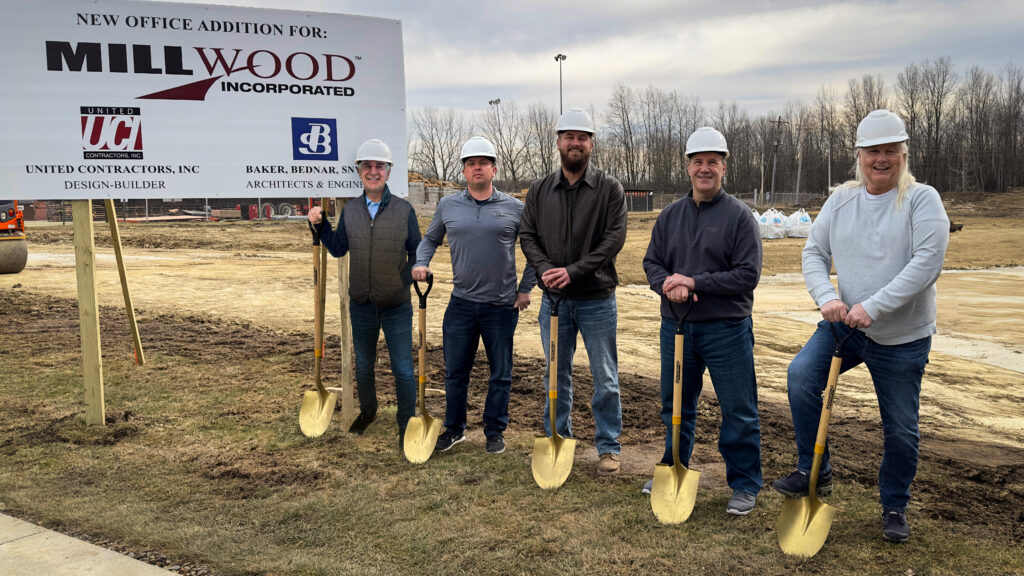
Includes 17,000 Square Foot Addition at Its Corporate Campus The past year has been another year of growth, achievement and fellowship for the Millwood family at our locations across the country. That growth trajectory includes expansions in Alabama, Texas and New Jersey and is being extended to the heart of our business at the corporate headquarters in Vienna, OH. Ground was recently broken on a 17,000-square-foot addition to the corporate office. “We are very grateful, and this is a fantastic opportunity for the company,” Millwood Chief Financial Officer Bruce Krarup said. “We appreciate the support provided by the Vienna township and the Trumbull county commissioners office as we developed the plans for this expansion.” Millwood has been headquartered in Trumbull County, OH for over 30 years. The announcement for this expansion came weeks after Millwood opened its newest location in nearby Lordstown, OH, also in Trumbull County, which added nearly 20 people to the Millwood family. Millwood leaders will continue to lean on God’s wisdom and guidance to explore other opportunities to grow in 2024 through our customers, suppliers, vendors and people. “God has His hand on this company, and it’s been very exciting to witness how He is working in and through us and our entire Millwood family across the United States,” Co-Presidents & Partners Chip Trebilcock and Steve Miller said in a joint statement. Growth & Expansion Barrington, NJ facility added in January 2023. Ellenboro, NC co-packer location added in May 2023. Huntsville, AL facility added in May 2023. Bridgeville, DE co-packer location added in September 2023. Lordstown, OH facility added in September 2023. New Kent, VA co-packer location added in February 2024. Millwood’s corporate office began a construction project in December for an additional building.
