Women In Trucking Association announces 2024 Distinguished Woman in Logistics Award finalists
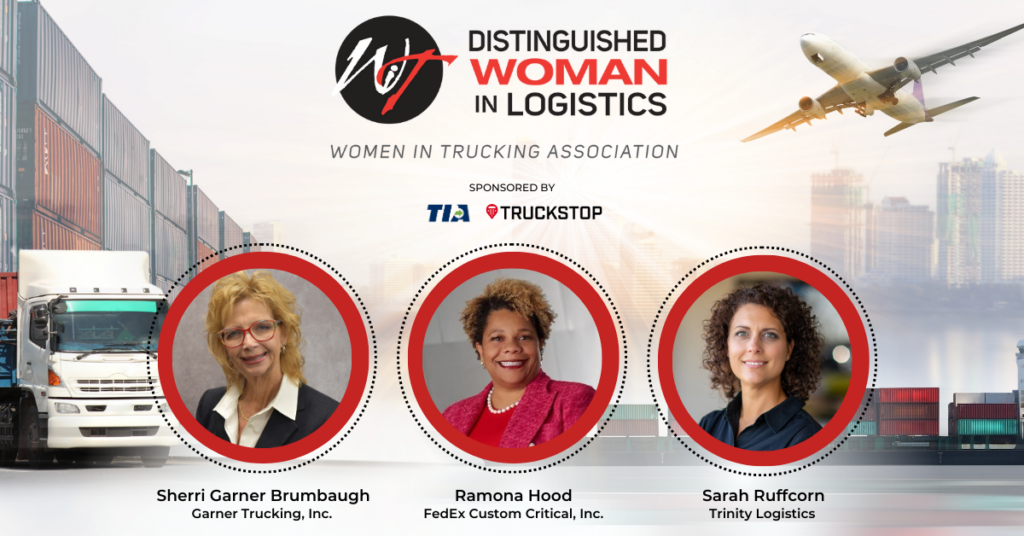
The Women In Trucking Association (WIT) has announced three finalists for the 2024 Distinguished Woman in Logistics Award (DWLA). Sponsored by the Transportation Intermediaries Association (TIA) and Truckstop, the award promotes the achievements of women employed in the North American transportation industry. Finalists for the 2024 DWLA have demonstrated extraordinary leadership within their company as well as the industry. This year’s finalists are Sherri Garner Brumbaugh, president and CEO, of Garner Trucking, Inc; Ramona Hood, president and CEO, of FedEx Custom Critical, Inc.; and Sarah Ruffcorn, president, of Trinity Logistics. Sherri Garner Brumbaugh has more than 33 years of experience in the trucking industry, beginning her career at her family-owned and operated truckload carrier in 1991. She became the owner of Garner Trucking, Inc. in 2012. This year, Garner celebrates 64 years in the industry. Garner Brumbaugh has served the industry as a board member for The American Trucking Association, the Ohio Trucking Association, and Indiana Motor Truck Association. She also served on the advisory committee on human trafficking for the Federal Department of Transportation. Other organizations important to Garner Brumbaugh are her volunteer efforts with the Boy Scouts of America and transporting a truckload of wreaths for Wreaths Across America to her hometown cemetery and Arlington National Cemetery. In 2024, for the eighth consecutive year, Garner Trucking, Inc. was named a Best Fleets to Drive For and recognized as a two-time Hall of Fame recipient. Ramona Hood is president and CEO of FedEx Custom Critical®. She began her career with FedEx in 1991 in an entry-level position and worked her way up to hold various executive leadership positions at FedEx Custom Critical and FedEx Supply Chain. Hood has been recognized for her excellence in thought leadership, responsibility, and passion-driven results. A few specific recognitions include Crain’s Cleveland 2022 Power 150 list, Business Insider’s powerful women leading top logistics companies in 2021 and service on the Brinker International Board of Directors noting her deep experience in sales, operations, supply chain, marketing, and talent management to promote growth and brand differentiation. Most recently, she was appointed to the Knight Foundation Board of Trustees due to the impact she has made on the Akron-area community as a business leader. Sarah Ruffcorn, president of Trinity Logistics, a Burris Logistics Company, is responsible for leading a complex people-centric freight solutions company arranging freight for businesses of all sizes. Ruffcorn joined Trinity Logistics in 2002 following completion of her Bachelor of Arts in Organizational Communications from Western Illinois University. Her natural curiosity and commitment to excellence led to roles with increasing responsibility and leadership. She has continued her education with executive education programs focused on strategy, finance, and leadership including attending the Wharton School of Business. A champion for servant leadership, Ruffcorn has a strong passion for coaching others to help them work at their highest potential. Ruffcorn currently serves on the Transportation Intermediaries Association (TIA) Board of Directors, TIA’s Women in Logistics Committee, and Tidal Health Medical Partners Board of Directors. Members of the judging panel include: Brent Hutto, chief relationship officer, Truckstop; Anne Reinke, president, and CEO, TIA; Dr. Stephanie S. Ivey, associate dean for research and professor, Herff College of Engineering; Erin Van Zeeland, chief commercial officer/senior vice president and general manager-logistics, Schneider and winner of the 2023 DWLA; and Jennifer Hedrick, president and CEO, WIT. The award highlights the crucial roles of leading women in the dynamic and influential field of commercial transportation and logistics, which encompasses logistics service providers as well as motor carriers. The winner of the 2024 award will be announced during the TIA Capital Ideas Conference and Exhibition on Thursday, April 11 in Phoenix, AZ.
PTDA to Host 2024 Canadian Conference
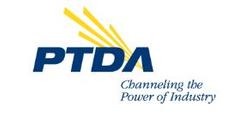
The Power Transmission Distributors Association (PTDA) will convene for the PTDA 2024 Canadian Conference in Niagara Falls, Ontario, Canada on June 4–6. Delegates in the power transmission/motion control (PT/MC) industry, representing PTDA distributor and manufacturer companies, will broaden cross-channel networks, expand connections and deepen business relationships. “Opportunities to cultivate strong relationships between channel partners in the Canadian PT/MC industry are crucial for both corporate and industry expansion,” says PTDA President, Brian Nowak, Kurz Industrial Solutions. “Attendees at this year’s Canadian Conference can look forward to a robust program offering valuable networking opportunities, information on critical market trends and insights on bolstering workforce support.” The conference’s Distributor-Manufacturer Idea Exchange (DM-IDEX) is a favorite of both manufacturer and distributor executives. This face-to-face cross-channel business program delivers measurable ROI. New this year, DM-IDEX will offer open time for more informal meetings, in addition to scheduled appointments for those who prefer time for deeper discussion of business ventures, market strategies and issues. Well-respected industry thought leaders and popular speakers will offer presentations on relevant and timely topics. Opening keynote Amber Mac, award-winning podcaster, author and media host on the topic of Artificial Intelligence (AI), will share practical lessons and insights as she guides attendees through her four-part blueprint for thriving in our AI future. A diverse panel of hiring experts from Indeed, a post-graduate program, and HR representatives from a PT/MC manufacturer and distributor company will share best practices to help reimagine hiring strategies. Using a universal issue—recruiting new employees—attendees will get creative during the interactive team activity, “Achieve Better Outcomes Through Disruptive Problem-Solving.” Led by Ken Tencer and Saquib Vali, and hosted by the PTDA Foundation, participants will learn to radically change their thinking and approach to appealing to the next generation of talent. Jeremy Bess, Economist, ITR Economics will present the closing keynote “Calculating the Risks and Opportunities for 2024 and Beyond.” In his presentation, Bess will provide a data-driven analysis of Canada’s economic trends, glimpsing what to expect for PT/MC-relevant industries. Receptions, group meals, and golf will provide opportunities for more informal networking throughout the conference. Those registering before April 30, 2024 receive a $100 discount.
