PTDA welcomes three new members
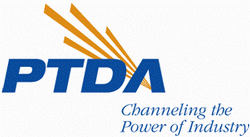
The Power Transmission Distributors Association (PTDA), the leading association for the industrial power transmission/motion control (PT/MC) distribution channel, is welcoming three new distributors to its membership. Distributors Gordon Russell Limited is a Canadian & family-owned business operating since 1930 supplying and servicing certified engineered products to industry in Western Canada and USA’s Pacific Northwest whose core focus is “We Keep Customers Moving Forward.” The company’s tried & tested quality products can be found in essential applications throughout Canada & USA’s Pacific Northwest resource-based economies. Learn more. MROSupply.com is the evolution of Los Angeles Rubber Company, a power transmission supplier that has been servicing the Los Angeles area since 1898. MROSupply provides its customers with 24/7 access to suppliers’ products. Learn more. W. Grainger, Inc.,is a Fortune 500 company founded in 1927 with more than 4.5 million customers worldwide. In its high-touch solutions business model, Grainger offers more than 2 million repair and operating (MRO) products and technical support and inventory management services. In its Endless Assortment segment, Zoro.com, offers customers access to more than 11 million items, and MonotaRO.com provides more than 20 million items. Learn more. The Power Transmission Distributors Association (PTDA) is a global association for the industrial power transmission/motion control (PT/MC) distribution channel. Headquartered in Chicago, PTDA represents power transmission/motion control distribution firms that generate more than $19 billion in sales and span more than 2,500 locations. PTDA members also include manufacturers that supply the PT/MC industry.
Getting ready for Hurricane Idalia: ALAN’s five key takeaways for businesses
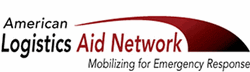
As Hurricane Idalia approaches landfall, ALAN (American Logisitics Aid Network) is busy preparing, and they are encouraging the logistics community to do the same. With that in mind, we’d like to share five pre-storm takeaways that we feel it’s especially essential for organizations to be aware of. They’re listed below, and we hope you’ll find them helpful. “Because this has the potential to be an especially destructive storm, we encourage you to visit ALAN’s Supply Chain Intelligence Center (https://www.alanaid.org/map/) and our Disaster Micro-Site (https://www.alanaid.org/operations/) frequently”, said ALAN Executive Director Kathy Fulton. “The first contains a wide variety of resources to keep you in the loop about everything from Hurricane Idalia’s latest path to how local and regional transportation infrastructure is being impacted. The second is where we will share details about some of ALAN’s key activities and how you and other members of the logistics community can help. We will be updating both resources frequently as events unfold”. added Fulton. “As always, all of us at ALAN are hoping that this storm will be much less severe than predicted and that any damage to life, health and property will be minimal. At the same time we are grateful for the many good people like you who stand ready to help. Thank you for supporting us and those we serve, and please join us in holding good thoughts for the people of Florida, Georgia and the Carolinas in the days ahead”, said Fulton. Here are the five takeaways: Don’t put your head in the sand. Make personal safety a priority If you or some of your business locations are located anywhere near Hurricane Idalia’s path, be sure to monitor the National Hurricane Center and your local National Weather Service forecast for real-time details. And please, don’t ignore any safety warnings that pertain to you or your personnel. This is expected to be a major hurricane with winds of up to 120 miles per hour as well as a massive storm surge and potential for flooding, which means its potential impact is not to be taken lightly. In light of this, please ensure that your employees who work in potentially affected locations have ample time to prepare, shelter in place or evacuate as needed – even if it means closing those operations early or telling employees not to report to work. Get the latest detailed information about storm-related road closures, facility closures and more by visiting ALAN’s Supply Chain Intelligence Center at https://www.alanaid.org/map/ It should tell you most of what you need to know. But should you wind up needing additional information, please contact us at ops@alanaid.org. Time permitting, we will do our best to work with our emergency partners to get you an answer. ALAN is actively fielding and fulfilling Hurricane Idalia and other major disaster relief requests (including many from the Maui fires). You can view the latest by going to the “What’s The Latest And How Can You Help With Relief Efforts?” section of our Disaster Micro-Site at https://www.alanaid.org/operations Over the past few weeks, we have been communicating with various emergency management and non-profit partners regarding their hurricane needs. Although there are no “open” requests for Hurricane Idalia support at the moment (although there are many more from other disasters) this situation could quickly change as Hurricane Idalia’s story unfolds. In fact, most of our requests usually come several days or weeks after hurricanes have hit. So stay tuned and stay ready – because as requests for transportation, warehousing, volunteers and material handling equipment come in, we will be posting them promptly. And we will need your help. If you’d like to “pre- offer” your space, equipment, expertise or services, please visit https://www.alanaid.org/how-to-help/ on the ALAN website to fill out a form ALAN finds such offers to be hugely helpful, because it lets us know who might be most willing to help us out with our most urgent needs. But rest assured that ALAN knows the difference between a pre-offer and a promise. We’ll still reach out to ask if you’re willing to help with a particular need rather than just assuming you will. Please don’t self-deploy to disaster-impacted sites, and please don’t participate in product collection drives Although the intention behind both of these activities is good, they often create more challenges than they solve, because they tend to get in the way of responders who are working to save lives – and add confusion to an emergency supply chain that is already under tremendous strain. If you’re looking for a meaningful way to help, pick a humanitarian organization and collect money for it instead. Such donations will be much more useful and efficient – and far more likely to actually reach storm survivors.
Omega Design’s debuts Robotic Bottle Unscrambler at Pack Expo
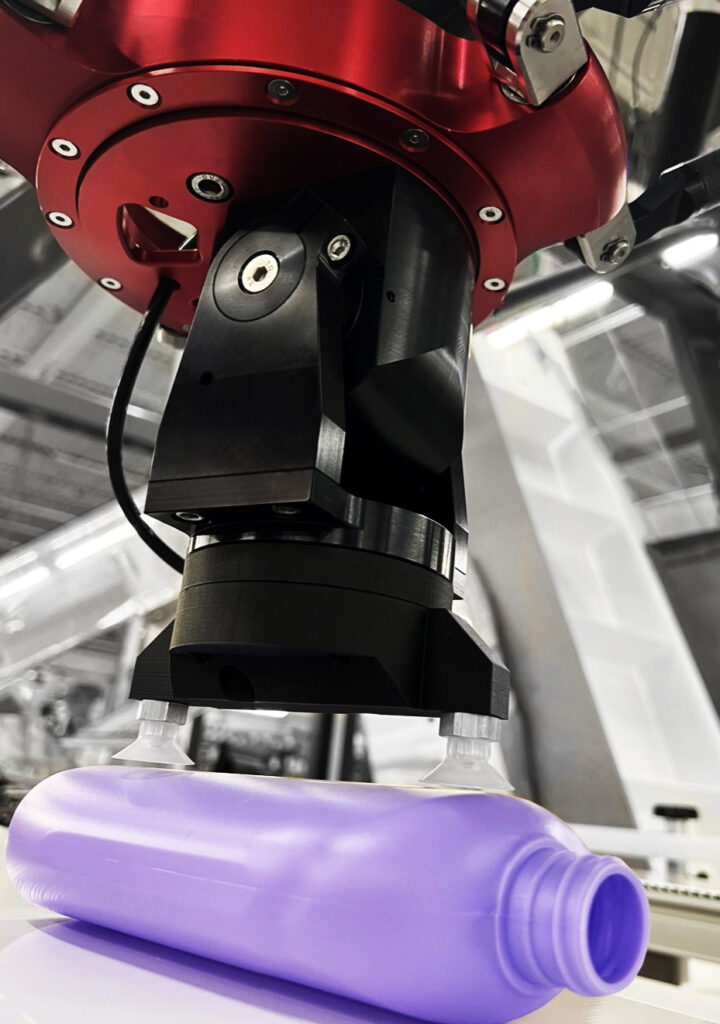
Dual infeed system maximizes robotic movements for heightened throughput; Modular, expandable design brings flexibility and versatility Omega Design Corporation, a global provider of innovative packaging machinery for the pharmaceutical, nutraceutical and consumer healthcare industries, and a worldwide provider in bottle unscrambling technology – will introduce a new fully Automatic Robotic Unscrambler at Pack Expo Las Vegas, September 11-13. At Booth C-3836, the company will demonstrate the new machine’s ability to provide smarter sorting by utilizing a parallel-kinematic, multi-axis, pick-and-place robot module, which separates, orients, and positions bottles onto a conveyor or into stabilizing pucks. Omega Design Corp.’s versatile new automatic unscrambler is ideal for applications running complex or multiple bottle shapes, including a broad array of containers, bottles, tottles, jars, vials, jugs and tubes. The limited number of changeover points greatly reduces setup times. Its integrated hopper minimizes footprint, and the conveying system is optimized for robotic handling, with intelligent infeed metering control reducing recirculation of bottles. The machine combines speed and accuracy via Omega Design’s dual infeed system, which purposefully presents two containers at once to the unit’s robotic arms from a single hopper. This process optimizes the robotic arms’ movements, yielding throughputs unobtainable by conventional methods. The setup also minimizes the machine’s overall floorspace footprint. Another strong suit of the new Automatic Robotic Unscrambler is flexibility. The system can be configured to meet a range of capacity needs and speeds. This includes increased hopper capacity, as well as additional robot modules to increase speeds by up to 90 containers per minute per robot. The machine features a user-friendly 15” touchscreen HMI, a sophisticated Rockwell Automation Optix visualization platform, and an advanced Allen Bradley integrated safety programmable logic controller (PLC). Rapid, repeatable pushbutton changeover with a limited number of change points helps diminish downtime between new product runs. “Introducing a fully automatic robotics unscrambler applicable to a wide variety of containers aligns with our ongoing mission to produce equipment solutions that simplify processes through reduced labor requirements and intuitive operation,” said Glenn Siegele, President of Omega Design Corporation. “Importantly, the machine also comes in a modular design that can be configured to meet the specific needs of every customer.”
