CHEP appoints Xavier Garijo to newly created CEO Americas position
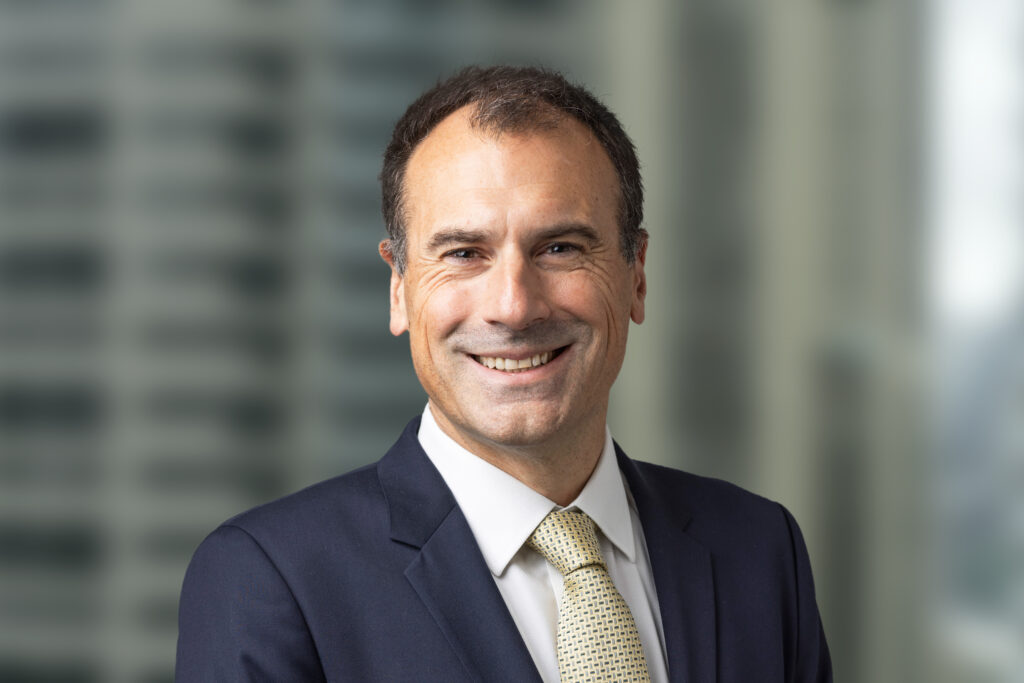
CHEP, a supply chain solutions, announced the appointment of Xavier Garijo as the CEO of Americas effective Jan. 1, 2024, following the announcement that CHEP North America’s president, Laura Nador, left her role on Dec. 31, 2023. Paola Floris, President of CHEP Latin America, and Frank Bozzo, Vice President and General Manager of CHEP Canada and Pallecon North America, will continue in their current capacities and report directly to Garijo. Garijo brings 25 years of experience managing global consumer good supply chains and operations, and multi-industry global logistics businesses. He was most recently a Global Executive Board Member for Contract Logistics at DB Schenker, a German logistics provider. He was responsible for the global contract logistics business, which had a workforce of 40,000 people in 60 countries. Prior to that, Garijo worked in the U.S. and Europe, for 20 years, including managing end-to-end supply chains and operations for Revlon as Chief Supply Chain Officer and in roles of increasing responsibility with Reckitt Benckiser and Unilever. In this newly-created position, Garijo will lead the Americas region combining the previously separate CHEP North America and CHEP Latin America business units. This change reflects the increasing collaboration and interconnectivity between CHEP’s North American and Latin American operations and will help further serve CHEP’s customers and retail partners across the globe. “I am delighted to be joining Brambles as it progresses its digital transformation to ensure ongoing, profitable growth and strengthen further our customer value proposition,” said Garijo. “The business has a vital role in supply chains, which, combined with its leading approach in sustainability, provides an exceptional foundation for continued success. I look forward to working with our internal teams, customers and vendors to drive value for all stakeholders.” As the Americas region continues its transformation, the organization is grateful for the strong contributions Laura Nador, CHEP North America’s former president, delivered in driving operational and safety excellence as well as her care for CHEP’s people and customers. “Xavier is well positioned to build on Laura’s legacy and successes to serve the market needs of today and the future,” said Graham Chipchase, CEO at Brambles, CHEP’s parent company. “As the Americas region moves into this new era, Xavier’s extensive experience in global supply chains and commercial management across the fast-moving consumer goods and logistics industries make him a fantastic choice to elevate the business and lead growth.”
Upcoming online auction features like-new equipment from Colorado ‘Green Hydrogen’ R&D Facility
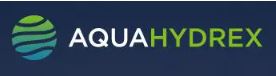
In court-ordered bankruptcy sale, Tiger Liquidity Services Energy Partners offers assets and IP of renewable energy firm AquaHydrex A Jan. 18 online auction by Tiger Liquidity Services Energy Partners (TLSEP), a strategic alliance between Tiger Group and Liquidity Services, brings to market assets from AquaHydrex’s 32,000-square-foot, green hydrogen prototype and R&D facility near Denver. Bidding opens at SoldTiger.com and AllSurplus.com at 10 a.m. (MT) on Thursday, Jan. 11. The event closes at 10 a.m. (MT) on Thursday, January 18. “The multimillion-dollar, court-ordered bankruptcy sale boasts many examples of high-quality, like-new machinery and equipment,” said Chad Farrell, Managing Director, Tiger Commercial & Industrial. “AquaHydrex had acquired a wide array of highly desirable laboratory, R&D and test and measurement equipment, making this online bankruptcy auction a strong opportunity for buyers in multiple sectors,” Farrell noted. “We also anticipate strong energy-sector interest in the gas-processing equipment that AquaHydrex employed as part of its electrolysis-based approach to extracting hydrogen from H2O.” “The sale features AquaHydrex’s intellectual property assets, such as patents, blueprints, proprietary tooling, molds, and more,” added Nick Jimenez, Vice President of Global Business Development at Liquidity Services. “In the renewable energy space, there is intense interest in—and government incentives for—green hydrogen. These IP assets could be valuable to operators looking to capitalize on these opportunities.” Lab equipment available in the auction includes autoclaves, environmental chambers, vacuum-tube furnaces, ovens, electron microscopes, spraying systems, chillers, fume hoods, mixers, surface plates, lab scales, glassware and more. Among the test and measurement assets are spectrometers, spectrophotometers, oscilloscopes, multimeters, tensile testers, digital micrometers (large quantity), calipers, gauges, inspection equipment, battery testers, inspection microscopes and more. The available R&D equipment includes: Matrix Technologies 10-cell hydrogen/oxygen process skid Clamping rig with 1- to 10-cell capacity (6,000 amps with hydraulic pump) Melco Steel autoclaves Agilent and MKS spectrometers Maccor Series 4000 battery tester Two unused 7,000-amp DC power supplies AquaHydrex operated an extensive machine shop at the Colorado facility. Available in the auction are: Haas vertical CNC milling machines Laser welders Lathes, spot welders, industrial robots, variable-speed band saws, drill presses, blasters, shop presses Sanders, grinders, bench vices, air compressors, parts cabinets, dust collectors, engine hoists, tooling, toolboxes Hundreds of cordless and manual hand tools Finally, a large quantity of plant support, material handling and office and IT assets are available in the bankruptcy auction. AquaHydrex was launched in 2012 and obtained substantial investment backing. Relying on renewable forms of energy such as solar and wind, AquaHydrex focused on deriving green hydrogen from water electrolysis, thereby assisting in the decarbonization of industrial operations, transportation, agriculture and other sectors. Inspections are available on Wed., Jan. 17, from 10 a.m. to 4 p.m. (MT). To arrange an inspection or obtain other information, email auctions@tigergroup.com or call 805 497-4999. Bidders must register in advance. For asset photos, descriptions, and other information, visit SoldTiger.com For more information and to view the available equipment, go to AllSurplus.com.
