Steele Solutions showcasing advanced structural steel platforms and material handling chutes at MODEX 2024
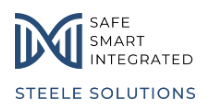
Booth highlights will include exclusive demonstrations of the future of elevated structural platforms and SST™ material handling chutes, with individual consultations on enhancing operational efficiency. Steele Solutions Inc., a manufacturer of structural steel work/equipment platforms, material handling chutes, and public-safety security lockers, has announced its participation in MODEX 2024 at the Georgia World Congress Center in Atlanta, Georgia, Monday, March 11 – Thursday, March 14. Attendees are invited to visit Steele Solution’s booth #C5081, conveniently located in Hall C on the main aisle, opposite the main entrance, and near the MODEX Backyard food court. “Steele Solutions is committed to delivering superior engineering and manufacturing solutions that meet the evolving needs of our customers,” said Kevin O’Neill, CEO of Steele Solutions. “Our participation in MODEX 2024 represents an excellent opportunity to showcase our latest innovations in structural steel platforms and chutes. We enjoy meeting one-on-one with attendees, listening to their challenges, and demonstrating how our tailored solutions can enhance operational efficiency and safety for businesses across various industries.” What to Expect at Steele Solution’s MODEX 2024 booth: Advanced elevated structural platforms: Discover the most advanced platforms that eliminate cross-bracing and offer increased space for walkways, workspaces, and storage. Slick Surface Technology (SST™) Material Handling Chutes: Experience firsthand the quality of SST material handling chutes, featuring a 100% welded, bolt-free frame for easier assembly, improved structural integrity, and reduced maintenance. Solution Center for Custom Solution Capabilities: Visit our new Solutions Center to learn how Steel Solution’s team of over 60 engineers can tackle complex challenges with tailored product solutions. Expert consultations: Schedule a meeting with our team of sales and project management representatives to discuss specific product needs and find out how we can assist in optimizing operations. Steele Solutions is known for its engineering expertise and dedication to producing high-quality products in the United States, serving e-commerce, retail, distribution, and manufacturing customers globally. For an in-depth and hands-on review of the future of structural steel platforms and material handling chutes, MODEX 2024 attendees can visit booth #C5081 on Monday, March 11, until Wednesday, March 13, from 10:00 a.m. – 5:00 p.m., and Thursday, March 14, from 9:00 a.m. – 1:00 p.m.
BALYO revolutionizes the move to robotics for warehouses and distribution centers at MODEX 2024
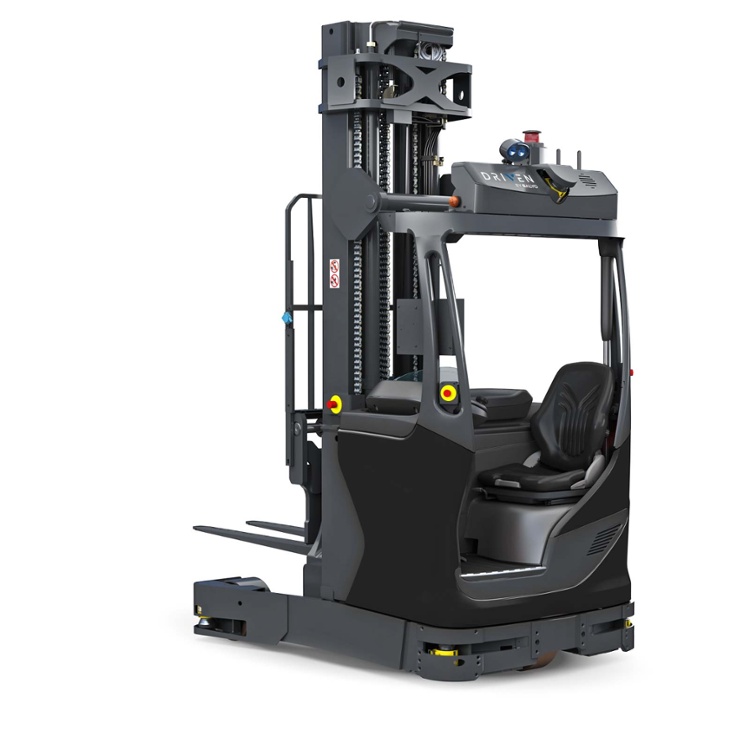
Empowering the Vertical Pallet Storage Revolution – Robotic Narrow Aisle High Reach Robot BALYO, the trailblazers in transforming standard forklifts into autonomous driverless forklifts, is set to showcase the future of vertical pallet movement and storage at MODEX 2024, Booth C8669. Under the spotlight will be BALYO’s revolutionary robotic narrow aisle high reach robot, the embodiment of simplicity and efficiency in autonomous pallet storage and retrieval. Maximize existing space & racking: BALYO’s reach robot is not just a machine; it’s a beacon lighting the way for companies to embrace a vertical pallet storage revolution. With the capability to pick pallets up to 1.7 tons to a towering height of 36 feet, this slim infrastructure-free autonomous robot operates in aisles of only 9’9” wide – the narrowest in-aisle turning space for high-reach robotic forklifts. This gives warehouses maximum space utilization, without the need to re-layout and re-install existing racking, which saves both time and money. The apex of intelligence & safety: This robotic wonder operates with the highest level of intelligence, using advanced LiDAR and a proprietary SLAM navigation algorithm. This combination allows for infrastructure-free localization and navigation with the highest degree of safety. The robot is further complemented by 3D cameras and sensors to safely recognize and handle virtually any globally-used pallet type. The message from BALYO’s Chief Sales Officer, Mark Stevenson: “Smart companies are scaling up – not out! The vertical revolution is here, and the key to safely and efficiently navigating it is to automate the storage and retrieval of goods,” declares Mark Stevenson, BALYO’s Chief Sales Officer. “BALYO robots operate at the absolute highest level of both safety and mission accuracy. Moving complex manual forklift operations to automated pallet transportation and storage is easy, fast and the ROI impact is compelling. For example, a typical end-of-line to-storage flow can be installed and running in as little as a few weeks, with minimal disruption to ongoing operations. The shift to robotic operations is a no-brainer in overcoming labor challenges and maximizing storage space utilization in existing facilities without expensive and production-invasive changes. BALYO is already helping our clients do this all over the world. “ Simplifying Change, Inspiring Progress: Stevenson reassures, “BALYO is here to dispel the legacy “fear of change” that somehow automating is complex, risky, and expensive. Many of our clients feared they did not have the expertise to automate pallet transportation and storage, and did not know where to start, or that changing existing processes is risky. Our robots can be running in weeks, not months. Our stock inventory of standard robots, simple tools and quick-start processes empower users to take charge of the transformation. Change has never been this easy.” Digital twins so you know before you go: At MODEX 24, BALYO will bring the reach robot to life, showcasing real-world pallet storage and retrieval scenarios. BALYO experts will demonstrate tools like BALYO eBudget for straightforward scoping of robotic projects. BALYO will also demonstrate their Road Editor software, which creates a digital twin of any space to create circuit planning and mission management so you “know before you go” on every project. A legacy of innovation: With nearly 20 years of experience, BALYO’s unique software has evolved to turn standard electric trucks into standalone intelligent robots, accelerating the gap between manual and autonomous operations. This technology doesn’t replace people; it liberates them to focus on improving operations and engaging in truly value-added activities. A symphony of solutions: The reach robot is just one note in BALYO’s symphony of sustainable robotic solutions, including stackers, counter-balanced robots, tuggers, pallet jacks, and a VNA (Very Narrow Aisle) robot reaching heights of 56ft.
Yale account executive honored as an emerging leader in food and beverage supply chain
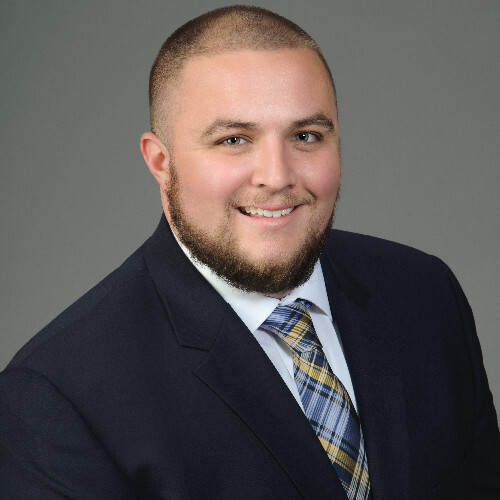
Forklift manufacturer’s director of major accounts recognized for industry expertise and prioritization of customer solutions Yale Lift Truck Technologies announced that Brendan McCann, Director of Major Accounts for Food Processing and Distribution, has been named a Rock Star of the Supply Chain by Food Logistics magazine. McCann is a winner in the rising stars category, which honors exceptional professionals under the age of 40. McCann leads a team responsible for providing lift truck solutions to 165 of the largest food processing, distribution and agriculture operations in North America, including more than 14,600 logistics locations. McCann firmly embodies the brand’s customer-driven philosophy by immersing himself in the challenges his customers face. He gathers insight and produces tailored recommendations, from plans targeting near-term productivity gains to holistic, long-term roadmaps that guide customers through the adoption of advanced lift truck technologies like operator assist systems and automation as their business evolves. In one instance, McCann helped a large customer design a new distribution center. The customer’s initial plans called for a footprint of more than 1 million square feet and more than 100 forklifts. By understanding the customer’s throughput and growth goals, McCann determined an alternative approach, with a footprint under 500,000 square feet and fewer than 40 forklifts, could save the customer millions in building costs while accomplishing their productivity goals with less equipment and space. Before joining the team at Yale, McCann was a Senior Account Manager for Briggs Equipment, a Yale® dealer, where he was named Salesman of the Year in 2017. During his tenure with the company, he was based in Gainesville, Georgia, “the poultry capital of the United States.” There, McCann built a deep foundational understanding of agriculture, food and beverage operations that he leverages every day and very intentionally shares with members of his team. “Anyone can put a lift truck in a building,” says McCann. “At Yale, it’s really about identifying or developing the right solutions to make a meaningful difference. Within my team, my ultimate goal is to instill in others my passion for helping customers overcome challenges and optimize their supply chain operations, and I’m honored that Food Logistics recognized the value in that approach.”
