Every thing your supply chain needs
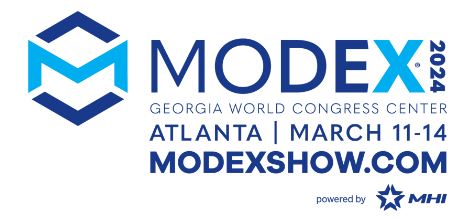
Connections. Innovations. Solutions. As the speed of the manufacturing and supply chain world continues to accelerate, building a more agile, sustainable and transparent operation depends on today’s forward-thinking decisions. MODEX brings together the entire industry to allow you to see end-to-end solutions — from traditional equipment to automation, robotics and emerging tech — and learn impactful trends from the industry’s key thought leaders. Make plans to attend MODEX 2024 and see in-person the full spectrum of what’s now and what’s next for supply chains. 1,000+ Leading Providers Experience over 1,000 of the leading providers and experience in person how their efficiency-enhancing, cost‑cutting equipment and technology solutions can futureproof your supply chain. 500+ Education Sessions Learn from the industry’s best minds how key industry trends and innovations can transform your manufacturing and supply chain operations during 150+ free education sessions and four powerful keynotes. 45K+ Education Sessions Connect face-to-face with your manufacturing and supply chain peers and leading solution providers. Experience the complete supply chain ecosystem With more than 1,000 exhibits, the world’s leading solution providers will be on hand to showcase their most innovative equipment and systems. Nowhere else will you have the chance to see these solutions in-person, in-action and determine which can best solve your manufacturing, transportation and supply chain challenges. By attending, you can connect with your peers and tap into the collective power of the industry’s solution and thought leaders, all gathered in one place. Packaging, containers & shipping equipment Box and Carton Makers, Dunnage Trays, Packaging and Unitizing Systems, Wrapping, Inspection of Products by Weight or Scanning, Pallets, Wire Baskets, Plastic and Metal Containers, Palletizing Equipment Dock & warehouse equipment & supplies Dock Levelers, Dock Pads, Doors, Forklift Trucks, Racks, Flooring, Handling Systems, Forklift Attachments, Conveyors, Hoists, Cranes, Monorails, Loading Dock Equipment, Below/Hook Lifting Devices RFID and auto ID equipment & systems Barcode Printers and Scanners, Vision Systems, Voice Recognition Systems, RFID Systems, Systems Integrators, IIoT, Sensor Technology Material handling & logistics equipment & systems Automated Storage and Retrieval Systems, Automatic Guided Vehicle Systems, Casters/Wheels/Tires, Hydraulic and Electrical Components and Controls, Robotics, Personnel/Burden Carriers, Racks, Forklifts, Batteries, Lift Trucks, Flexible Manufacturing Systems, Tool Handling, Conveyors, Mezzanines, Lift Tables, Scissor Lifts, Unit Handling Systems, Manufacturing Execution Systems, Warehouse Management Systems/ Supply Chain and Logistics Execution Systems, Ergonomic and Safety Equipment, Carousels, Modular Drawer Storage, Order Picking, Sortation Equipment, Shelving and Workstations, Third-Party Logistics Supply chain management & sustainability Alternative Fuel Systems, Parcel Management and Distribution, Reverse Logistics, Third Party Logistics, Sustainable Facility Equipment, Supply Chain and Logistics Execution Systems, Enterprise Resource Planning and Transportation Management Systems, Inventory Security Services Inventory management, information technology, & controlling technologies Computers, Controllers, Software Programs, Systems Integrators, Manufacturing Execution Systems, Warehouse Management Systems/Supply Chain and Logistics Execution Systems, Remote Control Equipment, Wireless Control Systems, Voice Recognition Systems, Enterprise Resource Planning, Order Management Systems, Transportation Management Systems Transportation, last mile, & logistics Road, Rail, Sea and Air Freight Transportation, Parcel Delivery, Security, Autonomous Vehicles, Robotics, Sensors, Supply Chain Management Software, Third Party Logistics and Reverse Logistics, Fleet Management, Last Mile Tech, Parcel Lockers, Omni-Channel Fulfillment, Micro-location, Route Optimization, Urban Logistics Emerging technologies Sensors, Software, Cloud Computing, Driverless Vehicles, Robotics and Automation, Predictive Analytics, Artificial Intelligence, Omni-Channel Fulfillment, Unified Commerce, Augmented Reality, Virtual Reality, Wearable and Mobile Technologies Show Exhibit Hours Monday – March 11, 2024 – 10:00 am – 5:00 pm Tuesday – March 12, 2024 – 10:00 am – 5:00 pm Wednesday – March 13, 2024 – 10:00 am – 5:00 pm Thursday – March 14, 2024 – 9:00 am – 1:00 pm
The Hot Air Factor. How full of it are you?
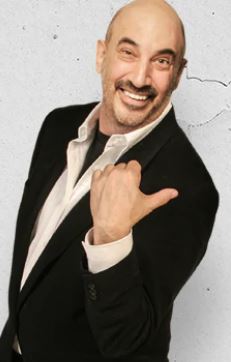
Sometimes salespeople get a bad rap. Sometimes they create it. Sales require self-confidence but there’s a fine line between self-confidence and cockiness. A finer line between self-assurance and arrogance. And the finest line between proud and egotistical. As a professional salesperson, there’s a career difference between self-talk = self-performance (the right way) and loose lips sink ships (the ultra-wrong way). Salespeople are not the most loved group of professionals to begin with. We rank above politicians, tax collectors, and (especially) lawyers, but below dentists and dog catchers. All that a salesperson can hope to do is establish a great reputation and let that propel him to success. Since the prospect buys the salesperson first, reputation is as valuable (and critical) an element as he or she can have. How is yours? One bad event, situation, or story can ruin years of hard work. Continuing stories of neglect or overpromising breed career destruction. A salesperson’s self-delusion (failure to admit the problem, and thinking nothing is wrong) will make the situation worse. Sales of hot air can occur at any level. Customers, prospects, bosses, and coworkers are all potential victims. “Come on Jeffrey,” you say, “Get to the point. Give me some examples of self-destructive talk. What is sales “hot air?” Relax, helium breath, here ‘tiz. 7.5 examples of Hot Air (even though I’m sure none of these apply to you). BTNA –Big talk no action. Too much time talking about the sales you’re going to make and not enough time making them. Bragging too soon.Before the deal is signed, sealed, and a check delivered. Bragging too much. No one but you want to hear it. If you need to hear yourself just record yourself and replay it in your car until youget as sick of it as others. Bragging at the expense of others. Beat the competition, but don’t beat them into the ground. A variation of this is making someone else look like a fool. Bragging about someone you took advantage of or tricked. Using others as scapegoats to get yourself off the hook. Better known as covering your butt, or the inability to accept responsibility. Blaming others for your failings is obvious to those who are listening and makes a fool out of the teller. Exaggerating the facts. Each year, the fish that got away size increases. Stay within the parameters of what you know to be true or less. Understated is always better. Using insincere words.Honestly, truthfully, quite frankly, and I mean that, are words that alienate. 7.5 Talking past the sale. Knowing when to shut up and go home. Employing any one of the above elements after a sale has been consummated but before you leave will jeopardize the sale. It’s known as “buying it back,” and it happens often. The rule of thumb in sales is “less is more.” Hot air has interesting negative side effects… It wastes everyone’s time. It’s the most unproductive and negative use of your time possible. It makes you look like a fool. It lowers your respect factor by 100. It gets people talking behind your back. It prevents advancement. It can get you fired. Who wants that? No one, but these side effects are linked to people with severe cases of hot air. How do you know if this is you? How do you know if you’re blowing hot air? Well, no one is without some guilt. It’s hard not to brag if you just made a big sale and took it out from under the nose of your biggest competitor. The rules are simple: Don’t say anything behind anyone’s back you wouldn’t say to their face. Don’t say something you wouldn’t want to be said about you. Don’t say anything you have to remember (lies must be remembered, or you get tripped up with the truth). Don’t say anything you couldn’t say in front of your mom. The key is to temper your remarks with humility. Your challenge is to always bring out the good side in your words. Your challenge is to employ self-discipline in getting past the hot air. Your challenge is self-rule or self-destruct. About the Author: Jeffrey Gitomer is the author of twelve best-selling books including The Sales Bible, The Little Red Book of Selling, and The Little Gold Book of Yes! Attitude. His real-world ideas and content are also available as online courses at www.GitomerLearningAcademy.com. For information about training and seminars visit www.Gitomer.com or email Jeffrey at salesman@gitomer.com or call him at 704 333-1112.
