Smart Vision Lights unveils LHI-DO Lightgistics with hidden strobe technology
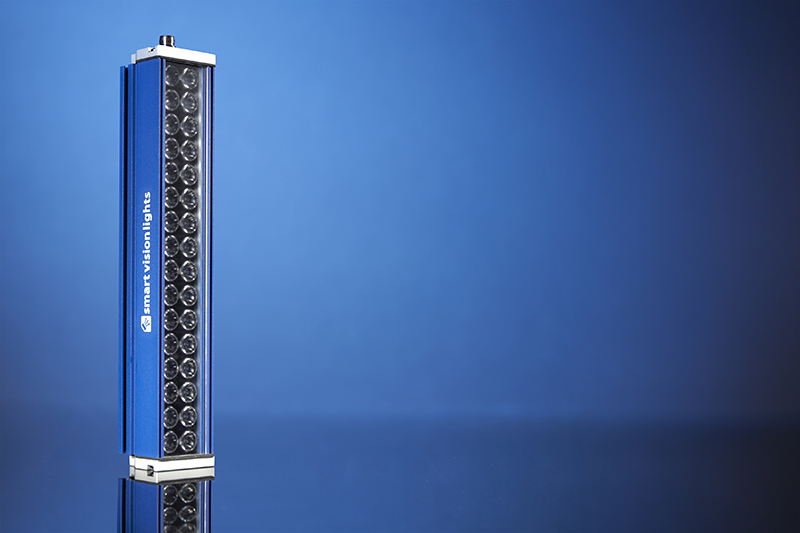
Smart Vision Lights has introduced the LHI-DO Lightgistics series light, which is available in 300 mm and 600 mm models designed to deliver intense linear light in high-speed scan tunnel systems. Equipped with Hidden Strobe technology, the light delivers the benefits of LED strobing while minimizing the disruption and disorientation associated with bright, pulsing lights. Hidden Strobe technology enables LEDs to rapidly self-trigger thousands of times per second at rates imperceivable to the human eye — giving off an illusion of continuous illumination. The novel technology helps logistics companies maximize the capabilities of machine vision systems while protecting employees against the harmful and disorienting effects of continuous flashing lights. “High-speed machine vision systems often use pulsating LEDs to capture images of objects moving at rapid speeds, but without a shield, the strobing can be disorienting and distracting for nearby workers,” said Steve Kinney, director of training, compliance, and technical solutions at Smart Vision Lights. “Machine vision lights such as the LHI-DO leverage Hidden Strobe technology to remove this nuisance and allow the machine vision system to safely and effectively leverage strobed LEDs for challenging high-speed applications.”Lighting the Way for Improved Track-and-Trace Machine vision systems attempting to perform accurate high-speed barcode scanning or optical character recognition (OCR) on packages with reflective plastic wraps or shipping bags run into significant issues with glare. Polarizers can overcome the glare problem, but this comes at a cost, with reduced light output and decreased clarity. Lightigistic lights featuring Dual OverDrive™ technology are designed specifically to overcome these issues. Dual OverDrive™ technology combines SVL’s Deca OverDrive™ and standard OverDrive™ engines to deliver lighting that is 10 times brighter than standard continuous mode. “Lights featuring Dual OverDrive™ technology, like the LHI-DO, produce enough brightness that end users can attach polarizers that retain exceptional light output while handling any speed,” said Kinney. “For applications involving polybags or plastic shrink wrap, this means the machine vision system does not have to slow down and decrease overall throughput.” The LHI-DO’s OverDrive™–only light source can be used to create tunnel systems capable of illuminating any package — ensuring perfect readability no matter the shape or material. With an integrated camera mount compatible with most machine vision cameras, the light can be directly connected and controlled through a camera’s trigger output. With onboard charging capacitors, the LHI-DO delivers powerful bursts of energy with a low consistent electrical draw. The IP65-rated LHI-DO can be used at working distances between 500 mm and 2000 mm with 10-, 14-, and 30-degree lens options.
SUN Automation Group® announces Amit Nayak as new Product Manager
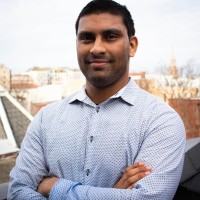
SUN Automation Group, providing innovative solutions to the global corrugated industry, has announced that Amit Nayak has been hired as the new Product Manager for SUN’s IIoT solution, Helios. Amit brings a wealth of expertise in business analytics and product management, positioning him to significantly expand Helios’ market presence and enhance its offerings to meet the evolving demands of box plants worldwide. Amit comes to SUN with a robust background in business intelligence and identifying customer needs through research and analytics. Amit earned his Bachelor of Science in Applied Mathematics and Master of Science in Business Analytics from George Washington University. Before joining SUN, Amit was instrumental in developing strategic product initiatives at MicroStrategy in Virginia, where he excelled in optimizing gateway solutions. “Amit’s exceptional skills in data analytics and product management make him a valuable addition to our team,” said Gokul Gopakumar, Vice President of Technology and Business Development at SUN. “His insights will be pivotal as we continue to advance Helios and better serve the needs of the corrugated sector.” In his new role, Amit will focus on optimizing the capabilities of Helios, SUN’s OEM-agonistic technology which is designed to minimize unplanned downtime and maximize output through advanced machine learning. In addition, Amit will work to drive sales and marketing strategies to expand SUN’s reach across the corrugated industry. “Amit’s ability to navigate and interpret business intelligence data, coupled with a keen understanding of customer needs, positions us for continued success in expanding Helios’ reach and capabilities,” says Greg Jones, Executive Vice President at SUN. “We look forward to Amit’s leadership as we elevate our IIoT solutions to meet the evolving demands of box plants globally.” Amit’s arrival marks a significant step in SUN’s ongoing effort to enrich its knowledge base and team, reinforcing the company’s commitment to delivering cutting-edge solutions to its customers. As the corrugated industry increasingly embraces artificial intelligence, SUN remains dedicated to leading the charge in equipping clients with the tools necessary for their operational success.
Episode 463: Insights into the heart of fulfillment with Jeff Kaiden from Capacity
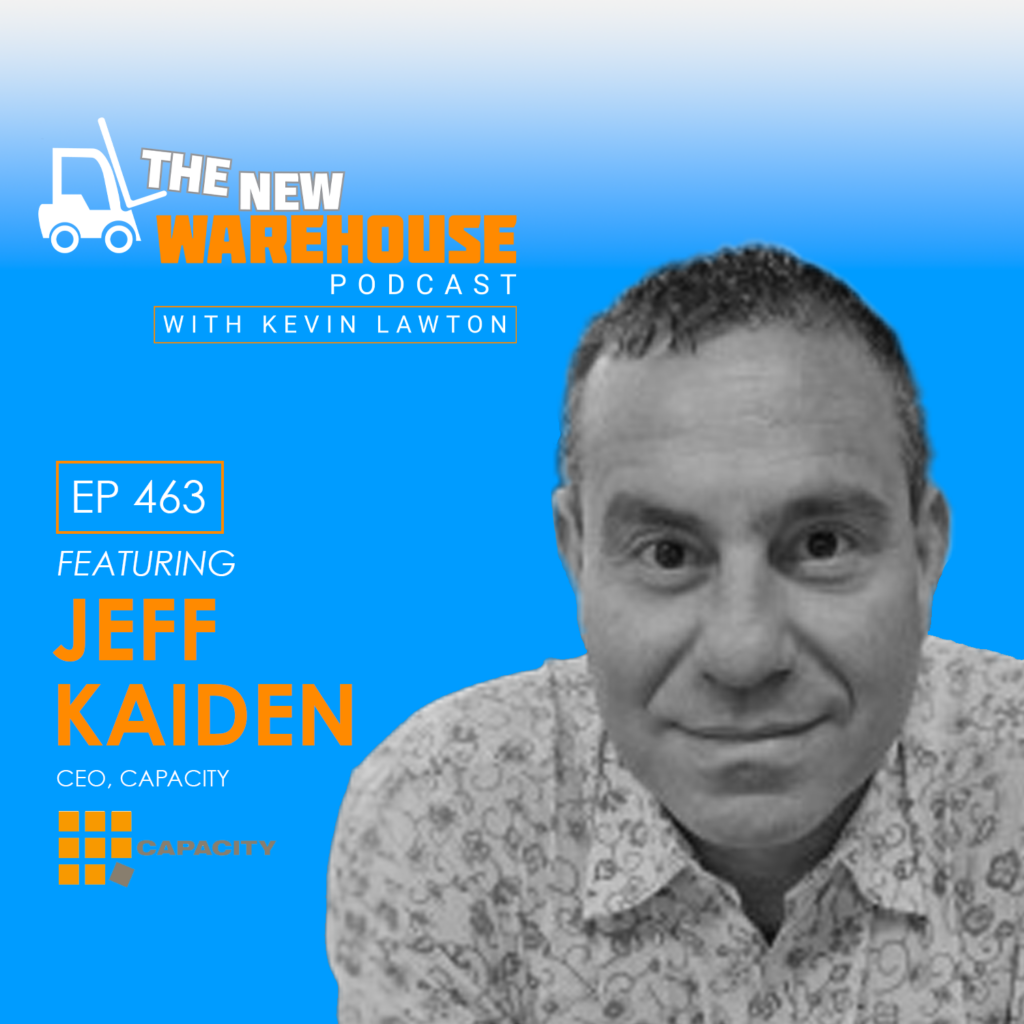
In this episode of The New Warehouse Podcast, we had the privilege of visiting Capacity’s headquarters in North Brunswick, New Jersey, where we were warmly welcomed by Jeff Kaiden, Capacity’s founder and CEO. Capacity, known for its omnichannel fulfillment services, has grown remarkably under Jeff’s leadership, servicing an array of significant brands with a keen focus on e-commerce and B2B fulfillment. The episode delves into Jeff’s fascinating journey in the fulfillment industry, the inception of Capacity, and the innovative technologies that have propelled the company to the forefront of warehousing and logistics. A Deep Dive into Capacity’s Innovative Edge The company’s investment in a bespoke, engineering-based approach and in-house IT solutions has enabled it to stay agile and responsive to customer needs. Jeff shares, “We have our own software development team… constantly adding value.” he adds, “To be in control of your own IT destiny is super important.” This strategy highlights Capacity’s commitment to leveraging technology for operational efficiency and agility. With a robust team of in-house developers, Capacity can swiftly adapt to the ever-evolving needs of its clients, ensuring that solutions are nimble and cost-effective. The team of approximately 20 developers is constantly “adding value” through process improvements and custom integrations, demonstrating a proactive stance in leveraging technology to enhance operational efficiencies. The Human Element in Fulfillment Capacity’s technological evolution is not merely about adopting new tools; it’s a holistic strategy encompassing data analysis, engineering excellence, and a profound understanding of the human element. “The most important people in this company are the ones who are doing the work,” Jeff Kaiden remarked, emphasizing the value of human capital in the logistics sector. By maintaining a close-knit environment and fostering a sense of community, Capacity ensures high levels of employee satisfaction and operational excellence. Moreover, Jeff’s anticipation of scalability challenges, particularly highlighted by the fluctuations between regular operation days and peak times like Black Friday, underlines the significance of scalable technology. “Our people are the key to all this,” Jeff