U.S. Rail Traffic for the week ending January 6, 2024
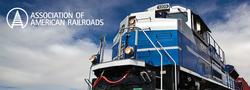
The Association of American Railroads (AAR) has reported U.S. rail traffic for the week ending January 6, 2024. For this week, total U.S. weekly rail traffic was 417,257 carloads and intermodal units, up 2.3 percent compared with the same week last year. Total carloads for the week ending January 6 were 208,176 carloads, up 0.9 percent compared with the same week in 2023, while U.S. weekly intermodal volume was 209,081 containers and trailers, up 3.7 percent compared to 2023. Seven of the 10 carload commodity groups posted an increase compared with the same week in 2023. They included chemicals, up 2,858 carloads, to 29,083; farm products excl. grain, and food, up 1,199 carloads, to 16,362; and grain, up 1,083 carloads, to 21,667. Commodity groups that posted decreases compared with the same week in 2023 were motor vehicles and parts, down 2,318 carloads, to 9,429; coal, down 2,190 carloads, to 61,747; and nonmetallic minerals, down 1,662 carloads, to 24,312. For the first week of 2024, U.S. railroads reported a cumulative volume of 208,176 carloads, up 0.9 percent from the same point last year; and 209,081 intermodal units, up 3.7 percent from last year. Total combined U.S. traffic for the first week of 2024 was 417,257 carloads and intermodal units, an increase of 2.3 percent compared to last year. North American rail volume for the week ending January 6, 2024, on 12 reporting U.S., Canadian, and Mexican railroads totaled 307,010 carloads, up 1.3 percent compared with the same week last year, and 304,136 intermodal units, up 12.5 percent compared with last year. Total combined weekly rail traffic in North America was 611,146 carloads and intermodal units, up 6.6 percent. North American rail volume for the first week of 2024 was 611,146 carloads and intermodal units, up 6.6 percent compared with 2023. Canadian railroads reported 85,204 carloads for the week, up 2.2 percent, and 59,601 intermodal units, down 1.5 percent compared with the same week in 2023. For the first week of 2024, Canadian railroads reported a cumulative rail traffic volume of 144,805 carloads, containers, and trailers, up 0.7 percent. Mexican railroads reported 13,630 carloads for the week, up 2.5 percent compared with the same week last year, and 35,454 intermodal units, up 329.9 percent. Cumulative volume on Mexican railroads for the first week of 2024 was 49,084 carloads and intermodal containers and trailers, up 127.8 percent from the same point last year. To view the Rail Traffic charts, click here.
Episode 451: Unlocking 3PL growth with Joe McIntyre of Twelve48
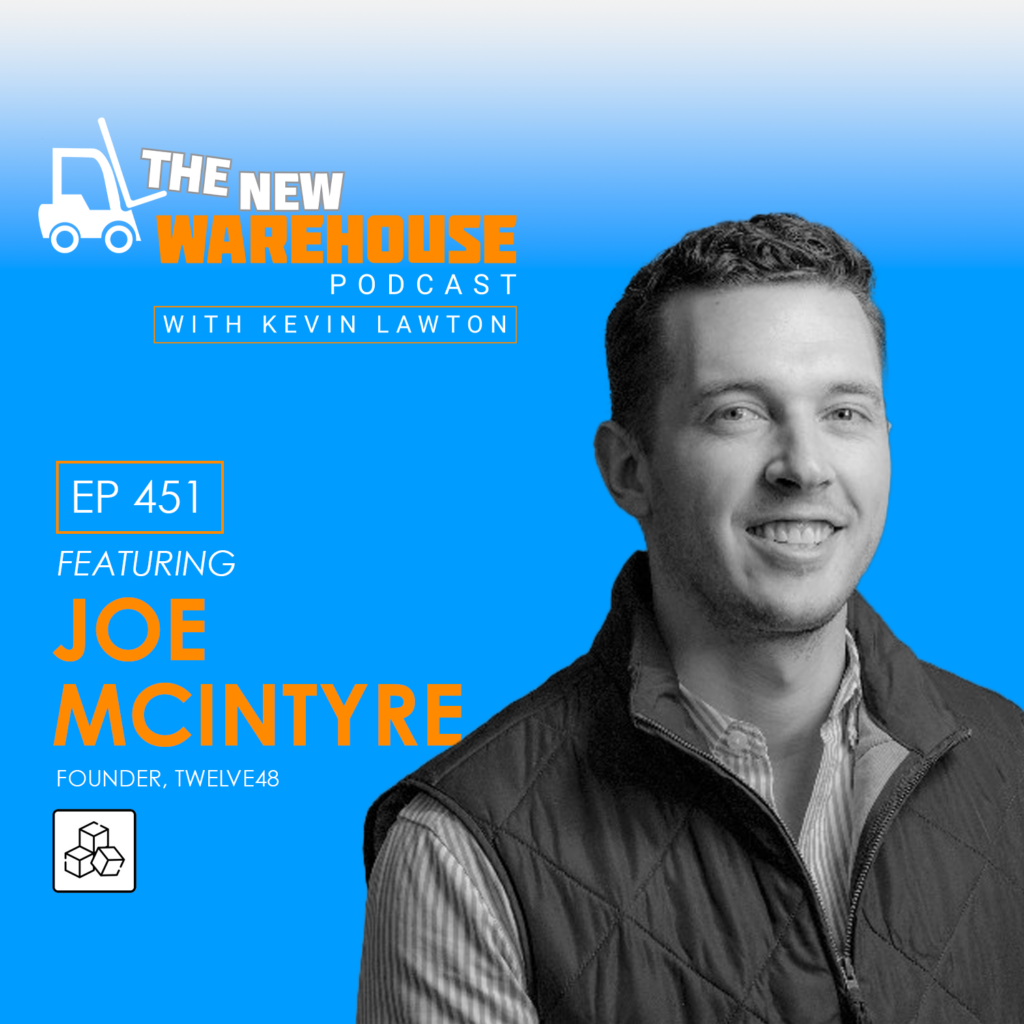
Joe McIntyre, the founder and principal of Twelve48, joins this episode of The New Warehouse to discuss the logistics and fulfillment world. This episode delves into McIntyre’s extensive experience and the innovative approach Twelve48 takes toward optimizing 3PL and brand relationships. Be sure to tune in to explore McIntyre’s journey through the industry, the inception of Twelve48, and why football great Mike Singletary may have a bone to pick with him. The Journey to Twelve48 McIntyre shares his career trajectory, emphasizing the importance of partnerships and the dynamic power swings between shippers and carriers. “I had a role very early in my career doing carrier partnerships and performance,” McIntyre recounts, highlighting the buzzword ‘shipper of choice’ and its influence on his career path and the founding of Twelve48. Reflecting on his stint in HR, McIntyre articulates its profound impact on his approach to operations. McIntyre stresses how this experience reshaped his understanding of operations and employee management, subsequently improving his effectiveness in leadership roles. How Twelve48 Bridges the Gap for Successful 3PL and Brand Relationships McIntyre discusses the challenges brands and 3PLs face in forming productive partnerships. “Not fully knowing who they are and therefore knowing who they need,” he notes as a standard stumbling block. In the crucial growth phase, retailers often grapple with transitioning from a scrappy, all-hands-on-deck mentality to a structured operational approach. While they excel in brand building and marketing, their supply chain and operations inexperience can strain the dynamic relationship with 3PLs. Effective communication and understanding forecasts are vital, as a retailer’s decisions significantly impact the 3PL’s capacity to manage labor and serve other clients. Conversely, 3PLs must clearly articulate their capabilities and set realistic expectations to ensure alignment with the retailer’s needs. Bridging this gap requires mutual effort, education, and a shift from viewing the relationship as merely transactional to a strategic partnership. He emphasizes the importance of understanding and communication between parties to ensure a mutually beneficial relationship. Key Takeaways from Twelve48 Value of Partnerships and Relationships: Joe discusses his early career in large retail and the importance of carrier partnerships and performance in the freight market. He emphasizes the concept of being a ‘shipper of choice’ and how providing consistency, even if it doesn’t always mean getting the lowest cost, was a critical lesson that influenced his career and the founding of Twelve48. Impact of HR Experience on Operations: Joe reflects on a pivot in his career when he moved into an HR role, focusing on employee relations at stores and warehouses. This experience was pivotal for him, providing a new perspective on people management and its critical role in operations. He learned about leadership development, the importance of creating a positive work experience, and how these factors directly impact operational efficiency and success. The Genesis and Mission of Twelve48: Joe describes the hypothesis behind starting Twelve48, driven by his encounters with brand owners who were phenomenal at product and brand development but lacked operational experience. He saw an opportunity to match brands and 3PLs and prepare them to make informed decisions. This mission was based on the observation that many great brands and 3PLs fail to connect effectively due to a lack of understanding and preparation. The New Warehouse Podcast EP 451: Unlocking 3PL Growth with Joe McIntyre of Twelve48
PTDA 2024 Industry Immersion Conference offers essential knowledge building and networking for those new to the industry
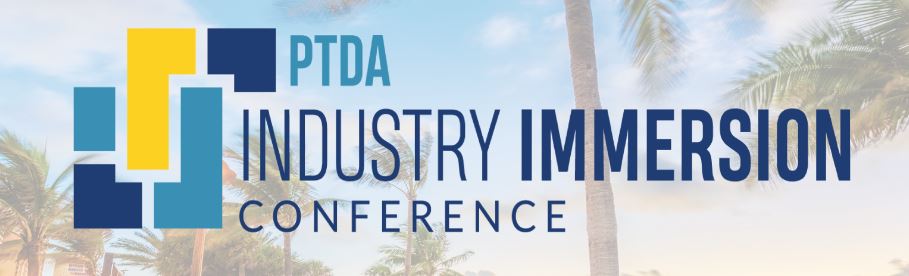
The Power Transmission Distributors Association (PTDA) will host a new talent development event, the PTDA 2024 Industry Immersion Conference in Hollywood, Fla. on February 29, 2024. This intensive program is designed to help those who are new to the power transmission and motion control (PT/MC) industry grow the interpersonal skills, networking capabilities and industry essentials for building successful relationships with coworkers, executives and customers. “Every PT/MC employer wants to develop their employees into trusted and valued contributors to their team, company and customers’ success,” says John Newman, vice president sales—Americas, BDI and Industry Immersion Task Force Chair. “This event is an exceptional investment in helping new talent hone the skills they need to outperform in 2024 and beyond.” The Industry Immersion Conference is designed to advance professional perspectives and experience of emerging leaders within the PT/MC industry. The curriculum of the program has been developed by experienced members and includes: A panel discussion designed to help newcomers discover best practices when working with channel partners. Panelists include veteran PTDA members Jeff Cloud (IBT Industrial Solutions) as moderator and Barabara Ross (Pfannenberg USA), Steve Kalgreen (Akron Bearing Company, Inc.) and AnnaMarie Donaldson (Regal Rexnord). A member panel aimed to help attendees understand how to maintain relationships with customers. Jason Sorce (Bando USA, Inc.) will moderate and John Newman (BDI), Mike Pulley (Bartlett Bearing Co., Inc.) Mitch Bouchard (General Bearing Service Inc.) and Darin Davenport (Affiliated Distributors, Inc.) will serve as panelists. Additional programming will include learning about various PTDA resources and programs to assist attendees in their roles and informal networking with PTDA leadership. For more information, visit ptda.org/IndustryImmersion.
