Hai Robotics launches new solutions aimed to heighten Warehouse Storage Density and real-time efficiency
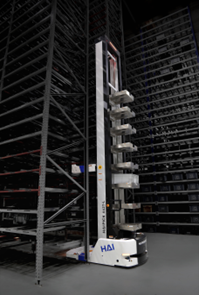
Hai Robotics (“Hai”), pioneer and provider in Autonomous Case-handling Robot (ACR) Systems, has announced the launch of the world’s first telescopic Grapple Hook ACR, the HaiPick A42T-E2, and the HaiPick System 3—two new innovations that address customer concerns around increasing storage density and performance at a smaller warehouse footprint. The telescopic Grapple Hook ACR can be integrated within HaiPick System 3, creating a nexus that facilitates higher performance while delivering enhanced storage density. The HaiPick A42T-E2—equipped with ChainPick technology—features a grappling hook with a picking speed of 2.7 seconds, quickly pulling totes one after another. Such ChainPick technology is key to enabling up to five-deep tote storage capacity, allowing shorter picking and placing time to further streamline the goods-to-person workflow. Horizontal space in between totes can be slashed by 60%, ensuring no space gap at the back and hence optimizing existing warehouse storage space. Businesses are also offered tailored solutions to scale up or down, allowing them to maintain a competitive edge without compromising on financial agility, while still achieving cost-efficiency. “Businesses nowadays are struggling to not only optimize their warehouse space, but also strike a balance between automation and leaving room for growth,” said Peter Guan, General Manager at Hai Robotics EMEA. “We are thrilled with the launch of the HaiPick A42T-E2. This project encapsulates our commitment to providing intelligent, flexible and efficient solutions for the modern warehousing industry, while keeping in mind the growing and dynamic needs of this market on a global scale.” The HaiPick System 3, on the other hand, is the latest solution in Hai’s portfolio, enabling ultra-high storage density up to 50 totes/㎡ and increasing worker efficiency up to six times. HaiPick System 3 is a highly standardized system incorporating Hai’s telescopic Grapple Hook ACRs and Fast-transit K50 autonomous mobile robots (AMR) running at a speed of 4m/s. HaiPick System 3 introduces fast deployment and efficient ACR-AMR collaboration: While ACRs handle totes from the top to the bottom of the racks, AMRs handle rack-bottom totes between racks and workstation swiftly. Additionally, the solution facilitates rack expansion by up to five-deep configuration, by using the telescopic Grapple Hook ACR, with a maximum picking height of up to 10 meters. “HaiPick System 3 is a high-performance and agile solution that scales alongside businesses to better achieve instantaneous customer satisfaction,” added Guan. “Combined with the telescopic Grapple Hook ACR, warehouses will be able to achieve a level of performance efficiency and ROI at new heights in both B2B and B2C operations, such as within 3PL and apparel industries.” Davide Tuzi, Country Manager of Italy at Hai Robotics, will discuss more details in the upcoming episode of HaiPulse webinar. The special edition, scheduled to air on October 20th, at 9:30 AM (CET), will cover an in-depth analysis of these two innovations. Sign up for this webinar here.
The Council of Supply Chain Management Professionals (CSCMP) announced the 2023 Supply Chain Hall of Fame Inductees
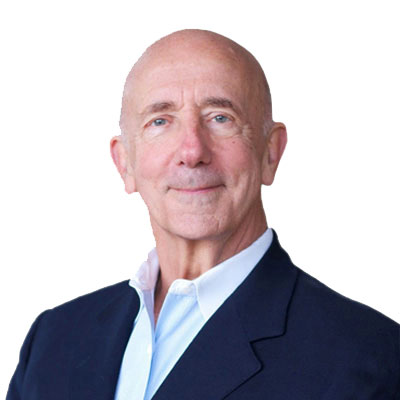
The Council of Supply Chain Management Professionals (CSCMP) names Lynn Fritz, Chairman and CEO of Fritz Companies as the 2023 Supply Chain Hall of Fame Inductee. The CSCMP Hall of Fame was first initiated in 2016 to recognize individuals for having made outstanding contributions to the supply chain discipline and served as role models to supply chain students, young professionals, budding entrepreneurs and career supply chain professionals. Since its inception, each of the Distinguished Service Award past winners were inducted into the Hall of Fame and all future DSA recipients will automatically be inducted each year. As such, the 2023 CSCMP Distinguished Service Award Recipient, Ted Stank, joins Lynn in receiving the Hall of Fame honor. A visionary in the global logistics industry, Lynn helped develop and operationalize the concepts of third-party logistics and supply chain services during his 30-year career as Chairman and CEO of Fritz Companies, Inc., which enabled this small San Francisco customs brokerage company to expand to 120 countries and 11,000 employees. The company went public in 1992 and achieved Fortune 1000 status in 1997. His enduring contribution redefined a fragmented and limited services industry through the use of technology. Upon UPS’s acquisition of Fritz Companies in 2001, Inc., Lynn shifted professional gears, dedicating the Fritz Institute to the development and deployment of logistics expertise to the global Humanitarian Sector. Lynn partnered with his wife, Business Professor, Dr. Anisya Thomas, and resolved to be the advocate for humanitarian logisticians, bring academic expertise and private sector resources and best practices to their endeavors. He invested significant financial resources and devoted a majority of his time partnering with a broad array of institutions and individuals in the creation of a field now recognized as humanitarian logistics. The software developed by Fritz Institute, used to track the delivery of necessary relief items, is utilized by the International Federation of Red Cross and Red Crescent Societies, Oxfam, Save the Children U.K. and World Vision. The Institute’s certified training programs and curriculum is the lynchpin of humanitarian logistics operational trading and benefits hundreds of relief logisticians and organizations, while Fritz Institute standards are being utilized in over 25 countries in Africa. Once the Fritz Institute was successfully underway, Lynn founded LynnCo Supply Chain Solutions, headquartered in Oklahoma, a compact technology driven new age domestic forwarding company. Simultaneously over the years, he had begun to appreciate the exceptional potential of a ranch he had purchased in 1980. Although originally intended as a family retreat, slowly over the ensuing 40 years it has become one of California’s leading ultra-premium wineries. CSCMP’s EDGE Conference is supply chain’s premier event™ and provides the finest networking and robust educational experiences unmatched by others in the industry.
KPI Solutions appoints Roger Counihan as Senior Vice President of Sales
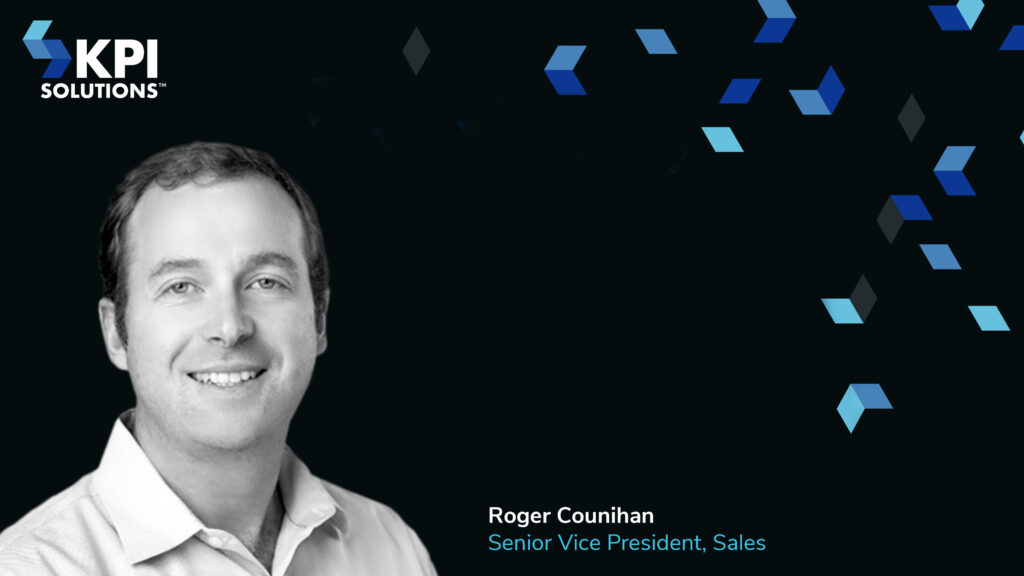
KPI Solutions (KPI), a provider in supply chain consulting, software, automation, and systems integration, today announced that Roger Counihan has joined the company as Senior Vice President, of Sales. In this role, Roger will provide strategic leadership to drive growth by delivering successful solutions that help clients reduce labor dependence, increase productivity, and build scalability. “I’m excited to join KPI Solutions as our team designs and integrates new processes coupled with world-class automation technology that supports our clients’ operational transformation,” said Roger. “Developing creative, bespoke solutions for clients is a passion and I look forward to leveraging my experience in supply chain strategy, distribution center design, robotics, and software to help clients meet today’s business challenges.” “We are happy to welcome Roger to the KPI Commercial team as another seasoned, highly skilled leader for our clients as they seek options to elevate performance,” said Ron Adams, Chief Commercial Officer at KPI. “Roger’s ability to quickly grasp business challenges and address them with innovative operational designs and high-performing technologies will create scalable, resilient, and agile automation solutions for our clients.” Most recently, Roger served as Chief Revenue Officer at CognitOps, a supply chain software services firm. Prior, he rapidly rose through positions of increasing responsibility in both sales and delivery roles at Fortna, global telecommunications provider Brightstar, and Capgemini. He holds a B.S. and M.S., Systems Engineering from the University of Virginia and resides in Atlanta.
Women In Trucking Association announces Sarah Smith of Penske Transportation Solutions as Vice Chair
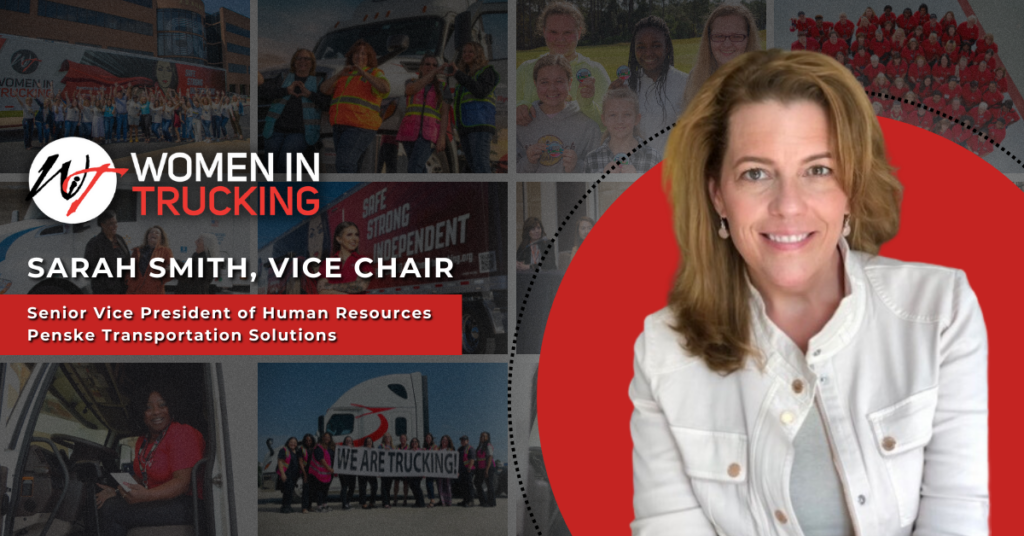
The Women In Trucking Association (WIT) has announced Sarah Smith as vice chair of the association. In this role, Smith will collaborate with WIT’s officers, board of directors, and staff to guide the association’s mission of encouraging the employment of women in the industry, minimizing obstacles they face, and promoting their accomplishments. Along with this volunteer leadership role, Smith is senior vice president of human resources for Penske Transportation Solutions. “We are extremely pleased to have Sarah in this leadership role as she brings a depth of experience that will be invaluable to the association,” said Jennifer Hedrick, president and CEO of WIT. In her current position at Penske, Smith leads teams responsible for corporate and field human resources as well as diversity and inclusion. Throughout her career, she has held several other roles with Penske, including director of labor relations and vice president, human resources operations. Additionally, Smith spent time in private practice as an attorney. She has a Bachelor of Arts degree in French from Wilkes University as well as her Juris Doctor degree from John Marshall Law School in Chicago, Il. “It’s an honor to hold a leadership position on the Women In Trucking Board of Directors,” said Smith. “Women In Trucking is the leading organization supporting women in transportation and encouraging more to join our strong industry. To contribute to that mission is professionally and personally rewarding to me. I believe that there is a tremendous opportunity for women in trucking and that my association with WIT demonstrates Penske’s commitment to diversity and inclusion for our association. I look forward to the impactful work that lies ahead.”
