Softeon hosts two innovative warehousing solutions sessions during MODEX

Softeon Warehouse Management System (WMS) experts will share the latest in WMS implementations, automated warehousing, and material handling at MODEX in Atlanta Softeon has announced it will share the latest in WMS implementations, automated warehousing, and material handling during two live sessions during MODEX 2024 at the Georgia World Congress Center in Atlanta, March 11-14. During MODEX, Softeon is sharing warehouse automation strategies, live demonstrations, and expert networking opportunities. In addition to exploring Softeon’s WMS software at Booth #C7466, MODEX attendees have the opportunity to engage with company leaders during two sessions: “Ensuring the ROI from WMS Implementations” | Brian Pier, VP, Solution Delivery Tuesday, March 12 | 1:30 – 2:15 p.m. ET | Theater A “Successfully Navigating the Great Material Handling Integration Challenge” | Mark Fralick, CTO Wednesday, March 13 | 3:30 p.m. – 4:15 p.m. ET | Theater I “Automation continues to be a solution for labor challenges, and automation and the integration of several platforms in turn cause operational challenges,” said Mark Fralick, Chief Technology Officer, Softeon. “Integration continues to be a major issue and barrier to success, leading to slow time-to-value. During my MODEX session, I’ll discuss how companies can get faster at WMS deployment. I also look forward to discussing how warehouse execution systems (WES) are enabling the orchestration of fulfillment processes across automated and non-automated processes, as well as the importance of mobile robot platforms for managing robots of different types and vendors in one environment.” According to a Gartner report, by 2026, over 50% of companies deploying intralogistics robots will have a multiagent orchestration platform. Hence, Fralick will discuss the need to be equipped with capable software to successfully integrate with the technology needed to meet the current and future needs of some of the world’s most complex warehouses. “Companies can improve WMS results by optimizing microflows and by leveraging a composable WMS, which creates flexibility and agility; therefore creating higher levels of adaptability and ROI over time,” said Brian Pier, Vice President of Solution Delivery, Softeon. MODEX attendees can hear first-hand from Pier about how to deliver expected results and reach time-to-value faster. In addition to attending Softeon’s warehouse-related sessions, MODEX attendees can join in a hole-in-one putting contest at the company’s booth #C7466. Global supply chain leaders are encouraged to register to meet with Softeon’s team during MODEX. Gartner “Predicts 2023: Supply Chain Technology” Dwight Klappich, Christian Titze, Tim Payne, Amber Salley, Simon Tunstall; 28 November 2022.
Yale integrated lithium-ion forklift beats out 10 other nominees for top spot in product of the year awards
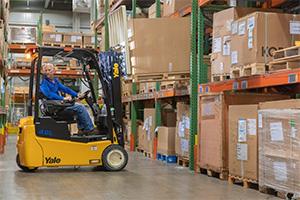
Readers of two material handling publications vote the ERP-VTL/VFL series the top lift truck of 2023 Yale Lift Truck Technologies announces the ERP-VTL/VFL integrated lithium-ion forklift series is the winner of the Readers’ Choice Product of the Year award determined by readers of Material Handling Product News and MaterialHandling247.com. The series, which includes three- and four-wheel models, was voted as the top product in the lift trucks and accessories category. Both the ERP040VTL, a three-wheel model, and the ERP040VFL, a four-wheel model, buck the traditional approach in which a battery box replacement converts counterbalanced lift trucks from lead-acid to lithium-ion battery power. Instead, the trucks are designed from the ground up around a space-saving lithium-ion battery pack. “Today’s warehouses need to capitalize on every possible opportunity to improve efficiency,” said Brad Long, Brand Manager, Yale Lift Truck Technologies. “Not only do these award-winning lift trucks provide a simpler pathway to the benefits of lithium-ion power relative to an aftermarket retrofit, but the strategic design around the fully integrated battery pack also delivers key productivity benefits, including improved operator ergonomics and stability.” An open-space design increases operator freedom to position feet and makes for easy entry and exit, maximizing comfort and convenience to help propel productivity, while a repositioned center of gravity enhances drive quality and improves truck handling in corners for greater operator confidence and performance. The lithium-ion power also supports productivity through fast charging and zero battery maintenance, allowing operators to focus more of their time on moving loads. The lift trucks produce zero tailpipe emissions and no gassing in battery charging or maintenance processes and offer lower energy costs compared to those powered by fossil fuels and lead-acid batteries. This award is the second for the ERP-VTL, which was previously named a winner of the GOOD DESIGN Award.
Signode unveils latest case packaging innovations with the LDX-RTB Premier
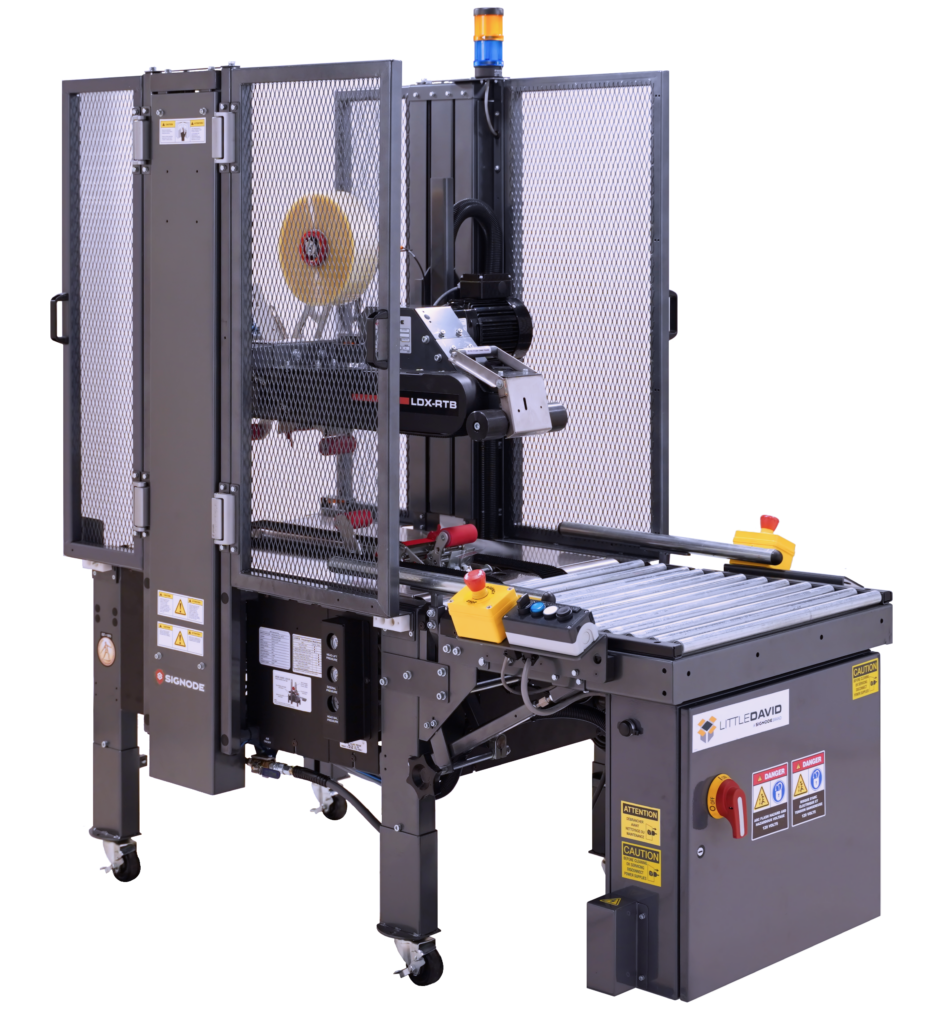
Signode, a manufacturer of a broad range of automated transit packaging equipment, tools, consumables, and automation solutions, has announced the latest addition to the Little David® family of case packaging equipment: the LDX-RTB Premier Case Sealer. The LDX-RTB family of case sealers is already well-known for speed, versatility, and efficiency in case handling applications. The new LDX-RTB Premier semi-automatic random case sealer not only offers unmatched flexibility in processing a large range of case sizes and fill levels at high speeds while minimizing downtime but also adds significant risk reduction feature sets that build upon the success of the existing LDX-RTB Standard, Deluxe and Premium models. This latest model features a smart guarding system and holds two National Recognized Testing Laboratory (OSHA NRTL) certifications for its electronic components, assuring manufacturers of a dependable solution for their production needs. “We developed the LDX-RTB Premier in response to customer needs for a versatile and fast case sealer capable of keeping up with the wide variance of both case dimensions and void levels commonly experienced in e-commerce applications,” says Drew Wenrich, Case Equipment Sales and Product Manager at Signode. “Before installation, we’ll do a customer consultation along with proof-of-concept demos and, where required, extensive factory acceptance with real-world transit testing. Following this procedure not only optimizes the performance of the equipment but also helps build our customers’ confidence in their investment.” With belt speeds of up to 155 feet per minute, the LDX-RTB Premier case sealer is particularly valuable in fast-paced environments like e-commerce and retail. The correlating CaseLocker™ series tape cartridges each feature a patented locking knife guard system, and offer pinch point prevention, pneumatic assist for high-speed operation, and a simplified threading path for tape loading. The LDX-RTB Premier will be on display at the Signode booth (B1411) at MODEX 2024 in Atlanta with opportunities to experience the machine’s capabilities firsthand.
