CLARK Material Handling employees spread holiday cheer
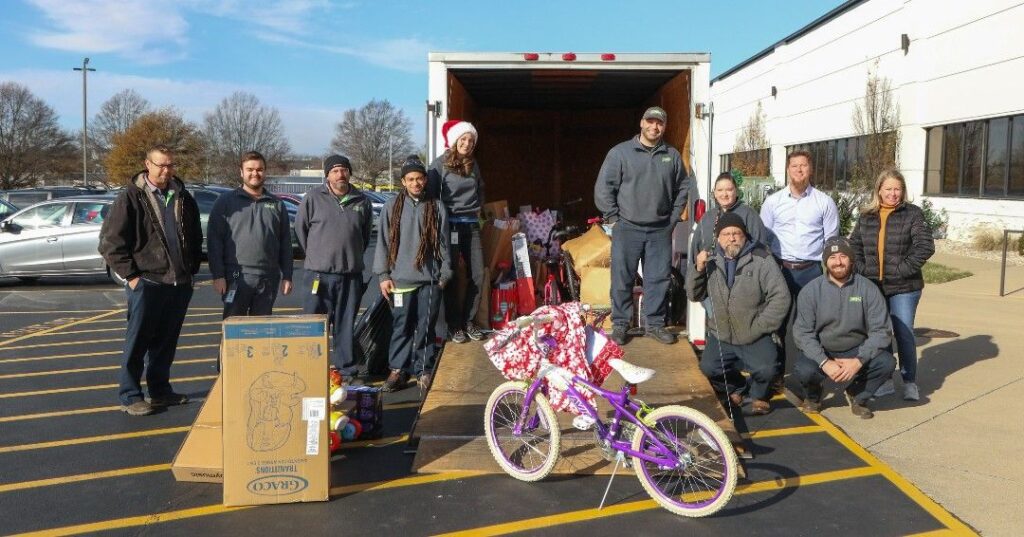
CLARK Material Company employees have been #RaisingHope and spreading Holiday cheer by sponsoring 100 children on the Lexington Salvation Army’s Angel Tree. This year, the need was greater than ever, with over 4,000 kids in need throughout Central Kentucky. As always, CLARK employees showed up for the kids we sponsored, filling the Beast of Burden trailer with presents for every child on our tree. The gifts were delivered to the Salvation Army, and CLARK volunteers will assist in sorting and distributing them next week. And, this year, CLARK was joined by their dealer, Ardent Industrial Equipment, whose employees sponsored several children from its tree. “Together, we can make a greater impact on those in need in Central Kentucky. This is the true meaning of the holiday season and a great way to partner with an organization making a difference in the lives of Kentucky children.” stated a statement of the CLARK LinkedIn social media page. #RaisingHope #CLARK
ASSP’s safety podcast tops 300,000 downloads over five years
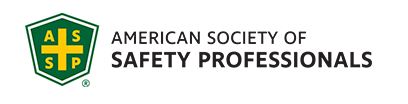
The American Society of Safety Professionals (ASSP) has shared practical workplace safety and health guidance and updates with thousands of safety professionals worldwide through its podcast series, which has surpassed 300,000 downloads over five years. New episodes of “The Case for Safety Podcast” are available every other week and focus on a range of topics to keep industry professionals informed. In its latest installment published today, the podcast discusses the impacts of winter weather on worker safety and health, and how keeping an eye on the outdoor temperature can help safety professionals and their employers have the right tools and procedures in place. The featured expert is Victor Rodriguez, operations meteorologist at Amazon, which is sponsoring the episode. ASSP’s safety podcast series debuted in September 2018 and has shared 123 episodes. “More than ever, ASSP supports the occupational safety and health community in finding ways to keep workers safe amidst new challenges,” said ASSP President Jim Thornton, CSP, CIH, FASSP, FAIHA. “Environments can change rapidly and our podcast continues to be a valuable resource in providing helpful insights.” An upcoming episode will focus on the revised ANSI/ASSP A10.48 voluntary national consensus standard, which covers the latest safety practices and training recommendations for the construction, demolition, modification and maintenance of communication structures. Recent podcasts have covered topics such as personal protective equipment for women, how to get safety improvement buy-in from your organization, tips for improving ergonomics, and how advancing workplace safety can increase productivity and benefit a company’s bottom line. The podcast series is free to access on the ASSP website. Listeners can also subscribe to “The Case for Safety Podcast” on Spotify and Apple Podcasts.
Episode 444: Harnessing data analytics for fulfillment optimization with Syncontext
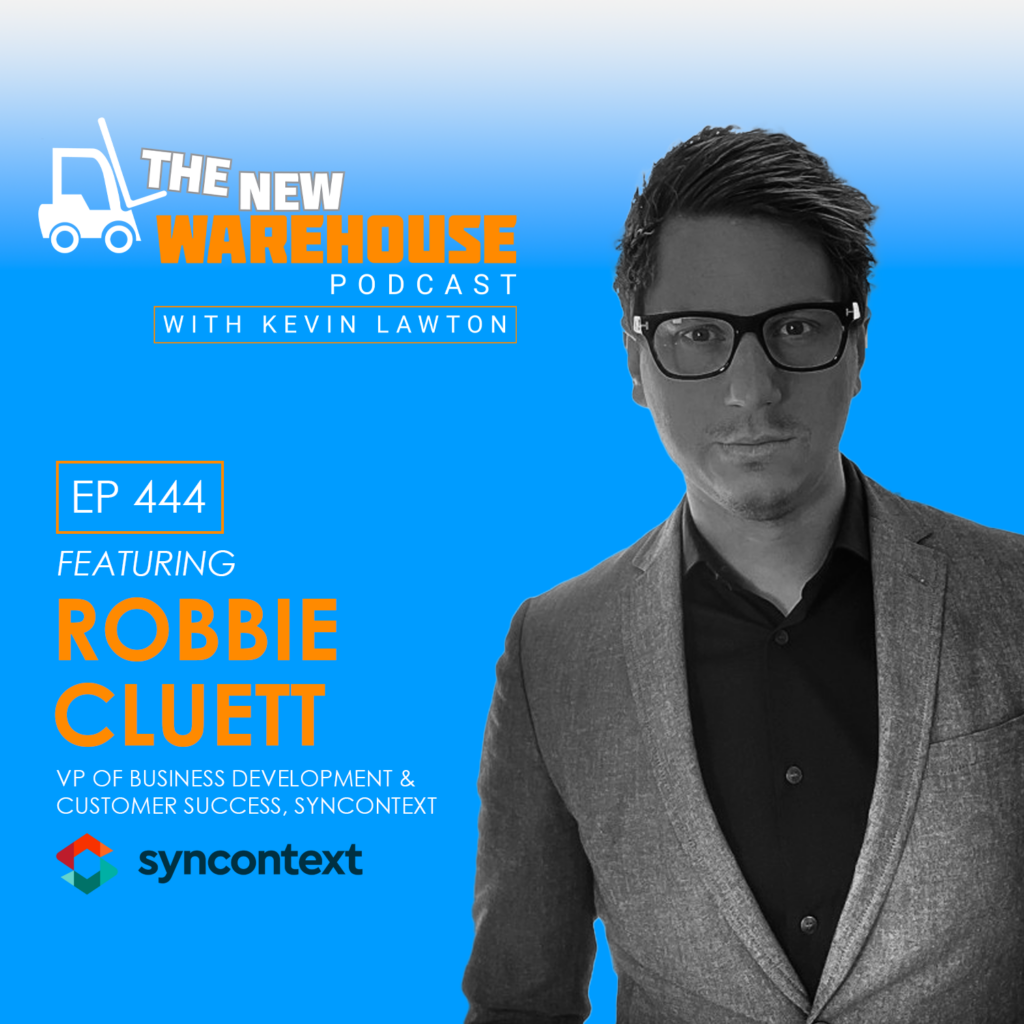
In the latest episode of The New Warehouse Podcast, Robbie Cluett, Vice President of Business Development & Customer Success at Syncontext, joins the show. Syncontext is a supply chain consulting and technology firm based in Vancouver, Canada, specializing in optimizing fulfillment operations by leveraging data analytics. Cluett shares valuable insights into how data analytics can transform warehouse operations, driving decisions and enhancing efficiency. Enhancing Warehouse Operations with Data Analytics Cluett emphasizes the critical role of data in optimizing warehouse operations. “We leverage data analytics to optimize fulfillment operations through slotting optimization and layout design,” says Cluett. He explains how their team, with a strong consulting background, assists in designing new distribution operations and making less disruptive layout adjustments based on data analysis. Cluett points out how in high-volume warehouse environments, such as those in the grocery sector, nearly 50% of skews change annually. Inventory turnover poses challenges in maintaining consistent and efficient operations over time, highlighting the need for adaptive and dynamic warehouse management strategies. The Role of Technology in Fulfillment Optimization Cluett highlights how Syncontext’s technology, particularly the SKUstream™ platform, integrates with various Warehouse Management Systems (WMS) to maximize productivity and efficiency. “SKUstream™ works along with most WMS and really leverages that transactional data on a daily basis,” he notes, pointing out the importance of daily slotting optimization and the continuous evaluation of warehouse operations. Future Outlook: Data and Warehouse Management Looking ahead, Cluett shares his vision of the evolving role of data in warehouse management. He predicts an increased focus on using robust analytics and data models that are flexible and customizable. “Optimization is not a one-size-fits-all approach,” Cluett remarks, emphasizing the need for tailored solutions based on specific operational constraints. Key Takeaways on Fulfillment Optimization Data-Driven Decision Making: Syncontext uses data analytics for efficient fulfillment operations and layout optimization. Seamless Technology Integration: SKUstream™ by Syncontext complements existing WMS to enhance warehouse operations. Customized Data Solutions: The future of warehouse management lies in flexible, data-driven optimization strategies. The New Warehouse Podcast EP 444: Harnessing Data Analytics for Fulfillment Optimization with Syncontext
Bobcat and its employees donate more than $175,000 during Annual Fall Giving Campaign
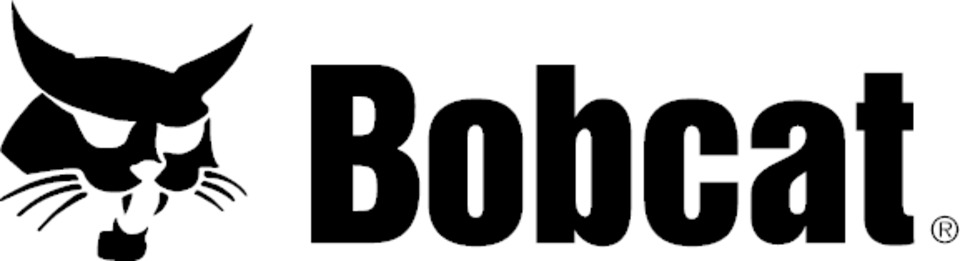
Bobcat Company and its employees recently held their annual fall giving campaign, garnering more than $175,000 in donations to nonprofit organizations in 17 states. To support its employees in their philanthropic pursuits, Bobcat matched employee donations dollar for dollar (up to $3,000 per person) to further amplify employees’ generosity. Employees were eligible to select any organization with a 501(c)(3) status to donate to. “We are thrilled we could further our employees’ donations and help them give back in a way that was personally meaningful to them through our fall giving campaign,” said Tina Amerman, Bobcat Director People Programs. “We continue to see strong participation in this annual event and have donated hundreds of thousands of dollars over the years to positively impact a wide variety of local organizations.” Bobcat continues to partner with United Way—a relationship that has spanned more than 20 years—to support its mission of inspiring and activating communities to improve lives. United Way remained a featured charity for this year’s campaign, receiving strong employee and organizational support in addition to more than 100 other nonprofit recipients selected by employees. The fall giving campaign wrapped up a season of volunteering and community efforts on behalf of the company. For example, in September, Bobcat announced that more than 1,000 employees dedicated their time and talents to participate in more than 100 volunteer projects globally. The companywide volunteer projects aimed to give back to the communities where Bobcat employees live and work. This volunteerism is on top of the generosity Bobcat employees exhibited financially. Additionally in 2023, Bobcat donated $5 million to support a new engineering facility at North Dakota State University and partnered with the National Recreation and Park Association with $250,000 in grants to help create sustainable community park and recreation areas throughout the U.S. In addition, Bobcat supports educational STEM programs through its annual grant program and serves as the lead sponsor for the Bobcat North Dakota Open, donating more than $1.2 million since 1984, in support of The Village Family Service Center’s community outreach services.