Women In Trucking Association announces its October 2023 Member of the Month
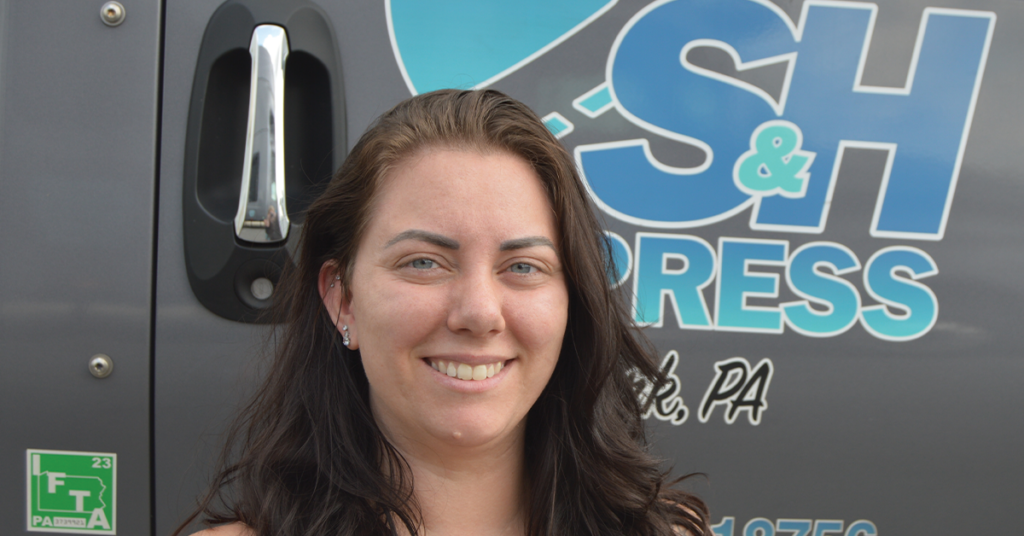
The Women In Trucking Association (WIT) has announced Lauren Keeney as its October 2023 Member of the Month. Keeney is a regional driver from S&H Express, Inc. based in York, PA. Keeney was inspired to earn her CDL while waiting at a traffic light. As she finished making Amazon deliveries for the day, she glanced at the tractor trailer beside her and saw a woman was behind the wheel. “I realized that if she could do it, I could too,” said Kenney. Shortly after, Lauren enrolled at the Shelly Truck Driving School in York, PA. Training Supervisor Bob Grimaldi remembers Lauren as someone who always in high spirits and quick to master even the most complicated material. “Lauren never shied away from a new challenge and never settled for good enough,” said Grimaldi, who has closely followed her career at S&H Express which is affiliated with Shelly Truck Driving School. “She wanted to be the best she could be, and she worked with her classmates to help them reach the same level.” S&H Express Recruiting Manager Andrea Whipple has known Lauren since they were teens working together at Tom’s Gas Station and says, “Lauren has always been a hard worker. Even as a kid, she strived to do better. She has one of the biggest hearts and would help anyone out, whenever.” Lauren’s desire to help others and her drive to succeed continues. In September 2021, after earning her CDL, Keeney signed with S&H Express. She has recently begun to train new drivers and is earning rave reviews. Last year, Dispatcher Tina Bailey assigned Keeney to an important dedicated account in Richmond, VA and Keeney has achieved 100% on-time service for the customer. “What is notable is that this is a five-times-per week York, PA to Richmond, VA run to a very difficult, very tight dock location,” said Bailey. “It’s a location that many other drivers have refused after their first run. Not Lauren, and she is always willing to help other drivers, even from other companies, who are having trouble backing into that customer location.” S&H Express Director of Operations Doug Forry adds, “Lauren has a bright future in trucking. She’s smart, determined, and always willing to go above and beyond in this male-populated industry. She is one of a kind!” Keeney’s advice for anyone who is thinking about trucking as a career, especially women, is to do their research stating, “talk to the director of a reputable school, ask to talk with a few of their graduates, and call the recruiting department of a small, large, and mega trucking company. Interview them and a few of their female drivers so that you can make an informed decision for yourself.” Further showcasing her love for the road, Keeney enjoys travel. Her York to Richmond assignment affords lots of opportunities to appreciate beautiful scenery and take note of sites that would be great for vacation.
Episode 424: Addressing testing challenges by implementing testing automation in the supply chain industry with Cycle Labs
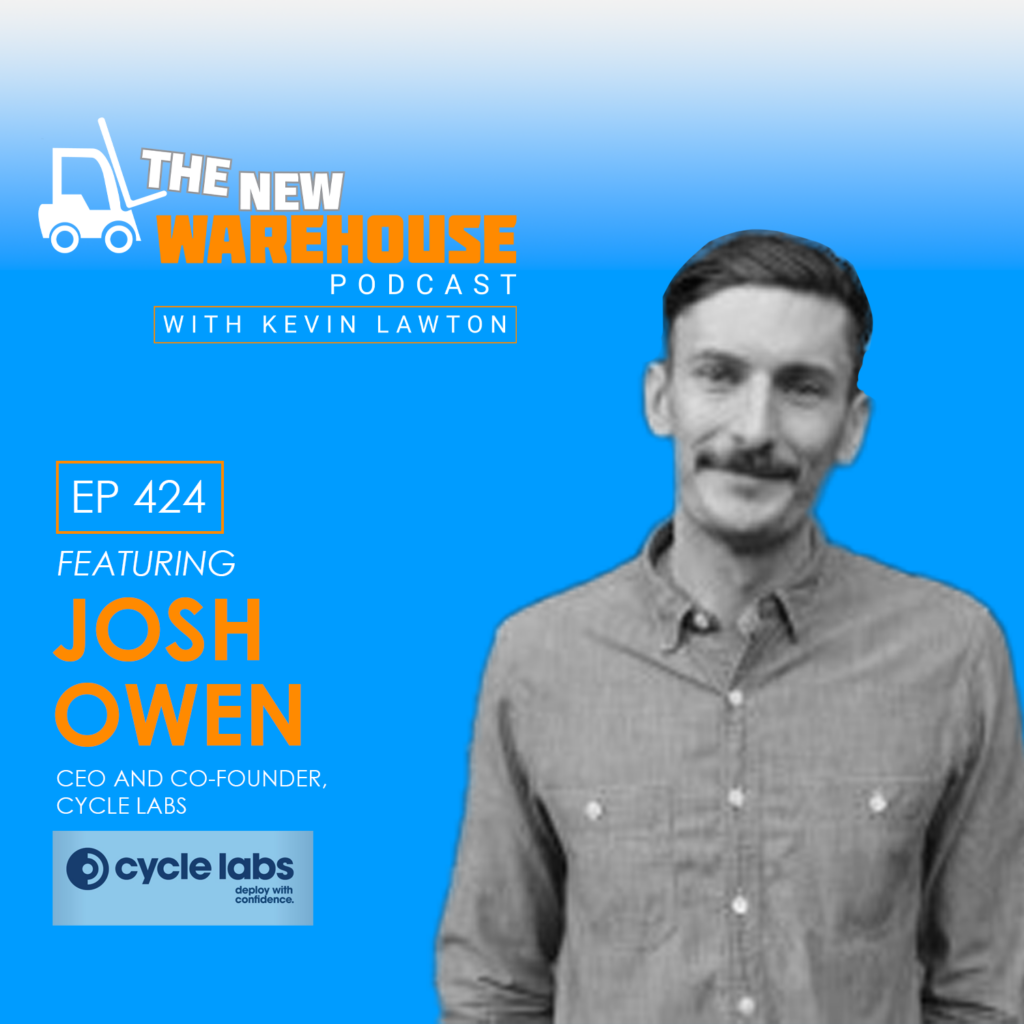
In this episode of The New Warehouse Podcast, we had the pleasure of speaking with Josh Owen, the Co-Founder and CEO of Cycle Labs, a company dedicated to revolutionizing testing in the warehousing industry. Cycle Labs is at the forefront of revolutionizing warehouse testing. By embracing automation and efficient testing, businesses can overcome the challenges of system upgrades and thrive in an environment that demands adaptability and innovation. Join us as we delve into how Cycle Labs is making waves in warehouse testing, helping businesses overcome their fears and anxieties regarding system upgrades and enabling them to thrive in this ever-evolving field. The Challenges of System Upgrades in Warehousing With his extensive experience in supply chain technology, Josh Owen recognizes the challenges that warehousing professionals face regarding system upgrades. He highlights, “Taking something as complicated as a warehouse management system and putting it into production can be trying times.” Manual testing, late nights, and weekend work become the norm, leading to burnout and increased risk. However, Josh emphasized that this is not a unique problem; many organizations share these challenges. It’s essential to understand that innovative solutions like Cycle Labs have addressed and solved these issues. The Role of Automation in Testing Josh stressed how Cycle Labs helps clients automate various testing scenarios, from regression testing during system upgrades to ongoing validation of critical processes. “We give our clients the ability to focus on the things that improve those projects and solve some of those challenges by giving them their time back.” In this light, automation is transforming the way warehouse testing is approached, making it more efficient and less resource-intensive. Josh’s insights convey how businesses can benefit from this approach and allocate their resources more strategically. The Impact of Testing Automation on the Warehousing Ecosystem By addressing the challenges of system upgrades and testing, Cycle Labs helps create smoother, more predictable relationships between systems integrators and their clients. Cycle Labs’ approach can lead to more frequent system upgrades, enhancing the overall competitiveness of warehousing businesses. Efficient testing can have a ripple effect, from fostering better relationships with OEMs to enabling businesses to embrace change and innovation. Key Takeaways on Testing Automation Efficient Testing Eases System Upgrades: Automation in testing alleviates the anxiety and resource drain associated with system upgrades. It allows businesses to confidently approach changes, knowing their critical processes are validated and error-free. Resource Allocation and Collaboration: By automating testing, businesses can allocate their resources more strategically, reducing the pressure on employees who would otherwise spend weekends testing. Collaboration between different stakeholders in the warehousing ecosystem becomes smoother and more predictable. Embracing Change and Innovation: Frequent system upgrades become more achievable, enabling businesses to adapt to the ever-changing warehousing landscape. This mindset shift can help organizations experiment, innovate, and stay competitive. The New Warehouse Podcast EP 424: Addressing Testing Challenges by Implementing Testing Automation in the Supply Chain Industry with Cycle Labs
Mitsubishi Logisnext Americas hosts “Formula For Success” event celebrating record year of achievements
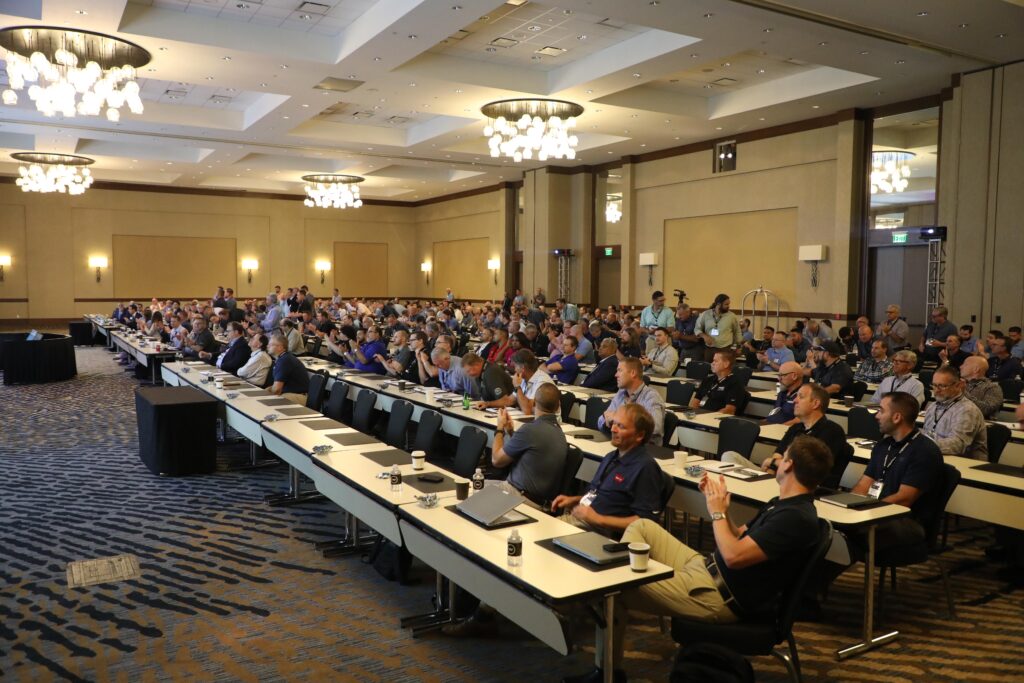
Mitsubishi Logisnext Americas (Logisnext), a North American provider and manufacturer of material handling and innovative automation and fleet solutions, held its Logisnext Dealer General Manager Meeting in Houston this week for the Cat® lift trucks, Mitsubishi forklift trucks and Jungheinrich® dealer network. During the significant two-day event, Logisnext showcased its “Formula For Success” strategy and future plans as the industry moves toward electrification, automation and digitalization. Nearly 300 attendees gathered, including Dealer Principals and top-level management from across Logisnext’s North American Cat lift trucks, Mitsubishi forklift trucks and Jungheinrich dealer network. Special guests included Formula 1 World Champion and Jungheinrich Brand Ambassador Nico Rosberg, alongside Christian Erlach, Member of the Board of Management, Sales at Jungheinrich AG. At the heart of the event was the unveiling of a forward-looking roadmap, which highlighted a focus on sustainability and advanced technology across automation, telematics and advanced power solutions to meet evolving market demands. Nico Rosberg engaged with attendees and shared his passion for advancing electric mobility and sustainability. As an entrepreneur and advocate for these causes, Nico pushes the boundary in support of innovation and advancement of green technologies. “I am dedicated to advancing green innovation, with a clear focus on accelerating sustainability through electrification,” said Nico Rosberg, Formula 1 World Champion and Jungheinrich Brand Ambassador. “I’m inspired to work alongside partners like Jungheinrich and Mitsubishi Logisnext Americas, who are driven to deliver advanced technologies and new solutions to power the material handling industry into the future.” Day One: Celebrating Record-Breaking