Comau showcases the power of automation with new robots and new solutions at Automate 2024
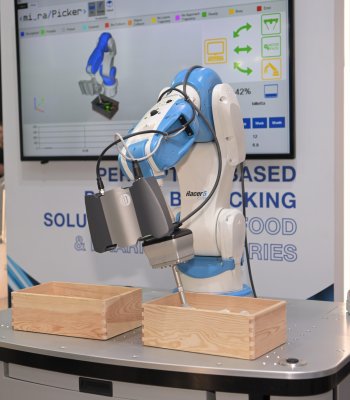
Comau will be exhibiting at Chicago’s McCormick Place from May 6-9, 2024 in Booth 4441 to present its digital-driven technology designed to accelerate deployment, increase quality, and ensure sustainable productivity inside and beyond the smart factory paradigm. Held every other year, Automate features the latest in cutting-edge robotics, vision, motion control, and related technologies. To represent our vision of the future, Comau’s theme for this year’s show is the “Power of Automation”. Visitors will experience the power of perception-guided picking systems, vision-backed handling solutions, advanced arc welding systems, and wearable robotics that help increase operator well-being during heavy and repetitive tasks. All of these solutions address the increasing shortage of skilled labor and the continued growth of automation, which is expected to exceed a growth of +10% CAGR 2022-2030*. In addition to these technologies, Comau will unveil a new generation of compact robots that specifically address the diverse needs found within automotive and non-automotive applications. To help companies save time, energy, and resources, improving the quality of the production processes, Comau’s fully-automated piece picking and bin-picking solutions can be applied across multiple industries including warehousing logistics. The company’s upper and lower body exoskeletons will also be on display and are designed to assist the wearer during lifting, bending, and repetitive tasks to offer both muscular relief and reduced perceived effort. This is a concrete example of Comau’s steadfast commitment to workers’ well-being and to develop technologies that help companies achieve their sustainability goals. Come see how Comau is applying its 50+ years of experience in automotive – one of the most complex realities in terms of processes, cycle times, flexibility requirements, and the highest technology rate – to drive the power of automation within new markets and application areas that until now, have been largely inaccessible with traditional robotic technologies. Stay tuned and we look forward to meeting you at our booth 4441 in Chicago!
Toyota Material Handling North America appoints Taggart as CFO
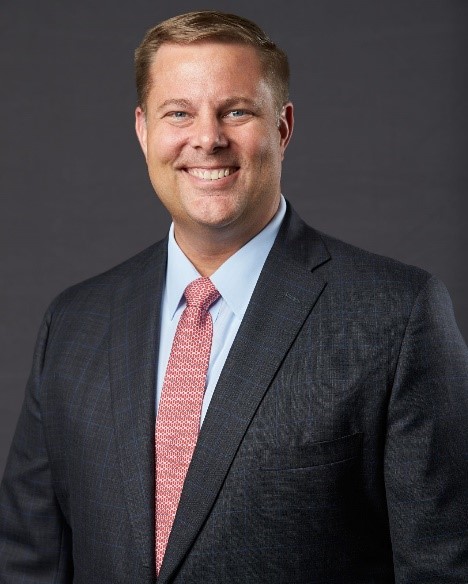
Mark Taggart assumed his new role as Chief Financial Officer of Toyota Material Handling North America on April 1. Taggart will continue as Chairman of Toyota Industries Commercial Finance. Mark Taggart, former Toyota Industries Commercial Finance (TICF) President & CEO, assumed the role of Chief Financial Officer (CFO) for Toyota Material Handling North America (TMHNA) on April 1. Taggart will continue his role as Chairman of Toyota Industries Global Commercial Finance, overseeing TICF. As TMHNA CFO, Taggart will shape the financial strategy of TMHNA’s major group companies – Toyota Material Handling and The Raymond Corporation – from his office in Coppell, Texas. Taggart plans to introduce efficient solutions to propel the company’s fiscal responsibility and success, aligning with Toyota’s culture of kaizen – or continuous improvement. “I am honored to step into this new role and look forward to further aligning the financial goals of TMHNA and all Toyota group companies,” Taggart said. “Through the consolidated resources of TMHNA, our goal is to always put our customers first with the best experience in each phase of the ownership lifecycle. I am excited about the future and look forward to continuing to work together toward our vision of being the most sought-after material handling, logistics, and financial services partner in the industry.” Taggart joined the Toyota group of companies in 1996 and has a proven track record of consistent profitable sales growth, along with a demonstrated commitment to providing outstanding service to dealers and customers. Taggart’s strategic vision has shaped the company’s global footprint with significant milestones. His ability to drive impactful initiatives was displayed in 2005 when he helped drive the establishment of Toyota Financial Savings Bank (TFSB). During an assignment in Japan in 2012, Taggart assumed key leadership roles at Toyota Financial Services Corporation (TFSC), culminating in his promotion to Vice President. In this position, Taggart oversaw sales finance companies in the Asia-Pacific Region. Upon returning to the United States, his oversight was integral in founding Toyota Financial Services International Corporation, TFSC’s second global headquarters. Prior to his most recent role at TICF, Taggart served as President and CEO of TFSB. These achievements not only underscore Taggart’s capabilities but position him for success as TMHNA’s CFO. John Crews, TICF General Counsel, Secretary and Chief Compliance Officer, will succeed Taggart as TICF President. “John is a strong leader that is committed to strengthening the great culture of our organization – a culture centered around our purpose, values, mission, and vision,” Taggart said. “John cares deeply about the associates at TICF, is an exemplary role model of our core values, and skillfully balances what is best for our associates, customers, dealers, and partners in all his decision-making.” Crews’ leadership ability has left an enduring and positive impact on TICF’s operations since he joined TICF in 2020. His legal and compliance expertise, combined with strategic insight, has proven crucial in solidifying TICF’s foundation while setting the course for sustained success and future growth.
U.S. Rail Report for the Week Ending April 6, 2024
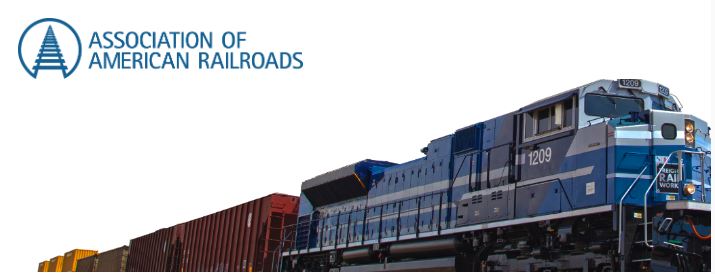
The Association of American Railroads (AAR) has reported U.S. rail traffic for the week ending April 6, 2024. For this week, total U.S. weekly rail traffic was 450,142 carloads and intermodal units, up 1.6 percent compared with the same week last year. Total carloads for the week ending April 6 were 209,142 carloads, down 4.5 percent compared with the same week in 2023, while U.S. weekly intermodal volume was 241,000 containers and trailers, up 7.6 percent compared to 2023. Six of the 10 carload commodity groups posted an increase compared with the same week in 2023. They included grain, up 3,221 carloads, to 22,000; motor vehicles and parts, up 1,983 carloads, to 16,315; and chemicals, up 1,574 carloads, to 31,907. Commodity groups that posted decreases compared with the same week in 2023 included coal, down 15,107 carloads, to 46,688; nonmetallic minerals, down 2,078 carloads, to 29,540; and metallic ores and metals, down 848 carloads, to 19,403. For the first 14 weeks of 2024, U.S. railroads reported a cumulative volume of 2,982,969 carloads, down 4.2 percent from the same point last year; and 3,509,647 intermodal units, up 9.0 percent from last year. Total combined U.S. traffic for the first 14 weeks of 2024 was 6,492,616 carloads and intermodal units, an increase of 2.5 percent compared to last year. North American rail volume for the week ending April 6, 2024, on 10 reporting U.S., Canadian and Mexican railroads totaled 321,182 carloads, down 1.3 percent compared with the same week last year, and 326,417 intermodal units, up 11.2 percent compared with last year. Total combined weekly rail traffic in North America was 647,599 carloads and intermodal units, up 4.6 percent. North American rail volume for the first 14 weeks of 2024 was 9,127,511 carloads and intermodal units, up 2.2 percent compared with 2023. Canadian railroads reported 95,326 carloads for the week, up 5.5 percent, and 72,636 intermodal units, up 12.7 percent compared with the same week in 2023. For the first 14 weeks of 2024, Canadian railroads reported a cumulative rail traffic volume of 2,218,935 carloads, containers and trailers, down 0.1 percent. Mexican railroads reported 16,714 carloads for the week, up 3.6 percent compared with the same week last year, and 12,781 intermodal units, up 146.5 percent. Cumulative volume on Mexican railroads for the first 14 weeks of 2024 was 415,960 carloads and intermodal containers and trailers, up 11.7 percent from the same point last year. View the report here.
