Episode 481: Achieving a fully autonomous supply chain with Nimble Robotics
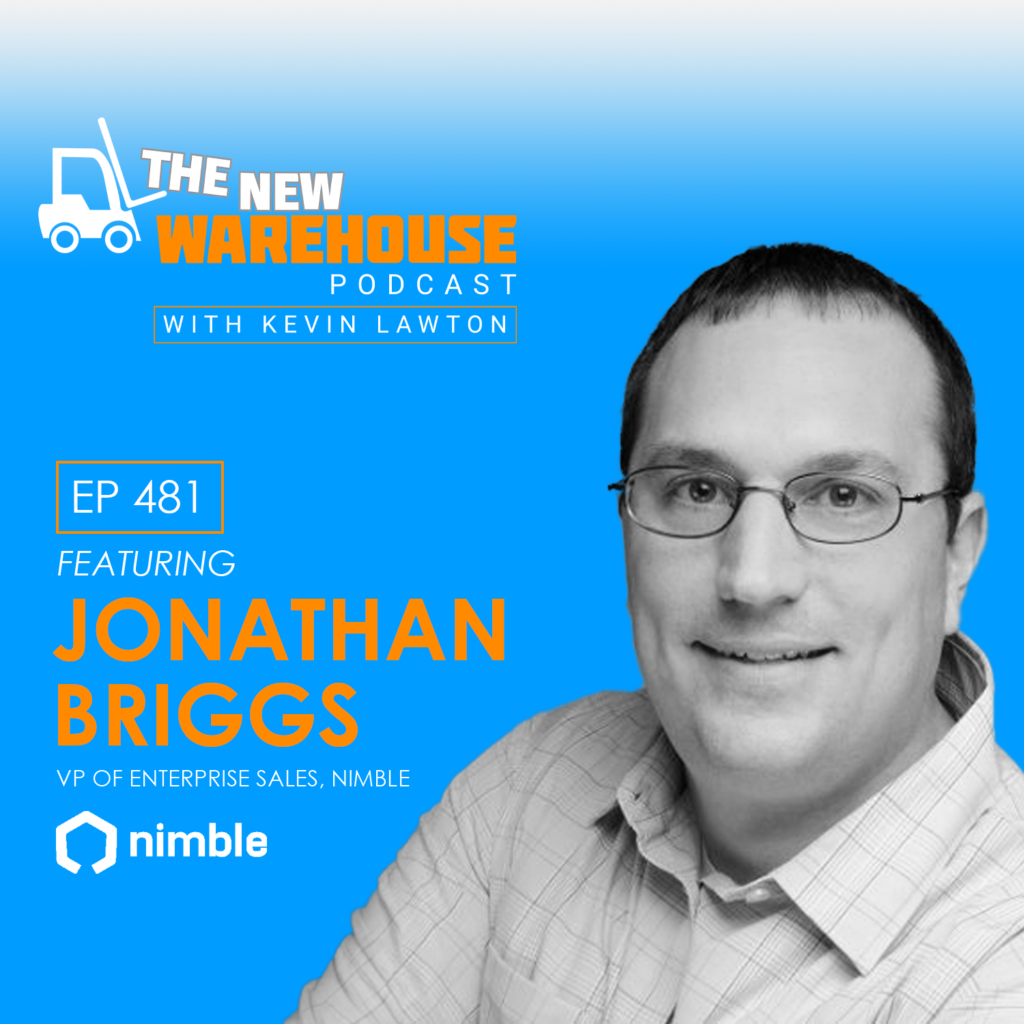
In this episode of The New Warehouse Podcast, Jonathan Briggs, VP of Sales and Solutions at Nimble Robotics, delves into Nimble’s transformative approach to logistics. Positioned at the vanguard of the industry, Nimble Robotics is redefining third-party logistics (3PL) with its fully automated solutions, merging cutting-edge robotics and artificial intelligence (AI) to reshape how logistics operations are conducted today. Overcoming Legacy Hurdles with Advanced Automation The logistics sector’s persistent challenges of increasing throughput and optimizing labor efficiency necessitate innovative solutions. Briggs reflects on the initial hurdles: “Finding the first customer willing to take the plunge into large-scale automation was not easy.” In response, Nimble innovatively became its own first client, pioneering a fulfillment network that fundamentally transforms warehouse configurations. Nimble significantly bolsters building efficiency by discarding traditional racks and aisles and adopting a vertical operational model. This strategic overhaul addresses the spatial and workforce limitations that typically constrain conventional warehouses. Overcoming Labor Obstacles Through Robotics Jonathan Briggs shares Nimble’s technology’s transformative impact on logistics workforce dynamics: “In my warehouse, I don’t have any pickers as a function of our building. We’ve eliminated the pick side of the business which is usually a good third if not two-thirds of the headcount in a building.” This strategic reduction in labor dependency is at the core of Nimble’s innovation. By implementing six-axis robots that excel in tasks requiring human-like vision, touch, and force control, Nimble not only enhances logistical precision, speed, and scalability but also significantly reduces the need for manual labor. Towards a Fully Autonomous Supply Chain Briggs casts a forward-looking perspective: “The future is going to be autonomous.” He elaborates on the company’s forward march towards comprehensive supply chain autonomy. Nimble not only aims to refine warehouse operations but also to integrate autonomous delivery systems, which are poised to revolutionize logistics efficiency at an unprecedented scale. “We’ve got a lot of stuff in development right now in terms of robotic sortation where we can do strategic sorts for our carriers,” Briggs reveals, indicating that Nimble’s innovations could streamline complex logistical tasks. “We want to be end-to-end autonomous when it’s all said and done.” Key Takeaways Nimble Robotics is leading the charge in transforming logistics with its fully automated 3PL solutions. Nimble enhances fulfillment operations’ speed, accuracy, and scalability through advanced robotics and AI. The company’s vision extends to achieving end-to-end autonomy in the supply chain, indicating a transformative future for logistics. The New Warehouse Podcast Episode 481: Achieving a Fully Autonomous Supply Chain with Nimble Robotics
Piab USA announced a new location in Canton, MA
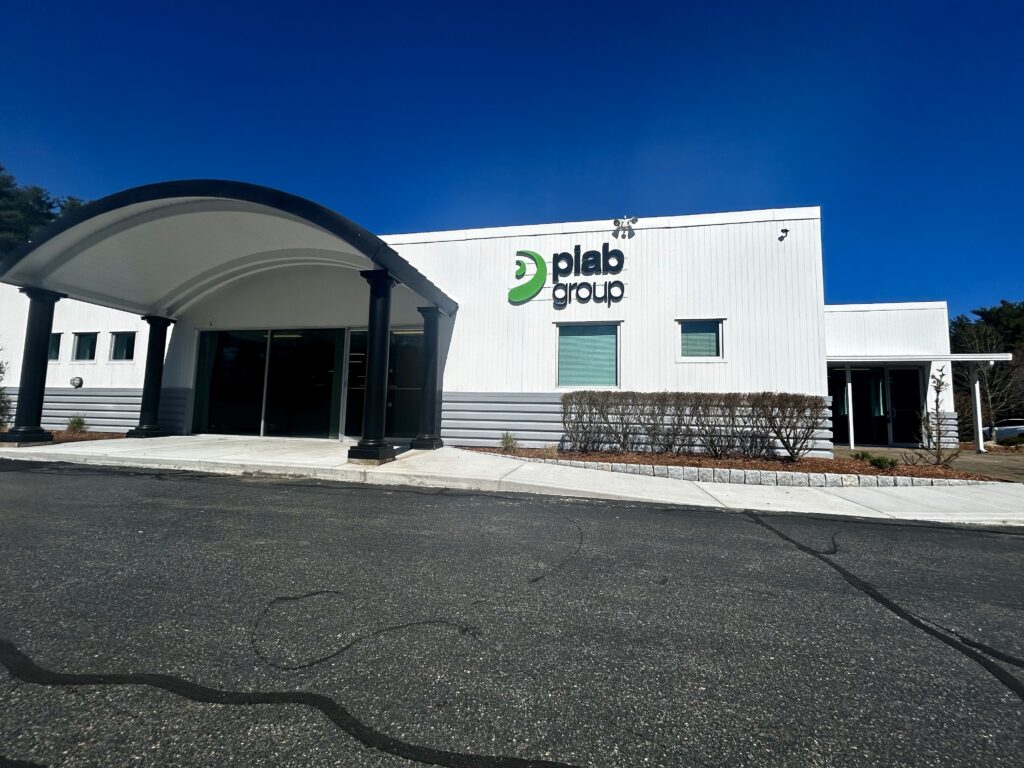
Piab USA has announced the relocation of its headquarters to a new, state-of-the-art office facility in Canton, Massachusetts. This move is part of Piab’s strategic initiative to accommodate rapid growth and expand its capabilities in providing innovative automation technologies. The new office, located at 100 Energy Drive, will serve as the central hub for Piab USA’s operations, housing its management, sales, support, R&D and distribution center. Enhanced Facilities for Innovation and Collaboration The new Canton office is designed to foster innovation and collaboration among Piab’s teams. Equipped with modern amenities, advanced technological tools, and spacious conference areas, the facility will enhance the company’s ability to develop and deliver high-quality automation solutions. The office layout encourages open communication and teamwork, which are key to Piab's agile and responsive business approach. A Word from the President of Piab USA “We are thrilled about the move to our new office in Canton, which marks a significant milestone in our journey,” said Ed McGovern, VP of Piab USA. “This new facility not only supports our growth ambitions but also reflects our commitment to providing our employees with a great working environment and our customers with exceptional service. We look forward to becoming an integral part of the Canton community and continuing to drive innovation in industrial automation.”
