H&E opens new branch in Texarkana, Texas
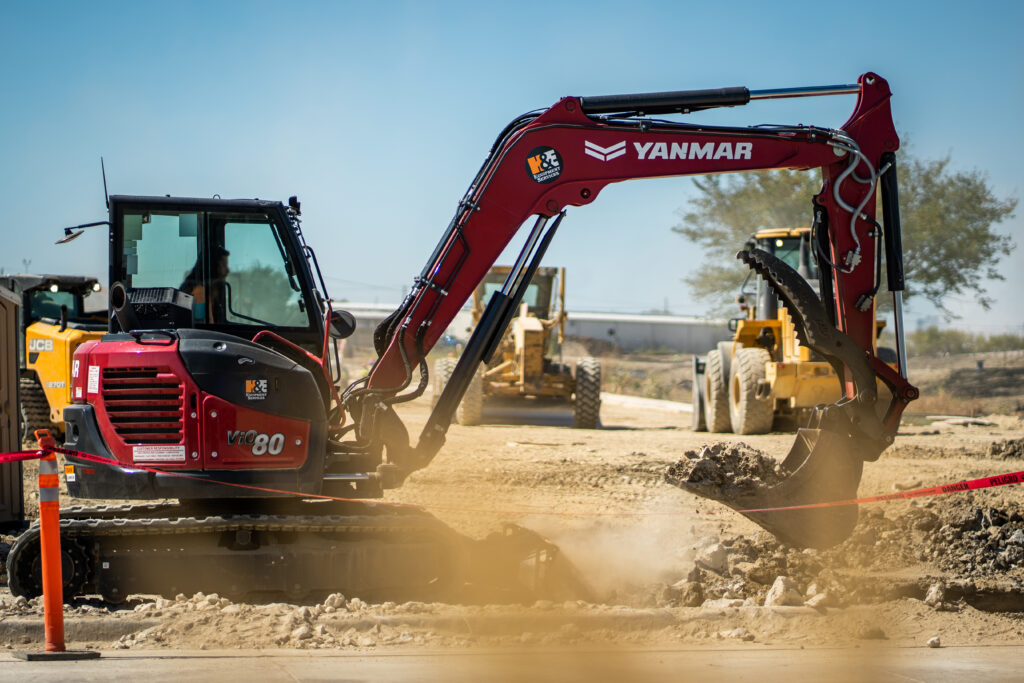
Effective November 6, 2023, H&E Equipment Services Inc. (H&E) announces the opening of its Texarkana branch. The location on the Texas-Arkansas line makes it the company’s 24th rental location in the state of Texas, but it is the third branch to serve the Arkansas market, primarily in the southwestern area of the state. So far this year, H&E has opened 13 new branches across the country. The facility is located at 4300 Gazola Street, Texarkana, TX 75501-7136, phone 430-455-4000. It includes a fully fenced yard area, offices, and a repair shop and carries a variety of construction and general industrial equipment. “H&E has extended its coverage across the Texas-Arkansas state line to easily reach any project between our existing Longview, Shreveport, El Dorado, and Little Rock branches. We’ve added greater fleet availability to the area, and the location of our new facility allows quick access to I-30, I-49, and state highways that branch off in all directions, so delivery of rental equipment to job sites is timely and efficient,” says Branch Manager Hunter Hatfield. “I’ve worked from our Dallas branch for many years, so I’ve hit the ground running and can help customers secure the right equipment for their projects from this new location.” The Texarkana branch specializes in the rental of aerial lifts, earthmoving equipment, telescopic forklifts, compaction equipment, generators, light towers, compressors, and more and represents the following manufacturers: Allmand, Atlas Copco, Bomag, Case, Club Car, Cushman, Doosan, Gehl, Generac Mobile, Genie, Hamm, Hilti, Husqvarna, JCB, JLG, John Deere, Kobelco, Kubota, LayMor, Ledwell, Lincoln Electric, Link-Belt Excavators, MEC, Miller, Multiquip, Polaris, Sany, Skyjack, SkyTrak, Sullair, Sullivan-Palatek, Tag, Towmaster, Unicarriers, Wacker Neuson, Yanmar, and others.
AIT Worldwide Logistics welcomes Susan Caldwell as vice president of talent management
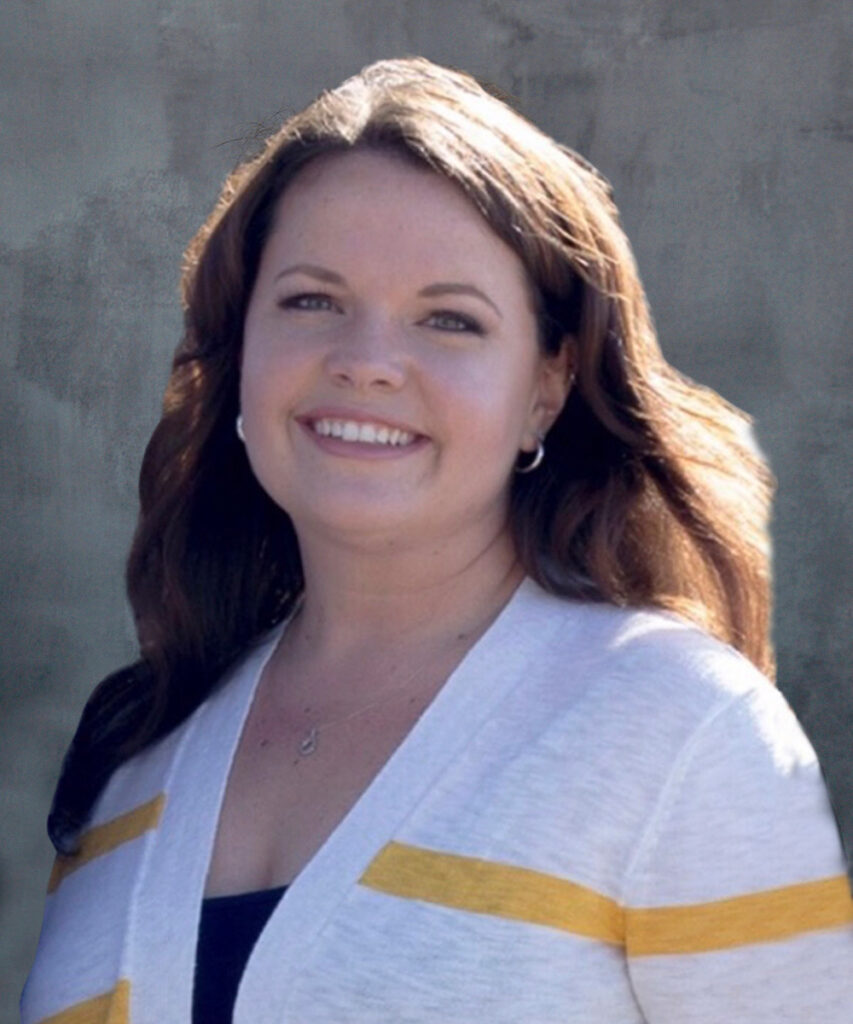
New role will enhance freight forwarder’s human resources programs across North America region AIT Worldwide Logistics has announced that Susan Caldwell who has joined the organization as vice president of talent management for the company’s North America region. In this role, Caldwell will shape talent strategy by designing and executing programs in areas including organizational development, talent development, teammate engagement, performance management, succession planning, change management and communications. She reports to Chief Human Resources Officer, Angela Mancuso. “Susan is an instrumental hire for us at a pivotal time of global growth for AIT,” Mancuso said. “Her bilingual proficiency, combined with her depth of experience across various sectors, positions us to further enhance our HR initiatives, talent management practices, and overall employee experience in the North America region.” As a trusted advisor to senior leaders for Fortune 500 companies across multiple industries, including manufacturing, retail, online marketplaces, and engineering, Caldwell has developed robust talent management practices and leadership coaching for enhanced team performance. “I am thrilled to join a fast-growing, values-focused organization like AIT,” Caldwell said. “I look forward to contributing a fresh perspective on talent management and fostering an environment where our thriving workforce enables our customers around the world to reach new heights.” Caldwell earned her bachelor’s degree in criminal justice from the University of Richmond, and her MBA from Virginia Commonwealth University, both located in Richmond, Virginia. Based out of AIT’s global headquarters in Itasca, Illinois, Caldwell spends her free time attending live music events and exploring hiking trails with her husband and two dogs.