Episode 473: Warehouse Staffing: A deep dive with Traba’s Read Egger
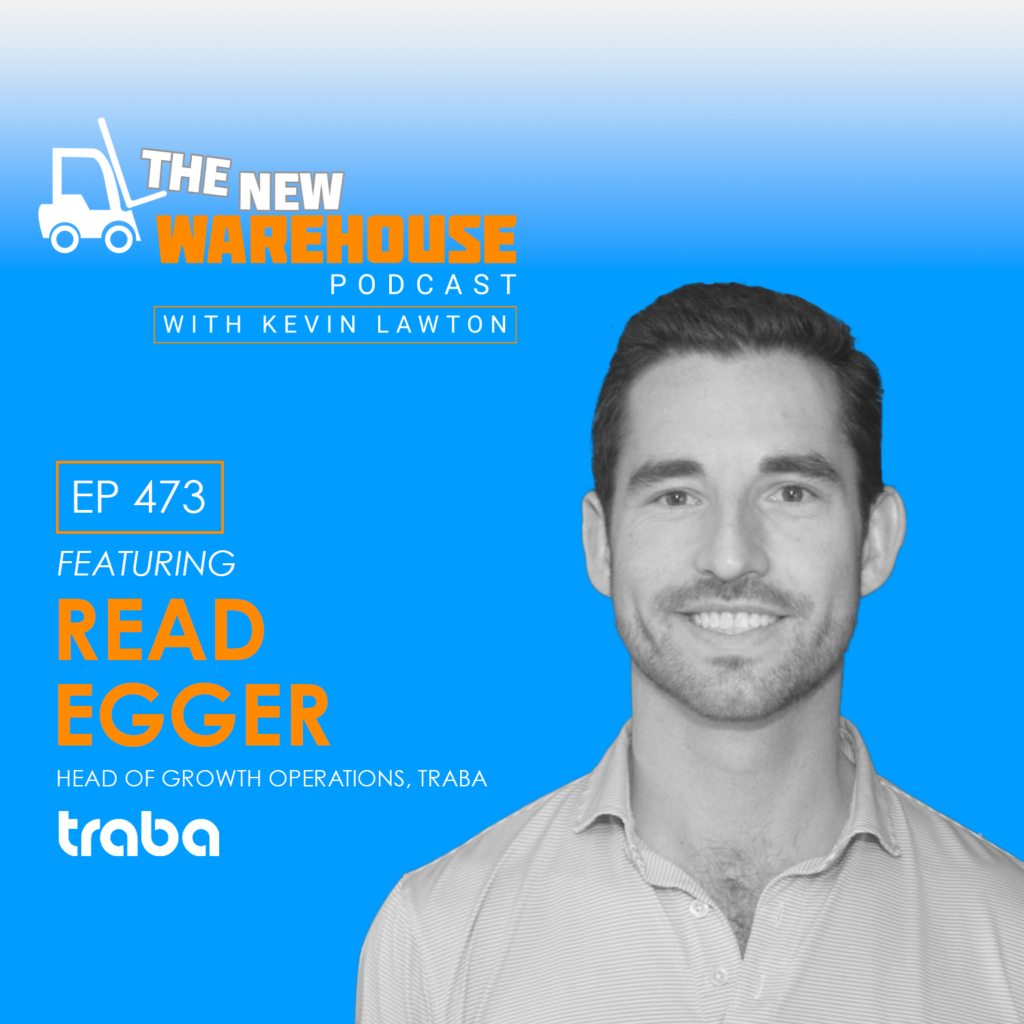
In this episode of The New Warehouse, Kevin is joined by Read Egger, the Head of Growth Operations and Go-To-Market at Traba. This innovative company is tackling the persistent challenges of staffing in the warehousing sector by merging technological solutions with thorough vetting processes, ensuring the delivery of not just any staff, but the right staff. Traba’s approach addresses critical staffing issues, leveraging technology to enhance the efficiency and effectiveness of warehouse operations. The conversation with Read provides valuable insights into how Traba is setting new standards in staffing solutions. Transforming Warehouse Staffing Through Technology Read explains, Traba is not your typical staffing agency. It’s a tech-enabled labor marketplace focusing on the light industrial sector, aiming to match the right workers with the right jobs. “We are a tech-enabled labor marketplace that specifically focuses on serving light industrial clients and light industrial workers,” Read explains. This approach not only streamlines the staffing process but ensures a higher quality of temporary labor by closely matching worker skills with client needs. “Our foundation is rooted in building products that help workers and businesses achieve their highest level of productivity when using temporary labor with a level of operational support not seen in staffing in general.” The Vetting Process: Ensuring Quality and Fit One of the cornerstones of Traba’s success is its rigorous vetting process. “You have to go through a background check…federal, county, global watch list, sex offender check all those things just to enter our labor supply,” Beyond background checks, Traba conducts interviews and on-job evaluations to verify worker skills and fit, setting a high bar for staffing quality in the industry. In cases where specialized skills or experience are necessary, like driving a stand-up forklift, the vetting process is critical. “It’s all those factors of vetting and clearly communicated expectations that flow into having a good end result for the worker and the business.” Future Directions: Data-Driven Workforce Solutions Looking ahead, Traba is set on becoming a vital component in the broader supply chain by leveraging data for labor management systems and demand planning. “And then from there, becoming more of an integral component of the greater supply chain,” Read shares, highlighting the ambition to integrate Traba’s solutions into larger operational frameworks, thus optimizing labor efficiency and productivity at a grander scale. Key Takeaways Traba is leveraging technology to solve traditional staffing issues in the warehousing sector. Their rigorous vetting process ensures that only qualified and suitable workers match client needs. Traba is looking towards the future by using data-driven solutions to enhance labor efficiency and supply chain operations further. The New Warehouse Podcast Episdoe 473: Warehouse Staffing: A Deep Dive with Traba’s Read Egger
Global Shop Solutions Director achieves 20-Year Milestone
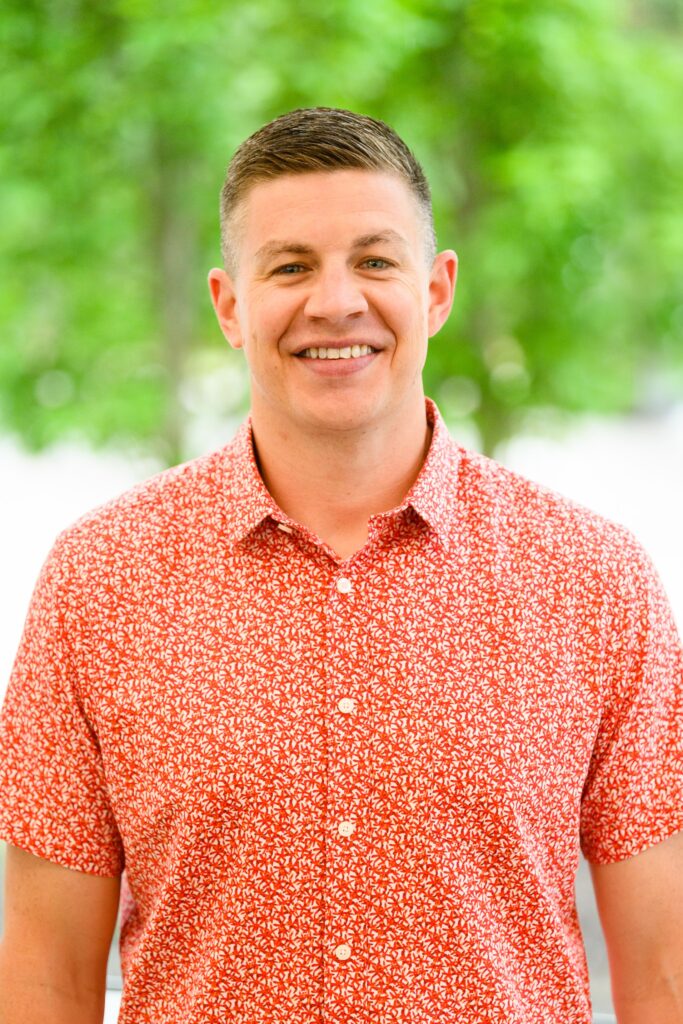
One of the most important aspects of ERP software for manufacturers is the stability of the software provider. Global Shop Solutions has recognized Chris Pinaire, MBA, Director of New Implementations, for his 20 years of dedicated service to the manufacturing industry. Pinaire began his career with Global Shop Solutions as a customer service representative. With his background in management information systems and keen problem-solving abilities, he was quickly promoted to helping manufacturers successfully implement ERP software and consulting with existing customers to simplify their manufacturing processes. After several years as a senior consultant, Pinaire was elevated to his current position where he has had a significant impact on the manufacturing industry. “Chris is smart, hardworking, and constantly looking for ways to make the implementation process faster and easier,” says Dusty Alexander, Global Shop Solutions President and CEO. “He manages a team of more than 70 implementation specialists, who average a 95% success rate for new implementations. His commitment to excellence makes us better every day.” Pinaire attributes his tenure at Global Shop Solutions to the work, the people, and the satisfaction of helping manufacturers solve problems and find the best solutions for their businesses. “The work is interesting and challenging,” says Pinaire. “There’s never a dull moment, and I love the people I work with. We operate as a unified team and always support each other to find the best solutions for our customers.” “I also admire the way Global Shop Solutions grows its people internally,” adds Pinaire. “Keeping people interested requires having a path for them to grow. Five, 10 or 15 years ago we didn’t have a lot of positions that exist today. Adding new positions as the business grew provided a path to keep our employees hungry and growing, playing a key role in the stability of our workforce.” For Pinaire, it’s ultimately all about helping the people associated with Global Shop Solutions achieve the results they want. “I’m motivated by helping our customers and my employees grow,” he says. “Transforming an inefficient, manual, paper-driven company into a lean, paperless manufacturing enterprise makes all the time, effort, and travel worthwhile. It is exceptionally rewarding to grow our new consultants into confident, independent experts.”
