Container xChange unveils January’24 Container Market Forecaster
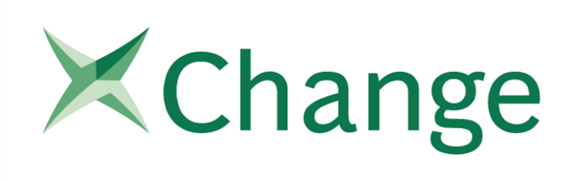
“The red sea situation is acute, but not chronic for shipping” says Christian Roeloffs, cofounder and CEO of Container xChange Shipping industry looking forward to up their game in ‘risk assessment and scenario planning’, ‘diversification of routes and suppliers’ & ‘regulatory compliance’ in 2024 as a response to geopolitical risks Shipping professionals see ‘associated costs’ as biggest headache in ‘24 due to geopolitical unrest BRICS expansion to lead polarisation of global trade Container xChange, a online container trading and leasing platform, releases its New Year’s Edition Container Market Forecaster, shedding light on the escalating geopolitical risks set to reshape the landscape of global trade in 2024. In response to these geopolitical risks, majority of shipping professionals surveyed in the month of December 2023, by Container xChange, are gearing up to enhance resilience through strategic initiatives like – ‘risk assessment and scenario planning’, ‘diversification of routes’ and ‘suppliers and regulatory compliance’. The biggest ‘headache’ resulting from geopolitical upheaval is the ‘associated costs’ that they will have to bear on top of the rising operating costs that they have to already face. Key Highlights: Strategic Focus Areas: In response to geopolitical risks, shipping professionals are prioritizing ‘risk assessment and scenario planning,’ ‘diversification of routes and suppliers,’ and ‘regulatory compliance’ in 2024. Rising Concerns: Survey findings reveal that the biggest concern stemming from geopolitical upheaval is the ‘associated costs,’ compounding the challenges posed by soaring operating costs. Many customers are worried about the rising costs resulting from the Red Sea situation like compliance charges, insurance premiums and war risk charges, etc. The operating costs have already been rising soon after the rates crashed in 2022, and demand failed to recover. On top of the rising costs, these additional surcharges will only add to the worries of shippers and forwarders. BRICS Expansion: The inclusion of new economies in the BRICS bloc, including Saudi, Iran, UAE, Egypt, and Ethiopia, sets the stage for potential polarization of global trade, impacting geopolitical compliance. Technology Utilization: Despite challenges, 82% of industry professionals acknowledge the importance of technology for resilience in 2024, with predictive analysis and forecasting tools taking center stage. Sanctions Compliance: Amidst geopolitical developments, sanctions compliance becomes critical for supply chain professionals, adding another layer of complexity to global trade. Fluctuating Freight Rates: freight rates will increase in the short to midterm, but not in the long run as demand and supply is still highly imbalanced with no clear signs of a strong revival. Talking about the Red Sea situation, Christian Roeloffs said, “The Red Sea is a vital artery for global trade which is currently blocked. Thankfully, there are ways to circumvent that artery and keep the global trade moving and therefore, the trade is not stopped. Therefore, the red sea situation is acute but not chronic in the long term for the shipping industry.” There are still many geopolitical risks that have the potential to significantly impact shipping trade in 2024. We have the Israel – Hamas war, the related situation in the Red Sea, the Russia Ukraine war with no end in sight, tensions between China and Taiwan and an increasing enlargement of the BRICS block. BRICS expansion “What can have a far- reaching and long-term impact on the global supply chain is the BRICS inclusions of more economies.” Roeloffs added. There is a host of countries being added in the BRICS block, namely, Saudi, Iran, UAE, Egypt, Ethiopia, while Argentina declined inclusion. BRICS has been viewed as a counterbalance to the Western-led world order. “If the block starts to increasingly align political decisions and geopolitical stances, then there could be added complexities to the global trade order with rising polarisation of global trade. Ultimately this might lead to a situation where one block is not allowed to trade with the other block and eventually, geopolitical compliance becomes more complex and difficult.” he added. The expansion of BRICS will bring further interesting developments worth noting. Iran and Saudi are now in the same organisation despite a strained relationship. Egypt has close commercial ties with Russia and India but also with the US. India and China together account for ~2.5bn people and could heavily influence global policymaking if they are more aligned. And finally, Russia and Iran being able to jointly influence “trade” policymaking within the BRICS group could lead to a “sharpening” of trade rethink of US-allies vs BRICS. Amidst these developments, sanctions compliance will become critical for supply chain professionals for doing business. Any geopolitical unrest has a direct and causal impact on global trade which results in market volatility. Classic case in point is the Gaza Strip and the resulting actions by Houthis in Jemen. This leads to trade rerouting, ultimately resulting in rising operating costs, delays, and service disruptions.” said Roeloffs.
OZ Lifting chain hoists lower $250k car
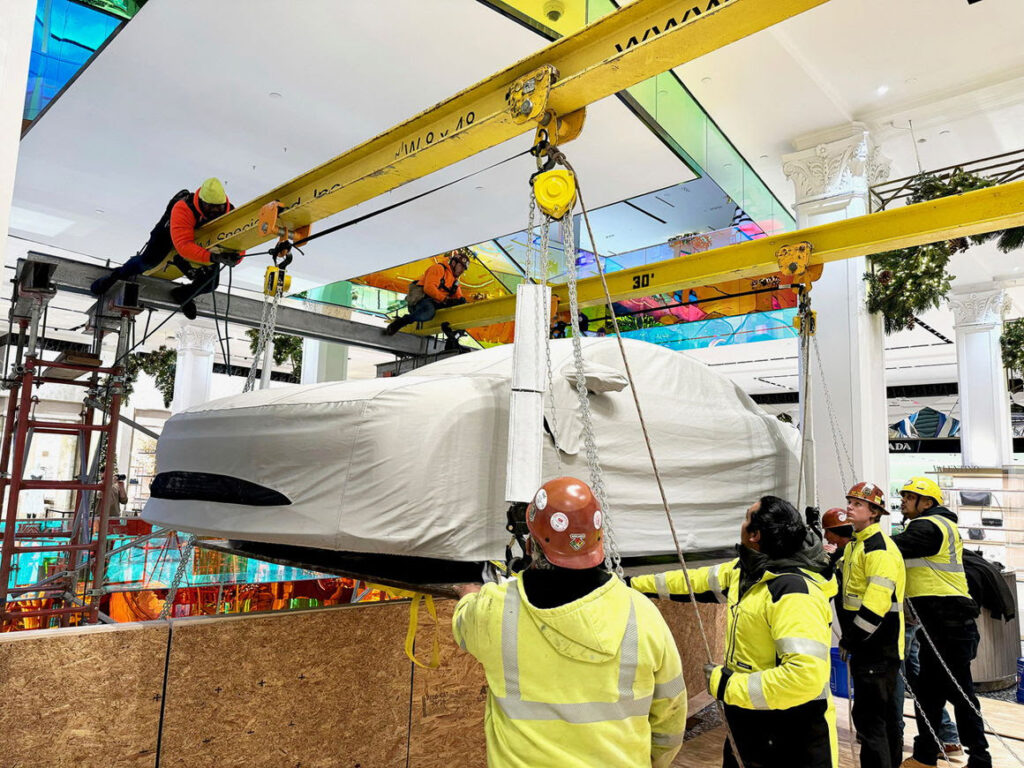
The vehicle was center of a holiday-season display in the jewelry section of the store, which is below street level. Getting it there took an overnight operation that involved four 3-ton capacity OZ Premium hand chain hoists, with a lifting height of 30 ft.; beam clamps attached to 30-ft. long beams; and a customized lifting platform. The 5,600-lb. car combined with the platform for a total load of 10,000 lb. To facilitate the lift (lower), four exterior doors were removed, an escalator bank was stripped, and the car was driven to the makeshift freight elevator. The store’s pillars were utilized to anchor the platform in preparation for the 28-ft. journey down to the vault level. OZ Lifting’s equipment was utilized at the point of use by the project’s rigging contractor, Concord Painting, which sourced it from OZ dealer, Eastern Rigging Supply. A steel fabricator was subcontracted to provide the lifting platform. Bob Eberheim, of Eastern Rigging, said: “The work was completed upon closure of the store one evening; it took 10 hours even when the Sapphire was in the store, such was the complexity of the job and the constant requirement to complete such lifts as safely as possible.” He added: “The yellow straps you can see in the photos were used to secure the vehicle in place, and the beams were supported by shoring towers.” The OZ Premium hand chain hoists are part of a range that spans 0.5-ton to 10-ton capacity. They offer minimal load lifting effort; double reduction gearing provides easy operation. A unique hand-wheel design enables the hand chain to successfully feed directly into the wheel sprocket from many directions and angles. Thus, the operator can use the hoist while standing to the side of, or even above, the load without fear of the hand chain jamming. All-steel construction features a long-lasting powder coat finish, while providing a long and dependable service life in harsh environments. An enclosed and protected Weston-style load brake stays clean and dry during the entire load operation. Hoists are also equipped with a unique twin pawl design for additional reliability. A sealed roller bearing provides smooth, controlled operation of the gears and shafts, which ensures maintenance-free lubrication. An article published in the New York Post reported, ‘…it’s probably the biggest stunt the store has pulled off since 1935’.