Seeq announces generative AI capabilities with Seeq AI assistant
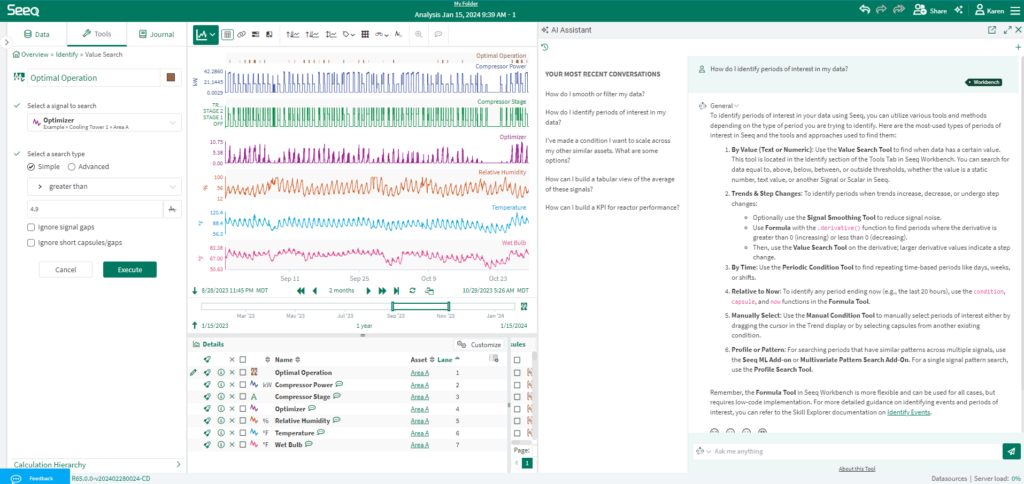
Seeq, industrial analytics, and AI have announced the Seeq AI Assistant, a generative AI (GenAI) resource embedded across its industrial analytics platform. The Seeq AI Assistant provides real-time assistance to users across the enterprise, empowering them to accelerate mastery of the Seeq platform, build advanced analytics, machine learning, and AI skills and knowledge, and accelerate insights to improve decision-making in pursuit of operational excellence and sustainability. In a recent study by Deloitte, 93% of industrial companies believe AI will be a game changer for driving growth and innovation in the industrial sector. The analytical insights required to bolster operational excellence continue encountering roadblocks due to a shortage of skills, siloed capabilities within organizations, and untapped stockpiles of time series data. Seeq has over a decade of experience working with some of the most recognizable names in the oil & gas, chemicals, pharmaceuticals, and other industrial sectors to remove or mitigate these roadblocks. The Seeq AI Assistant provides organizations with the opportunity to further debottleneck their most precious resource – the people at the frontlines of their processes and decisions. GenAI is a type of artificial intelligence capable of generating new content, such as text, images, and code in response to prompts entered by a user. GenAI models are trained with existing data to learn patterns that enable the creation of new content. While GenAI is a powerful technology, it isn’t innately capable of generating information and guidance applicable to the complexity and context of an industrial production environment. Seeq is uniquely positioned to drive industrial innovation with GenAI, given the company’s expertise in industrial data and its open and extensible analytics platform that was developed to leverage and serve subject matter experts and their enterprise decisions. Seeq provides on-demand access to critical time series data, data contextualization capabilities, and established intellectual property. Utilizing the extensive body of advanced analytics, data science, machine learning, and coding knowledge held in Seeq technical documentation and its knowledge base, Seeq is operationalizing the power of GenAI for its customers. Combining these competencies with prompt engineering curated by the world-class analytics and learning engineers at Seeq, the Seeq AI assistant generates accurate and actionable suggestions for analytical approaches and techniques, code generation, and more. Seeq also supports multiple providers and LLMs for organizational flexibility. “With the Seeq AI Assistant, we expect to decrease our process experts’ learning curve for advanced analytics and machine learning by 50% or possibly more,” said Brian Scallan, Director of Continuous Improvement at Ascend Performance Materials. “For our extensive user base, this translates into immediate enhancements in process quality and yields, significantly elevating efficiency and value across the organization.” “By combining GenAI with advanced industrial analytics, organizations can unlock new levels of efficiency, accuracy, and innovation that deliver measurable business impact,” said Dustin Johnson, Chief Technology Officer at Seeq. “Integrating the Seeq AI Assistant across the Seeq platform enables team members across industrial organizations to harness the power of GenAI to drive favorable operational excellence, profitability, workforce upskilling, and sustainability outcomes and stay ahead in an increasingly competitive landscape.” In short, the Seeq AI Assistant empowers frontline experts in process engineering, data science, and operations to rapidly bridge process, analytics, and coding knowledge gaps, unlocking workflows and results that were previously time and effort-prohibitive or impossible. “GenAI capabilities are a powerful inclusion in analytics software as a way to democratize AI and machine learning,” said Jonathan Lang, Research Director for IDC Industry Operations. “Based on conversations with industrial enterprises, GenAI offers a more natural interface to lower the barriers to data analytics, and Seeq has included features to alleviate one of the top concerns companies have about trust by including explainability to ensure the GenAI ‘shows its work.’” Seeq is available worldwide through a global partner network of system integrators, which provides training, services, and resale support for Seeq in over 40 countries, in addition to its global direct sales organization.
AutoScheduler Keith Moore named a 2024 Pros to Know
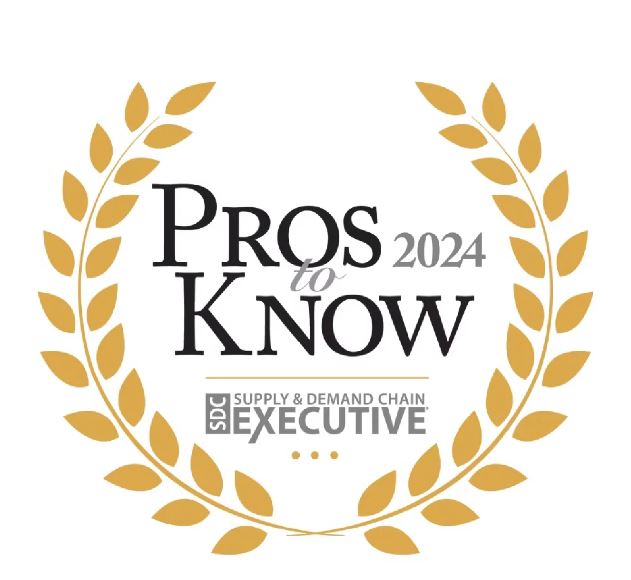
Named the next big winner in the Supply Chain Industry; Clean sweep of both categories – Judge’s Choice and People’s Choice AutoScheduler.AI, an innovative Warehouse Management System (WMS) accelerator, announces that CEO Keith Moore is one of the winners of this year’s Pros to Know award, which recognizes outstanding executives whose accomplishments offer a roadmap for other leaders looking to leverage supply chain for competitive advantage. This recognition is for the Rising Stars Category. “As one of twenty-five Rising Stars Category winners in the Pros to Know Awards, I am pleased to be chosen among hundreds nominated for making outstanding contributions to the supply chain space. I am an evangelist for using artificial intelligence and machine learning within warehouse solutions to help improve visibility, worker productivity, sustainability, and customer service. Clients benefit from greater customer service, labor reduction, and better ability to meet demand.” ~Keith Moore, Chief Executive Officer, AutoScheduler.AI “Many of today’s supply chain pros are more than just leaders within their space; they’re innovators, decision-makers, pioneers of change and growth. They’ve spent the last year (and more) creating safer, more efficient supply chains. New this year, we broke the award down into four distinct categories: Top Warehousing Stars; Top Procurement Stars; Rising Stars; and Lifetime Achievement. These winners continue to go above and beyond to overcome challenges, advance supply chain management and make the impossible, possible.” ~Marina Mayer, Editor-in-Chief of Food Logistics and Supply & Demand Chain Executive Keith Moore is CEO of AutoScheduler.AI, where he provides leadership and management, ensuring employee engagement, innovative product design and development, and top customer service while maximizing profitability. He oversees company operations, communicates between board members and other company executives, and makes critical decisions that impact the company’s brand identity and financial health. He leverages his knowledge of the warehousing industry and deep technology competencies to drive value in AutoScheduler’s offerings and to take the business to the next level.