Seeq announces partnership with Databricks to Accelerate IT-OT Data Convergence Across the Enterprise
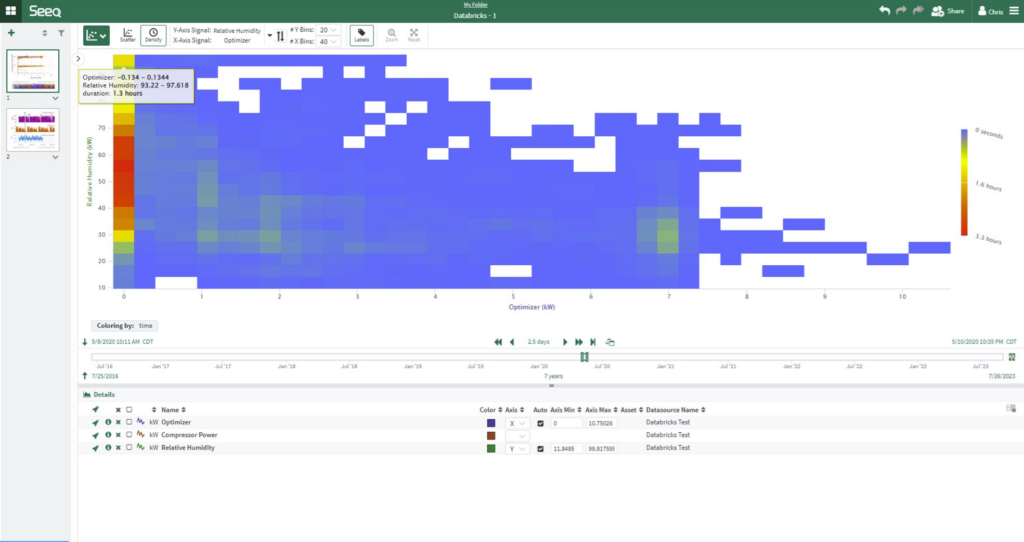
Partnership builds on Seeq advanced analytics innovations and Databricks enterprise AI capabilities to improve data accessibility and enhance machine learning workflows Seeq Corporation, a provider in advanced analytics for manufacturing, announced a partnership with Databricks, the data and AI company, that brings a native integration between each company’s platform to simplify access to high quality asset and process data, unify IT and OT data processing and accelerate AI/ML adoption across the industrial manufacturing, pharmaceuticals, chemicals and energy sectors. This bi-directional integration enables users to seamlessly combine contextualized time series data from industrial assets with a vast array of enterprise data sources to deliver more robust reporting, analytics and predictions in their business. Databricks customers can now take advantage of Seeq’s extensive connectivity to time series data sources and power a wide range of analytical use cases across the enterprise. Insights developed in Databricks Lakehouse Platform can be operationalized in Seeq, introducing new opportunities for process experts and data teams to deliver data-driven solutions to increase industrial productivity, improve operational reliability, enhance safety, and accelerate progress towards sustainability goals. For petrochemical manufacturer Chevron Phillips Chemical Company, the Seeq and Databricks integration accelerated the company’s ability to scale data science and machine learning efforts across multiple digital initiatives involving process and laboratory data. Brent Railey, Chief Data & Analytics Officer of Chevron Phillips Chemical Company comments, “We are very excited about this partnership, as it will be mutually beneficial for Databricks, Seeq, and their shared customers. Seeq brings key time-series functionality that just isn’t available in other solutions. Seeq also simplifies the complexities of connecting to various types of process data sources. Databricks brings scalable, elastic data engineering and data science capabilities at an affordable price. Seeq can bring data to Databricks for complementary analytic purposes within Databricks. Databricks can serve cleansed and refined IIoT data to Seeq for self-service analytics. This partnership should make this one-two punch even more powerful!” “Our collaboration with Seeq unlocks tremendous value for customers, making it simpler for organizations to operationalize and democratize IoT datasets by leveraging the open and secure foundation of the Databricks Lakehouse Platform. This significantly lowers the barrier to data-driven innovation in the industry,” says Shiv Trisal, Global Manufacturing Industry Leader at Databricks. “The Seeq and Databricks integration is a critical step toward bridging the communication gap between operations technology and information technology personnel, which will drive increased machine learning value across the enterprise,” says Megan Buntain, VP of Global Partnerships and Ecosystem at Seeq. “We’re thrilled to add Databricks to the Seeq partner ecosystem and look forward to continuing to innovate with their team to improve outcomes for manufacturers.” To learn more about the Seeq and Databricks partnership, visit seeq.com.
NSK presented with Motion’s Supplier of the Year award
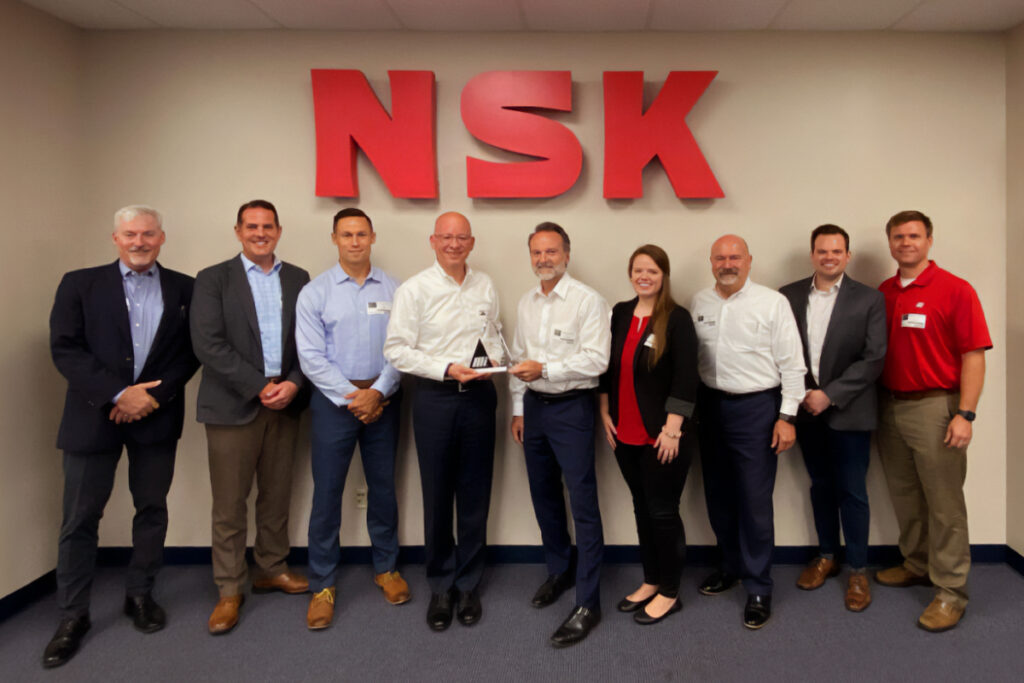
Motion Industries, Inc., a distributor of maintenance, repair and operation replacement parts, and a premier provider of industrial technology solutions, named NSK “2022 Supplier of the Year.” The award recognizes companies that have shown exceptional commitment to Motion through quality products and services and earned the highest score in the multi-faceted Supplier Stratification rating system. The presentation took place July 18, 2023, at NSK’s manufacturing facilities in Franklin, TN. “NSK consistently seeks opportunities to increase their alignment with Motion’s strategies,” said Joe Limbaugh, Motion’s Executive Vice President & Chief Operations Officer. “We appreciate NSK’s forward-thinking and their efforts to ensure Motion’s success in its growth plan.” “It’s an honor to accept this award on behalf of everyone at NSK, from the U.S. team members to our factories around the world who support our local activities,” said Tarek Bugaighis, Senior Vice President – Industrial Business Unit, NSK Americas, Inc. “The collaboration between our companies to serve the industrial market has been tremendous not only last year, but in the years prior as well, culminating with this year’s Supplier of the Year award. Thank you to Motion and to everyone from both companies that work so hard to deliver exceptional value to the industrial market. It has been a pleasure to work with Motion, and I look forward to all we can accomplish together in the years ahead.” Motion’s Supplier Stratification formula is a rating system that evaluates each supplier’s performance in a number of Supply Chain, Marketing and Field Support categories.