Growth During the event, Logisnext and its dealers aligned on strategic plans and celebrated the shared achievement of new historic milestones in electric market share growth and its resilience and adaptability in the changing post-COVID landscape. “Mitsubishi Logisnext Americas is heavily investing in the future with our dealers and strategic partner Jungheinrich,” said Jerry Sytsma, Executive Vice President, Sales and Aftermarket Services at Mitsubishi Logisnext Americas. “The industry is continuing to evolve – with electrification, automation and digitalization – and we’re proud to be partnering with our dealers to bring forward the latest solutions to customers across North America.” The day concluded with a compelling Q&A session featuring Rosberg and Christian Erlach, led by Sytsma at Mitsubishi Logisnext Americas. Day Two: Customer Event with Equipment Depot The celebration continued with a Customer Event dedicated to Jungheinrich customers and employees of Equipment Depot, one of Mitsubishi Logisnext Americas’ local Jungheinrich dealers. More than 100 attendees joined the event, which featured an exclusive interview with Rosberg hosted by Anthony Garcia, President of Equipment Depot. About Nico Rosberg Nico Rosberg was born in 1985 in Wiesbaden, Germany, the son of Formula One™ World Champion Keke Rosberg. Nico raced in F1 for eleven years and claimed the title of World Champion in 2016. Since his retirement from Formula One, he has embarked on a career as a sustainability entrepreneur and investor in green technologies and mobility start-ups. Based in Monaco, his team manages a large number of projects with the support of a dedicated team of international experts in Monaco, Great Britain and Germany. Rosberg has invested in numerous successful start-ups such as Lilium, Volocopter, What3Words, Tier and Formula E. In 2018, Rosberg was recognized for his commitment to sustainable innovation with the “GreenTec Entrepreneur of the Year” environmental award. A year later, he founded the GREENTECH FESTIVAL, a global platform for leading green technologies and a sustainable lifestyle. In 2020, Rosberg founded Rosberg X Racing to compete in Extreme E, a race series that highlights the impact of climate change and promotes the adoption of electric vehicles in the quest for a lower carbon future for the planet.
Equipment Depot’s management team sets revenue goal of a billion dollars within five years
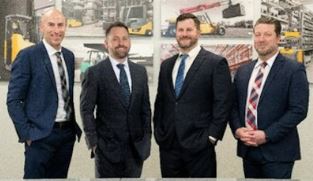
Equipment Depot said it is on track to meet its aggressive financial growth goal: to reach a billion dollars in revenue within five years. In 2020, Equipment Depot’s leadership began analyzing how the organization approached the material handling business. As a result, the team created its “2025 Vision Strategy”, which included investment in strategic hires, expansion into key U.S. material handling markets, extensive employee advancement training, and the creation of two new divisions: EQSolutions and Heavy Trucks & Port Equipment. The new divisions are cited as significant factors contributing to the company’s growth. As the company prepared for growth, top leadership positions began to evolve. Anthony Garcia, former regional vice president of the company’s South Region, was appointed president, succeeding president and CEO, David O. Turner. Garcia takes on this role after a strong showing as regional vice president of Mammoet Americas, a Dutch heavy lifting and transportation service company. Jonathan Hesener advanced from vice president of sales and customer experience to chief sales officer. Hugh Parry went from vice president of operations to chief operating officer – both recognized for their military leadership experience and involvement in General Electric’s well-recognized Leadership Program for former military officers. Clint McNair was tapped as the company’s new chief financial officer. McNair has 22 years at Deloitte and experience in the private equity sector — and is recognized for his strategic thinking and fresh perspective on aligning finance and operations. EQ Solutions, launched in 2019, specializes in engineering transformative warehouse and automation solutions for manufacturing, warehousing, and distribution facilities. This allows Equipment Depot to fill an industry shortcoming — by providing the first fully end-to-end, one-source solution to help customers solve various challenges within one department, the company said. Over the past five years, Equipment Depot has expanded into several new markets. It opened a new location in Los Angeles on the West Coast in 2021, acquired Norlift in Portland, Ore., and opened a new branch in Seattle, representing the newly formed Northwest region. “This expansion now covers seven of the top 10 U.S. material handling marets,” Hesener noted. “Equipment Depot is on an incredible trajectory. I’m pleased to be part of the pendulum shift at the company and within the material handling industry.” “From our leading-edge advancements in warehousing to bespoke automated and energy transition solutions, together with our exceptional service and emerging digital advancements, Equipment Depot is definitely becoming the envy of the industry,” said McNair. “Equipment Depot has the right ‘playbook’ to hit our billion-dollar revenue target,” added Parry. “For instance, our partnership with Mitsubishi Logisnext allows direct access to the manufacturing plant for Cat Lift Trucks, Mitsubishi, Jungheinrich, and UniCarriers Forklifts, providing an incredible benefit and relief to customers facing equipment supply chain challenges. Additionally, we have secured strategic OEM partners in the port and heavy equipment industry, and are introducing new technologies, such as robotics and automation, which are making a quantum leap in the material handling industry.” “I am proud and honored to continue Equipment Depot’s growth plans,” said Garcia. With the industry advancing at an incredible rate, from how automation, electrification, robotics, and AI are playing a role, there is huge potential to reshape the landscape — I envision Equipment Depot being at the forefront.”
Alta Equipment Group to acquire Burris Equipment adding to its Construction Business segment

Expands product portfolio and presence in the Illinois market Burris’s $40.6 million in revenue, $1.9 million in net income, $4.6 million in EBITDA on a trailing twelve-month basis is expected to be immediately accretive to the Company’s leverage, profitability, and earnings per share ratios Alta Equipment Group Inc. has announced that it has entered into a definitive agreement to acquire Burris Equipment Company (“Burris”), a supplier of construction and turf equipment with three locations in Illinois. “The acquisition of Burris will not only yield immediately accretive returns to shareholders but will also notably enhance our business in Illinois,” said Ryan Greenawalt, Chief Executive Officer of Alta. “In addition to adding important infrastructure and industry talent to the Chicago area in our Construction Equipment segment, we also eagerly embrace new OEM relationships stemming from the Burris acquisition, while simultaneously expanding with existing OEM partners to best serve Burris customers. This acquisition will fortify our product support presence and rental capabilities in the market, opening doors for the growth of our high-margin parts and service business. We extend a warm welcome to the Burris team as they become part of the Alta family.” Strategic and Financial Highlights Diversifies product portfolio and end markets in the Chicago area and expands Alta’s infrastructure in the region with three new branches in Joliet, Waukegan and Lakemoor. Burris generated approximately $40.6 million in revenue, $1.9 million in net income and EBITDA of $4.6 million for the trailing twelve-month period through July 2023. Deal is structured as an asset acquisition allowing for step-up in tax basis of assets acquired. Additional Transaction Details The purchase price is $14.0 million in cash, subject to working capital adjustments. The transaction is subject to customary closing conditions and is expected to close in the fourth quarter of 2023. Including Burris, since the Company’s initial public offering in 2020, Alta has completed 15 acquisitions which have contributed $487 million in revenue, and $58 million in Adjusted EBITDA. More information on Burris, its products and applications can be found at https://burrisequipment.com/home.
