American unity on display on Wreaths Across America Day
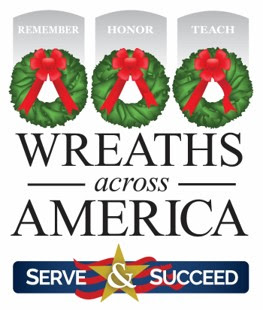
National Wreaths Across America Day sees the placement of three million sponsored Veterans’ wreaths at over 4,225 participating locations across the country National Wreaths Across America Day took place at over 4,225 participating locations across the country, including Arlington National Cemetery. Volunteers remembered our nation’s heroes as they said their names aloud, honoring over three million veterans this year. Wreaths Across America would like to thank the communities, dedicated volunteers, and generous sponsors for coming together in unity and supporting those who have protected our freedom. Each person has played a part in the year-long mission to Remember the fallen, Honor those who serve, and Teach the next generation the value of freedom. “What I love most about this day, and this mission, is that it is so much more than just the placement of a wreath. The wreath is the catalyst, it brings together communities – families and strangers — to learn about those who have served and sacrificed,” said Karen Worcester, executive director Wreaths Across America. “We have more than three million volunteers across the country and a third of them are children. This mission and the events happening today provide the opportunity to teach kids about what freedom is.” For centuries, fresh evergreens have been used to symbolize honor and a living tribute renewed annually. Wreaths Across America believes the tradition represents a living memorial that honors veterans, active-duty military, and their families. When volunteers say the name of a veteran aloud while placing a wreath, it ensures they live on in our hearts and memories and are always remembered. For more information about the year-long mission and ways to get involved in your own community, please visit www.wreathacrossamerica.org. National Wreaths Across America Day 2024 was held on Saturday, December 14.
Global survey highlights rise of technology-infused supply chains to address disruption, uncertainty, and cost pressures
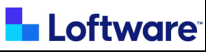
52% of companies host enterprise applications in the Cloud; 76% anticipate AI integration in supply chains by 2026 More than half (52%) of companies currently host critical enterprise applications in the Cloud while 76% believe artificial intelligence (AI) will be an important part of their supply chain within the next three years, according to an annual report published by Loftware, the largest global software company specializing in Enterprise Labeling and Artwork Management solutions. The global survey, which draws on insights from over 300 labeling, packaging, and supply chain professionals across industries in 55 countries, found that investing in cutting-edge technologies such as cloud computing, AI, and IoT solutions is no longer a tactical necessity but an enabler for business growth and agile supply chain operations. This shift in prioritization has primarily been driven by ongoing supply chain disruption, heightened consumer expectations, and growing sustainability demands. “As companies plan for 2024 and beyond, the combination of geopolitical uncertainties, climate instability, and the threat of recession continues to impact companies of all sizes. Organizations are grappling with disruptions that extend far beyond the traditional scopes, requiring a strategic recalibration to weather the storm and emerge stronger in the face of adversity,” said Josh Roffman, EVP of Marketing at Loftware. “With this in mind, a commitment to bolstering digital transformation strategies through investment in innovative technologies will be critical to streamline operations, drive growth, and increase profitability.” Gartner, a technology analyst firm, supports this notion and reports that global end-user spending on public cloud services is forecast to grow 20.4% to total $678.8 billion in 2024, up from $563.6 billion in 2023. The Loftware report also revealed that sustainability has become a crucial strategic and operational priority for organizations of all sizes around the globe. Of those surveyed by Loftware, 78% said they have already adopted sustainability initiatives across their organizations due to increased regulations and shifting consumer preferences. In fact, 77% of respondents believe stricter regulations and compliance requirements are pushing businesses to adopt sustainability practices, while 82% reported that consumer preferences for sustainable products are driving this approach. Facilitating transparency is a vital step in creating resilient supply chains and fostering better sustainability practices, so it’s no surprise that 79% of respondents flagged global traceability as a priority for their company – an increase from 70% just 12 months ago. Using cloud technology, digital traceability helps companies to ensure sustainable sourcing, protect consumers, streamline the location of inventory, guarantee on-time delivery to market, and address the growing issue of counterfeiting. Indeed, 48% of those surveyed believe the inability to effectively manage recalls is the biggest risk of not being able to track products through the supply chain. This compares to 33% five years ago. As highlighted by Loftware’s report, Industry 4.0 will continue to have an impact on companies and their manufacturing operations. Organizations operating across a range of industries, from automotive, electronics, and manufacturing to consumer products and life sciences, are embracing automation and standardized solutions which help them meet their own unique requirements. This is especially true for mission-critical business processes such as cloud labeling and printing, with 91% of respondents reporting seeing an advantage of using a single platform to support thermal transfer labeling and direct marking and coding. By adopting such a solution as part of a cloud-first strategy, businesses gain printing flexibility, accuracy, production line uptime, and efficiency to manage costs and support global growth. For more information about the trends identified by Loftware, access the full report and sign up for the ‘2024 Top 5 Trends in Labeling & Packaging Artwork’ webinar.
Seeq wins Silver in 13th Annual Best in Biz Awards
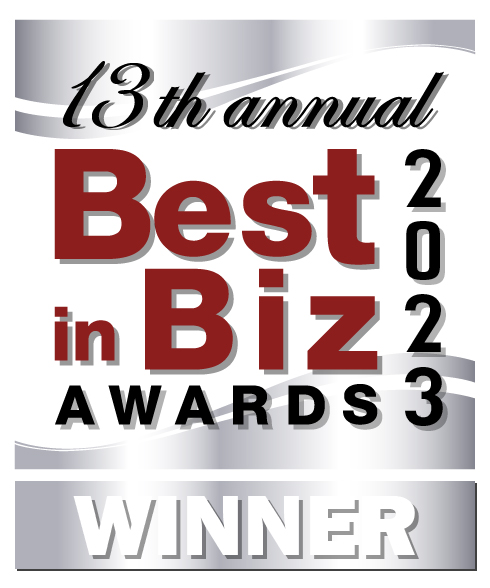
Accolade recognizes Seeq in the “Enterprise Product of the Year” category for its innovative advanced analytics and AI platform for addressing operational challenges impacting the manufacturing industry Seeq, a provider in advanced analytics and industrial AI, has been named a silver winner in the Enterprise Product of the Year – All Other Software category in Best in Biz Awards, the only independent business awards program judged each year by prominent editors and reporters from top-tier publications in North America. Seeq is being recognized for its self-service, advanced analytics and industrial AI platform that accesses and leverages vast amounts of historically underused data. By incorporating leading-edge technologies, including AI, machine learning and other capabilities, into its platform and leveraging its global partner network, Seeq powers a range of use cases for employees across the enterprise to accelerate digital transformation outcomes such as operational excellence and profitability, workforce upskilling, and sustainability. The 13th annual program saw intense competition among more than 600 entries from public and private companies, representing all industries and regions in the U.S. and Canada and ranging from some of the most iconic global brands to the most innovative start-ups and beloved local companies. This year’s judges highlighted the winning companies’ breadth and depth of innovation, their novel approaches to employing new technologies, impressive workplace benefits and employee diversity and inclusion programs, as well as continued community involvement and critical investments in environment and corporate social responsibility programs. “As a leading provider of self-service, enterprise SaaS solutions, we’re pleased to receive the Best in Biz Award for the Enterprise Product of the Year – All Other Software category,” said Dr. Lisa Graham, CEO at Seeq. “Industrial companies are turning to digital solutions to scale, empower, and maximize access to data to drive sustainability, operational excellence and profitability. Our advanced analytics and industrial AI platform empowers these organizations to accelerate their digital transformation initiatives by making operational time series data insights available to all stakeholders for improved business outcomes.” Since the program’s inception in 2011, winners in Best in Biz Awards have been determined by independent judging panels assembled each year from some of the most respected national and local newspapers, TV and radio outlets, and business, consumer, technology and trade publications in North America. Thanks to the unparalleled expertise and experience of the editors and reporters serving as judges and the impressive diversity of outlets they represent, Best in Biz Awards judging panels are uniquely suited to objectively determine the best of the best from among the hundreds of competitive entries. The 2023 judging panel included, among others, writers and contributors to Ad Age, Computerworld, Fast Company, Forbes, Inc., Portland Tribune, Washington Post. “As in years past, determining winners in some categories was a matter of selecting the very best from among the very good and came down to the smallest details,” said Best in Biz Awards staff. “Each year, the judges are impressed by the innovations, growth, and change emanating from the winning companies and permeating across layers of society, from their employees through clients to local and global communities.” Best in Biz Awards 2022 honors were conferred in 100 different categories, including Company of the Year, Fastest-Growing Company, Most Innovative Company, Best Place to Work, Customer Service Department, Executive of the Year, Marketing Executive, Most Innovative Service, Enterprise Product, Best New Product, App, CSR Program, Environmental Program, Website and Film/Video of the Year. For a full list of gold, silver and bronze winners in Best in Biz Awards 2023, visit: https://www.bestinbizawards.com/2023-winners.
