KION Group closes recycling loop for lithium-ion batteries
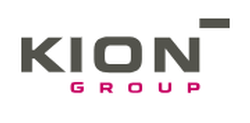
Intralogistics Group’s batteries now being recycled by strategic partner Li-Cycle in Magdeburg, Germany Sustainable process recovers up to 95 percent of the battery’s valuable minerals and materials KION Group CTO Henry Puhl: “We are helping to drive forward the transition to a low-carbon economy.” The KION Group is now sending lithium-ion batteries that have reached the end of their useful life to its strategic partner Li-Cycle Holding Corp. (“Li-Cycle”; NYSE LICY) for recycling. The Group’s objective is to have a total of up to 5,000 tonnes of end-of-life battery material professionally and sustainably processed at the Li-Cycle recycling plant in Magdeburg, Germany, by 2030. This tonnage is equivalent to around 15,000 large lithium-ion batteries of the kind used in forklift trucks. “We firmly believe that lithium-ion is the drive technology of the future. That is why it is so important to us to make the technology part of a closed loop – from manufacturing and usage through to resource recovery,” said Henry Puhl, Chief Technology Officer of KION GROUP AG at the official opening of Li-Cycle’s first recycling plant in Europe. The KION Group produces its own lithium-ion batteries at the KION Battery Systems plant in Karlstein am Main. These are then installed in the electric-powered industrial trucks of the KION brand companies Linde MH, Fenwick, STILL, and Baoli, as well as in automated warehouse logistics systems. “Together with Li-Cycle, we are now closing the loop and ensuring that nearly all of the valuable materials, including lithium, cobalt, copper, and nickel, are recovered from the lithium-ion batteries used in our trucks. These resources can then be used to make new batteries.” Puhl emphasized that the partnership with Li-Cycle will strengthen the KION Group’s sustainability credentials and further extend its market-leading position in electric-powered industrial trucks. While 88 percent of all industrial trucks sold by the KION Group brands last year were electric, the figure for the global market as a whole was just over 70 percent. “Not only are we helping to drive forward the energy transition, but we are also leading the way in the recovery of critical materials and the recycling of advanced lithium-ion batteries.” “We want to ensure that lithium-ion batteries do not end up in landfills, but instead that all their components are recycled in an environmentally responsible manner,” explains Richard Storrie, Li-Cycle’s President for the EMEA region. “The agreement with KION is an excellent example of a sustainable, long-term cooperation. Acting as a strategic partner, Li-Cycle will support the KION Group in hitting its recycling targets while at the same time helping it to meet EU requirements for battery management.” Modern and environmentally friendly recycling process Li-Cycle uses an innovative and sustainable two-stage process to recycle lithium-ion batteries and recover critical battery materials. In contrast to energy-intensive smelting methods, Li-Cycle uses non-thermal liquid-based size reduction technology. Li-Cycles technology can be used to process all types of lithium-ion batteries – regardless of shape, size, or chemistry. This liquid-based process is safer and avoids potential hazards such as fires. After the plastics and metals (copper, aluminum, and steel) are separated, they are rinsed, dried, and packaged ready to be shipped. The remaining intermediate, known as black mass, is then dealt with in stage two. In this hydrometallurgical process, materials such as lithium carbonate, cobalt sulfate and nickel sulfate are recovered from the black mass so that they can then be used in new batteries. The Li-Cycle process at its recycling facility in Magdeburg produces only minimal landfill waste, low air emissions, and no wastewater discharge. It has processing capacity for up to 30,000 tonnes of lithium-ion battery materials per year.
IDEC acquires shares in ez-Wheel providing innovative mobility solutions
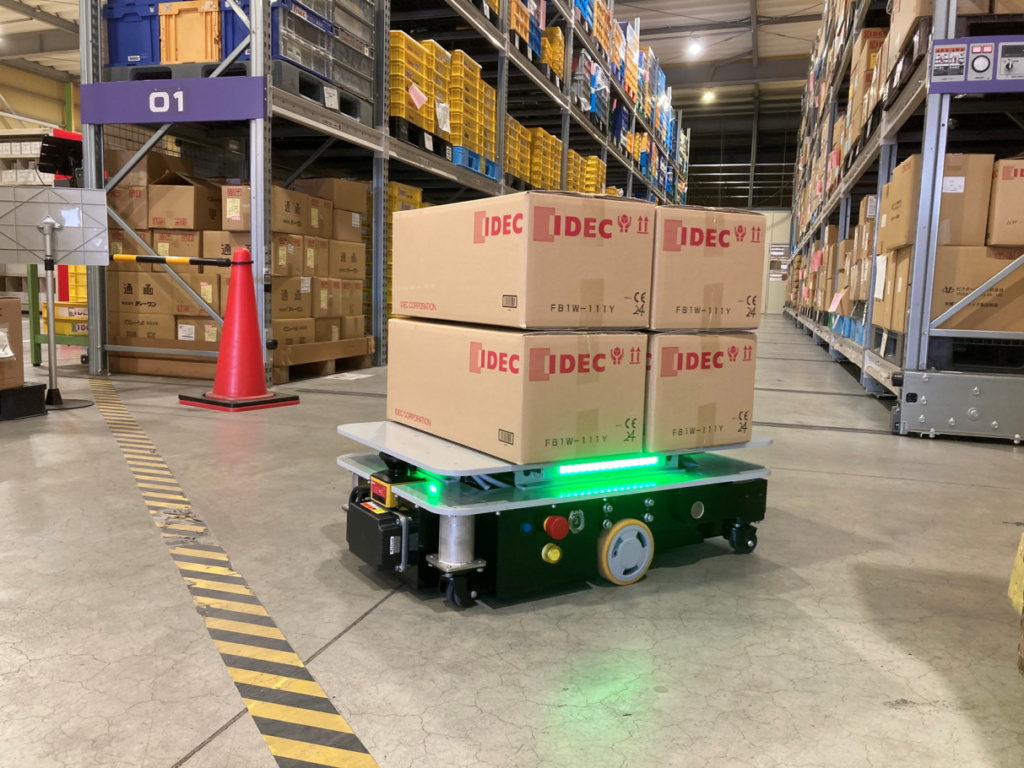
IDEC Corporation announces that it has acquired 80% of the shares of ez-Wheel SAS (Headquarters: France, “ez-Wheel”) as of August 1, 2023. This follows the strategic partnership agreement signed between IDEC and ez-Wheel on January 24, 2022. ez-Wheel was founded in Angoulême, France in 2009 with the mission of developing easier and safer means of transporting goods. They developed the world’s first self-propelled wheel in 2010, and the world’s first safe autonomous wheel in 2021. Self-propelled wheels incorporate driveline (motor, drive, gearbox) and control/safety elements within a single device. These products are an excellent fit for automated guided vehicles (AGVs), autonomous mobile robots (AMRs), mobile conveyors, material handling, and electrification of any type of motion or power assist device. All these categories are experiencing rapid growth throughout various industries to support progress in global automation, address labor shortages, and improve the safety and well-being of workers by reducing the burden of many tasks. In addition, ez-Wheel products are helping AGV/AMR designers to easily integrate and develop new equipment—and also to evolve legacy designs—for best compliance with safety requirements. IDEC will strengthen the research and development of the ez-Wheel team, and it will expand global sales of these mobility solutions in conjunction with complementary IDEC products, such as human-machine interfaces (HMIs) and safety-related equipment. These efforts will support IDEC’s HMI transformation (HMI-X) initiative to provide optimal, intuitive, and safe human-machine interactions, with a focus on human well-being. Key ez-Wheel products include the Electric Power Assist Wheel (EPAW) used for reducing the burden of transporting heavy loads on existing carts and trolleys, and the Safety Wheel Drive (SWD) which facilitates the development and certification of AGVs, AMRs, and other automated logistics applications. The SWD is equipped with safety operation monitoring functions as required by international safety standard ISO 3691-4, so it can be used in environments where people and robots coexist.
Staffing employment steady in September
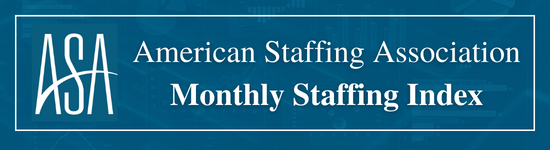
Almost half of all staffing firms report gains in new assignments Staffing employment edged up in the week of Sept. 11-17, with the ASA Staffing Index increasing by 1.1% to a rounded value of 101. Many staffing companies listed a holiday as a barrier preventing further growth. Staffing jobs were 4.8% below the same week last year. New starts in the 37th week of the year rose 5.9% from the prior week. Almost half of all staffing companies (49%) reported gains in new assignments week to week. The ASA Staffing Index four-week moving average increased from the prior week to hold at a rounded value of 101, and temporary and contract staffing employment for the four weeks ending Sept. 17 was 4.9% lower than the same period in 2022. “Staffing employment continues to trend below 2022 but above levels seen in the spring of 2023,” said Tim Hulley, assistant research director at ASA. This week, containing the 12th day of the month, will be used in the September monthly employment situation report scheduled to be issued by the U.S. Bureau of Labor Statistics on Oct. 6. The ASA Staffing Index is reported nine days after each workweek, making it a near real-time measure of staffing employment trends. ASA Staffing Starts are the number of temporary and contract employees placed in new assignments during the reporting week. ASA research shows that staffing employment has historically been a coincident economic indicator. For more information, visit americanstaffing.net/index.