asserts, acknowledging that while technology provides the framework, the human element within Capacity propels its success. This blend of cutting-edge technology and human ingenuity ensures that Capacity remains at the forefront of the fulfillment industry, ready to handle any volume surge with grace and efficiency. Mastering Data for Inventory Excellence Kaiden emphasizes the essential role of data management in precisely navigating the complexities of inventory and SKU management. Data First: It is essential to have detailed product data (dimensions, weight, hazard status) for efficient logistics. Inventory Readiness: Ensure ample stock before retail expansion to avoid fulfillment failures. Navigate Retail Complexities: Prepare for retailer-specific requirements and potential deductions. Balance Inventory: Avoid overstock and stockouts through careful planning and SKU management. SKU Strategy: Manage SKU proliferation to keep operations and inventory manageable. These insights offer a concise roadmap for brands to effectively manage their inventory and SKU portfolio, emphasizing the critical role of data management, preparation for retail expansion, and the strategic balance needed in inventory planning. Key Takeaways: Jeff believes automated put walls on the hardware side, along with AI and planning on the software side, provide the most bang for the buck in warehouse technology. The company places a high value on its workforce, fostering a culture of respect and teamwork to drive operational efficiency. Despite the rapid evolution of the e-commerce landscape, Capacity has adapted by focusing on customer service, scalable technology, and efficient inventory management. The New Warehouse Podcast EP 463: Insights into the Heart of Fulfillment with Jeff Kaiden from Capacity
Cimcorp promotes supply chains through automation
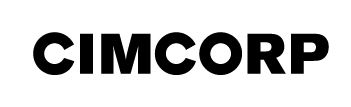
Equipped with Cimcorp’s material handling solutions, grocery retailers and tire manufacturers are maximizing efficiency and minimizing their environmental impact Cimcorp, a robotic handling solution, is helping customers in its core sectors, the fresh food and tire industries, achieve their sustainability goals through automation. When installed within tire factories and grocery distribution centers, Cimcorp’s automated material handling solutions enable greater energy efficiency, significantly reduce waste, and support greener overall supply chain operations. “Sustainability is increasingly important in both of our key sectors: grocery retail and tire manufacturing. These industries face growing pressure from consumers, shareholders, and governments alike to limit natural resource consumption and reduce waste across the supply chain. And one of the best ways to create more eco-friendly production, warehousing, and distribution operations is through automation,” said Adam Gurga, National Manager of Grocery and Retail Partnerships, Cimcorp. Cimcorp’s advanced robotics and intelligence software are designed with sustainability in mind. By leveraging Cimcorp’s solutions, clients benefit from: Energy efficiency: Cimcorp’s gantry robot solutions offer low energy consumption. The structure of each gantry robot is formed from aluminum, making the robots lightweight yet robust. They accelerate and move fast, optimizing the potential handling capacity for products moved in the distribution center (DC). Cimcorp’s gantry robots can carry multiple crates or cases simultaneously, instead of just one. Cimcorp’s crate solutions can carry a maximum of 250 kilograms at a time and can create stacks up to 2.5 meters tall. High volumes can be moved and handled quickly and efficiently. In addition, Cimcorp’s gantry robots reuse energy through regenerative braking. Braking energy is recovered to the power grid, making the robots even more energy efficient. Approximately 30% of energy is gathered and fed back. Optimized truckloads: Cimcorp’s Warehouse Control System (WCS) optimizes the loading of delivery vehicles, helping customers utilize truck space more efficiently. Space optimization creates fuller trucks, so fewer trucks are needed. This leads to fewer miles being driven, less pollution and exhaust fumes, and a greener supply chain. Reduced food waste: In grocery retail, the longer it takes fresh food to travel through the supply chain, the higher the chances of spoilage and waste. By optimizing distribution operations, grocery retailers can move produce from field to store in half the time. Today, Cimcorp has successfully accelerated distribution for grocery retail customers around the world. For example, Cimcorp’s solutions are helping Mercadona, Spain’s biggest grocery retailer, move produce to stores in under 24 hours. Reusable packaging: Cimcorp’s solutions are designed to match perfectly with reusable plastic crates (RPCs), which many modern grocers are now choosing over cardboard options. RPCs can be used thousands of times, replacing cardboard boxes as the method of transport for fresh produce from the farm to the store shelf. RPCs have a long and sustainable life cycle since they can be used over and over again from field to warehouse. Minimized scrap: In tire manufacturing, automated tire handling significantly reduces scrap in all process areas. With Cimcorp’s Warehouse Control System (WCS), tire manufacturers can minimize intermediate storage and avoid unnecessary scrapping of materials. If there is any disruption to the manufacturing process, all individual tire components can be tracked and traced to avoid scrapping of the whole inventory. Gurga said, “As a trusted partner for grocery retailers and tire manufacturers around the world, we’re proud to help our clients strategically plan and automate their warehousing and distribution operations so they can get more out of less. For any company looking to reduce their supply chain’s environmental impact, automation is a great step towards a greener future.”
Motion enters into definitive agreement to purchase two fluid power companies
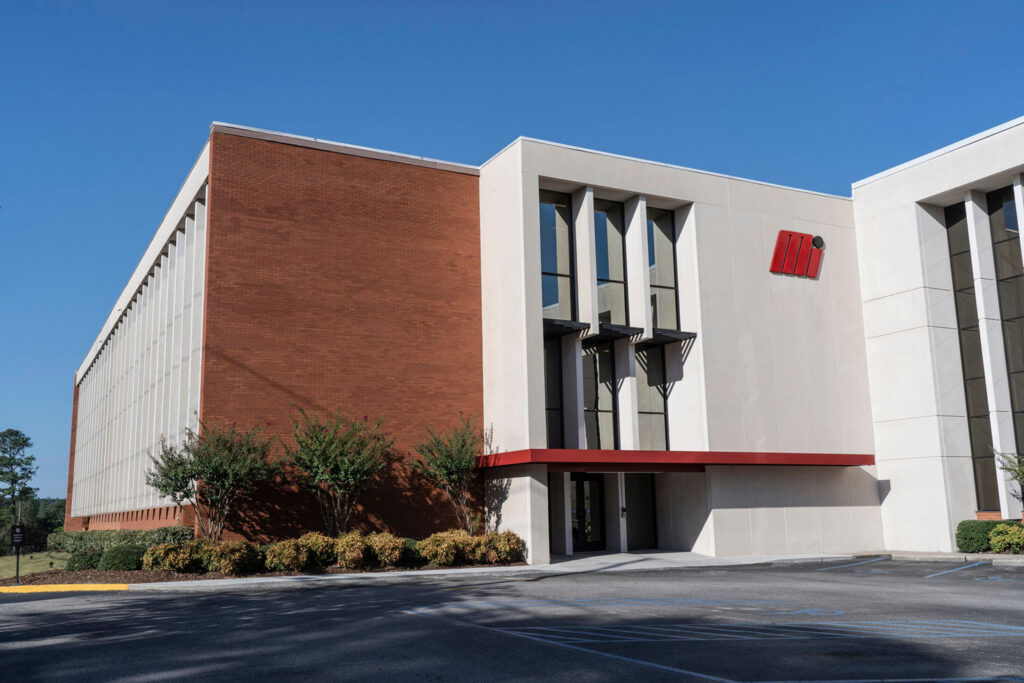
Motion’s Canadian hydraulic/pneumatic footprint to expand Motion Industries, Inc., a distributor of maintenance, repair, and operation replacement parts, and a provider of industrial technology solutions, signed a definitive purchase agreement to acquire the operating assets of Perfetto Manufacturing and SER Hydraulics. Subject to customary closing conditions, the transaction is expected to be finalized at the end of February. The affiliated organizations are well-established, with Perfetto in business since 1986 and SER Hydraulics since 1978. Located in Sudbury, Canada, each has grown to provide engineered solutions, service, and equipment for hydraulic/pneumatic cylinders, complex power units, and other assets used in fluid power systems throughout the area, which is central to the mining, agricultural, and forestry industries. The dual acquisition will expand and improve Motion’s services to these and other heavy-industry customers. “After more than 30 successful years in business, we want to thank our loyal customers and employees for contributing to our success,” said Gerald Perfetto Sr., Owner. “The Motion team is committed to continued investment in the business, which will bring great opportunities for our customers, employees, and the communities in which we work and live. We couldn’t be more pleased with the interest that Motion has taken in our business and wish everyone continued success.” “We look forward to welcoming these two terrific organizations, especially the talented employees,” said Randy Breaux, President of GPC North America. “These world-class experts will be key to our market growth strategy, and we look forward to extending our position together as a premier leader in industrial solutions.”
