Trew unveils new technology and education center
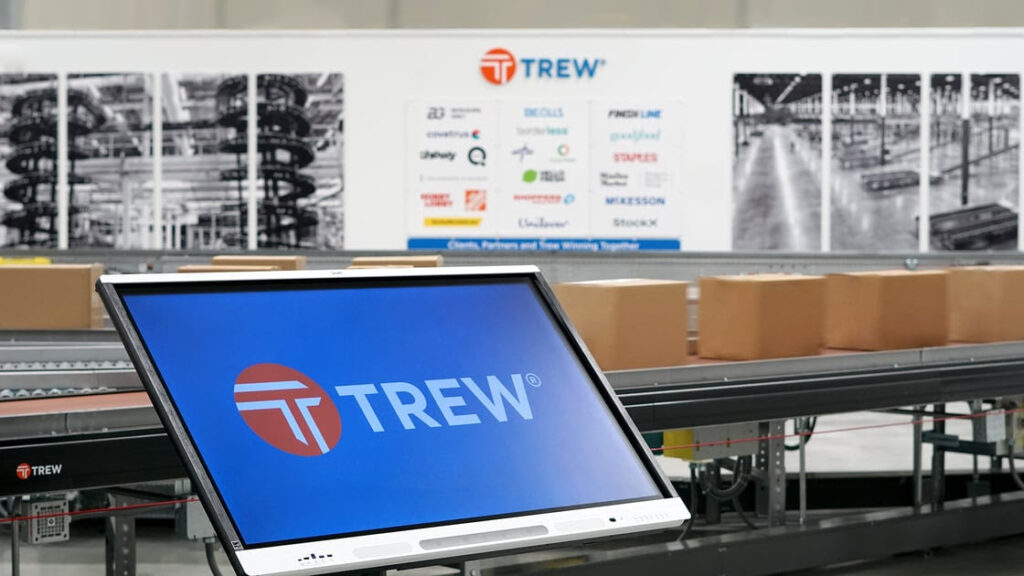
Trew, LLC has introduced its Technology and Education Center (TEC). Located in the company’s Fairfield facility, the TEC serves as a proving ground for research, development, and application testing as well as a training and collaboration space. It enables the company to showcase technologies and engage in discussions with clients and other organizations interested in warehouse and fulfillment automation solutions. Trew’s TEC started limited operations in July of 2023 and has already proven a valuable addition to the company’s portfolio. “The TEC enables us to engage in conversations about the challenges our clients face, opportunities to improve and rethink solutions, and the approaches we can take to win together with clients,” said Trew CEO, Alfred Rebello. The TEC is part of the outcomes of the previously announced R&D Grant from the state of Ohio’s private economic development corporation, JobsOhio: Trew (2023, January 4). Trew Investing in New Technology Center at Southwest Ohio Headquarters [Press release] “Our clients need innovations that fit their business and bring together process, technology, software, and people in a way that helps them thrive. The market is evolving quickly, and we are grateful for the state of Ohio’s economic assistance to accelerate our plans for this center,” continued Rebello. During the first six months of operation, the TEC has been used for application and accelerated product life cycle testing, with millions stress testing cycles. “In addition to collaborating on solutions, the TEC gives us the ability to harden technology and explore innovation ideas,” added Rebello. The TEC is open for client and industry visits. The company plans to continue expanding the TEC with emerging software and partner technologies.
U.S. Rail Traffic for the week ending February 24, 2024
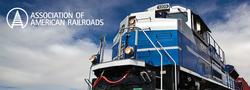
The Association of American Railroads (AAR) has reported U.S. rail traffic for the week ending February 24, 2024. For this week, total U.S. weekly rail traffic was 483,656 carloads and intermodal units, up 7.7 percent compared with the same week last year. Total carloads for the week ending February 24 were 224,251 carloads, up 2.6 percent compared with the same week in 2023, while U.S. weekly intermodal volume was 259,405 containers and trailers, up 12.6 percent compared to 2023. Seven of the 10 carload commodity groups posted an increase compared with the same week in 2023. They included chemicals, up 2,776 carloads, to 33,454; grain, up 2,470 carloads, to 21,698; and motor vehicles and parts, up 2,196 carloads, to 15,931. Commodity groups that posted decreases compared with the same week in 2023 were coal, down 2,561 carloads, to 61,556; nonmetallic minerals, down 1,968 carloads, to 27,533; and forest products, down 150 carloads, to 8,460. For the first eight weeks of 2024, U.S. railroads reported a cumulative volume of 1,690,310 carloads, down 4.6 percent from the same point last year; and 1,983,594 intermodal units, up 7.4 percent from last year. Total combined U.S. traffic for the first eight weeks of 2024 was 3,673,904 carloads and intermodal units, an increase of 1.5 percent compared to last year. North American rail volume for the week ending February 24, 2024, on 12 reporting U.S., Canadian, and Mexican railroads totaled 336,833 carloads, up 3.5 percent compared with the same week last year, and 341,906 intermodal units, up 10.8 percent compared with last year. Total combined weekly rail traffic in North America was 678,739 carloads and intermodal units, up 7.1 percent. North American rail volume for the first eight weeks of 2024 was 5,122,636 carloads and intermodal units, up 0.7 percent compared with 2023. Canadian railroads reported 94,066 carloads for the week, up 5.8 percent, and 69,511 intermodal units, up 4.3 percent compared with the same week in 2023. For the first eight weeks of 2024, Canadian railroads reported cumulative rail traffic volume of 1,233,049 carloads, containers and trailers, down 2.8 percent. Mexican railroads reported 18,516 carloads for the week, up 3.2 percent compared with the same week last year, and 12,990 intermodal units, up 14.0 percent. Cumulative volume on Mexican railroads for the first eight weeks of 2024 was 215,683 carloads and intermodal containers and trailers, up 6.8 percent from the same point last year. To view the weekly rail charts, click here.
New Age Industrial promotes Scott Schrum to Assistant National Sales Manager
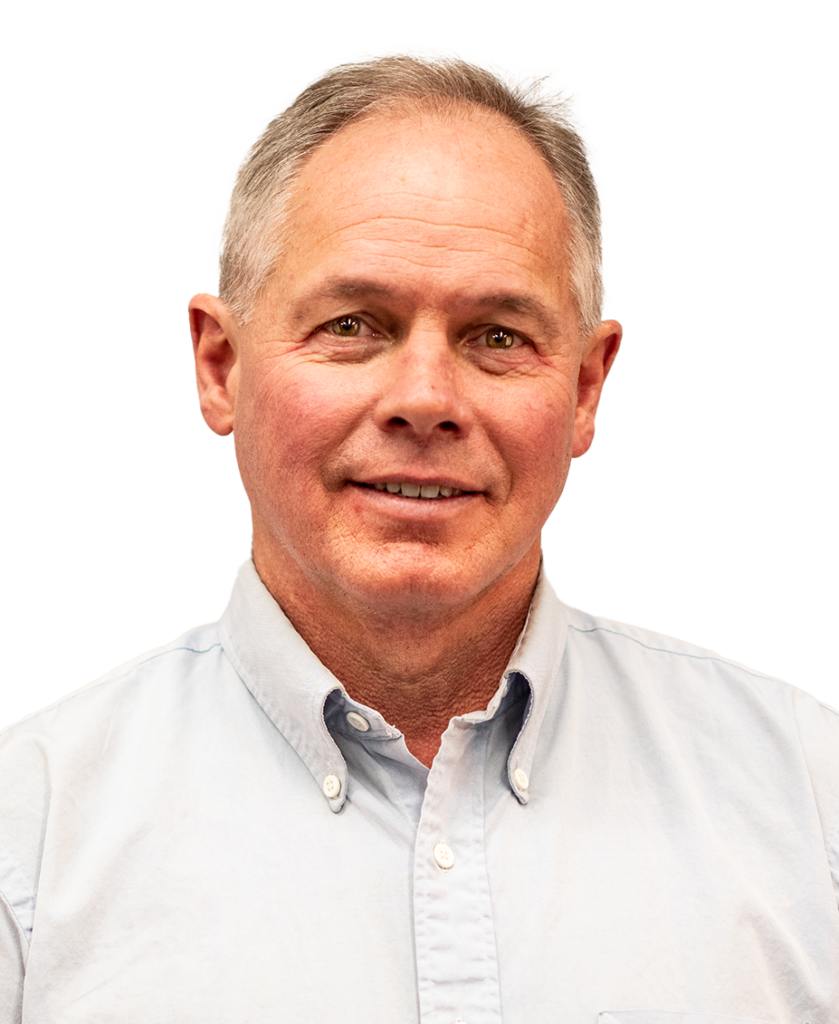
New Age Industrial has announced the promotion of Scott Schrum to Assistant National Sales Manager of the Material Handling Division. Scott is a driven business leader with over 30 years of success driving growth through effective sales and management strategies. He holds a Bachelor of Business Administration degree with a minor in Economics obtained from the University of Kansas. “With his deep commitment to customer focus, workplace safety, and efficiency, Scott truly embodies the core values of New Age Industrial,” said Tom Sharp, Vice President at New Age Industrial. “His ability to build strong, meaningful relationships will be crucial as we continue to expand our national presence. We’re thrilled to have him on the leadership team; his expertise in supply chain optimization and problem-solving skills will drive improvements throughout our operations and benefit our customers as well.” In his new position, Scott will collaborate with the New Age Industrial Sales and Marketing Teams, along with the manufacturer’s representatives, to secure existing business and generate new opportunities. Additionally, he will represent the company at key national trade shows alongside the Material Handling Team. Scott is eager to share his expertise in custom aluminum solutions and collaborate with manufacturers’ representatives, dealers, and consultants to optimize operations for their customers. Scott shared, “We have a unique opportunity to empower businesses by improving efficiency, safety, and overall operations through customized solutions.” Vice President, Tom Sharp said, “We congratulate Scott Schrum on his recent promotion to Assistant National Sales Manager. He will be instrumental in driving continued growth and success. We are confident that he will make significant contributions to the company and look forward to the future with him on board.”