Gebrüder Weiss welcomes Lars Nielson as Canada Country Manager
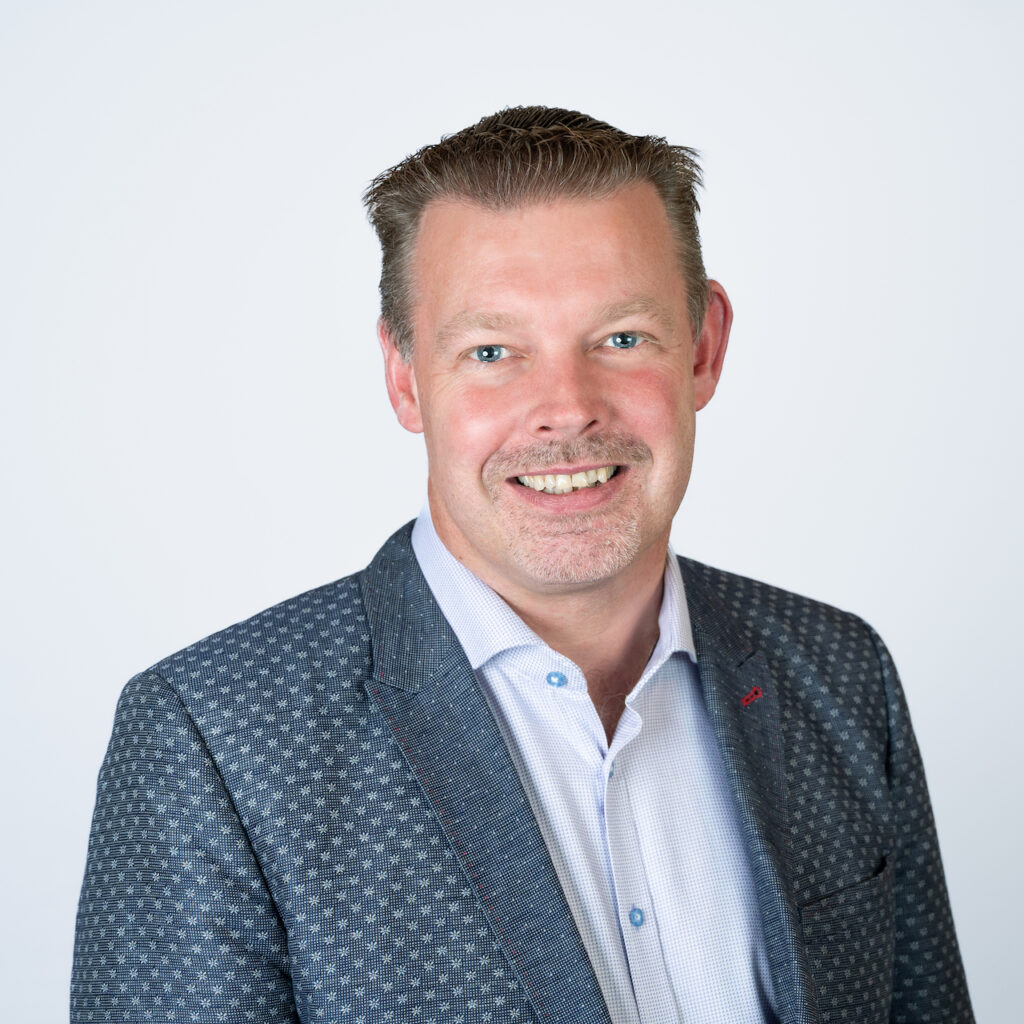
Gebrüder Weiss, an international transport and logistics company with a 500-year history, announced that Lars Nielsen has been named Canada Country Manager. The move is part of the company’s continued focus on enhancing customer experience and expanding trade routes for customers across all regions of North America. The expansion includes grand openings of branch offices and warehouse spaces in Laredo, Texas, and Miami, Florida, this year. Nielsen brings more than 30 years of experience in logistics, procurement, and supply chain operations in Canada to his new position. “Lars has a blend of pioneering vision and operational expertise that make him ideally suited for this role. He’s opened new markets across Canada and led teams to rapid growth while also managing the details of ROI, key performance indicators, and staff development,” said Mark McCullough. “We’re delighted to welcome Lars to the Gebrüder Weiss leadership team.” The Canada, United States, and Mexico region operates as the largest free trade zone in the world, and Canada’s role in North American and global trade continues to grow. Canada was the top purchaser of U.S. goods exports in 2022, responsible for $356.5 billion in total purchases, and was the third largest supplier of goods exports to the U.S.. Domestically, Canada is investing in in-demand trade sectors, such as critical minerals necessary for batteries and semiconductors, to make essential supply chain routes more accessible, efficient, and secure. “Gebrüder Weiss has set the standard for global logistics and led the industry in adapting to trade route shifts like nearshoring,” says Nielsen.” Canada is increasing its prominence in trade and supply chain operations, and I’m thrilled to be joining the company at this pivotal time.” Nielsen is based at the Toronto office in Ontario, Canada, and is responsible for the Gebrüder Weiss branches in Toronto, Montreal, and Vancouver.
Alta Equipment Group acquires Ault Industries expanding construction equipment segment to Canada

Expands product portfolio with new OEMs, including an exclusive distributorship with McCloskey Diversifies end markets with entrance into Ontario and Quebec’s aggregate and mining industries Ault generated approximately $50.3 million in revenue, $4.5 million in net income, and $7.5 million in adjusted EBITDA for the trailing twelve months through June 30, 2023 and is expected to be immediately accretive to the Company’s free cash flow conversion, profitability, and earnings per share ratios Alta Equipment Group Inc. has announced that it has acquired Ault Industries Inc. (“Ault”), a privately held Canadian equipment distributor with locations in Ontario and Quebec. “The acquisition of Ault represents Alta’s first investment in Canada for our growing construction segment. We are extremely excited to partner with the Ault team as they have built a high-performing equipment dealership in the aggregate and mining space, a growing end market in their region and for Alta,” said Ryan Greenawalt, Chief Executive Officer of Alta. “In addition to entering the major construction markets of Toronto and Montreal, we also eagerly embrace a new relationship with McCloskey, a market leading OEM in the crushing and screening product category. We extend a warm welcome to the Ault team as they become part of the Alta family.” Strategic and Financial Highlights The acquisition expands Alta’s Construction Equipment segment into Canada’s two largest markets. As part of the acquisition, Alta assumes Ault’s exclusive dealer agreement with McCloskey, a best-in-class product in the crushing and screening category. Given Ault’s leading market position and strong brand relationships, the Company expects the acquisition to be accretive to the Company’s EBITDA to cash flow conversion and earnings per share ratios. Additional Transaction Details Total purchase price of $36.0 million, consisting of $23.2 million cash at close, a $2.2 million seller note, and $10.6 million worth of Alta’s common stock, which will be issued at $13 per share, equating to 818,473 shares vesting annually over a five-year period. The purchase price is subject to post-closing working capital adjustments. Ault’s brand name, employees, and management team will remain in place post-close. Including Ault, since the Company’s initial public offering in 2020, Alta has completed 16 acquisitions which have contributed $537 million in revenue, and $66 million in Adjusted EBITDA.
What to do about burnout when you’re not burned-out–3 ways to keep burnout from spreading like wildfire
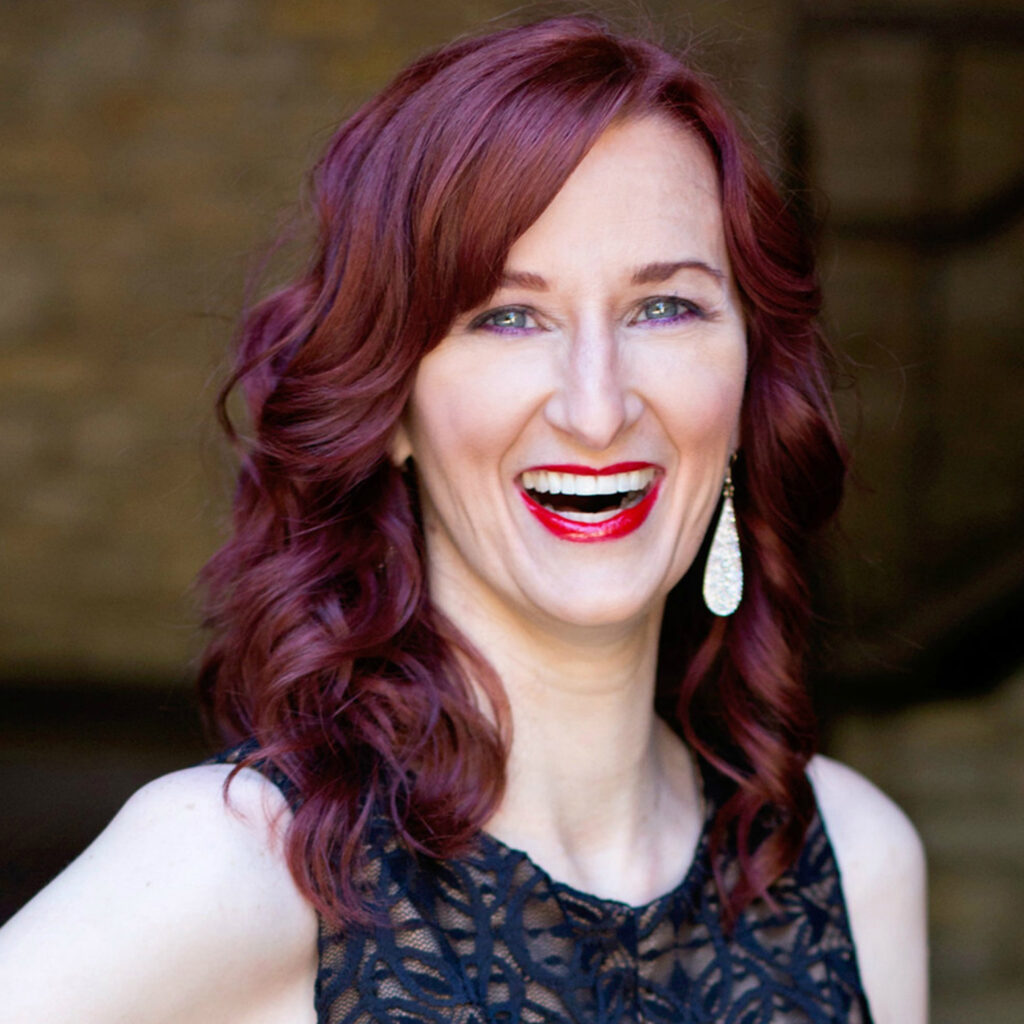
Burnout is impacting every company, position, and industry. With 90% of the workforce experiencing burnout in the last year, you can no longer afford to ignore this epidemic. It’s affecting teams, leaders, and the whole organization…even you. Even if you’re not the one in burnout, it still impacts you. Think of it this way. How do you feel the next morning when you don’t get quality sleep the night before? Grumpy? Groggy? Foggy? Impatient, irritable, unfocused? Lack of sleep impacts your perspective, attitude, how you respond to others, and how you react to situations. The same thing happens with burnout. It doesn’t stay self-contained. When a team member, let’s say Burnout Betty, has burnout, it impacts how she leads, communicates, listens, focuses, thinks, interacts, her behaviors, energy, mood and disposition. It literally impacts everything. When one person is in burnout, it also trickles out to others, because burned out people burn others out. Even if you don’t have burnout, you’re being impacted by it when someone else does or is on the brink of it. You have the power to do something about it. What can you do? Start a dialogue—Begin talking about burnout is the best place to start. Even though burnout is rampant in the workforce, there’s still some stigma around it. People often fear, if they admit they have it, what will others think, do or say. Will my leaders think I can’t do my job? Will they take away responsibilities or will they lose trust in me? If Burnout Betty (BB) isn’t focused, she becomes distracted, unproductive, and making more errors. She will do the same work multiple times, miss deadlines or forget to meet a client. Those are best case scenarios. BB will easily cut corners leading to cybersecurity attacks, safety issues and possible injuries. When BB misses deadlines, makes mistakes, or has to redo work, how does that impact you? You might have to stay longer, do some of her work, or maybe your