TAPPI & AICC announce attendee registration opening for SuperCorrExpo® 2024
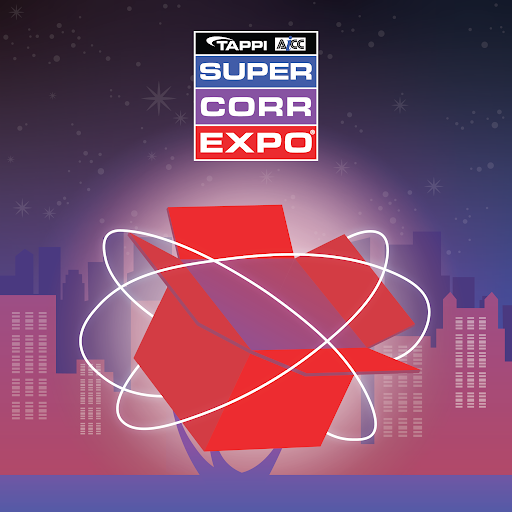
Time Tested, Future Forward: Celebrating Corrugated’s Storied Past and Bright Future The organizers of SuperCorrExpo® has announced that registration for SuperCorrExpo® 2024, the largest event in the corrugated packaging industry, is now open. The much-anticipated event will take place September 8-12 at the Orange County Convention Center in Orlando, Florida. Hosted jointly by TAPPI and AICC, SuperCorrExpo® 2024 is the leading industry event that draws professionals, suppliers, and innovators from across the globe. Participants can look forward to a dynamic and immersive experience, exploring the latest trends, cutting-edge technologies, and insights from key industry leaders. The theme of SuperCorrExpo® 2024 is Time Tested, Future Forward. TAPPI and AICC invite attendees to join the generations of forward-thinking professionals and companies that have stood the test of time with the newest technology, smartest thinking and freshest insights. Highlights of SuperCorrExpo® 2024 include: Exhibition Hall: Featuring more than 300 exhibitors showcasing working machinery, the latest technologies and solutions tailored for the corrugated packaging sector. Conference Sessions: Led by industry experts, offering deep insights into market trends, sustainability challenges, innovations and the future of corrugated packaging. Networking Opportunities: Interact and form valuable connections with professionals from across the industry spectrum. Innovative Showcases: Experience first-hand demonstrations of the latest industry technologies and solutions. Workshops and Tutorials: Designed to provide hands-on experience and enhance skills in various aspects of corrugated packaging. Box Manufacturing Olympics: Celebrating the best in innovation, sustainability, and design within the corrugated industry. “SuperCorrExpo® has always served as a melting pot for corrugated industry professionals. This year, we promise the biggest, most comprehensive and most innovative event yet,” said Larry Montague, President and CEO at TAPPI. “Our goal for the event is to facilitate knowledge exchange, foster partnerships and drive the industry forward.” Participants are encouraged to register early to benefit from early bird discounts and ensure access to preferred sessions and workshops.
Process Safety Technical Consultant Ehab Tayel joins the Hargrove Controls & Automation Process Safety Team
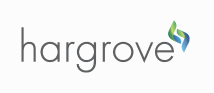
Ehab Tayel, TÜV (Rheinland), FSE, CFSE, brings nearly two decades of process safety experience and a passion for the safety lifecycle to Hargrove Controls & Automation’s process safety team in the Pasadena, TX office. Hargrove Controls & Automation has announced that Ehab Tayel joins their team as a Process Safety Technical Consultant. In his new role, Tayel will enhance the capabilities of Hargrove Controls & Automation’s process safety team and cultivate new and existing client relationships in the Houston Ship Channel area. “We are excited to welcome Ehab to the process safety team at Hargrove C&A,” said Chet S. Barton, P.E., FS Exp (TÜV Rheinland), Process Safety Industry Leader at Hargrove Controls & Automation. “As we collaborate with clients across various industries to optimize their process safety landscapes, Ehab’s deep understanding of risk assessment, hazard analysis, and safety management systems will be invaluable in our continuous pursuit of operational excellence and incident prevention for our clients.” Tayel received a Bachelor’s degree in Electrical Engineering from Al-Azhar University in Cairo, Egypt before beginning his career as an Implementation Engineer. Prior to joining Hargrove Controls & Automation, Tayel worked as a senior functional safety system engineer for a leading automation and engineering firm serving the oil & gas, pipeline, renewables, chemical, and biopharmaceutical industries. For his career, Tayel has continuously pursued opportunities to stay at the forefront of industry trends and best practices and to expand his knowledge of process safety topics including independent protection layers (IPL), safety integrity level (SIL) calculations, and fault tree analysis. He achieved the TÜV FS Eng certificate, the Certified Functional Safety Expert (CFSE) certification from Exida, and the ISA84 SFS certification from the International Society of Automation (ISA). Tayel has also progressively honed his skills through the completion of SIL2, SIL3, and SIL4 projects. He has cultivated a strong foundation in developing safety requirement specification (SRS) packages for corporate safety lifecycle documentation in alignment with ISA/IEC standards. “What excites me most about working at Hargrove is the opportunity to collaborate with a team of highly skilled professionals who share my passion for process safety. I’m eager to contribute my expertise and learn from others, fostering an environment of innovation and growth,” said Tayel. “Additionally, I’m looking forward to tackling challenging projects and seeing the impact of our collective efforts as we deliver process safety solutions for clients.” Hargrove Controls & Automation serves as a trusted partner for customized safety solutions to create a safe, secure, and compliant facility for their clients. Their certified Functional Safety Engineers have developed a meticulous methodology for process safety, adhering to IEC 61508 / 61511, ANSI/ISA-61511-2018, and the entire Safety Life-cycle.
PLASTICS Industry Association releases analysis: March jobs report
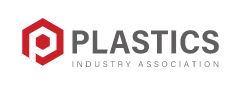
The Plastics Industry Association (PLASTICS) has released an official analysis of the March jobs report and its impact on the plastics industry, authored by PLASTICS Chief Economist, Dr. Perc Pineda. Dr. Pineda writes, “The U.S. labor market outperformed expectations in March, adding 303K nonfarm payrolls, demonstrating resilience despite a high-interest-rate environment. The unemployment rate remained low at 3.8%, with certain sectors reporting even lower rates. For instance, the manufacturing industry saw a 3.0% unemployment rate, while the plastics and rubber products manufacturing sector reported a mere 2.1% unemployment rate. It is worth noting, however, that despite these low unemployment rates, the plastics and rubber products manufacturing sector experienced a decrease in payrolls of 1.1K during the same period.” Read the full analysis on the PLASTICS blog page. The Plastics Industry Association (PLASTICS) is the only organization that supports the entire plastics supply chain, including Equipment Suppliers, Material Suppliers, Processors, and Recyclers, representing over one million workers in our $548 billion U.S. industry. PLASTICS advances the priorities of our members who are dedicated to investing in technologies that improve capabilities and advances in recycling and sustainability and providing essential products that allow for the protection and safety of our lives. Since 1937, PLASTICS has been working to make its members, and the seventh largest U.S. manufacturing industry, more globally competitive while supporting circularity through educational initiatives, industry-leading insights and events, convening opportunities and policy advocacy, including the largest plastics trade show in the Americas, NPE2024: The Plastics Show.