SuperCorrExpo® 2024 on track to break exhibitor records
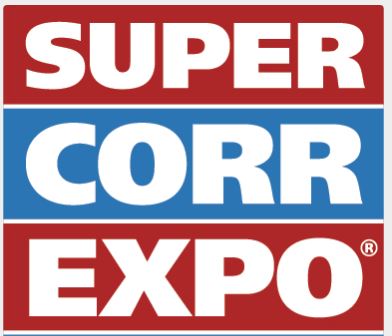
SuperCorrExpo® (SCE), co-hosted by TAPPI and AICC, returns to Orlando, FL, September 8-12, 2024 with a focus on “Future Forward. Time Tested.” With nearly 85% of the show floor already sold, expectations are high for a banner year in terms of attendance and a packed show floor of more than 300 exhibitors. More than 6,000 industry leaders from more than 70 countries are expected to attend this international event. Exhibitors will showcase live demos of cutting-edge, working equipment, while sharing state-of-the-art technological innovations designed to provide next generation capabilities for box makers. A record number of representatives from corrugated manufacturers from around the world are expected to attend in 2024. “As technology drastically improves, the corrugated industry is poised for major changes,” said TAPPI CEO and President Larry N. Montague. “SuperCorrExpo 2024 will be the biggest ever, with converters, engineers and buyers sharing how they plan to navigate the future of the industry. The show floor will feature working machinery, the latest technical advancements, presentations from industry leaders and exciting networking opportunities. SCE is the premiere event for exchanging ideas and forging powerful relationships.” Held at the Orange County Convention Center (OCCC), an international destination for both business and leisure travelers, SCE offers attendees multiple learning opportunities in addition to the expansive exhibit floor. These include technical sessions focusing on the latest industry developments and in-depth corrugated courses, as well as four lively keynote presentations from industry leaders and other socially relevant and timely speakers. “Anticipation is high for SCE 2024,” said AICC President Michael D’Angelo. “We’ve seen a lot of advancements in the last few years and this event is going to not only be a celebration of those achievements, but also serve as a springboard for future innovations – for all converters. In addition, the second-ever Box Manufacturing Olympics will feature innovative designs created over the last two years and entries will be available for viewing on the show floor. With 43 categories in the running, winners will be announced each day, and Best of the Industry winners announced on the last day of the show. Applications are being accepted until June 28, 2024 at supercorrexpo.org/BMO.
Carolina Handling donates proceeds from its Patriotic Forklift Auction
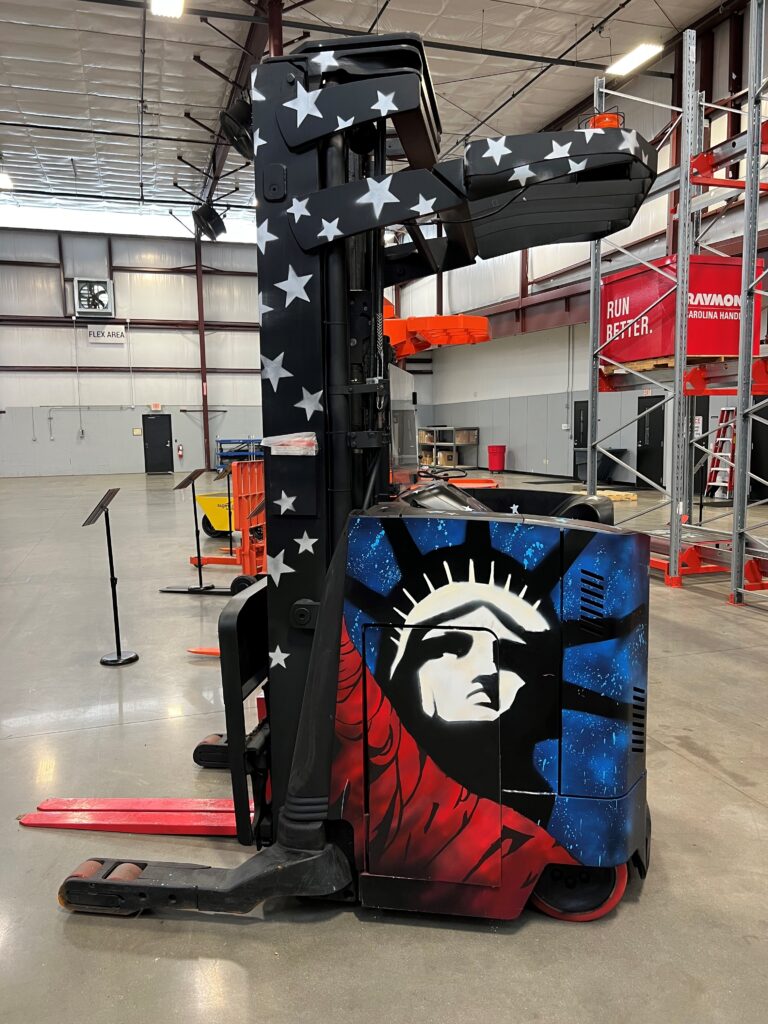
Carolina Handling donated proceeds from its recent patriotic forklift auction to Folds of Honor Palmetto State Chapter and Upstate Warrior Solution, with each organization receiving $5,000 during a check presentation held September 20th at the Rupert Huse Veteran Center in Greenville, South Carolina. The red, white and blue Raymond 7000-Series Reach Truck with images of Old Glory and Lady Liberty was purchased by Silmar Electronics of Greenville, South Carolina, A distributor of security systems, fire alarms, CCTV, access control, home automation and audio-visual systems, Silmar was in the market for a forklift when Greenville Branch Manager James Branton received an email about the auction. “The auction was an opportunity to get a usable forklift at possibly a good price and help a charity that helps veterans,” Branton said. “As a branch that has two veterans in house, this immediately turned the meaning of the forklift from functionality to purposeful.” Custom painted by a Carolina Handling renewed shop technician, who also serves in the South Carolina National Guard, the patriotic forklift features large images of Old Glory and Lady Liberty, white stars along the mast and operator cabin, and red forks. The colorful piece of material handling equipment was displayed outside the Carolina Handling Military & First Responders Skybox during the 2023 BMW Charity Pro-Am, then sold at auction after the tournament to benefit Folds of Honor and Upstate Warrior Solution. “Folds of Honor Palmetto State Chapter is grateful for the ongoing and continued support in providing educational scholarships for the children and spouses of fallen and disabled service members and first responders,” said Jeff Morris of Folds of Honor Palmetto State Chapter. “The support and money provided by Carolina Handling will allow us to continue to help those who serve our community and country.” Upstate Warrior Solution will use proceeds from the patriotic forklift auction to continue its work of providing wrap-around care for veterans, including housing, employment, mental health and peer support, according to Director of Marketing and Communications Catherine Pelicano. “As a community-based nonprofit, local support has always been crucial for sustaining our work,” Pelicano said. “We’re so grateful for partners like Carolina Handling who share our passion for serving the men and women who protect our country and community.” With 13 percent of its associates having served in the U.S. Armed Forces, Carolina Handling supports veteran’s organizations across the Southeast and is an annual sponsor of the Veteran Employment & Transition Summit presented by The RECON Network. “Careers at Carolina Handling offer a purpose-driven, military-to-civilian transition,” said Carolina Handling President & CEO Brent Hillabrand. “The skills developed while serving in the U.S. Armed Forces can make you highly successful in the material handling industry.”