Buckle Up: Cat® Lift Trucks marks 20 consecutive years for the Houston Livestock Show and Rodeo™
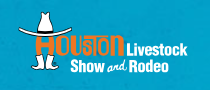
Mitsubishi Logisnext Americas, a manufacturer and provider of Cat® lift trucks across North, Central, and South America, has announced the 20th recurring year as the Official Lift Truck Provider for the Houston Livestock Show and Rodeo™. For two decades, Cat Lift Trucks and its local dealer, Darr Equipment Co., have played a critical role in the production of the largest livestock exhibition and rodeo in the world. The Houston Livestock Show and Rodeo is a beloved tradition for over 2.5 million visitors and 30,000 exhibitors each year, showcasing the very best in agriculture, entertainment, and Western heritage. “Cat Lift Trucks has been a driving force behind our operations of the Houston Livestock Show, ensuring our iconic event runs smoothly,” said Dr. Chris Boleman, president and CEO of Houston Livestock Show and Rodeo. “Their consistent dedication to providing top-tier products and unparalleled support has been pivotal. As we celebrate 20 years of partnering together, we look forward to continued excellence and a shared journey filled with memorable experiences for years to come.” As the Official Lift Truck Provider, Cat Lift Trucks, along with Darr Equipment Co., provides over 140 Cat lift trucks to ensure seamless operation from setup to tear down throughout the 300-acre complex. Darr Equipment Co.’s technicians will also be on-hand throughout the show to provide daily on-site service and maintenance for the forklifts throughout the Rodeo season. “It’s an honor to continue as the Official Lift Truck Provider – now in our 20th year”, said Jerry Sytsma, Executive Vice President, Sales & Aftermarket Services at Mitsubishi Logisnext Americas. “The work performed behind the scenes, by our forklifts and Darr’s technicians, allows us to help bring together the city of Houston in a meaningful way, while also indirectly helping to provide educational scholarships for deserving kids. It’s a real honor to help give back to our community in this way.” Beyond the operational support, Cat Lift Trucks embodies its commitment to nurturing future leaders and innovators with its scholarship program. Since its launch in 2005, the Cat Lift Trucks scholarship program has awarded $140,000 in educational assistance to 28 outstanding Houston-area high school seniors interested in pursuing a four-year degree related to the material handling industry. This year’s winner will be honored at the 2024 Houston Livestock Show and Rodeo™ and awarded a $5,000 scholarship to go towards their higher education.
Why do we separate change from day-to-day operations?
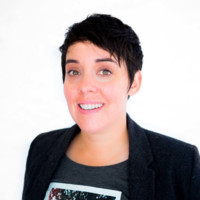
It’s a common trap that many executives fall into. Consider a company that creates widgets. They must produce the widgets on time and on schedule. They also have designed a competitive strategy which includes modernizing some major systems on the production floor. Say the company is having trouble with widget quality and missed deadlines. Should leadership focus on fixing the operational problems or on the strategy? Most executives would prioritize the former. They would say, “Let’s first patch the holes and then modernize the ship.” And most CEOs would say, “Ok.“ This is the mistake. A leader’s job is to implement changes. Change is what they should do. If an executive can’t delegate problems to their subordinates, are they a good leader? Good leaders only intervene when problems can’t be solved by their team without their direct help. Good leaders aren’t afraid of change. They thrive on it. Even if the problem is perceived to be big, there’s a reason you have a team in place. Your department heads, managers, and directors are there to solve problems and to keep the proverbial machine running. Circumstances will change, issues will arise, and they were hired to navigate it all. But once leadership has decided to take on a big change, there always seems to be some reason to put it off. Something happens inside the organization, in the competitive environment, in the regulatory space, etc. “We can’t tackle that change now. It will be too overwhelming – we need to wait until we’re ready.” But you’ll never be ready. There will always be something that comes up and those changes will be kicked back a few quarters, a few years, and in some cases, put on ice indefinitely. The worst part is that this lack of change causes the organization to get stuck in status quo mode. Things then continue to hum along as they always have. But as time passes, the gap between where you are and where you need to be widens. The big change was on the to-do list for a reason. While big change is intimidating, the impact of not taking action becomes way worse than the perceived risk of action. Then the pain of change is amplified, as the change becomes forced by external circumstances, rather than it being a choice you had control of earlier. In essence, leaders need to be in charge of driving change. Change isn’t separate from day-to-day operations – it’s a part of the way business is done. Inherent to both business and life, change is something that can be scary, but needs to be embraced. Don’t put off the inevitable, as it only becomes harder to change over time. About the Author Andrea Belk Olson is a keynote speaker, author, differentiation strategist, behavioral scientist, and customer-centricity expert. As the CEO of Pragmadik, she helps organizations of all sizes, from small businesses to Fortune 500, and has served as an outside consultant for EY and McKinsey. Andrea is the author of three books, including her most recent, What To Ask: How To Learn What Customers Need but Don’t Tell You, released in June 2022. She is a 4-time ADDY® award winner and host of the popular Customer Mission podcast. Her thoughts have been continually featured in news sources such as Chief Executive Magazine, Entrepreneur Magazine, Harvard Business Review, Rotman Magazine, World Economic Forum, and more. Andrea is a sought-after speaker at conferences and corporate events throughout the world. She is a visiting lecturer and startup coach at the University of Iowa, a TEDx presenter, and TEDx speaker coach. She is also an instructor at the University of Iowa Venture School. More information is also available on www.pragmadik.com and www.andreabelkolson.com.
DESTACO presents all-electric clamping system
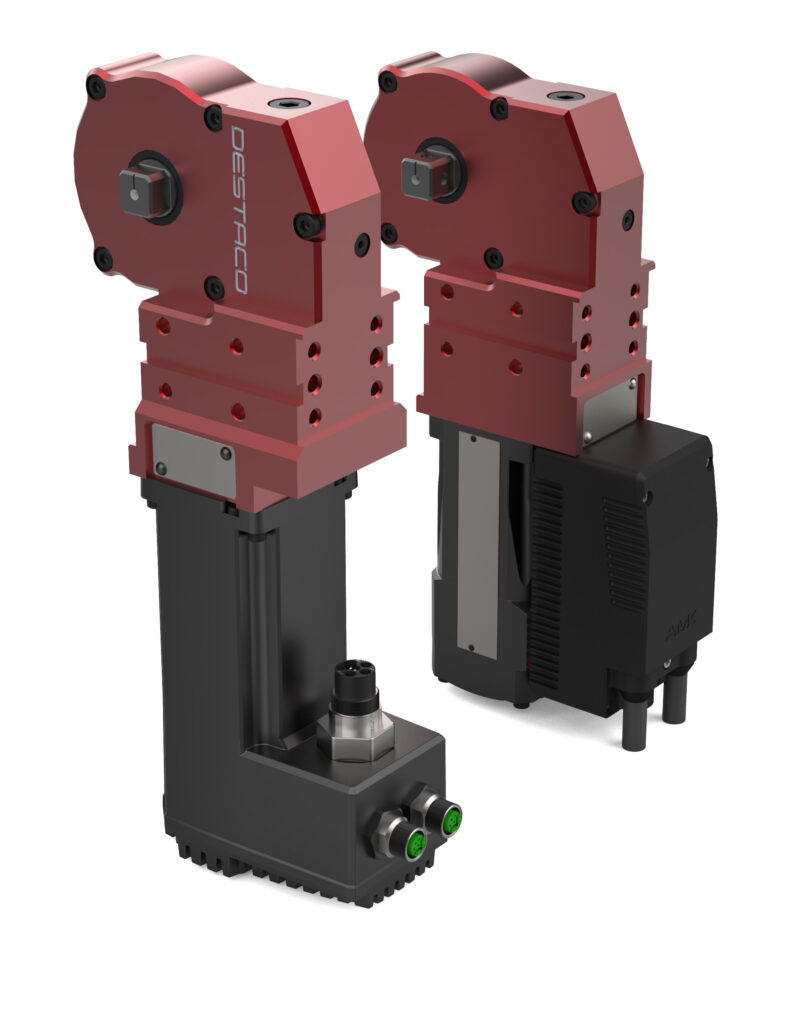
The 92W Series Power Clamp saves costs, CO2 and energy on the way to Industry 4.0 DESTACO, a provider of automation, clamping, and gripping solutions, has introduced the new intelligent 92W Series Electric Power Clamps. Operating completely without compressed air, the 92W power clamps set a new standard for efficient and environmentally friendly production operations. They reduce energy consumption and CO2 emissions – and as a plug-and-play solution, they pave the way for exceptionally flexible production processes. “Electric drives have clear advantages over pneumatic drives,” explained Christian Schubert, Global Product Manager for DESTACO. “They reduce CO2 emissions and energy costs by up to 85%. Their use of electric motors helps eliminate the need for lossy compressed air lines and associated pneumatic equipment. Electric drives also offer a high degree of flexibility, which significantly reduces the need for an expansive spare-parts inventory.” The 92W power clamp’s integrated intelligence also reduces the need for additional components, as it provides essential data for process optimization even without external sensors. Even during installation, these values allow the user to conveniently adjust the speed, positioning and/or torque to “fine-tune” production. During subsequent operations, the values are used to analyze process quality. The control of the electric clamps is decentralized and attached directly to the production devices, which reduces cable lengths and cabling costs. In this way, all automation functions can be implemented decently. This not only frees up space, but also ensures seamless integration of the clamping technology into the production system. Reliable voltage, signal, and data management also facilitate digital planning, along with providing quick and easy installation and commissioning. All of these features save time and, together with process optimization, reduce labor costs. Higher initial investments are therefore amortized in one to three years, depending on the configuration. The advantages of the new 92W power clamps will be able to help many manufacturing companies switch their production from pneumatic to electric drives. Many innovative companies are already using the first 92W power clamp units in their production processes and achieving excellent results. The powerful 92W electric power clamps hold workpieces in several positions; for example, during the production and assembly of body shells. Thanks to the power clamp’s integrated component control, no external sensors are required. In combination with the unit’s integrated tolerance compensation, this enables the control and production of different component types. In parallel to the smart electric clamps of the 92W Series, further economical variants of the series are being launched to the market. DPE/RPE Grippers, GTB/RPE Servo Positioners, and EcoCup Vacuum Cups also feature the advantages of electric drives.