work gets pushed back waiting on her to get her part to you, which means missing dinner with your family, being absent at your kids’ activities, or not meeting your deadlines. Lean into your storytelling skills. Share your burnout story with BB. When you were in it, what led to burnout in your life, and the strategies you implemented to move past it. When people are in burnout, they tend to pull away and isolate themselves. When you tell your burnout story, they will start to engage. The more you talk about burnout, the more it reduces this stigma. In the process, you allow others who are experiencing it to not feel alone and to know that someone, somewhere gets it and understands. You create a safe place of compassion and empathy. This lets others know it’s okay to feel burned out. You can still love your job and be burned out. Create awareness around burnout—Burnout doesn’t discriminate. It’s impacting your people. The more your team knows what to look for and what to do to prevent it, the less likely they will find themselves in it. Develop a keen eye, because you can’t change something you aren’t aware exists. Since burnout impacts mental health, Burnout Betty is easily frustrated or irritable, making it harder to communicate or interact with her, because others don’t want her mood to affect them. One Burnout Betty, Negative Nancy or Toxic Tim can bring a dynamic team to a halt. Talking to BB can leave the most positive person in a negative state, because she doesn’t listen or she’s in a bad mood. So, every conversation takes longer than it should, which means less time for you to tend to your daily tasks. Build a task force of people who want to be the eyes and ears in your organization in regards to burnout. They can gather information, ask questions to BB and other team members, and start creating a strategy to combat this epidemic. Then take the information they gather, and do something now to help them prevent it. This allows BB to know that she is being heard and understood and that she matters. One of the biggest qualities people want in their company is to know they matter. When BB knows she matters, she feels supported, knowing she will get the help she needs to combat burnout. Hint: Time off is great, but vacation won’t cure burnout. Once you create awareness around it, share with your people day to day strategies that work to help alleviate burnout. Implement a burnout program—This is the key, fundamental element. Talking about it is a great beginning, but it’s imperative to do more. The only way to prevent and address burnout is to be intentional and strategic with it. Workplace wellness programs aren’t enough; 97% of them don’t specifically address or help with burnout, which is also why 80% of employees aren’t actively involved in wellness programs. As a leader, you have to do your part to help your people with burnout. If you want long term results, your organization MUST implement a continual program (not a one and done) to help people like Burnout Betty with burnout and others to prevent it. A long-term strategy is where the magic happens with burnout. Burnout is a slow crawl, and working through it is multi-layered. Whether it’s an online course, bootcamp or Train the Trainer certification, burnout training is no longer a “nice to have.” It’s imperative if your company wants to keep their top talent and create a happy, thriving workplace and culture. The most successful burnout programs have these key components: accountability, support, encouragement, and Q&A. Burnout doesn’t go away on its own. With most industries incurring staff shortages, it’s up to you, as a leader, to invest in your people if you want to keep them. Since the #1 reason why people leave organizations is due to burnout, it’s a huge opportunity for you to end the burnout epidemic by starting the dialogue, creating
RIANTA RS60 packaging system receives the iba award
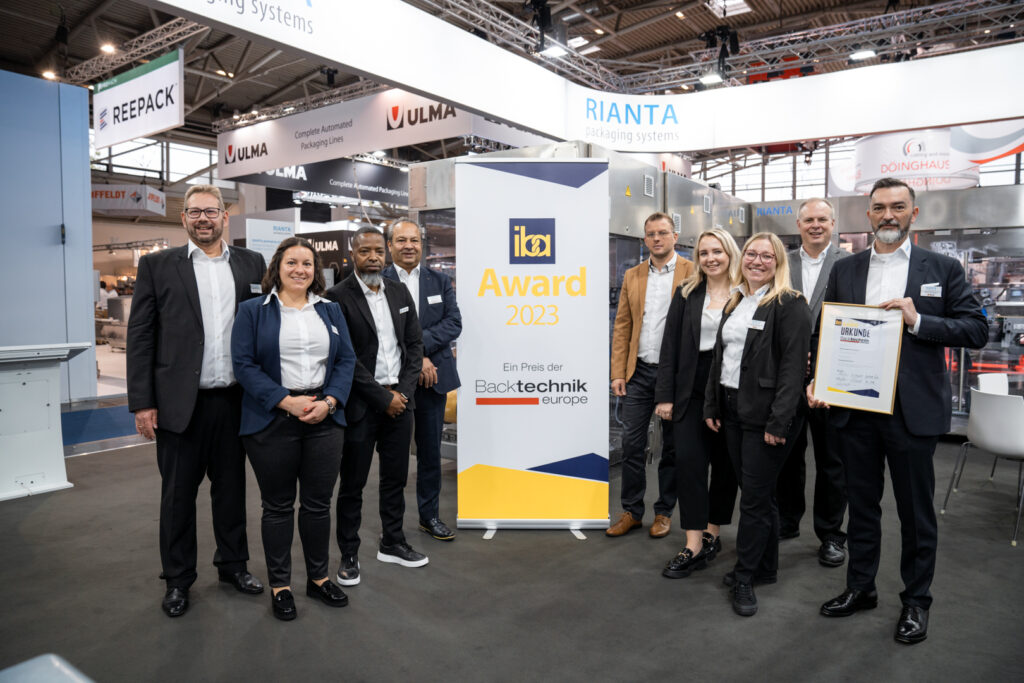
The RIANTA RS60 packaging system received the iba award for bakery technology at the International Bakery Exhibition. At the International Bakery Exhibition iba, awards were presented for the most innovative products and developments. Among the winners was the RIANTA RS60 packaging system. The machine presents a pioneering, fully automatic and modular solution that has been specially developed for cutting, stacking and packaging bakery products. The RS60 packaging system from Rianta has been honored with the International Innovation Award for its pioneering design and functionality. “The innovation of the RS60 is the newly created design, while retaining the proven processes and functional aspects and taking into account the hygienic design specifications of the EHEDG and the food industry,” said the jury in its assessment. “The modular design enables very good visual inspection and the fastest possible maintenance as well as easy replacement of individual modules.” The machine is easily accessible from anywhere and the use of the latest control and servo technology enables quick format changes via the HMI. Davor Kovacevic, Managing Director of Rianta: “Receiving the iba Award confirms the feedback and demand from our customers for state-of-the-art solutions in the bakery industry. For us, being the first manufacturer of packaging machines to be honored with this award is an important milestone and reinforces our innovative corporate strategy.” The prize, awarded by Backtechnik Europe magazine, recognizes innovations for the industrial and assembly line-oriented production of baked goods and highlights products that are being presented at the trade fair for the first time. Iba, the world’s leading trade fair for the baking and confectionery industry, takes place every three years at the Munich Exhibition Centre. This year’s iba attracted 57,000 visitors and 1,073 exhibitors to Munich.
Robroy Industries® Enclosures division announces promotion of Jeff Hall to Plant Manager
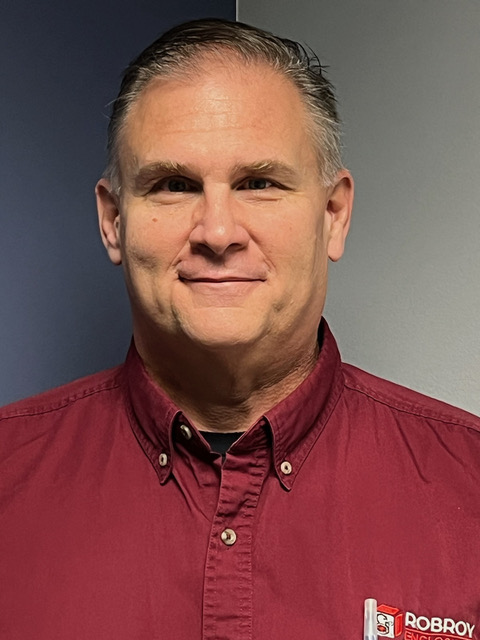
Robroy Industries Enclosures Division, manufacturers of Stahlin®, the leading brand of fiberglass electrical and industrial enclosures; and AttaBox®, the most durable, extensive family of polycarbonate enclosures, announces that Jeff Hall has been promoted to Plant Manager for the company’s enclosure manufacturing facility in Belding, Michigan. Hall will be responsible for all plant functions as well as managing maintenance team and providing support to the Operations Team. Jeff provides extensive experience from nearly 17 years with Robroy Industries as a plant engineer. Additional expertise includes tool and mold design, injection molding, and facilities management.