KEEN Utility Cincinnati 90 Degree heavy-duty work boot
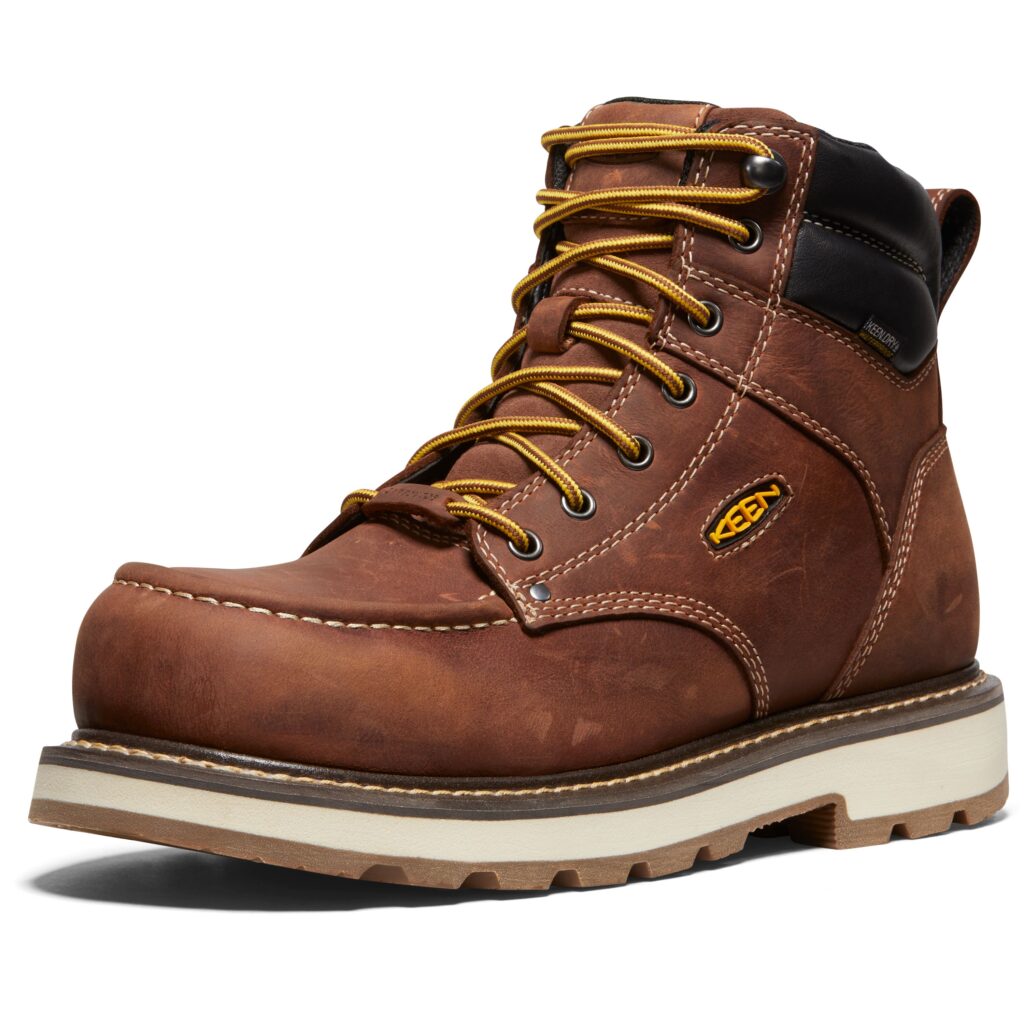
With the introduction of the Cincinnati 90 Degree, KEEN Utility now offers the fan favorite heavy-duty work boot with a 90-degree heel for a dependable grip on ladders or soft surfaces. Featuring an air-infused Lufttcell midsole for unbeatable comfort, an EH-rated rubber outsole to improve traction and barnyard resistant leather to protect feet from variables on the work site, this heavy duty boot is a stand-out for wet conditions with varied terrain. Additional safety features include carbon fiber toes that provide an unobtrusive fit and are 15% lighter than steel, along with continuous goodyear welt construction for enhanced durability under harsh work conditions. To maximize comfort, the Cincinnati also offers shellback heel support and a removable, PolyAer PU footbed with pillow-top cushioning. The Cincinnati 90 degree is available for men in two different colorways.
Raymond names to Food Shippers of America’s 2023 Top Food Chain Technology list

The Raymond Corporation, a global supplier of best-in-class material handling products and intelligent intralogistics solutions, has been named to Food Shippers of America’s (FSA’s) 2023 Top Food Chain Technology list for its iWAREHOUSE® FieldSense (iW.FieldSense) Proximity Notification System. The Top Food Chain Technology program annually highlights standout technologies that are leading the way to revolutionizing the supply chain within the food and beverage industry. iW.FieldSense is part of the iWAREHOUSE Intelligent Warehouse Solutions portfolio and Raymond’s intralogistics capabilities — empowering companies to optimize, connect and automate their operations with a variety of tools and services. The robust system is designed as a training reinforcement tool to alert pedestrians and lift truck operators when they come within a predefined distance of properly equipped lift trucks and pedestrians. iW.FieldSense also can alert vehicle operators to the proximity of structural elements in a facility. Using audible and visual alerts, the technology helps increase a user’s environmental awareness of other properly equipped users, reinforcing training and best practices in today’s congested warehouses. “Raymond offers the food and beverage industry an automated, integrated system — from operator assist technologies like the iW.FieldSense to automated guided vehicles that perform in repetitive applications and automated storage and retrieval systems that offer efficiencies to move goods through facilities,” said Brian Everett, group publisher and editorial director of Food Chain Digest, the official magazine of Food Shippers of America. “We acknowledge that Raymond’s intelligent intralogistics and automated solutions free up labor for food shippers to perform more value-driven tasks to reduce inefficiencies — a major supply chain pain point for many food companies.” Versatile for all operations, industries and applications, Raymond® products help enhance the entire warehouse and distribution operation while delivering actionable, data-driven insights. “This recognition is a testament to the hard work and dedication of our team,” said Dave Norton, vice president of customer solutions and support, The Raymond Corporation. “We are excited to continue innovating and elevating the food chain industry with cutting-edge technology.” View the full list of companies named to FSA’s 2023 Top Food Chain Technology list here.
ASA recognizes Best Job Training Programs in the U.S. Staffing Industry
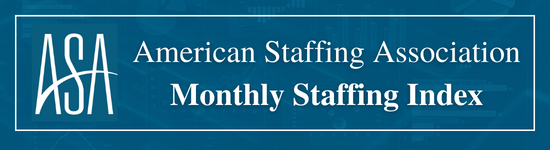
From programs addressing the health care worker shortage to classes developing real estate skills, the American Staffing Association’s 2023 Elevate Award winners display the range of staffing’s influence on the labor market. Created in 2018, the Elevate Awards celebrate the staffing industry’s most innovative workforce development programs for temporary and contract employees. Award classes are determined by company revenue. “The ASA Elevate Award highlights the staffing industry’s commitment to helping people future-proof their careers through training, upskilling, and reskilling,” said Richard Wahlquist, chief executive officer at ASA. “By fostering innovation and empowering the workforce through skill development, Elevate Award honorees are a testament to the transformative impact of staffing on individuals and industries alike.” Award winners will be honored during a ceremony at Staffing World®, the ASA annual convention and expo, Oct. 3-5 at the Charlotte Convention Center in Charlotte, NC. 2023 ASA Elevate Award Winners Staffing Agencies With More Than $100 Million in Annual Sales Nomad Health, “Every Clinician Matters” In the midst of a clinician shortage, Nomad Health developed a competency education program focused on evidence-based learning practice, which is customized to the needs of each individual registered nurse or Allied Health clinician. The program, which is in line with competency definitions by the Joint Commission and American Nurses’ Association, provides one-on-one tailored approach to more than thirty specialty areas. The focus includes care of patients that require high acuity management, dysrhythmia interpretation, recognition of patient deterioration and anticipating complications, as well as TJC national patient safety goals and key safety practices. Since the launch of the program in 2022, competency pass rates jumped 22% among clinicians who were previously identified as needing remediation. As a direct result of this program, clinicians have achieved a 95% average pass rate and are more confidently places at the bedside with the assurance they will provide the best care possible. Staffing Agencies With $25 Million to $100 Million in Annual Sales Hamilton-Ryker, “WorkWell” Hamilton-Ryker’s WorkWell nonprofit organization focuses on providing individualized support to reduce barriers to successful employment and career growth, positively transforming the lives of individuals, families, and communities in our nation. Since its inception, WorkWell services have been available to more than 1,000 apprentices at 400 employers. Through the WorkWell program, apprentices can gain access to financial literacy, planning, problem-solving, and advocacy strategies. Staffing Agencies With $7.5 Million to $25 Million in Annual Sales JWilliams Staffing, “Real Estate Learning Network” JWilliams Staffing is providing employees with in-demand real estate knowledge and skills. Their Real Estate Learning Network (RELN) is an online educational platform with courses for employees looking to grow their talents in new home sales, affordable housing, leasing, property management, and maintenance. Employees even have the option to receive a certification upon completion. Since the introduction of the program, JWilliams Staffing has awarded more than 1,500 career certifications through RELN. Honorable Mentions Staffing Agencies With More Than $100 Million in Annual Sales PeopleReady, “WorkUp” Randstad North America, “Transcend”
Pfannenberg appoints Barbara Ross as new Director of Channel and Representatives
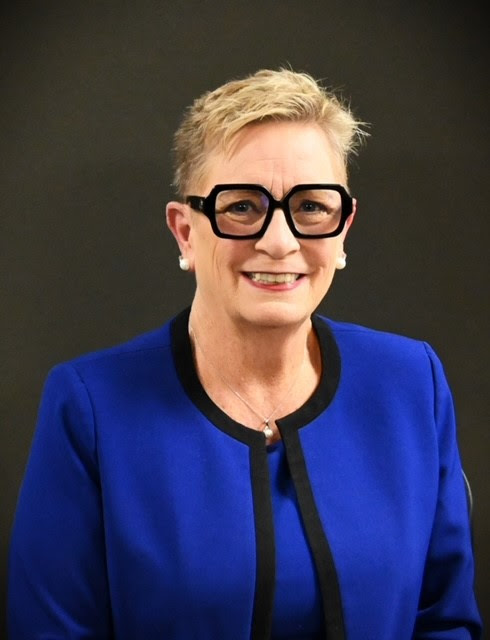
Over thirty years of leadership experience will drive continued growth for the company Pfannenberg, Inc., a global manufacturer of thermal management and signaling technologies, announced that Barbara Ross has been appointed as its new Director of Channel and Representatives. In her new role, Ross will focus on strategically aligning with Pfannenberg’s independent representative partners along with robust channel development. “All of us at Pfannenberg are thrilled to welcome Barbara to the team,” says Earl Rogalski, President. “Her dynamic leadership and impressive decades-long track record make her the ideal person to help drive Pfannenberg towards sustained growth.” Prior to this role, Ross has held several key leadership roles equipping her with over three decades of sales, representative, and distribution leadership experience. Beyond her daily work, Ross is a dedicated volunteer for the Power Transmission Distributors Association (PTDA) and PTDA Foundation. previously serving as the President of the PTDA Foundation Board of Trustees. Additionally, Ross is also a volunteer for the Power-Motion Technology Representatives Association (PTRA). Presently Barbara serves on the PTDA Foundation Board of Trustees and PTRA Board of Directors among other committees for the organizations. Ross’ exceptional leadership ability comes through in every organization she joins. This unwavering commitment has earned her prestigious recognition, including the PTDA Warren Pike Award for lifetime achievement in the power transmission/motion control (PT/MC) industry and the PTDA Foundation Wendy B. McDonald Woman of the Year Award. “Barbara is joining Pfannenberg at an exciting time of our growth trajectory,” continues Rogalski. “Her reputable leadership will be an indisputable value add to our community of trusted advisors, further fueling the speed at which we are able to innovate and engage our customer base.”