Potential $$ is coming your way
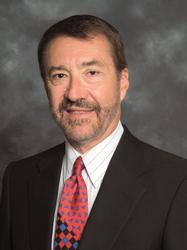
There are still plenty of questions and discussions taking place about what to expect in 2024. Management is really under the gun trying to properly budget profits and free cash flow, and at the same time trying to entice customers to buy units and parts and properly maintain equipment. Speaking of customers, seeing that they are in the same boat you are, are looking for ways to become more efficient through cost reductions and productivity gains, using help from vendors to help them do that. Hopefully, your management teams and OEMs are looking for answers to assist customers and are passing along those ideas for you to pass on to existing and prospective customers. Do you think customers would appreciate finding some potential cash that could be used for Cap-X purposes? Sure, they would. And would it not be great if you helped them find that cash? Believe it or not, some anticipated tax plays are coming about that I am assured will pass, and if they pass could provide immediate benefits in terms of tax payments. There are changes regarding: Bonus Depreciation Section 179 Interest Expense Limitation Contractor Employee Status The Tax Cuts and Jobs Act allowed 100% Bonus Depreciation starting September 27, 2017, and before January 1, 2023. So up through 2022. Starting in 23 the Bonus Depreciation would phase out at 20% per year until 2027. After that, it is back to normal tax depreciation methods. THE PROPOSED LAW EXTENDS 100% BONUS DEPRECIATION THROUGH JANUARY 1, 2026, WITH THE PHASEOUT BEGINNING THE YEAR AFTER. What is great about this is your ability to go back and use 100% for 2023. If you were basing your estimate payments using an 80% bonus to calculate taxable income, you can now adjust that annual result for the additional 20% you can adjust for. And of course, planning for 2024 would also include numbers using a 100% bonus. Of course, each company has its unique tax situation or position, and even with the changes, there are no general significant benefits. SECTION 179 is amended to increase the limit on Depreciable Business Asset expensing. For property placed in service after December 31, 2023, taxpayers can expense up to $1.29 million, reduced by the amount of cost of qualifying property over $3.22 million, adjusted for inflation. In terms of Business Interest, the proposal extends the use of EBITDA for purposes of regarding the limitation of the deduction for business interest. This amendment applies to tax years beginning after December 31, 2023 and will run through December 2025. These tax changes are positive for every dealer out there, but also very positive for customers who were not quite sure they wanted to invest in equipment in 2024. These unexpected funds could be used to buy, make a down payment, or just expand the business with the support of the new equipment. I suggest you put a plan together to discuss with customers to see where they stand on this issue. CONTRACT EMPLOYEE STATUS. This issue continues to tighten up because both tax and legal issues are involved to the point where not properly reporting payments for work could result in material taxes and penalties. We now have an economic reality test for determining workers’ status under FSLA. This new rule rescinds the 2021 Independent Contractor Rule and becomes effective March 11, 2024. There are now six factors to determine if a person is an employee or independent contractor: Any opportunity for profit or loss a worker might have. A financial stake or resources the worker has invested in the work. The degree of permanence of the work relationship. The degree of control an employer has over the person’s work. Work is essential to employers’ business. A factor regarding the worker’s skill and initiative. If the worker is an employee there are tax withholding requirements, as well as payroll taxes paid by both the worker and employer. Base pay and overtime, if earned, would also be included in the process. Then there are the Federal Unemployment Tax implications. And there could be benefits provided to employees. I am reminded that the contractor “payroll” may wind up being included for WC and General Liability insurance unless you notify the insurance company to not include the contractor expense. Contractors should supply an insurance certificate to the company. All I see here is a lot of exposure if you guess wrong. One other recent tax topic concern Limited Partner Status for SECA Tax (Self-employment tax). Since limited partnerships are popular these days, I thought I would throw this in to make you aware that if you participate as a limited partner the exemption requires a functional analysis of whether a partner was, in fact, active in the business of the partnership and a limited partner in name only. So, if you receive profit distributions from a limited partnership take steps to decide whether you are a limited partner or one active in the operation of the business. Document your functional analysis review. I believe a review of these topics with customers will be appreciated even though they have no additional funds coming. Will anyone else discuss these topics with them? About the Columnist: Garry Bartecki has been a CPA MBA with GB Financial Services LLC and a Wholesaler columnist since August 1993. E-mail editorial@mhwmag.com to contact Garry.
Service and part departments need to track their KPIs to achieve growth
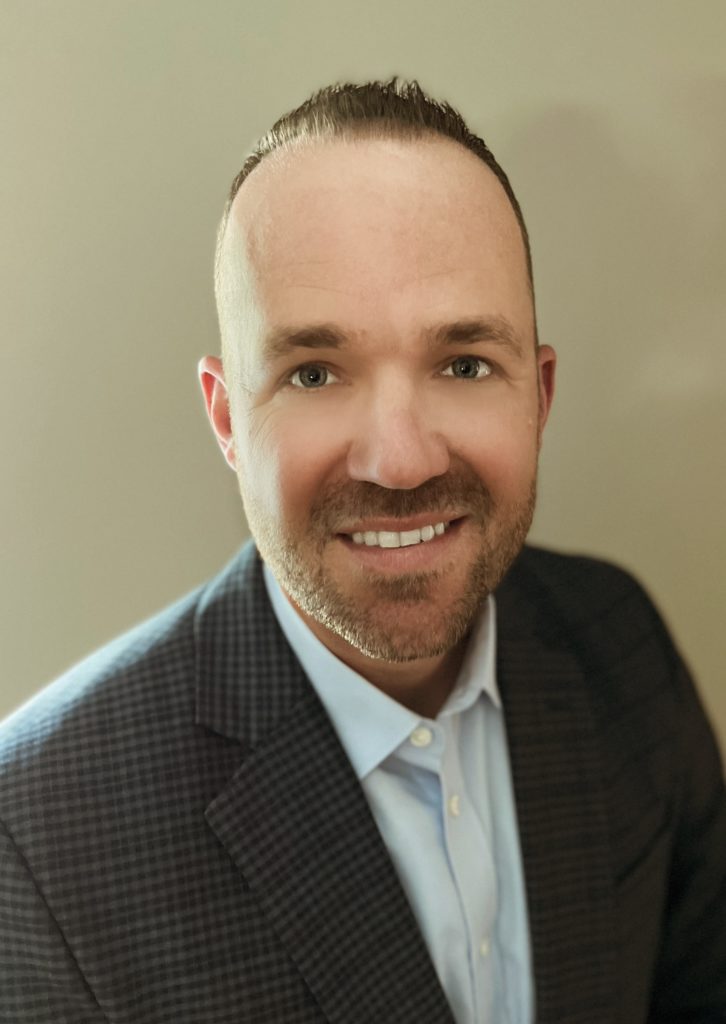
As we are well into the first quarter of 2024, the subject of labor shortages continues to be a trend across our industry. Dealers that I talk to stress that the growth of their service and parts departments’ revenue continues to be impacted by the shortage of skilled forklift technicians. The topic of attracting, hiring, and retaining technicians continues to be a hot topic, however, in this month’s column, I will focus on another topic as it relates to service technicians, technician productivity, and efficiency. The key to your dealership’s service department’s success goes beyond the number of technicians you have and how busy they are. The question to ask is how productive and efficient they are in their work. Long hours on the clock may not be the key metric; rather, it’s their productivity that impacts your dealership’s profitability. Today, many dealerships have adopted business system software that will track and compute these metrics as they pertain to technician productivity for you, yet sometimes this this Key Performance Indicator (KPI) is neglected. Service Department Efficiency Before measuring technician productivity and setting up KPIs, your service department operations and processes must first be efficient. Running an efficient service department within your dealership requires a combination of effective management, skilled personnel, and streamlined processes. The efficiency of your service department is critical in meeting your customer demands and driving the success and revenue of the department. A crucial factor is the proficiency of the service technicians on your staff, who should be well-trained and certified to handle the diverse range of equipment they are being asked to diagnose and service. Investing in ongoing and continuing training programs will ensure your technicians are up to speed on the latest technological advancements in equipment and diagnostic tools. Additionally, having a well-organized and stocked spare parts department or service van parts inventory is an important factor for efficiency. You want to ensure that the necessary spare parts are readily available to your service technician when your customer’s equipment goes down. Be sure your parts department staff have the necessary resources to look up, procure, inventory, and deliver the right parts as needed to positively impact technician efficiency and customer satisfaction. Establish clear communication channels with your customers so your service department and technicians understand their needs and expectations. Providing regular updates on the status of repairs and offering estimated completion times helps build trust and satisfaction with your customers. Additionally, if everyone at your dealership (service dispatcher, service writer, technician, customer service sales rep, etc.) is on the same page with the customer, it will show the customer that your dealership is running a customer-centric service department. Having efficient workflow processes and effective management of work-in-process is another critical element to the efficiency of your service department. There are many business systems and field service mobile solutions today that allow for the efficient documentation of service records and collaborations between your service, sales, and parts departments that further enhance the overall performance and customer satisfaction of your dealership. If you are still asking your technicians to use paperwork orders to document their service work orders and billable hours and turn them in manually to the office, it may be time to look to invest in a modern field service mobile solution. This will also streamline your processes of converting a completed service work order to a customer invoice more efficiently. An additional benefit, as you look to attract, hire, and retain technicians, is that state-of-the-art technology is more attractive to workers for their everyday job tasks. Technician Productivity Now that you’ve streamlined processes and demonstrated your service department can run efficiently, it’s also crucial to stress the importance of productivity. Simply computed, technician productivity can be calculated by dividing their working hours by the available hours and their efficiency by how long they take to complete a service job versus the standard time estimated to complete that job. For many dealers, a normal paid working day consists of eight hours for your service technicians, which you compensate them for even if they are unable to bill out all that time to retail customer service jobs. While not all their time will always be 100% billable to your customers, your processes should maintain accountability for every paid hour to be billed out to a customer invoice, internal invoice, or general ledger (GL). These three types of hours to be billed are commonly referred to as retail hours, internal hours, and expense hours. Retail hours are hours you can bill your customer for a service job. Internal hours billed include repairs to your rental fleet, pre-delivery inspection of new equipment sales, and equipment serviced under full maintenance lease agreements. Expense hours include training hours, team meetings, and other non-billable tasks. The key here is to invest in technology and systems that can effectively account for every retail, internal, and expense hour of your technician. The forklift service industry landscape is evolving, and strategic adaptation is key to the future profitability of your dealership. Embracing change, staying up to date with technological advancements, and consistently innovating your service offerings can position your dealership as a leader in your market, while also attracting and retaining customers with opportunities for revenue growth. About the Author: Chris Aiello is the Business Development Manager at TVH Parts Co. He has been in the equipment business for 17-plus years as a service manager, quality assurance manager, and business development manager. Chris now manages a national outside sales team selling replacement parts and accessories in various equipment markets such as material handling, equipment rental, and construction/earthmoving dealerships.