AutoScheduler partners with FourKites to bring visibility to products coming in/out of the warehouse
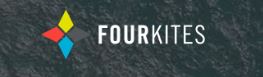
AutoScheduler Sponsors FourKites Visibility Conference in Chicago, Sept. 6-7th AutoScheduler.AI, an innovative Warehouse Management System (WMS) accelerator, partners with leading supply chain visibility provider FourKites to bring visibility to products coming in and out of warehouses and distribution centers. Such granular visibility will help executives see exactly what is happening in their supply chain, determine bottlenecks that slow fulfillment, and uncover areas of cost reduction. “More shippers than ever want visibility of their supply chain network, which includes production facilities, warehouses, transport modes, suppliers, and customers,” says Keith Moore, CEO of AutoScheduler. “We are pleased to partner with FourKites to maximize the throughput of companies’ distribution networks.” “This use case from a global food manufacturer is the first joint project to use FourKites data integrated with AutoScheduler, which resulted in a 28% increase in personnel productivity at their first site,” says Nimish Patel, Vice President, Global Alliances at FourKites. “We are very excited about this partnership with the AutoScheduler.AI team, and to bring the value of real-time supply chain visibility to more warehouses and distribution centers across the world.” FourKites gives shippers a comprehensive view of all their inventory in transit around their network. This inventory can be in the yard, within warehouses, with intra-campus transfers, or at the dock or production facilities. AutoScheduler uses this visibility to streamline product flow through key distribution nodes, ensuring that distribution sites are not the bottleneck to delivery, thereby improving customer satisfaction with better on-time, in-full fulfillment. AutoScheduler is sponsoring FourKites’ annual user conference, Visibility, which brings together over 700 supply chain leaders from the world’s largest brands, including Kimberly-Clark, Bayer, ARMADA, Eastman, and Dollar Tree, among others. AutoScheduler executives will be at the event in Chicago on September 6 – 7, 2023, to meet prospective customers and network with peers. To schedule a meeting with AutoScheduler.AI execs at the FourKites Visibility conference, send an email to: sales@autoscheduler.ai.
Episode 414: Dock scheduling with data docks: An interview with Nick Rakovsky
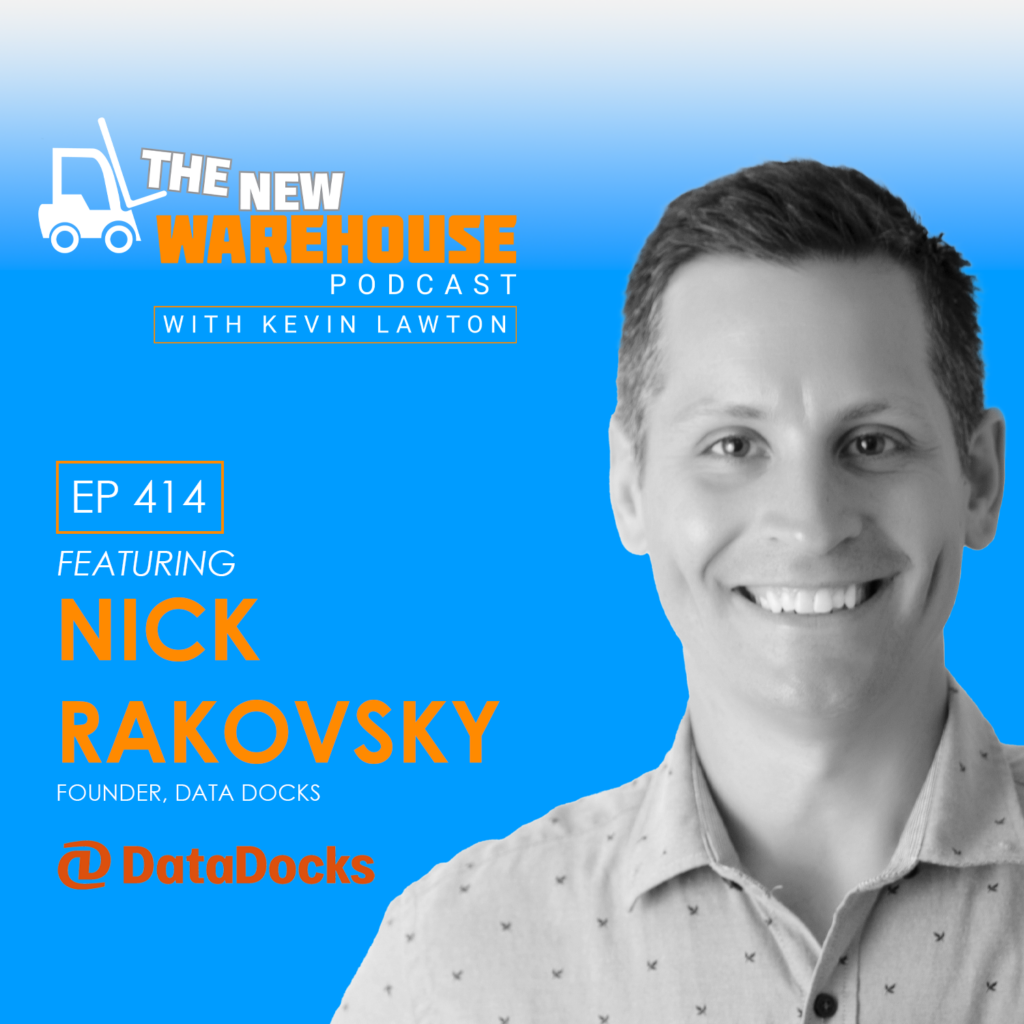
In this episode of the New Warehouse podcast, we sit down with Nick Rakovsky, the founder of Data Docks, a company dedicated to streamlining warehouse operations, explicitly focusing on dock scheduling and optimization. Nick shares insights into his background and what drove him to establish Data Docks. We explore the critical role of the dock within a warehouse and how Data Docks aims to bring efficiency and organization to the vital area of dock scheduling. Transforming Dock Scheduling and Efficiency Nick Rakovsky discusses the challenges he faced as a warehouse manager and how these challenges led to the inception of Data Docks. “I started off running a bunch of warehouses… The main pain points I was facing were accountability and communication. “He highlights the manual and time-consuming nature of dock scheduling and the need for a solution to streamline these processes. Enhancing Communication and Visibility with Dock Scheduling Data Docks provides a platform for customers and carriers to book appointments, receive updates, and streamline communication. Nick discusses the impact of reducing phone calls and emails, improving visibility for internal teams, and ensuring accurate information flows smoothly through the system. “We can validate the information. Now before they can actually go and create the appointment… it’s kind of like having that coordinator in the software, knowing where those rules and how they apply.” The Future of Dock Scheduling with Data Docks Nick Rakovsky shares his vision for the future of Data Docks, emphasizing the importance of further opening up communication and eliminating isolated issues within warehouse operations and dock scheduling. He discusses upcoming features, including a driver check-in portal and additional enhancements to improve communication and visibility. “The big vision is to… get rid of that communication back and forth with our clients and their customers.” Key Takeaways on the Impacts of Dock Scheduling Efficient Dock Scheduling: Data Docks streamlines manual and time-consuming processes, allowing users to gain back up to 60% of their day, allowing them to focus on more valuable tasks. Improved Communication: The platform enhances communication between warehouse teams, customers, and carriers, reducing the need for phone calls and emails and providing real-time updates. Future Innovations: Data Docks is committed to ongoing innovation, with upcoming features designed to enhance communication and visibility within warehouse operations further. The New Warehouse Podcast EP 414: Dock Scheduling with Data Docks: An Interview with Nick Rakovsky
Bobcat North Dakota Open merges golf and community outreach
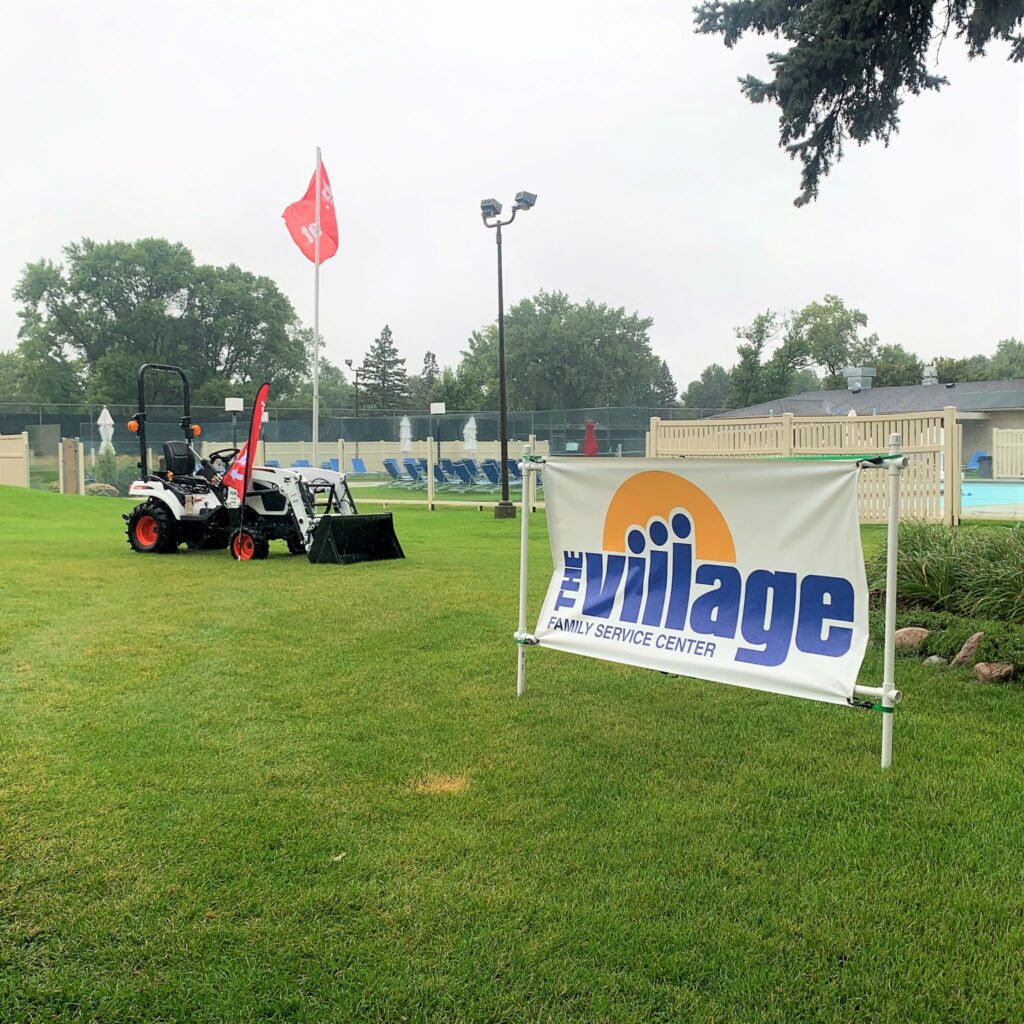