Bobcat innovates for jobsite of the future with smart, sustainable and connected machines at CES 2024
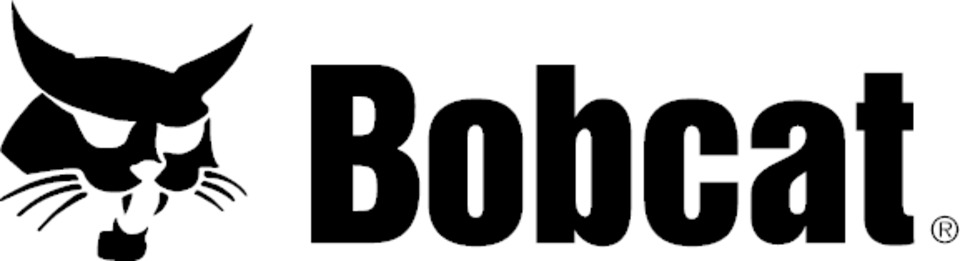
Doosan Bobcat, Inc., a company within Doosan Group, will showcase its latest product and technology concepts Jan. 9-12, 2024, at CES®, the world’s most influential technology event. Located in the Doosan booth (5941, West Hall, Las Vegas Convention Center), Bobcat will highlight several machines and unveil a new concept machine during CES’ Media Days at the Doosan press conference at 3 p.m., Jan. 8, at Mandalay Bay’s Tradewinds ballroom. “As a pioneer in the compact equipment industry, we are continually innovating to create solutions for our customers’ toughest challenges,” said Joel Honeyman, Doosan Bobcat vice president of global innovation. “By combining emerging technologies with our proven products, we are developing cutting-edge solutions to meet the demands of a changing world as we transform how we work, build and live.” The Bobcat display within the Doosan booth offers show attendees the opportunity to see the machines up close and interact with technology demos. Highlights include: New Smart Machine Transforms Farming Bobcat is launching new technologies for a better, more sustainable world. This includes a concept machine that is designed to make farming more sustainable, efficient and smart through AI, autonomy and electric operation. This machine and technology will change the way work is done and will be announced at CES Media Days and on display the week of CES in the Doosan booth. CES 2024 Innovation Award Honoree: The All-Electric Bobcat S7X Skid-Steer Loader Following the introduction of the all-electric Bobcat T7X compact track loader unveiled during CES 2022, Bobcat continues to evolve its all-electric product offering with the Bobcat S7X skid-steer loader. Powered with a lithium-ion battery, the S7X steer-skid loader is all-electric, as Bobcat eliminated all hydraulics, and instead uses electric drive motors and ball screw actuators for lift and tilt functions. By eliminating the hydraulics, the S7X has 50% fewer components, simpler componentry and 96% less fluid, coolants and lubricants compared to traditional diesel-hydraulic loaders. Bobcat was recognized as a CES Innovation Awards Honoree* as the S7X was honored in the categories of “Sustainability, Eco-Design & Smart Energy” and “Smart Cities.” The awards recognize outstanding product design and engineering in consumer technology products. Advanced Display Technology Enhances Operator Productivity Bobcat is displaying the future of advanced display technology with its transparent, touch display concept, which enables operators to seamlessly view both the jobsite and operation information. Built into the cab door of the S7X, the display serves dual purposes by transforming the machine’s main window to enhance operator productivity and efficiency to the task at hand. The display concept was developed in conjunction with LG Electronics and BSI Research. Bobcat RogueX2 Concept Loader Tests the Limits of Machine Functionality Bobcat is showcasing its latest concept loader, the RogueX2. This all-electric and autonomous concept machine produces zero emissions, as it features a lithium-ion battery, electric drive system and electric actuated lift and tilt kinematics with no hydraulics. RogueX2 is the second iteration of this Bobcat invention. The RogueX and subsequent RogueX2 were built as a proving ground to advance the Bobcat innovation roadmap, evaluate customer perceptions and challenge the paradigms of traditional kinematics and machine functionality. Built without a cab, this one-of-a-kind conceptual machine explores the idea of operating where humans cannot go to tackle more work in more places than ever from an autonomous or remote position. Show attendees can see the latest iteration of this loader with enhanced features designed to further advance the future of work. Bobcat ZT6200 Autonomous Zero-Turn Mower Addresses Labor Challenges Bobcat has advanced its innovations in the landscaping and grounds maintenance industries with its autonomous zero-turn mower, the Bobcat ZT6200. This machine offers game-changing efficiency and productivity by completing repetitive mowing tasks without the need for an onboard operator. Designed to operate with software developed by Greenzie, the Bobcat autonomous mower allows operators to plot a perimeter and mark areas for the mower to avoid during autonomous operations. The machine utilizes specialized mapping to execute the most efficient route that can be repeated, all of which can be managed or customized on a simple smartphone app. Bobcat Digital Technologies Revolutionize the Jobsite Show attendees can learn how to get the most from Bobcat equipment with its digital products such as Bobcat MaxControl and Bobcat Machine IQ. Learn more about how Bobcat is transforming the industry through its innovation leadership. Bobcat will exhibit alongside other Doosan Group business units at CES including Doosan Enerbility, Doosan Robotics and HyAxiom, Inc. *The CES Innovation Awards are based upon descriptive materials submitted to the judges. CTA did not verify the accuracy of any submission or of any claims made and did not test the item to which the award was given.
Brass Knuckle® Vader Goggle keeps vision clear
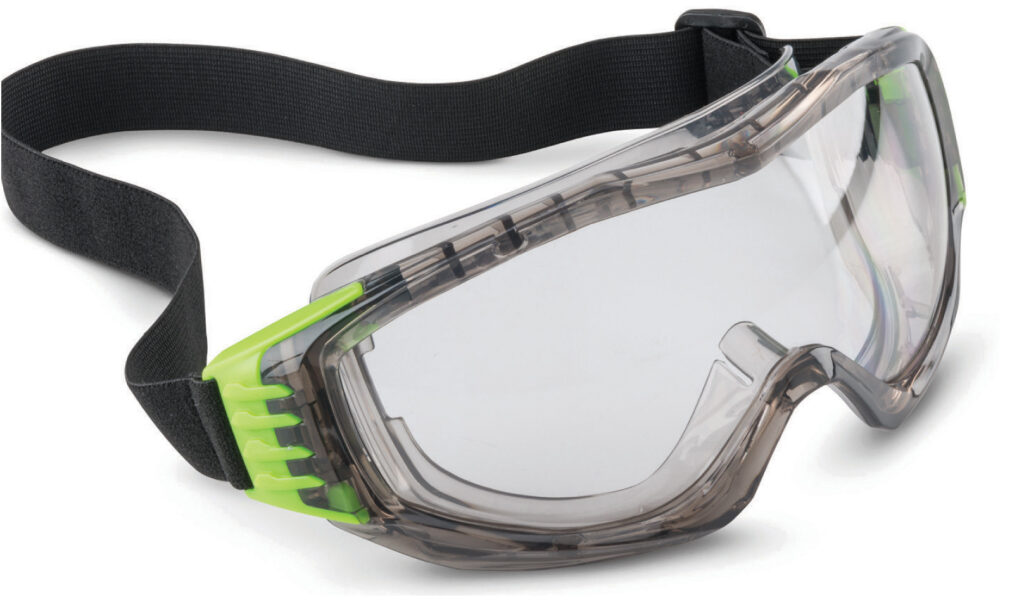
Sometimes, a seemingly otherworldly development comes along that rewrites performance standards and shatters expectations. The Brass Knuckle® Vader Goggle (BKGOG-2010N) doesn’t come from the far reaches of space (the U.S., actually), but it might as well be an alien concept when compared to more traditional eye protection. The Vader Goggle looks like it should be tearing up the slopes … yet it’s made to keep out splash and maintain vision in the toughest work environments. Made with exclusive BK-Anti-FOG coating, a durable anti-scratch treatment, and D3-rated for droplet and splash protection, Vader is as efficient and hardworking as the people who wear it. Brass Knuckle’s BK-Anti-FOG exceeds the EN 166/168 standard for a long-lasting, fog-free view in even the most demanding conditions. Washable and durable, BK-Anti-FOG protection lasts much longer than competitors’ anti-fog treatments, dispersing water molecules across the surface of the lens to restrict moisture buildup. With its wide 180-degree peripheral vision and face coverage, the Vadar is also roomy enough to wear over most prescription eyeglasses. The only material that touches the face is an ultra-soft conditioned rubber that forms the splash shield. Further maintaining clear vision is the Vader’s reverse-engineered venting system, promoting directional airflow across the inside surface of the lens and further reducing the potential for moisture buildup. The durable polycarbonate lens provides 99.9% UVA/UVB/UVC protection to help prevent eye damage. Vader meets demanding industry test requirements (ANSI Z87.1+, EN166K, EN166N, EN166UV) and meets or exceeds AS/NZS 1337.1:2010 for eye and face protection.