Federal HazMat and Emergency Management Expert joins safety non-profit
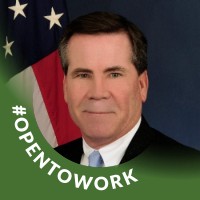
The Alliance for Innovation and Infrastructure (Aii) has named Timothy P. Butters to its Board of Directors. Butters, a senior executive in the Administration of Barrack Obama, served as the Acting Administrator and Deputy Administrator of the Pipeline and Hazardous Materials Safety Administration (PHMSA), where he was instrumental in safely and securely overseeing all hazardous materials shipped via air, land, rail, sea, and pipeline. “I am honored to be joining the Aii Board of Directors, and I look forward to leveraging my expertise as we address pressing issues,” said new Aii Board Member Timothy P. Butters. Following PHMSA, Butters also served at the Federal Aviation Administration (FAA), where he served as a senior advisor in FAA’s Office of Airports and provided public safety expertise in several key program areas including Unmanned Aircraft, Aviation Event Emergency Planning, and Commercial Space Transportation. Before his federal service, Butters was a professional firefighter and EMT in Fairfax City, Virginia, retiring as an Assistant Fire Chief. As a first responder, Butters was a member of the National Capital Region Type III Incident Management Team (IMT). He has been deployed to major disaster sites to support local incident management operations, including Hurricanes Katrina (MS) and Ike (TX), wildfires, presidential inauguration support, and other large events. Butters has also held senior leadership positions with the International Association of Fire Chiefs, the Chemical Transportation Emergency Center (CHEMTREC), and the Federal Emergency Management Agency. “We are fortunate to have Tim join the Board,” said Aii Chairman and Founder Brigham McCown. “Tim’s expertise as a first responder and regulator is a huge asset to our mission.” Celebrating a decade of non-partisan public policy service, the Alliance for Innovation and Infrastructure seeks to foster innovative solutions to significant infrastructure and public policy challenges.
Mitsubishi Logisnext Americas honors the recipient of the 20th Annual Cat® Lift Trucks Scholarship
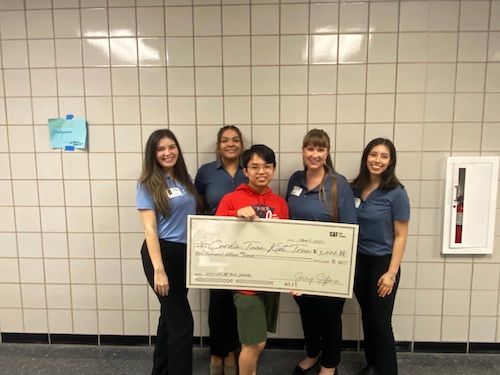
Mitsubishi Logisnext Americas, a North American provider and manufacturer of material handling and innovative automation and fleet solutions, announced the recipient of its 2024 Cat® Lift Trucks Scholarship Program. This year’s $5,000 scholarship winner is Cardin Tuan Kiet Tran, a high school senior at Davis High School in Houston. Cardin plans to major in civil engineering at Rice University, bringing with him a track record of leadership and involvement. Cardin is actively shaping his community as the Founder of the Davis High School Environmental Club and President/Editor-in-Chief of the Falcon Gazette Newspaper Club. His commitment extends to organizations such as the City of Houston Youth Ambassadors, National Technical Honor Society, Norman Borlaug Youth in Agriculture Program, and Child-Friendly Cities Initiative. Notably, Cardin’s impact was recognized for being the most effective student in promoting secondary education via trade schools at Lone Star and received an outstanding student award for Algebra II, OnRamps Physics, AP World History, and more. Today, Mitsubishi Logisnext Americas surprised Cardin at his high school, presenting him with a $5,000 check and complimentary Houston Livestock Show and Rodeo™ tickets for him, his family, and a teacher who inspired his educational journey. As someone passionate about urban and transportation centers, Cardin hopes to learn ways to build environmentally friendly infrastructure to serve society better. “Our applicants were outstanding this year, but Cardin’s vision for the future and dedication to STEM truly makes him a role model for future high school seniors,” said Jerry Sytsma, executive vice president, sales & aftermarket services at Mitsubishi Logisnext Americas. “We are committed to investing in students’ education as they are the future generations in our industry. It has been incredible to see the achievements of our scholarship recipients over the past 20 years.” Mitsubishi Logisnext Americas has been actively contributing to the Greater Houston community by honoring exceptional high school seniors pursuing a four-year degree related to the material handling industry. Over the past two decades, the Cat Lift Trucks Scholarship Program has awarded $145,000 in educational assistance to 29 Houston area students. To learn more about Mitsubishi Logisnext Americas, please visit logisnextamericas.com.
February 2024 Logistics Manager’s Index Report® LMI® at 56.5
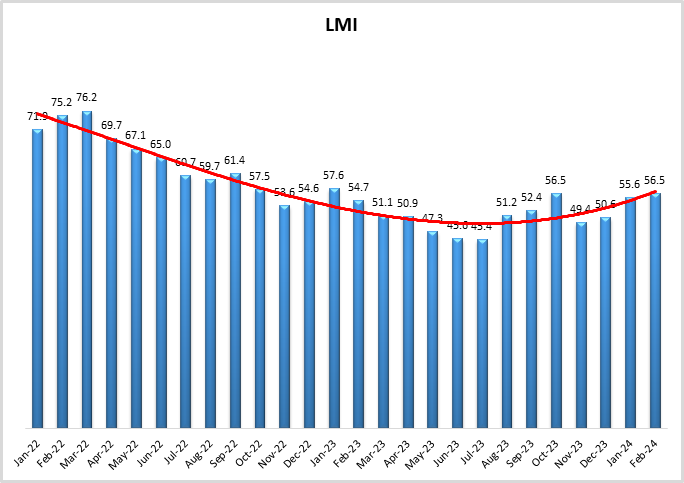
Growth is INCREASING AT AN INCREASING RATE for Inventory Levels, Warehousing Utilization, Transportation Capacity, Transportation Utilization, and Transportation Prices Growth is INCREASING AT A DECREASING RATE for Inventory Costs and Warehousing Capacity Growth is HOLDING STEADY for Warehousing Prices The Logistics Manager’s Index reads in at 56.5 in February 2024. This is up (+0.9) from January’s reading of 55.6 and is tied with October 2023 for the highest reading for the overall index in the last year. For the second month in a row, this growth is bolstered by expansion in all eight sub-metrics captured in the index. This is driven by a continued expansion in Inventory Levels (58.5) which has led to a tightening in Warehousing Capacity (52.8) and growth across all three transportation metrics. Particularly notable is the expansion in Transportation Prices, which at 57.6 have reached their fastest rate of growth since the start of the freight recession in June 2022. Interestingly, Transportation Capacity was also up this month to 60.9, bumping it higher than Transportation Prices and suggesting that we have not yet entered a true growth period in the freight market. Researchers at Arizona State University, Colorado State University, Florida Atlantic University, Rutgers University, and the University of Nevada, Reno, and in conjunction with the Council of Supply Chain Management Professionals (CSCMP) issued this report today. Results Overview The LMI score is a combination of eight unique components that make up the logistics industry, including inventory levels and costs, warehousing capacity, utilization, and prices, and transportation capacity, utilization, and prices. The LMI is calculated using a diffusion index, in which any reading above 50.0 indicates that logistics is expanding; a reading below 50.0 is indicative of a shrinking logistics industry. The latest results of the LMI summarize the responses of supply chain professionals collected in February 2024. The LMI read in at 56.5 this month, up (+0.9) from January’s reading of 55.6. This is the sixth time in the last seven months that the LMI has shown expansion. This growth is driven by continued progress in transportation and the buildup of inventories upstream at the manufacturing and wholesale levels. The overall index is up, but still below the all-time average of 62.4 – which in many ways epitomizes the current slow but positive and steady state of the U.S. economy. The University of Michigan Consumer Confidence Index stayed high in February, reading