Episode 450: The power of intelligent slotting with Fulfilld
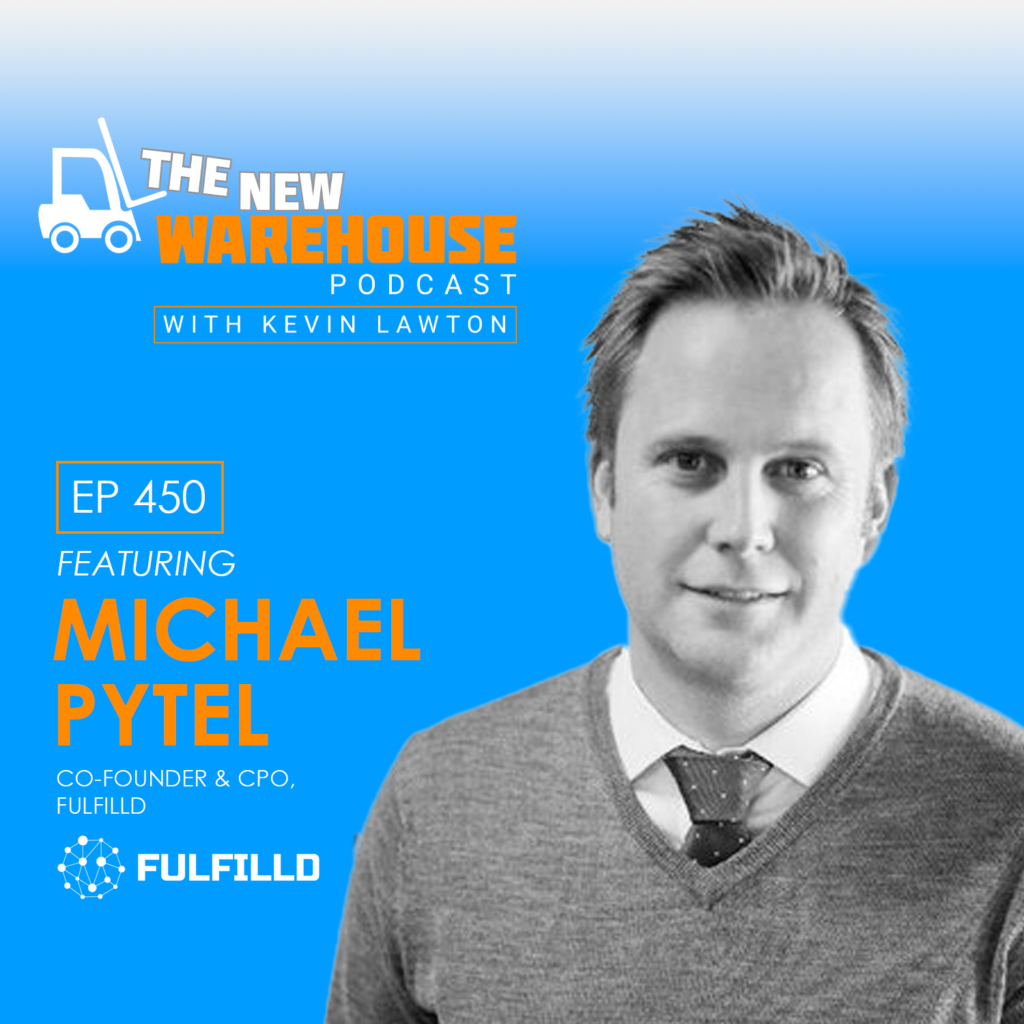
Michael Pytel is the co-founder and CTO of Fulfilld, a pioneering company introducing a new warehouse management system (WMS) to the industry. In this episode, Michael and Kevin dive deep into the concept of intelligent slotting within the warehouse environment, exploring its significance, challenges, and how Fulfilld’s technology is making a tangible impact. Understanding Slotting: The Backbone of Warehouse Efficiency Pytel explains, “Slotting is super important for the warehouse management system and for slotting tools to understand the physical space, the physical world to optimize how employees flow through the building.” He emphasizes the complexity of manual processes, especially in vast warehouses with thousands of products. By leveraging technology, Fulfilld aims to optimize product placement, significantly impacting warehouse flow and efficiency. Transforming Slotting with Technology: A Leap Towards Optimized Operations Pytel discusses the limitations of traditional methods and how Fulfilld’s intelligent slotting application revolutionizes this by creating a digital twin of the warehouse and understanding physical space. “By understanding physical space, creating that digital twin of the warehouse, we can more efficiently route and optimize labor inside the warehouse and robots,” says Pytel. Future-Proofing Warehouses: The Road Ahead for Fulfilld’s Slotting Innovations Looking ahead, Pytel shares its vision for integrating more labor information and predictive analytics into its application. This forward-thinking approach aims to enable more strategic shift planning and optimize warehouse capacity, addressing the dynamic needs of modern warehouses. Key Takeaways on Slotting Slotting directly impacts the flow of your warehouse and metrics like picks per hour. Proper product placement drastically improves your outbound and inbound flow of goods. Traditional methods are time-consuming and less efficient; technology can significantly enhance this process. Fulfilld’s intelligent slotting application creates a digital twin of the warehouse, understanding physical space for better optimization. The New Warehouse Podcast Episode 450: The Power of Intelligent Slotting with Fulfilld
Who’s your brand’s rival?
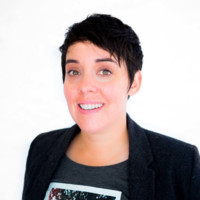
Everyone likes a good rivalry story. They inspire, build emotional connections, and create a deep level of authenticity with the characters involved. Your brand has rivals too, and capitalizing on those rivals can help you position your identity in a way that differentiates you from the herd. Rivals also play an essential role in storytelling and messaging. A rival is the main enemy of the protagonist. Their actions and motivations are typically opposed, creating conflict and driving the proverbial plot forward. Consider your brand’s story – do you have a rival that you can position your organization against? The trick with rival positioning is that your rival isn’t your typical competitor – it’s the single thing that your customers struggle to overcome that you and only you can help address, allowing you to connect on a deeper, more emotional level. Consider a few well-known brands that have identified non-traditional rivals that allow them to stand out uniquely from the competition: Nike Fighting Self-Doubt: The renowned “Just Do It” campaign connects with people’s struggle against self-doubt and procrastination. This positions Nike as a companion and motivator, helping emotionally connect by encouraging people to overcome their fears and pursue their goals. Dove Fighting Unhealthy Beauty Standards: Dove’s “Real Beauty” campaign pushes against the unrealistic and unattainable beauty standards perpetuated by the media. This positions Dove as an advocate for authentic beauty, emotionally connecting by celebrating diversity and self-acceptance. Patagonia Fighting Environmental Abuse: Patagonia is deeply rooted and highly focused on “environmental activism and sustainability”. This positions Patagonia as a steward of the environment and emotionally connects through the battle against pollution and the overuse of natural resources. How you position your organization doesn’t end with marketing, branding, and messaging. That distinct position should permeate all areas of your organization, guiding decision-making, and aligning those decisions with the core positioning. For instance, Patagonia uses its rival position to drive decisions on material purchasing, factory design, charitable contributions, and even organizational hires. As you consider your brand, examine the opportunity a rival positioning can bring.By broadening your horizons beyond a traditional competitor, and focusing on people’s emotional drivers, you can not only connect with customers on a deeper level but also create a market position that will be incredibly unique and even harder to contest. About the Author Andrea Belk Olson is a keynote speaker, author, differentiation strategist, behavioral scientist, and customer-centricity expert. As the CEO of Pragmadik, she helps organizations of all sizes, from small businesses to Fortune 500, and has served as an outside consultant for EY and McKinsey. Andrea is the author of three books, including her most recent, What To Ask: How To Learn What Customers Need but Don’t Tell You, released in June 2022. She is a 4-time ADDY® award winner and host of the popular Customer Mission podcast. Her thoughts have been continually featured in news sources such as Chief Executive Magazine, Entrepreneur Magazine, Harvard Business Review, Rotman Magazine, World Economic Forum, and more. Andrea is a sought-after speaker at conferences and corporate events throughout the world. She is a visiting lecturer and startup coach at the University of Iowa, a TEDx presenter, and TEDx speaker coach. She is also an instructor at the University of Iowa Venture School. More information is also available on www.pragmadik.com and www.andreabelkolson.com.
