MAN automates production logistics with 12 Magazino SOTO robots
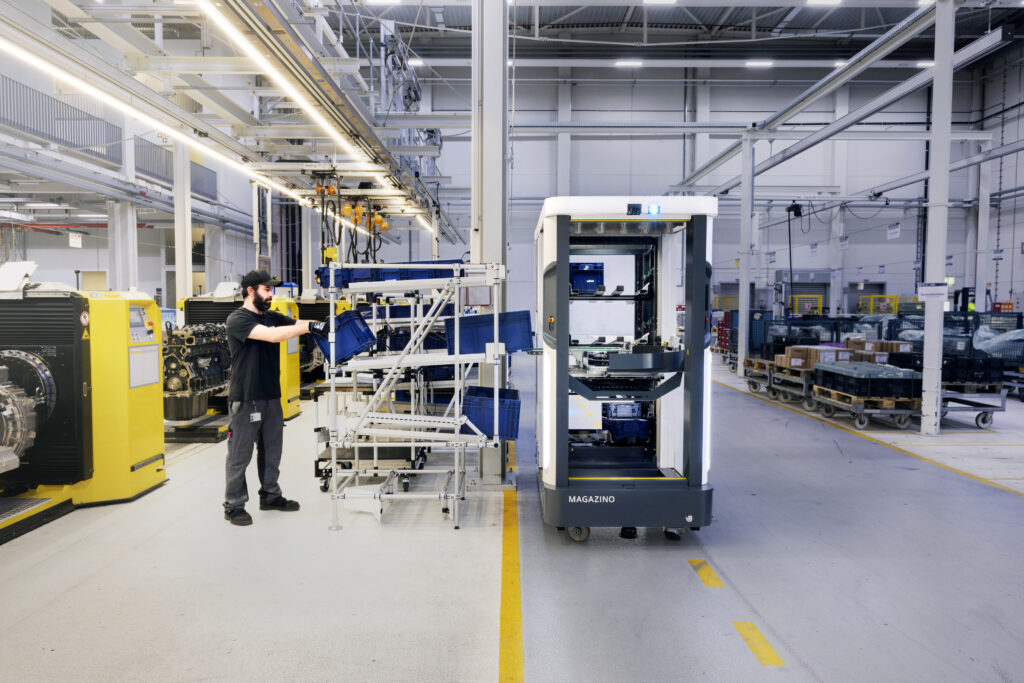
The Munich-based robotics company Magazino, which belongs to Jungheinrich, has won the MAN site in Nuremberg as a fleet customer for the SOTO robot. The SOTO mobile robot automates material supply between the warehouse and assembly line, transporting small load carriers (SLCs) completely autonomously. Following a one-year pilot project, the entire small load carrier supply process for engine assembly and future battery production will be automated with twelve SOTO robots starting in the autumn of this year. Magazino and MAN have been working together closely and in an application-oriented manner in the field of logistics automation since 2019 and have already pooled their specific expertise during the development phase of the SOTO robots. The functionality of the robots was extensively tested and optimized in live operation during a one-year pilot phase. Based on this positive trial, the MAN site in Nuremberg decided to deploy a fleet of twelve SOTO robots for the complete automation of small parts logistics. Simon Becker, project manager at MAN, says: “The introduction of SOTO marks a further step towards the future of logistics in the latest development of our plant in Nuremberg. Thanks to SOTO, the provisioning process with small load carriers is now also fully automated. These robots are, therefore, also exemplary for the ongoing digitalization and automation of our plant logistics and thus contribute to our overarching strategy. It is impressive to see how efficiently and harmoniously humans and robots can work together. The decision to introduce the SOTO robots is the result of many years of trustful cooperation with Magazino, which reflects our commitment to technological excellence and continuous improvement.” Markus Ruder, Magazino’s project manager for the joint project with MAN, describes the target process as follows: “The SOTO robots pick up the small load carriers independently at the automated mini-load warehouse and each robot brings up to 18 containers at a time to the individual assembly lines. They work in the same environment as humans and other mobile robots. At the assembly line, the SOTO robots place the containers, which currently weigh 12kg, directly onto the shelves. The worker can then conveniently access the individual parts for assembly on the opposite side of the rack. The SOTO robot also picks up empties autonomously and takes them to the central collection point.” The plant in Nuremberg uses standard container formats by the VDA standard, the German Association of the Automotive Industry. The robot’s adaptive gripper automatically adjusts to the corresponding container size and, like humans, also flexibly moves to different heights of the transfer racks. The robot uses machine-readable codes on the shelves and labels on the containers for identification. It receives the transport orders directly from the warehouse management system. While assembly lines in the manufacturing industry are highly automated today, replenishment in the vast majority of warehouses still takes place manually. Previous solutions, such as tugger trains or simple automated guided vehicles (AGVs), do not fully automate the process, as manual labor is required for loading and unloading. At MAN’s Nuremberg site, the small load carriers are already automatically de-palletised after delivery and stored in the automated miniload warehouse. With SOTO, MAN is now automating the “last mile” in the small load carrier provision process with the aim that the first human action in the process is the transfer of the empty small load carriers from the full load chute to the empties chute of the rack by the assembly workers, from where the robot collects the small load carriers again. The SOTO robot combines these elementary logistical process steps in a single, fully autonomous solution: picking up small load carriers of different sizes from a warehouse, autonomous transport of several small load carriers from source to sink and delivery to flow racks close to the line at different heights. Its capabilities include collecting empties and rotating small load carriers. In existing environments, the robot works safely in the same area as humans. These capabilities clearly set the SOTO robot apart from the market environment and enable genuine end-to-end automation in material supply with small load carriers for the first time.
Episode 464: Making the most of returns with Patturn’s Innovative Approach to Re-Commerce
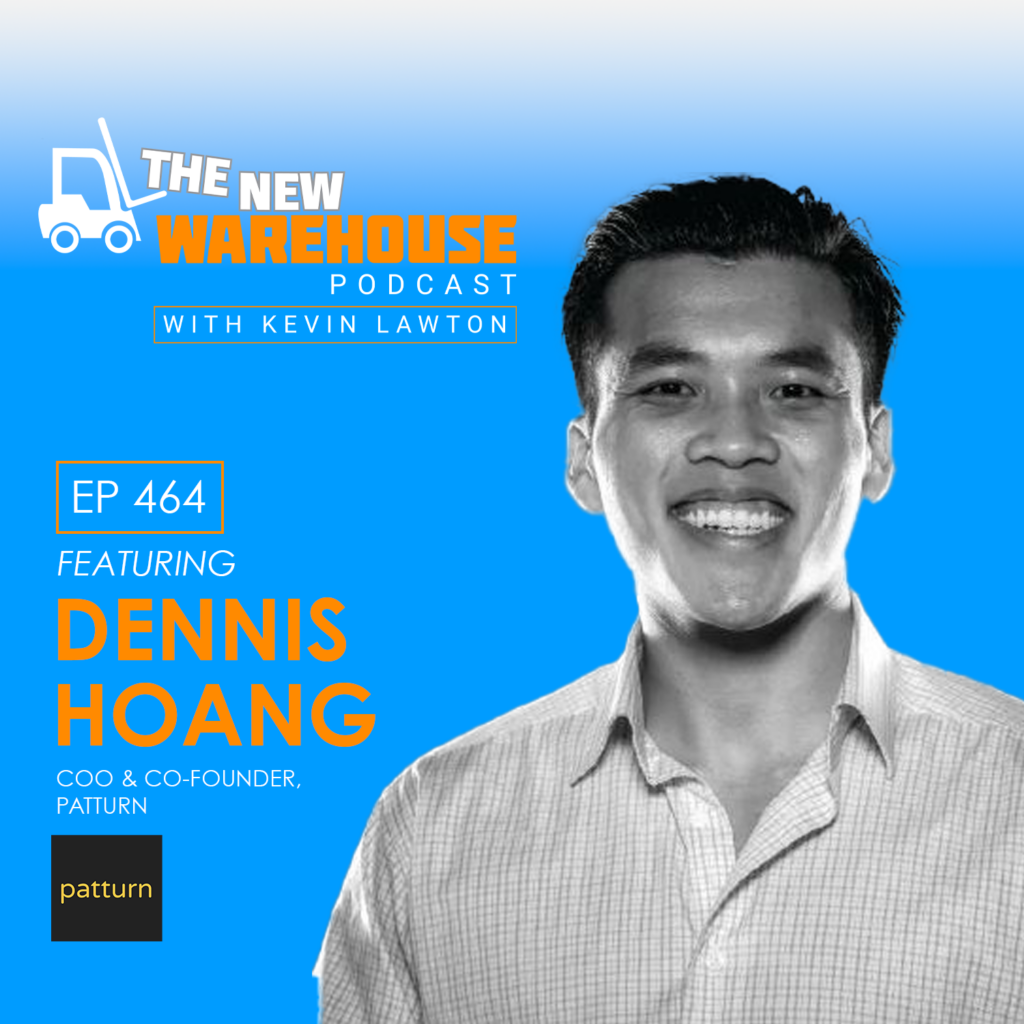
In this episode of The New Warehouse Podcast, Dennis Hoang, COO and Co-Founder of Patturn, delves into the innovative world of returns and re-commerce. Patturn is pioneering a shift in how companies manage this challenge, making the process simpler and more efficient. Dennis shares insights into Patturn’s origins, sparked by a personal connection to the challenges faced by small businesses and how these challenges inspired the creation of a comprehensive solution that is Patturn. The Returns Dilemma: Consumer Ease vs. Supply Chain Efficiency Hoang underscores the unique complexities within returns management, driven by its item-specific demands and the substantial variability in returned items. He reveals a critical market void for an all-encompassing solution that adeptly merges technological capabilities with the essential human elements of the returns process. Hoang notes, “On average, 30% of what people buy is being returned…but every retailer makes it easy because they want to keep their customers.” While beneficial for customer retention, this consumer-friendly policy introduces significant operational challenges for retailers. Identifying the need for a solution and an aim to simplify and streamline returns led to the creation of Patturn. The Patturn Return Process Dennis Hoang details Patturn’s comprehensive approach to managing retail returns, emphasizing efficiency and resale optimization. Here’s how Patturn transforms the process: Bulk Inventory Management: Retailers send returns inventory to Patturn by pallet or truckload. Inspection