AMT launches ROBiN AI-Powered flexible material handling solution for warehousing
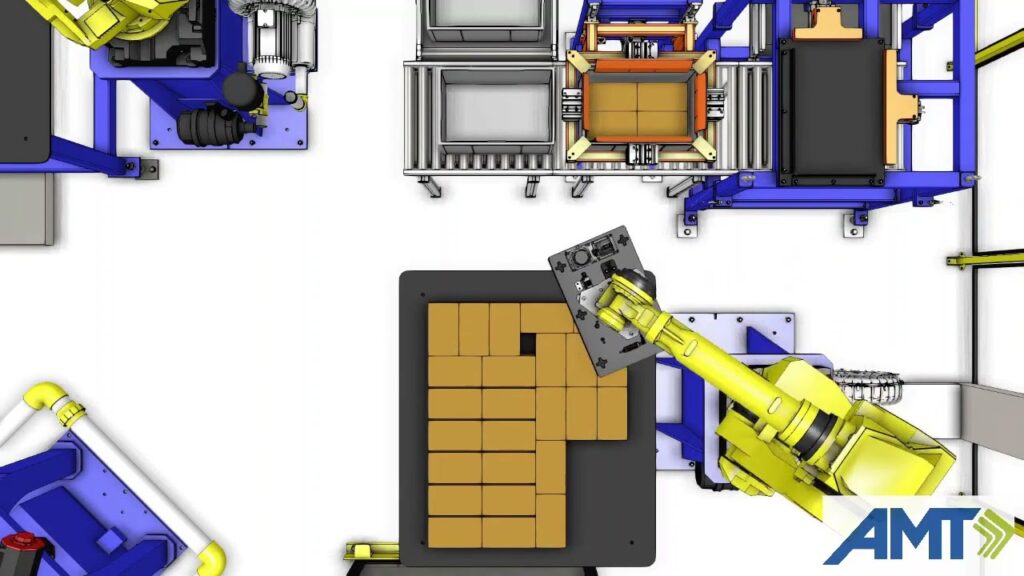
Applied Manufacturing Technologies’ latest material handling innovation ROBiN, Robotic Induction System, uses AI, machine vision, and intelligent algorithms to achieve efficiency gains in the induction of cases into automated storage and retrieval systems (ASRS). Applied Manufacturing Technologies (AMT), a material handling, system integration, and cutting-edge autonomous mobile robots (AMRs) for warehousing and logistics, has announced the launch of ROBiN, Robotic Induction System, a flexible material handling solution for efficiency and throughput gains in the warehousing industry. ROBiN, developed by AMT, is a robotic AI-enabled system designed to improve the process of removing and organizing layers of products on pallets for integration into automated storage and retrieval systems (ASRS). Utilizing advanced AI and machine vision technology, ROBiN is engineered to handle a diverse range of case sizes and shapes, without prior knowledge of the number of cases on a layer, their specific location, or orientation. This capability allows ROBiN to optimize the fill density of totes, therefore increasing efficiency in warehouse operations. ROBiN reflects AMT’s focus on advancing warehouse automation through the application of innovative technologies. “We are excited to launch ROBiN, our flexible material handling solution, which was designed to significantly enhance efficiency and throughput in warehouse induction operations,” said AMT President Craig Salvalaggio. “ROBiN’s unique and adaptable design supports various case dimensions and operates effectively without needing to know in advance the count of cases per layer or their precise placement and alignment. This flexibility enables us to meet our client’s diverse operational needs and drive forward the capabilities of automated systems.”
Fairchild Equipment acquires Yale® lift truck dealer territories in Wisconsin and Illinois
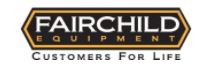
Fairchild Equipment, a provider of material handling solutions in the Midwest, has announced its expanded dealer footprint as the official Yale Lift Truck Technologies dealer across eleven key counties in Wisconsin and Illinois. This strategic move comes as a testament to Fairchild Equipment’s unwavering commitment to delivering outstanding customer service, unparalleled parts availability, swift responsiveness, and exemplary overall quality in the material handling industry. The counties now served by Fairchild Equipment include Crawford, Grant, Iowa, Lafayette, Green, and Rock in Wisconsin, along with Stephenson, Winnebago, Boone, Ogle, and Lee in Illinois. “Fairchild Equipment has earned a storied reputation for putting the needs and satisfaction of our customers at the forefront of our operations since my father founded the company in 1985,” said Chad Fairchild, Chief Executive Officer of Fairchild Equipment. “We are excited to bring our expertise and passion for creating Customers for Life to the users of Yale forklifts in these new areas. Our team of experts takes pride in ensuring that every customer receives the solutions they need for optimized operations.” By incorporating the Yale® brand in these new counties into its portfolio, Fairchild Equipment will offer an even more comprehensive selection of material handling equipment. Yale is one of the primary brands offered by Hyster-Yale Group, a globally integrated manufacturer of application-tailored lift trucks and technology solutions, engineered to meet customer-specific needs. “As part of our customer-centric approach, we at Fairchild Equipment are proud to offer an expansive rental fleet ready to cater to businesses in need of temporary material handling equipment,” noted Tim Rothe, Vice President of Operations at Fairchild Equipment. “Furthermore, our service guarantee promises a two-hour response time for all service calls, ensuring minimal downtime and the continued productivity of our customer’s operations.” As a testament to Fairchild Equipment’s outstanding organization, Yale Lift Truck Technologies has honored them as a Dealer of Excellence 28 times. This annual award celebrates Yale dealers who have exhibited focused leadership and continued to drive their customers to the highest level of performance in all functional areas of materials handling. In an ongoing effort to maintain exceptional response times and customer satisfaction, Fairchild Equipment is pleased to announce an increase in the number of service technicians operating in these newly acquired regions. To support this expansion, Fairchild is actively hiring to fill these crucial positions, seeking out skilled individuals who align with our dedication to excellence and customer satisfaction. With a growing team of experts, customers can expect the high standard of support that is a hallmark of the Fairchild Equipment experience.
Plus One Robotics expands automation capabilities with new depalletization and gripper technologies
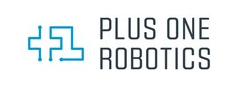
Major product updates will revolutionize induction and depalletization processes Plus One Robotics, a provider of AI vision software and solutions for robotic parcel handling, has announced two significant product updates designed to enhance efficiency and expand its reach into new market segments. The new updates offer significant advancements for businesses seeking to streamline and optimize their fulfillment operations where speed, accuracy, and efficiency are paramount. The new features include updates to depalletization and induction capabilities. Increase SKU Compatibility for Automated Depalletization The new depalletization feature addresses growing customer needs in grocery fulfillment, including the demand for increased SKU entitlement for shrink-wrapped cartons and trays. The new capabilities help overcome a longstanding technical challenge faced when automating the depalletization process — accurately distinguishing between groups of densely packed, shrink-wrapped food and beverage items. To tackle this issue, Plus One Robotics has developed new vision capabilities and AI to accurately identify different product configurations, streamlining the depalletization process and optimizing picking accuracy. This feature is robot-agnostic and designed to work with any of Plus One’s system integrators’ depalletization systems, offering an immediate solution for warehouses looking to automate their material handling process. “This new depalletization feature is a game-changer for the grocery industry,” said Shaun Edwards, CTO and co-founder of Plus One Robotics. “By leveraging innovative vision technology, we can now seamlessly automate the handling of various case pack configurations, significantly improving efficiency and throughput for our customers in the grocery segment.” Reduce Cost-Per-Piece of Varying Parcel Mix With New, Individual Cup Control Gripper Plus One Robotics is also strengthening its induction solutions with the introduction of a new gripper design. The Individual Cup Control Gripper (ICC Gripper) leverages the intelligence of Plus One’s PickOne vision software to grasp and singulate parcels using the optimal configuration of active suction cups. This advanced design offers several key benefits: Minimize Unintentional Multi-Picks: The combination of cup configurations enabled by this design allows the gripper to match the shape of the target parcel and avoid accidentally grasping adjacent parcels. Maximize Retention Force: By activating only the necessary suction cups, the gripper ensures that the full force of the vacuum is applied to the parcel surface, preventing the cost of damaged or dropped parcels. Reliability You Can Count On: Plus One Robotics follows a rigorous in-house reliability testing protocol to ensure dependability in the field. “The new Individual Cup Control Gripper exemplifies our unwavering focus on continuous improvement and efficiency,” said Erik Nieves, CEO and co-founder. “This software-driven innovation, tightly coupled with our PickOne software and AI detection, empowers users with unparalleled control and adaptability, regardless of the package type, whether it’s a box, polybag, envelope or irregular.” Plus One Robotics is exhibiting at MODEX 2024.