Caster Concepts expands manufacturing facility in Michigan
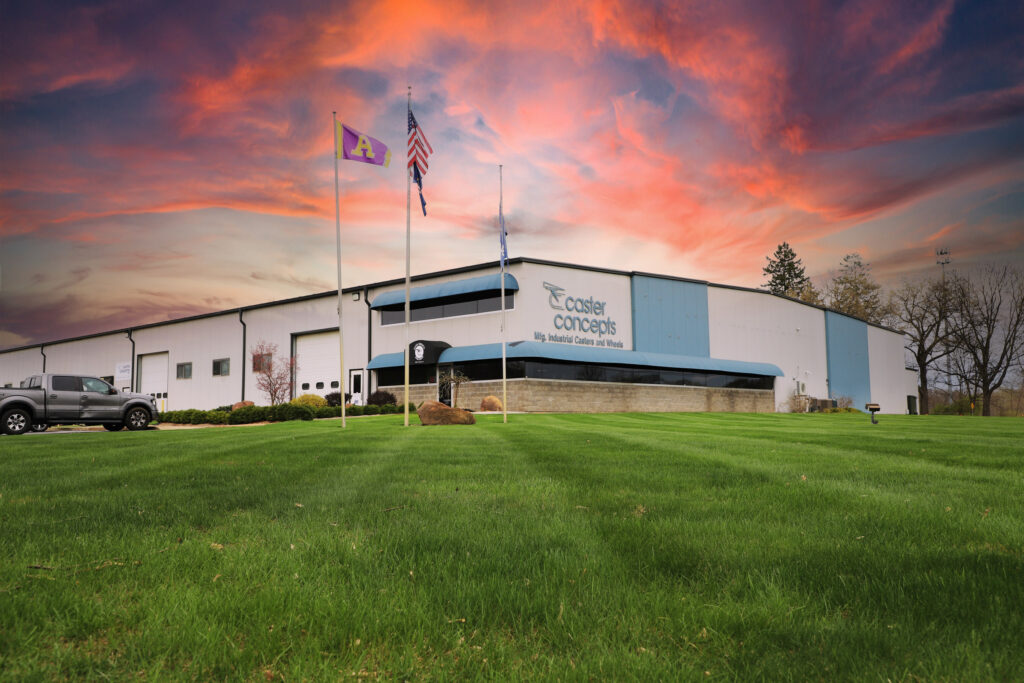
Caster Concepts, a manufacturer of heavy-duty casters and industrial caster wheels, has announced the completion of a 16,000 square foot expansion at their West Michigan Ave facility in Albion, Mich. This marks the company’s fourth expansion since 1995, reinforcing its commitment to long-term growth. “With continued onshoring and production growth in aviation, heavy equipment and automotive, we are seeing growth in customers seeking solutions that enable them to effectively move large components and finished goods through their manufacturing facilities and warehouses,” said Bill Dobbins, President, Caster Concepts. “Our expanded capabilities position us well to help our customers meet these challenges safely.” The facility in Albion focuses on production of the company’s core products and includes customized polyurethane fabrication capabilities, as well as other equipment and resources needed to match the right product to specific applications. Used properly, advanced caster technology – developed for the specific material handling challenge – provides up to 3X longer life and reduces push force by more than 70%, addressing major ergonomic and operational challenges.
It’s tax time! Are you prepared for what’s ahead?
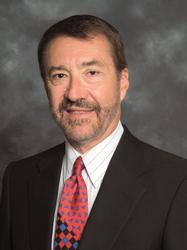
Is there never a “TAX TIME” in the U.S.? Don’t think so. And I believe “TAX TIME” is going to increase dramatically. The PROBLEM being that the U.S. continues to spend more than it takes in, which we all know does not work in any way, shape, or form. And how do we fix this? By taking more money from you and your company. THERE IS NOT A CHANCE IN HELL THAT THIS WILL NOT HAPPEN, because in four years U.S. debt will be about $40 Trillion, carrying $1.2 Trillion of interest cost (at 3%) and $1.6 Trillion (at 4%). At the same time the annual debt to GDP ratio we are talking about exceeds 100%. The estimates for 2023 are $4,439 Trillion of tax revenues against outlays of $6,134 Trillion of spending, with the debt balance growing yearly without a game plan to reverse the situation. It will take both higher revenues and spending cuts to reduce the deficit, considering that a large portion of spending is fixed (Social Security, Medicare, Health benefits and interest expense), which all together add up to approximately $4.0 Trillion of outlays. Not a pretty picture. No matter how you look at our situation revenues need to increase, and outlays reduced to lower the total debt. I have suggested on many occasions that management spend time with their tax folks to fully understand what their tax position was for the past year, how it looks for the current year, planning for the current year with enough time to execute “tax” programs and to see what is on the horizon for the following year. I hope you have been doing this. If you followed this suggestion, you should have a pretty good feel for your tax position and the impact on that tax position should Congress take steps to increase all the forms of taxes you pay related to payroll, company taxable income and personal income. We find ourselves currently working with the 2017 TAX CUT and JOBS ACT that will expire in 2025. So, to start with let’s assume this ACT will be repealed. As a reminder of what the TAX CUT act provided here is a brief list of the benefits. Lower tax rates— higher standard deduction—Estate and Gift Tax exemptions —-bonus depreciation—a reduced deduction for mortgage interest and state taxes. Suggestions for raising revenue are as follows: Repeal the 2017 Tax Cut Act Raise the top income rate to 45%. Apply the 12.4% Social Security Tax on incomes over $250,000 Payroll taxes to cover all pass-through income Raise total payroll taxes by 1% Reduce estate tax exemption from $12.9 to $3.9 million Raise Corporate Tax rate from 21% to 28 % Capital gains and dividends taxed at ordinary rates Tax unrealized capital gains at death with a $4 million exemption Wealth Tax of 2% for net worth over $50 million and 3% for over $1 billion Further limiting or eliminating deductions A 5% value added tax Limit Charitable Donation deductions 4% on share buybacks Entitlement Program Reform- later access and higher cost 15 cent gas tax The income tax changes will only apply to those making over some set amount, with lower income tax brackets excluded. Cost reductions are not part of this list. Some of you may be wondering why Bartecki is talking about tax exposure 15-20 months out. I did this because the changes are significant and because it may take you a year+ to get your potential tax situation under control. Maybe the ESOP plan sounds better now? Should you gift your wealth to family members via a trust now instead of waiting for probate to do so? Should you accelerate your technology plan to reduce labor costs? Could a life insurance policy help with lowering tax costs? So many options to consider, so easy to make a mistake. But no matter what, there will be a substantial increase in tax costs for both the company and shareholders. Another situation to consider is the expected company cash flow under current conditions. Could you handle a substantial increase in tax spending? Do you know what your free cash flow position will be for 2024 and 2025. With changes in pricing and interest rates, it may wind up lower than what you are generating now. What would I do? If I am in the “sell” range I would look at selling in 2024 or 2025, understanding that at current interest rates the price may be lower than you like. If I am not in the “sell” range and the company is highly profitable, then the ESOP should be reviewed. If I have a substantial estate, I will investigate how to avoid any increase in the Estate Tax or the Wealth Tax. (With ESOP you do not own the company). I would investigate employment benefit plans to find out options for the Roth or IRA. I would find a tax attorney who knows how to use trusts to accomplish reduction of estate value and potential income taxes. I would investigate how to channel transactions through various entities or states to reduce tax. The bottom line here is all will pay more. How much more is up to you. There is not doubt that rates will increase, deductions eliminated, a VAT Tax added and Wealth Taxes in the form of taxable dividends and capital gains and well as a net-worth tax. I would also assume that deductions for IRA’s and 401K’s will be limited. Every time Congress makes these changes companies and individuals get caught with its guard down and pays a heavy price going forward. But you now have a jump start on the situation, especially where the high-priced changes are involved. What works here is you can plan, but you don’t have to execute until you are ready. Happy New Year! About the Columnist: Garry Bartecki is a CPA MBA with GB Financial Services LLC
H&E Equipment Services signs Definitive Agreement to acquire Phoenix-Based Precision Rentals
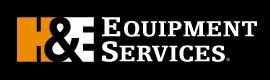
Based in Phoenix, Ariz., Precision operates a branch in Phoenix and a second location in Aurora, CO H&E Equipment Services just announced the signing of a definitive agreement to acquire the business of Precision Rentals. Based in Phoenix, Ariz., Precision operates a branch in Phoenix and a second location in Aurora, Colo. Precision offers a mix of general rental assets with a total fleet size, as measured by original equipment cost, of approximately $70 million and an attractive average fleet age of 37 months. The transaction is expected to close during the first quarter of 2024, following regulatory clearance and other customary closing conditions. Brad Barber, CEO of H&E Equipment Services Inc., identified compelling strategic benefits associated with the acquisition. “Since 2006, Precision Rentals has successfully grown its equipment rental business through a focus on reliability, fleet diversity and exceptional customer service,” said Barber. “The company’s branch operations are in cities with strong construction activity and excellent future opportunities, including several mega projects. The acquisition is expected to expand the H&E customer base as branch density is increased across the Phoenix and Denver metropolitan areas.” H&E continues to grow its branch network in 2023 through organic expansion and acquisitions, with 17 branches added through November, and an additional two branches upon this transaction.