and Tracking: Items go through inspection and receive a unique license plate for tracking purposes. Resale Across Marketplaces: Patturn handles the resale of items across various marketplaces and channels, including their own platforms. Storage and Forward Logistics: Beyond processing and reselling, Patturn manages the storage and forward logistics, streamlining the journey. Hoang highlights the “resale magic” that Patturn leverages, transforming returns into resalable inventory, aka “re-commerce,” thus recapturing value and minimizing waste. Mastering Inventory Management Hoang discusses the importance of aligning inventory with consumer demand, a seemingly straightforward strategy that necessitates a deep understanding of market trends, such as the seasonal popularity of certain products. This approach is fundamental to avoiding stockpiles of unsellable items and ensuring that inventory remains relevant and desirable to consumers. Beyond mere alignment with seasonal trends, Hoang delves into the critical role of analytics and the liquidation of stagnant inventory. From Hoang’s perspective, he believes the rate of returns is likely to increase, even with potential deterrents like return fees. Key Takeaways Patturn is filling a significant gap in the market with its end-to-end returns management solution. The complexity of returns management lies in the item-specific nature of the process, requiring both technological and manual oversight. 30% of products are returned and require effective re-commerce strategies to transform potential losses into opportunities. The New Warehouse Podcast EP 464: Making the Most of Returns with Patturn’s Innovative Approach to Re-Commerce
LOGiQ combines yard management and weighing technology fully automatically
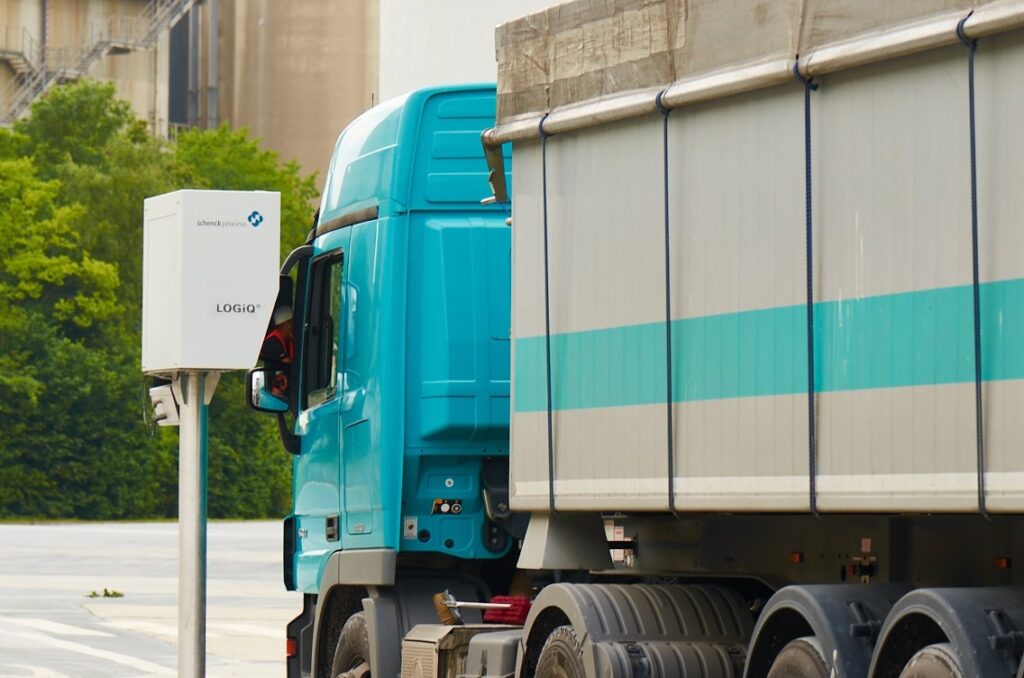
Schenck Process, a process-critical bulk materials application, offers the LOGiQ yard management system, a cloud-based software solution that combines smooth and efficient truck loading operations with fully automated weighing of bulk materials – supported by log-on terminals, which are also part of the LOGiQ product family. LOGiQ is a proven system in the cement and steel industry. However, the solution is also suitable for yard management in other segments of industrial production. LOGiQ handles all logistical steps from the entry of an authorized truck onto the company premises to the exit in a seamless process. The software system monitors and controls access, supports weighing processes, ensures correct loading and records all relevant data without delays. Multilingual terminals included in the LOGiQ complete package Access is controlled via LOGiQ registration terminals, which are intuitive to use and available in several languages on request. The truck drivers operate these terminals themselves and record their weighing processes and all steps during loading and unloading. The processes run automatically without the need for manual intervention by staff: “zero-touch fulfillment”. This reduces the susceptibility to errors in the process and increases safety. The basic need for personnel on the factory premises is also noticeably reduced thanks to automation. In addition, the responsible employees and support staff at Schenck Process can access and support all data in real time, regardless of location, if required.
Morse Watchman’s see growing adoption of KeyWatcher Touch solutions across the globe
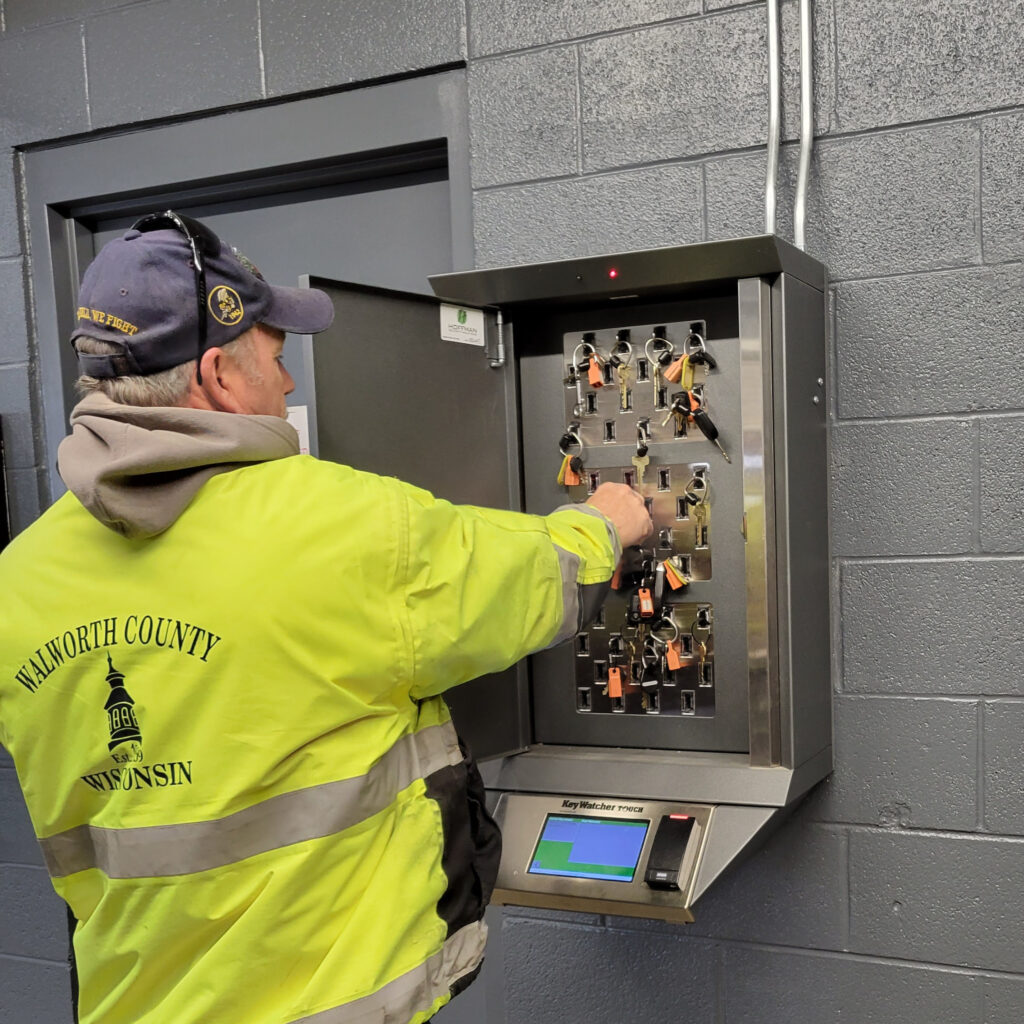
The company’s flagship system is lauded by small municipalities and medium-sized cities that rely on the use of physical keys to secure their property and assets Morse Watchmans, a key control and asset management system, reports a rising number of international cities and municipalities installing the company’s flagship key control system, KeyWatcher® Touch, to secure the buildings, equipment, and vehicles utilized by various municipal departments. “From public works to waste departments, courthouses, and beyond, the adoption of our KeyWatcher Touch solution continues to resonate positively across so many diverse cities,” said Tim Purpura, VP of Global Sales and Marketing, Morse Watchmans. “We take pride in knowing that our systems are being used to facilitate secure and efficient operations for some of the public’s most critical services.” By implementing effective municipal key control measures, cities can mitigate the risks associated with unauthorized key access while maintaining the operational integrity of public works. This proactive approach not only safeguards against potential security breaches but also fosters accountability and responsible use of resources among city employees. In this way, cities and municipalities can establish a foundation of trust and confidence within their communities. In one instance, the Walworth County Public Works Department in Wisconsin implemented a new KeyWatcher Touch system after the original key box system failed to adequately support the county’s hundreds of keys for government buildings and county fleet vehicles. After seeing the success of the KeyWatcher Touch solution at the Department of Public Works, other departments within Walworth County have also begun installing their own KeyWatcher Systems. “These boxes are starting to catch on, and departments are thinking about how they will use them for vehicles and building keys,” said John Miller, Senior Project Manager, Walworth County Public Works. Across the globe, the operational efficiencies of the KeyWatcher Touch solution are also appreciated. Blacktown City, a suburban community located approximately 22 miles west of Sydney, Australia, implemented a KeyWatcher Touch system at their Main Works Depot to help maintain usage accountability and eliminate the problem of missing or overdue vehicles, machinery, and building keys. “We manage keys for at least 500 vehicles and machines here at the Depot and each of them has at least two to three sets of keys,” said Joe Haddad, Facility Manager, Blacktown City Main Works Depot. “Without the KeyWatcher Touch automated control and tracking, the job of accurately keeping track of these many keys would be almost impossible.”
