A home run for Bigfork: Community impact project transforms local baseball field
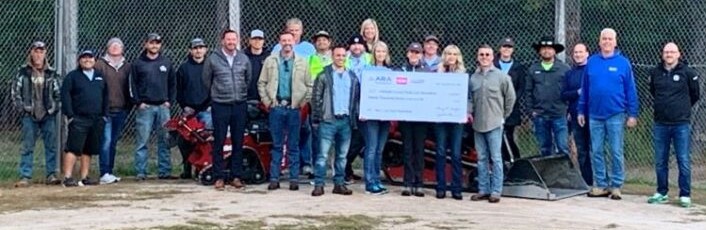
ARA, Toro Company Foundation, Local volunteers step up to the Plate for Area Youth The American Rental Association (ARA) Foundation, in partnership with The Toro Company Foundation, Flathead County Parks and Bigfork Baseball Association, completed a Community Impact project in Bigfork, Montana to benefit Aero Lane Park, a local baseball field. On September 27, volunteers from all four organizations worked together to enhance and upgrade the baseball diamond and park amenities. This included creating a new infield, new backstop fencing, refurbished bleachers and dugout benches as well as beautification updates throughout the park. “Creating high-quality playing fields is crucial to the ballplayers’ experience. ARA members from the local community and across the northwest region stepped up to the challenge, using their professional talents and equipment to transform the field and beautify the park,” said Judson McNeil, ARA Foundation director of programs and fundraising. To complete the work at the field, volunteers from ARA, The Toro Company Foundation and representatives from seven northwest regional and local rental operations turned out. The volunteers moved grass, replaced and stained bleachers, installed new gravel in the dugouts and parking areas, aerated the field and much more. All projects required the use of different equipment provided by local rental stores. “Having an outdoor space for our community’s youth to recreate, create memories, develop friendships and build character is an important aspect of our department,” said Chris Maestas, Flathead County Park director. “The generous monetary donation by ARA and Toro as well as the time and effort from their volunteers to improve a little league baseball field that is used heavily by the Bigfork community will have a lasting impact on the ball players and the community as a whole. Flathead County is fortunate to have the support of the groups and individuals who have stepped up to the plate to support our youth through parks and recreation.” The Bigfork project is the third Community Impact project the ARA Foundation has completed in partnership with The Toro Company Foundation in 2023. Planning is underway for the 2024 projects, visit the ARA Foundation website to learn more and submit an application.
BSL Battery: Industrial expands testing and product validation capabilities
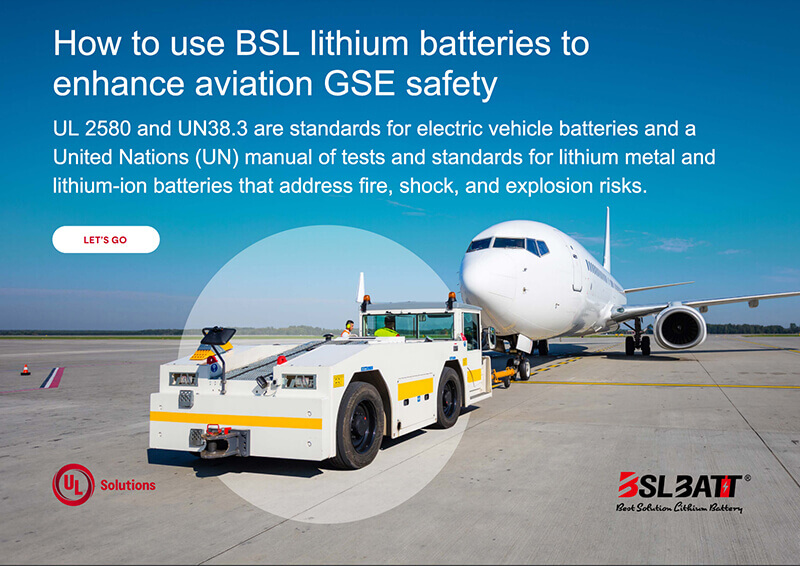
Ground support equipment (GSE) is traditionally powered by internal combustion engines (ICs), just like the aircraft they support. The burning of diesel, gas, or propane, however, results in carbon emissions that negatively impact the environment. Airlines and airports are replacing diesel-fueled ground support equipment (GSE) with lithium-ion battery-powered machines to meet evolving environmental requirements. By switching from diesel-fueled equipment, we reduce carbon emissions, fueling and engine maintenance costs, as well as the health risks associated with internal combustion engine emissions and noise. BSL Battery – Industrial Expands Testing and Product Validation Capabilities with Field Shaker To make sure the truck is “revived” immediately and the life expectancy is excellent after a “heart transplant”, BSLBATT Battery team conducts strict performance tests to assure all BSLBATT battery products meet industrial standards for quality and compatibility for every applications. Announcing Last month an expansion in-house with all the testing required to meetUL 2580 and UN/DOT 38.3compliance Testing and product validation capabilities for equipment, including field shakers. To learn more about UL 2580 testing and UN38.3 certification with BSL Battery – Industrial, keep watching our video or read on! As they work to convert their existing ground support equipment into more energy-efficient electric vehicles, key players in the aviation industry support the development of these safety standards.Retrofitting lithium-ion batteries into more traditional diesel-powered equipment when upgrading existing fleets is also addressed in the Standard. Most ground support equipment today is powered by gasoline or diesel engines, and some by lead-acid batteries. Emissions from internal combustion engines can harm the environment and ground personnel. Over the next three decades, airports around the world have committed to removing all diesel-powered vehicles from their apron and airside. A $640,000 (USD) grant was awarded by The Chicago Department of Aviation toward United Airlines’ $1.43 million (USD) joint investment with the Environmental Protection Agency to purchase 26 new zero-emission GSE vehicles.United Airlines will save more than 1.4 million gallons of diesel fuel and reduce emissions of carbon dioxide (CO2), the primary air pollutant in the generation of greenhouse gases, by more than 16,000 tons (as well as other byproducts of fuel emissions). The Voluntary Airport Low Emissions Program (VALE) offers financial incentives for airports to reduce their carbon emissions.According to the FAA, this program has funded 121 projects at 56 airports since September or 2020.Many airports around the world are eligible for grants. Retrofitting GSE lithium batteries Some aviation GSE is already powered by lead-acid batteries. However, lithium batteries are significantly lighter, smaller, and offer better energy storage and physical space than lead-acid batteries. Because of these reasons, the aviation industry is retrofitting its lead-acid-powered GSE fleets with lithium batteries. Since lithium retrofit batteries are not closely regulated, the aviation industry is particularly concerned about their safety. In order to address this concern, the Standard provides for the retrofitting of lithium batteries into more traditional diesel and lead-acid powered equipment. Maintenance and operations at airports Unlike lead-acid batteries, lithium batteries require no maintenance other than charging. Due to the prevalence of lead-acid powered GSE in their fleet inventory, most airline operations facilities already have charging equipment. Lithium battery chargers, new battery charging stations, and their facilities can be tested for safety compliance and for fire, electric shock, and explosion risks. In the aviation industry, managers of dangerous goods and ground support teams agree that prevention is the best way to increase safety. Haley Ning said: “UL’s comprehensive testing facility enables in-house qualification of everything from the smallest to the largest battery system, eliminating the need to outsource any testing aspects of UL or UN certification and speeding up the process. ”BSL Battery – Industrial Chief Operating Officer. “Our strong relationship with UTL, an Underwriters Laboratories compliant laboratory, coupled with these strong testing capabilities, enables BSL Battery – Industrial to rapidly develop and deliver world-class energy storage systems to critical applications for our end users. All BSL Battery – Industrial systems are designed and tested to meet the rigorous standards of the modern operating environment, with an unwavering focus on safety and reliability. We remain committed to providing clean energy solutions to this fast-growing market.” Lithium-ion Transition The first step in implementing lithium-ion battery technology is to assess the condition of the current fleet of ground support equipment. Consider these questions as a starting point: Is there equipment that is nearing the end of its useful life that would need to be replaced? Could you easily replace the lithium-ion battery pack on your existing electric GSE? You should evaluate the specifics of the fleet operations once you have answered the first two questions: What is the average number of hours per day that the GSE is used? Is there a requirement for battery charging infrastructure? What are the environmental and regulatory requirements? (not just today, but in the future as well) A detailed return on investment (ROI) calculation can provide insight into the economic benefits of switching to a lithium-ion or lead acid power source. Don’t forget to include maintenance costs, battery replacement costs, and refueling/charging infrastructure costs when calculating the total cost of ownership. GSE with zero emissions and high performance is in high demand. Because lithium-ion batteries provide significant benefits, IC engines are increasingly being replaced by lithium-ion batteries. In light of government regulations on emissions, now may be the right time to start looking at high performance lithium-ion batteries for GSE fleets.