Explore Raymond’s interconnected ecosystem of intralogistics solutions at MODEX 2024

Discover end-to-endless solutions to set the tempo of an optimized warehouse floor The Raymond Corporation continues to build on its more than a century-long history of innovation and will showcase its end-to-endless intralogistics solutions and material handling products at MODEX 2024. Attendees of the show, held March 11 to 14 at Atlanta’s Georgia World Congress Center, can visit Raymond at Booth B5406 to see and learn more about the complete line of Raymond intralogistics solutions. “For over 100 years, Raymond has been designing products to help customers address their ever-evolving operational needs through innovative solutions and technology,” said Mike Field, president and CEO of The Raymond Corporation. “We’re committed to serving as a single-source provider of complete intralogistics solutions, helping our customers tap into the tempo of their floor and find its flow. We’re looking forward to highlighting some of the industry’s most innovative products at MODEX 2024.” In the ever-evolving landscape of intelligent intralogistics solutions, lift trucks are indispensable workhorses within warehouses and distribution centers. However, optimizing vehicle functionality is more than mechanics; it depends on connected technologies. Raymond uses advanced technologies, data analytics, automation and lift trucks to integrate seamlessly into a networked ecosystem for a warehouse of optimization and maximizing efficiency. Total connectivity integration extends to energy management, where smart charging stations and renewable energy sources connect with operational logistics, ensuring sustainable practices while maximizing uptime. Together, lift trucks, connected technologies, and energy solutions form a symbiotic relationship, propelling the future of intralogistics toward unprecedented levels of productivity, sustainability, and interconnectedness. MODEX 2024 attendees will have the opportunity to learn about Raymond’s ecosystem of efficiencies through a variety of material handling equipment, connected technologies, energy solutions, automation products, and support services. Material Handling Equipment Raymond has built a reputation based on quality, innovation, and service. Its complete line of electric forklifts with integrated technologies are built to perform with increased efficiency and productivity with customers and operators in mind. See on display: Raymond® 8810 Side Entry Pallet Truck Raymond 8510 Rider Pallet Jack with the patented Pick2Pallet™ LED Light System and the patent-pending Raymond Advance® Operator Assist Technology Raymond 4800 Sit-down Electric Counterbalanced Truck Raymond 4250 Stand-up Counterbalanced Truck with Lithium-ion Batteries, iWAREHOUSE® Telematics and iWAREHOUSE ObjectSense Detection System Raymond 7530 High Capacity Reach-Fork® Truck with iWAREHOUSE FieldSense Connected Technologies The Raymond enterprise moves warehouse operations forward by offering advanced technologies connected with scalable, flexible and intelligent warehouse solutions. Scalable telematics solutions that collect and report vehicle and operator data help drive productivity across operations to create an optimized and intelligent warehouse operation. Energy Solutions Raymond energy solutions are specifically engineered to meet the demands of the toughest material handling applications while enabling data-based insights that allow managers to optimize energy efficiency and lift truck performance. In addition to helping optimize energy efficiency, the full line of Raymond energy solutions can help enhance productivity, lower operational costs and meet corporate sustainability goals. Raymond energy solutions include Energy Essentials Distributed by Raymond®, Industrial Lead Acid Batteries, and Advanced Lead Acid Batteries, including thin plate pure lead technology, providing high charge and discharge rates, a longer life span, and faster charging than traditional batteries. Energy Essentials Distributed by Raymond now comes with a new standard warranty of eight years, 5,000 cycles. Integrated Intralogistics Solutions and Automation The Raymond enterprise is a single source for complete intralogistics solutions, providing the technologies, systems and solutions that bring warehouse and distribution operations to exceptional levels of performance. Raymond Automated Swing-Reach® Truck. Facility managers can free their lift truck operators to focus on more critical tasks while the Raymond Automated Swing-Reach Truck moves, retrieves, and stores pallets — reliably, accurately, and autonomously. Regenerative lowering offers reduced downtime and improved energy efficiency thanks to fewer battery charges, while natural feature recognition allows infrastructure-free navigation. Automated and manual modes allow full pallet handling or case picking. Raymond Courier™ 3030 Automated Stacker. The enhanced Raymond Courier 3030 Automated Stacker features improved motion control, object detection coverage, increased speeds, and Lane Staging capabilities. New Raymond Courier Automatic Charging System. Enhance labor efficiency by automatically charging Raymond Courier Automated Guided Vehicles (AGVs). Integrates with iBATTERY® and IWAREHOUSE® systems for optimum performance Choose when and how the AGVs are dispatched to the charge station: off-shift/full charge; low battery/partial charge; or inactivity/opportunity charge. Raymond High Capacity Orderpicker with iWAREHOUSE Integrated Tether System and iW.ObjectSense. Specifically designed for the demands of today’s on-demand economy and to facilitate order picking a full rack higher than currently available models, the High Capacity Orderpicker features an industry-leading elevated height of 456 inches, allowing for rack storage access to 11% more picking slots. The High Capacity Orderpicker is equipped with Energy Essentials Distributed by Raymond Lithium-ion Batteries engineered to integrate seamlessly into Raymond’s family of forklifts. The High Capacity Orderpicker is also outfitted with the iWAREHOUSE Integrated Tether System, a first-of-a-kind operator assist tool designed to alert operators and managers and to limit lift truck functionality if an operator is not properly tethered. Radioshuttle® Storage and Retrieval System. This semi-automated storage and retrieval system allows for maximum use of warehouse space. The Radioshuttle is easily managed with remote control and executes orders to load or unload pallets into a lane. Total Solutions Provider Through Support Services and Consulting Raymond Solutions and Support Centers are committed to offering customers end-to-end solutions, from lift trucks to facility automation, with specialization in seamless technology integration for a customized customer-focused approach. Raymond Solutions and Support Center experts are part of The Raymond Corporation nationwide network and collaborate with customer teams to help optimize warehouses, boost productivity and strategically utilize data for continuous improvement, resulting in savings for customers’ operations. Raymond Solutions and Support Centers strive to be an extension of customer teams with a shared goal of maximizing facility uptime and reaching operational goals.
Bedford to showcase ReadySeries Modular FRP Safety Structures at MODEX 2024
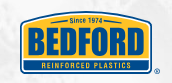
Bedford Reinforced Plastics will showcase its ReadySeries lineup in booth A10005 at the MODEX trade show. This will be Bedford’s inaugural appearance at MODEX, held March 11-14, 2024, at the Georgia World Congress Center in Atlanta. The Bedford ReadySeries lineup is the broadest FRP modular solution to meet the access and safety structure needs of those in the manufacturing and supply chain industries. The ReadySeries system includes industrial platforms, mezzanines, walkways, catwalks, fixed ladders, handrails, guardrails, stairs, stair towers, pedestrian bridges and more for nearly limitless configurations. Each easy-to-install modular product can be used independently or combined with other products in the series. An ideal solution for meeting industrial safety needs quickly and affordably, ReadySeries structures are OSHA-compliant. Unlike wood and metal, ReadySeries FRP is fire-retardant, corrosion-resistant, and non-conductive. Anti-slip coatings minimize slip and fall risks, while Bedford’s proprietary ReadyShield UV coating protects against ultraviolet (UV) light exposure, harsh weather, extreme heat, and humidity without changes to the structural integrity or surface appearance. Safety yellow coloring is available in all ReadySeries structures. “ReadySeries modular products can help those in the manufacturing and supply chain industry enhance productivity and efficiency while increasing facility safety,” said Eric Kidd, marketing director for Bedford Reinforced Plastics. “Our ReadySeries products create affordable, customized solutions for a warehouse by offering multiple configurations that are ready to ship and designed for easy installation.” ReadySeries products include: ReadyPlatform solutions are ideal for industrial access platforms, walkways, mezzanines and catwalk applications that don’t require a custom build. ReadyPlatform materials are available in 3×3′ increments and heights of 1-1/2′, 3′, 4-1/2′ and 6′. Customers can also add ReadyStair, ReadyLadder or ReadyRail components to get their ideal configuration. ReadyLadder solutions let customers quickly combine sections available in 10′ and 15′ increments to get the desired ladder height. If needed, customers can quickly trim one section with ordinary tools to get an exact fit or add a walk-through for a complete system. ReadyRail guardrail and handrail materials are perfect for both new structures and repairs. They are stocked in 3′ sections, and you can also specify the length of your railing run and Bedford will package all components into a handy kit. Materials can be used on their own or to complement ReadyPlatform products for a complete safety solution. ReadyStair stair towers adapt easily to almost any configuration. They fit in a 7-1/2′ by 12′ nominal footprint, rising in 6′ increments between landings. When needed, a short stretch of up or down stairs is provided for the final transition at the top. ReadyStair sections are also used in conjunction with ReadyPlatform materials to meet any configuration needed.
FORTNA launches OptiSweep robotic solution to automate post-sorting process in high-volume distribution centers
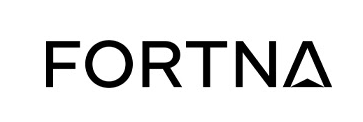
Mobile robots and software integration automate labor-intensive sorter destination changeover tasks in eCommerce and sortation facilities FORTNA, an automation and software company for the full logistics value chain, has announced the launch of FORTNA OptiSweep, a robotic solution to automate the consolidation and transportation of small orders away from sortation systems in high-volume eCommerce and sortation distribution centers. This innovative solution automates what is typically a labor-intensive process by using Geek+ robots to collect orders from sorter divert locations and bring them to specially designed goods-to-person locations to deposit orders for bulk consolidation and outbound processes. FORTNA WCS™ software and its proprietary algorithms seamlessly orchestrate the workflow, managing the mobile robots and communicating with the sorter and consolidation stations to maximize efficiency and balance product flow. FORTNA OptiSweep brings an innovative, proven, and flexible robotic technology to the sorter close-out process, replacing both manual operations and legacy technologies such as the bombay sorter. Traditionally, high-volume distribution centers use large linear and loop sorters to organize packages into categories, diverting them down appropriate chutes into destination-specific bags. These processes often have workers assigned to monitor specific destinations, physically remove items, and walk them to a consolidation station for downstream processes. The FORTNA OptiSweep solution significantly reduces these labor requirements and provides ergonomic improvements. It eliminates the need for workers to bend and reach into bags to move items and substantially cuts the distance and time spent walking in the warehouse. “Labor challenges are ubiquitous across supply chains, and this post-sorting process is a prime example, marked by frequent over- or understaffing,” stated Rob McKeel, CEO, FORTNA. “Businesses need automation solutions that provide consistent outcomes and can scale to match the spikes and dips of eCommerce. OptiSweep exhibits how FORTNA is merging robotic proficiency with unmatched design and implementation capabilities to effectively address issues related to labor dependency, variable throughput demands, capacity constraints, and more.” FORTNA OptiSweep easily integrates with sorter systems and can match a range of throughput requirements, offering processing flexibility from 4,000 to more than 34,000 pieces per hour. This throughput does not come at the price of reliability, as the solution also minimizes the recirculation rate in high-volume distribution centers. By mitigating the need for excess labor to accommodate demand fluctuations, OptiSweep enables businesses to maintain prolonged runtime without disruption, scale effectively, and optimize facility-wide efficiency.
