ALL Crane acquires two Faymonville HighwayMAX heavy-haul trailers
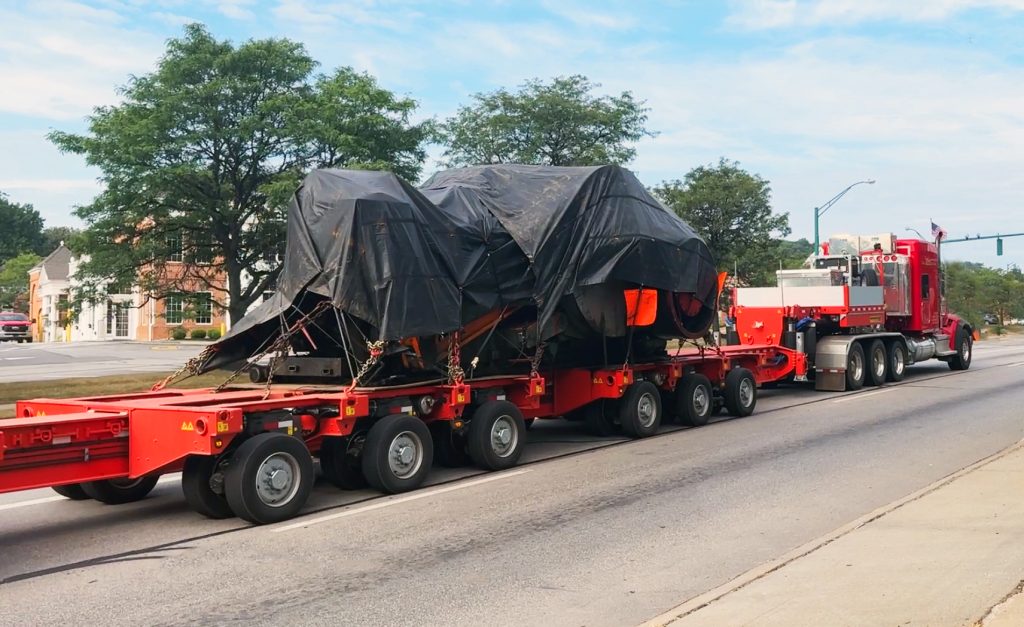
Nine-axle extendable trailers haul up to 170,000 pounds; available for rent The ALL Family of Companies has added two innovative heavy-haul trailers to its own trucking fleet and is making them available for rent to fulfill customers’ own heavy-hauling needs. ALL initially purchased the two Faymonville HighwayMAX trailers to carry the tracks for two newly acquired crawler cranes, the Liebherr LR 11000 and Liebherr LR 1800, but soon realized the trailers could be useful for other markets as well. The HighwayMAX is a nine-axle extendable highway trailer with nine hydraulically steered pendle-axles and a legal payload of up to 170,000 pounds (249,000-pound technical payload). Axle spacing is adjustable by up to 22.5 feet between each three-axle group, and each axle steers independently at 60 degrees for ultimate maneuverability in tight spaces. All axles are liftable. Faymonville is a European company, known for blending heavy industrial manufacturing expertise with technical know-how and cutting-edge technology. Their accompanying software package allows loads and trailer configurations to be planned in advance, much the same way 3-D lift planning for cranes enables ALL to design, plot, and practice lifts in the virtual world. “We’re able to simulate the load to make sure the axles are carrying an even amount of weight,” said Brian Meek, sales representative with ALL. “Because axle spacing and load limits vary by state, the HighwayMAX provides ultimate flexibility.” By combining technology with practical development, quality manufacturing, and innovative features, the new trailers offer great versatility, payload capacity, maneuverability, and quick mobilization. This versatility is expected to earn it many fans. “It will be in demand for transporting large industrial equipment, as well as work at steel mills and wind farms,” said Jimmy Hill, logistics manager for ALL. “For many of our customers, they will find that anywhere they thought they needed a Goldhofer, they can use the HighwayMAX.” One of the trailers already had its maiden voyage, transporting a 170,000-pound bolt press from Brecksville, Ohio, to Alsip, Ill. Other heavy-haul jobs have come in just through word-of-mouth. “Faymonville trailers are still fairly rare in the U.S.,” said Hill. “Once people see what they’re capable of, they’re interested in trying them out.”