LiftMaster launches new line of smart Commercial Door Operators
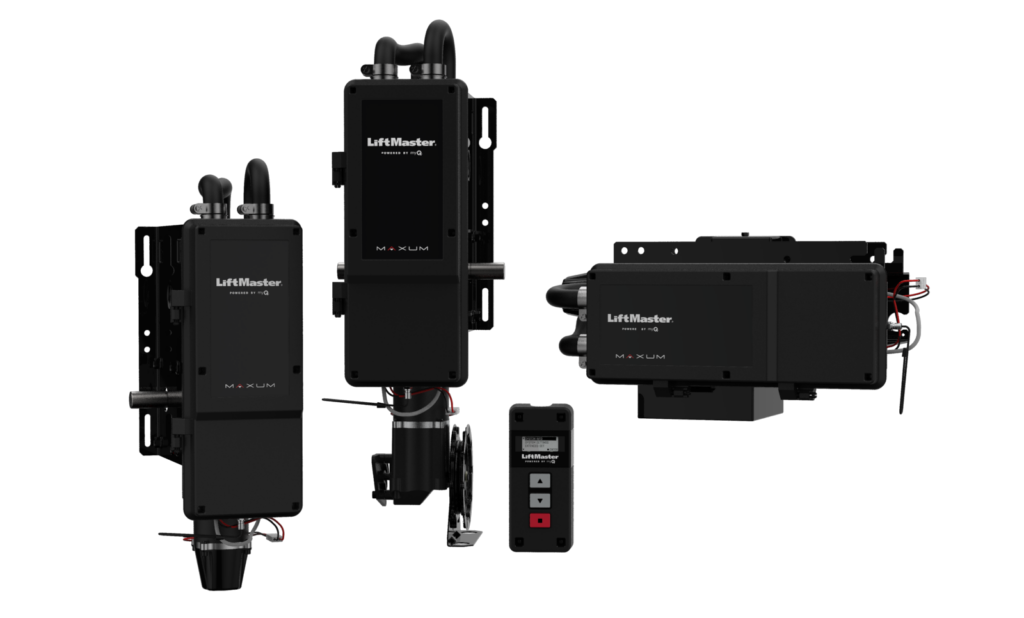
LiftMaster®, a brand of professionally installed access solutions that continues to set the standard in commercial door operator innovation has launched MAXUM, a new lineup of smart DC powered commercial door operators equipped with a floor level LCD display, soft start and stop, battery backup, and built-in Wi-Fi connectivity. MAXUM commercial door operators are now available for preorder through the LiftMaster Partner Portal. MAXUM commercial door operators will ship January 2nd, 2024. Partners who preorder will be eligible to receive special pre-sale offers and discounts including: A free 7Ah Battery Back-up with every pre-sale order 3 months free of myQ Facility for any MAXUM commercial door operator connected in 2024 3% discount off list price for a quantity of 5-39 units placed in a single order 5% off list price for a quantity of 40 or more units placed in a single order “LiftMaster is always listening to our dealers and working to provide them with solutions that anticipate the needs of users in commercial settings with a lineup that is fast, smart, and simple,” said Tracy Rizzi, Group Product Manager, Commercial Door Operators. “With the introduction of MAXUM DC commercial door operators, you get all the benefits of DC operation including soft start/soft stop, battery back-up, faster speed, lighter weight and so much more. Everything from installation to operation is faster, connectivity and continuous uptime is smarter, and modular parts and floor-level wall control with diagnostics make the operator simpler allowing businesses to maximize efficiency and profitability.” Pioneered to perfection, the new suite of commercial door operators is integrated with myQ® technology enabling more visibility through integrated myQ® Facility software. Facility Managers can see and control what is happening at their facility’s commercial doors and access data and analytics to improve their business. The integration with myQ Facility also allows dealers and installers to receive valuable diagnostic information, making scheduled maintenance a breeze. LiftMaster’s new product line has been consolidated into 26 new SKUs with different feature sets and a range of price points. Notable new features include: Sleek New Profile – Modular and purpose-built design that will fit the needs of any facility or commercial application. High-Efficiency DC Motors – The motor and gearbox are built to meet the high demands of traffic coming in and out of busy facilities. Soft-start & Soft-stop gives the operator a longer lifespan. It reliably works in extreme weather conditions too. Floor Level Control – 3-button control with easy-to-use, 4-line LCD display. When installers add a remote, they don’t have to track beeps and flashes and setup can be done simply from the screen. Faster Door Operation – Up to 33% faster than standard commercial door operators, allowing shipments in and out quickly. Average speed is 12″ per second. Battery Backup – Helps keep the door running even when the power goes out, ensuring safe and continuous operation. Floor Level Diagnostics and Troubleshooting – myQ Facility allows customers to see what the problem is on their myQ Facility interface so they can fix it or know when to call for service. With myQ Diagnostics dealers can know the installed door operator’s maintenance schedule and be alerted when there is a problem. Built-in Wi-Fi – Easily connects to myQ Facility software, allowing customers to get valuable data and insights to improve operations. Security+ 2.0® – Virtually eliminates radio wave interference and offers extended range.
BSL touts lithium-ion technology
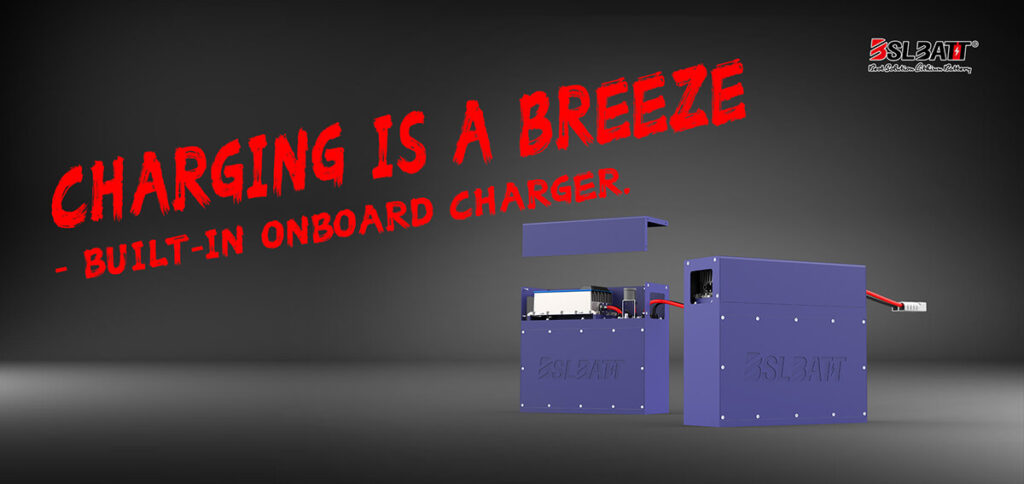
BSL New Energy Technology Co., LTD. is a fast-paced, high-growth (200% YoY) high-tech company leading the adoption of lithium-ion technology solutions. Mr. Zhang, product manager of BSL Battery – Industrial, said: “The launch of the lithium pallet truck battery and charger combination is a game-changing lithium battery for pallet trucks that enables forklift dealers to easily transport truck fleets. It is the largest lithium battery in the market. Ready-made replacement for most walk-behind pallet trucks, including Caterpillar, Clark, Crown, Big Joe and Toyota” “The new 24V battery has all the benefits of lithium batteries with more smart features built in. Our team of battery engineers developed We fully consider the needs of users when developing new products and provide reliable power supplies for a variety of forklift brands.” Traditional wet or sealed AGM batteries typically last 18 to 60 months before degrading or being replaced. The research behind the BSLBATT Pallet Truck Battery series shows that your company will now have a service life of 10 to 20 years on a single piece of equipment. On average, the battery lasts 8 to 10 times longer. Charging is a breeze – with the BSLBATT Pallet Truck Battery series you no longer need a central charging area; any standard 220V or 110V socket can be used when plugged into the built-in onboard charger. Cost savings come from reduced battery purchases, no longer the labor required to replace used batteries, labor and time spent watering batteries, lost productivity from mechanical failures, lost productivity from slow-moving pallet jacks, purchased Money saved on additional equipment, electricity saved, shorter charging times, and less wear and tear on equipment. Monitor battery health virtually anywhere – As a manager, you can always know the health of your battery without leaving your desk. You can access your batteries remotely via the BSLBATT cloud platform to view charge history, overall health, and even individual batteries in your fleet. Incredible power and energy density – BSLBATT lithium batteries maintain their integrity, resulting in a longer life cycle. They charge faster and less frequently, run powerful all day long, have better uptime and last an average of 10 times longer. Key features of 24V pallet truck lithium batteries include: Easy to install, after plugging into the built-in car charger, you can use any standard 220V or 110V outlet! Scalable system provides increased power and energy as needed. Features an intelligent cooling system to prevent key components from overheating and extend battery life. The powerful battery management system provides multi-layer protection against under-voltage, over-voltage, over-current and temperature conditions. CANbus connection allows the battery to transmit real-time operating statistics such as voltage, current, state of charge and health status. Up to 5 years or 10,000 hours warranty.