Kenco acquires The Shippers Group
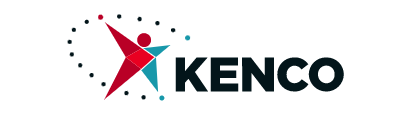
Acquisition expands Kenco Warehousing footprint by 3.8M square feet Kenco, a North American third-party logistics company, has announced the acquisition of The Shippers Group, a Dallas-based third-party warehousing company. This strategic partnership adds to Kenco’s capabilities by providing increased capacity, broader geographic reach, and an expanded suite of services for the benefit of customers. Terms of the acquisition are not being disclosed. Founded in 1901 as a regional warehousing company, The Shippers Group has evolved into a nationally recognized leader in the warehousing, co-packaging, fulfillment, and transportation management space. Its century-long legacy of strengthening supply chains through innovative solutions distinguishes the company as a reliable partner. The Shippers Group is led by majority owner and CEO Graham Swank and supported by a tenured leadership team committed to upholding the company’s collaborative, innovative, and growth-oriented culture. “Kenco and The Shippers Group have highly complementary capabilities and share a culture of excellence,” said Denis Reilly, CEO of Kenco. “Together, we bolster the combined suite of capabilities with increased scale and reach in key growth markets, enabling us to capitalize on market momentum, while continuing to deliver exceptional service to our customers. I have long admired The Shippers Group’s management team and look forward to working together in the next chapter of their growth.” The acquisition of The Shippers Group bolsters Kenco’s multi-client capabilities and North American presence through the addition of 3.8 million square feet of space across eight sites in Florida, Georgia, and Texas. Kenco customers will benefit from access to The Shippers Group’s facilities, increased transportation capacity, as well as co-packaging know-how and processes. “Today marks a pivotal moment in The Shippers Group’s journey to optimize supply chains for the benefit of our customers,” said Rob Doyle, President at The Shippers Group. “Kenco has built an exceptional platform from which to scale, and I am confident that our customers will welcome access to Kenco’s proven operating systems. Our alignment with Kenco’s culture, values, and commitment to innovation, coupled with Kenco’s infrastructure, positions us well to achieve new levels of performance and execute upon our growth opportunities.” Scott Mayfield, Chief Administration Officer of Kenco, added, “We knew Shippers Group would be a fit from the start. We have had a long-standing relationship with their owners and key executives. This strategic partnership signifies a milestone for Kenco and The Shippers Group, combining our strengths to deliver even greater value to our customers and further excel in the dynamic logistics landscape.”
The U.S. Plastics Industry in 2023 in seven charts
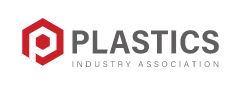
Assessing the plastics industry landscape in 2023 reveals a year marked with nuanced shifts across various sectors. From the fluctuations in production levels and shipments to the intricate interplay between labor constraints and export dynamics, the plastics industry encountered challenges and opportunities. Notably, the year witnessed divergent trajectories: while certain segments, such as plastics material pricing and resin manufacturing, grappled with equilibrium adjustments, others, like the mold for plastics trade, mirrored global economic oscillations. Unpacking these trends and projections explains a complex narrative of the industry’s path ahead into 2024. 1. Plastic Products Manufacturing 2023 saw a notable pullback from the production levels of 2022. The initial increase starting in March did not maintain momentum for the rest of the year. A significant decline occurred in July, followed by another downturn in August. While September witnessed a slight increase, it was followed by successive declines through November. There is a likelihood that production increased marginally in December. It is anticipated that the rate of decline in plastics production in 2024 will be lower than that observed in 2023. 2. Plastics and Rubber Shipments In 2023, the shipments of plastics and rubber remained relatively stable, hovering between $24.4 billion and $24.9 billion. Although there was an initial decline in the first four months, they rebounded until August before stabilizing, with minimal fluctuations projected for November and December. Despite robust economic growth, primarily fueled by personal consumption accounting for 87% of plastics production, inventories remained elevated, prompting a decrease in plastic shipments. Initial projections for 2024 indicate a tepid rise in shipments of plastics and rubber, signaling a modest increase. 3. Plastics Manufacturing Employment The U.S. plastics industry grappled with persistent labor supply constraints throughout 2023, echoing the challenges experienced across the broader manufacturing sector. From January to December, there was a probable 1.7% decrease in the workforce engaged in plastics product manufacturing. According to the U.S. Bureau of Labor Statistics, an estimated 608,000 employees were working in plastics products manufacturing in November, likely declining to 607,500 by December. The ongoing disparity between job openings and actual hires in manufacturing is anticipated to have persisted throughout November and December. These persistent imbalances in labor demand and supply, including within the plastics industry, are forecasted to extend into 2024. 4. Molds for Plastics Trades The slowdown in U.S. manufacturing and weakened economic conditions in export markets became evident in the molds for plastics trade. Projections suggest a notable 8.8% decrease in exports based on dollar value for 2023. Although the decline in inflation might indicate a lower dollar value of exports, year-to-date exports until October dwindled by 13.2% compared to the same period in 2022. Exports of molds for plastics fluctuated monthly, ranging between $37.0 million and $57.3 million. October indicated a potential 2.9% rise in export value, but these gains might have been tempered in December, historically a weaker month for exports compared to other months. Anticipating a global output slowdown in 2024, particularly in advanced economies, while stabilizing in emerging and developing economies, it’s likely that any improvements in molds exports will be weaker compared to the preceding two years. 5. Producers Prices in Plastics Material and Resin Manufacturing Plastics material and resin prices hit their peak in April this year, then gradually fell as demand and supply rebalanced. Reduced U.S. plastics production tempered resin demand, while supply increased from July to October compared to the previous year. November saw a 0.4% price hike, but December may mark a 0.2% decrease. Barring unexpected disruptions like adverse weather affecting resin production, it is unlikely we will see a reversal in the recent path of resin prices in 2024. 6. Capacity Utilization Rates in Plastics and Resin Manufacturing The capacity utilization rate in plastics product manufacturing declined throughout 2023, averaging 83.1% monthly in the preceding year and dropping to an average of 77.4% for the year, with an anticipated rate of 76.6% for December. This decline aligns with the observed decrease in plastics conversion activity during the year. Conversely, capacity utilization in plastics material and resin manufacturing experienced an uptick, notably increasing in the latter half of the year. December might have seen a slight decrease in both capacity (0.1%) and utilization rate (0.4%). The imbalance between resin supply and demand contributed to the decrease in the Producer Price Index for plastics material and resin manufacturing in 2023. Projections for 2024 suggest an anticipated increase in capacity utilization for resin manufacturing, albeit possibly at a slower pace compared to 2023. 7. Plastics Machinery Imports The U.S. imported plastics machinery amounting to $1.8 billion, with projected import values of $129.4 million in October and $150.1 million in November. This year’s total imports have decreased by 4.4% compared to the previous year. As a primary importer of plastics equipment, this data serves as a key indicator for understanding plastics manufacturing. Typically, an upsurge in plastics machinery imports signifies robust plastic conversion. The reduced imports of plastics equipment this year correlate with the decline in plastics product manufacturing. The possibility of an uptick in plastics equipment imports in 2024 relies on increased plastics production, provided there is a limited inventory of plastics equipment available. About the Author: The Plastics Industry Association (PLASTICS) is the only organization that supports the entire plastics supply chain, including Equipment Suppliers, Material Suppliers, Processors, and Recyclers, representing over one million workers in our $548 billion U.S. industry. PLASTICS advances the priorities of our members who are dedicated to investing in technologies that improve capabilities and advances in recycling and sustainability and providing essential products that allow for the protection and safety of our lives. Since 1937, PLASTICS has been working to make its members, and the seventh largest U.S. manufacturing industry, more globally competitive while supporting circularity through educational initiatives, industry-leading insights and events, convening opportunities and policy advocacy, including the largest plastics trade show in the Americas, NPE2024: The Plastics Show.
U.S. Rail Traffic for December and the week ending December 30, 2023
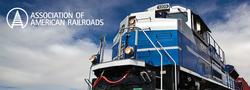
The Association of American Railroads (AAR) has reported U.S. rail traffic for the week ending December 30, 2023, as well as volumes for December 2023. U.S. railroads originated 876,881 carloads in December 2023, up 7.3 percent, or 59,804 carloads, from December 2022. U.S. railroads also originated 982,383 containers and trailers in December 2023, up 10.2 percent, or 90,881 units, from the same month last year. Combined U.S. carload and intermodal originations in December 2023 were 1,859,264, up 8.8 percent, or 150,685 carloads and intermodal units from December 2022. In December 2023, 16 of the 20 carload commodity categories tracked by the AAR each month saw carload gains compared with December 2022. These included: chemicals, up 14,636 carloads or 13.1 percent; coal, up 13,971 carloads or 5.9 percent; and motor vehicles & parts, up 7,212 carloads or 14.1 percent. Commodities that saw declines in December 2023 from December 2022 included: crushed stone, sand & gravel, down 2,781 carloads or 4.1 percent; nonmetallic minerals, down 1,105 carloads or 9.8 percent; and all other carloads, down 625 carloads or 3.3 percent. “Total U.S. rail carloads were up 2.0 percent in the fourth quarter of 2023 over the fourth quarter of 2022, while U.S. intermodal was up 5.5 percent over the same period. That means Q4 was clearly the best quarter of 2023 for U.S. rail volumes on a year-over-year basis,” said AAR Senior Vice President John T. Gray. “It appears that intense rail efforts to improve service quality are paying off. Railroads are hopeful that gains in the fourth quarter will carry over into the first quarter of 2024 and beyond.” Excluding coal, carloads were up 45,833 carloads, or 7.9 percent, in December 2023 from December 2022. Excluding coal and grain, carloads were up 40,036 carloads, or 8.0 percent. Total U.S. carload traffic for the first 12 months of 2023 was 11,701,875 carloads, up 0.7 percent, or 81,504 carloads, from the same period last year; and 12,667,354 intermodal units, down 4.9 percent, or 657,165 containers and trailers, from last year. Total combined U.S. traffic for the first 52 weeks of 2023 was 24,369,229 carloads and intermodal units, a decrease of 2.3 percent compared to last year. Week Ending December 30, 2023 Total U.S. weekly rail traffic was 370,800 carloads and intermodal units, up 3.4 percent compared with the same week last year. Total carloads for the week ending December 30 were 182,062 carloads, up 4.1 percent compared with the same week in 2022, while U.S. weekly intermodal volume was 188,738 containers and trailers, up 2.7 percent compared to 2022. Six of the 10 carload commodity groups posted an increase compared with the same week in 2022. They included chemicals, up 6,273 carloads, to 30,543; farm products excl. grain, and food, up 2,370 carloads, to 15,310; and petroleum and petroleum products, up 1,537 carloads, to 8,936. Commodity groups that posted decreases compared with the same week in 2022 included motor vehicles and parts, down 1,705 carloads, to 7,712; miscellaneous carloads, down 1,493 carloads, to 5,317; and nonmetallic minerals, down 898 carloads, to 18,723. North American rail volume for the week ending December 30, 2023, on 10 reporting U.S., Canadian and Mexican railroads totaled 270,807 carloads, up 5.0 percent compared with the same week last year, and 254,475 intermodal units, up 3.8 percent compared with last year. Total combined weekly rail traffic in North America was 525,282 carloads and intermodal units, up 4.4 percent. North American rail volume for the first 52 weeks of 2023 was 34,105,519 carloads and intermodal units, down 2.1 percent compared with 2022. Canadian railroads reported 75,463 carloads for the week, up 9.9 percent, and 56,220 intermodal units, up 6.4 percent compared with the same week in 2022. For the first 52 weeks of 2023, Canadian railroads reported cumulative rail traffic volume of 8,299,862 carloads, containers and trailers, down 2.4 percent. Mexican railroads reported 13,282 carloads for the week, down 8.1 percent compared with the same week last year, and 9,517 intermodal units, up 13.1 percent. Cumulative volume on Mexican railroads for the first 52 weeks of 2023 was 1,436,428 carloads and intermodal containers and trailers, up 2.1 percent from the same point last year. To view the traffic charts, click here.