AutoScheduler.AI adds Jordan Lawrence to Lead Commercial Strategy
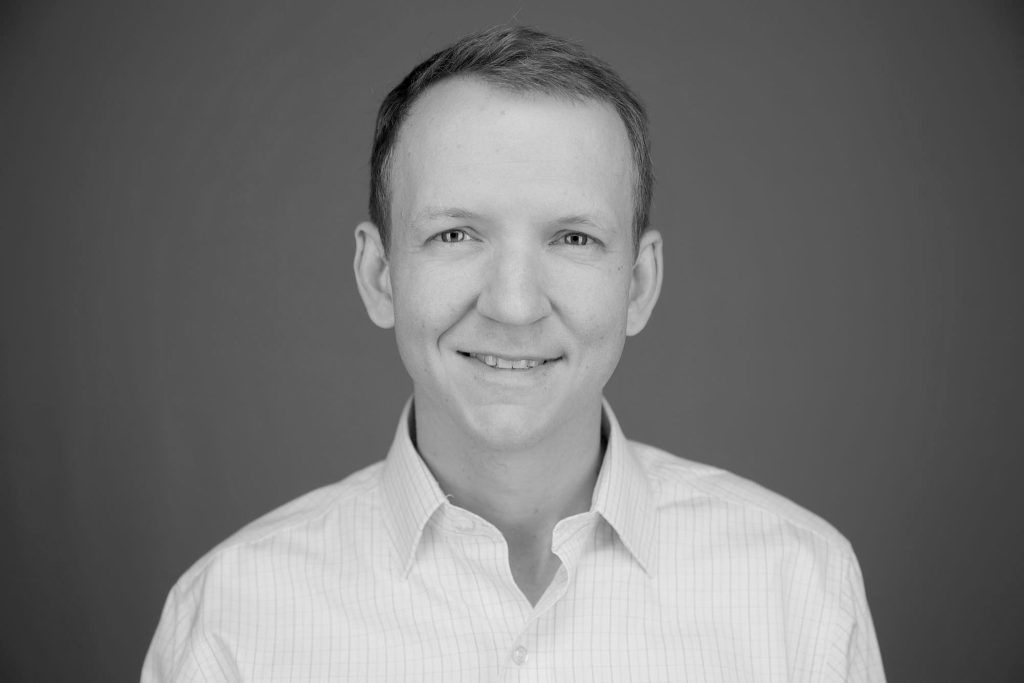
15 Plus Years of Experience in Enterprise Sales and Supply Chain Leadership AutoScheduler.AI has announced that it has added Jordan Lawrence as Vice President, Commercial Strategy, to broadly support the go-to-market strategy for its fast-growing warehouse orchestration platform. Jordan brings over 15 years of enterprise sales and supply chain leadership across distribution, manufacturing, transportation, and logistics technology. “Jordan Lawrence has extensive and robust experience supporting Fortune 500 supply chains with services and technologies that drive scaled execution,” says Keith Moore, CEO of AutoScheduler.AI. “He has the proven ability to positively impact clients by helping them improve efficiencies and grow their bottom-line profits. His deep experience and proven track record make him an ideal leader for our team.” As Vice President of Commercial Strategy, Jordan will help shape and scale AutoScheduler to continue reaching its growth targets. He will work closely with clients to understand their current challenges and then deliver appropriate solutions that create value in the supply chain. Jordan will also provide organizational feedback, including sales, marketing, and product/tech, based on client input and industry best practices to maximize revenue growth and improve market share. “I look forward to working for this best-in-class organization to develop new market opportunities, customer segments, and potential partnerships,” says Jordan Lawrence, Vice President, Commercial Strategy at AutoScheduler.AI. Previously, Jordan held several leadership positions at Flexe, a managed outsourced logistics solution provider for Fortune 500 Enterprise clients. He also worked for C. H. Robinson as a key account manager managing client and third-party relationships. He graduated from East Carolina University with a BS in Business Administration, Marketing, and Business.