Liberty Reach Inc. announces rebranding to Liberty Robotics Inc.

Liberty Reach Inc. rebrands as Liberty Robotics Inc. and adopts a new tagline, signaling a strategic shift towards advanced machine vision and robotic guidance technologies, with a continued commitment to automotive excellence and new ventures in warehousing and logistics. Liberty Reach Inc., a supplier of 3D volumetric vision guidance systems for robot applications, has announced the company has officially rebranded to Liberty Robotics Inc. This change aims to better represent the company’s increased focus on advancements in machine vision and robotic guidance technologies. Accompanied by a new tagline, ‘Machine Vision AI,’ the new name marks a strategic shift towards broader applications in robotics, beyond the company’s established base in the automotive sector. Liberty Robotics is a key player in providing robotic guidance solutions utilizing 3D vision volumetric sensors and proprietary software within the automotive industry, offering technologies for applications such as body sealing and material handling. With the rebranding, Liberty Robotics intends to maintain its presence in the automotive market while expanding into warehousing and logistics. “Our commitment to the automotive arena remains strong, yet we see significant opportunities in the warehouse and logistics sector,” says Bob Berry, President and CEO of Liberty Robotics Inc. “Our technologies are designed to advance automation across various fields and while our current focus is on optimizing goods packing and mixed-case pallet retrieval, this is just the beginning. We are setting our sights on extending applications to include container loading in the near future.” Liberty Robotics has adopted its new tagline and name to more accurately represent the company’s expertise, aligning with its core mission and highlighting its capabilities in machine vision and robotics. The company is nearing completion on the development of applications that aim to enhance robotic functionality, enabling more efficient task execution in warehousing and logistics environments, including palletizing and depalletizing operations.
Schreiner ProTech Supplies ESD-compatible, traceability-enabled labels for logistics robots at ifm
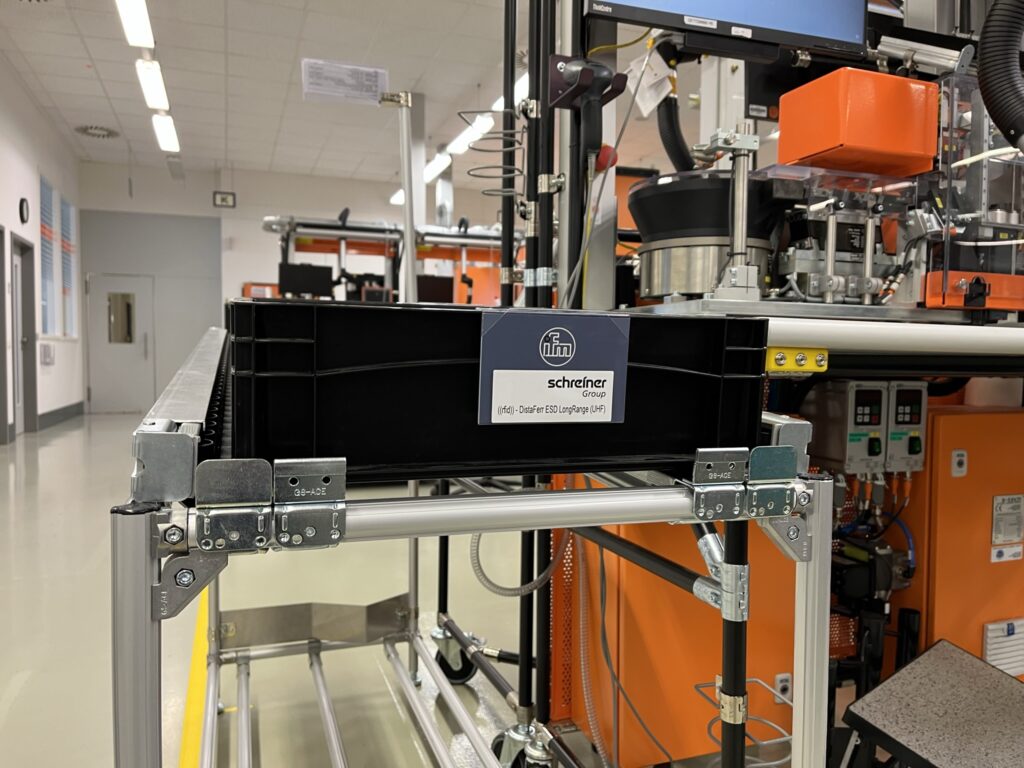
DistaFerr ESD long-range labels allow ifm’s team of driverless Automated Mobile Robots to find, deliver and digitally track all warehoused items. Schreiner ProTech has collaborated with electronics logistics provider ifm to develop a functional product marking system compatible with ifm’s team of retrieval robots. Schreiner ProTech’s ((rfid))-DistaFerr ESD LongRange Labels allow ifm’s crew of driverless Automated Mobile Robots (AMRs) to quickly and accurately find, deliver and digitally track products at its cavernous facility in Tettnang, Germany. For ifm, its Automated Mobile Robots must work efficiently when locating an item or finding its intended intra-facility destination. Each AMR travels approximately 30 kilometers per day, placing emphasis not only on finding and transporting the correct item, but doing so with the least possible lag time. At each stop, an AMR passes a special rack system – a type of gate – where the scheduled container can be dropped off and a new one picked up. Information on where and when to deliver an item is conveyed digitally, lending to optimal capacity utilization. Among the common challenges in such a setting are electrostatic discharge (ESD) containers, which have antistatic elements that adversely affect RFID functionality. Schreiner ProTech’s ((rfid))-DistaFerr ESD LongRange Labels are specially adapted to thrive even on ESD surfaces. For ifm, the result has been seamless interaction between marking, identification, and digitalization. The company is enjoying 99% delivery accuracy – especially impressive considering that its 155,000 customers worldwide generate around 1.3 million purchase orders per year. “It was crucial for all containers to be uniquely marked and automatically identifiable,” explains Ulrich Beller, Lean Manager for ifm. “The RFID labels were the key to this use case. As a result of now having combined two steps in one process we benefit from massive time savings and increase in efficiency.” “((rfid))-DistaFerr ESD LongRange is not exactly a niche product,” says Katharina Totev, Product Manager RFID at Schreiner ProTech, “but has been developed for a specific use case—that is for application to ESD materials. However, what makes this all-in-one solution unique is the combination of our marking and the Automated Mobile Robots from ifm.”