Conveyco Technologies welcomes Brian Keiger as VP of Sales
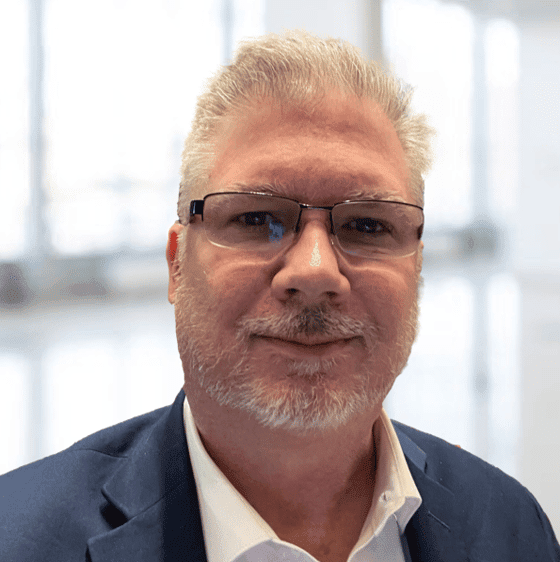
Conveyco Technologies has announced the appointment of Brian Keiger as Vice President of Sales. In this role, Keiger will lead Conveyco’s sales organization and drive revenue growth through strategic sales initiatives. Keiger brings over 30 years of sales and industry experience in the supply chain and warehousing automation industry to Conveyco. He most recently served as Sales & Marketing Director at Movu Robotics, where he was instrumental in expanding the company’s customer base across multiple sectors, including food & beverage, retail, automotive, and healthcare. “We are thrilled to welcome Brian to the Conveyco team,” said Raymond Cocozza, CEO of Conveyco Technologies. “His proven track record of success, deep industry expertise, and passion for fostering client relationships make him an ideal fit to spearhead our sales efforts.” At Conveyco, Keiger aims to implement agile and responsive sales processes to drive efficiency and productivity. His strong leadership skills and commitment to customer satisfaction will be invaluable assets as the company continues its growth trajectory. In addition to his professional accomplishments, Keiger is deeply involved in STEM education initiatives. He serves on the Industry Advisory Council for the National Center for Supply Chain Technology Education and as a Board Advisor for the Queen City Robotics Alliance. His dedication to nurturing the next generation of innovators aligns well with Conveyco’s corporate vision and forward-thinking approach. “I am excited to join the talented team at Conveyco Technologies,” said Keiger. “The company’s dedication to bringing our clients cutting-edge solutions and its commitment to excellence resonate strongly with me. I look forward to working closely with our customers and partners to deliver exceptional value with our RightFIT approach.” Keiger holds a bachelor’s degree in mechanical engineering and has received recognition for his achievements, including the 2013 Edison Award for Supply Chain Innovation.
Pettibone Celebrates 75th anniversary of Cary-Lift
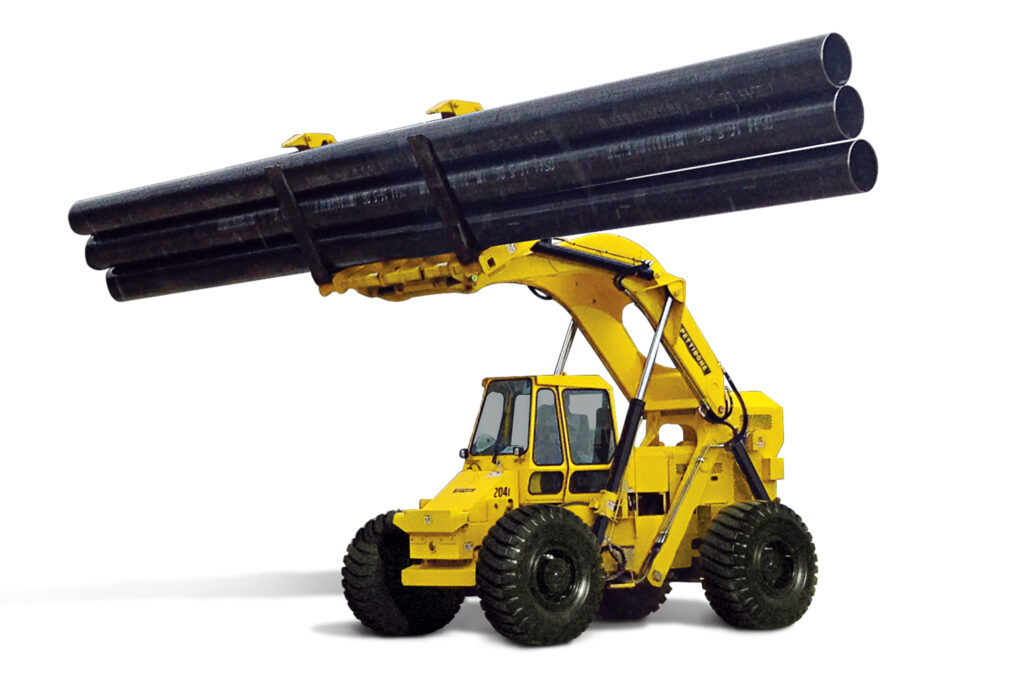
Pettibone Traverse/Lift, LLC is celebrating the 75th anniversary of the Cary-Lift, which became the world’s first forward-reaching, rough-terrain material handler upon its invention by Phil LaTendresse in 1949. Shortly after its origin, the Cary-Lift product line was acquired by Pettibone, and it remains an industry-leading solution for pipe, pole and log handling to this day. The inventor’s grandson, also named Phil LaTendresse, is currently Pettibone’s director of engineering and product support. “A local sawmill owner was looking for a better solution for unloading logs, and that’s when my grandfather came up with the concept of being able to reach forward with a forklift, which inspired the first prototype Cary-Lift,” said LaTendresse. “He built about 13 machines before selling the business to Pettibone Mulliken Corporation.” The Pettibone Cary-Lift provides distinct design advantages over wheel loaders and other tools often used to move pipe, poles or similar materials, making the machine a popular choice for worksites all around the world. The unique Cary-Lift overhead lift arm design gives the operator full front visibility, and its solid steel body frame allows the machine to take full loads into sharp turns without sacrificing stability. “I see the future of the Cary-Lift as evolving, just like it always has,” said LaTendresse. “The first machines were in forestry. We evolved into pipe and pole handling. And we’re looking ahead toward diesel-electric hybrids and new applications, trying to find that next new niche.”