Wauseon Machine to showcase integrated automation solutions at Automate 2024
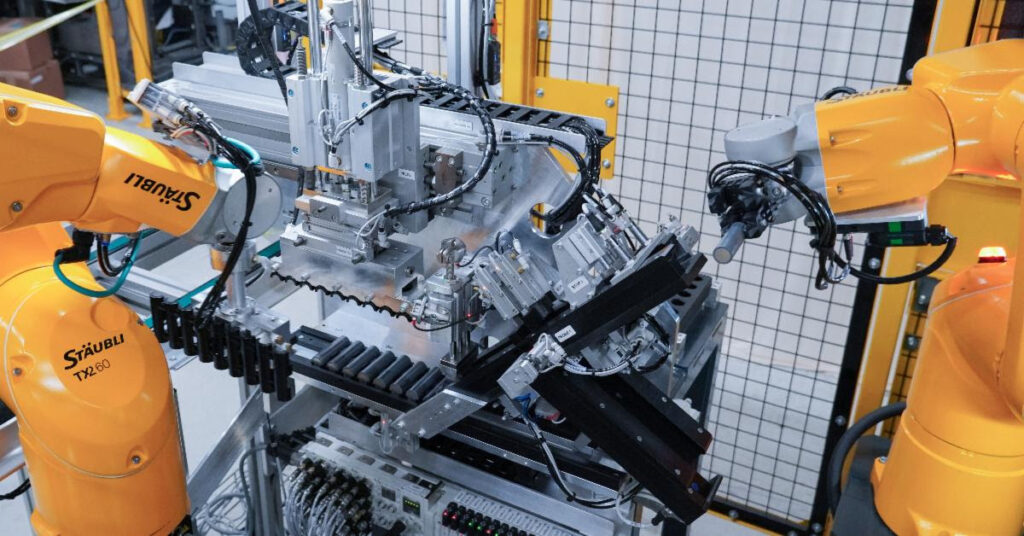
Visit Booth #1257 to learn more about robotic and custom-tailored automation solutions Wauseon Machine, Inc. (WM) has announced its participation in Automate 2024. The show is scheduled to take place from May 6-9, 2024, at McCormick Place in Chicago, Illinois. Automate is the premier event for automation professionals and Wauseon Machine will be showcasing cutting-edge technology. Wauseon’s expansive show floor will feature leading automation solutions ranging from robotics to vision systems, motion control, artificial intelligence, and more. Attendees will have the opportunity to explore tomorrow’s innovations and connect with Wauseon’s team and Executive leadership. As part of its commitment to delivering comprehensive automation solutions, Wauseon Machine is proud to partner with industry leaders including Fanuc, Staubli, Yaskawa, ABB, and Epson. These partnerships enable Wauseon Machine to integrate a wide range of capabilities, ensuring seamless automation solutions tailored to meet the unique needs of each client. McAlister Design & Automation, a subsidiary of Wauseon Machine, will showcase its innovative Battery Test and Assembly System, which caters to the growing demand for electric vehicles and consumer electronics. This system ensures the quality of battery packs by inspecting and testing individual cells before assembly, thus enhancing product reliability. Automate 2024 will not only provide an excellent platform for networking but also offer valuable training and educational opportunities. From panel discussions to expert-led training and on and off show-floor networking events, attendees can expect a rich and immersive experience designed to foster collaboration and knowledge sharing. “We are excited to participate in Automate 2024 and showcase our integrated automation solutions alongside our esteemed partners,” says Joe Gemma, CRO of Wauseon Machine. “Our collaborative approach enables us to deliver innovative and customized automation solutions that drive efficiency and success for our clients across various industries.” Visit Wauseon Machine at Automate 2024 to learn more about their integrated automation solutions and explore the future of manufacturing.
Upper Mississippi Waterway Association names Williams as executive director
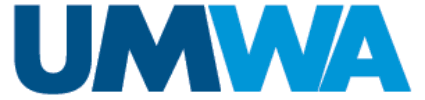
The Upper Mississippi Waterway Association (UMWA) has tabbed Gary Williams to lead the organization. Williams comes to UMWA with 35 years of experience in transportation, business development and merchandising of commodities. “We’re excited to have Gary on board as executive director,” UMWA President Jeremy Putman said. “He has a wealth of experience on the waterways and will help lead the strategic change of our association.” Williams’ experience includes barge, vessel, rail, truck, and containerized freight, trade, and logistics in the eastern and western corn belts, the Pacific Northwest, and Canada. He also served on the National Grain and Feed Association’s waterborne commerce committee. Williams has a degree in agriculture economics from Ohio State University. “I look forward to getting to know the membership better and understanding the challenges and opportunities facing the industry,” Williams said. In addition to Williams, UMWA is requesting ideas for strategic planning from its membership. The board is looking for member input, including a request for member profiles. “We want to connect with our membership and understand the challenges each faces as they go about their work on the waterways,” Putman said. “This is an exciting time to shape this organization and serve our membership for years to come.” UMWA member profiles So, what does a member profile look like? UMWA board members simply want to know your business and you better. The more the board understands its members, the better the strategic planning. Simply send a couple sentences, or paragraphs, to gwilliams@agmgmtsolutions.com explaining who you are, what you or your business does, and why you’re a member of UMWA. UMWA will take care of the rest.