in at 76.9. While this is down (-2.4) from January’s reading of 79.0 it is up 14.9% from the same period last year[1]. While core inflation in the U.S. was up by 0.4 percent in January, the PCE index (the Fed’s preferred measure) was only up 2.4 percent, which is down from the 2.6 seen in December. When taken together, the economy continues to grow, and consumer prices are largely moderating – though likely not quickly enough for the Fed to consider a cut to interest rates at their meeting in mid-March[2]. One of the factors behind the strong U.S. economy is immigration. Net immigration from August 2022 to July 2023 was the highest it has been since 2017 and immigrants now make up 18.6 percent of the labor force in the U.S., which has been a relief to some businesses that struggled with labor during the pandemic years. This is largely driven by tripling in refugees how have been granted asylum and quickly entered the labor force (up to 1.2 million from 423,000 year-over-year). This is bolstered by increased domestic energy production as the U.S. has continued to be a net exporter of energy[3]. While it may be politically complicated, abundant labor and abundant energy is a combination that is unique to the U.S. and is likely a major factor behind the increased pace of economic recovery seen in the U.S. relative to other developed nations. Eurozone inflation was down to a 2.6 percent annual increase in February which is lower than expected and down from the 2.8 seen in January. This is spurred on by lower energy prices across the continent[4]. The February Chinese service PMI was up to 51 in February which is its highest reading since September. Conversely, China’s manufacturing PMI was down to 49.1, which is lower than January and marks the sixth consecutive month of contraction, something that is a worrying sign for the country that is colloquially known as “the world’s factory”. Chinese manufacturing is being challenged by subdued domestic spending as well as tensions with many of their primary trade partners[5]. It will be interesting to see if the U.S. and European economies can truly reach robust rates of growth if the world’s second-largest economy continues to struggle. There is slowness north of the border as well as retail sales were down by 0.4% in Canada in January (although this came after a stronger-than-expected increase of 0.8% in December, so this could be a regression to the mean). Much like the U.S., Canada’s economy is growing but at a slower pace and the Canadian central bank is expected to leave interest rates where they are at their March meeting[6]. The resilience of the U.S. economy is apparent in Transportation Price movements. After moving from contraction to expansion for the first time in 20 months in January, Transportation Price growth increased again (+1.8) to 57.6 in February. This is a function of demand and not cost, as increasing Transportation Prices came despite U.S. diesel costs being down to $4.058 per gallon in the last week of February, which is $0.236 down from the same time a year ago[7]. Additionally, fears that the increases were only due to issues in the Red Sea also seem to have subsided with the price spikes due to Houthi attacks seem to have peaked as shipping rates from Asia to the U.S. declined in February. Rates are still up by over 100% from where they were in early December, but they have dipped slightly in recent weeks[8]. That does not mean the crisis is over. Maersk recently predicted that they
MHS Lift earns Summit Award from Crown Equipment Corporation for outstanding sales performance
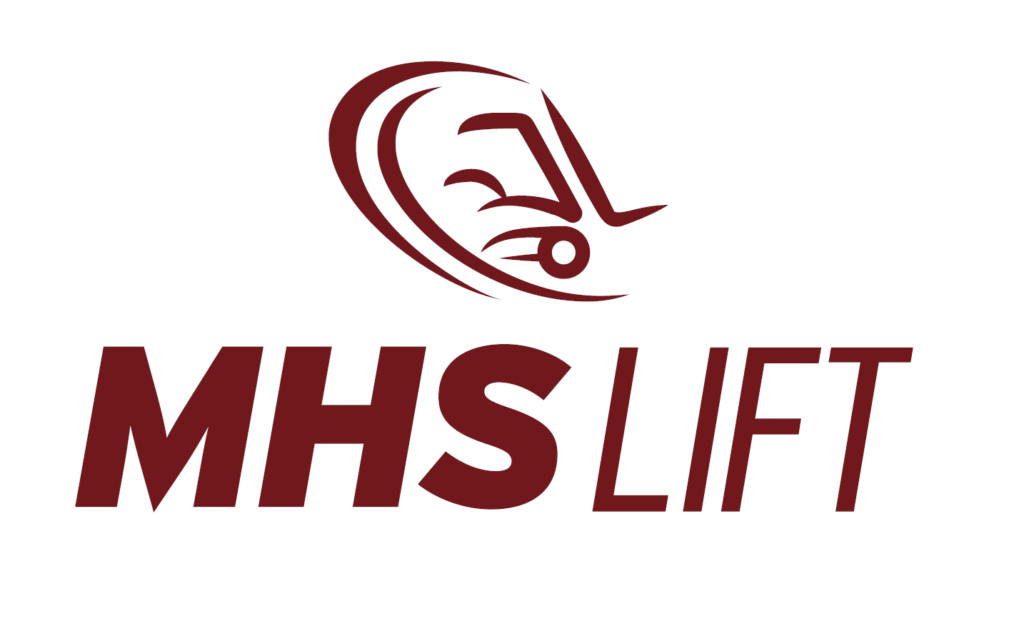
MHS Lift, Inc., a provider of warehousing and distribution solutions across North America, has received the prestigious 2023 Summit Award from Crown Equipment Corporation, one of the world’s largest material handling companies. Crown’s Summit Award recognizes outstanding sales and customer satisfaction achievements in its North American sales and service network. To qualify for the Summit Award, the company must be a Crown dealer and be considered the Best Dealer by market size. This is MHS Lift’s eighth Summit Award. “We are thrilled to receive the Crown Summit Award for our eighth year,” said Brett Levin, co-president, of MHS Lift. “Crown Equipment Corporation is a close partner of ours, and it’s an honor to be recognized by them.” “Receiving this award is proof to our team that hard work pays off – and our staff has been working tirelessly to provide top-notch service to our customers every day. We owe this accomplishment to them,” said Andy Levin, co-president, of MHS Lift.
Movu Robotics and PeakLogix introduce an easier automation to warehouses
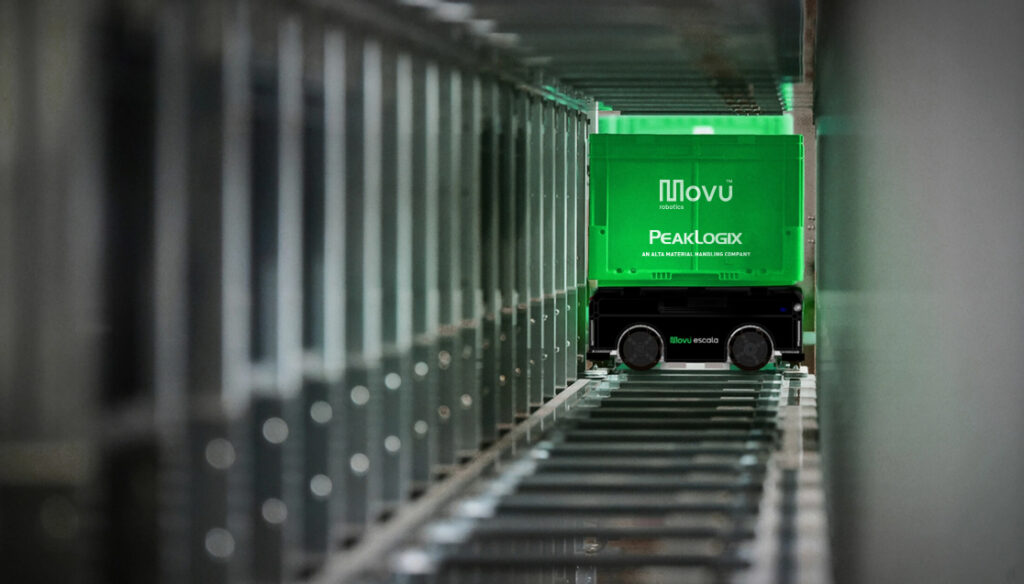
Movu Robotics has announced a strategic partnership with supply chain integration partner PeakLogix, an Alta Material Handling company. This partnership means Movu Robotics and PeakLogix can offer the benefits of Movu’s plug-and-play robotics portfolio as part of their solutions for customers in the North American market. Since 1989, PeakLogix has specialized in providing material handling solutions and warehouse optimization services. The company offers a range of services, including warehouse design, equipment integration, software solutions, and project management. PeakLogix helps businesses maximize efficiency and productivity in their warehouse operations through tailored solutions based on their specific needs and requirements. Over 30 years and thousands of successful projects, PeakLogix has earned its reputation for collaborating with clients to bring innovative solutions to life. With a philosophy of ‘no warehouse left behind’, Movu Robotics tackles automation with easier, modular, scalable, flexible and efficient solutions that customers need and helps them to upgrade their warehouses. The Movu portfolio is built around a range of innovative sub-systems designed to provide easier, scalable, flexible and energy efficient solutions accessible for all kinds of warehouses and quick to roll out. These include the Movu atlas, a pallet shuttle system for multiple deep lane storage; Movu escala the robotized 3D storage and fulfillment system; Movu ifollow Autonomous Mobile Robots (AMRs) for collaborative picking or transport of load carriers such as pallets; and the Movu eligo picking arm robot; as well as the appropriate supporting software. Stefan Pieters, CEO of Movu Robotics said: “This partnership opens up a world of possibilities for us and our clients. By combining our cutting-edge technology and proven solutions with PeakLogix expertise, we are excited to deliver even greater value and efficiency in warehouse operations. Movu Robotics sub-systems are designed with seamless integration in mind and I am glad that our strategic partnership with PeakLogix will bring automated solutions to more customers globally, helping them to meet their challenges and boost their performance, resilience and service levels.” Mike Holler, Executive Vice President of PeakLogix said: “Because our mission centers on solving current and emerging business challenges for our clients, the partnership with MOVU enables PeakLogix to provide a new portfolio of powerful solutions that solve operational problems.”