Holiday Fanfare: CT Manufacturer Hosts Patriotic Charity Campaign
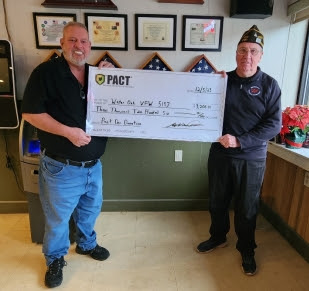
December is the time for holiday giving, but one Connecticut manufacturing company has been giving back to those who served our country all year long! Specifically, Watertown-based Packaging and Crating Technologies (PACT), today presented a $3,000 check to the Water-Oak VFW Post 5157 in Watertown based on a charitable campaign that it launched in November for National Military Appreciation Month. The local non-profit’s mission is to speed the rehabilitation of the nation’s disabled combat veterans, assist their families, and provide education and community service. “Although we, as an American company, are always patriotically minded, we consider it a privilege to highlight key military holidays and commemorative milestones like Memorial Day, Veterans Day, and most recently, Military Appreciation Month,” said Rodger Mort, President of PACT. “In doing so, we are raising both awareness and financial donations for our heroes and their families.” Mort notes that PACT has strong ties to the military which uses its various shipping and packaging container lines when individual soldiers are moved from station to station, including its patented LiftVan, PleatWrap, J-Crate, Spiral Foot, MP40, Sofa Crate, and Motorcycle Crate. Each item ranges in price between $40 and $2,000, is made from a durable and sustainable corrugated cardboard material, and is capable of being reused for hundreds of moves. Further, the company is a preferred vendor for the US Department of Defense and has been awarded a special permit from the US Department of Transportation for the shipping of lithium-ion batteries, as well as passed the proposed SAE-G-27 test standard. “PACT benefits the military through both its innovative product line, as well as in its generous charitable programs,” said Water-Oak VFW Post 5157 Commander Richard Noble. “We are extremely grateful for the company’s ongoing efforts in helping to ensure that the sacrifice of our servicemen and women is never forgotten.”
NORD DRIVESYSTEMS supplies the crane industry with innovative solutions to move the toughest loads
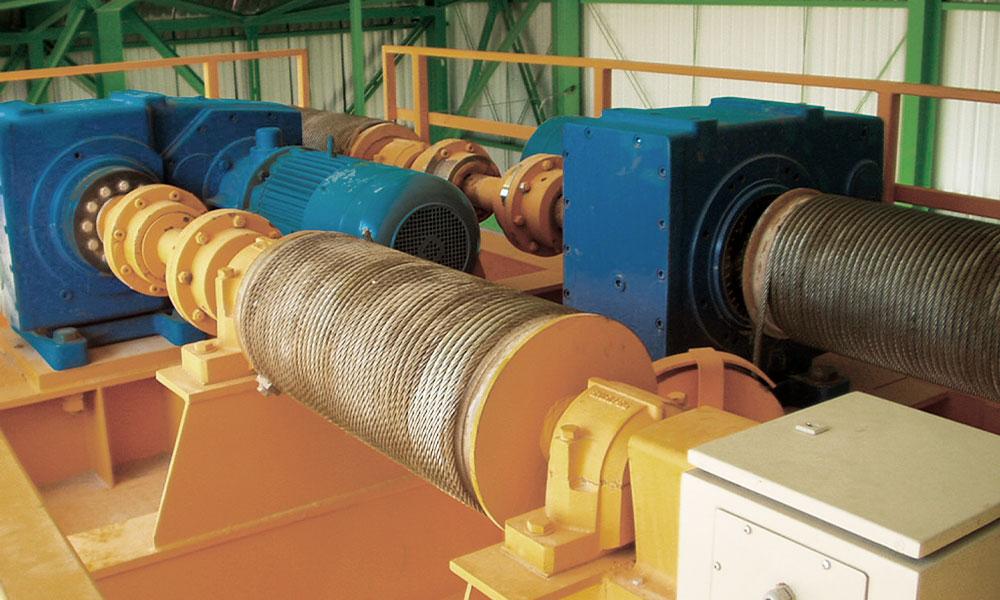
NORD’s drive solutions for cranes feature heavy-duty industrial gear motors, dynamic electronic control products, and functional safety modules to keep crane systems operating efficiently. Crane applications require special drives with a strong focus on reliability and safety. Loads must be safely lifted, precisely positioned, and gently set down, sometimes during simultaneous movement of trolleys. Whether gantry, building, bridge, floating, or other type of crane, NORD DRIVESYSTEMS offers complete drive solutions with flexible configuration options to perfectly match specific application requirements. NORD’s robust modular system offers drive systems that are easy to service and maintain along with high efficiency, output torques up to 2,495,900 lb-in, and variable frequency drives with integrated POSICON positioning mode and functional safety. NORD constructs all gear units according to their UNICASE™ housing principle. Housings are machined in a single step with bearing points precisely aligned to each other, resulting in a surface not subjected to torque and radial loads that also keeps operators protected from pinch points. This design also produces a more robust unit capable of handling heavy loads and harsh environmental conditions, while increasing service life. MAXXDRIVE® Industrial Gear Units deliver extremely high output torques up to 2,495,900 lb-in, quiet operation, and long service life. Thanks to their robust housing, they can withstand a wide variety of ambient conditions and perform well even in dusty environments, coastal areas, and environments with high humidity, heat, or large temperature fluctuations. These units feature both parallel shaft and right-angle designs and are highly configurable to application requirements with a variety of output shafts, output flanges, motor attachments, and input options to choose from. MAXXDRIVE XD Industrial Gear Units are the most recent expansion to the MAXXDRIVE product family and are engineered specifically for crane and hoist applications. These units feature a unique housing optimized for external loads and an extended center distance to accommodate a U-shaped design, enabling the cable drum and motor to be on the same side of the gear unit. Compared to NORD’s standard, compact MAXXDRIVE series, the XD center distance has been increased by 35%. The drives are available in 3-stage or 4-stage reductions with the same overall unit dimensions and center distances for a standardized design to reduce spare parts and variants. UNICASE Helical Bevel Gear Units from NORD offer a wide performance range of 0.16 – 250 hp and torque up to 442,537 lb-in. They have various shaft designs, mounting options, and bearing concepts that make them highly versatile and adaptable. When equipped with heavy-duty bearings and a spread bearing/flange mount design, these units achieve high axial and radial load capacity, experience minimum backlash, and provide a long service life to keep cranes operational with minimum downtime. NORD’s UNICASE Parallel Shaft Gear Units provide ultimate efficiency and reliability at a cost-effective price. Their compact design saves on installation space and requires less maintenance compared to traditional belt drives. They offer output torque up to 680,200 lb-in, versatile shaft and mounting options, and can be configured with heavy-duty bearings for maximum load capability. NORD variable frequency drives provide cranes with dynamic, intelligent movement. They can synchronize gear motors to work in tandem to hoists and move loads for trolley or travel drives, be programmed to enable steady operation for swivel drives, and provide soft starts and braking via defined adjustable ramps to safely pick up and set down loads. NORD’s cabinet control solutions include the NORDAC PRO SK 500P Variable Frequency Drives. This product family has five frame sizes to choose from with scalable functionality ranging from the basic SK 500P version to the advanced SK 550P version. Easy operation is achieved with multiple integrated interface options and full PLC functionality to configure each drive parameter. Functional safety options like STO and SS1 are also available to further protect operators, product, and entire systems. Decentralized drive solutions from NORD include the NORDAC FLEX SK 200E Variable Frequency Drives. These drives are NORD’s most flexible VFDs and offer reduced Total Cost of Ownership (TCO) and greater Return on Investment (ROI). With their versatile functionality, wide range of extension modules, and flexible mounting options, they can be customized to all application needs. Integrated brake rectifiers for motor brake control and an integrated brake chopper enable safe operation of heavy crane loads and ensure downtimes are avoided by proper speed management. NORDAC FLEX VFDs additionally offer multiple functional safety options such as STO, SS1, SLS, SSR, and PROFIsafe to further ensure systems operate safely. From design and commissioning to service and maintenance, NORD supports its customers in all phases of the project and supplies high quality solutions that meet international standards. Thousands of NORD drives are already in operation in crane systems around the world supported by a global assembly and service network guaranteeing short delivery times, comprehensive support, and rapid on-site service.