January 2024 drops 15% with Planned Industrial Construction Projects in one month
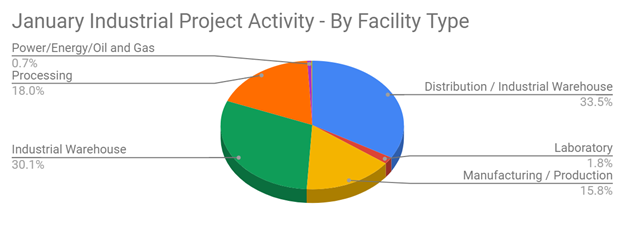
Research by SalesLeads’ experienced industrial market research team, shows 369 new planned industrial projects tracked during the month of January. Planned industrial project activity decreased 15% from the previous month. The following are selected highlights on new industrial construction news and project opportunities throughout North America. Planned Industrial Construction – By Project Type: Manufacturing Facilities – 90 New Projects Processing Facilities – 103 New Projects Distribution and Industrial Warehouse – 191 New Projects Power/Energy/Oil and Gas – 4 New Projects Laboratory Facilities – 10 New Projects Mine – 0 New Projects Terminal – 1 New Project Pipeline – 0 New Projects Planned Industrial Construction – By Scope/Activity New Construction – 177 New Projects Expansion – 83 New Projects Renovations/Equipment Upgrades – 120 New Projects Plant Closing – 23 New Projects Planned Industrial Construction – By Location (Top 10 States) Texas – 28 Florida – 27 New York- 23 California – 22 North Carolina – 19 Indiana – 16 Michigan – 16 Ohio – 15 Wisconsin – 13 Georgia – 12 Largest Planned Industrial Construction Project During January, our research team identified 30 new General Industrial facility construction projects with an estimated value of $100 million or more. The largest project is owned by Pathways Alliance, which is planning to invest $17 billion in the construction of a carbon capture and storage facility in WOOD BUFFALO, AB. They are currently seeking approval for the project. Top 10 Tracked Industrial Construction Projects ONTARIO: Automotive MFR. is considering investing $14 billion for the construction of an EV battery manufacturing facility and currently seeking a site in ONTARIO. ALBERTA: Oil and gas company is planning to invest $3 billion for the construction of a processing facility in WOOD BUFFALO, AB. They are currently seeking approval for the project. Construction will occur in two phases. MISSISSIPPI: Energy technology company is planning to invest $2 billion for the construction of an EV battery manufacturing facility in MARSHALL COUNTY, MS. They are currently seeking approval for the project. OKLAHOMA: Lithium producer is planning to invest $1.2 billion for the construction of a processing facility in MUSKOGEE, OK. They are currently seeking approval for the project. Construction is expected to start in Summer 2024. TEXAS: Renewable energy company is planning to invest $1 billion for the construction of an ammonia processing facility in PORT ARTHUR, TX. They are currently seeking approval for the project. NEBRASKA: Renewable energy company is planning to invest $650 million for the construction of an ammonia processing plant in AURORA, NE. They are currently seeking approval for the project. Construction is expected to start in early 2025, with completion slated for late 2026. NORTH CAROLINA: Diesel engine MFR. is planning to invest $580 million for the expansion and equipment upgrades on their manufacturing facility in WHITAKERS, NC. They are currently seeking approval for the project. ARKANSAS: Oil and gas service company is planning to invest $500 million for the construction of a bromine processing plant in COLUMBIA and LAFAYETTE COUNTIES, AR. They have recently received approval for the project. ILLINOIS: Copper products MFR. is planning to invest $500 million for the expansion and equipment upgrades on their manufacturing facility in EAST ALTON, IL. They are currently seeking approval for the project. CALIFORNIA: Semiconductor MFR. is planning to invest $432 million for the construction of a manufacturing facility in WEST OAKLAND, CA. They are currently seeking approval for the project. About Industrial SalesLeads, Inc. Since 1959, Industrial SalesLeads, based in Jacksonville, FL is a leader in delivering industrial capital project intelligence and prospecting services for sales and marketing teams to ensure a predictable and scalable pipeline. Our Industrial Market Intelligence identifies timely insights on companies planning significant capital investments such as new construction, expansion, relocation, equipment modernization, and plant closings in industrial facilities. The Outsourced Prospecting Services, an extension to your sales team, is designed to drive growth with qualified meetings and appointments for your internal sales team.
Maximizing Warehouse Space: Unleashing potential with Next Level’s Mezzanine Solutions
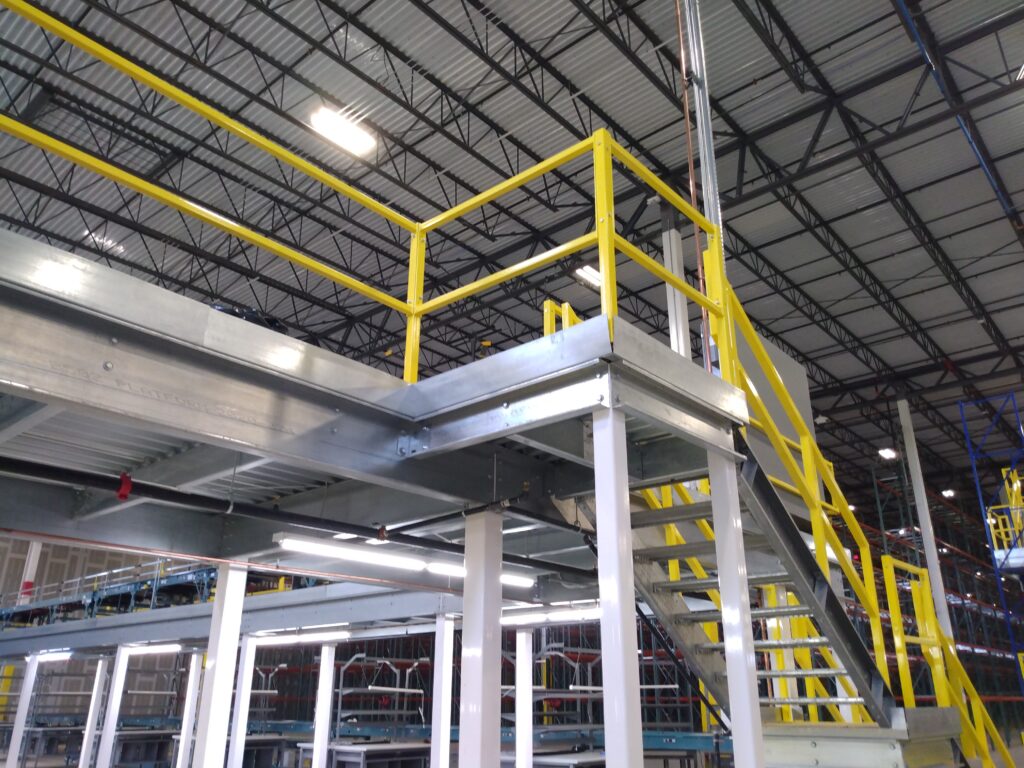
Optimizing warehouse space is a critical endeavor for businesses looking to enhance efficiency and reduce operational costs. One innovative solution gaining popularity is the use of mezzanine systems, and Next Level stands out as a provider that prioritizes strength, stability, and cost-effectiveness. In this article, we explore how Next Level’s mezzanine systems can help you maximize your warehouse space with their robust features and thoughtful design. Section 1: The Strength Advantage Next Level distinguishes itself through an unwavering commitment to providing mezzanine systems with unparalleled strength. The foundation of this strength lies in the meticulous selection of materials and construction techniques employed by Next Level, ensuring that their mezzanine systems offer robust support for diverse loads while maintaining long-term durability. Next Level’s emphasis on utilizing the strongest possible connections within their mezzanine systems speaks directly to the reliability and safety of these structures. Heavy-duty columns, carefully chosen for their load-bearing capabilities, are strategically incorporated to create a solid framework that stands up to the challenges of a bustling warehouse environment. This robust construction not only allows for the efficient use of vertical space but also instills confidence in businesses looking to optimize their storage and operational capacities. Moreover, the strength advantage provided by Next Level’s mezzanine systems contributes to the overall stability of the structure. This is especially crucial in warehouses dealing with heavy inventory or machinery. The mezzanine’s ability to withstand substantial loads without compromising stability ensures a secure and dependable platform for storage or operational needs. Beyond the immediate benefits, the strength advantage becomes a long-term asset for businesses, minimizing concerns related to structural integrity and reducing the likelihood of costly repairs or replacements. By investing in Next Level’s mezzanine systems, businesses can be confident that their warehouse space is fortified with a foundation designed to withstand the rigors of daily operations while providing a robust and enduring solution for maximizing storage capacity. Section 2: Stability without Bracing One of the distinctive features that sets Next Level’s mezzanine systems apart is their innovative design that eliminates the need for knee bracing or diagonal bracing. This design philosophy goes beyond mere aesthetics, presenting tangible benefits in terms of both installation simplicity and the creation of a versatile and unencumbered workspace beneath the mezzanine. Traditional mezzanine structures often require diagonal bracing or knee bracing to enhance stability, which can, in turn, limit the open space below. Next Level challenges this norm by engineering mezzanine systems that boast inherent stability without the need for additional bracing elements. This not only simplifies the installation process but also opens up possibilities for businesses seeking a more flexible and streamlined floor plan. The absence of knee bracing or diagonal