Multi-Conveyor sponsors Winneconne Robotics Club
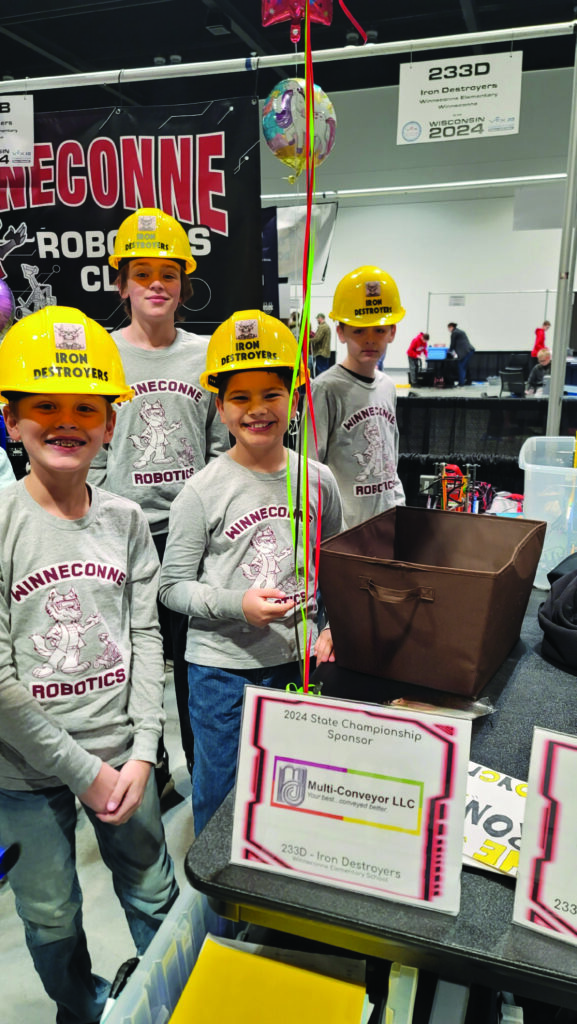
… 4 th and 5 th graders win big! CONGRATULATIONS to the Winneconne Robotics Club’s Cody Skadahl (grade 5), Jory Bastian (grade 5), Ryker Morden (grade 4), and Sullivan McCabe (grade 4), who earned two trophies at two separate tournaments this year, the Energy Award and The Innovate Award (State Qualifier). The robotics team participated in three (3) tournaments before qualifying for the state tournament in Green Bay, WI. Multi-Conveyor was proud to sponsor Team 233D Iron Destroyers for the State Tournament this year. Multi-Conveyor's own Jim Morden, mechanical engineer, had a great time coaching as the kids learned about designing, programming, documentation and testing their robot. Job well done!
Georgia Logistics Summit officials cancel the 2024 Summit
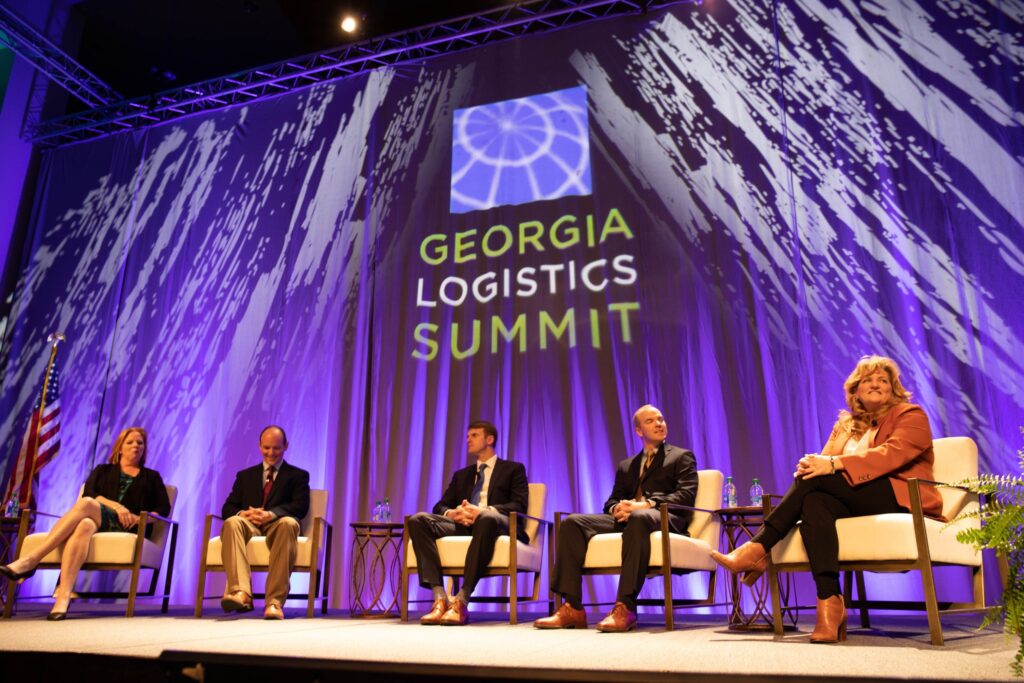
Officials who produce the annual Georgia Logistics Summit announced that the 2024 Summit in Savannah, GA on May 16th has been canceled. A press release to Material Handling Wholesaler said, “As you may know, our search for an alternate date and venue for the 2024 Georgia Logistics Summit was cost-prohibitive. As such, we made the very difficult decision to cancel the Summit for 2024. While disappointing for us too, we are pleased to announce the 2025 Georgia Logistics Summit will be held on April 23, 2025, in Atlanta, Georgia. Officials said more details will be shared in the months ahead, and encourage everyone to mark their calendar now. To learn more about the 2025 Georgia Logistics Summit, click here.
Alimerka leverages Cimcorp Automation to enhance supply chain efficiency and sustainability
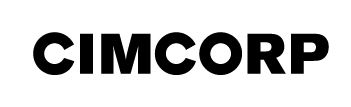
By optimizing storage and distribution processes, the Spanish supermarket chain has improved productivity, waste reduction, customer satisfaction, and employee safety Cimcorp has partnered with Spanish supermarket chain Alimerka to automate fresh food distribution processes. By integrating solutions from Cimcorp in its warehousing operations, Alimerka has reduced packaging material usage and enhanced distribution efficiency, making its supply chain more agile and sustainable. The partnership has also helped Alimerka ensure customer satisfaction with high-quality fresh products and protect employees through occupational safety improvements. Alimerka operates 173 supermarket stores across Northwest Spain, providing food and groceries to over 150,000 families across its locations. With future growth in mind, Alimerka selected Cimcorp for its ability to enable sustainable growth, optimize production processes, and improve ergonomics. Cimcorp has provided Alimerka with a solution that not only meets its current needs but also allows the company to grow and adapt to future challenges. “When considering the possibility of improving our logistics, especially in the fruit warehouse, we sought suppliers offering proven solutions in our sector. That’s when we came across Cimcorp, a company that had already implemented successful solutions in similar enterprises,” said Juan Carlos Suárez Fueyo, Logistics Director at Alimerka. “The partnership significantly changed our way of working, moving from nearly 100% manual preparation to highly automated preparation”. Supply chain sustainability Beyond improving operational efficiency, Alimerka sought to further its commitment to environmental conservation and waste reduction. The partnership with Cimcorp has contributed to this goal by reducing cardboard packaging usage and minimizing transportation times. “Sustainability is one of our strongest values,” said Iván Pravia, Head of Technical Office at Alimerka.”We work every day to improve our processes to be more sustainable and to transmit that commitment to our customers.” Quality and customer satisfaction In grocery retail, logistical efficiency translates to enhanced customer satisfaction. While end consumers are not always aware of the work behind the scenes, improvements to distribution operations are reflected in the quality and freshness of the products they find on Alimerka’s shelves. “The end customer is not always aware of what companies do, but when they see fresh and well-organized products, they know they are in a place where quality matters,” said Pravia. Ergonomics and workplace safety Furthermore, Alimerka and its employees now benefit from improved ergonomics and occupational safety. Cimcorp’s solution has provided greater order and uniformity in deliveries, resulting in improvements in the health of both store and warehouse workers, with a reduction in the number of accidents. Moving forward, Alimerka’s investments in automation will be essential to remaining a key player in the grocery retail market. Alimerka will continue to work with Cimcorp to improve warehousing operations with additional innovative solutions.