Episode 449: Leveraging AI to optimize last-mile delivery with Senpex
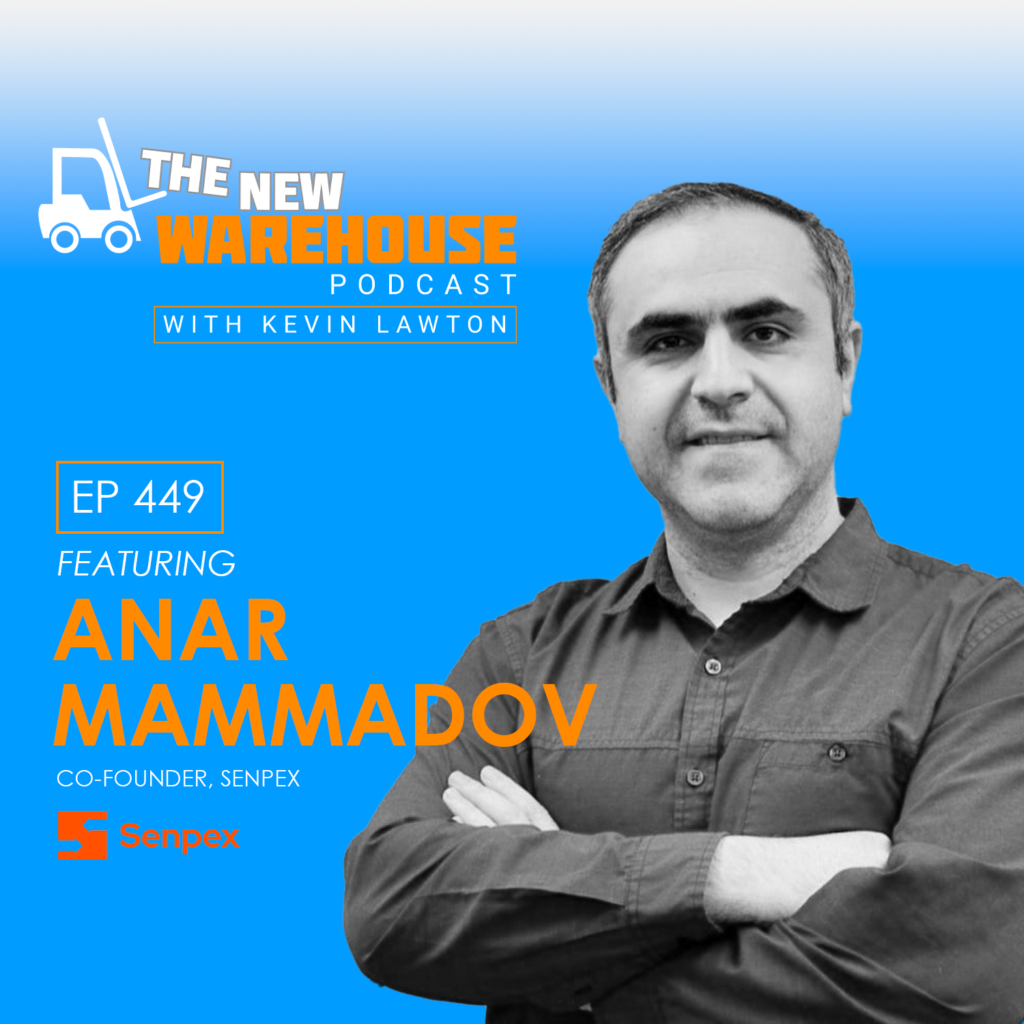
In this episode of the New Warehouse Podcast, Anar Mammadov, the Technical Co-Founder of Senpex, shares how Senpex uses artificial intelligence for route optimization to tackle persistent challenges of last-mile delivery. Mammadov shares his extensive experience and Senpex’s solutions to streamline logistics operations. The Genesis of Senpex: A Journey Led by Innovation Anar Mammadov recounts his journey into the logistics industry, “I’ve worked and managed different enterprise solutions. In supply chain, I have more than 18 years of experience.” He highlights the inception of Senpex as a response to glaring gaps in the U.S. logistics sector. “I did a lot of different projects and implemented different solutions and I just decided, why not try and solve this problem in the supply chain and find a way for people to receive their product from different verticals within an hour.” The Core of Senpex: Last-Mile Delivery Revolutionized Mammadov discusses Senpex’s mission, “We’re helping warehouses or 3PLs make proper planning of their routes from their warehouse to their customers efficiently with less resources.” He explains how Senpex specializes in optimizing routes for the timely delivery of various products, emphasizing the high costs and complexities of last-mile delivery. The Role of AI in Enhancing Logistic Efficiency Mammadov illuminates the transformative power of AI in logistics, emphasizing that despite advancements like drone and autonomous deliveries, the demand for direct-to-home services is surging. Mammadov elaborates on the emerging trend of ‘dark warehouses,’ which allows brands to distribute products closer to consumers, enhancing efficiency and speed. He believes dark warehouses will be crucial in this rapidly growing sector, enabling brands to establish a presence near their customers and facilitating faster deliveries through partners like Senpex. This approach not only maintains brand integrity but also significantly reduces delivery times. “We’re committed to optimizing routes and improving service reliability through AI. Our goal is to become the Shopify of last-mile logistics, continually innovating and addressing industry challenges,” Mammadov asserts, reflecting his ambition to lead in the logistics space through advanced AI applications. Key Takeaways Senpex leverages AI for route optimization, significantly improving last-mile delivery. The company focuses on efficient, timely delivery, addressing the high costs and complexities inherent in the logistics sector. Predictive analytics and data-driven strategies are pivotal in enhancing delivery services and reducing failure rates. The New Warehouse Podcast EP 449: Leveraging AI to Optimize Last-Mile Delivery with Senpex
E Tech Group announces name change of recently acquired System Integrator, E-Volve Systems
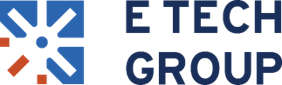
E Tech Group announces the immediate renaming of E-Volve Systems to E Tech Group, following their strategic acquisition on February 23, 2023, emphasizing a unified vision, expanded services, and enhanced client and market value through this integration E Tech Group has announced that the brand formerly known as E-Volve Systems has now been renamed as E Tech Group. Effective immediately, the brand formerly known as E-Volve Systems will operate under the name E Tech Group, unifying the two entities under one market-leading brand. The transition to the new name will be seamless for clients and partners. All existing commitments remain in place, ensuring continuity and stability. “We’ve gained the ability to market and deliver large scale projects that may not have been available to us prior to the acquisition due to our size,” said Kevin Stout, previous E-Volve Systems founder and president and current vice president at E Tech Group. “We’ve also gained a tremendous network of team members whose skillsets seem to be limitless.” E Tech Group’s acquisition of E-Volve Systems was finalized on February 23, 2023. This strategic move allowed E Tech Group to significantly expand its range of services, thereby enhancing the overall value offered to its clients. The acquisition was a step towards integrating complementary strengths, consolidating market presence, and fostering innovation in service delivery. “The name change at this time is a formality as E-Volve Systems has been a part of the E Tech Group since late February 2023,” said Matt Wise, Chief Executive Officer of E Tech Group. “Their contributions have positioned E Tech Group to elevate its service offerings and reach with the added benefit of resources located throughout North America as well as a broader suite of services, allowing us to automate every facet of a facility, from process and discrete automation through cybersecurity and data intelligence services, leveraging a team of over 600 automation specialists.”