Trelleborg tires brings more resilience to material handling applications with premium full tire range at LogiMAT 2024
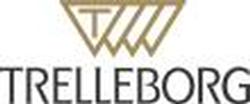
Trelleborg Tires will showcase its full premium portfolio for material handling and logistics at LogiMAT 2024, the international trade fair taking place March 19-21, 2024 in Stuttgart, Germany. Trelleborg’s Stand A23 • Hall 10 will feature innovative tire technologies, including advanced treads and high-performance rubber compounds for solid endurance, safety, and performance. In today’s multitude of material handling operations, having the right solution is key to maximizing efficiency. The Trelleborg full range of solid resilient forklift tires offers something for everyone, helping businesses handle low to maximum-intensity jobs with ease, starting from the user-friendly labeling system for selecting the right tire for specific operations, depending on the intensity and working conditions, thereby improving overall endurance, performance, and efficiency. Top-of-the-line is the Trelleborg XP1000 tire for maximum-intensity applications. The XP1000 tire has been proven to deliver optimal performance, with extra traction and minimal tire vibration, giving better driver comfort and less fuel consumption. This newest tire is available in a variety of special rubber compounds, including the unique ProTEX: the non-marking electrically conducting compound engineered for use on Materials Handling applications operating in potentially explosive environments. Equipped with effective Pit Stop Line technology, Trelleborg XP1000 is shown to improve safety and tire change planning. Once 100 hours of operating time remains, an orange band appears on the tread, helping forklift drivers and fleet managers schedule tire changes and avoid unplanned downtime. The Trelleborg XP900 tire, made for high-intensity applications, provides exceptional stability and maneuverability when loading and unloading goods in warehouses, factories, and more. Its rubber compounds have been developed using special raw materials tested for long-lasting performance and sustainability, promising a further reduction in CO2 emissions. To support medium-intensity operations in all indoor and outdoor conditions, the Trelleborg XP800 tire is key to reaching the highest performance maintaining, at the same time, the cost control with its advanced tread design. The Trelleborg XP700 tire has been designed to perfectly match the needs of low-intensity material handling operations. Anton Stoynev, Director of Material Handling & Construction Trelleborg Central Europe states: “Our extensive Trelleborg XP range gives operators a wide selection to choose from our complete resilient solid tire portfolio, depending on the material handling application they need. We are proud to be a strategic partner to the forklift industry, delivering advanced solutions to support our customers maximizing their performance under any working conditions while minimizing the environmental impact. We have worked hard to make sure our tires are ready for the next generation of material handling vehicles and the intense jobs they’re required to perform.”
December 2023 Manufacturing Technology orders beat expectations as December adds $491 Million
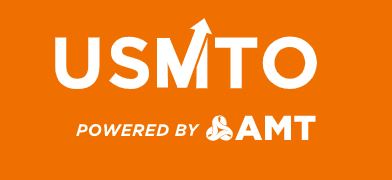
In an upside surprise, December 2023 orders of manufacturing technology totaled $491 million, up nearly 22% from November 2023, and nearly 12% above December 2022, according to the U.S. Manufacturing Technology Orders Report published by AMT. Just like the larger U.S. economy fared better than many predicted at the beginning of 2023, orders of manufacturing technology, measured by the U.S. Manufacturing Technology Orders Report published by AMT – The Association For Manufacturing Technology, outperformed even the best expectations. In an upside surprise, December 2023 orders totaled $491 million, up nearly 22% from November 2023, and nearly 12% above December 2022. This was the second-highest order level in 2023 and the first month of the year to outperform 2022 order levels. Orders in 2023 totaled $4.94 billion, 11.2% behind the $5.56 billion recorded in 2022. Although a decline, orders in 2023 surpassed many predictions, with some of the most pessimistic forecasters expecting the year to be down nearly 20% from 2022. Contract machine shops decreased their 2023 orders just over 21% compared to 2022. This customer segment, the largest customer for manufacturing technology, is mostly small-to-medium-sized businesses, so their capital investment tends to be tied to a shorter-term economic outlook. Even with their pullback in orders, 2023 exceeded expectations due to investment from larger OEMs, which tend to operate on much longer production schedules. Automotive orders in 2023 rose 2% from 2022. This growth came primarily from manufacturers of automotive transmissions, who made their second-largest investment since 2000, falling short of 2015 by only 1.3%. While a lot of attention has been paid to investments in electric vehicle production lines, such as the one recently announced by Toyota, automakers have also been heavily investing in production lines that make traditional internal combustion engines. Although the aerospace sector’s 2023 orders decreased nearly 9% from 2022, it still recorded its fourth-best year for manufacturing technology orders. Despite issues with the Boeing 737 MAX-9 that have dominated news cycles, the aerospace sector decreased orders in 2023 by less than the overall market and is positioned to continue investing in manufacturing technology in 2024. Manufacturers of ventilation, heating, air conditioning, and commercial refrigeration equipment made the largest investment in manufacturing technology since 2012, increasing orders by over one-third from 2022. This investment was likely driven by the massive uptick in new construction that was brought about by recent government legislation and investment, such as the Chips and Science Act, Inflation Reduction Act, and Infrastructure Investment and Jobs Act. Orders of manufacturing technology outperformed expectations in 2023, and there are several reasons to believe the momentum will carry over into 2024. For example, shipments of cutting tools increased in 2023 by nearly 7%, as measured by the Cutting Tool Market Report, a collaboration between AMT – The Association For Manufacturing Technology, and the U.S. Cutting Tool Institute. This increase in shipments of consumables used in the metal machining process indicates that machines in the field are increasing output. This is a good sign for machinery orders in 2024, as increased output could signal a coming need for additional capacity. The January 2024 reading of the Gardner Business Index, a sentiment indicator produced by Gardner Business Media, shows the manufacturing sector is still in a moderate contraction but improving to its highest confidence level in nine months. Further, expectations of business conditions over the next 12 months are quite positive. There are certainly challenges to the manufacturing technology industry that have been highlighted in previous articles but also many opportunities as we head deeper into the new year and toward another IMTS in September 2024.
Episode 462: Harbor Lockers simplifies pickups and returns for logistics
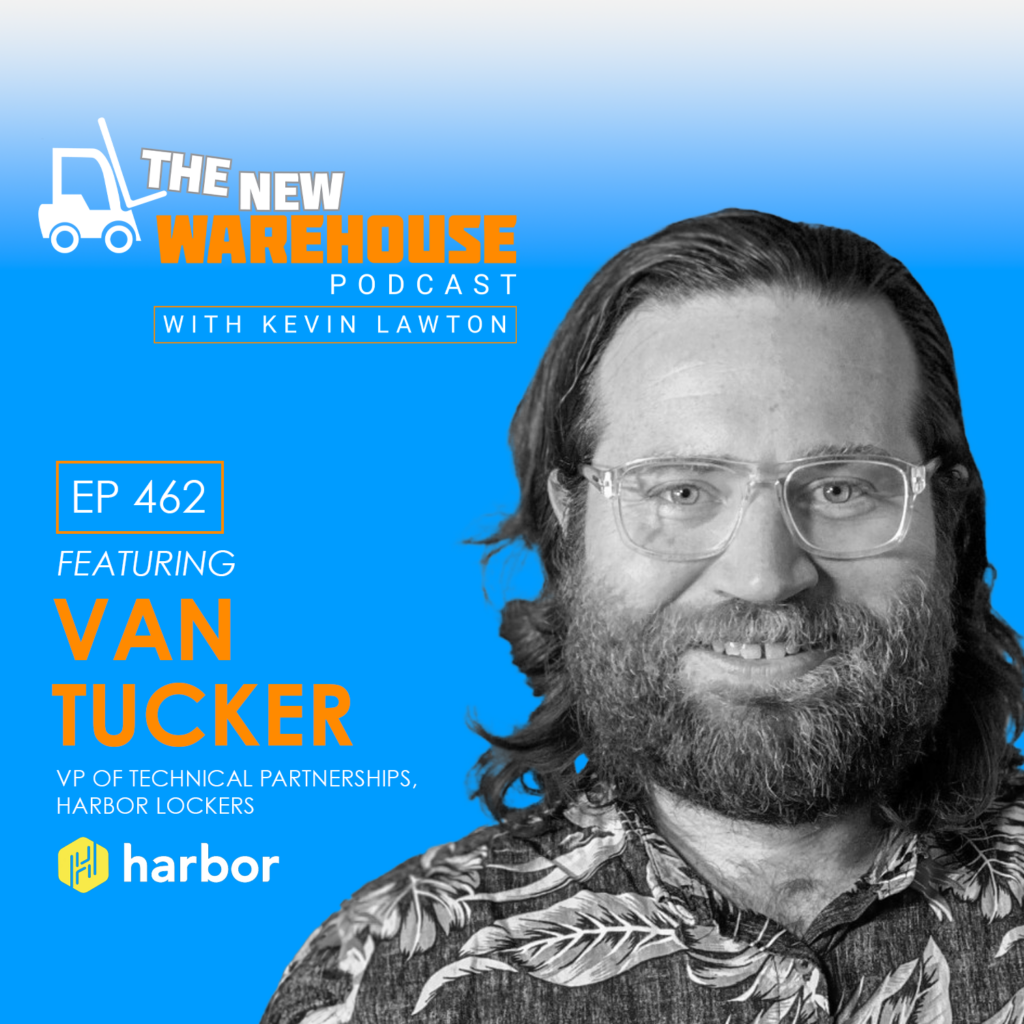
In this episode of The New Warehouse podcast, we’re joined by Van Tucker, VP of Technology Partnerships at Harbor Lockers. Part of Luxer One, Harbor Lockers is at the forefront of logistics innovation, offering versatile drop-off and pick-up locker solutions that enhance the delivery and return process for consumers and businesses alike. We delve into the mechanisms behind Harbor Lockers, the technology that powers them, their cost-saving benefits, and the problems they aim to solve within the supply chain. Innovative Solutions with Harbor Lockers With over 10,000 locker locations across the U.S., Harbor Lockers caters to many uses beyond parcel pickup and returns, including micro-warehousing. Van Tucker shares, “We’re seeing a lot of other novel use cases as we’ve been deploying more of these public locker locations around the United States in the last year.” The Technology Behind the Convenience The open technology platform allows for easy integration with retailers and carriers. “You can literally just hit our API and you can see all of our locker locations instantly,” explains Tucker. This seamless integration is a cornerstone of their user-friendly approach, offering a native experience without additional investments in infrastructure. Cost Savings and Logistical Efficiencies Harbor Lockers significantly reduces the cost of returns and facilitates collaborative cost-saving strategies. Tucker highlights the economic and operational benefits: “We work with multiple brands to facilitate cost savings when they combine services.” This approach saves costs and enhances efficiency within the logistics network. Key Takeaways from Harbor Lockers Expanding the utility of locker systems in logistics offers innovative solutions beyond traditional parcel pickup and returns. The technology platform enables seamless integration for carriers and retailers, enhancing the customer experience. Lockers offer a cost-effective solution for logistics challenges, promoting efficiency and savings through collaborative partnerships. The New Warehouse Podcast Episode 462: Harbor Lockers Simplifies Pickups and Returns for Logistics
Antares Vision Group to showcase automatic inspection machines for vials and more at INTERPHEX
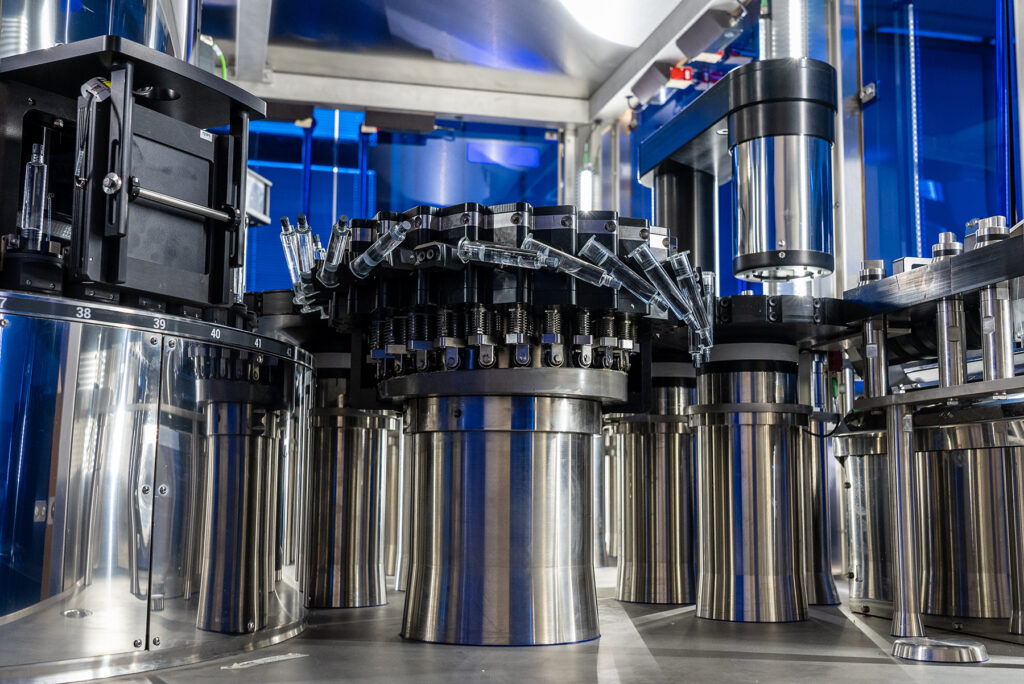