Green Cubes closes out 2023 with 10,000 Lithium SAFEFlex battery units Sold, totaling 297MWh
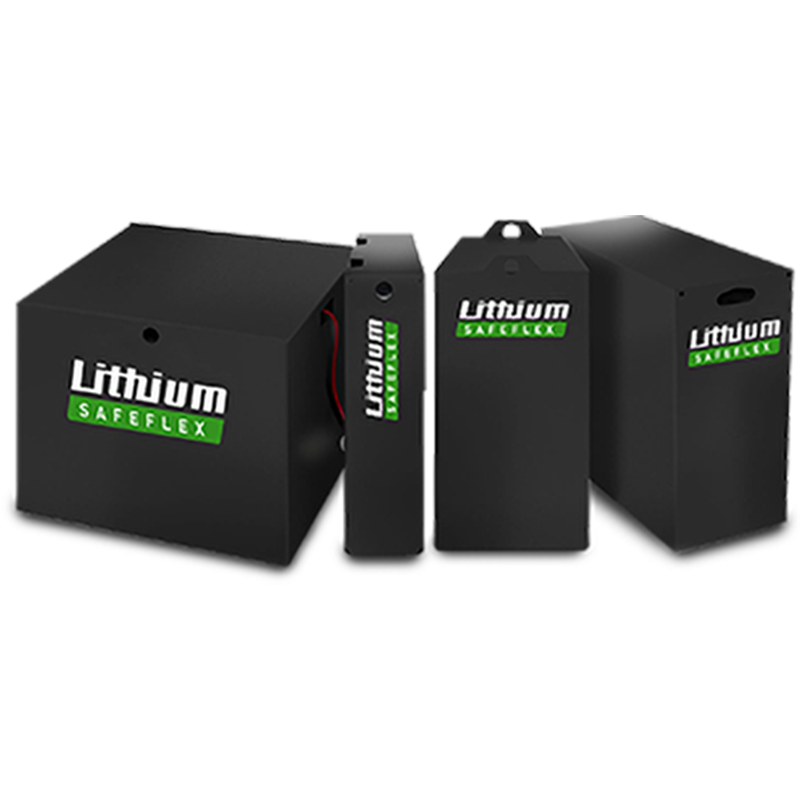
The milestone follows the company’s celebration of ten years of motive power technology leadership for material handling and ground support equipment with Lithium SAFEFlex Green Cubes Technology (Green Cubes), the manufacturer in producing Lithium-ion (Li-ion) power systems that facilitate the transition from lead-acid batteries and Internal Combustion Engine (ICE) power to green Lithium-ion (Li-ion) battery power, has announced the 10,000th sale of its Lithium SAFEFlex Battery. This flagship suite of solutions is designed to meet the cost, performance, efficiency, and durability requirements of the rugged warehouse, distribution, and airport environments. Lithium SAFEFlex industrial lithium battery systems are designed as drop-in replacements for traditional Lead acid batteries. They eliminate the need for watering and battery swaps and increase equipment up-time with fast opportunity charging. This significant milestone was achieved shortly after the company celebrated a decade of motive power technology leadership with its flagship suite of electrification solutions for the material handling industry. Measured by total power shipped, the 10,000 batteries represent 297 Mega Watt Hours (MWh) which is enough to power 110 thousand pallet jacks, 27 thousand end riders, 12 thousand reach trucks, or 9 thousand Class 1 trucks. “This achievement was made possible by the tireless efforts of Green Cubes’ world-class team,” said Michael Walsh, Chief Executive Officer for Green Cubes. “We are passionate about meeting our customers’ ever-increasing needs for high-quality state-of-the-art Li-ion power for motive equipment.” In 2024, Green Cubes will continue to invest in technology innovation and manufacturing excellence while expanding its service and customer application infrastructure. Green Cubes recently added a 36,000-square-foot facility to produce Lithium SAFEFlex batteries and house engineering and service talent to support customers. Additionally, Green Cubes established a new Technology Center in Switzerland, to focus on product innovation. Together these teams are working to improve technology and service offerings based on a decade of field learning and experience. Listen to Michael Walsh told to Kevin Lawton from The New Warehouse by clicking here.
Trade up at Port of Long Beach in November
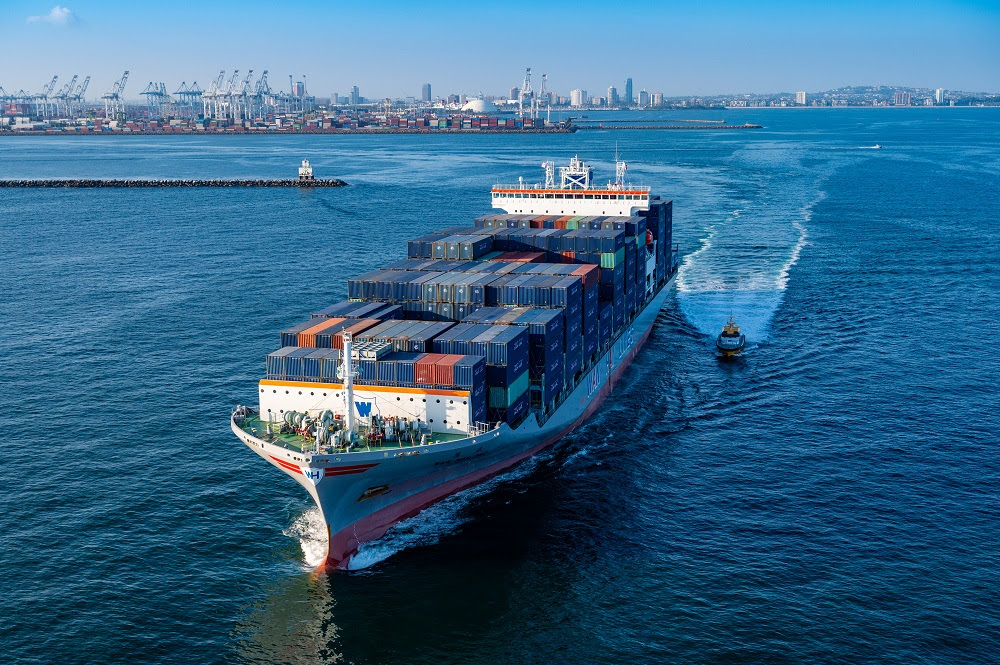
Cargo boosted by holiday shopping demand, rising market share Shippers continued to reposition cargo back to West Coast seaports in November, lifting trade for a third consecutive month at the Port of Long Beach. Dockworkers and terminal operators moved 731,033 twenty-foot equivalent units (TEUs) last month, a 24.2% increase from November 2022. Imports rose 37% to 355,339 TEUs and exports declined 13% to 108,798 TEUs. Empty containers moved through the Port were up 30.6% to 266,896 TEUs. “We are recapturing market share, online shopping is on the rise and retailers are keeping the shelves stocked to meet rising consumer demand for the holidays,” said Port of Long Beach CEO Mario Cordero. “We remain optimistic as cargo returns to this critical gateway for trans-Pacific trade.” “We appreciate the outstanding work of our waterfront workforce and terminal operators who are moving goods to ensure consumers are able to purchase gifts during the holiday season,” said Long Beach Harbor Commission President Bobby Olvera Jr. “We plan to continue delivering top-notch customer service and building for a sustainable future into the new year.” The Port has moved 7,308,848 TEUs during the first 11 months of 2023, down 14.9% from the same period last year. Cargo flows this year have been approximately on pace with pre-pandemic levels, when the Port of Long Beach moved more than 6.96 million TEUs through November 2019. For complete cargo numbers, visit polb.com/statistics.