LG unveils new automated warehouse robots at MODEX 2024
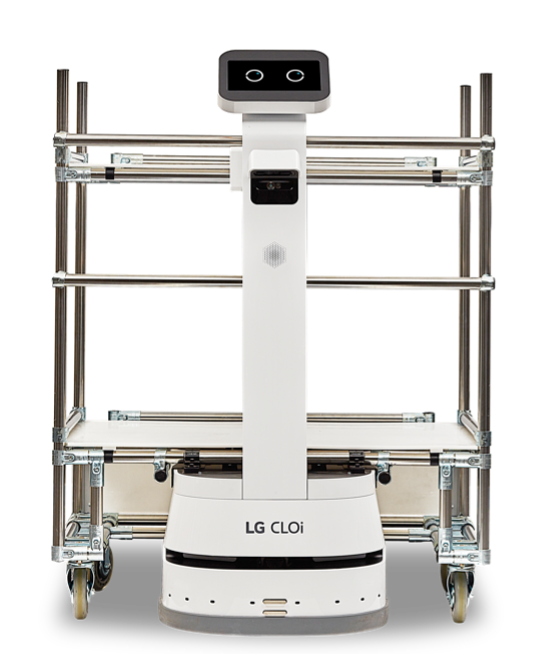
New LG CLOi ‘CarryBot’® launching at MODEX 2024 to provide fast, intelligent point-to-point delivery, reduce strain on warehouse workers LG Business Solutions USA aims to set a new standard for warehouse efficiency and flexibility with the new LG CLOi CarryBot® family of autonomous mobile robots (AMRs) designed to intelligently navigate complex floor plans to move and deliver payloads in customizable configurations, with loading and unloading performed by workers. LG CLOi CarryBot will be officially launched in the United States at the MODEX 2024 trade show, March 11-14 in Atlanta. LG’s booth (A11918) in the Georgia World Congress Center also will preview LG’s P5G, the company’s private 5G technology under development for dedicated robot networks supporting reliable, stable performance. Development of the new LG P5G network is leveraging the vast technical resources and deep expertise of global innovator LG Electronics. “The new LG CLOi CarryBot can immediately begin solving warehouse inefficiencies by providing on-time movements and consistent, reliable operation that allows workers to stay within their zones and increase productivity,” said Tom Bingham, Senior Director, LG Business Solutions USA. “CLOi CarryBot offers seamless package movement and delivery within a warehouse and eliminates the need for workers to physically transport packages.” Having already launched autonomous robots that transport products, guide customers, deliver food and beverages, and provide information in commercial settings, LG is now expanding its robotic line to “help provide true solutions for warehouses of any size by reducing lead times and enhancing efficiency,” Bingham explained. Featuring LG’s advanced AMR platform for autonomous navigation, the latest Wi-Fi capabilities, ergonomic hardware design, an intuitive fleet management system, and an efficiency-boosting material control system that optimizes order distribution and scheduling, the LG CLOi CarryBot can streamline product movement and adjust to real-world situations while reducing physical strain on workers. With a top speed of 2.7 miles per hour, a typical runtime of 18.5 hours and autonomous dock charging in 6 hours, LG CLOi CarryBot is a powerhouse for delivering small-to-medium packages across virtually any distance. These powerful hardware capabilities combine with cutting-edge software and machine learning for seamless integration with various facets of Warehouse Management Systems, including material control, fleet management and robot management systems. Interfacing with material control systems enables smart order grouping, picking item categorization, order information distribution, and total picking cooperation support including notations of shortages or skipped items. Fleet management system integration provides path-planning for multi-AMR users, intelligent AMR fleet navigation and prioritization, traffic balancing and detouring, obstacle avoidance, and automated return for dock charging. On the backend, the robot management system provides managers instant access to location info, AMR status, alerts for abnormal interactions, and statistical data to support decision-making. The Mounting Type CLOi CarryBot features two shelves that are 30 inches wide and 16.5 inches deep, making it ideal for smaller package needs or use in tight spaces. It features a convenient front-facing 9.2-inch touchscreen and an integrated holder for barcode scanners, making inventory tracking and verification easier than ever. The Rolltainer Type CLOi CarryBot combines the autonomous abilities of CLOi CarryBot with the large platform of a traditional rolling container, offering enhanced payload capacity through the use of two shelves that can accommodate packages up to 29 inches wide and 19 inches deep. The 9.2-inch touchscreen is rear-mounted for easy accessibility. “LG CLOi robots have already proven their navigation and automation prowess in a variety of industries and environments, and now warehouse owners and managers can shift their operations to more automated routines to improve efficiency and enhance daily productivity,” Bingham said. The LG CLOi CarryBot can be programmed for virtually any floor plan with practically unlimited pickup and delivery points, enabling precise navigation, multi-point deliveries, and AI-enhanced decision-making that streamlines deliveries when multiple AMRs are servicing a single zone. At the end of its “shift,” or when power is low, the LG CLOi CarryBot can automatically return to a designated multi-AMR charging dock.
Emerson’s new flow meter solution for challenging applications
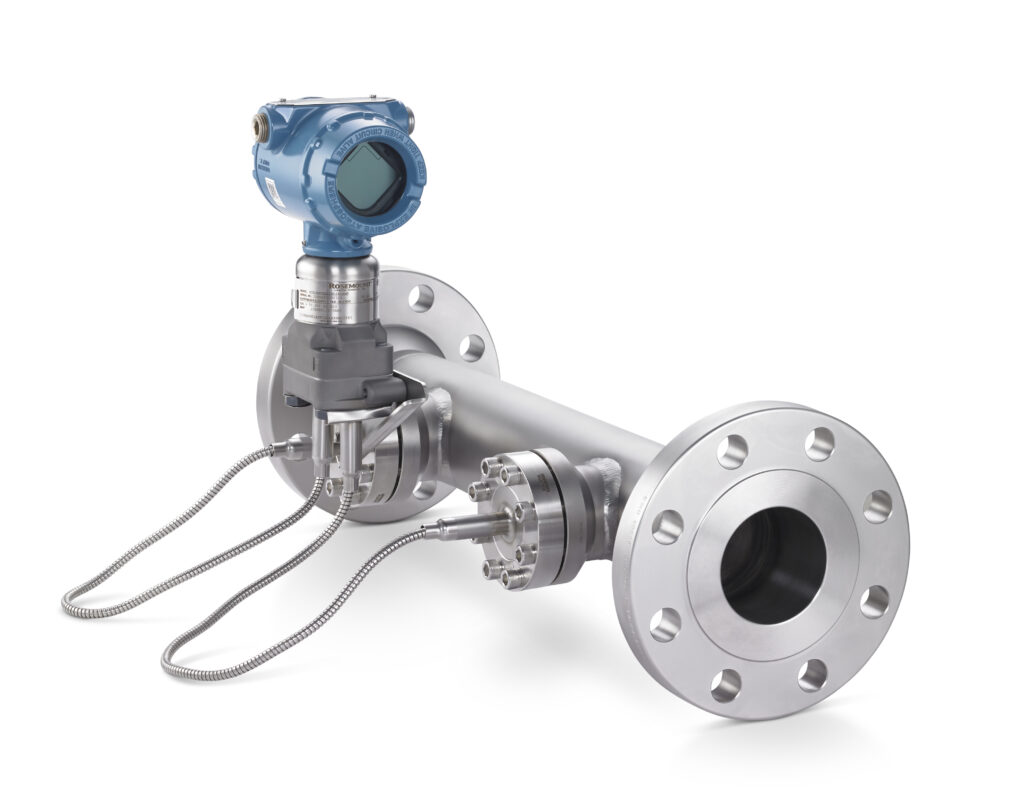
Rosemount 9195 Wedge Flow Meter optimizes performance in applications with high-temperature, high-viscosity, or abrasive liquids, while reducing lifecycle costs Emerson has released the Rosemount™ 9195 Wedge Flow Meter, a fully integrated solution consisting of a wedge primary sensor element, supporting components, and a selectable Rosemount pressure transmitter. The new meter’s unique flexible design is ideal for measuring process fluids with a wide range of demanding characteristics in various heavy industry applications, including metals and mining, oil and gas, renewable fuels, chemicals and petrochemicals, pulp and paper, and others. It can be very difficult to measure volumetric flow accurately and reliably in applications where the process liquid is highly viscous, extremely abrasive, prone to plugging, at high temperatures, or a combination of these conditions. In applications with low ambient temperatures, hot process media, or a combination of both, heat tracing is often required, necessitating a supply of electrical power, and creating a maintenance-intensive single point of failure. The Rosemount 9195 Wedge Flow Meter addresses these and other common measurement challenges with its unique design. The wedge element itself has no small passages that could plug due to entrained particles, and it is abrasion-resistant due to the shallow approach angle of the process liquid and the lack of critical sharp edges. Highly viscous liquids are measured accurately due to the linear response of the meter, even at low Reynolds numbers. The sensor’s operating temperature range is -40 to 1,000 degrees Fahrenheit (-40 to 538 degrees Celsius), and the meter is available with Emerson’s Rosemount 3051S Thermal Range Expander for measuring hot or viscous liquids, without the need for heat tracing. “The Rosemount 9195 offers a fully assembled design for accurate measurement of liquids that wear or plug other meters,” said David Wright, global product manager for Emerson’s measurement solutions business. “This new design solves a range of difficult customer problems by integrating innovative features into a trusted technology.” Two-way digital connections from the selected pressure transmitter to a host, such as a distributed control or an asset management system, can be made via 4-20 mA HART®, WirelessHART®, FOUNDATION™ Fieldbus, Modbus®, or BSAP/MVS. Depending on the selected transmitter, a wide range of process variables can be sent to host systems for process control and monitoring, diagnostics, and other purposes. Application flexibility is provided with three sensor/transmitter connection styles: Compact: Reduces pipe standoff to address plugging and cleaning concerns. Saddle-style remote seal connection reduces the weight of the meter by 50%. Flanged: Incorporates a 2-inch NPS/DN50 connection. This traditional style is used if flushing rings and valve assemblies are required. Threaded: Incorporates an ½ inch NPT connection with tubing, ideal for applications where plugging is less of a concern than erosion or wear. To simplify ordering and ensure the correct remote seal system is specified, five optional application packages—including standard, abrasive, ultra-high process temperature, cold environment, and remote mount—are available for the sensor element. Available line sizes for the sensor are 2-inch to 8-inch (50 to 200 millimeters). All wetted materials are 316L stainless steel, and the meter complies with ASME B31.3 and CRN safety standards. Additional materials and sizes can be accommodated upon request.