Unirope becomes first AWRF accredited member
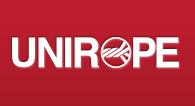
Unirope Limited was the first rigging shop to become an Associated Wire Rope Fabricators (AWRF) accredited member. Unirope completed a successful in-person audit, conducted by AWRF’s third-party auditors, the Lifting Equipment Engineers Association (LEEA). The AWRF Accreditation Program is a voluntary opportunity for all member companies and their affiliated branches. Using the current revision of AWRF RP&G, Recommended Practice for the Operation of Sling Shops, as a basis for evaluation, LEEA works with interested members to ensure compliance. In other words, the audit was developed by LEEA according to requirements set out by AWRF. Unirope—it is also a LEEA member—is a specialist in the manufacture, distribution, testing, certification, and inspection of high-performance wire rope and rigging products. It has additional facilities in Quebec and Alberta; the three sites combine to deliver service nationwide and to select customers in the U.S. and Europe. Justin Brown, president at Unirope, said: “There is a sense of pride that comes with being first across any line or to be the first to achieve a goal. That said, we undertook this as a project to support AWRF, our industry, and all the end users of rigging products that will in the future be looking for a way to distinguish quality rigging fabricators from the rest. “In three to five years, this program will be the benchmark in our industry. End users of rigging products will demand that they are produced by an AWRF Accredited Member and there will be a clear quality benchmark between those that can comply and those that cannot.” Having completed the audit, Unirope can now market itself as an AWRF Accredited Member, which includes the use of a logo that has recently been developed. The goals of the program are to ensure safer sling shop operation; to drive more business to member companies; and to help member companies win more market share—ultimately adding value to being a member. Brown said: “The third-party audit and accreditation is significant beyond AWRF membership—and it is important to know the difference. Membership alone brings a lot of benefits but simply being a member of a trade association doesn’t prove that you abide by its recommended best practices. It’s the difference between talking the talk and walking the walk.” Rallying call Interestingly, 25% of AWRF membership is from outside of the U.S. Half of the international contingent is based in Canada, and nearly all Canadian members are rigging shops. The AWRF Accreditation Program is not the same as being a LEEA accredited member. As Unirope proved, LEEA members must still proceed via the same processes as non-LEEA members—and Brown has urged all AWRF members, LEEA members and not, to join the program. He said: “Everything we do at Unirope starts with one basic idea that guides every decision. And that is the basic right that everyone who uses or comes into contact with our products gets to go home after their shift; we extend that idea to the entire industry, which is why we will encourage every rigging shop to gain accreditation. The more AWRF members that get on board, the safer our industry will become. Companies will find things during their audits that need to be changed or improved and implement those changes as part of this process. “The marketing power you gain by being accredited will prove invaluable. Accreditation demonstrates and sets a quality benchmark, exhibits accountability to the market, reduces risk, and increases efficiency. There are endless ways to cut corners in our industry, which is counter to the needs of such a high-risk sector. For example, things like die maintenance and verification of after-swage dimensions, are convenient to bypass or ignore, but critical to the performance of the final product.” The accreditation is valid for three years, with annual visits and check-ups. An audit must be completed for each location.
Wolter, Inc. secures strategic growth investment from BBH Capital Partners

Wolter, Inc., a provider of material handling solutions, automation, overhead cranes, industrial dock and door services, and power systems, is thrilled to announce a significant growth investment from BBH Capital Partners (BBHCP). This strategic partnership will enable Wolter to accelerate its expansion plans, including acquisitions and real estate investments, further solidifying its position in the industry. Founded in 1962 and based in Brookfield, WI, Wolter has become a trusted name in the material handling industry, offering an expansive range of services and solutions, including new and used equipment sales, service and training, robotics and automation, overhead cranes and hoists, standby power generators, and more. With a dedicated team of over 590 employees, Wolter serves a broad customer base across seven states, including Wisconsin, Northern Michigan, Indiana, Ohio, and Kentucky, with plans to expand into the mid-Atlantic, Southeast, and mid-South regions. Jerry Weidmann, President of Wolter, Inc., expressed his enthusiasm about the partnership, stating, “Our alliance with BBH Capital Partners marks a milestone in Wolter’s journey. Their investment and expertise will significantly enhance our ability to pursue strategic acquisitions and make impactful real estate investments, enabling us to serve our customers better and expand our market presence.” BBH Capital Partners, a private equity strategy of Brown Brothers Harriman & Co., is known for providing capital solutions to growth-oriented middle-market companies. Their minority investment in Wolter underscores their confidence in Wolter’s potential for continued growth and expansion. Matthew Salsbury, Co-Manager of BBHCP, commented, “We are proud to partner with Wolter and support their ambitious growth strategy. The company’s strong family values, commitment to excellence, and strategic vision align perfectly with our investment philosophy. We look forward to contributing to Wolter’s success in the coming years.” Robert W. Baird served as the exclusive investment banker for Wolter in this transaction, underscoring the strategic importance and potential of the partnership between Wolter and BBHCP. This investment is poised to continue making a significant impact on the material handling, overhead crane, industrial dock and door, and power systems sectors.
SVT Robotics enhances SOFTBOT® platform to maximize uptime
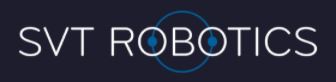
SVT Robotics™, a software provider empowering IT teams to seamlessly integrate, monitor, and scale automation, has expanded the SOFTBOT® Platform to include real-time monitoring capabilities. The updated SOFTBOT Platform now includes a single dashboard that can maximize uptime across disparate technologies and systems. The tech-agnostic SOFTBOT Platform allows companies to rapidly connect and orchestrate new automation with prebuilt, reusable and self-documenting integrations. Providing an alternative to traditional, custom-coded approaches, the platform enables organizations to easily scale and adapt to changing business requirements, all while driving innovation and lowering the total cost of ownership. With the expansion of the platform, IT teams will now be able to monitor their overall system health across multiple technologies and facilities. “Our customers know how important it is to reduce downtime when something goes wrong,” said A.K. Schultz, Co-Founder and CEO of SVT Robotics. “By automatically detecting issues and alerting individuals in real-time, the SOFTBOT Platform helps teams quickly identify the root cause of a system failure – which is critical to maximizing uptime and minimizing the financial impact of an incident.” Leveraging the SOFTBOT Platform not only provides robust monitoring, but the ability to empower an entire business in real-time with aggregated and normalized data from all connected technologies. This level of transparency has historically been challenging for teams with custom-coded integrations, but now IT owners can easily access a standard set of data across disparate technologies. Operators have real-time visibility and can take immediate action from insights, such as reallocating labor or optimizing facility operations, while other stakeholders use the data from multiple systems to better support resource planning. “IT teams tell us that they lack the resources and visibility to onboard, support and maintain new technologies at the rate their businesses demand,” said Nick Leonard, Senior Vice President of Products at SVT Robotics. “The enhanced SOFTBOT Platform changes the game for our customers, giving them a way to proactively support systems with multi-site monitoring and real-time alerting.”
FOX IV’s new, high-performance automated label print and apply system at MODEX 2024.
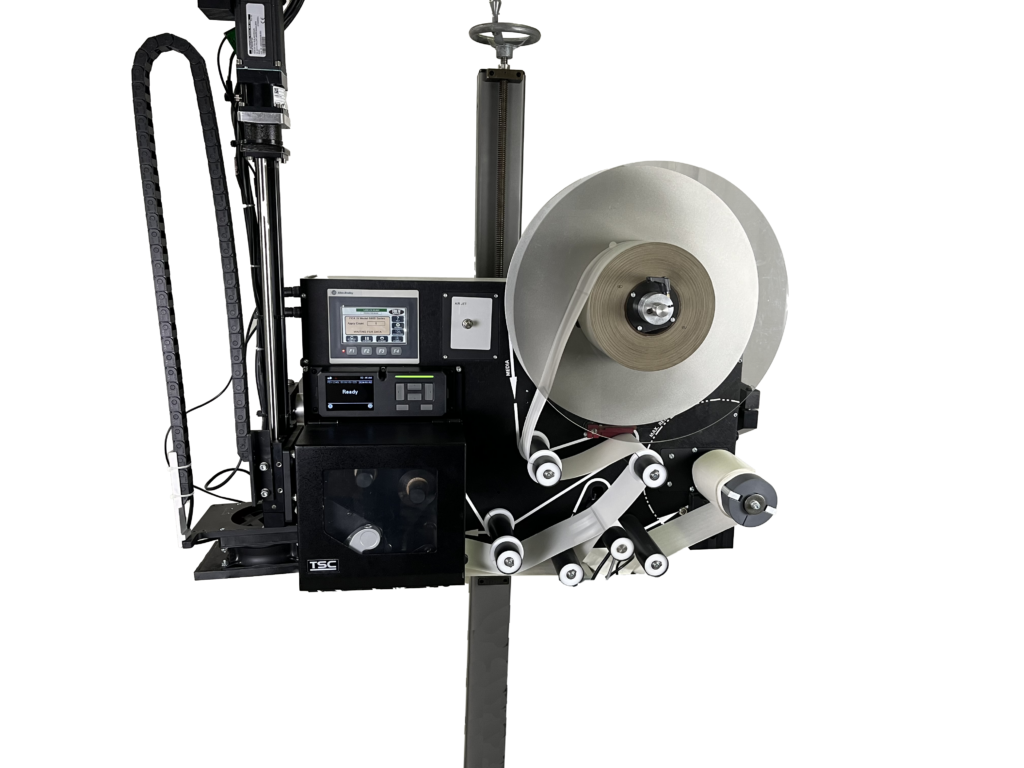
FOX IV Technologies, a label print and apply equipment design, will proudly introduce the FOX IV 6974 Label Printer-Applicator at MODEX 2024. With a TSC/Printronix print engine integrated into FOX IV’s upgraded Series 8 industrial design, the 6974 provides flexibility, durability, and compatibility in one user-friendly automated labeling system. The heart of the system is the TSC/Printronix PEX-2000 print engine. The PEX-2000 is designed for durability and high performance for all types of automated labeling applications. The die-cast structure and robust metal chassis provide a stable media path for outstanding print quality and accuracy while withstanding even harsh environments. Print speeds up to 18 ips are achieved with precise label positioning. FOX IV’s new Series 8 body design incorporates the TSC/Printronix print engine into a precision-engineered center wall that virtually eliminates label tracking or breakage. With an upgraded heavy-duty backing rewind system, extra-large 16” OD label roll capacity, and intuitive color control displays, the 6974 is ideal for manufacturing and logistics applications where reliable, extended-run label printing and application are expected. Additionally, both the Allen-Bradley control system and addressable Ethernet I/O enable faster and easier integration into production and fulfillment lines. The 6974 is compatible with most major label printer languages, making it simple to use in a mixed print engine environment, on a new line, or as a replacement for other labeling systems. It comes standard with TSPL-EZD printer language, which is compatible with EPL, ZPL, ZPL II, and DPL. Optionally, the TSPL-EZS printer language, compatible with EPL, ZPL, ZPL II, and SBLPL, can be requested. This means that whatever your current label print stream – Zebra, Datamax, Eltron, or SATO – the 6974 gives you out-of-the-box compatibility and ease of installation for new or existing labeling applications. Key features and options are available to customize the 6974 to meet specific application requirements. Print resolutions of 200, 300, and 600 dpi provide quality printing no matter the size or character. The optional RFID module enables encoding, printing, and application of RFID tags onto products or packaging while the Ribbon Saver option maximizes thermal ribbon use, reducing the cost of production and minimizing ribbon waste. The 6974 also features a small label mode capable of printing labels as small as 5 mm in height. Additionally, the 6974 includes many user-friendly features: our Swing-away cylinder and open head design enable clear access to the print head and rollers for cleaning or threading purposes, printed label and ribbon paths allow for ease of media threading, and simple to remove printheads facilitate ease of replacement and cleaning. Standard label application options include varying lengths of pneumatic and electric cylinders, two-panel labeling, tamp, tamp-blow, tamp-roll, and merge/wipe. Other application options such as rotary actuators, multi-axis applicators, and vacuum belt applicators are also available. For unique applications, FOX IV’s in-house engineering team can design a labeling system to meet a customer’s specific requirements.