Episode 433: Vecna Robotics removes the fear of Warehouse Automation Integration
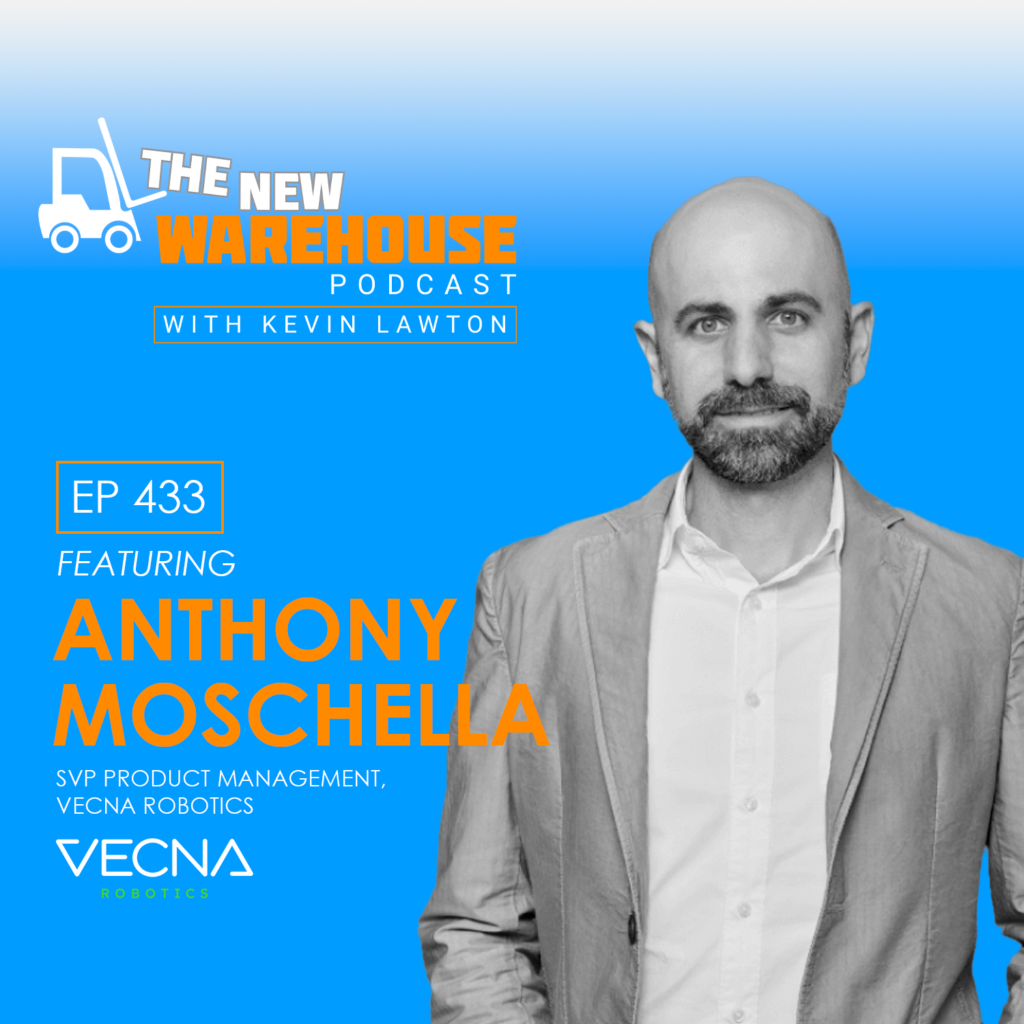
In today’s episode of The New Warehouse Podcast, we have the privilege of welcoming Anthony Moschella, the Senior Vice President of Product Management at Vecna Robotics. Vecna Robotics is at the forefront of warehouse automation, specializing in vehicular robotics for warehouse, distribution, and manufacturing centers. What sets Vecna Robotics apart is its commitment to a human-centric approach in robotics, aiming not to replace humans but to collaborate with them, enabling advanced workflows and greater efficiency. In this conversation, we’ll delve into the current state of warehouse automation, explore user experience in the industrial sector, and uncover Vecna Robotics’ exciting partnership with Geodis. So, if you’re eager to discover how cutting-edge robotics are shaping the future of warehousing while enhancing the human element, listen to the full episode. Overcoming Fear in Warehouse Automation Integration There is a widespread acknowledgment of the need for automation, with nearly 98-99% of warehouse operations leaders considering its adoption. However, as Anthony points out, there is a palpable fear surrounding this transformative technology. Anthony believes what holds warehouse operators back from embracing automation is the fear of the unknown impact on their established processes and the workforce. There’s a prevailing concern about the disruption that automation might bring and the potential for job displacement. To address these fears, Anthony highlights Vecna Robotics’ unique approach, emphasizing collaboration between humans and robots rather than replacement. He notes, “We’re not here to replace your workers with robots. We’re here to look at your system and identify where to deploy in a way that makes sense.” This approach ensures that human expertise is still a crucial part of warehouse operations, working in tandem with robots to achieve greater efficiency. A Turnkey Approach to Warehouse Automation Integration One key aspect of Vecna’s approach to automation integration is to offer a range of scaled engagement options, allowing warehouse operators to begin with smaller deployments to demonstrate utility. This gradual approach minimizes disruption while showcasing the benefits of automation in a controlled setting. Furthermore, Vecna Robotics provides turnkey solutions with flexible API integrations, ensuring that their technology can adapt to existing IT environments. Anthony notes, “We have a very flexible API that can integrate into your existing IT environment. So, we’re trying to take some of that friction out of it.” To bolster confidence in the reliability of their automation solutions, Vecna Robotics has introduced the Pivotal Command Center, a 24/7 teleoperation and remote monitoring service staffed by their employees. This constant oversight and immediate response to issues contribute to a sense of security and trust in the technology. By addressing fears, offering turnkey solutions, and providing ongoing support and optimization, Vecna Robotics aims to empower warehouse operators to embrace automation as a valuable tool for enhancing productivity and efficiency in their facilities. Revolutionizing Case Picking with Collaborative Automation Anthony provides insights into the partnership between Vecna Robotics and Geodis and how the approach to case-picking automation promises to redefine the industry. The concept revolves around creating a seamless association between orders and robots. In traditional warehouse operations, associates manually navigate the facility, picking items for specific orders. This one-to-one relationship between associate and order often results in inefficiencies, labor-intensive processes, and a limited capacity for processing orders. However, with Vecna Robotics’ innovative solution, the equation changes. The robot dynamically generates routes to pick locations, and associates work collaboratively with the robots to fulfill orders. This dynamic coordination, akin to an Uber-like system for robotics and human workers, optimizes efficiency, enhances reliability, and ensures the safety and satisfaction of associates. Early results demonstrate remarkable improvements, with almost 200% greater efficiency than conventional one-to-one operations. This transformative approach holds the promise of not only streamlining case picking but also revolutionizing workflows in warehouses and distribution centers, ultimately creating a win-win scenario for businesses and their workforce. Key Takeaways Collaborative Robotics: Vecna Robotics promotes collaboration between humans and robots in warehouse automation, ensuring efficiency while preserving the human element. Turnkey Solutions: Vecna offers scalable, disruption-minimizing automation solutions with flexible API integrations for easy adoption. Revolutionizing Case Picking: The partnership with Geodis transforms case picking, increasing efficiency by nearly 200% and enhancing worker satisfaction. The New Warehouse Podcast EP 433: Vecna Robotics Removes the Fear of Warehouse Automation Integration
U.S. Rail Traffic for October and the week ending October 28, 2023
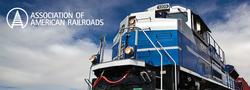
The Association of American Railroads (AAR) has reported U.S. rail traffic for the week ending October 28, 2023, as well as volumes for October 2023. U.S. railroads originated 921,591 carloads in October 2023, down 0.3 percent, or 2,921 carloads, from October 2022. U.S. railroads also originated 1,075,731 containers and trailers in October 2023, up 2.2 percent, or 23,201 units, from the same month last year. Combined U.S. carload and intermodal originations in October 2023 were 1,997,322, up 1.0 percent, or 20,280 carloads and intermodal units from October 2022. In October 2023, nine of the 20 carload commodity categories tracked by the AAR each month saw carload gains compared with October 2022. These included: petroleum & petroleum products, up 5,046 carloads or 14.2 percent; chemicals, up 3,842 carloads or 3.2 percent; and motor vehicles & parts, up 3,154 carloads or 5.4 percent. Commodities that saw declines in October 2023 from October 2022 included: coal, down 12,284 carloads or 4.5 percent; grain, down 4,373 carloads or 4.7 percent; and crushed stone, sand & gravel, down 795 carloads or 0.9 percent. “Combined carload and intermodal volumes on U.S. railroads in October were the most for any month since June 2021, a span of 28 months,” said AAR Senior Vice President John T. Gray. “Part of that relates to intermodal seasonality and concerns over Panama Canal capacity, but part of it also reflects an economy that remains resilient as reflected by recent strong GDP data.” Excluding coal, carloads were up 9,363 carloads, or 1.4 percent, in October 2023 from October 2022. Excluding coal and grain, carloads were up 13,736 carloads, or 2.5 percent. Total U.S. carload traffic for the first 10 months of 2023 was 9,696,421 carloads, up 0.2 percent, or 21,802 carloads, from the same period last year; and 10,405,065 intermodal units, down 7.2 percent, or 808,532 containers and trailers, from last year. Total combined U.S. traffic for the first 43 weeks of 2023 was 20,101,486 carloads and intermodal units, a decrease of 3.8 percent compared to last year. Week Ending October 28, 2023 Total U.S. weekly rail traffic was 499,389 carloads and intermodal units, down 1.2 percent compared with the same week last year. Total carloads for the week ending October 28 were 227,575 carloads, down 4.2 percent compared with the same week in 2022, while U.S. weekly intermodal volume was 271,814 containers and trailers, up 1.5 percent compared to 2022. Three of the 10 carload commodity groups posted an increase compared with the same week in 2022. They were chemicals, up 1,334 carloads, to 31,336; petroleum and petroleum products, up 1,182 carloads, to 9,978; and farm products excl. grain, and food, up 246 carloads, to 16,788. Commodity groups that posted decreases compared with the same week in 2022 included coal, down 7,264 carloads, to 63,676; nonmetallic minerals, down 1,573 carloads, to 32,423; and grain, down 1,303 carloads, to 22,941. North American rail volume for the week ending October 28, 2023, on 10 reporting U.S., Canadian and Mexican railroads totaled 339,642 carloads, down 2.6 percent compared with the same week last year, and 353,354 intermodal units, down 0.8 percent compared with last year. Total combined weekly rail traffic in North America was 692,996 carloads and intermodal units, down 1.7 percent. North American rail volume for the first 43 weeks of 2023 was 28,145,583 carloads and intermodal units, down 3.5 percent compared with 2022. Canadian railroads reported 95,880 carloads for the week, up 3.8 percent, and 70,444 intermodal units, down 7.1 percent compared with the same week in 2022. For the first 43 weeks of 2023, Canadian railroads reported cumulative rail traffic volume of 6,843,396 carloads, containers and trailers, down 3.5 percent. Mexican railroads reported 16,187 carloads for the week, down 13.5 percent compared with the same week last year, and 11,096 intermodal units, down 11.5 percent. Cumulative volume on Mexican railroads for the first 43 weeks of 2023 was 1,200,701 carloads and intermodal containers and trailers, up 2.0 percent from the same point last year. To view rail traffic charts, click here.