Raymond celebrates 150,000 submitted Kaizens

An intentional approach empowers associates to foster a continuous improvement culture The Raymond Corporation has hit a milestone in its mission to drive a culture of continuous improvement, as employees have reached their goal of filing over 150,000 kaizens. Previously, in 2024, the Greene location celebrated operations, hitting 100,000 submitted kaizens. Kaizen is based on the idea that small changes over time will result in significant improvements. Raymond has seen a positive shift in employee engagement since the 2006 introduction of the program, plus the additions of functions in the corporate office, Muscatine, Iowa, and Syracuse, New York. “I am incredibly proud of our team’s dedication to continuous improvement and the innovative spirit that propels us forward,” said Michael Field, president and CEO of The Raymond Corporation. “Our monthly kaizen submissions are a testament to the hard work and creativity of our employees, reflecting our unwavering commitment to excellence in everything we do. I also want to acknowledge the invaluable support our Solutions and Support Centers provide to our customers and the continuous improvements they bring to their operations by implementing Raymond Lean Management (RLM).” The goal of kaizen is to simultaneously strengthen processes to create increased customer value and develop associates — allowing them to remove frustration and provide more time for value creation. Kaizen is a critical component of RLM and fosters respect and teamwork, as well as creates a challenge and go-and-see mindset, within the organization. “Kaizen has played an instrumental role in developing our employees and fostering a culture of continuous improvement fueled by open communication,” said Tony Topencik, vice president of operations, quality, and EHS, The Raymond Corporation. “Kaizen empowers our employees who know the job best to openly communicate ideas to improve the work done in their department and the entire business.” Since 2006, over 5,100 associates have submitted at least one kaizen. With nearly 60% of the workforce being with the company for less than five years, Raymond has found it is critical to engage associates early in their careers to create a continuous improvement mindset. With an 87% implementation rate, a kaizen in Raymond’s corporate office has a median savings of 4.25 hours. Raymond utilizes the statistics from the kaizen program to refine the company’s continuous improvement journey further. As an enterprise, Raymond celebrated 100,000 kaizens in September 2019 and currently has, on average, 865 kaizens submitted monthly. “Based on our recent research, kaizen participation is the leading indicator for driving a culture of continuous improvement. It builds confidence with associates on being engaged and empowered to constantly improve our standards — therefore, creating more value for our customers,” said Justin Sturek, continuous improvement manager at The Raymond Corporation. “We focus our efforts to coach, teach and develop all of our associates to refine their problem-solving capabilities so they are able to become fully proficient in their lean management journey.” Each month, Raymond’s leadership, with the goal of highlighting employees’ work, selects four implemented kaizens to highlight during a presentation by the submitters’ direct supervisors. The submitters can talk about their work and receive special recognition. “In order to foster a culture of continuous improvement, it is important that we celebrate it and bring visibility to excellence at every level of our organization. Monthly kaizen reviews and implemented kaizens provide us with a platform to recognize our team members who are dedicated to hard work, innovation and truly embody our culture of continuous improvement,” said Dave Norton, vice president of customer solutions and support, The Raymond Corporation. “We want our employees to have a rewarding career in a culture in which they can feel trusted, respected and valued. Kaizens are just one way we ensure we are living up to this culture.” To learn more about Raymond’s continuous dedication to improvement or the Raymond Lean Management System, visit https://www.raymondcorp.com/optimization/lean-management.