Toyota’s Brett Wood re-elected as Chairman of Industrial Truck Association
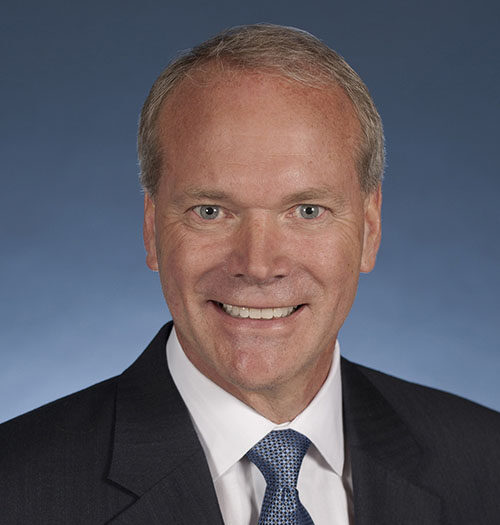
Toyota Material Handling North America President and CEO, Brett Wood, serves a second term as Industrial Truck Association Chair Toyota Material Handling North America President & CEO (TMHNA) Brett Wood remains at the forefront of the material handling industry as the second individual in the 70-year history of the Industrial Truck Association (ITA) to be elected twice as Chair of the Board of Directors, effective January 1. Wood has served in various roles during his three decades with the ITA. During his first term as ITA chairman from 2015 to 2018, Wood was pivotal in establishing the ITA’s economic impact report Lifting America: The Economic Impact of Industrial Truck Manufacturers, Distributors and Dealers. This marked a significant milestone as the first-ever initiative to quantify material handling statistics that provide invaluable insights to the industry. “I am honored to serve as a champion for the ITA, to drive positive change and promote the impact of the powered industrial truck industry,” said Wood, who also serves as a Senior Executive Officer for TMHNA’s parent company – Toyota Industries Corporation. “The ITA serves as an invaluable resource to its members, creating industry-wide initiatives and driving positive change for the collective whole and all who work closely with powered industrial trucks.” As chair, Wood collaborates with the executive board to determine ITA’s strategy, communicates the association’s position on industry issues and drives industry-wide initiatives, and promotes the positive impact the powered industrial truck industry has on the global supply chain. By embodying Toyota’s culture of Kaizen – or continuous improvement – and upholding Toyota’s core values, Wood’s leadership is integral in advancing and promoting the vital role industrial trucks play in manufacturing, warehousing, logistics, and distribution. “We are thrilled to welcome Brett as the Chair of the ITA’s Board of Directors,” said Brian Feehan, President of ITA. “His leadership and deep industry expertise will be invaluable assets as we continue to drive member value and raise awareness on safety.” Wood championed the founding of National Forklift Safety Day, an annual event dedicated to reinforcing safety protocols and practices among forklift manufacturers. The 11th National Forklift Safety Day will be held on June 11, 2024, in Washington, D.C. This initiative continues to serve as a testament to Wood’s commitment to prioritizing operator safety and promoting safety standards.
U.S. Rail report for February & the week ending March 2, 2024
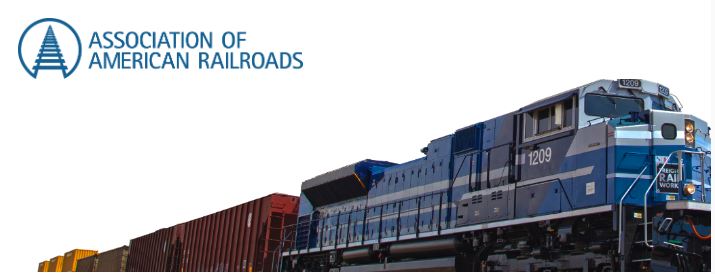
The Association of American Railroads (AAR) has reported U.S. rail traffic for the week ending March 2, 2024, as well as volumes for February 2024. U.S. railroads originated 885,548 carloads in February 2024, down 1.3 percent, or 11,410 carloads, from February 2023. U.S. railroads also originated 1,040,312 containers and trailers in February 2024, up 10.9 percent, or 102,140 units, from the same month last year. Combined U.S. carload and intermodal originations in February 2024 were 1,925,860, up 4.9 percent, or 90,730 carloads and intermodal units from February 2023. In February 2024, 13 of the 20 carload commodity categories tracked by the AAR each month saw carload gains compared with February 2023. These included: motor vehicles & parts, up 6,777 carloads or 12.3 percent; chemicals, up 6,522 carloads or 5.1 percent; and grain, up 4,971 carloads or 6.3 percent. Commodities that saw declines in February 2024 from February 2023 included: coal, down 31,912 carloads or 11.7 percent; crushed stone, sand & gravel, down 8,037 carloads or 10.1 percent; and nonmetallic minerals, down 1,467 carloads or 12.7 percent. “In February, U.S. rail traffic recovered from disruptions caused by severe winter weather in January. However, a closer look at February’s rail traffic data shows elements that inspire optimism and elements that call for caution,” said Dr. Rand Ghayad, the newly appointed Chief Economist at the Association of American Railroads. “Intermodal volumes have consistently grown over the past six months, signaling increased confidence among consumers and retailers. At the same time, carloads of industrial products remain below levels from last spring and summer, reflecting ongoing challenges in the industrial sector. “Looking ahead, we hope to see improvements in manufacturing output and consumer spending, which are key drivers of rail transportation. This comes as the goods-producing sector begins to rebound from the stagnation experienced in the sector following the post-COVID-19 period.” Excluding coal, carloads were up 20,502 carloads, or 3.3 percent, in February 2024 from February 2023. Excluding coal and grain, carloads were up 15,531 carloads, or 2.8 percent. Total U.S. carload traffic for the first two months of 2024 was 1,910,716 carloads, down 4.6 percent, or 91,135 carloads, from the same period last year; and 2,246,326 intermodal units, up 7.9 percent, or 165,335 containers and trailers, from last year. Total combined U.S. traffic for the first nine weeks of 2024 was 4,157,042 carloads and intermodal units, an increase of 1.8 percent compared to last year. Week Ending March 2, 2024 Total U.S. weekly rail traffic was 483,138 carloads and intermodal units, up 3.9 percent compared with the same week last year. Total carloads for the week ending March 2 were 220,406 carloads, down 4.3 percent compared with the same week in 2023, while U.S. weekly intermodal volume was 262,732 containers and trailers, up 12.0 percent compared to 2023. Eight of the 10 carload commodity groups posted an increase compared with the same week in 2023. They included motor vehicles and parts, up 1,625 carloads, to 15,890; metallic ores and metals, up 1,525 carloads, to 19,732; and miscellaneous carloads, up 1,303 carloads, to 8,939. Commodity groups that posted decreases compared with the same week in 2023 were coal, down 14,965 carloads, to 57,929; and nonmetallic minerals, down 1,797 carloads, to 28,835. North American rail volume for the week ending March 2, 2024, on 10 reporting U.S., Canadian and Mexican railroads totaled 324,643 carloads, down 4.6 percent compared with the same week last year, and 344,823 intermodal units, up 10.9 percent compared with last year. Total combined weekly rail traffic in North America was 669,466 carloads and intermodal units, up 2.8 percent. North American rail volume for the first nine weeks of 2024 was 5,792,102 carloads and intermodal units, up 0.9 percent compared with 2023. Canadian railroads reported 89,148 carloads for the week, down 3.6 percent, and 71,183 intermodal units, up 9.2 percent compared with the same week in 2023. For the first nine weeks of 2024, Canadian railroads reported a cumulative rail traffic volume of 1,393,380 carloads, containers and trailers, down 2.3 percent. Mexican railroads reported 15,089 carloads for the week, down 14.0 percent compared with the same week last year, and 10,908 intermodal units, down 2.2 percent. Cumulative volume on Mexican railroads for the first nine weeks of 2024 was 241,680 carloads and intermodal containers and trailers, up 4.7 percent from the same point last year. To view the weekly rail charts, click here.