Orbis announces expansion of its manufacturing plant in Urbana, OH
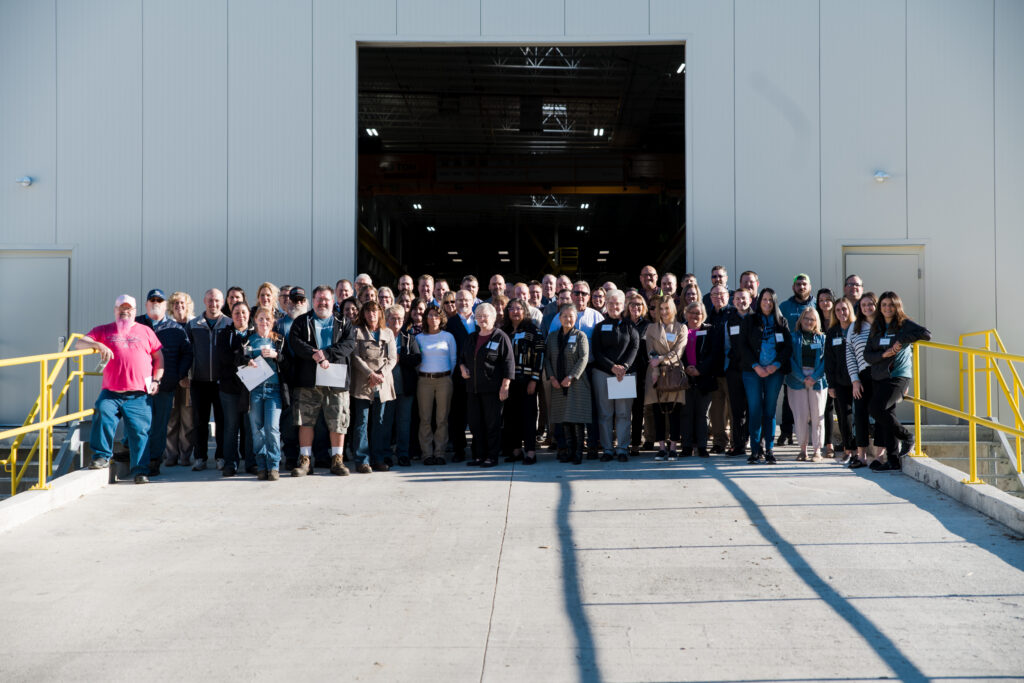
Expansion adds capacity and promotes sustainability in reusable packaging manufacturing ORBIS® Corporation, an international provider in reusable packaging, has expanded its manufacturing facility located in Urbana, Ohio. This expansion adds 30% more space for the production of ORBIS totes and pallets, and allows ORBIS to add more presses and tools, increase capacity and shorten lead times. Coupled with its favorable geographic location for freight optimization, the Urbana plant expansion will help ORBIS better serve its customers nationwide. “A more sustainable supply chain starts with reuse. Our customers rely on us to help them move their goods in the supply chain more sustainably with reusable packaging,” said Norm Kukuk, president at ORBIS. “This expansion gives us the flexibility and capacity to enhance production of our packaging products. The people of our Urbana plant are dedicated, committed and focused on serving the customer. This expansion gives them the infrastructure to make that possible.” ORBIS helps companies move away from single-use packaging and into reusable packaging products that offer long service life and many trips in the supply chain. Reusable packaging products produced at the plant are used in many industries, including automotive, food, beverage and consumer packaged goods. “ORBIS has been a part of Urbana for decades,” said Todd Mathes, executive vice president of Operations at ORBIS. “This expansion, located at 200 Elm Street, is not only an investment in our current infrastructure but also an opportunity to harness emerging manufacturing technologies.” Part of Menasha Corporation, headquartered in Oconomowoc, Wisconsin, ORBIS operates 11 manufacturing plants throughout the United States, Canada and Mexico. This expansion in Urbana increases the company’s overall molding capacity by 10% while also increasing energy efficiency. “This new facility is the culmination of a 13-year-long effort to revitalize the former site and bolster the community,” said Rich Ebert, director of the Champaign Economic Partnership. “As a community, we’re thrilled that ORBIS Corporation has chosen to expand its presence here in Urbana; its dedication to providing reusable packaging helps meet the sustainability demands of today’s supply chain. We’re looking forward to seeing it thrive as the leader in sustainable packaging, and very much looking forward to continuing to grow our yearslong partnership.” ORBIS worked with local Ohio contractors to develop and build this expansion. ORBIS also partnered with Damewood Enterprises and its related business, Phoenix AG, to lease 672,000 square feet of warehouse space in its all-new off-site warehouse in Urbana. For more information, please visit ORBIS online at: https://www.orbiscorporation.com/en-us/.
Jungheinrich wins third consecutive EcoVadis platinum certificate for sustainability
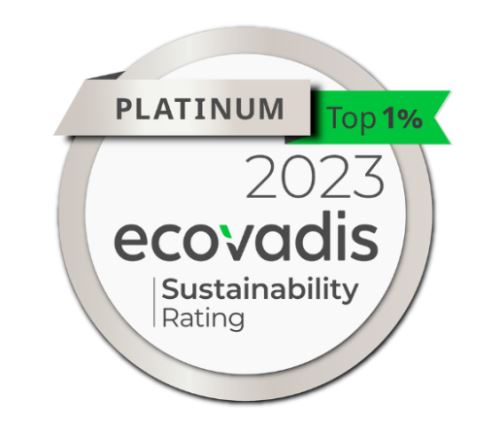
Jungheinrich is once again certified as one of the world’s most sustainable companies Awarded for “outstanding” environmental performance The award reflects Jungheinrich’s comprehensive commitment to human rights and sustainable supply chains Jungheinrich has once again been awarded a platinum certificate from EcoVadis for its corporate commitment, confirming its position among the top 1% of the world’s most sustainable companies. For the third time in a row, the international CSR rating agency EcoVadis has awarded Jungheinrich a platinum certificate for corporate responsibility. The award is recognition of Jungheinrich’s outstanding commitment to the environment, labour and human rights, ethics and sustainable procurement. With the platinum certification, EcoVadis once again confirms that Jungheinrich continues to rank among the top 1 per cent of the world’s most sustainable companies. “Jungheinrich creates sustainable value. We aspire to combine economic success with ecological and social responsibility. EcoVadis’s renewed platinum certification proves that we are succeeding in this. For us, it is both a confirmation of our strategy to date and an obligation to continue to drive forward and expand our commitment in the future as part of our Strategy 2025+. Sustainability is and will remain the foundation of our Group activities,” says Dr Lars Brzoska, Chairman of the Board of Management of Jungheinrich AG. Pioneer in environmental protection and human rights This year, EcoVadis particularly highlighted Jungheinrich’s “outstanding” environmental performance. Here, the company achieved the maximum number of points thanks to (among many notable factors) its effective measures to reduce greenhouse gas emissions and conserve valuable resources. Jungheinrich has made a clear commitment to the 1.5-degree target and aims to establish CO2e-neutral business operations at all sites and plants worldwide by 2030. All Jungheinrich sites in Germany, including the six German factories, have been sourcing exclusively green electricity since 2021. Since then, the Jungheinrich Group has continued to push ahead with the switch to renewable energies worldwide, with the transition to green electricity now complete in 21 countries. An important factor in this is the generation of the company’s own solar power. The company continues to equip its sites with photovoltaic systems, and recently covered the parking lot of its corporate headquarters in Hamburg with a 1,100-square-metre photovoltaic system. Jungheinrich also conserves resources by remanufacturing used forklifts on an industrial scale. Through this process, up to 99 per cent of the raw materials used in the truck are reused or recycled, saving up to 80 per cent CO2e compared to new production. In addition, Jungheinrich makes great efforts to ensure compliance with human rights along its value chain. To this end, the company has expanded its existing sustainable procurement management system to take particular account of human rights aspects. To tighten internal processes for ensuring human rights due diligence, Jungheinrich has also implemented an appropriate risk management system and defined the role of its Human Rights Officer and Human Rights Council, which brings together human rights experts within the Group. Jungheinrich conducts regular risk analyses to identify, assess and prevent potential human rights violations at an early stage. Jungheinrich’s platinum EcoVadis certifications in 2023, 2022 and 2021 build on the award of gold certificates in 2020 and 2019. EcoVadis is considered one of the world’s leading institutions for assessing corporate responsibility. Only the most sustainable 1% of all companies assessed receives a top platinum certificate from EcoVadis. In total, EcoVadis analyses the sustainability management of more than 100,000 companies worldwide with regard to the environment, labour and human rights, ethics, and sustainable procurement.
Women In Trucking Association announces its November 2023 Member of the Month
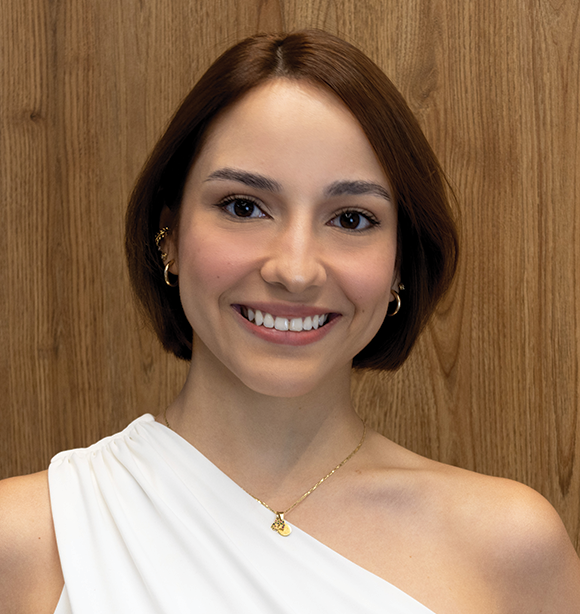
The Women In Trucking Association (WIT) has announced Maria Cardenas as its November 2023 Member of the Month. Cardenas is the marketing manager at Sworkz, a nearshoring and staffing service provider. Cardenas’ father’s first job was providing food to truckers on the highways. Years later, as a little girl, he used to sit her on his lap, and she would steer the wheel in a parking lot while he drove slowly. Those moments with him sparked her fascination with driving. “It’s funny how it all comes full circle,” said Cardenas. “From those childhood memories to now working in an industry that’s intrinsically tied to my family’s history.” She is now 27 years old and believes being a young woman in this industry has its own unique set of challenges such as feeling the need to prove yourself and fighting against stereotypes of how a woman should conduct herself or act. However, Cardenas considers herself lucky to have been born into a family where her grandmother, mother, and sister all exuded leadership and strong character. From their example, she has learned to be a strong woman and unapologetically herself. As a result, she has held onto her values and principles, and surrounds herself with empowered women who have guided her through her journey. Cardenas is determined to carve a path not just for herself, but for other women too; enabling them to shine even brighter by staying true to themselves, even in a world that often casts being unique in a negative light. Cardenas feels her journey wasn’t conventional as she has worked in various marketing agencies, spanning B2B and B2C industries to e-commerce to NGOs and education platforms. But it was Sworkz that led her to the nearshoring industry and its unique challenges. “The idea of empowering women in this male-dominated field resonated with me deeply. As part of the leadership team, I have the privilege and ability to make impactful decisions, advocating not just for women’s talents but also helping some of them as business owners to grow their companies,” said Cardenas. “At Sworkz, we are more than just hollow words – we realize we need to lead with our actions. Our leadership team is 50% women, and our marketing team is almost 90%. As a nearshoring and staffing service provider, we have a responsibility to embody the change we want to see in the industry.” Cardenas hopes her story inspires women to keep breaking more barriers saying, “if you’re a woman considering working in this industry, never apologize for being yourself. Embrace your uniqueness, your skills, and your passion. I hope my journey can be a testament that age and gender are not a barrier and what truly matters is your dedication, kindness, and the mark you want to leave on the world.”