Securely fasten loads
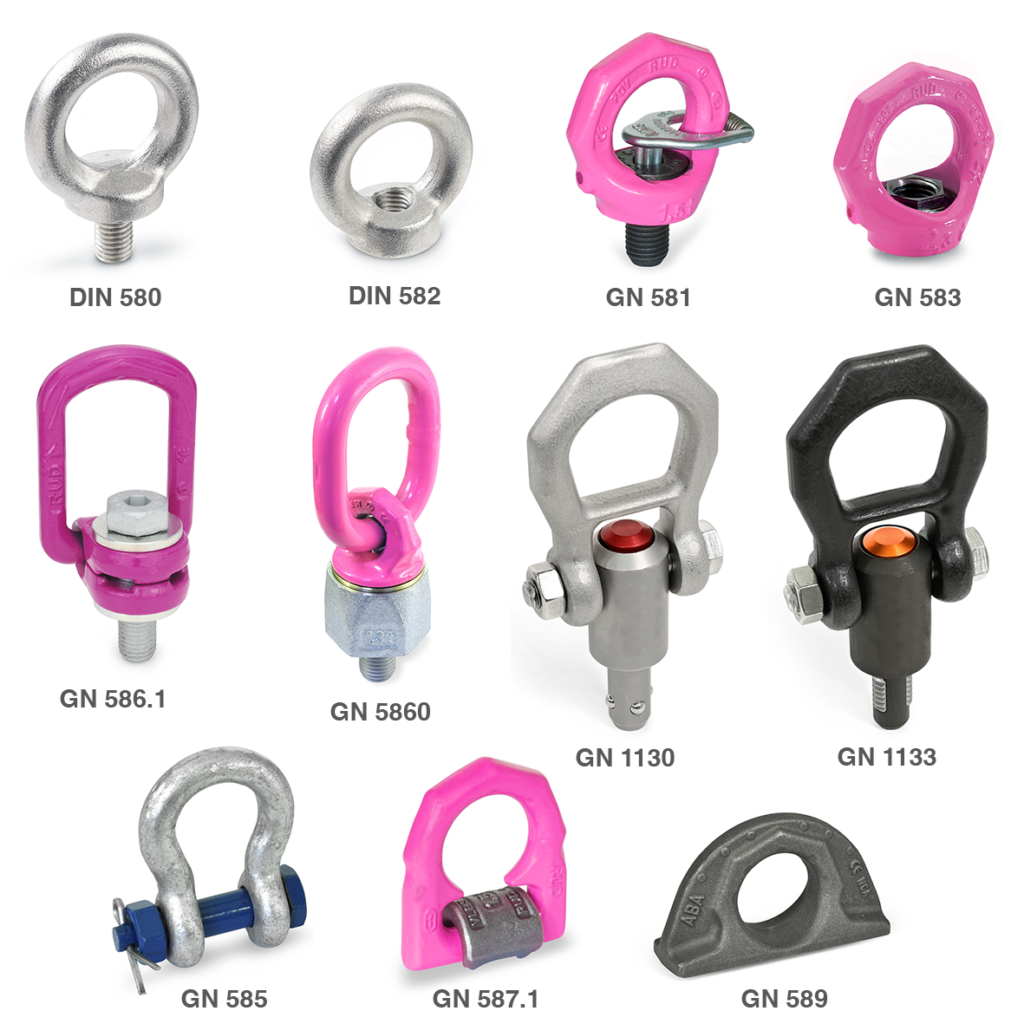
A crane, rope, or chain may be required when something needs lifting – plus anchoring points on the load. JW Winco offers a wide range of solutions to fasten the load securely. The classic and simplest lifting points are lifting eye bolts, when a female threaded hole is present the DIN 580, lifting bolt is used, when a male threaded stud is present a female DIN 582 is used. JW Winco offers these standard parts in steel and stainless steel. JW Winco’s portfolio reveals far better and stronger lifting points that are optimized for specific materials and easier to handle. The integrated RFID tags make it possible to clearly identify specific lifting points during wear and safety inspections and manage them digitally and without system interruption. Such RFID tags can be found in the lifting eye bolt GN 581 and the lifting eye nut GN 583, which can rotate around their vertical axis even after installation. These options also identify load rings GN 586.1, although the lifting eye can be folded down. And thanks to the eye ring with ball bearing, load rings GN 5860 are fully rotatable even under load. Load rings GN 587.1 are not screwed in but welded on. This load ring is also suitable for outdoor applications since the design of the weld-on block permits a closed seam that is safe from corrosion. The ring can swivel 180 degrees, and an optionally integrated spring can secure it in any position. The lifting point GN 589 for welding can accept loads from any direction and impresses with its minimal height. This is an essential feature when the maximum hook height of the lifting equipment is limited. A practical alternative to threaded or welded solutions is the mounting bolt solution, predestined, for example, for devices or tools that change position frequently and quickly. GN 1130 operates according to the lifting pin principle with axial locking and a release button. The new threaded lifting pin GN 1133 eliminates the time-consuming process of screwing into and out of the thread on the load. Rather than balls, this part uses threaded segments that are retracted and extended at the push of a button to create a positive connection. The integrated shackle, which rotates 180 degrees, connects to the lifting gear. The shackles GN 585 are based on the US standard RR-C-271 and feature a significantly higher load capacity than the DIN version.
PTDA welcomes three new members
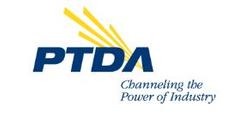
The Power Transmission Distributors Association (PTDA), an association for the industrial power transmission/motion control (PT/MC) distribution channel, welcomes three new members. Distributor Pacific International Bearing, Inc. has been a leading supplier of bearings and related products to OEMs in the aerospace, miniature, commercial, military and industrial sectors for more than 30 years. The company also offers bearing cleaning and relubrication in its designated Class 10,000 clean room. Manufacturer Reliable Bronze & Manufacturing, Inc., founded in 1968, manufactures its proprietary R-Lube® and R-Con® cast bronze bearings, bushings, bearings, wear plates, customized powder metal bushings, and made-to-order products. Additionally, the company builds custom graphite parts, grooving, and other product alterations. Associate Blue Meteor Inc. leverages artificial intelligence and Cloud technologies to provide easy-to-use B2B and B2C product data management solutions. Its proprietary products—DataBridge, AmazePXM, and DataXchange—seamlessly integrate with any enterprise Product Information Management (PIM) or Master Data Management (MDM) solution. The Power Transmission Distributors Association (PTDA) is the leading global association for the industrial power transmission/motion control (PT/MC) distribution channel. Headquartered in Chicago, PTDA represents power transmission/motion control distribution firms that generate more than $19 billion in sales and span more than 2,500 locations. PTDA members also include manufacturers that supply the PT/MC industry. PTDA is dedicated to providing exceptional networking, targeted education, relevant information and leading-edge business tools to help distributors and manufacturers meet marketplace demands competitively and profitably.
Reliance label solutions launches free hazardous chemical labeling operations assessment
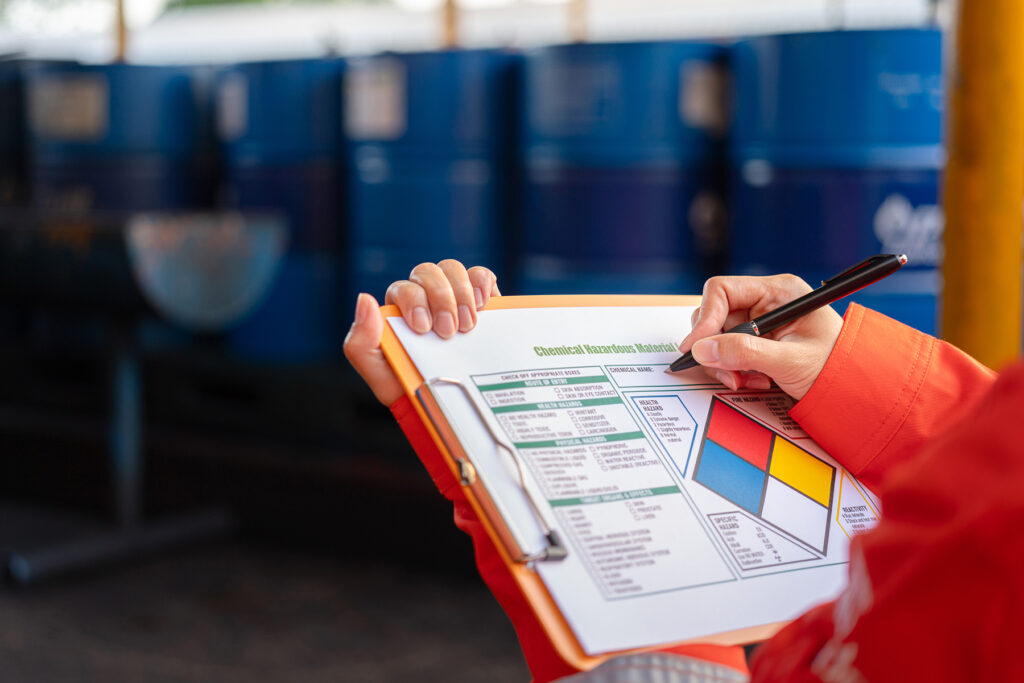
Confidential and complimentary, new GHS L.A.B.E.L. Profile helps companies labeling hazardous chemicals follow compliance best practices. Reliance Label Solutions, which specializes in manufacturing hazardous container labels for the petroleum, chemical, and environmental industries, has introduced a new program designed to help companies hone and streamline their chemical labeling operations. Called the GHS L.A.B.E.L. Profile – short for Leading Assessment for Best Practices and Efficacy of Labels, the confidential and complimentary technical inspection service provides an expert-driven assessment to help ensure companies handling and labeling hazardous chemicals follow compliance best practices. Valued at $3,500, Reliance Label’s GHS L.A.B.E.L. Profile creates an accessible labeling safety and standardization platform between chemical companies and labeling compliance experts. Steeped in best practices accrued over decades, Reliance Label’s team can seamlessly engage with chemical companies to determine their most pressing labeling compliance challenges. With an eye to these priorities, a Reliance Label compliance expert then conducts an onsite assessment visitation, followed by a comprehensive report that offers practical improvements where appropriate. Reliance Label’s portfolio of hazardous container labeling solutions is designed to withstand and thrive in harsh environments. While best known for chemical drum labeling solutions that meet stringent GHS, HazCom and IMDG labeling requirements, the company also offers labeling-adjacent GHS-compliant solutions such as printing software, color printers and printer consumables. Consultative, collaborative, and customized, the GHS L.A.B.E.L. Profile appraisals also include a weighted average that highlights any areas particularly at risk of non-compliance. Several manufacturing, warehousing, and logistical scenarios can be assessed, including labeling application infrastructure maintenance, storage temperature and humidity, and other issues that can adversely affect mission-critical label performance. “Our new GHS L.A.B.E.L. Profile comprises a confidential all-things-label health checkup for companies handling hazardous chemicals,” said Troy Lucas, Product Engineer for Reliance Label Solutions. “Our chemical customers intimately understand that labeling environmentally sensitive materials is far more complex than a quick print-and-apply. In this industry, labels and their application techniques must stand up to exceptionally tough conditions, and this is our way of standing with our customers to best ensure compliance and overall labeling success.”