Episode 479: Insights into the 3PL Industry with Aaron Hodes
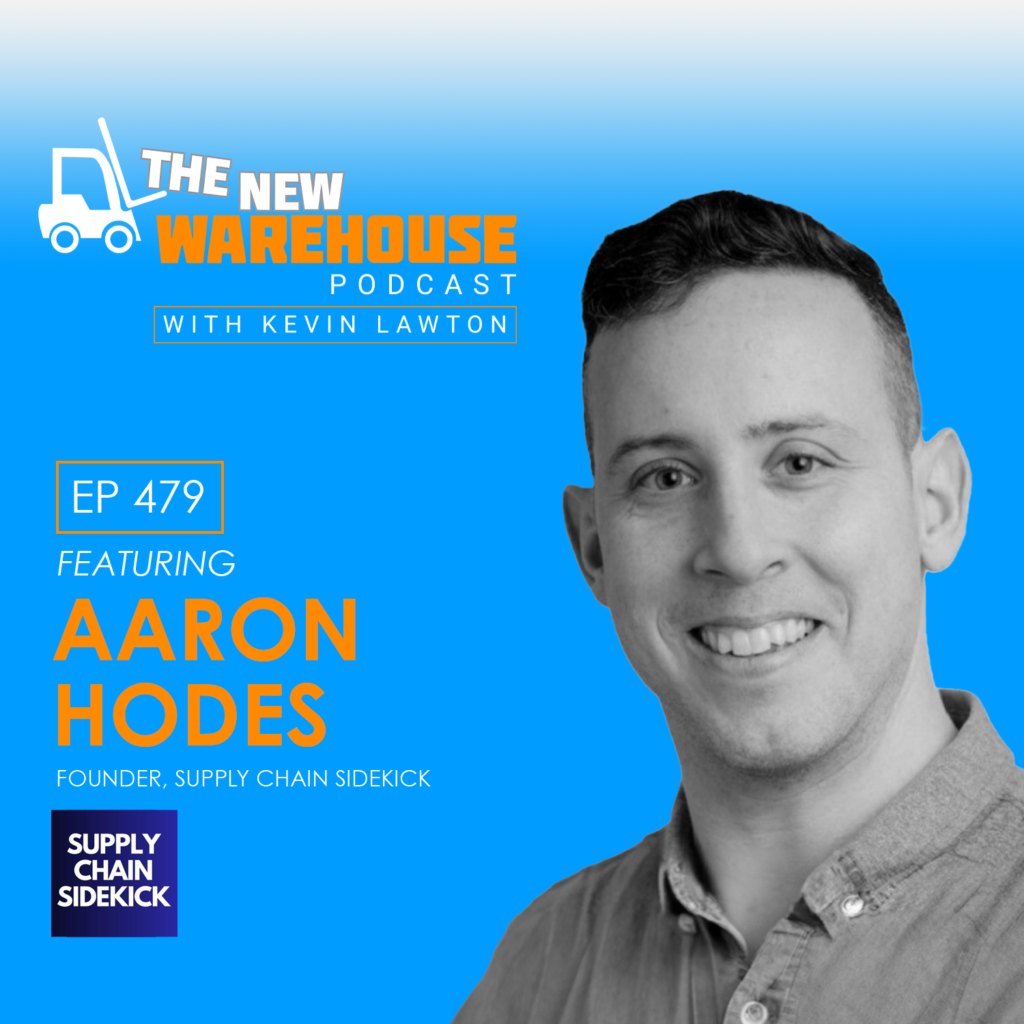
In this episode of the New Warehouse podcast, we’re thrilled to welcome back Aaron Hodes, who is now your Supply Chain Sidekick. With a rich history in the 3PL (Third-Party Logistics) industry, most notably at ShipBob, Aaron brings a wealth of knowledge and experience in partnering with e-commerce brands to optimize their logistics and fulfillment strategies. This episode dives deep into the complexities and challenges of the 3PL industry, offering invaluable insights and recommendations for brands looking to navigate this critical aspect of their operations. Finding the Right 3PL Fit Aaron believes, “There’s not a one-size-fits-all 3PL for any e-commerce brand.” This straightforward insight stresses the importance of matching a brand’s specific needs with a 3PL’s strengths. He advises brands to “really understand and get their own house in order” before picking a 3PL. Drawing from his time at ShipBob, Aaron has seen that every brand’s challenges are unique, making the right fit crucial. He suggests looking beyond cost to find a 3PL that aligns with your brand’s goals and can grow with you. This approach ensures not just efficiency but also customer satisfaction down the line. Overcoming Operational Misalignments As Aaron points out, one of the significant hurdles in the 3PL-brand partnership is operational alignment. He sheds light on common challenges brands face, such as miscommunication with 3PLs and inadequate preparation for fulfillment demands. Aaron emphasizes that the solution lies in thorough vetting, transparent communication, and strategic planning between brands and their 3PL partners. He advocates for a collaborative approach to ensure that both parties’ expectations and capabilities are aligned, thereby fostering a more productive and harmonious relationship. Looking Ahead at the 3PL Industry Looking ahead, Aaron shares his vision for the future of 3PL partnerships, focusing on integrating AI and machine learning technologies to enhance logistics operations. This vision for the future indicates a shift towards more agile, efficient, and data-driven 3PL services capable of adapting to the fast-paced changes in the e-commerce landscape. Key Takeaways on the 3PL Industry The importance of personalized 3PL solutions tailored to each brand’s unique needs. The need for operational alignment and strategic communication between brands and the 3PL industry. The future of 3PL partnerships lies in leveraging AI and machine learning for enhanced operational efficiency and intelligence. The New Warehouse Podcast Episode 479: Insights into the 3PL Industry with Aaron Hodes
NRF statement on the final overtime rule
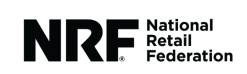
The National Retail Federation has issued the following statement from Executive Vice President of Government Relations David French after the Department of Labor’s (DOL) final overtime rule was released. Originally proposed in Sept. 2023, the rule will increase — in two steps — the minimum annual salary threshold that determines overtime pay eligibility under the Fair Labor Standards Act. “NRF acknowledges the steps that DOL took to phase in the full impact of the new rules in response to employer concerns. The delay in full implementation of the new higher threshold, for example, will enable retailers to prepare for the full impact of the rule more thoroughly. We remain concerned, however, that the new rules curtail retailers’ ability to offer the most flexible, generous, and tailored benefits packages to lower-level exempt employees across the industry. “We are also concerned that the Department has not provided adequate time for retailers to implement changes to the first