U.S. rail traffic for the week ending December 9, 2023
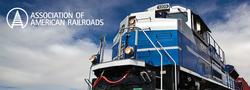
The Association of American Railroads (AAR) has reported U.S. rail traffic for the week ending December 9, 2023. For this week, total U.S. weekly rail traffic was 499,094 carloads and intermodal units, up 1.7 percent compared with the same week last year. Total carloads for the week ending December 9 were 229,424 carloads, down 2.5 percent compared with the same week in 2022, while U.S. weekly intermodal volume was 269,670 containers and trailers, up 5.5 percent compared to 2022. Five of the 10 carload commodity groups posted an increase compared with the same week in 2022. They included motor vehicles and parts, up 2,430 carloads, to 17,486; chemicals, up 1,850 carloads, to 30,948; and metallic ores and metals, up 1,189 carloads, to 20,622. Commodity groups that posted decreases compared with the same week in 2022 included coal, down 5,641 carloads, to 66,911; nonmetallic minerals, down 3,165 carloads, to 28,980; and grain, down 1,834 carloads, to 20,701. For the first 49 weeks of 2023, U.S. railroads reported cumulative volume of 11,054,418 carloads, up 0.1 percent from the same point last year; and 11,954,641 intermodal units, down 5.8 percent from last year. Total combined U.S. traffic for the first 49 weeks of 2023 was 23,009,059 carloads and intermodal units, a decrease of 3.0 percent compared to last year. North American rail volume for the week ending December 9, 2023, on 12 reporting U.S., Canadian and Mexican railroads totaled 338,908 carloads, down 2.4 percent compared with the same week last year, and 352,675 intermodal units, up 3.8 percent compared with last year. Total combined weekly rail traffic in North America was 691,583 carloads and intermodal units, up 0.6 percent. North American rail volume for the first 49 weeks of 2023 was 32,202,281 carloads and intermodal units, down 2.8 percent compared with 2022. Canadian railroads reported 93,684 carloads for the week, up 1.0 percent, and 70,668 intermodal units, down 1.3 percent compared with the same week in 2022. For the first 49 weeks of 2023, Canadian railroads reported cumulative rail traffic volume of 7,833,834 carloads, containers and trailers, down 3.1 percent. Mexican railroads reported 15,800 carloads for the week, down 18.3 percent compared with the same week last year, and 12,337 intermodal units, down 2.4 percent. Cumulative volume on Mexican railroads for the first 49 weeks of 2023 was 1,359,388 carloads and intermodal containers and trailers, up 2.6 percent from the same point last year. To view the weekly traffic charts, click here.
Episode 445: Flexible E-Commerce Fulfillment: Ware2Go & Palouse brand’s partnership
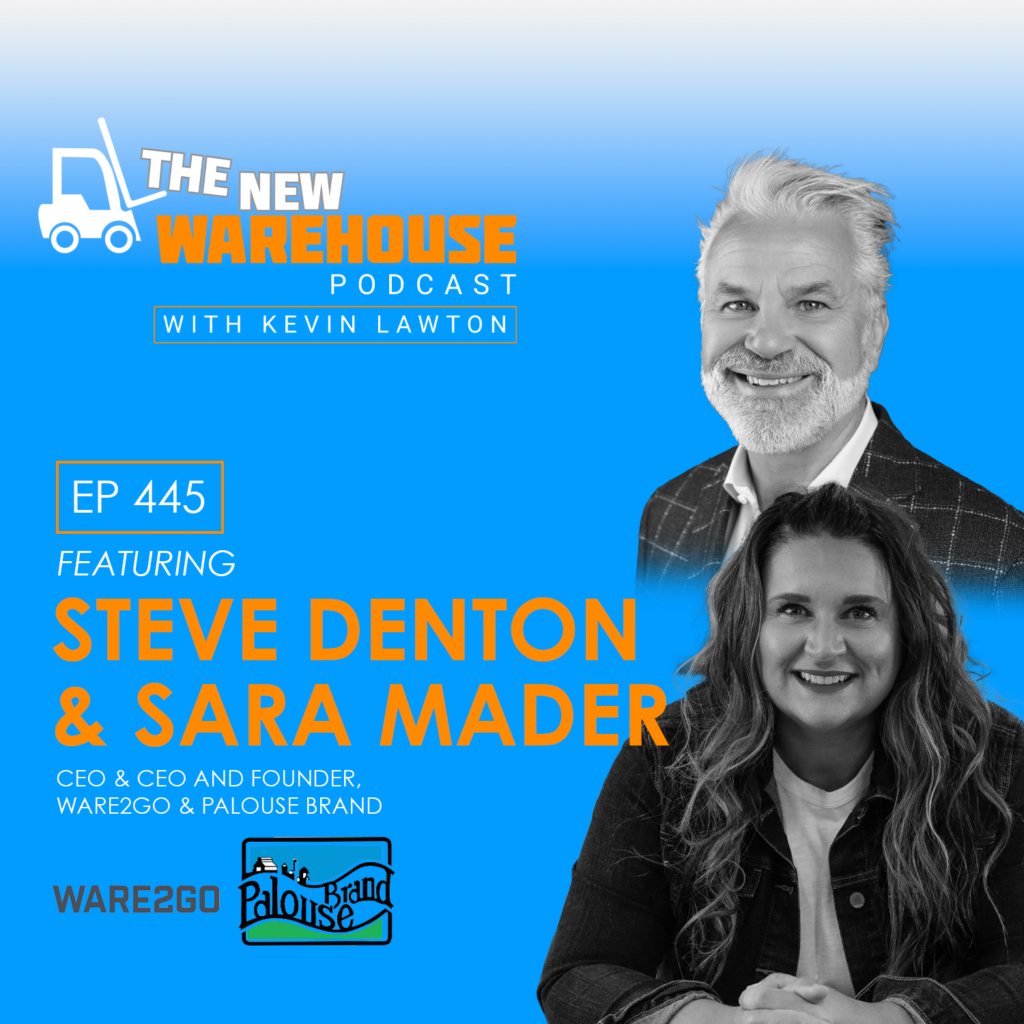
Steve Denton, CEO of Ware2Go, and Sara Mader, CEO of Palouse Brand, join episode 445 of The New Warehouse Podcast to discuss their amazing flexible e-commerce fulfillment story. They delve into the collaboration between Ware2Go, a subsidiary of UPS offering logistics solutions, and Palouse Brand, a family-owned, vertically integrated farm specializing in transparency and a unique farm-to-table consumer experience. This episode explores their combined efforts to optimize e-commerce fulfillment and tackle explosive growth. Transforming E-commerce with Flexible Fulfillment Solutions Denton shares Ware2Go’s role in enhancing the e-commerce experience for brands like Palouse. “Our technology-led approach allows for flexibility and scalability, crucial for rapidly growing businesses like Palouse,” Denton states. He explains how Ware2Go’s adaptive network and technology platform support diverse operational needs and scale with their clients’ growth. “Our shared purpose is to simplify the end-to-end supply chain to help merchants of all sizes compete and grow,” adds Denton. Leveraging Flexible E-commerce Fulfillment to Support Explosive Growth Mader recounts the Palouse Brand journey, highlighting how Ware2Go helped them manage a 4000% growth spike. “Our partnership with Ware2Go was vital in scaling our operations and meeting customer demand,” Mader shares, emphasizing the importance of having a resilient and scalable logistics partner to handle such rapid growth. The Future of Flexible E-commerce Fulfillment Collaboration Discussing future trends, both guests emphasize the growing need for data-driven, customer-centric fulfillment strategies. They highlight how technology and strategic partnerships will play a critical role in meeting the evolving demands of the e-commerce market. Key Takeaways Adaptive Fulfillment Models: Ware2Go’s flexible solutions cater to diverse e-commerce needs. Growth and Collaboration: The partnership between Ware2Go and Palouse Brands demonstrates the power of strategic collaborations in e-commerce. Future Trends in E-commerce: Data-driven and customer-focused approaches will dominate the e-commerce fulfillment sector. The New Warehouse Podcast EP 445: Flexible E-Commerce Fulfillment: Ware2Go & Palouse Brand’s Partnership
TAPPI/AICC announce Jake Hall and Greg Gumbel to Keynote at SuperCorrExpo® 2024
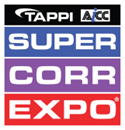
TAPPI and AICC, co-producers of the mega corrugated event SuperCorrExpo® (SCE) 2024, have announced Jake Hall and Greg Gumbel will be keynote speakers at the corrugated industry’s quadrennial event taking place September 8-12, 2024 in Orlando, FL. Jake Hall is a leading voice in the manufacturing industry. Through his popular platform, The Manufacturing Millennial, Jake seeks to educate manufacturing professionals on the latest cutting-edge automation and manufacturing technologies and their transformative impact on the industry. Committed to the long-term sustainability and growth of manufacturing, he is a fervent advocate for drawing Millennials and Gen Z into the industry, recognizing the vital role they play in driving innovation and progress. Prior to founding The Manufacturing Millennial in 2020, Jake garnered over a decade of experience in a variety of roles in the manufacturing industry, beginning his journey on the ground floor, maintaining and cleaning CNC equipment. After graduating from Grand Valley State University in 2013 with a bachelors in Product Design and Manufacturing Engineering and a minor in Biomedical Engineering, Jake swiftly transitioned into the sales domain, where he further developed his versatility and understanding of the manufacturing industry. At SuperCorrExpo® 2024, Jake will bring light to key innovations within the corrugated industry, as well as strategies for attracting and retaining the younger generation of professionals. Greg Gumbel is a renowned sports broadcaster with 50 years of experience, known for covering a wide range of major sports events including the NFL, NBA, MLB, and the Olympics, and hosting programs like “The NFL Today.” In 2001, Greg made history when he became the first African-American announcer to call play-by-play of a major sports championship in the United States when he announced Super Bowl XXXV for the CBS network. Greg has also been a key figure in March Madness since 1988, anchoring CBS’s