Hyster introduces two new cost-effective integrated lithium-ion forklifts
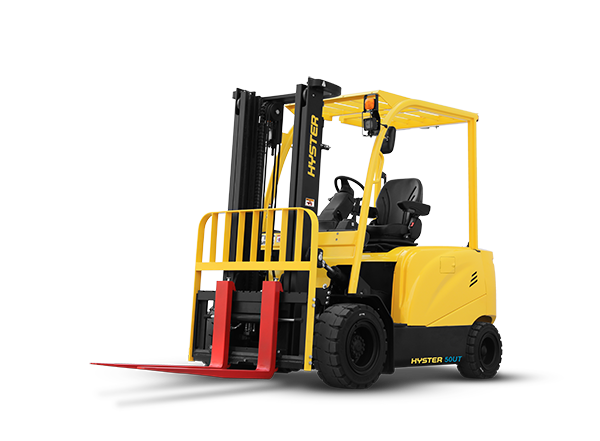
Hyster Company announces the expansion of its integrated lithium-ion forklift lineup with the addition of the three-wheel J32-40UTTL and four-wheel J30-70UTL. The UTTL and UTL are both powered by a factory-installed lithium-ion battery and provide a new avenue for electrifying forklift applications with less demanding requirements in industries such as chemicals and plastics, third-party logistics and trucking. Available in capacity ranges of 3,200-to-4,000-pounds and 3,000-to-7,000-pounds respectively, the trucks are designed to help an even broader range of operations meet sustainability targets and productivity goals through the benefits of this advanced electric power source, including zero tailpipe emissions, fast charging times, consistent power delivery and zero battery maintenance. The trucks complement existing models in the UT series and create opportunities to electrify applications when doing so had historically been cost-prohibitive. “The counterbalanced forklift market is seeing an accelerating shift towards electric, signaling electrification and sustainability as priorities across industries and in materials handling in particular. Advances in motive power, especially lithium-ion, are the catalysts driving the transition,” said James Nielson, Senior Business Product Manager for Motive Power and Electrification, Hyster. “These new UT models deliver a competitive value that makes lithium-ion more accessible to more applications, without complex warranty or support limitations.” Hyster provides service and warranties on the truck, battery, and charger for maximum uptime, productivity, and customer satisfaction. The lithium-ion battery can fully charge in about two-and-a-half hours and opportunity charging allows the trucks to work for the majority of a full day. The trucks also offer several ergonomic features, including a low step height, a small, adjustable steering wheel, and a wide-view mast that helps maximize visibility and supports operator comfort. The Hyster UT line was initially launched in 2019 with a series of lift trucks powered by internal combustion engines. The series was further expanded in 2022 with several electric warehouse models and earlier in 2023 with multiple sit-down counterbalance lead acid battery-powered trucks.
Creform to feature several of its products at 2024 Assembly Show South
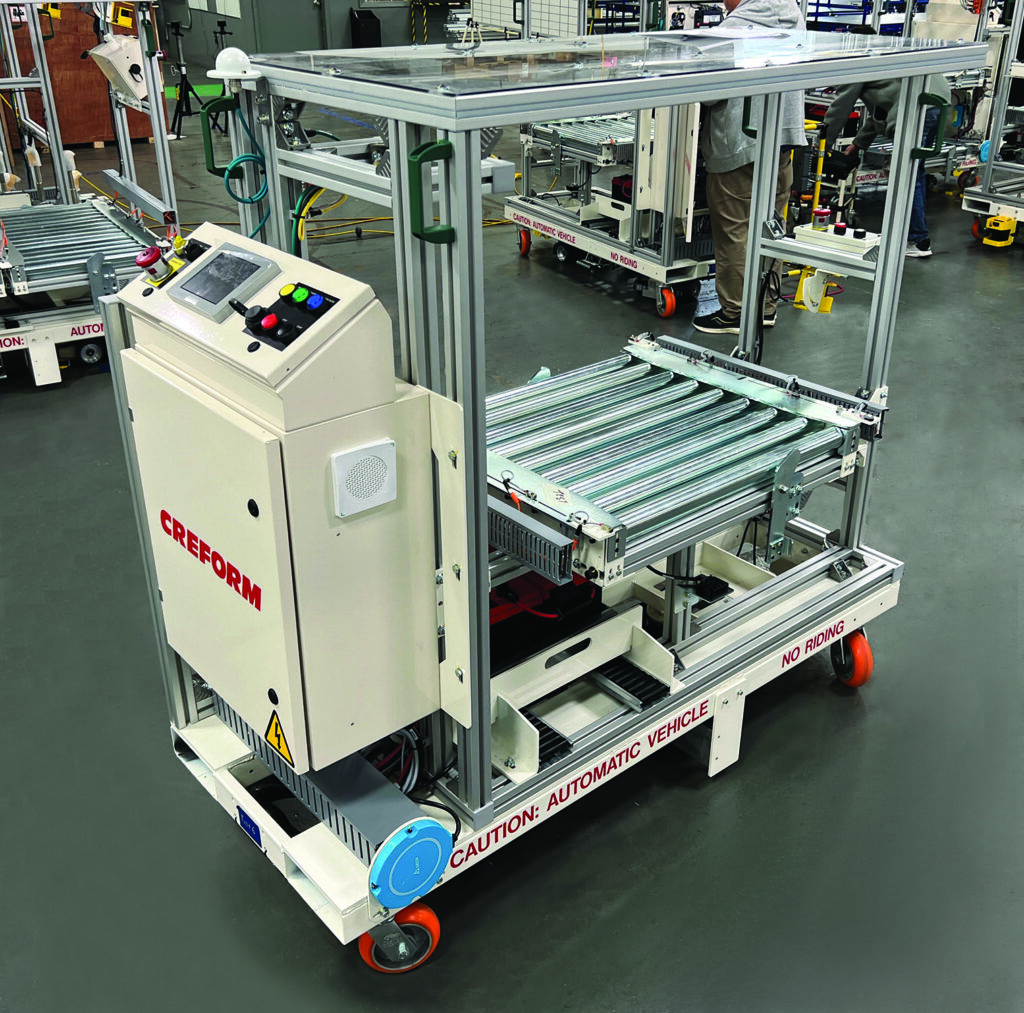
Creform Corporation, a manufacturer of unique products for the design and building of material handling structures and AGVs, will showcase AGVS, gravity roller conveyors, workstations, carts, and flow racks in booth 863, at the 2024 Assembly Show South, May 1-2, 2024 Nashville, TN. Highlighting the exhibit will be gravity roller conveyors and an AGV which can control up to 50 courses with 128 commands each via HMI touch screen and built-in RFID for traffic control. The Creform System consists of over 700 components including plastic-coated steel pipe, fittings, and accessories for building AGVs, flow racks, carts, workstations, and other material handling structures. The company has over 15 gravity roller conveyors, including Placon and skatewheel. Gravity roller conveyors are effective for difficult material handling challenges because their superior construction and wide plastic wheels accommodate a broad range of applications while being noticeably quiet. AGVs, from simple bolt-on units to sophisticated low-profile tuggers. Systems can be simple loops for kit cart delivery to plant-wide material delivery that are managed by Creform’s traffic control system. Units have a variety of load ratings, configurations, and power sources. Flow racks are designed and built as single-lane parts feeders to supermarket systems for kitting. As with all Creform flow racks, capacity, size, and configurations are all custom-designed for the application. Carts, from small general-purpose push carts to model-specific kitting carts are Creform specialties. They are built using a system of 28 mm and 42 mm plastic-coated steel pipe and metal joints and can be configured for ESD (anti-static) applications. Creform workstations are built for single-person use to multi-person assembly cells. Workstations can be configured for a stand-up or a sit-down position and can be built and designed on wheels or stationary. The Creform System is used to create an array of material handling and efficiency-enhancing devices and is a proven component in continuous improvement and lean manufacturing programs. The company partners with customers in developing and enhancing these programs.