U.S. Rail Traffic report for the Week Ending September 18, 2024
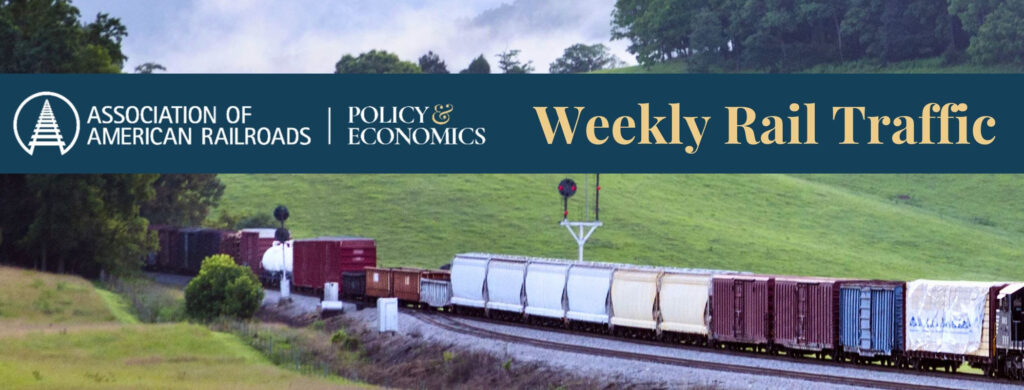
The Association of American Railroads (AAR) has reported U.S. rail traffic for the week ending September 14, 2024. For this week, total U.S. weekly rail traffic was 522,557 carloads and intermodal units, up 6.8 percent compared with the same week last year. Total carloads for the week ending September 14 were 232,154 carloads, down 0.0 percent compared with the same week in 2023, while U.S. weekly intermodal volume was 290,403 containers and trailers, up 13.0 percent compared to 2023. Seven of the 10 carload commodity groups posted an increase compared with the same week in 2023. They included grain, up 3,048 carloads, to 19,372; miscellaneous carloads, up 1,837 carloads, to 10,781; and farm products excl. grain, and food, up 820 carloads, to 17,227. Commodity groups that posted decreases compared with the same week in 2023 were coal, down 5,797 carloads, to 63,017; nonmetallic minerals, down 1,853 carloads, to 32,020; and chemicals, down 310 carloads, to 32,444. For the first 37 weeks of 2024, U.S. railroads reported cumulative volume of 8,012,176 carloads, down 3.3 percent from the same point last year; and 9,641,820 intermodal units, up 9.5 percent from last year. Total combined U.S. traffic for the first 37 weeks of 2024 was 17,653,996 carloads and intermodal units, an increase of 3.3 percent compared to last year. North American rail volume for the week ending September 14, 2024, on 9 reporting U.S., Canadian and Mexican railroads totaled 338,817 carloads, down 0.8 percent compared with the same week last year, and 374,207 intermodal units, up 9.8 percent compared with last year. Total combined weekly rail traffic in North America was 713,024 carloads and intermodal units, up 4.5 percent. North American rail volume for the first 37 weeks of 2024 was 24,587,434 carloads and intermodal units, up 2.6 percent compared with 2023. Canadian railroads reported 91,036 carloads for the week, down 1.3 percent, and 71,170 intermodal units, down 0.3 percent compared with the same week in 2023. For the first 37 weeks of 2024, Canadian railroads reported cumulative rail traffic volume of 5,853,653 carloads, containers and trailers, up 0.2 percent. Mexican railroads reported 15,627 carloads for the week, down 8.9 percent compared with the same week last year, and 12,634 intermodal units, up 2.1 percent. Cumulative volume on Mexican railroads for the first 37 weeks of 2024 was 1,079,785 carloads and intermodal containers and trailers, up 4.8 percent from the same point last year.