coverage alongside notable analysts. His broadcasting excellence has earned him three Emmy awards and the prestigious Pat Summerall Award. Building on his distinguished career, Greg Gumbel is also recognized as a renowned keynote speaker. At SuperCorrExpo®, he will be presenting Rewind, Review, and Replay, an entertaining and motivational presentation which draws on Greg’s personal stories, anecdotes, and insights from the world of sports. “We are honored to have Jake Hall and Greg Gumbel join us as keynote speakers at SuperCorrExpo®,” said TAPPI CEO and President Larry N. Montague. “Jake’s expertise in manufacturing technology and Greg’s lively presentation will offer our attendees a diverse and enriching experience. We are also in the process of lining up two more esteemed keynote speakers to further enhance the caliber and diversity of our program.” SuperCorrExpo® 2024 takes place at the Orange County Convention Center in Orlando, FL. Considered one of the most influential corrugated packaging-focused trade shows in the Western Hemisphere, SCE brings together more than 6,000 producers and suppliers from over 70 countries. A record number of representatives from corrugated manufacturers from around the world are expected to attend in 2024. “SuperCorrExpo® is shaping up to be an extraordinary event,” said AICC President Michael D’Angelo. “With a record number of international participants and an exceptional lineup of speakers and exhibitors, we are eagerly anticipating an event that promises unparalleled opportunities for learning, networking and growth.” To learn more about how to be a part of this fast-selling event, contact SuperCorrExpo® Sales Director Linda Cohen via email or by phone at 914-944-0377.
Shuttles or stackers?
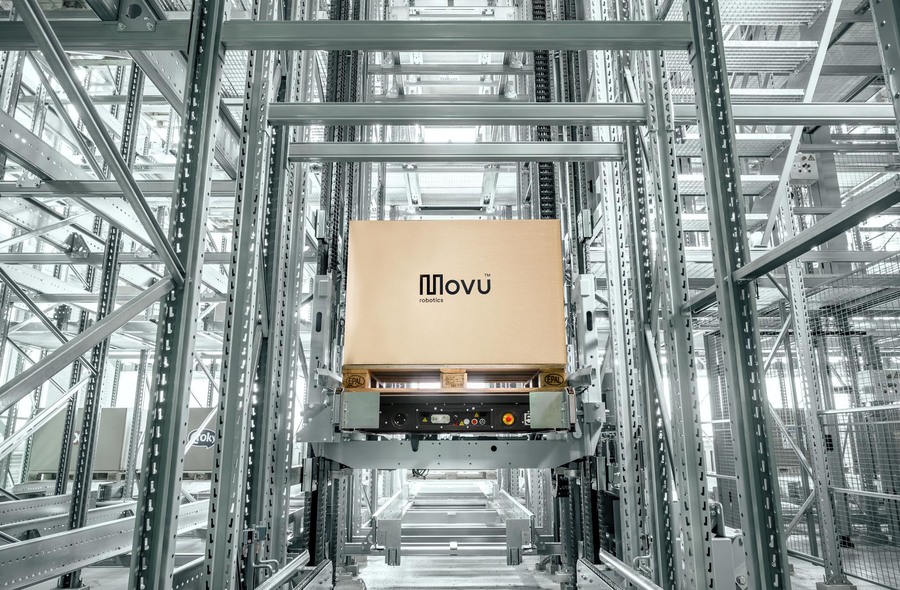
When considering automated warehousing, stacker cranes have often been the default storage and retrieval choice for pallets and bins. Shuttles, however, are increasingly being seen as the more efficient, flexible, and sustainable alternative, as Stefan Pieters, CEO of Movu Robotics, explains. Most firms that must move quantities of palletized goods moving in, out or through a warehouse are familiar with that old stalwart – the stacker crane. Indeed, it is no exaggeration to say that in many cases the warehouse is designed and built around the craneage. That, though, is far from ideal, whether viewed in terms of operational efficiency or through the increasingly important prism of sustainability. Stacker cranes are undeniably chunky. They consume a lot of material in their construction, and a lot of energy moving all that mass around. Partly as a result they require significant upfront capital investment, which is a particular challenge for smaller businesses with budget constraints. They are also very wasteful of available, expensive, floor area. They require generous aisle space to work in which reduces the overall storage density within the warehouse. They are not well suited to more space-efficient deep storage. They require the site to be all on one level, which for a warehouse of any magnitude often means building on a flood plain. They may demand floors to have a greater load-bearing capacity and place other demands on the building’s structure and services that are difficult to meet in older facilities. Also, a stacker crane layout cannot make effective use of the irregularly shaped pockets of the site that are common in older developments or in urban areas. On some warehousing sites well over 50% of potential storage space is reckoned to be wasted. Being complex systems, stacker cranes are demanding of meticulous planned maintenance, which must be carried out in situ, and whilst that is in progress that aisle is essentially out of action. Similarly, any breakdown or malfunction will disrupt operations – they constitute a ‘single point of failure’ – just one apparently minor problem can render an entire aisle’s inventory inaccessible. Perhaps most fundamentally, warehouse systems built around a stacker crane concept are fundamentally inflexible. The specific configuration of locations, aisles and cranes places a fixed limit on the maximum throughput of the facility: increasing throughput is likely to require a fairly large scale and expensive redesign and rebuild. Shuttles and space Stacker cranes still have their place – particularly for heavy goods, and where maximizing the use of the vertical space is imperative, although as we will see that is less of a differentiator nowadays. But for many palletized warehouse operations there is an increasingly attractive and viable alternative in the form of shuttle systems, such as those manufactured by Movu in alliance with our group partner stow Racking. Pallet shuttles are small vehicles with a low height, and with a footprint essentially that of the pallet they are moving. They move on rails within the storage lanes of the racking system to bring pallets to and from a loading/unloading end aisle which can also be used to transfer pallets between storage lanes. Shuttles operate in two dimensions in each ‘layer’ of the racking system but can be transferred vertically as well as between lanes. The latter is carried out automatically, through the management system and, unlike some earlier systems, without the use of a forklift truck to affect the transfer. Movu Atlas shuttles, for example, can carry pallets of 1 m x 1 m, or 1 m x 1.2 m, weighing up to 1,500 kg. Besides greatly reducing the amount of ‘wasted’ aisle space required, this approach has several advantages. There is no particular limit to vertical height – 18 meters is commonplace, and we have one client whose racking extends to an eye-popping 46 meters. Odd-shaped pockets of the site, whether this is in the plans or because of uneven ground, can be brought into use economically simply by using some shorter lanes. And because shuttles, unlike stacker cranes, are in no sense fixed, it is relatively straightforward and economical to reconfigure the racking if needs be – the racking itself is of modular design. Being battery-powered and mobile, shuttles can be moved out of the way of operations for battery charging, routine maintenance, or in the case of breakdown, so not impairing the operation of the warehouse. At times of peak activity, the number of shuttles in use can be increased – either across the warehouse or by transferring shuttles between lanes or levels, to meet increased demand in a particular section of the warehouse. Shuttle systems can thus be fully scalable and flexible. Sustainability advantage In terms of sustainability, as well as making better use of scarce real estate, shuttle systems employ much less material both in their construction and in terms of building modifications. And the saving in energy consumption simply from not having to move massive cranes around is substantial – a shuttle weighs 300 kilograms; a crane may weigh up to 15 tons, and so a shuttle system can be up to five times more energy efficient than craneage. The shuttle concept can also be applied to transporting bins of material in goods-to-person picking operations. Carrying a lighter loading (up to 50 kg) enables a significant difference from pallet shuttles. Movu’s escala shuttles, for example, can work in full 3D, moving up and down ramps to access different storage layers – a bit like a multi-story car park. Integrating with Autonomous Mobile Robots (AMRs), picking arm robots or with other forms of automation permits a high degree of automation that can yield further sustainability benefits. These can support areas of a warehouse that does not have to support regular human labor so can be run ‘lights out’ or with reduced heating. Cold store operations, meanwhile, can be made more energy efficient – Movu equipment, for example stands out as capable of working in temperatures down to -25° C. Bringing easier automation to warehouses Shuttles offer a flexible,