Siemens expands its SIMATIC MICRO-DRIVE servo-drive system for extra-low-voltage material handling and manufacturing applications
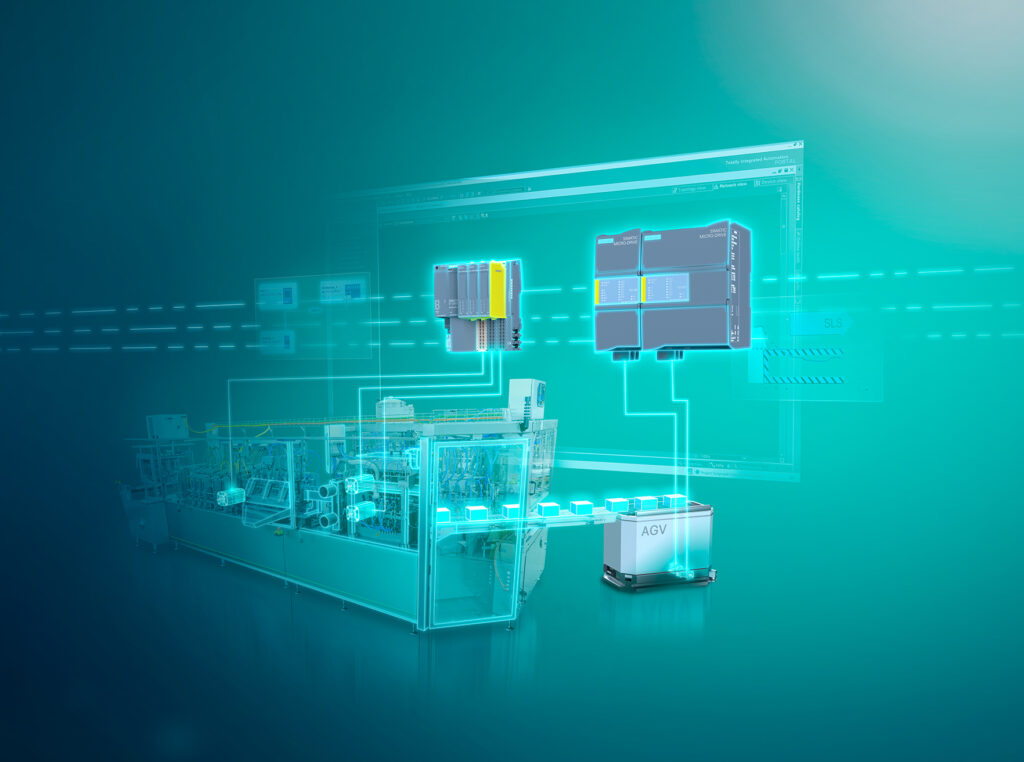
User benefits include seamless network integration, integrated drive safety, versatility, easy installation and commissioning Siemens is extending its drive portfolio in the extra-low-voltage range for 24–48V EC motors with its new SIMATIC MICRO-DRIVE. The new product line with UL- and CE-marked components consists of the PDC (Profidrive Control) servo drive in conjunction with a flexible range of motors and connecting cables from product partners, along with the TM (technology module) format with servo and stepper drives in compact 20mm width that can be used in conjunction with distributed or open controllers. Simple connectivity to Siemens programmable logic controllers (PLCs) helps significantly reduce the engineering workload, while integration into Siemens automation technology via its TIA Portal makes for simple commissioning and servicing. Attributes such as smart encoders and one-button tuning add to its plug-and-play startup. Communication takes place over PROFINET using PROFIsafe and PROFIdrive profiles. The new Safety Integrated function SLT (Safely Limited Torque) limits torque by monitoring motor current in running operation. To address its customers’ requirements with maximum flexibility, Siemens utilizes product partnerships with companies such as Dunkermotoren, ebm-pabst, Harting and KnorrTec when it comes to the motors and cables used with MICRO-DRIVE. Other third-party motors can also be utilized with support for various encoder types. SIMATIC MICRO-DRIVE PDC focuses on higher performance applications with 100W and 600W units that permit side-by-side rail mounting. They are available in standard (hardwired Safe Torque Off (STO)) and fail-safe versions. STO, SS1, SLT, SLS, and SSM Safety Integrated functions are available with the MICRO-DRIVE PDC100F variant. SIMATIC MICRO-DRIVE TM units are designed for basic performance in industries with a focus on compactness and simple safety requirements. They are available in 280W-rating and come standard with hardwired Safe Torque Off (STO) safety functions. In addition to servo, TM units feature new modules to control stepper motors with or without incremental encoders. Machine builders and users will benefit from a compact design, easy wiring and installation to ensure top performance. Both SIMATIC MICRO-DRIVE PDC and TM systems are suited to a wide range of diverse applications such as automated guided vehicles (AGVs), conveyors, shuttles, storage and retrieval machines for warehousing systems, diverters, assembly machines, and industrial positioning applications. The Siemens Totally Integrated Automation (TIA) Portal is used to configure drives and motors quickly and easily including the activation of safety functions with a Fail-safe PLC via PROFIsafe. Machine operating data can be transmitted directly to the controller from MICRO-DRIVE and transferred to Cloud-based platforms such as MindSphere over MindConnect.
Combilift launches their 2023 Christmas video
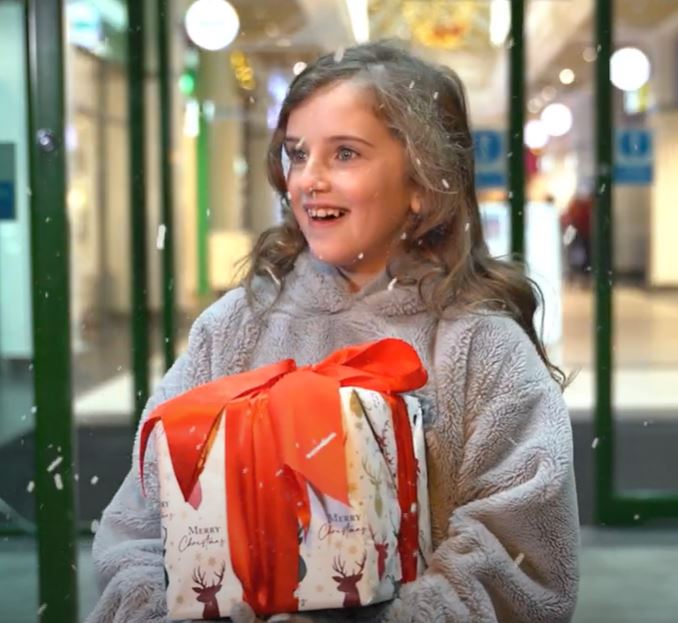
Irish-based forklift manufacturer Combilift celebrated 25 years in business in 2023 and has wrapped up the year by producing a very special message during this holiday season. Made in-house by the staff themselves, this heart-warming video brings a little bit of added sparkle to the manufacturing b2b industry. In this video you will see Santa’s sleigh started running low on magic dust and was forced to make an emergency stop in Ireland. Luckily for him (and children everywhere!) he lands in Combilift and is able to save Christmas with only his Christmas sparkle and a little ingenuity!