phase of the rule, which will increase the minimum salary threshold from $35,568 to $43,888 by July 1, 2024. We urge the Department to allow until at least Sept. 1, 2024, to implement this change. “Even with the phased-in implementation timeline, the new rules will cause employers to reexamine compensation packages for millions of workers nationwide. Some workers may lose the status of a managerial position. Some may lose much-desired flexibility as to when, how, and where they work, including the ability to work from home. Some may lose the capability to travel on the employer’s behalf. Some may lose valuable educational and training experiences. “Finally, retailers remain concerned that the inclusion of future automatic increases exceeds the Department’s legal authority and oversteps longstanding Fair Labor Standards Act and Administrative Procedure Act principles.” In Nov. 2023, NRF submitted comments to DOL opposing its proposed rule on overtime regulation. Additionally, NRF commissioned Oxford Economics to analyze the economic effects if implemented, which found that the proposed rule could impact more than 7.2 million workers. As the leading authority and voice for retail, NRF will continue to advocate for workplace rules that promote workplace flexibility and economic growth.
Herc Holdings reports strong First Quarter 2024 and affirms 2024 full-year guidance
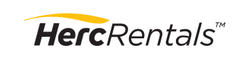
Record first quarter total revenues of $804 million, an increase of 9% Net income decreased 3% to $65 million, or $2.29 per diluted share Adjusted EBITDA of $339 million increased 10%; adjusted EBITDA margin increased to 42.2% Rental pricing increased 5.1% year-over-year Added 15 new locations through M&A and greenfield openings Corporate credit rating upgraded by S&P Global to BB Herc Holdings Inc. has reported financial results for the quarter ended March 31, 2024. “We are off to a strong start in 2024, achieving record first-quarter revenue and adjusted EBITDA margin as we continue to capitalize on key growth markets, like semiconductors, data centers, renewables, and public infrastructure, while also investing in our network scale through greenfields and acquisitions, and elevating our higher-return specialty product lines,” said Larry Silber, president and chief executive officer of Herc Rentals. “Once again, our teams are delivering for customers both in the local markets and at the national level, capitalizing on our broad geographic coverage and strong demand for our products and services. “We are making progress against each of our key 2024 priorities — enhancing our customer experience through our E3 business operating system, managing fleet efficiency and expenses with discipline, and scaling our network through greenfield locations and acquisitions in top 100 metropolitan markets,” said Silber. “Based on this strong performance and current line-of-sight to market trends, we are affirming our annual performance targets, excluding Cinelease, of 7-10% year-over-year equipment rental revenue growth and adjusted EBITDA of $1.55 billion to $1.60 billion for 2024.” 2024 First Quarter Financial Results Total revenues increased 9% to $804 million compared to $740 million in the prior-year period. The year-over-year increase of $64 million primarily related to an increase in equipment rental revenue of $65 million, reflecting positive pricing of 5.1% and increased volume of 8.0%, partially offset by unfavorable mix driven primarily by inflation. Sales of rental equipment decreased by $2 million during the period. Dollar utilization was 39.7% in the first quarter, flat over the prior-year period. Direct operating expenses were $307 million, or 42.7% of equipment rental revenue, compared to $281 million, or 43.0% in the prior-year