Pratt introduces its super lightweight 412 container Chassis
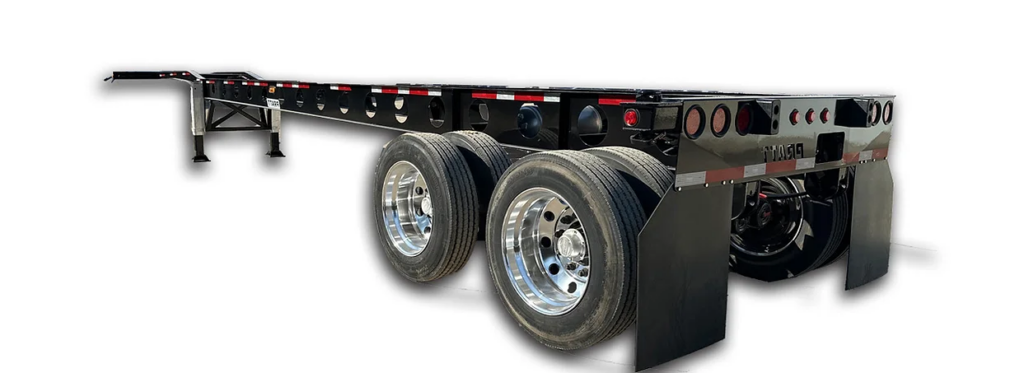
Pratt’s Super Lightweight 412 boasts a gross payload carrying capacity of 66,000 pounds, but weighs a mere 4,550 pounds unladen. Pratt Industries unveiled its Super Lightweight 412 (GSL 412) today. The newest in a long line of innovative intermodal chassis, the GSL 412 is being introduced in commemoration of the company’s 50th anniversary. “The GSL 412 represents Pratt’s renewed commitment to our customers and their needs, a core value that extends back to the company’s founder 50 years ago,” said Joel Schubach, chief operating officer for Pratt and one of the company’s owners. “The new GSL 412 embodies our customer commitment by addressing their needs to maximize load capacity and reduce fuel consumption — all in a robust and highly functional chassis design that will stand the test of time.” Over the previous five decades, Pratt has diversified into tank & container chassis; truss & modular home trailers; gas & energy trailers; heavy haul, lowboy and gooseneck trailers; EZ ramp utility trailers; flatbed & platform trailers; log & pole trailers; and trailer refurbishment. However, the company’s legacy leadership position in the chassis sector remains a top priority. The GSL 412 is 700 pounds lighter than previous models and has been engineered to be remarkably strong for its 4,550-pound weight profile. The new GSL 412 maintains the same structural integrity as preceding generations of Pratt chassis, and end users can further reduce the new chassis’ weight to 4,450 pounds, saving another 100 pounds by switching from standard dual tires to super singles. “End users can feel confident that they are buying the most advanced, lightweight intermodal chassis out there, and that we will continue to support that chassis for another 50 years,” said Garrett Musick, chief sales officer for Pratt, and another one of the company’s owners. “That’s an important point, because we still have some of our original chassis in the field, and recently received a request for replacement parts for one of our 1978 models.” Schubach and Musick both agree that Bob Pratt, the company’s founder, would be exceptionally proud of the new Gooseneck Super Lightweight 412. Both also concur that the new chassis renews the company’s dedication to its 1974 intermodal roots. “The GSL 412 will allow users to maximize intermodal payload capacity when laden and to save on fuel costs when not,” noted both Schubach and Musick. The GSL 412 is also designed to include best-in-class components that will please end users and enhance trailer functionality. The trailers feature aluminum landing gear, large-diameter axles, sealed wiring harnesses and LED lighting. To underscore its commitment to customer satisfaction and support, the company also recently launched it enterprise resource planning (ERP) system, which will help the organization to better track trailer orders by customer, type and industry. The ERP system enables Pratt to immediately access customer data and to answer questions quickly and accurately on order lead times and delivery schedules. It also helps the company successfully manage urgent orders that might otherwise negatively impact production burden rates. More than 95 percent of the new GSL 412 is made in the U.S., and the company owners agree that they are committed to the reshoring movement currently sweeping American manufacturing. “This is a strategic business decision that is focused on enhancing economic stability and growth here at home, and to revive domestic industry as a whole,” they said. “In its first 50 years, Pratt has seen plenty of economic cycles, but we know keeping things a bit closer to home will improve quality, reduce financial exposure and enhance supply chain resiliency.”
OTR’s REAPER Tire designed for zero-turn mowers and garden tractors
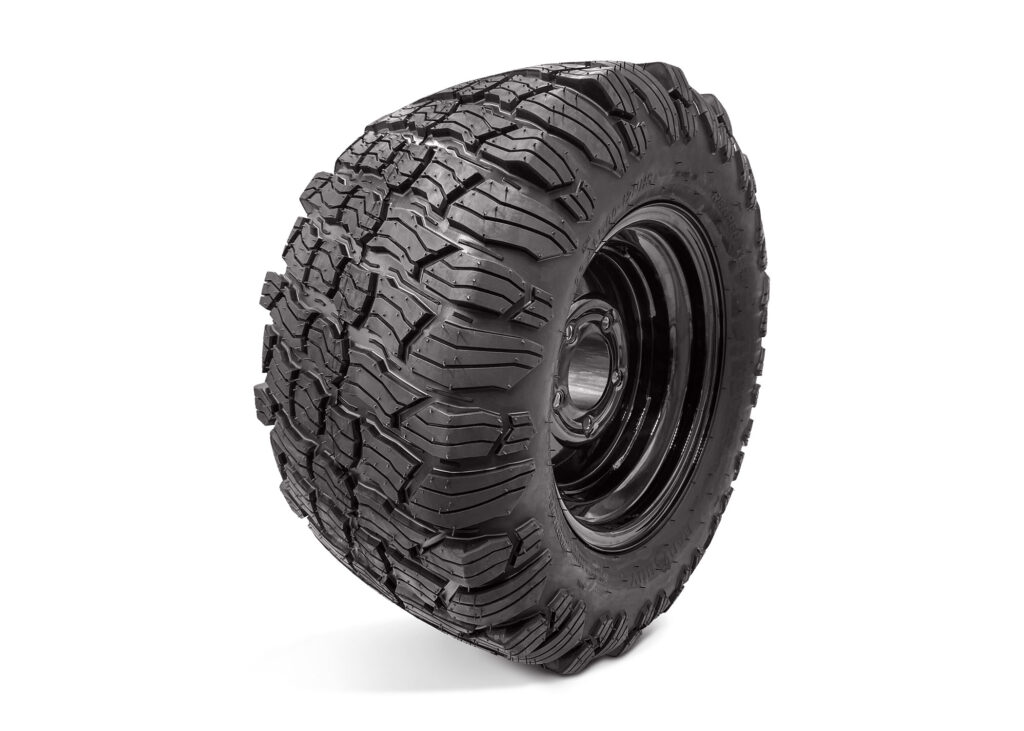
OTR Engineered Solutions (OTR) is offering its REAPER tire for multiple brands of zero-turn mowers and garden tractors. This tire combines a turf-specific design that yields superior traction, stability, and control with aggressive styling that appeals to end customers. The REAPER tire features a wider footprint to maintain surface contact that enhances stability and steering responsiveness as well. Additionally, a wrap-over grip edge enhances traction when driving on uneven terrain. This feature, combined with OTR’s unique tread design, delivers eye-catching styling for added value. The proprietary all-season rubber compound used to make the REAPER tire optimizes performance in both wet and dry conditions. It also helps create softer sidewalls for a smooth ride. The REAPER tire is sold as an assembly, including both the tire and wheel, for easy bolt-on installation. It is available in multiple sizes to fit a variety of vehicles. Brian Walter, Vice President-OEM Sales, said, “The REAPER is a tire OTR’s formerly named Hoosier Wheel unit originated as a highly engineered turf tire that delivers more value for the money. It not only performs exceptionally well in virtually any turf environment—smooth or rough—but it looks good, too. We’re confident this tire will make our OEM customers’ equipment more effective and appealing.” OTR Engineered Solutions is a market-leading global enterprise specializing in off-the-road solutions for original equipment manufacturers (OEMs) and aftermarkets. Known for market-leading tire and wheel innovations, OTR also provides value-added services such as warehousing, tire mounting, and sequencing. The firm has long established strategic partnerships with OEMs covering Construction, Lawn & Garden, Powersports, Agriculture, Forestry, Mining, Material Handling, and Specialty Vehicle markets. OTR’s infrastructure comprises 31 facilities and warehouse locations throughout the U.S., Canada, Europe, and Asia, serving customers globally.