Michael Larsson announced as new president of Dematic and Member of Executive Board of KION Group AG
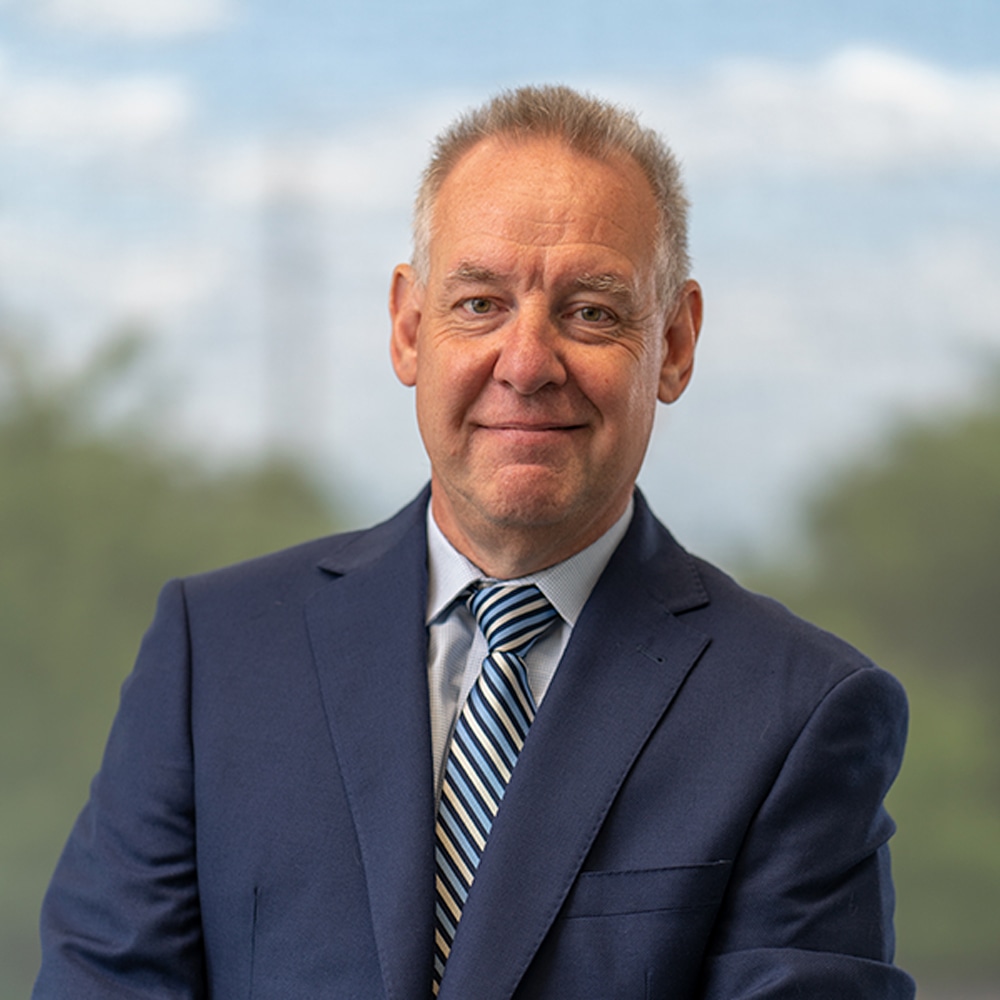
Dematic has announced that KION Group AG (KGX.DE) has appointed Michael Larsson as President of Dematic Corp. and Member of the Executive Board of KION Group AG. Larsson succeeds Hasan Dandashly, who has retired from the company. In his Board-assignment Larsson will also have responsibility for the KION Industrial Truck Segment (ITS) for the Americas while retaining responsibility for the Dematic Americas region. “With his responsibility for the Dematic SCS business globally and ITS in the Americas, Michael Larsson will further drive our strong commitment to profitable growth. He will expand our integrated solutions strategy on lighthouse projects with top customers,” said Rob Smith, CEO of KION GROUP AG. “It’s a very exciting time to lead Dematic, having the opportunity to work alongside an incredible team of industry experts to build upon our proud history and serving our customers. With the industry undergoing fundamental change, driving the need for increasing levels of automation, Dematic is in a great position to lead with innovative software and technology solutions. I would like to thank Hasan for his strong contributions to the company over the last five years building a strong foundation for future growth,” said Larsson. A 35-year veteran of Industrial Automation and Robotics, Larsson has a proven track-record as a strategic business leader with a focus on customers and people. Most recently, he served as Executive Vice President of Dematic’s Americas Region responsible for accelerating growth and driving a market-leading presence in the US, Canada, Mexico and South America. Over the past three years, as leader of the Americas Region, he successfully led the company through complex challenges during the Covid-19 Pandemic as well as historical eCommerce surges of 2021 and 2022. Prior to joining Dematic, Larsson served as Senior Vice President and Managing Director of ABB’s Automotive Business Unit. During his 30-plus-years at ABB, he also served in increasing levels of executive leadership, as CFO and Business Leader across four continents. He has a Bachelor of Business Administration from Stockholm University School of Economics in Sweden.
November 2023 Manufacturing Technology Orders fall despite economy’s soft landing
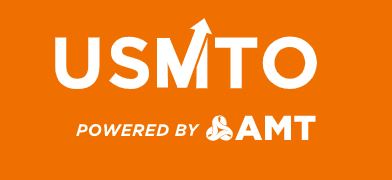
The soft landing the U.S. economy generally experienced through 2023 did not affect all sectors of the economy evenly. Even in the face of improving economic health, orders of manufacturing technology, measured by the U.S. Manufacturing Technology Orders Report published by AMT – The Association For Manufacturing Technology, consistently fell short of orders placed in 2022. November 2023 was no different, with orders falling to $399.8 million, 10.3% lower than those placed in November 2022 and 2% behind orders placed in October 2023. Year-to-date orders reached $4.45 billion in 2023, 13.3% below the same period in 2022. Contract machine shops, the largest consumer of manufacturing technology, decreased their November 2023 orders by nearly 16% from October 2023. The decline was nearly balanced by increases from other manufacturing sectors. Of those sectors that increased orders in November, aerospace manufacturers peaked at 60% above the monthly average compared to the rest of 2023. Electrical equipment manufacturers also increased orders. Tight conditions in the labor market persisting through the holiday travel and shopping seasons necessitated additional investment in automation to help manufacturers meet consumer demand. While overall orders for the year were down compared to their near-record levels in 2022, several regions and industries saw a late-year rally, showing strong order activity through November 2023. The Northeast and South-Central regions only declined by around 2% from their 2022 totals – virtually flat compared to the steeper declines seen in other regions. The minimal comparative losses in these regions were driven by significant year-over-year growth in orders from aerospace manufacturers. The South-Central region also benefited from significant growth in orders from the automotive sector. The release of December 2023 USMTO data will determine if the November bright spots were outliers or the beginning of a rebound that could drive manufacturing technology investment into 2024.