Stryten Energy launches new line of lithium batteries at MODEX 2024
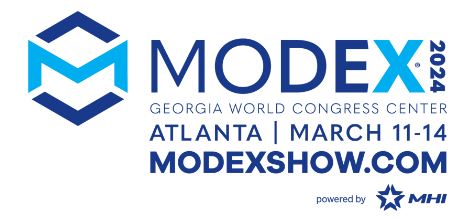
The M-Series Li600 available in Class I, II and III is the latest addition to Stryten Energy’s portfolio of motive power battery solutions. Stryten Energy LLC, a U.S.-based energy storage solutions provider, will launch the M-Series Li600, a new line of Class I, II, and III lithium batteries, at MODEX 2024 in Atlanta. Li600 batteries, the latest addition to Stryten Energy’s extensive motive power offerings, are available in Class I, II, and III, in a full range of voltages with optional cold storage capability down to -40 C. The Li600 for Class III features an onboard charger option. The full line of Li600 batteries is compatible with the M-Series X-3 and X-7 chargers. Visitors to Stryten Energy’s Booth #B1813 will see: Lithium and Advanced Lead Batteries: New M-Series Li600 Class I, II, and III Lithium Solutions: The Li600 is based on lithium iron phosphate (LFP) chemistry. This chemistry has a longer calendar life and a longer cycle life than other lithium chemistries. It is a cost-competitive option, comprised of readily available materials, and is one of the safest lithium technologies. Key features include a fully configurable CANbus protocol, remote monitoring capable, comprehensive diagnostics via a color touch screen, and auto hibernation/sleep mode after a period of inactivity to prevent unintended discharge. The M-Series Li600 products are designed to meet UL2580, and UL certification is in process. M-Series T310 Lead Solution: The T310 low-maintenance tubular offers the best level of power, performance, cost and reduced maintenance for medium to heavy-duty lift truck applications. Stryten Energy’s round tube design is more efficient and delivers longer run times than competitive square tube designs. Opportunity and Fast Charging Solution: The M-Series X-7 4-bay charger delivers 30kW of power while handling lead and lithium battery types, and can be configured for standard, opportunity or fast charging. Its modular design offers flexibility, reduced operating costs, and accelerated charging times to meet the demands of the toughest fleets. Energy Performance Management Software: Stryten Energy inCOMMAND™ is an energy performance management software tool that makes it easy to design and deploy web-connected battery and charger solutions. inCOMMAND allows dealers and end users to monitor and manage their batteries and chargers right from their computers. A demo of inCOMMAND will be available at the booth. “At Stryten Energy, we understand the dynamic needs of today’s material handling industry,” said Matt Gould, Vice President of Industrial Sales and Service at Stryten Energy. “With the addition of the M-Series Li600 line, we are a “one-stop-shop” to serve our customers’ needs with a complete portfolio of battery technologies.” Stryten Energy also provides comprehensive, nationwide motive power services that ensure fleets operate at full capacity at all times. The Li600 line is field serviceable by Stryten Energy’s service network strategically located across the U.S., Canada, and Mexico. Trained stored energy experts provide planned maintenance, repair services, predictive service, installations, de-installation, recycling, application audits, power studies, training, and inspections.
Women In Trucking Association names 2024 Top Women to Watch in Transportation
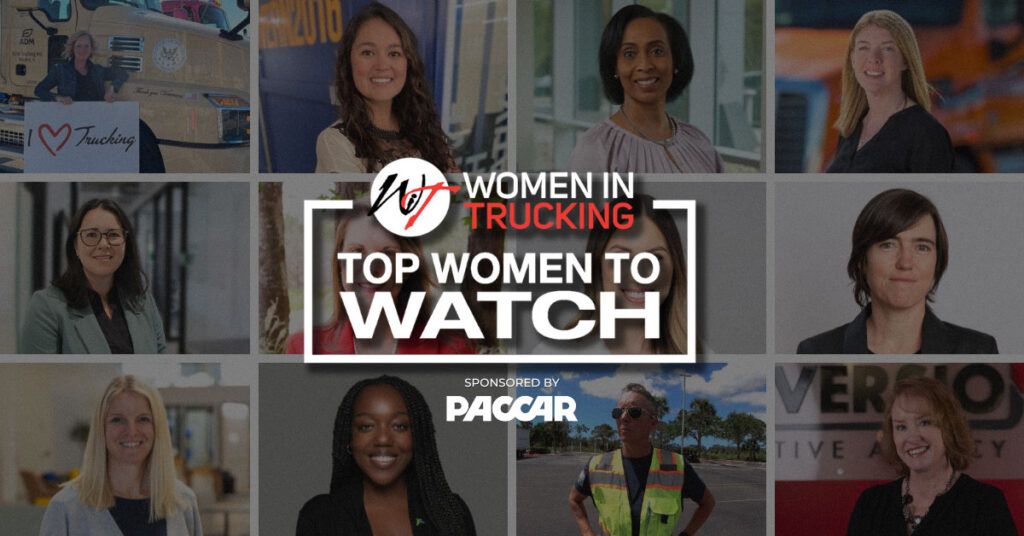
The Women In Trucking Association (WIT) announced today its 2024 Top Women to Watch in Transportation. The editorial staff of Redefining the Road, WIT’s official magazine, selected these individuals for their significant career accomplishments in the past 12 to 18 months, as well as their efforts to promote gender diversity. “This year’s list is comprised of 75 impressive women who have excelled in their career in a male-populated industry,” said Brian Everett, group publisher and editorial director of Redefining the Road magazine. “We are pleased to take this opportunity to shed light on the incredible achievements of these accomplished professionals.” “For eight years, we’ve been pleased to recognize the accomplishments of women in transportation who make a significant impact to the industry and those around them,” said Jennifer Hedrick, WIT president and CEO. “These women exemplify the mission and values of the Women In Trucking Association and truly are top women to watch in our industry.” Those recognized on the 2024 Top Women to Watch in Transportation list work for a broad range of company types, including motor carriers, third-party logistics companies, equipment manufacturers, retailer truck dealers, professional services companies, technology innovators and private fleets. Their job functions include sales/marketing (29%), safety/operations (19%), human resources/talent management (17%), corporate management (12%), customer experience/service (10%), engineering/technology 6%, driver/training (4%), and financial (3%). Individuals recognized as 2024 “Top Women to Watch in Transportation” are: Jessica Bennett, remarketing sales manager, Premier Truck Group Jennifer Biehn, VP, human resources, The Evans Network of Companies Hannah Bryan, fleet solutions sales manager, The Goodyear Tire & Rubber Company Heather Callahan, director of logistics, Daimler Truck North America Frances Craig-Watson, transportation feeder division manager – south Florida, UPS Katrina Cribbs, manager of national accounts customer support, Old Dominion Freight Line Brittany Cutler, business development manager, Crossroads Equipment Lease & Finance Christina Davis, VP of marketing & business relations, AMX Jenny DeArmond, corporate recruiter, Stoops Freightliner – Western Star Christina Denvit, senior director, dedicated contract solutions (DCS) operations, J.B. Hunt Transport Tracy Derival, marketing assistant, Fleet Advantage Tonyah Dillahunt, PR & marketing communications manager, Peterbilt Motors Company Tanika Dunlap, software development manager, Southeastern Freight Lines Sydney Emrich, senior manager, customer experience, J.B. Hunt Transport Abbi Failla, VP of business operations, EASE Logistics Angela Fish, executive VP, human resources, Schneider Tena Fisher, service center manager, XPO Melissa Forman, president, executive VP, TriumphPay Melanie Franklin, group director, sales, Ryder System, Inc. Paula Frey, chief human resources officer, Echo Global Logistics Lori Fulmer, VP, enterprise human resources, Covenant Logistics Rosa Gamboa, business development manager, Crossroads Equipment Lease & Finance Lauren Gassmann, operations manager, Booster Vanessa Gauci, sr. transportation efficiency manager, Frito-Lay North America Armida Gonzalez, assistant plant manager, Peterbilt Motors Company Angel Grable, manager of business operations learning, Werner Enterprises Mandy Graham, chief operating officer, Great West Casualty Company Jodanna Hall, sr. director customer logistics transportation management, Ryder System, Inc. Debra Hamlin, director of operations, Bridgestone Commercial Dealer Network, Bridgestone Americas Abby Hamm, VP, sales, Covenant Logistics Lynne Hansen, national accounts sales executive, PLM Fleet Lauren Harper, sr. strategist for business operations, Kodiak Robotics Gwen Hill, SVP of transportation & compliance, Clean Harbors Selin Hoboy, VP – EHS & compliance, GFL Environmental Shannon Jedlicka, recruiting & compliance, ADM Trucking Megan Knight, director of product marketing, PACCAR Parts Hannah Koury, sr. customer success manager, TA Dedicated Amy Lester, VP, quality, Navistar Monica Maez, sr. project manager, Standard Logistics Sylvia Mahfouz, director of recruiting, TCI Transportation Sue Maier, VP of sales systems and analytics, Penske Truck Leasing Christina Mannella, sr. director – west transportation command center, Walmart Kelley Martin, director, pricing strategy, Daimler Truck North America Samantha McCracken, strategic operations manager, Bridgestone Americas Kris McLennan, VP of yield management, A. Duie Pyle Megan Miller, director of commercial sales channel development, Bridgestone Americas Sarmona Miller, director of revenue management, Saia LTL Freight Leah Miller, director, culture & communication, Trimac Wendy Mitckes, tax manager, Navistar Alyssa Myers, VP technology, RXO Jill Nash, VP – national accounts & brokers, GFL Environmental Nicole Neumann, VP, human resources, XPO Cari Olive, people operations/human resources, Armstrong Transport Group Kaitlyn Olsen, director of human resources, Christensen Ann Peng, patent agent, Plus Caitlin Powell, director of communications & marketing, TA Dedicated Sarah Quick, associate VP, safety & compliance, USA, Day & Ross Cassie Quien, director of business development, FreightVana Logistics Jessica Ramirez, VP of human resources, Velocity Vehicle Group Beverly Ringstaff, VP of brand & design, Conversion Interactive Agency Michelle Roberts, lead CDL instructor, FleetForce Truck Driver Training Lissette (Lisa) Rodriguez, talent acquisition supervisor, Air Products Martha Ross, account resolution team leader, Volvo Financial Services Suzanne Scalone, director of fleet operations, Performance Food Group Mary Schreiber, benefits & payroll manager, Tri-National, Inc. Andrea Sequin, director, regulatory services & driver training, Schneider Heather Shirazi McAfee, engineering & strategic analytics manager, Saia LTL Freight Cindi Smith, operations specialist, Candor Expedite Pamela Stine, district manager, Waste Connections Abby Szafranski, head of product management, fleet, Irdeto Alexandria Uribe, sr. director, total talent management, WM Raquel Urtasun, founder & CEO, Waabi Khristine Vanzuiden, surface network planning manager, UPS Natalie Williams, VP of client operations, Ancora Training Jaimie Wilson, learning & development manager, Atlantic Logistics This year’s recognition program is sponsored by PACCAR. The women will be featured in the upcoming edition of WIT’s Redefining the Road magazine and online at www.womenintrucking.org/top-women-to-watch.