Episode 448: ShipPlug – Streamlining shipping with data-driven solutions
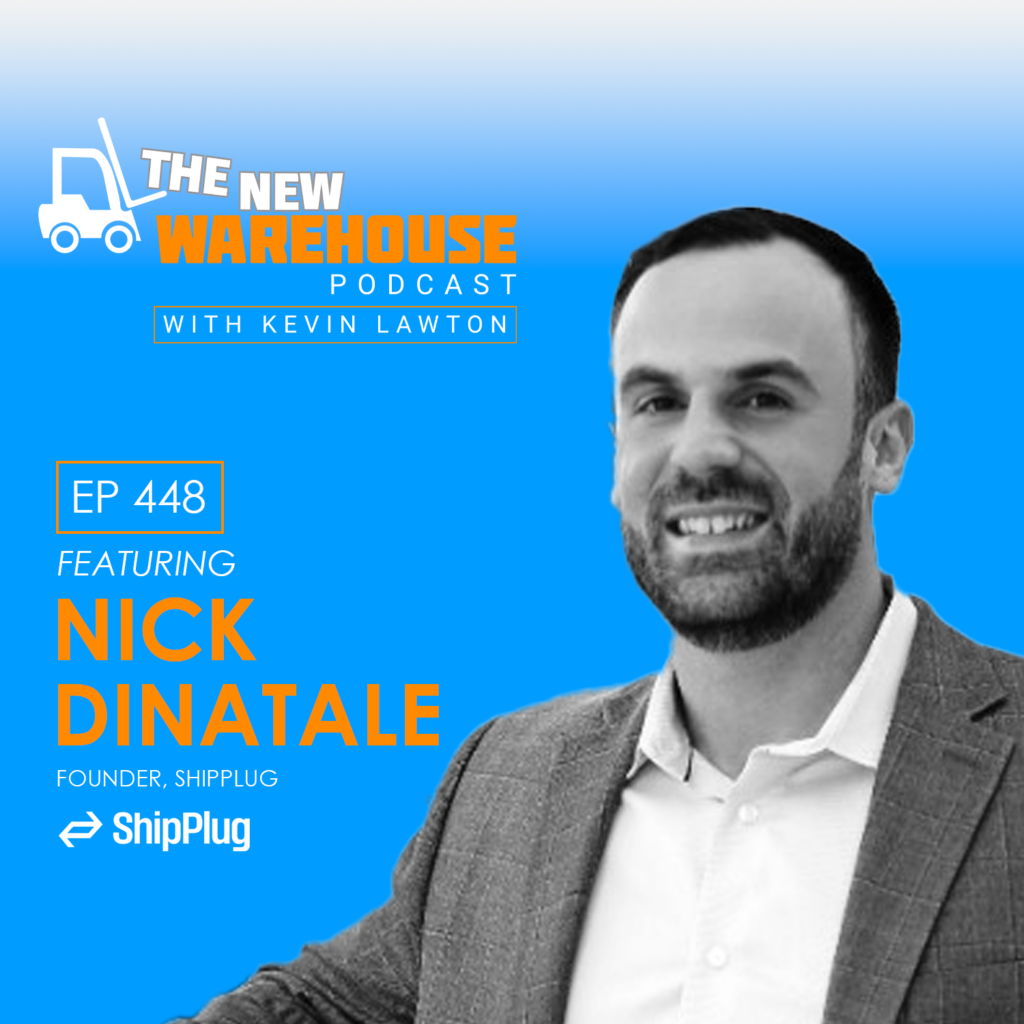
Episode 448 of The New Warehouse Podcast features an engaging conversation with Nick DiNatale, co-founder and CEO of ShipPlug. ShipPlug specializes in providing integrated shipping solutions, simplifying the shipping process for businesses. The episode explores ShipPlug’s innovative approach to combining multiple shipping services into a cohesive, user-friendly platform. Bridging the Gap in Shipping Data Access DiNatale compares the challenges faced by large and small shippers. He explains that large enterprises, shipping millions of dollars worth of goods, often have dedicated supply chain teams who analyze data regarding package shipments, costs, and delays. Small shippers, however, struggle with accessing this kind of data due to limited resources. They often resort to guessing shipping costs and sometimes choose not to sell certain products because they can’t work out profitable shipping strategies. DiNatale highlights that accessing and understanding supply chain data is increasingly complex and challenging for all, especially for small shippers lacking resources. He adds, “When we started ShipPlug, our goal was to make data easy to understand.” ShipPlug Simplifies the Freight Claim Process through Automation DiNatale highlights ShipPlug’s role in demystifying and streamlining the freight claim process, particularly for late shipments and damage claims. He notes how the traditional claims process is tedious and often confusing, deterring many shippers, especially smaller ones, from pursuing refunds or understanding their shipping costs. ShipPlug’s software automates this process, enabling shippers to file claims quickly, track late shipments, and receive detailed reasons for delays. This data allows for more informed decisions about carrier performance and helps e-commerce businesses manage the increasingly complex world of shipping costs and demand surcharges. Unified Carrier Integration and Pricing Transparency with ShipPlug DiNatale discusses ShipPlug’s ability to integrate various carriers, offering a unified platform for diverse shipping needs. “Providing data, especially around pricing, that’s the true value not only to make the claims process easier but to truly help you understand what they are paying,” he states. While the General Rate Increase (GRI) for carriers averages around 5.9%, DiNatale points out some surcharges go up as high as 17%. Delivery surcharges are becoming so confusing and difficult to manage that they become one of the biggest struggles for shippers. “Having the data to make actionable decisions on the best carrier or carrier mix can make or break a company,” DiNatale emphasizes. He details how ShipPlug’s platform is designed for simplicity, incorporating features like streamlined label printing and address verification. Key Takeaways ShipPlug’s integration of multiple carriers simplifies the shipping process for businesses. Focus on user experience and technology enhances the efficiency of shipping operations. Emerging e-commerce trends underscore the importance of versatile, integrated shipping solutions. The New Warehouse Podcast EP 448: ShipPlug – Streamlining Shipping with Data-Driven Solutions
Walker takes reins as CEO of MHEDA
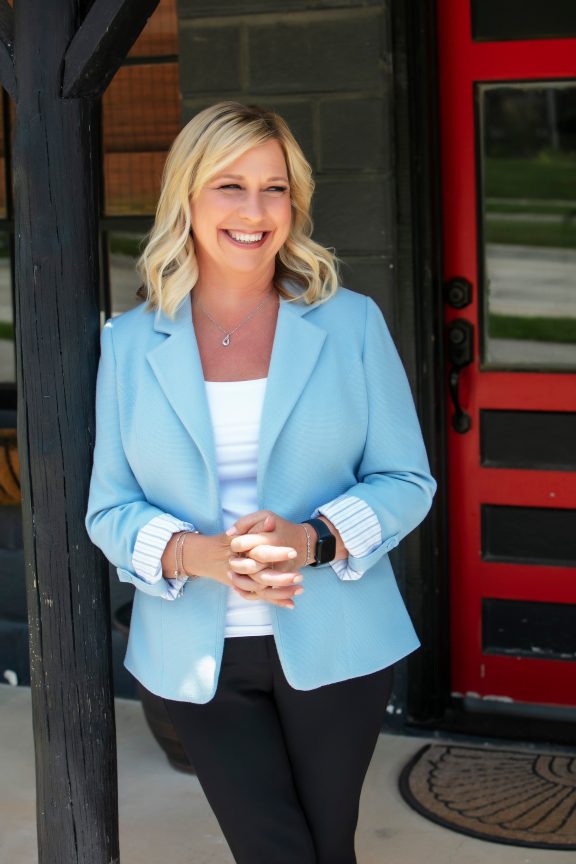
Jeannette Walker is the new chief executive officer of the Material Handling Equipment Distributors Association (MHEDA). She served as interim chief executive officer when Liz Richards retired on December 31, 2023. “Jeannette is the ideal selection given her vast background in executive leadership, marketing and communications, all the traits that are essential in association management.” said Liz Richards. “Combined with Jeannette’s knowledge and deep relationships with industry members and with the MHEDA team, this is a win-win-win for everyone.” added Richards. Walker has held executive positions in the materials handling sector for 22 years, most recently at TVH. “I am truly honored to have been selected for this pivotal role, and I am eager to contribute my skills and experience to MHEDA,” she said. ““I am committed to building upon the foundation that has been laid by Liz Richards’ inspirational vision and leadership.”” added Walker.
