Powering the warehouse: Battery and Chargers are key to successful operations
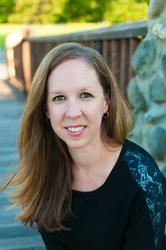
Powering equipment is one of the main considerations of any material handling operation. What type of battery power to use and how much of an investment to make. How to match a business’ objectives with evolutions within the industry. All are often top-of-mind when establishing an operation’s power system. This month, Material Handling Wholesaler looks at some of the trends in batteries and chargers, along with how some companies are thinking about energizing equipment. New tech and trends Flight Systems Industrial Products offers battery chargers and modules, controllers, dash displays, joysticks, the Xtender Battery Regenerator and other battery management products to service markets, according to the business website. Dustin Love, business development manager, said the company is preparing to launch a product that will improve lithium-ion battery shipping safety by discharging battery energy. “Right now, there’s not really regulation when it comes to shipping lithium batteries,” said Love, noting that the safest shipping would be for a battery to be at zero volts. The Flight Systems’ machine, called The Battery Terminator, can discharge a battery all the way down to negative 2 volts, according to Love. The Battery Terminator would largely serve the material handling market, although Love foresees it having a lot of use in automotive markets and even scrap yards as well. Love explained that lithium-ion batteries are supposed to last around 15 years. The popularity of the batteries has been growing in recent years, and soon there will be a time when replacements are needed. “At some point, there’s going to be a large bottleneck. We are trying to get ahead of the game,” he said. Also in new technology, Flight Systems has begun selling a wireless charger. The 1-kilowatt charger includes a charging pad on the vehicle that connects wirelessly to a wall charger. Love added that more powerful options are coming from the company this year and that the wireless chargers are mainly for AGVs and AMRs. “You can program robots to drive up to them and start charging,” Love said. While lithium-ion power is “the talk of the town,” Love does not predict a complete shakeup of the market in the near future. “When it comes down to it, lead acid is still king. I don’t think it’s going to go anywhere for some time,” he said. Love noted that while lead acid batteries require certain types of work to maintain, lithium-ion batteries come with their own type of operational maintenance. “Lead acid requires watering and equalized chargers. Lithium has tech programs and troubleshooting. It’s just a different kind of maintenance,” he said. On the lithium side, Love noted that there are developments outside of material handling occurring on CAN signals. “If you look at the automotive market with lithium, there used to be two different CAN signals. “Now it’s pretty much compiling into one,” he said, noting that in material handling, signals differ by various manufacturers. “In order for lithium to really have a hold in the market, there will need to be some kind of compliance on the BMS protocol side, a more uniform approach to charging the batteries,” Love said. A holistic approach At Raymond Corporation, a variety of vehicle integration and power types are offered, including lithium-ion, lead-acid and more, according to the website. Raymond recently expanded its line of advanced energy solutions with the launch of the Energy Essential Distributed by Raymond® 48-volt drop-in lithium-ion battery (48V LIB), which is available in multiple configurations, according to the business. Damon Hosmer, general manager of Raymond’s Energy Storage Solutions, agrees with Love that lithium-ion and hydrogen fuel cell power are “hot topics” currently. “Those are the big trends that we tend to hear about a lot,” he said. Hosmer said customers lately have been taking a more holistic approach to establishing energy in an operation; considering technology, ways to reduce facility demand and more. “Energy and labor are the two most prevalent pain points,” he said, noting interest in the industry in reducing the footprint of banks of chargers in battery rooms, concerns about safety, and pursuit of sustainability. Hosmer said Raymond’s thin plate pure lead batteries have been “a really exciting effort” over the past three years. The TPPL batteries are a solution especially helpful in facilities with cold storage, according to Hosmer. In 2024, Hosmer predicted new technology will emerge domestically and he believes wireless charging will be in demand. “Wireless charging is really coming into place,” Hosmer said. As to types of battery power, lithium-ion technology does present certain advantages, according to Hosmer. “Lithium has really emerged as the superior option from a performance perspective. The standard one-size-fits-all approach with lead acid may not be optimal,” he said. Overall, expectations concerning energy are at a high level in the industry, according to Hosmer. “They expect the highest level of performance,” he said, noting that OEM’s are now working to keep up with the rapid pace of change. “The technology that comes out is changing daily,” he said. Raymond is working to help customers navigate evolving technology and policy, including implementation of the Inflation Reduction Act. Sustainability sourcing is also key within the industry, including end-of-life stages for batteries, Hosmer said. “Another advancement this year is the continued efforts around recycling,” said Hosmer, who said Raymond is helping close the gap around misconceptions related to recycling in the lithium-ion space. “It’s interesting to see the development of the value of those secondary life materials,” Hosmer said. A ‘mainstream’ product Green Cubes Technology, producer of lithium-ion power systems, announced late last year that the company had sold 10,000 of its Lithium SAFEFlex Battery. In terms of watt hours, that totals 297 megawatt hours, according to Robin Schneider, director of marketing. Schneider said the company sees lithium-ion power as being aligned with more mainstream expectations of customers. “Lithium-ion products in general have gone from an early adopter experimental phase to a mainstream product,” she said, adding that now for some customers considerations are focused on commissions of larger installations, as opposed to one or two experimental models. As to reuse, Schneider said that although Green Cubes has
Screwy numbers
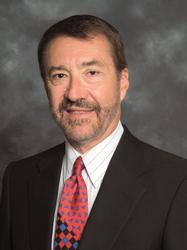
I spend a good couple of hours each day reviewing stock markets and other investment commentary. Always loved investment adventures and even produced my MBA thesis discussing the merits associated with distressed long-term bonds. And guess what? For the period I was covering returns from buying distressed long-term bonds produced above average returns if you select bonds of companies that have a good chance of covering their debt service and paying off the bond on the original due date. As it turns out there is a service available to find the “good” distressed bonds if you are interested. During my daily review of the market, I keep hearing about this Company and that Company reporting earnings for the month or quarter. It seems the most important number is the sales number and how sales have increased consistently over the last couple of years. Thinking about that I say to myself, “If inflation hit 30% for inventory and other operating costs should I not have an increase in sales, even if unit sales took a hit?” HHHHHMMMM? Next question is: If sales increased, did I make more money? Next question is: How about additional cash flow? Considering that every $ of increased sales requires more capital to support it, how did I make out having a larger floor plan and higher AP balances. It is no secret that you need to spend money before you collect money, and thus the increase is working capital to cover the spread. Next Question is: Even if you believe you covered the price increases for new and used equipment, did you Increase margins enough to cover increases in operating expenses, payroll, and interest expense. It is also a time to compare actual activity along with sales dollars: Did you sell more new units and maintain margins? Did you sell more used units and maintain margins? Did you sell more parts and maintain margins? Did you sell more hours and maintain margins? Was your overall required gross margin attained? Does the total gross margin cover total operating expenses including interest? And when you consider that last question about covering total operating expenses and interest you must understand that this is a moving target since the monthly inflation rates keep jumping around, which means pricing may need to be adjusted throughout the year as expenses keep increasing. For example, if you have new units costing $20000 in your inventory and then received a delivery with a cost of $26000 and your goal is a minimum 13% gross margin on the sale, the selling price on the $20000 unit would be $23000 with a $3000 margin, with the newer more expensive unit requiring a $29900 price and $3887 margin at 13%. All in all, the cost, sales and gross profit all increased 30%, leaving you with an additional $887, some of which will cover increased expenses such as floor plan interest, insurance as well as contribute to expense increased operating expenses. You must go through this exercise for each profit silo to determine if the overall results and better than the previous year as well as the current year budget. If you are not careful this could turn into a full-time job. Maybe you can get AI to help you. If you are like the car dealers many of you are sitting on these high price units you ordered that you eventually received a year late, leaving you wonder what you are going to do with them. This is a BIG DEAL because Sally down the street avoided the high price unit problems and is now ready to sell units for less than you can. Now what? Do we give up the business? Do we take a hit on the sales? Do we buy Sally out? I guess you have some play with the pricing but wish to avoid giving up that $887 if you can help it. Do these enough times and the margin for the year will turn downward. And considering that new and used sales drive aftermarket sales, you do have to be careful not to upset the apple cart. What you do not want to do is sit on these higher priced units. The pricing will only get worse as time moves on. And I assure you that your banker will eventually ask you to pay down the units to an acceptable collateral number. So, it is better to find some kind of solution now to avoid a hit to the cash account. What to think about: Are there dealers who need inventory you can sell to at your cost to get it off your balance sheet? Can you work out a rental program using these units where you can transfer part of the risk to a future period? Can you sell off rental assets that are priced at the current levels and replace them with the new units to rent them out to pay down the units to a value where you can be competitive with pricing? Can you get the OEM to help? You also must consider these same issues with your parts department. You have parts at the old low cost mixed in with a good percentage of newer parts at the higher prices. If you’re using the first-in first-out method to account for parts costs, your current sales and going to look good but it will not look so good when the lower priced units are gone leaving you with a parts cost 30% higher when we are probably in a recession where business is slowing up at the same time. And consider that your customers will not what to pay the “higher” parts costs. It’s funny how they always have a handle on this sort of transaction. And if the economy does slow down with inflation following along, it probably means we are in a recession where you will start hearing the word “deflation” caused by vendors trying to unload excess inventory. Will it happen in your industry….
