Combilift launches world’s first autonomous sideloader with the option to operate manually
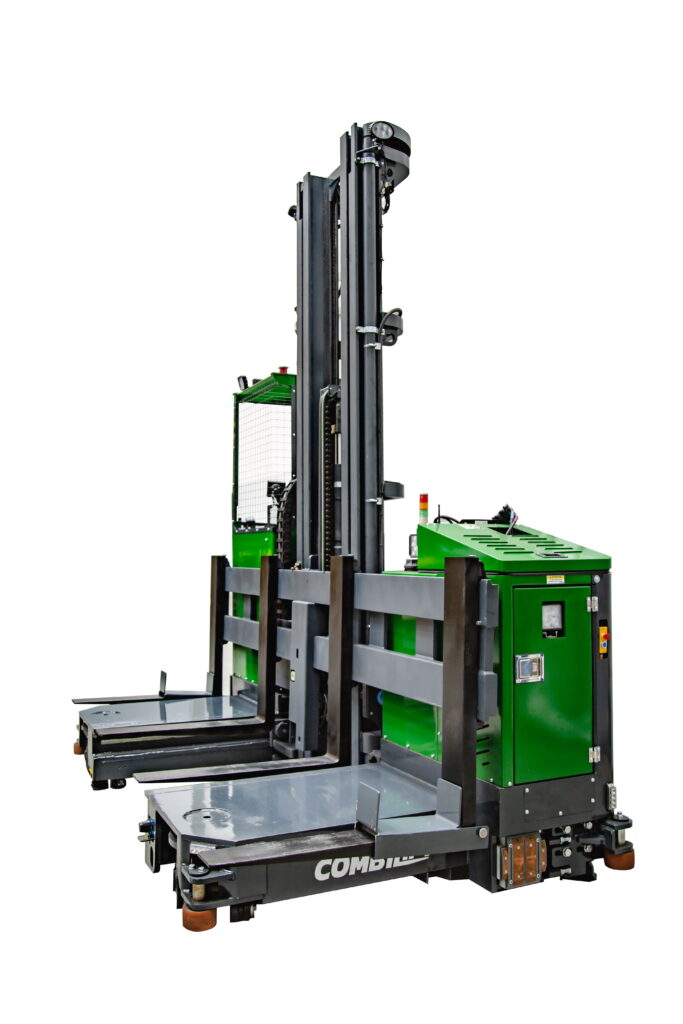
Irish materials handling manufacturer Combilift has launched its first autonomous vehicle at the annual Fabtech trade show. Developed by Combilift’s dedicated automation team, the Combi-AGT is a 4-wheel electric stand-on model, which is the world’s first autonomous dual operational sideloader for long loads. Celebrating 25 years in business, Combilift is acknowledged as being at the forefront of innovation in the global material handling sector with its wide range of customized products, and the Combi-AGT harnesses the very latest smart technology to meet customer demands for driverless sideloader capability. These were driven in part by safety to eliminate the presence of personnel in aisles, consistency in handling procedures and to maximize order fulfilment, while also having a backup manual mode in case of power outages or internet disruptions. Combilift’s automation team has spent three years liaising with specialist steel suppliers to identify the best specifications for the Combi-AGT. The new model, with a lift capacity of 5,000kg/11,000lbs and various lift heights, addresses the requirements of steel service centers and the metal industries, which typically handle long loads. Combilift worked in tandem with IMR (Irish Manufacturing Research) during the development process to enable seamless integration with multiple client warehouse management systems. Its design is based on the electric manually operated Combi-GTE model which has long been a very popular choice for service centers due to its ability to work efficiently in rail guided narrow aisles. The first Combi-AGT unit was supplied to Kansas based Steel and Pipe Supply 18 months ago, and since then Combilift have collaborated with a number of leading metal service centers across North America during the development process. The laser-based sensors, fitted at various positions on the chassis, constitute of an anti-collision safety system, as required by the American National Standards Institute. If the machine senses an obstacle or pedestrian that has entered its path, it automatically slows down and will, if necessary, stop in cases of emergency, it will then continue to drive automatically when the obstacle has cleared its safety sensor area. The enhanced adaptive safety system enables the size of the obstacle detection fields to increase or decrease as per the steer angle and speed of the truck. The natural feature navigation system is superior to traditional methods of truck navigation based on wire guidance or artificial landmarks such as reflectors. Instead, it uses the naturally occurring features in a warehouse – walls, racking and columns for example, avoiding the need to add to or change the warehouse infrastructure. Its newly developed load dimension detection system (patent pending) operates by performing a laser scan of the load to check that its length matches the task sent to the machine. Similarly, when unloading, it checks that the rack in front has sufficient free space to accept the load. Combilift CEO and Co-founder Martin McVicar said: “We have deliberately not rushed into incorporating autonomous products into our portfolio. As with any new launch we have carried out extensive field tests to make sure it is fit for purpose by liaising with a number of leading customers in the metal service industry during the product development stage. We are fortunate to have a very motivated group within our autonomous team of software and mechatronics engineers who are committed to scaling this business unit. The Combi-AGT signals a new milestone in product development with further expansion of our autonomous range in the pipeline.” In 1998 Combilift originally made history with its world-first multidirectional C8000 3-wheel, all-wheel drive forklift. 25 years on the company is still challenging the market and the Combi-AGT is no exception.
Episode 419: Navigating Fleet Electrification with Kevin Kushman of Electrada
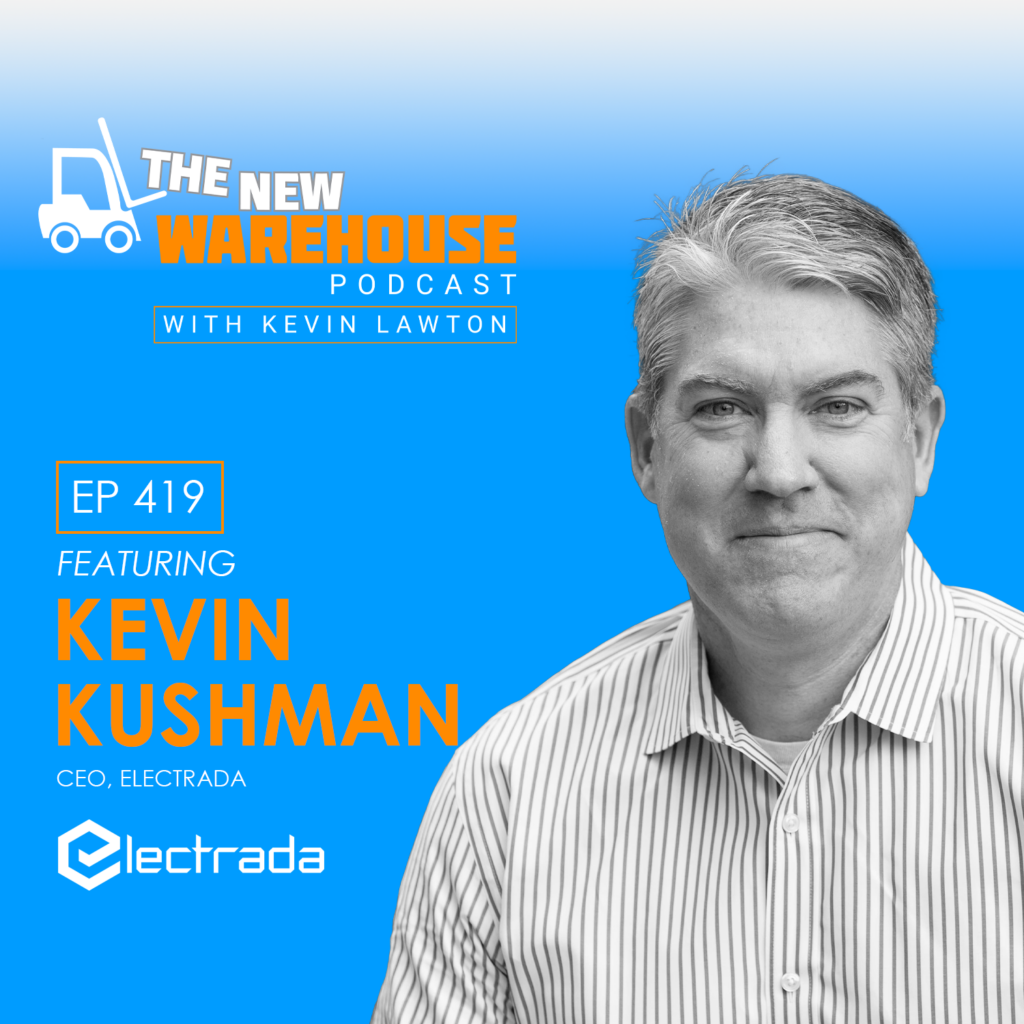
The New Warehouse Podcast is excited to bring insights from Kevin Kushman, CEO at Electrada. Kevin is a leading authority in fleet electrification. Electrada is a trailblazing company helping warehouse operators seamlessly transition to electric fleets. If you’re grappling with how to steer your warehousing operations into the future of electrification, this is a conversation you can’t afford to skip. Energy Planning: The Critical Backbone of Fleet Electrification Kushman couldn’t emphasize it more: “When you’re building out an electric fleet, you’ve got to start thinking about energy at the same time you start thinking about vehicles.” In an industry where time is money, delays in energy infrastructure can cost you dearly. According to Kushman, taking 8 to 12 months to deploy charging infrastructure is not uncommon. It’s clear that energy planning is not merely an ‘add-on’ but forms the critical backbone of your transition to an electric fleet. The planning shouldn’t be an afterthought but a parallel process to vehicle acquisition. Understanding the Challenges of Fleet Electrification Kushman offers caution for those thinking of going alone: “We’re finding opportunities to come in and help those folks.” He adds, “Electrada takes a surgical look at what we call load shape, which translates to what the energy capacity needs look like for fleets of all sizes and how that translates to power.” Challenges include: Multi-site interactions with utilities Inability to scale further Understanding the new realm of energy risks and the cost of power Bandwidth constraints Identifying the lowest cost per mile Bottlenecks in progress caused by the DIY approach Electrada develops and invests in the solution, acting as the infrastructure owner while providing charging as a service. This approach takes all risk away from the fleet owner, covering technology, reliability, and cost. 360 Charging as a Service 360 Charging as a Service is a comprehensive electric vehicle charging solution encompassing system design, operation, and maintenance under a multi-year contract. The service aims to provide reliable and sustainable electric fuel at a competitive cost compared to traditional fuels. Eliminating extra fuel stops also enhances operational efficiency. Kushman adds, “What we’re describing with 360 as a service is a fully wrapped, capitalized, and guaranteed performance environment where we come in and design the system.” Electrada is technology agnostic and requires technology providers to live up to the commitment of 99% uptime and are One Charge Point Protocol (OCCP) compliant. The focus is on demonstrating cost savings and reliability to facilitate the transition to electric fuel. Key Takeaways Robust energy planning should coincide with vehicle acquisition to avoid costly delays. Electrada offers a comprehensive charging service, acting as the infrastructure owner and risk-bearer, which provides clients with a predictable fuel cost under a performance contract, removing all technological and energy risks. Early consultation with experts can save you from common pitfalls and help you navigate the complex landscape of warehouse electrification. The New Warehouse Podcast EP 419: Navigating Fleet Electrification with Kevin Kushman of Electrada