National Ladder Safety Month is coming
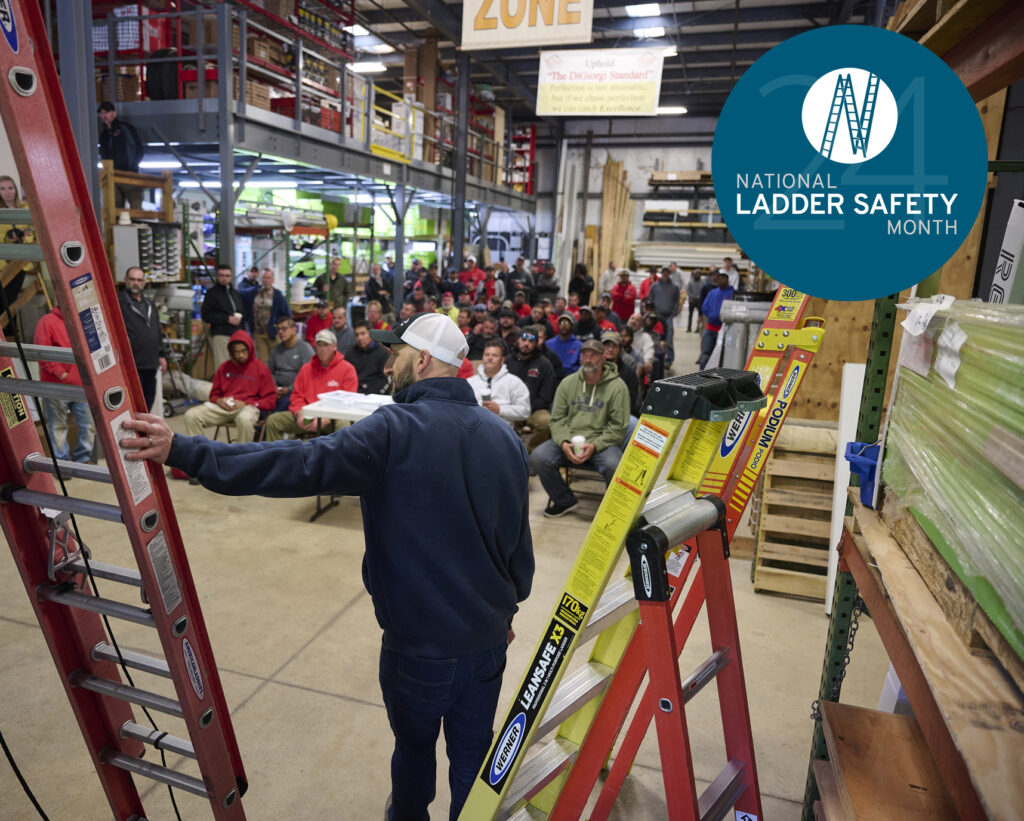
National Ladder Safety Month is observed next month, as it is every March. Begun by the American Ladder Safety Institute (ALI), the event raises awareness about ladder safety and encourages employers and their workers to engage in annual ladder safety training. In industrial settings, ladders and climbing are often integral to certain job functions, so safe practices are critical to success. If your job responsibility includes employee safety, now is the time for you to sign up at ALI’s Ladder Safety Training site, and prepare for training. The site makes safety training easy all year long, with an organized curriculum, video, and resource libraries – all completely free. Training courses are designed to seamlessly complement and integrate with an organization’s existing training program. Managers can choose as much or as little as they require; use the entire program wholesale or select a la carte to bolster gaps in their training. After signing up, trainers and training managers can develop a custom dashboard, called a Trainer’s Toolbox, in which they select training and testing, assign them to trainees, and monitor trainee performance and progress on the assignments. These dashboards can track everything from a handful of trainees for smaller organizations all the way up to hundreds for larger enterprises. Topics covered include single and extension, articulated, mobile, and stepladders, with courses available in English or Spanish. Taking training on laddersafetytraining.org does not require an invitation from a trainer. Anyone who wishes to enhance their awareness of ladder safety can sign up. And, obviously, training is available 24/7/365 – not only during Ladder Safety Month. These four weeks each year allow ALI to take deep dives into different aspects of ladder safety, narrowing in tightly on one topic each week, to promote safety tips and training. This year’s topics include Week One: Training and Awareness; Week Two: Inspection and Maintenance; Week Three: Stabilization, Setup, and Accessories; and Week Four: Safe Climbing and Positioning.
The ARA Show heads west to Las Vegas in 2025
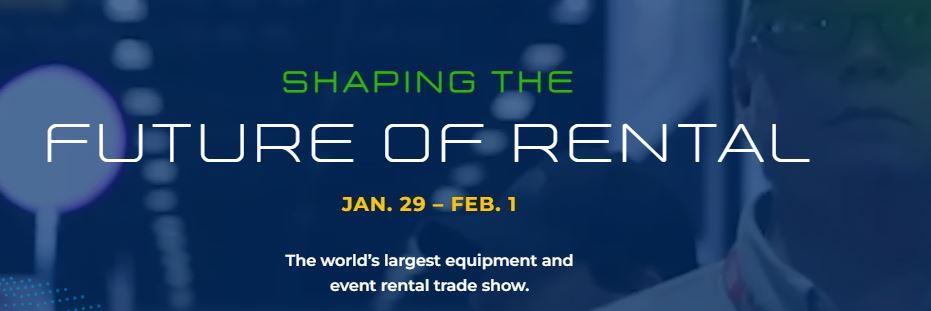
Next year, The ARA Show™ will head back to Las Vegas and the Las Vegas Convention Center. A full day of education will begin the show on Wednesday, Jan. 29, followed by the three-day trade show from Thursday, Jan. 30, through Saturday, Feb. 1. Future of Equipment Rental will return in 2025 and take place on Tuesday, Jan. 28 As planning begins for 2025, attendees and exhibitors should note the change in days of the week from a typical show to the Wednesday-Saturday schedule the show will be on in Las Vegas. The desert of Las Vegas has been a long-time favorite for attendees with the fun, nightlife, and bright lights of the city. Las Vegas continues to grow in excitement and the American Rental Association (ARA) looks forward to bringing the show back to Vegas in 2025, following a successful return in 2021. More details about The ARA Show 2025 will be available in the coming months. Check out ARAshow.org and the show’s social media channels for the latest information.
Skyjack launches all new Micro-Scissors at the ARA Show
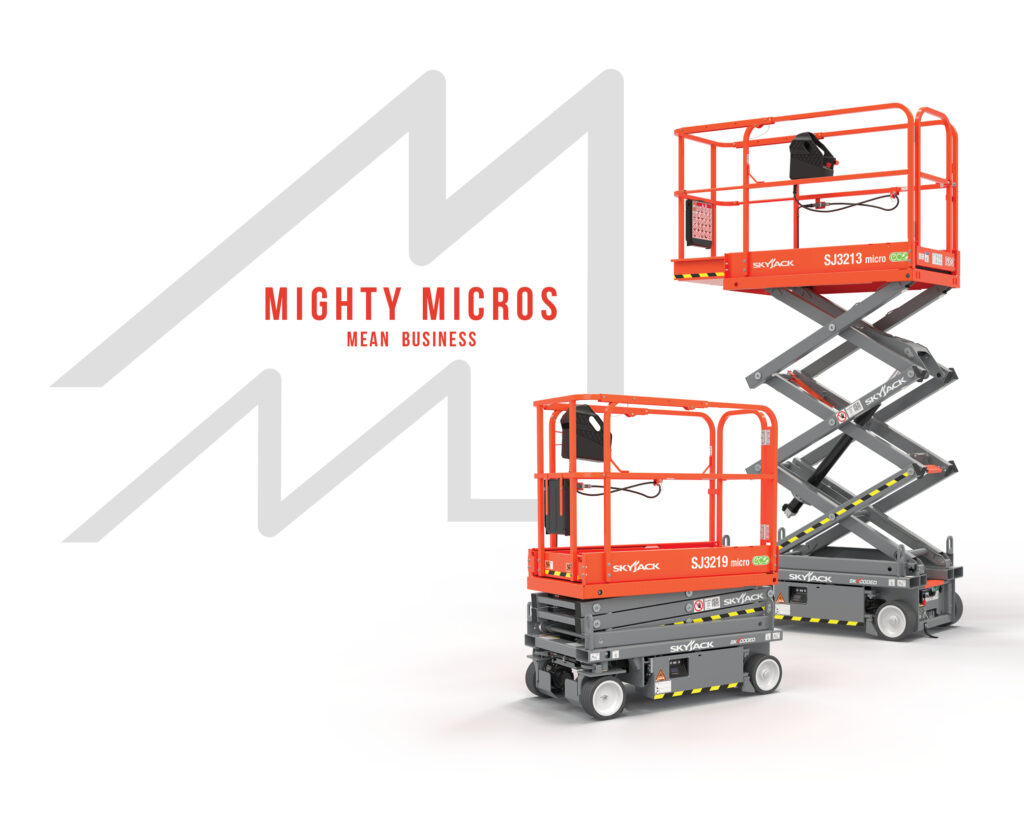
Linamar Corporation’s Skyjack division arrived at The ARA Show ’24 to announce the launch of a new micro scissor line in the SJ3213 micro and SJ3219 micro. Skyjack’s new micro scissor range represents a significant new choice in the low-level access arena. The SJ3213 micro and SJ3219 micro remain simply reliable, combining the low cost of ownership with Skyjack’s renowned product support. Fully proportional drive and lift controls offer superior drive with more efficiency, controllability, and improved torque, while variable speed brushless AC electric front wheel drive provides exceptional duty cycles. “Building on the success of the previous SJ3013/14 micro we now have not one but two new micros. Featuring E-Drive – improving controllability and providing consistent power, torque, and traction,” shares Senior Product Manager Corey Connolly. “Our focus is always on improving productivity and cost of ownership, and E-Drive allows our newest micro scissors to give you more for less.” The newest micros have been designed to fit most passenger-style elevators and work in environments where space is at a premium while still providing a substantial work area. Key features of the latest micro line include: 13ft and 19ft platform heights, 500lb platform capacity, AC electric drive performance, Fits through a standard door (rails up), 20” rollout extension to increase work area and provide up-and-over capability, Low GVW fitting into the standard elevator, Low floor loading. “This is an exciting launch for Skyjack,” explained Skyjack President Charlie Patterson. “Our team understands the importance of maximum uptime and we pride ourselves on providing machine features that combine durability, quality and serviceability. Our new micro line is no exception, combining low cost of ownership with our world renowned product support for easy accessibility into tight spaces, earning the mighty micros moniker.” Rental companies and major contractors face increasing demands for sustainability information. Skyjack has introduced its ECO mark to support our customers by providing products that deliver benefits in environmental performance and long-term sustainability. Skyjack’s E-Drive scissors ECO benefits include: 16% operational carbon saving compared to previous model, Up to 20% improvement in duty cycle over equivalent hydraulic drive machine, ZERO emissions, 90% recyclable (by weight), Optional ECOtray leak containment, Approved for use with bio-degradable hydraulic oil, Telematics allowing for remote diagnostics reduces site visits and operational footprint. Skyjack has showed its commitment to the low level access segment with the design and development of this all new two model range. Targeted at the North American market, the SJ3213 micro and the SJ3219 micro will replace the previous SJ3013 model in North America. The SJ3014 will remain available in Europe.