WIT Index shows of DEI policies on the rise in transportation
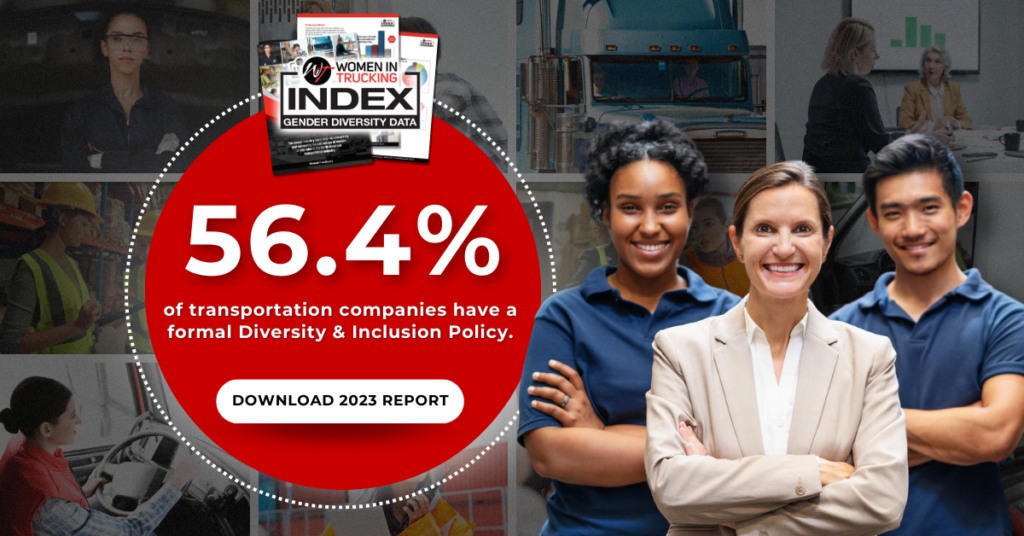
Workplace cultures that are strong in diversity and inclusion have been linked in increased productivity, and companies in commercial freight transportation are increasingly formalizing diversity and inclusion (D&I) policies, according to the 2023 WIT Index. Developed by the Women In Trucking Association (WIT), the WIT Index is the industry barometer to benchmark and measure each year the percentage of women who make up critical roles in transportation. For the second year in a row, WIT has included in its 2023 WIT Index if participating companies have a formal Diversity & Inclusion (D&I) policy. Approximately 56.4% of companies confirmed their organization has a formal policy, showing a significant increase from 2022, while 19.3% say their company currently does not have a formal policy in place. Approximately 19.3% confirmed that their company is currently in the process of developing a formal D&I policy. In addition, the percentage of female leaders in transportation companies continues to increase, according to the 2023 WIT Index. The WIT Index shows that 31.6% of C-suite executives in transportation companies are women, 36.9% of company leaders are female, and 28.4% of boards of directors are women. “In recent years, many companies in transportation have made their D&I policies publicly available not only to provide transparency to potential job seekers on the importance of gender diversity to their corporate culture but also for customers and business partners,” said Jennifer Hedrick, president and CEO of WIT. “As a result, diverse and inclusive workplaces earn deeper trust and more commitment from their employees and key stakeholders.” Initiated in 2016, the WIT Index is based upon reported statistics by companies in transportation, including for-hire trucking companies, private fleets, transportation intermediaries, railroads, ocean carriers, equipment manufacturers, and technology companies. Data involving the 2023 WIT Index was confidentially gathered from January through April of 2023 from 350 participating companies of various sizes operating in the trucking industry. Percentages are reported only as aggregate totals of respondents rather than by individual company. For more information on the WIT Index and to download a full executive summary of the 2023 WIT Index findings, visit https://www.womenintrucking.org/index. Click Here for Prevalence of Diversity and Inclusion Policies
Episode 426: E-Commerce fulfillment and growth with NFI
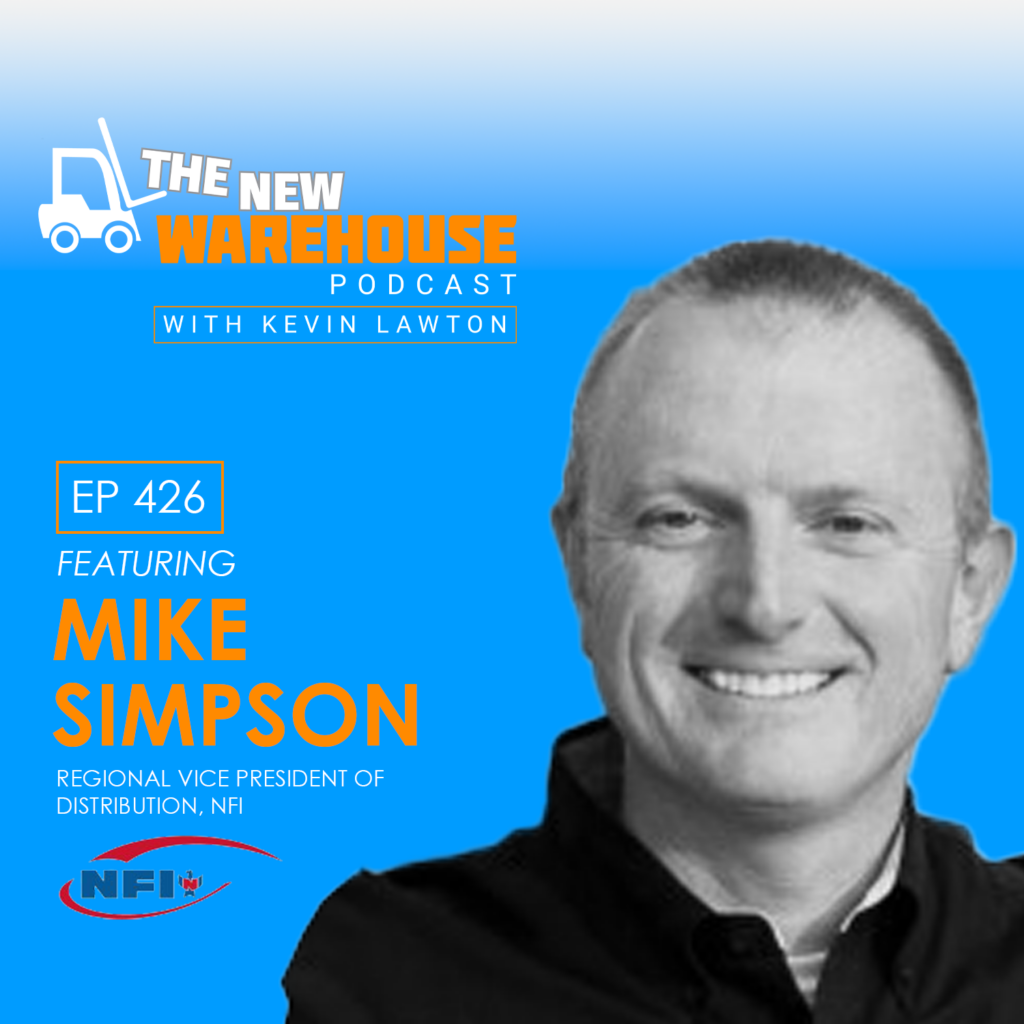
Welcome back to The New Warehouse Podcast, where today we are joined by Mike Simpson, the VP of e-commerce at NFI. With a 90-year history, NFI is a provider in the third-party logistics (3PL) industry and is known for its expansive operations across the United States and Canada. In this episode, we focus on the e-commerce aspect of NFI, exploring the trends and challenges they have faced in this rapidly evolving sector. NFI’s Dive into E-Commerce Operations The shift towards digitalization has been a significant aspect of NFI’s growth strategy over the last decade. Alongside other services like trucking, port operations, and warehousing, e-commerce has increasingly become a focal point for the company with its NFI eCom solution. This change came after six months of rigorous market research involving over 100 interviews with brands and retailers. The findings showed a significant gap in the market, especially in the mid-market brand segment. Mike elaborates on two significant challenges they found in the market: Limited Scalability – Many 3PL providers promised growth but lacked the operational infrastructure to handle the rapid scaling requirements of mid-market brands. Inefficient Customer Service – Another stumbling block was the lack of high-level customer service to assist brands in their growth phases. This comprehensive research prompted NFI to focus on offering solutions tailored for the mid-market, providing the reliability and scalability often missing from smaller 3PL providers. Leveraging Automation and Robotics for Scalability and Efficiency A noteworthy point from the conversation revolves around the role of automation and robotics in NFI’s operations. According to Mike, NFI invests in innovation to stay ahead of the curve. This focus is not just to replace human labor but to supplement it, given the low unemployment rates in the logistics sector. Technologies like goods-to-person systems and robots that assist workers in trailer unloading are being tested and implemented. The goal is to enhance operational efficiency while tailoring solutions to meet specific customer needs. These innovations range from complete automation to semi-automated solutions, and they are all aimed at increasing efficiency while balancing the cost to serve customers effectively. NFI considers automation a spectrum where the application depends on multiple factors, including customer requirements and operational efficiency. Navigating the Future of E-commerce Fulfillment As we move into peak season and beyond, the e-commerce landscape expects to continue its steady growth. While the astronomical growth rates seen during the pandemic may not be sustainable, Mike anticipates that the sector will continue to chip away at the market share of brick-and-mortar retail stores. He also mentions that this peak season will indicate the rate at which different players in the retail market grow, potentially favoring mid-market brands that have successfully leveraged marketing and advertising. Key Takeaways In the U.S., E-commerce currently accounts for about 24% of retail sales for physical goods. Experts predict this will rise to around 33% by 2027. NFI strongly emphasizes employee retention through a culture-driven approach that starts from the top down, focusing on attracting, retaining, and developing as their mantra while prioritizing safety at all levels of the organization to support and sustain growth. The speed of deliveries could potentially determine the future of e-commerce fulfillment, not just the quantity delivered. The New Warehouse Podcast EP 426: E-Commerce Fulfillment and Growth with NFI
Mitsubishi Logisnext Americas hosts over 60 students at Marengo facility for National Manufacturing Day
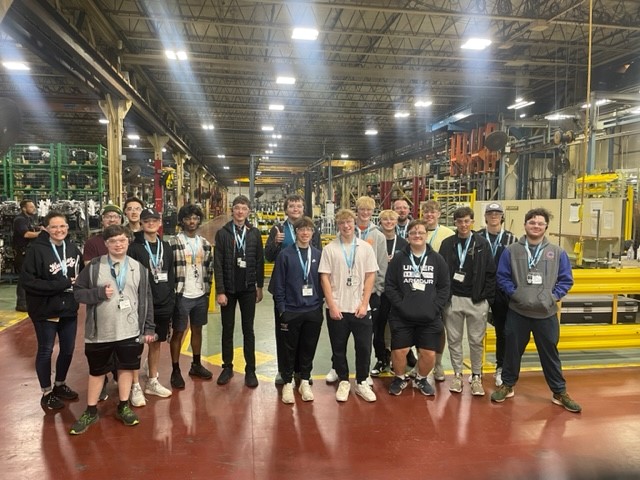
Mitsubishi Logisnext Americas group (Logisnext), a North American provider and manufacturer of material handling and innovative automation and fleet solutions, proudly opened its doors to over 60 local high school students for an exclusive tour of the Marengo facility in celebration of National Manufacturing (MFG) Day, Oct. 6. Led by Jon Crane, Senior Manager of Manufacturing Engineering and Facilities, Rob Jasinski, Director, Production, and Kenzie Heatherwick, Manufacturing Engineering Lead, from Mitsubishi Logisnext Americas, the tour provided an invaluable opportunity for students to explore the manufacturing world and discover exciting career prospects across the globe. During this tour, students had the chance to learn more about Logisnext’s cutting-edge technologies and innovative solutions. They gained firsthand experience with the manufacturing process which included everything from the fabrication of parts and robotic welding to powder coat painting and product assembly. “Innovation fuels manufacturing and tours like these are essential in nurturing our youth’s curiosity,” said Jon Crane, Senior Manager of Manufacturing Engineering and Facilities, Mitsubishi Logisnext Americas. “Our mission at Mitsubishi Logisnext Americas is not only to provide innovative solutions but also to inspire the next generation of manufacturing leaders. We aim to bridge the gap between education and industry providing students with a glimpse into the dynamic realm of manufacturing.” According to the National Association of Manufacturers, there is a pressing need to fill 4.6 million high-skill, high-tech, and high-paying jobs over the next decade. National MFG Day serves as a collaborative platform for manufacturers to address shared challenges, promoting not only individual growth but also community development and ensuring a thriving future for generations to come. Mitsubishi Logisnext Americas remains committed to fostering the growth of the manufacturing sector. The student tour underscores the company’s dedication to nurturing talent and promoting innovation within the industry.