AAR reports Rail Traffic for the week ending September 9, 2023
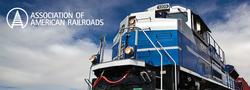
The Association of American Railroads (AAR) has reported U.S. rail traffic for the week ending September 9, 2023. For this week, total U.S. weekly rail traffic was 447,345 carloads and intermodal units, down 1.7 percent compared with the same week last year. Total carloads for the week ending September 9 were 218,101 carloads, up 0.6 percent compared with the same week in 2022, while U.S. weekly intermodal volume was 229,244 containers and trailers, down 3.8 percent compared to 2022. Six of the 10 carload commodity groups posted an increase compared with the same week in 2022. They included motor vehicles and parts, up 1,585 carloads, to 14,913; petroleum and petroleum products, up 1,416 carloads, to 9,734; and coal, up 866 carloads, to 68,367. Commodity groups that posted decreases compared with the same week in 2022 included grain, down 2,427 carloads, to 14,626; nonmetallic minerals, down 679 carloads, to 30,163; and forest products, down 514 carloads, to 7,840. For the first 36 weeks of 2023, U.S. railroads reported cumulative volume of 8,071,215 carloads, up 0.1 percent from the same point last year; and8,549,682 intermodal units, down 9.0 percent from last year. Total combined U.S. traffic for the first 36 weeks of 2023 was 16,620,897 carloads and intermodal units, a decrease of 4.8 percent compared to last year. North American rail volume for the week ending September 9, 2023, on 12 reporting U.S., Canadian and Mexican railroads totaled 323,563 carloads, up 0.0 percent compared with the same week last year, and 305,358 intermodal units, down 6.0 percent compared with last year. Total combined weekly rail traffic in North America was 628,921 carloads and intermodal units, down 3.0 percent. North American rail volume for the first 36 weeks of 2023 was 23,304,320 carloads and intermodal units, down 4.1 percent compared with 2022. Canadian railroads reported 89,460 carloads for the week, up 0.5 percent, and 64,914 intermodal units, down 13.2 percent compared with the same week in 2022. For the first 36 weeks of 2023, Canadian railroads reported cumulative rail traffic volume of 5,674,192 carloads, containers and trailers, down 3.4 percent. Mexican railroads reported 16,002 carloads for the week, down 9.4 percent compared with the same week last year, and 11,200 intermodal units, down 4.3 percent. Cumulative volume on Mexican railroads for the first 36 weeks of 2023 was 1,009,231 carloads and intermodal containers and trailers, up 4.7percent from the same point last year. To view the Rail Traffic charts, click here.
Rockwell Automation signs agreement to acquire autonomous robotics Clearpath Robotics
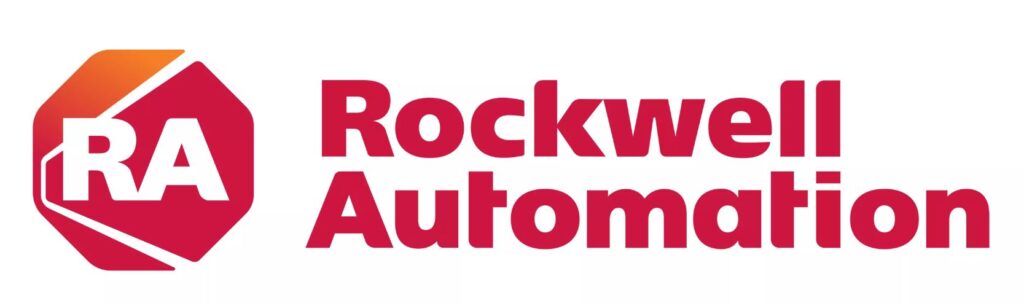
Acquisition to accelerate Rockwell’s end-to-end autonomous production logistics solutions, providing safer, more efficient manufacturing environments for customers Rockwell Automation, Inc. has announced it has signed a definitive agreement to acquire Ontario, Canada-based Clearpath Robotics Inc., a provider in autonomous robotics for industrial applications. Autonomous mobile robots (AMRs) are the next frontier in industrial automation and transformation, and this acquisition will supercharge Rockwell’s lead in bringing the Connected Enterprise to life. Transporting parts and materials to assembly lines and between manufacturing cells is one of the industry’s most complex and inefficient tasks, often resulting in production bottlenecks. Autonomous production logistics will transform the workflow throughout a manufacturing plant, enabling substantial reductions in cost and greater operational efficiency. Clearpath’s OTTO Motors Division offers AMRs and fleet management and navigation software, which dramatically increase throughput and reduce costs by ensuring components and subassemblies are in place when needed and by transporting finished goods to a truck or warehouse upon completion. Combined with Rockwell’s strong continuing partnerships in fixed robotic arms, solutions such as Independent Cart Technology, and traditional leadership in programmable logic controllers (PLCs), the addition of OTTO Motors’ AMR capabilities will create a complete portfolio of advanced material handling solutions unmatched in the industry. According to Interact Analysis, the market for AMRs in manufacturing is expected to grow about 30% per year over the next five years, with an estimated market size of $6.2 billion by 2027. This acquisition is expected to contribute a percentage point to Rockwell’s fiscal 2024 revenue growth. “Rockwell and Clearpath together will simplify the difficult and labor-intensive task of moving materials and product through an orchestrated and safe system to optimize operations throughout the entire manufacturing facility,” said Blake Moret, Chairman and CEO, Rockwell Automation. “The combination of autonomous robots and PLC-based line control has long been a dream of plant managers in industries as diverse as automotive and consumer packaged goods. With Clearpath, Rockwell is uniquely positioned to make that dream a reality across virtually all discrete and hybrid verticals, optimizing planning, operations, and the workforce.” Data from Rockwell’s offerings and OTTO Motors’ AMRs will be harnessed in artificial intelligence-powered Software as a Service information management applications, such as those by Rockwell’s Plex and Fiix businesses. With this, Rockwell will deliver a unified solution for manufacturing, enabling autonomous execution and optimization to increase efficiency and allow for traceability and real-time adjustments. The combined technology will also amplify Kalypso’s production logistics consulting practice. “Industrial customers are under ever-increasing pressure to do more with less. Autonomous production logistics is becoming a necessity to meet targets and stay competitive. We are excited to join Rockwell and help expand their leadership position in advanced material handling,” said Matt Rendall, co-founder and CEO of Clearpath. “Together, we will create safer and more productive workplaces with autonomous technology.” Founded in 2009, Clearpath got its start offering robotics technology to global research and development markets, and in 2015, launched its OTTO Motors Division. The acquisition will be funded by a portion of the proceeds from the sale of Rockwell’s investment in PTC. It is subject to customary regulatory approval and is expected to close in the first quarter of Rockwell’s fiscal year 2024. At close, Clearpath will report to Rockwell’s Intelligent Devices operating segment. Goldman Sachs & Co. LLC served as Rockwell’s financial advisor.