Caldwell celebrates 70 Years
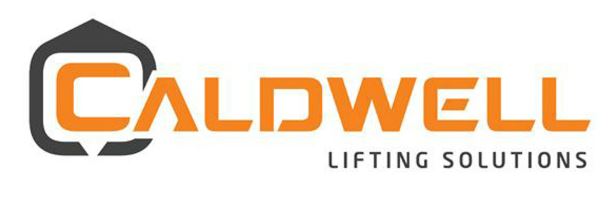
The Caldwell Group Inc. is celebrating 70 years. The below-the-hook and material-handling equipment manufacturer will mark the occasion with a series of events, culminating in a late-summer gala with customers, partners, suppliers, and staff. Founded by Leslie Caldwell in 1954, as a maker of lifting slings, the firm has expanded and moved several times over the decades, now occupying two large manufacturing and warehouse facilities. The company has been shaped by numerous acquisitions and collaborations, including the purchase of the J.C. Renfroe lifting clamp business and a strategic partnership with RUD to bring lifting points and other products to the U.S. and Canada. Today, Caldwell employs over 120 people. Doug Stitt, president and CEO, said: “Not only have we existed for 70 years, but we have evolved and developed what we provide to the marketplace. “We’ve contributed to how people lift and move things, and how they can do it more safely. We’ve been able to provide a great place to work and created a community, so it’s a celebration of all our people, suppliers, and customers that have supported and contributed to success and longevity.” He added: “Business becomes tougher and tougher every year, it seems, so taking some time to appreciate our accomplishments is worthwhile. Nothing can be taken for granted in today’s marketplace. It’s important to celebrate significant milestones because it pays respect to all those who helped build the company and those who are currently working toward the next 70 years. “It’s crazy to think we started with sewing machines making slings and now we are one of the leading fabricators of welded, steel lifting products.” Recent highlights include partnering with Majestic Steel USA to deliver coil grabs, sheet lifters, and hooks for a facility in Arkansas; expanding the series of RUD ACP-Turnado lifting points by adding Max and Supermax versions; and designing a 2,500-lb. capacity transport cradle, to facilitate final assembly of Intuitive Machines’ lunar lander, Nova-C. The wider portfolio includes an assortment of below-the-hook lifters, for handling beams, coils, and sheets; mill-duty lifters; Posi-Turner load rotation equipment; vacuum lifters; construction lifters; fork truck attachments; jib and gantry cranes; Rig-Release remote releasing hooks, Dura-Lite composite lifting products; Renfroe lifting clamps; and RUD lifting points. Stitt added: “Yes, the products we offer are different now, but we still focus on quality; we still focus on helping our customers solve problems, and we are still integral in keeping safe lifting at the forefront. We’ll continue to introduce new products and services for our customers, but I expect the next 70 years to focus on building quality products and providing our customers with the best overall experience possible—that’s what matters.”
Green Cubes Technology announced Lithium SAFEFlex PLUS Batteries for motive power applications
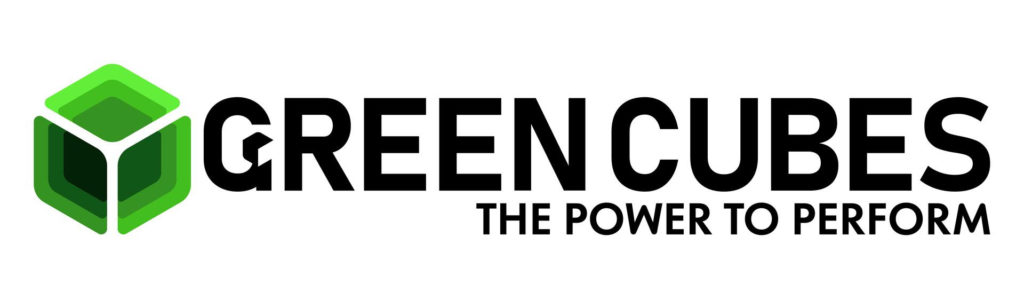
As electrification of material handling equipment continues to gain traction, Green Cubes offers modular battery technology to ensure safety and sustainability for electric fleets. Green Cubes Technology (Green Cubes), a producing Lithium-ion (Li-ion) power systems that facilitate the transition from lead-acid batteries and Internal Combustion Engine (ICE) power to green Lithium-ion (Li-ion) battery power, has announced Lithium SAFEFlex PLUS Motive Power Lithium Batteries. The batteries are sized to fit the standard material handling lead acid battery compartment and meet truck battery weight requirements. “With an enhanced feature set developed based on ten years of experience with the groundbreaking Lithium SAFEFlex product line, Lithium SAFEFlex PLUS is a comprehensive battery solution designed to meet the cost, performance, efficiency, and durability requirements of the rugged warehouse environment,” said Robin Schneider, Director of Marketing for Green Cubes. “The Lithium SAFEFlex PLUS drop-in replacement batteries make upgrading from Lead Acid to Lithium simple and the modular design improves serviceability and facilitates family safety certifications.” The battery’s flexible design is ideal for high-current truck applications and will perform safely and efficiently even in extremely low-temperature cold storage operations. Additional features include modular design with individual cell monitoring, distributed BMS intelligence and data logging, advanced Wi-Fi connectivity, and network security protocols. Charge ports or single-point battery connections replicate today’s lead acid without special truck or charger modifications. Lithium SAFEFlex PLUS Motive Power Lithium Batteries will be available for shipment in 36V and 48V models in the second half of the year.
Ignition Gold Certified Integrator Patti Engineering announces further credentials, elevating expertise in industrial control solutions
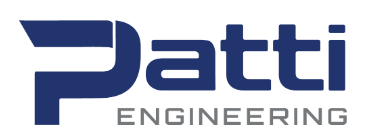
Ignition Gold Certified Integrator Patti Engineering’s Akash Agarwal has earned the Ignition Core Certification by Inductive Automation, providing certified expertise in SCADA, MES, and IIoT applications. Patti Engineering, Inc., an Ignition Gold Certified Integrator and control system integration company with offices in Michigan, Texas, and Indiana, has announced that Controls Engineer Akash Agarwal achieved Ignition Core Certification by Inductive Automation, joining six additional team members holding specialized certifications on the Ignition platform. Agarwal has completed Core Certification competency exams for Inductive Automation’s Ignition, a powerful web-based industrial software platform for SCADA, MES, and IIoT applications. Additional employees certified for Ignition at Patti Engineering are Jeffrey Watts, who recently achieved Gold Certification, along with Abigail Engle, Cassandra Boman, Daniel Ragozzino, John Shipley, PE, CAP, and Scott Grunwald, all having attained Core Certifications. These certifications demonstrate advanced proficiency in the design, development, and implementation of tailored control solutions that optimize efficiency, productivity, and operational visibility using Ignition. “As a Gold-level partner in our Integrator Program, Patti Engineering has an advanced capability with Ignition,” said Chris Fischer, Integrator Program Manager at Inductive Automation. “The solutions that companies like Patti Engineering create are among the best in the industry because their knowledge and experience with Ignition enables them to create innovative solutions for clients. Patti Engineering’s Ignition certifications provide them with a competitive advantage in the integration industry, giving clients confidence in the robustness of their tailored solutions.” As an Ignition Gold Certified Integrator, Patti Engineering specializes in control system integration and digitalization services in the manufacturing and industrial sectors. The company’s demonstrated expertise ensures the smooth implementation of industrial automation software and hardware in a wide range of areas such as HMI, PLC, edge computing, data analytics, cybersecurity, asset management, and remote monitoring. The recent achievement of Ignition Core Certification by Agarwal, along with several other team members, illustrates Patti Engineering’s commitment to providing specialized expertise to meet the diverse needs of manufacturing and industrial clients. “We commend our engineers for helping Patti Engineering achieve and maintain Ignition Gold Certified Integrator status,” remarked Patti Engineering CEO Sam Hoff. “Our team’s dedication to training and best practices is pivotal in maintaining our ability to deliver the quality solutions our clients need in the industries we serve.”