February Manufacturing Technology orders up 2.1% over January; Contract Machine Shops decreased orders, while Aerospace increased
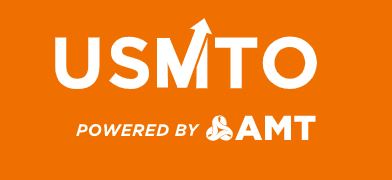
Orders of manufacturing technology, measured by the U.S. Manufacturing Technology Orders Report published by AMT – The Association For Manufacturing Technology, totaled $343.3 million in February 2024. Orders of manufacturing technology, measured by the U.S. Manufacturing Technology Orders Report published by AMT – The Association For Manufacturing Technology, totaled $343.3 million in February 2024. This was a 2.1% increase from January 2024 but a 26.5% decline from February 2023. Year-to-date orders reached $679.6 million, a decline of 16.9% from the first two months of 2023. While orders have thus far fallen short of the expectations from the beginning of the year, it is important to remember how good orders were in the first quarter of 2023. Manufacturing technology orders in the first three months of 2023 averaged $455.6 million per month. In the remainder of the year, monthly orders only reached $395.9 million. This is high by historical standards but reachable given the resilient economy and IMTS returning to Chicago’s McCormick Place later in the year. Small and medium-sized businesses, primarily contract machine shops, continued to fall behind the market, yet OEMs in several sectors increased their capital investment. Contract machine shops, the largest consumer of manufacturing technology, continued to decrease their orders. While they have generally ordered less relative to the overall market in recent months, this is only the second time since September 2021 that job shops decreased machinery orders while the overall market was expanding. Manufacturers of engines, turbines, and power transmission equipment increased orders to the highest level since February 2023. Orders from this sector have been elevated in recent years due partly to extreme weather requiring infrastructure improvements to improve grid reliability as well as government incentives around clean energy generation. The last time orders were at these levels was between late 2007 and the summer of 2008 when natural gas plants started becoming the dominant source of energy generation in the United States. The aerospace industry posted the second-largest order volume since December 2022, only surpassed by December 2023. While commercial aviation is a large part of the sector, there will be several large opportunities in the defense side of the business throughout the year. The Pentagon recently announced funding for new programs to improve the F-35 Joint Strike Fighter and both Lockheed and Boeing were recently awarded contracts to develop or supply missile systems. March is the end of the fiscal year for several companies, so in most years, orders tend to increase. With an order value of $548.8 million in March 2023, it will be difficult to surpass if demand from contract machine shops continues to fall behind the overall market. Even if orders fall short of 2023 levels next month, there are positive signs the remainder of 2024 will provide some opportunities for growth. The March 2024 ISM® Manufacturing PMI® showed the manufacturing sector was expanding for the first time since September 2022. If new orders and production continue to improve, orders of manufacturing technology will surely increase as OEMs begin to give work to contract machine shops to keep pace with their customers’ demands. Given the typical lag between increased demand and new machinery orders, shops may begin to need additional capacity just in time to ‘kick the wheels’ at IMTS 2024.
Episode 476: Fabric’s bold approach to micro fulfillment solutions
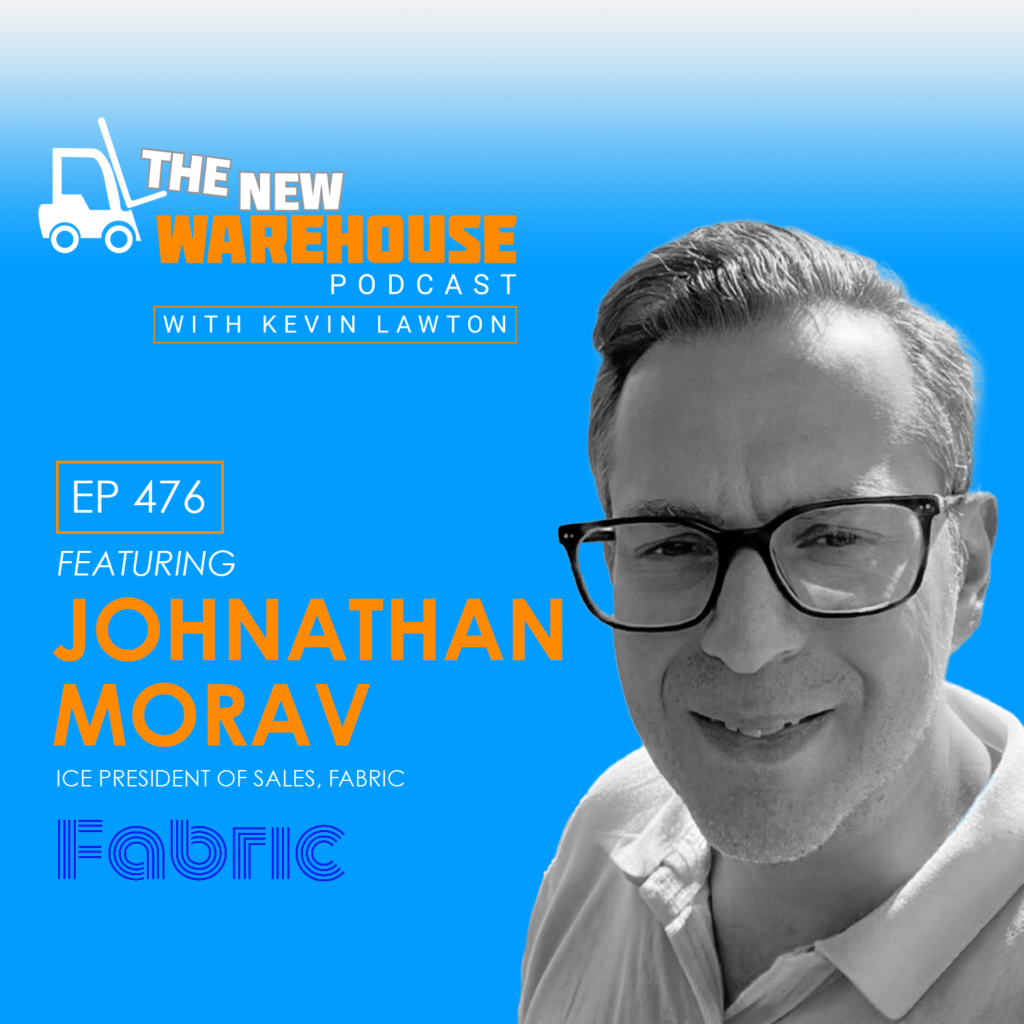
This episode of The New Warehouse Podcast transports us into the heart of Brooklyn, New York, to a site that’s reshaping the optics of fulfillment. Here, in an unassuming building, lies Fabric’s fully automated micro-fulfillment center. Our guest this week is Jonathan Morav, the VP of Sales at Fabric. This episode covers a topic near and dear to our hearts, micro-fulfillment, and the role of technology that continues to advance the fulfillment industry. Tune in to learn how these small, non-traditional spaces leverage unique robotic fulfillment solutions to pack a mighty punch. What Exactly is Micro Fulfillment? There are varying definitions and misunderstandings about exactly what Micro-fulfillment is. According to Jonathan, “For us, the story of micro fulfillment was always how do you deploy a system in a very dense urban area in order to unlock on-demand same-day deliveries.” His definition is rooted in the company’s Fabric’s origin of “pulling the operating point closer to the end customer,” ensuring swift, efficient, and economically viable deliveries. This approach is revolutionary, especially in dense urban settings where traditional fulfillment methods falter. Jonathan explains, “You typically would not support such an operating point, so we built a solution from the ground up that allowed for the maximum flexibility,” emphasizing their unique capability to harness irregular spaces for high throughput. A Closer Look at Micro Fulfillment Solutions Fabric’s technological marvel doesn’t just stop with flexibility; it’s about maximizing every square inch of real estate. Their system, designed for high throughput per footprint, enables operations to “do a meaningful amount of volume out of these types of facilities.” This efficiency is vital, especially when real estate is premium in urban areas. Jonathan offers three key considerations for the successful deployment of fulfillment in dense areas: Topology “You can’t be very fixed in how you think about your topology. You can’t have a rigid structure with no modularity to it because there’s no way you can scale across many facilities because there are only so many facilities that can match the profile of something that a fixed architecture, would allow.” Expensive Real Estate “You need to utilize every square foot and maximize the amount of output you can gain from that facility.” For instance, cube-based solutions take advantage of vertical height, which allows for a maximum amount of density, throughput, and output. Flexibility “If you don’t have the flexibility in the architecture to be able to design a viable operation around the automation, the automation is going to yield very little, and you’re going to be disappointed.” Applying the right automation tool for the job requires a deep understanding of what that solution can delivery for the problem you are trying to solve. Reducing Bottlenecks in the Fulfillment Process Jonathan introduces the concept of “graceful degradation,” which enables the continuity of the operation should something fail. “The idea is to deliver a solution with extremely high uptime, but even when there is an event, you can continue your operations in a relatively efficient and productive manner.” Fabric is able to pull this off by decoupling the lift robot and the ground robot so that if one stops, the others can simply work around it and avoid a complete stoppage of work. “It’s all about continuity of operations. It’s paramount to any business remaining viable.” According to Jonathan, an unintended byproduct of decoupling the two machines was the ability to drive down the cost of manufacturing. The ground robot is simple, cheap, and reliable, while the lift is a more complex machine. This drives down the overall cost of both units, “whereas, if you just combine the two, it becomes a much more complex machine with significantly more incremental costs associated with it.” Key Takeaways on Micro Fulfillment Solutions Fabric’s fulfillment technology is a game-changer for dense urban logistics. “If robots don’t unlock an efficient flow and a holistic end-to-end view of the operations, they will not do what they need to do. You must ensure you have the tools, software, and logic outside of the automation that unlocks an efficient end-to-end flow.” Labor continues challenging the material handling industry and solutions like Fabric fill jobs that would otherwise go unfilled. The New Warehouse Podcast Episode 476: Fabric’s Bold Approach to Micro Fulfillment Solutions