Episode 418: Navigating e-commerce fulfillment with Radial
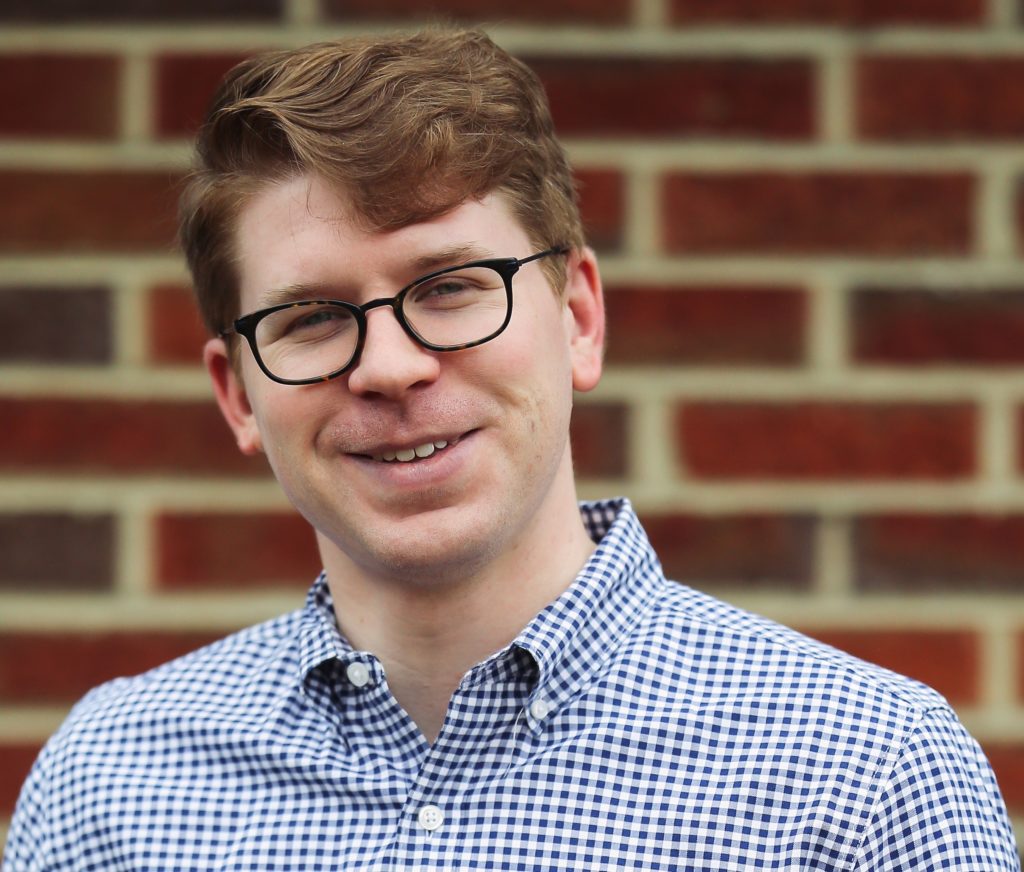
In today’s episode of the New Warehouse podcast, we have the privilege of Laura Ritchey, the Executive Vice President and COO at Radial, as our guest. Radial is a company that specializes in providing e-commerce fulfillment services to various brands, offering a wide range of logistics solutions for the modern world of online shopping. With a substantial footprint in the e-commerce landscape, Radial aims to streamline operations and enhance the customer experience. In this episode, we dive deep into Laura’s extensive experience, the challenges of e-commerce fulfillment, and the exciting trends. E-Commerce Fulfillment: Balancing Quality, Cost, & Service Laura emphasizes the intricate nature of the supply chain and how Radial tackles these challenges. She highlights that their teams operate as an extension of the brand or retailer, sharing the same passion to delight end consumers and provide agreed-upon services to clients. Laura references a survey conducted by Radial during the previous holiday season, highlighting the growing trend of customer expectations returning to two to three-day delivery times. The valuable advice given is to engage customers to understand their preferences directly. Recent client experiences have made them realize that, contrary to their previous assumptions of needing one or two-day delivery to remain competitive, they should prioritize ensuring transparency and visibility throughout the shipping process. The core idea centers around the significance of a seamless and transparent consumer experience and reliable delivery timelines. Delivering a Competitive Advantage in E-Commerce Fulfillment In today’s fiercely competitive e-commerce landscape, creating a competitive advantage for brands is a multifaceted endeavor. It all begins with seamless integration, where real-time data exchange plays a pivotal role. Laura notes, “We’re transmitting activities and updates around the order. So there has to be a level of integration…to make sure that all that data gets to the right places and triggers the right notifications to the customer.” This integration extends to internal systems and the customer-facing aspects of a brand’s operation. The ability to provide customers with up-to-the-minute information, such as order updates and inventory availability, is a vital component of the competitive edge. Essentially, it’s about meeting customer expectations in an era where convenience and speed reign supreme. By leveraging technology and data analytics, brands can keep pace and stay one step ahead by optimizing product offerings, inventory management, and the overall customer experience. Empowering Employees Laura emphasizes the significance of leveraging technology to enhance the employee experience, boost retention rates, and foster a positive workplace culture. “Happy and satisfied employees will give us better quality and service metrics.” She shares stories of employees’ interactions with robots, dispelling displacement concerns and showcasing how technology can enhance the human workforce. “If you don’t offer a good place to work if you don’t offer opportunities for advancement… competitive benefits package… it’s a real struggle.” Laura shares a story of one employee who began as a receiving clerk and is now running one of their sites. These stories are powerful and inspiring to other employees and convey the opportunities and resources available to them. Key Takeaways Customer Expectations: E-commerce fulfillment success hinges on meeting customer expectations for speed, visibility, and accurate delivery. Technology Synergy: Integrating AI, robotics, and automation empowers brands to optimize operations, increase efficiency, and elevate the employee experience. Employee Engagement: Enhancing the employee experience through technology fosters a motivated and dedicated workforce. Leveraging technology to streamline training, improve communication, and offer growth opportunities contributes to employee satisfaction and operational excellence. The New Warehouse Podcast EP 418: Navigating E-commerce Fulfillment with Radial
June 2023 Orders of Manufacturing Technology reach $411.3 Million; Slide from peak continues
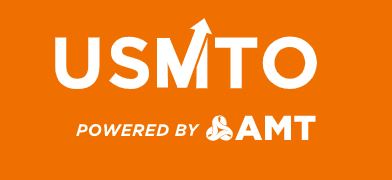
New orders of manufacturing technology totaled $353.9 million in July 2023, according to the latest U.S. Manufacturing Technology Orders Report published by AMT – The Association For Manufacturing Technology. July orders declined 12.4% from June 2023 but were only 10.5% lower than July 2022. Year-to-date orders reached $2.83 billion, 12.7% lower than this point last year. “July is typically one of the slower months for manufacturing technology orders, so to be down slightly is not surprising,” said Douglas K. Woods, president of AMT. “The more interesting trend is that for two consecutive months, the gap in year-to-date orders has narrowed over what have been historically slow months. Job shops have continued to decrease orders, but other industries that have benefited from recent reshoring or government investment have been filling in the gap.” Among individual sectors, job shops, the largest customer segment, placed their lowest total monthly orders since August 2020. Metal valve manufacturers recorded their third-highest monthly order value on record, which was last surpassed in September 2018. Their monthly orders reached nearly 5% of the total manufacturing technology order value for July 2023. Manufacturers of motor vehicle transmissions, which we highlighted in last month’s USMTO press release, continued to order machinery at an elevated pace. While still representing a large share of the market, the aerospace industry continued to order well below the peaks reached in early 2022. Several recently announced projects, such as the federal government’s $1.5 billion investment in communications satellites, could reverse the trend. “Manufacturing technology orders have definitely begun to feel the effects of higher interest rates and economic uncertainty, but the buildup of domestic capacity means that there are more diverse sales opportunities than there have been in decades,” said Woods. “That is what has kept manufacturing technology orders well above their historical levels despite the recent downward trend, and it will likely lead the industry out of any mild recession on the horizon.”