Episode 468: Sustainable retail returns with Brian Adams of Retail Reworks
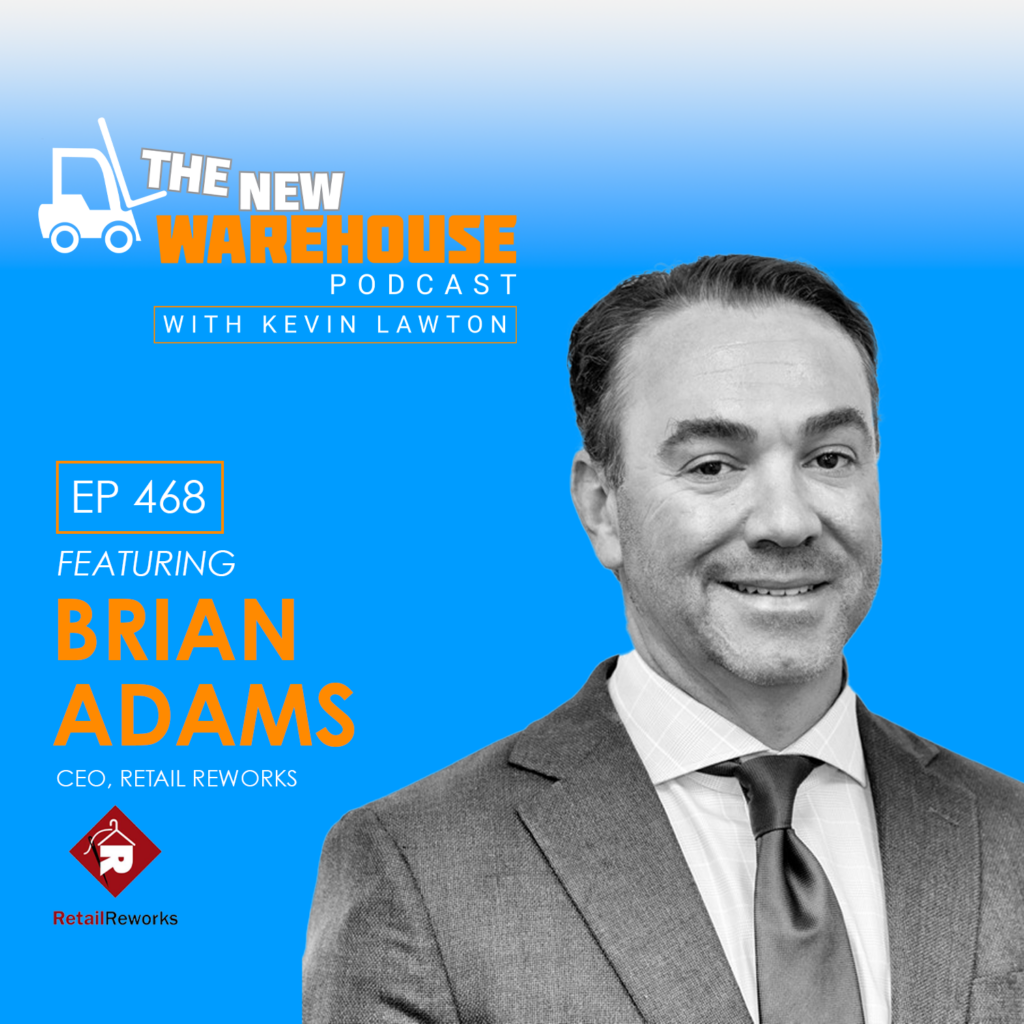
It’s an away game for The New Warehouse Podcast as Kevin visits the headquarters of Retail Reworks in Houston, Texas. He engaged in a thought-provoking conversation on sustainable retail returns with co-founder Brian Adams. With an average retail return rate of over 16%, this $800 billion-plus industry needs sustainable retail returns practices. Retail Reworks focuses on innovating in returns, re-commerce, and remanufacturing. Be sure to tune in to learn all about the evolving challenges and solutions in managing returns, alongside providing a wealth of industry insights. The Evolving Landscape of Retail Returns The market for retail returns has undergone significant shifts, primarily driven by changes in consumer behavior and economic pressures. Adams notes,“I think forever, you know, returns are something that a 3PL had to do if they wanted to gain the business… And as return rates get higher and manufacturing costs get lower, returns became an impediment on people’s profitability.” However, the traditional model of handling returns has become unsustainable. He adds, “Returns are a very big piece in people’s businesses, not just a small line item on a P&L statement.” As consumer expectations have moved towards more lenient return policies, the economic burden on retailers has intensified. Adams highlights a pivotal moment in February 2023, marking a major correction in the valuation market, signifying the start of a new era in how returns are perceived and managed within the industry. Pioneering a Sustainable Retail Returns Solution Retail Reworks’ approach to addressing the return dilemma is not about selling a service but partnering for sustainable solutions. Adams emphasizes the importance of “making the circles smaller” to enhance the efficiency and sustainability of the returns process. By leveraging a network of locations and innovative software, Retail Reworks developed a system that allows for boxless, fraud-less returns, immediate refund initiation, and instant item availability for resale. This model not only cuts down logistical costs but also significantly reduces the environmental footprint of returns. Towards a Circular Economy As Adams discussed, the future of returns is undeniably circular. With a growing emphasis on sustainability and efficient resource utilization, the retail industry is gradually shifting towards models prioritizing circularity.“It’s all about speed… the faster you can recapture the revenue on the return, the lower that the cost of the inventory you’re going to have,” emphasizes Adams. Retail Reworks’ efforts to remanufacture and repurpose returned items into new products are a testament to the potential of sustainable retail returns. Key Takeaways The landscape of retail returns is changing, necessitating innovative and sustainable management practices. Retail Reworks champions a solution that addresses the logistical and economic challenges of returns and promotes environmental sustainability. The future of sustainable retail returns lies in adopting circular economy principles, emphasizing the repurposing and efficient utilization of resources. The New Warehouse Podcast EP 468: Sustainable Retail Returns with Brian Adams of Retail Reworks
Latest research report reveals Key Drive for ‘Accuracy’ Amongst Warehouse Operations
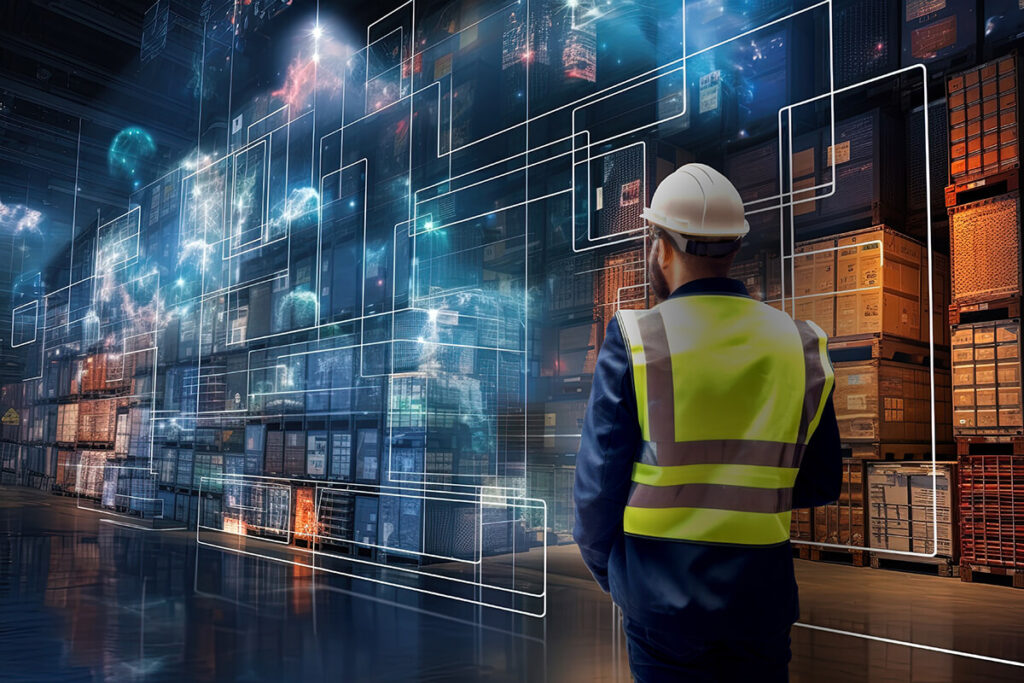
The importance of accuracy has doubled in two years; drive to adopt new technology in the warehouse to improve accuracy also increasing The latest report from StayLinked, independently conducted by VDC Research, shows that the focus on accuracy within warehouse operations has reached new heights. The drive for accuracy, to achieve the ‘perfect order rate’, has almost doubled since StayLinked’s 2022 survey. Provided with a list of ten different areas of improvement, accuracy was listed as the most important area by 15.1% of respondents, rising from 8.7%. “As market conditions continue to be volatile and unpredictable, this latest survey shows the importance of building accuracy into warehouse operations to drive resilience, flexibility and agility through accurate visibility of warehouse operations,” said Justin Griffith, StayLinked’s chief technology officer. The latest research from StayLinked, conducted by VDC Research, is published here: Making Supply Chain Resilience Work: Keeping Up with Ever-Demanding Warehouse Operations. The research of warehouse operations technology decision makers, across multiple industries including retail, manufacturing, transportation/logistics, retail, and wholesale organizations was conducted in 2023 and the report is being published now. “The 2022 survey was all about speed, with the focus being on-time shipments and getting orders out the door as quickly as possible,” continued Griffith. “That is still relevant now, but the focus on accuracy has leaped up.” Increased accuracy is not a pipe dream as emerging technologies can dramatically improve the accuracy of warehouse operations. Technologies also exist that can meet the survey’s other top improvement initiatives: continuing to ensure that goods are shipped quickly and helping to significantly improve the warehouse worker’s experience. However, to be adopted in the warehouse, these new technologies need to integrate with and ‘talk to’ the organizations’ warehouse management systems (WMS). This latest report highlights the link between the age of the underlying enterprise applications underpinning supply chain and warehouse operation and the ability to successfully deploy new technology. The report states: “There is a strong correlation between the age and flexibility of the underlying enterprise applications supporting logistics operations – be it WMS, ERP, WCS or others – and the ability for organizations to streamline logistics technology evaluation and integration. Maximum system flexibility is required to be able to integrate the planned, growth-defined future adjustments in warehousing and to control them in a coordinated manner.” The survey data showed that there has been an increased emphasis on the WMS – 61.1% of organizations were on the most current WMS or running just one or two years behind – a significant increase from 45% in 2022. This has seen a comparative increase in new technologies introduced into the warehouse. Warehouses that haven’t been able to move to the latest WMS will fear that they are in danger of permanently losing ground on their competitors. That fear is often combined with frustration at the impossible task ahead of them to replace the WMS. However, for those running an older WMS, it’s not true that a complex, risky, and expensive ‘rip and replace’ option is always required. “It’s like renovating your house. For most of us, we have to do it bit by bit, prioritizing different rooms as we go,” explained Griffith. “StayLinked can help warehouse operators similarly introduce new technologies. They don’t need to knock down the house – or rip out the WMS – in one go. They can simply adopt the new technology they need when they need it.” StayLinked’s enterprise-grade terminal emulation (TE) software SmartTE and its no-code technology adoption platform, Evolve, allow warehouse operators to modernize their existing WMS so that they can deploy a mixture of new technologies. One emerging technology will not rule them all, so it is crucial that multiple new technologies can be integrated into the warehouse operations’ workflows where they best fit and can deliver the most benefit, and at a pace that works for the warehouse operator. The research highlighted some of the emerging technologies that are most likely to be adopted by warehouses: Over 97% of warehouses plan to be using Locationing Systems and Predictive Analytics by 2027. Currently only in use by 20% of warehouses, nearly 85% of all warehouses plan to have deployed Person-to-Goods AMRs by 2027. Drones are the least popular of the emerging warehouse technologies. 36% of all surveyed said they had no plans to use drones at all. StayLinked can help warehouses quickly and easily integrate all of these new technologies into their existing warehouse management system to help them improve productivity, increase efficiencies, and most importantly, according to the research, improve accuracy. Download a copy of the report from StayLinked’s website: Making Supply Chain Resilience Work: Keeping Up with Ever-Demanding Warehouse Operations.