Episode 521: Transforming perishable fulfillment with GRIP
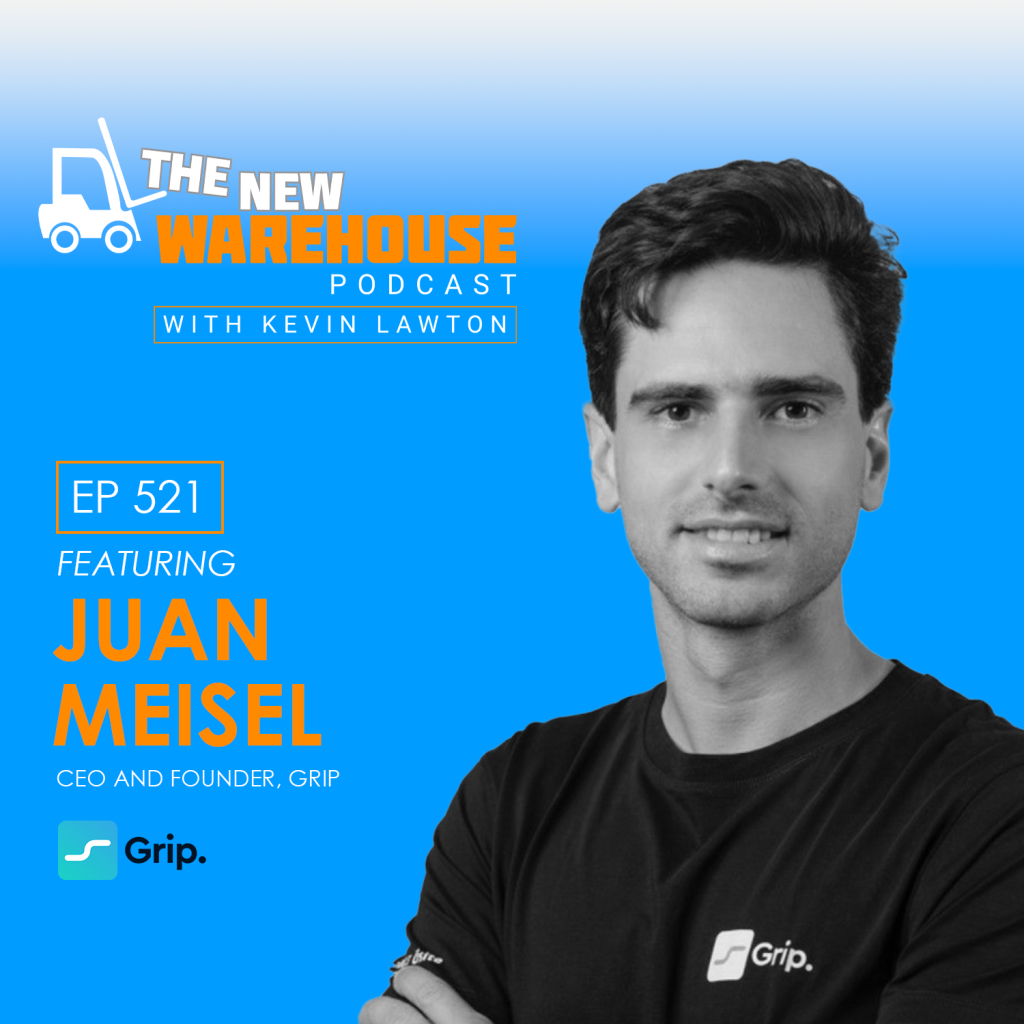
In this episode of The New Warehouse Podcast, we welcome Juan Meisel, the founder and CEO of GRIP, a company specializing in perishable fulfillment services. Juan shares his journey to founding GRIP to solve perishable fulfillment problems on a larger scale. For example, GRIP’s powerful shipping engine optimizes the delivery process for temperature-sensitive products. Tune in as we dive into the unique obstacles of perishable logistics and how GRIP’s innovative technology is making a difference. Overcoming Perishable Fulfillment Challenges GRIP’s journey began with the realization that traditional logistics solutions weren’t ideal for shipping perishable goods. Juan highlights the importance of ensuring that products like frozen meat arrive in perfect condition. Also, any failure could lead to substantial financial losses and customer dissatisfaction.“Every single one of these boxes that are frozen, if you don’t deliver it how you’re supposed to, you have to either reship or refund,” Juan explains, emphasizing the high stakes involved. GRIP’s shipping engine, developed through years of experience, dynamically adjusts shipping parameters based on real-time data. By incorporating temperature and transit times, GRIP can maximize the likelihood of successful deliveries. Integrating Perishable Fulfillment with Cutting-Edge Technology Recognizing the need for a comprehensive solution, GRIP expanded its services to include end-to-end fulfillment. Additionally, customers asked for a unified system that could handle everything from order processing to final delivery. “We quickly realized that for this to be a complete game changer and like industry enabler, we just have to do all the fulfillment for it as well,” Juan notes. GRIP’s platform now integrates order management, shipping, and fulfillment under one roof, allowing brands to focus on their strengths while GRIP handles the complexities of logistics. Furthermore, this approach streamlines operations and provides clients with the data-driven insights necessary to make informed decisions about their supply chain. The Future of Perishable Fulfillment As GRIP continues to grow, the company is looking toward the future of cold chain