Yokohama TWS Sri Lanka awarded Best Exporter for 2021/22 and 2022/23
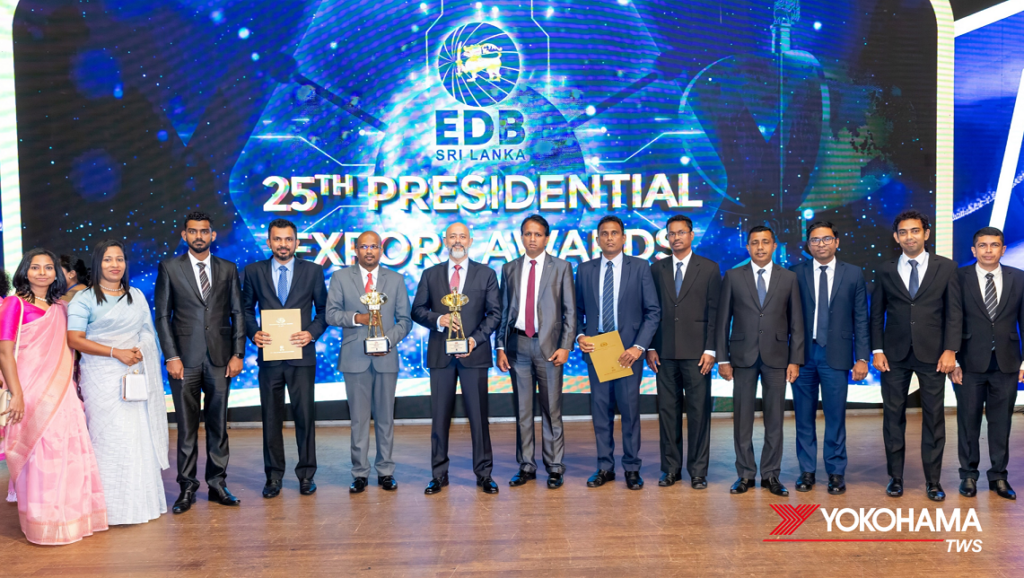
Yokohama TWS Sri Lanka has been recognized for its exceptional export achievements by receiving the prestigious ‘Best Exporter in the Dry Rubber Products Category’ award at the 25th Presidential Export Awards (PEA) for two consecutive years, 2021/22 and 2022/23. The PEA is the highest recognition bestowed by the Head of State of Sri Lanka upon exporters who have been fostering growth and made outstanding contributions to the country’s export sector and economic advancement. Sanjay Melvani, Managing Director Sri Lanka at Yokohama TWS, expressed his enthusiasm upon receiving the award, stating, “We are incredibly proud to receive the ‘Best Exporter Award’ in recognition of our unwavering commitment to boosting our country’s exports, especially during this unprecedented period of social, political, and financial uncertainty. Despite facing challenges, winning the award for two consecutive financial years in the Dry Rubber Products Category highlights the drive and hard work of our team. I am grateful for the opportunity to make a positive impact on Sri Lanka’s economy through our business operations.” The award winners are carefully evaluated based on their performances considering factors such as Export turnover, Export Proceed repatriation, Net-foreign exchange earnings, market diversification, product diversification, Value addition, Innovations, and Sustainable efforts in exports. The selection of the award winners was meticulously carried out by an esteemed Panel of Judges headed by a retired Judge of the Supreme Court. Award winners are selected under two categories: Overall Awards and Product/Services sector Awards, where Yokohama TWS come out as the winner specifically in the Dry Rubber Products Category.
IDENTCO hires Brian Kady as Vice President of Global Sales
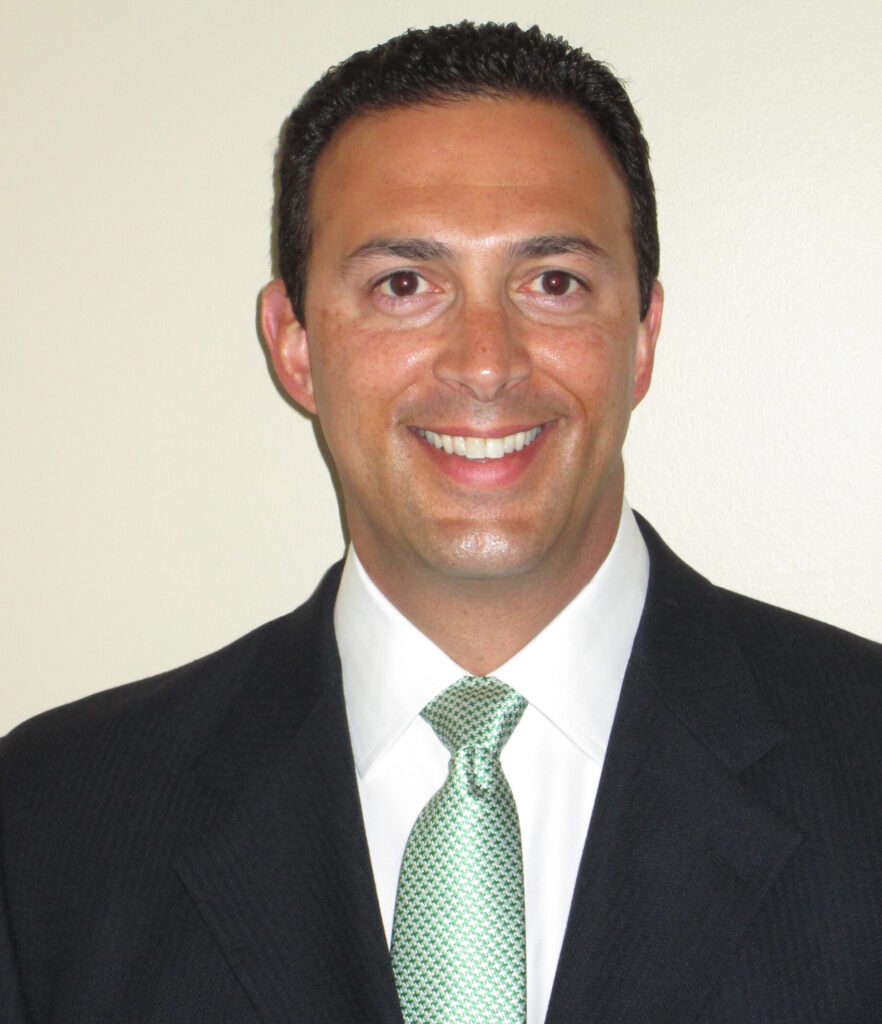
IDENTCO, a manufacturer of high-performance labeling solutions for the power equipment, electronics, transportation, and general industrial sector, has hired longtime materials supply executive Brian Kady as Vice President of Global Sales. He officially joined the company on November 20, and will oversee IDENTCO’s far-reaching sales efforts in the company’s four distinct business units. Mr. Kady also is responsible for sales activities for Reliance Label Solutions, another company under the Industrial Labels Holdings Corp flag. Most recently, Mr. Kady served as Vice President of Sales at Pregis Polymask, where he drove double-digit sales growth for the protective films company. Before that, he gained ample adhesives and coatings experience during tenures with both Avery and 3M, two of the largest entities in that sector. He also has served as Director of Sales – Performance Adhesives Group for Ohio-based Mactac. Mr. Kady joins IDENTCO at a promising time. The company has been steadily adding to its extensive portfolio of labeling solutions, which it designs, manufactures and supplies for demanding sectors such as automotive components, electronics applications, industrial machinery & tools, and commercial transportation. In addition, IDENTCO recently introduced VortexID, an automated wire marking system whose throughput and durability set new industry benchmarks. “Brian is a people-first yet results-driven business development executive with a track record of expanding revenue growth and extending market share,” said Brad Zechman, CEO of IDENTCO. “As IDENTCO continues to bolster and broaden our solutions portfolio across each of our four main business units, Brian’s industry experience and leadership qualities will be a tremendous asset.” Mr. Kady earned an MBA from Walsh College in Troy, Michigan, and a bachelor’s degree from Central Michigan University in Mt. Pleasant, MI.
Warehouse Trade Association welcomes new staff
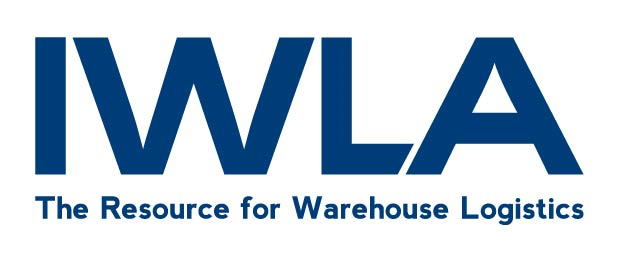
The International Warehouse Logistics Association (IWLA) recently added two staff members to its education department, bolstering the organization’s commitment to deliver exceptional development opportunities for warehouse professionals across North America. IWLA is the ONLY trade association focused on the needs of third-party warehouses (3PLs), their leaders, and their employees. The association offers in-person, warehouse-specific educational events, distance-learning opportunities, and a large network of warehouse logistics professionals. “One IWLA strategic focus is delivering the BEST in warehouse education – for all levels and positions in third-party warehouses,” says Jay D. Strother, IWLA president & CEO. “Wil and Bennett bring a fresh approach and practical experience to ensure IWLA fulfills that promise. We are excited about the possibilities now that they are on board.” The new staff members started earlier this fall: William Carton, Director of Professional Development & Convention With an extensive industry background, Wil Carton hails more recently from True Value Company where he served as senior training specialist. His work there focused on warehouse safety, onboarding, and building effective operations in True Value’s distribution centers. Prior to that, he served as the senior training manager for Marcus Corporation. This is all built on his time as chairman of Animation/FX & Design for Tribeca Flashpoint College (now part of Columbia College) and time helming a Chicago-based media company as creative director and co-managing partner. “I have a passion for fostering professional and personal growth,” Carton says. “I hope to use my educational programming expertise to create engaging development experiences for warehouse professionals across all levels.” Carton oversees all IWLA education and meetings personnel, manages aspects of the IWLA Convention & Expo, and updates the core warehouse-management-focused curriculum. Bennett Judson, Meetings & Registration Coordinator Bennett Judson brings a wealth of experience from her tenure at the National Roofing Contractors Association. There she led the meeting services department, coordinating annual convention events, committees, and board meetings. She will play a pivotal role in planning and executing in-person and webinar education programming, including sourcing event locations. She will collaborate with staff, member volunteers, and committees to enhance IWLA’s educational initiatives. “Please join me in welcoming these new additions to the IWLA team,” Strother says. “Their collective expertise will contribute to the continued success and growth of IWLA’s educational initiatives.”