NFI Driver earns highest recognition by Truckload Carriers Association
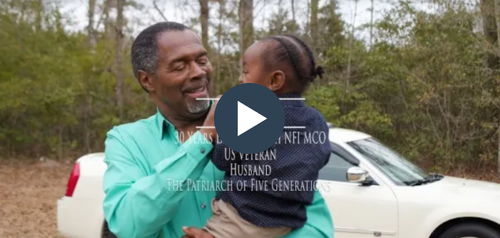
On March 26, Howard Robinson of NFI was awarded the TCA Professional Driver of the Year award at the Truckload Carriers Association’s (TCA) Annual Convention. Howard was one of five recipients of this distinguished title and is a shining example of perseverance, professionalism, and safety in the transportation industry. Howard has been a driver for 30 years, starting his career with MCO Transport, which was acquired by NFI in 2022. Throughout his 30 years of driving, he has achieved a perfect record of zero accidents and violations. Howard stresses the importance of safety at every turn, and in 2023, he was a recipient of NFI’s Million Mile Award, which awards drivers for completing over a million safe miles. “It’s exciting to have one of our own recognized with such an honor by the TCA. We pride ourselves on safety and our people,” said Brian Webb, President of Port Services at NFI. “Driving for more than 30 years and over a million miles without any accidents or violations is admirable. Howard sets a great example for all drivers, and we’re proud to have him on our team.” At NFI, Howard is known for his radiant personality, neverending smile, and conscientious nature. He is highly regarded and cherished by his team, customers, management, friends, and family. Often the first in the yard and the last to leave, Howard is always willing to go the extra mile to ensure the job gets done. Outside of NFI, Howard has an extensive list of accomplishments. As a proud Veteran, Howard dedicates his life to serving others. Along with his wife, Judy, he leads a prison ministry and a Bible study at a local nursing home. Howard has transformed a troubled past and the lives of others through his unwavering commitment to his faith, family, and community. This award is a testament to his drive for excellence and paves the way for current and future NFI drivers.
ProGlove and topsystem partner to deliver ultimate hands-free picking solution
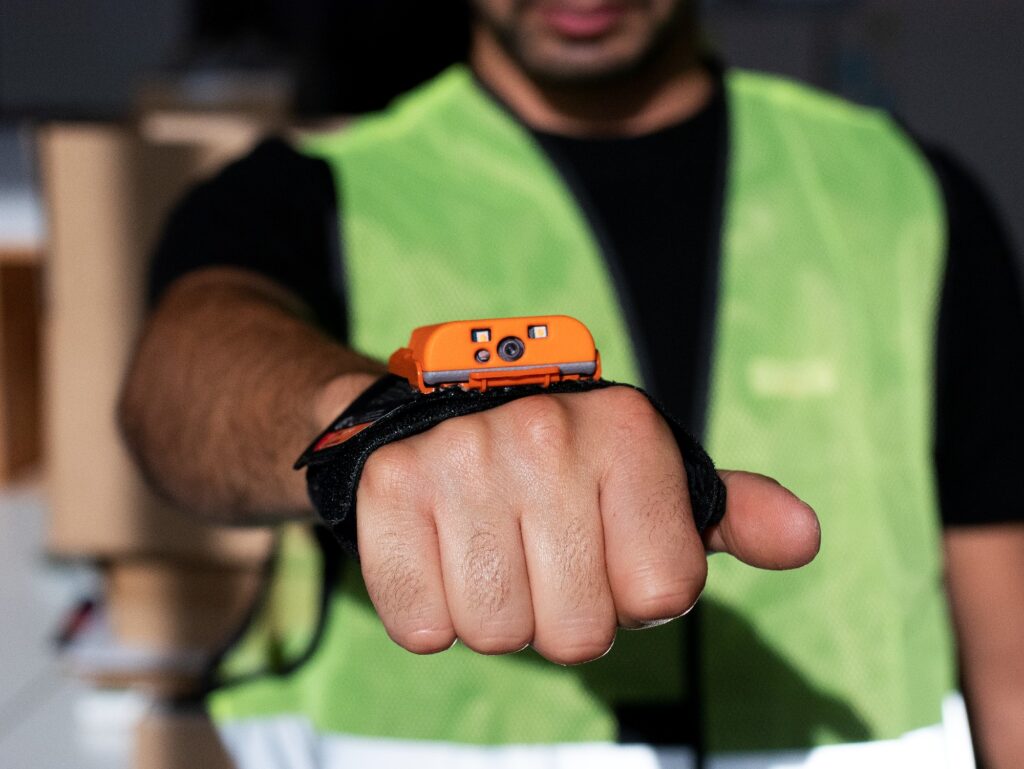
Product bundle combines trailblazing Pick-by-Voice solution with best of breed wearable scanners ProGlove is joining forces with topsystem, a division of Ehrhardt Partner Group (EPG), to address the industry’s highlighted need for mobile logistics solutions. The two organizations will offer a joint bundle that combines topsystem’s LYDIA Voice Pick-by-Voice solution with ProGlove’s MARK family of wearable barcode scanners. This will further untether the frontline worker, enabling additional mobility while providing additional guidance. Operators will benefit from the ultimate hands-free experience to improve safety, quality and efficiency. Easy pairing for extended data capturing To connect topsystem’s LYDIA Voice solution with ProGlove’s wearable scanning products, operators simply scan a pairing QR barcode. The combined solution then enables faster job completion and improved data quality in processes where advanced data capture is required. This is the case, for example, if serial or batch numbers need to be captured. Initial tests suggest that processes can be accelerated by up to 15 percent in environments that require the input of extended numeric sequences. The new bundle will be a perfect match for jobs such as picking, replenishment, sorting, inventory counting, cross-docking and more. “We are very excited to have ProGlove as a strategic partner and to be able to sell this bundle to our customers. Pick-by-Voice is based on a hands-free concept, but whenever an industry or process requires extended data capture, it makes sense to combine Pick-by-Voice with scanning technology. Due to its ergonomic design and high performance, the Pro-Glove scanners harmonize perfectly with LYDIA Voice, as employees still have their hands free,” said Sascha Egener, Director Sales Voice Solutions at topsystem. “Combining LYDIA Voice with our wearable scanners is a huge step forward for shop floor workers,” said Pierre Mikaelsson, CPO at ProGlove. “It gives them the ultimate hands-free working experience while providing guidance to promote their well-being, efficiency and effortless data collection.”
Dematic FIRST® Scholarship program applications open
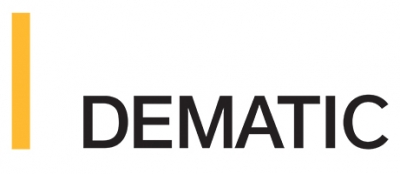
Applications for the Supply Chain and Logistics Scholarship Due Saturday, May 18 THE SITUATION: The Dematic FIRST® Scholarship program supports high school and college students in their journey to become future supply chain and logistics leaders and innovators. This scholarship will award: Two $5,000 scholarships 10 $1,000 scholarships THE APPLICATION: Applications will be submitted online. Students will be asked to upload: High school transcripts for graduation verification or expected graduation date. A one-page essay (1,000-word limit) responding to this prompt: You have been awarded a grant to design and develop a robot of your choice. Describe the purpose of your robot and the problem it solves, highlighting its positive and negative impacts on the world. Explain your design process, including how you prioritize features and navigate trade-offs between different components. Identify the key team members you will need and justify their roles in the project. A letter of recommendation (recommended, not required) from an adult mentor/coach on your FIRST team, teacher, or guidance counselor. WHO: To be eligible to apply for this scholarship, students must: Have participated in a FIRST® Robotics Competition (FRC®) or a FIRST® Tech Challenge (FTC®) Team during high school. Apply and be admitted to a post-secondary institution (including trade schools) as a full- or part-time student. You do not need to have already been admitted at the time of application for this scholarship. Must be pursuing a post-secondary degree or certification at a North American academic institution. STEM degrees and certifications are preferred. Available for any undergraduate students for the fall of 2024. Previous Dematic FIRST Scholarship program winners are ineligible to win again. WHEN: Applications are due Saturday, May 18. APPLY HERE
MHI and WERC responds to Key Bridge tragedy
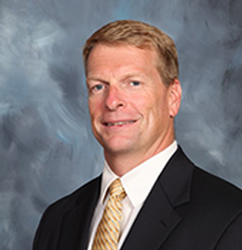
MHI and our Warehousing Education and Research Council (WERC) division are deeply saddened by the devastating collapse of the Francis Scott Key Bridge in Baltimore. Our thoughts and prayers are with the victims, their families, and all those affected by this tragic event. “We are humbled by the efforts of the first responders and rescue teams for their bravery in the face of danger. We stand in solidarity with the city of Baltimore, the state of Maryland, and all involved as they navigate through this incredibly challenging time,” said John Paxton, CEO of MHI. “This tragedy serves as a stark reminder of the importance of resilience to keep the supply chain moving even during crisis and disruption. As a major East Coast logistics hub, supply chains will face major challenges in the days ahead as the Port of Baltimore and surrounding intermodal, trucking, and warehousing infrastructure are disrupted.”, added Paxton. The robustness and agility of the supply chain industry point to a rapid recovery from this tragedy. As associations serving this industry, MHI and WERC are committed to supporting its members and the broader community during this recovery.