Schneider electric debuts new collaborative robots at MODEX 2024
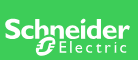
Robotics innovations from Schneider Electric enable efficiency, cost savings, and consistent outputs for manufacturers New offers allow Schneider Electric to provide customers complete, customized automation solutions simplifying sourcing, commissioning Schneider Electric, a digital transformation of energy management and automation, has announced the release of two new Lexium cobots (collaborative robots) at MODEX 2024, the Lexium RL 3 and RL 12, as well as the Lexium RL 18 model coming later this year. Schneider Electric innovations in robotics and motion will be on display at their booth, #B7232. From single-axis machines to high-performance multi-axis machines, the comprehensive Lexium line enables high-speed motion and control of up to 130 axes from one processor for precise positioning to help solve manufacturer production, flexibility, and sustainability challenges. Schneider Electric goes beyond robots to provide fully integrated automation systems – digitally designed from concept to operation and maintenance. Integrating robots into the machine control solution through the EcoStruxure architecture enables collaborative data flow from the shop floor to the top floor, by connecting smart products, robots, controls, software, and services. Controlled by Modicon motion controllers, which unify PLC, motion, and robotics control functionality on a single hardware platform and integrated into EcoStruxure Machine Expert software, it offers a complete robotic solution. “As US manufacturing increases, the demand for smart machines is growing and customers are requiring robots with digital twin capabilities that validate machine performance to help them quickly increase production consistently, efficiently, and sustainably,” said Christine Bush, Robotics Center of Excellence Leader, Schneider Electric. “We are partnering with our customers to understand their challenges and pain points, then responding with complete, customized automation solutions – from power products and HMIs to PLCs and robotics – to simplify the process and meet their needs.” Compatibility with EcoStruxure Machine Expert Twin, a digital twin software suite that creates digital models of real machines, allows for virtual test strategies and commissioning, as well as shortened factory acceptance testing (FAT). Digitizing these processes can reduce time-to-market by up to 50% and commissioning time by up to 60%. A 20-40% savings in investment costs can also be realized due to faster time-to-market. Lexium cobots are part of a full line of robotics and automation solutions developed to meet manufacturer needs across industries, including warehouse/logistics, life sciences, consumer packaged goods, and beyond. Benefits of Lexium robotics and motion solutions include: Fast deployment: Built on open automation standards and protocols, cobots offer flexibility, scalability, and easy third-party equipment integration. They can be easily applied to existing or new production lines in a variety of different industries. Streamlined integration: Enhanced computing power, open software, and networking technologies facilitate quicker assembly, installation, and maintenance of robots. A centralized architecture with a unified programming platform using open standards promotes seamless interoperability among automation systems, machines, and robots. Consistent output: Designed to handle repetitive tasks without errors or distractions, cobots can maintain Overall Equipment Effectiveness while manufacturing higher volumes of quality goods over shorter periods 24/7 without fatigue. This produces a consistent output with little variability over a given production batch. Workplace health and safety: Cobots perform well in harsh environments and can handle riskier operator tasks involving heavy weights to reduce accidents and injuries. Amidst the rapid growth of US manufacturing, companies are increasingly seeking digital, efficient, and sustainable solutions to meet expanding output demands. Embracing Industry 4.0’s digitization, with advancements in artificial intelligence, machine learning, IoT, and digital twins, has become imperative to drive operational excellence. Software solutions are also playing a critical role in empowering manufacturers to innovate rapidly, reduce commissioning time, and stay competitive in this evolving landscape. As the industry transitions to Industry 5.0, the Lexium motion and robotics offers are poised to redefine efficiency and enable personalized autonomous manufacturing. To learn more about the innovations on display at MODEX and those coming in the fall, visit the Schneider Electric Booth B7232 at Building ABC, Level 1 at MODEX 2024
ELOKON introduces safety system for driverless transport vehicles at MODEX 2024
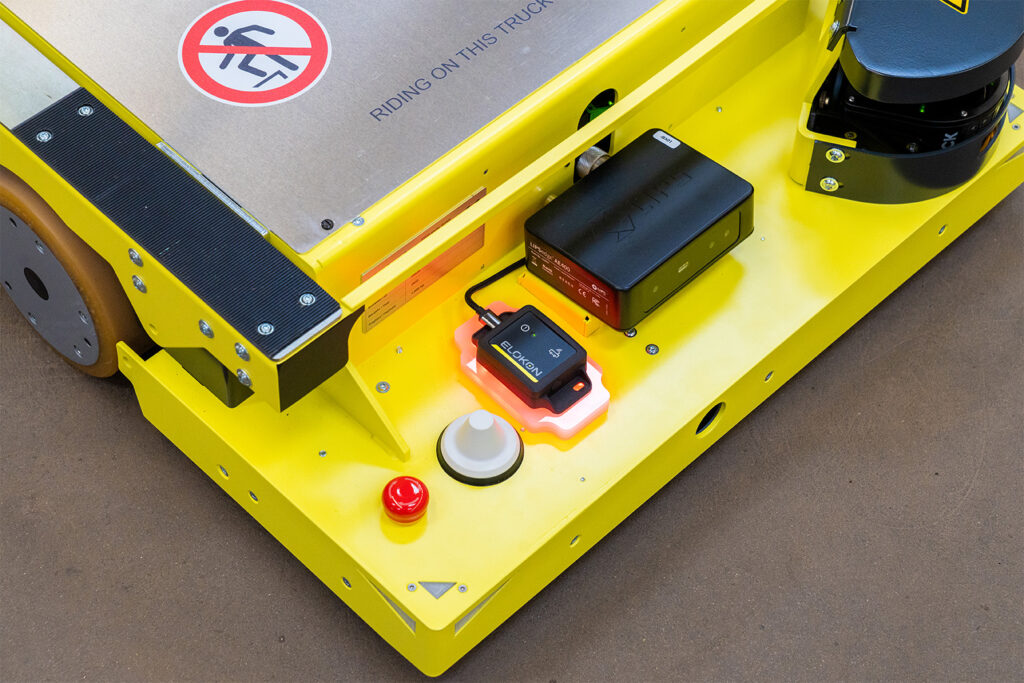
Attendees can experience the ELOshield forklift safety and pedestrian detection system, the new ELOshield module for automated guided vehicles/autonomous mobile robots and the ELOfleet telematics system in booth #B9206 in Atlanta March 11-14; CEO Alex Glasmacher hosts three interactive seminars on how to benchmark safety systems for material handling equipment in warehouses, distribution centers and manufacturing plants. ELOKON, Inc., an innovator in automated forklift safety and fleet management systems, will showcase its new ELOshield module for driverless transport vehicles such as automated guided vehicles (AGVs) and autonomous mobile robots (AMR) at the MODEX Show March 11-14 in Atlanta. With ultra-wideband (UWB) wireless sensors that offer a 360-degree range of up to 82 feet, the ELOshield AGV/AMR module prevents collisions between these small and often overlooked vehicles in warehouses, distribution centers, and manufacturing plants and forklifts equipped with the ELOshield forklift safety and pedestrian detection system. The radio-based ELOshield AGV/AMR module acts as a stand-alone antenna that can be easily installed on these material-handling vehicles due to the module’s small size (3.3in x 2in x0.8in). The module can be used in fleets with all different types and brands of AGVs and AMRs and can be pre-installed by vendors or suppliers or retrofitted onto existing fleets, no matter how long they’ve been deployed. “With driverless transport vehicles an integral part of today’s warehouses, distribution centers and even manufacturing plants, the ELOshield AGV/AMR module significantly increases worker safety while protecting the organization’s major investment in automated material handling technologies,” said Alex Glasmacher, CEO, ELOKON. “When combined with warning lights, gate controls or projectors, as companies often do, they see an even more comprehensive improvement in operational safety without compromising vehicle productivity in any way.” ELOshield, the ELOshield AGV/AMR module and ELOKON’s cloud-based forklift fleet management solutions (ELOfleet) will be shown in booth B9206. ELOshield and ELOfleet are used by many of the world’s largest companies to make their warehouses, distribution centers and manufacturing plants safer and more efficient. Join interactive discussions in three benchmarking material handling equipment safety seminars In his three seminars, Glasmacher will discuss how to benchmark safety systems for material handling equipment during on-floors seminars each day of the show. The interactive presentations will provide: An overview of the current state of safety systems in materials handling equipment (MHE), including the latest technology advancements and industry standards. Discuss real-world case studies and experiences from industry leaders, highlighting the importance of implementing robust safety systems to prevent accidents and injuries. Present a systematic framework for benchmarking safety systems, including key performance indicators, testing methodologies and evaluation criteria. Explore emerging technologies, such as UWB two-way ranging solutions, UWB RTLS solutions, camera-based RTLS solutions, AI, Data Analytics and IoT, and their role in enhancing safety measures within MHE operations. Facilitate discussions and knowledge-sharing among participants, encouraging collaborative efforts to improve safety standards across the industry. Provide an innovation outlook on further developments in IoT sensors, machine learning algorithms, Data Analytics and merging telematics and safety systems for even more sophisticated safety solutions “The rapid advancement of material handling equipment (MHE) technology has significantly improved efficiency and productivity in various industries, but ensuring the safety of both operators and the workplace environment remains a paramount concern,” Glasmacher added. “To address this, we’ll explore the critical need for evaluating and comparing safety systems within the MHE domain. We encourage MODEX attendees to join our interactive discussions at one of these three sessions to help improve safety standards across the industry.” The “Benchmarking Safety Systems for Material Handling Equipment: A Comprehensive Evaluation” seminars are scheduled for: March 12, 12:45 p.m. – 1:30 p.m. Theater B March 13, 3:00 p.m. – 3:45 p.m. Theater H March 14, 9:30 a.m. – 10:15 a.m. Theater C