Company also will emphasize its recently launched DIAMIND ecosystem, a portfolio of interconnected software and hardware systems for comprehensive traceability. Antares Vision Group will showcase a variety of its latest, state-of-the-art inspection equipment at INTERPHEX NYC, April 16-18. At Booth 2821, the company also will emphasize its recently launched DIAMIND, a series of interconnected software and hardware systems providing physical products with the digital identities necessary to meet traceability mandates and streamline production and supply chain operations. Among the DIAMIND Line solutions showcased at INTERPHEX will be an automatic visual inspection machine for prefilled syringes. Antares Vision Group’s Visual Rotating Inspection (VRI) unit can handle up to 400 pieces per minute. The module can process SVP glass and plastic prefilled syringes up to 24mm in diameter, and inspect liquids with a wide range of viscosities – from water-like products to emulsions and gels. Like each of the company’s VRI systems, an additional camera mounted on a secondary carousel yields 100% inspection of the syringe surface. Fast, smooth single-point handling minimizes the risk of product breakages and scratches, thanks to individually motorized grippers and guideless conveying with vacuum-operated starwheels. Antares Vision Group also specializes in precise, high-speed vial inspection. At INTERPHEX, the company will showcase a module from its Visual Rotating Inspection (VRI) series capable of inspecting up to 400 liquid-filled glass containers per minute. The machine combines sophisticated particle and cosmetic detection with technology-driven closure integrity verification at an exceptionally rapid production pace. The VRI unit can inspect liquids in a wide variety of viscosities, including water-like, oily, suspension, gel, emulsion, lyophilized, and powder products. Vials are also inspected for cosmetic defects such as crimping quality, flip-off color, neck-shoulder sidewalls, and stopper position. Molded glass and plastic containers also can be inspected. Antares Vision Group will also display its CT, which automatically inspects vials and cartridges at speeds up to 200 pieces per minute. The unit is designed for accurate cosmetic and particle detection of small-volume containers up to 36mm in diameter. Compact and reliable, the CT features three stations for particle inspection equipped with both backlight and bottom light, and is configurable for reflecting and non-reflecting particles. Optional inspection stations include tip/cap and vial sealing, as well as CCIT-high voltage leak detection. DIAMIND integrated ecosystem for comprehensive production management Also, at INTERPHEX, traceability experts from Antares Vision Group will be on hand to discuss the company’s recently launched DIAMIND, an integrated ecosystem of solutions offering holistic transparency, production optimization and supply chain streamlining. DIAMIND operates at the line, factory, warehouse, enterprise, and supply chain levels, guaranteeing everything from product quality through sophisticated inspection systems to end-to-end traceability via integrated, cloud-based data management. DIAMIND’s integrated setup provides a single reference point for substantially simplified project management and centralized support services. The result Is heightened and interconnected quality assurance extending from raw materials and line production to warehouses, store shelves, and end users. All totaled, DIAMIND comprises multiple production and supply chain suites, making them applicable to manufacturers, distributors, wholesales and even government organizations.
Rider mezzanine access lifts
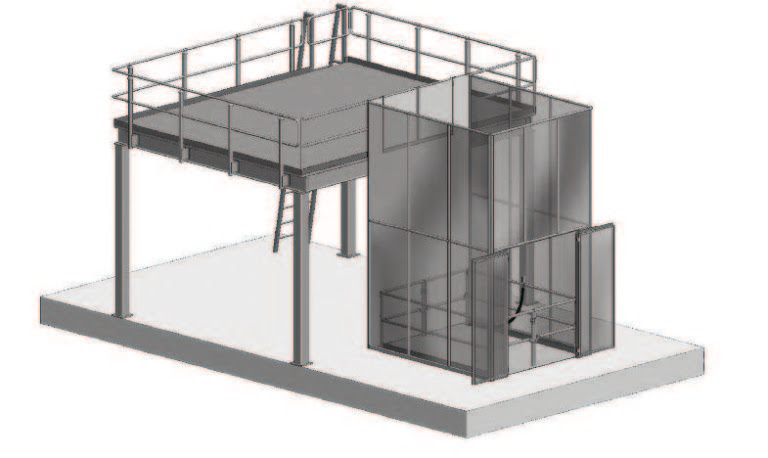
How to get personnel and material from ground level to mezzanine level quickly, safely, and efficiently Scissors lifts have been moving men and material from ground level to higher elevations for more than 60 years. They offer a distinct advantage over vertical reciprocating conveyors because people ride industrial scissors lifts along with the materials that they are moving. This greatly enhances the utility of the mezzanines. The cost is very competitive with VRC’s and the installation can offer significant savings because industrial scissors lifts come from the factory fully assembled instead of in kit forms like elevators and some vertical reciprocating conveyors so they avoid costly field assembly by elevator installers. Only the gates and enclosures need to be assembled on-site. Three main features make industrial scissors lifts different from other kinds of lifts: Scissor lifts are fully assembled at the factory and not field assembled from kits. Scissors lifts have no external guide rails and/or pulley mechanisms to entangle riders. All the stability and lifting is provided by the scissors lift mechanism beneath the platform. Rider scissors lifts use constant pressure push buttons which means the rider operator is in constant control of the lift movement. Governing codes The International Building Code for 2015 was printed in June of 2014 and has clarified matters greatly. Chapter 30 Elevators and Conveying Systems, Section 3001.2 Referenced standards, sites ANSI MH29.1 Safety Requirements for Industrial Scissors Lifts. This clears up any confusion with other codes such as ASME17.1 for elevators, ASME B20.1 for vertical reciprocating conveyors or ASME 90.1 for other types of scissors lifts. Virtually all states, counties and municipal agencies accept the references cited by the International Building Code because they respect the rigorous (multi-year and multi-constituency) review process conducted by the ICC (International Code Council). Note that the MH29.1:2012 was the standard reviewed and accepted and that this version differs substantially from previous versions. Also, note that other codes such as those governing the height of guardrails or enclosures on mezzanines or upper floors must be reviewed in conjunction with the industrial scissors lift code. Enclosure heights at upper levels may vary in different jurisdictions. The essential ingredients of a proper mezzanine lift One of the essential ingredients of a proper mezzanine lift is a properly configured industrial scissor lift. The platform should be equipped with 42” high guardrails with mid rails and 4” toe plates. The lift platform should have electrically interlocked gates that prevent lift movement unless the lift gates are closed. The interlocked gates are not required by code but will be a common sense addition required by most municipalities and inspectors. The unit should have proximity switches or limit switches for each level. The control shall be a constant pressure pushbutton that the rider operator must keep depressed to maintain movement of the lift (the use of call/send buttons is not allowed with riders on the lift). The lift should also be equipped with an emergency down valve on the power unit to lower the lift in case of power failure. Again, this is not a code requirement, but most municipalities or inspectors will require it. Another essential ingredient of a proper mezzanine lift is a smooth mezzanine fascia. The entire surface of the mezzanine adjacent to the lift from ground level to the top of the guardrail on the upper level must be equipped with a smooth face to eliminate shear points. This may be wallboard, polycarbonate GP sheets or fine mesh. Interlocked doors & windows are allowed. A proper mezzanine lift would also include an enclosure system. The sides not adjacent to the mezzanine must be enclosed from ground level to the height of the highest guardrail in the fully raised position. The guardrail on the mezzanine and the access gates on the enclosure must be electrically interlocked to prevent lift movement when the gates or doors are opened and mechanically locked so that they cannot be opened unless the lift platform is present. The gap between the platform and the mezzanine should be 1”. The gap between the platform and the enclosure on all other sides should be approximately 3” to 4”. This gap requirement is not by code, but another common sense requirement required by most inspectors. The configuration should look like this: Advance lifts will always supply a configuration drawing after receipt of order so that users and inspecting authorities can make comments before the equipment is built and shipped. What about inspections of these lifts? Advance Lifts has studied elevator inspection forms from several states and realized that the forms closely followed the underlying elevator code. Advance Lifts then developed an inspection form following the same reasoning based on the latest draft of ANSI MH29.1. This form was then reviewed by elevator inspectors and further refined into its current form which is called the “Inspection Checklist For Industrial Scissors Lifts At Mezzanines” form AL-2010 Rev 1. This should be a big help to elevator inspectors and municipal building commissioners around the country. Landing lock option All multistage scissor lifts have some sway and some deflection inherent to their design. The BFL models typically used in mezzanine access lifts are exceptionally stout and rigid, but there still is some sway and deflection. This is by no means dangerous, but some people find this undesirable. Therefore, Advance Lifts created a Landing Lock (patent pending) which consists of two (2) locking pins that are extended into receivers when a unit arrives at an upper elevation. This eliminates sway and deflection at the loading edge of the platform. A discussion about specific applications is necessary to determine a recommendation on this option. By Henry J. Renken, Advance Lifts, Inc.