logistics, emphasizing faster and more accurate decision-making. Juan envisions a future where technology, particularly AI, plays a central role in anticipating and responding to challenges before they impact the customer. “The more AI that you have available, the better algorithms that you have to make all these decisions, then the faster and more accurate decisions you can make,” he predicts. By combining advanced data analytics with hands-on operational expertise, GRIP aims to set new standards in the industry for shipping perishables. Key Takeaways GRIP addresses the unique challenges of perishable logistics, especially in ensuring the successful delivery of temperature-sensitive products. The company’s shipping engine dynamically adjusts shipping variables based on real-time data to maximize delivery success. GRIP offers a comprehensive, integrated platform that handles everything from order processing to fulfillment, allowing brands to focus on their core strengths. GRIP plans to leverage AI and advanced analytics to enhance decision-making and operational efficiency in cold chain logistics. The New Warehouse Podcast Episode 521: Transforming Perishable Fulfillment with GRIP
New features for JLG® electric lifts and more
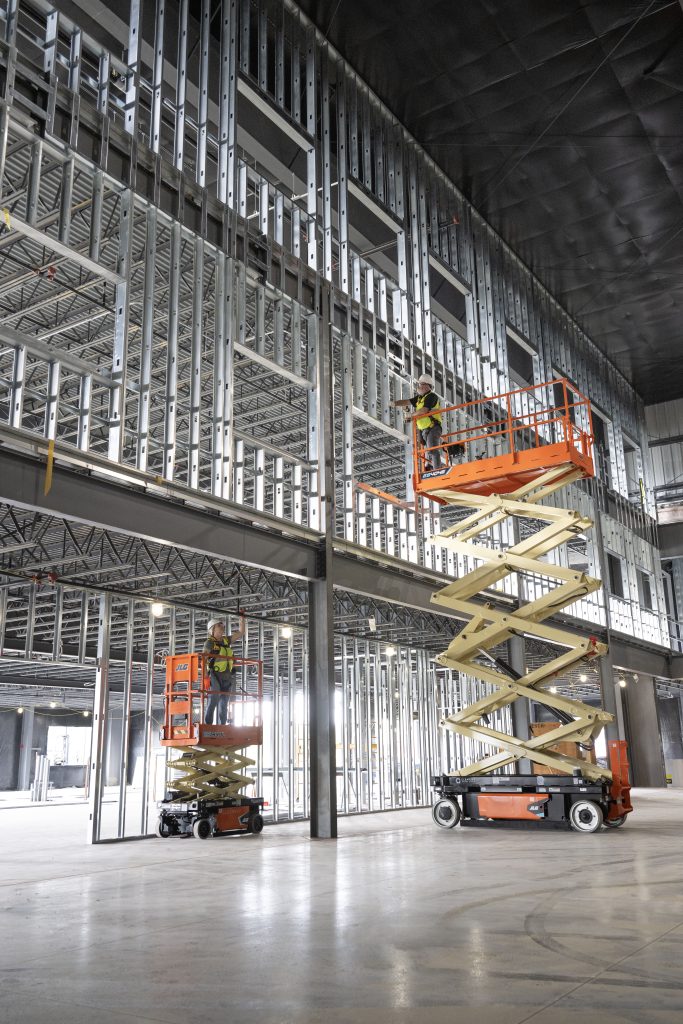
JLG Industries, Inc. has introduced new features and options on its line of ES electric slab scissor lifts, ERT electric rough terrain scissor lifts, E18 drivable vertical lifts, and E18 drivable stock picker. Updates to the JLG lines include standard AC drive motors, lithium-ion battery options and a range-extending genset charging option to enhance the models’ productivity, efficiency and versatility on job sites and around facilities. AC Drive Motors Now Standard When it comes to zero-emission or noise-controlled work sites, the JLG® ES line of electric scissor lift models meets the challenge. The ES1932, ES2632, ES2646 and ES3246 models now feature AC drive motors as standard equipment. These permanent magnet AC drive motors offer peak efficiency through lower energy consumption, require less battery draw and are virtually maintenance-free. JLG’s ES4046 and DaVinci™ all-electric AE1932 scissor lift models already come standard with AC drive motors. Lithium-Ion Battery Options Select JLG ES scissor