Achieve precision product movement with the new DualMove Pallet System Conveyor
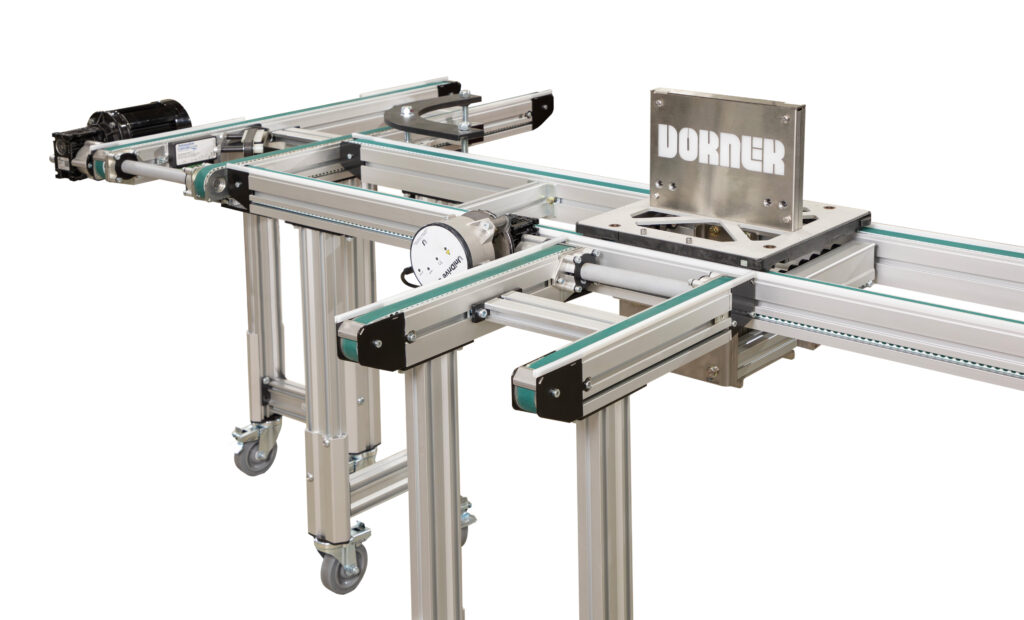
Dorner, a conveyor technology, has introduced the new DualMove Pallet System conveyor. This product excels in many applications, including – but not limited to – electronics, appliances, automotive, and battery production. Joining Dorner’s collection of innovative pallet systems, the DualMove utilizes twin-strand timing belts to precisely place, orientate, and transfer pallets to workstations for robotic or human interaction. DualMove completes the portfolio of Dorner’s pallet system offering, providing a more cost-effective option for those needing to move products safely and securely. DualMove is a fully configurable conveyor with seven different pallet lengths and widths and several accessory modules, allowing you to customize it to your unique requirements. Because of the variety of pallet sizes, it can carry a load of up to 100 lbs. per pallet, making it perfect for small to medium-sized appliances and electronics that require assembly and packaging processes to be completed. DualMove is easily configurable with several options that help end users achieve the production goals needed. Both regular and heavy load corners allow for seamless navigation of pallets. Accessory modules such as lift and transfer, lift and locate, and lift and rotate allow DualMove to prioritize getting products where they need to be on time and in the correct position. Diving into the standout attributes and benefits of the DualMove: Extruded Aluminum Frame: Increasing flexibility with a sturdy framing with an industry-standard T-slot Low Product Lead Time: Dorner’s production process is designed to get solutions to customers faster than the competition. For standard DualMove products, you can expect an industry-best lead time of 20 days or less. Larger T10 Timing Belt: The DualMove has been outfitted with a larger T10 timing belt that allows for increased load capacity and strength. Flexibility of Automation Sensors or Equipment: The DualMove can be equipped with automation sensors and modules to meet product requirements. Engineered Excellence: DualMove is designed with the end user in mind by promoting easy installation and configuration based on unmatched flexibility in construction, utilization, and process matching. Take the next step in your automation journey with the DualMove Pallet System – where robust strength, unparalleled versatility, and innovative engineering combine to elevate your production.
PAC Machinery to show maximum flexibility in packaging options MODEX 2024
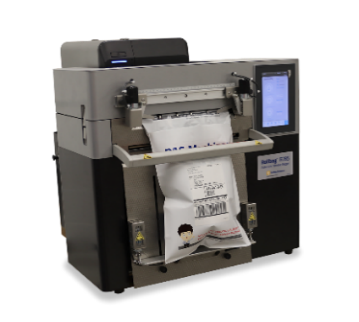
PAC Machinery, a packaging industry with a range of equipment, will exhibit at MODEX 2024 several packaging options that save companies money on materials, help increase production, and provide flexible solutions for sustainable packaging. The MODEX Expo is held at the Georgia World Congress Center in Atlanta, GA, March 11-14, 2024. The most exciting and latest option in automatic bagging and fulfillment will be the focal point of PAC Machinery’s exhibit. See the flexible Rollbag® R3200 Fulfillment Automatic Bagger that can run with three different types of material for added cost savings and versatility in sustainable packaging that includes PAC Machinery’s sustainable poly bags made with at least 25% recycled resins (available up to 100% recycled resins). Additionally, the R3200 Fulfillment works with Fiberflex® curbside recyclable paper packaging for plastic-free packaging that will be running on the machine at Modex. This versatile bagger can also run using PAC’s proprietary poly tubing that makes the bag to the length of a product, reducing material usage and cost. “We are excited to showcase the combination of our most versatile bagger with the first-ever paper packaging for automatic bagging, Fiberflex, that is curbside recyclable, said Greg Berguig, Vice President, PAC Machinery. “Fiberflex is a plastic-free packaging option for select PAC Machinery Rollbag bagger models and on one of our flow wrapper models, Berguig said. Paper packaging for packaging automation is one of the newest environmentally friendly advancements in the packaging industry today. Modex attendees can see this new innovative packaging solution at PAC Machinery’s exhibit located at #C4488. PAC Machinery will also be exhibiting the top-selling Rollbag R785 tabletop bagger with a thermal transfer printer – a great first bagging machine with the ability to print directly on the bag. This machine can package items in mailers or clear poly bags up to 12” wide. See PAC’s largest bagger, the R3200XL Fulfillment bagger that works with bags up to 22″ wide x 36″ long. This powerhouse packager is for larger items and gives manufacturers the ability to also print on the bags and right-size the bag to the product for additional savings using poly tubing. In addition, PAC Machinery automatic baggers will be running with poly bags made with at least 25% recycled resins, showcasing sustainable packaging. MODEX 2024 is expected to be the largest supply chain and logistics show of the year and automated packaging equipment and materials with flexibility and sustainability like PAC Machinery will exhibit is sure to be one thrilling and informative exhibit at C4488.
Port of Long Beach prepares for ‘Year of Rail’ in 2024
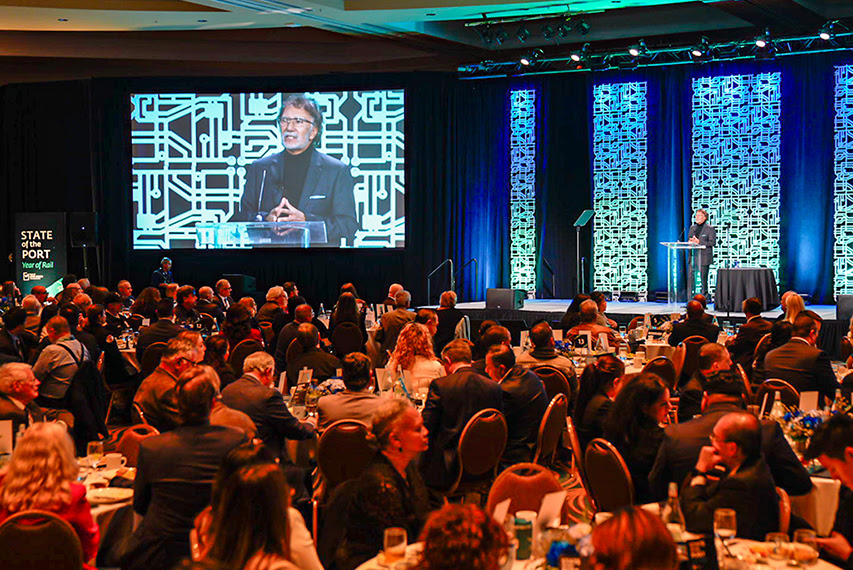
State of the Port highlights construction, zero-emissions goals “The Port of Long Beach is laying the tracks for a sustainable future by modernizing rail facilities and enhancing air quality,” CEO Mario Cordero said Wednesday during his seventh State of the Port Address. To make Long Beach the world’s first zero-emissions seaport, Cordero announced construction will start this year on the Pier B On-Dock Rail Support Facility, which aims to move cargo more quickly, make the port more competitive, and improve the environment for nearby communities. “Today, I can represent to you that the state of our Green Port is strong,” Cordero told 800 industry partners, community members, and civic leaders gathered at the Long Beach Convention Center Grand Ballroom for the State of the Port address – available for viewing now. “We have gone through one of the greatest challenges with the COVID-19 pandemic – and we’ve emerged, still the premier gateway for trans-Pacific trade,” Cordero said. “At the end of this decade, the Port of Long Beach will be on the cusp of not only operational transformation given our rail investment but also environmental transformation – to a zero-emission port.” As the centerpiece of the Port’s on-dock rail projects, the state-of-the-art Pier B On-Dock Rail Support Facility will move freight faster and more sustainably. It will double the size of the existing Pier B rail yard to 171 acres and more than triple the volume of on-dock rail capacity handled annually to 4.7 million twenty-foot equivalent units (TEUs). More than 1,100 construction-related jobs will be created by the $1.567 billion project, which will be built in phases and is scheduled for completion in 2032. So far, the Port has secured $643 million in federal, state, and local grant funding to help complete the Pier B On-Dock Rail Support Facility – more than $500 million of which was awarded in 2023. “Pier B will enhance the Port’s competitiveness, maintain its role as an economic force for the region, and serve as a sustainability model for ports in the U.S. and abroad,” said Long Beach Harbor Commission President Bobby Olvera Jr. “We’re rebuilding, electrifying equipment and decarbonizing operations while developing the skilled human talent that will make the Port thrive for decades to come.” The Port closed 2023 with 8,018,668 TEUs moved, down 12.2% from 2022 and slightly ahead of pre-pandemic levels reported in 2019. Imports declined 12.7% to 3,804,356 TEUs and exports decreased 9.4% to 1,282,437 TEUs. Empty containers moved through the Port were down 12.7% to 2,931,876 TEUs. For complete cargo numbers. “The Port continues to be an engine for economic activity for the city and region, a leader in decarbonizing the maritime industry, and a positive force in nearby communities,” Long Beach Mayor Rex Richardson said. “And while we continue to innovate and revolutionize goods movement, we are developing the skilled workforce needed to move cargo in the future.” More than $792 million in grants from federal, state, and local sources were secured in 2023, marking a record year of public investments for infrastructure, security, and clean air initiatives that will further the Port of Long Beach’s goal to transition to zero-emission cargo handling by 2030 and zero-emissions trucking by 2035. Cordero said he anticipates additional funding over the coming year for several projects, including the Port’s effort to develop a “hydrogen hub” that would fuel cargo-handling equipment with zero-emissions technology. Additionally, progress will continue through the next year to develop Pier Wind, a proposed 400-acre terminal designed to facilitate the assembly of offshore wind turbines, which would be towed to wind farms in the ocean off Central and Northern California. If approved, the proposed Pier Wind project would be the largest facility of its kind in the nation and would help California meet its goals for renewable energy sources. Later this year, interactive and immersive exhibits highlighting the Port’s history, operational achievements, and environmental stewardship will be on display with the opening of the Congressman Alan Lowenthal Global Trade and Education Center. Located within the Port Administration Building in Civic Center Plaza, the 10,000-square-foot space is named for Lowenthal, who represented Long Beach in the state Legislature from 1998 to 2012 and in Congress for 10 years until his retirement in 2023. The Port of Long Beach is a global leader in green port initiatives and top-notch customer service, moving cargo with reliability, speed, and efficiency. As the premier U.S. gateway for trans-Pacific trade, the Port handles trade valued at $200 billion annually and supports 2.6 million jobs across the United States, including 575,000 in Southern California. In 2023, industry leaders named it “The Best West Coast Seaport in North America” for the fifth consecutive year. During the next 10 years, the Port is planning $2.2 billion in capital improvements aimed at enhancing capacity, competitiveness, and sustainability.