Millwood Inc. opens new location in Lordstown Ohio
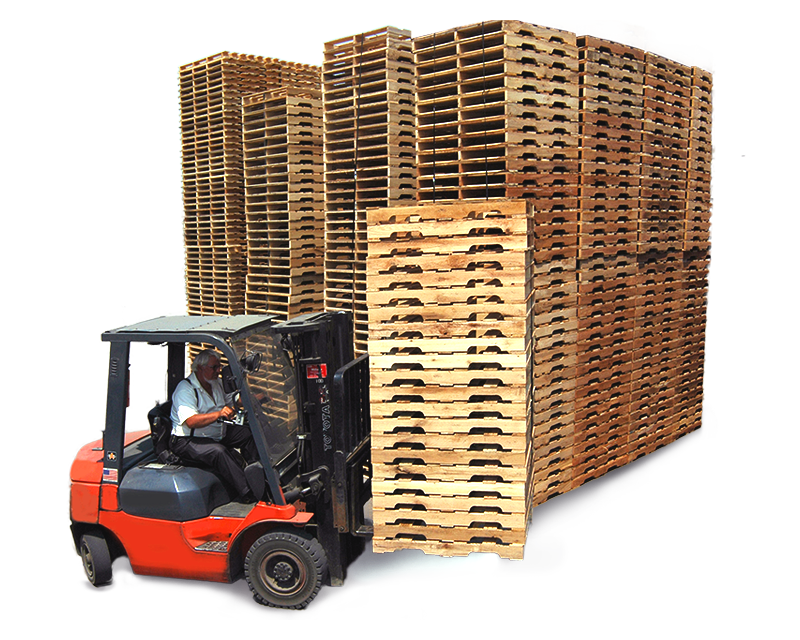
New location to employ nearly 20 new team members Millwood, Inc. has opened its 39th location nationwide in Lordstown, OH, just minutes from its corporate headquarters in Vienna, OH. A team of 16 team members will operate the 43,200 square-foot space at 5232 Tod Ave SW Warren, OH 44481 including a chaplain who will be available 24/7 to meet their personal, professional and spiritual needs. “We are excited about this new operation as it will expand our coverage area across different regions in the U.S.,” General Manager Lionel Trebilcock said. “Equipment is being installed, and we plan to begin shipping product from the operation by the end of September.” Through various, ongoing relationships with many carriers, this location will serve customers in the Midwest, Northeast and Southeast regions of the U.S. “The operations group has worked tirelessly to get this operation up and running at maximum capacity,” Vice President of Sales Lee Evans III said. “The sales team is excited to have another protective packaging product manufactured by Millwood to support our customers’ increasing demands for streamlined solutions.”
What’s the future for piece-picking robots?
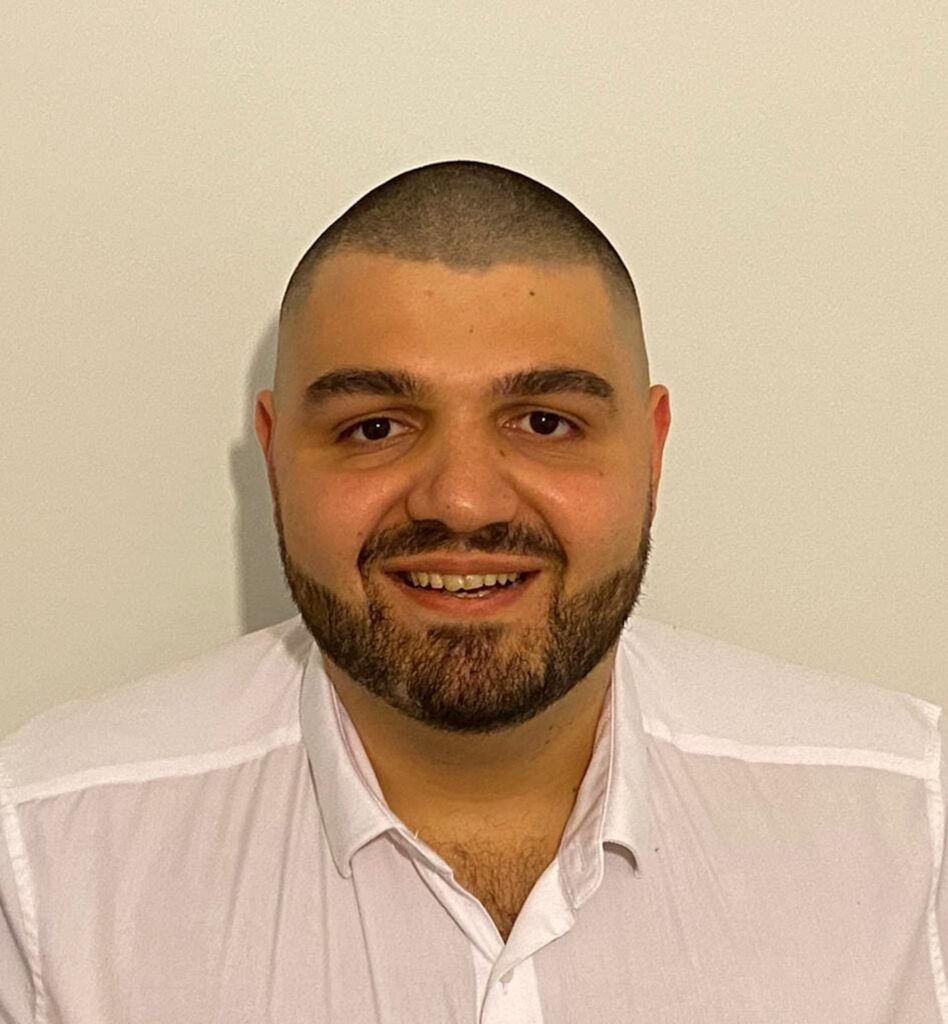
Piece-picking robotics is making big strides in the warehouse and with the aid of AI could soon be within the grasp of SMEs. Dan Migliozzi, Head of Sales at independent systems integrator, Invar Group, sets out where we are on the journey What news can there possibly be around piece-picking robots? Arm finds item, picks it up, manipulates or orients it, puts it in the right place – end of. It’s the classic application of industrial robotics and has been so, at least on high volume production lines, for four decades. But in a sense, that application is barely robotics at all – functionally, an old-fashioned juke box did much the same thing, and the machine typically can only work with one or a very limited set of items, presented to it in a very structured way. As early investors in robotics discovered to their cost, these ‘general purpose robots’ were in practice highly task-specific and although they have become essential in high volume production, they have been of limited utility in the warehouse and similar situations where the need is to pick from a very wide range of items varying in shape, size, robustness and orientation. Now, however, and seemingly overnight – although in reality these developments have been years in the making – advances in sensors, vision systems, handling devices and the means of controlling them, including the beginnings of Machine Learning (ML) and Artificial Intelligence (AI), are making general purpose picking robots a practical reality. For Invar, as a leading independent systems integrator, this is becoming a very exciting space. Presented with a mixed selection of items, the robot can now identify the correct piece, either by scanning a barcode or RFID signal, or purely by analysing the input from a vision system. Either way, algorithms can work out the current and required orientation. The robot can handle the piece according to parameters ‘attached’ to the identity of the piece, including what tool to use to pick the piece up, and how much force is appropriate – or in the case of increasingly popular manipulation by vacuum suckers, which elements from an array of suckers to use, and how much suction to apply. Using developing forms of ML/AI, the robot can be ‘trained’ to deal with novel items, and even optimise its own operations. This is important for many industries and companies because up to now, piece part picking has tended to be highly labour-intensive and stubbornly resistant to automation. Many parts were awkwardly shaped, too fragile, too small or there was too large a range of sizes/weights. Also, they might require prior operations to present them in the right orientation for the robot or there may be quality issues which require pre-screening, and so on. In these circumstances any return on investment in automation has often seemed nebulous, and manual labour has often been preferred. But now, not only is human labour scarce and increasingly expensive, manual pick rates may be slow by comparison with more advanced forms of automation, with high numbers of errors – often exacerbated by illness or fatigue. A business operating in, for example, direct to consumer pharmaceuticals, a growing field, cannot tolerate less than 100% accuracy. Similarly, there is no ‘acceptable’ level of damage to electronic components and this can’t be guaranteed with manual systems. However, the good news is, item picking technology is moving ahead at quite a pace and is fast becoming affordable to SMEs, with a reasonable ROI. So, as labour continues to be hard to find and costly, piece picking robots are likely to become more and more attractive, and when allied to the availability of highly scaleable Autonomous Mobile Robots (AMRs) can represent a significant de-risking of the business. There are a number of options as to how picking robots are deployed. Picking arms may be in fixed locations with goods reaching them on conveyors, AMRs, mobile racking, carousels or the like – and completed picks similarly removed. Or they may rove the warehouse floor mounted on AMRs. They may be designed as cobots, specifically to work safely alongside people, or they may be ‘fenced off’ – physically, or through software and safety features. There is a further important point of consideration. As noted, previous piece-picking robots have often required goods to be presented in closely defined orientations. For example, so that the barcode can be scanned, or the shape recognised, or so that they don’t overlap. This can require either manual intervention or an array of handling devices that in sum may be as complex and expensive as the robot itself – they also take up a lot of space. It is increasingly likely that with advanced, AI-enabled vision and other systems, much or all of this preparation can be dispensed with. Piece-picking robots are becoming far more dextrous, quick-learning and adaptive. But, of course, there is still a need to train the robots with the right images and algorithms. It’s fair to say that both suppliers and integrators are actively engaged in working out the most effective ways of organising this, but what is evident to us is that, at this stage in the development and adoption of the technology, there is a real need for open collaboration between all the travellers on this journey into robotic picking. As independent integrators of advanced warehouse technology with a dedicated division of software developers, we are closely involved in the fast-evolving field of piece-picking robotics and in progressing the smooth interface between robots, controllers and warehouse management systems. Further independent advice on transforming operational performance in the warehouse can be found at: www.Invargroup.com About the Author: Invar Group, headquartered in Cranfield UK, is focused on delivering complete turnkey warehouse automation solutions using advanced technologies such as industrial robotics, AMR goods-to-person solutions, pick-to-light technology, sortation systems, as well as conventional warehouse automation. The Group comprises: Invar Systems, a developer of warehouse control and management systems; Invar Integration (Greenstone Systems), a front runner in solutions design, hardware integration and project management; and Invar
Ports of Los Angeles-Long Beach and Shanghai unveil Implementation Plan Outline for first Trans-Pacific green Shipping Corridor
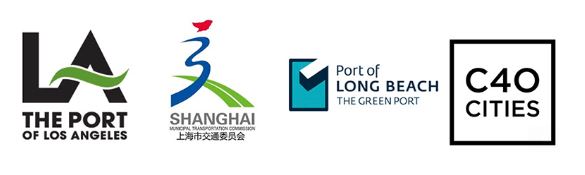