AGV wireless evolution
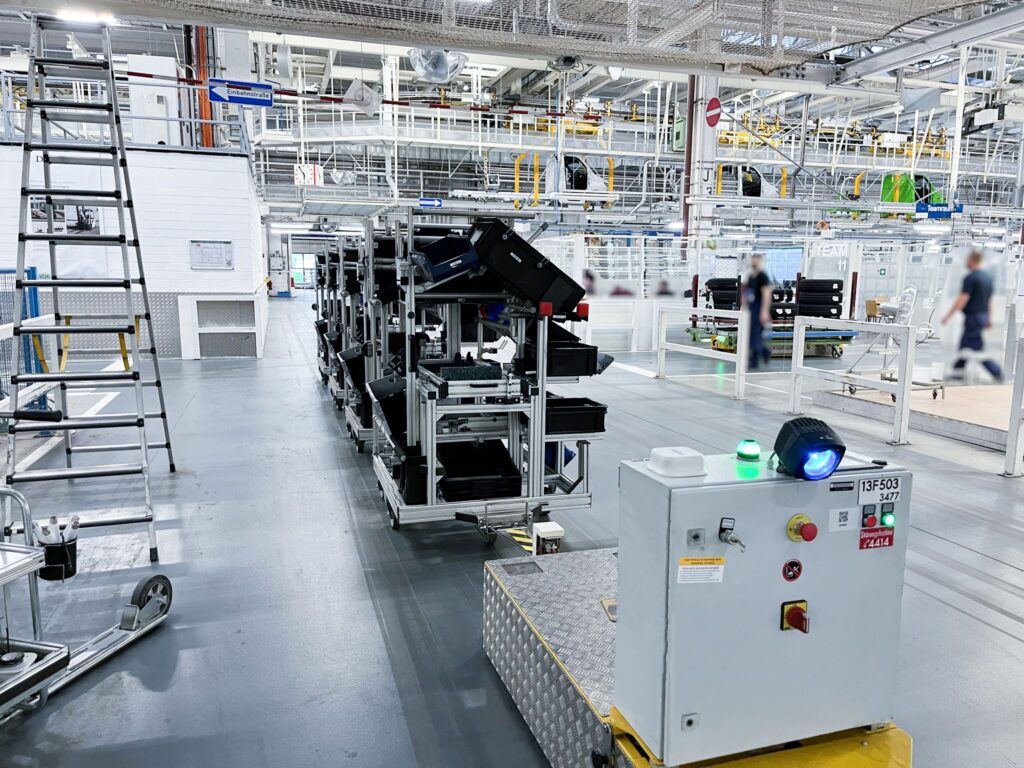
Discover how HMS Networks’ wireless expertise and Anybus products took Mercedes-Benz’s Automated Guided Vehicle (AGV) installation to the next level. When Mercedes-Benz wanted to expand its AGV installation, they called HMS. HMS provided the wireless expertise, products, and hands-on support to ensure the AGVs moved efficiently and safely around the factory. Mercedes-Benz Mercedes-Benz, a globally recognized automotive manufacturer, is renowned for its innovative technology, craftsmanship, and luxury design. At their state-of-the-art automotive factory in Ludwigsfelde, over 70 AGVs move automotive parts to the assembly line. These AGVs transport everything from heavy engines to smaller electronics across distances ranging from 300 to 800 meters. Each AGV is equipped with an onboard Programmable Logic Controller (PLC) from Siemens or Schneider Electric, which ensures their efficient and safe navigation. Good communication is key Guiding the AGVs effectively relies on good communication between the AGVs and the factory’s control system. This communication enables the factory to track the AGVs’ whereabouts, cargo, and real-time status. Mercedes-Benz’s previous AGV system used Bluetooth technology and HMS’ Anybus Wireless Bolt and Anybus Bridge products. However, they wanted to improve the system’s efficiency and be able to comply with the Machinery Regulation (EU) 2023/1230, which becomes mandatory in January 2027. Maximilian Lichan explains: “While Bluetooth worked well, we now want to enhance our AGV system to support higher throughput, fast roaming, and lower latency. We also need to comply with the soon-to-be mandatory EU safety regulations. Equally important, we want the equipment and experts from the same company, and we want them to come onsite, install the equipment, and verify that everything works”. Time to see how HMS helped implement a wireless system to meet the needs. HMS wireless experts pave the way Mercedes-Benz provided key information, such as floorplans, to HMS’ wireless experts. Using this information, HMS first conducted a predictive site survey to determine the optimal placement and number of access points required. HMS then visited the factory to verify the accuracy of the survey and make any necessary adjustments. Mercedes-Benz used the updated predictive site survey to install the required power outlets and network cabling. Once the required infrastructure was in place, HMS returned to install and configure the Anybus Wireless products before verifying that the installation worked as planned. Anybus wireless products The wireless infrastructure uses Anybus Access Points powered by Anybus PoE L2 Managed Switches, with an Anybus Wireless Bolt II mounted on each AGV. The Anybus Wireless Bolts handle communication from the AGVs to the traffic control system and connect to the 12 different access points in the factory’s ceiling. As an AGV moves out of range of one access point, it transitions to the next, ensuring uninterrupted communication. A critical aspect to the project’s success was the utilization of the 5GHz frequency band, while the Bolt II’s similarity to its predecessor also simplified the installation. Maximilian explains: “We wanted to use the 5GHz frequency band where we have four dedicated channels that didn’t interfere with our existing systems. It was also convenient that the Bolt II fits in the same hole as the original Bolt”. The results With the wireless expertise of HMS and their Anybus Wireless products, Mercedes-Benz successfully achieved its goal of efficient and safe transportation of goods within the factory. Maximilian happily reflects on the outcome: “Everything worked as we hoped. The connection is very stable, and we are now able to comply with the safety machinery regulation. The support for more bandwidth has even allowed us to manage and configure the AGVs remotely, which, while not a key objective is a nice bonus”. Finally, what are your tips to users who are thinking of going wireless? “A key factor for us was that HMS was on hand to design and install the wireless infrastructure. That was important for us. We wanted to have wireless experts onsite to ensure that everything went smoothly. We’re not wireless experts, HMS is. We make cars, which you probably already know,” Maximilian adds with a smile.
Cavaion Baumann USA welcomes Paul Bilson as Director of Dealer Development and National Accounts.

Paul will lead the effort to strengthen the Baumann dealer network throughout the U.S. and Canada. National accounts will also fall under Paul’s responsibility. Paul comes from Hyundai Material Handling where he was responsible for directing dealer development, national accounts, and government sales. He was a key contributor to Hyundai’s rise in the North American market over the past twelve years. He has also been involved with organizations such as MHEDA and NPCA (National Precast Concrete Association,) and will continue to be going forward. “Paul is a great fit for our organization,” said Rob Alling, President, and CEO of Baumann USA. “He comes highly regarded, and his relationships with forklift dealers throughout North Americas, in addition to his experience working with major accounts in the precast, steel, and lumber industries is what we were looking for to help grow our presence in the U.S. and Canada,” added Alling. “There is untapped potential for the use of heavy-duty side loaders in North America, and I am excited to be representing Baumann, a brand with a reputation for quality and design, much like the Hyundai big trucks I represented for many years,” Bilson said.
Invent Analytics wins RetailTech breakthrough award
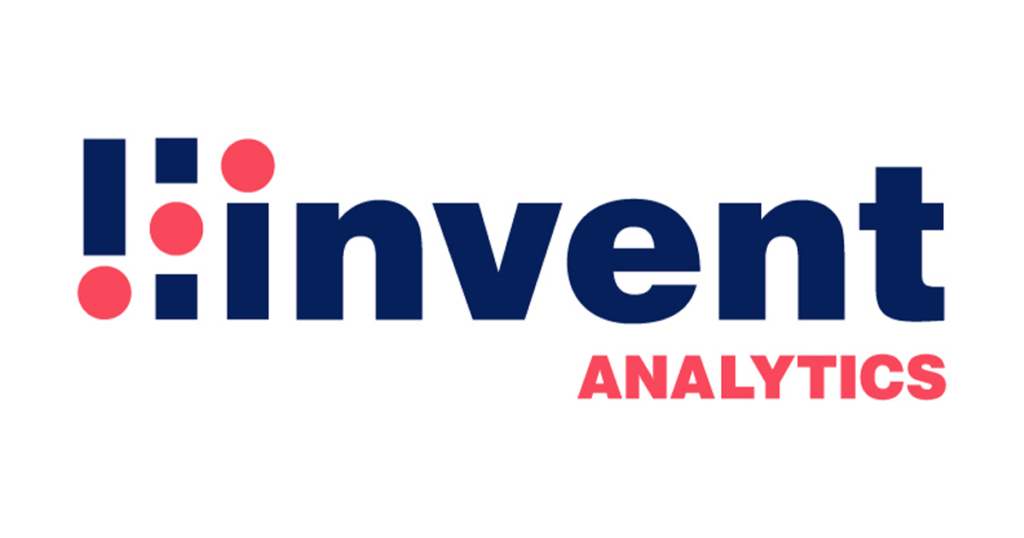
The winning AI-driven Returns Positioning solution streamlines and profit-optimizes omni-channel returns by determining the optimal position for each item in real time Invent Analytics, announced it has won “Return Management Innovation of the Year” in the 2024 RetailTech Breakthrough Awards, an annual program that highlights the world’s best companies, products, and services in the retail technology industry. Invent Analytics was honored for its AI-driven Returns Positioning solution that enables omni-channel retailers to optimize the returns process for greater efficiency and profitability. The RetailTech Breakthrough Awards aims to perform the most comprehensive evaluation of retail technology tools, services, and companies today. With nominations coming in from innovators around the world, the program honors those who break through the crowded marketplace. Invent Analytics stood out for helping retailers leverage AI technology to overcome the rising complexities and costs of managing omnichannel returns. Invent Analytics’ Returns Positioning solution optimizes the returns process through: Intelligent rerouting: AI automatically determines the optimal position for each returned item in real-time Profit maximization: Inventory is placed where it has the highest probability of selling with the lowest routing cost Future returns forecasting: Return pattern forecasts to support proactive planning and efficient inventory allocation “While omni-channel has become the new standard, many retailers still manage returns based on simplistic rules. This outdated approach cannot handle the sheer volumes or complexities of omnichannel returns, and retailers end up with misallocated goods, lost sales, unnecessary liquidations, and lower profits,” said Tav Tepfer, Chief Revenue Officer, Invent Analytics. “At Invent, we offer a better way and we can go live in just a few weeks. Our Returns Positioning solution uses AI-decisioning to analyze every possible variable, then instantly determines where to route each returned item to give it the highest probability of reselling for the most profit before the season ends.” Notably, Invent Analytics’ Returns Positioning solution offers rapid implementation, and retailers see results in as little as 90 days. By leveraging the solution, Invent Analytics’ clients have successfully: Increased sales by 25-50% through the quicker reintroduction of returned items to the sales floor Increased profitability by sending items to where they have the highest likelihood of resale Reduced liquidations by 2-5% by optimally positioning inventory to decrease on-hand units at the end of the season Tepfer continued, “We’re very excited to be named a winner in this year’s RetailTech Breakthrough Awards. Our team looks forward to continuously delivering innovative, AI-driven solutions that ensure our retail clients are well-equipped to satisfy the demands of modern consumers.”