KION North America launches new electric forklift
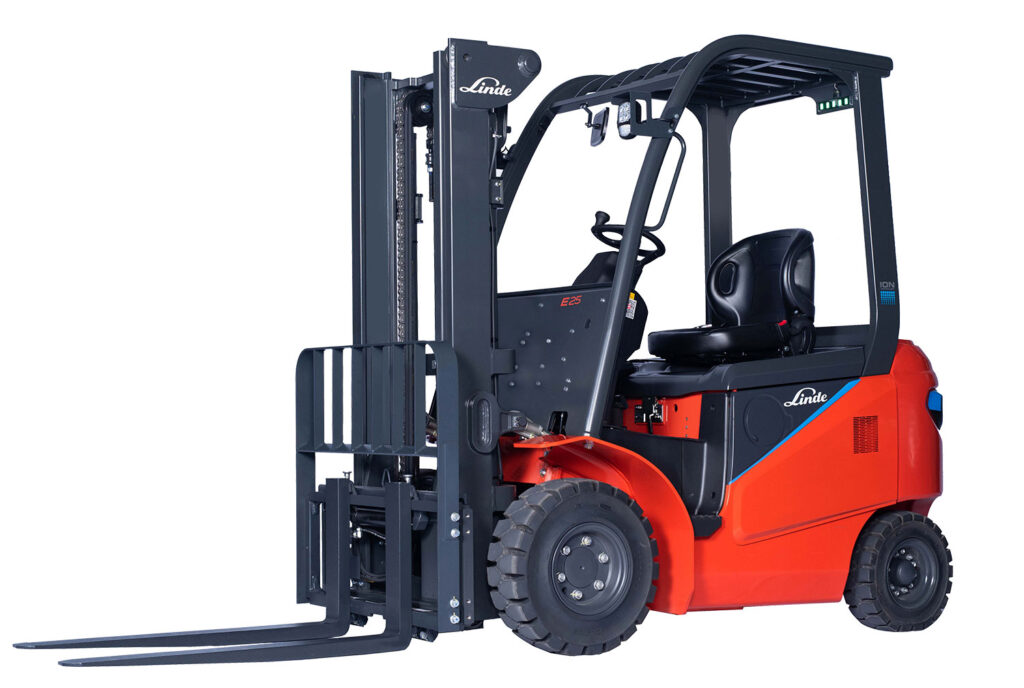
The Linde series 1293 KION North America makes another addition to its product portfolio of powered industrial lift trucks. The Linde Series 1293 includes models E20BHP and E25BHP, electric counterbalance forklifts with 4,000 – 5,000 lb. capacity, and both powered by Linde Li-ION batteries. The next generation of material handling equipment across the world includes power sources such as this, proving an important balance between sustainable energy and energy efficiency. That means businesses don’t skip a beat when adopting more environmentally conscious practices. Developing trucks for the future means more than equipping the truck with an electric energy source. Linde Material Handling takes it a step further by engineering these models to compete where electric counterbalance forklifts typically cannot. After rigorous international standards testing, the Linde Series 1293 stands together with traditional internal combustion forklifts in day-to-day outdoor applications. The water-resistant design opens the door to outdoor stacking, storage, and transport. Like other Linde counterbalance trucks, the E20BHP and E25BHP have an ultra-durable, one-piece steer axle which greatly improves durability while driving over bumpy and uneven terrain. “The Linde 1293 is adaptable to a wide range of applications and customer types,” said Jena-Christine Lawrence, Director of Product Management & Product Strategy. “The E20BHP and E25BHP are powered by Linde lithium-ion batteries, and combine sustainable power with exceptional performance, making these models the ideal choice for both indoor and outdoor applications. We are proud to deliver another solution to North America that not only meets the evolving needs of our customers but also contributes to a greener and more efficient future.” In addition to the benefits that the E20BHP and E25BHP provide to applications switching to electric, there are also important features that lend to an easier, more comfortable operator experience. These models are outfitted with our standard full suspension seat and easy-to-reach seat-side mast control levers to assist operators in comfortably and accurately maneuvering throughout their shift. The dashboard features a 4.5-inch color display which keeps the operator informed of truck functions such as speed, state of charge, and many more. Lastly, the 1293’s easy-to-access Li-ION battery charging port encourages the operator to make use of opportunity charging, which extends the battery life over longer or several shifts.
EnerSys® to premier latest NexSys® charger innovations at MODEX 2024
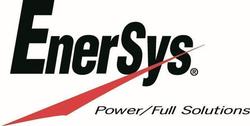
EnerSys® will premier its latest NexSys® charging innovations at MODEX 2024 – the NexSys® AIR wireless charger and the NexSys®+ Outdoor charger. Engineered for a wide range of Automated Guided Vehicles (AGVs), the new NexSys® AIR wireless charger offers a space-saving design to provide integration flexibility while eliminating mechanical charging connections and related maintenance. It also provides advanced safety features that help protect workers and equipment – giving facility operators and AGV Original Equipment Manufacturers (OEMs) an integrated, safe charging solution to optimize both efficiency and equipment autonomy. Designed to withstand the elements, the new NexSys®+ Outdoor charger provides the advanced performance and features of the NexSys®+ charger, protected by an IP54 rated enclosure for protection against dust, water, and seasonal temperatures. The NexSys®+ Outdoor charger is ideal for use at farms, airports, building material yards, rental facilities, ports, cargo terminals and other working environments exposed to the weather. Both the NexSys® AIR wireless charger and NexSys®+ Outdoor charger are compatible with all EnerSys® battery technologies, including traditional flooded lead-acid, Thin Plate Pure Lead (TPPL) and lithium-ion (Li-ion). “As material handling applications continue to migrate towards automation and electrification, EnerSys is committed to offering customers advanced charging systems, like the NexSys®AIR wireless charger and the NexSys®+ Outdoor charger to complement our proven battery technologies – including our advanced NexSys® line of maintenance-free batteries,” said Harold Vanasse, Senior Director of Marketing, Motive Power Global at EnerSys. “Our goal is to ensure fleet managers and OEMs have the broadest possible selection of motive power technologies to support their operations – including those that are automated or outdoors.” These next-generation chargers will be showcased at MODEX 2024 in EnerSys booth B8032 from March 11-14, 2024, at the Georgia World Congress Center in Atlanta, GA. Both chargers will also be displayed in EnerSys trade show stands at Intermodal (booth M010) in Sao Paulo, Brazil from March 5-7, 2024, and LogiMat (booth 10B09) in Stuttgart, Germany from March 19-21, 2024.
Mid America Paper Recycling will be at MODEX 2024
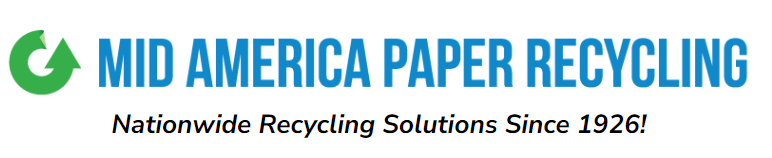
Mid America Paper Recycling, an independent brokers, processors, and exporters of recovered paper in the Central United Sates, will exhibit at MODEX 2024, March 11-14, at the Georgia World Congress Center in Atlanta, in booth B7054. Mid America will highlight its first-of-its-kind Waste Audit, an initiative focused on tracking and increasing the value of the recycling waste streams generated by logistics firms, commercial printers and paperboard converters. Hosted by The Material Handling Industry of America, the MODEX show/conference will feature advancements in supply chain solutions, materials handling equipment, services, technology and logistics and smart systems. “MODEX 2024 will allow us to educate our customers and attendees about the hidden benefits of their recyclable waste,” explains Don Gaines, CEO of Mid America Paper Recycling. “We plan to do the same with visitors to our booth and explain the tremendous value in adopting a continuous improvement plan for their waste streams.” Mid America works closely with many operations creating a customized, continuous improvement process that identifies where their waste is generated, establishes key collection procedures, and sets objectives that continually improve their waste stream’s revenue contribution to their business. “No other company offers as comprehensive and value-added a solution,” Gaines said. Mid America exhibit staff will be available to fully describe the recycling program, explain its many benefits, how it works, and illustrate why it is a key component for all types of companies, from small and newer businesses to the well-established Fortune 500. The innovative recycling management program helps producers build a scorecard process by benchmarking, monitoring, and continuously upgrading their recycling operations to help them achieve their sustainability goals and grow the financial worth of their waste. “Recyclable materials can be wasted, which doesn’t meet anyone’s environmental goals,” Gaines notes. “But we show companies how their waste can be a significant, value-added contributor to their profitability if professionally managed. We target hidden savings opportunities in an operation’s indirect costs using our innovative Waste Audit process. When we introduce and outline the Audit with plant operations personnel, it gets them thinking, triggering discussion and raising questions.” Mid America shows producers how they can grow the worth of the recyclable waste produced. Gaines says it is an important and detailed process that begins with how the waste is generated and where it flows through a plant, to how loads of the recyclable waste materials are shipped and how all of the steps within the recycling process can be improved to accrue more revenue per ton. Taking Mid America’s free Waste Audit Survey is the first step on the path to recycling improvement. Easy to use, the survey takes only 10 minutes to fill out, but is comprehensive in scope. Because manufacturing operations often create tons of waste each year, – ranging from pre-consumer, high-grade recyclable paper to production trim and paperboard – Mid America’s Audit Process can help these operations realize significant revenues. “Continuous Improvement is so important today in many areas of an operation,” Gaines said. “We designed the Audit to bring this same strategic process to a recycler’s current waste handling practices and build a smart program that continuously improves the worth of their waste.”