Alexander Baumann named new Managing Director of HUBTEX North America
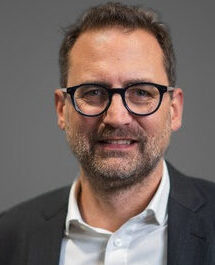
HUBTEX North America’s new Managing Director Alexander Baumann is assuming responsibility for the industrial truck manufacturer’s operations in its most important non-European market with immediate effect. The 51-year-old will focus on sales and marketing in his day-to-day work. The wholly owned subsidiary of the Fulda-based HUBTEX GmbH & Co. KG emerged from the Group’s acquisition of all shares in the general importer Design Storage & Handling (DSH). Alexander Baumann, who has over 20 years experience in the market for in-company material flows, will take charge of all the company’s sales and marketing activities in North America in his new position. “HUBTEX is among the world’s leading manufacturers of side loaders, order pickers, custom-built industrial trucks, and specialist vehicles for the transport of long, heavy, and bulky goods, and we want to consolidate this position further in North America in the steel processing industry as well as the building materials trade and the lumber industry,” Baumann says. He brings a wealth of expertise that HUBTEX needs as it shifts its focus to North America. He has already masterminded the successful delivery of pioneering projects in an intercultural environment in his previous roles at two companies, Genkinger (a manufacturer of custom-made industrial trucks) and bAKA (a specialist in bespoke material flow solutions).
ProMach acquires Zacmi
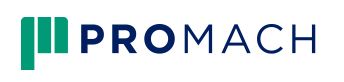
ProMach, a processing and packaging solutions, has announced that it has acquired Zanichelli Meccanica S.p.A. Known to the market as Zacmi, the Parma, Italy-based company is a manufacturer of filling, seaming, and pasteurization technology. The addition of Zacmi further expands ProMach’s extensive product portfolio and strengthens its position as one of the world’s largest providers of process, filling, and systems integration solutions. Founded in Parma in 1954, Zacmi is one of the food industry’s most respected suppliers of high-quality filling, closing, and sterilization equipment. Zacmi has a strong portfolio of filling machines for food and pet food products, as well as seamers for metal cans. The company also provides pasteurization tunnels for sterilizing food products and has developed rehydrated pea and legume preparation lines to support its food clients. Zacmi holds nearly 50 patents and is well known for its hygienic machine designs and its commitment to innovation. Since the company’s inception, over 2,500 Zacmi machines have been installed worldwide. With over 120 employees supporting its loyal customer base, Zacmi has operated as a typical “pocket-sized multinational,” a family business with an operating subsidiary in the United States and Italian-based R&D and manufacturing facilities dedicated to the development and assembly of innovative packaging equipment solutions. This acquisition will further strengthen ProMach’s product offering and allow it to solve a wider range of customer challenges, it will also offer Zacmi the opportunity to provide more solutions in the market sectors that ProMach currently serves, including beverage and powdered products. “We’re pleased to welcome the Zacmi team to ProMach,” said ProMach President and CEO, Mark Anderson. “The addition of Zacmi further strengthens our position as one of the industry’s leading suppliers of filling and process technology. This acquisition also allows us to add key products to ProMach’s overall packaging equipment portfolio, like food can filling and seaming. Most importantly, this acquisition further supports our strategic vision of providing customers around the world with complete solutions and support from a strong global partner.” Zacmi and its entire team will join ProMach’s Primary Packaging business line led by Business Unit President, Doug Stambaugh. With go-to-market product brands including Fogg, Modern, P.E. Labellers, and Zalkin, ProMach’s Primary Packaging business line provides a broad solution offering that includes filling, labeling, and closing. Zacmi will work closely with other ProMach brands to offer complete packaging line solutions. The acquisition allows ProMach to establish a powerful position in the food and pet care sectors where can filling and sterilization are required. “The Zacmi team has a reputation for designing strong technical solutions, manufacturing high-quality equipment, and for providing exceptional customer service,” said Mr. Stambaugh. “The addition of Zacmi to our Primary Packaging team not only strengthens our filling and closing portfolio, but it also significantly bolsters our ability to offer integrated systems. The opportunity to pair Zacmi filling and closing technology with other ProMach companies like Allpax, a global leader in retort, will allow us to better serve our customers by offering more complete solutions,” adds Mr. Stambaugh. Zacmi’s current leadership team will remain intact, with current Managing Director, Giorgio Boselli, assuming the role of VP & General Manager, and in recognition of her years of leadership as Zacmi’s President, Caterina Pagani will retain an honorary directorship. “We’re excited to be a part of the industry’s most respected packaging and processing company,” said Mr. Boselli. “ProMach has a proven track record of investing in its companies and leveraging its scale to better serve its customers. In ProMach, we have found a partner that will enhance the value of our business and ensure continuity for our customers and our people. Our employees will benefit from ProMach’s extensive portfolio of solutions and relationships, and we know that this move will ensure the continued growth of Zacmi.”
January 2024 starts out strong with 191 New Distribution and Supply Chain planned industrial projects
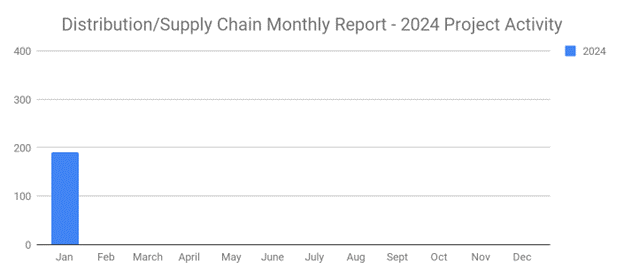
SalesLeads has announced the January 2024 results for the new planned capital project spending report for the Distribution and Supply Chain industry. The Firm tracks North American planned industrial capital project activity; including facility expansions, new plant construction, and significant equipment modernization projects. Research confirms 191 new projects in the Distribution and Supply Chain sector as compared to 204 in December 2023. The following are selected highlights on the new Distribution Center and Warehouse construction news. Distribution and Supply Chain – By Project Type Distribution/Fulfillment Centers – 21 New Projects Industrial Warehouse – 172 New Projects Distribution and Supply Chain- By Project Scope/Activity New Construction – 99 New Projects Expansion – 33 New Projects Renovations/Equipment Upgrades – 60 New Projects Closing – 7 New Projects Distribution and Supply Chain – By Project Location (Top 5 States) Texas – 20 New York – 16 Florida – 15 Wisconsin – 11 Michigan – 10 Largest Planned Project During January, our research team identified 6 new Distribution and Supply Chain facility construction projects with an estimated value of $100 million or more. The largest project is owned by Pathways Alliance, which is planning to invest $17 billion in the construction of a carbon capture and storage facility in WOOD BUFFALO, AB. They are currently seeking approval for the project. Top 10 Tracked Distribution and Supply Chain Project Opportunities MASSACHUSETTS: Energy solutions company is planning to invest $170 million for the construction of a wind farm terminal and staging facility in SALEM, MA. They are currently seeking approval for the project. Construction is expected to start in 2024, with completion slated for 2026. WISCONSIN: Corrugated packaging product mfr. is planning to invest $140 million for the construction of a 550,000 SF manufacturing and warehouse facility at 9423 Koessl Court in PLEASANT PRAIRIE, WI. Construction is expected to start in Spring 2024. FLORIDA: Global retail chain is planning for the construction of a 1.8 million SF distribution center in PORT ST. LUCIE, FL. Construction will occur in 2 phases. They will relocate their operations from 5851 45th St. in WEST PALM BEACH, FL upon completion. The site allows for a future 208,000 SF addition. IOWA: Public transportation authority is planning to invest $95 million for the construction of a warehouse, office, and maintenance facility on Vandalia Rd. in DES MOINES, IA. They are currently seeking approval for the project. Construction will occur in three phases, with completion of phase one slated for 2026. ONTARIO: Food processing company is planning to invest $76 million for the expansion and equipment upgrades at their grain terminal at Port Windsor in WINDSOR, ON. They are currently seeking approval for the project. TEXAS: Cold storage service provider is planning to invest $55 million for the construction of a 305,000 SF cold storage warehouse on Silent Valley Rd. in LOCKHART, TX. They are currently seeking approval for the project. Completion is slated for Spring 2025. VIRGINIA: Logistics service provider is planning to invest $50 million for the renovation and equipment upgrades on a recently acquired 254,000 SF warehouse facility on Lee Hwy. in ROANOKE, VA. They are currently seeking approval for the project. Completion is slated for early 2025. MICHIGAN: Global retail chain is planning to invest $42 million for the construction of a 158,000 SF warehouse facility in FLINT, MI. They are currently seeking approval for the project. Construction is expected to start in Spring 2024, with completion slated for late 2024. TEXAS: Commercial airlines are planning to invest $38 million for the renovation and equipment upgrades on a 509,000 SF distribution center in HUMBLE, TX. They have recently received approval for the project. CALIFORNIA: Fertilizer MFR. is planning to invest $30 million for the construction of a warehouse and processing facility in SANTA PAULA, CA. They are currently seeking approval for the project. About Industrial SalesLeads, Inc. Since 1959, Industrial SalesLeads, based in Jacksonville, FL is a leader in delivering industrial capital project intelligence and prospecting services for sales and marketing teams to ensure a predictable and scalable pipeline. Our Industrial Market Intelligence identifies timely insights on companies planning significant capital investments such as new construction, expansion, relocation, equipment modernization and plant closings in industrial facilities. The Outsourced Prospecting Services, an extension to your sales team, is designed to drive growth with qualified meetings and appointments for your internal sales team.