A voluntary partnership of leading maritime goods movement stakeholders, including the Ports of Los Angeles, Long Beach and Shanghai, some of the largest shipping lines in the world, with input from leading cargo owners, have developed a Green Shipping Corridor Implementation Plan Outline to accelerate emissions reductions on one of the world’s busiest container shipping routes. Plan development was supported by C40 Cities, the global network of mayors working to deliver the urgent action needed to confront the climate crisis. C40 is the facilitator of the Green Shipping Corridor, providing support to the cities, ports and their corridor partners by coordinating, convening, facilitating, and providing communications support in furtherance of the corridor’s goals. Carrier partners supporting this plan have set goals to begin deploying reduced or zero lifecycle carbon capable ships on the corridor by 2025. The creation of the first-ever green shipping corridor across the Pacific is taking shape. Today, a voluntary partnership of leading maritime goods movement stakeholders, including the Ports of Los Angeles, Long Beach and Shanghai, some of the largest carriers in the world, and key leading cargo owners unveiled a Green Shipping Corridor Implementation Plan Outline to accelerate emissions reductions on one of the world’s busiest container shipping routes across the Pacific Ocean. The plan is the first of its kind and was developed with support from C40 Cities as part of its effort to reduce carbon emissions from the largest cities in the world. The plan is an important step toward decarbonizing the global supply chains that power our economies, and transitioning toward zero lifecycle carbon emission ships. It will showcase cutting-edge goods movement technologies, decarbonization applications and best management practices to enhance efficiency, and catalyze technological, economic and policy efforts to progressively decarbonize shipping and port-related activities. As part of the historic plan, the carrier partners will begin deploying reduced or zero lifecycle carbon capable ships on the corridor by 2025, and work together to demonstrate by 2030 the feasibility of deploying the world’s first zero lifecycle carbon emission container ship(s). Carrier partners include CMA CGM, COSCO Shipping Lines Co., Ltd., Maersk, and ONE. Core partners include the Shanghai International Port (Group) Co., Ltd., the China Classification Society, and the Maritime Technology Cooperation Centre of Asia. Participants of the Green Shipping Corridor Partnership will take steps to reduce carbon emissions and harmful pollutant emissions impacting air quality, through methods such as expanding use of shore power and supporting the development of clean marine fueling infrastructure. Cargo owner partners have set goals to contract with carriers to use zero lifecycle carbon emission shipping services, and in an effort to measure progress toward decarbonization, all partners will develop metrics to track decarbonization progress. Gene Seroka, Executive Director of the Port of Los Angeles, said: “This trans-Pacific green corridor will be a model for the global cooperation needed to accelerate change throughout the maritime industry. Reducing emissions in this corridor will yield substantial reductions. For perspective, most of the emissions associated with moving cargo by ship occur in the mid-ocean part of the journey between ports. This corridor will help reduce mid-ocean emissions while continuing the work we have done to cut emissions within our ports.” Mario Cordero, Chief Executive Officer of the Port of Long Beach, said: “This initiative will drive emissions reductions across the world’s largest ocean and lead to greener practices from supply chain participants along these vital trade routes. The new and innovative vessel technologies, increased availability of sustainable fuels and better practices created through this green corridor will also impact society’s transition to a cleaner future far beyond the areas served by our ports.” Mark Watts, Executive Director of C40, said, “C40 is proud to support this first-of-its-kind green shipping corridor aimed at demonstrating that zero-carbon shipping at scale is feasible by 2030, and that less polluting ships and ports will also mean cleaner air, less noise and more jobs for local communities.” Read the Green Shipping Corridor Implementation Plan Outline. Watch a video about the Green Shipping Corridor.
Bobcat introduces E40 Compact Excavator; new model numbers for 3-to-5-ton excavators
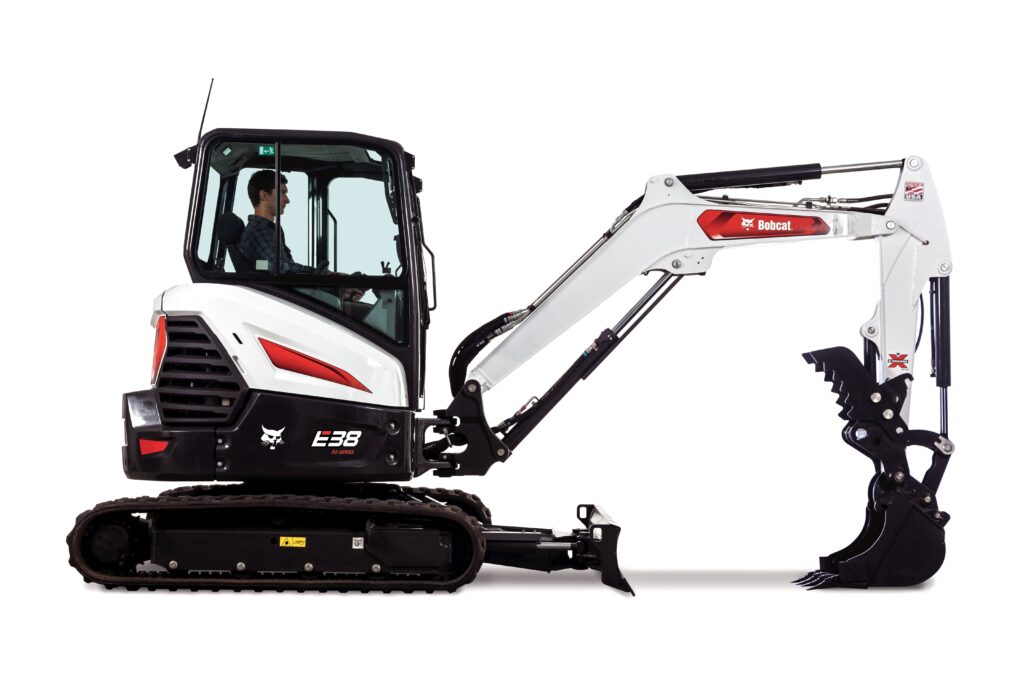
Bobcat Company, a global manufacturer of compact equipment, has expanded its lineup of compact excavators to include the newly released Bobcat E40. As part of the lineup expansion, Bobcat has also revised the model numbers for its 3-to-5-ton excavator lineup to more closely align with the industry’s size class. With the E40, operators get high performance, fast cycle times and optimal maneuverability with practical features and pricing to match. It’s a minimal tail swing excavator, with less than two inches of overhang and a standard long arm. The E40’s lift capacity is among the best in its class. It delivers an over-the-blade lift capacity and over-the-side lift capacity that competitors can only achieve – or come close to – with conventional tail swing models. The E40 is an ideal jobsite solution for those who demand leading performance, convenient trailering and the maneuverability to complete challenging work in confined jobsites. The E40 offers premium performance with simplified option packages for base-level pricing. Features of the new E40 include: Powerful non-DPF, turbocharged Bobcat engine Standard long arm High lift capacity and powerful slewing performance Dual-flange track roller system for improved lift performance and a smoother ride Standard low-effort joysticks, LED lights and integrated lift eye Extensive attachment versatility The E40 will be available in late 2023. Bobcat will preview the E40 in booth 3052 at Equip Exposition, Oct. 17-20, in Louisville, Ky. Updated Model Numbers With the introduction of the new E40, Bobcat has revised select model numbers in its 3-to-5-ton excavators’ size class to better reflect the machines’ size and performance within the industry. “Our compact excavator lineup within the 3-to-5-ton size class has grown, and the updated model numbers better reflect the outstanding performance capabilities that empower our customers to accomplish more each and every day,” said Mike Wetzel, director of product development at Bobcat Company. “The updated portfolio more closely aligns with the excavators’ capabilities when compared to other machines within the same size class.” The model number changes are as follows: The 33-hp Bobcat E35 has been renamed the Bobcat E38. This zero tail swing excavator provides for unobstructed rotation while the turbocharged engine and proven Bobcat hydraulics produce the digging, lifting and slewing capabilities you might expect in a larger, less maneuverable compact excavator. The 25-hp Bobcat E35 will retain its model designation. The Bobcat E42 has transitioned to the Bobcat E48. The conventional tail swing E48 is a well-balanced machine, delivering the horsepower, precise controls and comfort for increased productivity and first-rate jobsite results. The Bobcat E50 has been renamed the Bobcat E55. A minimal tail swing excavator with less than one inch of overhang, the E55 puts more power and controllability in a compact package—all designed to support faster cycle times and take operator productivity to the next level. With these changes and the launch of the E40, the Bobcat 3-to-5-ton compact excavator lineup now includes: E32, E35, E38, E40, E48 and E55. Bobcat offers compact and larger excavators ranging from 1-2-ton to 16-18-ton size classes, as well as battery-electric excavator models. To see the full lineup of Bobcat excavators, visit bobcat.com.