Slamcore Aware brings the power of vision to Real-Time Location Systems (RTLS)
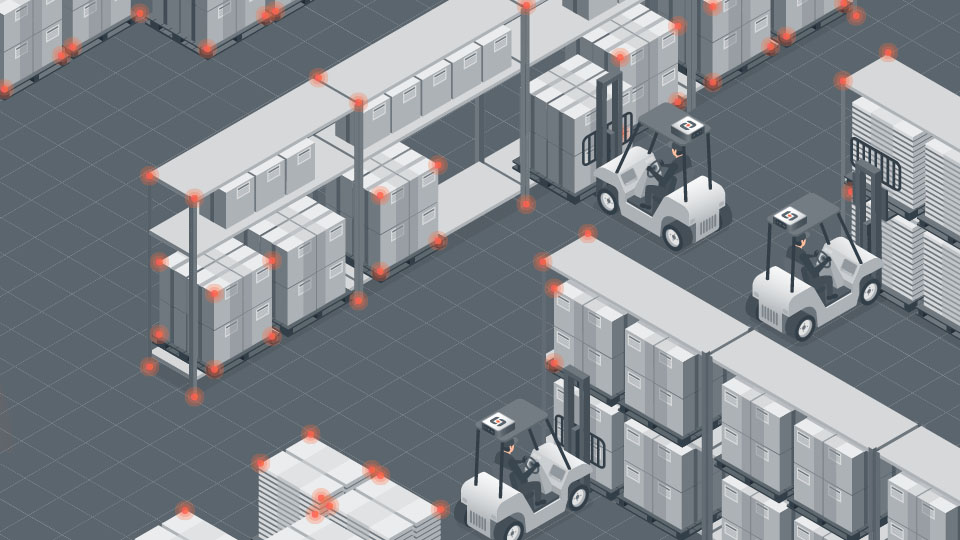
Slamcore launches Visual Intelligence Localization solution for manually driven intralogistics vehicles at Modex Slamcore Aware combines the power of the Slamcore SDK with industrial-grade hardware Simple and quick to commission, scales with the fleet irrespective of the size of the facility to deliver more accurate and robust spatial data for RTLS Visual Spatial Intelligence identifies people and other vehicles for enhanced safety and efficiency Slamcore, a visual-spatial intelligence, launches Slamcore Aware. This easy-to-commission hardware and software solution improves the accuracy, robustness, and scalability of 3D localization data for tracking intralogistics vehicles. Collecting and processing visual data, Slamcore Aware provides rich, real-time information on the exact position and orientation of manually driven vehicles. Unlike existing solutions, Slamcore Aware scales easily across large and complex, ever-changing industrial and warehouse sites. Slamcore Aware combines the power of the Slamcore SDK with industrial-grade hardware, providing an all-in-one solution for fast installation on intralogistics vehicles and seamless integration with new and existing Real Time Location Systems (RTLS). Incorporating Slamcore’s advanced AI, Slamcore Aware perceives and classifies people and other vehicles. RTLS applications can use this enhanced data to significantly improve the efficiency and safety of operations. Commenting on the new product, Owen Nicholson, CEO of Slamcore, said: “Prospective customers tell us that they are looking for a fast-to-deploy and scalable method that will provide the location data they desperately need to optimize warehouse and factory intralogistics for speed and safety. Slamcore Aware marks a significant leap forward in intralogistics management bringing the power of visual-spatial awareness to almost any vehicle in a way that is scalable and can cope with the highly dynamic and complex environments inside today’s factories and warehouses.” See us at MODEX 2024 at booth #A13918
Liberty Robotics Inc. introduces Advanced Robotic Vision Technologies at MODEX Trade Show with Signode at MODEX 2024
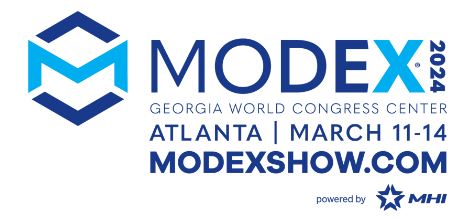
Together with partner Signode, Liberty Robotics will showcase their new AI robotic vision technology, VPack™, in booth #B1411 at Modex Trade Show on March 11-14, 2024 at the Georgia World Congress Center in Atlanta, Georgia. Liberty Robotics Inc., a 3D volumetric vision guidance system for robot applications, has announced its participation in the upcoming MODEX trade show, where it is set to unveil its latest developments in robotic vision and automation. This year’s highlight, the VPack™ system, will be presented through an interactive mixed-case palletizing display at booth #B1411, marking a significant advancement in material handling technology. This initiative is in collaboration with Signode, an end-of-line packaging solutions. “Our collaboration with Signode at MODEX 2024 marks a significant milestone in our journey towards revolutionizing the warehousing, logistics, and end-of-line packaging industries,” said Bob Berry, President and CEO of Liberty Robotics Inc. “We are excited to showcase how our Vision AI technologies can transform the future of automation and create more efficient, reliable, safe, and productive operations.” Attendees of the MODEX trade show will have the opportunity to witness firsthand the capabilities of Liberty Robotics’ advanced machine vision systems, focusing on the mixed case palletizing capabilities of the recently launched VPack™ system. VPack™ features ad hoc picking capabilities and digital twin technology, along with high-accuracy sensors for precise box detection. Representing Liberty Robotics Inc. at the MODEX trade show will be Bob Berry, President and CEO, G Neil Haven, CTO and founder, and Myron Czubko, Business Development Manager. Berry oversees the company’s day-to-day operations as well as strategic direction. Haven, who founded Liberty Robotics in 2005, specializes in designing real-time algorithms for vision applications. Czubko focuses on business development for Liberty Robotics’ automated warehouse vision systems, VPack™ and VPick™, bringing over 30 years experience in the machine vision industry. MODEX 2024 is where the manufacturing and supply chain industries converge to explore the breadth of new technologies and strategies for streamlining operations and achieving greater efficiency and transparency. The event promises to deliver an extensive array of insights with five keynotes and 200 educational sessions, showcasing the solutions of over 1,175 leading providers. With an anticipated attendance of over 45,000 professionals, MODEX 2024 offers a unique opportunity to engage with the latest in traditional equipment, sustainability initiatives, automation, robotics, and emerging tech.
Rockwell Automation to showcase warehouse and fulfillment solutions at MODEX 2024
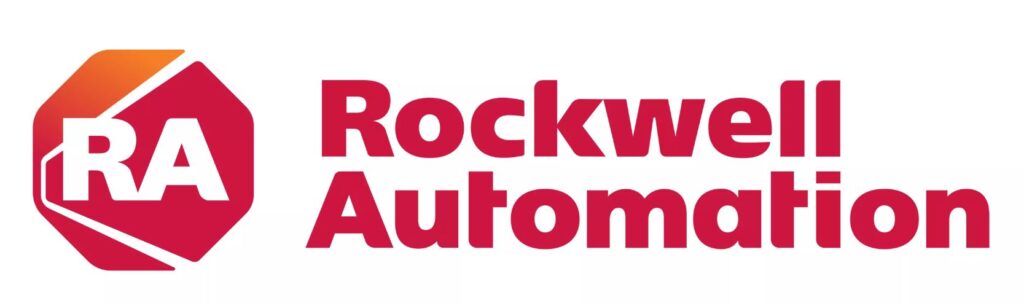
Rockwell Automation, Inc. plans to expand its presence at MODEX 2024 in Atlanta, GA., March 11-14. The company will showcase the latest warehouse and fulfillment solutions across two booths, including an innovative new category, autonomous production logistics (APL), from its latest acquisition, OTTO Motors. This new category unlocks a vision of a fully connected factory, designed for end-to-end efficiency. “I can’t think of a better place to see the future of warehouse automation and intelligent material movement than the Rockwell Automation and OTTO Motors properties at MODEX,” said Evan Kaiser, industry director of Warehousing and Logistics at Rockwell Automation. “Workforce shortages and demand fluctuations continue to create complex value chains in the industry. Our technologies help logistics professionals innovate their business and compete in a digital-first marketplace.” MODEX attendees can stop by Rockwell Automation’s booth (#B2419) to experience the latest technologies driving flexibility, productivity, and sustainability in the material handling and supply chain industries. Here are just a few of the technologies that will be on display for attendees to experience first-hand. OTTO Motors Autonomous Material Handling: Discover how OTTO Motors automates material handling tasks to help manufacturers tackle workforce shortages, scale their business, and increase productivity. Attendees can see a live demonstration of OTTO 100, the smallest autonomous mobile robot (AMR) capable of moving payloads up to 150 kg (331 lbs.). Emulate3D™ Simulation Station: See how MODEX veteran Emulate3D™, Rockwell Automation’s digital design software, can reduce time to market, improve startup reliability, and enable scenario planning. 3D warehouse drawings modified in real-time will demonstrate the software’s ease of use for logistics professionals. Armor™ PowerFlex® Drives: Get access to updated Armor™ PowerFlex® distributed control solutions that simplify design, integration, and maintenance through on-machine motor control. Attendees will discover how these scalable solutions prioritize safety and durability in material handling environments. Interactive Virtual Warehouse: Explore videos and demos of the latest warehouse and logistics solutions — like independent cart technology, digital facility design, unified robotic control, and more. Attendees can connect with industry experts to discuss how these solutions can optimize their unique warehousing configuration. The company’s expanded presence will also include a demonstration of the full fleet of AMRs at the OTTO Motors by Rockwell Automation booth (#B9419). This includes two OTTO 100 AMRs and two OTTO 1500 AMRs equipped with lift and conveyor attachments that can move payloads up to 1500 kg (3300 lbs.). OTTO Lifter, the autonomous forklift capable of moving 1200 kg (2640 lbs.), will be rotating pallets with the OTTO 1500. While getting front-row seats to the industry’s most comprehensive AMR fleet in action, attendees can also explore OTTO Motors’ powerful software suite and learn about AMR deployments in mission-critical operations worldwide. Additionally, the latest Rockwell Automation solutions will be on display across MODEX in nearly 50 of its PartnerNetwork™ member booths. Attendees who experience Rockwell Automation’s game-changing solutions at MODEX will discover how their warehouse and logistics operations can become more connected, sustainable, and efficient.