January 2024 delivers a slow 97 new Industrial Manufacturing Planned Projects
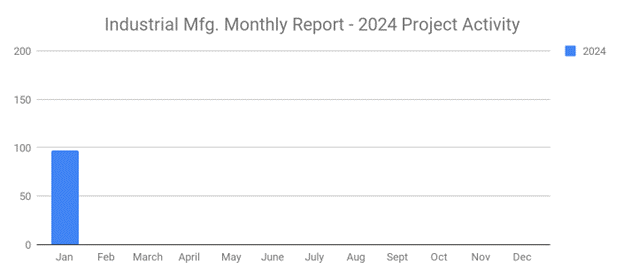
SalesLeads has announced the January 2024 results for the new planned capital project spending report for the Industrial Manufacturing industry. The Firm tracks North American planned industrial capital project activity; including facility expansions, new plant construction and significant equipment modernization projects. Research confirms 97 new projects in the Industrial Manufacturing sector as compared to 136 in December 2023. The following are selected highlights on new Industrial Manufacturing industry construction news. Industrial Manufacturing – By Project Type Manufacturing/Production Facilities – 85 New Projects Distribution and Industrial Warehouse – 78 New Projects Industrial Manufacturing – By Project Scope/Activity New Construction – 34 New Projects Expansion – 30 New Projects Renovations/Equipment Upgrades – 36 New Projects Plant Closings – 14 New Projects Industrial Manufacturing – By Project Location (Top 10 States) North Carolina – 11 Indiana – 7 Ontario – 7 Michigan – 6 California – 5 Ohio – 5 Washington – 5 Kentucky – 4 Massachusetts – 4 New York – 4 Largest Planned Project During January, our research team identified 12 new Industrial Manufacturing facility construction projects with an estimated value of $100 million or more. The largest project is owned by Honda Motor Company, which is planning to invest $14 billion in the construction of an EV battery manufacturing facility and is currently seeking a site in ONTARIO. Top 10 Tracked Industrial Manufacturing Projects MISSISSIPPI: Energy technology company is planning to invest $2 billion for the construction of an EV battery manufacturing facility in MARSHALL COUNTY, MS. They are currently seeking approval for the project. NORTH CAROLINA: Diesel engine MFR. is planning to invest $580 million for the expansion and equipment upgrades on their manufacturing facility in WHITAKERS, NC. They are currently seeking approval for the project. ILLINOIS: Copper products MFR. is planning to invest $500 million for the expansion and equipment upgrades on their manufacturing facility in EAST ALTON, IL. They are currently seeking approval for the project. CALIFORNIA: Semiconductor MFR. is planning to invest $432 million for the construction of a manufacturing facility in WEST OAKLAND, CA. They are currently seeking approval for the project. INDIANA: Building materials mfr. is planning to invest $200 million for the construction of a 300,000 SF manufacturing facility in ANDERSON, IN. They are currently seeking approval for the project. INDIANA: Semiconductor MFR. is planning to invest $152 million for the renovation and equipment upgrades on a 170,000 SF manufacturing facility at 301 N. Curry Pike in BLOOMINGTON, IN. They have recently received approval for the project. Completion is slated for Fall 2024. WISCONSIN: Corrugated packaging product MFR. is planning to invest $140 million for the construction of a 550,000 SF manufacturing and warehouse facility at 9423 Koessl Court in PLEASANT PRAIRIE, WI. Construction is expected to start in Spring 2024. CALIFORNIA: EV MFR. is planning for the construction of a 630,000 SF manufacturing and office facility on Avenue H in LANCASTER, CA. They are currently seeking approval for the project. NEW YORK: Biotechnology company is planning to invest $100 million for the renovation of a 235,000 SF laboratory, processing, and office facility at 1 Avon Pl. in SUFFERN, NY. They have recently received approval for the project. INDIANA: Military agency is planning to invest $100 million for the construction of a munition manufacturing facility in CRANE, IN. They are currently seeking approval for the project. About Industrial SalesLeads, Inc. Since 1959, Industrial SalesLeads, based in Jacksonville, FL is a leader in delivering industrial capital project intelligence and prospecting services for sales and marketing teams to ensure a predictable and scalable pipeline. Our Industrial Market Intelligence identifies timely insights on companies planning significant capital investments such as new construction, expansion, relocation, equipment modernization, and plant closings in industrial facilities. The Outsourced Prospecting Services, an extension to your sales team, is designed to drive growth with qualified meetings and appointments for your internal sales team.
CLARK Europe introduces new management
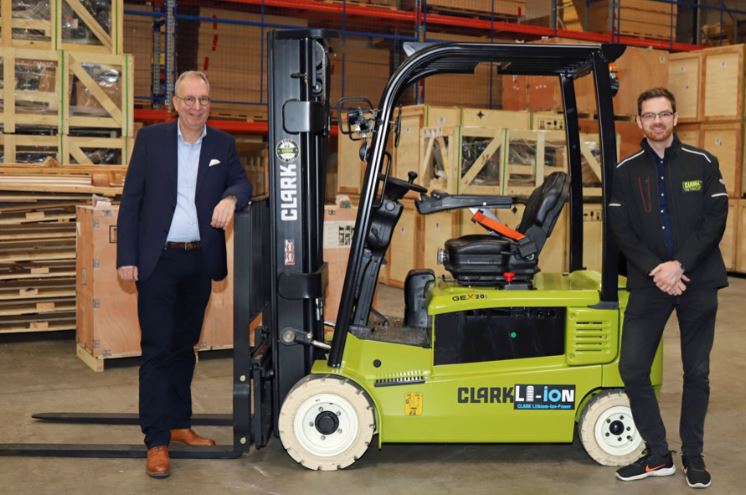
CLARK Europe GmbH, based in Duisburg, has expanded its management team. With this step, the industrial truck manufacturer wants to set the course for the upcoming generational change in good time. In addition to his role as Director of Sales and Marketing, Stefan Budweit will assume responsibility for operations management as COO (Chief Operating Officer) with immediate effect. Budweit has been with CLARK Europe since 2012 and can look back on more than 30 years of national and international experience in the field of material handling. Before joining CLARK Europe, he worked as a key account manager for Toyota and Jungheinrich, among others. Budweit started his career at CLARK Europe as a Business Development Manager. Here he was responsible for the strategic orientation and further development of CLARK Europe. As Regional Sales Manager in Scandinavia and parts of Germany, he was also instrumental in expanding the sales activities of the forklift specialist. Thomas Bach has also joined the management team as Director of R&D and Purchasing with immediate effect. Bach started his career at CLARK Europe as a development engineer in 2015 after completing a master’s degree in mechanical engineering. Here he demonstrated his skills in the design and development of industrial trucks and warehouse technology. In 2020, he took over as team leader of the design and development department, where he coordinates development and design projects, among other things. He also manages the collaboration with international suppliers and develops the product strategy and planning in coordination with CLARK’s global plants in the USA, Korea, Vietnam, and China. “With the new strategic positioning of our management team, we have optimally equipped ourselves for the future so that we can meet future challenges and the increasing demands of our customers even better,” explains Rolf Eiten, President & CEO of CLARK Europe, to whom the Sales and Finance divisions continue to report directly.