Avid Solutions marks significant growth in green hydrogen and decarbonization
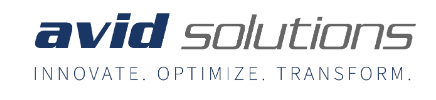
Avid Solutions, selected as the preferred delivery partner for hydrogen solutions by Rockwell Automation, has recorded exceptional revenue growth and expanded its team to meet the rising demand for innovative solutions in low-carbon emissions. Avid Solutions, a Gold Rockwell Automation System Integrator Partner specializing in process expertise and digitally-enabled solutions, today announced significant growth in demand for the company’s decarbonization and green hydrogen (H2) services. Avid Solutions, having been named the preferred delivery partner for hydrogen solutions by Rockwell Automation, has expanded its team by 35 members in the past year to meet the increasing interest for sustainable energy projects. Avid Solutions’ contributions to low-carbon emission initiatives have been marked by a series of achievements. The company was named the preferred green hydrogen delivery partner for Rockwell Automation after supporting decarbonization projects with control system integration, front-end engineering, PlantPAx implementation and standardization of liquefactions systems. Avid Solutions was also a nominee for an innovation award at the Rockwell Automation Partner Network Conference, based on their work in the hydrogen sector. “We are seeing many original equipment manufacturers (OEMs), process licensors, and producers entering the green H2 economy. They need expertise to scale, as well as speed to market entry,” said Tom O’Reilly, vice president, of sustainability, at Rockwell Automation. “With more than three decades of expertise in the process industries and helping OEMs scale, Avid Solutions is uniquely suited to help new green H2 clients implement best-in-class technology and ensure their business needs are met.” Rockwell Automation collaborates closely with Avid Solutions to address eco-friendly hydrogen manufacturing initiatives through the delivery of specialized services, including H2 liquefaction and turnkey plant automation using Rockwell Automation PlantPAx. Avid has supported projects across various sectors, including electrolyzer OEMs, H2 liquefaction licensors, and compressor OEMs. Avid engineers are actively involved in several ongoing projects, including an initiative in Texas aimed at delivering 45 tons of green hydrogen per day. These projects have led to record revenue and significant growth in the company’s Texas and Georgia offices, with the Brazilian team doubling in size to meet the needs of clients in the sustainability sector. “This growth and recognition underscore our efforts in shaping a cleaner, greener future,” said Gordon Bordelon, vice president, operations and technology, Avid Solutions. “The emergence of the hydrogen economy opens up exciting avenues in industrial manufacturing, power generation, and mobility. For producers looking to seize these opportunities, it’s important to partner with seasoned experts who can harness advanced technologies and confidently manage risks.” “We are located in one of the seven Regional Clean Hydrogen Hubs (H2Hubs) selected through the Bipartisan Infrastructure Law (BIL), and we are actively involved in most of them.” said Avid Solutions Vice President, Sales and Marketing Mike Kiehl. “Avid Solutions continues to deepen relationships with engineering, procurement, and construction (EPC) firms in the industry and solidify our position as a leader in decarbonization efforts. Our goals are to enable the production of 450 tons of green hydrogen per day by 2025 and 1,000 tons per day by 2030.”
ASSP names 2024 Outstanding Safety Educator
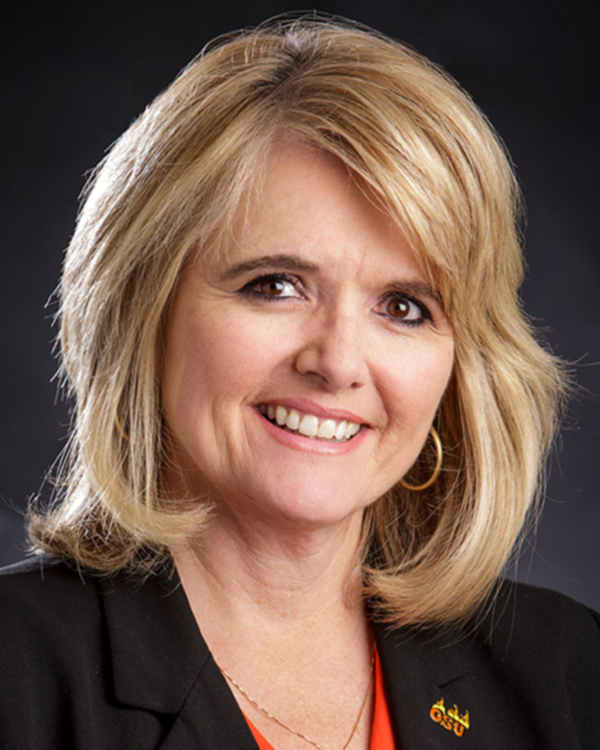
Leslie Rex Stockel, a widely respected educator in the occupational safety and health field and member of the American Society of Safety Professionals (ASSP) for 35 years, is the Society’s 2024 William E. Tarrants Outstanding Safety Educator. Stockel, Ph.D., CSP, SMS, is an associate professor of professional practice at Oklahoma State University in Stillwater, OK. She also is faculty advisor for the university’s student section of ASSP’s Oklahoma City Chapter, actively recruiting students to pursue degrees in occupational safety and health. Stockel’s teaching philosophy models a professional career environment, holding students to high standards. She uses her vast network to enhance the learning experience through guest lectures and field trips to industrial operations such as power plants, manufacturing facilities and construction sites. As a result, her students develop critical understanding and competencies that are fundamental to a successful safety and health career. Nominated for the ASSP honor by her students, Stockel is an esteemed faculty member with student evaluations rating her above both college and university averages. Students have described her as a passionate instructor who clearly knows the material and is dedicated to making her classes fun and informative. “Dr. Stockel constantly engages with her students and genuinely cares about our ability to understand the topics presented in class,” said Brady Hook, president of ASSP’s student section at the Stillwater campus. “She is a selfless individual who wants her students to succeed, so we know we can always go to her for guidance.” After a lengthy and successful career in industry, Stockel joined the university faculty in 2016 in the Fire Protection and Safety Engineering Technology program. She has made significant contributions to its continued growth and development while keeping her courses aligned with industry trends. She guides efforts to plan and execute career events where prospective employers meet with students about summer internships and permanent employment. She also encourages students to collaborate on campus and community service projects. “Her dedication to enhancing academic growth, mentoring students, and championing professional development has been truly invaluable,” said Chulho Yang, Ph.D., P.E., professor and interim head of the university’s Division of Engineering Technology. “Her instructional caliber is underscored by consistently earning impressive course evaluations. She is widely recognized as an outstanding instructor.” Stockel is a presenter at local, regional, and national safety education conferences. Several of her articles have appeared in peer-reviewed publications such as ASSP’s Professional Safety Journal. She was a co-project initiator when the U.S. Department of Labor selected Oklahoma State as an authorized OSHA Education Center in 2017. “Dr. Stockel is an asset to our program and the students she teaches,” said Dr. Virginia Charter, Ph.D., P.E., coordinator of the university’s Fire Protection and Safety Engineering Technology program. “She has made great contributions to the success of our students and their future safety careers.” Stockel will be honored at ASSP’s Safety 2024 Professional Development Conference and Exposition, held Aug. 7-9 in Denver. The global event will bring together thousands of safety professionals to learn about best practices, industry trends, and the latest product innovations in the workplace safety and health field. Each year, ASSP honors a member who demonstrates outstanding achievement in occupational safety and health education. These top instructors help students reach their full potential and become results-producing safety professionals. ASSP’s Outstanding Safety Educator Award is named after William E. Tarrants, a pioneer in safety education who was an ASSP Fellow and president (1977-78).