1,500 local officials deliver letter to Congress opposing bigger tractor-trailers
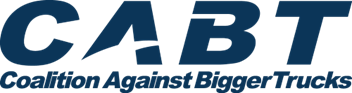
As Congress focuses on critical, must-pass legislation as it returns from Congressional recess, over 1,500 local government leaders from across the country sent a letter to Capitol Hill asking policymakers to oppose any increases in truck size or weight, including heavier single-trailer trucks. The signers include county and municipal officials as well as public works directors and county engineers. The letter, entitled “Bigger Trucks: Bad for America’s Local Communities” and organized by the Coalition Against Bigger Trucks, was delivered today to Capitol Hill offices. “Local governments, and our constituents, are the backbone of this county and we want Congress to know the policies they debate and implement have serious consequences,” said Berks County, Pennsylvania Chairman Christian Leinbach. “Heavier and longer trucks will damage our roads and bridges, leaving local taxpayers footing the bill. We cannot afford this and Members of Congress need to hear our concerns.” The joint letter states, “Local communities and our residents are what drive this country. We work every day to make sure the needs and safety of our residents are met. Allowing heavier and longer trucks will most certainly set us back in our efforts.” Leinbach, who also serves on the Board of Directors of the National Association of Counties, noted that while the current debate is about increasing truck weights on interstate highways, local infrastructure will be impacted. “Trucks do not load and unload on interstates. These trucks find their way on to local roads and bridges, whether it is for meals and gas or to deliver their cargo. This impacts us all.”The letter is being sent at the same time bigger-truck proponents lobby legislators to allow longer and heavier trucks on the road. This includes efforts to get their favored language in must-pass legislation, such as the farm bill and appropriations funding bills. These bills are too important to be put at risk by including such a deeply controversial issue. Studies have shown heavier and longer trucks damage infrastructure, especially bridges, and are more dangerous. In fact, the U.S. Department of Transportation (USDOT), in its 2016 Comprehensive Truck Size and Weight Limits Study recommended against any such increases and did not recommend any pilot projects. And a recent study, The Impacts of Heavier Trucks on Local Bridges, found over 72,000 local bridges that would be put at-risk by 91,000 pound trucks, the current weight limit being debated in Congress. The study found the cost to replace those bridges at over $60 billion, a cost that would be paid for by state and local governments. No current weight increase legislation includes any additional funding for infrastructure. Kevan Stone, CEO/Executive Director of the National Association of County Engineers, explained the importance of the local bridge study. “The impact of heavier and longer trucks on locally owned bridges is an important issue that needs to be explored nationally, including by Congress,” Stone said. “While we have long known that heavier trucks increase bridge damage, this study represents the first attempt to work directly with local officials to quantify the real world impacts. County officials, specifically county engineers, know their bridges better than anyone else.” Buchanan County Engineer and an author of the study Brian Keierleber knows firsthand the damage these heavier trucks cause. “Let me be clear – heavier trucks damage bridges. I have spent my entire professional career building and maintaining infrastructure, specializing in bridges,” said Keierleber. “And for those who think posting a bridge solves the problem of keeping these heavier trucks from crossing, it does not. The only time posting works is if I am standing on the bridge, in front of the truck.” Keierleber, who is a past president of the National Association of County Engineers, also raised concerns about safety. “My job is the build and maintain roads and bridges. But I also care about the dangers heavier and longer trucks create to motorists. When a truck and a car are involved in a crash, most of the time the car loses. Adding weight will only make the situation worse.”
Why terminology matters
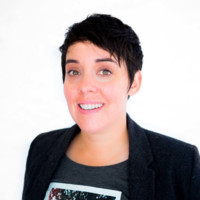
Rapid Unscheduled Disassembly vs. Explosion. Pre-Owned vs. Used. We’ve seen a lot of terminology changes over the years, and it’s because words matter. How you communicate and frame something has been a technique used by marketers for decades. Yet as organization leaders, we often make terminology more abstract and complicated instead of simple, compelling, and clear. This is one of the main causes why our organizations don’t understand what we do and why we do it. Take any mission statement. They all sound the same. Here’s one from a well-known big box store: “Our goal is to provide the highest level of service, the broadest selection of products, and the most competitive prices.” Who is it? Doesn’t matter, because it could apply to anyone or anything. Why wouldn’t you want to deliver the highest level of service? What does the highest level even mean? Or take any vision statement. Here’s a good one from a major tech company: “Design a more enlightened way of working”. It’s virtually impossible for an employee to understand what that means to their day-to-day. It’s also impossible to tie that vision in any way to key business decisions that impact the future. The worst culprit is values. Here are just a few that have come from 16 different companies and industries, yet all the same: “We are honest and ethical”, “We support our customers”, “We are fiscally responsible”, “We value other people’s opinions”, and “We care about quality service”. These could apply to anyone, anywhere, and really should be fairly common sense statements, which don’t bring any unique value to the company or culture. They shouldn’t even have to be said. That given, how do we look at our use of terminology in a different way? Let’s go back to our examples in the beginning. Pre-owned versus used. This change of wording was intentional – to reposition the perception people have about used cars. Used indicates old. Used indicates wear. Pre-owned says something different. Ownership implies a level of respect and care given to the thing that was owned. It’s a smart change, that has impacted not just the marketing and messaging of used cars, but their perceived purchase value. When we look at our own organizational terminology, what have we done to sharpen its impact on our customers and employees? When we say “quality service”, we should focus on what that truly means. What terminology illustrates this in a more meaningful way? Should it be, for example, “seamless service”? This more specific term provides more ability to build a vision and direction around. With more specificity, you can narrow the definition and scope. “Seamless service” may mean you invest and work on ensuring customers aren’t shuffled from one department to another, or their online and in-person experiences can be interchanged without additional steps. Or it may mean the customer makes one request and the company handles the rest. Whatever you decide, the terminology has a direction. Even with existing, generic terminology, such as “support our customers”, can have a more robust definition to support it, but without a clear direction, this often becomes more vague phrases with even more broad platitudes. It’s important to look at your company terminology and really assess whether it’s working to help your message get across and if your audiences have an aligned definition of it. Otherwise, they’re just those Dilbert-esque words on paper that no one really understands and no one really cares about. About the Author Andrea Belk Olson is a keynote speaker, author, differentiation strategist, behavioral scientist, and customer-centricity expert. As the CEO of Pragmadik, she helps organizations of all sizes, from small businesses to Fortune 500, and has served as an outside consultant for EY and McKinsey. Andrea is the author of three books, including her most recent, What To Ask: How To Learn What Customers Need but Don’t Tell You, released in June 2022. She is a 4-time ADDY® award winner and host of the popular Customer Mission podcast. Her thoughts have been continually featured in news sources such as Chief Executive Magazine, Entrepreneur Magazine, Harvard Business Review, Rotman Magazine, World Economic Forum, and more. Andrea is a sought-after speaker at conferences and corporate events throughout the world. She is a visiting lecturer and startup coach at the University of Iowa, a TEDx presenter, and TEDx speaker coach. She is also an instructor at the University of Iowa Venture School. More information is also available on www.pragmadik.com and www.andreabelkolson.com.
The vital importance of plastic to the U.S. economy
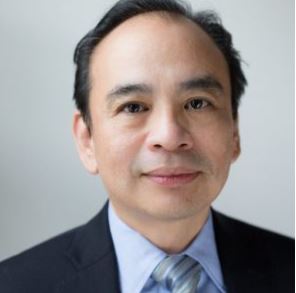
The U.S. Plastics Industry employs over a million Americans, is one of the largest continually growing sectors despite a less than robust economy and produces vital products through investment in innovations for about every major industry. Given this perspective, if you believe the claims made by anti-plastics activists about this essential material and industry, the statistics might come as a surprise. Opponents of the plastics industry would have you think that eliminating plastics production is a realistic goal with no detrimental impact on our economy, even suggesting it would ‘promote conservation,’ which couldn’t be further from the truth. The plastics industry is deeply engrained in our economy for valid reasons. Essential plastic materials provide cost accessibility to manufacturers and consumers and can be used in a wide range of applications. Whether that’s keeping food fresh, protecting health care workers and patients, making cars safer and more sustainable, or helping first responders during natural disasters, this industry emerged from innovation based on society’s demand and has consequently improved our lives and well-being every single day. Additionally, plastic is the best environmental choice in all applications. While plastic has in some cases become a negative target, in reality, plastic materials can be recycled and reused extensively. Thanks to the practicality of plastic, it consistently emerges as the most efficient and cost-effective option given its minimal energy and resource requirements during manufacturing, lower transportation costs, and reduced energy demand to recycle than other materials. Here’s the data on three essential ways the plastics industry vitally impacts the U.S. economy: The U.S. plastics industry not only provides substantial income for a significant number of Americans but also continues to create jobs. The U.S. plastics industry sustains employment for over one million individuals, encompassing diverse skills and backgrounds, from factory workers to corporate executives. When suppliers of the plastics industry are considered, this number increases to over 1.59 million jobs. These industries include those that supply fuel, spare parts, and transportation services. Remarkably, every two jobs created by the plastics industry supports another job elsewhere in the economy. The U.S. plastics industry continues to grow. Over the last 10 years, employment, real shipments and real value added fared better than manufacturing as a whole. Between 2012 and 2022 employment in plastics manufacturing grew 1.3% per year while manufacturing as a whole grew only 0.7% per year during that same period. Real plastics manufacturing shipments grew at a 0.4% annual rate from 2012 to 2022, while real value added grew 3.0% annually despite the pandemic recession. Currently, the plastics industry is the 7th largest manufacturing industry in the U.S. Capital expenditures have surged in the plastics industry. These include spending on nonresidential structures, such as factories or warehouses, equipment, and intellectual property. Between 2010 and 2022, capital expenditures in the industry soared by 7%, reaching a staggering $15 billion in the past year. Additionally, and importantly, as a continuously innovating industry, this includes research and development spending that enables the industry to create new sustainable manufacturing processes and products. This data does not paint a picture of an industry that’s going away. Rather, it unequivocally underscores the enduring strength of the industry. Any potential threat to the plastics industry would have severe repercussions for our country’s economy, potentially contributing to collapse. The industry’s growth hinges on our ability to produce sustainable materials and products, which is why the plastics supply chain is committed to tirelessly enhancing recyclability and investing billions into recycling technologies. It is a collective responsibility for all to increase recycling efforts, and the plastics industry recognizes that this is imperative. Sustaining plastics production in the U.S. is not just beneficial; it is crucial. Eliminating plastic manufacturing in the U.S. could result in increased reliance on imports from countries with more greenhouse gas-intensive manufacturing practices, thereby making our supply chains more vulnerable to global market fluctuations and harming our environment. The production of plastic in the U.S. is as indispensable as the material itself, and any proposal to eliminate it places our economy’s well-being and the livelihoods of the millions of Americans employed by the plastics industry at risk. About the Author: Perc Pineda, PhD is the Chief Economist for the PLASTICS Industry Association.