Columbia Machine Palletizer Division joins Techmatik at Warsaw Pack in Poland
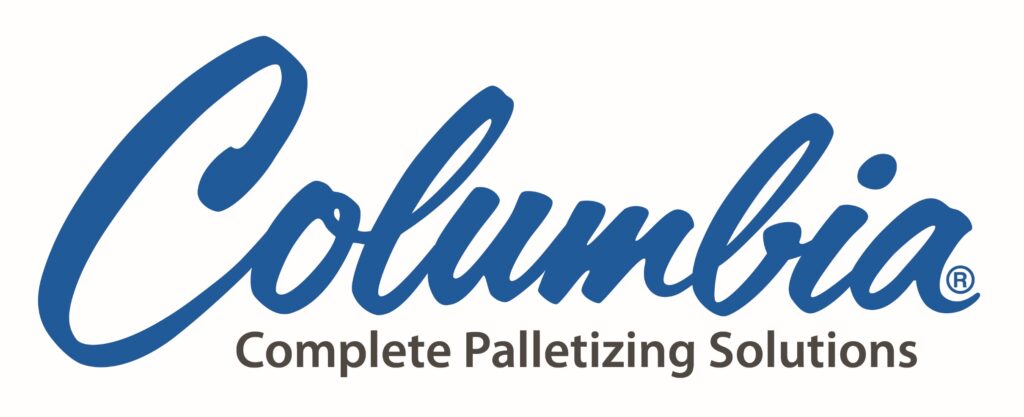
A team from the Columbia Machine Inc. Palletizer Division joins Techmatik S.A., a Columbia Machine Company, in Poland for Warsaw Pack to expand the worldwide presence of Columbia’s conventional palletizer product line. Warsaw Pack is an international trade show focusing on packaging technologies and finished goods packaging. The show is taking place at Ptak Warsaw Expo, the Largest Exhibition and Congress Center in Central Europe. This show brings together all branches of the packaging industry and allows visitors to see all of the latest industry innovations available from over 375 exhibitors. The fair will take place April 23rd – April 25th, 2024.
Brent Barcey joins OSARO as SVP to fuel growth in e-commerce

Barcey’s broad experience in selling advanced robotics, logistics and fulfillment solutions into leading e-commerce operations aligns with OSARO’s mission to broaden market adoption of its precision pick-and-place robotics solutions in fast-paced e-commerce environments. OSARO has announced the appointment of industry veteran Brent Barcey as senior vice-president of corporate development. Barcey brings 25 years of experience growing global businesses and teams in the e-commerce, warehousing, and logistics industries to OSARO, where he will spearhead the company’s commercial growth as it addresses the surging global demand for e-commerce fulfillment solutions. Barcey joins OSARO from Plus One Robotics, where he served as vice president of sales and business development. In this position, he played a key role in driving revenue and establishing strategic partnerships. Prior to Plus One Robotics, Barcey held the position of executive director of global sales at FANUC America Corporation, a leading industrial robot manufacturer. He is currently Chair of Events for The Robotics Group Committee at the Materials Handling Industry (MHI) trade association. “We are pleased to welcome Brent Barcey to the OSARO team,” said Derik Pridmore, CEO of OSARO. “Brent’s proven track record in sales and business development within the robotics industry makes him an invaluable asset. His deep understanding of the global e-commerce landscape and the critical role automation plays in fulfilling customer demands will be instrumental in propelling OSARO’s growth.” Barcey’s appointment comes at a pivotal time for OSARO, which recently announced a partnership with Tokyo-based IHI Logistics & Machinery Corporation (IHI). The e-commerce market is experiencing explosive growth, placing immense pressure on fulfillment centers to meet ever-increasing customer expectations. OSARO’s AI robotic software powers a broad and compelling range of automation solutions, enabling fulfillment centers to reduce labor challenges, improve efficiency, and reduce costs by automating piece-picking tasks across the operation–from depalletizing incoming inventory to packaging outbound orders in kits and polybags. “I’m delighted to join OSARO at this time in its evolution,” said Barcey. “OSARO’s intelligent robotic solutions, powered by its industry-leading SightWorks Perception System, are demonstrably revolutionizing complex tasks across the fulfillment center by offering a compelling mix of fast time-to-value, flexibility, and adaptability. I’m eager to leverage my experience building strategic partnerships and expanding market reach to ensure OSARO remains at the forefront of this exciting revolution.”
TIA launches 5 ways logistics leaders can harness AI successfully
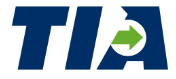
The Transportation Intermediaries Association (TIA) released a new white paper titled Transforming Freight Logistics in the Era of Generative AI. The paper covers the five ways logistics leaders can harness AI to scale efficiency, security, and growth. “AI is forever changing the world as we know it,” said Anne Reinke, president & CEO of TIA. “While many are scared of the future, we feel that the 3PL industry can use AI strategically to work more efficiently, leading them to spending more time on relationship building with customers and carriers.” The latest white paper from TIA covers the five key areas that AI can help business run more efficiently: data synthesis and insights; front-end automation; identifying potential fraud on web-based platforms; customer service; and ethical concerns and governance. The white paper concludes by stating AI is transforming logistics companies’ operations, from synthesizing data and generating insights to automating processes and detecting fraud. As with any transformative technology, there are ethical considerations and governance challenges. Organizations must establish clear guidelines and expectations to ensure responsible AI deployment while safeguarding against potential vulnerabilities. Ultimately, the successful adoption of AI in freight logistics hinges on balancing technological innovation with human expertise. By harnessing AI as a force multiplier rather than a replacement for human labor, logistics companies can empower their workforce, improve customer service, and stay ahead of the curve in an ever-evolving industry landscape. Transforming Freight Logistics in the Era of Generative AI
PTDA hosts Industry Immersion Conference
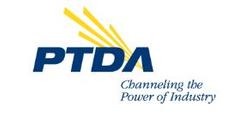
The Power Transmission Distributors Association (PTDA) held the first Industry Immersion Conference in Hollywood Florida on February 29. This one-day intensive program—developed and led by power transmission/motion control (PT/MC) practitioners—aimed to advance the professional perspectives, experience and confidence employees and emerging leaders need to cultivate successful relationships within the industry. “Successful business teams and relationships don’t just happen, they are cultivated,” said Industry Immersion Task Force Chair John Newman, BDI. “This conference equipped those new to the PT/MC industry with the tools and skills needed to build and sustain the relationships essential for becoming a solutions-oriented partner.” Michael Cinquemani, CEO, Master Power Transmissions, Inc., facilitated the conference, which included plenty of face-to-face networking, plus: Panel discussions led by industry veterans who shared their experience and tips for navigating meaningful and productive relationships with colleagues, peers and current or prospective customers. Interactive sessions to help participants understand the “why” and “how” of creating a personal brand and ways to leverage it to networking and, ultimately, develop relationships built on trust. An overview of critical PTDA resources and programs to aid in building industry knowledge so to strengthen customer service and sales skills. “I learned a lot about not only how to build successful relationships within the industry but also what a successful relationship looks like, which was very insightful,” says Melissa Fuentes, RBI Bearing Inc. “I enjoyed the opportunity to connect with other new and some familiar faces,“ says Chris Myer, G&G Manufacturing Company. “Putting the networking skills taught in practice were great in demonstrating to how to market yourself and start new conversations.”