Federal Railroad Administration 2023 data affirms rail’s strong safety record
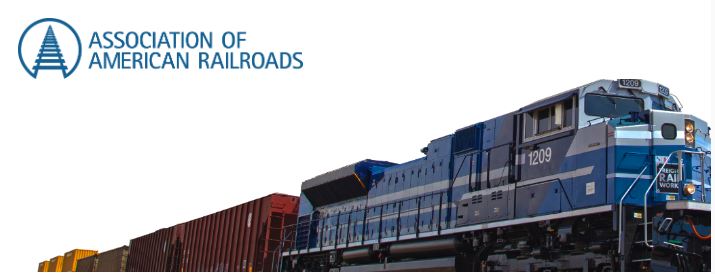
Newly released data from the Federal Railroad Administration (FRA) has confirmed that the industry’s safety-centered approach to investments and operations delivers overall improvements that have made the last decade the safest ever for rail. Specifically, these strong, unrelenting efforts have driven the train accident rate down 27% since 2000 and 6% since 2022. Notable employee safety statistics include: For all railroads, on-duty fatalities declined 71% since 2000 and reached an all-time low in 2023. For Class I railroad employees, the rate of injuries and fatalities has dropped by 63% since 2000 reaching an all-time low in 2023. Analysis of 2023 FRA Data per million train miles indicates: For all railroads, the derailment rates have dropped 30% since 2000. Per carload, the hazardous materials (hazmat) accident rate is at its lowest ever and down 75% since 2000 based on preliminary data. Class I railroads’ mainline accident rate is down 42% since 2000 but increased slightly compared to 2022. Class I railroads decreased yard accident rate per million-yard switching miles by 11%, reversing last year’ increase. “Our highly skilled workforce, uncompromising safety culture, and sustained investments delivered strong safety results across the industry in 2023,” said AAR President and CEO Ian Jefferies. “Our commitment to enhancing safety never ends, with railroads taking meaningful action to meet the challenge.” Railroads’ durable safety record is built and maintained by the industry’s unmatched private investments, commitment to continuous improvement and the expertise of its workforce. In a new white paper, AAR outlined how railroads are taking decisive, meaningful steps to build a safer future. Among other things, the paper examines how carriers employ a multi-faceted strategy to safeguard its workforce and the public by addressing and mitigating the leading causes of accidents – infrastructure or track defects, equipment malfunctions, and human error. Year-over-year human error and equipment-caused accident rates both improved, decreasing 18% and 31% respectively since 2000. Although the track-caused rate increased slightly since 2022 underscoring the need for continued action, it remains down 50% since 2000. “While there remain areas for improvement, both 2023 and the historical trendline demonstrate the railroads’ tireless pursuit of further safety gains and their success in achieving tangible results,” said Jefferies. “Across the nation, railroads are putting the right training, people, and technology in place to keep a watchful eye and prevent accidents before they happen. Actions driven by this culture of vigilance will continue to drive sustained results into the future.” As outlined in the white paper, railroads are expanding their use of advanced technologies to monitor the health of cars, locomotives, and track in real-time, while also investing significantly in maintenance and upgrades. These advanced technologies help railroads keep tabs on equipment while in use, enabling proactive steps to fix issues early. Work continues to implement concrete, voluntary safety commitments made in 2023 to enhance railroads’ ability to detect certain equipment defects and act before they result in an accident. More than 95% of all rail-related injuries and fatalities are attributable to trespassers and grade-crossing users. In 2023, grade crossing collision rates declined slightly year over year and were down 25% compared to 2000. As of March 1st, trespassing fatalities in 2023 are up 22% compared to the year prior. Traditionally, the number of trespassing deaths calculated for a particular year declines during the next year as many of those incidents are reclassified as suicides. These preventable accidents remain persistent challenges across the national rail network. Ultimately, railroads, rail employees, policymakers, and the public share the same goal of making the rail network even safer. Railroads continue to lead with actions that enhance safety and stand ready to partner with policymakers to advance measures that encourage the adoption and expansion of both new and existing technologies. The paper outlined how federal officials can support a forward-looking framework that builds on successes and keeps the door open to future rail safety innovations.
Numina Group and Weber packaging announce partnership
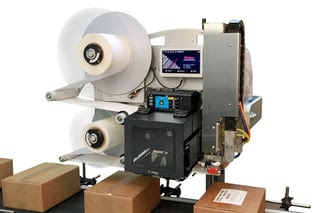
Numina Group’s alliance with Weber Packaging Solutions enhances its mission to offer fully integrated, end-to-end, top-tier warehouse automation solutions that automate the entire pick, pack, and ship order fulfillment operation. Numina Group brings decades of experience implementing software-driven warehouse automation solutions that incorporate Weber’s full family of state-of-the-art print and apply labeling automation technologies. Numina Group, an independent warehouse automation integration firm with over 1000 print and apply labeling solutions throughout North America. By allying with Weber Packaging, Numina enhances its market offering to include Weber’s state-of-the-art print and apply labeling solutions. Weber Packaging Solutions’ sales and distribution channel now has access to a software-driven, fully designed, and integrated SLAM labeling solution (scan, label, apply and manifest) for their manufacturing and warehousing customers. The two companies are leveraging their vast combined experience in automated packaging to deliver a new level of customer confidence, reliability, and speed. “This partnership will bring together some of the industry’s most experienced packaging professionals to design complex packaging solutions. Weber and Numina will help customers streamline their operations, boost efficiency, and improve customer satisfaction,” said Harrison Chien, Vice President of Sales and Marketing at Weber. Numina Group has already started integrating Weber Packaging’s latest generation print-and-apply line of applicators into Numina’s RDS labeling automation module. The RDS labeling automation module supports “labeling tunnels” ranging from two to six applicators to automatically apply packing slips, carton content labels, and retailer compliance labels required by Amazon, Walmart, and other retailers. Dan Hanrahan, founder, and CEO of Numina Group stated, “We’re excited about this partnership with Weber Packaging, a well-respected company with over ninety years of experience in all aspects of label application and manufacturing technology.” He added, “Weber Packaging’s solutions are renowned for their quality, and their print-and-apply technology offers the flexibility we need to continue providing the right technologies for end-of-line warehouse automation solutions that meet or exceed our customers’ requirements.” As an independent systems integrator, Numina Group evaluates, selects, and integrates the right blend of warehouse automation and material handling technologies to automate the entire order fulfillment operation. Numina Group’s warehouse automation platform automates everything from order release to picking, packing, and shipping. Numina works with companies in diverse industries, requiring flexible and reliable automation. “Our experience with Weber Packaging to date makes it clear the company’s products and support organization are a perfect match with Numina’s culture of excellence,” stated Hanrahan. Both Numina Group and Weber Packaging Solutions are customer-centric organizations and are always excited to provide the latest technology to their customers.
Hyster to supply 10 zero-emission battery electric terminal tractors to APM Terminals
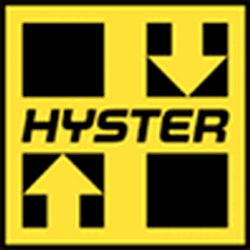
Hyster Company announced an agreement to provide APM Terminals with 10 battery-powered terminal tractors for their location at the Port of Mobile in Alabama. The electric terminal tractors, which are scheduled to be delivered in 2024, are part of a $60 million investment in port equipment electrification pilots by APM Terminals. “We have made an industry-leading commitment to be net zero across scopes one, two, and three by 2040,” says Jelle Burger, Program Lead for Electrification Pilots, APM Terminals. “Decarbonizing our container handling equipment is a critical component of our progress towards those targets. Hyster has been a trusted resource for container handling equipment, and our collaboration will help us to expand this global effort with the first Hyster electric terminal tractors in North America.” The electric terminal tractors are designed to provide a zero-emission option to help the terminal, and other port and distribution operations, achieve clean energy targets while maintaining diesel-like performance levels. Each tractor will be powered by a 260-kilowatt-hour lithium-ion battery, which is expected to provide about 9.5 hours of continuous run time on a full charge. “We are seeing a clear demand for zero-emission port equipment, including terminal tractor options. Our long history of electrifying forklifts and our ground-breaking work to electrify container handling equipment positions us to bring expertise and learnings to terminal tractors, so we are stepping in to deliver,” says Niek Willems, Manager, Big Truck Global Accounts, Hyster. “In doing so, we are reinforcing our commitment to provide clean power choices that allow businesses pursuing emission reductions to access the solution that is most effective and appropriate for their unique application, without compromise.” The terminal tractors will operate as a gang, serving as a ship-to-shore crane at APM Terminals Mobile, a world-class, high-productivity terminal connecting sea, road, and rail from the U.S. Gulf Coast. As the crane unloads containers from the ship, the tractors will transport laden and unladen containers between the crane and the yard. Each tractor has an 182,000-pound gross combined weight rating. The electric terminal tractors, which Hyster has worked with Capacity Trucks to develop and will be built in Texas, represent one of several clean power-focused port equipment projects that the company is engaged in.