The Gordon Report: A changing mindset on training: Activate the “Hidden Workforce
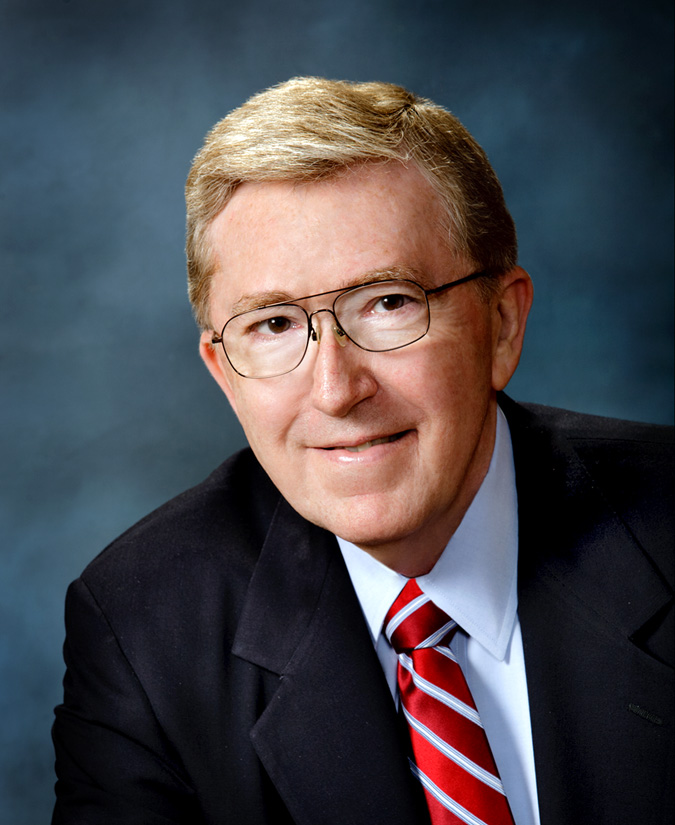
At long last, there are signs that companies are increasing employee training and participating in talent development programs. Why is this finally happening? A recent Federal Reserve program held in Chicago focused on how companies in four Midwestern states are partnering with their local communities to upskill younger entry-level workers. Companies from many businesses sectors are collaborating with K-12 and post-secondary institutions to offer both career information and educational programs aligned with current job requirements. This program also included a public high school graduate who told the audience how mentorships and a career exploration program interested him in pursuing a STEM career. He is now eager to begin post-secondary education that will qualify him for a career in information technology. A barrier that discourages publicly traded corporations from developing human capital is now being challenged. Arcane financial accounting rules currently classify employees of these companies as costs rather than assets. The Securities and Exchange Commission (SEC) is now considering proposals to require publicly listed companies to report spending on training and other human capital outlays. This may be a step toward moving the Financial Standards Accounting Board (FASB) to change accounting rules thereby giving companies the option of capitalizing and depreciating employee development as an investment, rather than expensing it as a cost that reduces earnings. The Current U.S. Labor Market Employer job training is also growing as an answer to the unprecedented demographic meltdown. Over this decade 10,000 workers are retiring each year (approximately 3.6 million workers annually). This will continue into the 2030s. Up to 66 percent of job openings are to replace these retirees. A recent National Federation of Independent Business survey reported that 42 percent of their members (companies with 500 or fewer workers) had vacancies they cannot fill. The number-one problem facing members of the Association of General Contractors is the shortage of skilled labor. Contractors are reporting that this is causing them to turn down new construction projects. In 2021 U.S. business experienced over 8 million job vacancies that resulted in a profit and productivity loss of over $1 trillion. By 2022 this had risen to over 12 million jobs and a $2 trillion loss. This trend seems to have abated somewhat this year. However, labor cost per unit rose to 6 percent in 2023. Average hourly earnings have increased 4.3 percent above last year as employers have raised wages to find qualified workers. Wage inflation is likely to continue unless businesses begin to enlarge the pool of skilled workers. But where can this “hidden workforce” be found? According to U.S. Department of Labor reports, about 100 million Americans of working age are not participating in the labor force. Our research shows that at least 20 million of these workers have given up looking for employment because they lack some of the specific skills a job requires. They are capable of filling such job vacancies if employers offer the job training needed to mobilize these skilled workers. As many other nations are dealing with a declining working-age population and significant skills shortages, it is important to develop all our own resources. There are hidden workers in our midst who could become productive employees if their skills are updated. Are U.S. businesses now beginning to realize that persistent job vacancies cost them more than it would to start entry-level skills training or to participate in community partnerships that are renewing local talent pipelines? About the Author: Edward E. Gordon is the founder and president of Imperial Consulting Corporation in Chicago. His firm’s clients have included companies of all sizes from small businesses to Fortune 500 corporations, U.S. government agencies, state governments, and professional/trade associations. He taught in higher education for 20 years and is the author of numerous books and articles. More information on his background can be found at www.imperialcorp.com. As a professional speaker, he is available to provide customized presentations on contemporary workforce issues.
Hess Auctioneers founding partner James “Jim” Germak passes at 72
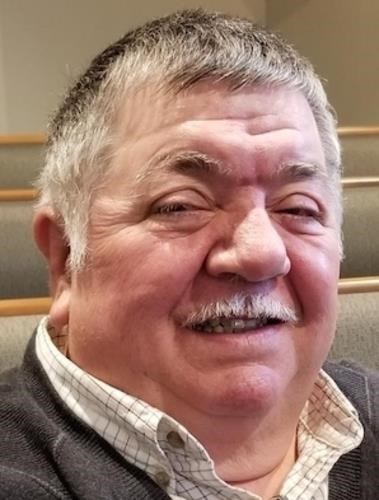
Hess Auctioneers shared the sad news that one of its founding partners has passed away. James “Jim” Germak, 72, of Elizabethtown, PA died on Saturday, September 2, 2023. From an early age, Jim wanted to be a truck driver and started his trucking career at the age of eighteen. In 1982, Jim founded Jagtrux, Inc. of Marietta, Pa. Jim was also a founding partner of Hess Auctioneers in Marietta, Pa. Jim graduated from Middletown Area High School in 1968. He was a member of PMTA, and served on the state board of directors and Lancaster PMTA Chapter. Jim loved spending time at his cabin and enjoyed various outdoor activities including hunting, boating, and driving his ranger. Jim had a passion for auctions and a “good deal.” The biggest enjoyment in his life was spending time with his children and grandchildren and sharing stories with friends. “Many auction weekends, you would see Jim driving around on his golf cart to make sure everything was running smoothly or chatting with the team to make sure they had everything they needed. He enjoyed a good story, great conversations, and of course, the auction, especially anything on wheels. He loved his community, friends, partners and family said Bill Troop of Hess Auctioneers. He is survived by his wife, Linda (Hilsher) Germak; daughter Rita Sovereign (Calvin Sovereign); sons Andrew Germak (Sarah Germak) and Zachary Germak (Linsey Stitt-Germak); nine grandchildren; brother Thomas Germak (Susan); and sister Barbara Thomasco (Dan). Services will be held at Community Bible Church, 331 Anderson Ferry Rd, Marietta, Pa. 17547, on September 16, 2023, visitation is scheduled from 9:00 – 11:00 a.m. with the service to promptly start at 11:00 a.m. In lieu of flowers, the family requests donations be made to ECHOS at 105 East Washington Street, Elizabethtown, Pa. 17022, an organization Jim felt strongly about. Memories and condolences may be shared at www.FinkenbinderFamily.com. Arrangements entrusted to Miller-Finkenbinder Funeral Home & Crematory, Elizabethtown. www.pennlive.com/obits
The National Bobblehead Hall of Fame unveils Iowa Hawkeyes Football Bobbleheads
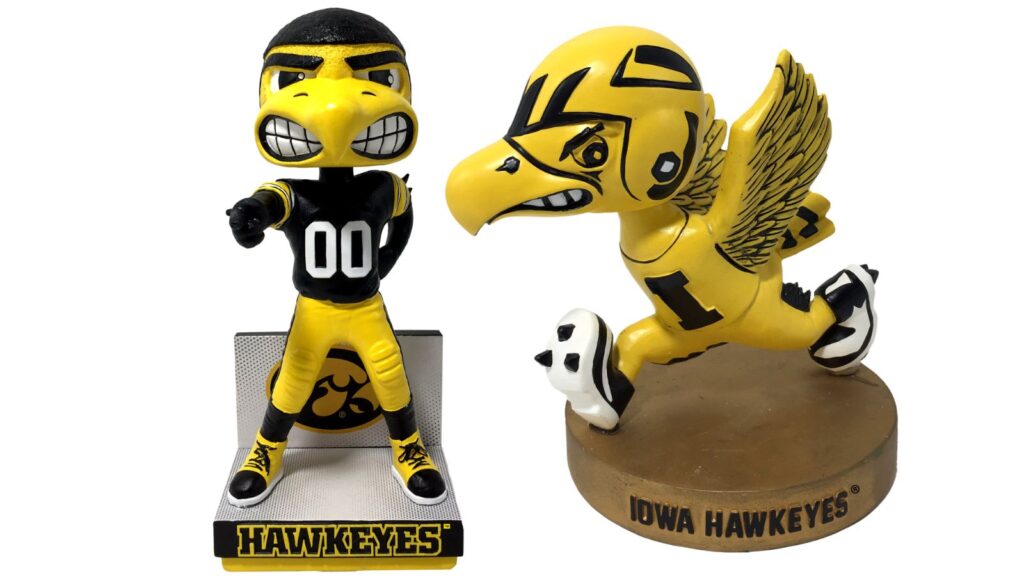
The officially licensed bobbleheads are being produced by the National Bobblehead Hall of Fame and Museum The Herky the Hawk Football Bobblehead will be available in the National Bobblehead Hall of Fame and Museum’s Online Store at this link and the Old School Football Bobblehead will be available at this link. The Herky Football Bobblehead is scheduled to ship in October and the Old School Bobblehead is scheduled to ship in December. The Herky Bobbleheads are individually numbered to only 2,023 and the Old School Bobbleheads are individually numbered to 1,847 to coincide with the year of the University of Iowa’s founding. Both bobbleheads are $35 each plus an $8 flat-rate shipping charge per order. “We’re excited to be releasing these special edition Iowa Hawkeyes Bobbleheads to coincide with the start of the 2023-24 school year and the football season,” National Bobblehead Hall of Fame and Museum co-founder and CEO Phil Sklar said. “We know how passionate Hawkeyes fans are about their school and bobbleheads, so we expect these bobbleheads to be extremely popular.” The National Bobblehead Hall of Fame and Museum, which is located at 170 S. 1st. St. in Milwaukee, Wisconsin, opened to the public on February 1st, 2019. The HOF and Museum also produces high quality, customized bobbleheads for retail sale as well as organizations, individuals, and teams across the country.