NPE: The Plastic’s Show 2024 debuts never-before-seen show features
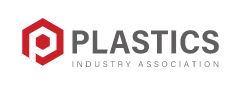
The Plastics Industry Association (PLASTICS)has announced brand-new features ahead of its upcoming trade show, NPE: The Plastics Show, taking place from May 6-10, 2024, at the Orange County Convention Center in Orlando, Fla. NPE2024 is shaping the future of the plastics industry with the inclusion of new educational offerings such as keynote speakers and industry briefings, highlighting the Open Platform Communications Unified Architecture (OPC UA), and offering spaces designed for innovation and connection through Podcast Point and the Sustainability Hub. The addition of these new elements addresses the changing industry landscape and will empower plastics businesses to innovate, compete and succeed in today’s dynamic market. They will also provide every player in the industry with the knowledge and resources to thrive. “The plastics industry is evolving and everyone at NPE will be at the forefront of that change – guiding and leading it. These brand-new features like the keynotes, the Sustainability Hub and industry-specific briefings demonstrate our continued commitment to grow and strengthen the future of our industry,” said Matt Seaholm, PLASTICS President and CEO. Some of the new features debuting at NPE2024 are: Keynote Speakers: Open to all attendees, NPE will have keynote speakers whose expertise will shape the future landscape of the plastics industry. Micheal Cicco, President and CEO at FANUC America Corporation and Michael Heinz, Chair and CEO at BASF Corporation, have been confirmed as the two keynote speakers. On Monday, Cicco’s session, titled “Unlocking the Potential: Robotics, AI and Automation in the New Tech Era”, will address how robotics and automation advancements are revolutionizing the industry and explore the exciting future of human-machine collaboration. On Wednesday, Heinz’s session, titled, “Our Plastics Journey: The Road to Shaping a Sustainable Future”, will highlight industry challenges, the importance of collaboration with legislators and NGOs and provide inspiration for the future. Focused Industry Briefings: The reimagined education experience at NPE features the first-ever industry briefings, in which plastics thought leaders from the top attendee fields – automotive, building and construction, consumer goods, medical and packaging – will speak to emerging trends and technologies in their areas. Plastics industry briefings will also include market trends, future recycling forecasts and a review of the Global Plastics Treaty. OPC UA: The machine-to-machine data exchange will be demonstrated live for all NPE attendees to experience in several exhibitor booths – including Arburg, Plasmatreat, Sumitomo Demag and more. Participants can dive into Industry 4.0 and witness how OPC UA can reduce costs, increase data security and streamline manufacturing operations. Podcast Point: Designed to elevate media resources, this space gives podcasters a chance to share the excitement, learnings and solutions of NPE live from the event. Podcasts like PMM Insight, Sustainable Packaging, MMT Chats and PlastChicks will be streaming before, during and after the show, keeping the public up to date with everything happening at NPE. 3 Spark Stages: NPE’s Spark Stages – Bottling, Sustainability and Innovation – are open to all attendees and offer 30-minute educational sessions on the show floor. These sessions cover critical topics in the plastics industry, from advancements in bottling to the latest innovations in sustainability. With sessions on everything from Industry 4.0 to thermoplastic processing, there are insights for everyone in the plastics industry. Sustainability Hub: This interactive showcase tangibly illustrates the plastics circular economy and allows attendees to follow the environmental journey of plastics and the steps the industry is taking to reduce plastic waste and improve its sustainable footprint. The space will feature recycled materials, sustainable and advanced manufacturing, circularity processes, prevention and recovery efforts and more. NPE happens only once every three years, gathering the entire global plastics industry in the U.S. to share new products and insights. “With these new innovative features, NPE2024 promises to be an unparalleled event for the plastics industry, fostering collaboration, knowledge sharing, and ultimately, a bright future for all participants and the plastics industry as a whole,” said Arlene Davis, NPE Director of Content and Attendee Experiences.
ProMach’s ID technology acquires Etiflex
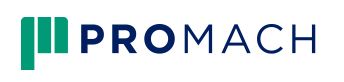
ProMach has announced that it has acquired Etiflex. The addition of Etiflex further expands ProMach’s labeling and coding capabilities throughout North America and represents the company’s first acquisition in the Mexican market. Founded in 1981 in Mexico City, Etiflex is one of the leading converters in Mexico for variable information-printed labels, tickets, and RFID labeling. The company has an extensive portfolio of label-converting solutions that serve a broad range of industries, including food & beverage, textile, automotive, personal care, cosmetics, pharmaceutical, and retail & logistics. Additionally, Etiflex produces tickets, badges, and bracelets for events and transportation. “We are pleased to welcome the Etiflex team to ProMach,” said Mark Anderson, ProMach President and CEO. “Their addition to our business continues the expansion of our label converting capabilities, and it significantly extends our ability to offer a complete portfolio of labeling equipment solutions beyond our existing markets in the United States and Canada.” Anderson continued by saying “This acquisition truly supports our commitment to provide best-in-class labeling and coding solutions and support from a partner that is geographically close to our customers, wherever they are located throughout North America.” Based in Mexico City, Mexico, Etiflex and its team of more than 500 employees will join ProMach’s Labeling & Coding business line led by Group President Alan Shipman. With go-to-market product brands that also include ID Technology, EPI, Panther, Code Tech, and Greydon, ProMach’s Labeling & Coding business line provides broad solution offerings to customers throughout North America. The company’s vertically integrated product portfolio includes both labels and machinery, which are supported by an extensive network that includes seventeen regional sales and service offices, as well as eight existing label-converting facilities. The company’s label-converting facilities provide decorative labels for both high volumes or short runs via flexographic and digital capabilities, blank and shell labels, RFID labels, specialty labels, and more. “The addition of Etiflex to our Labeling & Coding business line continues to underscore the true differentiation of our business by providing exceptional label products and support to our customers, in addition to our labeling equipment,” said Mr. Shipman. “Etiflex brings a trusted industry reputation for providing exceptional quality products, and their geographic footprint will provide tremendous benefits to our current and future customer base in Mexico. With this expansion of our growing label production capabilities and reach, we continue to deliver high quality labels to customers faster, because we’re closer. This means real bottom line benefits for them due to shorter shipping distances – especially for our multinational customers,” Shipman added. Sergio Shor and Ari Vonderwalde, Co-Director Generals of Etiflex, will continue leading the Etiflex team. Shor will serve as VP and General Manager, and Vonderwalde will assume the role of VP of Operations. “Joining ProMach’s Labeling & Coding group is an exciting opportunity to continue and expand the original vision that has guided us for over 40 years”, said Shor and Vonderwalde. “Our philosophy has always been rooted in being a true business partner with strong employee connections and development. We are also proud of our long-standing relationships with our customers and suppliers, and this opportunity will reinforce that effort,” they offered. “ProMach has a proven track record of success and a reputation of investing in its companies to leverage everyone’s strengths, offer more complete solutions, and better serve its customers.” “We are very grateful for all of the support, passion, and dedication the entire Etiflex team has delivered over the past 43 years that took us to this exciting and promising moment,” Shor and Vonderwalde added.