Key takeaways from the fourth quarter Plastics machinery shipment
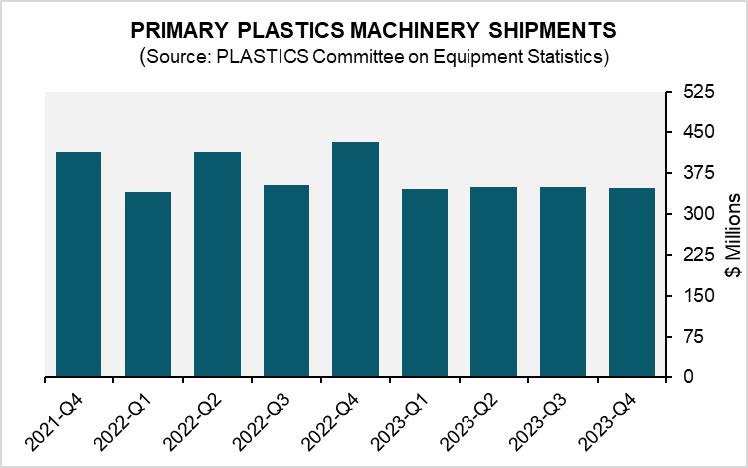
The Plastics Industry Association’s Committee on Equipment Statistics (CES) has unveiled the fourth-quarter shipment data for primary plastics machinery, covering injection molding and extrusion activities in North America. Initial estimates for Q4 2023 indicate a shipment value of $348.1 million, reflecting a 0.4% decrease from the revised figure of $349.6 million in the preceding quarter. When compared to the same period in the previous year, the value of shipments shows a notable 19.5% decrease. In the domain of primary plastics machinery, single-screw extruders experienced a notable 19.5% decrease in quarter-over-quarter (Q/Q) analysis but showed a 4.9% increase year-over-year (Y/Y). Twin-screw extruders also witnessed a comparable decrease of 19.4% Q/Q and a more substantial 23.8% decrease Y/Y. Conversely, injection molding shipments increased by 3.8% Q/Q but faced a 21.1% decrease Y/Y. “Last year saw minimal fluctuations in quarterly plastics machinery shipments. The modest upturn observed in the second quarter was short-lived, with shipments remaining steady until the year’s end,” noted Perc Pineda, Chief Economist at PLASTICS. “The decline in U.S. manufacturing activity, coupled with a high-interest-rate environment, contributed to a slowdown in business investment spending, including in plastics machinery,” Pineda added. In the latest quarterly survey by CES polling plastics machinery suppliers for market insights and equipment expectations, results showed a notable uptick in participants anticipating improved market conditions over the next twelve months compared to the previous year. The percentage of those expecting conditions to either remain the same or improve rose to 82.9%, signaling optimism compared to the 56.1% recorded in the prior quarter. As 2023 concluded, U.S. exports of plastics equipment saw a 5.1% increase in the fourth quarter, reaching $284.6 million from the previous quarter. Year-over-year exports surged by 19.6%. Mexico and Canada maintained their positions as the top export markets for U.S. plastics equipment, accounting for a combined export share of 62.3%. Half of these exports, totaling $124.3 million, were directed to Mexico, while less than a fifth (18.6%) to total exports went to Canada, totaling $53.0 million. Meanwhile, imports experienced an 11.7% quarter-over-quarter increase, reaching $427.6 million, but faced a 14.1% year-over-year decrease. “While the unexpected 2.5% U.S. economic growth in 2023 averted a recession, primarily fueled by robust household spending in the services sector, signs of recovery may emerge in 2024. Sustained consumer spending could prevent economic deterioration, especially if labor markets continue to stay healthy. As interest rates begin to return to normalcy from inversion, there’s a likelihood that business investment, including in equipment, will reverse course,” remarked Pineda.
Diversified Fall Protection names industry Veteran Travis Nelson as New CEO
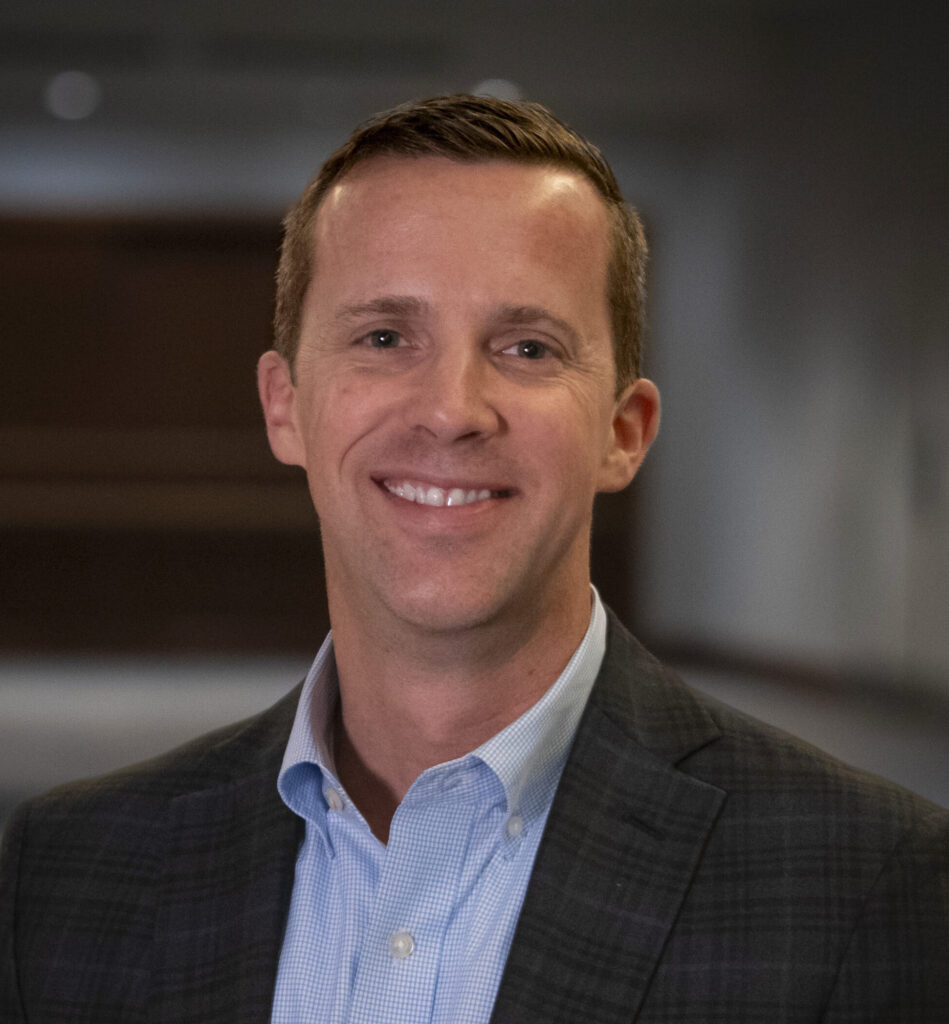
Diversified Fall Protection (DFP), a fall protection integrator in the U.S. for regulatory-driven systems and services, has announced the appointment of Travis Nelson, PE, CSP as the company’s new CEO. Nelson is a distinguished leader and influencer in the fall protection industry and brings over 20 years of industry experience to the position. “We are truly honored to have someone of Travis’ reputation and expertise at the helm of our company,” said William Huber, chairman of the DFP Board and partner with North Branch Capital, which invested in DFP in May of 2019. “His industry knowledge, visionary leadership, and ability to unite teams toward a shared vision are precisely what DFP needs to solidify its position as an industry leader.” Nelson’s journey with DFP began in 2019, initially as Vice President of Engineering and later as Vice President of Strategy. His tenure at DFP commenced after the acquisition of PEAK Fall Protection, where Nelson served as managing partner and president for nearly 12 years. “I am thrilled about the opportunities that this appointment presents,” said Nelson. “DFP is truly exceptional, primed for remarkable growth and success. With a team of exceptionally dedicated and talented individuals, possessing the requisite expertise and commitment, we are poised to elevate our service standards and foster innovation. Our industry is not just compelling; it’s critical because we ensure that workers return home safely every evening.” Established in 1994, DFP currently employs over 300 professionals across six U.S. locations. The company has experienced exponential growth, quadrupling in size since 2019, propelled in part by four strategic acquisitions between late 2019 and 2021 (PEAK Fall Protection, Fall Protection Services (FPS), Rooftop Anchor, and Versatile Systems, Inc.). Since 2021, DFP has achieved a remarkable 30% growth rate. DFP specializes in partnering with strategic clients as their trusted advisor, assessing fall protection concerns within their portfolio, identifying risks, and delivering programmatic recommendations. DFP services encompass the implementation of engineered solutions, alongside ongoing inspection and certification, ensuring compliance and safety.