lifts, E18 vertical lifts and the E18 stock picker can now be outfitted with lithium-ion batteries. Customers can choose between Lithium, which offers one battery on most models, and Lithium+, which provides an additional battery to amp up duty cycles. These new battery options offer zero performance degradation, fast charging capabilities and extended battery lifespan. Genset Option for ERT Models JLG has introduced a genset option for its electric rough terrain (ERT) scissor lift models. This 2610W, 58V, 45 Amp unit allows operators to recharge batteries anytime and anywhere, extending the range and increasing productivity and job site versatility. “JLG’s lifts are designed to work in various applications, from new construction to facility maintenance,” says Bob Begley, director of product management for JLG’s scissor lift, vertical mast lift, and low-level access lift product lines. “With these enhancements, JLG continues to offer solutions that meet the industry’s evolving needs, including requirements for zero-emission and noise-controlled work sites.”
Mid-Week dates and return of Future of Equipment Rental Planned for The ARA Show 2025
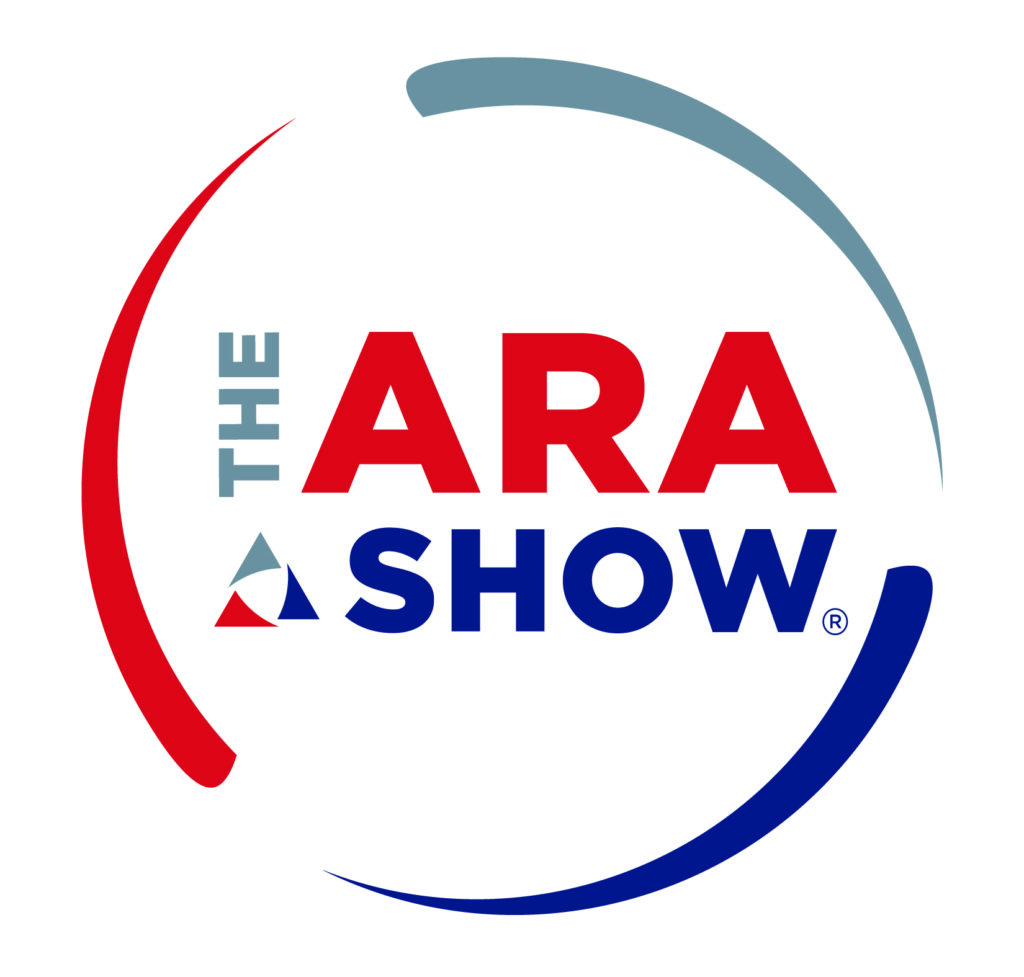
The ARA Show will return to the Las Vegas Convention Center in 2025, featuring a mid-week schedule and the Future of Equipment Rental. Registration for The ARA Show 2025 opens Tuesday, September 24. Register early to benefit from incentive pricing through October 8 and advance pricing through January 26. The American Rental Association’s (ARA) annual trade show is a can’t miss event for those looking to discover what’s next in rental. The trade show has a few twists in store with a shift to a mid-week schedule in 2025 and the return of Future of Equipment Rental. The schedule kicks off with Future of Equipment Rental on Tuesday, January 28; a full day of education sessions planned for Wednesday, January 29; and a three-day trade show will take place from Thursday, January 30 to Saturday, February 1. “We are excited to introduce a change in schedule for The ARA Show 2025 that will better accommodate our members and prospective members as they plan for a successful year ahead,” says Christine Hammes, Vice President of Association Services and Events. “The ARA Show continues to raise the bar on