Vertical Cold Storage surges to sixth largest cold storage provider in North America
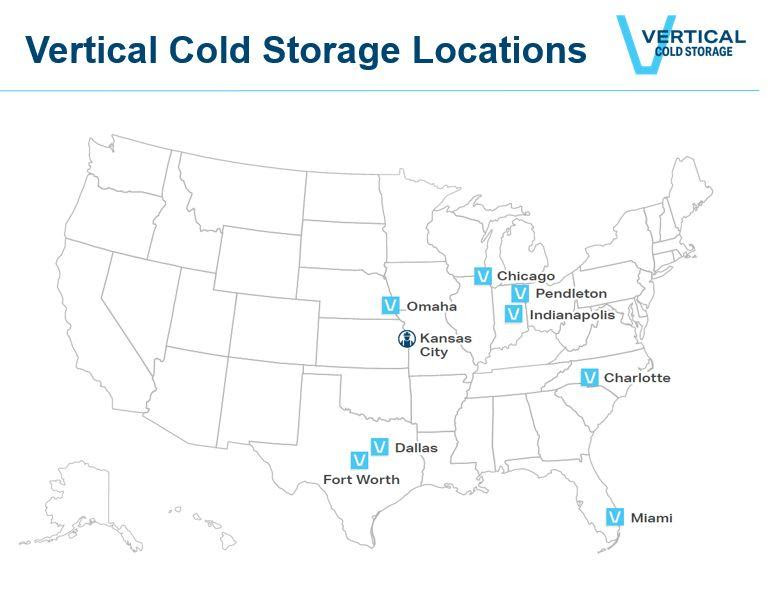
Latest rankings from GCCA also list company as 12th largest globally Vertical Cold Storage, a developer and operator of temperature-controlled distribution centers sponsored by real estate investment firm Platform Ventures, moved from 15th to sixth on the Global Cold Chain Alliance’s (GCCA) North American Top 25 List of Refrigerated Warehousing and Logistics Providers. The company now has more than 77 million cubic feet of capacity in nine locations and employs more than 400 full-time team members. In the past 12 months, Vertical Cold acquired MWCold in Indiana, purchased a second facility in the Dallas-Fort Worth market, and is currently finishing the construction of its first distribution center in the Kansas City market. “It’s been a great year for Vertical Cold, with expansion in new and existing markets. More importantly, it’s been a great year for our customers, for whom we continue to help drive supply chain value, and for our team members, who are committed to servicing our customers safely and efficiently,” said West Hutchison, President and CEO of Vertical Cold Storage. “Our growth platform is strong. There will be continued growth through acquisition, expansion, and development in pursuit of our goal to have a national network that embraces the complexities of our customers, which many of our competitors avoid or price their way out of.”
Nucor Warehouse Systems hosts Open House in Houston
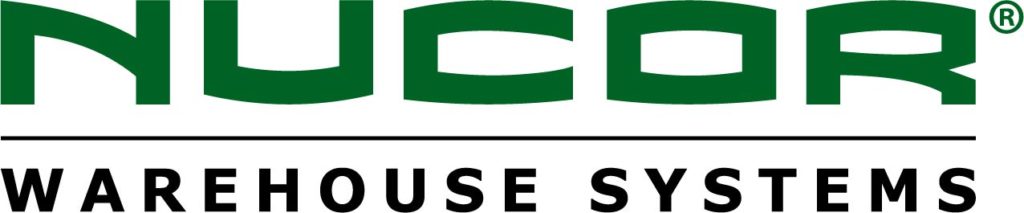
Nucor Warehouse Systems (NWS) has opened its doors to its Texas location at its Houston open house on Friday, April 26th. This event will be an extension of the company to fellow industry members and the community at large featuring mill tours, an opportunity to connect with the NWS team, and on-site activities in store for attendees. NWS welcomes the opportunity to discuss the future of warehousing in the broader market in Texas and is seeking to strengthen relationships with its distribution network. This event will serve as an opportunity for the company to show gratitude towards peers and members of the Houston community and highlight the dependability of Nucor steel in combination with the wealth of resources the company offers. they are a trusted partner and rack provider for businesses of all sizes. With its strategic location in Texas, the company can serve local distributors as a trusted partner and rack provider for any warehouse. “We’re excited for the chance to reconnect and build on relationships with our material handling network in Texas,” said Jonathan Miles, sales manager at Nucor Warehouse Systems, Monroe. “It’s important to us as a company to support our local economy and businesses. These are the kind of projects that make a big impact so it’s a priority for us to show our appreciation and recognition to these potential collaborators.”
Episode 480: The future of safety in warehousing with Powerfleet
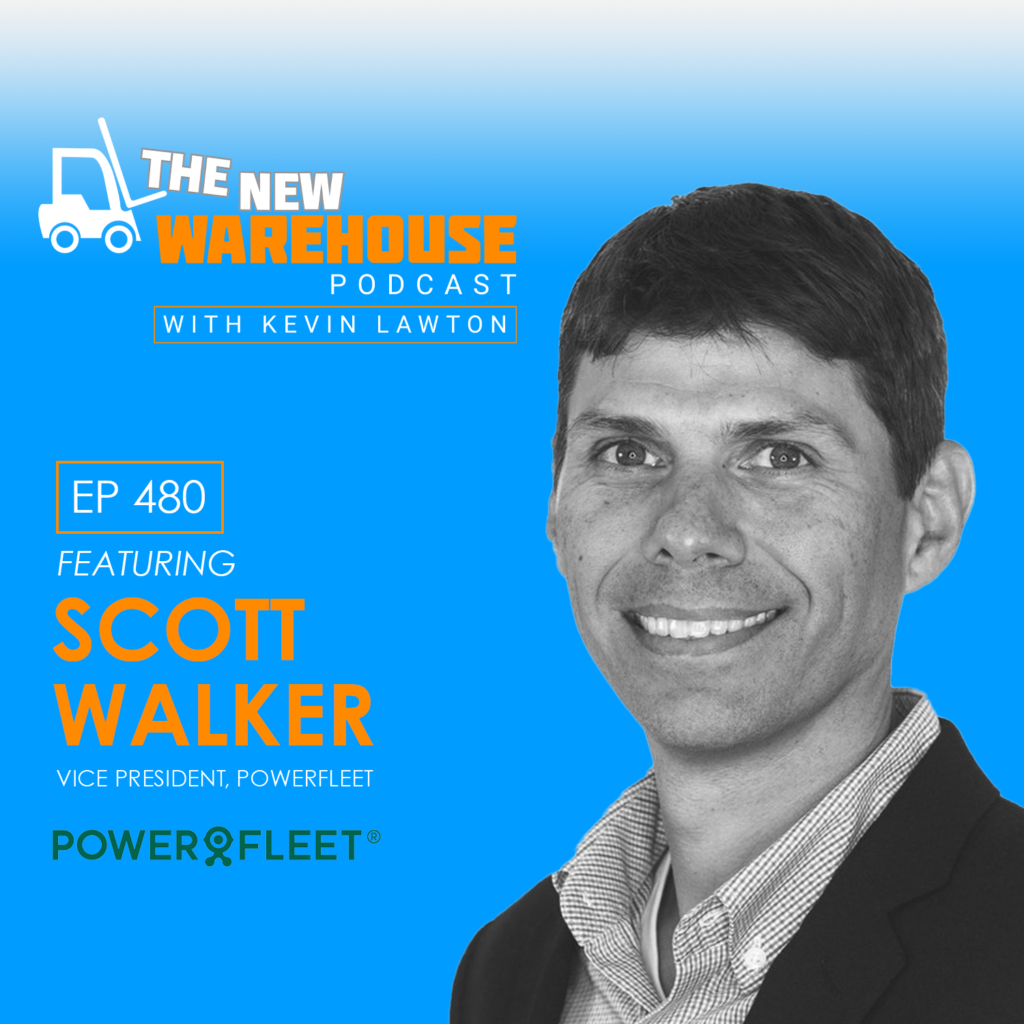
The latest episode of The New Warehouse Podcast, featuring Scott Walker, Vice President of Supply Chain Product Management at Powerfleet. Powerfleet, a leader in the Artificial Intelligence of Things (AIoT) space and a finalist in the Artificial Intelligence Excellence Awards program, focuses on bringing people-powered safety technologies and solutions to the material handling industry. In today’s episode, we explore Powerfleet’s innovative pedestrian proximity detection solution, designed to enhance safety in warehousing environments by integrating advanced AI capabilities. Join us as we delve into how this technology is set to revolutionize industry practices and ensure safer operational environments. Innovating Safety in Warehousing Through AIoT Scott describes the essence of Powerfleet’s approach as “people-powered AIoT,” emphasizing the integration of human insights with automated systems to enhance decision-making processes. He states, “It’s about moving beyond data collection to making proactive safety decisions.” This concept transforms warehouse safety using AI to predict and prevent potential incidents, thus significantly reducing workplace hazards and improving efficiency. Overcoming Safety Challenges with Smart Technology According to Scott, “The goal is not just to track incidents but to prevent them from happening in the first place.” Powerfleet addresses this by deploying AI-driven pedestrian proximity detection systems that analyze environmental data to foresee and alert on potential safety threats. This proactive approach not only mitigates risk but also enhances the overall safety culture within logistics operations, showcasing significant improvements in incident prevention and response times. Predictive and Preventive Innovations in Warehouse Safety Looking ahead, Scott is optimistic about the role of AI in safety technology, particularly in how predictive analytics can integrate with operational systems to forecast potential issues before they arise. He mentions, “The integration of AI allows us to be predictive, not just reactive.” This shift is expected to transform safety measures in warehousing by enabling more informed and timely decision-making, ultimately leading to more robust safety protocols and reduced risk of accidents. Key Takeaways Powerfleet is leveraging AIoT to enhance safety and operational efficiency in warehouses. The new pedestrian proximity detection solution predicts potential safety threats, improving response strategies. Future innovations focus on predictive analytics to preemptively address safety concerns, integrating data with practical operations. The New Warehouse Podcast Episode 480: Enhancing Efficiency and Safety in Warehousing
The Logistics World Summit & Expo 2024-BSL Battery debuts Top Lithium Battery Product