H&E Equipment Services report Fourth Quarter and Full Year 2023 results
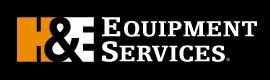
H&E Equipment Services, Inc. has announced results for the fourth quarter and full year ended December 31, 2023, with record strategic expansion, impressive revenue growth, and steady margin appreciation contributing to another year of record financial performance. On October 1, 2021, the Company sold its crane business, (the “Crane Sale”). All results and comparisons for the periods reported are presented on a continuing operations basis with the Crane Sale reported as discontinued operations in certain statements and schedules accompanying this report. Also, on December 15, 2022, the Company sold its Komatsu earthmoving distribution business, resulting in a pre-tax gain of $15.4 million in the fourth quarter of 2022, including $12.9 million recorded as a gain on the sale of property and equipment, and $2.5 million as a gain on other, net. FOURTH QUARTER 2023 SUMMARY WITH A COMPARISON TO FOURTH QUARTER 2022 Revenues increased 9.3% to $385.8 million compared to $353.1 million. Net income totaled $53.5 million compared to $51.2 million. The effective income tax rate was 19.4% compared to 26.1%. Adjusted EBITDA (earnings before interest, taxes, depreciation, and amortization) increased 6.5% to $185.2 million compared to $173.9 million. Prior year results included the pre-tax gain associated with the sale of the Komatsu earthmoving distribution business. Adjusted EBITDA margin was 48.0% compared to 49.2%. Total equipment rental revenues were $316.9 million, an increase of $41.2 million, or 14.9%, compared to $275.7 million. Rental revenues were $280.6 million, an increase of $35.6 million, or 14.5%, compared to $245.0 million. Sales of rental equipment increased 34.3% to $40.6 million compared to $30.2 million. Margins improved to 66.0% compared to 51.2%. Sales of new equipment totaled $9.8 million, a decline of 54.5% compared to $21.5 million. Gross margin improved to 48.3% compared to 45.1%. Total equipment rental gross margins were 48.2% compared to 47.9%. Rental gross margins were 54.2% compared to 53.1%. Average time utilization (based on original equipment cost) was 68.4% compared to 72.0%. The Company’s rental fleet, based on original equipment cost, ended 2023 at approximately $2.8 billion, representing an 18.3% increase. Average rental rates improved 3.8% from the year-ago quarter and 0.8% on a sequential quarterly basis. Dollar utilization was 40.3% compared to 41.9%. Average rental fleet age on December 31, 2023, was 39.7 months compared to an industry average age of 49.0 months. Paid regular quarterly cash dividend of $0.275 per share of common stock. Reviewing the Company’s fourth quarter and full year performance, Brad Barber, chief executive officer of H&E, referred to several important developments. Mr. Barber pointed out, “Strong execution of strategic initiatives and resilient non-residential activity resulted in healthy financial metrics throughout the year. Total revenues in the fourth quarter improved 9.3% compared to the year-ago quarter, while rental revenues grew 14.5% over the same period, resulting in a rental margin of approximately 54.2%. For the full year, total revenues set a Company record of just under $1.5 billion, representing an 18.1% increase compared to total revenues in the previous year. Over the same period, rental revenues grew 24.1%, exceeding $1.0 billion for the first time, and completed the year with an average margin of 52.1%. Indicative of the durable industry fundamentals, rental rates in the fourth quarter improved 3.8% compared to the same quarter in 2022, and 0.8% on a sequential quarterly basis. For the full year, rental rates were 5.6% better than 2022. Our strategic accomplishments in 2023 included a record gross fleet investment totaling $737 million, exceeding our revised target range for the year. We completed the year with a fleet original equipment cost (OEC) of approximately $2.8 billion, or 18.3% greater than our fleet OEC at the conclusion of 2022. Our average fleet age of 39.7 months remained among the youngest in the industry.” Mr. Barber went on to state, “The pace of branch expansion remained impressive throughout 2023, further strengthening the Company’s competitive position. The success of our accelerated branch expansion program led to a record 14 branch additions in 2023, including three new locations in the fourth quarter. These branch additions established greater density in the Gulf Coast, Mid-Atlantic, Southeast and Midwest regions, providing the Company with increased exposure to new projects. Also, additional growth and improved positioning was accomplished through the acquisition of attractive and well-managed businesses with operations in core metropolitan statistical areas of the U.S. One transaction, which closed in the fourth quarter, added three locations in California, increasing the number of branch additions to 17 in 2023, or a 14% increase across our branch network when compared to the branch count at the conclusion of 2022.” Addressing 2024 strategic growth initiatives, Mr. Barber said, “We plan to slow our 2024 gross fleet expenditures to a range of $450 million to $500 million. We believe our record fleet expenditures in 2023 and young fleet age advantageously position the Company to address the ongoing growth in construction markets and these factors should support steady improvement in physical utilization. Regarding our branch network, new branch growth will remain a fundamental component of our strategic plans in 2024 with 12 to 15 new locations expected in our branch expansion program. In addition, branch growth could be enhanced through attractive acquisition opportunities that offer access to vibrant construction markets in the U.S., as demonstrated by our latest acquisition which closed in early 2024, adding one location each in Phoenix and Denver.” Mr. Barber noted the outlook for the equipment rental industry remains encouraging, supporting the point by saying, “Commentary from our customers regarding pending construction opportunities in 2024 remains optimistic and supports a business climate characterized by stable to modestly higher non-residential and industrial activity. Construction starts are projected to grow on a year-over-year basis with the growth reinforced by mega projects and increased spending on infrastructure programs. Also, we remain confident that expanding rental penetration will be a meaningful catalyst for increased industry growth.” FINANCIAL DISCUSSION FOR FOURTH QUARTER 2023 Revenue Total revenues increased 9.3% to $385.8 million in the fourth quarter of 2023 from $353.1 million in the
ORBIS expands OPTEBULK™ portfolio with addition of 48×45 series footprint
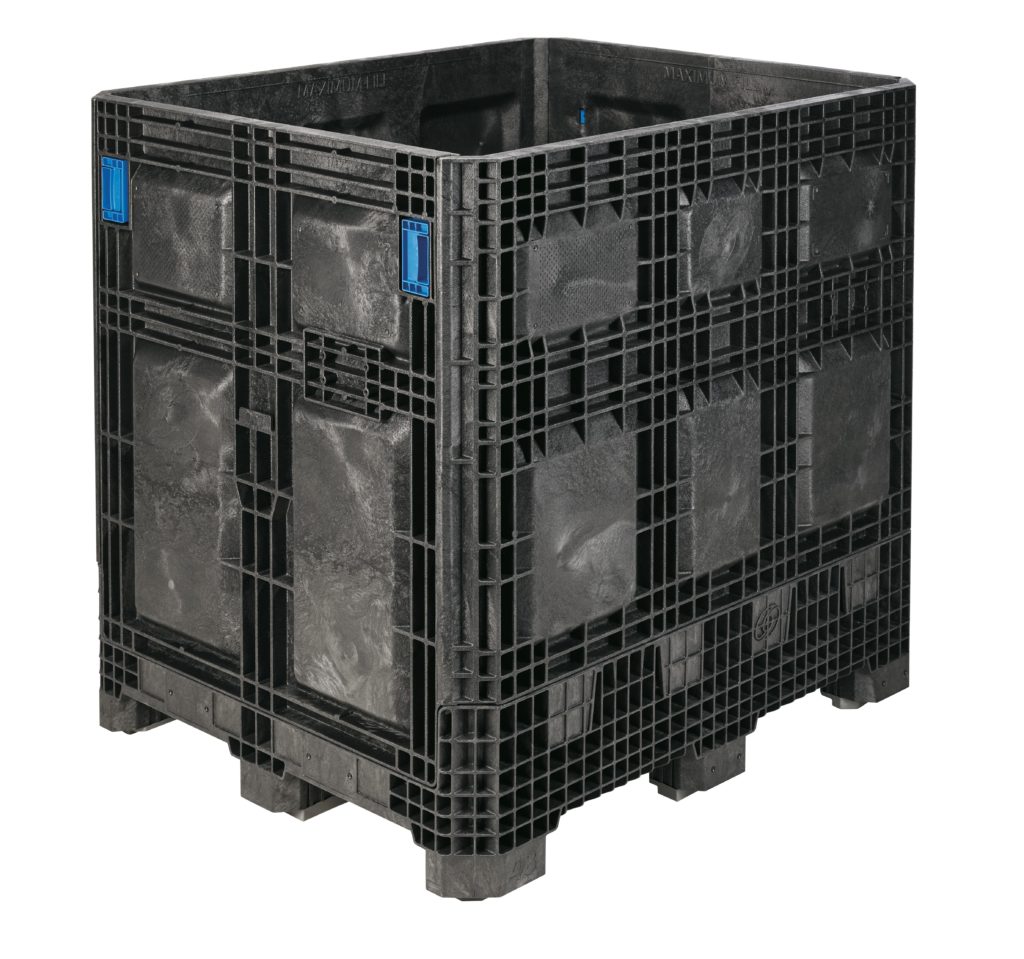