bracing beneath the mezzanine creates a spacious and obstruction-free area that businesses can utilize for a variety of purposes. Whether it’s organizing inventory, setting up workstations, or accommodating machinery, the unobstructed space fosters an environment where operational efficiency and adaptability thrive. Furthermore, this design choice contributes to a cleaner and more visually appealing warehouse layout. The absence of additional bracing elements not only enhances the overall aesthetics but also facilitates easier navigation and movement within the warehouse. Businesses can, therefore, design their floor space with greater freedom, optimizing the layout to suit specific operational needs without the constraints imposed by traditional bracing requirements. In summary, Next Level’s commitment to stability without bracing not only simplifies the installation process but also transforms the space beneath the mezzanine into a versatile canvas for businesses to optimize their workflow and spatial efficiency. It’s a testament to Next Level’s forward-thinking approach to mezzanine design, providing a solution that not only meets structural requirements but also enhances the overall functionality and aesthetic appeal of the warehouse environment. Section 3: Zinc Coating for Durability Next Level takes a proactive approach to ensuring the longevity and durability of their mezzanine systems by offering zinc-coated beams, struts, and joists as a standard feature from the factory, without incurring any additional cost. This meticulous coating process involves applying a layer of zinc to the structural components, creating a protective barrier against corrosion, rust, and environmental wear and tear. The zinc coating not only serves as a shield against the harsh conditions commonly found in industrial environments but also enhances the overall lifespan of the mezzanine system. This protective layer acts as a corrosion-resistant barrier, preventing degradation over time and reducing the need for frequent maintenance. As a result, businesses can rely on Next Level’s mezzanine systems for sustained performance, minimizing the risk of structural deterioration that might compromise the safety and functionality of the warehouse space. In addition to its protective qualities, the zinc coating contributes to the aesthetic appeal of the mezzanine components. The clean and polished appearance not only reflects a commitment to quality but also adds a professional touch to the overall warehouse environment. By incorporating zinc-coated elements into their mezzanine systems, Next Level ensures that businesses not only maximize their storage capacity but also invest in a solution that stands the test of time and looks great doing it. Section 4: Cost-Effective Solutions Next Level’s dedication to providing zinc-coated components without additional charges extends beyond durability; it translates into a cost-effective solution for businesses seeking to expand their warehouse space. The decision to include zinc coating as a standard feature without extra cost reflects Next Level’s commitment to delivering value and reducing the total cost of ownership over the lifespan of the mezzanine system. By opting for Next Level’s mezzanine systems, businesses not only benefit from the durability and corrosion resistance of zinc-coated components but also make a strategic investment in long-term cost savings. The reduced need for maintenance and potential replacements due to corrosion leads to lower operational costs and a higher return on investment over time. In summary, Next Level’s combination of zinc coating for durability and a commitment to cost-effective solutions ensures that businesses not only maximize their warehouse space but do so with a keen eye on durability, maintenance costs, and long-term financial benefits. It’s
U.S. Rail Traffic for the week ending February 21, 2024
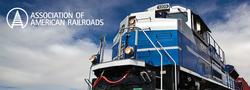
The Association of American Railroads (AAR) has reported U.S. rail traffic for the week ending February 17, 2024. For this week, total U.S. weekly rail traffic was 474,226 carloads and intermodal units, up 3.7 percent compared with the same week last year. Total carloads for the week ending February 17 were 220,529 carloads, down 0.6 percent compared with the same week in 2023, while U.S. weekly intermodal volume was 253,697 containers and trailers, up 7.9 percent compared to 2023. Seven of the 10 carload commodity groups posted an increase compared with the same week in 2023. They included miscellaneous carloads, up 1,983 carloads, to 9,616; chemicals, up 1,543 carloads, to 33,899; and motor vehicles and parts, up 1,187 carloads, to 14,849. Commodity groups that posted decreases compared with the same week in 2023 were coal, down 7,122 carloads, to 59,534; nonmetallic minerals, down 652 carloads, to 27,126; and petroleum and petroleum products, down 122 carloads, to 9,467. For the first seven weeks of 2024, U.S. railroads reported a cumulative volume of 1,466,059 carloads, down 5.6 percent from the same point last year; and 1,724,189 intermodal units, up 6.7 percent from last year. Total combined U.S. traffic for the first seven weeks of 2024 was 3,190,248 carloads and intermodal units, an increase of 0.7 percent compared to last year. North American rail volume for the week ending February 17, 2024, on 12 reporting U.S., Canadian, and Mexican railroads totaled 331,196 carloads, down 1.0 percent compared with the same week last year, and 337,305 intermodal units, up 7.6 percent compared with last year. Total combined weekly rail traffic in North America was 668,501 carloads and intermodal units, up 3.2 percent. North American rail volume for the first seven weeks of 2024 was 4,443,897 carloads and intermodal units, down 0.2 percent compared with 2023. Canadian railroads reported 92,737 carloads for the week, down 3.0 percent, and 70,767 intermodal units, up 5.0 percent compared with the same week in 2023. For the first seven weeks of 2024, Canadian railroads reported cumulative rail traffic volume of 1,069,472 carloads, containers and trailers, down 4.0 percent. Mexican railroads reported 17,930 carloads for the week, up 5.0 percent compared with the same week last year, and 12,841 intermodal units, up 19.2 percent. Cumulative volume on Mexican railroads for the first seven weeks of 2024 was 184,177 carloads and intermodal containers and trailers, up 6.7 percent from the same point last year. To view the weekly rail charts, click here.
Governors America Corp. welcomes Jeff Little as director of product management
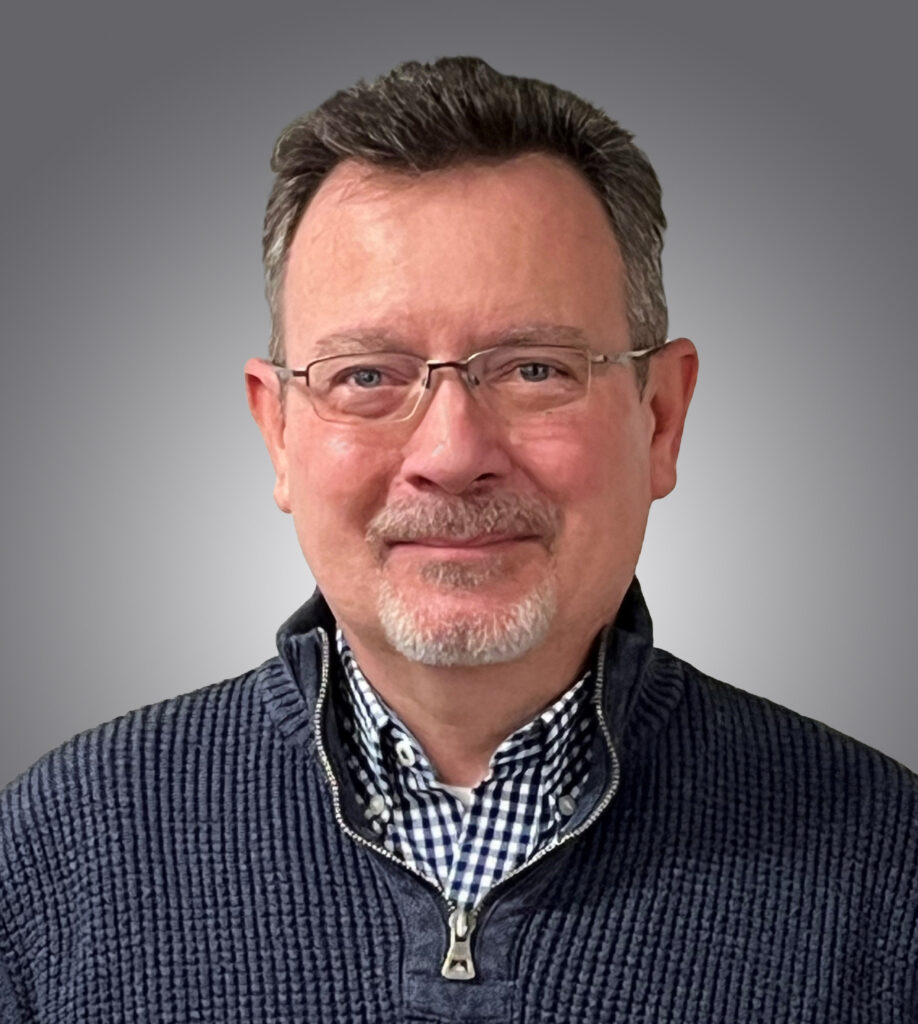
Oklahoma resident brings nearly three decades of experience to his role Governors America Corp. (GAC) recently welcomed Jeff Little as its new director of product management. “We’re thrilled to bring Jeff on board,” said Sean Collins, President and CEO. “He has decades of experience in the field, particularly in the area of instrumentation, display and control products for the industrial stationary, off-highway and recreational power sports market. His insight and expertise are exceptionally valuable.” As director of product management, Little’s responsibilities include aligning product strategy with business goals; driving product discovery, market research and competitor research; driving innovation and new product development initiatives; communicating product vision and strategy to stakeholders; and monitoring and maintaining product health. Little, a resident of Sapulpa, Oklahoma, received his B.S. in electrical engineering from Mississippi State University. He has garnered 27 years of experience in the industry, most recently as director of product management at Enovation Controls.