China Huizhou, BSL Battery-Industrial a provider in designing and manufacturing smart lithium-ion batteries (up to 50% more efficient than its peers in the market) for industrial forklifts used in the storage and distribution industries, exhibited at its first participation at the 2024 The Logistics World Summit & Expo, April 10-11, 2024 in Centro Citibanamex, Mexico. With a rich manufacturing history of more than 10 years, BSL Battery-Industrial has become a trusted manufacturer of lithium battery solutions for material handling. With significant investment, lean manufacturing capabilities, seamless supply chain integration, and a 180-year professionally designed technical team in the lithium battery industry, BSL Battery-Industrial is fully capable of providing high-quality products and the best-tailored lithium battery solutions to forklift manufacturers, forklift dealers, and battery dealers. Exhibiting for the first time at The Logistics World Summit & Expo, BSL Battery-Industrial was bustling and attracted a lot of visitors, including friends from all over the Americas. The company representatives had in-depth discussions with the participants, exchanged views on the industry trends, and demonstrated BSL Battery-Industrial’s firm determination to enter the North American market and achieve excellent results. The future is very exciting In the highly anticipated process, our new third-generation forklift lithium battery was finally lit up at 10:00 am on April 10th, which was warmly welcomed and highly praised by our customers! BSL Battery-Industrial Chief Technology Officer Mr.Lin Peng said, “This third-generation forklift lithium battery is a leading product in the material handling industry. Using a UL2580-certified BSL lithium battery module and a proprietary cloud-based BMS ™ remote information processing and asset management system independently developed by BSL. Outstanding performance in food and beverage, third-party logistics (3 PL), warehousing and manufacturing, and other industries, easily meeting customer needs. Medium to large fleets with fleet management systems will notify you before the problem occurs. View battery performance, monitor fleet activity generate real-time metrics, optimize performance, and save energy. In addition to the above products, we have also demonstrated a variety of lithium battery products used in AGV, GSE, aerial work platforms, and golf carts. It is worth noting that we have deployed about 12,000 batteries throughout North America and provided China’s first UL2580-certified lithium-ion battery pack for material handling equipment. BSL Battery-Industrial, AMER Area Manager, Bebinca Wu, said: “The Logistics World Summit & Expo is a key stage for us that not only strengthens our foothold in the Americas but also introduces novel products to our respected product portfolio, demonstrating our commitment to providing excellent quality, superior service and strong support to our customers in the Americas. Missed us at The Logistics World Summit & Expo 2024? Reach out today! If you didn’t attend The Logistics World Summit & Expo 2024, explore BSL Battery-Industrial’s 3.0 lithium battery solution. Don’t worry, our commitment to 3.0 lithium battery product samples and cost reduction continued after the event. Whether you are still hesitant about lithium-ion batteries or want to bring the advantages of proprietary cloud-based BMS ™ telematics and asset management systems into your operations, our energy experts will answer your questions here! Although you may have missed the opportunity to visit our Logistics World Summit & Expo, you can still contact us by virtual means. BSL Battery-Industrial is committed to providing customers with the best lithium battery solutions and building mutually beneficial partnerships worldwide. Over the past 10 years, BSL Battery-Industrial has gained good recognition in many markets, including China, ASEAN, Australia, South Asia, the Middle East, the Americas, and Europe. To better serve local customers, BSL Battery-Industrial is actively seeking local dealers and partners to enhance its competitiveness in these areas.
Terex reports strong First Quarter 2024 results; raises full-year outlook
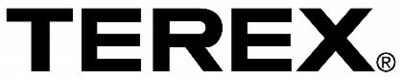
Sales of $1.3 billion increased 5% year-over-year Income from operations of $158 million, up 7% year-over-year Operating profit margin of 12.2% improved 20 bps year-over-year Earnings per share of $1.60 Return on invested capital of 27.6%, up 370 bps from the prior year Raising full-year 2024 EPS outlook to a range of $6.95 to $7.35 Increasing full-year 2024 sales outlook to a range of $5.2 to $5.4 billion Terex Corporation, a global manufacturer of materials processing machinery and aerial work platforms, today announced its results for the first quarter 2024. “Terex delivered excellent first quarter results, achieving sales growth and margin expansion versus the prior year,” said Simon Meester, Terex President and Chief Executive Officer. “The Terex team continues to perform at a high level and demonstrate the power of its focused strategy and its proven ability to create value.” “We are raising our full-year outlook to reflect our strong first quarter performance, while also prudently planning for continued softness in Europe over the balance of the year.” Meester continued, “Overall, customer demand remains strong for Terex’s differentiated products as evidenced by our robust backlog. In addition, we are advancing our new product initiatives to bolster the Company’s portfolio of market-leading businesses that will continue to benefit from megatrends over the coming years. We are focused on accelerating our profitable growth strategy and are committed to delivering strong performance through the cycle.” First Quarter Operational and Financial Highlights Net sales of $1.3 billion increased 4.6%, up from $1.2 billion in the first quarter of 2023. The increase was primarily driven by continued demand for our products across multiple businesses. Income from operations of $158.3 million, or 12.2% of net sales improved from $147.7 million, or 12.0% of net sales during the prior year. The year-over-year increase of $10.6 million was primarily due to incremental profit achieved on higher sales volume, improved manufacturing throughput and disciplined price-cost management. Income from continuing operations was $108.5 million, or $1.60 per share, compared to $109.9 million, or $1.60 per share, in the first quarter of 2023. Return on invested capital was 27.6%, up 370 bps from the prior year and significantly exceeded our cost of