Q3 2023 new Industrial Manufacturing planned projects remain flat with 150 for September
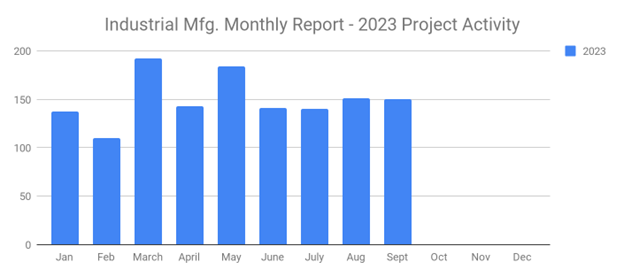
SalesLeads has announced the September 2023 results for the new planned capital project spending report for the Industrial Manufacturing industry. The Firm tracks North American planned industrial capital project activity; including facility expansions, new plant construction and significant equipment modernization projects. Research confirms 150 new projects in September as compared to 151 in August and 140 in July. The following are selected highlights on new Industrial Manufacturing industry construction news. Industrial Manufacturing – By Project Type Manufacturing/Production Facilities – 139 New Projects Distribution and Industrial Warehouse – 90 New Projects Industrial Manufacturing – By Project Scope/Activity New Construction – 42 New Projects Expansion – 57 New Projects Renovations/Equipment Upgrades – 48 New Projects Plant Closings – 17 New Projects Industrial Manufacturing – By Project Location (Top 10 States) California – 11 Michigan – 11 Wisconsin – 10 Ohio – 9 Indiana – 8 Texas – 8 Pennsylvania – 7 Georgia – 6 Ontario – 6 New York – 5 Largest Planned Project During the month of September, our research team identified 19 new Industrial Manufacturing facility construction projects with an estimated value of $100 million or more. The largest project is owned by Cummins Inc., who is considering investing $3 billion for the construction of a battery manufacturing facility and currently seeking a site in INDIANA. Top 10 Tracked Industrial Manufacturing Projects ALBERTA: Packaging and paper product MFR. is planning to invest $584 million for the expansion and equipment upgrades on a manufacturing facility in HINTON, AB. They are currently seeking approval for the project. Completion is slated for Fall 2027. QUEBEC: Copper foil MFR. is planning to invest $514 million for the renovation and equipment upgrades on a manufacturing facility in GRANBY, QC. They are currently seeking approval for the project. Completion is slated for 2026. PENNSYLVANIA: Custom corrugated packaging products MFR. is planning to invest $500 million for the renovation and equipment upgrades on their multiple manufacturing facilities in PA. They are currently seeking approval for the project. OHIO: Air taxi MFR. is planning to invest $478 million for the construction of a manufacturing and warehouse facility in DAYTON, OH. They have recently received approval for the project. Construction is expected to start in 2024, with completion slated for 2025. NEW MEXICO: Semiconductor MFR. is planning to invest $300 million for the renovation and equipment upgrades on a manufacturing facility in RIO RANCHO, NM. They are currently seeking approval for the project. BRITISH COLUMBIA: Wood product MFR. is planning to invest $200 million for the construction of a manufacturing facility in HOUSTON, BC. They are currently seeking approval for the project. Construction is expected to start in 2024. OHIO: Global plumbing and heating equipment MFR. is planning to invest $200 million for the construction of a 180,000 SF manufacturing facility in SHALERSVILLE, OH. They are currently seeking approval for the project. Construction is expected to start in late 2023, with completion slated for early 2025. TEXAS: Solar panel MFR. is planning to invest $200 million for the construction of a 1-million sf manufacturing and distribution facility in WILMER, TX. They are currently seeking approval for the project. Completion is slated for 2024. VIRGINIA: Glass MFR. is planning to invest $155 million for a 360,000 SF expansion of their manufacturing and distribution facility in RIDGEWAY, VA. They are currently seeking approval for the project. Completion is slated for late 2025. FLORIDA: Aerospace company is planning to invest $150 million for the construction of a 200,000 SF manufacturing facility in TITUSVILLE, FL. They are currently seeking approval for the project. About IMI SalesLeads, Inc. Since 1959, IMI SalesLeads, based in Jacksonville, FL is a leader in delivering industrial capital project intelligence and prospecting services for sales and marketing teams to ensure a predictable and scalable pipeline. Our Industrial Market Intelligence, IMI identifies timely insights on companies planning significant capital investments such as new construction, expansion, relocation, equipment modernization and plant closings in industrial facilities. The Outsourced Prospecting Services, an extension to your sales team, is designed to drive growth with qualified meetings and appointments for your internal sales team. Visit us at salesleadsinc.com.
Port of Long Beach named ‘Best West Coast Seaport’
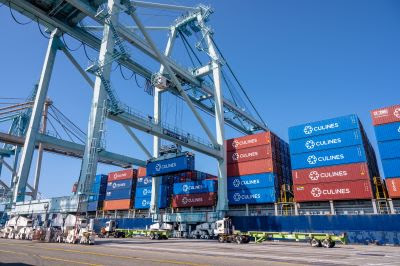
Earns honor from trade publication for fifth consecutive year The Port of Long Beach has been named the Best West Coast Seaport in North America for the fifth year in a row by the readers of shipping trade publication Asia Cargo News. The honor was announced during the Asian Freight, Logistics and Supply Chain Awards held Sept. 28 in Singapore. Asia Cargo News hosts and organizes the awards ceremony yearly to recognize the top seaports, shipping lines and other logistics industry leaders. More than 15,000 readers of Asia Cargo News made the nominations for each category, then determined the winner from a list of eight finalists in each category. Find the full list of winners here. “It’s wonderful to be honored again by the very customers we serve,” said Port of Long Beach CEO Mario Cordero. “Thank you to the waterfront workforce and industry partners who continue to make the Port of Long Beach the most sustainable, efficient gateway for trans-Pacific trade.” “We are investing $2.2 billion during the next 10 years to upgrade our rail infrastructure, modernize terminals, deepen channels and enhance our operations to stay ahead of our competition,” said Long Beach Harbor Commission President Bobby Olvera Jr. “We are grateful for the recognition by Asia Cargo News and the support of its readers.”