Advance Lifts highlights its MSL Multi Stage Scissors Lift Tables for the food processing industry
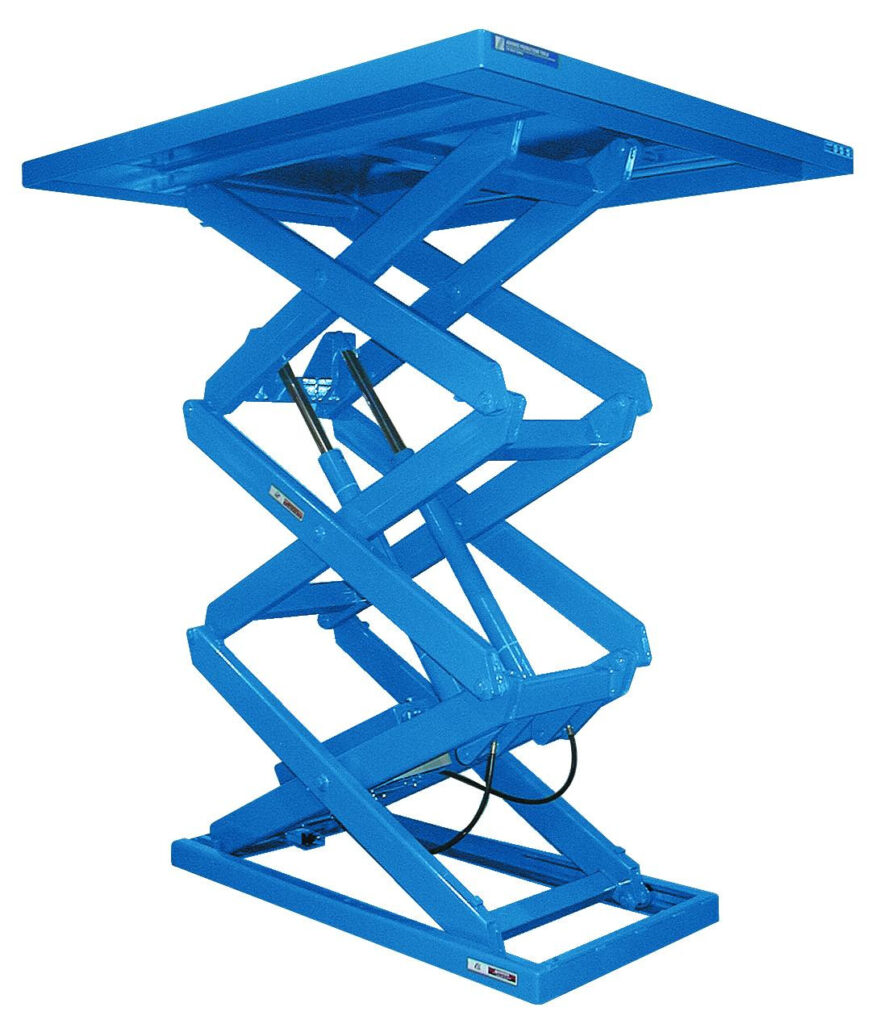
Durable Lift for travel food processing applications with limited available platform length Advance Lifts, a North American manufacturer of industrial scissor lift tables and dock lifts, highlights its MSL Multi Stage Scissors Lift Tables, extremely durable lifts requiring both high vertical travel and compact platform lengths, a combination that is not possible with single scissor designs for applications in the food processing industry. The MSL Series hydraulic lifting platforms are constructed with superior quality, ensuring durability and minimal lifecycle costs while extending their lifespan. Advance Lift’s patented “Platform Centering Devices” double or triple the lift life. The MSL Series lifts are available in a wide range of capacities and sizes, all designed for durability, and cost-efficiency. The lighter capacity units feature solid steel legs, providing a more compact and cost-effective design. Meanwhile, the larger capacity units are constructed with structural tubing legs to enhance rigidity, reduce weight, and optimize costs. Quality is evident throughout the entire system. The cylinders are machine-grade and feature clear plastic return lines, enhancing quality, longevity, and reliability. Pressure hoses are double-wire braided with JIC fittings. To withstand temperature variations, the MSL Series lifts use mild steel reservoirs instead of the plastic often found in competitor systems. The entire system is completely primed and finished with baked enamel. The MSL Series comes in 36 models, with a wide range of sizes, speeds, and load capacities, with vertical travel options ranging from 48″ to 144″, platform sizes up to 66×98 or 54×104, and load capacities of up to 12,000 lbs. Custom sizes are available to fit your specific food processing needs. All the controllers are Underwriter Laboratory-listed assemblies. Advance Lifts hydraulic lifting platforms conform to all applicable ANSI codes.
Movu Robotics and Equipment Depot, Inc. forge alliance to upgrade U.S. Warehouses with seamless plug-and-play solutions
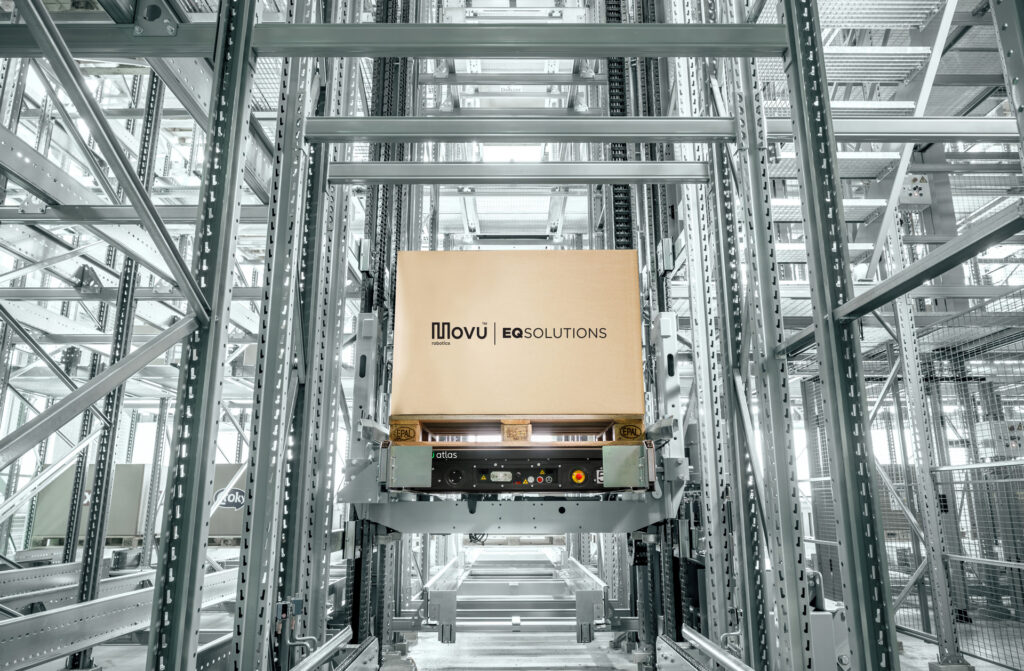
Movu Robotics, a global designing, manufacturing, and implementing advanced storage solutions and automated warehouse systems, has announced a strategic partnership with EQSolutions, the systems integration division of Equipment Depot, America’s largest independently operated material handling and equipment rental source. This partnership between Movu Robotics and EQSolutions marks a significant step forward in leveraging advanced technology to address the evolving needs and challenges businesses face in logistics and warehousing. Combining Movu’s accessible robotic solutions for easier automation and EQSolutions’ expertise in integration, the collaboration aims to deliver comprehensive, tailored solutions and professional services that enhance efficiency, productivity, and sustainability for clients across the U.S. EQSolutions specializes in engineering transformative warehouse and automation solutions for manufacturing, warehousing, and distribution facilities, providing a one-source solution to solving a variety of industry challenges. “This collaboration perfectly marries Equipment Depot’s long-standing reputation for providing industry-leading material handling equipment with Movu’s innovative ‘plug and play’ automation technologies,” says Marc Terwilliger, VP of EQSolutions. “Together, we are setting new standards in warehouse efficiency by providing a competitive edge to businesses looking to leverage integrated warehouse solutions and modern innovation.” Movu Robotics shares the excitement of this partnership. “At Movu Robotics, we are committed to pushing the boundaries of robotics technology to solve real-world challenges. Our solutions are designed to make warehouse automation and robotics not only more accessible but also more scalable. Teaming up with EQSolutions allows us to amplify our impact and deliver accessible plug-and-play robotics solutions with an expert end-to-end full-service integration. By harnessing both organizations’ collective expertise, resources, and capabilities, the partnership aims to drive progress and unlock new opportunities in logistics and warehousing with the power of easier automation.” said Stefan Pieters, CEO of Movu.
The Women In Trucking Association names 2024-2025 Board of Directors
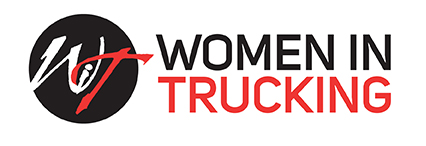
The Women In Trucking Association (WIT) has announced its 2024-2025 board of directors, which were elected during WIT’s annual meeting last month in Dallas, TX. The role of WIT’s board of directors is to provide strategic guidance in the association’s mission to encourage the employment of women in the industry, minimize obstacles they face, and promote their accomplishments. Newly elected WIT officers are: chair Kary Schaefer, chief engineer of cab, entire vehicle & DT Mexico engineering, Daimler Trucks North America; vice chair Sarah Smith, senior vice president of human resources, Penske Transportation Solutions; treasurer Jim Taber, national accounts manager, Arrow Truck Sales; and secretary Lori Taylor, director carrier administration, C.H. Robinson. Ingrid Brown, an owner-operator with Rollin B LLC, is a newly elected board member. Directors continuing their terms on the WIT board are: Pierluigi Cumo, vice president of marketing North America with Michelin; Domenica Farmer, area vice president with WM; LaTres Jarrett, executive director of commercial sales with Bridgestone Canada; Lesley Kerr, vice president of human resources with Ryder System; Jennifer Macalaguin, vice president of engineering with Navistar; Ryan McDaniel, senior vice president of supply chain with Walmart; Trina Norman, SoCal division manager with UPS; Jennifer Plumlee, vice president of transportation with J.B. Hunt Transport Services; Laura Roan Hays, regional sales manager with Great Dane; Michele Rodgers, engineering section manager with Peterbilt Motors Co.; and Bonnie Voldeng, vice president freight marketing with FedEx Freight Direct. “It’s a privilege to announce and welcome the 2024-2025 WIT board of directors,” said Jennifer Hedrick, president and CEO of WIT. This talented group of leaders is committed to advancing the mission of WIT and driving both WIT and the industry forward.