Big Lift LLC acquires ePicker LLC
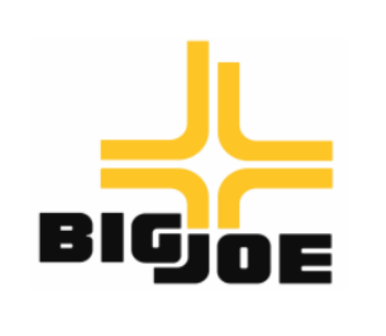
ePicker relaunched as EP to bring additional resources to growing dealer network Big Lift LLC has announced that it completed the acquisition of ePicker LLC, a fast-growing material handling equipment provider based in Fort Worth, Texas. Since its launch in 2021, ePicker has built an impressive network of industry-leading material handling distributors that market its portfolio of electric pallet jacks, stackers, access vehicles, and lithium-ion-powered forklifts to customers across North America. Big Lift is the North American subsidiary of EP Equipment, one of the fastest-growing and most innovative material handling equipment companies in the world. EP Equipment specializes in designing and manufacturing lithium-powered forklifts, warehouse equipment, and autonomous material handling solutions. Big Lift currently distributes Big Joe Forklifts, a North American material handling brand founded in 1951, which is well known for its innovative products and exemplary aftermarket support. Big Joe pioneered the Class III “walk-behind” lift truck market segment and continues to have the broadest portfolio of powered walk-behind lift trucks in North America. Following its acquisition of ePicker, Big Lift will re-brand ePicker as EP to capitalize on its parent company’s strong global brand reputation. The North American EP brand will utilize the former ePicker leadership team that joined the company through the acquisition. The Big Joe and EP brands will be distributed through their current sales channels while focusing on different product segments. The Big Joe channel will continue to focus on innovative niche products and in-between-handling applications while the EP channel will primarily focus on “purpose-built” lithium-ion forklifts. Both brands will offer market-leading autonomous solutions. “This acquisition is an important part of Big Lift’s strategy to become the market leader in lithium-powered material handling solutions and, specifically, the industry leader in lithium forklifts in North America. The addition of the ePicker team and ePicker forklift distributors will benefit both channels as it will enable Big Lift to dramatically increase our resource base, significantly strengthen our aftermarket support capabilities, and ensure we continue to launch high-quality, innovative products,” said Dan Rosskamm, President of Big Lift. “Building off the success of ePicker, EP North America will hit the ground running, bringing best-in-class lithium-powered forklifts to retailers, warehouses and DCs,” said Jason Bratton, General Manager for EP North America. “As demand for new energy forklifts is increasing, I am excited to be part of a larger global team that shares the vision of what North America needs for material handling solutions.” EP North America is based in Fort Worth, Texas and offers a range of material handling solutions from lithium-ion Class 1 forklifts to lithium battery solutions, stackers, pallet jacks and access vehicles. EP brings specialized products to the North American market to maximize efficiency in various applications and environments. As part of Big Lift, EP North America will have additional resources available to its dealer network as well as the end-user, including increased engineering capabilities, marketing support, customer service, aftermarket parts and warranty support.
Asking the right questions
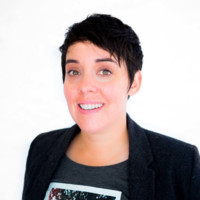
We ask questions all the time. At work, at home, amongst friends. Often, we ask questions that we already know the answer to, and other times, we ask questions that validate our existing perceptions. But in business, when we’re trying to find answers to complex, layered, multi-faceted problems, we need excellent questions to get the answers and insights we need to make the best decision possible. But we’re usually pretty bad at it. For example, I sat in on a discussion between a CEO and the VP of Sales at a large product company. Sales were flat to plan. The CEO wanted to know why sales were flat and wanted to know how they would reach their 10% revenue growth goal that year. The CEO began with the usual questions – “Why are sales flat?” and “What will it take to reach our growth goal?”. The VP of Sales had the following responses, “We had two territories that missed their targets, and two others that surpassed their goals, making sales flat. But we will reach our growth goal by working more closely with the two lagging territories and get them back to the right trajectory.” This conversation, while appeasing the CEO and making the VP of Sales feel like there was a clear “plan” in place, there is no plan. This is because the right questions weren’t asked. What insight does either party have as to the why? What is the CEO learning that will help them make better decisions going forward? No one is really steering the ship, just riding the waves that already exist. More often than not in this scenario, the high-performing territories will continue to grow, making up the difference of the laggards, and the 10% growth goal will be met. The weak territories will be reshuffled, or those folks will be replaced with a fresh new set of sales personnel. The issue with this is that there’s no transparency to the actual problem. The right questions weren’t asked. Take a different example – say you want to develop a new offering to increase revenue. Do you go and ask customers, “What do you want and need that we don’t offer?” and then simply go and do those things? Do you just pick the things that were within your budget to implement? What happens when revenue doesn’t meet expectations? Because you only asked a surface question and then went directly to implementation, there’s no insight as to why it didn’t work. There’s no insight on what to change, do differently, or eliminate, because you didn’t ask the right questions. Furthermore, not asking the right questions gives you the same answers your competitors are getting. You need to ask deeper, smarter, better questions than the competition to get new and unique insights that drive differentiation, revenue growth, and organizational insight. Asking the same questions as everyone else will get you the same answers as everyone else. To ask the right questions, you need to first identify what you’re trying to understand. This means in both of our examples, what is the real question you have that you want answered? For our CEO and VP of Sales, it’s not “Why are sales flat” but “What issues are impacting the success of our sales team?” For our new offering, the question for customers isn’t “What do you need that we don’t offer” but “What problems do you have that aren’t getting addressed?” The difference is exploratory – opening the door for more opportunities for different insights and perspectives. You want to ask questions that generate further, deeper clarifying questions. You want to ask questions that help you gain new perspectives you hadn’t considered before. You want to ask questions that help you gain insights you can take direct action on and make a clear, measurable business decision. Think about a 4-year-old, who asks relentless questions. They always dig into the “why”. There’s nothing wrong with finding out the why behind things. Utilize curiosity and drive for deeper understanding to create a questioning dialogue. This will help you not only ask the right questions and gain better information for decision-making but also set an example for your team on how to ask the right questions themselves. About the Author Andrea Belk Olson is a keynote speaker, author, differentiation strategist, behavioral scientist, and customer-centricity expert. As the CEO of Pragmadik, she helps organizations of all sizes, from small businesses to Fortune 500, and has served as an outside consultant for EY and McKinsey. Andrea is the author of three books, including her most recent, What To Ask: How To Learn What Customers Need but Don’t Tell You, released in June 2022. She is a 4-time ADDY® award winner and host of the popular Customer Mission podcast. Her thoughts have been continually featured in news sources such as Chief Executive Magazine, Entrepreneur Magazine, Harvard Business Review, Rotman Magazine, World Economic Forum, and more. Andrea is a sought-after speaker at conferences and corporate events throughout the world. She is a visiting lecturer and startup coach at the University of Iowa, a TEDx presenter, and TEDx speaker coach. She is also an instructor at the University of Iowa Venture School. More information is also available on www.pragmadik.com and www.andreabelkolson.com.