AutoScheduler adds Stephen Zujkowski to executive team as Vice President
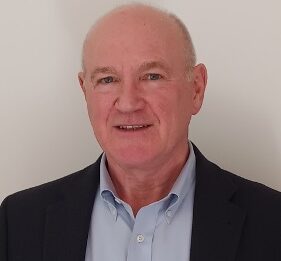
AutoScheduler.AI, an innovative Warehouse Management System (WMS) accelerator, has announced that Stephen Zujkowski has joined the company as the Vice President of Customer Success. With over thirty years in the supply chain industry, Stephen will bring his extensive experience to help AutoScheduler grow profitably and achieve scale while driving value in customers’ supply chains. “Stephen will be the critical guiding force that oversees our deployment strategy, metric capture and tracking, and overall customer delivery success,” says Keith Moore, CEO of AutoScheduler.AI. “He will be the face of success for all AutoScheduler’s customers, ensuring the talented team continues delivering exceptional services and fostering true partnerships.” “The executives at AutoScheduler are some of the most innovative in the industry, and I am pleased to join them to focus on improving deployment processes and measuring KPIs in customer success,” says Stephen Zujkowski, Vice President of Customer Success at AutoScheduler.AI. “I will ensure customer satisfaction is central to business decisions throughout the organization.” As Vice President of Customer Success, Stephen is responsible for overseeing the strategy, execution, and management of all aspects related to customer deployments and satisfaction. He will ensure that customers derive maximum value from AutoScheduler, leading to improved fulfillment, better labor utilization, and lower costs. As the leader in the Customer Success organization, he will drive measurable positive business outcomes, customer satisfaction, retention, and expansion across the customer base. Previously, Stephen was VP, Global Supply Chain IT at CHEP, a Partner in the Supply Chain practice at Accenture, and a Vice President at Oracle Corporation. He has extensive experience installing and operating Supply Chain technology solutions along with hands-on experience managing warehouses. He combines operations and technology expertise to capitalize on rapidly changing business imperatives. He graduated with a BS in Logistics from Penn State University. He received his MBA in Finance from Fairleigh Dickinson University.
Registration opens for ASSP’s Safety 2024 in Denver
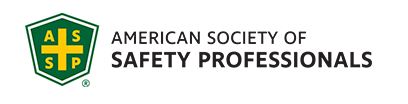
The American Society of Safety Professionals (ASSP) has opened registration for its signature safety education event, held two months later than usual this year. The Safety 2024 Professional Development Conference and Exposition is set for Wednesday, Aug. 7, to Friday, Aug. 9, at the Colorado Convention Center in Denver. Safety 2024 offers workplace safety and health professionals a vast networking experience while highlighting best practices, industry trends and the latest product innovations. More than 200 continuing education sessions will provide practical information that safety professionals can immediately put to use at their organizations. “Our conference and expo is a dynamic learning and networking experience that supports our mission to help protect workers in every industry worldwide,” said ASSP President Jim Thornton, CSP, CIH, FASSP, FAIHA. “It’s a place to find real solutions to occupational safety and health challenges, especially now when environments can quickly change. We’re excited about the experience we have in store for attendees.” Thousands of safety and health professionals look to ASSP’s annual conference – now in its 63rd year – to advance their careers and interact with experts who will share proven techniques for elevating safety at their companies. Attendees will also be inspired, entertained and informed by popular general sessions. As a focal point of the event, the exposition will feature more than 500 exhibitors showcasing innovative safety solutions that can help organizations eliminate hazards and risks that cause injuries, illnesses and fatalities. The expo floor will include an expanded Career Advancement Center that will serve all attendees, not just those looking for a new position. “Our expo is so illuminating and engaging that safety and health professionals find it just as educational as the sessions,” Thornton said. “Many vendors also bring their product developers and present meaningful learning opportunities.” Safety professionals can earn 1.5 continuing education units (CEUs) for career advancement. Register online to get the discounted early rate through March 21. “If your job involves the safety and health of your organization, Safety 2024 is the place to gain critical insights and knowledge to advance your work environment,” said Stephanie Gurnari, CSP, chair of ASSP’s Professional Development Conference Planning Committee. “It’s a comprehensive experience that provides significant value for occupational safety and health professionals at every level of experience.” Denver is one of the most popular locations for ASSP’s events. The pedestrian-friendly Mile High City is known for its natural beauty with more than 200 city parks and views of the Rocky Mountains. There are trendy restaurants and cafes, a thriving arts scene and countless outdoor activities, such as kayaking on the river that runs through downtown. At the State Capitol, the 13th step is exactly 5,280 feet above sea level.
Queen City Robotics Alliance prepares at their new facility for 2024
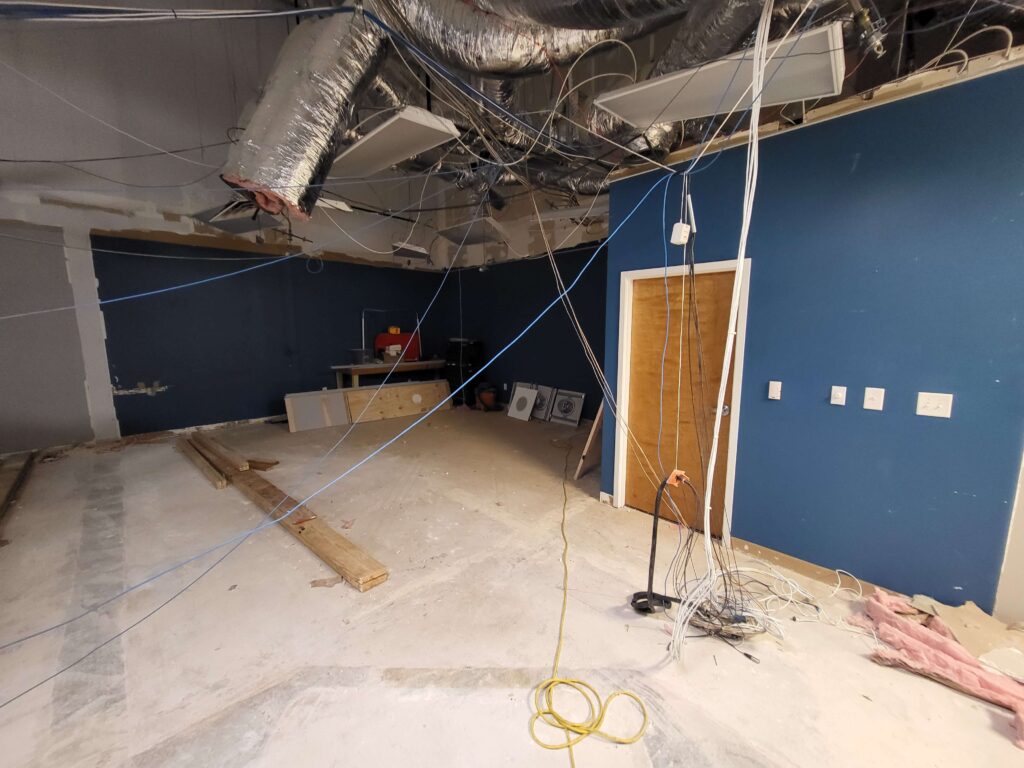
Queen City Robotics Alliance (QCRA) recently finished updates and construction of several important projects at The Zone, a 3,000 sq. ft. practice field. On January 6, students and mentors were at The Zone where they learned about the upcoming FIRST® Robotics competition season and received their Kickoff Kits. The 2024 theme is Crescendo presented by Haas. As QCRA and Charlotte-area FIRST Robotics teams get ready for competition, they will be a part of some 3,500 robotics teams around the world participating in Crescendo, which has a theme revolving around music, sound, and performance as part of the robotic competition. New Avian Robotics 9005 team member Alex C. of East Mecklenburg High School had this to say about his first competition season. “I expected my team to be very serious and purely focused on one goal. However, this was not the case. I was greeted with many smiles and helpful advice on how to improve myself, not just as a future engineer, but as a human being in general. It is very fun being around them and I look forward to building our new robot with them.” Avian Robotics lead mentor Annette Miller was also enthusiastic. “I am so excited about the game itself. It requires lots of thinking and planning and more involvement from the team and our alliance. I feel it gives new teams like ours more opportunities to be successful. I am looking forward to lots of ‘light bulb moments’.” Last September, QCRA moved into a new, larger facility called The Zone in Charlotte’s Ayrsley neighborhood and it is a space where Charlotte area robotics teams can strategize and practice while building teamwork and organizational skills. QCRA also uses The Zone to hold after school and summer computer coding and drone camps open to all Charlotte area students. However, the former marketing research space needed some upgrades to make the space work for QCRA students. First the HVAC and electrical needed an upgrade so everyone could be comfortable through the changing seasons. Next was the creation of the robot practice field. That project involved knocking down several walls to create a 3,000-sq. ft., 16-ft. high practice field where teams can prepare their robots for competition. Locke Hudson of commercial real estate company JLL not only helped QCRA find the new facility, but oversaw the renovations and provided this update on the new space. “It’s exciting to be wrapping up the project to create a dedicated playing field area at The Zone. The completed playing field will be a unique asset for QCRA teams as there is not another dedicated field with a 100-mile radius and allows teams to have hands-on experience testing and practicing with their designs.” “This project was a team effort,” he added, “and would not have been possible without the financial backing and the partnership of our landlord’s property manager Frank Bass, GC Stocker Associates, and the significant in-kind donation of Ray Kimble who performed all of the electrical work.”