U.S. Rail Traffic for November and the week ending December 2, 2023
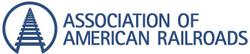
The Association of American Railroads (AAR) has reported U.S. rail traffic for the week ending December 2, 2023, as well as volumes for November 2023. U.S. railroads originated 1,128,573 carloads in November 2023, down 0.0 percent, or 102 carloads, from November 2022. U.S. railroads also originated 1,279,906 containers and trailers in November 2023, up 5.0 percent, or 60,486 units, from the same month last year. Combined U.S. carload and intermodal originations in November 2023 were 2,408,479, up 2.6 percent, or 60,384 carloads and intermodal units from November 2022. In November 2023, 12 of the 20 carload commodity categories tracked by the AAR each month saw carload gains compared with November 2022. These included: chemicals, up 8,322 carloads or 5.7 percent; motor vehicles & parts, up 4,611 carloads or 6.6 percent; and petroleum & petroleum products, up 4,510 carloads or 10.1 percent. Commodities that saw declines in November 2023 from November 2022 included: crushed stone, sand & gravel, down 8,052 carloads or 8.0 percent; all other carloads, down 6,851 carloads or 25.6 percent; and grain, down 6,290 carloads or 5.4 percent. “U.S. intermodal volume rose 5.0% in November, its third straight year-over-year gain after 18 straight declines and the biggest year-over-year percentage gain for intermodal in 29 months. Overall, the last week of November had the highest carload plus intermodal volumes in two years,” said AAR Senior Vice President John T. Gray. “Much will depend on how the broader economy continues to evolve, but railroads are hopeful November will provide much-needed momentum for the rest of 2023 and into 2024.” Excluding coal, carloads were down 1,059 carloads, or 0.1 percent, in November 2023 from November 2022. Excluding coal and grain, carloads were up 5,231 carloads, or 0.8 percent. Total U.S. carload traffic for the first 11 months of 2023 was 10,824,994 carloads, up 0.2 percent, or 21,700 carloads, from the same period last year; and 11,684,971 intermodal units, down 6.0 percent, or 748,046 containers and trailers, from last year. Total combined U.S. traffic for the first 48 weeks of 2023 was 22,509,965 carloads and intermodal units, a decrease of 3.1 percent compared to last year. Week Ending December 2, 2023 Total U.S. weekly rail traffic was 509,626 carloads and intermodal units, up 4.9 percent compared with the same week last year. Total carloads for the week ending December 2 were 237,049 carloads, up 1.4 percent compared with the same week in 2022, while U.S. weekly intermodal volume was 272,577 containers and trailers, up 8.2 percent compared to 2022. Five of the 10 carload commodity groups posted an increase compared with the same week in 2022. They included chemicals, up 6,869 carloads, to 33,692; petroleum and petroleum products, up 1,401 carloads, to 10,902; and motor vehicles and parts, up 1,168 carloads, to 16,209. Commodity groups that posted decreases compared with the same week in 2022 included nonmetallic minerals, down 3,167 carloads, to 29,043; miscellaneous carloads, down 1,740 carloads, to 7,600; and grain, down 1,276 carloads, to 23,425. North American rail volume for the week ending December 2, 2023, on 10 reporting U.S., Canadian and Mexican railroads totaled 351,272 carloads, up 2.3 percent compared with the same week last year, and 356,459 intermodal units, up 6.9 percent compared with last year. Total combined weekly rail traffic in North America was 707,731 carloads and intermodal units, up 4.6 percent. North American rail volume for the first 48 weeks of 2023 was 31,531,507 carloads and intermodal units, down 2.8 percent compared with 2022. Canadian railroads reported 97,615 carloads for the week, up 3.2 percent, and 71,079 intermodal units, up 0.1 percent compared with the same week in 2022. For the first 48 weeks of 2023, Canadian railroads reported cumulative rail traffic volume of 7,669,482 carloads, containers and trailers, down 3.2 percent. Mexican railroads reported 16,608 carloads for the week, up 12.7 percent compared with the same week last year, and 12,803 intermodal units, up 21.2 percent. Cumulative volume on Mexican railroads for the first 48 weeks of 2023 was 1,352,060 carloads and intermodal containers and trailers, up 4.6 percent from the same point last year. To view the weekly rail traffic charts, click here.
Plastics Industry Association (PLASTICS) opens nominations for William R. Carteaux Leadership Award
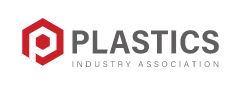
The Plastics Industry Association (PLASTICS) has opened nominations for the William R. Carteaux Leadership Award, presented to an industry professional who has achieved distinction in working for the betterment of the plastics industry. Any employee of a PLASTICS member company who personifies the values of Bill Carteaux—unity, dedication, perseverance and selflessness—is eligible for the award, named in honor of the former President and CEO of PLASTICS. “Bill Carteaux’s passion and dedication to our industry were remarkable,” said Matt Seaholm, President and CEO of PLASTICS. “Even through tough times, Bill was committed to PLASTICS and advocated for our entire industry including the millions of workers it employs. He was relentlessly optimistic about the future of the plastics industry, bringing together leaders and innovators to address our sustainability goals.” “It’s our great honor to provide an award that reflects Bill’s professional and personal values. I look forward to participating in our award ceremony this Spring in Orlando, Florida,” concluded Seaholm. “It was an honor to be the first recipient of the William R. Carteaux Leadership Award,” stated Brad Crocker, CEO of Epsilyte and recipient of the Carteaux Leadership Award. “Bill Carteaux was a selfless leader who was passionate about our industry and its future. This award exemplifies what it means to lead with the values Bill personified: dedication, unity, perseverance, and selflessness.” Prospective candidates can be nominated by their peers, friends, or family. To submit nominations, please click here. Nominations will be accepted through Friday, February 2, 2024. The award will be presented as part of the Plastics Hall of Fame Ceremony in Orlando, Florida on Sunday, May 5, 2024.
Episode 443: AI Integration & Visibility: Boosting warehouse performance with Arvist
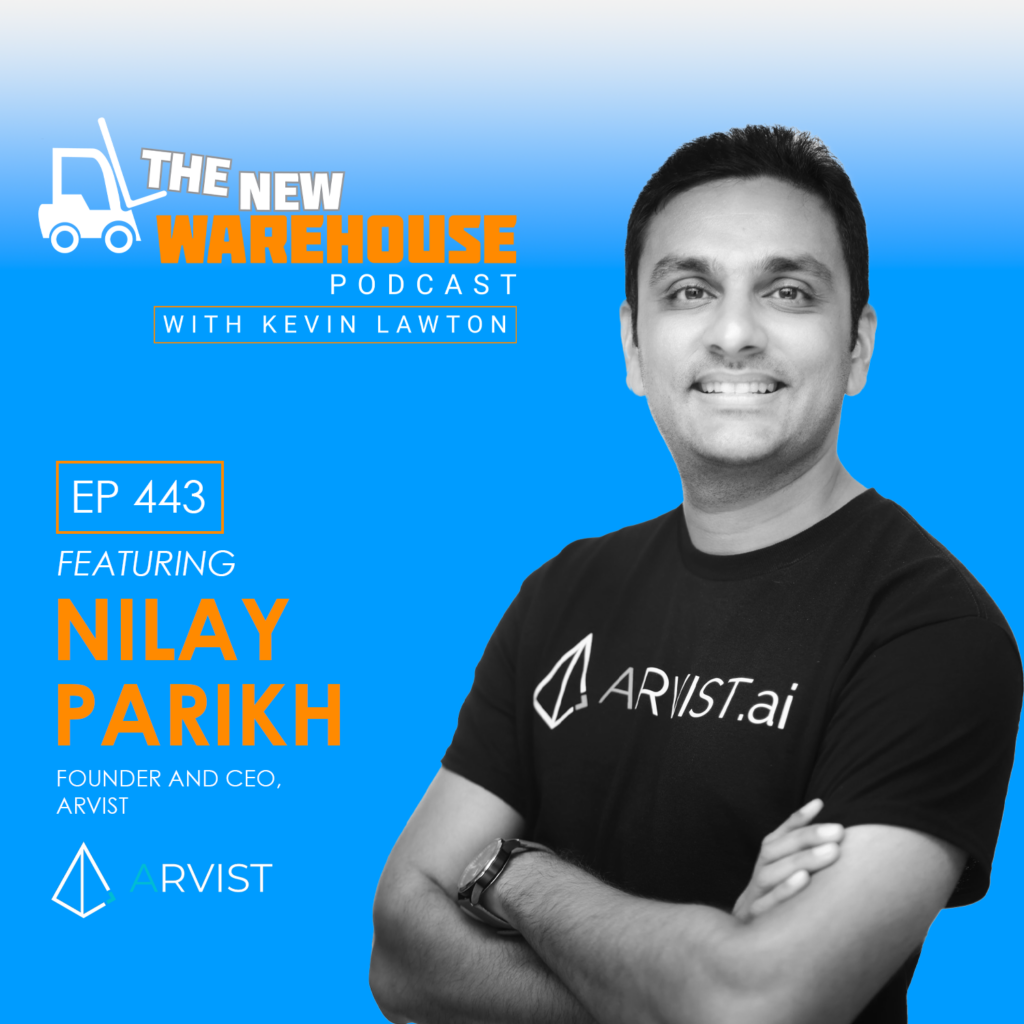
In this episode of The New Warehouse podcast, Kevin welcomes Nilay Parikh, the founder and CEO of Arvist. By leveraging AI, Arvist focuses on harnessing the power of data to enhance safety, productivity, and quality in the supply chain. Parikh brings a wealth of knowledge and experience in AI technology, offering unique perspectives on its practical applications in warehousing. In this engaging conversation, he delves into how Arvist’s solutions are shaping the future of warehousing, addressing current challenges, and setting new standards for operational efficiency and safety. AI Integration for Enhanced Warehouse Safety Parikh discusses Arvist’s innovative approach to using AI for proactive warehouse safety measures. Arvist’s technology can identify potential safety hazards and compliance issues in real time by analyzing data from existing security cameras and systems. Parikh explains that instead of looking at accidents after they happen, the Arvist AI platform proactively spots risks, allowing immediate corrective action. This approach not only enhances the safety of workers but also fosters a culture of prevention, fundamentally transforming traditional safety management in warehouse environments. AI-Driven Operational Efficiency Arvist’s AI platform offers a significant leap in operational efficiency for warehouses by harnessing existing data sources like security cameras, WMS, and ERP systems. This includes optimizing loading dock operations, enhancing inventory management, and streamlining workflow. Parikh highlights a case where their AI solutions significantly reduced loading dock bottlenecks, demonstrating the practical impact of their technology on day-to-day operations. Future of Warehouses with AI Integration Looking into the future, Parikh envisions an increasingly integrated role for AI in warehouse operations. He anticipates AI not only complementing existing automation technologies but also paving the way for more advanced solutions. He envisions a warehouse environment where AI-driven systems work seamlessly with robotics to achieve unprecedented levels of productivity and accuracy. This vision points to a future where warehouses operate optimally, driven by intelligent algorithms that continuously learn and adapt to changing demands and environments. Key Takeaways Proactive Safety Measures: Arvist leverages AI to enhance warehouse safety proactively. Operational Efficiency: Integrating AI with existing data sources streamlines warehouse operations. Future Trends: AI will drive more sophisticated and efficient warehouse management. The New Warehouse Podcast EP 443: AI Integration & Visibility: Boosting Warehouse Performance with Arvist
It’s that time of year: “Call me back after the holidays.”