Episode 467: Driving warehouse efficiency with autonomous forklift products from VisonNav
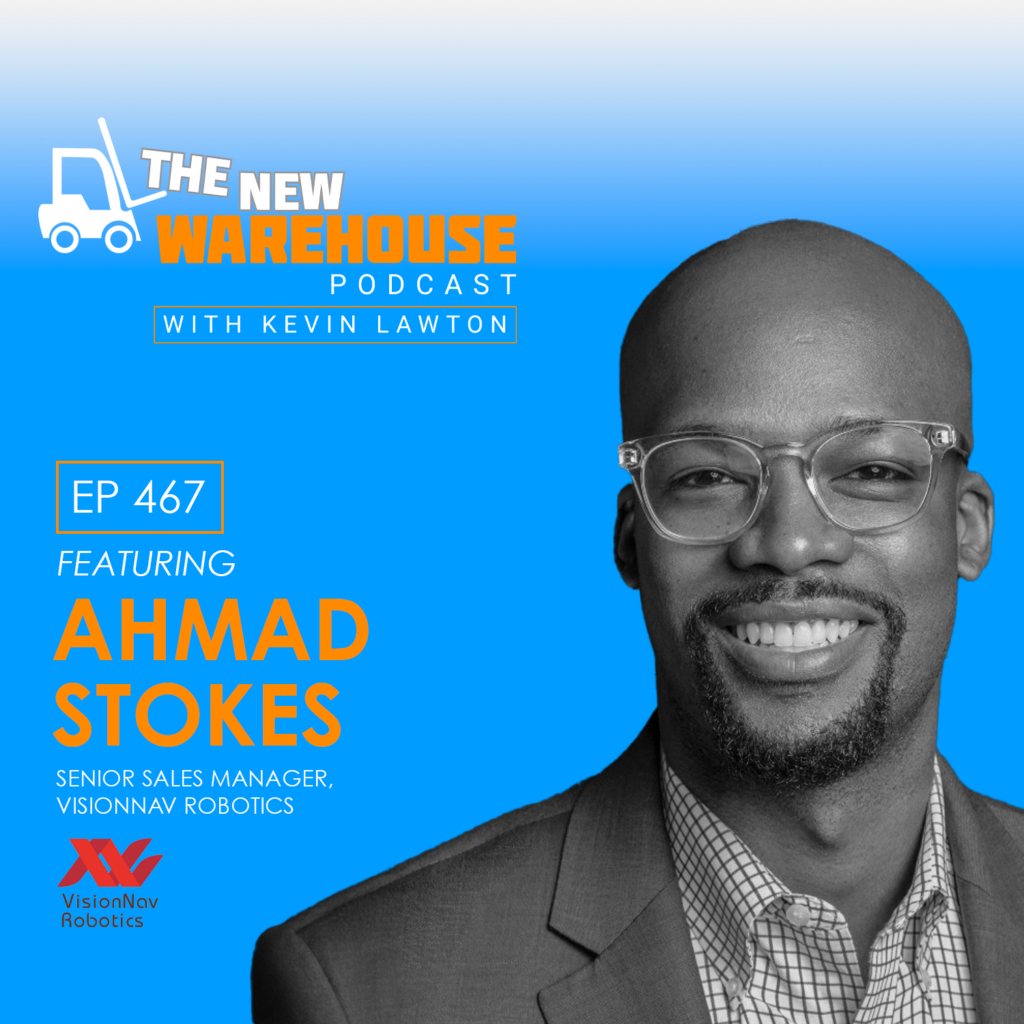
In this episode of The New Warehouse Podcast, we delve into the transformative power of automation in warehousing and logistics with Ahmad Stokes, Senior Sales Manager at VisionNav Robotics. VisionNav is leading the charge in autonomous warehousing solutions, breaking new ground with its “infrastructure-free” approach to automation. Ahmad delves into VisionNav’s cutting-edge technologies and their comprehensive suite of autonomous forklift products, including a glimpse into VisionNav’s new trailer loading and unloading solution they are featuring at Modex 2024. VisionNav’s Unique Approach to Automation VisionNav Robotics stands out in the warehouse automation landscape with its “infrastructure-free” approach, leveraging advanced technologies to address the unique demands of modern logistics. Ahmad shares, “We are infrastructure-free, but what separates us…is our ability to perceive not only standard pallets but unique payloads.” This capability is powered by a blend of 3D, LIDAR, ultrasonic, photoelectric, and image-sensing technologies, enabling VisionNav’s vehicles to handle various tasks with precision and adaptability. Optimizing Space with Autonomous Forklift Products The logistical landscape faces constant challenges, from space optimization to improving operational efficiency. VisionNav Robotics addresses these issues by providing solutions that allow warehouses to maximize their space utilization—a crucial advantage as warehouse rent prices soar. By automating complex tasks, such as handling diverse payloads and navigating intricate spaces, VisionNav’s autonomous forklift products offer a solution that enhances productivity while reducing the need for extensive manual labor. Solving Modern Warehousing Challenges with Autonomous Forklift Products Looking ahead, VisionNav Robotics is not just content with the status quo but is actively pushing the boundaries of what’s possible in warehouse automation. Ahmad shares, “Our solution is capable of handling full, closed pallets, a unique feature distinguishing it from other products.” This will be on full display in booth C4075 at Modex 2024. This innovation represents a significant leap forward, showcasing VisionNav’s commitment to developing autonomous forklift products that set the stage for a more efficient, agile, and futuristic supply chain ecosystem. Key Takeaways Emerging technologies in warehouse automation can now handle a wide variety of payloads with precision, drastically enhancing operational flexibility and efficiency. As warehouse operational costs rise, innovative solutions are crucial for maximizing space utilization and streamlining processes, addressing the pressing need for cost-effective logistics operations. The industry continues introducing groundbreaking solutions for challenges like trailer loading and unloading, indicating a shift towards more agile, future-ready warehousing strategies. The New Warehouse Podcast EP 467: Driving Warehouse Efficiency with Autonomous Forklift Products from VisonNav
KEEN Utility Arvada Shift perfect for long hours on your feet
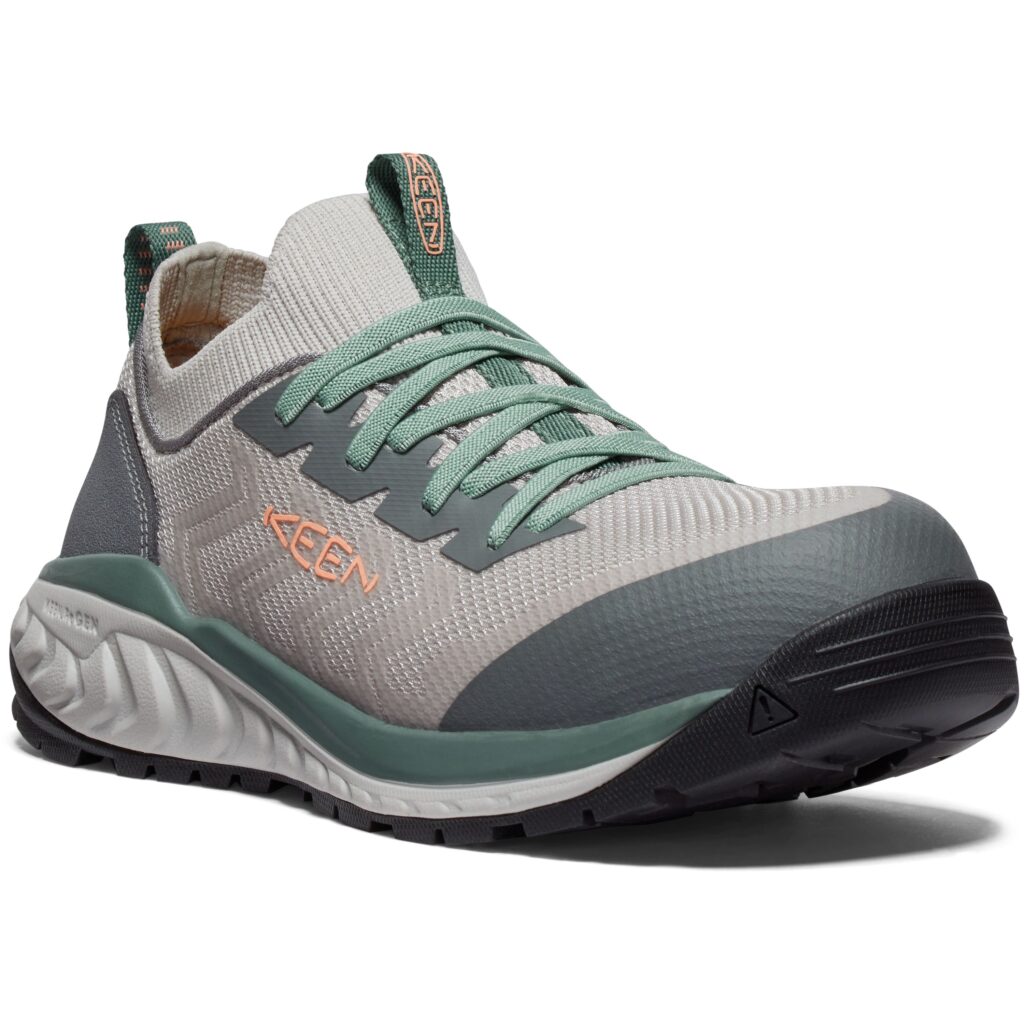
New for Spring ‘24, KEEN Utility’s Arvada Shift is designed for jobs requiring constant movement and long hours on your feet. With an elastic-equipped slip-on fit for easy transitions into work mode, this work sneaker is a perfect blend of athletic-level cushioning and style. Standout highlights include a lightweight, compression-resisting KEEN.ReGEN midsole that returns 50% more energy than standard EVA foam and a sneaker-like ultra-breathable mesh upper to keep feet cool. At the same time, the Arvada Shift does not sacrifice when it comes to safety offering asymmetrical carbon-fiber safety toes that are unobtrusive and 15% lighter than steel and an EH-rated oil-and-slip-resistant rubber outsole provides dependable footing. Combining energy-returning job site performance and convenience for the modern worker, the Arvada Shift will be available for both men and women in several colorways as well as an ESD option.