U.S. Rail Traffic for the week ending January 13, 2024
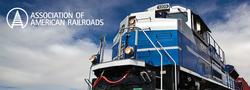
The Association of American Railroads (AAR) today reported U.S. rail traffic for the week ending January 13, 2024. For this week, total U.S. weekly rail traffic was 457,453 carloads and intermodal units, down 4.1 percent compared with the same week last year. Total carloads for the week ending January 13 were 213,277 carloads, down 10.2 percent compared with the same week in 2023, while U.S. weekly intermodal volume was 244,176 containers and trailers, up 1.9 percent compared to 2023. Three of the 10 carload commodity groups posted an increase compared with the same week in 2023. They were chemicals, up 2,591 carloads, to 33,076; petroleum and petroleum products, up 389 carloads, to 10,374; and forest products, up 80 carloads, to 8,193. Commodity groups that posted decreases compared with the same week in 2023 included coal, down 10,924 carloads, to 58,478; grain, down 8,017 carloads, to 18,776; and nonmetallic minerals, down 4,515 carloads, to 25,446. For the first two weeks of 2024, U.S. railroads reported a cumulative volume of 421,453 carloads, down 5.0 percent from the same point last year; and 453,257 intermodal units, up 2.7 percent from last year. Total combined U.S. traffic for the first two weeks of 2024 was 874,710 carloads and intermodal units, a decrease of 1.1 percent compared to last year. North American rail volume for the week ending January 13, 2024, on 12 reporting U.S., Canadian, and Mexican railroads totaled 316,875 carloads, down 9.1 percent compared with the same week last year, and 319,987 intermodal units, up 0.4 percent compared with last year. Total combined weekly rail traffic in North America was 636,862 carloads and intermodal units, down 4.6 percent. North American rail volume for the first two weeks of 2024 was 1,222,708 carloads and intermodal units, down 1.5 percent compared with 2023. Canadian railroads reported 86,253 carloads for the week, down 10.8 percent, and 64,295 intermodal units, down 8.3 percent compared with the same week in 2023. For the first two weeks of 2024, Canadian railroads reported a cumulative rail traffic volume of 295,353 carloads, containers, and trailers, down 4.9 percent. Mexican railroads reported 17,345 carloads for the week, up 19.0 percent compared with the same week last year, and 11,516 intermodal units, up 25.8 percent. Cumulative volume on Mexican railroads for the first two weeks of 2024 was 52,645 carloads and intermodal containers and trailers, up 16.3 percent from the same point last year. To view the Rail Traffic charts, click here.
Episode 453: Charting New Paths in E-Commerce and 3PL with Yong-Soo Chung
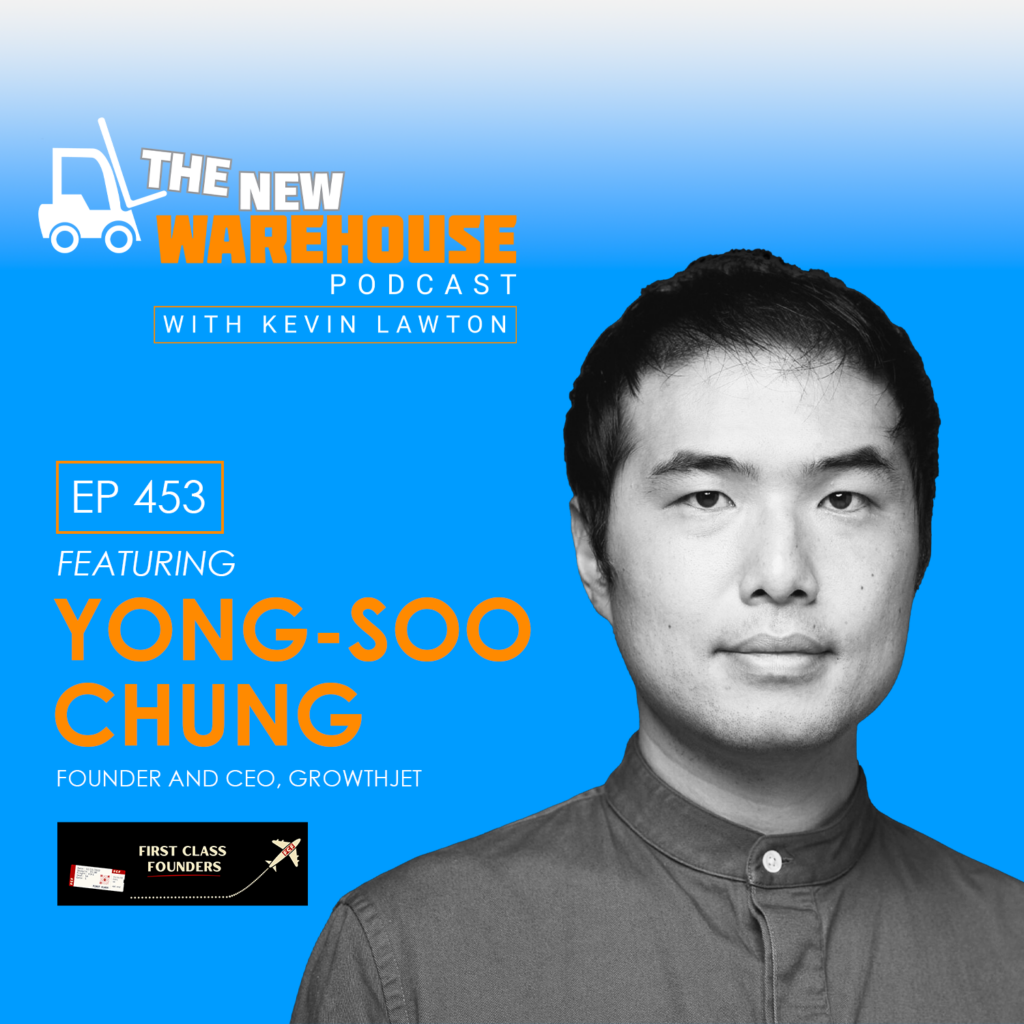
In this episode of The New Warehouse Podcast, Kevin speaks with Yong-Soo Chung, Founder and CEO of First Class Founders and GrowthJet, and more. The episode provides insights into Yong-Soo’s entrepreneurial journey, shedding light on his successful e-commerce ventures and innovative approach in the third-party logistics (3PL) sector. Be sure to tune into this informative and inspirational episode. Stepping into E-Commerce Yong-Soo Chung began his entrepreneurial path with Urban Everyday Carry (EDC), an e-commerce platform. He discusses the importance of aligning business with personal passion, revealing how this synergy drove the success of Urban EDC. Yong-Soo highlighted his interest in doing something manageable on his own, which was a good start for his first endeavor. Pioneering a Sustainable 3PL The inception of GrowthJet stemmed from Yong-Soo’s frustration with existing 3PL services. He adds, “Back then (2015), the standard was so low, I couldn’t reach anyone…and the last straw was when one of my customers received an empty box.” He aimed to establish a company prioritizing high service quality and sustainable practices. “The first thing I realized was there’s a lot of waste in the industry, and in a way, it’s inevitable.” His commitment to these values is evident in his statement: “We became climate neutral certified… it became an advantage because people were like, ‘This 3PL cares about other things aside from the bottom line.’” Entrepreneurial Challenges Yong-Soo shares his challenges, such as choosing the right business partners and scaling his operations. He often found that they would start talking to a brand and find out they were not the right fit. He emphasizes that GrowthJet, a boutique 3PL, focuses on delivering the highest quality and service level rather than competing on price. “The best clients for us are the ones that have experienced the other end of the spectrum where it’s cheap but also a nightmare.” Key Takeaways Aligning personal passion with business ventures: Yong-Soo Chung’s success with Urban EDC demonstrates the importance of integrating personal interests into business, especially in the initial stages of entrepreneurship. Commitment to sustainability in 3PL: GrowthJet’s focus on high service quality and sustainable practices, including becoming climate neutral certified, sets it apart in the 3PL industry and reflects a deep understanding of industry challenges and customer needs. Overcoming business challenges through quality focus: GrowthJet’s approach to prioritizing quality service over competing on price addresses common pain points in the 3PL industry and aligns with clients seeking reliable, high-quality logistics solutions. The New Warehouse Podcast EP 453: Charting New Paths in E-Commerce and 3PL with Yong-Soo Chung
Manitowoc Board of Directors elects Ryan M. Gwillim as New Director
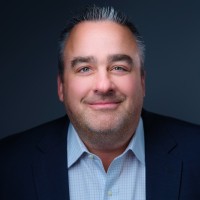
The Manitowoc Company, Inc. (the “Company”), a global manufacturer of cranes and lifting solutions, announced that Ryan M. Gwillim has been elected to the Company’s board of directors effective immediately. Additionally, the Company announced an increase in the size of the Board from nine to ten directors. Mr. Gwillim is a senior executive with over 20 years of experience in finance and law. He currently serves as Executive Vice President and Chief Financial Officer at Brunswick Corporation, where he previously held successively senior positions including Vice President, Finance and Treasurer; Vice President, Investor Relations; Associate General Counsel International and Mergers and Acquisitions; Assistant General Counsel Corporate and Securities, International Counsel – EMEA; and Corporate Counsel. Prior to Brunswick, Mr. Gwillim was an Associate at Baker and McKenzie. Mr. Gwillim holds a Bachelor of Science in Accounting, a Master of Science in Accounting, and a JD degree from the University of Illinois, Urbana-Champaign. “The Manitowoc Board of Directors is very pleased to have Ryan join the Board. With his strong financial skills and qualifications, along with his extensive background in international mergers and acquisitions, Ryan will contribute greatly to our efforts to increase shareholder value,” said Kenneth W. Krueger, Chairman of Manitowoc’s Board of Directors.