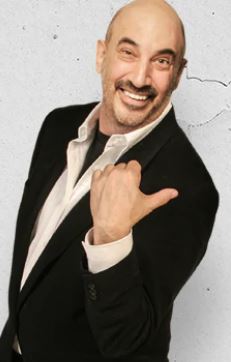
“Call me after the holidays” is the second most-heard objection in sales. (First being, “Your price is too high.” Third being, “I have to think about it.”). It comes up year after year and salespeople get frustrated year after year, unnecessarily. Here’s how to think about it and here’s what to do about it: Humbug. Salespeople hate holidays. It’s an excuse for decision makers to put buying decisions on hold. But the worst of them are the Christmas to New Year, “Call me back after the holidays,” and “Call me after the first of the year.” Two of the most hated phrases in sales. (They still rank behind “We’ve decided to buy from someone else.”) “Call me after the holidays” is not an objection. It’s worse. It’s a stall. Stalls are twice as bad as objections. When you get a stall, you have to somehow dance around it, and then you still must find the real objection before you can proceed. Here are 11.5 clever lines and winning tactics to use that will help overcome the stall: Close on the stall line. “What day after the first of the year would you want to take (would be most convenient to take) delivery?” Firm it up, whenever it is. Ask, “When after the first of the year? Can I buy you the first breakfast of the new year?” Make a firm appointment. If it’s just a callback, make the prospect write it down. Call backs must be appointed, or the other guy is never there when you call. Writing it down makes it a firm commitment. Tell them about your resolutions. “I’ve made a New Year’s resolution that I’m not going to let people like you who need our service, delay until after the first of the year. You know you need it.” Offer incentives and alternatives. Invent reasons not to delay. Bill after the holiday. Order now, deliver after the holiday. Question them into a corner – and close them when they get there. “What will be different after the holidays? Will anything change over the holidays that will cause you not to buy?” (Prospect’s answer — “Oh no, no, no.”) “Great!” you say, “Let’s get you order in production (service scheduled) now, and we’ll deliver it after the holiday. When were you thinking of taking delivery (beginning).” Agree. Then disagree. I know what you mean lots of people feel that way. Most don’t realize that the money wasted between now and the first of the year, will equate to a huge savings if they buy now. Are you sure you want to waste the money? Get a testimonial letter. Ask someone who bought before the holidays and was glad they did to write you a two paragraph testimonial. Video it if you can. Get one paragraph about the value they received and how they originally wanted to wait. The second paragraph should be about how happy they are about your service after the sale. Similar situations are more powerful than your sales pitch. Drop-in with holiday cheer. Use a small holiday plant or gift to get in the door. (No one says no to Santa — unless you live in Philadelphia. There they boo Santa.) Create urgency. There’s a product or delivery back-up after the first — schedule now. Be funny. Say, “So many people have said call me after the first that I’m booked until April. I do however, have a few openings before the first. How about it?” Making the other person laugh (smile) will go a long way towards getting past the stall. An alternative joke is, “What holiday?” 11.5 Beg. Pleeeeaaase. I’ll be your best friend. Reality check. The success with which this stall is able to be handled is directly related to the quality of the relationship that’s been built with your prospect or customer. A good relationship allows more liberty to press for immediate action. A weak relationship will mean you wait until after the holiday. Or longer. Prevention – the best cure. If you know this objection is coming, do something BEFORE it happens. Prevention of objections and stalls is the most obvious, most powerful, and least used sales technique. Here are a few prevention methods: Start in early November to create urgency. Set price raises in September to take effect January 1. Announce them right away and communicate them weekly into the holiday season. Create a holiday special. Have a five-day sale in December. Offer December price incentives or special value incentives. Throw a holiday party. Invite prospects and customers, and offer them a “Tonight only deal.” Hold a series of seminars that are about important issues to your prospects and customers. Have the best one just before the holidays. Serve great food. Create an internal sales contest with a great first second and third prizes. Build relationships all year long. The bottom line is – as sure as you’ll spend lots of money this holiday season, someone will ask you to call them after it’s over. When they do, don’t get mad, get creative. Don’t get frustrated, get a relationship. Happy holidays! If you need more information on this subject, call me – after the first of the year. Ho, ho, ho. About the Author: Jeffrey Gitomer is the author of twelve best-selling books including The Sales Bible, The Little Red Book of Selling, and The Little Gold Book of Yes! Attitude. His real-world ideas and content are also available as online courses at www.GitomerLearningAcademy.com. For information about training and seminars visit www.Gitomer.com or email Jeffrey at salesman@gitomer.com or call him at 704 333-1112.
Signode showcases Automation Solutions and total support services at MODEX
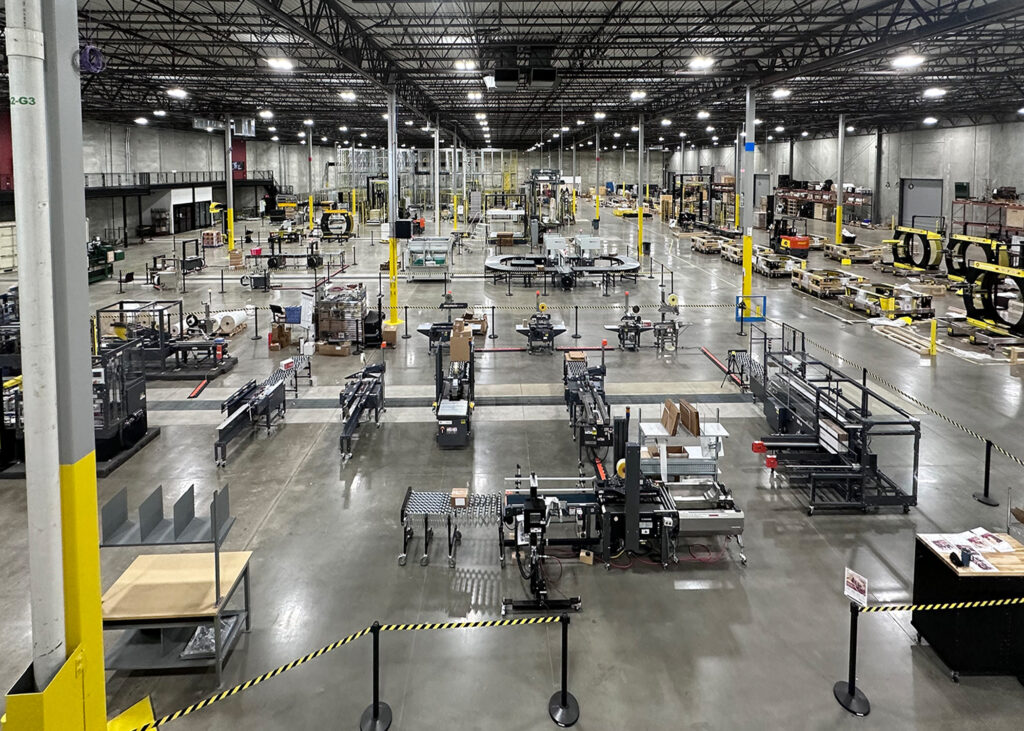
Signode, a global manufacturer of a broad range of automated transit packaging equipment, tools, consumables, automation and support solutions, is highlighting industry-leading technologies at MODEX 2024 in Atlanta. Held at the Georgia World Congress Center March 11-13. Those who stop by booth B1411 can expect a preview of Signode’s two-pronged approach to solving customer challenges: Innovative packaging and automation solutions backed by comprehensive application testing, and a robust post-installation service and support program. Highlights at MODEX include: Automation Equipment and Protective Packaging Whether you’re looking to upgrade a single machine or automate your entire production line, Signode offers thoughtful and customizable solutions to build a system that meets your operation’s specific needs. By utilizing its broad portfolio of protective transit packaging solutions, Signode assists its customers across industries in achieving optimal outcomes. An expansive portfolio includes semi- and fully automated equipment, robotics and other packaging machinery to protect products on their transit journey from the production line to their final destination. Solutions include: Automation Systems, including Palletizers/Depalletizers, AMRs, ASRS Protective Packaging Case Packaging Equipment Strapping Equipment and Consumables Stretch Wrapping and Hooding Equipment and Consumables An Industry-Leading Approach Signode takes partnerships seriously, working with customers to discover underlying needs and delivering tailored solutions to meet specific requirements. Its innovations in transit packaging equipment and consumables are driven by customer and industry trends, which is why Signode has expanded its offering to include total customer support beyond the equipment. Providing customizable resources designed to promote success, confidence, and knowledge are what truly sets Signode apart in the marketplace. Customers have access to Signode’s Packaging Plus Reliability Services, which employs more than 500 field service engineers and technicians around the world who utilize the latest technology, tools, and training to keep customers’ packaging equipment operating at peak performance. Signode also offers a hands-on approach at their Customer Experience Center (CEC) in Roselle, IL. Customers have access to a product showroom, where they can see Signode’s portfolio come to life, the ISTA-Certified Packaging Lab, and Factory Acceptance Testing space. At the industry’s marquee transit packaging testing facility, real-world transit and environmental conditions are simulated to show how Signode machines adeptly handle and package your specific products before making a purchasing decision, and FAT testing determines that your investment will integrate with existing equipment.