Atlantic Forklift Services recognized as top Bobcat Company material handling dealer
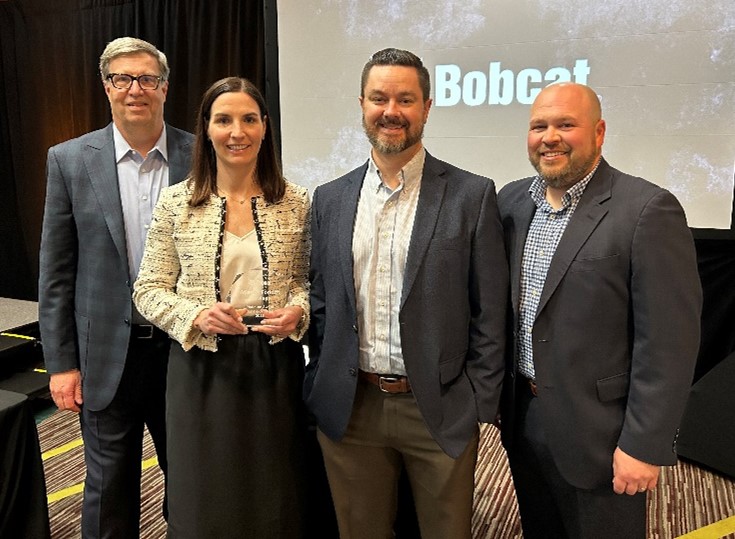
Awards given to top-performing material handling equipment dealers Atlantic Forklift Services was recently recognized for superior performance as a Bobcat Company top material handling dealer. The top dealers were recognized based on sales, volume, and other dealer engagement metrics. “We are pleased to recognize such a deserving group of dealerships for their efforts and achievements,” said Jarrod Steck, Bobcat vice president of material handling products. “While forklifts are a new product offering within the Bobcat portfolio, these dealerships bring years of expertise and experience within the material handling industry, and we are thrilled to award these top performers and valued dealer partners.” In recognition of this award Keith Driscoll, President of Atlantic Forklift Services, said, “As we reflect on our journey, I want to express my deepest gratitude to our team of dedicated professionals who work every day to be noticeably best. Their unwavering dedication and tireless efforts have been the cornerstone of our success. Additionally, I would like to extend our sincerest gratitude to our valued customers. Their trust and loyalty are the driving force behind everything we do. Thank you for choosing us, for believing in our vision, and for being an integral part of our journey. We are truly honored to serve you. Finally, I would also like to thank Bobcat material handling for recognizing our successes over this past year. We look forward to our continued partnership.”
Former Yale employee honored with lifetime achievement award by supply chain industry publication
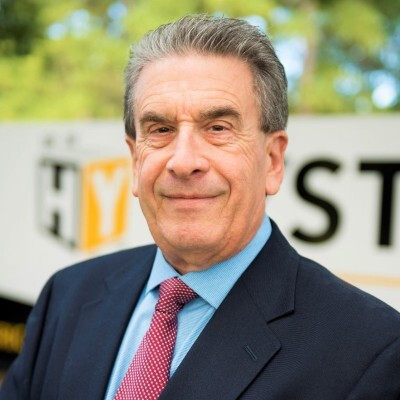
Yale Lift Truck Technologies has announced that Jay Costello, who formerly served as director of dealer marketing, has received a lifetime achievement award from Supply & Demand Chain Executive. Costello retired in late 2023 after more than 50 years with Yale – approximately half of the brand’s 100-plus years in business. His time with the organization included 36 years as the brand’s vice president of marketing, followed by positions as director of training and director of dealer marketing. During his long tenure, the brand underwent several significant transformations and throughout, Costello helped to shape the culture of the organization, unify global marketing and maintain strong relations with the dealer network. When the brand transitioned from a division of Eaton Corporation to Yale Materials Handling Corporation and later to Hyster-Yale Materials Handling, Costello played a pivotal role in forming and supporting the Yale identity. Costello applied this knowledge and experience to support the continued evolution as the brand unveiled its new identity and positioning at ProMat in 2023. Other notable accomplishments throughout his career include: Creating the company’s global product development process, which ultimately led to global marketing and product launches aligned across regions Securing the business of one of the organization’s largest and longest-tenured customers, a major hardware retailer Helping to plan and manage the company’s Experience Center facility, where customers, dealers and employees can access educational resources to improve lift truck utilization and advance training and innovation Costello has spent much of his career focused on mentoring young professionals who will continue to shape the company and the wider materials-handling industry. Helping others succeed in their careers has been such a passion and source of joy that Costello hopes to continue serving as a mentor even in retirement. “Jay was a leader at Yale long before I walked through these doors, and his mentorship has ensured that his legacy will be a lasting one,” said Brad Long, Brand Manager, Yale Lift Truck Technologies. “This recognition is a testament to the impact he has left not only on our brand, but on our industry as a whole, and more importantly, on the people working in it.”
Shibaura Machine announced new SCARA features at Automate 2024
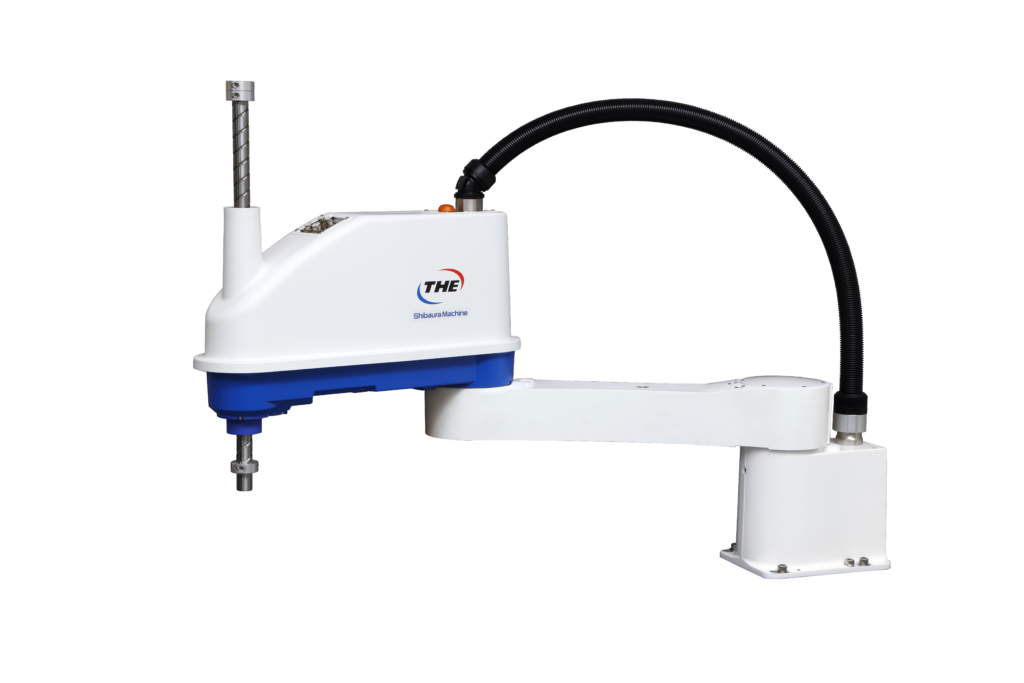
Shibaura Machine will display THE SCARA range and showcase its robots in action Shibaura Machine will be exhibiting at Automate 2024 alongside TM Robotics. Shibaura Machine will showcase THE SCARA range of industrial robots, powered by TM Robotics, at booth 661 at the show and unveil new features to enhance its product offerings. Organized by the Association for Advancing Automation (A3), Automate offers industry professionals the chance to see first-hand the latest innovations and advancements in automation. Attendees can expect to see over 800 exhibitors from a huge range of sectors and will have the opportunity to attend various networking and education events throughout the show. Shibaura Machine will be displaying its full range of THE SCARA robots, along with a selection of its Cartesian and six-axis robots. Visitors will be able to see the two newest models in THE range, the THE800 and THE1000, in action at the show at its booth managed by TM Robotics. The THE800 is designed to excel in assembly and inspection processes where precision and payload capacity are crucial factors. With a maximum payload of 20 kg and improved accuracy and precision, the THE800 offers high-speed operation with a maximum cycle time of 0.41 seconds. The THE1000 has an impressive reach of one meter, making it ideal for assembly and inspection processes requiring larger components. It also has a maximum payload of 20 kg and high-speed operation with a maximum cycle time of 0.44 seconds. The THE100 will be working at full speed and handling its maximum payload at the show, highlighting its potential in industrial applications. Not only will Shibaura Machine be demonstrating its THE range in a display powered by partner TM Robotics, the company will also be unveiling a new suite of optional extras that end-users will be able to add to their robotic solutions later this year. This includes ceiling mounting, IP65 ingress protection allowing them to become part of the manufacturing process in food and pharmaceutical production lines, and clean room options. This significantly enhances the versatility of the THE range and broadens the spectrum of potential applications for these robots. Shibaura Machine will also be displaying a THE400 SCARA and a TVL700 six-axis robot working collaboratively with a SICK vision system for handling and inspection applications, demonstrating how harnessing the synergy between robots and advanced systems can help to optimize industrial operations. “Our robots are engineered to meet the demands of modern manufacturing and automation processes, delivering precision, speed, and reliability, said Nigel Smith, CEO of TM Robotics. “Our demonstrations at Automate 2024 in collaboration with Shibaura Machine will showcase how industrial robots can drive efficiency and productivity in a huge range of production applications. The new range of optional extras for the THE models will also offer our users an even wider scope for incorporating robotics into their operations — ultimately saving time, cutting costs and building smarter production lines.”