U.S. Rail Report for the Week Ending March 23, 2024
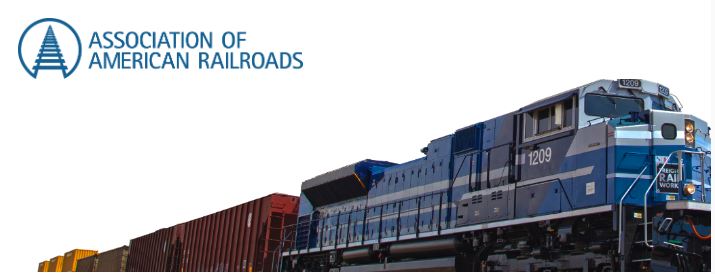
The Association of American Railroads (AAR) reported U.S. rail traffic for the week ending March 23, 2024. AAR also weighed in on the Francis Scott Key Bridge collapse and how railroads are working to limit disruptions. “The top priority following the tragic collapse of the Francis Scott Key Bridge must be supporting the individuals and families impacted,” said AAR SVP of Policy and Economics Dr. Rand Ghayad. “At this time, there are many unknowns about the long-term business impacts. However, recent years have shown us the resilience of railroads and the broader logistics sector in adapting swiftly to challenges while continuing to serve our customers. Those lessons will be put to work in the days ahead to minimize disruption to the fullest extent possible.” For this week, total U.S. weekly rail traffic was 470,593 carloads and intermodal units, up 2.1 percent compared with the same week last year. Total carloads for the week ending March 23 were 215,277 carloads, down 6.1 percent compared with the same week in 2023, while U.S. weekly intermodal volume was 255,316 containers and trailers, up 10.2 percent compared to 2023. Five of the 10 carload commodity groups posted an increase compared with the same week in 2023. They included grain, up 2,735 carloads, to 21,467; chemicals, up 1,822 carloads, to 33,702; and motor vehicles and parts, up 888 carloads, to 16,109. Commodity groups that posted decreases compared with the same week in 2023 included coal, down 14,169 carloads, to 53,727; nonmetallic minerals, down 2,835 carloads, to 27,607; and metallic ores and metals, down 2,129 carloads, to 18,519. For the first 12 weeks of 2024, U.S. railroads reported a cumulative volume of 2,555,094 carloads, down 4.3 percent from the same point last year; and 3,014,729 intermodal units, up 9.1 percent from last year. Total combined U.S. traffic for the first 12 weeks of 2024 was 5,569,823 carloads and intermodal units, an increase of 2.5 percent compared to last year. North American rail volume for the week ending March 23, 2024, on 10 reporting U.S., Canadian and Mexican railroads totaled 324,001 carloads, down 5.3 percent compared with the same week last year, and 340,799 intermodal units, up 9.4 percent compared with last year. Total combined weekly rail traffic in North America was 664,800 carloads and intermodal units, up 1.7 percent. North American rail volume for the first 12 weeks of 2024 was 7,798,583 carloads and intermodal units, up 1.8 percent compared with 2023. Canadian railroads reported 91,620 carloads for the week, down 3.1 percent, and 73,851 intermodal units, up 7.9 percent compared with the same week in 2023. For the first 12 weeks of 2024, Canadian railroads reported a cumulative rail traffic volume of 1,887,198 carloads, containers, and trailers, down 0.9 percent. Mexican railroads reported 17,104 carloads for the week, down 7.8 percent compared with the same week last year, and 11,632 intermodal units, up 3.2 percent. Cumulative volume on Mexican railroads for the first 12 weeks of 2024 was 341,562 carloads and intermodal containers and trailers, up 6.6 percent from the same point last year. View the charts
Is your customer feedback used to diagnose or sell?
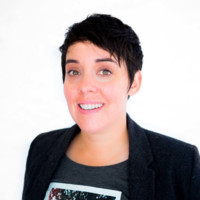
You walk into your general practitioner’s office. You have some pain in your knee lingering for a while from an old sports injury, and it’s starting to cause concern. When the doctor comes in, she doesn’t start by asking questions about your condition. Instead, she hands you a short survey with some broad questions – including things like, “When it comes to selecting a heart medicine, what do you look for?” Then, she says that as an expert, you must have heart disease and writes you a prescription for her own product. This would be an incredibly frustrating and worrisome experience. Why did the doctor not take the time to listen to me? Why did they not want to understand my specific concerns? Why did they presume a wholly separate issue? Even worse, you know you don’t have heart disease and feel you were sold a solution for an issue you didn’t have. It sounds ridiculous. You’d likely never want to see that doctor again. However, businesses exhibit this behavior all the time. Consider how many companies conduct customer outreach through surveys to gather information that is not used to diagnose, but rather gather insights to more effectively sell what they offer. Consider how many companies approach potential clients with a solution without truly understanding the customer’s problems. Why don’t companies take more time to truly understand customer needs? In short, because it’s hard, it takes time, and sometimes, we don’t want to hear what they have to say. Customer feedback isn’t simply about capturing data from questionnaires, reporting the top three frustrations customers have, and then deciding which one is the least costly and painful to implement. It’s also not rolling your eyes when you hear the same concerns over and over again. The hidden opportunity with customer feedback is if you take the time to have qualitative conversations with customers and observe them in the context of their challenge, you can uncover new opportunities to grow, differentiate, and innovate that your competitors don’t see. If your competitors are doing the same surveys and taking the same generic approaches to customer feedback as you, they are gathering the same insights and information. This isn’t leverage, it’s box-checking. Think about some of the greatest companies you admire and the products and services they’ve produced. Every one of them began with a founder or inventor who saw a problem that wasn’t addressed, overlooked, or not considered by other companies. They saw past the superficial insights and focused on the small, nuanced, subtle things. They understood how their competitors operated and thought, and saw an opportunity. This takes honest thought, observation, reflection, and validation of our assumptions. As leaders, we want our companies to grow. We ask our teams for feedback and ideas. We want to find the next innovation that will catapult our organization to the next level. But if no one in the organization is out there genuinely examining customers’ needs, fears, and frustrations, but rather simply listening to sell, you’ll get the same thing you’ve always got – another missed opportunity to create a unique competitive advantage. About the Author Andrea Belk Olson is a keynote speaker, author, differentiation strategist, behavioral scientist, and customer-centricity expert. As the CEO of Pragmadik, she helps organizations of all sizes, from small businesses to Fortune 500, and has served as an outside consultant for EY and McKinsey. Andrea is the author of three books, including her most recent, What To Ask: How To Learn What Customers Need but Don’t Tell You, released in June 2022. She is a 4-time ADDY® award winner and host of the popular Customer Mission podcast. Her thoughts have been continually featured in news sources such as Chief Executive Magazine, Entrepreneur Magazine, Harvard Business Review, Rotman Magazine, World Economic Forum, and more. Andrea is a sought-after speaker at conferences and corporate events throughout the world. She is a visiting lecturer and startup coach at the University of Iowa, a TEDx presenter, and TEDx speaker coach. She is also an instructor at the University of Iowa Venture School.