Staffing employment seasonally dips in December
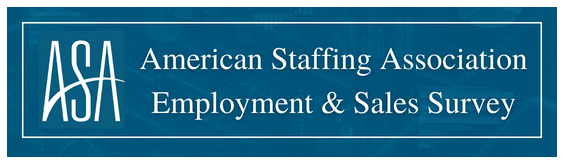
Staffing employment dipped in the week of Dec. 11-17, with the ASA Staffing Index decreasing by 0.9% to a rounded value of 97. Some staffing companies mentioned seasonal business fluctuations and the holidays as primary factors that limited further growth. Staffing jobs were 8.3% below the same week last year. New starts in the 50th week of the year were down 2.5% from the prior week. Nearly four in 10 staffing companies (35%) reported gains in new assignments week to week. The ASA Staffing Index four-week moving average decreased from the prior week to a rounded value of 97, and temporary and contract staffing employment for the four weeks ending Dec. 17 was 8.3% lower than the same period in 2022. “The ASA Staffing Index saw a slight drop in December, though some holiday frostbite is typical for staffing employment this time of year,” said Noah Yosif, chief economist at ASA. This week will be used in the December monthly employment situation report scheduled to be issued by the U.S. Bureau of Labor Statistics on Jan. 5. To learn more about the quarterly ASA Staffing Employment and Sales Survey, visit americanstaffing.net/quarterly-survey or follow ASA research on X.
Rail Traffic for the Week Ending December 23, 2023
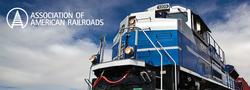
The Association of American Railroads (AAR) today reported U.S. rail traffic for the week ending December 23, 2023. For this week, total U.S. weekly rail traffic was 486,787 carloads and intermodal units, up 24.2 percent compared with the same week last year. Total carloads for the week ending December 23 were 230,946 carloads, up 23.7 percent compared with the same week in 2022, while U.S. weekly intermodal volume was 255,841 containers and trailers, up 24.7 percent compared to 2022. All of the 10 carload commodity groups posted an increase compared with the same week in 2022. They included coal, up 16,458 carloads, to 66,730; motor vehicles and parts, up 4,936 carloads, to 16,287; and grain, up 4,475 carloads, to 21,237. For the first 51 weeks of 2023, U.S. railroads reported a cumulative volume of 11,519,813 carloads, up 0.6 percent from the same point last year; and 12,478,616 intermodal units, down 5.0 percent from last year. Total combined U.S. traffic for the first 51 weeks of 2023 was 23,998,429 carloads and intermodal units, a decrease of 2.4 percent compared to last year. North American rail volume for the week ending December 23, 2023, on 12 reporting U.S., Canadian, and Mexican railroads totaled 340,069 carloads, up 21.4 percent compared with the same week last year, and 337,542 intermodal units, up 25.3 percent compared with last year. Total combined weekly rail traffic in North America was 677,611 carloads and intermodal units, up 23.3 percent. North American rail volume for the first 51 weeks of 2023 was 33,580,237 carloads and intermodal units, down 2.2 percent compared with 2022. Canadian railroads reported 93,678 carloads for the week, up 23.1 percent, and 70,358 intermodal units, up 33.5 percent compared with the same week in 2022. For the first 51 weeks of 2023, Canadian railroads reported a cumulative rail traffic volume of 8,168,179 carloads, containers, and trailers, down 2.5 percent. Mexican railroads reported 15,445 carloads for the week, down 11.0 percent compared with the same week last year, and 11,343 intermodal units, down 2.2 percent. Cumulative volume on Mexican railroads for the first 51 weeks of 2023 was 1,413,629 carloads and intermodal containers and trailers, up 2.1 percent from the same point last year. For the traffic charts, click here
Key Texas Rail Gateways Reopen, Railroads ready to restore service
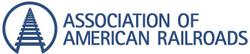
After five days of closures at Eagle Pass and El Paso, TX, U.S. Customs and Border Protection (CBP) announced today that the agency would reopen these key international crossings. With each passing day, rail customers, communities and the larger supply chain experienced increasing impacts as rail shipments remained halted at the border. Today, the Biden Administration answered wide-spread, resounding calls to restore this critical link in the supply chain. “The Biden Administration made the right decision to protect our supply chain and keep goods moving between the U.S. and Mexico,” said AAR President and CEO Ian Jefferies. “In the face of the unprecedented humanitarian crisis, CBP has been working under exceptionally difficult circumstances, but these ill-advised closures were a blunt force tool that did nothing to bolster law enforcement capacity. As CBP continues their work to address this crisis, railroads strongly encourage the agency to abandon this tactic moving forward in favor of approaches that are capable of meaningfully enhancing its response capabilities. “With the crossings reopened, railroads are focused on closely partnering with CBP to maintain the secure, reliable service that customers deserve and our nation requires.”
Equipment Depot becomes an early adopter of AWS Supply Chain in the material handling industry
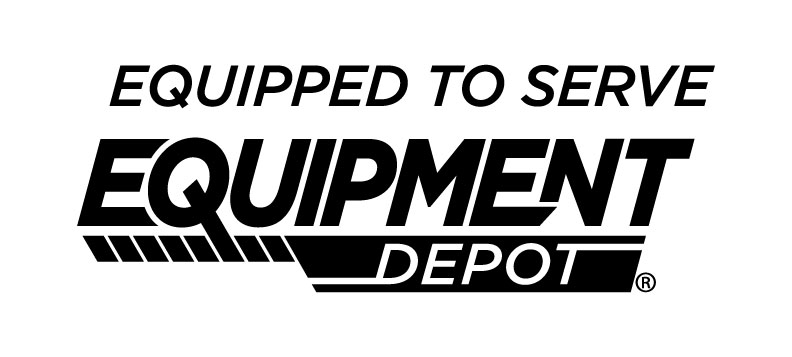
Equipment Depot announced that they have been selected by Amazon Web Services, Inc. (AWS), to adopt AWS Supply Chain, a cloud-based application. As an early adopter in the material handling industry, AWS Supply Chain is designed to increase supply chain visibility to make faster, more informed decisions that mitigate risks and lower costs. Its primary directive will focus on Equipment Depot’s $22 million in parts inventory. “We have over 50 branches covering 3000 miles, plus 850 technicians; the AWS Supply Chain technology will provide machine learning (ML) technology capable of anticipating low parts inventory and OEM delays and reallocating parts to multiple branches and service fleets with real-time forecasting.” According to Joakim Langkaas, Director of Operations at Equipment Depot, “AWS Supply Chain automatically combines and analyzes data across multiple platforms, finding trends and quickly taking inventory rebalancing actions. We are pleased to include the AWS Supply Chain technology in our overall digital transformation strategy.” AWS Supply Chain is a cloud-based application that unifies data and provides ML-powered actionable insights, built-in contextual collaboration, and demand planning. The application can connect to existing enterprise resource planning (ERP) and supply chain management systems without re-platforming, upfront licensing fees, or long-term commitments. AWS Supply Chain will increase focus on data-driven supply decisions by leveraging advanced algorithmic capabilities within a simple and intuitive interface. Carol Tesarek, Director of Customer Experience at Equipment Depot, adds “AWS Supply Chain introduces ML and predictive maintenance capabilities to our supply chain operations. This allows us to provide an even greater customer experience by ensuring our technicians are fully equipped during customer service calls, resulting in increased speed of service, decreased equipment downtime, and an improved customer experience. I’m excited to witness the impact on customer experience, our technicians, and our entire process in the parts department.”
Carolina Handling named South Carolina Veteran Friendly Employer
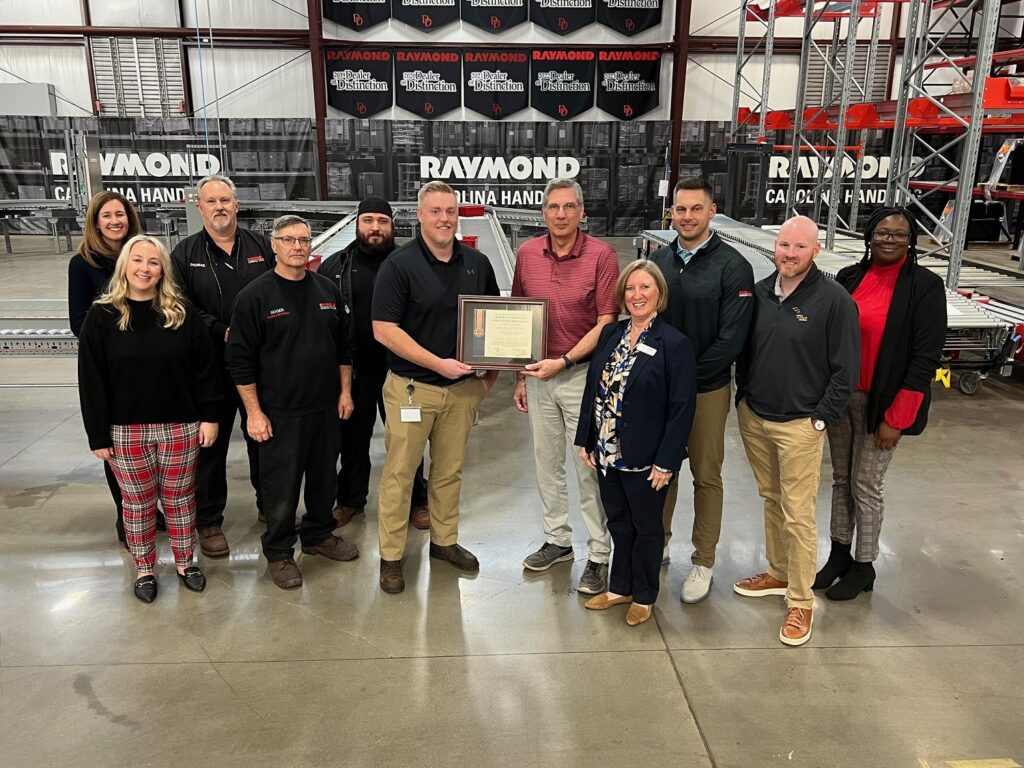
Carolina Handling was named a veteran-friendly employer by the South Carolina Department of Veterans Affairs (SCDVA) during a presentation held on December 5, 2023, at the company’s Hilton Learning Center in Piedmont, South Carolina. The SCDVA program recognizes South Carolina businesses that actively recruit military veterans and empower and enhance their employment through training and career development opportunities. Carolina Handling received the program’s certificate of bronze standard. “It’s an honor to be here to give you this award on behalf of the South Carolina Department of Veterans Affairs and Secretary Todd McCaffrey and to recognize Carolina Handling not only for the great services you provide veterans in your workforce, but also veterans in your community,” said SCDVA Operations Coordinator Kailay P. Washington. The exclusive Raymond Solutions and Support Center in South Carolina, North Carolina, Georgia, Alabama and the panhandle of Florida, Carolina Handling in a leading materials handling equipment supplier, offering consulting, design and engineering services, and integrated automation solutions for manufacturers, warehouses and distribution centers. About 12.5 percent of Carolina Handling’s 759 associates served in the U.S. Armed Forces. The company has 212 South Carolina associates, 31 of whom are military veterans. The presenting sponsor of the Veterans Employment & Transition Summit hosted by The RECON Network and a multi-year sponsor of the Military & First Responders Skybox at the BMW Charity Pro-Am in Greenville, South Carolina, Carolina Handling is committed to raising awareness among military veterans about careers in material handling. “The skills developed while serving in the U.S. Armed Forces can make you highly successful in the material handling industry,” said Carolina Handling President & CEO Brent Hillabrand. “Carolina Handling offers comprehensive onboarding and continuous training to assist with a meaningful military-to-civilian transition and a purpose-driven career.”