Proceeds benefit community with over $1.2 million raised since 1984 The 59th annual Bobcat North Dakota Open brought exciting pro and amateur golf to the Fargo Country Club August 25-27, while also supporting The Village Family Service Center, a local non-profit agency dedicated to improving the lives of area children and families. Andre Metzger won the tournament, becoming the first player to ever win the Bobcat North Dakota Open tournament four times. Tied for second place, behind Metzger, was Zander Winston and Chris Gilman. Ian Siminoch topped the amateur division of the tournament. Bobcat Company has served as the lead corporate sponsor for the tournament since 1984, donating more than $1.2 million in support of The Village’s community outreach services. “All of us at Bobcat Company are proud to support this annual tournament and the greater Fargo-area community,” said Mike Ballweber, president of Doosan Bobcat North America. “The Bobcat North Dakota Open is a great way to host and showcase pro and amateur golf talent while also helping The Village build a brighter future for area kids and families in need of our support.” The three-day pro-am golf tournament concluded Sunday with an awards presentation during which Bobcat representatives presented a check for $1.2 million to Kelly Olson, president and CEO of The Village. The check represents Bobcat Company’s total donations while serving as the annual tournament’s title sponsor. “We are incredibly grateful for the support of Bobcat Company,” said Kelly Olson, President and CEO of The Village Family Service Center. “Their generosity is truly making a difference in the lives of the people we serve, and we look forward to continuing this important partnership in the years to come.” Other major sponsors of the tournament were: Bell Bank, Bremer Bank, D-S Beverages, J & M Printing, Lapham-Hickey Steel Corp, Lenker Consulting, and Swanston Equipment Corporation. A large field of amateur golfers were paired with pros during Friday’s and Saturday’s rounds. The tournament’s events also included a kick-off celebration, barbeque and a Big Brothers Big Sisters program golf clinic for children who each received a set of junior golf clubs courtesy of the North Dakota Golf Association. The 59th annual Bobcat North Dakota Open is a part of the Dakotas Tour, an 18-event, professional golf tour played in Minnesota, Iowa, North Dakota and South Dakota.
Seun Salami joins Terex Corporation Board of Directors
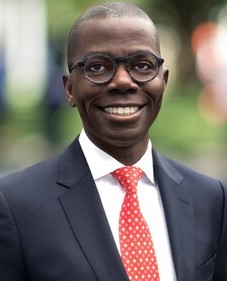
Terex Corporation has announced that Seun Salami has been appointed to the Company’s Board of Directors. Mr. Salami currently serves as the Executive Vice President and Chief Financial Officer of Nuveen, a global asset management firm. Mr. Salami joined TIAA, Nuveen’s parent company, in May of 2018 as corporate controller, and later served as both TIAA’s chief accounting officer and principal financial officer of TIAA Real Estate Account. “Seun Salami will be an excellent addition to our Board of Directors,” commented John L. Garrison, Jr., Terex Chairman and CEO. “Seun is an executive with a successful track record of leading multifunctional teams from finance and operations to deliver strong results for global organizations.” Prior to joining TIAA/Nuveen, Mr. Salami was Executive Vice President and Global Controller, Corporate Solutions at Jones Lang LaSalle Inc. (JLL), a Fortune 500 global real estate company. Prior to JLL, he spent over eleven years at Deloitte serving Fortune 500 clients. Mr. Salami holds a Bachelor of Science in Management and Accountancy from Obafemi Awolowo University, a Master’s degree in Financial Economics from Ohio University, and an executive management certificate from Columbia Business School. He is a chartered accountant and a certified public accountant, licensed in Illinois.
Protective eyewear for workers who need corrective lenses
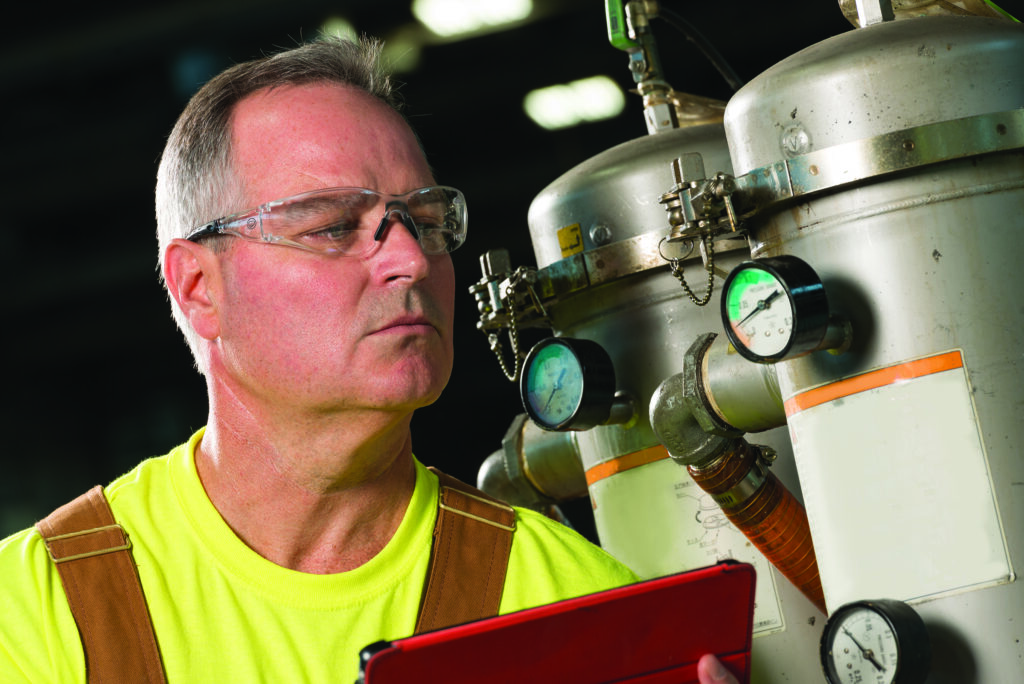
A worker who wears corrective lenses is not exempt from wearing proper eye protection. Typical corrective eyeglasses don’t provide the necessary impact and side protection of work-grade spectacles and goggles. These workers could wear over-the-glasses (OTG) protective eyewear. But, for a less-bulky, maximum-comfort solution, there is Brass Knuckle® Read (BKREAD-6010). Read is great-fitting, cost-effective, super-light bifocal eye protection available in five diopter strengths: 1.0, 1.5, 2.0, 2.5, and 3.0. A durable polycarbonate frame provides extra side protection and all-day comfort. And of course, the clear lenses are ANSI-rated hard-coated polycarbonate with BK-Anti-FOG. BK-Anti-FOG lasts a full two minutes, 15 times longer than European EN 166/168, the only current documented standard in the world. It is permanently bonded to the lens, will not wear off or wash off, and retains its anti-scratch, anti-static, and UV protection properties. The number of Americans between the ages of 55 and 64 in the workplace will increase by nearly 44 percent over the next decade. These workers will continue to read gauges and valve settings, set machinery controls, and monitor production screens on the plant floor. They will calibrate, cut, and tune. And they will take their protective eyewear off and slide on their readers to make this close work easier — unless we see the problem before the accident happens. Even the revised ANSI/SEA Z87.1-2015 standard recognizes the need for protective readers that offer magnification for the wearer. Brass Knuckle® meets this need with Read BKREAD-6010.