Episode 466: Outerspace empowers brands with personalized 3PL services
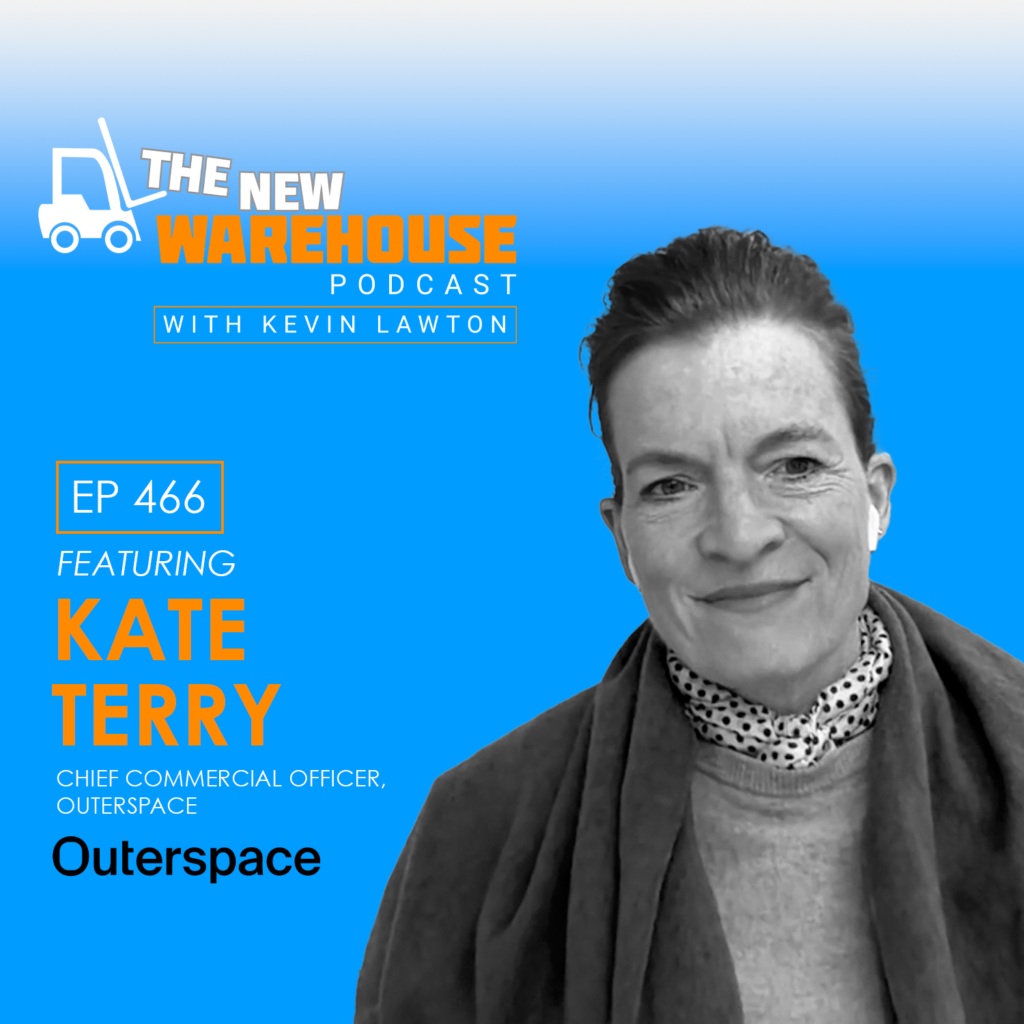
In this captivating episode of the New Warehouse podcast, we discuss personalized 3PL services with Kate Terry, Chief Commercial Officer at Outerspace. Outerspace is a full-service 3PL specializing in high-touch brands and customer experiences. Outerspace, born from the founders’ frustration with existing 3PL services, has swiftly transitioned into a multi-channel, national powerhouse, prioritizing the brand’s perspective in every operation. Join us as Kate shares invaluable insights into creating memorable shopping experiences that foster business growth. From Brand Owners to Logistics Pioneers As brand owners themselves, Outerspace’s inception story is a testament to turning frustrations into opportunities. After working with a few 3PLs, the founders brought fulfillment in-house. They did it so well other brands came to them and asked them to take over their fulfillment. Kate adds that they decided to make a go of Outerspace with the premise: “We would like to run the operation the way we would want to be treated if we were the brand.” Outerspace’s ability to execute personalization at an unmatched speed exemplifies its commitment to understanding and serving brand needs. The Art of Personalized 3PL Services Kate covers the level of detail it takes and why it’s not easy for 3PLs to make personalization a strong suit. “There’s a great deal of specialized knowledge. You have to be able to do that well and have an eye for detail.” By offering services like custom handwritten notes and tissue wrapping and advanced personalization techniques such as embroidery, laser engraving, and UV printing, Outerspace elevates the customer experience. This level of personalized 3PL services helps brands stand out, drives loyalty, and underscores a unique approach to logistics and differentiation. A Partnership for Growth Outerspace differentiates itself by viewing its relationship with brands as not a mere transaction but a collaborative partnership aimed at mutual growth. Kate emphasizes this philosophy: “Anything we can do to make their business grow, we will grow.” This mindset of investing in the client’s success ensures Outerspace delivers on core services while contributing to the brand’s expansion. Outerspace’s commitment to acting as an extension of the brand’s team exemplifies a forward-thinking approach that redefines the role of a 3PL provider in today’s competitive market. Key Takeaways Embracing transparency within logistics can dramatically enhance operational efficiency and build trust across the supply chain. Offering personalized 3PL services transforms customer interactions into unique experiences, setting a brand apart. Adopting a partnership-oriented logistics approach fosters innovation and propels mutual growth. The New Warehouse Podcast EP 466: Outerspace Empowers Brands with Personalized 3PL Services
Forklift-International and Material Handling Wholesaler will be at MODEX 2024
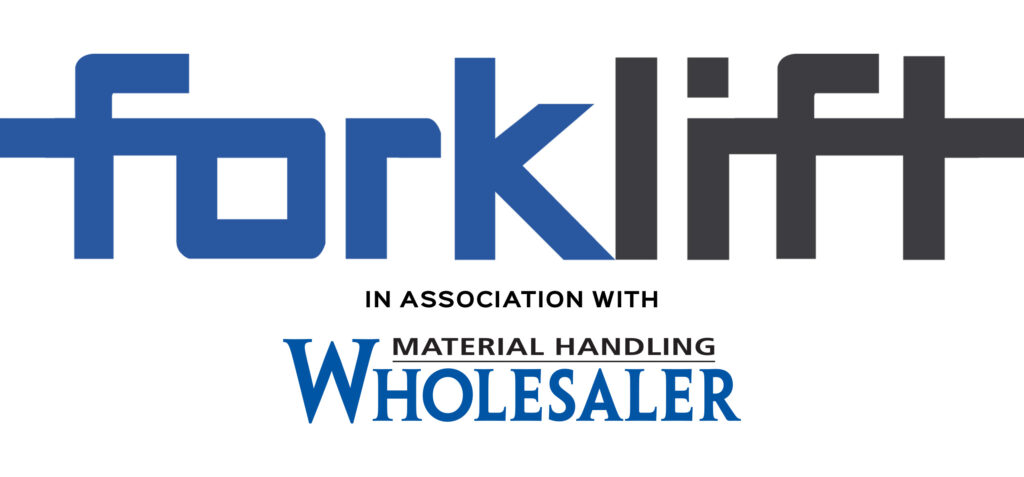
Forklift International.com and Material Handling Wholesaler will have a booth at MODEX 2024 on March 11 – 14 in Atlanta, GA. All industrial equipment dealers should stop by booth #B7214 and demo the Forklift software and see how you can get your equipment online, plus much more. There will be a special offer for dealers who sign up for an annual dealer membership. Stop by the booth for details. Forklift-International.com is the largest online market for used forklifts, attachments, and work platforms.