IDENTCO to demo space-saving pick & place label presenter at IPC APEX Expo
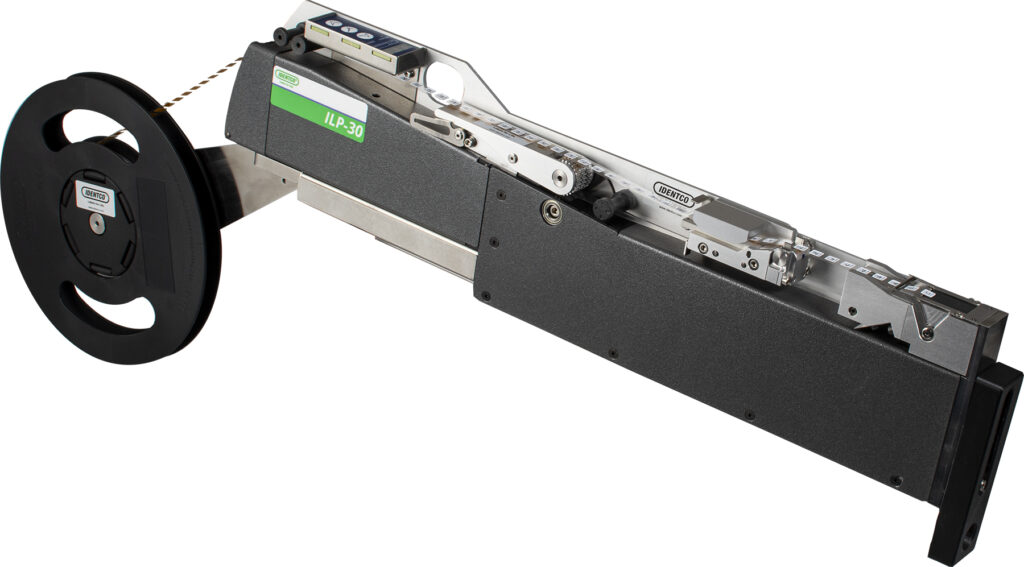
IDENTCO also will demonstrate its robust VortexID automated wire marking system, and PCB label series with company-exclusive substrate. IDENTCO, a manufacturer of high-performance labeling solutions for the power equipment, electronics, transportation, and general industrial sector, will highlight a variety of electronics marking systems and products at IPC APEX Expo, April 6-11 in Anaheim, CA. Among other solutions, at its Booth #3823, the company will offer live demonstrations of the ILP-30 Slimline Label Feeder for pre-printed label placement. Named for its slender 30mm width – half that of conventional feeders – the label presenter requires only one feeder position on pick & place machines, freeing up valuable space along congested SMT production lines. Providing precise and accurate placement, IDENTCO’s ILP-30 Slimline Label Feeder is suitable for label sizes from 3mm x 3mm to 25mm x 25mm and features an integrated compartment that collects liner materials for easy disposal without line stoppage. The module is compatible with many popular pick-and-place systems, and its reliable electronic operation yields low maintenance costs. The ILP-30 Slimline works best when paired with IDENTCO’s pre-printed labels, and aligns with the company’s emphasis on automation technologies that improve placement accuracy and application speed. Also at IPC APEX, IDENTCO will provide demonstrations of its recently introduced automated wire marking system whose stamina and speed set new benchmarks for wire and harness label application. The company’s VortexID can precisely apply up to 20 labels per minute – outpacing other automated units and doubling the most expedient manual setups – and operate 24/7, a stark departure from the single-shift limitations of competing models. VortexID features 600dpi printing capabilities, with labels applied via a vacuum plate with a rotating mechanism for reliable application on cylindrical products. Notably, IDENTCO’s new module is materials agnostic, expanding customer choice and potentially decreasing overall labeling materials costs. IDENTCO also will display its DuraTrack label series, which provides comprehensive traceability for printed circuit boards and electronic components. Engineered for use in surface mount technology and throughout the entire assembly process, DuraTrack thermal transfer printable labels can endure harsh fluxes, the latest cleaning chemistries, and high temperatures encountered in today’s circuit board assembly processes on both sides of the board. As a result, the label series is fully compatible with track & trace incorporation – an increasingly attractive internal quality control and supply chain transparency feature for brand owners producing high-leverage electronics. Finally, IDENTCO will showcase a series of labels for PCB applications featuring a substrate developed exclusively for IDENTCO by a prominent industry materials and coating supplier. The PCB labels easily withstand prolonged, repeated exposure to the chemicals and high temperatures typical to post-production washing processes. Helpfully, the series is designed for on-demand thermal transfer printing of variable information – a plus for electronics companies incorporating serialization and/or anti-counterfeiting coding into their production practices.
RightHand Robotics signs agreement with Staples® to deploy AI-Powered picking robots
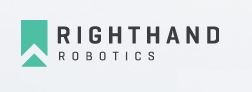
RightHand Robotics, an autonomous AI robotic picking solution for order fulfillment, has announced a multi-year agreement with Staples Inc., America’s leader in workspace products and solutions. The agreement allows Staples to deploy and install the company’s RightPick™ item-handling system to automate operations for higher service levels and Next-Day Delivery to over 98% of the U.S. Managing an industry-leading distribution and fulfillment network with various levels of AI and automation, Staples has long been an innovator in the U.S. market. “We have always valued automation, and we see it as the future of eCommerce picking,” said Amit Kalra, Chief Supply Chain Officer at Staples. “After evaluating other solutions, the RightPick system met our high performance and reliability standards, picking items with different shapes, packaging, sizes, and weight.” The RightPick system is an autonomous item-handling robot powered by advanced hardware, sensor suite, and RightPick AI software designed for a wide range of end-to-end warehouse tasks. It offers damage-free picking across a broad range of items and provides industry-leading performance, reliability, throughput, and safety. Through close collaboration with Staples, RightHand Robotics developed new features that have nearly doubled the range of items that a RightPick station can handle while reducing the number of required interventions by 80%. These advancements have far-reaching implications beyond the Staples brand, benefiting a wide range of industries and applications. Brian Owen, CEO of RightHand Robotics, shared, “Our RightPick system sets a new standard in the flexibility, autonomy, and reliability of warehouse robotics. We’re thrilled that Staples recognized the benefits of using our technology to further enhance their automation strategy. It’s great to team up with an established industry leader to optimize their fulfillment operations.”
Novel Destuff-It™ Machine by Gorbel® primed to shake up the supply chain industry at MODEX 2024
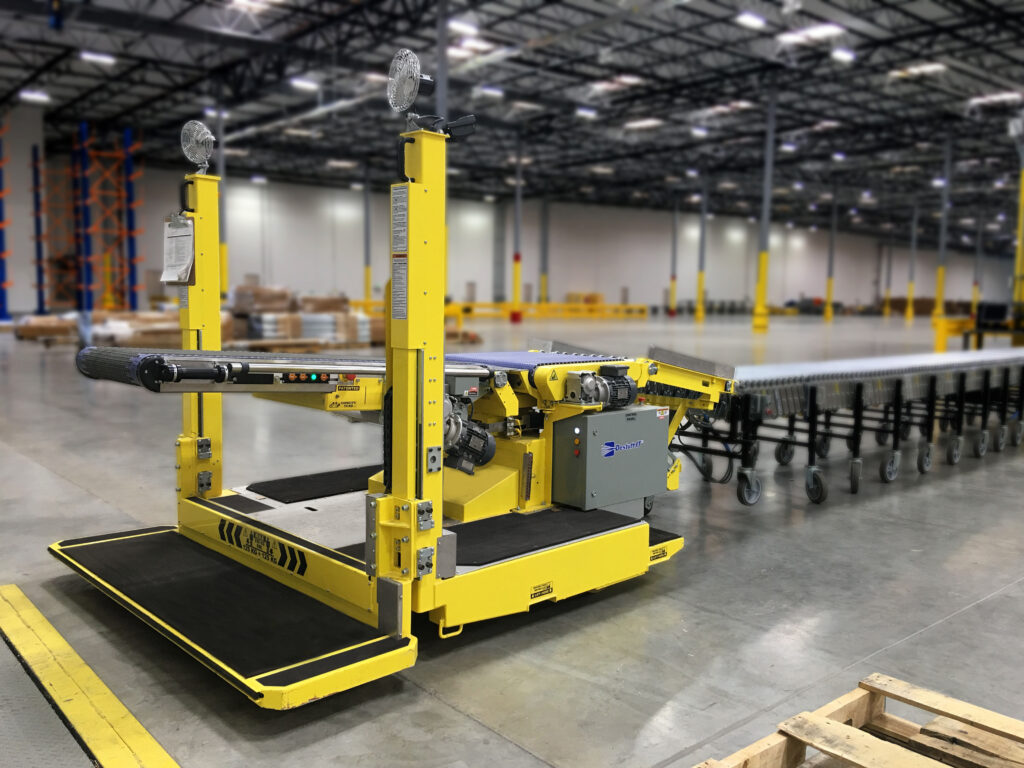
Engineered to load and unload trailers or floor-loaded products, the Destuff-it™ offers an ergonomic solution for an industry facing rapid growth amidst labor shortages Gorbel®, a material handling innovator, is set to exhibit its groundbreaking Destuff-it™ machine at the highly anticipated MODEX 2024 supply chain industry trade show in Atlanta from March 11-14. The Destuff-it™ represents an ergonomic approach to material handling, defined by semi-automation that assists workers instead of displacing them. Featuring an adjustable hydraulic platform, the machine allows one or two workers to precisely position themselves against floor-loaded product walls for efficient handling. Instead of repetitive reaching or bending, the Destuff-it™ brings workers to the products to significantly reduce strain and fatigue. This is revolutionary for operations dealing with a high volume of trailers and labor turnover, especially in warehouses or distribution centers. “Most containers and trailers are floor-loaded, meaning there are no pallets, just boxes stacked from the floor to the ceiling,” said Vice President of Sales and Customer Experience Pete Friedrich. “It’s a tiring job to do if you’re just having boxes all day long with no assistance from any other kinds of equipment.” Gorbel® is excited to exhibit the Destuff-it™ at MODEX 2024, along with their renowned Overhead Solutions, and showcase how these innovative products align with their mission to “Improve People’s Lives.” Attendees can experience live demonstrations and interact with a team of product experts.