January 2024 remains steady with 66 New Food and Beverage Industry planned projects

SalesLeads has announced the January 2024 results for the new planned capital project spending report for the Food and Beverage industry. The Firm tracks North American planned industrial capital project activity; including facility expansions, new plant construction and significant equipment modernization projects. Research confirms 66 new projects in the Food and Beverage sector as compared to 67 in December 2023. The following are selected highlights on new Food and Beverage industry construction news. Food and Beverage Project Type Processing Facilities – 47 New Projects Distribution and Industrial Warehouse – 24 New Projects Food and Beverage Project Scope/Activity New Construction – 24 New Projects Expansion – 16 New Projects Renovations/Equipment Upgrades – 29 New Projects Plant Closing – 4 New Projects Food and Beverage Project Location (Top 10 States) Florida – 9 California – 6 New York – 6 Michigan – 4 Ohio – 4 Pennsylvania – 4 Indiana – 3 Virginia – 3 Wisconsin – 3 Georgia – 2 Largest Planned Project During January, our research team identified 3 new Food and Beverage facility construction projects with an estimated value of $100 million or more. The largest project is owned by Natures Bakery, which is planning to invest $237 million for the construction of a 339,000 SF processing facility in SALT LAKE CITY, UT. They have recently received approval for the project. Completion is slated for Summer 2025. Top 10 Tracked Food and Beverage Projects ONTARIO: Sugar producer is planning to invest $135 million for the construction of a processing facility in HAMILTON, ON. They are currently seeking approval for the project. Completion is slated for 2025. CALIFORNIA: Global retail chain is planning for the construction of a 1.8 million SF distribution and warehouse complex in TRACY, CA. They are currently seeking approval for the project. NEBRASKA: Meat processing company is planning to invest $43 million for the expansion of their processing facility in HASTINGS, NE by 11,000 SF. They are currently seeking approval for the project. ARKANSAS: Bakery company is planning to invest $37 million for the expansion and equipment upgrades on their processing facility at 2700 E. 3rd Street in HOPE, AR. They have recently received approval for the project. WISCONSIN: Candy MFR. is planning for the renovation and equipment upgrades on a recently leased 447,000 sf distribution center at 9403 136th Ave. in BRISTOL, WI. They will relocate a portion of their regional distribution operations upon completion in Summer 2024. ILLINOIS: Distillery is planning for the renovation and equipment upgrades on a 157,000 SF production and warehouse facility at 2400 SW Washington St. in PEORIA, IL. They are currently seeking approval for the project. GEORGIA: Herbal supplement MFR. is planning for the renovation and equipment upgrades on an 85,000 SF of warehouse space at 2323 Brown Rd. in BUFORD, GA. They are currently seeking approval for the project. MICHIGAN: Pickle products MFR. is planning to invest $10 million for the expansion of their processing and warehouse facility in LEXINGTON, MI. They are currently seeking approval for the project. NORTH CAROLINA: Distillery is planning to invest $10 million for the construction of a 28,000 SF production facility at 178 Old Airport Rd. in STATESVILLE, NC. They are currently seeking approval for the project. FLORIDA: Snack food MFR. is planning for the construction of a 104,000 SF distribution center at 9111 Cheetos Cir. in FORT MYERS, FL. They are currently seeking approval for the project. About Industrial SalesLeads, Inc. Since 1959, Industrial SalesLeads, based in Jacksonville, FL is a leader in delivering industrial capital project intelligence and prospecting services for sales and marketing teams to ensure a predictable and scalable pipeline. Our Industrial Market Intelligence identifies timely insights on companies planning significant capital investments such as new construction, expansion, relocation, equipment modernization and plant closings in industrial facilities. The Outsourced Prospecting Services, an extension to your sales team, is designed to drive growth with qualified meetings and appointments for your internal sales team.
Anyline unveils autonomous drone scanning technology for enhanced warehouse inventory management
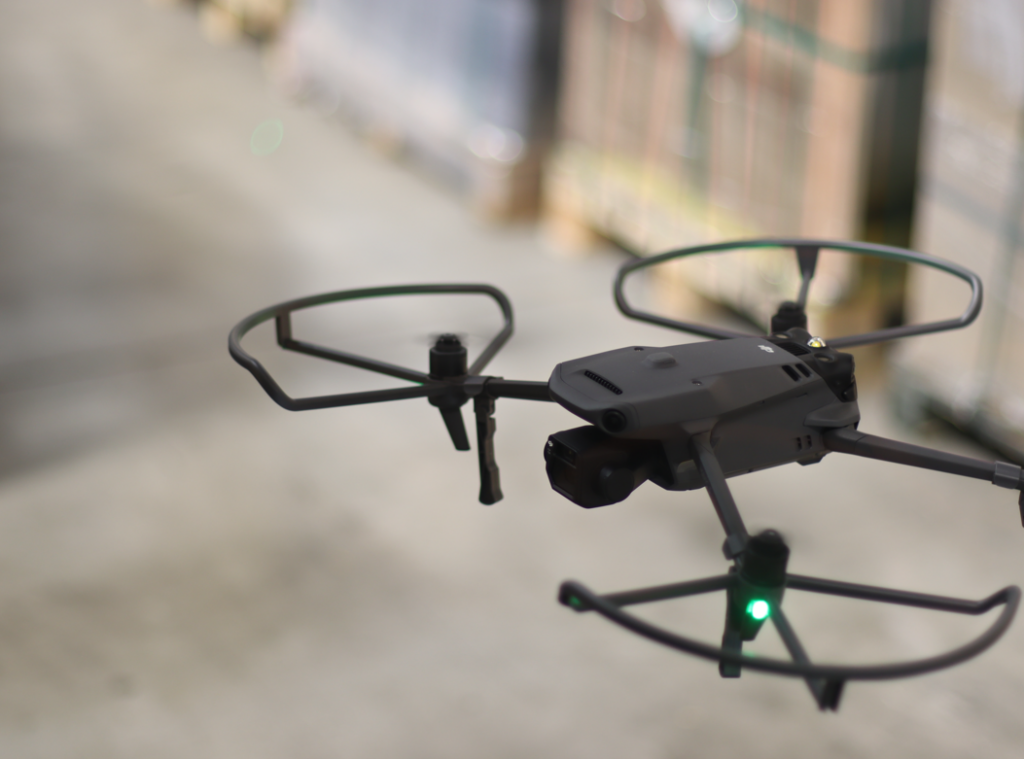
Anyline and Mondi collaboration leads to groundbreaking solution capable of scanning entire inventory storage and distribution centers Anyline, a mobile data capture and data insights, has introduced a new autonomous drone inventory management software that can scan an entire warehouse efficiently. Anyline worked with Mondi to develop this autonomous drone barcode scanning solution. Seeking to improve its inventory management process across multiple, large warehouse locations, Mondi tested several technology options including handheld RFID and camera scanners. A breakthrough was achieved when the company engaged Anyline to apply its mobile data capture technology to DJI Mini 3 Pro drones. “Taking inventory in a warehouse using autonomous drones was an exciting challenge and we were happy to partner with Anyline to make it a reality,” says Rainer Steffl, CIO at Mondi. “After several months of testing, problem-solving, and integrating with our backend systems, we have successfully counted our first full warehouse, proving the technology a success.” Before using barcode scanning drones, multiple workers used forklifts to manually lift two people at a time to scan inventory across large warehouses, sometimes only once per year. This process involves working at heights and, due to the need for space and extra safety measures, had to be done with overtime outside of warehouse operating hours. Now, a single drone operator can scan all the inventory aisle-by-isle in a warehouse during operating hours. The new modern process is safer, very accurate and alleviates a mandatory after-hours full warehouse count all at once. “Both Anyline and Mondi are passionate about innovation,” says Lukas Kinigadner, CEO and co-founder at Anyline. “We are proud to be a part of this project, which is redefining what is technologically possible in inventory management but can also be applied across other industries. We look forward to continuing to work with Mondi and other organizations redefining expectations and inspiring others to innovate and transform the way they work.” For more information or to explore similar collaboration opportunities with Anyline, interested parties can visit Anyline’s website or contact its customer support team directly.