Cascade Corporation celebrates 80 Years in business
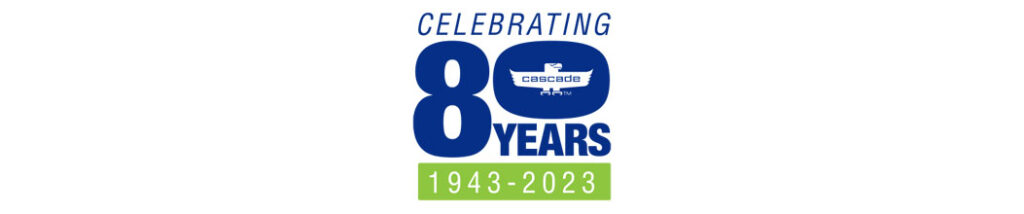
Founded in 1943, Cascade Corporation, the global manufacturer of attachments, forks and related technologies for forklifts and AGVs as well as a leader in quality mast products and manufacturer of construction attachments, celebrates a momentous 80th anniversary this year. First opened as a small, five-person machine shop in Portland, Oregon, Cascade has since grown into a global operation with over 3,000 employees and 33 locations around the world including manufacturing plants, offices and distribution centers. This global reach gives Cascade teams the unique ability to coordinate operations across their facilities worldwide to meet customers’ needs anywhere, anytime. Quality teamwork is the foundation of Cascade’s success, empowering employees to collaborate on an international stage while providing superior local service and support customers depend on. “The Cascade story and product advancement are directly related to our employees around the world who work every day to provide high-quality solutions along with reliable support for our customers,” says Davide Roncari, President & CEO of Cascade Corporation. “Their commitment, passion and innovation make us who we are today – and will continue to serve us well in the future.” Over the past 80 years, as the industry has evolved, Cascade has evolved with it. Cascade’s extensive history has not only fostered global growth, but positioned Cascade as a leader in emerging material handling trends in areas such as automation, electrification and digitalization. From hydraulic attachments and custom fork products to all-electric AGV attachments and complete front-end mast/attachment combinations, Cascade has a solution for nearly every industry and application. Cascade is constantly innovating—working with state-of-the-art technologies and incorporating them into industry-leading solutions. Today, Cascade meets changing needs with products that offer integrated data solutions, sensor technology, advanced damage reduction, smart attachments and accessories, and a commitment to energy efficiency and sustainability. “We sincerely thank all of our customers around the world who have made it possible for Cascade to achieve this level of success,” says Roncari. “Cascade wouldn’t be in business and growing at the rate we have been without them. We look forward to providing many more decades of unparalleled service and industry-leading solutions.”
Mitsubishi Logisnext Americas breaks ground on new electric facility to meet growing demand in electric products
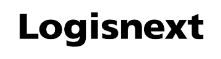
Mitsubishi Logisnext Americas (Logisnext), has celebrated the groundbreaking for its new production facility in Houston, Texas. The state-of-the-art facility will provide increased production capabilities to further support the growing demand for electric lift trucks and warehouse products. Located on Logisnext’s Houston headquarters campus, the new facility will support manufacturing of key electric warehouse products across the Jungheinrich®, Cat® lift trucks, Mitsubishi forklift trucks and UniCarriers® Forklift product lines. The new facility represents a key investment in Logisnext’s long-term electric growth strategy to support its customers throughout North America. With a total floor area of 73,000 square feet, the new facility will expand Logisnext’s current electric manufacturing capabilities by serving as a dedicated fabrication space for in-house welding and painting of masts and frames. The facility will also integrate cutting-edge technologies such as Mixed Model Line Design, Industry 4.0 process monitoring and one-piece flow. The expansion of robotic welding, along with the optimization of paint capacity and weld fixtures, will contribute to Logisnext’s ongoing focus for improved efficiency. “Today marks an exciting milestone for Logisnext as we break ground on our newest electric forklift manufacturing facility in Houston,” said Jay Gusler, executive vice president of Operations at Mitsubishi Logisnext Americas. “The material handling industry is rapidly changing, and we’re proud to be on the forefront of this change. We’re committed to investing in our manufacturing capabilities and new product development to ensure we continue providing our customers with the most advanced, yet sustainable, electric products and solutions in the future.” On August 23, the company celebrated the start of construction with a groundbreaking ceremony alongside its Houston campus employees. Leading the groundbreaking was Ken Barina, President, Mitsubishi Logisnext Americas and Jay Gusler, Executive Vice President of Mitsubishi Logisnext Americas. Construction is expected to be completed in the first quarter of 2024.
Reusable Packaging Association announces the 2023 Excellence in Reusable Packaging Award winners
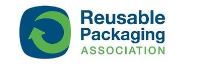
Award ceremony to take place September 12 at 3 pm PST at PACK EXPO Las Vegas in the RPA Pavilion The Reusable Packaging Association (RPA) has announced the winners of the esteemed 2023 Excellence in Reusable Packaging Awards. The awards feature a winner in each of three categories, Reusable System, Design Innovation, and Product Technology. The three winners in 2023 are OK Produce for Reusable System, Schaefer Plastics North America, LLC, for Design Innovation, and the Rehrig Pacific Company for Product Technology. OK Produce, a fresh produce wholesaler based out of Fresno, California, wins the Reusable System award for their implementation of a plastic pallet program in the distribution of perishable foods to their network of customers. OK Produce has introduced the reusable pallet program to 90% of their customer base, achieving cost-reductions, operational efficiencies, and solid waste reductions. Schaefer Plastics North America, a manufacturer of reusable transport packaging products, wins the Design Innovation award for their electrostatic discharge (ESD) bulk bin. The Grounder™ is a 48-inch-wide x 45-inch-long x 45-inch-tall plastic molded bin with metal plungers that protect shipped electronic parts against electrostatic contamination while reducing expendable packaging materials. Rehrig Pacific, a supplier of integrated sustainable solutions for logistics and delivery customers, including environmental waste and recycling, supply chain, and direct store delivery, wins the Product Technology award for their Vision Object Recognition (VOR) system. VOR offers warehouse customers an advanced technology solution featuring integrated components such as smart pallets, artificial intelligence, and machine learning to improve material handling, recordkeeping, inventory tracking, and quality control. Introduced more than a decade ago, the Excellence Award initiative maintains its steadfast momentum recognizing visionaries and commercial successes within the reusable transport packaging industry. The prestigious awards identify primary (end) user companies and suppliers who increasingly find new opportunities to innovate and advance reusable packaging in the supply chain. Award submissions are assessed by an independent panel of judges and are scored based on narration of the reuse opportunity, demonstration of business or economic improvements, and quantification of environmental impacts. RPA would like to recognize and thank our expert judges for the 2023 awards: Rick LeBlanc, editor, Reusable Packaging News Laszlo Horvath, associate professor and director, Center for Packaging and Unit Load Design, Virginia Tech Michelle Fay, program manager, StopWaste Ziynet Boz, assistant professor of Sustainable Food Systems Engineering, University of Florida About the Excellence Awards: The RPA Excellence in Reusable Packaging Awards recognize companies and organizations who have developed and implemented innovative and measurable reusable packaging solutions in a business-to-business supply chain. The Reusable System award recognizes primary user companies and associated product suppliers that have developed and implemented measurable reusable packaging solutions in a business-to-business supply chain. The Design Innovation award celebrates the commercial use of a cutting-edge product that has led to a benefit in the market. The Product Technology award salutes the deployment of smart automated systems with reusable packaging. The annual award program is celebrating its 12th year, and will honor the award recipients at an awards ceremony on September 12th at 3:00 pm, at the close of the RPA Learning Center at PACK EXPO Las Vegas.