First Citizens Bank Equipment Finance names Shanks Head of Business Development
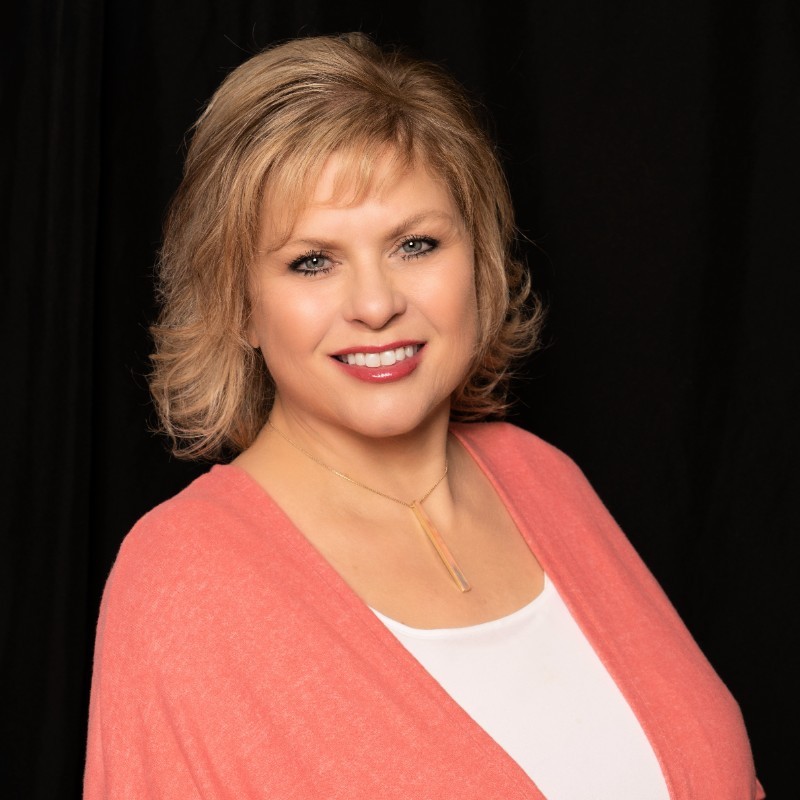
First Citizens Bank has announced that its Equipment Finance business has named Joy Shanks as senior vice president and head of business development dedicated to supporting and growing equipment finance vendor acquisition business. Shanks will be responsible for acquiring and cultivating new vendor relationships in key industries, as well as driving long-term business growth and generating meaningful end-user equipment financing transaction volume. She will also manage the internal sales cycle of the Equipment Finance business, including the advancement of key sales protocols. Shanks will lead a high-performing sales team and report directly to Ken Martin, a managing director at First Citizens Bank Equipment Finance. “Joy brings a wealth of knowledge and experience in driving sales growth, capturing new business development opportunities and promoting brand awareness for companies in the financial services and technology industries,” said Ken Martin. “We are excited to welcome Joy to our team and are confident her skillset and perspective will contribute to the success of First Citizens Bank Equipment Finance as we strive to be the best salesforce in America.” Shanks joins First Citizens Bank with over 30 years of experience in sales, business development, operations and marketing. She most recently served as senior director, Global Channel Leader at Hewlett-Packard Enterprise Financial Services where she led Global Business Development function and championed partner development, lead generation and sales enablement activities. Prior to that she held several roles at Dell in global marketing, strategy and sales. She also served in business development roles at Frost National Bank and HP Compaq. Shanks attended Oakland University. First Citizens Bank Equipment Finance works with manufacturers, franchisors, distributors, resellers, dealers and systems integrators to finance their equipment, software and services to commercial customers.
New Distribution and Supply Chain Planned Industrial Project Drops for November 2023 to Below June Levels
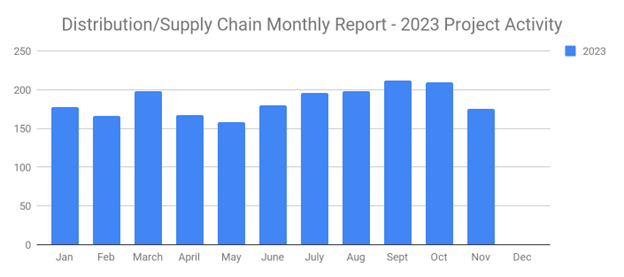
Industrial SalesLeads announced the November 2023 results for the new planned capital project spending report for the Distribution and Supply Chain industry. The Firm tracks North American planned industrial capital project activity; including facility expansions, new plant construction and significant equipment modernization projects. Research confirms 175 new projects in the Distribution and Supply Chain sector as compared to 210 in October. The following are selected highlights on new Distribution Center and Warehouse construction news. Distribution and Supply Chain – By Project Type Distribution/Fulfillment Centers – 19 New Projects Industrial Warehouse – 158 New Projects Distribution and Supply Chain- By Project Scope/Activity New Construction – 88 New Projects Expansion – 30 New Projects Renovations/Equipment Upgrades – 51 New Projects Closing – 8 New Projects Distribution and Supply Chain – By Project Location (Top 5 States) Texas – 16 California – 13 Florida – 13 Illinois – 10 Pennsylvania – 9 Largest Planned Project During the month of November, our research team identified 1 new Distribution and Supply Chain facility construction project with an estimated value of $100 million or more. The largest project is owned by Nucor Corporation, who is planning to invest $280 million for the expansion and equipment upgrades on their manufacturing and warehouse facility in TUSCALOOSA, AL. They have recently received approval for the project. Completion is slated for Summer 2027. Top 10 Tracked Distribution and Supply Chain Project Opportunities VIRGINIA: Specialty metal processing company is planning to invest $82 million for the expansion of their processing and warehouse facility in SOUTH BOSTON, VA. They have recently received approval for the project. ILLINOIS: Eyewear MFR. is planning to invest $80 million for the construction of a 150,000 sf manufacturing, warehouse, laboratory, and office facility on Allen Lane in PEORIA, IL. They have recently received approval for the project. Completion is slated for late 2025. SOUTH CAROLINA: Corrugated packaging products MFR. is planning to invest $68 million for the renovation and equipment upgrades on a 259,000 SF manufacturing and warehouse facility at 1105 Scotts Bridge Rd. in ANDERSON, SC. They have recently received approval for the project. VIRGINIA: Logistics service provider is planning to invest $60 million for the expansion of their distribution and warehouse center in NORFOLK, VA by 450,000 SF. They have recently received approval for the project. CALIFORNIA: Airport authority is planning to invest $40 million for the construction of a 521,000 SF warehouse and office facility at 1497 S Commerce Pw in ONTARIO, CA. They are currently seeking approval for the project. TENNESSEE: Logistics service provider is planning to invest $38 million for the construction of an 85,000 SF warehouse facility in KNOXVILLE, TN. They are currently seeking approval for the project. NEW YORK: Automotive MFR. is planning to invest $30 million for the construction of a distribution center in FISHKILL, NY. They will relocate their MANSFIELD, MA operations upon completion in 2025. WISCONSIN: Construction equipment MFR. is planning to invest $30 million for the renovation and equipment upgrades on their manufacturing facility in MENOMONEE FALLS, WI. The project includes the construction of a 100,000 SF warehouse at the site. They are currently seeking approval for the project. ARIZONA: OEM parts supplier is planning for the renovation and equipment upgrades on a 420,000 SF distribution center in GLENDALE, AZ. Completion is slated for late 2024. GEORGIA: Auto parts supplier is planning for the construction of a 205,000 SF warehouse at 3351 Gateway Centre Pkwy in GAINESVILLE, GA. They are currently seeking approval for the project. About Industrial SalesLeads, Inc. Since 1959, Industrial SalesLeads, based in Jacksonville, FL is a leader in delivering industrial capital project intelligence and prospecting services for sales and marketing teams to ensure a predictable and scalable pipeline
Industrial News and Planned Industrial Construction Projects for November 2023 Recap
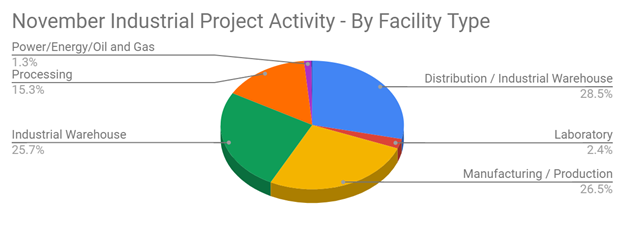
Research by Industrial SalesLeads’ experienced industrial market research team, shows 423 new planned industrial projects tracked during the month of November. Manufacturing and Production increased 4.3% as well as Industrial Warehouse by just about 3%. Overall, planned industrial project activity increased 1% from the previous month. The following are selected highlights on new industrial construction news and project opportunities throughout North America. Planned Industrial Construction – By Project Type: Manufacturing Facilities – 163 New Projects Processing Facilities – 94 New Projects Distribution and Industrial Warehouse – 175 New Projects Power/Energy/Oil and Gas – 8 New Projects Laboratory Facilities – 15 New Projects Mine – 1 New Project Terminal – 0 New Projects Pipeline – 0 New Projects Planned Industrial Construction – By Scope/Activity New Construction – 177 New Projects Expansion – 106 New Projects Renovations/Equipment Upgrades – 151 New Projects Plant Closing – 23 New Projects Planned Industrial Construction – By Location (Top 10 States) Texas – 29 California – 27 New York- 23 Indiana – 21 Ohio – 21 Michigan – 17 Wisconsin – 17 Florida – 16 Illinois – 16 North Carolina – 16 Largest Planned