Flux Power appoints Kevin Royal as Chief Financial Officer
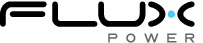
Veteran Financial Leader to Fortune 500 Technology Companies to Lead Next Phase of Company Growth Flux Power Holdings, Inc., a developer of advanced lithium-ion energy storage solutions for electrification of commercial and industrial equipment, has announced the appointment of Kevin Royal, CPA, a seasoned finance and accounting executive, as Chief Financial Officer of the Company, replacing Chuck Scheiwe as part of a planned transition given the Company’s strong financial performance and inflection point. Scheiwe will remain with Flux Power in a consulting role for the near term to help facilitate the transition. Kevin Royal brings over 20 years of experience as a Chief Financial Officer for four publicly traded companies, with oversight of Finance, Accounting, IT, HR, Legal, Investor Relations, and M&A. He has a history of demonstrated achievements contributing to superior corporate performance through expert alignment of financial initiatives and operational goals with organizational objectives. Before joining Flux Power, Kevin was Executive Vice President and CFO for Zovio Inc. (formerly Bridgepoint Education) where he led vision, strategy, and execution for all facets of corporate finance and accounting. Previously he was Senior Vice President and CFO of Maxwell Technologies, a publicly traded developer and manufacturer of energy storage and power delivery products for automotive, heavy transportation, renewable energy, wireless communications, and industrial and consumer electronics applications. There he introduced product cost reduction and pricing controls that substantially increased gross profit margins from the sale of the company’s energy storage, power delivery, and radiation-mitigated microelectronic products. He also served as CFO at Blue Coat Systems and Novellus Systems. Kevin holds a Bachelor of Business Administration in accounting, from Harding University and is a Certified Public Accountant. As Chief Financial Officer of Flux Power, Royal will provide financial leadership to assist in building on the Company’s goal of delivering value to its shareholders by implementing short, medium, and long-range financial planning, budget development, risk management, corporate strategic development, system implementation, process improvement, regulatory compliance reporting, financial reporting for management, internal controls and tax advice. “On behalf of our board and management team, I would like to welcome Kevin as our Chief Financial Officer, and we are privileged to have someone of his caliber and financial skill set serve as our CFO,” said Ron Dutt, Flux Power Chief Executive Officer. “I would like to thank Chuck for successfully leading the finance team and for his contribution in helping move Flux Power to this inflection point. We now look forward to leveraging Kevin’s expertise in energy storage and power delivery products. His achievements as well as expertise in financial management of listed companies will make a significant contribution to the strategic operation and development of our company going forward.” Royal added, “I am excited to be appointed as CFO as we prepare Flux Power for the future with a pipeline of orders and new customer opportunities that combined with cash profitability improvement initiatives, is leading the company toward near-term profitability. I look forward to working with Ron, the senior leadership team, and our finance team as we continue to execute our strategic and financial priorities and our commitments to all shareholders.”
Orbital Wrapper Manufacturer introduces dual dispensing on fully automated wrapping system
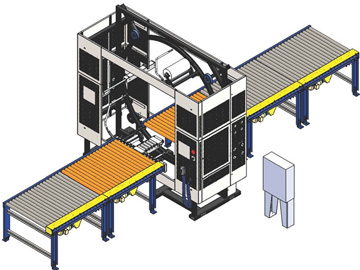
TAB Wrapper Tornado Perfect Storm applies two stretch wrap rolls at the same time Orbital wrapper manufacturer TAB Industries, LLC, has introduced a dual roll dispensing system on its fully automated TAB Wrapper Tornado Perfect Storm wrapping systems. Offered as an option, the dual dispensing system sets two stretch wrap roll dispensers on the wrapping ring instead of one to apply the plastic film from two rolls at the same time, doubling the speed of the application. In tandem with dual, companion automated cut and wrap devices that cut the ends of both stretch wrap rolls after wrapping, the dual dispensing Perfect Storm automatically stretch wraps pallet loads in as little as seven seconds, based on a standard 48” x 48” pallet. Featuring the company’s patented orbital wrapping technology, the dual dispensing TAB Wrapper Tornado Perfect Storm automatically senses the presence of a pallet load ready for wrapping on its infeed conveyor determines the ideal number of wraps and then feeds, stretches wraps, and discharges the pallet load as a stable, unitized load ready for delivery, staging, or storage. The entire, automated pallet wrapping process may be performed by a single lift truck operator. The TAB Wrapper Tornado Perfect Storm with dual roll dispensers is designed and manufactured in the company’s Reading, Pennsylvania headquarters. The automated wrapping systems are custom-engineered for each installation and delivered with a full warranty.
BBI expands nation-wide field sales team
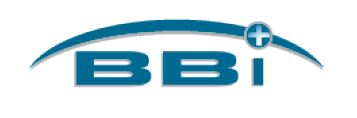
Battery Builders is excited to announce several new additions to our Field Sales team: Trey Hitson, Director of Sales Trey joined the BBI team in April 2023 and brings a wealth of knowledge from his over 15 years of experience in the Industrial Motive Power industry. When asked about the motivation behind transitioning to the BBI team, he responded, “I have always known the product was top tier from my days selling against them at the beginning of my career. After conversations with the new executive leadership team, I was excited to embrace their vision and recognize the opportunity to expand this business. I am grateful to be entrusted with this responsibility.” Trey currently lives in Maryville, TN, with his wife Crista, 4-year-old daughter Willow Grace, 3 dogs (Buddy, Chippy, & Kirby), and Willow’s American Quarter Horse (Charlotte). Mark Rigor, Regional Sales Manager Mark joined the BBI team in September of 2023. Previously working at Raymond, Power Designers, and Bulldog Batery, Mark has been in the material handling industry for over 22 years. Currently living in Yorba Linda, CA with his wife (Judy), Mark says he was excited to join BBI “because of the exponential growth opportunities and BBI’s reputation for making a quality product”. He shares a lot of excitement about his only daughter (Lisa) who is a Bio-Surgical Specialist in Las Vegas, CA. Andy Trout, Regional Sales Manager Andy joined BBI in August of 2023 and came to us with over 10 years of experience in the battery industry. Before Battery Builders, Andy served as the Customer Support and Sales representative at Complete Power Systems, an independent battery dealer in TN. Earlier this year, Andy relocated from Nashville and accepted the position to head the Mid-East sales region for BBI, sharing it was “a great opportunity to further [his] experience in the material handling world.” Andy now lives in Cincinnati with his fiancée, two cats (Waffles and Olive), and their senior dog (Jack). Led by the direction of John Gaughan, VP of Sales, the creation of our Field Sales team allows BBI to expand our nationwide support to assist in the sales and service of your motive power applications.
Haver & Boecker Niagara appoints new Marketing Director and Marketing Coordinator
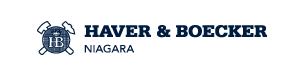
Company Expands Global Marketing Organization with Strategic Appointments Haver & Boecker Niagara, a provider of screening, pelletizing, and mineral processing plants and systems for the mining, aggregate, and industrial mineral industries, has announced the appointment of Julie Andras as director of marketing and Julie Alguire as marketing coordinator. Andras brings more than 30 years of marketing experience to the director role, including 11 years in the mineral processing industry. Prior to joining Haver & Boecker Niagara, she led the global marketing initiatives for a large international equipment manufacturer. Stepping into her new role, Andras brings a wealth of industry experience that equips her to understand the unique challenges and opportunities of Haver and Boecker Niagara’s customers. Her responsibilities will entail developing and delivering the company’s strategic marketing initiatives globally. “Haver & Boecker Niagara has a longstanding reputation for delivering high-quality, innovative solutions to customers,” Andras said. “I am thrilled to work with a team of talented professionals to build on this legacy. There are so many opportunities to partner with our customers and contribute to their success. This is going to be an amazing journey.” Alguire will lend her expertise to the company’s sales and marketing initiatives in North America and Australia. As marketing coordinator, she will also work in conjunction with Haver & Boecker Niagara’s global marketing network to build brand recognition and foster continued growth. Prior to joining Haver & Boecker Niagara, Alguire worked at a leading Canadian publishing company where she oversaw global marketing initiatives for nearly 30 years. Her science and environmental studies background uniquely equips her to inform and educate customers about the company’s services and solutions. “I’m eager to work with the team to advance the success of Haver & Boecker Niagara while finding new ways to serve our customers,” said Alguire. “My primary objective is to assist in the long-term development of marketing strategies that will allow them to make the best decisions for their operations.” Karen Thompson, the president of Haver & Boecker Niagara’s North American and Australian operations, emphasized that these new hires will enable the company to educate the market on strategies that strengthen productivity and increase profits. “These appointments represent the addition of a phenomenal asset to our organization,” Thompson said. “Both Julie Andras and Julie Alguire bring unique areas of expertise that will help us deepen relationships with our customers and continue to grow their business, and ours, globally.”
