Hy-Brid Lifts has announced Gary Coke as director of sales covering the south-central United States. Coke’s responsibilities include providing customer support as well as continuing the growth and channel development of the Hy-Brid Lifts line of low-level scissor lifts.
“I am excited to join this team and look forward to the opportunity to work with past and future customers. Coming from equipment manufacturing, I understand the importance of quality equipment and customer service backed by a solid service department,” said Coke. “After meeting the Hy-Brid Lifts team and seeing all of the new products in the pipeline, it’s no surprise that this company is continuing to grow, and I look forward to being a part of that growth.”
Coke brings 19 years of industry experience to his new role, largely derived from his time in equipment manufacturing with SkyJack. He spent a majority of his career in sales with a strong emphasis on customer relationships and going above and beyond for every customer.
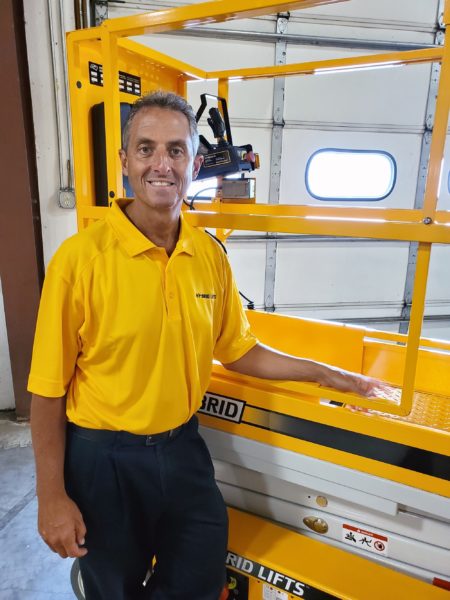
“The entire Hy-Brid Lifts team is excited to have Gary on board to serve the south-central United States. Gary has a wealth of sales and rental industry knowledge that will strengthen our ability to serve our customers,” said Dave Wanta, Custom Equipment LLC vice president of sales. “Gary Coke is a valuable addition to the team, and we look forward to the contributions that he will provide for our company’s continued growth.”