New Renishaw TEMPUS™ technology achieves up to 50 percent reduction in additive manufacturing build times
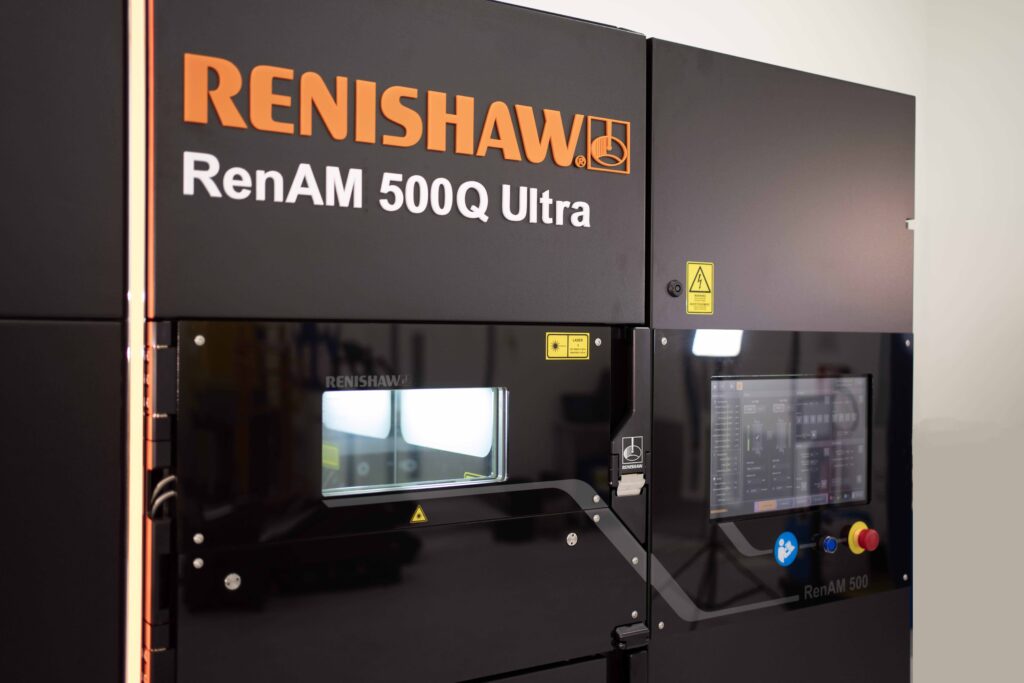
Patented technology enhances the class-leading productivity of the RenAM500 series metal additive manufacturing systems with reduced build times, detailed build insights and advanced process monitoring. New technology to be exhibited at the upcoming AAOS and RAPID shows. Renishaw’s new TEMPUS™ technology enables users of RenAM 500 series metal additive manufacturing (AM) systems to reduce build times by up to 50 percent. The technology uses advanced scanning algorithms that sequence the layer data in a way that maximizes productivity while maintaining part quality. The optimization suits some part geometries more than others, but all geometries can see some productivity benefits. Parts with thin, vertical features, for example, are likely to experience proportionally higher productivity savings. This new technology will be on display in February at the American Association of Orthopaedic Surgeons trade show (February 12-16 in San Francisco) and in April at the RAPID show (April 23-25 in Anaheim, CA). TEMPUS technology is standard with the new RenAM 500 Ultra system, as well as advanced process monitoring software. The combination of significantly reduced build times and detailed build insights means that the RenAM 500 Ultra delivers cost-effective, reliable additive manufacturing for metal component production. Existing RenAM 500 series customers can access TEMPUS technology as a paid-for upgrade, helping them to make the most of their machine investment. TEMPUS technology: jumping forward in AM productivity While traditional powder bed systems require the powder recoater to fully distribute powder before the layer can be consolidated, TEMPUS technology fires the lasers as the recoater is moving. The patented technology employs seamless communication between advanced software and hardware components to synchronize the system lasers with the powder recoater, removing up to nine seconds of build time from every layer. With builds frequently containing thousands of layers, this can reduce total build times by tens of hours. Yet crucially, there is no reduction in part quality. For uses in consumer electronics and computing, Renishaw has entered into an exclusive partnership agreement with metal component expert Alloyed, which has been using TEMPUS technology since 2021. “Reducing cost per part is critical to the wider adoption of AM technology,” explained Louise Callanan, Director of Additive Manufacturing at Renishaw. “The dominant contributing factor to part cost for most components today is the time spent building the part on the machine itself. Reducing the amount of machine time per part therefore results in more cost-effective production. “We believe the time and cost savings that both TEMPUS technology and the RenAM 500 Ultra system bring will open AM up to mass production applications where the technology would previously have been unviable,” added Callanan. “Meanwhile, these innovations will deliver crucial productivity gains for AM users who want full-scale production at the lowest cost per part.” The Ultra: The latest in the RenAM 500 Series The RenAM 500 Ultra system includes all the existing benefits of the RenAM 500 series – including industry-leading optical, chamber and gas-flow design – with the addition of the productivity-boosting TEMPUS technology. The RenAM 500 Ultra’s advanced process monitoring software delivers detailed insights into the build, equipping users with data and providing in-process visibility. Using the RenAM 500 Ultra to create production-ready metal parts means AM users can remain agile when faced with changing demands, are unrestricted by complex part geometries, and can seamlessly scale capacity to suit business needs. All of Renishaw’s RenAM 500 series systems, including the RenAM 500 Ultra, are available with one (500S) or four (500Q) high powered lasers, each able to access the whole powder bed simultaneously. This allows for efficient laser assignment and significantly higher build rates, improving productivity and lowering the cost per part. RenAM 500 Ultra models are equipped with automated powder and waste handling systems optimized for volume production. The RenAM 500 Ultra is available to order now.
Thomson video explores shift toward electrification of applications using linear actuators
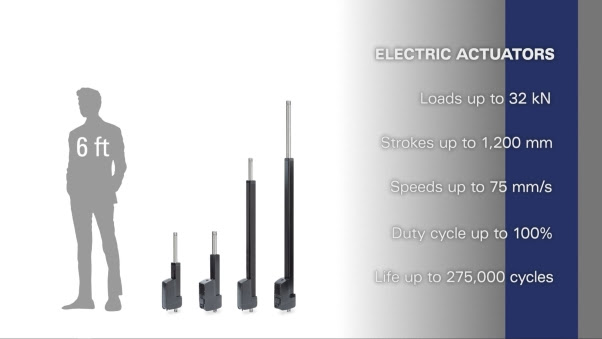
Thomson Industries, Inc, a manufacturer of linear motion control solutions, has released a video: ‘Clean and Simple: The Electrification of Applications with Linear Actuators,‘ which highlights the growing trend towards electric actuators and the advantages they bring over traditional technologies such as hydraulic, pneumatic and even manual actuation. For decades, hydraulic and pneumatic systems have been the preferred choice for heavy-duty applications. However, these systems pose challenges, including complexity, noise, high energy consumption, safety concerns, and adverse environmental impact. Electric actuators are now changing the game. This video explores the shift toward electric actuators, highlighting the increased load-handling capabilities that put them on par with hydraulic systems, as well as advanced controls and diagnostics that enable seamless communication with other machines in the network. The video also touches on numerous advantages of electric over traditional systems, including compact design, simplified wiring, and being entirely fluid-free, ensuring zero leaks, and minimal energy consumption and maintenance. “Electrification isn’t just a technological leap; it’s a profound transformation in how we approach motion control. It’s about harnessing efficiency, ensuring reliability, and securing a sustainable future,” said Travis Gilmer, Product Line Manager – Linear Actuators at Thomson. A prime example of how far electrification has come is the new Thomson Electrak® XD actuator, which can handle larger loads, longer strokes, and higher travel speeds, all with increased durability. Additionally, the XD goes toe-to-toe with hydraulics in shock load handling, making this unit versatile for various applications. Thomson’s commitment to innovation is driving the trend toward electrification in motion control applications. Their electric actuators are the embodiment of advanced controllability and safety and provide unparalleled durability. To explore these innovations further, click on the video link here – Clean and Simple: The Electrification of Applications with Linear Actuators | Thomson (thomsonlinear.com).
Registration for Queen City Robotics Alliance 2024 Summer Camps now open
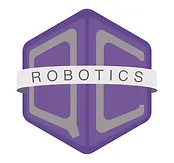
Come build bots with us! Registration for Queen City Robotics Alliance (QCRA) 2024 Summer Camps is open so now is the time to sign up your kids for summer fun. These weekly camps offer students ages 9-13 (Grades 4-8) the opportunity to learn about and program robots in a collaborative, hands-on environment while learning valuable STEM lessons and real-world life skills. These camps will also introduce students to FIRST® LEGO® League (FLL) Challenge programs where they will learn how to build a robot and bring it to life. Camps are in one-week, all-day sessions beginning June 24 and run through the week of August 5. All camps take place at The Zone, QCRA’s home for robotics learning. In the morning students will learn coding led by QCRA’s talented peer instructors while in the afternoon the kids will take what they learned to solve an FLL Challenge. On the last afternoon of the camp, students will display their new talents in a robot showcase. Coding experience is not necessary, but students will need a laptop computer. Contact QCRA to request a computer loan if needed or parents and guardians can purchase a low-cost laptop from E2D. A brown bag lunch is also recommended. The cost is $320 per student. With special thanks to our longtime sponsor Sullenberger Aviation Museum, QCRA has grants available to families with financial need. Slated to open Summer 2024, the museum is working to increase accessibility and inclusivity in STEM education for students across the region. “At Sullenberger Aviation Museum, we support our longtime partner Queen City Robotics Alliance,” said Misty Sweat, VP of Education for the museum, “by funding camperships for their summer camps and providing financial aid towards STEM exposure for students lacking economic means. This initiative aligns with our mission to inspire, educate, and elevate the next generation of innovators through accessibility and inclusivity for those that have been historically underrepresented in STEM careers.” Learn more about the camps or to sign up your budding robotics student.