Bobcat Compact Loader inventors inducted into National Inventors Hall of Fame
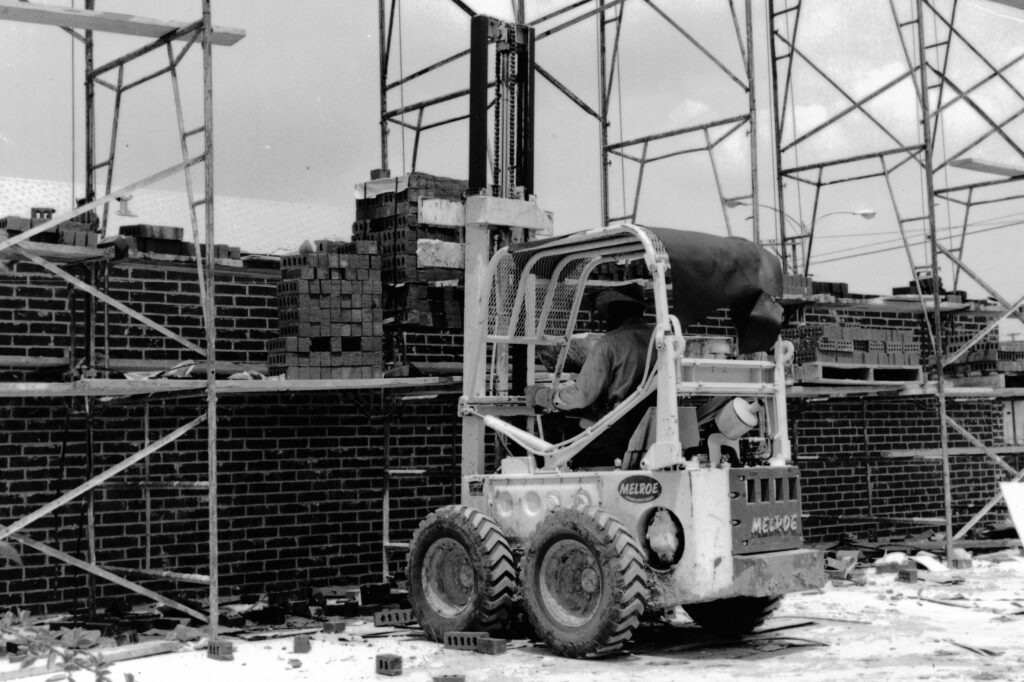
Cyril and Louis Keller Recognized During Illumination and Induction Ceremonies in Washington, D.C. Cyril and Louis Keller, the brothers who invented the world’s first compact loader (later named the Bobcat® skid-steer loader), have formally been inducted into the National Inventors Hall of Fame (NIHF). The Keller brothers were posthumously recognized during the NIHF Illumination and Induction Ceremonies held Oct. 25-26 in Washington, D.C. NIHF annually recognizes inventors, promotes creativity and advances the spirit of innovation and entrepreneurship. Bobcat representatives, along with members of the Keller family, were in attendance to celebrate this achievement. “The ingenuity of the Keller brothers spurred the compact equipment industry,” said Mike Ballweber, president, Doosan Bobcat North America. “Today at Bobcat, their spirit of inventiveness lives on, as our organization continues to innovate for the jobsite of the future and empower our customers to accomplish more.” The Illumination Ceremony at the National Inventors Hall of Fame Museum was celebrated Oct. 25 in Alexandria, VA. New inductees or their family members placed their names on illuminated hexagons in the museum’s Gallery of Icons. Members of the Keller family represented Cyril and Louis in this symbolic ceremony. The 2023 National Inventors Hall of Fame Induction Ceremony was held Oct. 26 at The Anthem in Washington, D.C., where the new Inductee class was honored for its contributions to society. Joe Keller, son of Louis, said, “If Dad and Cyril were here to accept this award, they would accept it for all the early and current Bobcat employees that have all helped bring the little Keller loader to be the Bobcat machine it is today. There is no one that the Bobcat loader hasn’t affected or helped through life—even though they may not know it.” Inventing an Industry In the 1950s, brothers Cyril (1922- 2020) and Louis (1923-2010) operated a small machinist-blacksmith shop in Minnesota, building and repairing machinery for local farmers. A farmer approached them with a need for a self-propelled loader light enough to be lifted to the second floor of a turkey barn and small enough to clean around the barn’s upright poles. In 1957, the Kellers built a three-wheeled loader with two drive wheels in front and a caster wheel in the rear – the precursor to the modern skid-steer loader. The loader came to the attention of Melroe Manufacturing Company (now Bobcat Company), which was awarded exclusive manufacturing rights to the machine on a royalty basis. Melroe hired the Kellers to refine the design and put the machine into production. To improve the design of the loader, a second set of drive wheels was added to the back of the loader in 1960. With four-wheel drive, the M400 became the world’s first true skid-steer loader. “Skid-steer” describes the unique steering system that enables the machine to turn within its own length. Later, the Bobcat brand name was established because of the machine’s toughness, quickness and agility. Commemorating its History In celebration of this recognition, Bobcat has its history on display in a new exhibit within the NIHF Museum. The museum exhibit features one of the Keller brothers’ original three-wheel loaders, along with a timeline of Bobcat’s history and a video display highlighting various aspects of Bobcat’s products, people and initiatives. The Bobcat exhibit will be on display through April 2024. Learn more about the history of Bobcat.
ASSP’s McNelly appointed to ANSI Board of Directors
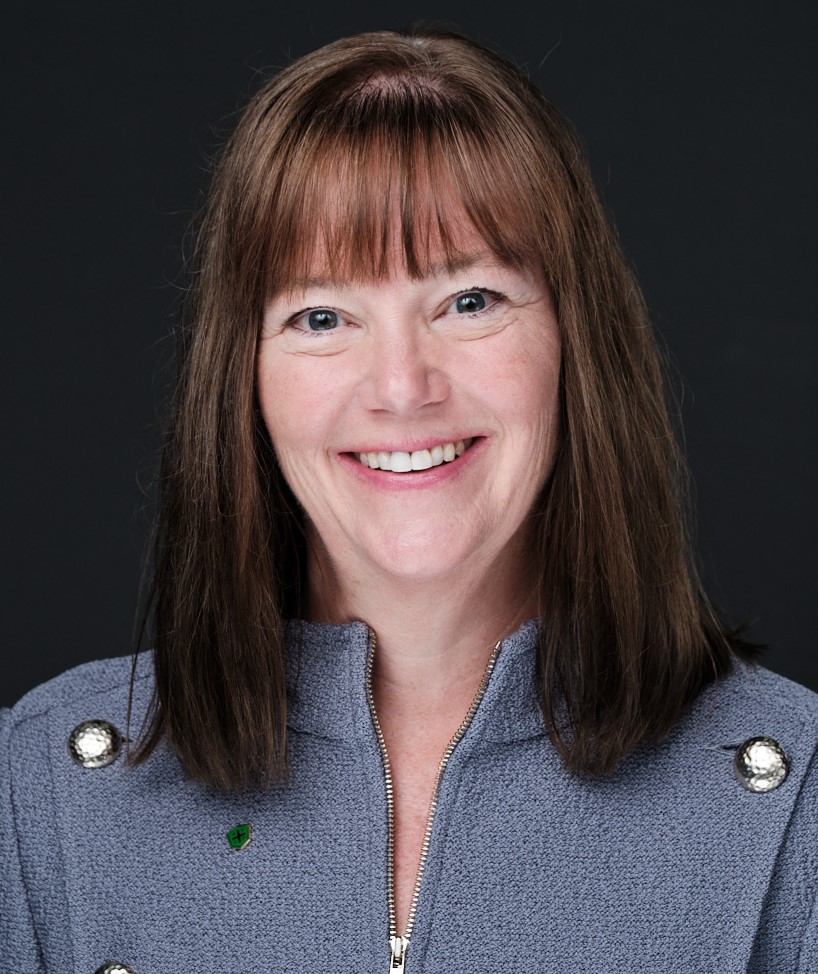
CEO Jennifer McNelly of the American Society of Safety Professionals (ASSP) has been appointed to the board of directors of the American National Standards Institute (ANSI), which provides a framework for safety standards development and conformity assessment systems. Her three-year term as a director-at-large begins Jan. 1. McNelly, CAE, will continue her full-time role at ASSP during her time on the ANSI board. She will attend ANSI’s board meeting and year-end event as a guest on Dec. 6-7 in Washington, D.C. “I look forward to helping advance ANSI’s and ASSP’s valuable work developing voluntary national consensus standards,” McNelly said. “Our longtime collaboration with ANSI has been an important element of our successful efforts to elevate workplace safety standards.” ANSI accredits standards that are developed by government agencies, consumer groups and other standards organizations such as ASSP, which is a global leader in creating voluntary national consensus standards to protect workers. The standards provide the latest expert guidance and fill gaps where federal regulations don’t exist. Companies rely on voluntary consensus standards to drive improvement, injury prevention and sustainability. Since regulatory requirements are slow to change and often out of date, compliance is not sufficient. A standards-based approach to workplace safety also improves productivity and boosts a company’s bottom line. “With Jennifer giving ASSP a voice on the ANSI board, it will improve our alliance and support the standards process in today’s changing world of work,” said ASSP President Jim Thornton, CSP, CIH, FASSP, FAIHA.