capital. Business Segment Review Materials Processing Net sales of $520.0 million were down 6.1% or $33.8 million year-over-year, primarily driven by lower end-market demand for material handling equipment and cranes in Europe, partially offset by growth for aggregates in North America. Income from operations decreased to $72.1 million or 13.9% of net sales, compared to $85.3 million, or 15.4% of net sales, in the prior year. The decrease was primarily due to the impact of lower sales volume and net unfavorable product mix. Aerial Work Platforms Net sales of $772.7 million were up 12.7% or $86.8 million year-over-year. The increase was primarily driven by higher demand, as well as improved supply chain and manufacturing performance. Income from operations increased to $107.3 million or 13.9% of net sales, compared to $83.1 million, or 12.1% of net sales in the prior year. The increase was primarily due to incremental profit achieved on higher sales volume, improved manufacturing throughput and disciplined price-cost management. Strong Balance Sheet and Liquidity As of March 31, 2024, the Company had liquidity (cash and availability under our revolving line of credit) of $866 million and net leverage of 0.5x. Terex deployed $35 million for capital expenditures during the first quarter of 2024 to support business growth. CFO Commentary Julie Beck, Senior Vice President and Chief Financial Officer, said “We expanded total company operating margin by 20 bps compared to last year and delivered ROIC of more than 27%. We expect a significant step-up in free cash flow over the balance of the year and remain on-track to generate more than $300 million of free cash flow for a second consecutive year. The strength of our balance sheet and expected cash flow provide significant capacity to fuel our strategic growth initiatives and return capital to shareholders.” Full-Year 2024 Outlook (in millions, except per share data) Terex Outlook (1) PREVIOUS Outlook UPDATED Outlook Net Sales $5,100 – $5,300 $5,200 – $5,400 Operating Margin 12.8% – 13.1% 12.8% – 13.1% Interest / Other Expense ~$60 ~$65 Tax Rate ~22% ~22% EPS $6.85 – $7.25 $6.95 – $7.35 Share Count ~68 ~68 Depreciation / Amortization ~$65 ~$65 Free Cash Flow (2) $325 – $375 $325 – $375 Corp & Other OP ~($80) ~($85) Segment Outlook (1) PREVIOUS Outlook UPDATED Outlook Net Sales Operating Margin Net Sales Operating Margin Materials Processing $2,200 – $2,300 15.6% – 15.9% $2,200 – $2,300 15.6% – 15.9% Aerial Work Platforms $2,900 – $3,000 13.4% – 13.7% $3,000 – $3,100 13.5% – 13.8% (1) Excludes the impact of future acquisitions, divestitures, restructuring and other unusual items (2) Capital expenditures, net of proceeds from sale of capital assets: ~$145 million Non-GAAP Measures and Other Items
Carolina Handling wins Kautex Safety Award for AGV implementation
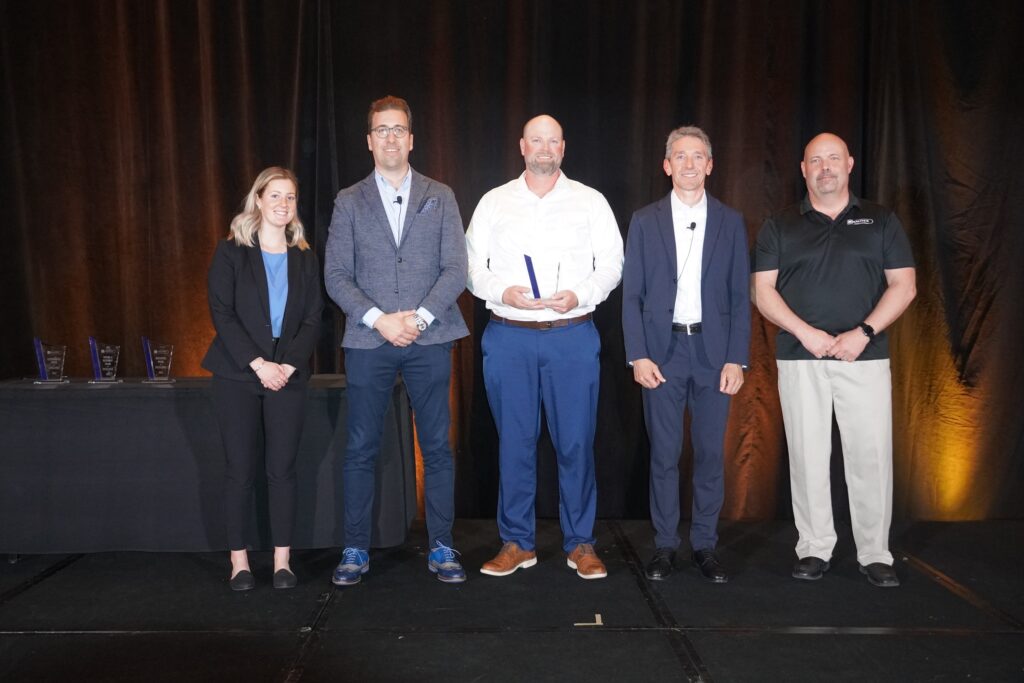
Carolina Handling has received the 2023 Health & Safety Award for Excellence from Kautex, A Textron Company, a Tier One automotive supplier with more than 30 manufacturing facilities in 13 countries. The award was received for an Automated Guided Vehicle (AGV) project at the company’s facility in Lavonia, Georgia, and recognizes Carolina Handling as a top-performing supplier. The courier implementation was one of the smoothest among any of Kautex Textron’s equipment distributors worldwide, according to the company, which operates AGVs at most of its facilities around the globe. Carolina Handling is one of the Southeast’s leading integrated material handling solutions providers and the exclusive Raymond Solutions and Support Center for North Carolina, South Carolina, Georgia, Alabama, and Florida’s Central time zone. The company provides a full range of lift trucks and automation solutions for manufacturers, warehouses, and distribution centers, along with parts, warehouse equipment and supplies. A Tier One global automotive supplier, Kautex Textron designs, develops, and manufactures traditional and hybrid fuel systems, advanced cleaning solutions for assisted and autonomous driving, engine camshafts, and plastic industrial packaging solutions.
COVAL launches the new generation of Multi-stage Mini Vacuum Pumps: The CMS M Series
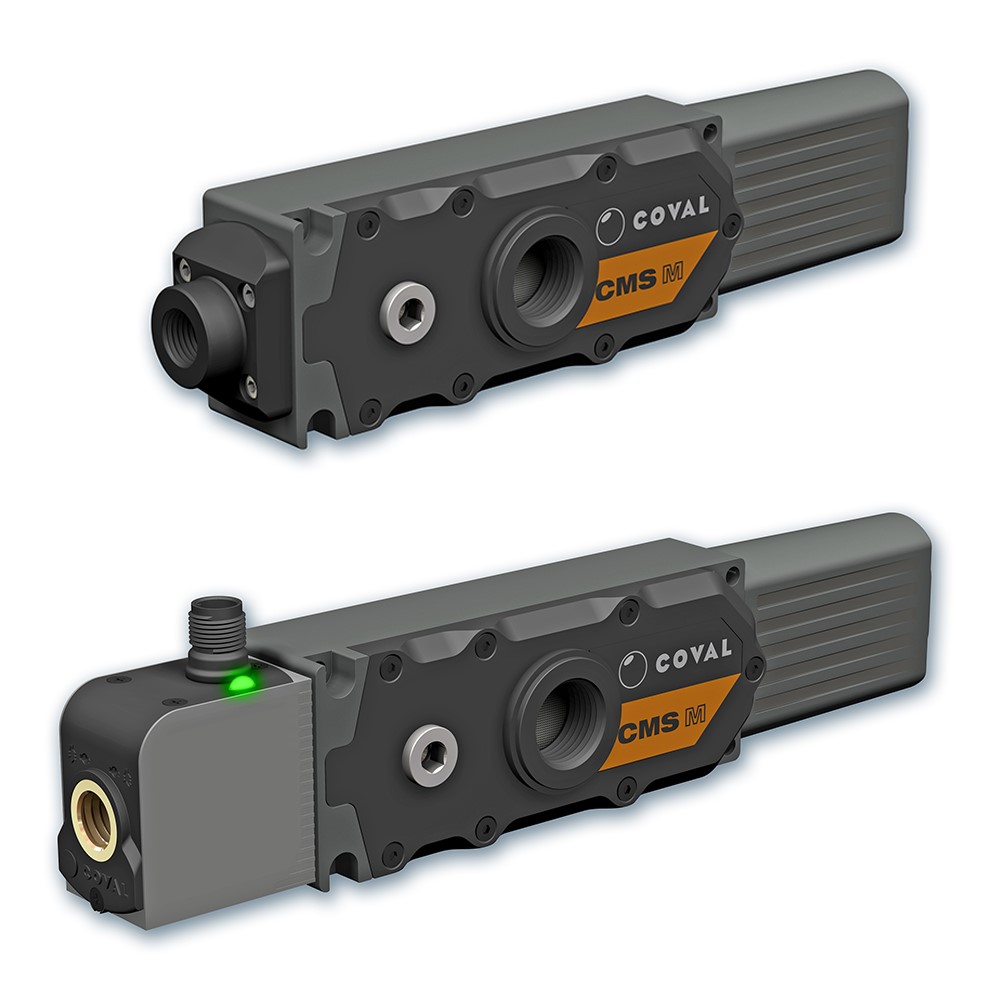
The mini pump with max performance! The CMS M series, the latest addition to COVAL‘s range of multistage vacuum pumps has been designed and developed with two guiding objectives: compactness and performance. It offers an optimum solution for industrial applications which require high suction flow rates. Enhanced performance and robustness CMS M multi-stage mini vacuum pumps are the product of COVAL’s advanced research, seeking to provide a powerful, durable solution for handling porous parts, emptying tanks, or random gripping in harsh industrial environments. Thanks to their ultra-compact design and optimized multi-stage Venturi system, these pumps guarantee powerful suction flows of up to 19.42 SCFM, while reducing compressed air consumption in a compact footprint. Modularity and ease of maintenance An outstanding feature of the CMS M series is its modularity, making it easy to adapt to a variety of applications and simple to maintain. These mini pumps also offer two exhaust configurations to perfectly match each specific need, available in two suction capacities (10.59 SCFM to 19.42 SCFM) and with or without vacuum and blow-off control. Advanced multi-stage technology for maximum efficiency COVAL’s multi-stage technology maximizes the energy input of compressed air by cascading several stages of Venturi profiles and combining their respective suction flows. Intermediate valves progressively isolate each stage to achieve maximum vacuum level. This technology makes it possible to generate high suction flow at low vacuum levels. This innovation reflects COVAL’s commitment to providing efficient, energy-saving solutions for the industry. A trusted technology partner An ISO 9001:V2015 certified company, based in the South of France, COVAL continuously innovates in vacuum handling. The company is recognized worldwide for its expertise in developing customized, reliable, and efficient solutions that improve the safety and productivity of industrial processes.