Percentage of female technicians shows substantial increase
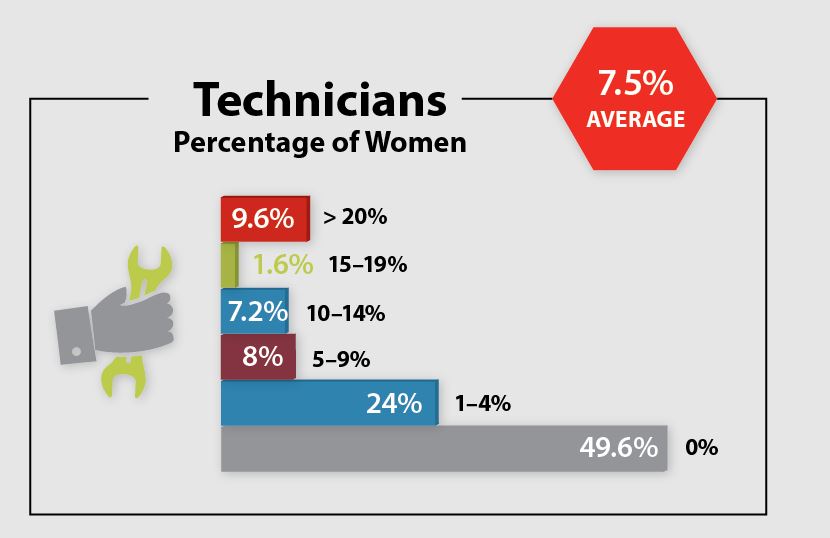
According to new data from the 2023 WIT Index, which was released recently by the Women In Trucking Association (WIT), the percentage of female equipment technicians in corporations with for-hire or private fleets in the commercial freight transportation industry has shown a substantial increase. The WIT Index is the industry barometer to benchmark and measure each year the percentage of women who make up critical roles in transportation. The 2023 WIT Index shows that more than 7% of technicians in companies in transportation are women. This number reflects an increase of nearly 4% from the reported 3.7% of women in technician roles in the 2022 WIT Index. “A major concern of the trucking industry is the widely reported shortage of professional truck drivers, who play a vital role in the U.S. economy by safely transporting the nation’s freight,” said Jennifer Hedrick, president and chief executive officer of WIT. “But drivers cannot complete that mission when their trucks are in the shop or broken down on the side of the road – whether it’s caused by a problem with the engine aftertreatment system, an electrical issue, or a problem with the truck’s brakes. That’s when it becomes abundantly clear that skilled truck maintenance technicians are indispensable in keeping professional drivers productive, on the road, and delivering on-time.” Initiated in 2016, the WIT Index is based upon reported statistics by companies in transportation, including for-hire trucking companies, private fleets, transportation intermediaries, railroads, ocean carriers, equipment manufacturers, and technology companies. Data involving the 2023 WIT Index was confidentially gathered from January through April of 2023 from 350 participating companies of various sizes operating in the trucking industry. Percentages are reported only as aggregate totals of respondents rather than by individual company. In 2022, WIT expanded its collection of the percentage of women to include not only technicians but also operations, human resources and talent management. The WIT Index historically also has identified the percentage of women who are in leadership roles and professional drivers with the commercial freight transportation industry. For more information on the WIT Index and to download a full executive summary of the 2023 WIT Index findings, visit https://www.womenintrucking.org/index. Click here for Technicians – Percentage of Women
Anand Raghavendran: Transforming supply chain documentation with AI Power
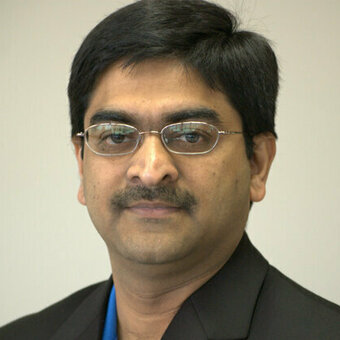
Industry Veteran Shares Vision for AI in Logistics Processes KlearNow, a company specializing in Artificial Intelligence (AI)-powered logistics and supply chain solutions, recently announced the appointment of Anand Raghavendran as its new Chief Product Officer. Raghavendran brings over 25 years of valuable experience to his new role and is expected to continue driving the KlearNow team in their pursuit of modernizing traditional supply chain processes. Raghavendran has a comprehensive background in leading product and technology teams, which has been integral to his success in the industry. His history of creating and guiding high-performance teams to achieve transformative results has been recognized and lauded in the sector. At KlearNow, Raghavendran’s extensive experience is anticipated to significantly bolster the company’s strategy for innovation-driven growth. KlearNow stands to benefit from the integration of Raghavendran’s vast experience into its operations. This will ideally enhance the maturity, market-friendliness, and relevance of its AI-driven solutions. Raghavendran has expressed enthusiasm for his new role, stating his desire to act as the crucial link between the end users and the engineering teams at KlearNow. He is dedicated to delivering a product that will maintain and potentially increase KlearNow’s market impact. “As we continue to build on KlearNow’s capabilities, my goal is to establish a framework that offers a seamless end-to-end user experience. This involves packaging our product to ensure consistency and trust, provide enhanced visibility, and become the single source of truth for supply chain data for Enterprises as well as SMBs. It’s about blending the strength of our technology with the needs of the industry to create transformative solutions,” said Raghavendran. Raghavendran has identified KlearNow’s AI capabilities as its market differentiator, the KlearNow platform is capable of not just extracting data from unstructured sources with high accuracy, it also creates a meaningful shipment grouping from these documents for faster customs clearance. “This makes us unique from other OCR-based solutions in the market,” said Raghavendran. KlearNow has already demonstrated its prowess in solving key domain problems, such as centralizing data sources, enhancing visibility and cost-efficiency, and obtaining the endorsement of respected names in the industry. These achievements set KlearNow apart in a highly competitive market. With respect to competition in the industry, Raghavendran recognizes the importance of constant evolution and improvement. He pointed out, “While KlearNow does have a distinct advantage with our AI-driven solutions, we cannot afford to rest on our laurels. Anticipating potential advancements from other market players is key. We need a balanced strategy that involves both proactive innovation and reactive adaptation to maintain our leading position in the supply chain industry.” KlearNow has built a reputation for its AI-based supply chain solutions, which has contributed to its substantial growth. The company has steadily increased its client base (currently over 1350), a testament to its commitment to delivering efficient and reliable solutions. As it continues to develop and innovate, KlearNow remains dedicated to modernizing the supply chain industry.