Toyota Material Handling launches new Electric Pneumatic Forklifts
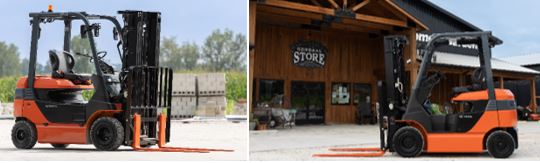
New electric models come with lift capacities ranging from 3,000 to 7,000 lbs. and deliver dependable power for outdoor applications Toyota Material Handling is launching a new line of electric pneumatic forklifts with 48V and 80V models. This durable line is built to withstand outdoor terrain and work in various weather conditions, making them ideal for retail applications such as lumberyards, home centers, landscaping, and store support applications. “Our goal at Toyota is to embrace the spirit of Kaizen – or continuous improvement – in everything we do and every product we offer,” said Tony Miller, Toyota Material Handling Senior Vice President of Engineering, Operations and Strategic Planning. “These new 48V and 80V electric pneumatic forklifts set a new standard in quality material handling solutions, helping elevate work efficiency for operators with the integration of cutting-edge technologies and versatility across a wide range of tasks and terrains.” These new models, featuring six different lift capacities ranging from 3,000 to 7,000 pounds, offer cost-effective and reliable solutions for end-users. Toyota’s innovative System of Active Stability (SAS) springs into action when operators encounter unanticipated loads and speed conditions. Additionally, Toyota’s Operator Presence Sensing System (OPSS) along with the optional Seatbelt Interlock Encourages operators to maintain a properly seated position with the seatbelt buckled or travel and load handling operations will be limited. Built with standard AC drive and lift motors, along with significantly lower noise and vibration levels this forklift provides a smooth operation. The regenerative braking system adjusts the speed of the truck when the operator’s foot is removed from the accelerator and conserves energy when speeds begin to slow by returning energy to the battery, increasing operational time, and improving the overall efficiency of the forklift. An optional Slope Assist feature maintains the speed of the forklift on a slope by switching the power mode of the truck. The load-sensing power steering capabilities provide smooth handling operation for operators, while also keeping more power in the battery. In addition to the industry-leading lineup of material handling solutions, the new 48V and 80V electric pneumatic forklifts provide customers with superior performance options while maintaining energy efficiency.
What’s sinking your employee’s wellbeing? Five Titanic lessons for leaders to keep their crew afloat
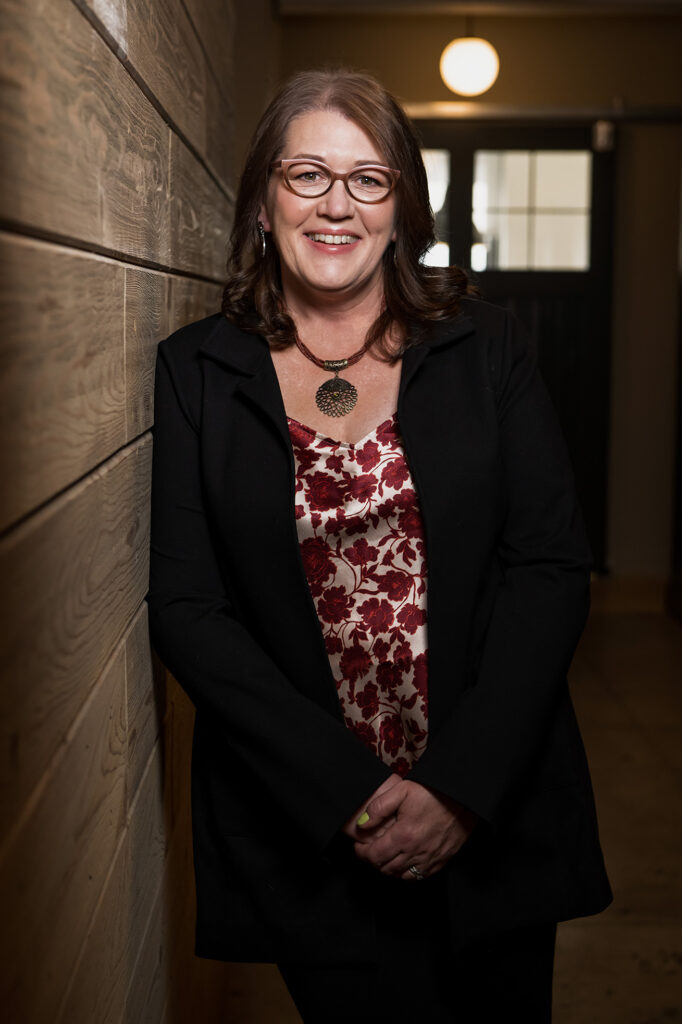
The sinking of the Titanic stands as a tragic and haunting reminder of human fallibility. And, surprisingly, the parallels between the Titanic disaster and today’s workplace wellbeing cultures are striking. The Titanic, once deemed “unsinkable,” faced unforeseen challenges, inadequate preparation, and communication breakdowns – all factors that bear an uncanny resemblance to issues plaguing today’s workplaces. The correlation demonstrates that critical aspects of employee wellbeing, such as mental health, communication, and a feeling of psychological safety, impact the business’ management of risk, profitability and productivity no matter what the situation. This article embarks on a journey to unravel the synergy between the Titanic’s tragic narrative and the intricate tapestry of workplace culture to shed light on valuable lessons that can be applied to foster healthier, more resilient, and safer work environments. So, let’s explore the correlation between history’s most infamous shipwreck and the ever-evolving landscape of workplace wellness. Lack of Vision (mental health): The Titanic had binoculars hidden away in a locked cabinet. Yet, these crucial tools remained untouched throughout the voyage. The reason? A lack of confidence and the fear of consequences, because the ship was brand new, prevented the crew from breaking the glass cabinet to access them. Not feeling empowered to make the decision left them with severely limited vision, so they didn’t see the iceberg until it was too late. Just as the Titanic’s fate could have been different with better vision, business leaders today should heed this lesson and equip their talent with the necessary tools and insights to ensure forward vision and the confidence to take action. It’s not enough to thrive in the present; leaders must prepare for the future, recognizing that mental wellbeing directly impacts productivity, which directly impacts profits. This proactive approach guarantees that wellbeing programs and benefits remain effective and adaptable, capable of meeting the ever-evolving demands of the modern workplace. Communication Breakdown (setting expectations): Just as poor communication protocols and delayed response played significant roles in the Titanic disaster, within an organization, they can have a ripple effect that deteriorates the workplace culture. In the absence of clear communication channels, information isn’t adequately disseminated and feedback mechanisms fail, so employees’ access to vital support and resources become compromised. This, can lead to a decline in overall productivity. Much like the Titanic crew needed clear communication protocols to navigate expectations and obstacles, modern organizations must foster an environment of open and honest communication, where expectations are well-defined and readily accessible so employees can be fully engaged and effectively address the evolving demands of today’s workplace. In doing so, leaders not only enhance employee satisfaction, mental health, and productivity but also safeguard their profits from potential disasters on the horizon. Neglecting warning signs (leadership): The Titanic received several warnings about icebergs in its path, which were not adequately heeded because they prioritized sending messages for the first-class passengers. Similarly, poor workplace cultures may neglect warning signs of employee distress, such as high attrition, increased absenteeism, or declining productivity because it is focusing attention in the wrong areas. When leadership fails to recognize and address these signals, the repercussions can be profound, impacting employee satisfaction and overall wellbeing which can lead to disengagement. By actively recognizing and addressing signs of employee distress, they not only enhance well-being but also safeguard the overall health and success of the organization. In this era where leadership and employee wellbeing are intrinsically linked, astute and empathetic leadership can make all the difference. Inadequate planning (crisis/risk management): The Titanic’s sinking was partly attributed to insufficient planning and failure to account for potential risks, such as ICEBERG COLLISIONS! Inadequate workplace wellbeing programs often stem from a lack of strategic planning and risk assessment. Neglecting to anticipate and address employee wellbeing issues can set the stage for increased stress, burnout, disengagement, and physical and mental illnesses which increases the risk of attrition, injuries, employee driven lawsuits, costly mistakes, and eventually customer dissatisfaction. The Titanic serves as a sobering reminder that crisis and risk management are essential. Organizations can proactively identify and mitigate risks by safeguarding not only the health and happiness of their workforce but also their own stability and success in an ever-changing and challenging business environment. In this era where wellbeing and risk management are intertwined, foresight and preparedness can make all the difference. Insufficient resources and support (profits): The Titanic was designed with limited lifeboats, a short-sighted and arrogant approach that prioritized profits over passenger safety. Similarly, inadequate resources and support allocated to workplace wellbeing programs can hinder their effectiveness. When organizations cut corners with insufficient funding, lack of dedicated staff, or inadequate training, they risk limiting the program’s ability to address the pressing needs of their employees. In today’s workplace landscape, organizations must recognize that