The hidden costs of industrial printing and how to reduce them
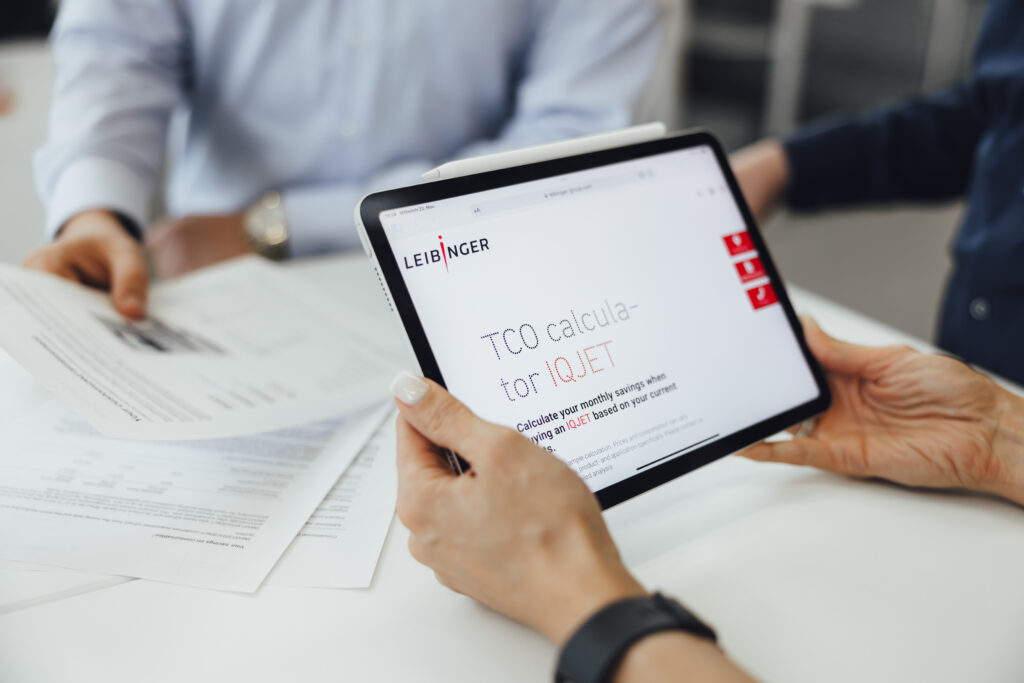
Identify hidden costs in two minutes with the total-cost-of-ownership-calculator How much do the printers you use on your production line cost? What we mean is, how much do they cost? As the pressure increases on producers and packagers to make their production lines more efficient, we are often asked about how our customers can reduce their printing costs. And the answer we give often surprises them. Here are six ways that your printers cost money and how to reduce your total cost. Not only that – you will also get access to our new TCO calculator, which will give you an actual figure personalized to you and your business. So where is all that money going? 1. Downtime This is the cost that is most often overlooked when talking about coding & marking. Downtime can be created by poor print quality as well as by poor printer performance. Some conventional printers need cleaning between pauses in production. So, the production line sits idle while someone takes the printer through the cleaning cycle. Some printers can take up to 20 minutes to stabilize before they are ready to print again. This delay costs money: according to Senseye’s True Cost of Downtime Report, the cost of a lost hour ranges from USD 39,000 in the FMCG sector to more than USD 2 million in the automotive sector. With LEIBINGER, this is not a cost you need to worry about. The LEIBINGER printer technology keeps unused ink in a 100% airtight system. It doesn’t dry out or clog, production schedules are not held up for cleaning, and no precious production time and money is wasted. High-quality printing results are guaranteed at any time. 2. Maintenance It’s important to keep machines serviced and in good working order, and this can be a significant part of the overall cost unless you have a LEIBINGER IQJET. The IQJET is maintenance-free for five years. This is possible because we use durable, high-quality components and a unique product design that minimizes ‘wear and tear’ (e.g. no need for a continuously running feed pump). And it removes the maintenance cost altogether. In contrast many of the other prominent printing solution providers today seem to lack a crucial focus on minimizing parts and maintenance requirements, as their approach revolves around the wholesale replacement of entire ink core modules, which means the entire hydraulic system, at predetermined time intervals such as annually or biennially. Typically, this process is governed by timeout chips, leading to automatic printer shutdowns when these intervals expire. Consequently, this enforced printer downtime results in production halts for manufacturers. This approach not only lacks sustainability but also incurs exorbitant costs. We are not merely referring to the substantial expenses incurred in replacing ink core modules, which are up to USD 1.500 per year; Downtime costs, in terms of lost production, are equally significant. Therefore, the query regarding maintenance and spare parts policies should be one of the primary questions to ask your coding and printing solutions provider, as it can constitute a significant long-term cost factor. 3. Labor Given the current labor shortage, it is particularly important to consider the time cost of people. How long do operators spend setting up or cleaning printers? Or re-programming them between jobs? What is the expected timeframe for commissioning and installation at the facility? Printers that are easy to install, manage, configure, and with remote control options. For example, staff don’t have to walk miles around the plant to operate them will cost less in the long run. Such features are included in LEIBINGER printers. The Plug & Print performance of IQJET is unparalleled in the global market. The drag-and-drop interface and the simplest print job creation process are not only effortless but also highly intuitive, and no extensive training of employees is required. 4. The purchase price The most obvious cost of printing is the upfront cost of equipment, although this is typically less than 30% of the total costs. As with everything, a high-quality, reliable brand will cost more than a cheaper one. And of course, printers cost more if they go faster or provide more features – so the best way to economize is to ensure you don’t pay for features or speeds that you don’t need. In the long term, the best bet is a reputable supplier with a wide range so you can find a price point that suits you. 5. Consumables Reduce the amount of ink and solvent you use, and reduce your costs.Not all printers perform equally. LEIBINGERs latest printers have one of the lowest consumption ratings on the market, 2.7 ml per hour of solvent for MEK inks (competing products typically consume between 6 and 10 ml per hour), and we make sure that ink cartridges are emptied down to the last drop and do not require separate disposal (unlike many conventional CIJ systems). So, you pay less for your consumables. 6. Power Energy prices remain high, so the power required to run your printers is an important factor. Not only does it cost money, but it also contributes to your organization’s carbon footprint. Choose equipment with a low wattage rating, such as our new IQJET: drawing only 36W it costs less than any other printer to run. Show me the money! While it is useful to know the different ways that your printers cost money, you need to see the numbers. You need to know exactly how much you’re paying and how much could you save. And with our online Total Cost of Ownership Calculator, you can have those numbers in about two minutes. Check out the Total Cost of Ownership Calculator now. About the Author: About Paul Leibinger GmbH & Co. KG (LEIBINGER) LEIBINGER is a globally operating specialist in coding & marking systems with headquarters in Tuttlingen, Baden-Württemberg (Germany). The third-generation family-run company, founded in 1948, develops and produces industrial inkjet printers as well as inks for various applications – with a workforce of close to 300. Innovative technologies and an
GRI launches its NEXT GENERATION sustainable tires at the GREEN IMPACT 2024
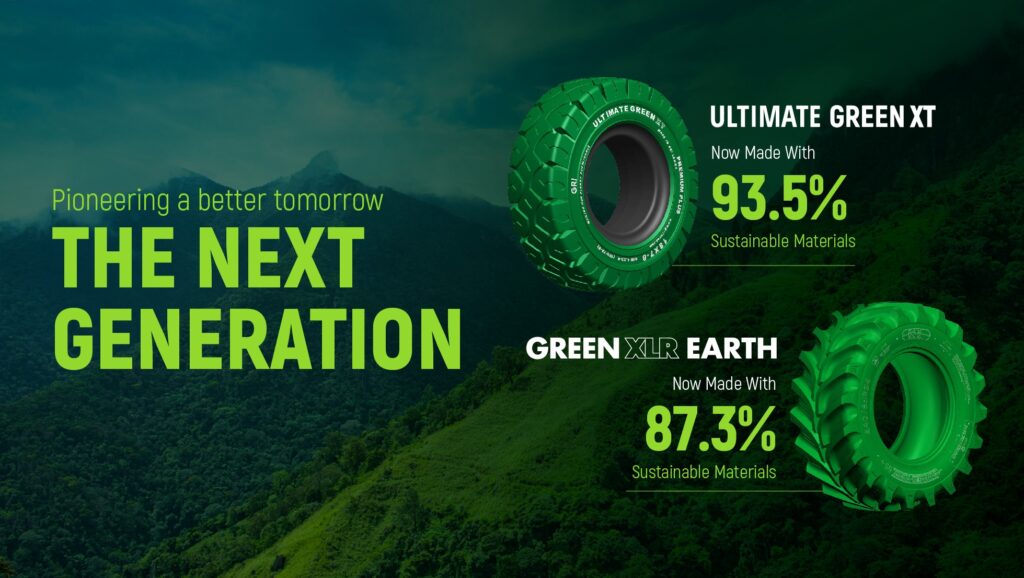
GRI, a producer of specialty tires for agriculture, material handling, and construction machines, unveiled its NEXT GENERATION of environmentally friendly specialty tires with very high sustainable material content. GRI’s sustainable agriculture tire range, the GREEN XLR EARTH series, now comes with 87.3% sustainable material whilst the ULTIMATE GREEN XT the sustainable material handling tire boasts an impressive 93.5% sustainable material. These NEXT GENERATION tires embody GRI’s vision of moving humanity towards making a positive impact on our planet and dedication to reducing its environmental footprint while delivering high-performance specialty tire solutions. Leveraging innovative technology and advanced natural rubber compounds, GRI continues to lead the way in sustainability across its entire value chain. This significant product launch took place at The GREEN IMPACT 2024 in Sri Lanka, an event that brought together industry professionals and key media personnel from across the globe. Spanning across 3 days, The GREEN IMPACT marked a significant milestone in GRI’s sustainability journey, reaffirming its commitment to environmental stewardship and innovation in Specialty Tire technology. Bureau Veritas, a business-to-business service provider in the field of testing, inspection, and certification, validated GRI’s commitment to environmental responsibility by attesting to the carbon footprint reduction of the environmentally friendly, “green” specialty tires. “This certification underscores GRI’s unwavering dedication to sustainability in tires and quality of product” stated Dr Mahesha Ranasoma, CEO of GRI who presented the products to the attendees. Mr. Prabhash Subasinghe, Managing Director of GRI remarked, “The NEXT GENERATION of GRI’s green tires are more than just products; they are symbols of our unwavering dedication to sustainability. With the highest percentage of sustainable materials, these Agriculture and Material Handling tires represent a beacon of hope for a greener tomorrow. From its conception to its production, every aspect has been meticulously crafted to minimize environmental impact without compromising on performance.” With the introduction of the NEXT GENERATION of environmentally friendly Specialty Tires, GRI continues to drive sustainable innovation and set new benchmarks in the Specialty Tire industry.