PLA announces opening of Northwest Arkansas Pallet Management facility
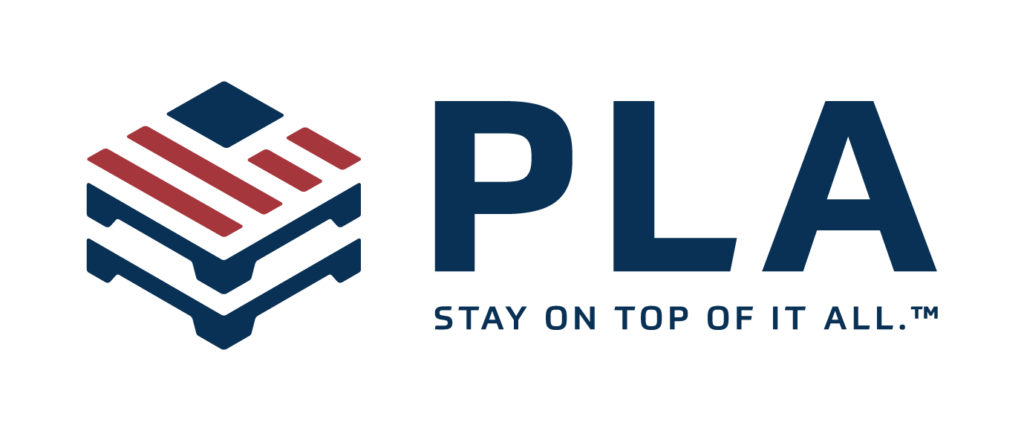
New location further expands PLA’s nationwide pallet, logistics, and supply chain services capabilities PLA, a portfolio company of Silver Oak Services Partners, LLC (“Silver Oak”) has announced the opening of its newest pallet services operation in Northwest Arkansas. The new PLA pallet operation is co-located with an existing Propak facility in Siloam Springs, AR and adds new and recycled pallet supply, repair, and retrieval services to the reverse logistics, transportation, and 3PL services provided to customers throughout the greater Northwest Arkansas area. Conveniently located just off I-49 and I-40, this location will serve PLA’s supply chain customers across a 150-mile radius. The nearly 30,000 square foot facility will process over 1.5 million pallets annually. “PLA continues to expand both our infrastructure and our service offerings across the country,” said Kyle Otting, PLA’s CEO. ”Propak has been providing comprehensive logistics solutions to customers across Northwest Arkansas for nearly 25 years, and we’re very pleased to expand our services to include pallet management for the area.” The new operation will bring approximately 20 new jobs to the area and is located at 701 East Kenwood Street, Siloam Springs, AR 72712.
Combilift Comb-LC crafted to cater to the intricate load handling demands of large-scale offshore wind turbine manufacturers
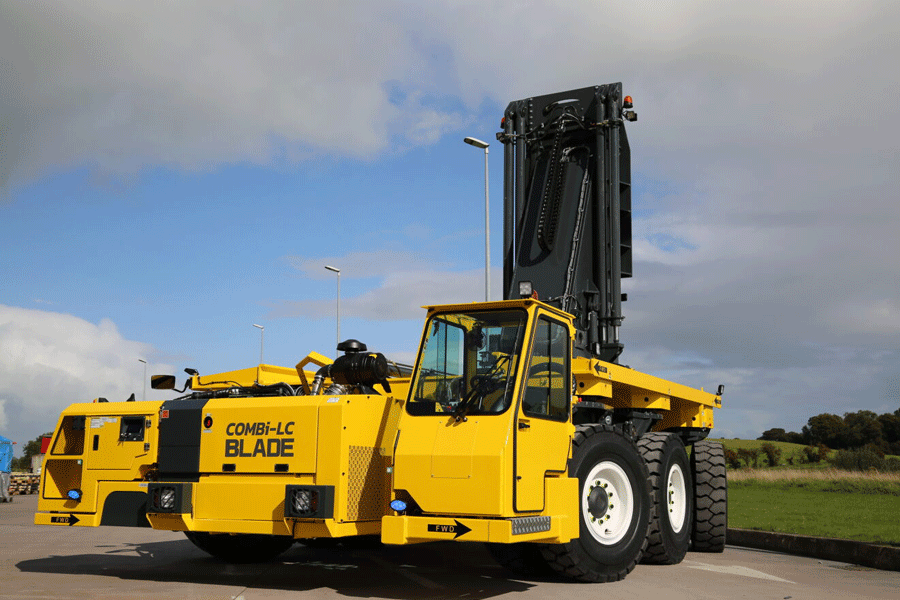
The Combi-LC facilitates the transport of wind turbine components, handling lengths of up to 115m and weights of about 70t. This system streamlines the movement across production stages and to storage sites, even spanning distances of up to 5km. As the green energy sector continually pushes the boundaries of height and size for components like wind turbine towers and blades, there arises an ever-growing need for novel methods to transport these finished products from the manufacturing facility to the storage yard before dispatch to their intended destinations. Combilift has collaborated with industry giants in this sector to engineer stable and highly efficient lifting solutions for these challenging and exceptionally valuable loads, culminating in the creation of the Combi-LC. The Combi-LC carrier unit boasts a unique attachment designed to securely grip the substantial cylindrical end of the blade, firmly affixed to the generator hub. This robust machine, powered by a 75-ton capacity diesel engine and equipped with 12 wheels, offers versatile multidirectional steering with 6 wheels. What sets it apart is its “tip side” carrier unit, which smoothly maneuvers beneath the blade, supporting it via a hydraulic tilting table-mounted clamp toward its narrower tip. Notably, this root side unit represents the first Combi-LC iteration to feature a cab, a customization made at the request of our customers. This addition proves invaluable, especially when traversing the 5km distance to reach the storage yard. When not engaged in lifting duties, the cab-equipped Combi-LC can travel at an impressive 10km/h, significantly expediting the operator’s commute. It’s worth mentioning that these units often operate in demanding environments with less-than-ideal ground conditions, making their robust design and adaptability all the more essential.
Microcrane® integrates with pure cycle water’s new reclamation facility
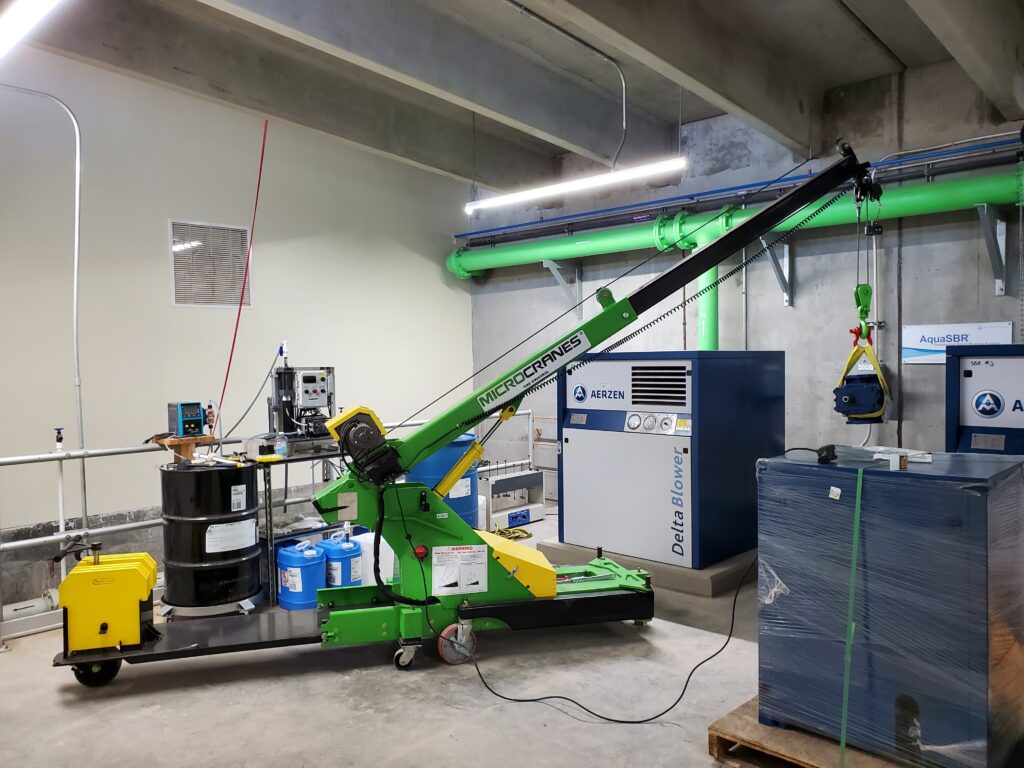
Microcranes, Inc., a portable mini crane producer in the USA, provides indoor and outdoor green energy lifting solutions to a variety of industries. Pure Cycle Water/Rangeview Metro District, located in Colorado, finds the battery powered Microcrane® unit useful for maintenance lifting tasks at their new state-of-the-art water reclamation facility serving Sky Ranch in Denver. Pure Cycle is a vertically integrated water and wastewater resource development company. As a vertically integrated company, they also own and manage a full ecosystem of facilities needed to withdraw, store, treat, deliver and collect water and wastewater. Their goal is to provide sustainable, high-quality water to their customers and make prudent use of reclaimed water for outdoor irrigation and industrial demands. Sky Ranch Water Reclamation Facility is their latest $10 million, state-of-the-art water reclamation facility completed in 2020, serving Sky Ranch, a master-planned community providing residential, commercial, retail, and light industrial lots along Denver’s booming I-70 corridor. The facility uses the latest green technology which includes dispensing highly treated reclaimed water for irrigation and other uses, active odor control technology; and green roofing will cover 90% of the main plant. Green energy is a constant theme, including within the maintenance department. The battery powered M1 Model Microcrane® is being used for maintaining Aerzen blowers, pulling pumps out of basins and preforming various lifting jobs throughout the plant. The compact, flexible mini crane requires no fuel, emits zero fumes and has low sound levels. “The tightness of the working areas make it difficult to get people in place safely for manual lifts. The Microcrane® allows us to accomplish maintenance tasks with ease and with only one person!” said Mike Dean of Pure Cycle Water.