period, reflecting better cost performance and fixed cost absorption on higher revenue despite increases related to additional headcount, facilities and maintenance expenses associated with strong rental activity and an expanding branch network. Depreciation of rental equipment increased 5% to $160 million due to higher year-over-year average fleet size. Non-rental depreciation and amortization increased 12% to $29 million primarily due to amortization of acquisition intangible assets. Selling, general and administrative expenses was $115 million, or 16.0% of equipment rental revenue, compared to $106 million, or 16.2% in the prior-year period due to continued focus on improving operating leverage while expanding revenues. Interest expense increased to $61 million compared with $48 million in the prior-year period due to increased borrowings on the ABL Credit Facility primarily to fund acquisition growth and invest in rental equipment and higher interest rates on floating-rate debt. Net income was $65 million compared to $67 million in the prior-year period. Adjusted net income decreased 3% to $67 million, or $2.36 per diluted share, compared to $69 million, or $2.35 per diluted share, in the prior-year period. The effective tax rate was 20% compared to 11% in the prior-year period. Adjusted EBITDA increased 10% to $339 million compared to $308 million in the prior-year period and adjusted EBITDA margin was 42.2% compared to 41.6% in the prior-year period. Continued focus on improving operating leverage while expanding revenues resulted in the improvement in margin year-over-year. Rental Fleet Net rental equipment capital expenditures were as follows (in millions): Three Months Ended March 31, 2024 2023 Rental equipment expenditures $ 181 $ 332 Proceeds from disposal of rental equipment (61) (49) Net rental equipment capital expenditures $ 120 $ 283 As of March 31, 2024, the Company’s total fleet was approximately $6.4 billion at OEC. Average fleet at OEC in the first quarter increased 10% compared to the prior-year period. Average fleet age was 47 months as of March 31, 2024 and 2023. Disciplined Capital Management The Company completed 4 acquisitions with a total of 11 locations and opened 4 new greenfield locations during the quarter. Net debt was $3.7 billion as of March 31, 2024, with net leverage of 2.5x which is unchanged from the same prior-year period. Cash and cash equivalents and unused commitments under the ABL Credit Facility contributed to $1.4 billion of liquidity as of March 31, 2024. The Company declared its quarterly dividend of $0.665, an increase of $0.0325 or 5%, paid to shareholders of record as of February 21, 2024 on March 7, 2024. Outlook The Company is affirming its full year 2024 equipment rental revenue growth, adjusted EBITDA, and gross and net rental capital expenditures guidance ranges presented below, excluding Cinelease studio entertainment and lighting and grip equipment rental business. The guidance range for the full year 2024 adjusted EBITDA reflects an increase of 6% to 9% compared to full year 2023 results, excluding Cinelease. The sale process for the Cinelease studio entertainment business is ongoing. Equipment rental revenue growth: 7% to 10% Adjusted EBITDA: $1.55 billion to $1.60 billion Net rental equipment capital expenditures after gross capex: $500 million to $700 million, after gross capex of $750 million to $1 billion As a provider in an industry where scale matters, the Company expects to continue to gain share by capturing an outsized position of the forecasted higher construction spending in 2024 by investing in its fleet, optimizing its existing fleet, capitalizing on strategic acquisitions and greenfield opportunities, and cross-selling a diversified product portfolio.