investing in comprehensive programs not only benefits their employees but also contributes to their long-term prosperity. Organizations must understand that neglecting employee well-being can lead to negative outcomes, impacting both their people and their bottom line. A holistic and comprehensive commitment to employee welfare is a wise and forward-thinking strategy that ensures lasting success and sustainability. Conclusion The parallels drawn between the Titanic disaster and the realm of workplace culture underscore critical lessons for organizations striving for success. The Titanic’s tragic fate, serves as a stark reminder of the importance of proactive strategies and resource allocation in safeguarding the wellbeing of the business and its employees so they can navigate the complex waters of today’s business world with confidence and resilience. By addressing risks, providing ample resources, and staying attuned to warning signs, creating robust wellbeing programs with effective communication and a vision for adaptability are the essential tools in navigating the complex waters of today’s ever-evolving workplace. So, don’t make the titanic error of neglecting workplace wellbeing as a “nice to have” initiative. Instead, chart a course towards a healthier, more prosperous and resilient future by prioritizing the wellbeing of your organization’s greatest asset—its employees. About the Author Diane O’Connell is an author, speaker, coach, workplace culture reinvention
ASSP president will help dedicate Triangle Fire Memorial
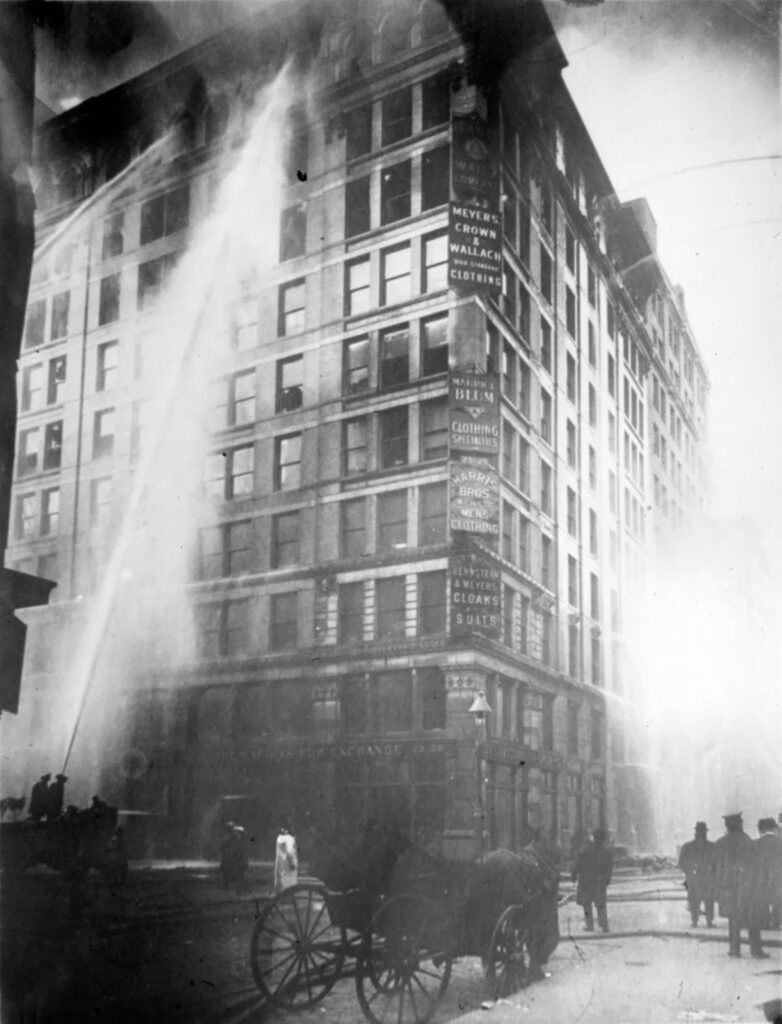
The American Society of Safety Professionals (ASSP) is anchored to the Triangle Shirtwaist Factory fire that killed 146 garment workers in New York City more than 100 years ago. ASSP President Jim Thornton will join Acting Secretary of Labor Julie Su, New York Governor Kathy Hochul and other dignitaries in honoring those workers on Oct. 11 when a memorial is dedicated at the original building in Manhattan. The event will take place from 11:30 a.m. to 1 p.m. ET. The Triangle fire revealed great negligence in worker safety when the tragedy occurred on March 25, 1911. A few months later came the creation of the United Association of Casualty Inspectors, now known as ASSP, the world’s oldest professional safety organization. “The memorial will stand as a symbol to forever remember our nation’s legacy of reform while paying tribute to the workers who died,” said Thornton, CSP, CIH, FASSP, FAIHA. “It’s a significant achievement by the Remember the Triangle Fire Coalition, whose members worked tirelessly over the past decade to bring the project to fruition.” The main body of the stainless-steel memorial is on a corner of the Brown Building at Washington Place and Greene Street, resembling a ribbon that descends from the 9th floor where most deaths occurred. It evokes the appearance of mourning ribbons that were draped on buildings in times of public grief. Twelve feet above the sidewalk, the memorial splits horizontally to flank the building’s facades, where the names and ages of the victims are stenciled into the ribbon and appear in a reflective panel at street level. ASSP contributed $32,519.11 to the memorial’s construction, connecting the seven digits of the fire’s date (3/25/1911) to emphasize the significant moment in U.S. history. The ASSP Foundation donated an additional $25,000 to the project. Both names will be listed on a donor plaque affixed to the building near the memorial. “The Triangle fire inspired our country to address workplace safety in an organized way that didn’t previously exist,” Thornton said. “The horrific incident led to a series of laws and regulations that better protected workers. And ASSP continues to advance worker safety and health to this day.” During the Triangle disaster, fire exit doors were locked and other doors only opened inward, making it impossible for the onrush of workers to get out. The fire escape was poorly constructed and didn’t meet weight requirements. Fire department ladders couldn’t reach the upper floors of the 10-story building. Many workers died by jumping out of windows and into an elevator shaft as they tried to escape the flames. From its inception on Oct. 14, 1911, ASSP has grown into a global membership organization of more than 35,000 occupational safety and health professionals whose efforts reduce workplace injuries, illnesses and fatalities. But the work of safety organizations, employers and federal agencies is never complete. According to the U.S. Bureau of Labor Statistics, more than 5,000 people were fatally injured on the job in 2021. “We have always championed the need to protect workers because safety, health and well-being are inherent rights of every worker,” Thornton said. “History must continue to motivate us to do better. It takes all of us working together to make sure that tragedies like the Triangle fire never happen again.” Find more information about the Triangle Fire Memorial and the upcoming dedication ceremony on the Remember the Triangle Fire Coalition’s website at rememberthetrianglefire.org.
UgoWork introduces UgoPilot: Transforming energy management and battery intelligence for industrial trucks
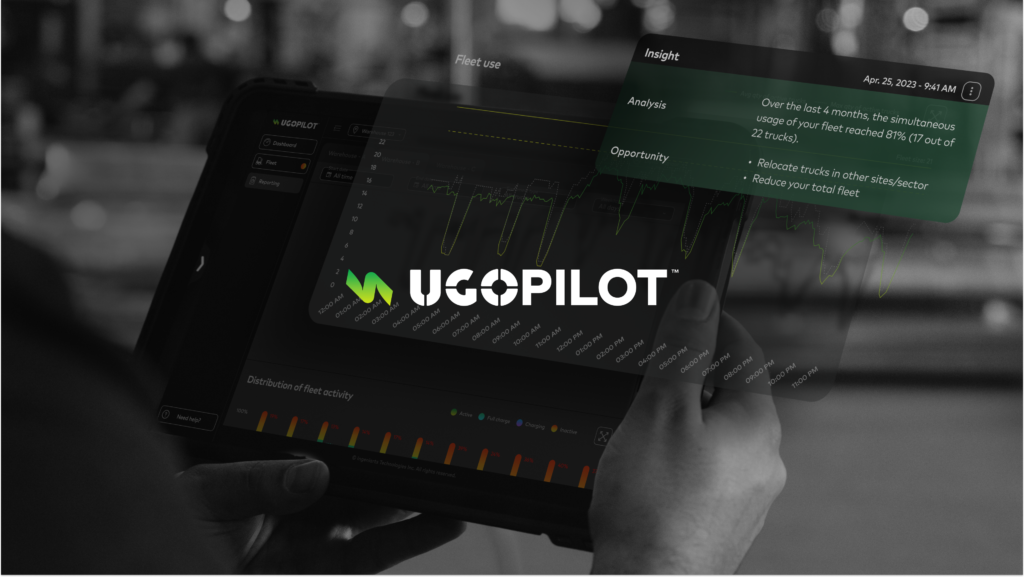
Innovative software platform enhances fleet performance, operator safety, and sustainability UgoWork™, a Canadian lithium-ion energy solutions provider specialized in the material handling industry, is proud to introduce UgoPilot™, an innovative energy and battery intelligence management platform designed exclusively for industrial vehicle fleets. With a focus on real-time insights and data-driven decision-making, UgoPilot heralds a new era in energy management, empowering organizations to maximize fleet efficiency while prioritizing performance, safety, and sustainability. “We’ve cultivated intelligence and harnessed our energy expertise through meticulous data collection from our cloud-connected batteries since Day 1,” said Philippe Beauchamp, president and CEO of UgoWork. “Today’s industry is shifting towards high performance products to meet safety, productivity and sustainability goals. The UgoPilot software suite is all about providing clarity. It generates the data-driven insights operations managers need to maximize the use of their fleets and enter into a new era of energy management that truly reduces carbon footprint and costs. Thanks to UgoPilot, batteries are not just black boxes anymore.” Pioneering fleet management transformation Capitalizing on proven field results, UgoPilot will unlock multiple opportunities that include: Secure: Safe and efficient equipment operation through real-time data Reduce: Comprehensive fleet data to confidently eliminate underused equipment Optimize: Predictive analytics to maximize fleet throughput and asset life Support: Instant access to energy experts dedicated to helping you boost operational performance and achieve your mission-critical KPIs A better battery is just the start Beta testers are already praising UgoPilot as a game-changer for the industry. An early adopter of UgoWork solutions and beta tester operating one of the largest 3PL operations in Canada shared, “UgoPilot’s analysis of raw data provides insight that translates into action. Its prioritized features such as real-time fleet status, instant notifications, and personalized reporting have revolutionized our operations. UgoWork’s Energy Experts provide unparalleled support, helping us reach our fleet reduction and productivity goals.” UgoPilot is set to reshape industries such as food and beverage, third-party logistics (3PL), warehousing and manufacturing. Designed for companies operating medium to large sized fleets, with each truck logging over 2,000 operational hours annually, UgoPilot stands as a beacon for businesses seeking enhanced fleet visibility, optimized performance, and significant energy savings. Elevating industrial battery management UgoPilot redefines energy management and battery intelligence for industrial trucks. With a phased rollout to select existing customers that started in the summer, the platform is now globally available, providing organizations the tools to harness actionable insights for unparalleled fleet performance.