NAW vehemently opposes Acting Secretary Su’s renomination for Secretary of Labor
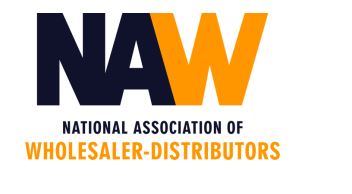
The National Association of Wholesaler-Distributors (NAW), representing the 8.2 trillion-dollar wholesale distribution industry and 6 million American workers, strongly opposes President Biden’s renomination of Julie Su for Secretary of Labor. Brian Wild, Chief Government Affairs Officer at NAW, issued the following statement: “Ms. Su’s time as Acting Secretary has been marked by a disregard for the diverse needs of both businesses and workers, evidenced in her flawed and harmful policies that threaten jobs, stifle growth, and undermine essential freedoms. The proposed overtime pay rule, with its unprecedented hike in the salary threshold, stands as a prime example. This rule, demonstrably harmful to the wholesale distribution industry – the very backbone of our nation’s supply chain – would limit employee development opportunities, diminish workplace autonomy, and restrict flexibility for millions of employees. This is not an isolated misstep. We see Acting Secretary Su’s influence on other alarming policies, like today’s new Labor Department rule redefining independent contractors, a biased regulation that threatens the flexibility and earning potential of millions of Americans. Furthermore, Ms. Su’s oversight of the Department of Labor has yielded flawed proposals like OSHA‘s proposed walkaround rule, a rule that not only fails to advance workplace safety but also violates property rights, imperils trade secrets, and endangers businesses to increased liability risks. This pattern of harmful decisions is simply unacceptable for a leader entrusted with managing an agency that has such a profound impact on our economy. NAW unequivocally calls upon President Biden to withdraw his renomination of Julie Su. We urge the President to appoint a leader who will work tirelessly to build a future where both businesses and workers can thrive.”
ELOKON promotes Mark Stanton to president & General Manager for North America
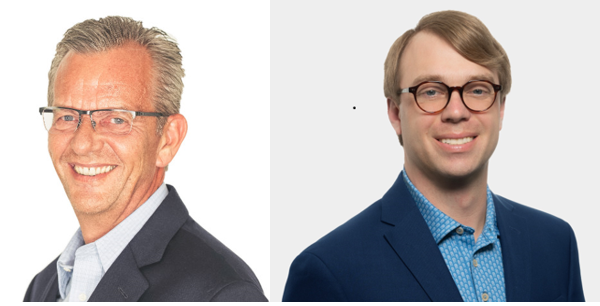
Material handling specialist to lead overall operations throughout the U.S., Canada, and Mexico for the automated forklift safety and fleet management system company, with Alex Johns taking over as vice president of sales ELOKON, Inc., an innovator in automated forklift safety and fleet management systems, has promoted senior vice president of sales Mark Stanton to the new position of president and general manager for the North American region, effective immediately. Alex B. Johns, ELOKON’s national sales director since 2021, will become the new vice president of sales for the region. Stanton joined ELOKON in May 2023, bringing more than 25 years of experience in the materials handling industry, a deep knowledge of forklift fleet management and forklift safety systems, and an impressive track record of driving growth and innovation. During the 8 months Stanton has been with the company, ELOKON has increased sales by approximately 30 percent and doubled the size of the ELOKON Inc. team. “We expected big things from Mark when we brought him on to lead our sales team in North America last May, and he most definitely delivered,” said Alexander Glasmacher, CEO, ELOKON. “His extensive knowledge of forklift fleet management and safety systems, combined with strong leadership skills and an unparalleled strategic vision, has already resulted in higher sales and stronger employee morale. Mark is the best person to run our growing business in the U.S., Canada, and Mexico.” Johns poised to grow sales, increase workplace safety and productivity in expanded sales role ELOKON’s cloud-based forklift fleet management solutions and forklift safety systems are used by some of the world’s largest companies to make their warehouses, distribution centers, and manufacturing plants safer and more efficient. North America is the largest addressable market for ELOKON’s solutions, growing steadily over the last three years with Johns playing a pivotal role in the positive growth trajectory. “Alex’s performance as our sales director in the U.S. has been simply stellar, with exceptional engagement with customers large and small,” said Stanton, who works from the company’s U.S. headquarters in Atlanta. “He’s a truly supportive team leader who inspires new sales members as well as current and new customers as we help them to become safer and more productive throughout their warehouses, distribution centers, and manufacturing plants.” Prior to joining ELOKON in May 2021, Johns served as the director of sales for Advanced Mechatronics Solutions in Atlanta, following sales leadership and marketing roles at companies such as Acuity Brands, RAIT88, and Adams Beverages of NC, LLC. He holds a bachelor’s degree from Auburn University’s Harbert College of Business.
Machinery Manufacturer Norwalt continues to invest for career path program for aspiring college students
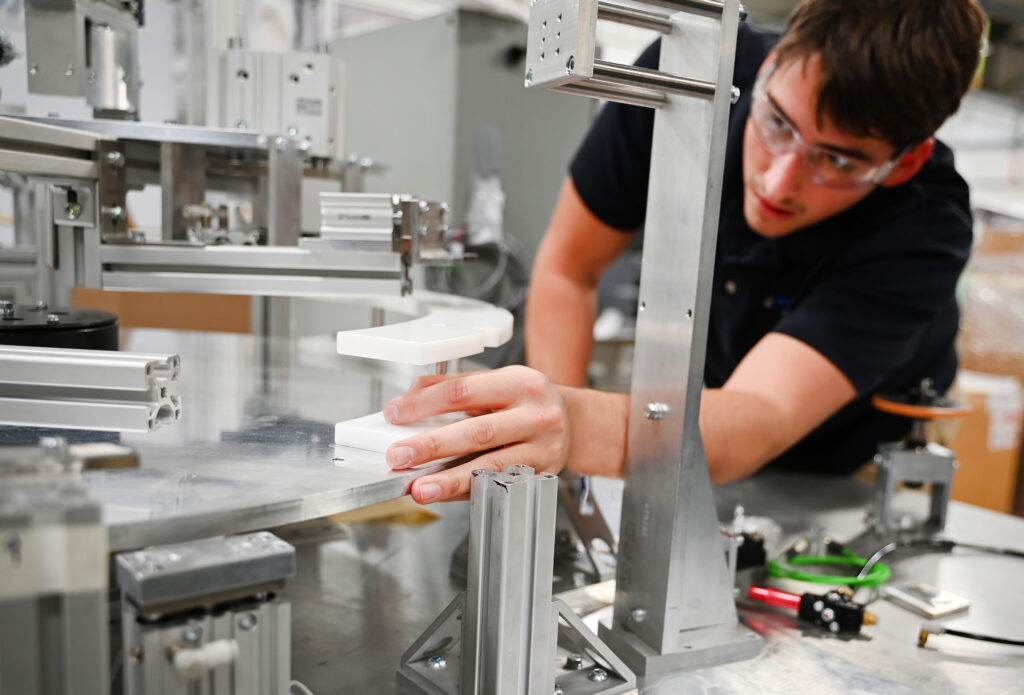
‘The Collegiate Automation Program’ helps prepare students for careers in machine design and manufacturing. Norwalt, a specialist in custom-built automation and line integration machinery for complex manufacturing applications, continues to expand on its immersive education program for college students interested in careers in machine design, manufacturing, and other automation-adjacent niches. The company’s Collegiate Automation Program (CAP) forges partnerships with the University of Delaware and other colleges to give aspiring students real-life experiences that bolster their learning in the classroom. For example, at the University of Delaware, Norwalt is assisting with facets of the school’s engineering curriculum, and providing funding for hands-on junior- and senior-level projects that complement classroom instruction. Norwalt also offers internship programs and conducts recruitment seminars offering opportunities to join its machine design team. Financial donations and close collaboration with the school’s education administrators round out Norwalt’s CAP program. In recent years, Norwalt has also reached out to the County College of Morris, and several other community colleges with machinery component donations, helping these educational facilities maintain equipment vital for comprehensive student instruction. With facilities in Randolph, New Jersey, and Tampa, Florida, Norwalt is a supplier of concept-to-completion manufacturing equipment solutions. The company’s engineers design, construct, validate, and install premium production equipment whose functionalities include – but are by no means limited to – packaging and product assembly, post-mold automation, modular automation cells, and robotics systems. Norwalt serves customers in a wide array of sectors, from medical devices and food & beverage applications to personal care and household items. “It is highly rewarding to have the opportunity to nurture and mentor the machine designers and engineers of tomorrow,” said Mike Seitel President at Norwalt. “Our partnership with the University of Delaware is already showing tremendous promise, as we strive to provide real-life machining experience that positively influences the overall education process. Supplementing classroom instruction with hands-on scenarios is vital in a field such as ours, and we’re grateful to do our part.”