Fairchild Equipment expands in Marinette WI
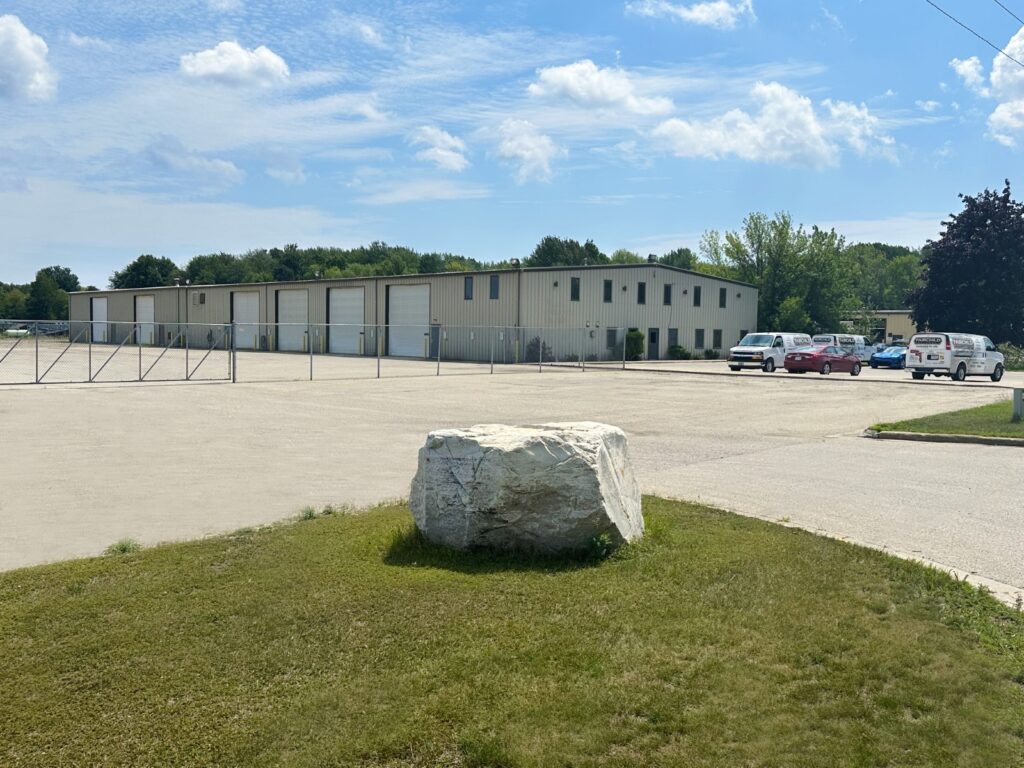
A new facility to support business communities in Northern Wisconsin and Upper Michigan Fairchild Equipment has announced the opening of its new facility in Marinette, Wisconsin. Since opening its first Marinette location at 2815 Mary Street in 1992, the company has experienced tremendous growth, leading to the need for a larger facility. Effective October 1, 2023, all operations will be conducted out of the new location at 2505 Biehl Avenue. “We are excited to be taking this step to help us continue to support the business communities in Northern Wisconsin and Upper Michigan,” said CEO of Fairchild Equipment, Chad Fairchild. “It has been our commitment to those businesses and their trust in us that has allowed us to become a major supplier of material handling equipment, parts, service, and fleet management for Northern Wisconsin and Michigan’s Upper Peninsula.” This new facility marks the fourth facility expansion since 2020 in Fairchild Equipment’s network of locations throughout the Midwest. It will better accommodate the expansive product line Fairchild Equipment offers, which includes warehouse and material handling equipment as well as engineered storage solutions and fleet management services. “Our team’s commitment to our mission of creating Customers for Life in this area is what has allowed us to grow to another level,” said Fairchild. “We are confident that our new facility will help us even better serve our customers and provide the best possible service.” The new facility is triple the size of the previous one. It will feature a showroom and a variety of new, used and rental equipment in stock. It will also feature a larger parts department, helping customers to get the parts they need faster. With a larger service department, customers will also be able to get their equipment serviced more quickly. “We are excited to be able to offer our customers a larger facility with more services and products,” said Mark Stammer, Director of Sales for Wisconsin, Michigan and Illinois. “We want to thank the companies that have entrusted us with supplying and maintaining their material handling equipment over the years. It’s been our commitment to those businesses and their trust in us that has allowed us to become a major supplier of material handling equipment, parts, service, and fleet management for Northern Wisconsin and Upper Michigan. We look forward to continuing to provide industry-leading support to our current customers and to the new customers who choose to partner with us in the future.”
Hyundai Material Handling introduces new branding

Hyundai Material Handling, a business unit of HD Hyundai Construction Equipment North America, Inc., is introducing new branding that reflects its growing presence and evolving mission in North America and as a global leader in the manufacturing of advanced material handling equipment. “Forging our own path sets Hyundai apart,” said Lewis Byers, Executive Vice President/COO, Hyundai Material Handling. “Now, it’s time that our brand – the name, image, and message, we send to the marketplace – captures our commitment to innovation and our focus on the future.” The branding includes a new corporate name and logo, new branding colors, and an updated look for its HYUNDAI MATERIAL HANDLING equipment brand. The new corporate name is HD Hyundai Xitesolution-Material Handling. The HD stands for Human Dynamics, reflecting the company’s mission of helping individuals achieve their goals. The Hyundai Xitesolution name links together it’s world-famous brand with how Hyundai is going beyond manufacturing to be a solutions provider to customers in an ever more competitive and complex world. “Material Handling” will continue to identify the equipment Hyundai offers and the market it serves. Included in the updated logo is a new “Forward Mark” icon that replaces the company’s familiar triangles. This new icon conveys Hyundai’s commitment to pushing forward, finding new innovations and new ways to help its customers move forward and be more efficient and productive in a changing world. As part of Hyundai’s commitment to sustainability, the new branding includes a new color treatment, merging its traditional blue with green. While the company has a new corporate logo, for dealers and customers, the company’s main brand ID will remain HYUNDAI MATERIAL HANDLING, helping to sustain the company’s dramatic growth in sales and awareness in the North American market. “A lot is changing in the way we present ourselves to the market,” added Lewis Byers. “But we want our dealers and forklift owners to know that some things will never change for us, and that’s our dedication to offering quality, value, and innovation in our products and services, and our commitment to make certain that when it comes to material handling, no one delivers more.”
Husky wins Plastics Industry Association Bioplastics Innovation Award
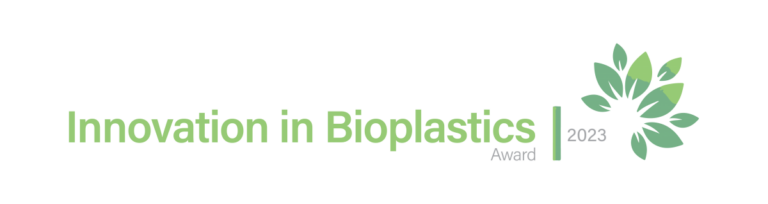
The Plastics Industry Association (PLASTICS) announced Husky Technologies (Husky), as the winner of PLASTICS’ 2023 Innovation in Bioplastics Award. The announcement came as part of PLASTICS’ eighth annual, online #BioplasticsWeek awareness and education event. Husky won the award for their hot runner system, UltraMelt, which was engineered for the efficient and sustainable injection molding of bioresins. Bioresins, made in whole or in part from renewable biological resources, present unique challenges in injection molding. According to Husky, UltraMelt specifically addresses these challenges with non-reactive surfaces and stainless-steel components to preserve the sensitive chemistry of bioresin materials and minimize degradation. After rigorous testing and optimization, UltraMelt was introduced to the marketplace in 2022, becoming a pioneering solution for bioresin melt delivery. Patrick Krieger, PLASTICS’ Vice President of Sustainability congratulated Husky saying, “This is the first time PLASTICS has awarded an equipment company and their original technology for using more bioplastics, and I congratulate Husky on this achievement. Equipment design is complex and takes significant investment. The time and resources Husky spent on this technology speaks to the importance and potential of bioplastics in the plastics industry.” “On behalf of the Husky team I would like to thank you, the Plastics Industry Association, for this prestigious honor. Bioplastics, together with advancements in circular polymer processing, are key parts of Husky’s sustainability strategy. We are convinced that by working together as an industry we will turn challenges into opportunities. We will demonstrate that the circular economy is not just a buzzword but a reality”, said John Galt, CEO of Husky. “Polymers preserve and protect more effectively than any other substrate. They can be formed into an infinite number of shapes and sizes. They are lightweight and unbreakable. They have the lowest overall environment footprint. They keep consumer costs down. Investing and working together to building truly circular solutions is good for our industry, for our children and the planet.” A formal presentation of the Bioplastics Innovation Award will be made on the Sustainability Stage at NPE2024: The Plastics Show, which will take place from May 6-10, 2024, in Orlando, Florida. PLASTICS member companies interested in submitting innovations for consideration in the 2024 Innovation in Bioplastics Award competition can look forward to the opening of the submission window in May of 2024 at https://www.plasticsindustry.org/who-we-serve/plastic-recycling/bioplastics/innovation-in-bioplastics-award/.