Episode 413: Creating a Sustainable Supply Chain: Strategies for a greener future
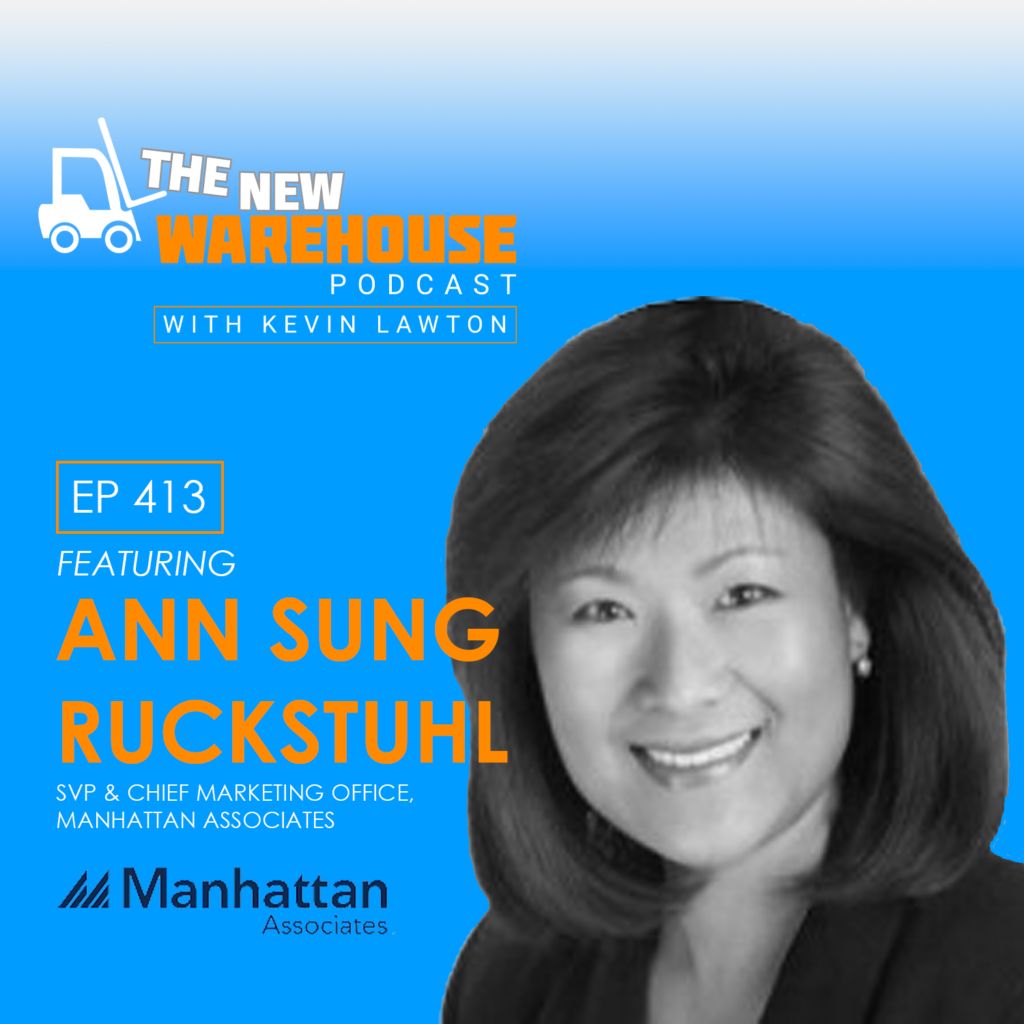
In this episode of The New Warehouse Podcast, Ann Sung Ruckstuhl, Senior Vice President and Chief Marketing Officer of Manhattan Associates, discusses sustainability and efficiency within the warehousing and logistics industry. Manhattan Associates is at the forefront of sustainable supply chain transformation through innovative systems and software solutions for the warehouse and transportation segments. Sustainability isn’t just a buzzword to Ann; it’s a critical aspect of modern business, intertwining passion and science. As Ann aptly puts it, “Sustainability has a bleeding hearts element, but there’s a science element to it as well. Without the passion and the science, nothing real will happen.” So, let’s embark on a journey to explore how sustainability is becoming an integral part of the warehousing and logistics landscape. The Urgent Need for a Sustainable Supply Chain Ann points out that the logistics industry is a significant contributor to global carbon emissions, responsible for 60% of the world’s carbon emissions. This alarming statistic makes it clear that we, in the logistics industry, are both guilty and empowered to drive change. A sustainable supply chain isn’t just a nice-to-have; it’s an urgent need. She emphasizes, “When you want to solve a problem, you look for the variable with the biggest influence. We’re the biggest variable in this whole equation. That’s one of the biggest reasons we must focus on sustainability.” Furthermore, we live in an era where technology, climate change, and shifting human behavior converge. Technology gives us the tools to gain visibility and control over supply chains. Climate change forces us to confront the urgent need to reduce our carbon footprint. And human behavior is shifting towards more sustainable choices. Ann explains, “We have a unique window of opportunity where technology, climate change, and human behavior change converge. This convergence empowers us to operate supply chains most efficiently, sustainably, and socially responsibly.” The Consumer-Driven Sustainability Ann highlights Manhattan’s survey results, revealing that 49% of global consumers prioritize sustainability in their purchase decisions. However, only 27% of retailers consider sustainability a top business priority. This gap between consumer expectations and retailer priorities is an area that needs attention. Ann emphasizes, “Consumers care about sustainability, and brands must catch up. The level of urgency is not matched, but the winners who make money in unified commerce do more on sustainability.” One way Manhattan Associates is empowering consumers is through improved visibility and control. By partnering with Google, Manhattan ensures consumers can access vital information such as product availability, location, and accurate delivery promises. This enhanced visibility benefits consumers and aligns with the sustainability goals of reducing unnecessary trips and improving overall efficiency. A Sustainable Supply Chain Yields Profitable Results Sustainability isn’t just about reducing environmental impact; it also makes good business sense. Manhattan Associates’ recent Unified Commerce Benchmark proves this. Leaders in sustainability practices within the commerce sector are experiencing revenue growth three to six times that of their counterparts. Ann shares some empirical facts from the benchmark. Leaders are twice as likely to offer sustainable packaging, 87% of them disclose sustainability practices related to product sourcing, and 60% disclose sustainability product-specific information. These actions resonate with consumers increasingly purchasing based on a brand’s sustainability efforts. Ann explains, “Sustainability is a good business. It’s important, measurable, trackable, and optimizable. These practices benefit the environment and boost revenue and profitability.” Key Takeaways for a Sustainable Supply Chain Urgent Need for a Sustainable Supply Chain: The logistics industry significantly contributes to global carbon emissions, making sustainability an urgent need. Converging factors, including technology, climate change, and shifting consumer behavior, provide a unique opportunity for positive change. Consumer-Driven Sustainability: Consumers prioritize sustainability, but many retailers lag in making it a top business priority. Enhanced visibility and control, facilitated by Manhattan Associates, empower consumers to make more sustainable choices. Profitable Sustainable Practices: Sustainable supply chain practices are environmentally responsible and drive revenue and profitability. Leaders in sustainable supply chain practices experience substantial revenue growth and are more likely to disclose sustainability efforts. The New Warehouse Podcast EP 413: Creating a Sustainable Supply Chain: Strategies for a Greener Future
AAR reports Rail Traffic for the week ending August 19, 2023
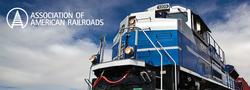
The Association of American Railroads (AAR) has reported U.S. rail traffic for the week ending August 19, 2023. For this week, total U.S. weekly rail traffic was 478,853 carloads and intermodal units, down 2.7 percent compared with the same week last year. Total carloads for the week ending August 19 were 228,972 carloads, down 0.6 percent compared with the same week in 2022, while U.S. weekly intermodal volume was 249,881 containers and trailers, down 4.6 percent compared to 2022. Four of the 10 carload commodity groups posted an increase compared with the same week in 2022. They included motor vehicles and parts, up 2,326 carloads, to 16,293; coal, up 1,486 carloads, to 69,773; and petroleum and petroleum products, up 781 carloads, to 9,420. Commodity groups that posted decreases compared with the same week in 2022 included grain, down 3,541 carloads, to 15,796; forest products, down 1,289 carloads, to 7,683; and farm products excl. grain, and food, down 1,011 carloads, to 15,638. For the first 33 weeks of 2023, U.S. railroads reported cumulative volume of 7,394,978 carloads, up 0.2 percent from the same point last year; and 7,828,854 intermodal units, down 9.2 percent from last year. Total combined U.S. traffic for the first 33 weeks of 2023 was 15,223,832 carloads and intermodal units, a decrease of 4.9 percent compared to last year. North American rail volume for the week ending August 19, 2023, on 12 reporting U.S., Canadian and Mexican railroads totaled 335,400 carloads, up 0.9 percent compared with the same week last year, and 329,819 intermodal units, down 6.8 percent compared with last year. Total combined weekly rail traffic in North America was 665,219 carloads and intermodal units, down 3.1 percent. North American rail volume for the first 33 weeks of 2023 was 21,354,794 carloads and intermodal units, down 4.0 percent compared with 2022. Canadian railroads reported 90,149 carloads for the week, up 3.1 percent, and 71,108 intermodal units, down 12.6 percent compared with the same week in 2022. For the first 33 weeks of 2023, Canadian railroads reported cumulative rail traffic volume of 5,204,561 carloads, containers and trailers, down 3.0 percent. Mexican railroads reported 16,279 carloads for the week, up 11.5 percent compared with the same week last year, and 8,830 intermodal units, down 16.2 percent. Cumulative volume on Mexican railroads for the first 33 weeks of 2023 was 926,401 carloads and intermodal containers and trailers, up 4.9 percent from the same point last year. To view the weekly rail charts, click here.
Staffing Employment holds steady in August
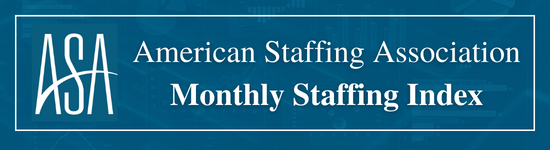
Over four-in-ten staffing firms report gains in new assignments Staffing employment edged up in the week of Aug. 7-13, with the ASA Staffing Index increasing by 0.1% to hold at a rounded value of 102. Staffing companies listed no one primary factor as a barrier preventing further growth. Staffing jobs were 4.4% below the same week last year. New starts in the 32nd week of the year inched down 0.8% from the prior week. More than four-in-10 staffing companies (44%) reported gains in new assignments week to week. The ASA Staffing Index four-week moving average increased from the prior week to a rounded value of 102, and temporary and contract staffing employment for the four weeks ending Aug. 13 was 4.7% lower than the same period in 2022. “Staffing employment has returned to the same levels we saw earlier this year even as it remains lower than last year’s historic numbers,” said Max Aldrich, ASA research coordinator. This week, containing the 12th day of the month, will be used in the August monthly employment situation report scheduled to be issued by the U.S. Bureau of Labor Statistics on Sept. 1.