Mitsubishi Logisnext Americas President Ken Barina honored for Visionary Leadership in the material handling industry
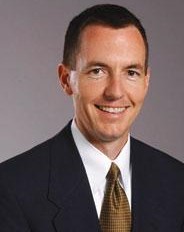
Mitsubishi Logisnext Americas (Logisnext) announced that Ken Barina has been recognized as a ‘Most Admired CEO’ by the Houston Business Journal. The annual award program celebrates Houston-area leaders who have demonstrated exceptional vision, innovation and dedication within the Houston region. Barina was recognized alongside other leaders from prominent industries, such as energy and technology companies, non-profits, among others. “I am honored to receive this prestigious award. It’s a true testament to the commitment and drive of Logisnext’s entire team – all who play a collective role in helping to achieve our vision to Move The World Forward,” said Ken Barina, President of Mitsubishi Logisnext Americas. “Together, we have experienced remarkable growth over the past decade – tripling sales revenue, doubling market share and tripling our number of employees. I’m extremely proud of our accomplishments.” The material handling industry plays a pivotal role in the global economy, enabling the efficient movement of goods across supply chains. Logisnext remains committed to building a positive culture that empowers employees and the company to achieve success and help Move The World Forward. Ken currently serves as a member of the Board of Directors for both Mitsubishi Logisnext Americas and Equipment Depot. He also holds the position of Senior Executive Officer at Mitsubishi Logisnext Co. Ltd. His extensive background includes previous board membership in various Logisnext subsidiary companies and the Industrial Truck Association (ITA) for more than 15 years. Barina was honored at the ‘Most Admired CEO’ awards ceremony on August 24 in Houston, where he was acknowledged for his remarkable contributions to both Logisnext and the broader Houston community
Plus One Robotics’ Co-Founder Paul Hvass slated to lead Netherlands office as General Manager
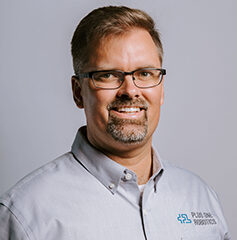
Plus One Robotics, a provider of AI vision perception software and solutions for robotic parcel handling, has announced that co-founder Paul Hvass has been named general manager for the European operations, relocating to Utrecht, The Netherlands. This move supports the ongoing sales growth among e-commerce and parcel post companies throughout Western Europe. “Having Paul located in Europe reinforces the significance of our commitment to the region for both our customers and our partners,” said Erik Nieves, Plus One CEO and Co-Founder, “This level of local leadership ensures global alignment across our teams positioning us to provide our multinational customers the highest level of service.” According to Mordor Intelligence, the rise in e-commerce and the persistent labor shortage is creating a gap that can be addressed by robots and automation. The Europe Warehouse Automation Market size is estimated at USD 3.74 billion in 2023, and expected to reach USD 7.32 billion by 2028, growing at a CAGR of 14.40% during the forecast period (2023-2028). Given that 80% of warehouses are still manually operated, this presents a huge opportunity for Plus One. Plus One established the Dutch office, Plus One Robotics BV in 2021 where Hvass sits on the board of directors. “I’m excited about this move and look forward to developing and strengthening associations with our European customers and collaborative partners,” said Hvass. “Despite the convenience of living in a digital world, local proximity still serves us well in developing relationships and better understanding regional trends and needs.” Headquartered in San Antonio, Texas, the company has three U.S. locations in addition to The Netherlands office
Stahlin® introduces PolySlim™ low-profile Polycarbonate Enclosures providing maximum mounting space with optimized depth
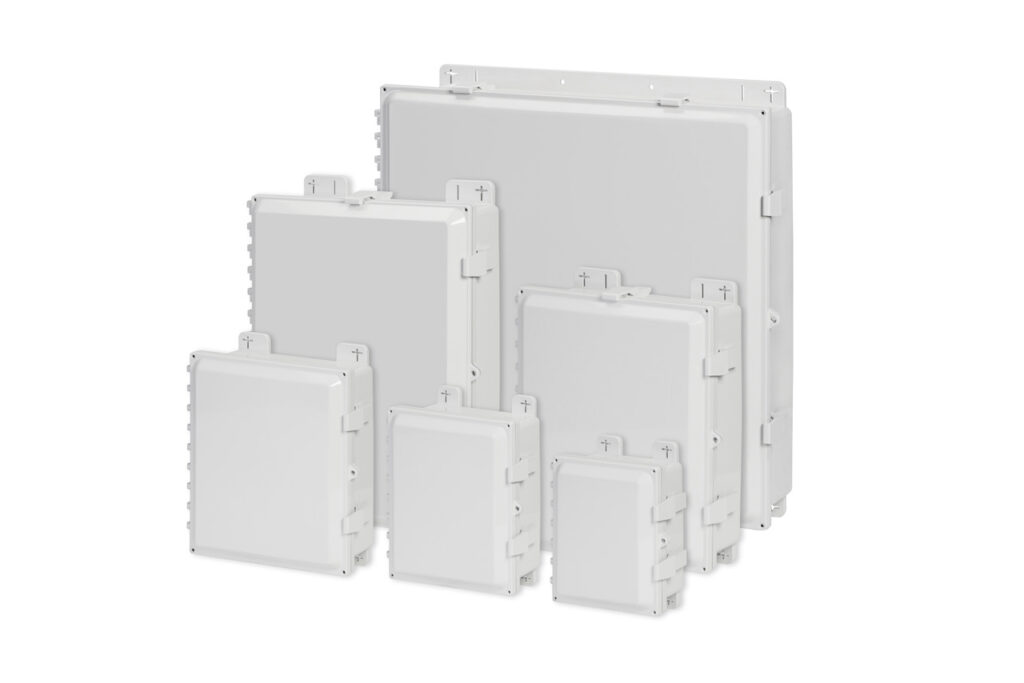
Stahlin® Enclosures, manufacturers of high-performing non-metallic electrical and industrial enclosures, announces the availability of PolySlim™ low-profile polycarbonate enclosures. These extremely durable enclosures are designed for OEMs and installers for the purpose of solving application challenges. PolySlim enclosures accommodate existing panel designs, eliminate unneeded depth and material, optimize installations, and save space and cost. The low-profile design of PolySlim makes these enclosures ideal for use on building exteriors and in tight spaces. They reliably protect equipment in non-hazardous industrial and commercial applications where space is a premium, and safeguard network components such as routers and switches in harsh conditions. PolySlim enclosures are well-suited for electrical control, wireless communications, measurement, monitoring, and security applications with minimal-depth equipment. PolySlim polycarbonate enclosures are available in seven sizes from 10” x 8” x 3” to 24” x 24” x 6” and can be configured as a hinged/screw cover or a hinged/ latched cover. High-impact rated yet lightweight for ease-of-installation, PolySlim enclosures feature a nonmetallic hinge that does not penetrate the inside of the enclosure. Thick, robust, smooth side wall construction eliminates side wall flexing and maximizes fitting mounting space. The low-profile design meets aesthetic requirements when mounting in visible areas on or inside buildings. Molded-in mounting feet with added mounting cross and holes, and added embosses in the back for DIN rail mounting, provide ease-of-installation and reduce costly on-site modification. Additional benefits of PolySlim include inhibitors that provide effective protection from UV degradation. An ABS Back panel option is available to optimize wireless signal transmission. Latch options include fully non-metallic or stainless steel. Cover options are available in clear or opaque. Larger sizes are compatible with the new, innovative Stahlin SolarShield® HMI Cover. PolySlim polycarbonate enclosures provide an Operating Temperature Rating of -40°F to +248°F (-40°C to +120°C) and an Outdoor UV Exposure (UL 746C) (f1) rating. Resin has passed tests for UV exposure and water immersion. Additional ratings include cULus per file #E319779 Type 1, 3R, 4, 4X, 6P*, 12 as well as UL50, UL50e, UL508A and IEC 60529: UL Listed per file #E362920 IP66, IP68*. Certifications and Compliance include: cULus, CE, REACH, and RoHS.