November 2023 Logistics Managers’ Index released
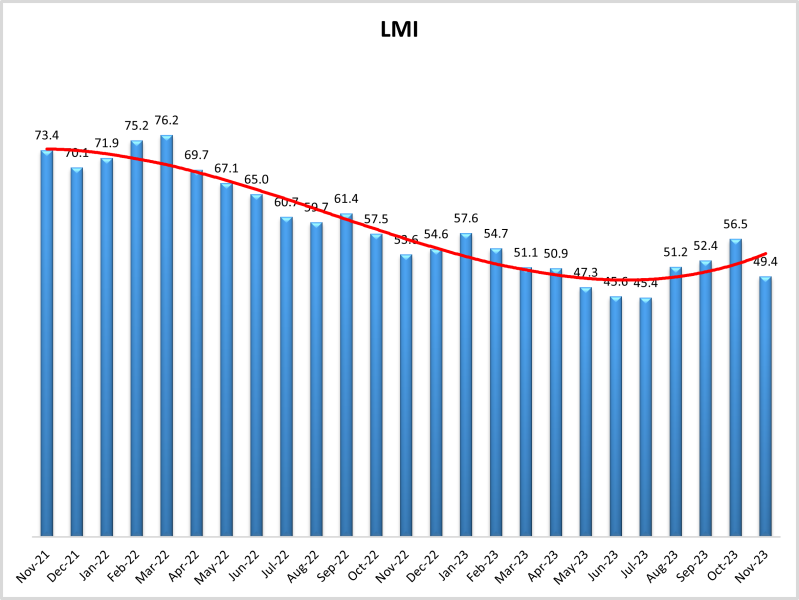
The road to recovery is not always linear – something that is clearly evidenced by the backwards step the Logistics Managers’ Index took this month. November’s Logistics Manager’s Index read in at 49.4, down (-7.1) from October’s reading of 56.5. This dip back into (very mild) contraction ends what had been three consecutive months of expanding rates of growth. The 7.1-point drop is the largest since the start of the ongoing downturn back in April 2022.However, the reason behind this decline is much different than the one from 19 months ago. November’s dip was largely triggered by a decline in Inventory Levels (-9.1) which is attributable to Q4 holiday sales and the subsequent dips in Warehousing Capacity (+3.6) and Transportation Capacity (+5.2) and slowdown in Warehousing Utilization (-14.0) and Transportation Utilization (-10.7). We saw a similar decline in utilization metrics back in April 2022, but in that instance, it was because inventories were holding still. Essentially, November’s decline seems to have come because firms are selling off inventories quickly. The previous large decline from April 2022 happened because firms had too much inventory and couldn’t sell any of it. Both of these scenarios led to large drops in the overall LMI, but this more recent drop is significantly less concerning. Researchers at Arizona State University, Colorado State University, Rochester Institute of Technology, Rutgers University, and the University of Nevada, Reno, and in conjunction with the Council of Supply Chain Management Professionals (CSCMP) issued this report today. Results Overview The LMI score is a combination of eight unique components that make up the logistics industry, including: inventory levels and costs, warehousing capacity, utilization, and prices, and transportation capacity, utilization, and prices. The LMI is calculated using a diffusion index, in which any reading above 50.0 indicates that logistics is expanding; a reading below 50.0 is indicative of a shrinking logistics industry. The latest results of the LMI summarize the responses of supply chain professionals collected in November 2023. As with every report chronicling the month of November, we should begin the discussion with “Cyber Week” – the five-day period between Thanksgiving and Cyber Monday that has often functioned as the true kickoff to holiday spending. According to the National Retail Federation 200.4 million shoppers made purchases between Thanksgiving and Cyber Monday. This was significantly higher than predicted turnout. Consumers spent $12.4 billion on Cyber Monday and $38 billion in online sales across Cyber Week which is up 7.8% from 2022[1]. The jump in sales at the end of the month is a potential explanation for the increase in activity we see in the second half of November. The increase did not only come from ecommerce, as physical retail store traffic grew as well, up 1.5% from 2022[2]. Electronics, apparel, furniture, groceries, and toys led the way, accounting for 60% of all consumer spending in November[3],[4]. One interesting note on the spending is that the use of “buy now pay later” providers and eschewing the use of the store credit cards which had previously been so lucrative for retailers. This shift in the use to the type of credit consumers are using is likely partially due to the changing demographics of shoppers, with younger spenders less drawn to high-interest cards for multiple stores when compared to previous generations. This wave of spending comes after consumer spending was only up 0.2% in October, which was the slowest increase in spending since May – which is one of the reasons Inventory Levels had built up last month. The low spending was a major contributor to the continued slowdown of inflation[5]. This dip was also reflected in the San Francisco Fed’s measure of inflation factors, which showed demand as being deflationary in October, the first time since January 2022 when consumers first started stepping back from the record spending of 2021[6]. The Fed is not ready to say that they are through raising interest rates. However, given the continued improvement in their preferred inflation metrics, it seems unlikely they will raise rates at their December meeting. Whether or not this is indicative of an eventual reduction in rates remains to be seen[7]. If consumer spending is muted through the end of the year, a rate reduction may enter into the realm of possibility. Markets seem to be expecting this possibility. In the U.S., the Dow rose for the fifth consecutive week at the end of November which marks its longest period of expansion since 2021. The S&P 500 and Nasdaq have increased over the last five weeks as well as investors grow more hopeful of a slowdown in interest rates[8]. LMI respondents are optimistic about growth in the logistics industry over the next 12 months. For that growth to occur it is likely that the predicted relaxation in interest rates will have to have happened first. Despite the dip in the overall LMI (-7.1) to the very mild rate of contraction of 49.4, the North American economy continues to chug along. The “earnings recession” that U.S. firms had been mired in seems to have ended. Earnings had been down since Q4 of 2022 but rebounded in Q3 2023 with corporate profits reaching a total of $3.28 trillion – just shy of the all-time record of $3.3 trillion set in Q3 of last year[9],[10]. However, as has been the case through most of 2023, this recovery is not consistent across the globe. The slowdown in the Panama Canal is sending fuel prices skyrocketing in Asia as the LPG carriers are being given last priority (behind passenger and cargo ships) to get through the canal[11]. This could potentially lead to inflation in Asia this winter as heating becomes more expensive. This would be particularly unwelcome news for China, which is already struggling due to low consumer demand fueled by their faltering real estate market and continually contracting factory activity[12]. Sailings through the Panama Canal will be restricted through at least February. High fuel prices for the world’s second-largest economy could potentially have ripple effects around the
The carbon footprint of electric forklifts: a Cradle-to-Grave analysis
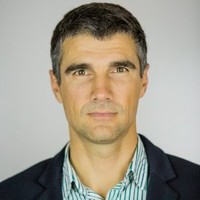
Green Logistics The logistics and transport sector (operating commercial and industrial trucks and forklifts) contributes just over a third of global carbon dioxide (CO2) emissions, making it the largest-emitting sector in numerous developed countries. And that share keeps growing. We are relatively well-informed about the cradle-to-grave CO2 emissions of passenger cars. Even though battery-powered industrial trucks have a 70% share of the US market, there is little information about the carbon footprint of electric forklifts in terms of a full life cycle analysis (LCA). We will address this gap in this article. While passenger EVs are idle 95% of the time, forklifts are moving loads throughout 2–3 work shifts, up to 20 hours a day! High utilization of electric equipment drives up the share of emissions from the use of electric energy (Scope 2) to over 90%, even with zero tailpipe emissions (Scope 1). Emissions from the manufacturing of both a forklift and a battery (Scope 3) account for an estimated 9% of its total carbon footprint. LCA of Electric Forklift Carbon Emissions Electric industrial trucks offer several environmental benefits and can significantly reduce the carbon footprint of warehouses and distribution centers. However, these operations are not net-zero just yet, and the US companies are required by law to track and report their emissions. The total sum of emissions from any vehicle comes from the three main categories: tailpipe emissions (Scope 1, a direct result of operating the equipment), zero in the case of electric forklifts; emissions from the generation of energy used by a vehicle (Scope 2), in our case—electricity; emissions from the manufacturing of the industrial truck (Scope 3), including manufacturing of the battery, mining, and refining of key components (steel, copper, battery metals, plastics, etc.). It’s the Law! The United States requires facilities that emit at least 25,000 metric tons of carbon dioxide (CO2) per year to report greenhouse gas emissions to the Environmental Protection Agency (EPA). This requirement to report Scope 1 emissions has been in place since 2009. California’s Senate Bill 253, known as the Climate Corporate Data Accountability Act, requires companies with over $1 billion in annual revenue to publicly report their Scope 1, 2, and 3 greenhouse gas (GHG) emissions starting in 2026 (for 2025). This is pivotal, as scope 3 emissions often account for more than 90% of an organization’s climate impact and are notoriously difficult to measure. The bill stipulates that companies will have to submit emissions calculations to a digital reporting platform, and they must make disclosures easily comprehensible to residents, investors, and other stakeholders. They will also be required to hire independent auditors to verify their reported emissions. It will take time, but chances are that this practice will eventually be adopted in the rest of the USA. Energy Use With zero tailpipe emissions, electric forklifts are a more sustainable alternative to their fossil fuel counterparts. However, it is important to recognize that their environmental impact extends beyond just the operational phase. CO2 emissions from the production of electric power used by forklifts represent the lion’s share of their total CO2 footprint. With passenger EVs, manufacturing of the car and the battery reaches 34% of the total emissions (calculated for a 16-year lifespan or 160,000 miles), and energy use adds the other 66%. According to the model used by the European Rental Association, generating the electric energy to charge a forklift’s battery exceeds 90% of its total carbon footprint (calculated for a 10-year lifespan). Both calculations are based on the average CO2 emissions from electricity-generating plants in the US, but the reality is more nuanced. Ten percent of the electricity generated in the US in 2023 comes from renewable sources, and power plants that still rely on fossil fuels differ dramatically: coal generates about twice the amount of CO2 as natural gas does. California and Texas have massively increased the share of renewables in their energy portfolio, while Arkansas still gets over 35% of its electric power from burning coal. The bottom line is that a forklift’s carbon footprint will differ dramatically from state to state, depending on the technology of electricity generation. Steel Another part of the CO2 footprint associated with forklifts comes from the