Port of Long Beach hosts open house for engineers
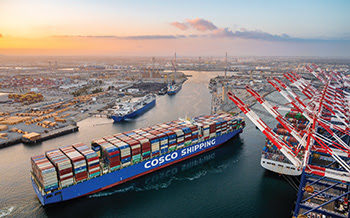
Learn about career opportunities at the March 9 event The Port of Long Beach will host an “Engineering Open House” for engineering professionals and students to find out more about staff career positions offered at the nation’s second-busiest port on Saturday, March 9, from 9 a.m. to 1 p.m. As it builds the Port of the Future, the Port of Long Beach’s Engineering Bureau is looking for established, up and coming, and student engineers who may want to join the Port’s team of in-house engineers who are re-imagining, re-making and maintaining the Port’s physical infrastructure. Opportunities exist in the Port’s Program Management, Construction Management, Design and Project Controls engineering divisions. “We’re planning more than $2 billion worth of capital improvements to the Port over the next 10 years, as we enhance the efficiency, velocity and environmental sustainability of cargo movement,” said Port of Long Beach CEO Mario Cordero. “Our engineers are the ones who will make that happen.” “This is a great opportunity to be part of a diverse, top-notch, award-winning team of professional engineers,” said Long Beach Harbor Commission President Bobby Olvera Jr. “If you’re an engineer and you’ve got the skills, talent and drive, you should join us for the Open House on March 9.” Guests at the Engineering Open House will be able to speak with Port engineers and human resources professionals about joining the POLB team. Opportunities will be available to apply for certain positions at the event. The Open House will be held at the Port of Long Beach Administration building, 415 W. Ocean Blvd., Long Beach, 90802 in the Long Beach Civic Center. Attendees must RSVP at www.polb.com/engineersevent. Those who RSVP will be eligible for free parking.
Green Cubes announces battery pack to power computer cart systems
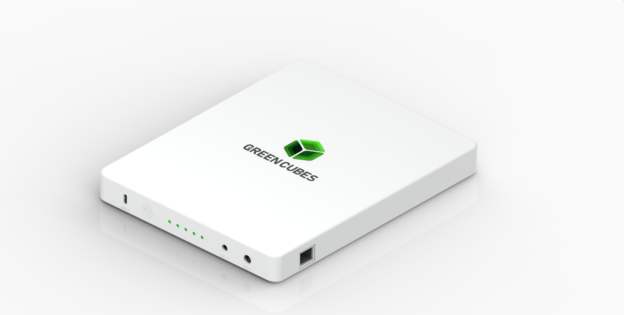
Slim, rugged portable pack is UL-certified to power multiple devices at different voltages with built-in DC adapters. Green Cubes Technology (Green Cubes), the leader in producing lithium-ion power systems that facilitate the electrification of mobile workstations, today announced the Green Cubes Power Bank, a slim, rugged portable battery pack to extend the runtime of laptops and small computer systems. “Powering a laptop or computer system has never been easier using the adjustable DC output from the Power Bank,” said Robin Schneider, Director of Marketing for Green Cubes. “Simply connect any commercial power supply up to 100W with a USB-C connection for dependable, extended power.” With a universal DC output and built-in charger, the Power Bank simplifies running mobile computing platforms for longer with a fully configurable output voltage and 230 Whr capacity rating. “The Power Bank features two independent DC outputs and built-in DC regulators, so multiple devices can be powered at different voltages from the same battery,” said Wayne Pavlovic, Founder and CTO for Simplifi Medical. “We simply program the voltage of the battery to the requirement of our devices, and we can power a monitor and a micro-PC from the same battery pack on our portable medical cart.” The Green Cubes Power Bank is now available for implementation with OEM cart systems.
Movu Robotics and Bastian Solutions partner to bring easier automation to more warehouses globally
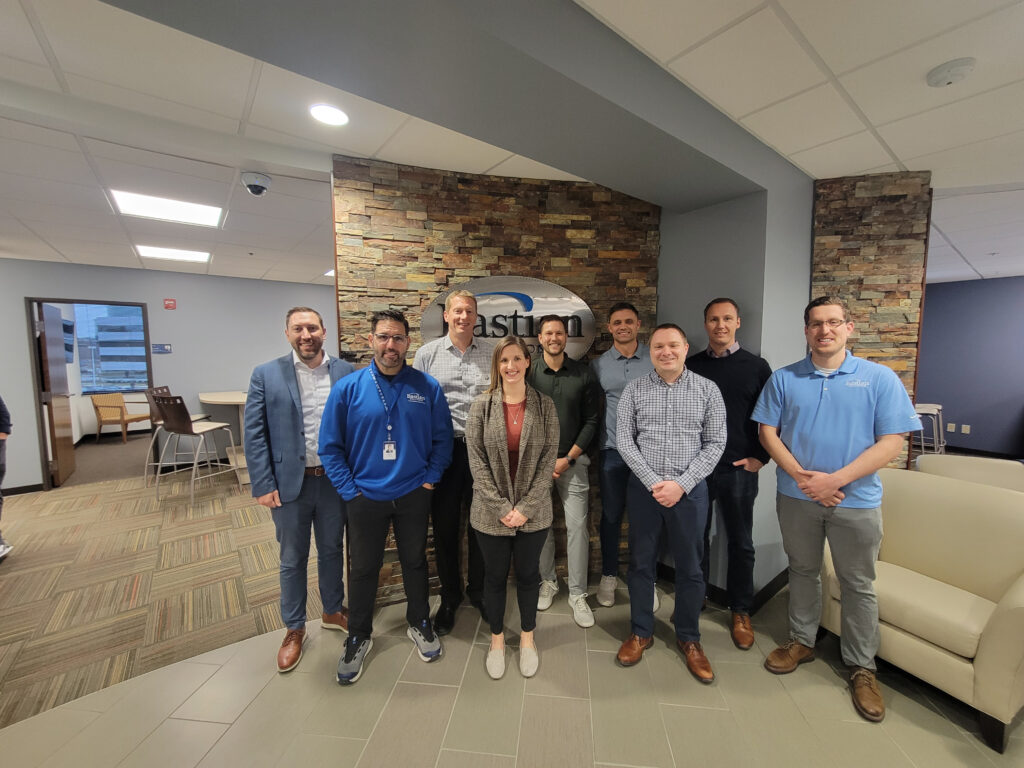
Movu Robotics, a global warehouse automation solution that stands out by bringing easier logistics automation technologies to the world’s warehouses, has announced Bastian Solutions, a Toyota Advanced Logistics company, as its newest systems integration partner. With this move, Bastian can offer customers the benefits of Movu’s portfolio of flexible robotics technologies as part of its global automation solutions, including the North American market. Established in 1952, Bastian Solutions has grown into a global corporation with over 20 US offices as well as international offices in Brazil, Canada, India, and Mexico. In 2017, the company was acquired by Toyota Advanced Logistics, a subsidiary of Japan-based Toyota Industries Corporation (TICO). As a systems integrator, Bastian works to optimize material handling processes, flow, and operational efficiencies to increase productivity, throughput, and order accuracy all while reducing costs, maximizing warehouse space, and minimizing errors. Relying on their years of expertise they work with their customers to analyze their needs, select the ideal equipment for their business objectives, and optimize everything to perform efficiently and work seamlessly. With a philosophy of ‘no warehouse left behind’, Movu Robotics tackles automation with easier, modular, scalable, flexible, and efficient solutions that customers need and helps them to upgrade their warehouses. The Movu portfolio is built around a range of innovative sub-systems, which are designed to provide easier, scalable, flexible, and energy efficient solutions that are accessible for all kinds of warehouses and quick to roll out. The core Movu products integrated by Bastian Solutions include the Movu atlas, a pallet shuttle system for multiple deep storages; and the Movu ifollow Autonomous Mobile Robots (AMRs) for collaborative picking or transport of load carriers such as pallets; as well as the appropriate supporting software. Stefan Pieters, CEO of Movu Robotics, said: “Automated technology offers a productive answer to a multitude of materials handling challenges across many market sectors. These include the need for greater efficiency, flexibility and productivity, while overcoming skills shortages, to fulfil growing volumes as well as handling peaks. Movu Robotics sub-systems are designed with seamless integration in mind, and I am excited that our strategic partnership with Bastian Solutions will bring automated solutions to more customers globally, helping them to meet their challenges and boost their performance, resilience, and service levels.” Bastian Solutions President & CEO Aaron Jones said, “This partnership with Movu marks a significant step forward in offering our customers cutting-edge, innovative unit handling solutions for warehouse automation. Combined with our systems integration expertise, we’re well positioned to enhance efficiency and productivity for pallet distribution and manufacturing facilities worldwide.”