Genuine Parts Company announces officer promotion

Genuine Parts Company has announced its board of directors has appointed James F. Howe to the position of President, Motion, the company’s industrial business, effective April 1, 2024. With nearly three decades of dedicated service to the company, Howe brings a wealth of experience and expertise to his new role. Most recently, Howe served as the Executive Vice President and Chief Commercial and Technology Officer, where he played a pivotal role in shaping the corporate trajectory of Motion. His leadership in overseeing eCommerce, strategic pricing, sales excellence, corporate accounts, and human resources has been instrumental in driving the company’s success. In his new capacity, Mr. Howe will continue to report to Randy Breaux, Group President, GPC North America. “James has an impressive history, having served in numerous executive roles during his long career at Motion,” said Paul Donahue, Chairman and CEO. “His extensive experience makes him an excellent choice to lead Motion. We feel confident that under James’s leadership, our talented and experienced Motion team will continue to achieve great results.”
Episode 475: The Pivotal Role of Barcodes in Supply Chain Management with GS1
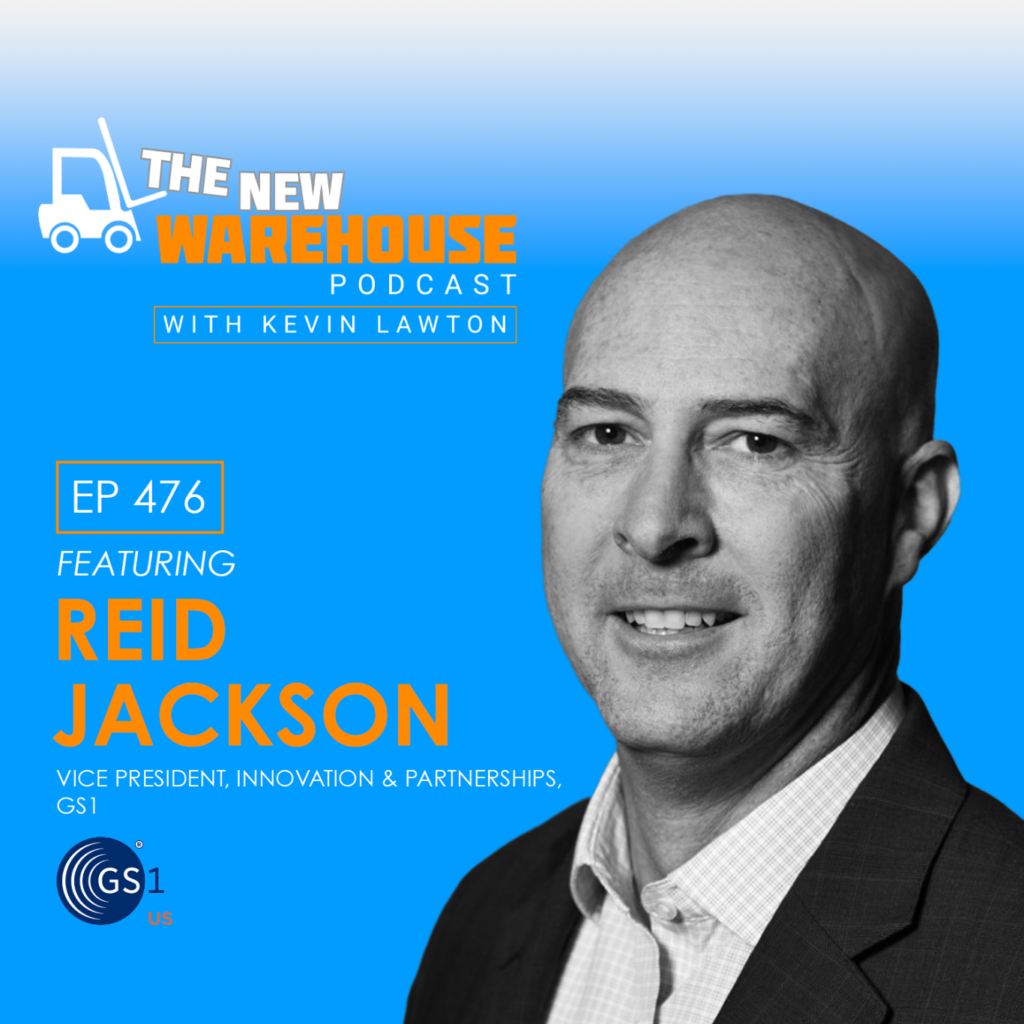
Barcodes are often underrated and underappreciated, but they play a pivotal role in product safety, efficiency, and movement within the global supply chain. In this episode of The New Warehouse Podcast, Reid Jackson, Vice President of Business Development at GS1 US, gives us the rundown on UPC barcodes and their role as passports for products in the supply chain. GS1 is renowned for setting the global standard in the supply chain, famously known for introducing the UPC barcode, an innovation that revolutionized retail and beyond. This episode delves into the foundational role of GS1 in standardization, its evolution alongside technology, and the future of supply chains. GS1 and the UPC Barcode The inception of GS1 is a story of necessity and innovation. Reid Jackson recounts, “We need the brands to have some type of identifier on them to speed up the checkout and to increase the accuracy.” This need led to creating the UPC barcode, marking a pivotal moment in retail and manufacturing. The initiative stemmed from the grocery industry’s demand for efficiency and accuracy at the checkout. GS1’s role extended beyond the barcode, emphasizing its technology-agnostic approach to solving industry-wide challenges. Leveraging Barcodes in Supply Chain Management The application of UPC codes and GS1 standards illustrates the vast impact on industries, exemplified by Reid’s Subway story. “Subway… would take product lettuce, tomato, meat, spreads, everything… take it into their inventory from tons of different suppliers, but they would inventory it all the same. When it came in, it was lettuce.” If there were ever a recall, they would have to return everything. “Now they’ve moved to GS1 standards,” Reid adds, allowing them to only send back impacted products in the case of a recall. This anecdote underscores the efficiency and safety GS1’s standards introduce to supply chain management, highlighting how specific product tracking can mitigate extensive product recall, ensure consumer safety, and reduce waste. Advancing Technology with GS1 Standards GS1’s engagement with emerging technologies signifies its continuous evolution. “We’re heavily involved with MIT and the Auburn RFID lab and constantly looking at these technologies and how they’re being implemented and used,” Reid shares. This forward-looking approach ensures GS1 standards remain relevant amidst advancements in warehousing, material handling, robotics, and beyond. GS1’s collaboration with technology institutions and industries fosters innovation while maintaining the utility and integrity of supply chain standards. Key Takeaways on Barcodes in Supply Chain Management GS1 pioneered the UPC barcode, significantly enhancing retail and supply chain efficiency. Applying GS1 standards exemplifies the profound impact on product safety and recall management. GS1’s proactive involvement with technology and research institutions ensures its standards evolve with emerging supply chain innovations. The New Warehouse Podcast Episode 475: The Pivotal Role of Barcodes in Supply Chain Management with GS1