Episode 412 Unlocking the secrets of labor market in the warehousing industry: Insights from Kim Vidrine of Employbridge
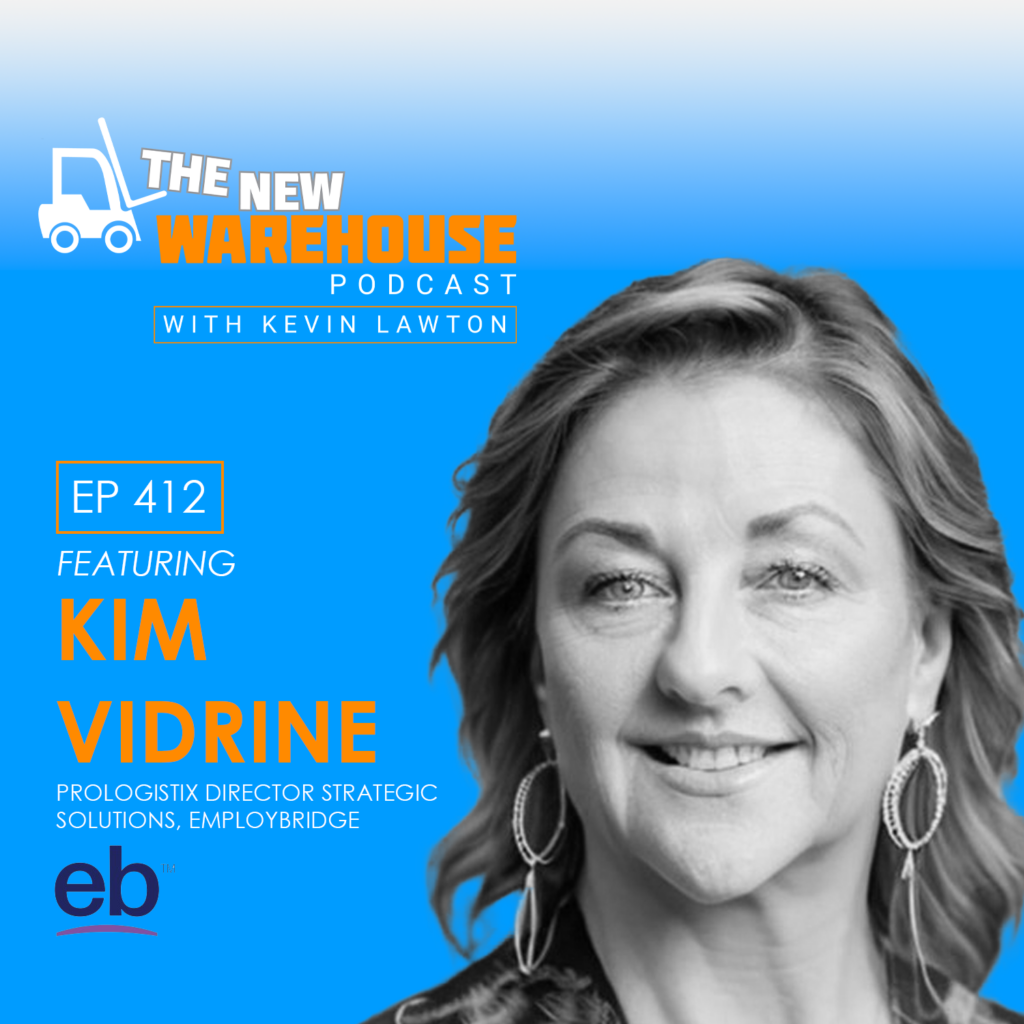
What is going on with the labor market in the warehousing industry? We delve into these pressing questions with our special guest, Kim Vidrine, Director of Operations at Employbridge, the supply chain’s largest staffing provider. Kim Vidrine is a seasoned professional with over two decades of experience at Employbridge. As the Director of Operations, she plays a vital role in overseeing the operations of this prominent staffing company. Employbridge boasts a national footprint with 400 branches across the United States, placing nearly 500,000 associates in jobs each year. Under the Employbridge umbrella, eight specialized brands cater to various supply chain roles. So if you’re curious about the current state of the labor market in the warehousing industry and how companies are navigating the challenges of attracting and retaining workers, this episode is for you! Now, let’s dive into the key topics covered in this podcast episode: The State of the Labor Market in the Warehousing Industry When discussing the current state of the labor market, Kim points out that while there’s a noticeable softening in the market, the demand for logistics positions continues to rise. She highlighted that, based on data from Indeed, job postings for logistics roles have increased by 55%. This growth brings the industry back to levels similar to January 2021. Kim adds, “The workforce participation rate is the space where we want to motivate people to get back into the workforce.” This segment took a significant hit during the COVID-19 pandemic but has been slowly recovering. This metric reveals the need to motivate people to rejoin the workforce, which segues into a discussion about Employbridge’s survey, “The Voice of the American Workforce.” Insights from “The Voice of the American Workforce” Survey Employbridge conducts an annual survey to understand what matters most to workers in the supply chain industry. In their 17th edition of the survey, they found valuable insights into the priorities and preferences of workers. Notable findings about the labor market in the warehousing industry from the survey include: Pay Rates: Pay remains the primary factor influencing job decisions for the labor market in the warehousing industry. Quote from Kim Vidrine: “Pay rates have consistently been the primary driver for people looking for a new job.” Flexible Schedules and Gig Work: Many respondents expressed interest in more flexible work schedules, with a particular preference for shorter shifts, allowing them to balance work with other obligations. Job Security: In a shift from previous years, job security has gained importance among workers, reflecting economic uncertainty. Respect and Appreciation: Treating employees with respect was identified as a crucial factor in building loyalty and retaining workers. Advancement Opportunities: Many logistics workers expressed willingness to invest their time in upskilling, highlighting the importance of training and advancement opportunities. Kim believes, “People are looking for commitment from their employers. They’re looking for a way forward, training opportunities, and appreciation.” Workforce as a Service: The Introduction of Blue Crew Employbridge’s recent acquisition of Blue Crew brings an innovative approach to the labor market in the warehouse industry. Blue Crew operates as a “workforce as a service” provider, offering a blend of a W-2 labor force, a cutting-edge platform, and data analytics. Kim shares, “We’re eliminating some of the obstacles to get people to work. This is going to revolutionize our industry” by offering flexibility for employers and employees. With a strong focus on the transparency and control provided by the platform, employers can select and manage their workforce while employees can choose opportunities that suit their preferences. Key Takeaways About the Labor Market in the Warehousing Industry Prioritize Competitive Pay Rates: The labor market in the warehouse industry continues to see compensation as a high priority. Attracting and retaining talented individuals requires competitive compensation rates. Competitive compensation improves engagement and dedication and fosters a sense of value and recognition within the organization. Offer Flexibility and Training: Embrace flexibility in work schedules and provide opportunities for upskilling. Workers are eager to learn and adapt to new technologies. Focus on Respect and Job Security: Show respect and appreciation to your employees. Make job security a priority, especially during times of economic uncertainty. The New Warehouse Podcast EP 412: Unlocking the Secrets of the Labor Market in the Warehousing Industry with Kim Vidrine of Employbridge
Yale earns green award for expansive lineup of lift truck motive power solutions
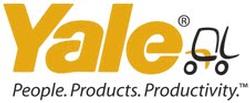
Yale Lift Truck Technologies announces its 12th consecutive annual recognition as a Green Supply Chain Partner by Inbound Logistics magazine. The recognition honors the company for its rigorous focus on developing and manufacturing a broad range of lift truck motive power solutions engineered to address the sustainability challenges of warehouse operations, most recently through the expansion of its integrated lithium-ion lift truck lineup. The company’s full set of options, the Yale Power Suite, gives operations the freedom to select the power source that best suits them, incorporating lithium-ion batteries, hydrogen fuel cells, internal combustion engines and lead-acid batteries across a comprehensive range of lift trucks. Dealers and sales staff guide customers through a consultative process to help select the right power option that allows them to meet their unique requirements, rather than being restricted to limited choices. “Today’s warehouses are striving towards aggressive goals to reduce their carbon emissions, and those challenges don’t exist in a vacuum – they’re simultaneously under pressure to meet growing productivity demands, while also navigating labor shortages and safety challenges,” says Brad Long, Brand Manager, Yale Lift Truck Technologies. “These businesses need lift truck power technologies that not only help them to make progress towards their sustainability goals but also address the full scope of the needs of their operation.” Yale most recently added to its roster by introducing 4,000-pound capacity integrated lithium-ion-powered three-wheel and four-wheel models. The new models allow warehouses in industries like food and beverage, 3PL and retail and e-commerce to reap the benefits of an advanced electric power source, whether transitioning from internal combustion engine-powered trucks or lead-acid batteries. Both the ERP040VTL, the three-wheel model, and the ERP040VFL, the four-wheel model, buck the traditional approach in which a battery box replacement converts counterbalanced lift trucks from lead-acid to lithium-ion battery power. Instead, the trucks are designed from the ground up around a fully integrated, space-saving lithium-ion battery pack. Lithium-ion batteries generate zero harmful emissions, and a lithium-ion battery pack can last over four times longer than a lead-acid battery, helping reduce recycling waste.