At SMTA Guadalajara, IDENTCO to showcase new Automated Wire Marking System and tout local engineering expertise
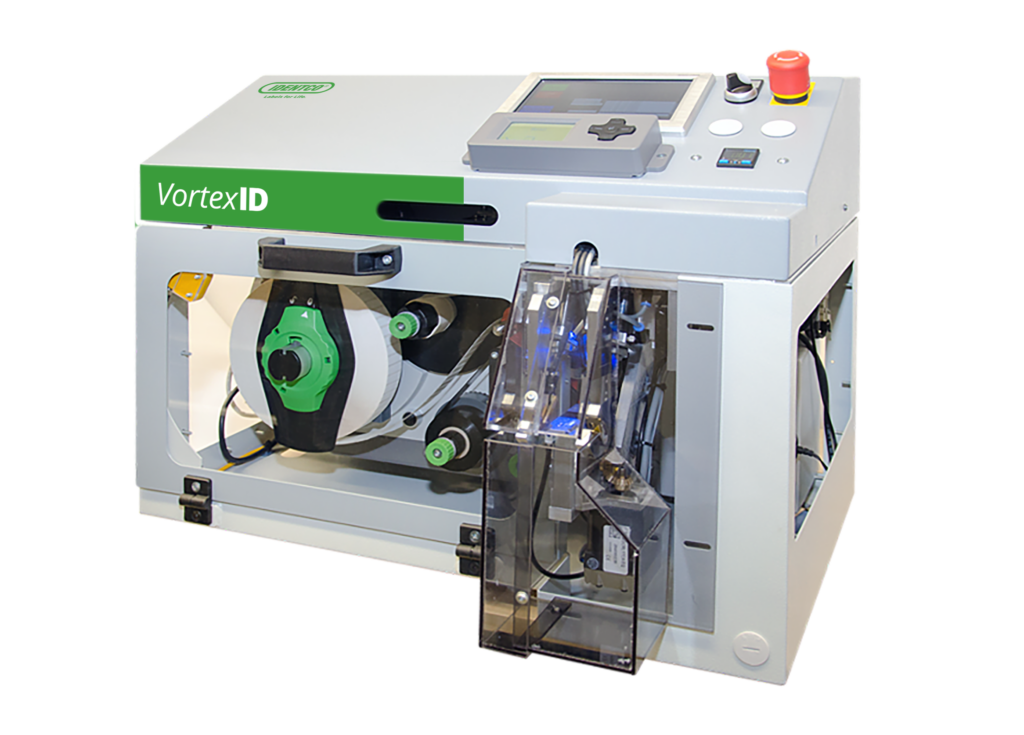
IDENTCO, a manufacturer of high-performance labeling solutions for the power equipment, electronics, transportation and general industrial sectors will feature its rugged new automated wire marking system at SMTA Guadalajara, October 25-26, 2023. At Booth 1214, the company will offer live demonstrations of VortexID, whose stamina and speed raise benchmarks for wire and harness label application. This marks the first time IDENTCO is exhibiting the new solution, which entered the marketplace earlier this year. In addition, in advance of the show, IDENTCO has announced that one of its longstanding label application engineers, Cesar Ramos, is relocating to the Guadalajara area. The move provides existing and potential customers in the region with even more hands-on, optimized service. VortexID can precisely place up to 20 labels per minute – outpacing other automated units and doubling the output of even the most efficient manual setups – and operate 24/7, a welcome upgrade from the continuous use limitations of many label applicators. The machine can handle a variety of American wire gauge sizes (AWGs), making is suitable for a broad array of sectors whose products incorporate wires and harnesses – particularly automotive and electronics components manufacturing. It offers high-resolution, 300dpi printing capabilities, with labels applied via a vacuum plate whose rotating mechanism ensures reliable application to cylindrical products. Notably, IDENTCO’s VortexID is materials agnostic, expanding customer choice and potentially decreasing overall materials costs. The unit can apply both self-laminating and flag labels, an attractive two-for-one modularity accomplished by an interchangeable applicator. This versatility by design is another differentiator, providing customers with a flexible solution that eliminates the need to purchase specific machines for each label type. For both types, the VortexID’s application consistency and repeatability ensure neat, secure labels whose crucial product traceability and electronics testing information must be pristinely printed and unobscured. Still, the new unit’s robustness may be its most groundbreaking strength. While most automated applicators in its space max out at eight hours of continuous use, VortexID can operate continuously, processing thousands more products per day. “With demand surging, customer needs for high-volume wire and harness manufacturing continue to rise, prioritizing solutions that automate key processes along the production line – including the labeling process,” said Cesar Ramos, Label Application Engineer for IDENTCO. “We designed the VortexID automated wire marking unit with speed and durability in mind, combining high throughput and continuous operation with precision printing and label placement for long-term information readability.”
Elevating logistics: Discover the power of METTLER TOLEDO’s TLD970 Dynamic Pallet Dimensioner
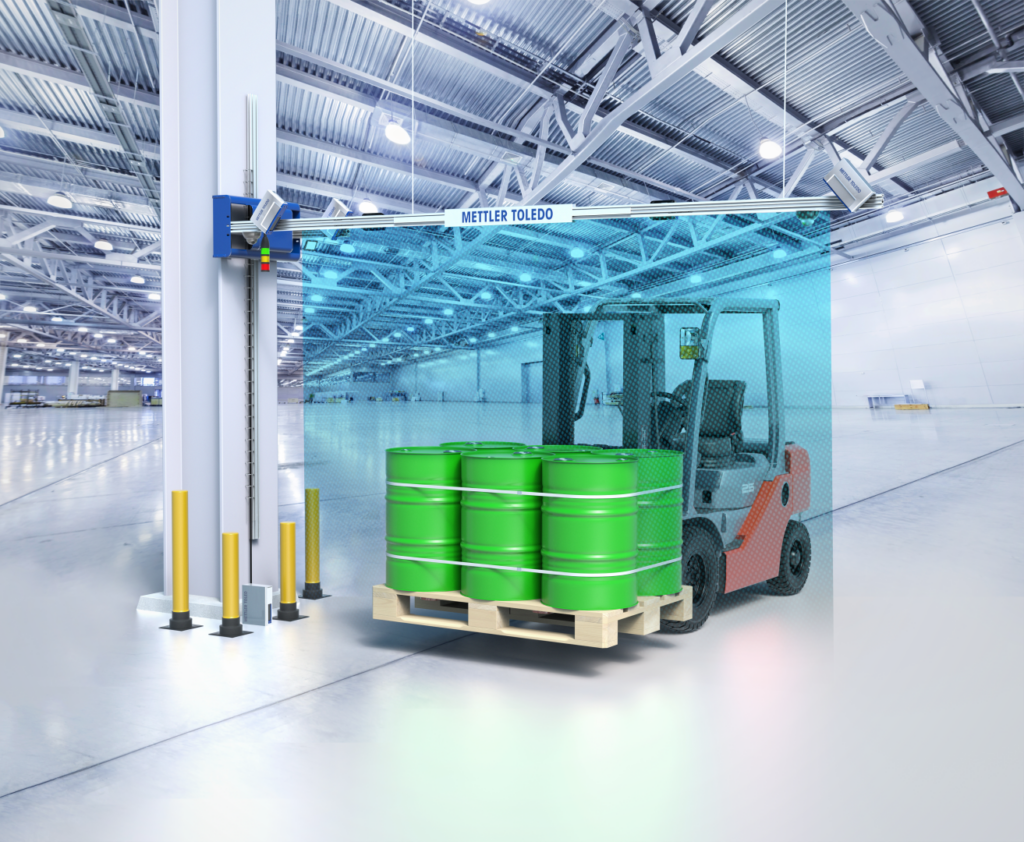
The dimension-in-motion technology of the TLD970 represents a revolutionary advancement, automating the precise capture of cargo dimensions in a groundbreaking manner. Precisely knowing the length, width, and height of each handling unit is critical for optimal utilization, accurate customer billing, and customs regulations. Utilizing light detection and ranging (LiDAR) technology, the TLD970 provides the measurements of a single cargo item within seconds regardless of lighting conditions, enhancing pallet handling efficiency while conserving precious labor resources. The TLD970 is NTEP and MID approved to measure all pallet shapes, including irregulars at speeds up to 10 mph/15 kph. There are multiple customer success stories from companies who have used METTLER TOLEDO’s dimensioning technology. One transportation and logistics company reported that the TLD970 system maximizes revenue recovery on 100% of pallets. The company was able to process up to 720 pallets per hour, tripling the productivity of their previous throughput. Another METTLER TOLEDO customer, who is a Top 5 Global Freight Handler, announced that it has been able to capture dimensions on over 95,000 shipments of all shapes and sizes per day, which is over 85% of all shipments. Find more details on customer testimonials here. Combining the TLD970 Dynamic Pallet Dimensioner with METTLER TOLEDO’s robust TLF820 Forklift Scale enables customers to capture all critical cargo information in a seamless, safe, and efficient way, facilitating accurate billing, optimized utilization of cargo space, and simple compliance. Experience the power of precision, efficiency, and automation with reliable pallet dimensioning, weighing, and scanning solutions that elevate your cargo handling capabilities to new heights. Click here to learn more.