LEDtronics expands industrial controls with non-relampable panel indicator series
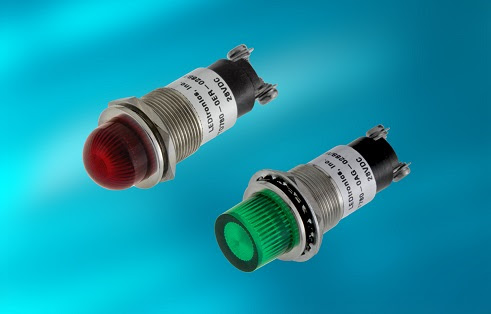
Continuing to expand its offerings of LED indicators for industrial, medical, and other controls and retrofit panel mount applications, LEDtronics® introduces new additions to its family of bolt-on, non-relampable and front-mounting panel indicators with screw terminals, featuring various color options and lens types. The new series of direct incandescent-replacement LED lights for mounting in holes of Ø0.681 inch (Ø17.3mm) diameter is an excellent choice for machine tool applications as well as heating, ventilation, and air conditioning control panels; medical equipment and signal and pilot lights, among many others. They feature slotted 0.05-inch tab terminals for panels no thicker than 0.180 inch (4.57mm) and a choice of cylindrical top hat or dome lens types. Offering energy savings with a much lower power consumption of only 0.5 watts or less, these indicator lamps provide sunlight-visible LED light in super yellow, super red or aqua-green colors, with a viewing angle of 10 to 80 degrees for the dome lens units, and 20 and 80 degrees for the flat, top-hat lens units, depending on lens color. They are rated for 28VDC input voltage, with the dome lens units providing illumination of 1 to 2.3 lumens and a luminous intensity ranging from 1.3 to 2.4 maximum candela, while the cylindrical flat-lens units offer 34 and 76 lumens and a luminous intensity of 44 and 93 maximum candelas. The series operates on an input current ranging between 0.08 to 0.017 amps. The PTx780-028B/WP Series comes in a nickel-coated brass housing, a slotted 0.05-inch, brass-coated terminal, a nylon base, and a polycarbonate lens. An integrated series resistor prevents short-circuiting, eliminating the necessity of special fuses. They mount to the front of a panel, accommodating panels up to 0.3 inch (7.62mm) in thickness. They are also lightweight — weighing only 1.0 ounce (28.35 grams). These durable LED lamps provide years of reliable performance with sustained color fidelity and energy efficiency, with an IP65 protection rating — they are water-tight and splash-proof for outdoor locations, operating in a wide temperature range of -30°C to +80°C (-22°F to 176°F). The new LEDtronics series PTD780-0xx-028B/WP (dome lens) and PTF780-0xx-028B/WP (cylindrical top-hat lens) panel front mounting, bolt-on indicator LED lamps come with an unconditional 3-year U.S. factory warranty, and are available through LEDtronics distributors. Other options, such as standard voltages, other LED colors, bulb styles or tabs are available for qualified volume orders.
Matrix Design Group hosts groundbreaking ceremony in Indiana
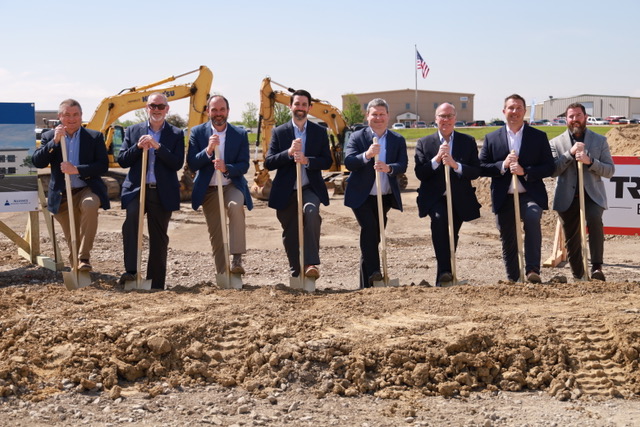
Matrix Design Group, LLC hosted a groundbreaking ceremony for its new headquarters in Newburgh, Indiana on April 18. It was attended by local community leaders and key stakeholders from Matrix Design Group and Alliance Resource Partners, L.P. The event signifies Matrix’s commitment to the local community and its vision for growth and innovation. The facilities will feature a new state-of-the-art product testing lab, expanded office space for growth, and a training center for employees, customers and distributors enabling increased education, support and development related to Matrix’s product lines. “Our new facilities will foster new opportunities. We are excited to expand our existing presence in Newburgh and, in the process, enable our growth internationally,” said Mark Watson, President of Matrix Design Group. “Since 2006, Matrix has distinguished itself as a leader in safety and productivity technological solutions. With this groundbreaking, we are building upon our company’s past success while growing to meet the needs of the customers and industries who benefit from our technologies.” With construction slated for completion by January 2025, Matrix is poised to expand its presence in the region and attract top technological talent from across the tristate area. Ultimately, the new headquarters will accommodate Matrix’s hiring of more than 150 additional employees over the next five years. “We are thrilled to be part of the Newburgh and greater Evansville community and look forward to further contributing to its economic growth and development,” said Joseph W. Craft III, Chairman, President and Chief Executive Officer of Matrix’s parent company, Alliance Resource Partners, L.P. (NASDAQ: ARLP). “We’re proud of the success of Matrix and their contributions to the safety and productivity of mining companies worldwide. As we look to the future, this investment in Matrix strengthens the company’s ability to attract and retain the highest-caliber tech and engineering minds in the region, while providing the organizational resources necessary for rapid growth and solving tomorrow’s challenges that businesses will face.”