Iron Ore and Steel continue to lead the way for US Great Lakes Shipping in July
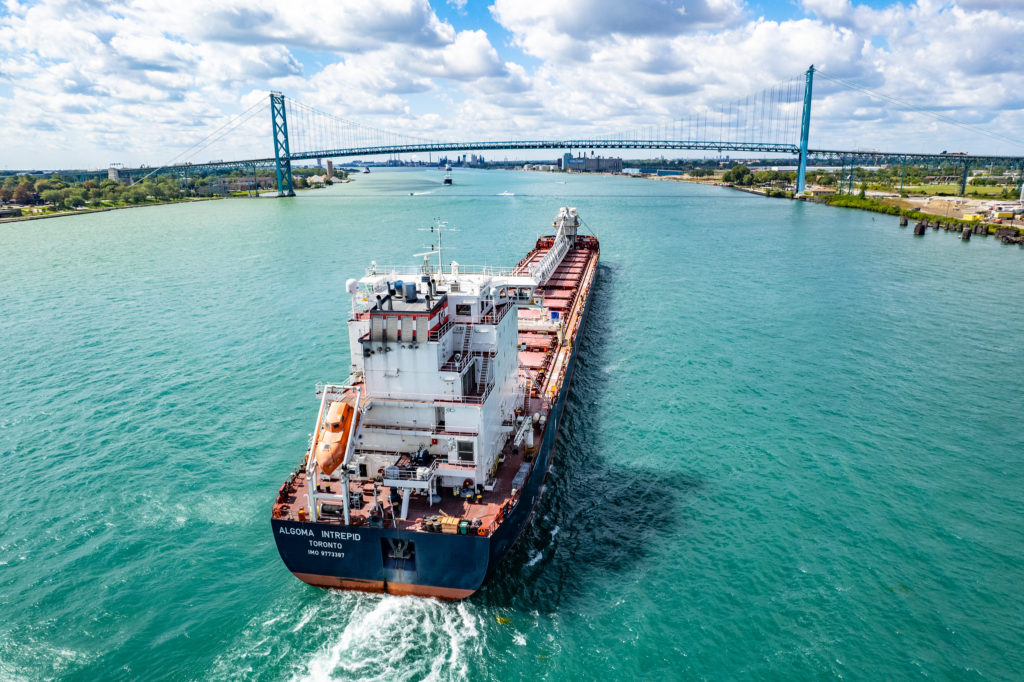
US Great Lakes shipping activity continues to be on par with the previous year, as approximately 15.7 million tonnes of total cargo traffic traveled the seaway system for the year to date. Two key steel making commodities continue to show strong traffic volumes, with more than 3 million metric tonnes of iron ore moving through the system thus far (a year over year increase of 351,000 tonnes), and more than 1 million tonnes of coal transiting the system (a year over year increase of 248,000 tonnes). In addition, cement and stone showed increases over the prior year’s traffic, with 900,000 tonnes of cement transiting the system (an increase of 80,000 tonnes) and 146,000 tonnes of stone traveling through the system (an increase of 69,000 tonnes, or almost 90%). The Port of Duluth-Superior is one of the key ports managing much of this traffic, having recently handled the most iron ore from Duluth-Superior in a single month since May 1993. Several other bulk cargoes also posted summer gains through North America’s furthest-inland seaport, including salt (up 13.2% YOY), limestone (up 5.9% YOY) and cement (more than double the 2022 pace). “It’s definitely been a good first half for many of the bulk cargoes that move through our port, led of course by our king cargo, iron ore,” said Deb DeLuca, executive director of the Duluth Seaway Port Authority. “We’re seeing the effects of steady manufacturing and construction activity throughout the Great Lakes region, which helps drives demand, and also an increase in exported iron ore, which was up more than 26% over last year’s pace through July.” In addition to a brisk pace of cargo movement through the port (11% ahead of last year’s pace through July 31), Duluth is also progressing on construction of a new 56,000-square-foot dockside warehouse at the Clure Public Marine Terminal. This project is expected to reach completion by the end of August, increasing Duluth Cargo Connect’s total warehousing capacity over 500,000 square feet. The developments taking place in Duluth are representative of a vibrant North American maritime shipping industry that plays a central role in supporting economic strength. Per the recently released economic study “Economic Impacts of Maritime Shipping in the Great Lakes – St. Lawrence Region” by Martin Associates, shipping on the Great Lakes St. Lawrence Seaway supported: $36 billion (USD) in economic activity; more than 240,000 jobs that generated more than $17.8 billion (USD) in wages; the movement of 135.7 million metric tons of raw materials and finished goods; and $6.3 billion (USD) in taxes. “The exciting developments taking place at ports like Duluth and the statistics shown in the independent Martin economy study are all evidence of why marine shipping remains the strongest, most significant, and most sustainable link in the North American supply chain,” said Bruce Burrows, President and CEO of the Chamber of Marine Commerce (CMC). “The current mix of visionary research and development activity and service expansion by CMC members, coupled with unprecedented engagement and support by federal, provincial, and state governments, is setting the stage for a stronger and greener supply chain that will benefit business and consumers for generations to come.”
UgoWork signs pan-Canadian distribution agreement with Liftow
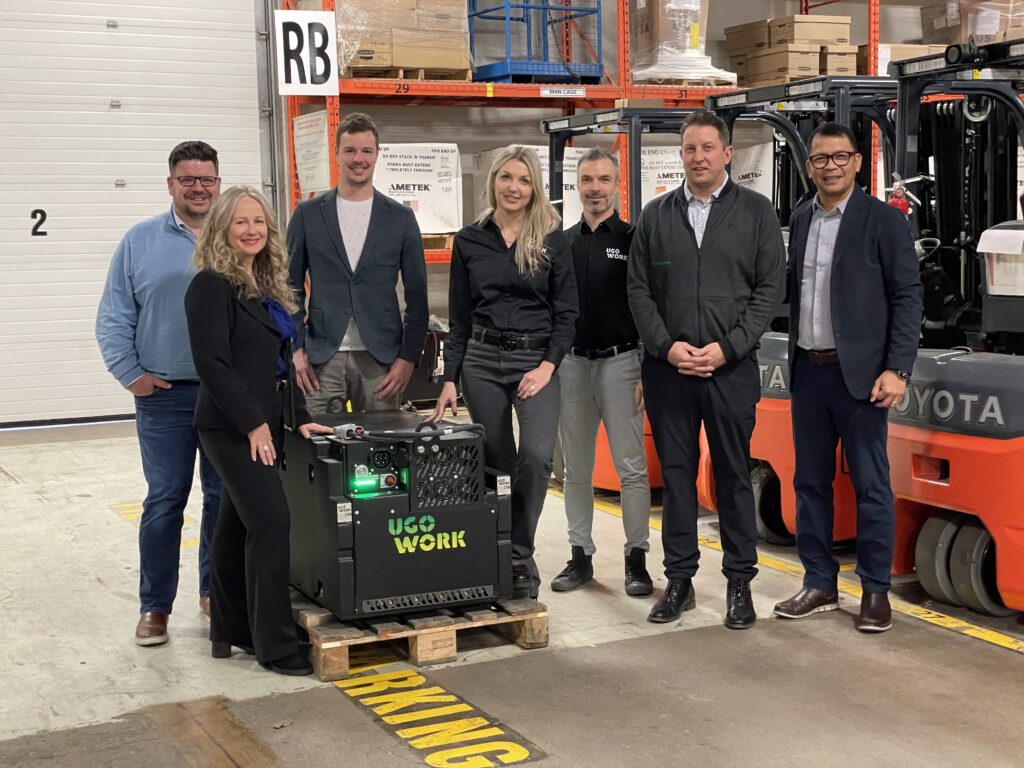
UgoWork®, a Canadian energy solutions provider specialized in the material handling industry, has announced that it has signed a pan-Canadian distribution agreement with Liftow Limited, Canada’s partner for end-to-end Toyota forklift and material handling solutions since 1960. In an effort to quickly expand Liftow’s offering, its sales and technical teams in Ontario and Québec have already been trained on UgoWork products. Under the official agreement, Liftow will offer UgoWork’s complete line of lithium-ion batteries for electric forklifts. In addition, Liftow customers will be able to take advantage of UgoWork’s flexible pay-for-performance consumption model. Also known as Energy as a Service, this industry-first consumption model offers an array of benefits, including minimized upfront costs and capital expenditures. Companies only pay for what they use, which contributes to healthier bottom lines. Furthermore, UgoWork’s team of battery experts works alongside customers to proactively monitor their lithium-ion batteries’ state of health to optimize fleet uptimes as well as drastically reduce unplanned maintenance and replacement costs. “We are thrilled that Liftow, as a reputable Canadian leader, recognizes the tremendous value UgoWork can bring to material handling teams—in terms of productivity, capacity and cost-savings,” said Philippe Beauchamp, President and CEO at UgoWork. “Thanks to this agreement, companies throughout Canada can speed up their material handling throughput without breaking the bank. We look forward to working alongside the Liftow teams as they continue to expand their service offering with innovative new technologies and operational approaches that are adapted to today’s customer challenges.” UgoWork convened in late 2022 in Toronto, where key representatives from Liftow Limited including Amanda Coulson, General Sales Manager – Central Division; Sean McBurney, Equipment Sales Manager – Central Division; and Red Andal, Marketing and Customer Experience Manager; to formalize the important distribution agreement.