Link improves popular LB20 ramp family
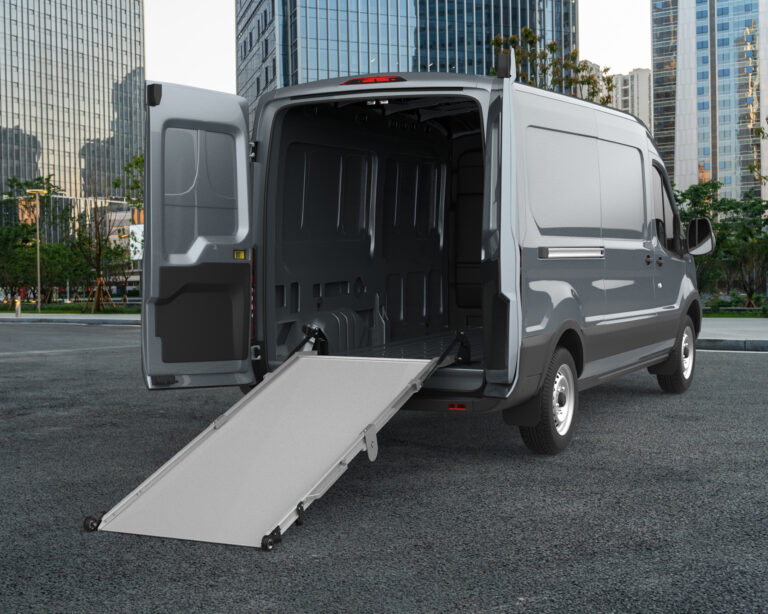
Link’s family of LB20 ramps are now 25 pounds lighter, feature pull-style, gas-spring-assist lifting mechanisms, stow at an 8-inch vertical depth, ship fully assembled and are even easier to install than previous models. Link Mfg., Ltd., a U.S. manufacturer of lightweight folding aluminum ramps, announced the introduction of its newly redesigned LB20 family of ramps today. One of nine models of the LB20 will be on display to the industry for the first time during NTEA Work Truck Week 2024, March 5–8, 2024, in Link’s booth 4619. Link’s family of LB20 ramps has been reengineered to significantly improve installation time, operational functionality, and the end-user experience. Seven of the nine ramps now each feature two pull-style, gas-spring-assist lifting mechanisms. The gas-spring devices are lighter weight, leading primarily to the ramps’ 25-pound weight savings and providing greater lift assistance, meaning less exertion and lifting force required by users. “With their new gas-spring-assist feature, Link’s LB20 ramps are now even easier to deploy and stow, making them ideal for vehicles that use their ramps with greater frequency,” said Lynn Blake, senior account manager for Link Mfg. “And with older individuals and females making up an ever-increasing percentage of the workforce, the reduced lifting effort and increased ease of use will be greatly appreciated.” Fitted with their slimmer gas springs, the re-engineered LB20s provide significantly greater clearance and less interference with steps and with both standard and extended bumpers. The ramps now feature a lower-profile transition threshold at their top, making it easier and smoother for dollies and other wheeled equipment to enter and exit the vehicle. When stowed, the ramps have a narrow, less than 8-inch silhouette, providing 34 percent more valuable room in the cargo area. “When in their upright, vertical folded position, the redesigned ramps now take up less than 8 inches of horizontal space just inside the door,” Blake said. “Now our ramps can be mounted even closer to the doors and can be quickly accessed, opened and then closed again and out of the way in seconds. And unlike hydraulic liftgates and small electric cranes, Link ramps require no training to operate, enabling workers to start using them immediately after installation.” The LB20’s new base plate has also been reduced to 11 inches in depth and now features a larger mounting pattern to accommodate more mounting holes and fastener sizes, making installation even easier for upfitters. Link LB20 ramps will now have consolidated part numbers and will ship fully assembled with attached base plate, wheels, and gas springs on the applicable seven models. Customers will continue to experience the industry’s lead times with fully assembled LB20 ramp units. Link is also happy to drop ship ramps on a just-in-time basis through a Link-certified dealer. Link ramps are designed to meet a wide variety of uses, with dimensions ranging from 24 to 47 inches in width, comfortably accommodating standard hand trucks and other cargo conveyance and wheeled equipment. Link’s bifold ramp lengths vary from 72 to 135 inches, and extended LT30 ramp models reach 119 inches and feature adjustable support mechanisms for added stability. A 42-inch by 108-inch version of the LB20 ramp is also available, catering to an array of applications. The 42-inch-wide ramp is perfect for fleets and vehicles serving the last-mile delivery segment that don’t have to deploy ramps at every stop, because it leaves enough room for door entrance and egress without being unfolded. Seven of the nine LB20 models will be available with the spring-assist feature, and the two smaller and lighter of the nine ramps will come without it. All models will now also come with Link’s wheel kit as a standard feature, which will allow the ramps to deploy and retract on a wide variety of surface angles and materials more smoothly. LB20 ramps are and have always been designed for reliability and durability, using extruded high-strength aluminum. The extensive line of nine LB20 sizes provides an option for virtually any application. “Link ramps are designed to be so robust, our upfitter customers tell us that they often outlast more than one vehicle,” said Blake. “Whereas liftgates and cranes can drain vehicle batteries, they also require significantly more maintenance and cost between two and four times more to purchase and install than a ramp, making ramps far more practical.” Link LB20 ramps will be commercially available in the second quarter of 2024. The new ramps will ship in the form of a fully assembled unit. The LB20 ramp can be ordered through Link’s nationwide network of ramp dealers.
Emerson’s new compact, rugged PC built to connect industrial floor to Cloud
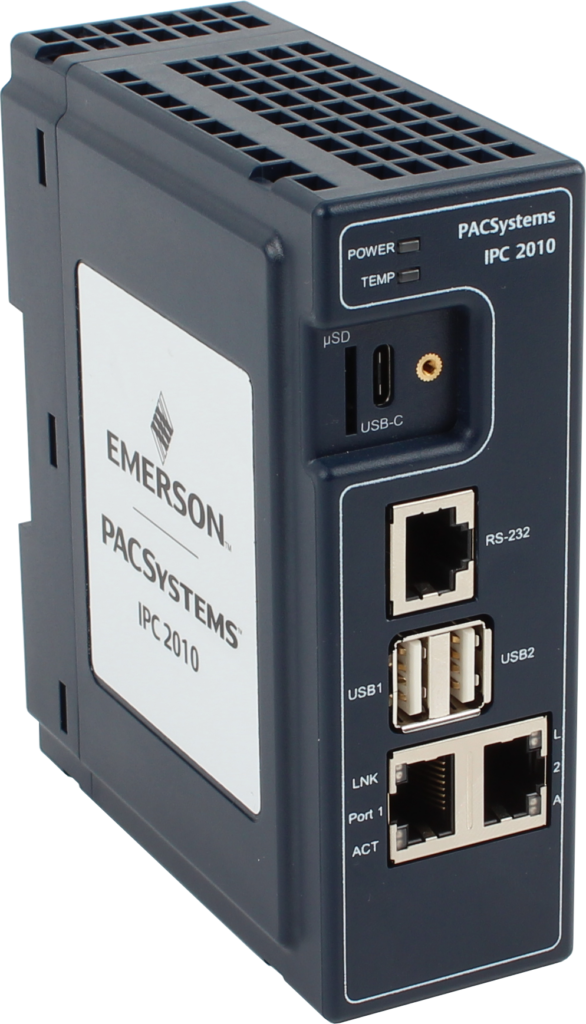
PACSystems IPC 2010, pre-loaded with Movicon software and PACEdge IIoT platform, delivers high-performance computing for industrial edge data visualization applications Emerson has announced the new PACSystems™ IPC 2010 Compact Industrial PC (IPC), a rugged industrial computer designed to handle a wide range of machine and discrete part manufacturing automation applications. The new solution is designed to serve manufacturing sites and OEM machine builders who need a ruggedized, compact, durable IPC to cost-effectively support their Industrial Internet of Things (IIoT) and other digital transformation initiatives. The IPC 2010 addresses this by pre-loading the PACEdge™ industrial edge platform and elements of Movicon.NExT™ SCADA software, helping users run applications quickly using browser-based configuration. Provisions are included for keeping the software platform current and passively maintained, minimizing user effort, while maximizing reliability. Running an industrial version of Linux, and including serial and Ethernet connectivity, the IPC 2010 can be used as a communications gateway in a variety of topologies, and simultaneously or separately as an edge computing device. Users can implement the IPC 2010 as a flexible protocol converter—and for many other computing functions—in many IIoT, edge, OT/IT convergence, HMI visualization, SCADA connectivity, and digital transformation roles. Both the hardware and software are designed to be adaptable, universal, and scalable, providing a standardized and unified user experience that is easy to use, powerful, and supported by Emerson’s lifecycle services. The compact form factor IPC 2010 features the widest operating temperature range of any passively cooled IPC, with a low power consumption of just four watts, and tough packaging so it can be installed virtually anywhere. The IPC 2010 offers an advantageous price/performance ratio, with no ongoing annual licensing costs, or charges for general and cybersecurity updates. Additional features, such as Movicon Connext© or WebHMI, can be activated or added at any time. “Many customers undergoing a digital transformation want to start small and earn trust as they seek out value from edge-enabled applications,” said William Paczkowski, product manager for the IPC 2010 for Emerson’s discrete automation business. “The IPC 2010 is specifically designed as a pre-packaged and economical solution so they can get running quickly and cost effectively.” Emerson is already building the IPC 2010 into a range of larger offerings for leak detection, compressed air monitoring, batching systems, cloud enablement services, and other packaged solutions. This flexible industrial technology will enable customers of all types to benefit from their advanced capabilities.