Staffing employment declines in second quarter
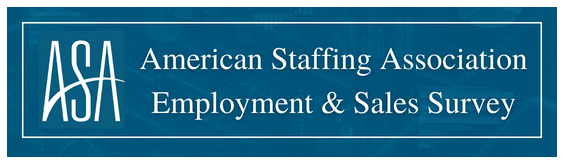
2Q/23 staffing sales decreased 9.1% year-to-year The number of temporary and contract workers employed by U.S. staffing companies declined 4.6% to an average of 2.5 million workers per week from the first to the second quarter of 2023, according to data released by the American Staffing Association. The decline represents a deviation from the typical pattern of temporary and contract employment in the U.S., in which staffing employment and sales typically decline in the first quarter, grow in subsequent quarters, and peak in the fourth quarter. In the face of a slowing economy and continued macroeconomic uncertainty, temporary and contract staffing sales also declined by 4.0% during the same period. Staffing jobs declined 12.2% in the second quarter of 2023 from the same period in 2022, while temporary and contract staffing sales decreased 9.1% over that span to total $35.9 billion in the second quarter of 2023. “The staffing, recruiting, and talent solutions industry faced some headwinds this year as employers across several industry sectors scaled back the massive hiring they undertook in 2021 and much of 2022,” said Richard Wahlquist, ASA chief executive officer. “Nevertheless, demand for labor remains healthy, and the staffing industry continues to play an important in providing talent solutions to companies and impactful employment opportunities to millions of American workers every day. “Looking ahead, survey respondents from private staffing firms are cautiously optimistic about demand picking up, with median projected year-over-year fourth quarter results expected to be flat compared to 2022.” To learn more about the quarterly ASA Staffing Employment and Sales Survey, visit americanstaffing.net/quarterly-survey
Episode 423: Navigating future-ready warehousing with Mark Wheeler of Zebra Technologies
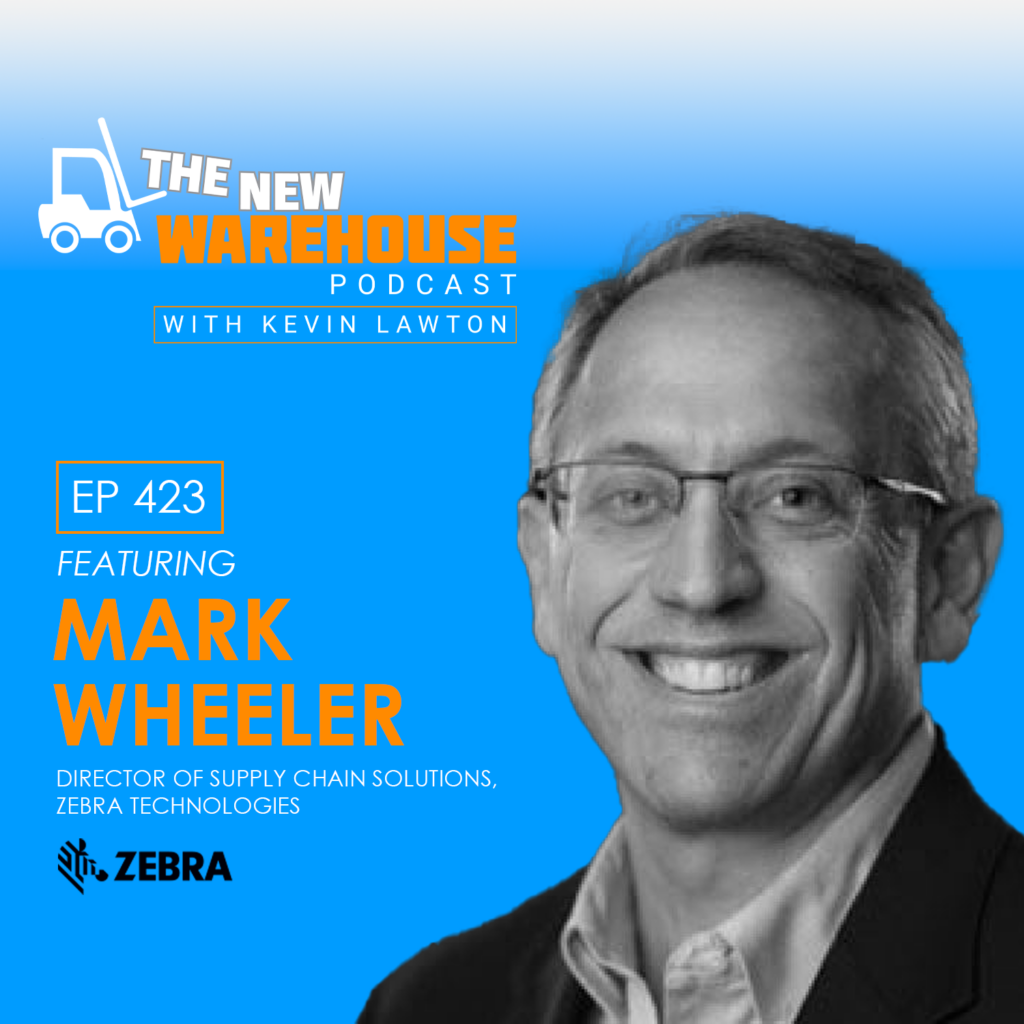
We are thrilled to welcome Mark Wheeler, the Director of Supply Chain Solutions at Zebra Technologies, to today’s episode of The New Warehouse podcast. Zebra Technologies is at the forefront of developing state-of-the-art solutions to optimize productivity and efficiency in the warehousing industry. Mark joins us to delve into the game-changing findings of Zebra’s recent Warehousing Vision Study. Continue reading and tune in to the podcast for some actionable insights that could redefine how you approach warehousing. The Pulse of the Industry: Shaping Future-Ready Warehousing Mark explains, “We’ve been doing the vision study for a number of years now, and it has become an annual study, mostly due to the dynamic nature of the warehouse market that we’ve seen over the last five years.” The study’s value lies in its snapshot of the current state and its ability to track changes over time. By interviewing around 1,400 respondents globally, the research covers a broad spectrum of perspectives. In recent editions, the study expanded to include warehouse associates and decision-makers to provide a well-rounded perspective of what’s happening in the industry. Mark highlights one particularly insightful point from this year’s study: “We’re in a really interesting time, with regard to the warehouse market, with kind of a little bit of a pause in the rapid growth that we saw in the previous years.” The pause Mark refers to appears to be a temporary blip rather than a trend. While some major players are rethinking their expansion strategies, the underlying growth drivers, like e-commerce, are still robust. Technologies like RFID are gaining significant attention, showing that the industry is not standing still but evolving. Mark underscores the industry’s emphasis on “supply chain visibility and incorporating things like over-the-road visibility and yard management visibility into operations.” The Path to Warehouse Automation The shift toward warehouse automation has gained momentum due to evolving supply chain dynamics and the relentless growth of e-commerce. As Mark articulates, the path to automation involves multiple layers: Understanding Service Level Agreements (SLAs) for setting operational goals Prioritizing labor optimization through wearable technologies Implementing intelligent mechanization for routine tasks Investing in sensor technologies for enhanced operational visibility These elements align technology with evolving service demands and operational efficiencies. As the industry pivots, the focus shifts from merely expanding capacity to optimizing for cost and service. Companies are reassessing their physical locations, operational scale, and technology investments. In this transitional period, the emphasis is on a balanced approach that harmonizes labor, technology, and location to meet market demands. This adaptation represents a strategic step toward a more sustainable and efficient future in warehouse management. Supply Chain Visibility in Future-Ready Warehousing Achieving visibility enhances overall efficiency by providing real-time insights into the movement of goods, shipments, and inventory. It eliminates the frequent back-and-forths between departments and reduces uncertainty about shipment arrivals and the location of products within the yard. Enhanced visibility translates into better coordination and minimizes errors, significantly improving the supply chain operation. Mark notes that RFID technology, in particular, is becoming a cornerstone for achieving supply chain visibility. Companies increasingly prioritize this technology as it benefits inventory accuracy, loss prevention, and overall operational effectiveness. Beyond RFID, the drive for better visibility pushes the adoption of various edge technologies and sensors. These technologies not only alleviate labor burdens but also add a layer of precision and speed to supply chain operations. Considering the increasing complexity and pace of the e-commerce landscape, the focus on inventory accuracy and visibility has become the top operational challenge, surpassing delivery speed. Investing in technologies will bring more visibility into supply chains, which is foundational for future success. Key Takeaways on Future-Ready Warehousing The shift in focus from rapid expansion to operational efficiency and technological integration suggests that the industry is moving towards a more sustainable and tech-driven future. Companies are no longer solely focused on grabbing market share and space. Instead, they are actively re-strategizing, considering optimal locations, facility sizes, and effective technology implementation for automation and modernization. Strategic investment in new technologies is crucial for operators to adapt and thrive in the evolving supply chain landscape. The New Warehouse Podcast EP 423: Navigating Future-Ready Warehousing with Mark Wheeler of Zebra Technologies
AAR Rail Traffic for the week ending September 23 2023
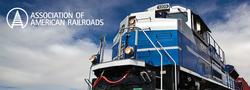
The Association of American Railroads (AAR) has reported U.S. rail traffic for the week ending September 23, 2023. For this week, total U.S. weekly rail traffic was 493,323 carloads and intermodal units, up 2.8 percent compared with the same week last year. Total carloads for the week ending September 23 were 234,904 carloads, up 4.7 percent compared with the same week in 2022, while U.S. weekly intermodal volume was 258,419 containers and trailers, up 1.2 percent compared to 2022. Seven of the 10 carload commodity groups posted an increase compared with the same week in 2022. They included metallic ores and metals, up 3,256 carloads, to 22,732; motor vehicles and parts, up 2,929 carloads, to 16,085; and chemicals, up 2,070 carloads, to 31,067. Commodity groups that posted decreases compared with the same week in 2022 were coal, down 1,860 carloads, to 68,846; grain, down 226 carloads, to 18,072; and forest products, down 73 carloads, to 8,490. For the first 38 weeks of 2023, U.S. railroads reported cumulative volume of 8,538,842 carloads, up 0.2 percent from the same point last year; and 9,065,168 intermodal units, down 8.5 percent from last year. Total combined U.S. traffic for the first 38 weeks of 2023 was 17,604,010 carloads and intermodal units, a decrease of 4.5 percent compared to last year. North American rail volume for the week ending September 23, 2023, on 12 reporting U.S., Canadian and Mexican railroads totaled 346,962 carloads, up 3.7 percent compared with the same week last year, and 342,697 intermodal units, down 0.3 percent compared with last year. Total combined weekly rail traffic in North America was 689,659 carloads and intermodal units, up 1.7 percent. North American rail volume for the first 38 weeks of 2023 was 24,663,751 carloads and intermodal units, down 3.9 percent compared with 2022. Canadian railroads reported 96,025 carloads for the week, up 5.3 percent, and 72,918 intermodal units, down 4.6 percent compared with the same week in 2022. For the first 38 weeks of 2023, Canadian railroads reported cumulative rail traffic volume of 6,006,685 carloads, containers and trailers, down 3.4 percent. Mexican railroads reported 16,033 carloads for the week, down 15.2 percent compared with the same week last year, and 11,360 intermodal units, down 3.9 percent. Cumulative volume on Mexican railroads for the first 38 weeks of 2023 was 1,053,056 carloads and intermodal containers and trailers, up 2.8 percent from the same point last year. To view rail charts, click here.