SINAMICS G115D distributed drive system specifically designed for conveyor applications
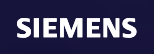
Comprised of the drive, motor, and gearbox, this new distributed drive system is available as a complete solution for motor-mounted and wall-mounted horizontal motion control conveyor applications. With its new SINAMICS G115D, Siemens is introducing a new, compact, and powerful drive system specifically designed for horizontal conveyor applications. The drive system comprises the motor, drive, and gearbox in one unit and is offered in two versions — wall-mounted and motor-mounted. The SINAMICS G115D drive system is characterized by a robust design with a high IP protection class (up to IP66 / UL Type 4X) and is suitable for use in harsh environments. Thanks to its compact dimensions, the SINAMICS G115D can be easily installed in confined areas. The drive system can also be operated reliably over a wide temperature range of -30 to 55 degrees Celsius (-22 to 131 degrees Fahrenheit), enabling operation in deep freezing applications. SINAMICS G115D is suitable for applications in intra-logistics and airports, as well as in the automotive and food and beverage industries. Its power ranges from 0.37 to 7.5 kilowatts (1/2 to 10 hp) for wall-mounted applications and 0.37 to 4 kilowatts (1/2 to 5 hp) for motor-mounted applications. The drive system can be put into operation quickly and easily with comprehensive integration into the Totally Integrated Automation (TIA) portal including Startdrive commissioning software or the SINAMICS Smart Access Module (SAM) web server for Wi-Fi setup and diagnostics. To be prepared for digital transformation and to enable cloud-based analysis, SINAMICS G115D is integrated into the entire MindConnect portfolio and is compatible with MindSphere applications such as Analyze MyDrives. Thanks to Profisafe, the SINAMICS G115D has Safety Integrated in the form of STO (Safe Torque Off) SIL2, which standardizes and facilitates the certification process. For flexibility in terms of installation, service, and maintenance, the solution is equipped with a plug-in connector and flexible connection possibilities. The device is particularly suitable for interaction with SIMATIC controllers such as the S7-1200 or ET200 for motion control. Siemens offers warranty extensions for SINAMICS G115D through its Service Protect package. As part of this service package, an additional one or two-year warranty extension may be purchased for failure coverage. The package offers simplified processing under normal warranty conditions for an extended period.
Movu Robotics and Reesink Logistic Solutions: A powerful alliance transforming warehouse logistics with innovative solutions
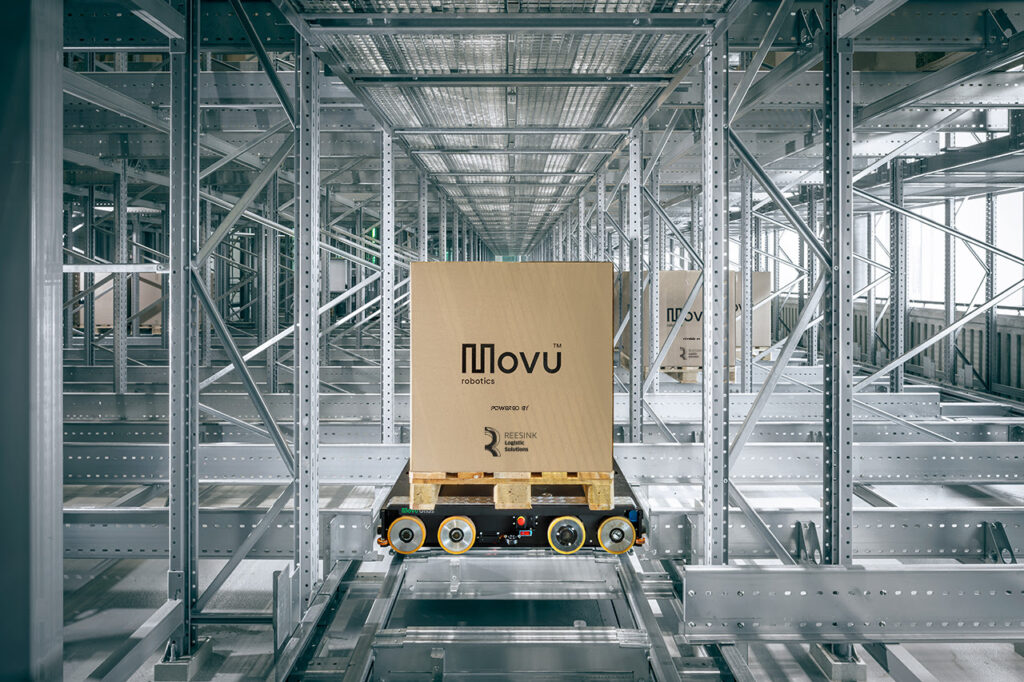
Movu Robotics is proud to spotlight their enduring partnership’s success through groundbreaking projects across Europe. Highlighting their successful long-term collaboration, two flagship projects for the Weinig Group in Germany and B&S in The Netherlands showcase the partnership’s innovative approach to logistics challenges, including a first-of-its-kind venture into next-level cold store logistics. Tailored Solutions for the Weinig Group In Germany, the Weinig Group, renowned for its wood processing technologies, will benefit from a compact and high-performance automated pallet & item storage and retrieval system designed by Reesink Logistic Solutions. This cutting-edge system streamlines the flow of parts, semi-finished and finished products, significantly enhancing efficiency and reducing manual handling using a Movu atlas pallet shuttle system. The solution underscores the beauty of a unique fit-for-purpose solution in the manufacturing and processing industry. Innovative Cold Store Logistics for B&S The B&S project in The Netherlands takes automation a step further with its unique concept for a pallet-based Goods-to-Person Solution in a cold store environment. Within this project, the Movu atlas pallet ASRS, the Movu ifollow AMRs, the pallet conveying system and the FAST PICK STATIONS are combined into this unique, state-of-the-art and scalable pallet-based Goods-to-Person solution. Both the Movu atlas shuttles and the ifollow AMR’s can operate in temperatures ranging from -25 to +40°C. The B&S solution exemplifies how Reesink and Movu’s innovative technologies can be utilized to meet the stringent requirements of temperature-controlled warehousing while ensuring operational excellence. The Power of Collaboration Machiel van den Hazelkamp, Commercial Director at Reesink Logistic Solutions, states, “Our enduring partnership with Movu Robotics is instrumental in our mission to provide our customers with future-proof, next-level warehousing solutions maximizing their competitive position. The projects for the Weinig Group and B&S not only demonstrate our joint capability to tailor our standard products into unique solutions in response to our client’s specific needs but also highlight our commitment to advancing logistics technology in both standard and challenging environments like cold stores.” Future-Focused Movu Robotics and Reesink Logistic Solutions are pioneering the future of logistics by focusing on high-density storage, scalability, flexibility, sustainability, and the integration of advanced technologies. They’re leading the shift towards eco-efficient operations, ensuring their solutions can adapt to changing market demands using minimal space. By integrating advanced technologies, they’re setting new efficiency standards, making warehousing smarter and more responsive. This strategic emphasis positions them at the forefront of sustainable and flexible logistics innovations, ready to meet tomorrow’s challenges today. Leaving no warehouse behind with next-level solutions Movu Robotics, known for its innovative warehouse automation solutions, brings to this partnership its expertise in robotics and automation technology. The Movu atlas and ifollow solutions represent a significant advancement in pallet handling. With more than 50 years of experience in warehouse automation, Reesink Logistic Solutions brings a wealth of knowledge and a track record of integrating over 850 warehouse automation projects. Together, Movu Robotics and Reesink Logistic Solutions are set to redefine the standards of warehouse automation, delivering solutions that are not just efficient and cost-effective, but also tailored to the unique needs of each warehouse.
Magline Inc. announces leadership changes

Magline, Inc., manufacturer of Magliner® aluminum and steel material handling equipment, has announced the promotion of Greg Ecker to Chief Executive Officer and the addition of Mike Howard as President and Chief Operations Officer. “Magline has experienced strong and steady growth under Greg’s guidance. His appointment by the Board to the position of CEO is recognition of this past success and a strong vote of confidence in his ability to lead us to new heights,” said Bruce Law, Chairman of Magline’s Board of Directors. “Greg will shift his focus and attention to business development, growth, and corporate strategy.” Ecker joined Magline as Global Supply Chain Director in 2007 and held executive positions in Operations, Sales, and Marketing before being named President and Chief Operating Officer in 2013. Prior to joining Magline, Ecker held senior positions with Whirlpool Corporation and Electronic Data Systems. Howard, a Michigan native, joins Magline following leadership positions as President of Judson Smith, an ATW Company, and General Manager at a division of Parker Hannifin. He earned a Bachelor of Science degree from Western Michigan University and a Master of Business Administration from Michigan State University. “Mike’s hands-on approach, enthusiasm, eagerness to learn, and passion for helping individuals achieve new levels of performance strongly position him to have a meaningful impact on people and achieve organizational success,” stated Ecker. “I am excited to be joining this well-respected organization and the opportunities to continue the growth and success of the organization,” stated Howard. “I am happy to be back in Michigan and in a position to contribute to the ongoing legacy and value proposition Magline holds in the markets we serve.”