Bobcat announced lineup of new products
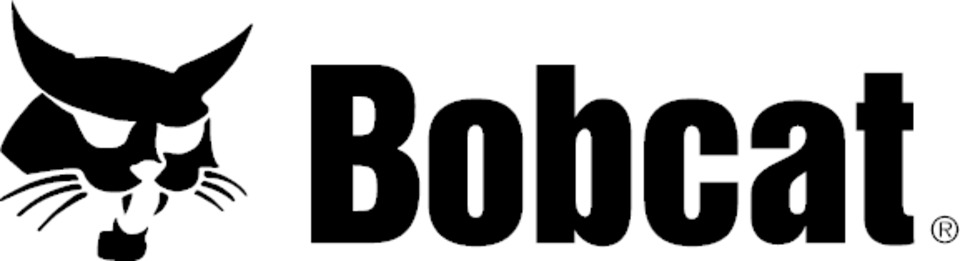
Bobcat Company, an equipment, innovation, and worksite solutions brand, has expanded its product portfolio with the introduction of forklifts; industrial air compressors; turf renovation equipment; and portable power products including air compressors, generators, and light towers. “Through our unwavering commitment to innovation and excellence, we have significantly broadened our product portfolio to not only meet the needs of our loyal customers but also to inspire and empower new customers to conquer their toughest job site challenges,” said Scott Park, CEO and vice chairman of Doosan Bobcat Inc. “With an expanded range of solutions, we’re empowering even more customers to accomplish more.” These products are now available at select Bobcat dealerships throughout North America. Last year, Bobcat announced Doosan Industrial Vehicle, Doosan Portable Power, Doosan Industrial Air, and RYAN turf renovation products would change to the Bobcat brand as part of the organization’s global brand strategy. All product lines have officially rebranded under Bobcat in North America with transitions on these product lines also happening globally in applicable markets. Customers can now purchase these Bobcat branded products, which includes: Forklifts: Internal combustion cushion and pneumatic tire forklifts, electric counterbalance forklifts, narrow aisle forklifts, pallet trucks/stacker forklifts, and warehouse vehicles. Industrial air: Industrial air compressors ranging from 30- to 200-hp, with both fixed and variable speed offerings. Turf renovation equipment: Aerators, sod cutters, dethatchers, overseeders, and other specialty products that serve landscaping and grounds care professionals across a variety of industries including golf, sports turf, landscaping, and rental. Portable power: Air compressors ranging from 185 to 1600 CFM, mobile generators ranging from 25 to 570 kVA, and light towers with runtime up to 105 hours.
Hargrove Controls & Automation’s Chet Barton, P.E. awarded Functional Safety Expert Certificate
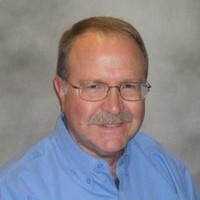
Process Safety Industry Leader Chet Barton, P.E. of Hargrove Controls & Automation achieves a prestigious Functional Safety (FS) Expert Certificate from TÜV Rheinland, joining an elite group of professionals globally. Hargrove Controls & Automation, a leading industrial automation system integrator and a subsidiary of global EPC firm Hargrove Engineers & Constructors, has announced that Process Safety Leader Chet Barton has been awarded the highest level of certificate from TÜV Rheinland, a Functional Safety Expert Certification. This designation is only available to professionals who meet TÜV Rheinland’s top global standards to be able to call themselves a process safety expert. Barton has been certified as an FS Engineer with TÜV Rheinland since 2010. After gaining years of experience, submitting the required documentation, and fulfilling all requirements such as participating in standard committees, submitting technical papers, presenting at technical symposiums, and obtaining two letters of recommendation, Barton has now achieved the FS Expert (TÜV Rheinland) certificate in Safety Instrumented Systems. “I am deeply honored to receive the FS Expert certificate from TÜV Rheinland, the most recognized testing service provider in the world in the Process Safety field,” said Barton. “This marks a significant milestone in my career; I leveraged my years of experience, community involvement, and dedication to educating others for this achievement. I am committed to mentoring and guiding others in the crucial practice of enhancing facility safety. This certificate represents the next step in my journey, allowing me to contribute more effectively to our shared goal of a safer industry. For me, this achievement is more than just a personal accomplishment; it’s a commitment to making a real difference in the world.” “We are incredibly proud of Chet’s achievement,” expressed Karen Griffin, Vice President of Hargrove Controls & Automation. “This prestigious certificate is a testament to Chet’s dedication, expertise, and his unwavering commitment to safety in the industrial automation sector. His accomplishment not only elevates his professional stature but also reinforces Hargrove’s commitment to maintaining the highest standards of safety and technical excellence.” You can learn more about Barton’s safety expertise and knowledge in Hargrove Controls & Automation Insights. The TÜV Rheinland Functional Safety & Cybersecurity Training Program, established in 2004 in collaboration with multinational enterprises, has played a pivotal role in the professional development of engineers and technicians over the past 20 years. It stands out as the only global vocational training program that encompasses both Functional Safety and Cybersecurity (FS & CySec) with its content and competencies validated by a neutral third party. Over 30 international companies and their experts back the FS & CySec Training Program, ensuring the highest quality of training. To date, the program has had more than 18,000 engineers participate, each of whom has earned the globally acknowledged FS Engineer (TÜV Rheinland) certification, marking a significant contribution to the field of industrial safety and security.