Janam unveils breakthrough All-in-One UHF RFID reader
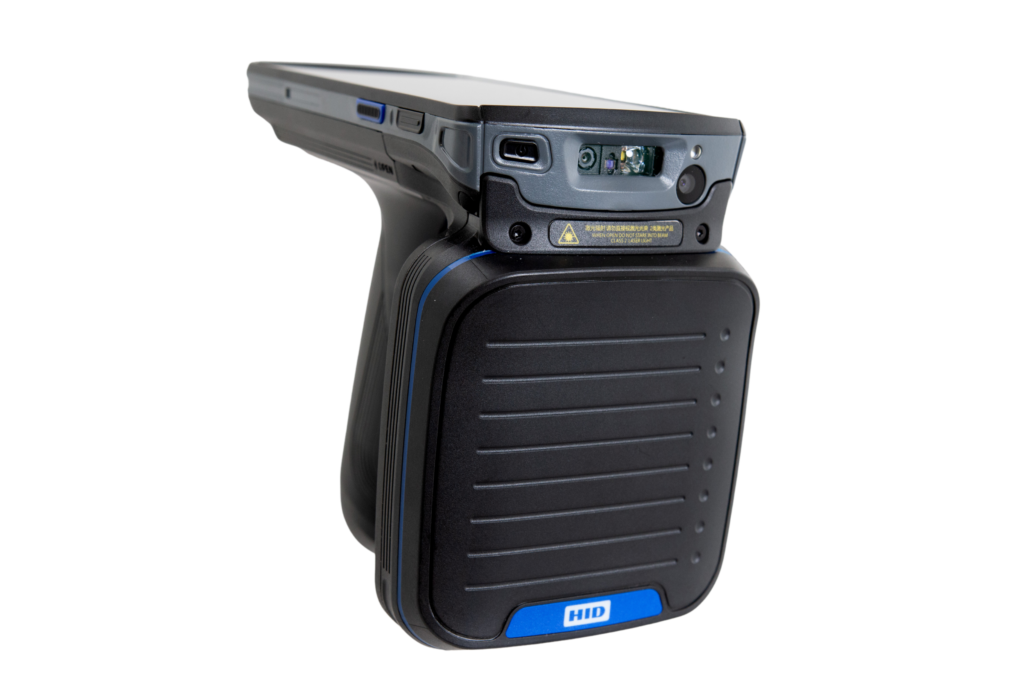
XR2 sets a new benchmark in RFID technology with unmatched speed, accuracy and affordability Janam Technologies, a provider of rugged mobile computers and contactless access solutions, has announced the launch of its XR2 UHF RFID Reader – an all-in-one device designed for real-time tracking and unprecedented visibility into the location and status of items throughout the supply chain. Built to thrive in demanding warehouse, manufacturing, and logistics operations, XR2 combines the most advanced RAIN RFID technology with a sleek, intuitive, and ergonomic design that sets a new standard for power and performance. Superior sensitivity, long-range RFID reading, and lightning-fast processing speeds bring enormous value to inventory management, asset tracking, and other line-of-business applications. KEY FACTS XR2 is a state-of-the-art, handheld RFID reader that optimizes workflow in the most challenging environments. It helps businesses tackle the complexities of modern supply chains with efficiency and precision and sets a new benchmark for what’s possible in asset tracking and inventory management. XR2 is priced to deliver unparalleled value to enterprise customers that don’t want to spend more than is necessary to acquire a superior, uncompromising, all-in-one UHF RFID reader. Powered by the industry-leading Impinj E710 reader chip, XR2 guarantees exceptional signal clarity and incorporates self-jammer cancellation to ensure robust tag detection in areas with a high concentration of tags. Capable of scanning more than 1,000 EPC Class 1 Gen 2 tags per second and from up to 60 feet away, XR2 delivers new levels of efficiency in asset management and inventory control, significantly reducing the time and labor required for businesses of all types and sizes. Equipped with an advanced Honeywell 1D/2D imager for high-throughput capture of even the most difficult-to-read barcodes, XR2 ensures every barcode is acquired and decoded swiftly and accurately. With JanamConnect®, an optional multi-carrier SIM card solution available to XR2 users, businesses gain access to the best-performing cellular networks worldwide, including AT&T, Verizon, T-Mobile, and more than 600 other networks. XR2’s built-in GPS functionality not only provides accurate location data but also enhances asset tracking and management. By merging precise tag location information with RFID data, XR2 enables businesses to gain business-critical insights into asset logistics, streamline operations and significantly boost efficiencies across the modern supply chain.
EDC Bolsters Midwest presence with Dean Grosel
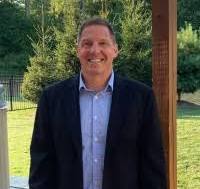
Electronic Drives and Controls expands its presence in the Midwest by appointing Dean Grosel as the new regional representative for Indiana, Kentucky, Ohio, and Michigan. Grosel’s experience and network will support EDC in delivering innovative solutions and service to its growing customer base in the region. Electronic Drives and Controls, Inc. (EDC), a control system integrator and field service company for industrial automation and drive technology, has announced the appointment of Dean Grosel as the new regional representative for the Midwest region, covering Indiana, Kentucky, Ohio, and Michigan. “We are thrilled to announce Dean’s addition to the EDC team as a strategic move to expand our sales efforts in the Midwest in the converting and web handling industries,” said Chuck Dillard, Vice President at EDC. “Dean brings a wealth of experience in tension controls and a proven track record of success that aligns perfectly with our goals for growth in this key region. His expertise and innovative approach will be invaluable to meeting the needs of clients in the Midwest.” By appointing a manufacturer’s representative for the Midwest, EDC strengthens its presence in the region and improves its ability to offer localized and direct support to its clients. Grosel’s company, Grosel Industrial Sales Inc., has more than 50 years of experience in converting industries, with long-standing customers requiring expertise in web handling, extrusion, tension controls and drives integration. Grosel’s markets align directly with EDC’s portfolio of services, benefitting both Grosel’s and EDC’s customers. “I’m truly excited to join the EDC team and to contribute to their dynamic growth initiative,” said Grosel on recently joining the EDC team. “I’m excited to build upon EDC’s innovative solutions and exceptional service to help businesses in Indiana, Kentucky, Ohio, and Michigan achieve their automation goals. ” EDC holds certifications from Rockwell Automation as a Recognized System Integrator and from Siemens as a Solution Partner in Automation Drives, in addition to being CSIA-certified. These certifications, coupled with EDC’s regional expansion, further the company’s ability to serve a broader customer base. “Our certifications represent our commitment to professionalism and expertise,” said Bob Pusateri, Director of Business Development at EDC. “Coupled with our Midwest expansion and maintenance of high standards, we are better equipped to offer enhanced in-person service and support, solidifying our ability to serve a broader clientele.”