Tompkins Solutions appoints Quinntin Teeling Account Executive
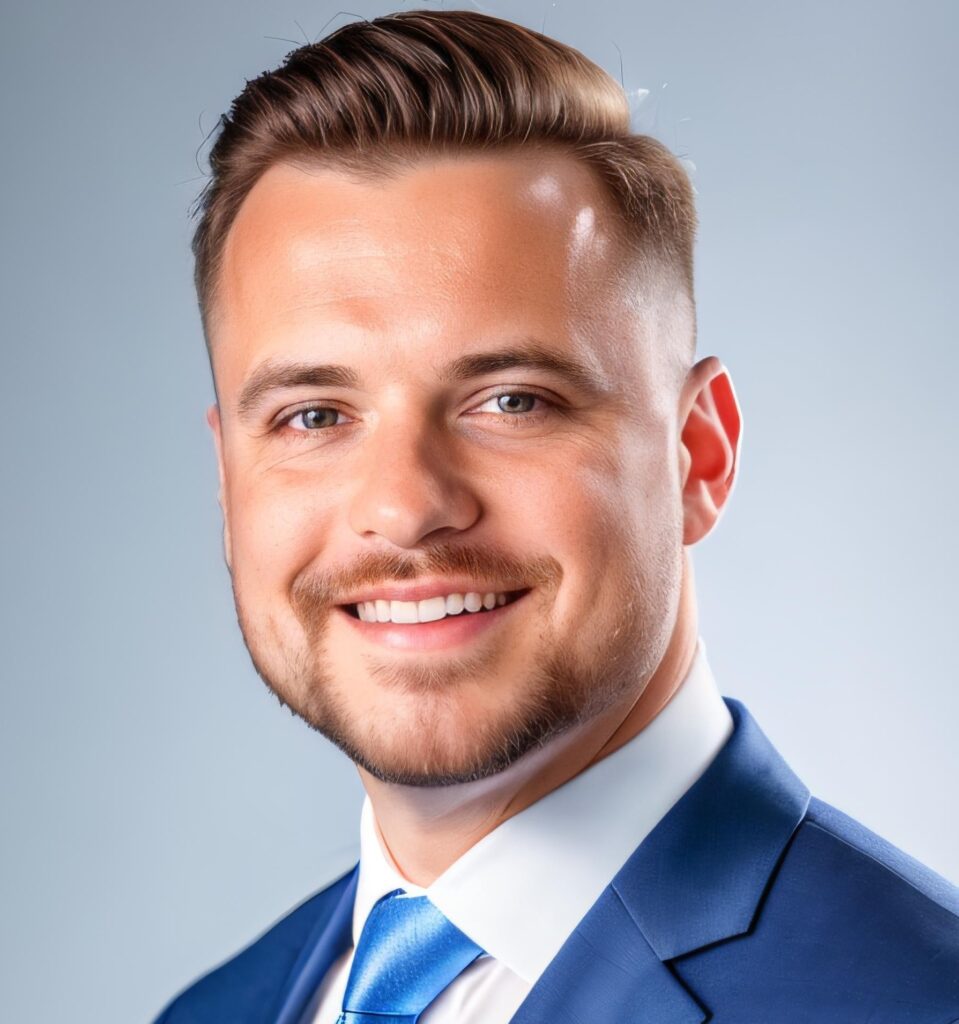
Tompkins Solutions, a supply chain consulting and material handling integration firm, announced that Quinntin Teeling has joined the company as an account executive. In this role, Teeling will be responsible for delivering tailored supply chain solutions that increase operational efficiency and return on investment. With more than half a decade of material handling automation experience, Teeling has worked with major corporations including Amazon, Boeing, Starbucks, PepsiCo and TJX, among others. Prior to joining Tompkins, Teeling held management positions with Dematic and also served as account manager for Pepperl+Fuchs. “We are excited to welcome Quinntin to the Tompkins team,” said David Latona, CEO of Tompkins Solutions. “His successful track record of implementing large-scale enterprise solutions and cutting-edge automation technologies will be integral to the growth and success of both our clients and our organization.”
Mezzanine Safeti-Gates, Inc. expands custom engineering for pallet drop safety gates
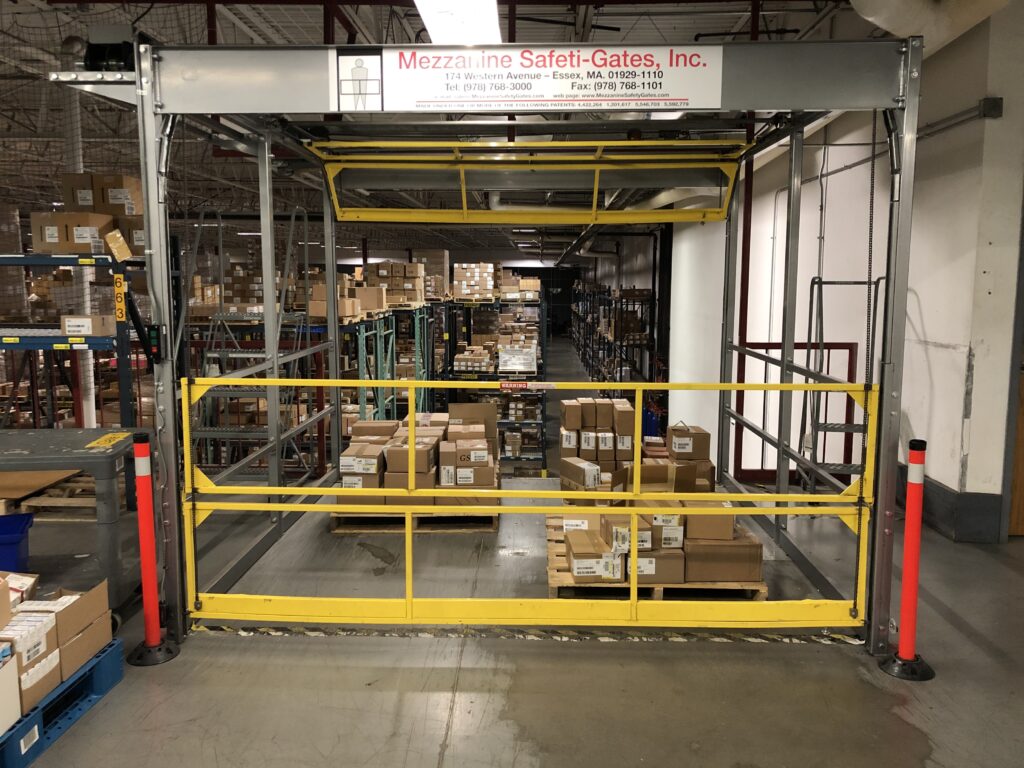
Mezzanine Safeti-Gates, Inc. is expanding its custom engineering design services to meet the growing demand for development. The company has added a new building on its current property in Essex, MA. All of the pallet drop safety gates manufactured by Mezzanine Safeti-Gates come in standard single-wide and double-wide sizes. Additionally, the gates can be manufactured in stainless steel or powder-coated steel and finished in any color. Custom engineering can be obtained for standard designs with uncommon pallet drop area sizes or for completely new safety system designs. “With advances in automation, we are seeing a greater need for custom-engineered safety gate designs,” said Chris Conway, vice president, of engineering at Mezzanine Safeti-Gates, Inc. “We are getting more requests to design pallet drop gates that not only protect employees but also the equipment being used within the facility. In addition, companies are getting very creative in using their current facility space as the applications shift, so many times gates need to be designed for unique spaces.” Some of the unique custom-engineered pallet drop safety gates created recently by the company include: TCA safety gate design with product containment netting on both the ledge and rear gates, as well as the two sides; the customer needed to keep material completely inside the pallet drop area while ensuring employees have no access to the ledge at any time. Roly safety gate design that opens and closes with the lift within a vertical reciprocating conveyor (VRC) that protects robots from falling into the shaft as materials move through levels. Roly safety gate design for an automated parking garage All custom-designed safety gates are thoroughly tested to ensure they fully comply with OSHA’s Walking-Working Surface Fall Protection regulations as well as ANSI fall protection standards. Used in thousands of locations throughout the world, pallet drop safety gate systems offered by Mezzanine Safeti-Gates can be equipped with power, remote operation, radio frequency sensors, and photo eyes.