Kardex FulfillX for AutoStore at MODEX 2024
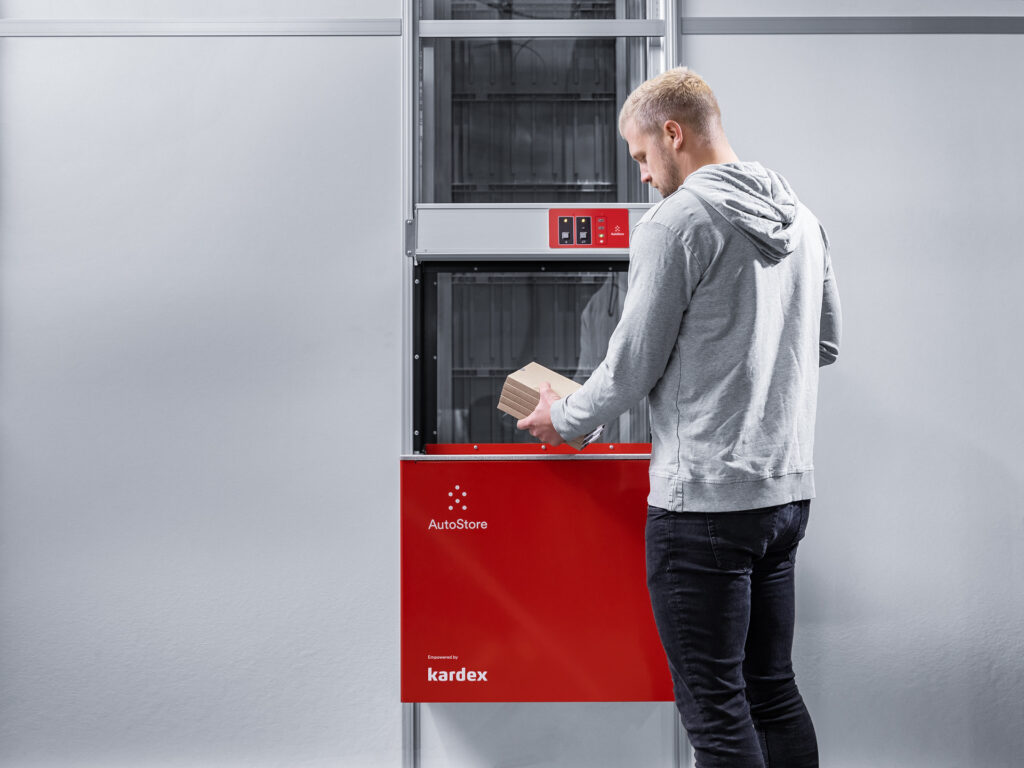
Kardex, a manufacturer of automated storage and retrieval systems (ASRS), is presenting Kardex FulfillX, an innovative warehouse execution system designed specifically for AutoStore empowered by Kardex systems, at MODEX 2024. Kardex FulfillX takes the surprises out of go-live and allows new AutoStore systems to ramp up faster and meet or exceed business cases in as little as 6 months. Showcasing its latest developments in automation software, MODEX visitors will experience a new way to maximize automation and robotics potential in Atlanta, March 11 – 14, in booth B6410. In addition to new developments in warehouse software, visitors will also be able to experience live demonstrations of Kardex’s Intuitive Pick Assistant which projects relevant picking information directly onto the surface of the access opening for both Kardex Remstar and AutoStore ports. This user-friendly picking display responds to movements and enables ergonomic, fast, and error-free picking. Kardex will present two live on-floor seminars and hold a media event during the exhibition: ‘Maximizing Space & Optimizing Labor: Transforming Your Warehouse with ASRS Automation’ on Tuesday, March 12 at 11:15 AM – 12:00 PM in Theater F ‘Transformational Robotics and Software: How AutoStore Empowered by Kardex Helped Cutter & Buck Reinvent Their Omnichannel Business’ on Wednesday, March 13 at 11:15 AM – 12:00 PM in Theater D A media event presenting FulfillX to members of the press on Tuesday, March 12 at 10 – 10:30 AM in the MODEX Press Conference Room, Building B, Level 2, Room B217
IDEC 7” combined PLC+HMI increases display size and I/O options
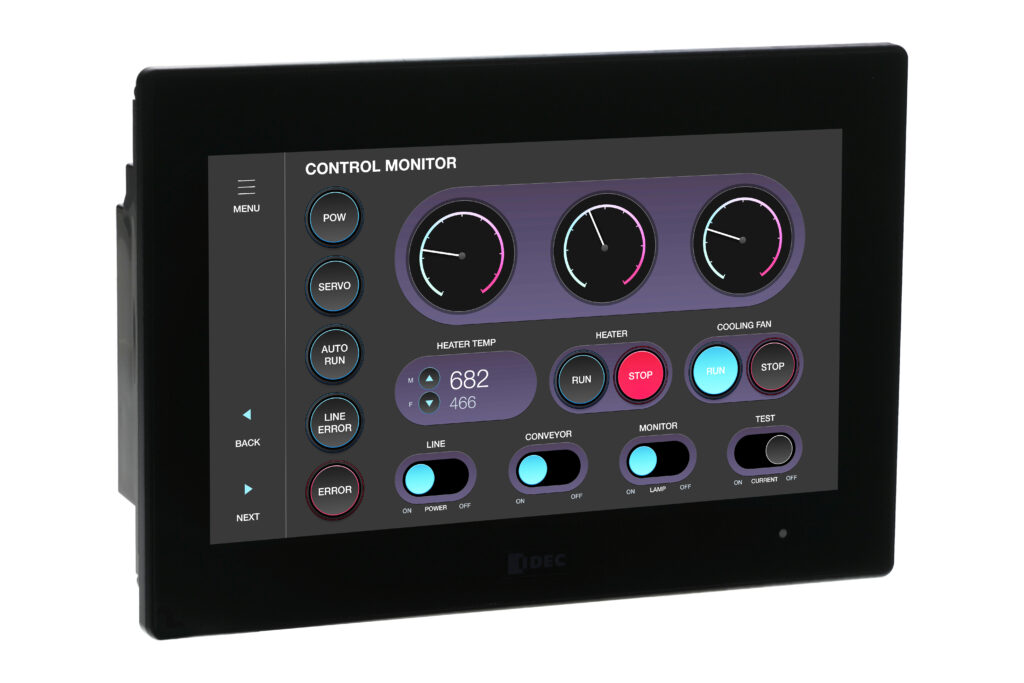
A large 7” vivid multi-touch display, with an integrated controller and expandable I/O, enables the new FT2J Series PLC+HMI to handle more applications than ever before. IDEC Corporation has expanded its SmartAXIS touch family with the new FT2J Series combined PLC+HMI. A compact all-in-one form factor combines built-in full-function controller features and functions, both onboard and expandable I/O, and an advanced technology 7” touchscreen display, providing many advantages for a wide variety of industries. Compact, simple, and streamlined An all-in-one PLC+HMI is compact and consumes far less panel space than separate units. Because the PLC and HMI are internally connected, require only one power supply, and share the same network connection, installation is simplified. The FT2J is ready to use and communicate right out of the box, and end users perform configuration with an intuitive and easy-to-use integrated development environment for both PLC and HMI functions, cutting configuration and programming time. Powerful PLC features The integrated PLC and HMI each have their own dedicated CPU and user memory for optimized scan time performance, and they communicate natively with each other. Built-in I/O includes 14 points of DC discrete inputs (5 of them configurable as high-speed counters), and 4 points of analog inputs (configurable as 0-10VDC or 4-20mA). A relay version provides 8 points of relay outputs, while transistor versions provide 6 points sinking or 6 points sourcing of discrete outputs (4 of them configurable as pulse outputs) and 2 points of 0-10VDC or 4-20mA analog outputs. The FT2J supports up to two expansion cartridges of discrete or analog I/O, with several options offered including a 2-point RTD/thermocouple analog input version. All analog inputs and outputs are 12-bit resolution. Industrial-grade HMI design The HMI’s projected capacitive touch panel (PCAP) advanced technology—similar to what is used for smartphones and tablets—saves space and improves performance. Besides being water- and scratch-resistant, PCAP is responsive and provides a high tolerance to resist false signals when dirt or water droplets are present on the face of the HMI. Fewer layers and better light transmission ratings mean less backlight power is needed, and the display provides an industry-leading 500 cd/m² brightness level and 50,000-hour backlight life. A small bezel provides the greatest possible display area compared with the installation footprint, and the entire package requires only a shallow mounting depth clearance. In addition to being multi-touch, users can interact with the touch HMI while using thin gloves. Durable performance The glass-top design is wear-resistant and delivers a long life, even in harsh environments. A battery-free design using a hyper-capacitor, and a long 50,000-hour rated backlight life, make these units low maintenance. Ratings for extreme temperatures from -20 to 55˚C, IP66 and IP67 for wash-down areas, IP66F and IP67F for oil resistance, UL60101, UL Type 4X/12/13, and Class I Div 2 mean the FT2J PLC+HMI can be used in a wide range of applications and locations. Flexible configuration All PLC and HMI configuration is accessed through IDEC’s standard WindOI-NV4 software, which is easy-to-use and intuitive, with a drag-and-drop interface and extensive image library. Projects can automatically be converted from one HMI size to another within seconds. Script programming, PIDD loop control, multilingual capabilities, security, trend charts, data logs, alarm logs, and other functions and features are supported for both the HMI and the PLC. Connectivity Two USB-A ports support flash drives for data logging, recipes, and program transfer—along with dongles for speakers, Wi-Fi, and Bluetooth. The embedded Ethernet port provides users with easy access for remote maintenance and communication as well as Modbus TCP protocols and other intelligent devices. The built-in RS232C and RS422/485 serial communication ports support Modbus RTU and also allow the FT2J to communicate to other serial devices like barcode readers or temperature controllers. Communications and IIoT Many communication options are available for users to create automation and IIoT solutions incorporating multiple industrial protocols, the FTP protocol, remote monitoring and control, email/text messaging, iOS and Android apps, and custom web pages.