Two division directors appointed at Port of Long Beach
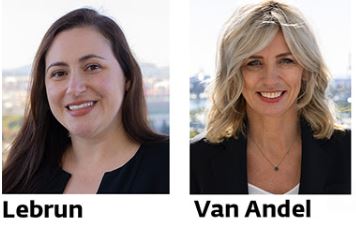
Promotions OK’d for Program Management, Central Procurement Services The Long Beach Board of Harbor Commissioners on Monday approved the appointment of directors for the Port of Long Beach’s Program Management Division and the newly created Central Procurement Services Division. Monique Lebrun, who has served as the Port’s assistant director of Program Management since December 2022, will become Director of Program Management. She joined the Port in September 2008 and has worked in several roles within the Design and Program Management divisions. The Program Management Division, part of the Port’s Engineering Services Bureau, oversees improvements to harbor, wharfs, terminals, railroads, bridges, roadways and utilities. Terra Van Andel, the Port’s Streamlines project manager since 2022 within the Finance Division, will become the Port’s first Director of the Central Procurement Services Division, which was formed to standardize purchases and contracts across the Long Beach Harbor Department’s 19 divisions. The Central Procurement Services Division will centralize how external contracts and purchases are initiated, processed and executed in an effort to heighten consistency, transparency and efficiency. Lebrun is a registered professional engineer and holds a Master of Science Degree in civil engineering from UC Berkeley and Bachelor of Science degrees in both civil engineering and architectural engineering from the University of Miami. Prior to joining the Port, she worked as an engineer in the private sector for five years. Van Andel joined the Port’s Finance Division as the contract compliance manager in 2020 and has spent the past year assisting with the Port’s transition to a centralized procurement system. She previously served two years as the business process improvement officer in the City of Long Beach Department of Financial Management after working 13 years in the City Auditor’s Office, where she rose to deputy city auditor. Van Andel earned Bachelor of Science degrees in both accounting and in management with an emphasis in leadership from Arkansas State University. The appointments are effective Jan. 13. The Port of Long Beach is a global leader in green port initiatives and top-notch customer service, moving cargo with reliability, speed and efficiency. As the premier U.S. gateway for trans-Pacific trade, the Port handles trade valued at $200 billion annually and supports 2.6 million jobs across the United States, including 575,000 in Southern California. In 2023, industry leaders named it “The Best West Coast Seaport in North America” for the fifth consecutive year. During the next 10 years, the Port is planning $2.2 billion in capital improvements aimed at enhancing capacity, competitiveness and sustainability.
The perfect medium-duty glove is better than ever
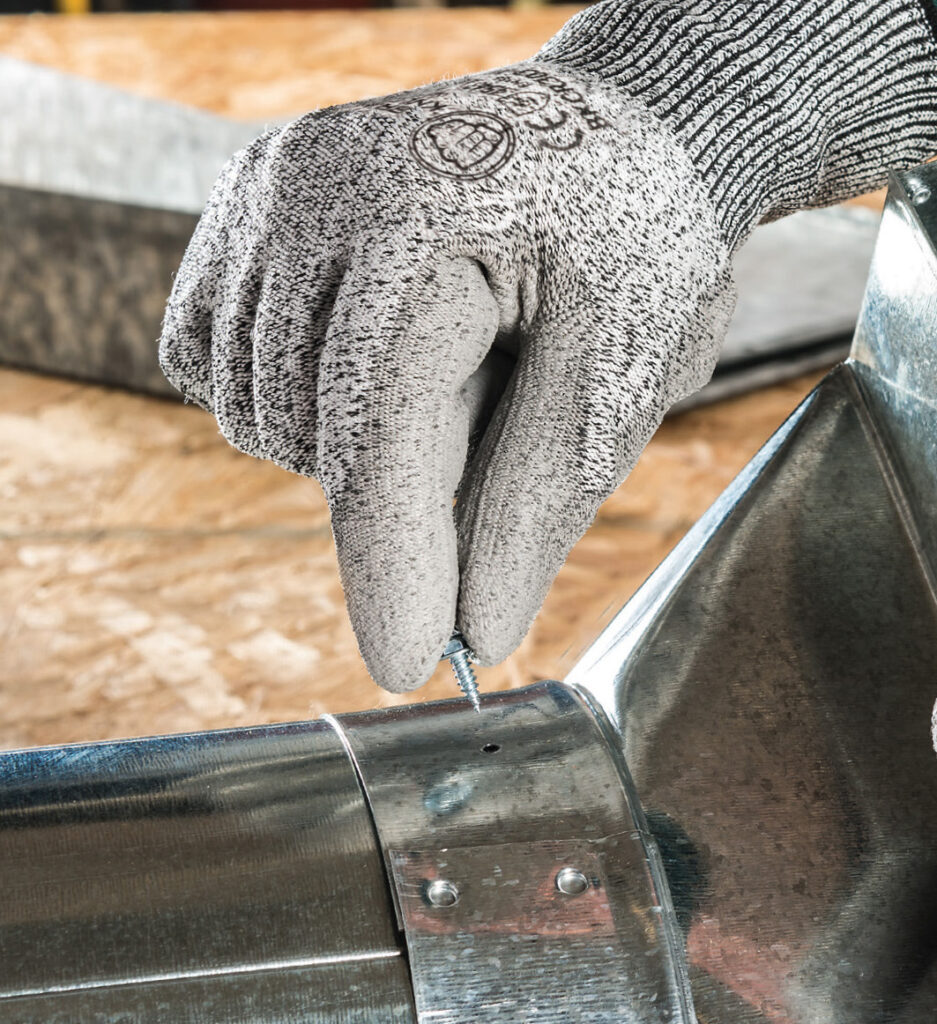
Brass Knuckle® SmartCut™ BKCR303 triples up with better fit, dexterity, and A2 cut protection The perfect medium-duty glove is now even better. Brass Knuckle® SmartCut™ (BKCR303) offers triple-threat benefits with A2 cut protection, amazing dexterity, and superior grip. Now improved with better tactile sensitivity, better fit, and the same great protection. OSHA estimates that over 70 percent of hand and arm injuries could be prevented with the proper protective equipment. That means considering form and fit as well as function. A glove that fits well promotes compliance. It’s one that workers will want to wear. BKCR303 starts with ultra-high-molecular-weight polyethylene fiber for ANSI cut resistance level A2 protection and thinner, 13-gauge material for dexterity. A non-sticky polyurethane (PU) coating on the palm and fingers creates a solid-gripping glove. Polyurethane also delivers enhanced puncture protection and abrasion resistance, all without adding bulk or reducing sensitivity. The glove is designed specifically to provide enhanced flexibility and deliver the right balance of protection, performance, and comfort for medium-duty jobs. SmartCut BKCR303 is the natural choice for material-handling applications requiring cut resistance and dexterity. The polyurethane palm and finger coat delivers excellent grip even against oils, fats, and greases. An uncoated back and wrist improves ventilation, while a seamless and stretchable full knit wrist provides a snug fit and prevents dirt, debris, and cold from getting inside the glove. Color-coded cuffs easily indicate glove size.
Motion names new SVP Strategy and Markets
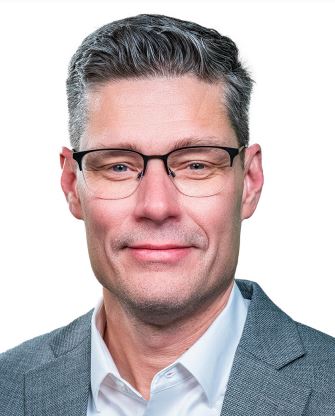
Motion Industries, Inc., a distributor of maintenance, repair and operation replacement parts, and a premier provider of industrial technology solutions, named Chris Cleland to Senior Vice President of Strategy & Markets, effective immediately. Mr. Cleland’s career spans over 25 years in consulting, strategy, marketing, branding, e-commerce, business development, and transformation. In his previous role as Principal Consultant at Cummings Creative Group (CCG), for the past 20 years, he led multiple successful initiatives across several industry verticals, driving growth and innovation for clients—including 12+ years consulting with Motion on marketing and strategy projects. Prior to his time with CCG, Mr. Cleland gained valuable experience as President/Owner of LithoSigns and as a Sales Manager with Citadel Broadcasting. In his new role, Mr. Cleland will lead the Company’s strategy development for its business groups, plus the e-commerce and digital teams. He will report to James Howe, Motion’s Executive Vice President – Chief Commercial Officer/Chief Technology Officer. “Chris brings a wealth of experience and expertise to our team,” said Mr. Howe. “His impressive track record in innovation and transformation makes him a perfect fit for guiding our companywide strategic planning process and shaping our future growth and success. We look forward to an exciting journey ahead.” Mr. Cleland graduated from The University of Alabama at Birmingham (UAB), earning a Bachelor of Science in Business.