Raymond introduces industry’s first wireless Integrated Tether System
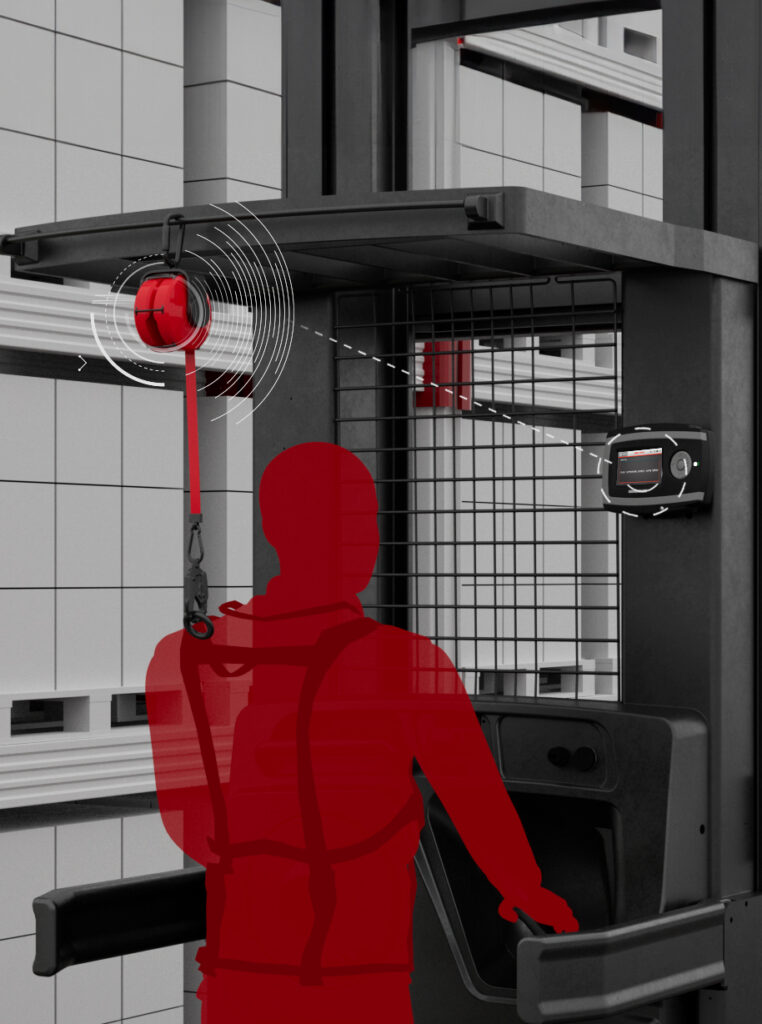
System provides controlled slowdown functionality and valuable data to help reinforce operator training for very narrow aisle lift trucks Continuing a long tradition of industry-leading innovation, The Raymond Corporation introduces the Integrated Tether System, a first-of-a-kind operator assist tool designed to alert operators and managers and to limit lift truck functionality* if an operator is not properly tethered. The wireless connection in the Integrated Tether System is compatible with Raymond® lift trucks, is unique in the marketplace and offers valuable data-gathering capabilities that can help reinforce best practices with all operators, enhancing security and confidence. “Over the last several years, facility owners and managers have had to deal with increasing the number of operators in the warehouses and the need to reinforce and monitor best practices,” said Shannon Curtis, product manager at The Raymond Corporation. “As a result, managers are looking for technology-based offerings that can help assist managers with these ever-increasing demands. This solution comes at a perfect time to support the new U.S. Department of Labor Occupational Safety and Health Administration national emphasis program and reinforces Raymond’s dedication to providing secure solutions for operations.” The Integrated Tether System features a smart tether that uses a sensor to connect to and communicate with the lift truck and offers audio and visual notifications to alert the operator of tether status — connected or disconnected. When operators pair Raymond lift trucks and Raymond iWAREHOUSE® and iMONITOR® Telematics, the lift truck will respond in one of two ways: when the operator’s harness is properly connected to the self-retracting lanyard (SRL), the lift truck retains full travel speed and full lift-height capability; or if the operator is not properly connected, the lift truck limits travel speed to 1 mph and disables lift capability. Offering a single-source solution for those facilities with mixed fleets or facilities without iWAREHOUSE Telematics, the comprehensive system will still share audio and visual notifications to operators if a tether connection has not been properly made. In addition to controlling lift truck functionality, the Integrated Tether System offers valuable reporting capabilities through iWAREHOUSE and iMONITOR Telematics, allowing managers to simplify workforce management and training by providing data and metrics on operator connection histories, system involvements, and more. “That’s what sets the Raymond Integrated Tether System apart,” Curtis said. “Wireless integration with iWAREHOUSE Telematics means the tether is less expensive to integrate and there are fewer parts to maintain. Factor in the data-reporting capabilities,* and the Integrated Tether System becomes an easy choice for facilities that frequently hire new or inexperienced operators.” The Integrated Tether System offers full functionality when used with iWAREHOUSE Telematics and Raymond Very Narrow Aisle Equipment; 5300, 5400, 5500, and 5600 models and the Raymond 9600 and 9700 Swing-Reach® Trucks. Operators can use the Integrated Tether System with a full-body harness and an SRL.
Propane Council calls attention to energy resiliency for National Propane Day
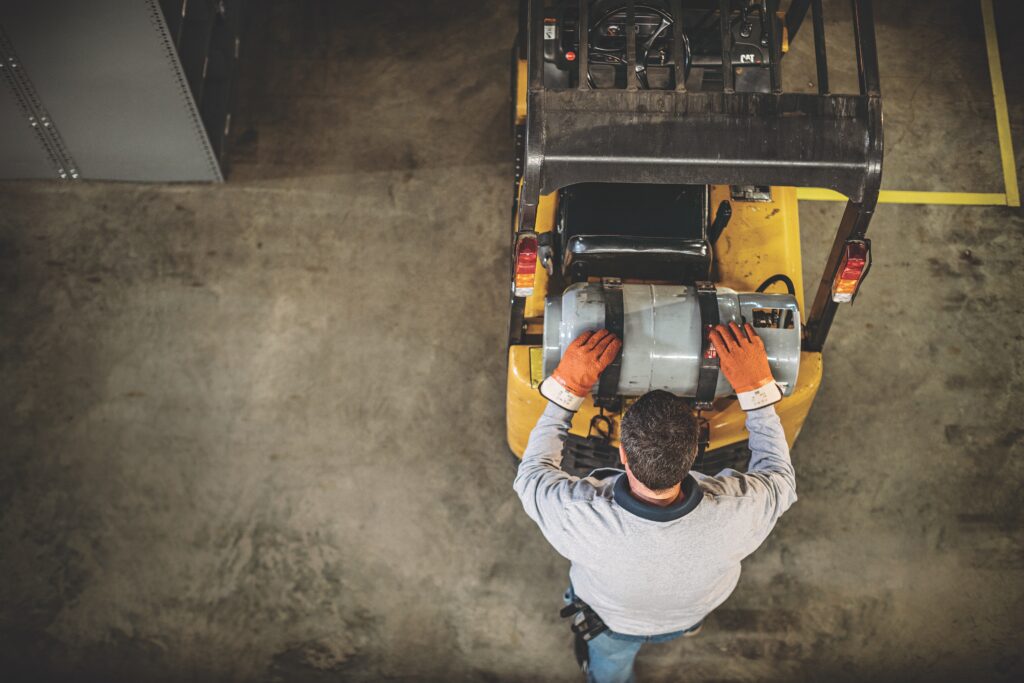
The Propane Education & Research Council (PERC) is celebrating the second annual National Propane Day on October 7, 2023. National Propane Day is an opportunity to celebrate all the ways propane keeps America running and to highlight all the benefits propane offers to users everywhere, including material handling professionals. “By keeping both small and large material handling operations running, propane is the powerhouse of the U.S. supply chain,” said Jim Bunsey, director of commercial business development at PERC. Material handling operations throughout the U.S. have used propane for decades and continue to rely on it to provide 100 percent power. Propane can be safely used in well-ventilated structures both indoors and out to keep product moving while keeping the air free from harmful emissions. Today, propane can be found powering forklifts, terminal tractors, and light- and medium-duty vehicles. As a low-carbon, highly efficient, and reliable energy source, propane is an ideal choice to ensure warehouses and ports stay resilient. With the ability to power prime and backup generators, facilities can stay operational no matter the electric grid’s status. “National Propane Day is about recognizing the impact of propane on material handling operations throughout the nation,” said Bunsey. As part of National Propane Day, PERC is also celebrating the continued growth and production of renewable propane—an ultra-low carbon option that further moves the propane industry down the path to zero carbon emissions. Renewable propane is made primarily from plant and vegetable oils, animal fats, or used cooking oil. It offers the same great features as conventional propane—reliability, portability, and power—with the added benefit that it introduces no new carbon into the environment. For more information on how propane power material handling operations, visit Propane.com/material-handling.
ALAN announces 2023 Humanitarian Logistics Awards winners
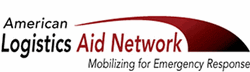
The American Logistics Aid Network (ALAN) has announced the 2023 winners of its Humanitarian Logistics Awards. “Today we’re honored to recognize a few of the people and businesses that have been a beacon of hope during disasters like Hurricane Ian and the conflict in Ukraine, as well as those who work diligently to fight systemic disasters like food insecurity,” said ALAN Executive Director Kathy Fulton. “Their combined efforts have shown the power logistics has to make a difference in the lives of disaster survivors – and inspire us to grow this network of giving more and more each day.” This year’s recipients include: United States Cold Storage, which received ALAN’s Outstanding Contribution To Disaster Relief Efforts Award Flexport.org, which received ALAN’s Outstanding Contribution To Disaster Relief Efforts Award ARPCO Transport Services, which received ALAN’s Outstanding Contribution To Disaster Relief Efforts Award Scotlynn, which received ALAN’s Employee Engagement Award And Dr. Diego Vega, Associate Professor of Supply Chain Management and Social Responsibility and Director of the HUMLOG Institute at the Hanken School of Economics, who received ALAN’s Research And Academic Contribution Award. United States Cold Storage was honored for providing seven months of frozen warehouse space free of charge to store 150 pallets of frozen pork – enough to help the requesting non-profit feed 500,000 future disaster survivors. Flexport.org merited its award for delivering more than 74 million lbs of relief supplies to over 91 different countries since 2018, providing support to 100 million people – including survivors of the war in Ukraine, drought and regional instability in the Horn of Africa, and COVID-19. ARPCO Transport Services received its award for donating transportation services to move more than 350,000 pounds of food and supplies to Fort Worth Hope Center Food Bank to combat food insecurity. Scotlynn was honored for providing financial and volunteer services to community members, employees and a local food pantry following Hurricane Ian – and for supporting the National Guard’s emergency response operations by transporting relief materials throughout southwestern Florida. Dr. Diego Vega was lauded for his 12+ years of research and thought leadership into how different logistics services providers can contribute to the establishment of more efficient and effective humanitarian supply chains. He’s the creator and lead educator of the first Introduction to Humanitarian Logistics MOOC, a board member of the World Humanitarian Forum’s SCM programming board, and will help review the 2022-2026 UN’s Global Logistics Cluster strategy. “These outstanding honorees are living, breathing examples of what selfless logistics is all about,” Fulton said. “We are thrilled to recognize them today – and proud they represent an industry that takes action to uplift the well-being of disaster survivors around the globe.”