IFS delivers strong Q3 2023 results thanks to increased demand for AI
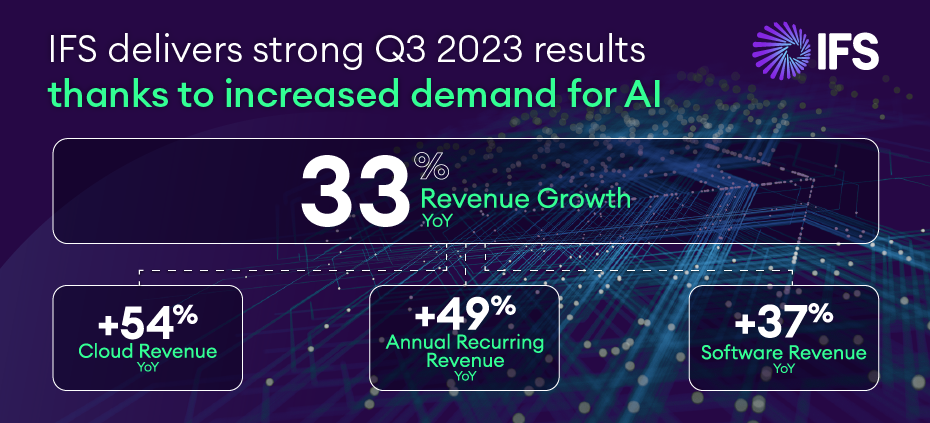
IFS, the global cloud enterprise software company, has announced its financial results for the year to date (YTD) ending September 30th, 2023. The company reported substantial YoY increases in annual recurring revenue (ARR) of 49 percent, cloud revenue of 54 percent, and software revenue of 37 percent, which represents an impressive 80 percent share of total revenue. The company’s commitment to delivering rapid time-to-value has resulted in significant wins and upgrades from global customers including: Tele2, Culligan, Van Oord, Roxtec International and De Havilland. The advanced industry capabilities, user experience, and value offered by IFS Cloud continue to attract new customers and motivate existing ones to extend their usage and leverage IFS technology to create outstanding Moments of Service for their customers. This is compounded by sustained IFS investment in technology that is seeing capabilities for ESG and Artificial Intelligence (AI) drive demand. The macro interest and appetite for AI bodes well for IFS with its AI architecture, IFS.ai, that extends the value of AI across all its capabilities and throughout a customer’s business. Reflecting on the impact IFS technology has for its customers, Forrester Research’s recently announced study that evaluates the benefits of deploying IFS Cloud found that the average customer achieved over $36m USD in savings over three years, of which over $13m were sustainability benefits. IFS CEO Darren Roos stated: “The 37 percent increase in software revenue over the last 12 months is a testament to the trust our customers have in IFS and the dedication of our teams.” He added: “IFS has transformed into a cloud-first technology vendor that continues to create value through organic growth and acquisition to stay at the forefront of innovation.” Roos concluded: “IFS.ai is a continuation of our ambition to innovate and puts IFS in a leading position to democratize AI for all users. Our goal is to anticipate our customers’ needs and deliver when it matters to them, creating value at every step.” IFS Chief Financial Officer, Matthias Heiden, commented: “It is evident that the macro-economic challenges continue to impact many industries.” Heiden continued: “That said, we are pleased to be engaged with many forward-thinking customers who understand the need and opportunity to leverage technology to drive efficiency in their business. IFS is well positioned to help them achieve competitive differentiation. This has translated into significant growth with total revenue up 33 percent year-to-date vs 2022 and ARR up 49 percent YoY.” Heiden concluded: “Reviewing our performance so far in 2023, I am not only proud that we are outperforming the market but that we are achieving this robust mix without compromising on any other metrics; we are building on the strong performance of previous years delivering the value customers need.” Through its software and success services, IFS is making it possible for customers to buy and consume technology in the way that creates the most value for them, so they can deliver amazing Moments of Service.” Financial* and Operational Highlights for YTD FY2023: YTD FY2023 software revenue was EUR 597m, an increase of 37% versus YTD 2022 YTD FY2023 recurring revenue was EUR 560m, an increase of 38% versus YTD 2022 YTD FY2023 cloud revenue increased 54% versus YTD 2022 YTD FY2023 total revenue was EUR 749m, an increase of 33% versus YTD 2022 *Note: all figures based in Euros and reported in constant currency. In line with WorkWave establishing itself as a standalone business at the end of Q2 2021, the performance reported above excludes WorkWave’s contribution to the IFS Group. Additional highlights: IFS was named a Leader in the IDC MarketScape: Worldwide Service Life-Cycle Management Platforms 2023–2024 Vendor Assessment IFS was named a Visionary in the Gartner Magic Quadrant for Cloud ERP for Product-Centric Enterprises, 2023
Industrial Forklifts adds new Major Accounts Manager
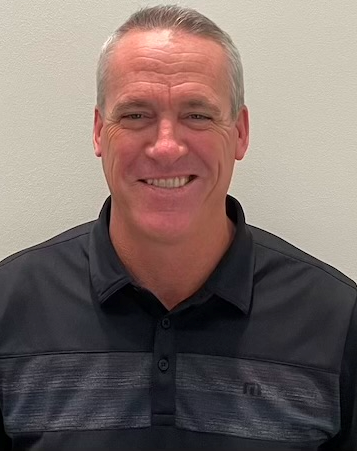
Industrial Forklifts in Phoenix, AZ has announced Trevor Cavanaugh will be their New Major Accounts Manager handling Oklahoma, Texas, New Mexico, Wyoming, Colorado, Arizona, and Southern California. Trevor brings a wealth of experience and a fresh perspective to their team. With 25 years of proven success in the industry, and an NCAA background, he has a track record of driving sales growth and fostering collaboration. His strategic vision and leadership skills will undoubtedly help your sales team and provide better support with Industrial Forklifts. Trevor will oversee Industrial Forklifts dealer development and implementing sales strategies.
Port of Long Beach names two managing directors
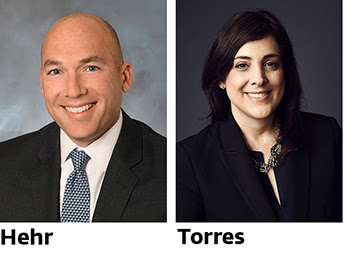
Harbor Commission appoints Commercial Services, Strategic Advocacy leaders The Long Beach Board of Harbor Commissioners has approved the appointments of managing directors for the Port of Long Beach’s Commercial Services and Strategic Advocacy bureaus. Casey Hehr, the Port’s Security Division director, will take up the leadership role for the Commercial Services Bureau, comprising the Business Development, Tenant Services, Information Management and Security divisions. In a newly created position, Eleanor Torres, the Port’s Government Relations director, will head the Strategic Advocacy Bureau – the Government Relations and Communications and Community Relations divisions. The organizational change will bring together the functions and activities of government advocacy, communications with the public and workforce development, telling the story of one of North America’s busiest seaports within a strategic framework. “The goods movement industry is in an era of dynamic change as seaports around the world find more efficient ways to move cargo, more closely engage with communities we serve and reduce operational impacts on the environment,” said Port of Long Beach CEO Mario Cordero. “Casey and Eleanor understand the importance of these goals to the Port of Long Beach and the collaboration between internal and external stakeholders that’s needed for us to accomplish our organizational objectives.” “A big part of this business is relationships, and Casey and Eleanor are experienced directors here who know the needs of our labor, government and industry partners,” said Long Beach Harbor Commission President Bobby Olvera Jr. “We look forward to their contributions to the Port of Choice as we continue to be a leader in sustainable development and operational excellence.” Hehr joined the Port of Long Beach in October 2016 as assistant director of the Security Services Division. He was named director in August 2018. Prior to his position at the Port, Hehr served with the U.S. Coast Guard for more than 20 years, retiring as the Chief of Operations and Response for the Los Angeles-Long Beach Sector. He earned his bachelor’s degree in Mechanical Engineering from the U.S. Coast Guard Academy, and a master’s degree in Business Administration at the Boston College Carroll School of Management. Both Hehr and Torres will report to Chief Operating Officer Dr. Noel Hacegaba. Torres has been the Port’s Government Relations Division director since December 2019. Before then, she worked for 12 years at the Orange County Water District, where she was Director of Public Affairs. Prior to the water district, she spent 10 years working for the California Legislature, including serving as district director for then-Assembly Majority Leader Dario Frommer. Torres earned a bachelor’s degree in economics from Smith College in Massachusetts.
Toyota Material Handling leadership gives back in St. Louis
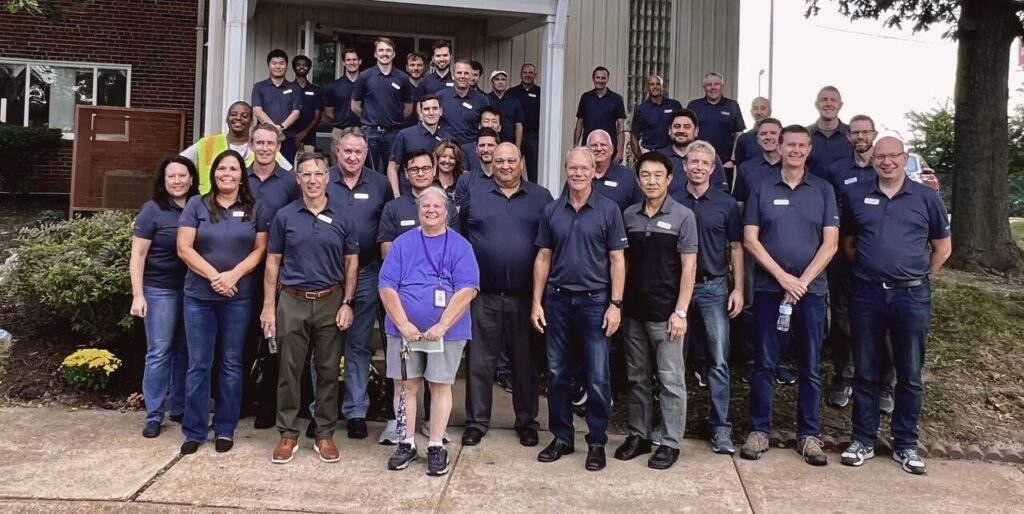
The Toyota Material Handling North America leadership team held a Strategic Planning Session in St. Louis and gave back during their business meeting. On Brett Wood’s LinkedIn page he made mention of this special giving back opportunity. “I’m proud that our entire leadership team always makes time in their schedule to volunteer in the city where we host our meeting. This is a perfect opportunity to put our corporate responsibility into practice and prioritize Toyota’s Core Values.” said Wood. This year the Toyota Leadership team volunteered at Lydia’s House, a center that provides a place of healing and hope for women and children who are victims of domestic violence. “We helped improve their landscaping, cleaned apartments, and set up furniture and essential items in apartments that provide a positive atmosphere to these families when they need it most.” said Wood. “These leaders make me proud for arriving a day early to volunteer at impactful organizations like Lydia’s House. These events are poignant reminders that if you want to lift yourself up, lift someone else first.” added Wood.