Combilift enters growing offshore wind sector
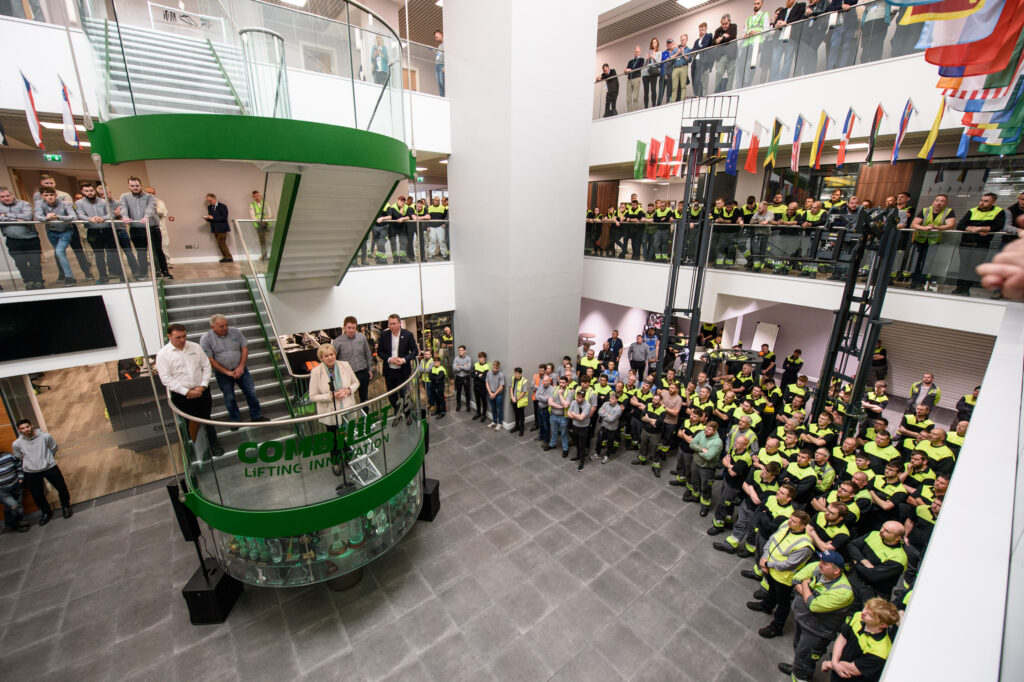
Monaghan based manufacturing firm celebrates 25 years with three new product launches Combilift, largest global manufacturer of multidirectional, articulated forklifts and straddle carriers, has announced its move into the offshore wind sector with the launch of a new product designed to meet the load handling demands of largescale offshore wind manufacturers. As the green energy sector sees a surge in larger wind turbine components, including towers and blades, Combilift joined forces with industry leaders to engineer safe, stable, efficient, lifting and storage solutions across its supply chain. The Combi-LC, designed at Combilift’s HQ and Manufacturing plant in Ireland, in collaboration with Siemens Gamesa, allows for the movement of wind turbine blades and towers – some as long as 115m and weighing in at around 70t, through production stages and on to storage locations – which can sometimes be as far as 5km apart. The concept of bespoke Load Carriers [patent pending design] is based on two fully customisable remote-control units with low-level chassis beds that can work in tandem master and slave operation, with dimensions and wheel configurations that vary according to load type and weight. Siemens Gamesa, one of the world’s largest offshore wind suppliers, has become the first company to leverage the new technology by signing a multi-million order for a number of the bespoke Load Carriers, and Combilift is in active discussions with other offshore wind companies with similar demands. Combilift expects to generate over €50m in revenue per year in this market segment by 2026. Josh Moffett, Heavy Equipment Manager at Combilift, commented on the company’s move into the offshore wind sector: “We are thrilled to have launched this new product – The Combi-LC, and we hope it will act as a gateway for us to further progress within our venture into the wind energy sector. The scale of offshore wind projects around the world leads to a very unique set of challenges, one of which being the ability to transport the very large components that make up a wind turbine. We recognised this and used our expertise in load handling to develop a solution to support those in the industry. The product is specifically made to order and therefore can be uniquely customised to fit specific applications.” Additionally, Combilift launched two other new products – the Combi-AGT, and Combi-Connect. Combi-AGT Already in operation at a number of leading steel service centres in the United States, Combilift’s Autonomous Guided Truck (Combi-AGT), designed specifically for the automated handling of long loads, boasts dual-control capability, enabling manual operation when necessary – a world first. Combined with its unique “natural feature navigation” this truck is a world-leader in autonomous material handling, with positive customer feedback from companies reporting staffing flexibility and utilization benefits. Combi-Connect The third product launched by Combilift is Combi-Connect. It is a telematic software product that provides its customers with greater levels of insight into fleet management and utilization, providing real-time data on fleet performance, including location tracking, usage analytics, and maintenance alerts. With this invaluable information at their fingertips, businesses can optimise operations. Based on a subscription model, Combi-Connect offers fully transparent data analytics enabling not only dealers, but the customers themselves, to manage and make informed decisions. Speaking at Combilift’s 25th Anniversary event, Minister for Rural and Community Development, Heather Humphreys TD said: “Over the past 25 years, Combilift has made a very important impact to the Irish economy. Combilift is a visionary company in every sense and I’m delighted that the Irish government, through Enterprise Ireland, has supported Combilift through its incredible 25-year journey. Martin McVicar – Managing Director of Combilift: “We have a track record of innovation at Combilift. We invest 7% of our revenue annually in R&D and today is the culmination of many years’ hard work. We are delighted to be continuing this tradition of innovation 25 years on. Now employing over 800 people in Monaghan and 200 people in other locations across the world, the success of Combilift is testament to our people, our customers and our supporting dealers around the world . We are looking forward to the next 25 years at Combilift.” Michael Woods – Head of Offshore Equipment Operations at Siemens Gamesa: “Seeing the new LC Blade mover in the flesh is impressive, it is fantastic to see it come from design to fruition, the manoeuvrability and functionality looks great, we can’t wait to see it onsite moving blades.”
Supply Chain Quarterly’s Outstanding Women in Supply Chain
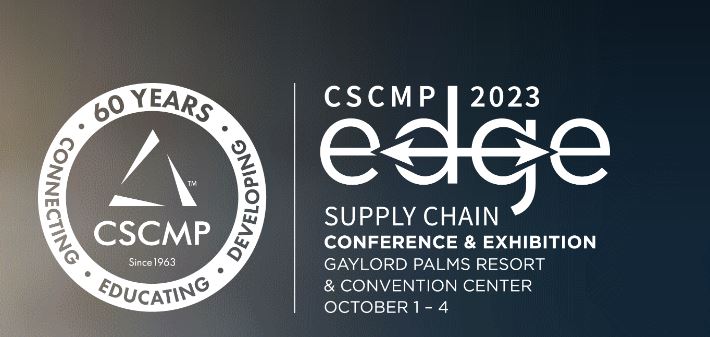
Supply Chain Quarterly has announced the inaugural Outstanding Women in Supply Chain awards. We’ll honor three exceptional women who have made remarkable contributions to the supply chain industry at the upcoming CSCMP EDGE 2023 conference. This industry requires strategic thinking, innovative problem-solving, and effective leadership, and these women have consistently demonstrated their commitment to excellence. Their dedication, passion, and accomplishments have not only advanced the supply chain landscape but have also served as an inspiration to countless professionals. INTRODUCING THE HONOREES Ammie McAsey, Senior Vice President, Customer Distribution Experience, McKesson U.S. Pharmaceutical Ammie McAsey is responsible for leading the supply chain strategy across the U.S. for brand, generic, and specialty pharmaceuticals. She oversees more than 40 distribution locations and central fill pharmacies, transportation services, network design, operations quality, inventory replenishment, and customer support. Previously, McAsey was the vice president and general manager of the company’s three Strategic Distribution Centers, where she was responsible for leading supply chain synergies with the national buying center, manufacturers, field distribution centers, and customers. She has also served as vice president distribution operations for the North Central region and director of operations. In these roles, McAsey collaborated across functions to deliver operational excellence, talent development, and financial performance. McAsey is a member of the Women Business Leaders of the U.S. Healthcare Industry Foundation, Supply Chain Leaders in Action, Health Care Distribution Alliance, and Fortna Advisory Board. She serves on the Board of Directors for U.S. Venture in Appleton, Wisconsin. Jackie Sturm, Corporate Vice President, Global Supply Chain Operations, Intel Jackie Sturm leads operations for Intel’s multibillion-dollar global supply chain, which has been one of the top 20 in Gartner’s Supply Chain Top 25 for 19 consecutive years. Her international team supports both direct and indirect procurement; business continuity; supply chain systems and analytics; and Intel’s Supply Chain Environmental and Social Governance program, which includes Intel’s Conflict Minerals initiative. Sturm sponsors targeted advancement programs to address challenges faced by women and under-represented minorities in technology. Sturm is on the advisory board for Banff International Research Station, Gartner and SAP’s Supply Chain practices, Howard University Center for Supply Chain Management, and Women’s Business Enterprise National Council. She is a recipient of several Intel Quality Awards, and she and her team have been recognized with the Intel Achievement Award, Intel’s highest standard of excellence. Sturm received the 2016 AWESOME Legendary Leader Award and has been cited in the IBM, Supply Chain Digital, and Alcott Global Top 100 Women in Supply Chain. Meredith Westafer, Industrial Engineering Manager, Tesla Meredith Westafer leads the Tesla Factory Design team, designing the layouts and material flow for new Tesla Gigafactories. She joined Tesla in 2015 as the company was just beginning construction on its first Gigafactory in Nevada. She was responsible for the material flow design for getting all parts to the powertrain manufacturing lines, including developing an automated guided vehicle program with more than 50 AGVs. Her engineering team also designed the layouts and material flow strategy for Gigafactories in Shanghai, Berlin, and Texas. Her ability to drive systems-level solutions to complex, ambiguous, companywide problems has catapulted her scope to include global factory design and strategic planning. Westafer was named one of Business Insider’s Most Powerful Female Engineers in 2018 and has spoken at industry events. She graduated the University of South Florida in 2010 with a Bachelor of Science degree in Industrial Engineering and a master’s degree in Engineering Management. The Outstanding Women in Supply Chain event will take place at CSCMP EDGE in the Ask the Experts Theater on Monday, October 2, from 12:30 – 1:30 p.m. Come and listen to their fascinating stories and participate in a Q&A session. It will be moderated by SCQ’s executive editor, Susan Lacefield.