H&E opens new branch in Daytona Beach Florida
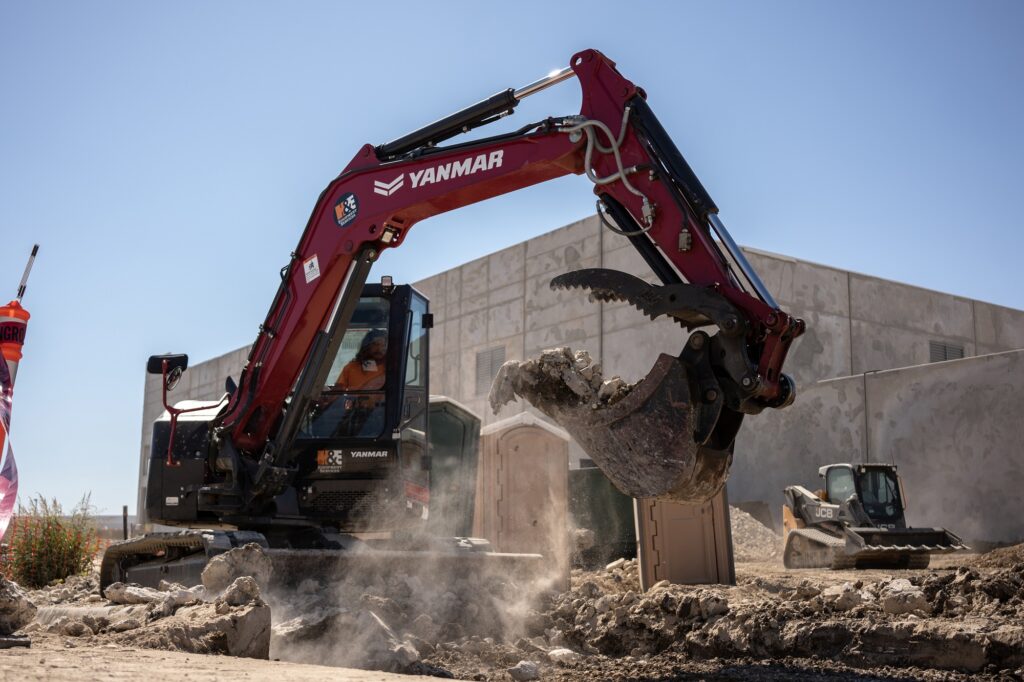
Effective October 4, 2023, H&E Equipment Services Inc. (H&E) announces the opening of its Daytona Beach branch, its 13th rental location in the state of Florida. Since the beginning of the second quarter of 2023, H&E has opened 12 new branches across the country, and this is the fifth new location in the Sunshine State since the second half of 2022. The facility is located at 998 Bellevue Avenue, Daytona Beach, FL 32114-5162, phone 386-368-7301. It includes a fully fenced yard area, offices, and a repair shop and carries a variety of construction and general industrial equipment. “The location of our Daytona Beach branch gives H&E total coverage of the Atlantic Coast and Central Florida. The new facility is located between H&E’s Jacksonville and Palm Bay branches, and our Orlando and Ocala locations are even closer, so we can source equipment and reach any job site across the area with ease,” says Branch Manager Stefan Garza. “Our proximity to I-95, I-4, U.S. 1, and A1A is ideal for getting our new fleet to job sites.” The Daytona Beach branch specializes in the rental of aerial lifts, earthmoving equipment, telescopic forklifts, compaction equipment, generators, light towers, compressors, and more and represents the following manufacturers: Allmand, Atlas Copco, Bomag, Case, Club Car, Cushman, Doosan, Gehl, Generac Mobile, Genie, Hamm, Hilti, Husqvarna, JCB, JLG, John Deere, Kobelco, Kubota, LayMor, Ledwell, Lincoln Electric, Link-Belt Excavators, MEC, Miller, Multiquip, Polaris, Sany, Skyjack, SkyTrak, Sullair, Sullivan-Palatek, Tag, Towmaster, Unicarriers, Wacker Neuson, Yanmar, and others.
AAR Rail traffic for September and the week ending September 30 2023
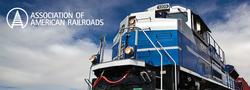
The Association of American Railroads (AAR) has reported U.S. rail traffic for the week ending September 30, 2023, as well as volumes for September 2023. U.S. railroads originated 921,716 carloads in September 2023, up 2.3 percent, or 20,754 carloads, from September 2022. U.S. railroads also originated 1,008,896 containers and trailers in September 2023, up 0.7 percent, or 7,096 units, from the same month last year. Combined U.S. carload and intermodal originations in September 2023 were 1,930,612, up 1.5 percent, or 27,850 carloads and intermodal units from September 2022. In September 2023, 13 of the 20 carload commodity categories tracked by the AAR each month saw carload gains compared with September 2022. These included: motor vehicles & parts, up 8,327 carloads or 15.2 percent; petroleum & petroleum products, up 5,547 carloads or 16.0 percent; and chemicals, up 5,530 carloads or 4.6 percent. Commodities that saw declines in September 2023 from September 2022 included: grain, down 6,651 carloads or 9.0 percent; coal, down 4,012 carloads or 1.4 percent; and coke, down 1,062 carloads or 9.1 percent. “Rail traffic, although improving, remains in uncertain territory along with the economy,” said AAR Senior Vice President John T. Gray. “Intermodal had the best volume month of the year in September, showing, after three years, that ‘peak season’ still exists although much more reserved and occurring somewhat later than past peaks. Grain shipments improved slightly from extremely low summer levels, while chemicals and petroleum products had reasonably solid months. However, a sustained boost across rail categories will require stronger overall industrial growth.” Excluding coal, carloads were up 24,766 carloads, or 4.0 percent, in September 2023 from September 2022. Excluding coal and grain, carloads were up 31,417 carloads, or 5.7 percent. Total U.S. carload traffic for the first nine months of 2023 was 8,774,830 carloads, up 0.3 percent, or 24,723 carloads, from the same period last year; and 9,329,334 intermodal units, down 8.2 percent, or 831,733 containers and trailers, from last year. Total combined U.S. traffic for the first 39 weeks of 2023 was 18,104,164 carloads and intermodal units, a decrease of 4.3 percent compared to last year. Week Ending September 30, 2023 Total U.S. weekly rail traffic was 500,154 carloads and intermodal units, up 2.8 percent compared with the same week last year. Total carloads for the week ending September 30 were 235,988 carloads, up 3.7 percent compared with the same week in 2022, while U.S. weekly intermodal volume was 264,166 containers and trailers, up 2.0 percent compared to 2022. Nine of the 10 carload commodity groups posted an increase compared with the same week in 2022. They included metallic ores and metals, up 2,681 carloads, to 23,142; chemicals, up 2,151 carloads, to 31,750; and motor vehicles and parts, up 1,403 carloads, to 15,973. One commodity group posted a decrease compared with the same week in 2022: grain, down 2,417 carloads, to 18,501. North American rail volume for the week ending September 30, 2023, on 10 reporting U.S., Canadian and Mexican railroads totaled 350,483 carloads, up 3.6 percent compared with the same week last year, and 346,771 intermodal units, down 1.5 percent compared with last year. Total combined weekly rail traffic in North America was 697,254 carloads and intermodal units, up 1.0 percent. North American rail volume for the first 39 weeks of 2023 was 25,361,005 carloads and intermodal units, down 3.8 percent compared with 2022. Canadian railroads reported 97,896 carloads for the week, up 2.1 percent, and 70,662 intermodal units, down 13.6 percent compared with the same week in 2022. For the first 39 weeks of 2023, Canadian railroads reported cumulative rail traffic volume of 6,175,243 carloads, containers and trailers, down 3.4 percent. Mexican railroads reported 16,599 carloads for the week, up 12.2 percent compared with the same week last year, and 11,943 intermodal units, up 7.4 percent. Cumulative volume on Mexican railroads for the first 39 weeks of 2023 was 1,081,598 carloads and intermodal containers and trailers, up 3.0 percent from the same point last year. To view the rail traffic charts, click here.