Nearly $147,000 raised in first stage of PTDA Foundation’s Fundraising Campaign
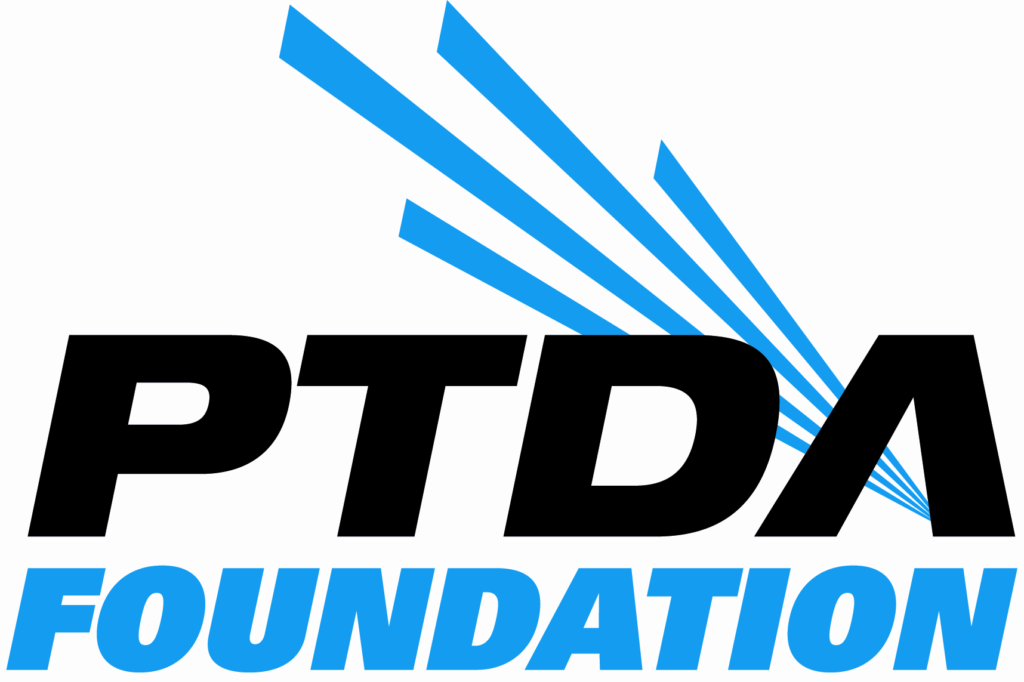
The PTDA Foundation is off to a strong fundraising start in 2024, raising nearly $147,000 during the first three months of its 2024 Fund Drive campaign. Contributions support the PTDA Foundation in empowering PT/MC (power transmission/motion control) industry employers to be more successful in their recruitment and retention efforts. “Our industry plays a crucial role in driving the global economy, and the individuals we bring on board our companies are fundamental to its growth and prosperity,” says 2024 PTDA Foundation President Matt Pavlinsky, Applied Industrial Technologies. “Our employers need help in securing and retaining the best talent and cultivating exceptional teams. This year, as the Foundation prepares to launch new scholarship programs and a bold campaign to raise awareness of careers within our industry, we are grateful to those who demonstrated a commitment to our vision with a pledge to the 2024 Fund Drive. We look forward to sharing more information on these two exciting programs soon.” Thank you to these 2024 PTDA Foundation Vanguard Contributors who led our fundraising efforts with a pledge made October 2023 – January 2024. Partner Contributors ($15,000+) Allied Bearing & Supply, Inc. Investor Contributors ($10,000-$14,999) Applied Industrial Technologies Stakeholder Contributors ($5,000-$9,999) Continental Dodge Industrial DXP Enterprises, Inc. NSK Americas NTN Bearing Corporation of America WEG Benefactor Contributors ($2,500-$4,999) BDI Americas (USA & Canada) Bearing Service Inc. Flexco Houston Bearing & Supply Co., Inc. Interlynx Systems Lafert North America NTN Bearing Corp. of Canada Ltd. Precision Pulley and Idler (PPI) RBC Bearings/Climax Metal Products Renold U.S. Tsubaki Power Transmission LLC (UST) W.C. DuComb Co., Inc. Leadership Contributors ($1,000-$2,499) FICODIS JIE USA Inc. M. B. McKee Co., Inc. Moline Bearing Company PEER Chain Pfannenberg San Antonio Belting & Pulley Company, Inc. Transply, Inc. Webster Industries Foundation Sponsor Contributors ($500-$999) Beardslee Transmission Equipment Co., Inc. Bearing Chain & Supply, Inc. Belden Universal Brewer Machine & Gear Co. Dayco Incorporated Freudenberg-NOK Sealing Technologies Integrated Distribution, Inc. KHK USA Inc. MAXCO Chain MPT Drives, Inc. Orthman Conveying Systems Overly Hautz Motor Base Co. TBC, Inc. Texas Bearing Company USA Roller Chain & Sprockets Colleague Contributors ($250-$499) Royersford Foundry & Machine Co., Inc. Whittet-Higgins Company Individual Contributors Rex Davis Paul Dent Hafeez Hameer Betsy & Alan Haveson Sue & John Masek (in honor of Mary Sue Lyon and in memory of Terry Hutton) Mike & Katie McLain Bill Moore Keith & Sharon Nowak (in memory of Ed Nowak) Matt Pavlinsky Barb Ross Jos Sueters The PTDA Foundation 2024 Fund Drive has a goal of $300,000. To date, the Foundation has raised 49 percent of its goal. Pledges can be made online, or you may download a pledge form at ptworkforce.org/GiveNow.
Trew MODEX 2024: Newest Stingray Shuttle
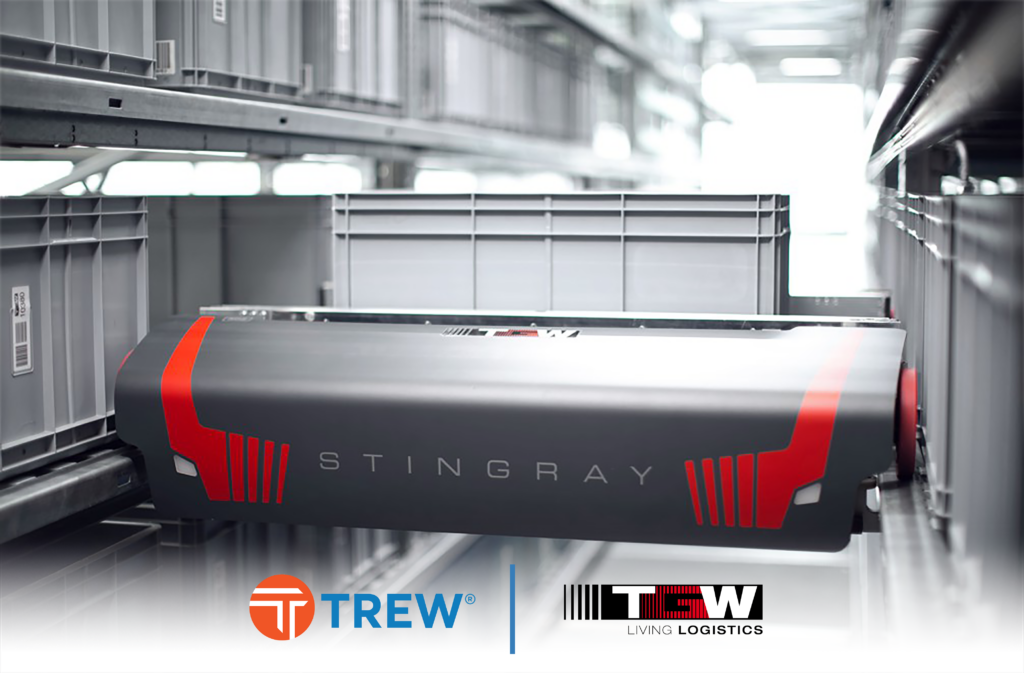
Trew showcases solutions and cooperation with TGW Logistics Trew, LLC, a North American manufacturer of warehouse automation solutions, is debuting the newest TGW Stingray ASRS Shuttle in North America. Trew highlights the new Stingray capabilities and how it integrates with automated material handling solutions in their booth at MODEX 2024 in Atlanta, Georgia, March 11–14. The newest Stingray shuttle system incorporates inventive energy recovery technologies and sustainable material in a design that allows for multi-deep storage and high-capacity throughput. The new shuttle design is highly efficient and reliable and includes new self-healing capabilities. Thanks to intelligent software, autonomous correction of problems and errors, and realigns items to maintain an optimized picking environment, reducing manual intervention by up to 90% compared to other solutions. “Our cooperation with TGW Logistics is another excellent example of how Trew is dedicated to bringing leading ideas and technology to our clients,” said Trew Chief Revenue Officer, John Naylor. “Winning together means enabling our clients to tackle their biggest business challenges with solutions that deliver results.” The Stingray system is a powerful, automated shuttle system for totes and cartons with throughput performances of up to 1,500 load carriers per hour in each aisle. It is a highly flexible, modular system designed for high performance, lower storage location costs, optimized space-saving, and includes integrated maintenance and diagnostic tools. Already proven worldwide with more than 20,000 TGW Stingray shuttles in use, Trew is excited to showcase the technology in North America. To see the shuttle in person at MODEX 2024, visit Trew’s booth #B9632.