New, reusable bulk container offers increased shipping efficiencies and storage optimization across various industries ORBIS® Corporation adds a new pallet, top cap, and reusable sleeve pack system to its suite of economical and collapsible plastic bulk solutions with the OpteBulk™ 48×45 series. This new addition enhances sustainability, transportation, and cost-saving benefits with a total of 28 positions per 53’ trailer, setting it apart from other 48×45 sleeve packs currently in the market by having two more positions. Maximizing truckload space not only reduces shipping costs but also reduces emissions due to fewer return trips. The OpteBulk is a unit load system, with the ability to stack multiple full containers and collapse empty containers to save valuable space in a wide variety of applications, including the efficient storage and distribution of products within the industrial, electric vehicle, and tier supplier industries. The sleeve is manufactured from a trilaminate-structured core plastic with bidirectional strength, offering additional protection during transport. With rounded top edges, the sleeve not only minimizes potential injury due to sharp, worn edges but adds durability to the system’s overall structure. ORBIS’ clamshell design allows all three components to be kitted for reverse logistics with the sleeve folding into the pallet envelope and top cap unitizing. This feature offers unparalleled dunnage design versatility, enabling collapsible fabric dunnage solutions. ORBIS OpteBulk systems include active sleeve locks in both the pallet and top cap to eliminate the need for expendable unitizing packaging. “Innovation is at the heart of ORBIS, and with the introduction of the OpteBulk 48×45 series, we’re providing the market with a 28-position solution and securing our position as a leader in the market,” said Mike Ludka, senior product manager at ORBIS. “We remain dedicated to creating reusable packaging systems that enable our clients to move products faster, better, safer, and more cost-effectively along the supply chain.” By implementing this system, companies can reduce the environmental waste associated with single-use fiber corrugated boxes and wood pallets in their supply chain. Reusable packaging improves the flow of products along the supply chain to reduce total costs. ORBIS uses proven expertise, industry-leading knowledge, and superior products to create reusable packaging systems that help world-class companies move their products faster, better, safer, and more cost-effectively.
Tompkins Solutions names Steven Leavengood Senior VP of sales
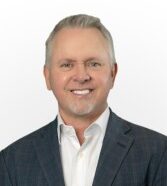
Tompkins Solutions, a leading supply chain consulting and material handling integration firm, today announced that Steven Leavengood has joined the company as senior vice president of sales. In this role, Leavengood will be responsible for leading the business development and sales team for the fast-growing supply chain services firm. Leavengood has more than 25 years of domestic and international sales and management experience, with a strong background in supply chain, material handling and automation solutions. Prior to joining Tompkins, Leavengood held senior sales management positions at Swisslog, Interroll, Knapp and Scott Automation. “We’re excited to welcome Steven to the Tompkins team,” said David Latona, CEO of Tompkins Solutions. “His demonstrated success driving innovation and growth and building highly engaged teams will be invaluable as we continue to create new solutions and strategies to help our customers remain competitive and meet increasing demands.” In addition to Leavengood, Tompkins Solutions also recently announced that Bryan Perkins was hired as senior vice president of engineering and Quinntin Teeling joined the company as account executive.
Flux Power to exhibit at MODEX 2024 Tradeshow March 11-14 at the Georgia World Congress Center in Atlanta
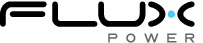
Company to Showcase its New G2 Product Line of Heavy-Duty Battery Packs and SkyBMS® Telematics Solution Flux Power Holdings, Inc., a developer of advanced lithium-ion energy storage solutions for the electrification of commercial and industrial equipment, has announced it will exhibit at MODEX 2024 in Hall C Booth C4085 at Georgia’s World Congress Center March 11-14. Flux Power will showcase its next-generation battery packs, including lithium-ion solutions for Class I-III material handling equipment. These next-generation lithium-ion battery packs are equipped with newer technology and more capacity for fleet operations with a heavy workload. Along with showcasing the new line of heavy-duty products, Flux Power will also conduct demonstrations of its SkyBMS® telematics solution, which helps operation managers better manage their fleet by providing them with real-time data and actionable insights. ”We look forward to showcasing our complete line to new and existing customers,” said Tod Kilgore, VP of Sales at Flux Power. “Our state-of-the-art lithium-ion solutions solve a variety of existing performance challenges with a common theme: longer run times, sustained high power performance, limited maintenance, and a more sustainable solution. Flux Power delivers these advantages at price points that significantly lower the total cost of ownership compared to conventional battery offerings.”
Hyster honored with design award for A Series forklifts
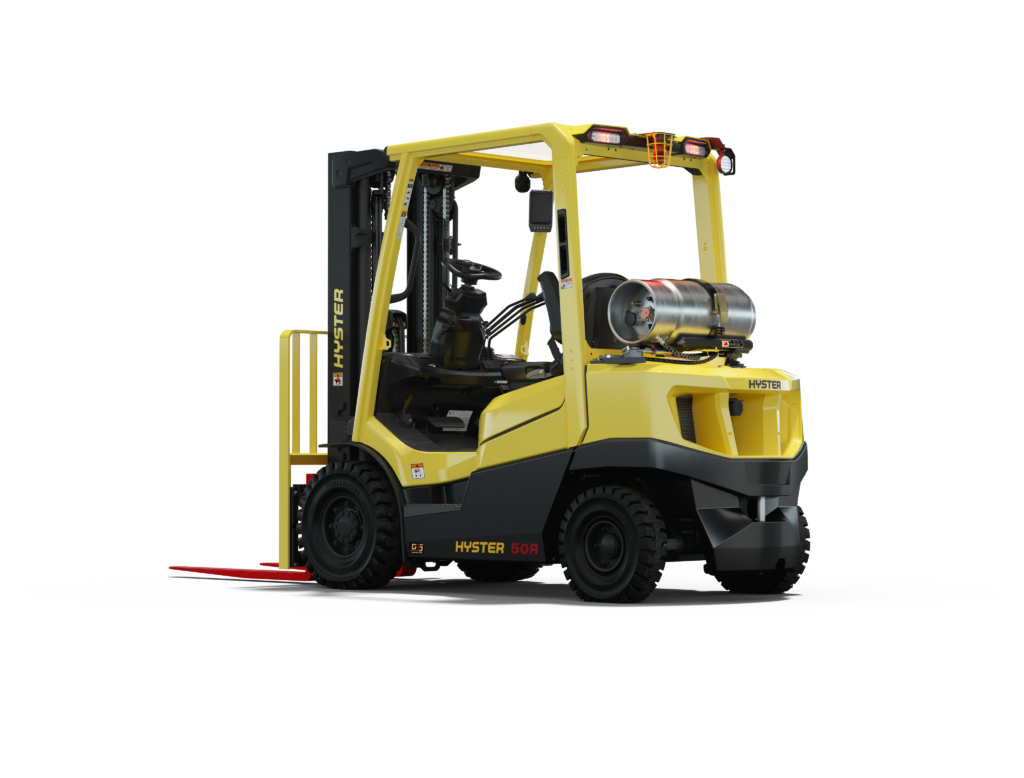
Hyster Company announces the Hyster® H40-70A forklift series is a winner of the prestigious 2023 GOOD DESIGN® Award. The configurable internal combustion engine-powered forklifts are the first in the A Series, which offers robust ergonomic features, a low total cost of ownership and an innovative technology engineered to help reduce the likelihood of forklift tip-overs. The H40-70A models, which are available with 4,000-to-7,000-pound lift capacities, are designed around a singular base configuration derived from direct feedback from operators, managers, technicians, safety coordinators, and other professionals. From there, operations can tailor additional features, creating a forklift based on their specific application. “While every operation faces its unique challenges, some are common across industries – strained forklift operators, safety concerns, and rising operating costs,” says Jimmy Anderson, Product Manager, Hyster. “Hyster is dedicated to designing solutions that address these widespread problems, while also helping operations tackle challenges specific to their business.” To support operator comfort and productivity all shift long, the H40-70A models are designed for ergonomics and convenience. In particular, the operator compartment enables easy entry and exit with a lowered seat, contoured hood, increased floor space, and generous head and shoulder clearance. A foot-activated, hand-released parking brake requires less effort than a hand-applied brake to minimize operator lean and back strain, while dynamic seat adjustment provides up to 25% more forward and backward seat adjustability than the leading competitive model. Several features help boost visibility, including a low dash and wide mast design that provide excellent forward visibility. A high-strength laminated glass roof is available to provide operators with an unobstructed upward view to help place loads at height. The forklifts are also available with the Hyster Dynamic Stability System (DSS), a solution that continually monitors truck performance to help reduce the likelihood of forward and sideways tip-overs and reinforces operating best practices. When it detects the truck exceeding designated thresholds while carrying a load, DSS automatically implements measures like limiting truck speed and tilt range. None of the DSS sensors require maintenance, and the trucks’ durable components and extended service intervals are designed to help control maintenance spend and bolster reliability and uptime.