October 2023 Manufacturing Technology orders up over September but down from 2022
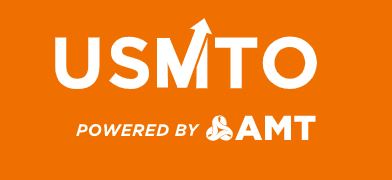
Despite a more optimistic outlook, orders for manufacturing technology, measured by the USMTO report, continued to fall relative to 2022. Through October 2023, orders totaled $4.05 billion, 13.5% behind the total for the first 10 months of 2022 As the summer of 2023 ended, the number of economists predicting a recession dwindled nearly as fast as the amount of sunlight each day. Despite the generally more optimistic outlook, orders for manufacturing technology, measured by the U.S. Manufacturing Technology Orders Report published by AMT – The Association For Manufacturing Technology, continued to fall relative to 2022. Through October 2023 orders totaled $4.05 billion, 13.5% behind the total for the first 10 months of 2022. Although total orders were behind, October was slightly above the average monthly value in 2023. October orders totaled $409.7 million, 4% above September order values. This growth was driven by orders placed in the West region, which grew nearly 60% over September. The South Central and Southeast regions also saw growth but at a much more modest pace. The Northeast and North Central-East regions declined by modest single digits, while the North Central-West region declined nearly 30% from the value of September 2023 orders. The six-week United Auto Worker’s strike lasted most of October, ending with a tentative agreement at the end of the month. Despite the shuttering of production lines, auto manufacturers continued to invest in manufacturing technology. Investments by automotive transmission manufacturers increased earlier in the year, but this is the second month in a row where manufacturers of other automotive components have increased investment. Job shops decreased the value of their orders in October while increasing the number of units purchased. This indicates that job shops are purchasing machinery to increase capacity. In contrast, OEMs have been increasing order value at a faster pace than units, suggesting that they are purchasing machinery for a designated purpose. Of these OEMs, manufacturers of household and major appliance manufacturers made their largest investment since September 2018. Manufacturers of engines, turbines, and other power transmission equipment have continued their elevated pace of orders, already 8% above the amount invested in 2022. This sector is benefiting from recent government investment, pushing orders of manufacturing technology to levels not seen since the industry was transitioning from coal-fired plants to natural gas. The November 2023 jobs report, published last Friday, came in slightly above expectations, with 199,000 new jobs added. This addition of jobs brought the unemployment rate down to 3.7% and demonstrated the continued strength of labor markets in the United States. Of those jobs added in November 2023, 28,000 were in the manufacturing sector. In addition to strong labor market conditions, consumer confidence improved for the first time in November following a three-month decline, according the Conference Board Consumer Confidence Index. A strong labor market and improving consumer confidence will have positivetrickle-down influence on the manufacturing technology markets. The Federal Reserve meets on Wednesday for the final time in 2023. Although the recent cycle of interest rate increases has coincided with a decline in orders for manufacturing technology, this doesn’t align with historic trends. The Summary of Economic Projections from the meeting will be a critical gauge of where the Fed sees growth and inflation headed in the coming months and years. Further interest rate increases aren’t expected. However, even if rates remain elevated, manufacturing technology will continue to be needed in the future if consumers continue to demand goods and services.
Steve Freckmann retiring as GM of ALL Crane’s Dawes Rigging & Crane Rental
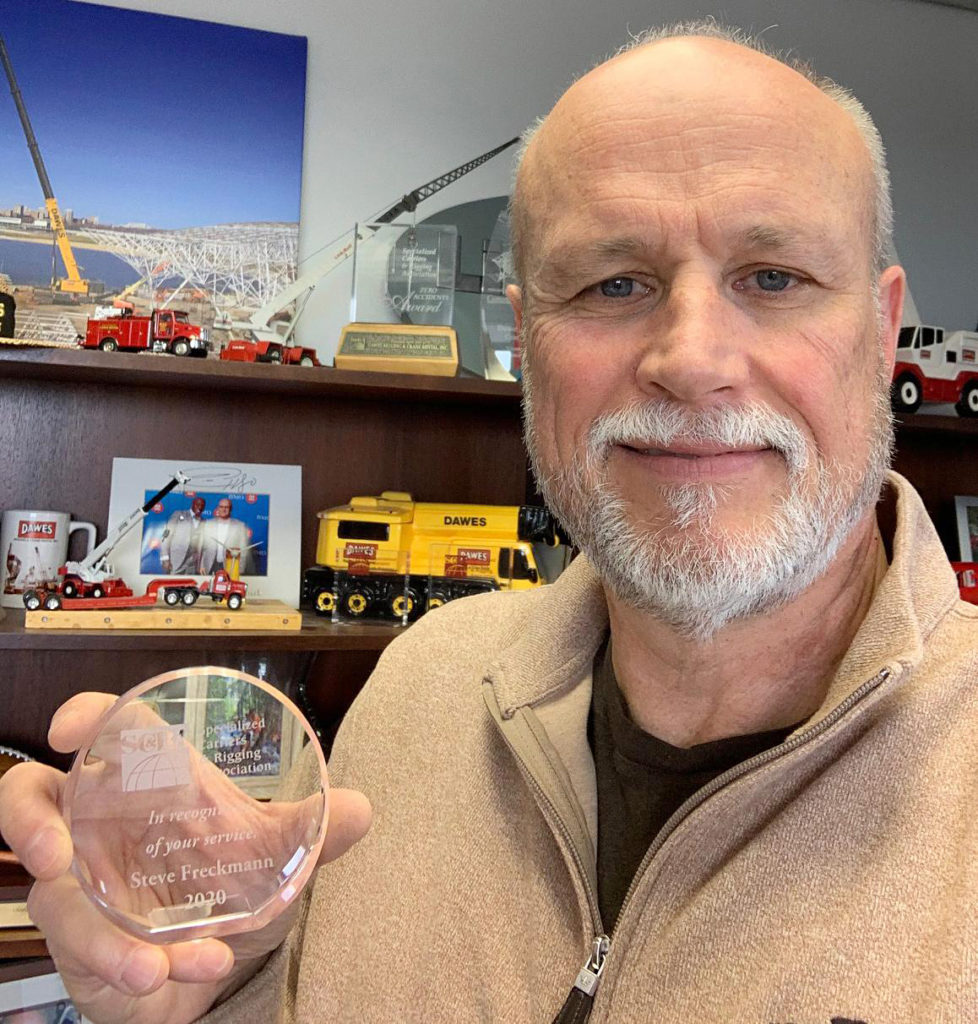
Crane biz lifer logged 34 years at helm; 45 years total with company The new year will bring big changes to Dawes Rigging & Crane Rental, a member of the ALL Family of Companies, as it will be the first time in more than three decades that Steve Freckmann isn’t its general manager. Freckmann is retiring at the end of 2023 after 34 years as GM and 45 total years with Dawes. Freckmann is a crane business lifer, starting out part-time in the shop and yard as a pre-teen. In fact, it was Freckmann’s father, Thomas, who was a part owner of Dawes before selling to the ALL Family in the late 1970s. Steve Freckmann succeeded his dad as general manager in 1989. Steve Freckmann has been active and highly visible in the local and national business communities. “I’m proud of my involvement serving on the board of directors of the Association of General Contractors of Greater Milwaukee as well as various committees,” said Freckmann. “Also, I’m grateful for the time I’ve spent serving on the various committees of the Specialized Carriers & Rigging Association.” Freckmann is a longtime believer in the value of SC&RA, including a decade and a half serving on various committees, with a chairmanship on the Crane & Rigging Group, and a three-year term on the board of directors. He currently serves on the Crane & Rigging Group Labor Committee. “Even though I’ll be departing my formal service in SC&RA, I’m pleased that ALL is still represented through the participation of Rick Mikut, ALL’s crawler crane division manager, and Derek Baumgartner, our director of risk management and counsel,” said Freckmann. “The Freckmann name is legendary within the ALL Family,” said Michael L. Liptak, CEO and president of ALL. “Steve’s leadership has helped make Dawes synonymous with quality performance, integrity, and service. We wish him all the best as his decades with us come to a close.” So, what does a man do after devoting his life to cranes? For Freckmann, it will mean more time to bike, hike, and travel with his wife. There will even be some time in the winter months chasing great cross-country skiing weather in northern Wisconsin. Continuing ALL’s legacy of promoting from within, Ryan Harrison, current branch manager of the Madison, Wis., Dawes branch and a 24-year ALL veteran, will succeed Freckmann as general manager.