Waabi partners with Uber Freight with AI-powered automomous trucks
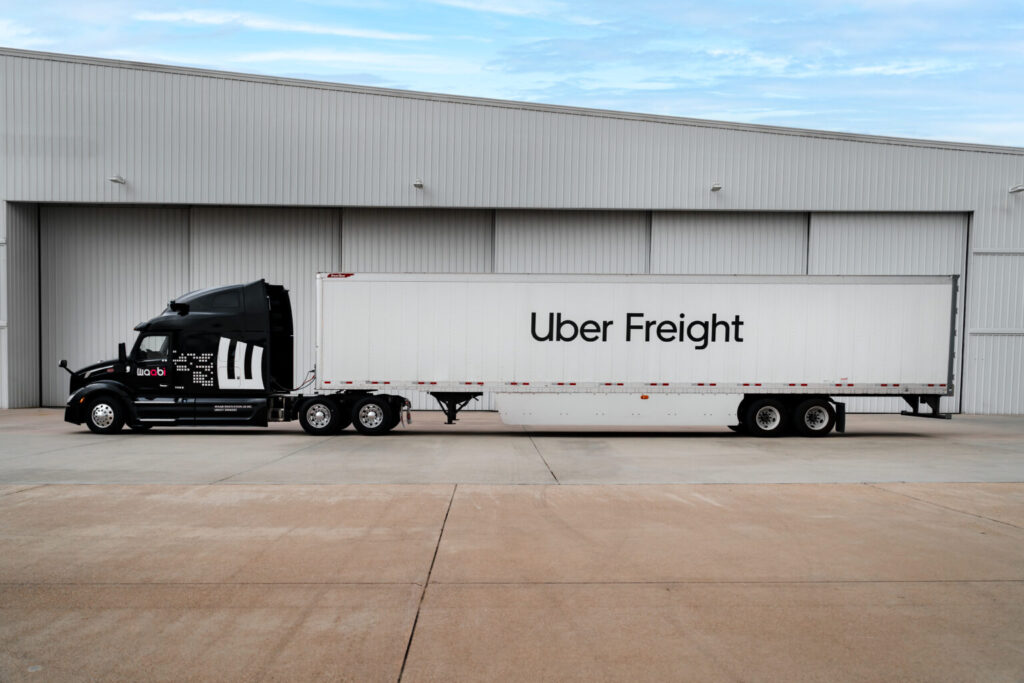
September 21, 2023 marked a significant milestone for Waabi and the logistics industry. They have announced a strategic partnership with Uber Freight to accelerate the safe deployment of AI-powered autonomous trucks at scale. The agreement pairs Waabi’s core technology—the Waabi Driver—with Uber Freight’s vast logistics platform and marketplace technology to deliver a turnkey driver-as-a-service solution that will be the first of its kind. This unique solution will empower carriers to dynamically and effectively deploy the Waabi Driver while also unlocking critical capacity for shippers and driving value throughout the supply chain. By providing carriers with the services and infrastructure to deploy, maintain and manage their autonomous assets seamlessly, our bundled solution can help increase asset utilization significantly as well as drive profitability for carriers of all sizes. Over the next ten years, Waabi and Uber Freight also intend to deploy billions of miles of Waabi Driver capacity alongside carrier partners on the Uber Freight network, ensuring the technology will have a meaningful impact for shippers and carriers over the long term. To gather valuable insights for the joint solution, our autonomous trucks have already been deployed on the Uber Freight network, giving their customers early access to autonomous freight capacity. The autonomous commercial loads, the first of which ran this week, will run regularly between Dallas and Houston and give the thousands of shippers and carriers on the Uber Freight network an opportunity to better understand what the future of supply chain operations will look like and how autonomous trucks can improve overall network efficiency. As the partnership continues to advance, we will quickly expand to other key lanes in Texas and beyond. A new model for AI-powered autonomous truck adoption and deployment While autonomous trucks represent a huge opportunity for the logistics industry to increase asset utilization, improve road safety, lower carbon emissions, and improve drivers’ livelihoods, reaching their full potential hinges on integrating into a scaled freight network that can optimize load matching, orchestrate hub-to-hub operations, and provide carriers a streamlined experience for onboarding, load booking and execution, trailer hand-offs, payments and asset maintenance. The industry-first driver-as-a-service solution at the center of our partnership will pair the Waabi Driver with Uber Freight’s technology and services to offer carriers the most technologically advanced, operationally efficient and holistic model for safely and effectively adopting autonomous trucks within their fleets. In the future, carriers with Waabi Driver-enabled trucks will have the option to deploy their assets instantly and seamlessly on the Uber Freight network, taking advantage of continuously optimized routes, as well as an ecosystem of partnerships with transfer hub infrastructure, roadside assistance, and national maintenance providers. A robust technical integration will enable shippers to tap directly into Waabi Driver capacity from Uber Freight’s digital tools, making it easy to transform procurement strategies and incorporate efficient and reliable autonomous capacity into their day-to-day operations. With $18 billion of Freight Under Management, Uber Freight is uniquely positioned to improve reliability and cost-effectiveness for shippers by optimizing routes and combining shipments, ultimately maximizing utilization of autonomous and human-driven trucks across entire networks. Importantly, this partnership will make it effortless for carriers and shippers to unleash our generative AI-powered technology within their own operations. We’re tackling autonomous driving in a new way, the Waabi Driver is the first and only autonomous truck solution to be built around a foundation AI model, which unlike traditional approaches that require painstaking manual code adjustments, can automatically learn from data and generalize its learnings to all the situations it might encounter on the road, including those that it has never seen before. The Waabi Driver’s development is front loaded within our revolutionary simulator, Waabi World — the most scalable, highest fidelity closed-loop simulator to ever exist. In Waabi World, generative AI reconstructs digital twins automatically from raw sensor data. These digital twins can then be modified to create infinite potential new scenarios, exposing the Waabi Driver to the vast diversity of experiences needed to hone its driving skills, including common scenarios and safety-critical edge cases. This approach drastically reduces the need to drive in the real world, resulting in a solution for carriers and shippers that is not only more sustainable, but also smarter, safer, and more scalable. Accelerating the future of logistics and driving positive change across safety, efficiency, jobs and the environment This partnership comes at a time when logistics innovation is needed most. Not only is the industry facing considerable inefficiencies across supply chains, with an estimated ~20-35% of miles being driven empty, and a looming shortage of truck drivers, expected to reach 160,000 by 2028, but persistent safety issues continue to plague the industry. The National Highway Traffic Safety Administration (NHTSA) reported that in 2019, large truck crashes accounted for more than 5,000 lives lost—and 87% of large truck crashes involve human error, according to historical data from the Federal Motor Carrier Safety Administration (FMCSA). Additionally, transportation is the only sector with emissions that are still growing in US & Europe and freight trucking, in particular, accounts for nearly 7% of US CO2 emissions. Autonomous trucks have tremendous potential to address these issues, significantly increasing asset utilization, reducing carbon emissions, improving road safety, and positively reimagining the career outlook and quality of life for truck drivers. A recent study by the Department of Transportation found that autonomous trucks could actually stimulate job growth and increase total U.S. employment by 26,400 to 35,100 jobs per year on average. Together, we look forward to advancing logistics and delivering on the promise of autonomous trucks.
Raymond shapes future of Manufacturing and inspires next generation with virtual Manufacturing Day event
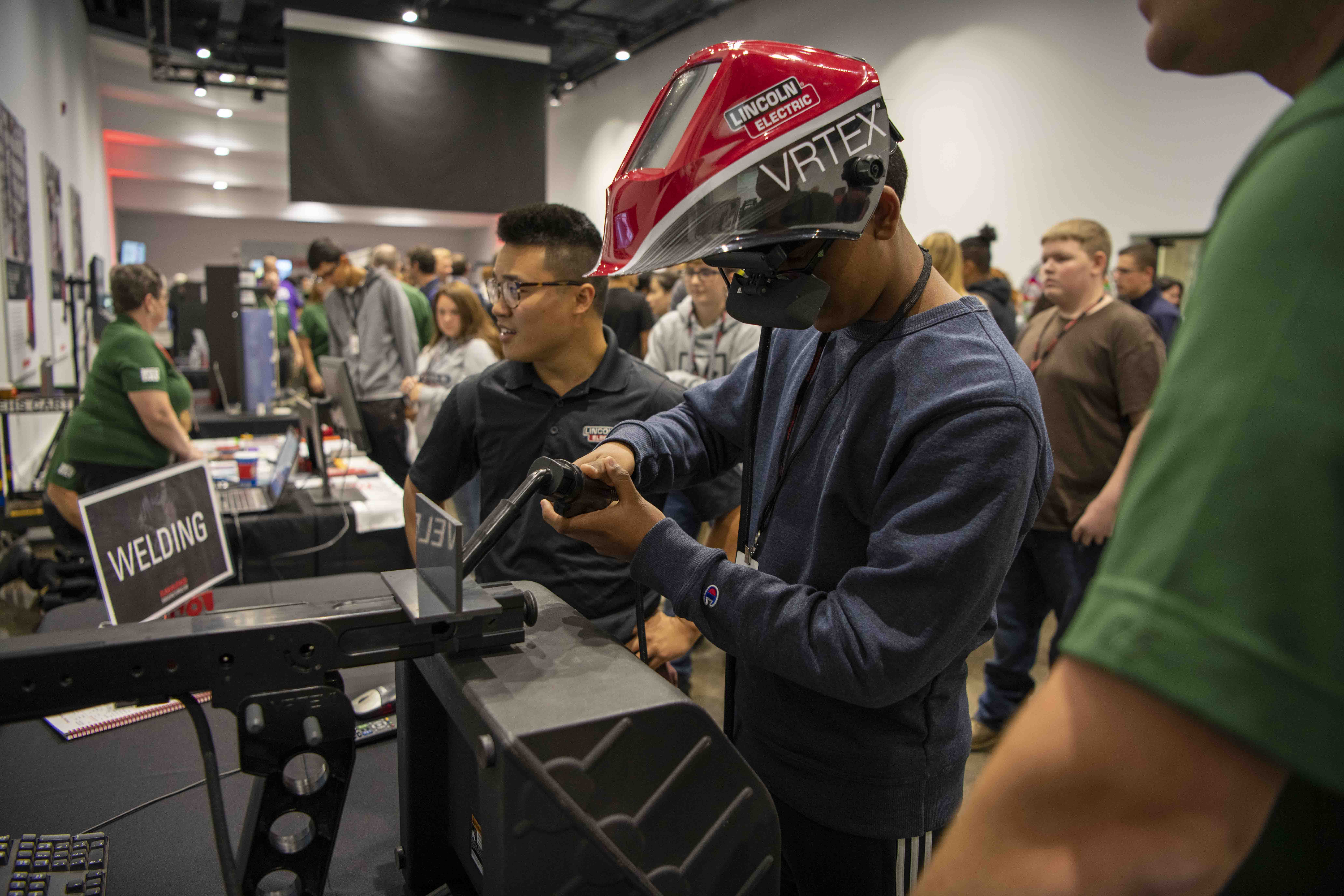
Virtual event aims to celebrate the manufacturing industry, highlight the importance of skills development and inspire the next generation as Raymond continues to innovate The Raymond Corporation will kick off its ninth annual Manufacturing Day event, The Raymond Corporation’s 2023 Virtual Manufacturing Day, on Oct. 6, 2023. National Manufacturing Day is an annual celebration of the manufacturing industry and organized by the National Association of Manufacturers (NAM) since 2012. This year is the fourth year Raymond’s Manufacturing Day will be an entirely virtual event. This online program, starting Oct. 6 and continuing through Oct. 27, will help teachers and students learn more about future careers in modern manufacturing. Students from schools across the globe will have the opportunity to learn about building skills for the future through a virtual manufacturing facility tour, highlights of industry technology and discussions with Raymond’s associates and leadership team. “We’re excited to shine a light on the incredible advancements happening in the material handling industry and hope to ignite curiosity and passion in the next generation of innovators,” said Tony Topencik, vice president of operations, quality, environmental health and safety at The Raymond Corporation. “It’s crucial to recognize that there will always be a demand for skilled workers who play essential roles in keeping our supply chains running smoothly. We’re dedicated to creating an environment where individuals can thrive and make their mark in shaping the future of manufacturing.” For over 100 years, Raymond has been a leader in manufacturing, engineering and the material handling industry and is recognized for its leadership and innovation through various awards over the years, including: Forbes Best Midsize Employer, 2021, 2022 and 2023 Manufacturing Leadership Award, 2021, 2022 IndustryWeek Best Plants Award, 2018, 2022 Plant Engineering Product of the Year Award, 2020, 2023 “Raymond’s commitment to innovation and nurturing the next generation of leaders in manufacturing helps ensure that they have the tools and resources required to make a positive impact on the supply chain,” said Randy Wolken, president and CEO at Manufacturers Association of Central New York. “We are proud to be part of their journey as they continue to drive progress and shape the future of this dynamic industry right here in the heart of New York state.” Individuals interested in joining the virtual celebration can find more information below. What: The Raymond Corporation will host its ninth annual Manufacturing Day event. The month-long event, kicking off Oct. 6, will be a self-guided, interactive exploration of The Raymond Corporation, including: A virtual factory tour, in which students can explore Raymond’s manufacturing floor. Associate testimonials from Raymond’s headquarters in Greene, New York, covering its apprentice program, co-op program, and various departments on its manufacturing floor. A technician spotlight which will showcase two Raymond Solutions and Support Centers from across the United States. Industry technology showcasing the future of manufacturing. When: Starting Friday, Oct. 6, 2023, at 8 a.m. This is not a live event, and participants are free to join at their convenience through Friday, Oct. 27, 2023, at 5 p.m. The experience is expected to take approximately one hour to complete. Where: www.raymondcorp.com/ManufacturingDayRegistration Who: This virtual event is open to all middle and high school students globally via teacher registration. Please email manufacturingday@raymondcorp.com if you have any questions. Interview Subjects: Steve VanNostrand, executive vice president at The Raymond Corporation, and Tony Topencik, vice president of operations, quality, environmental health and safety at The Raymond Corporation.