WIZE Solutions positioned for growth with expanded resources and capabilities
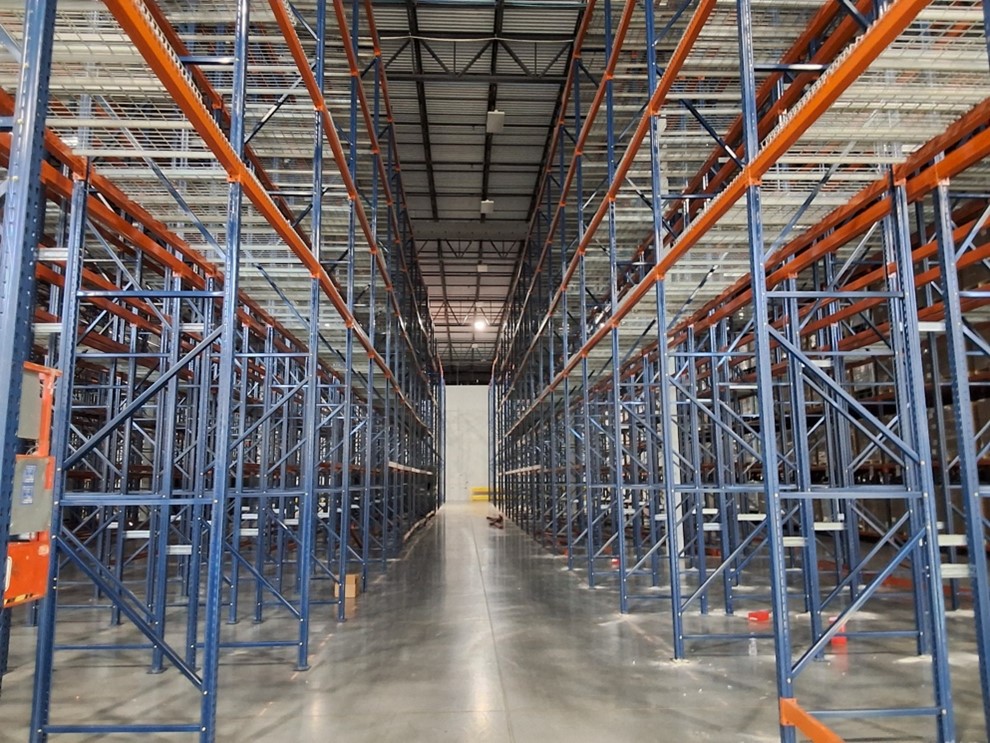
Offering its installation and project management solutions to some of the largest warehouse projects nationwide, WIZE Solutions is experiencing growth that is on-pace to set records for the material handling company in 2024 including its expansion into the automation sector. Since recent strategic investments and acquisitions, WIZE has grown from 175 employees in July of 2023 to 315 employees with key personnel additions in sales, operations, and installation teams. “WIZE Solutions and our teams across the United States continue to grow while providing customers with knowledgeable and efficient project management that stays on track to get a job done right, and on schedule,” Tyson Bigelow, president of WIZE Solutions. “With almost 17 years of successfully helping move the supply chain forward in all 50 states and beyond, we are committed to implementing additional resources like technology, robotics, and automation, as well as the staff to support any new challenge that comes our way.” Wize has made a significant investment in people and processes to provide customers with a full array of services including full automated systems and high-rise rack supported buildings. While growing in these areas, the company continues to focus on warehouse builds of all sizes for full rack installation, pick modules, mezzanines, shelving products, rack repair, and dock door services. WIZE recently acquired Warehouse Equipment Contractors, Inc. and its employee installation teams across the US. This acquisition will provide WIZE with additional experienced teams of employees in the SoCal market, providing excellent service to the newly expanded customer base.
Webasto Charging Systems expands access to ProCore Edge 10 Bay Industrial Charger
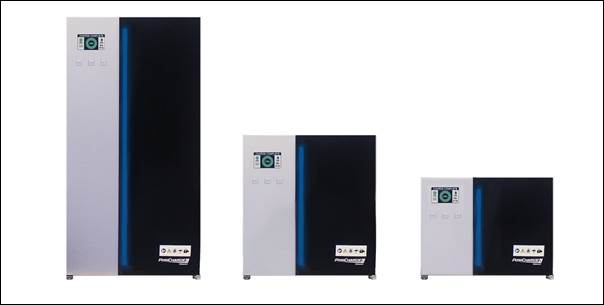
PosiCharge, the industrial charging division of Webasto Charging Systems Inc., a subsidiary of Webasto Group, its divestment of the charging business to Transom Capital Group, has announced the expansion of its PosiCharge ProCore Edge™ line with the introduction of the ProCore Edge 10 Bay. Formerly reserved for select key customers, the ProCore Edge 10 Bay is now available to all Material Handling Equipment customers and other interested parties. The ProCore Edge 10 Bay seamlessly integrates into Webasto Charging Systems’ intelligent charging solutions, catering to various industrial material handling batteries of different types, brands, voltages, and sizes. Leveraging proven technology from the ProCore line, the Edge series features intelligent controls, a universal board, and proprietary algorithms for optimal lead acid and lithium battery performance. Tailored to meet the charging demands of large-scale operations, the ProCore Edge 10 Bay is an ideal solution for facilities that require continuous charging. It is particularly suitable for environments that operate around the clock or have double shifts. This innovative charging system optimizes operations, enhances productivity, and ensures workplace safety. It achieves this by freeing up warehouse space, reducing personnel requirements, and eliminating the need for battery rooms. The ProCore Edge 10 Bay is equipped with wireless BMID, delivering real-time battery data, and ensuring safe and efficient charging. It is a cost-effective solution that offers maximum ROI and strengthens Webasto Charging Systems’ presence in conventional, opportunity, and fast charge sectors. The ProCore Edge 10 Bay is available for immediate shipping, making it an attractive option for businesses that require quick and reliable charging solutions. The ProCore Edge’s intelligent system offers multi-voltage flexibility and seamless adaptability to any battery chemistry, and a user-friendly interface supports it. Utilizing the same innovative app as the original ProCore series, operators can easily program, download data, and manage their fleet from smartphones. Remote setup, troubleshooting, and real-time monitoring capabilities ensure efficient charging management from any location.
KNAPP launches shuttle for freezer applications
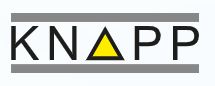
OSR Shuttles Technology released for sale across North American Cold Chain KNAPP has announced that they will commence the sale and implementation of their industry-leading OSR shuttle technology for cold chain applications and projects. Regarded as one of the most demanding application categories for any type of automated storage & retrieval application, KNAPP announced that it has completed a rigorous testing process in a beta testing application that includes conveyor hardware, AS/RS shuttles, and software. The successful beta test included over 2 million cycles and 7000 miles of travel. Israel’s leading supermarket chain, Shufersal, is the first customer to implement the solution. This 294,000 square feet fulfillment center covers all temperature zones for its e-commerce food retail business. Cold chain technology has been frequently used since the 1950s when it was used to preserve animal-based tissue. As medical breakthroughs have increased, including Covid 19 and other vaccinations, so needs innovative cold chain automation solutions. According to Jusuf Buzimkic, CSO of KNAPP Inc., “The company is uniquely positioned to enter this market and rapidly succeed as it is currently a market leader in ‘track and trace’ technology, software, and shuttle-based automation.” Another factor that contributes to the prospective success of KNAPP is the desire on the part of cold chain operators to keep workers out of the harsh freezer environment which is both costly and hard to staff. According to Mr. Buzimkic, some other factors and synergies have driven KNAPP’s interest in this market, including: Automation solutions help to address labor volatility. Automating work in the freezers by giving tasks to robots is safer Cold-chain warehouses are typically tasked with assembling pallets containing different products. KNAPP mixed load palletizing technology includes a unique set of attributes that are conducive to the needs of many cold chain operators. Manual warehouses often use reach trucks operated by human workers in freezers, but those pieces of equipment have height limitations, around five or six levels. Automated warehouses often use automated storage and retrieval systems (ASRS), which deploy cranes and shuttles programmed to retrieve pallets as directed by warehouse management systems (WMS). That configuration allows freezers to be built taller, which has several advantages. Taller freezers create a greater density of products in the same footprint and can reduce the land costs for the cold-chain warehouse. Building taller contributes to more efficient building designs. These high-density structures are much more efficient to cool. Additionally, the openings in the freezer get a lot smaller because you have only a conveyor and a pallet or a box moving through a smaller aperture. Robots are more accurate and systems calculate up front how they’re going to build out a pallet and how to load it in an economical way.