Doosan Bobcat expands global brand strategy; RYAN® Turf Renovation Equipment transitions to Bobcat trand
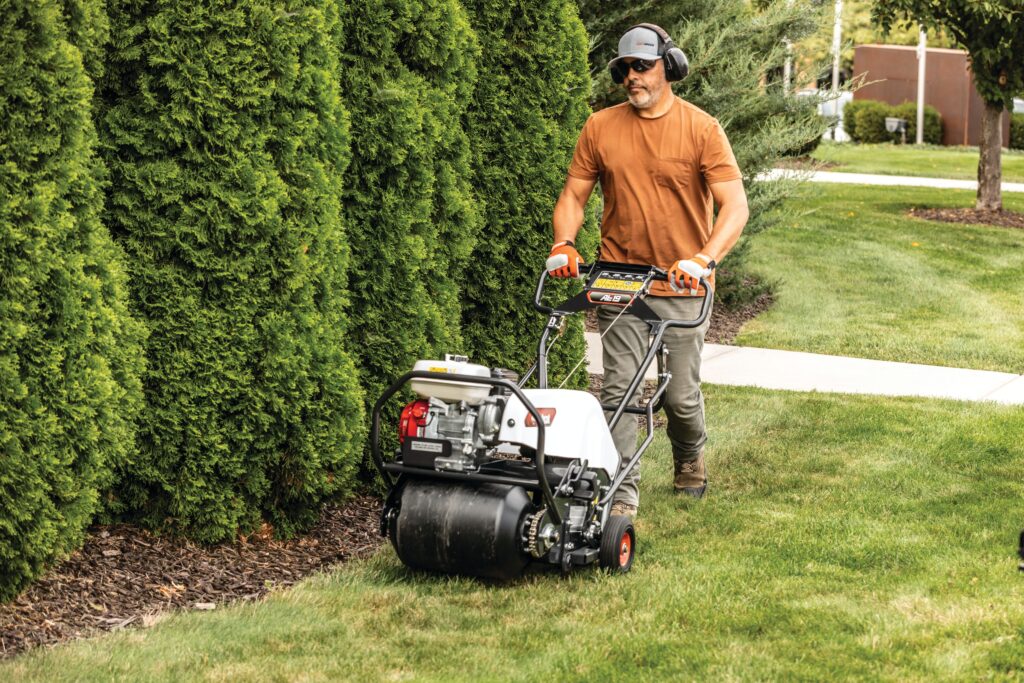
Doosan Bobcat, Inc., a company within Doosan Group, has expanded its global branding strategy as it announces its RYAN® turf renovation equipment will rebrand under the Bobcat trade dress in 2024. Bobcat, a global compact equipment, innovation and worksite solutions brand, invented the compact equipment industry when it introduced the first compact loader in 1958. RYAN equipment joined the Doosan Bobcat portfolio in 2020, following the acquisition of BOB-CAT Mowers and the Steiner and RYAN brands of grounds maintenance equipment from Schiller Grounds Care, Inc. RYAN has produced trusted turf renovation equipment for more than 75 years and features a unique product lineup including aerators, sod cutters, dethatchers, power rakes, overseeders and other specialty products that serve landscaping and grounds care professionals across a variety of industries including golf, sports turf, landscaping and rental. Following the company’s success in new product industries such as mowers, compact tractors and grounds maintenance equipment, Bobcat has streamlined its branding approach to strengthen overall brand equity, market recognition and consumer recall of all product offerings. The transition aims to create a cohesive customer experience and grow the organization’s footprint, making the brand more accessible to more customers in more places. “Bobcat has been a recognized name for decades—known for its toughness and versatility. We are proud to extend the brand to new product categories so we can empower even more people to accomplish more,” said Scott Park, Doosan Bobcat CEO and vice chairman. Earlier this year, Doosan Bobcat announced its Doosan Portable Power, Doosan Industrial Air and Doosan Industrial Vehicle brands would transition into the Bobcat product portfolio in North America and applicable markets worldwide in 2024. “The Bobcat brand has grown tremendously over the past years, and we recognize the opportunity to further unleash the brand in bold, new ways by extending it into new product categories as we grow our brand portfolio,” said Laura Ness Owens, Doosan Bobcat vice president of global brand and North American marketing. With this refreshed identity, RYAN products will undergo design and aesthetic changes in alignment with current Bobcat branding. The turf renovation equipment is produced at the Doosan Bobcat manufacturing facility in Johnson Creek, Wis., and will continue to be manufactured there following the brand transition. Bobcat-branded RYAN equipment, along with its newly rebranded portable power, industrial air and material handling, is expected to be available for customer purchase through Doosan Bobcat’s extensive, global dealer network in 2024. Bobcat and these rebranded product lines will proudly remain part of the broader Doosan Group portfolio. The Bobcat-branded turf renovation products will be displayed in the Bobcat indoor booth (3052) at Equip Exposition in Louisville, Ky., from Oct. 17-20.
Episode 425: Exploring Portable Storage Solutions with Pete Warhurst of Red Rover
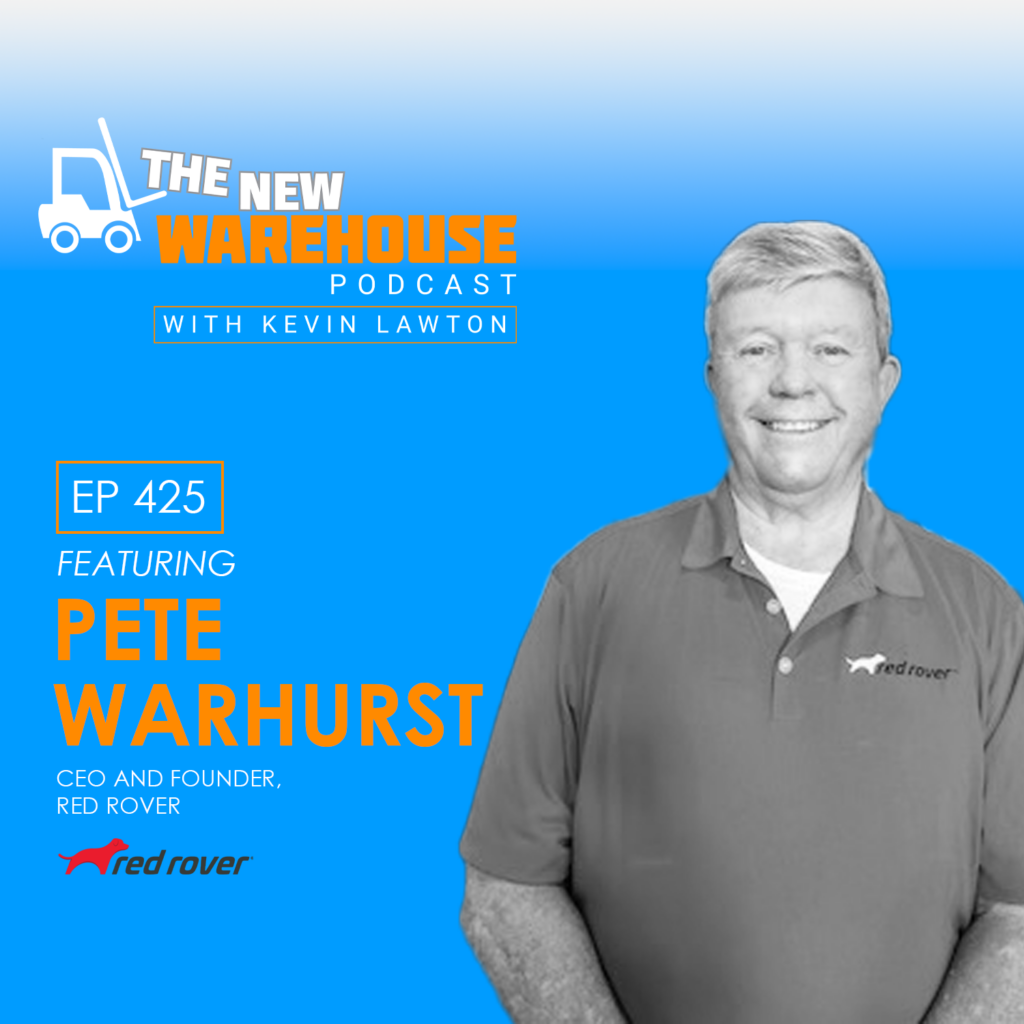
We’re delighted to host Pete Warhurst, the CEO of Red Rover and PODS founder, on today’s episode of The New Warehouse podcast. Red Rover has found a creative solution for the moving and storage industry with its “fetchable” solutions. Tune in to hear Pete discuss the unique value proposition of their product, the technology behind it, and its potential application in the warehousing and logistics sector. Navigating Transportation in the Portable Storage Industry The portable storage industry has its own set of unique challenges and opportunities. Initially, the main hurdle was efficiently delivering the storage container to the consumer’s driveway. Traditional methods like roll-off tow trucks were not viable solutions, as they could damage the driveway and disarrange the items inside the container. Pete and his team had to innovate to find a more customer-friendly delivery mechanism that didn’t involve tilting or sliding the container off the truck bed. Pete discovered that consumer demands often drove innovation as the business evolved. For example, customers started asking to move their containers from one county to another, pulling the company into the moving industry. This need led to expanding services to meet consumer demands, from local to inter-county moves. Interestingly, customer creativity didn’t stop there; people continued to find new uses for these portable storage containers inside and outside traditional warehousing environments. This consumer-driven innovation prompted the company to adapt continually, leading Pete to his next venture, RedRover. At the core of RedRover is eliminating the logistical headaches that come with delivery and transportation. Pete realized that even with route optimization and increased density, delivery was still a break-even proposition and often a source of customer dissatisfaction. RedRover aims to eliminate the frustration from this part of the business, focusing on streamlining logistics to enhance customer satisfaction and operational efficiency. Red Rover’s Portable Storage Solution Empowers Consumers Through Flexibility and Control Customers start by booking a truck and a container online or through the app. After confirming their reservation, they drive to a designated Red Rover facility, where they can access their reserved truck using a secure gate code. The Red Rover model offers two unique styles of trucks, which are: Ramp Truck – This is the initial truck style Red Rover started with. It features a versatile ramp the customer can position anywhere around the truck. This allows consumers to load items conveniently through doors on the side or the back of the truck. Retriever Truck – This newer truck model works best for those who need longer-term storage solutions and the convenience of a container. The container comes off the truck with the push of a button and is placed directly onto the consumer’s driveway, eliminating the need for the truck to remain parked there. Once they pick their desired truck, consumers can manage their portable storage needs without relying on a delivery schedule. The truck is free for up to 16 hours for loading and unloading. Once the customer is ready, they can simply return the container for convenient storage or efficient transportation across town or the country. Leveraging Portable Storage for Future Applications in Warehousing This Red Rover portable storage solution has significant potential for warehousing with wide use of storage containers. The safety measures, the ease of operation, and the potential for added automation could transform warehouse container management. Additionally, the Red Rover system could offer new opportunities in scenarios like driver shortages, where time and efficiency are of the essence. Warehousing operations could greatly benefit from this technology, as it could ease the process of unloading containers from chassis, saving time and boosting efficiency. As warehouses evolve, especially with the demand for space and quick turnover, solutions like Red Rover could become essential tools for handling storage and transportation challenges effectively. Key Takeaways Red Rover Revolutionizes Delivery: The company has innovated a more efficient, customer-friendly way to deliver storage containers, resolving traditional logistical headaches. Self-Service Model: Red Rover’s unique model allows consumers to manage their portable storage needs on their schedule, enhancing flexibility and control. Future Warehousing Applications: Red Rover’s technology can potentially solve warehousing problems, particularly in scenarios like driver shortages and quick turnover demands. Listen to the episode below and leave your thoughts in the comments. The New Warehouse Podcast EP 425: Exploring Portable Storage Solutions with Pete Warhurst of Red Rover
Help for truckers one-stop event returns Oct. 17-18 at the Port of Long Beach
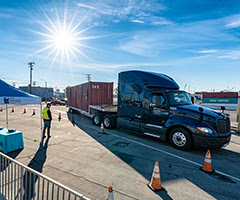
Truck drivers and others can enroll in certifications and learn about new regulations required to work at the San Pedro Bay ports complex at a one-stop event at the Port of Long Beach scheduled for October 17 and 18. The event will allow truckers to enroll with the Transportation Worker Identification Credential (TWIC), obtain radiofrequency ID tags (RFID) and sign up for the Port’s Truck Alert traffic notification system. Additionally, representatives from the California Air Resources Board will be available to provide information about the Advanced Clean Fleets regulation, requiring any new drayage trucks registered after Jan. 1, 2024, to be zero-emissions. The Port of Long Beach is hosting the event in partnership with CARB, the Transportation Security Administration and the identity certification company IDEMIA. The event is scheduled for 8:30 a.m. to 4:30 p.m. on Tuesday, Oct. 17 and Wednesday, Oct. 18 at the Port of Long Beach Terminal Access Center, 1265 Harbor Ave., Long Beach (southwest corner of Harbor Avenue and West Anaheim Street). Free tacos will be available to participants from 11 a.m. to 2 p.m. each day, while supplies last. This will be the final Help for Truckers event for the year. TWIC appointments and pre-enrollment are available at universalenroll.dhs.gov/programs/twic. Click New Enrollment, complete the information and in Step 9 – Select Appointment Location, choose “Pop Up: Port of Long Beach, 10/17-10/18.”