New Lucas Systems Market Study reveals game mechanics can drive employee engagement
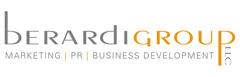
Gamified workplaces entice 84% of warehouse workers Warehouse workers who play together, stay together, according to market study insights released today from Lucas Systems, a distribution center technology company providing software to workers in more than 400 warehouses worldwide. In the study – which polled 750 U.S. and UK on-floor warehouse workers – nearly 84% of workers said they were more likely to stay with a company that developed workplace competitions around their day-to-day tasks. Workers like gamifying their work; they embrace the benefits gamified teamwork could bring; and they are eager to participate if it means earning company recognition or prizes such as company merchandise. The study explored how workers feel about game mechanics such as workplace competitions, rewards, teamwork, and leaderboards. These game mechanics are tasks that govern the actions and responses of gameplay. “The results point to new and innovative ways for managers to attract and keep warehouse workers,” says Lucas Systems Chief People Officer Bud Leeper. “Employee engagement comes from good relationships, recognition, satisfaction of achievement, and having some fun – all of which can be enhanced through workforce gamification.” Lucas Systems says the time is right to implement warehouse gamification as 98% of workers (regardless of age) have some experience with game mechanics at work and 94% already participate in games in their personal lives. Gamification can be a differentiator for employers looking to fill the more than 250,000 warehouse worker job openings in the U.S. right now. Other market study insights: Workers embrace competing as a team, as it puts less pressure on individual performance. Top motivations include strengthening the team (57%), the opportunity to engage with more co-workers (55%), and learning from teammates (53%). 88% said they are comfortable with day-to-day performance measures being shown to other employees. Boomers are generally lowest in comfort level, but still, over 80% favorable. There is strong acceptance of game mechanics, regardless of generation. Among non-supervisor warehouse workers, Gen Z are the most enthusiastic about workplace competitions. An overwhelming 90% would participate for a 10% cash bonus or lower incentive, dwarfing the already enthusiastic 77% of Gen X workers who say the same. “Warehouse operators can turn repetitive day-to-day tasks into more fun but that should be done thoughtfully and with the worker at the center,” adds Leeper. “It’s a trust exercise between workers and management. Workers must trust they will benefit from participating.”
Dematic invests in future workforce scholarships
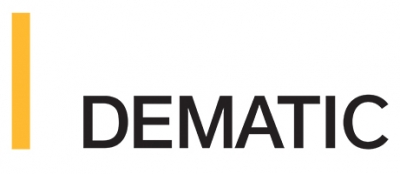
The scholarships celebrate the 10-year anniversary of Dematic’s Automated Storage Retrieval System in the Mary Idema Pew Library Dematic recently granted scholarships to five Grand Valley State University (GVSU) students in celebration of the 10th anniversary of the Mary Idema Pew Library and the Dematic Automated Storage Retrieval System (AS/RS) installation. GVSU students were invited to participate in the scholarship opportunity by reading about the Dematic AS/RS that powers library book retrieval at the Allendale and Grand Rapids, Michigan campuses, and answering a question related to the technology. The scholarship recipients were each awarded $1,000 to use toward their educational needs at the university. Who they are: Kallie Crouch – junior English, education, and writing major Isabella Gielniak – senior education, English, and history-teaching major Julia Jones – freshman recreational therapy major Tanja Morhard – freshman health information management and healthcare information systems major Chloe Spradlin – sophomore biochemistry major “We believe in investing in technology as well as in our future workforce and community,” says Mike Larsson, President, Dematic, KION Group Executive Board Member. “These scholarships reflect our commitment to education and innovation, shaping a brighter tomorrow for Grand Valley State University students and the Grand Rapids community.” Installed at GVSU’s Allendale campus in 2013, the Dematic AS/RS fully automates the book collection process. Students and library patrons request materials through the library’s ordering system, triggering the robotic crane to retrieve the book within minutes of the request. The Dematic AS/RS at the Mary Idema Pew Library on the Allendale campus is integrated via a software control system with another Dematic AS/RS in the Steelcase Library on the Grand Rapids campus. This has eliminated off-campus storage while reducing retrieval times from days to around two minutes. The system ensures near 100% accuracy through barcode scanning. Both library storage areas are temperature-controlled, helping to preserve materials and have a total capacity of 800,000 items. “Dematic’s AS/RS technology at GVSU has made accessing study materials quick and easy,” says scholarship recipient Isabella Gielniak. “From checking out materials to now receiving support for my future studies, it showcases how technology enhances educational accessibility and the positive impact of innovation in the Grand Rapids community.”
ABB acquires Sevensense expanding its leadership in next-generation AI-enabled mobile robotics
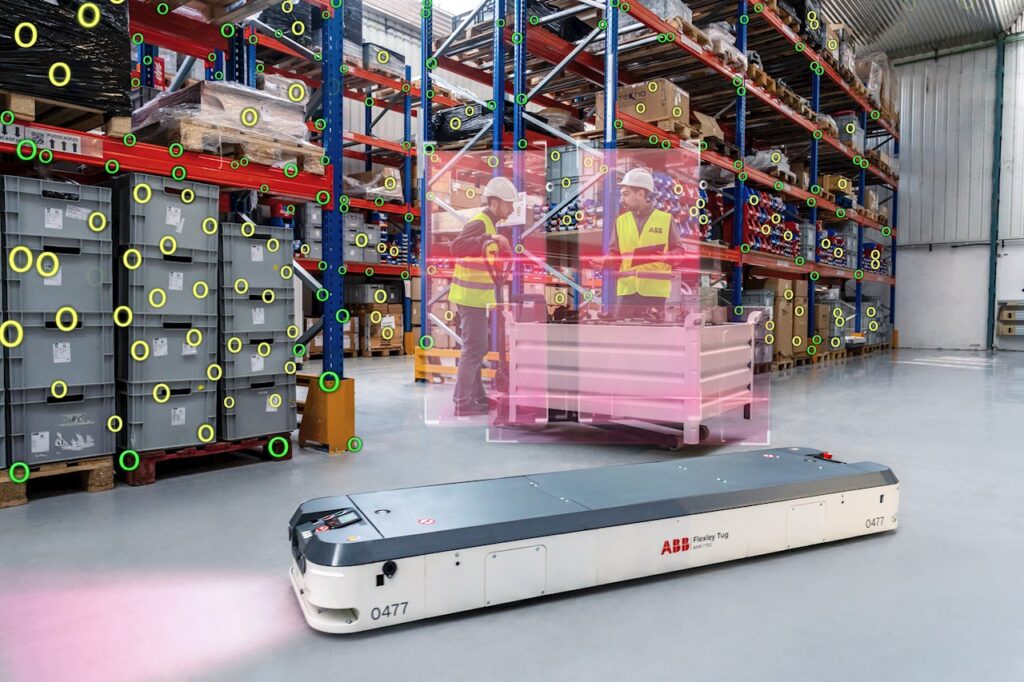
Swiss start-up Sevensense, a provider in AI-based navigation, enables the highest levels of speed, accuracy and autonomy of mobile robots, one of the fastest growing robotics markets Acquisition underlines ABB’s strategic investment focus on innovative AI solutions transforming industries, such as logistics and manufacturing ABB becomes leader in next-generation AMRs, integrating Visual SLAM technology with leading hardware and software portfolio ABB has announced that it has acquired Swiss start-up Sevensense, a leading provider of AI-enabled 3D vision navigation technology for autonomous mobile robots (AMRs). Sevensense was founded in 2018 as a spin-off from Swiss technical University, ETH Zurich. “This marks a significant step towards our vision of a workplace where AI-enabled robots assist people, addressing our customers’ needs for greater flexibility and intelligence amidst critical skilled labor shortages,” said Sami Atiya, President, ABB Robotics and Discrete Automation Business Area. “Each mobile robot, equipped with vision and AI, scans a unique part of the building; collectively these robots complement each other’s view to form a complete map, enabling them to work autonomously in a rapidly changing environment.” The acquisition follows ABB’s minority investment in Sevensense after it joined the company’s innovation ecosystem in 2021, the same year ABB acquired ASTI Mobile Robotics. Financial details of the transaction were not disclosed. Following pilot customer projects in the automotive and logistics industries, ABB will integrate Sevensense’s technology into the company’s AMR portfolio, offering an unprecedented combination of speed, accuracy, and payload. The market for mobile robots is expected to grow at 20 percent CAGR through 2026, from $5.5bn to $9.5bn and ABB’s AI-powered 3D vision technology is at the forefront of this growth.1 Sevensense’s pioneering navigation technology combines AI and 3D vision, enabling AMRs to make intelligent decisions, differentiating between fixed and mobile objects in dynamic environments. Once manually guided, mobile robots with Visual Simultaneous Localization and Mapping (Visual SLAM) technology create a map that is used to operate independently, reducing commissioning time from weeks to days and enabling the AMRs to navigate in highly complex, dynamic environments alongside people. Maps are constantly updated and shared across the fleet, offering instant scalability without interrupting operations and greater flexibility compared to other navigation technologies. Today, this AI-enabled navigation technology is already transforming the automotive manufacturing and logistics sectors, delivering value through faster and more efficient operations. For automotive manufacturer Ford, Visual SLAM enabled ABB AMR’s will create efficiency gains in production sites in the US, while Michelin will use the technology in intralogistics at its factory in Spain. Other automotive manufacturers will roll out the technology in the UK, Finland and Germany. “Offering more autonomy and cognitive intelligence, ABB’s unique market-proven technology paves the way for a shift from linear production lines to dynamic networks. Intelligent AMRs autonomously navigate to production cells, tracking stock inventory as they go and sharing this information with other robots, while collaborating safely side-by-side with humans,” said Marc Segura, President of ABB’s Robotics Division. “With the acquisition of Sevensense, ABB becomes the leader in next-generation AMRs, offering Visual SLAM in Autonomous Mobile Robots, together with an integrated portfolio covering robots and machine automation solutions, all managed by our value-creating software.” Gregory Hitz, CEO of Sevensense, said: “This is a significant moment in our shared journey, as we introduce our home-grown technology to a wider range of markets and sectors. ABB is the ideal home for us to continue scaling our versatile platform for 3D visual autonomy, serving OEMs across the automated material handling and service robotics industries. Together, we will redefine the limits of AI-enabled robotics.” This revolutionary technology has the potential to impact robotics far beyond AMRs, leading to greater efficiency, flexibility and accuracy throughout production and intralogistics. The technology will also continue to be sold across segments including material handling, cleaning and other service robotics fields under the product name Sevensense. The Sevensense partnership highlights the success of ABB’s commitment to nurturing the next generation of innovations. Through its partner ecosystem and collaboration with start-ups and universities, ABB develops leading technology for the benefit of global businesses. Sevensense’s approximately 35 employees will continue to be based at its Swiss office in Zurich.