NFI continues expansion and commitment to Canada

NFI underscores its growth and commitment to Canada with strategic appointments and industry accolades. Glenn Nicodemus joined NFI with the acquisition of SDR and is expanding his role as he assumes responsibility for all Canadian warehouse facilities at NFI. Additionally, NFI’s Intermodal team secured high scores in a 2023 Journal of Commerce survey, solidifying its standing in the Canadian supply chain landscape. With nearly 1,000 employees and five million square feet of warehouse space nationwide, NFI stands at Canada’s forefront of multichannel supply chain solutions. The expanded role of Glenn Nicodemus, a proud Canadian resident with 30 years of logistics experience, underscores NFI’s commitment to fostering local talent and leveraging decades of industry expertise to drive excellence in Canadian operations. “Glenn’s appointment as President of our Canadian group speaks to his strong leadership and commitment to excellence for our customers and employees,” said Kevin Patterson, President of NFI Distribution. “Under Glenn’s guidance, NFI is poised for continued success and growth in Canada.” While NFI emphasizes the importance of precision in inventory management and distribution, its robust Canadian leadership team ensures unparalleled service across all service lines. In a recent 2023 Journal of Commerce survey, NFI received an outstanding Net Promoter Score of 90 for its asset and non-asset intermodal services, primarily managed throughout Canada. The recognition reflects the company’s focus on customer satisfaction and service levels. Notably, NFI excelled in equipment availability and on-time pickup and delivery. “NFI’s Intermodal service reflects our overall strategy to live our commitments to our customers and our carrier partners,” commented Mark McKendry, SVP of Intermodal at NFI. “We offer flexibility, network optionality, national coverage, and one of the most experienced teams in the industry.” NFI expanded its Canadian reach in 2016 with the acquisition of Dominion Warehousing, building on its already established presence. In 2022, the company made an investment that doubled its intermodal scale, increasing its Canadian assets to 500 owned dry and refrigerated intermodal containers. The acquisition of SDR in 2023 marked another significant milestone, doubling NFI’s Canadian distribution footprint and its team of supply chain experts.As it expands, NFI remains dedicated to delivering exceptional supply chain solutions and driving value for its North American partners.
Caster Concepts earns certification from Ergonauts for TWERGO® Ergonomic Caster Wheel
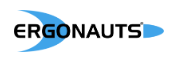
Certification Program focuses on ergonomic products that improve worker safety and productivity Caster Concepts, a manufacturer of industrial heavy-duty casters and wheels, has announced that their innovative TWERGO® ergonomic caster wheel has earned the industry’s first Ergonauts ergonomic approval. The Ergonauts approval confirms that TWERGO® heavy-duty industrial casters have been tested and validated to reduce push forces by 55% compared with traditional cart casters. “Keeping associates safe is critical to optimizing operations effectiveness,” said Steve Davis, CVO, Ergonauts. “Lower push forces help ensure associates avoid back strain and other common industrial ergonomic problems, which are leading causes of lost time and injury costs.” To earn certification by Ergonauts, a product must be tested, and results confirmed by two senior professional ergonomists. The approval confirms that workplace safety can be enhanced as a result of the ergonomic benefits of an approved product. “We are honored to be the first material handling company to achieve this level of approval. TWERGO casters were designed to minimize back strains and other common issues related to traditional material handling carts’” Doug Backinger, Vice President of Sales at Caster Concepts, explained. “By taking a user-first approach with our product development, we design casters that make operations safer and more efficient. We are committed to continuous innovation to improve our customers’ safety and productivity.” The TWERGO® caster line is built around patented technology and features a multiple-wheel-in-one design. The tapered wheels spin independently and can rotate in either direction at any rate. The advantages of this unique design include minimized friction and reduced initial and continuous push force, as well as the associated force exerted to turn.
Bobcat announces its 2024 Dealer Leadership Group, honors 16 North American Dealers for Achievement
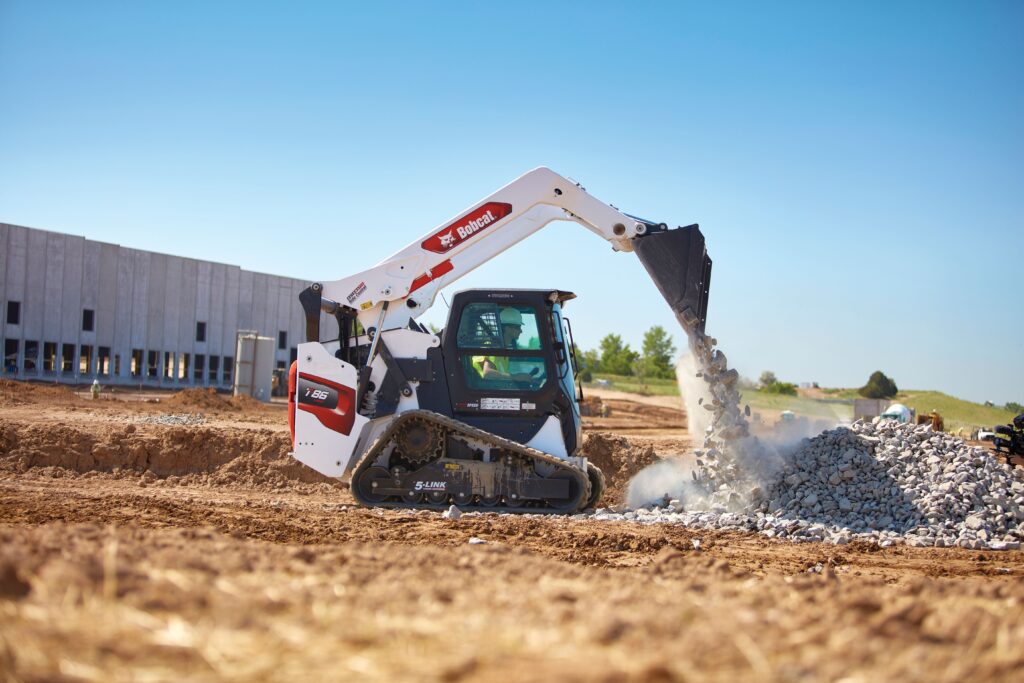
The Program Recognizes the Company’s Highest Performing Dealers Across the U.S. and Canada Bobcat Company has announced its 2024 Dealer Leadership Group. The 16 Bobcat dealerships honored this year are its highest-performing dealers in North America according to the company’s Dealer Performance Review. “Every year, our dealer network keeps raising the bar,” shared Brady Seavert, Vice President of Construction Sales at Bobcat. “We’re thrilled to recognize these outstanding businesses for their dedication and impressive accomplishments across the board.” The 2024 Bobcat Dealer Leadership Group includes: Bobcat of Brandon – Manitoba, Canada Bobcat of Brantford, Inc. – Ontario, Canada Bobcat of Dallas – Texas Bobcat of Fort Wayne – Indiana Bobcat of Gwinner – North Dakota Bobcat of Lincoln – Nebraska Bobcat of New York City – New York Bobcat of the Rockies, LLC. – Colorado Bobcat of Vineland – New Jersey Bobcat of Westchester/Jim Reed’s Equipment – New York Curtis Lane Equipment – North Carolina Duron Equipment, Inc. – Manitoba, Canada Ironhide Equipment, Inc. – North Dakota Jordan Equipment – Maine North Jersey Bobcat – New Jersey White Star Machinery – Kansas The Bobcat Dealer Performance Review is not only used to help dealers compare their performance against their peers, but it also identifies the top-performing dealers across Bobcat’s North American network, which is comprised of 300-plus dealer enterprises in the United States and Canada. As members of the Dealer Leadership Group, representatives from these recognized dealerships will function as the “voice” for the dealer network and meet with Bobcat senior leadership throughout the year to provide insights and feedback. To recognize and celebrate the achievements of this select group, Bobcat will also honor members at a dealer incentive trip to Prague, Czech Republic later this year. Each year, Bobcat Company continues to grow its North American dealer network. As part of the Bobcat dealer partner program, dealerships are provided with development opportunities, ongoing training, and educational and marketing resources to help position their customers, employees, and businesses for long-term success. “Our dealers play a crucial role in advancing the Bobcat brand,” Seavert continued. “Their commitment and teamwork are vital to our continued growth. We’re constantly inspired and thankful for the meaningful difference they bring to our customers every day.”