Distrust in recruiting: 49% of employed job seekers say AI recruiting tools are more biased than humans
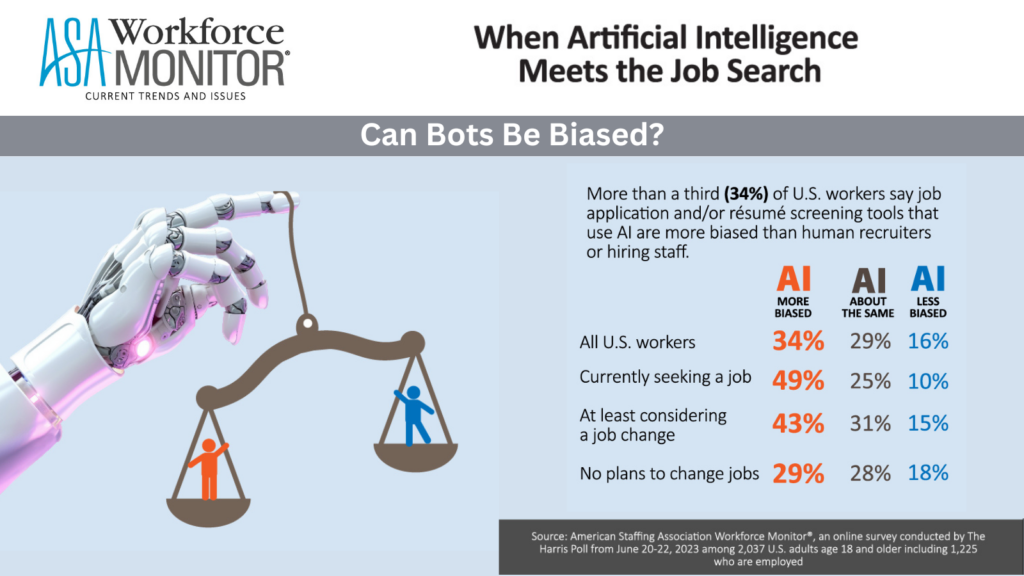
However, 39% of Gen Z, Millennials report using AI tools in job hunt Nearly half of employed U.S. job seekers (49%) believe artificial intelligence (AI) tools used in job recruiting are more biased than their human counterparts, according to the latest American Staffing Association Workforce Monitor® online survey conducted by The Harris Poll. The news comes just weeks after the Equal Employment Opportunity Commission released guidance on how to incorporate AI into a job search while still adhering to the Civil Rights Act of 1964 and the Americans with Disabilities Act, and amid ongoing discussions of AI screening tools acting with inherent bias when making important decisions. The skepticism is higher among individuals actively involved in the job-seeking process. Among those who are at least considering a new job, 43% believe AI recruiting tools are more biased than humans, compared to just 29% of those with no immediate plans for a job change. At the same time, the study found that 39% of current job seekers have used AI tools to assist in applying for a job. Usage varies based on race/ethnicity among U.S. residents, with 36% of Hispanic and 34% of Black U.S. adults saying they have used AI when applying for a job, compared to only 17% of White Americans. “Job seekers may feel comfortable using artificial intelligence tools in their job search, but that does not equate to trusting AI to make fair hiring decisions,” said ASA chief executive officer Richard Wahlquist. “As AI tools become more widely deployed, it’s critical that hiring managers work to increase transparency and accountability in their hiring processes and use tools that meet current and emerging antibias standards. It’s also critically important that policymakers and technologists thoughtfully consider measures intended to lower bias in AI hiring systems.” Survey Methodology This survey was conducted online within the U.S. by The Harris Poll on behalf of ASA from June 20–22, 2023, among a total of 2,037 U.S. adults age 18 and older, of whom 1,225 were employed. The sampling precision of Harris online polls is measured by using a Bayesian credible interval of +/-2.7%.
H&E opens new brnach in Wichita KS
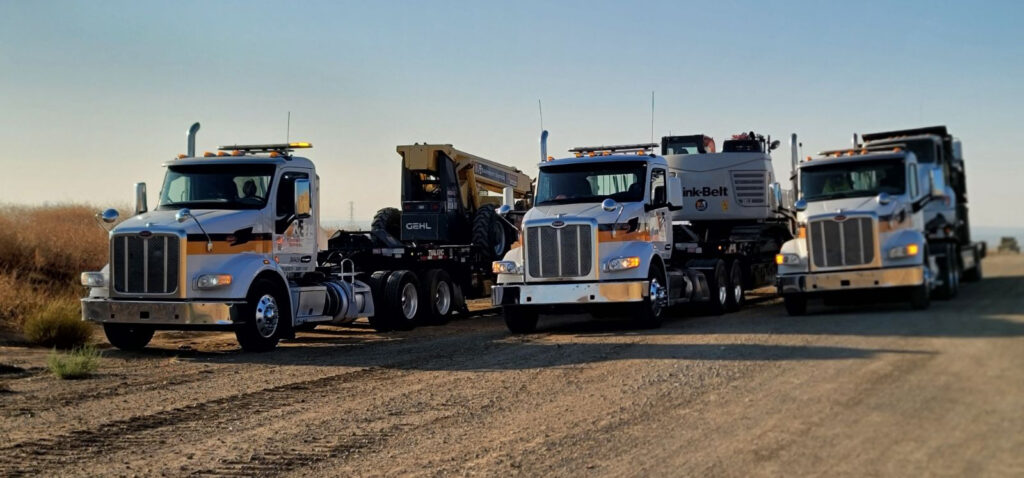
H&E Equipment Services Inc. hasannounced the opening of its Wichita branch, its first rental location in the state of Kansas. Since the beginning of the second quarter of 2023, H&E has opened 11 new branches across the country. The company now serves 30 states. The facility is located at 3540 S Hoover Road, Wichita, KS 67215-1213, phone 316-869-0100. It includes a large yard area, offices, and a repair shop and carries a variety of construction and general industrial equipment. “Our new Wichita branch is centrally located to reach both the large metropolitan market and also surrounding areas beyond. We already have established branches in Kansas City, Oklahoma City, and Tulsa, so this new location bridges the geographic gap between them and brings additional fleet and resources to customers in the region. Our proximity to I-35 and many feeder highways allows us quick delivery times and responsiveness,” says Branch Manager Cody Richardson. “I’m a Wichita native and started in the equipment business here 20 years ago. I know the area and am excited to introduce H&E to my state.” The Wichita branch specializes in the rental of aerial lifts, earthmoving equipment, telescopic forklifts, compaction equipment, generators, light towers, compressors, and more and represents the following manufacturers: Allmand, Atlas Copco, Bomag, Case, Club Car, Cushman, Doosan, Gehl, Generac Mobile, Genie, Hamm, Hilti, Husqvarna, JCB, JLG, John Deere, Kobelco, Kubota, LayMor, Ledwell, Lincoln Electric, Link-Belt Excavators, MEC, Miller, Multiquip, Polaris, Sany, Skyjack, SkyTrak, Sullair, Sullivan-Palatek, Tag, Towmaster, Unicarriers, Wacker Neuson, Yanmar, and others.