Caldwell adds RUD ROV hooks to in-stock program
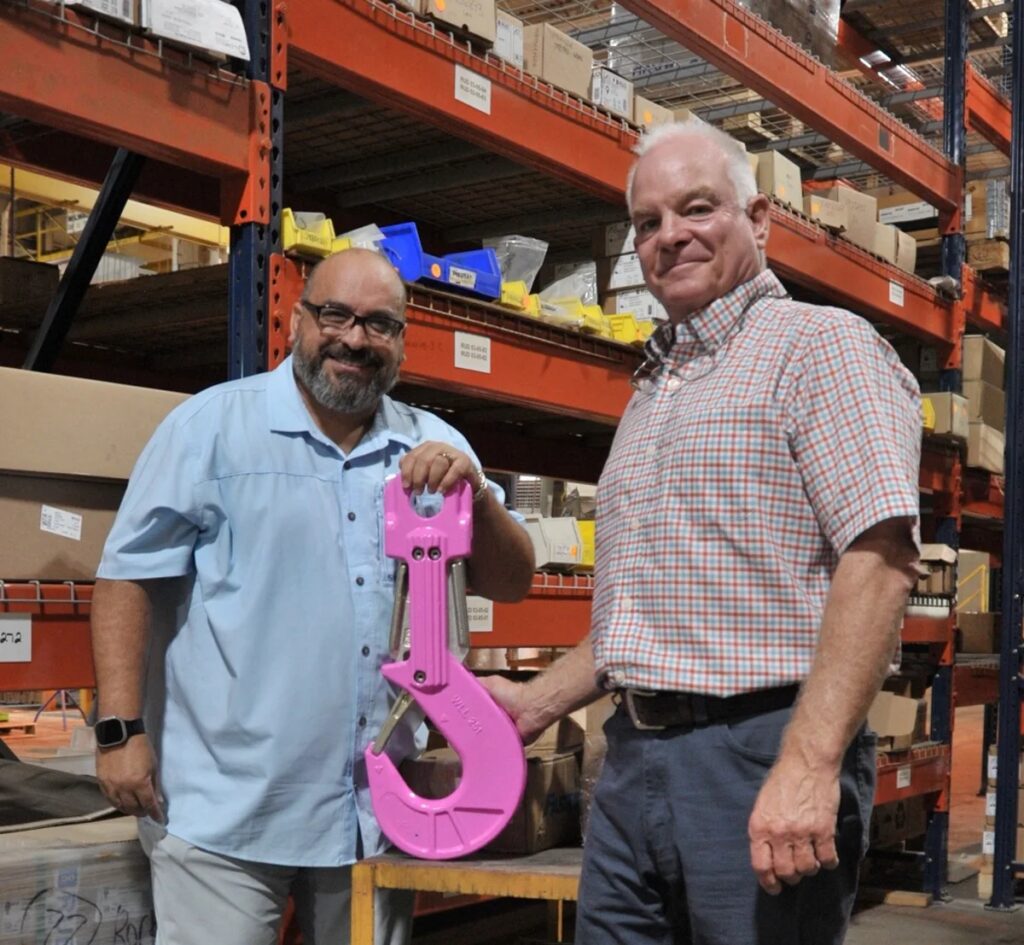
The Caldwell Group Inc. has added remotely operated vehicle (ROV) hooks from RUD to its in-stock program. The hooks, available in 10t and 25t capacity, are primarily for use in underwater applications in the Gulf Coast region. Caldwell and the RUD Group unite their sales and marketing activities in North America, and now stock more ROV hooks here than ever before. Access to ROV hooks is important to major subsea, and oil and gas, contractors for utilization in multi-million-dollar projects to handle valuable loads in hazardous environments, often many miles offshore and up to water depths of 10,000 ft. The safe lifting and lowering of loads on deck and underwater—coupled with ambient conditions, unpredictable currents, and difficult lighting—presents enormous challenges. The sector is nearly always time-pressured, and precision is fundamental to safety. The hooks can be used by major contractors, like Oceaneering International Inc., to install long baseline transponder frames, rigid M-shape jumpers, and associated subsea distribution hardware, for example. Users must eliminate the risk of dropped objects, especially when passing through the water interface, and provide a user-friendly subsea solution. Twin trigger mechanism The RUD ROV hooks can be operated by all commonly used ROV manipulators, including the grabber. The hook eliminates the risk of snagging and accidental rigging; the outer profile is smooth with no protruding hook nose. The outwardly opening safety latch, which can be operated by a single manipulator, automatically closes when the ROV releases the triggers, and it is securely locked in the closed position. Overall hook design minimizes the time the ROV takes to carry out the attachment/detachment operation. Jay Schroeder, western sales manager at Caldwell, said: “Just like every other market segment when someone needs it, they need it now. Many times, you can’t anticipate when you have a failure or an emergent need, and it is important to keep the job running. Overall, we must have these hooks in stock. The equipment our ROV hooks are lifting is often worth well over a million [dollars].” A standout feature of RUD ROV hooks is the twin trigger mechanism; it opens only by pressing both triggers simultaneously. It only requires one hand to operate whereas most alternatives need two hands to open and close. The yellow oblong master link serves as the target for operators. Radio-frequency identification (RFID), meanwhile, enhances inspection and tracking. Schroeder added: “RUD is a high-quality, Germany-manufactured product, so it takes a certain type of company to be able to deliver it here in North America, keeping lead times short and stock levels high, close to the point of use.”