Siemens expands its SIMATIC MICRO-DRIVE servo-drive system
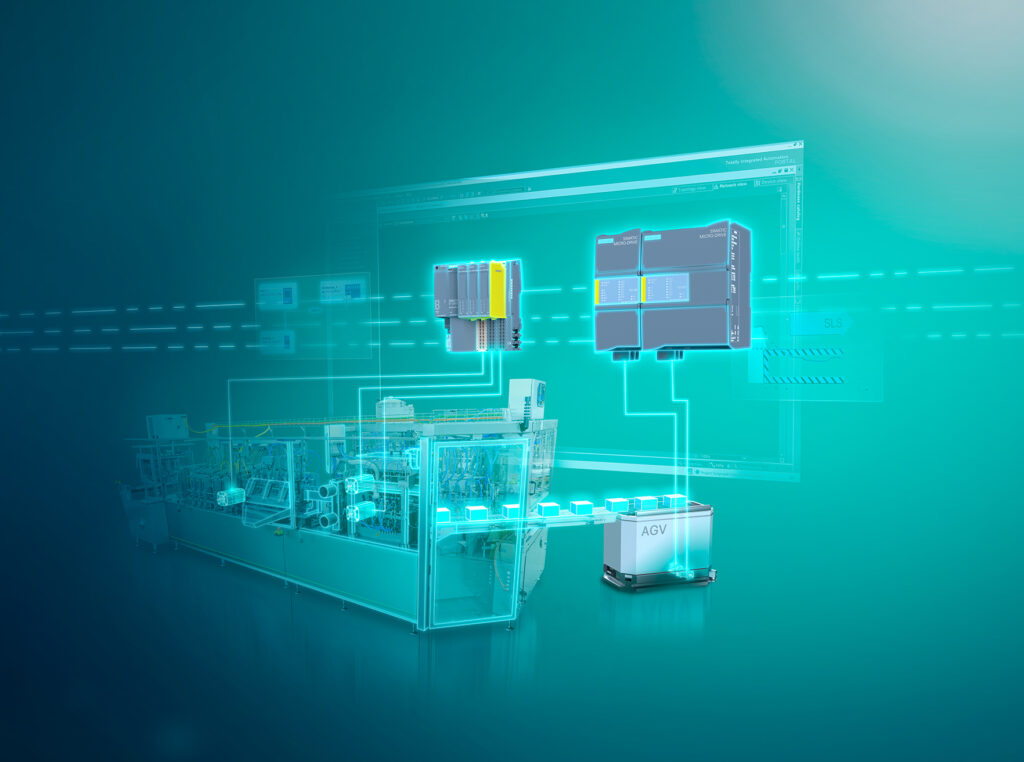
Siemens is extending its drive portfolio in the extra-low-voltage range for 24–48V EC motors with its new SIMATIC MICRO-DRIVE. The new product line with UL- and CE-marked components consists of the PDC (Profidrive Control) servo drive in conjunction with a flexible range of motors and connecting cables from product partners, along with the TM (technology module) format with servo and stepper drives in compact 20mm width that can be used in conjunction with distributed or open controllers. Simple connectivity to Siemens programmable logic controllers (PLCs) helps significantly reduce the engineering workload, while integration into Siemens automation technology via its TIA Portal makes for simple commissioning and servicing. Attributes such as smart encoders and one-button tuning add to its plug-and-play startup. Communication takes place over PROFINET using PROFIsafe and PROFIdrive profiles. The new Safety Integrated function SLT (Safely Limited Torque) limits torque by monitoring motor current in running operation. To address its customers’ requirements with maximum flexibility, Siemens utilizes product partnerships with companies such as Dunkermotoren, ebm-pabst, Harting and KnorrTec when it comes to the motors and cables used with MICRO-DRIVE. Other third-party motors can also be utilized with support for various encoder types. SIMATIC MICRO-DRIVE PDC focuses on higher performance applications with 100W and 600W units that permit side-by-side rail mounting. They are available in standard (hardwired Safe Torque Off (STO)) and fail-safe versions. STO, SS1, SLT, SLS, and SSM Safety Integrated functions are available with the MICRO-DRIVE PDC100F variant. SIMATIC MICRO-DRIVE TM units are designed for basic performance in industries with a focus on compactness and simple safety requirements. They are available in 280W-rating and come standard with hardwired Safe Torque Off (STO) safety functions. In addition to servo, TM units feature new modules to control stepper motors with or without incremental encoders. Machine builders and users will benefit from a compact design, easy wiring and installation to ensure top performance. Both SIMATIC MICRO-DRIVE PDC and TM systems are suited to a wide range of diverse applications such as automated guided vehicles (AGVs), conveyors, shuttles, storage and retrieval machines for warehousing systems, diverters, assembly machines, and industrial positioning applications. The Siemens Totally Integrated Automation (TIA) Portal is used to configure drives and motors quickly and easily including the activation of safety functions with a Fail-safe PLC via PROFIsafe. Machine operating data can be transmitted directly to the controller from MICRO-DRIVE and transferred to Cloud-based platforms such as MindSphere over MindConnect.
American Logistics Aid Network (ALAN) announces new Board Chair
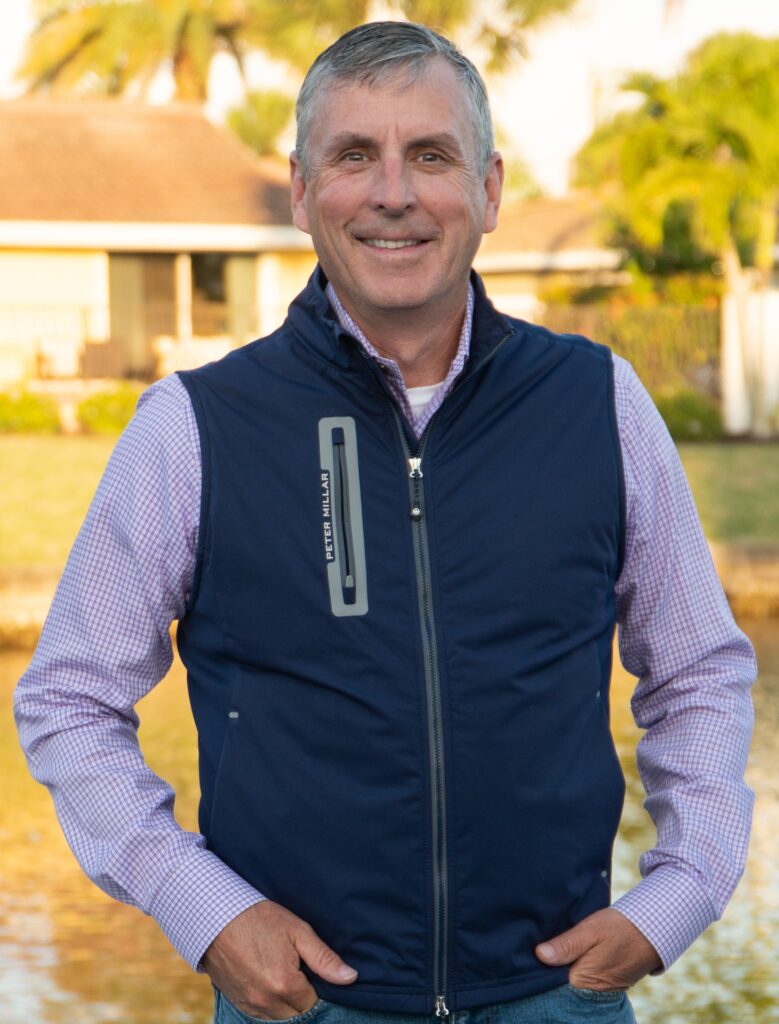
The American Logistics Aid Network (ALAN) has announced that it has named Robert O. Martichenko chairman of the board. Martichenko assumes his new role from current ALAN board chair and co-founder Mark E. Richards. “As ALAN enters a new year, I’m delighted to hand off the baton of leadership into Robert’s very capable hands,” said Richards. “His combination of heart, compassion, creativity and logistics experience makes him the ideal choice to guide ALAN as it continues to forge innovative paths in disaster response.” An ALAN board member since 2019, Martichenko is a longtime industry thought leader and active member of the business community. Passionate about the people side of enterprise excellence and the future of workforce development, he co-founded TrailPaths Inc. in 2022, a people development and technology company whose purpose is to create Meaningful Employment Environments™. Prior to that, he spent 15 years as founder and CEO of LeanCor Supply Chain Group. He is an award-winning author of five business books, multiple articles related to Lean, enterprise excellence, supply chain management and leadership, and one novel, Drift and Hum, which won multiple awards, including the IBPA Benjamin Franklin Gold Winner Award for Best First Book-Fiction. He’s the recipient of numerous prominent industry awards, most notably the Council of Supply Chain Management Professionals’ Distinguished Service Award. He is also a popular speaker and active participant/volunteer on multiple advisory boards, including the Association for Manufacturing Excellence (AME). “It is extremely humbling to step into Mark’s current role,” said Martichenko. “Both he and ALAN Executive Director Kathy Fulton are visionary leaders whose passion and work ethic have earned ALAN an upstanding reputation throughout the supply chain industry. I look forward to working side by side with them as ALAN continues to show how meaningful logistics is to the disaster relief community.” “Over the years, Mark has guided us so capably through everything from hurricanes and tornadoes to global pandemics, all with incredible calmness, intelligence and humanity,” said Fulton. “However we’re delighted to know that we have such a capable successor in Robert. We’re looking forward to the amazing talent and new energy and ideas he’ll bring to this role.”