Industrial Construction Project During the month of November, our research team identified 26 new General Industrial facility construction projects with an estimated value of $100 million or more. The largest project is owned by Dow Chemical Canada, who is planning to invest $10 billion for the construction of a processing facility in FORT SASKATCHEWAN, AB. They are currently seeking approval for the project. Construction is expected to start in 2024, with completion slated for 2029. Top 10 Tracked Industrial Construction Projects NORTH CAROLINA: Automotive MFR. is planning to invest an additional $8 billion for the expansion of their currently under-construction EV battery manufacturing facility in LIBERTY, NC. Completion is slated for 2025. TEXAS: Global electronics MFR. is planning to invest $8 billion for the construction of an additional 2.7 million manufacturing facility in TAYLOR, TX. They are currently seeking approval for the project. Construction is expected to start in late 2024. ALBERTA: Oil and gas company is planning to invest $2 billion for the construction of a processing facility in STRATHCONA COUNTY, AB. They are currently seeking approval for the project. BRITISH COLUMBIA: Battery MFR. is planning to invest $1 billion for the construction of a manufacturing facility in MAPLE RIDGE, BC. Construction is expected to start in Summer 2024, with completion slated for 2028. LOUISIANA: Chemical company is planning to invest $800 million for the construction of two processing facilities in ST. GABRIEL, LA. They are currently seeking approval for the project. Construction is expected to start in 2025, with completion slated for 2026. ALBERTA: Specialty fiber board MFR. is planning to invest $800 million for the construction of a manufacturing facility in STETTLER, AB. They are currently seeking approval for the project. NORTH CAROLINA: Battery material MFR. is planning to invest $650 million for the construction of a 1.5 million SF manufacturing campus in WILMINGTON, NC. They have recently received approval for the project. Construction is expected to start in 2024, with completion slated for 2026. SOUTH CAROLINA: Automotive component MFR. is planning to invest $500 million for the expansion and equipment upgrades on their manufacturing and warehouse facility at 2846 N. Old Laurens Rd. in GRAY COURT, SC. They have recently received approval for the project. CALIFORNIA: Aerospace company is planning to invest $500 million for the renovation and equipment upgrades on their manufacturing and research facilities in LONG BEACH, CA, and MOJAVE, CA. They are currently seeking approval for the project. ALABAMA: Steel company is planning to invest $280 million for the expansion and equipment upgrades on their manufacturing and warehouse facility in TUSCALOOSA, AL. They have recently received approval for the project. Completion is slated for Summer 2027. About Industrial SalesLeads, Inc. Since 1959, Industrial SalesLeads, based in Jacksonville, FL is a leader in delivering industrial capital project intelligence and prospecting services for sales and marketing teams to ensure a predictable and scalable pipeline.
61 New Food and Beverage Industry Planned Projects for November 2023 Holds Firm with October
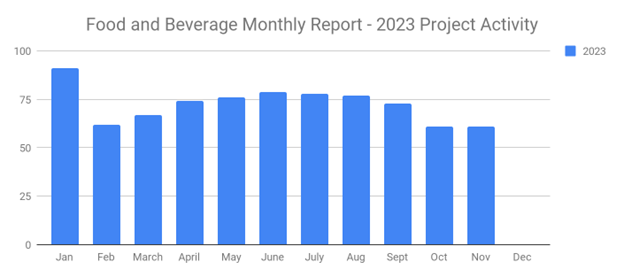
Industrial SalesLeads announced the November 2023 results for the new planned capital project spending report for the Food and Beverage industry. The Firm tracks North American planned industrial capital project activity; including facility expansions, new plant construction and significant equipment modernization projects. Research confirms 61 new projects in the Food and Beverage sector for both November and October. The following are selected highlights on new Food and Beverage industry construction news. Food and Beverage Project Type Processing Facilities – 33 New Projects Distribution and Industrial Warehouse – 34 New Projects Food and Beverage Project Scope/Activity New Construction – 27 New Projects Expansion – 25 New Projects Renovations/Equipment Upgrades – 17 New Projects Plant Closing – 1 New Project Food and Beverage Project Location (Top 10 States) California – 8 New York – 5 Texas – 4 Illinois – 3 Tennessee – 3 Kentucky – 2 Michigan – 2 Minnesota – 2 North Carolina – 2 South Carolina – 2 Largest Planned Project During the month of November, our research team identified 1 new Food and Beverage facility construction projects with an estimated value of $100 million or more. The largest project is owned by Nissin Foods USA, who is planning to invest $228 million for the renovation and equipment upgrades on a recently acquired 641,000 sf processing and warehouse facility at 1170 Bracken Rd. in PIEDMONT, SC. Completion is slated for late 2025. Top 10 Tracked Food and Beverage Projects TEXAS: Grocery chain is planning to invest $60 million for the expansion and equipment upgrades on their processing and warehouse facility at 4710 N. Interstate 35 in SAN ANTONIO, TX. Construction is expected to start in early 2024, with completion slated for Summer 2025. WISCONSIN: Dairy company is planning for the construction of a 311,000 SF of distribution, cold storage, and office facility on County Line Rd. in FRANKLIN, WI. They are currently seeking approval for the project. CALIFORNIA: Specialty nut oil producer is planning for the expansion of their processing, warehouse, storage, and office facility in DENAIR, CA by 62,000 SF. They are currently seeking approval for the project. Construction is expected to start in Summer 2025. GEORGIA: Vending equipment MFR. is planning to invest $20 million for the renovation and equipment upgrades on a manufacturing, training, warehouse, and office facility in SAVANNAH, GA. They are currently seeking approval for the project. They will relocate their operations upon completion. NEVADA: Food packaging service provider is planning to invest $13 million for the renovation and equipment upgrades on a processing facility in NORTH LAS VEGAS, NV. They are currently seeking approval for the project. MINNESOTA: Food processing company is planning to invest $7 million for the renovation and equipment upgrades on a 360,000 SF processing, warehouse, and office facility in CANNON FALLS, MN. They have recently received approval for the project. They will consolidate their operations upon completion. TEXAS: Specialty food products MFR. is planning to invest $4 million for the renovation and equipment upgrades on 122,000 sf of warehouse and office space at 31895 US Hwy. 90 in BROOKSHIRE, TX. They will relocate their operations upon completion in early Fall 2024. PENNSYLVANIA: Fresh produce company is planning for the expansion of their warehouse and office facility in ALLENTOWN, PA by 49,000 SF. They have recently received approval for the project. MASSACHUSETTS: Animal feed MFR. is planning for the construction of a 21,000 SF processing facility at 233 Old Webster Rd. in OXFORD, MA. They are currently seeking approval for the project. CALIFORNIA: Winery is planning for the construction of an 18,000 SF production facility in ST. HELENA, CA. They are currently seeking approval for the project. About Industrial SalesLeads, Inc. Since 1959, Industrial SalesLeads, based in Jacksonville, FL is a leader in delivering industrial capital project intelligence and prospecting services for sales and marketing teams to ensure a predictable and scalable pipeline. Our Industrial Market Intelligence, IMI identifies timely insights on companies planning significant capital investments such as new construction, expansion, relocation, equipment modernization and plant closings in industrial facilities.