Linde Material Handling to showcase new products and automated solutions at MODEX 2024
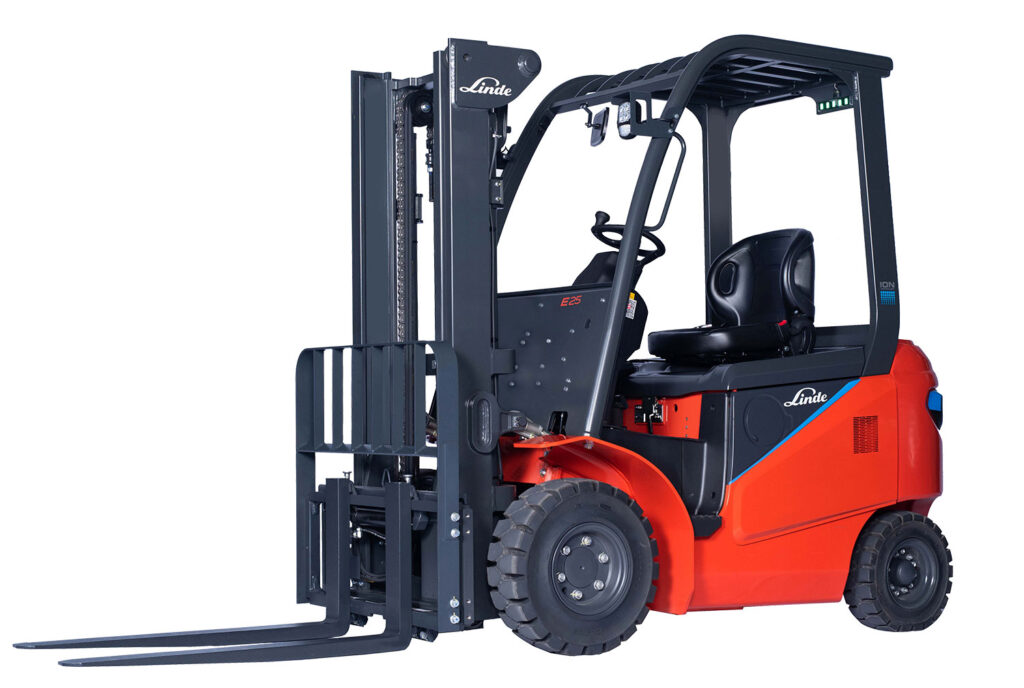
Linde Material Handling (LMH) is set to make a notable presence at MODEX 2024, taking place from March 11 to 14, 2024, at booths #B8011 and #C7495. The showcase will feature a diverse range of offerings, including recently launched products, popular warehouse solutions, engaging speaking sessions, and live demonstrations of cutting-edge Linde Automated Solutions. Attendees will have the chance to personally encounter innovative material handling solutions that include the following: Automated Solutions: View two demos live for the duration of the event. Booth #B8011 will display the K-MATIC (automated VNA turret truck) in action. Booth #C7495 showcases an automated counterbalance, the L-MATIC, driven by Linde MH’s easy-to-install AGV management system, PACS. Finally, Jack Kaumo, Intralogistics Sales Leader, will be hosting the keynote session “Getting the Most Out of Your Labor”, discussing insights and solutions for struggling with personnel management and considering the switch to an automated fleet. Operation Enhancers: Demonstrations and subject-matter experts will be available on the event floor for two operation-enhancing add-ons: Linde Guardian and Linde Li-ION Batteries. Linde Guardian is a communication system used to minimize the risk of forklift collision with infrastructure, pedestrians, or other trucks. The system includes various sensors and alerting devices that keep the operator aware of potential hazards, even around corners. Linde Li-ION Batteries are Linde’s solution for miscommunication between lift trucks and energy sources. Receive an accurate state-of-charge display and improve the energy efficiencies between the forklift and its battery. Electric Forklifts: Embrace sustainability in every environment without sacrificing performance. Experience the Linde Series 5195, and the Series 1346, and the new Series 1254X in-person this year. The 5195 is a narrow aisle reach truck built for your high-density warehouses. It’s accompanied by several ergonomic, efficiency, and easy access features to keep your operator, warehouse manager, and maintenance technician happy on the job. The 1346 is a stand-up electric counterbalance, built to maneuver easily through heavy-traffic warehouses. Its small footprint, low height suspended platform, and robust frame are purposefully designed for highly challenging applications. The 1254X pushes the performance of electric trucks to meet that of internal-combustion; it’s capable of operating shoulder-to-shoulder in the same environment, with the added benefit of more efficient energy solutions. Next Generation of Pallet Trucks: The MT15B and MT22 will debut for the first time in a public forum this March. These trucks are engineered for flexibility, with features to bring high-performance material handling to multi-shift workplaces. The MT15B is equipped with a Li-ION battery and onboard charger, with the option to replace the charger with a second battery. The MT22 combines higher capacity lifting with a small footprint for ease of use in confined spaces.
GreyOrange demonstrates results-driven robotics during MODEX 2024
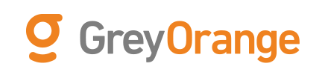
GreyOrange will showcase how the vendor-agnostic GreyMatter fulfillment orchestration platform ensures seamless warehouse automation during live demos with partners in Booth #C5692 during MODEX GreyOrange Inc., an AI-driven fulfillment automation, is demonstrating what tailored results-driven robotics within fulfillment environments look like during MODEX 2024 in Atlanta at the Georgia World Congress Center. GreyOrange will also share some of its booth space with seven partner companies that are part of its Certified Ranger™ Network (CRN) ecosystem. “GreyOrange continues to set standards and advance the industry by partnering with credible hardware vendors as part of our Certified Ranger Network, including Hai Robotics, Quicktron, Youibot, Wellwit Robotics, Mushiny, Tompkins Robotics, and Cypher Robotics,” said Akash Gupta, Co-Founder and CEO, GreyOrange. “Robots manufactured by each of the partnering companies seamlessly integrate with GreyOrange’s fulfillment orchestration platform GreyMatter, allowing customers to use a combination of their preferred robot types or functions to get specific tasks completed.” The bots manufactured by the partnering vendors undergo extensive testing and are certified by GreyOrange. The integration of these solutions with GreyMatter exemplifies GreyOrange’s ability to prepare its customers for the future of fulfillment by providing tailored end-to-end warehousing with guaranteed performance. MODEX attendees can visit Booth #C5692 to engage with GreyOrange leaders during live demonstrations, including several Certified Ranger Network bots that will demonstrate how GreyMatter is providing “results-driven robotics” – also GreyOrange’s MODEX theme – within automated warehouses. In addition, attendees will get to experience customer sites and cutting-edge automation through a VR experience. “GreyOrange’s GreyMatter – our fulfillment orchestration platform – seamlessly coordinates multiple process flows and hardware agents, including robots, to complete tasks efficiently,” said Gupta. “Our demonstrations during MODEX will feature four distinct products – Rack-to-Person, Tote-to-Person, Assisted Picking and Intralogistics, with each robot or hardware solution manufactured by different vendors, yet harmoniously orchestrated by GreyMatter.” GreyOrange’s MODEX in-person demonstrations are designed for 3PL providers, big box retailers, fashion, and industrial end users seeking innovative and future-proof automation solutions. Committed to GreyMatter’s hardware agnostic capabilities, GreyOrange enables end users to select from various hardware service providers to complete work including Goods-to-Person (GTP) and other autonomous mobile robot (AMR) functions. GreyMatter’s flexibility and configuring capabilities drive results by assigning multiple agents – robots and humans – to complete work across various areas of the distribution center and material flows to increase efficiency and scalability. MODEX will be held at the Georgia World Congress Center in Atlanta from March 11-14. Attendees from across the globe can register for the conference and schedule to meet with a GreyOrange subject matter expert to witness multiagent orchestration firsthand as AMRs from GreyOrange, HAI Robotics, Quicktron, YOUIBOT, Wellwit Robotics, and Mushiny work together for seamless fulfillment.