Lineage acquires warehousing and e-Commerce assets of Burris Logistics
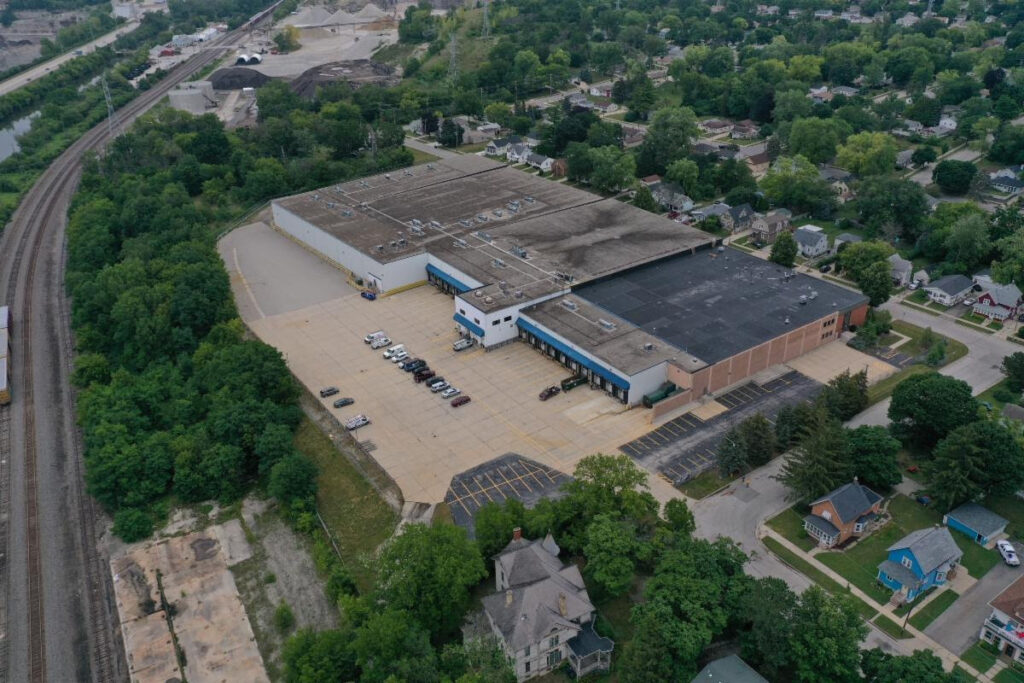
Acquisition of eight facilities strengthens Lineage’s network across the Eastern and Midwestern United States, providing customers with greater access to end-to-end cold storage solutions. Combination enhances Lineage’s existing e-commerce and direct-to-consumer fulfillment business that serves more than 100 customers Lineage Logistics, one of the world’s temperature-controlled industrial REITs and integrated solutions providers, has announced the acquisition of eight facilities from Burris Logistics (“Burris”), a temperature-controlled food distribution company. Financial terms of the transaction were not disclosed. The addition of these eight cold storage facilities to Lineage’s warehousing network will provide nearly 1.3 million square feet of capacity and approximately 115,000 pallet positions across facilities in Lakeland, Florida; Jacksonville, Florida; McDonough, Georgia; Edmond, Oklahoma; New Castle, Delaware; Waukesha, Wisconsin; and Federalsburg, Maryland. The transaction represents Lineage’s third proprietary deal with Burris. Lineage acquired both its Lyndhurst, Virginia and Haines City, Florida locations from Burris in 2020 and 2021, respectively. “This deal represents the trust we have built and the track record we have delivered across our longstanding relationship with Burris, which is demonstrative of Lineage being the industry’s acquiror of choice,” said Greg Lehmkuhl, President and CEO of Lineage. “As with our previous acquisitions from Burris, these complementary locations and their supremely dedicated team members will further fuel Lineage’s fierce customer-driven approach and serve our vision to become the world’s most dynamic temperature-controlled logistics company.” A nearly-century old, family-owned business, Burris has developed deep relationships with some of the nation’s leading retailers and foodservice companies. The acquired facilities are strategically located in the Eastern and Midwestern United States, near major highways and transportation hubs, and will serve densely populated markets to help Lineage’s direct-to-consumer fulfillment operation reach all 50 states. Lineage’s team has over 14 years of e-commerce and direct-to-consumer fulfillment experience, managing the end-to-end experience for more than 100 customers across eight existing locations. The acquisition of these facilities will bolster Lineage’s comprehensive direct-to-consumer solution that harnesses Lineage’s leading cold storage network. Burris’s remaining portfolio will primarily consist of Honor Foods, its foodservice redistribution company, and Trinity Logistics, its freight solutions provider.
Nucor launches campaign highlighting commitment to sustainable steelmaking
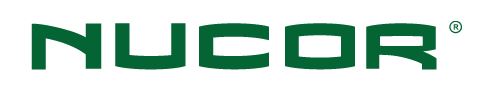
Nucor Corporation launched “Made for Good,” a campaign highlighting the company’s more than five decades of producing steel using the cleanest methods commercially available, while also showcasing its work with customers in a broad range of industries to help them achieve their sustainability goals and, at the same time, our nation’s sustainability goals. “Sustainability is being driven by our customers’ values and focus on reducing emissions in their supply chains. As a steel industry leader, Nucor recognizes the importance of environmental stewardship and continuously challenges ourselves to reduce our emissions even more. Through purposeful innovation, Nucor is providing not just steel but solutions that empower our customers to meet their business and environmental goals successfully,” said Dan Needham, Executive Vice President of Commercial at Nucor. Nucor is among the world’s most sustainable steel producers, annually making more than one-quarter of the steel produced in the United States. The company is a leading pioneer in using a circular, recycling-based manufacturing process with an emissions intensity that is more than three times lower than the average of extractive steelmaking methods using blast furnaces. Nucor is dedicated to further reducing its carbon footprint through innovation and was the first industrial company to join the UN 24/7 Carbon-Free Energy Compact, which is aimed at accelerating the decarbonization of the world’s electricity systems and ensuring access to clean and affordable electricity. “Made for Good” features the company’s recent achievements in sustainable innovations and invites customers, investors, and policymakers to partner with Nucor in tackling the challenge of decarbonization. The campaign’s highlighted case studies include Nucor’s investments in next generation technologies, such as small modular reactor (SMR) nuclear systems, fusion, Nucor’s involvement in reducing embodied carbon emissions in mass-market consumer vehicles, and Nucor’s own innovations, such as Elcyon, the first domestically produced sustainable steel product for offshore wind energy applications. “For more than 50 years, Nucor has been pioneering circular steelmaking and building a resilient and environmentally sustainable future. This campaign focuses on our dedication to building processes and investing in efficient systems that positively impact the world. The goal of Made for Good is to shape that sustainability narrative and uniquely capture Nucor’s position as an essential partner in constructing a greener tomorrow,” said Peter Campbell, Director of Marketing at Nucor. In addition to its sustainable steelmaking leadership, Nucor has engaged in policy conversations to accelerate greenhouse gas emission reductions within the industry. Nucor is a founding member of the Global Steel Climate Council (GSCC), which has developed the Steel Climate Standard – a single global standard to measure and report carbon emissions for steel companies in order to increase transparency and drive international investment in lower emission technology. Nucor partnered with Lippincott, a global creative consultancy, to generate the campaign and Luquire, a marketing and PR agency, to place the media. To explore the campaign, visit Nucor.com/madeforgood. Learn more about Nucor’s commitment to sustainability there and follow the conversation on LinkedIn and Instagram.