Scott Schrum joins outside sales team at New Age Industrial
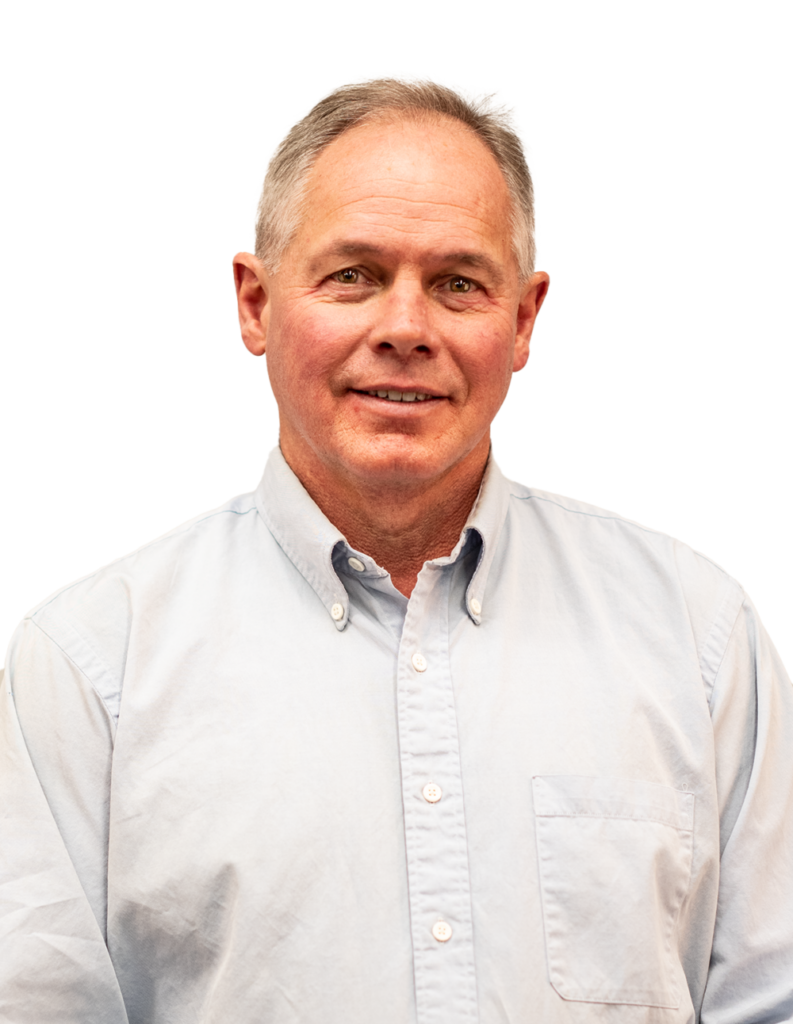
New Age Industrial has announced the appointment of Scott Schrum for outside sales in the Material Handling Division. Scott is a passionate and dedicated business professional with over 30 years of experience in sales and management. After graduating from the University of Kansas in 1992 with a Bachelor of Business Administration and a Minor in Economics, he began his career in the grocery industry. For 10 years, he worked at New Age Industrial in the Supermarket Sales Division. Since then, Scott has held a variety of sales and management positions with Walmart and is an entrepreneur with a portfolio of successful businesses. Scott is a strong team player with a proven track record of success in building relationships and motivating others. He has a deep understanding of e-commerce and is a safety and efficiency expert. His hands-on experience in the supply chain and warehouse side of the business has given him a keen eye for identifying opportunities for improvement through thoughtful solutions. In his new position in Outside Sales, Scott will work directly with the National Sales Manager, Bob Brackle, and the manufacturer’s representatives to maintain existing business and create new opportunities. He will also attend a variety of national trade shows with the Material Handling Sales Team. According to Scott, one of his primary goals at New Age Industrial is to educate others about the company’s unique ability to design and manufacture custom aluminum solutions. Another of his top priorities is to help customers identify areas for improvement within their warehouses and distribution centers. Scott shared, “We have a chance to show people a better way to be more efficient and safer while improving their overall businesses and processes.” When asked what made him want to come back to work for New Age Industrial, he said, “New Age is a great company with great people and great work ethic, and they produce great products. Material handling has evolved so much, so it’s an exciting area of the business to be involved in. I’m glad to be a part of this growing division!” He also shared, “It was nice to come back after so many years and see some of the same faces that were here when I left New Age in 2002. That level of loyalty from the employees says a lot about this company!” We congratulate Scott Schrum on his new role and look forward to working with him. We are excited to have him on the team. Scott said, “I am excited to rejoin the team at New Age Industrial. I am impressed with the company’s commitment to quality, and I am confident that I can make a positive contribution to the team.”
Cisco-Eagle announces strategic acquisition of Trinity Controls

Cisco-Eagle, a material handling systems integration company has announced the acquisition of Trinity Controls, an innovative controls engineering company located in Birmingham, Alabama. “This acquisition is a significant milestone in for both companies,” said Cisco-Eagle President and Chief Operating Officer Bryan Gauger. “Trinity’s expertise in creating efficient and reliable control systems aligns with our commitment to delivering outstanding value to our customers and helps us expand our ability to serve industrial automation customers of all types.” Established in 2005, Trinity specializes in PLC (programmable logic controls) engineering. It focuses on design, programming and PLC panel fabrication for automation projects in the manufacturing and distribution sectors. Trinity is highly experienced in conveyor systems, material handling, heavy machinery and motor control applications. “With Trinity’s exceptional talent and track record, Cisco-Eagle is better positioned to address the needs of our clients and stay ahead in a rapidly changing automation landscape,” said Gauger. This acquisition transfers Trinity Controls operations to Cisco-Eagle, forming the Cisco-Eagle Systems Technology Group. Trinity’s staff will join the family of Cisco-Eagle employee-owners. “Our culture is built on empowered employees who all own shares in the company. I’m thrilled to welcome Trinity’s staff to our family and look forward to our journey together,” said Gauger. “We are excited about the opportunities for developing more advanced and integrated solutions,” said Tim Norwood, founder of Trinity. “Our combined expertise, experience and ability to create solutions will let us serve our industrial automation customers even better.” Norwood will continue his leadership as Cisco-Eagle’s Director of Systems Technologies. The company will continue its work with a variety of clients throughout the industry in the material handling and industrial automation space.
Episode 452: Navigating the return maze with Pollen Returns
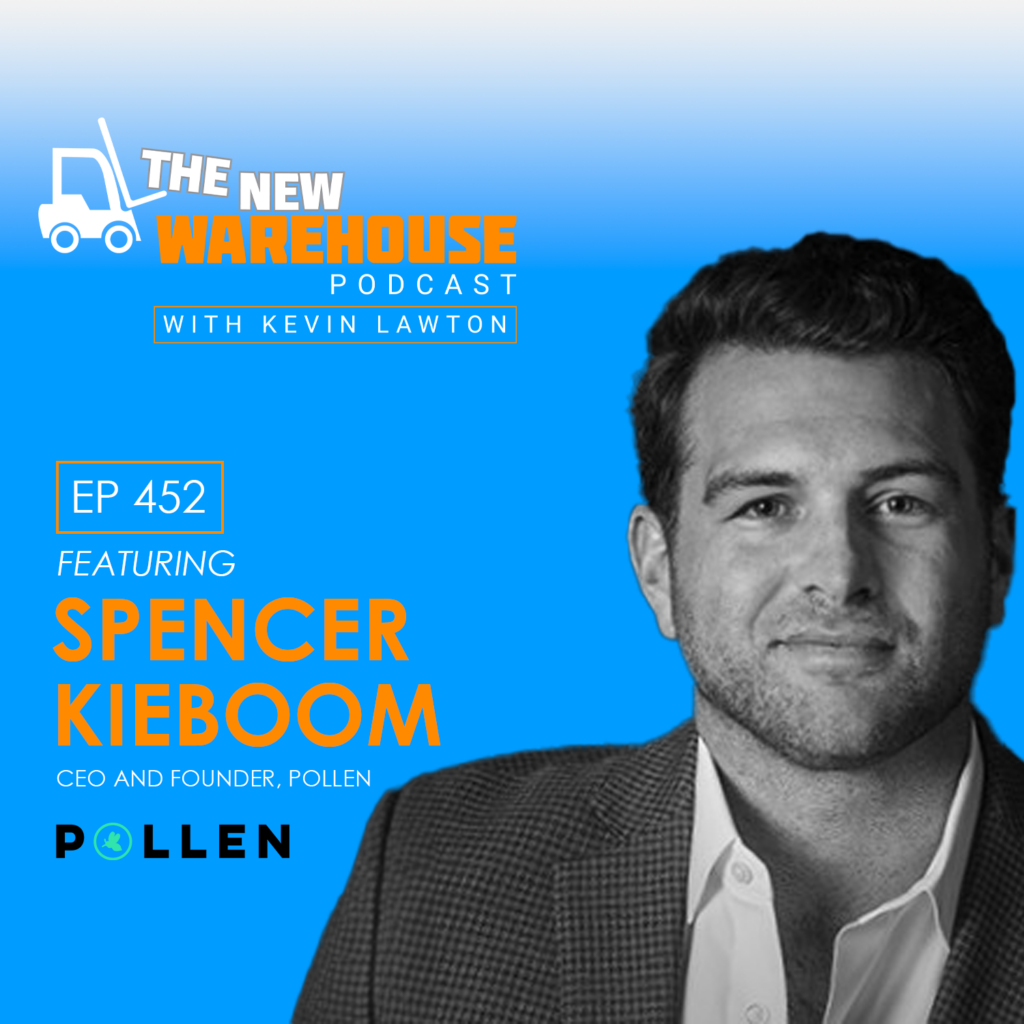
In this episode of The New Warehouse Podcast, we’re diving into the intriguing world of returns with Spencer Kieboom, co-founder and CEO of Pollen Returns. Once a major league catcher, Spencer now tackles the challenges of the returns industry, striving to enhance the experience for both retailers and customers. Join us as we uncover the current state of returns and the innovative solutions Pollen Returns is implementing to revolutionize this essential yet complex sector. Journey from the Diamond to Pollen Returns Spencer Kieboom shared his transition from baseball to addressing the returns problem. He stated, “The idea stems from before my playing days of baseball. It stems all the way back as a freshman in college.” His analytical skills honed on the field, where he delved deep into data and strategy, now fueling his approach to the returns industry. The Returns Dilemma Delving into the heart of the returns problem, Spencer Kieboom sheds light on its multifaceted challenges. He questions the industry’s status quo, “Why are returns costing retailers hundreds of billions of dollars?” This critical inquiry prompts a deeper exploration of the issue. He points out how the lack of a streamlined process and understanding of customer behavior significantly hampers efficiency and drives up costs. Spencer emphasizes the ripple effect of returns on retail operations and customer satisfaction, stating, “Every return is a lost opportunity, not just in revenue but in building trust and loyalty with the customer.” By dissecting the problem, he suggests a paradigm shift from viewing returns as mere transactions to opportunities for engagement and improvement. Spencer’s insights underscore the urgent need for innovative, customer-centric solutions to redefine the returns landscape. Innovative Solutions at Pollen Returns Kieboom introduces the Pollen Returns approach, focusing on turning returns into opportunities for more sales. He explained, “We look at ourselves as a sales augmentation platform for retailers to parlay their returns into more sales.” Their strategies include seamless exchanges, label-less returns, and proprietary pickup services, aiming to enhance both the customer experience and operational efficiency. Key Takeaways from Pollen Returns The journey from professional sports to entrepreneurship provides unique analytical and strategic insights. Understanding the underlying causes of returns is crucial for developing effective solutions. Innovative approaches like sales augmentation platforms can transform returns into opportunities for retailers. The New Warehouse Podcast EP 452: Navigating the Return Maze with Pollen Returns