ORBIS to showcase industry-leading packaging innovations at MODEX 2024
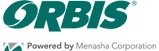
Supply chain leaders and executives attending MODEX 2024 this March will have the opportunity to see the latest in sustainably produced packaging products and automated packaging technologies, all courtesy of ORBIS Corporation. “At ORBIS, we’re immensely proud of our ongoing contributions to a more efficient and sustainable supply chain,” says Lynn Hediger, vice-president of product management. “Our reusable totes and pallets improve the flow of product in today’s automated systems and the overall supply chain. We design products to interface seamlessly in automated systems to drive repeatable performance and system uptime. We believe the relationships we’ve forged in this space are a testament to the strength of our vision for supply chain sustainability, and we’re proud to display our products with those of other industry leaders.” In addition to the latest sustainable packaging products from ORBIS, visitors to the ORBIS booth will have the opportunity to see products in-action from partner manufacturers, including: Agilox. AGILOX is a leading manufacturer of Autonomous Mobile Robots (AMRs) that provide highly innovative material handling solutions. The company’s mission is to revolutionize the world of AMRs with their robots focusing on ease of use and scalability, allowing users to seamlessly integrate new AMRs and adjust workflows. The robots move their loads autonomously by navigating warehouses while optimizing routes in real-time, offering unique advantages over centralized systems. All components are developed in-house. Established in Austria in 2009, AGILOX has a global presence, serving customers in Europe, North America, and Asia, with the US head-office located in Atlanta, GA. AGILOX will demo its Autonomous Mobile Robots at this year’s MODEX 2024 in Atlanta (AGILOX Booth C7492 & Orbis Booth B2809). Visitors will get a chance to see the AMRs interfacing with ORBIS’ new 40 x 48 Odyssey Pallet and learn more about the unique advantages of the AGILOX technology: precise navigation, movement in tight spaces, stacking, and certified safety features. Black-I Robotics.Black-I Robotics’ revolutionary Fullscope mobile heavy lift robotic arm, riding atop an Autonomous Mobile Robot (AMR), helps resolve the logistics industry’s most severe problem, worker scarcity. The system offsets up to five workers per 24-hour shift, while its hot swap battery function enables the unit to operate 24×7. The robot features a range of patented and proprietary technology, including an AI-based vision system featuring multiple 2D and 3D cameras that live stream an optimum path to storage spaces, securely and safely picking and placing totes and bins. The robotic arm, capable of lifting up to 100 pounds, twice the capacity of other heavy lift arms, will be displayed with an AMR handling ORBIS AROS® totes. AROS totes are reusable, recyclable, and designed specifically for automated storage systems. The uniformity that ORBIS’ reusable containers offers makes the process faster and more accurate. Combi Packaging Systems. As a premier manufacturer of automated packaging solutions, Combi offers custom-designed robotic packaging and palletizing systems, case packers, and more. Combi equipment will be displayed with ORBIS PlastiCorr® reusable corrugated boxes. PlastiCorr is the first reusable brown box replacement and features all-plastic construction for water and moisture resistance, box durability, and merchandise protection. ORBIS PlastiCorr boxes will run through the automated Combi 2-EZ HS 20 Case Erector and associated equipment, the TBS-100 Case Sealer and EZ-PZ 8 Palletizer. These cases will be erected, taped and palletized, with a co-bot, on this automated system. Combi is a worldwide provider of industrial packaging systems. Combi engineers and manufactures case erectors, tray formers, case sealers, case packers, robotic packaging systems and ergonomic hand-packing stations. Steel King Industries. Reusable Odyssey pallets in drive-through Steel King racking. Our Odyssey line of pallets hold up to 2,800 lbs loads and travel 400+ trips in the supply chain. Steel King Industries, Inc., is a leading manufacturer racks that improve operational efficiency in a variety of environments including manufacturing, assembly, distribution centers, storage facilities, and warehouses. Steel King is the nation’s only single-source manufacturer of pallet racks, drive in rack, flow rack, pushback rack, pick modules, mezzanines/work platforms, cantilever racks, portable racks, industrial containers, custom shipping racks, and industrial safety guard railing. Visit Steel King at MODEX Booth B4824. In addition, visitors to the ORBIS booth at MODEX will have the chance to see other innovative products from ORBIS. ORBIS XpressPickup® system designed especially for buy-online/pick-up in-store applications. This innovative tote design features enhanced dolly and cart capabilities, and can help streamline the picking, staging, and delivery of curbside orders. ORBIS will also feature its OPTEBulk sleeve pack system for warehousing and storage, metal racks for automotive part packaging, and its Bulkpak containers for part shipments. “The supply chain and its associated industries are evolving as quickly as any other industries today,” continues Hediger. “We’re looking forward to being at MODEX, speaking with customers, and showing off some of the most exciting innovations in packaging and automation technologies.” ORBIS will also be presenting two on-floor seminar options: Tue. Mar. 12 | 12:45 PM – 1:30 PM — Managing Your Reusable Pallet Program to Accelerate Efficiencies Wed. Mar. 13 | 2:30 PM – 3:15 PM — Maximizing Success when Implementing Reusable Totes and Pallets The MODEX show “brings the entire supply chain ecosystem together to showcase…supply chain solutions from over 1,100 of the leading providers” and boasts an attendance of over 45,000. The event runs March 11-14, 2024, at the Georgia World Congress Center, Atlanta.
Port of Long Beach cargo increases in January
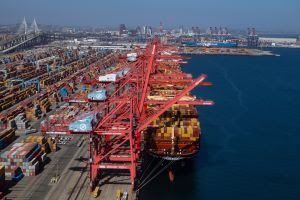
Retailers push to fill warehouses ahead of Lunar New Year celebrations Trade moving through the Port of Long Beach rose in January as retailers stocked up ahead of Lunar New Year, when east Asian factories typically close for up to two weeks. Dockworkers and terminal operators moved 674,015 twenty-foot equivalent units (TEUs) last month, up 17.5% from January 2023. Imports increased 23.5% to 325,339 TEUs and exports were down 18.1% to 86,525 TEUs. Empty containers moved through the Port increased 28% to 262,151 TEUs. “Retailers stocked their warehouses in January ahead of the slower import activity we typically see during Lunar New Year celebrations,” said Port of Long Beach CEO Mario Cordero. “We are ready to grow our volumes and hope to see continued growth through 2024 as we gradually recapture market share.” “The waterfront workforce and terminal operators are energizing the economy by keeping the goods moving at the Port of Long Beach,” said Long Beach Harbor Commission President Bobby Olvera Jr. “We’re staying the course by attracting business, operating sustainably and developing projects that will ensure our long-term growth.” The strong start to 2024 marks the fifth consecutive monthly year-over-year increase following 13 months of declines in cargo movement at the Port. Complete cargo numbers here The Port of Long Beach is a global green port initiative and top-notch customer service, moving cargo with reliability, speed, and efficiency. As the premier U.S. gateway for trans-Pacific trade, the Port handles trade valued at $200 billion annually and supports 2.6 million jobs across the United States, including 575,000 in Southern California. In 2023, industry leaders named it “The Best West Coast Seaport in North America” for the fifth consecutive year. During the next 10 years, the Port is planning $2.2 billion in capital improvements aimed at enhancing capacity, competitiveness, and sustainability.
U.S. Rail Traffic for the week ending February 10, 2024
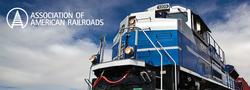
The Association of American Railroads (AAR) has reported U.S. rail traffic for the week ending February 10, 2024. For this week, total U.S. weekly rail traffic was 484,840 carloads and intermodal units, up 4.5 percent compared with the same week last year. Total carloads for the week ending February 10 were 220,362 carloads, down 2.5 percent compared with the same week in 2023, while U.S. weekly intermodal volume was 264,478 containers and trailers, up 11.1 percent compared to 2023. Five of the 10 carload commodity groups posted an increase compared with the same week in 2023. They included chemicals, up 1,854 carloads, to 33,109; motor vehicles and parts, up 1,769 carloads, to 15,028; and grain, up 1,687 carloads, to 21,551. Commodity groups that posted decreases compared with the same week in 2023 included coal, down 7,264 carloads, to 61,908; nonmetallic minerals, down 3,111 carloads, to 26,637; and miscellaneous carloads, down 1,066 carloads, to 8,123. For the first six weeks of 2024, U.S. railroads reported a cumulative volume of 1,245,530 carloads, down 6.4 percent from the same point last year; and 1,470,492 intermodal units, up 6.5 percent from last year. Total combined U.S. traffic for the first six weeks of 2024 was 2,716,022 carloads and intermodal units, an increase of 0.2 percent compared to last year. North American rail volume for the week ending February 10, 2024, on 12 reporting U.S., Canadian, and Mexican railroads totaled 329,758 carloads, down 1.4 percent compared with the same week last year, and 345,065 intermodal units, up 8.9 percent compared with last year. Total combined weekly rail traffic in North America was 674,823 carloads and intermodal units, up 3.6 percent. North American rail volume for the first six weeks of 2024 was 3,775,396 carloads and intermodal units, down 0.8 percent compared with 2023. Canadian railroads reported 92,811 carloads for the week, down 0.5 percent, and 69,516 intermodal units, up 2.9 percent compared with the same week in 2023. For the first six weeks of 2024, Canadian railroads reported a cumulative rail traffic volume of 905,968 carloads, containers, and trailers, down 4.7 percent. Mexican railroads reported 16,585 carloads for the week, up 9.1 percent compared with the same week last year, and 11,071 intermodal units, down 2.3 percent. Cumulative volume on Mexican railroads for the first six weeks of 2024 was 153,406 carloads and intermodal containers and trailers, up 5.9 percent from the same point last year. View Rail Traffic Charts