manufacturing stages. Both the forklift itself and the battery used as its power source require resources and energy, and involve high emissions-generating processes, from mining and refining raw materials to assembling various components. We based our calculations on the specifications of a Hyster E70XN electric forklift with a chassis-integrated lithium battery. The total truck weight without a battery is 7500 pounds, at least 7000 pounds (roughly 3.5 tons) of which is steel. Globally, producing steel generates as much as 9 % of human-caused CO2 emissions every year—more than any other heavy industry, including cement and chemical production. Typically, integrated (coal-burning) steelmaking generates nearly 2 metric tons of CO2 emissions for every metric ton of steel produced. However, about 70 percent of America’s steel today is made in over 100 electric-arc furnaces, while roughly 30 percent of steel is produced in integrated mills. In the rest of the world, the story plays out in reverse: About 70 percent of global steel production is made in coal-hungry furnaces, while 30 percent comes from melting scrap metal. When it comes to curbing CO2, scrap-based steelmaking has a clear advantage. According to the Steel Manufacturers Association 2022 report, America’s electric-arc furnaces generate about 0.37 metric tons of CO2 for every 1 metric ton of crude steel they produce, or roughly three-quarters less than primary steelmaking. Recycling and Repurposing Lastly, the disposal of electric forklifts at the end of their life cycle must be managed responsibly to minimize their environmental impact. Fortunately, many manufacturers and industry organizations have established recycling and battery repurposing programs. By participating in these programs, companies can actively contribute to reducing the environmental impact of electric forklifts throughout their life cycle, and the model we used shows a 2% reduction of the total emissions with an average “best practice” approach to recycling. LCA of Electric Lithium Battery-powered Forklift CO2 Footprint We used the European Rental Association CO2 calculator to estimate the total footprint of a Hyster E70XN model of an electric lithium industrial truck. The calculations are based
AIT Worldwide Logistics acquires European life sciences specialist Mach II Shipping Ltd
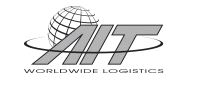
Deal includes global partner network, highly accredited locations in Netherlands, United Kingdom AIT Worldwide Logistics has acquired Mach II Shipping Ltd, a U.K.-based freight forwarder specializing in worldwide distribution of pharmaceuticals and related products. The deal includes a subsidiary in the Netherlands in addition to a global network of life sciences partners. According to AIT’s Executive Vice President, Life Sciences, Chris Amberg, the acquired company (commonly known as Mach 2 or Pharmafreight) has earned a reputation for extremely high-quality shipping solutions in the demanding life sciences industry, including transportation programs for clinical trials, active pharmaceutical ingredients (APIs), pharmaceutical machinery, and finished products. “In addition to temperature-controlled air freight, Mach 2 provides outstanding dedicated road service for high-value life sciences moves throughout Europe with a managed fleet of temperature-controlled vehicles operated by Good Distribution Practices-trained independent contractors,” Amberg said. “Additionally, their value-added services include in-house customs clearance and a temperature-controlled warehouse in Ashford, Middlesex, near London Heathrow Airport.” Services at the Ashford location are mirrored by a second office in the Netherlands, opened in 2019 as a response to the United Kingdom’s withdrawal from the European Union. Customers requiring a post-Brexit alternative to working in the U.K. receive the same top-quality standard of service from the Nieuw-Vennep office, located just minutes away from Amsterdam Airport Schiphol, while avoiding Brexit-related customs or regulatory challenges. The Netherlands facility features an ultra-low temperature (ULT) freezer farm, safely and securely storing oncology products at below -60°C. Mach 2’s global Pharmafreight partner network is also included as part of the acquisition. Formed in 2000, the network has grown over the past two decades under the leadership of Mach 2 Shipping Commercial Director, Andy Hughes. As a result of careful recruitment and vetting, Pharmafreight is a first-rate collective of audited, approved independent freight forwarders operating under Good Distribution Practices in 30 countries across Africa, Asia, Europe, North America, and South America. In addition to promoting best practices for total quality across the network, Pharmafreight ensures consistent quality with international partner training (including GDP training) and a global sales call program to boost cooperation between network partners. “Our teammates across Mach 2 and Pharmafreight are eagerly continuing to provide stable, high-quality service for our customers as we prepare to integrate fully with AIT in 2024,” Hughes said. “This acquisition is providing a phenomenal opportunity to enhance our solutions for customers as we tap into AIT’s vast worldwide network.” “I’m delighted to welcome Mach 2 and Pharmafreight teammates to the company,” said AIT’s President and Chief Operating Officer, Keith Tholan. “Their well-tenured expertise provides an instant boost to our world-class Life Sciences Division, and we look forward to elevating cold chain service for our customers, especially in Europe.” In addition to being Authorized Economic Operator and Good Distribution Practices certified, the Mach 2 United Kingdom office is one of just 20 forwarders with Wholesale Distribution Authorization (WDA) granted from the U.K.’s Medicines and Healthcare products Regulatory Agency (MHRA). Likewise, the Netherlands location is one of only 15 forwarders to earn API storage registration; it has also obtained Japanese Foreign Manufacturer Accreditation, and the facility will soon hold its own Dutch WDA and Manufacturers Import Authorization (MIA) license. Terms of AIT’s acquisition of Mach II Shipping Ltd have not been disclosed.
Rental Hall of Fame inductees announced
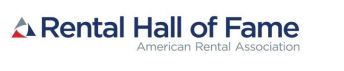
Each year, the American Rental Association (ARA) honors individuals for outstanding service to the association and the rental industry. This year, two longtime rental industry leaders will become the newest inductees into the Rental Hall of Fame and will be honored at The ARA Show™ 2024 in New Orleans. The Rental Hall of Fame was created in 2000 to honor those individuals who have changed the trajectory of the equipment and event rental industry. Each year, nominations are accepted to recognize outstanding industry leaders who have made a substantial and lasting impact on the industry’s success and growth at the national and/or international level. “The Rental Hall of Fame is ARA’s most prestigious award. This year, we recognize two individuals whose contributions made a significant impact on growing the equipment and event rental industry. Their dedication has been felt across the rental community and we look forward to bestowing them with the rental industry’s highest honor,” says Tony Conant, ARA CEO. Bruce Campbell, Do It Best Corp., Fort Wayne, Ind. Bruce Campbell, an equipment rental industry veteran began his career in 1968 in Fort Wayne, Ind., as an employee of an independent rental store. In 1974 he relocated to the Cincinnati area. Then in 1984, he founded L&B Equipment Rental in Harrison, Ohio. As a rental operator, Campbell served a term as vice president of the ARA of Ohio and two terms as president of the Greater Cincinnati Tool Rental Association. In 1989, he earned an ARA President’s Image Award for L&B Equipment Rental. Campbell sold his rental business in 1992, retired, and became a rental consultant. In 1994, Campbell was instrumental in the launching of a rental program for Do it Best Corp., then known as HWI (Hardware Wholesalers, Inc.). Do it Best Corp., a cooperative that supplies products and services to independent hardware, lumber, and home improvement retailers, was looking for an expert with rental knowledge to help develop the program. Campbell contributed his consulting services to the initiative and helped many Do it Best Corp. members become successful rental operators. Campbell helped create the Do it Best Rental School – a member education event through which he provided extensive knowledge of equipment, procedures, safety, the latest trends and strong financial knowledge. Through this program, Campbell aimed to instill high standards and the importance of product quality, inventory and customer service. Over the years, Campbell has worked to continuously enhance the Do it Best Rental School’s curriculum and offerings. Along the way, he has served as an invaluable resource for learning all aspects of the rental industry for program members across the U.S. and abroad. Campbell also strongly advocates for his Do it Best Rental School students to become active in ARA both locally and nationally. Jay D. Chapin, Taylor Rental Corp., Springfield, Mass. The late Jay D. Chapin of Westfield, Mass., past president and co-founder of Taylor Rental Corp., began working at Dealer Supply Co. in 1959, the same year that the organization put together the first Taylor Rental franchise. He became vice president of Dealer Supply Co. in 1963. Chapin was named company president in 1971, and in 1972 Dealer Supply Co. became Taylor Rental Corp. Seven years later, there were 626 Taylor Rental Centers (TRCs) in full operation in 49 states in the U.S. As president of the organization, Chapin helped family owned, small-business entrepreneurs prosper by backing them with the knowledge, experience and opportunities that a major corporation could provide. Under Chapin’s leadership, Taylor Rental Corp. was at the forefront when digital information was in its infancy in the rental industry. In the late 1970s, he introduced TOPIC–the TRC equivalent of Taylor Rental Corp.’s proprietary point-of-sale computer system, CompuRent. In 1982, he made CompuRent available to independent rental outlets. During his career, Chapin developed many products, programs and services that enabled TRC franchises to grow and expand the rental concept in communities throughout the U.S. He instituted a team of business management consultants to provide on-site guidance and support to franchisees, developed private-label products to enhance brand recognition, created in-store designs and signage, built a 100,000-sq.-ft. warehouse to allow for faster delivery of products to franchisees, and instituted national advertising programs. Chapin also encouraged TRC members’ involvement in ARA.