Orbital Wrapper manufacturer introduces Hot Wire Cutting System to eliminate blade maintenance
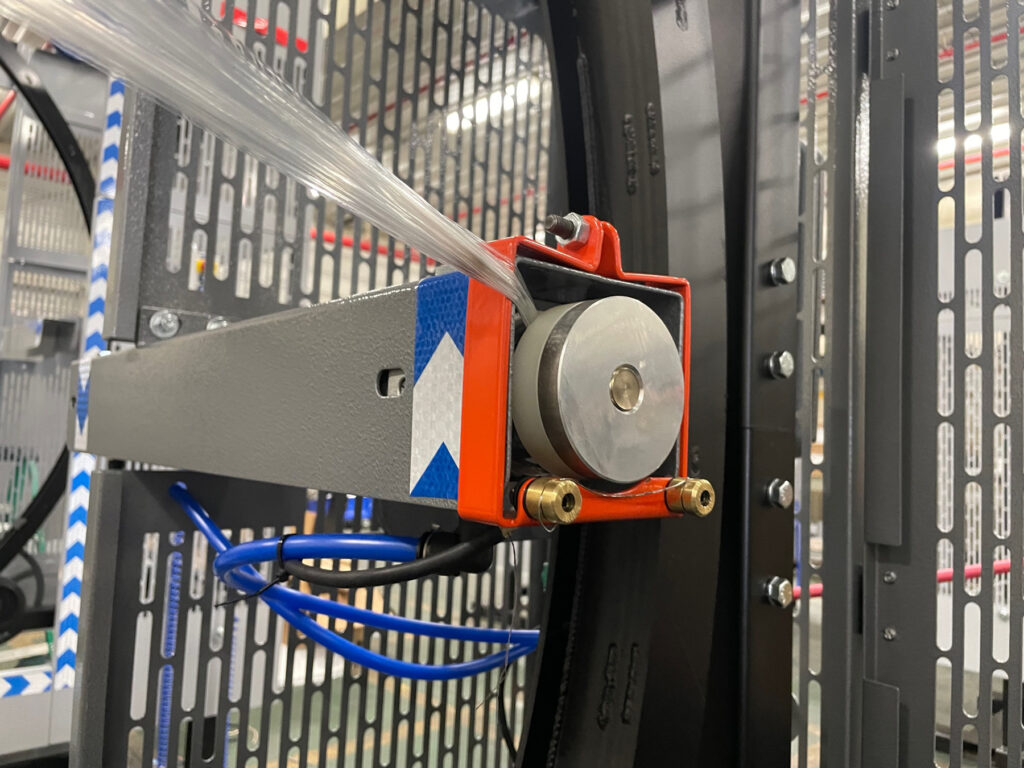
Orbital wrapper manufacturer TAB Industries, LLC, Reading, Pa., has introduced a Hot Wire Cutting System for its TAB Wrapper Tornado line of orbital wrapping machines. Offered as an option, the new Hot Wire Cutting System features proprietary technology that automatically cuts the end of the stretch wrap after pallet wrapping by drawing a heated metal wire through the plastic film, then safely conceals the wire for quick cooling. The new design replaces the standard design that uses a blade, eliminating the need for sharpening and replacement along with a potential safety hazard while ensuring a clean cut every time. To be introduced at FABTECH booth #A-5142 in Chicago, Ill. on Sept. 11, 2023 on the latest TAB Wrapper Tornado orbital stretch wrapper model, the Hot Wire Cutting System is available on all of the company’s standard, semi-automated, and fully automated orbital wrappers. The automated device is also available for retrofit on wrapping machines in the field. The TAB Wrapper Tornado orbital wrapping machines apply stretch wrap 360 degrees around and under the pallet and load to create a stable, unitized load that eliminates the need for boxes, crates, and banding. The patented stretch wrapping machines and Hot Wire Cutting System are designed and manufactured at the company’s Reading, Pa. headquarters and delivered with a full warranty.
Concentric LLC acquires critical DC power provider Retech
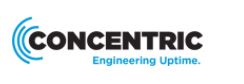
Concentric, LLC announced the acquisition of Retech. An established market leader across the US, with headquarters on the west coast, Retech specializes in designing, integrating, and managing critical DC power systems and critical infrastructure construction with a particular focus on the telecom and cable industry. This acquisition expands Concentric’s service footprint in critical power to the west coast, while adding new construction capabilities for critical power from telecom to energy storage to utilities and data centers. A full-service EF&I specialist, Retech’s in-house team of experienced engineers and technicians will be joining Concentric, bringing a proven track record of supporting world-class companies as they navigate the dynamic and challenging telecommunications landscape. Their expertise ranges from network infrastructure support services to network audits, staging, rack and stack, installation, de-commissioning/de-installation, resale and recycling, and as a general contractor, full site builds, upgrades or decoms. Retech is led by Co-Founders, Julie and Dennis Pulos, veterans of the critical power industry who will remain in leadership positions after the acquisition. “Retech is a well-respected team across the west coast and we’re thrilled to incorporate their expertise at Concentric as we expand our capabilities for engineering, design and installation services across the US. The Retech team share our values and mission to deliver superior, engineered power systems and we look forward to supporting them in their future growth from coast to coast,” said Concentric Chief Operating Officer, John Winter. “We are excited to join the Concentric team to accelerate our customers’ success by expanding our nationwide footprint. Joining forces with Concentric will enable us to add the resources we need to be able to quickly scale and meet our customers’ growing needs,” said Retech Co-Founder and President, Julie Pulos.
AAR reports Rail Traffic for August the week ending September 2, 2023
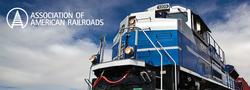
The Association of American Railroads (AAR) has reported U.S. rail traffic for the week ending September 2, 2023, as well as volumes for August 2023. U.S. railroads originated 1,133,375 carloads in August 2023, down 2.0 percent, or 23,323 carloads, from August 2022. U.S. railroads also originated 1,239,290 containers and trailers in August 2023, down 6.3 percent, or 83,717 units, from the same month last year. Combined U.S. carload and intermodal originations in August2023 were 2,372,665, down 4.3 percent, or 107,040 carloads and intermodal units from August 2022. In August 2023, nine of the 20 carload commodity categories tracked by the AAR each month saw carload gains compared with August 2022. These included: motor vehicles & parts, up 9,374 carloads or 13.6 percent; petroleum &petroleum products, up 5,567 carloads or 12.9 percent; and primary metal products, up 1,792 carloads or 4.6 percent. Commodities that saw declines in August 2023 from August 2022 included: grain, down 22,064 carloads or 22.9 percent; coal, down 9,754 carloads or 2.8 percent; and pulp & paper products, down 2,334 carloads or 10.2 percent. “August was the third straight month in which total year-over-year U.S. rail carloads have fallen,” said AAR Senior Vice President John T. Gray. “A major reason why is that other than automotive manufacturing, the industrial economy, in recent months, has not been doing as well as other areas of the economy. Until industrial activity, and especially manufacturing, recovers, rail volumes in many key markets could remain constrained.” Excluding coal, carloads were down 13,569 carloads, or 1.7 percent, in August 2023 from August2022. Excluding coal and grain, carloads were up 8,495 carloads, or 1.2 percent. Total U.S. carload traffic for the first eight months of 2023 was 7,852,770 carloads, up 0.0 percent, or 3,625 carloads, from the same period last year; and 8,320,438intermodal units, down 9.2 percent, or 838,829 containers and trailers, from last year. Total combined U.S. traffic for the first 35 weeks of 2023 was 16,173,208 carloads and intermodal units, a decrease of 4.9 percent compared to last year. Week Ending September 2, 2023 Total U.S. weekly rail traffic was 476,851 carloads and intermodal units, down 5.4percent compared with the same week last year. Total carloads for the week ending September 2 were 231,113 carloads, down 1.6percent compared with the same week in 2022, while U.S. weekly intermodal volume was 245,738 containers and trailers, down 8.7 percent compared to 2022. Five of the 10 carload commodity groups posted an increase compared with the same week in 2022. They included motor vehicles and parts, up 2,274 carloads, to 16,073; metallic ores and metals, up 1,968 carloads, to 22,786; and chemicals, up 1,889 carloads, to 32,942. Commodity groups that posted decreases compared with the same week in 2022 included coal, down 4,408 carloads, to 68,598;grain, down 4,403 carloads, to 14,961; and nonmetallic minerals, down 1,219 carloads, to 32,305. North American rail volume for the week ending September 2, 2023, on 10 reporting U.S., Canadian and Mexican railroads totaled 337,338 carloads, down 0.1 percent compared with the same week last year, and 328,232 intermodal units, down 9.9 percent compared with last year. Total combined weekly rail traffic in North America was 665,570 carloads and intermodal units, down 5.2 percent. North American rail volume for the first 35 weeks of 2023 was 22,675,055 carloads and intermodal units, down 4.1 percent compared with 2022. Canadian railroads reported 89,904 carloads for the week, up 2.2 percent, and 72,134intermodal units, down 14.6 percent compared with the same week in 2022. For the first 35 weeks of 2023, Canadian railroads reported cumulative rail traffic volume of 5,519,818 carloads, containers and trailers, down 3.3 percent. Mexican railroads reported 16,321 carloads for the week, up 9.2 percent compared with the same week last year, and 10,360 intermodal units, down 3.5 percent. Cumulative volume on Mexican railroads for the first 35 weeks of 2023 was 982,029carloads and intermodal containers and trailers, up 5.1 percent from the same point last year. To view the rail traffic charts, click here