Hubbell Incorporated completes acquisition of Systems Control
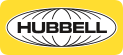
Hubbell Incorporated has announced that it has completed its acquisition of Northern Star Holdings, Inc. (commercially known as Systems Control), a portfolio company of Comvest Partners. Hubbell financed the acquisition and related transactions with net proceeds from borrowings under a new unsecured term loan facility in the aggregate principal amount of $600 million, cash on hand, and issuances of commercial paper. Systems Control is a manufacturer of substation control and relay panels, as well as turnkey substation control building solutions. These highly engineered offerings are mission-critical to grid reliability, enabling utility customers to protect and control substation infrastructure while detecting faults and controlling the flow of electricity.
GreyOrange and Hai Robotics Dynamic partnership advances automated robotic fulfillment

GreyOrange software together with Hai Robotics bots increase throughput, storage density and agility GreyOrange Inc., a global provider in automated robotic fulfillment and inventory optimization software, and Hai Robotics, a global provider in Automated Storage and Retrieval Systems (ASRS), elevate their strategic partnership, resulting in customer competitive advantages. Together, after more than two years of partnership, GreyOrange software and Hai Robotics hardware yield increased throughput, storage density and agility, resulting in accelerated customer operations and growth. In just a short span of two years, GreyOrange and Hai Robotics have completed more than 10 projects together, helping solve some of the most challenging fulfillment operations that include the largest retailer in the U.S., one of the largest fashion retailers in the world, and many other large-scale retailers across the U.S. and Europe. The two companies have come together to create a uniquely advanced offering for warehouses and distribution centers around the globe. GreyOrange’s fulfillment orchestration platform, GreyMatter™, utilizes its Multi-agent orchestration(MAO) capabilities to connect and run both Hai’s Tote to Person AMRs and GreyOrange’s Rack to Person AMRs on a single grid – unifying complex or cross-functional operations throughout a facility for streamlined operations. Hai Robotics’ ASRS – driven by Autonomous Case-handling mobile Robots (ACR) – offer unparalleled flexibility with industry-leading storage density for tote, tray, box or oversized items within an automated storage system. Hai’s goods-to-person systems can be constructed using almost any industry standard racking and containers. Systems can have varying heights up to 10 meters high, and varying container sizes and material, stored up to 5 totes deep. With such adaptable capabilities, Hai systems can be modified to help advance facilities in ways that historic automated storage technologies were previously unable to achieve. The joint solution with GreyOrange’s GreyMatter fulfillment orchestration platform creates a unique solution that can deliver maximized operational efficiency, increased speed to order fulfillment, and improved order accuracy. The partnership of these two companies provides a unified solution across technologies, while providing the ability to adapt to surges in demand and the ever-evolving consumer behavior. “Combining GreyOrange’s GreyMatter fulfillment orchestration platform with Hai Robotics‘ cutting-edge vertical Autonomous Case-handling Robotic (ACR) technology, the two companies have paved the way for solutions that are revolutionizing the industry,” said Brian Reinhart, Chief Revenue Officer, Hai Robotics. “What we’ve done together is provide end users with the throughput they need to meet their growing demand, the storage density to make the best use of their warehousing space, as well as the flexibility so that they’re not tied down in this ever-changing environment.” “The Hai Robotics and GreyOrange partnership is the perfect use case for innovation within the warehouse automation space. The industry directly benefits from our customer-centric approach to automated fulfillment,” said Akash Gupta, Co-Founder and CEO, GreyOrange. “This partnership combines our cutting edge GreyMatter software that orchestrates the largest and most complex robotic installations in the world with the vertical AMRs from Hai Robotics, including a first of its kind five deep storage solution.” In addition to simultaneous orchestration of GreyOrange AMRs and Hai Robotics ACRs with GreyMatter, this partnership has resulted in direct picking into on-demand packing boxes – eliminating extra touches from picking operations. The strategic partnership has also benefited the automated robotic fulfillment space with a fully integrated micro-fulfillment center (MFC) solution, boasting the highest storage density in the industry. This MFC solution offers the flexibility to fulfill orders in less than an hour, demonstrating an impressive level of efficiency.
Vector Security®, Inc. hires Ahsan Sheikh as President of the Vector Security® Networks Division
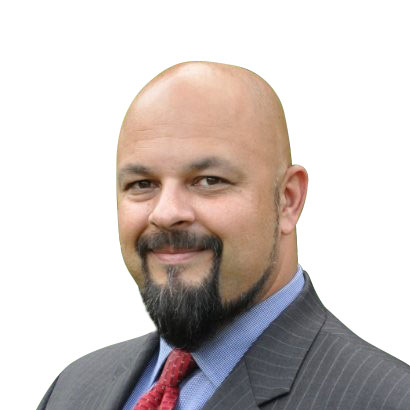
Sheikh to oversee sales, growth, retention and hands-on operational aspects of Vector Security Networks Vector Security®, Inc. has hired Ahsan Sheikh as President of its Vector Security® Networks division, the single-source provider of physical security solutions and managed network services to multi-site businesses across North America. As President of Vector Security Networks, Sheikh leads all aspects of the division, including sales, growth, customer retention and operations. Additionally, he will oversee the establishment of new sales channels and the development of sales strategies that drive Vector Security Networks to achieve its business goals and objectives. Sheikh joins Vector Security Networks from a global security solutions company where he spent more than 26 years, most recently as Global Vice President providing strategic direction and leadership for global clients within various vertical markets spanning 58 countries. “Ahsan brings strong operations and business acumen to Vector Security Networks,” said Pamela J. Petrow, President and CEO, Vector Security. “We welcome him to the team and look forward to the leadership he will provide as we expand our business and position the division for continued growth and success.” “I’m very excited to lead Vector Security Networks as we expand our physical security and managed network offerings while bringing our solutions into a broader range of verticals and new markets, building upon the successes that have made us a top integrator for some of the largest multi-site businesses in North America,” Sheikh said. Sheikh will be part of Vector Security’s Executive Management Team reporting to Petrow.
Port of Long Beach names two division directors
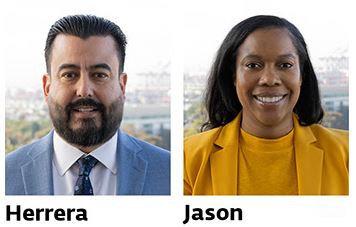
The Long Beach Board of Harbor Commissioners has approved the appointments of new directors for the Port of Long Beach’s Human Resources and Engineering Design divisions. Khristina Jason, previously the Port’s assistant director of Human Resources since November 2021, will become Director of Human Resources. She joined the Port’s HR Division in April 2021 as Manager of Talent Relations and Engagement, having served various roles in the City of Long Beach Department of Human Resources beginning in 2015. The Port’s Human Resources Division oversees the Port’s human capital strategies and provides services for about 570 employees of the City of Long Beach Harbor Department. Clint Herrera, who has been the Port’s assistant director of Engineering Design since 2019, worked previously in public works with the cities of South Gate, where he was deputy city engineer and Corona, where he rose to senior civil engineer. His experience also includes private sector engineering work on transportation projects. The Engineering Design division is critical to the development and maintenance of Port infrastructure such as channels, roads, wharfs, utilities and other facilities, producing technical reports, studies, plans and specifications for Port construction projects. Jason has a bachelor’s degree in healthcare administration with a minor in human resources management as well as a master’s degree in public administration from California State University, Long Beach. Prior to her city service, she worked in human resources for the Transportation Security Administration. Herrera is a registered professional engineer and earned a bachelor’s degree in civil engineering from Loyola Marymount University and a master’s degree in public administration from California State University, San Bernardino. The appointments are effective Dec. 16.