Murata Machinery USA celebrates 50 Years of automation in North America

Murata Machinery USA (Muratec), a manufacturer of game-changing industrial automation, celebrates its 50th anniversary across North America. Various activities are planned throughout 2024 to commemorate Muratec’s golden year. Operating as a subsidiary of Kyoto, Japan-based Murata Machinery Ltd., Murata Machinery USA provides sales, service, and support for the Muratec brand. Muratec has a rich history of innovation and leadership in North America, revolutionizing the automation landscape with groundbreaking solutions that are often the first of their kind, the only ones available, or the world’s fastest. “Murata Machinery USA has been a beacon of excellence, driving industrial innovation and achieving continental success,” said Toshiyuki Komori, President and CEO, Murata Machinery USA. “Unwavering in our commitment, we aim to propel the Muratec brand of end-to-end automation to new heights across North America, helping customers maintain their competitive edge with automation.” In May 1974, Murata Machinery Ltd. established Murata of America, Inc. in Charlotte, NC, initially focusing on textile machinery. In October 1989, it acquired the Wiedemann Division from the Warner & Swasey Company, creating Murata Wiedemann, Inc. The unified brand “Muratec” was introduced in October 1991. By June 2002, the company consolidated its U.S. subsidiaries, Murata of America, Inc. and Murata Wiedemann, Inc., into Murata Machinery USA, Inc. Throughout North America, Muratec expanded its automation portfolio to encompass material handling, machine tools, fabrication technology, and cleanroom automation solutions, showcasing a broadened range of offerings. Historic Innovation Across Four Divisions For over five decades, Muratec’s breakthroughs have marked many turning points in automation, helping our customers enhance their competitive efficiencies across diverse industries. Some of these significant innovations in automation advances include: Textiles: Muratec revolutionized textile manufacturing with Spinning, Winding, Twisting, and Texturizing Machines. This led to the invention of Air-Jet Spinning, which utilized high-pressure air to enhance the texture and bulkiness of yarns at higher production speeds. Other advancements supporting textile manufacturing included the Automatic Winder that seamlessly linked with Ring Spinning Machines. The game-changing VORTEX machine was introduced in 1997 and evolved into the VORTEX 870 in 2011, creating the world’s fastest spinning machine that eliminated Roving and Winding with over 6,000 units installed globally. Logistics & Automation (L&A): In the 1990s, Muratec revolutionized North American Automotive Stamping with an integrated turnkey solution, effortlessly combining Die Handling, Blank Processing, Stamping Warehousing, and Transport Control. This streamlined processes and minimized waste by integrating Automated Storage and Retrieval Systems (ASRS) and Automated Guided Vehicles (AGV), reshaping the automotive sector’s logistics and material handling approach. Muratec positioned itself as a key industry influencer of versatile automation systems covering high-rise warehouses, unmanned transporting systems, robotic automation, and cutting-edge factory automation. Clean Factory Automation (CFA): As a cleanroom industry leader, Muratec invented cutting-edge floor and overhead transport systems (OHTs) to optimize fabrication processes, maximize space, and ensure product integrity with minimal vibration. These solutions set industry benchmarks that smoothly interfaced with customer Manufacturing Execution Systems (MES) and tools, establishing a new standard in boosting productivity, reliability, and operational excellence. Muratec is one of the world’s largest semiconductor clean room automated manufacturers. Machine Tools Division (MTD): In 1980, Muratec revolutionized CNC machining with the MW25, the inaugural twin-spindle automated chucker lathe that seamlessly integrated automation with an industry-first gantry loader. Then, in 1994, Muratec set a new industry standard by inventing the world’s first electric servo motor CNC turret punch press. The MOTORUM 2000 was known for its eco-friendly design, low noise, and highly productive hydraulic oil-less operation, inspiring numerous imitations and knockoffs. Muratec’s machine tools, spanning turning, sheet metal fabrication, and automated handling systems combine high speed and precision through cutting-edge control technology. In 2024, Muratec will mark 50 years of automation innovation with initiatives. In September, new innovative machinery will be introduced along with ten (10) cutting-edge machine demonstrations at the 2024 International Manufacturing Technology Show, Sept. 9-14, at McCormick Place in Chicago, Booth 338844.
Borgman Capital sells Aerial Work Platforms, Inc. to Herc Rentals Inc.
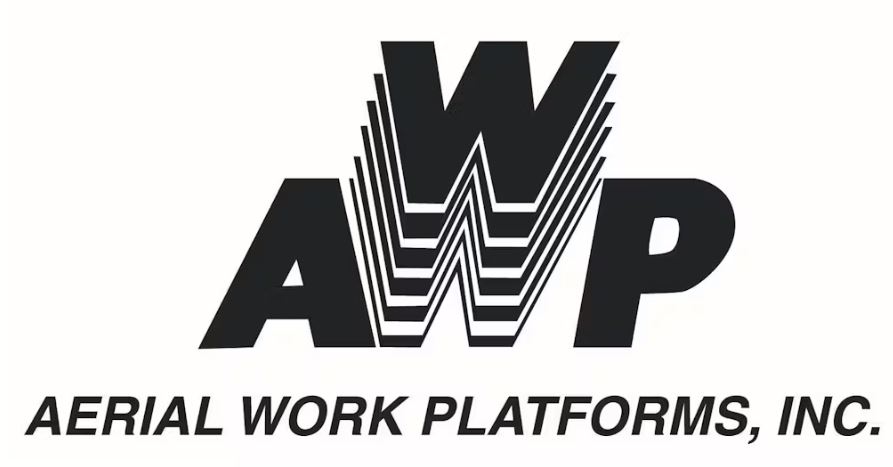
Borgman Capital, a lower middle market private equity firm, announced the sale of its portfolio company Aerial Work Platforms, Inc. (“AWP”), an equipment rental company, to Herc Rentals Inc. Terms of the transaction were not disclosed. Founded in 1979, AWP specializes in the rental, service, and sale of aerial lift equipment including scissor lifts, boom lifts, telehandlers, and forklifts. Borgman Capital acquired AWP in December 2020 from the company’s founder, Pat Barney. AWP has locations in Sussex, Janesville, Neenah, and Kenosha, Wisconsin, and is the number one independent rental equipment company in the state based on fleet size. During the three-year investment period, AWP’s growth was driven by strategic equipment purchases, fleet diversification, operational improvements, geographic expansion to Kenosha, and increasing market share. Following Mr. Barney’s planned retirement, Borgman Capital hired rental equipment industry veteran Robert Rivera as president. “We executed many new growth initiatives during the investment period. At the end of the day, AWP’s success comes down to Robert’s leadership and the strong customer service culture he built,” said Sequoya Borgman, founder and CEO of Borgman Capital. “AWP is an example of what’s possible when the right leader is put in place to build on a founder’s legacy after an ownership transition. It was a pleasure to partner with Robert and the team over the last three years and we will be cheering everyone on in their next phase of growth.” Rivera said: “The outstanding success we achieved is a direct result of the incredible talent at AWP. The team’s dedication to customer service will remain our focus as part of Herc Rentals. I am appreciative of Borgman Capital’s support and the latitude I was given to lead, set ambitious goals, and make the pivotal decisions needed to grow the business.” Founded in 1965, Herc Rentals is one of the leading equipment rental suppliers in North America with 2023 total revenues of approximately $3.3 billion. Herc Rentals’ parent company, known as Herc Holdings Inc., was listed on the New York Stock Exchange on July 1, 2016, under the symbol “HRI.” Herc Rentals serves customers through approximately 400 locations and has about 7,200 employees in North America. Reinhart Boerner van Deuren served as Borgman Capital’s legal counsel on the transaction.