Material Handling Wholesaler is hiring

Material Handling Wholesaler is now accepting applications for a rare sales position opening. Click here for details and to apply.
December 2023 Logistics Manager’s Index Report® LMI® at 50.6
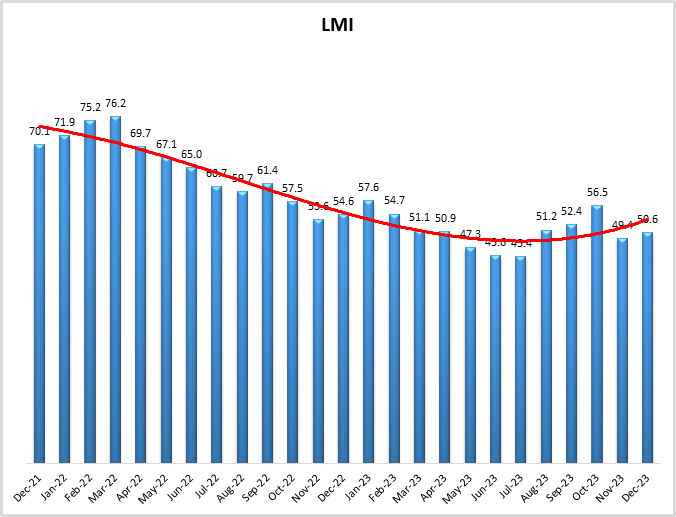
Growth is INCREASING AT AN INCREASING RATE for: Warehousing Utilization, Warehousing Prices, Transportation Capacity, and Transportation Utilization Growth is INCREASING AT AN DECREASING RATE for: Inventory Costs and Warehousing Capacity Inventory Levels and Transportation Prices ARE DECREASING The Logistics Managers’ Index moved back into expansion territory in December. This movement back to growth was led by increased activity among the three warehousing metrics. Warehousing Capacity is tighter (-5.5) while Utilization (+7.4) and Prices (+1.2) are both expanding at increasing rates. Inventory Levels continued to decline at a steady pace (although they were breaking even Downstream – likely indicative of JIT practices products selling briskly). This movement is likely the catalyst behind Transportation Utilization moving back into expansion (+4.6). Despite this, freight continues to struggle, with Transportation Prices decreasing at an increasing rate (-1.1). Finally, it is worth noting that Inventory Costs are growing at 55.8 (-6.3) but at the lowest level recorded in the history of the index. It will be interesting to continue monitoring this metric to see if it continues to moderate given the clear push towards JIT inventory management. Researchers at Arizona State University, Colorado State University, Florida Atlantic University, Rutgers University, and the University of Nevada, Reno, and in conjunction with the Council of Supply Chain Management Professionals (CSCMP) issued this report today. Results Overview The LMI score is a combination of eight unique components that make up the logistics industry, including: inventory levels and costs, warehousing capacity, utilization, and prices, and transportation capacity, utilization, and prices. The LMI is calculated using a diffusion index, in which any reading above 50.0 indicates that logistics is expanding; a reading below 50.0 is indicative of a shrinking logistics industry. The latest results of the LMI summarize the responses of supply chain professionals collected in December 2023. The LMI read in at 50.6 this month, up (+1.2) from November and back into mild expansion. As is always the case in December, movements in the logistics industry were driven by holiday shopping. The strength shoppers showed over cyber week continued throughout the holiday shopping season, with U.S. retail sales up 3.1% from November 1st to Christmas Eve. Online retail – which requires more trucks and warehouses located close to consumers – was a major part of this activity, with growth of 6.3%. Interestingly, sales per day was down slightly in December from November ($13.8B from $14.9B). This is reflective of both consumers increasingly spending earlier in the holiday season to avoid stock-outs, and the longer than usual 31-day gap between Black Friday and Christmas caused by an early Thanksgiving[1]. This spending was spurred in part by inflation continuing to drop. The personal-consumption expenditures (PCE) index was down 0.1% in November, which is the first drop in the PCE since the height of covid lockdowns in April of 2020. Wallstreet has taken this as a sign that interest rates will almost assuredly come down over the next year as all major indexes have now been up for eight consecutive weeks[2]. A significant portion of deflation can be traced to shifts in the logistics market. Aggregate Logistics costs (measured on a scale of 0-300, with 150 as the “break-even level) read in at 164.4, which is down (-6.2) from November’s reading of 170.6 and well below the readings during the heavy inflation period of 2022 which were often over 250.0. This is consistent with the San Francisco Fed’s measure of contributors to inflation, which showed supply costs as deflationary for both core and headline PCE inflation in November[3] – a direct reflection of decreased inventory costs inherent to the move back to JIT practices. The impact of JIT on this deflation is evidenced by Inventory Costs, which read in at 55.8 (-6.3) – their lowest level in the history of the index. The costs are particularly low Upstream, where they read in at 50.8 which is very close to no movement at all. This metric has never contracted in the history of the LMI. It will be interesting to see if that changes in the new year or if this is the low point and manufacturers and wholesalers will begin building inventories up again. An Upstream rebuild is expected among respondents, who predicted Upstream Inventory Levels will increase at a rate of 56.2 over the next 12 months. This stands in contrast to high-turnover program with our Downstream respondents. Downstream Inventory Levels are 50.0 in December and are expected to be 50.0 over the next 12 months – the clearest sign yet that retailers are looking to get back to JIT and get off the inventory roller coaster they have been riding over the last few years. For this to happen there will need to be some restocking as current Inventory Levels read in at 44.3, which is a level of contraction that is identical to what we saw in November. Some of the strategy behind the designs on JIT can be seen in the shift in how U.S. firms are importing goods. Sailings from China to the West Coast of the U.S. remains subdued[4]. While this is consistent with seasonal trends, it is still notable, and perhaps reflective of the continued shift in manufacturing from China to sources closer to the U.S. Conversely, over $105 billion of goods have been diverted away from the Red Sea due to attacks by Houthi Pirates. Between the instability in the Red Sea and the low water levels at the Panama Canal, moving goods from Asia to Europe or the East Coast of the U.S. – or vice-versa – has become difficult. This is reflected in container prices from Shanghai to the U.K. jumping to $10,000 for a 40-foot container – up from $2,400 in mid-December[5]. Conversely, more of the manufacturing base continues to nearshore to Mexico to take advantage of low-cost labor, technical expertise, proximity to the U.S., and the free border crossings allowed by the USMCA. Reflective of the increased freight volume coming in from Mexico, U.S. Customs and Border Protection is
AIT Worldwide Logistics welcomes Richard Lee as vice president of global project management office, contract logistics
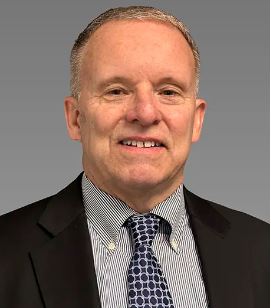
AIT Worldwide Logistics has welcomed freight forwarding industry veteran Richard Lee, who has joined the organization as vice president of global project management office (PMO) and contract logistics. In this new role, Lee will apply his decades of industry experience by focusing on strategic, efficient resource management services, while also streamlining the process to integrate recently acquired companies. He reports to Chief Business Officer, Greg Weigel. “As AIT continues to expand our footprint across the globe, both organically and via acquisition, Rick’s extensive background and his visionary approach to consultative contract logistics relationships make him a valuable addition to our leadership team,” Weigel said. “We are confident his guidance will help the company continue to deliver increasingly beneficial solutions to our customers.” Across leadership positions with CEVA Logistics, SEKO Logistics and Avaya, Lee has a proven track record of collaboration, strategic planning, seamless acquisitions, and development of customized, integrated solutions for a diverse array of sectors and regions. Lee said he believes his deep supply chain experience – including an extensive quality management background, more than two decades of global contract logistics experience, and support for more than a dozen acquisition integrations in a span of just three years – will bring value to AIT’s vast global network. “I’m excited to work alongside the industry leaders here at AIT and look forward to collaborating across operations and borders,” Lee said. “With AIT still expanding into new markets around the world, this role is a great opportunity to help extend and build upon the company’s mission to earn customers’ trust by delivering quality driven, exceptional solutions.” Lee studied business at the University of New Haven in West Haven, Connecticut. Based out of AIT’s global headquarters in Itasca, Illinois, he enjoys woodworking, cooking and playing golf in his spare time.