Analysis of the Top Nine misunderstandings about forklift lithium-ion batteries
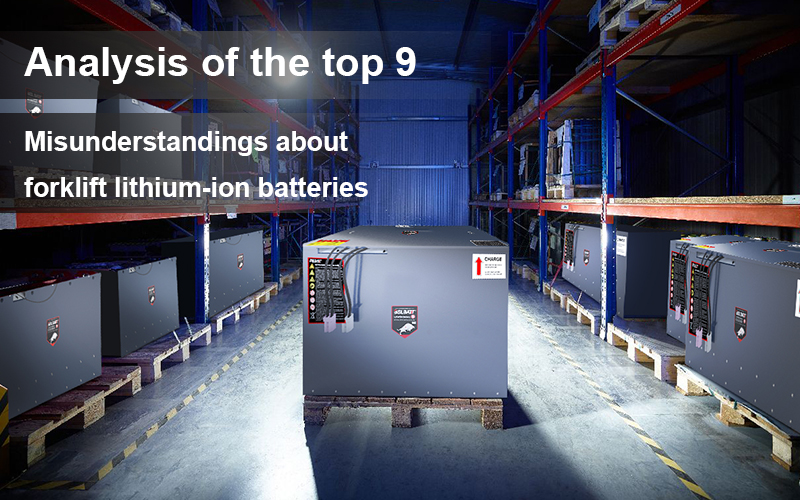
Interest in and use of lithium-ion batteries in industrial trucks is growing. There are many advantages to this revolutionary technology, most notably its fast charging and ability to charge “on the go” rather than “charge to full” all at once. However, there remains widespread confusion and misunderstanding about battery technology and its suitability for material handling applications. Visit our Forklift Lithium Battery website or read on for what BSL Battery – Industrial technical experts have to say about some misconceptions. 1. We do a lot of heavy lifting that electric machines can’t handle With modern battery-operated equipment, lifting capacity is not an issue. If the capacity plate rating is the same as the equivalent internal combustion engine (ICE) model, the ability to lift heavier loads is also the same. For example, Hyster®’s updated J2.5-3.0XNL trucks are designed to match hydrostatic IC trucks. Also, remember that while lifting uses a lot of energy, electric forklifts are more energy efficient than IC forklifts, so the only real potential drawback is the machine’s ability to store and use that energy. This means the end user must consider whether there are sufficient opportunities to recharge the battery throughout the day. This video provides an in-depth look at how lithium-ion technology works and how Hyster® can replace multiple lead-acid batteries depending on truck power requirements while increasing productivity! 2. You can get all the benefits by replacing your lead-acid batteries with lithium-ion batteries Of course, aftermarket lithium-ion batteries are a huge improvement over lead-acid batteries, but to enjoy the real benefits, you should consider a forklift factory-approved OEM lithium-ion battery manufacturer, which has inherent advantages. For example, the integrated battery has CANbus connectivity, which means the truck’s factory BDI still works accurately. The OEM technician can connect to the battery and diagnose any issues through the truck software, eliminating the need to call a 3rd party provider. In addition, BSL Battery is a major lithium battery supplier in China. It serves Toyota Material Handling, Combilift Forklift, Clark Forklift, Xilin Forklift and Raniero Forklift. When considering a swap solution (lead-acid batteries replacing equivalent lithium-ion batteries), users must determine whether their application allows sufficient time to charge the batteries. They also need to consider additional energy infrastructure costs, such as cables and sockets capable of handling higher power consumption. In addition, they need to install new power points closer to work areas or break rooms to avoid unnecessary trips to existing lead-acid charging room distances. 3. Lithium-ion batteries are very expensive It’s imperative to think about long-term costs. Although lithium-ion batteries have a higher initial purchase price than lead-acid batteries, their cost per cycle is lower due to their longer lifespan, making them the most cost-effective solution in the long run. BSLBATT’s lithium-ion batteries, in particular, have extremely low internal resistance and the most efficient technology, which means less grid energy is wasted and saves 30% (charging and CO2 emissions) compared to lead-acid batteries. Therefore, in the long run, with the decline of lithium carbonate, now comparing the prices of lithium-ion batteries and lead-acid batteries, purchasing a lithium battery with the same capacity only costs 1.5 times that of a lead-acid battery. Lithium batteries are cheaper in the long run. 4. We need to replace our entire lead-acid fleet with lithium-ion machines Of course, it often makes sense to replace the entire fleet so that operators don’t have to switch between different charging regimes and operating procedures. It also makes sense for the aging fleet, which has decided to retire all existing machines and “start over.” Replacement is also recommended when a business has an incentive to replace. This could be a commitment to reduce overall CO2 emissions or a desire to eliminate hazardous battery replacement or reduce ongoing maintenance requirements. However, if the utilization of certain trucks is not sufficient to warrant lithium-ion batteries, a mixed fleet is possible and we have helped many customers with phased rollouts. If you operate a mixed fleet, you need to know that lead-acid and lithium-ion batteries often require different chargers, so charging areas may need to be marked and instructions provided to staff. 5. Our power supply must be upgraded Yes, lithium-ion battery chargers have higher output, which means they require higher input current than lead-acid chargers. However, BSL Battery – Industrial offers a variety of battery/charger combinations based on utilization, application intensity, and available charging window. At the same time, to reduce customers’ charger investment, we have communicated with the world-renowned SPE, Fronius, and Delta-Q, which means that customers do not need to purchase additional chargers when switching to BSLBATT lithium batteries using chargers from these three brands. Charger! 6. Our drivers must be retrained and change their work habits Agreed, retraining is required as standard AS2359:2 practice states that each user should have a safe work systems policy in place, including supervisory practices, on-the-job training, and ongoing regularly updated training. Therefore, users must maintain records of ongoing training. The good news is that lithium-ion batteries are easy to use The battery management system communicates with the charger to prevent overcharging. It manages power delivery to prevent excessive discharge. It does not require charging or watering to work properly. The operator must simply know how to plug it into the charger when not used. Our clients found that their work habits needed to change, but for the better. Battery maintenance tasks are virtually eliminated, as are hazardous battery replacement and battery damage due to battery misuse. Unlike lead-acid batteries, lithium-ion batteries thrive on opportunistic charging, meaning operators can charge the forklift during breaks. The charging process will be faster and easier since there is no longer a need to open the hood to connect the charger to the truck. 7. Lithium-ion batteries are not as stable as lead-acid batteries and pose safety threats This is a common myth, but lithium-ion batteries are safer than traditional lead-acid batteries. Although the energy density is higher than that of lead-acid batteries, BSLBATT lithium-ion batteries have multi-level safety systems such as cells, modules, and casings, as well as a battery management system (BMS) with comprehensive protection functions.
Gordon Report: The current U.S. Labor-market conundrum
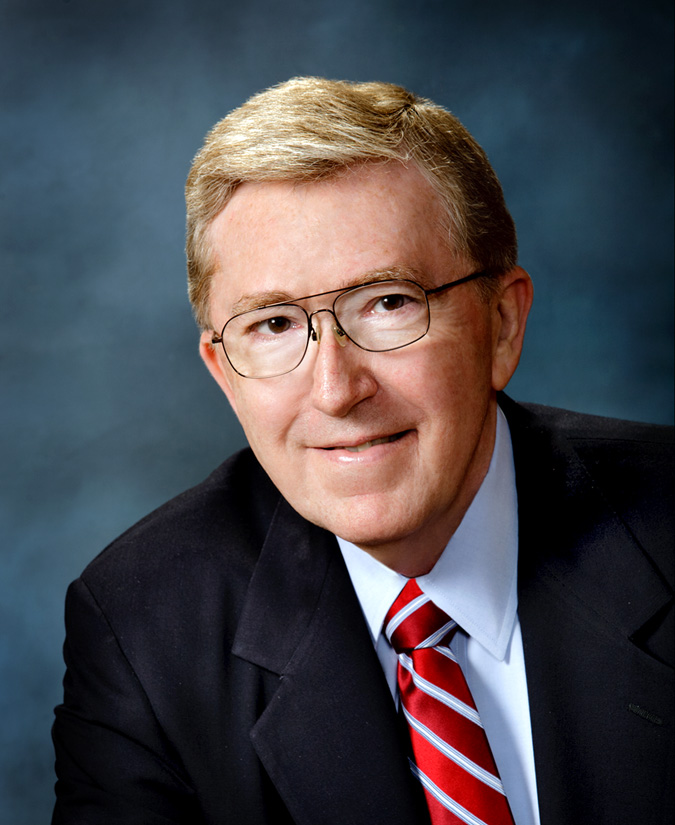
The February 2024 BLS jobs report showed a surge of 353,000 jobs added in January, more than double than what was predicted in economic surveys. This follows a gain of 330,00 jobs in December. Another surprise in this February report is that average hourly wages grew rather than holding steady. Over the past year, they have grown 4.5 percent. What factors may be behind these unexpected numbers? An average of 10,000 workers from the large baby-boomer population have been retiring each day. This year the average will grow as the baby-boomer retirements peak. This flood of retirees will continue until 2030. Therefore, this year and until the end of this decade, many job openings will arise from the need to replace retirees. In at least some sectors of the economy, it appears that employers are raising wages to find workers with the skills they need. Chief Economist Bill Dunkelberg of the NFIB (an association of small business owners) reported on their January survey, “Owners continue to raise compensation to retain and attract workers with the skills and willingness to do the job, but hiring remains a struggle in a tight labor market.” So far, this strategy has not been very successful. In that same survey, 39 percent of the respondents reported having unfilled job openings. Members of the Association of General Contractors also have high levels of unfilled jobs despite providing a wage premium of almost 19 percent over that of the average for private-sector production employees. In some cases, higher wages may attract people who have not been participating in the labor force to seek a job if the pay level would offset the costs of childcare, a long commute, or obtaining additional training. A recent Korn Ferry survey of job seekers, however, found that many applicants do not have the skills required for open jobs. In some cases, this is due to the development of new types of jobs with recently updated skill sets. The above data points to a current labor market with a significant skills-jobs mismatch. However, the Training Industry Annual Survey of 2023 reported that business investment in employee training remained flat. Going forward, predictions are that companies will cut their training budgets. The irony is that one way or the other business will have to pay more to find skilled workers either through continuing to raise wages or by investing in more in-house or collaborative training programs. About the Author: Edward E. Gordon is the founder and president of Imperial Consulting Corporation in Chicago. His firm’s clients have included companies of all sizes from small businesses to Fortune 500 corporations, U.S. government agencies, state governments, and professional/trade associations. He taught in higher education for 20 years and is the author of numerous books and articles. More information on his background can be found at www.imperialcorp.com. As a professional speaker, he is available to provide customized presentations on contemporary workforce issues.
US Cutting Tool orders totaled $187.9 Million in December 2023 which brings the Year-to-Date total up 6.9% from 2022
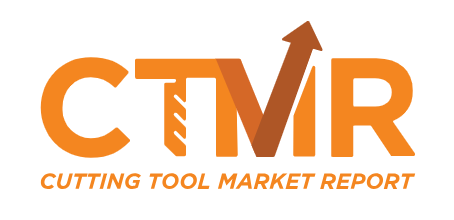
December 2023 U.S. cutting tool consumption totaled $187.9 million, according to the U.S. Cutting Tool Institute (USCTI) and AMT – The Association For Manufacturing Technology. This total, as reported by companies participating in the Cutting Tool Market Report collaboration, was down 7.3% from November’s $202.7 million and down 0.3% when compared with the $188.4 million reported for December 2022. With a year-to-date total of $2.45 billion, 2023 is up 6.9% when compared to the same period in 2022. “With 2024 comes change and challenge,” stated Steve Boyer, president of USCTI. “The U.S. cutting tool industry will continue to see growth opportunities in aerospace, automotive, medical, and computer-related segments but slowing and declines in other markets. While forecasts initially anticipated interest rate declines as we moved into 2024, recent inflation indicators appear to temper those expectations. We enter the new year with a guarded view anticipating continued challenges and uneven growth.” Mark Killion, director of U.S. industries at Oxford Economics, added: “After a strong start to 2023, shipments of cutting tools weakened in the last quarter of the year, falling 7.3% in December. As a result, shipments ended the year near their 2022 levels.” The Cutting Tool Market Report is jointly compiled by AMT and USCTI, two trade associations representing the development, production, and distribution of cutting tool technology and products. It provides a monthly statement on U.S. manufacturers’ consumption of the primary consumable in the manufacturing process – the cutting tool. Analysis of cutting tool consumption is a leading indicator of both upturns and downturns in U.S. manufacturing activity, as it is a true measure of actual production levels. Historical data for the Cutting Tool Market Report is available dating back to January 2012. This collaboration of AMT and USCTI is the first step in the two associations working together to promote and support U.S.-based manufacturers of cutting tool technology. The graph below includes the 12-month moving average for the durable goods shipments and cutting tool orders. These values are calculated by taking the average of the most recent 12 months and plotting them over time.