expectations each year, providing an unmatched combination of education sessions, networking opportunities, and a trade show that showcases the latest and greatest products and services for rental businesses.” Future of Equipment Rental — a full-day education and networking workshop for those in equipment rental — will be held on January 28. After a successful debut in 2023, the workshop returns with speakers and sessions focused on new technology and emerging trends for any size rental business. Future of Equipment Rental takes place one day before the start of The ARA Show and requires a separate registration fee. The ARA Show 2025 officially kicks off with a full day of education on Wednesday, January 29. The mid-week date is a change from the traditional schedule, but we will continue to offer exceptional sessions focusing on various relevant topics for rental professionals at every level. David Pogue will deliver the Keynote Session on Thursday, January 30. A technology expert and speaker, Pogue is a New York Times bestselling author of “Pogue’s Basics,” a series of essential tips and shortcuts, as well as several books in the “For Dummies” series and the “Missing Manual” series of computer books. He has been at the forefront of new and emerging tech trends for decades and will leave Keynote Session attendees informed about the state of science and technology today and how it’s shaping our future. The trade show floor will open immediately following the Keynote Session for two and a half days of product introductions and the latest innovations. An outdoor exhibit area will be located in the Diamond Lot next to the Convention Center West Hall. It provides space for equipment demonstrations and will include special attractions, food trucks, and more. Other featured networking events held throughout The ARA Show 2025 include the ARA’s Industry Awards Lunch, Regional Receptions, Breakfast hosted by Women in Rental, ARA Young Professionals Cocktails & Contacts, and The ARA Show Opening Reception, which will take place on Thursday, January 30. Advanced registration and ticket requirements may apply to select networking events. For complete show details, including registration and pricing information, visit ARAshow.org.
Cyclonaire welcomes Scott Berner as Channel Sales Manager
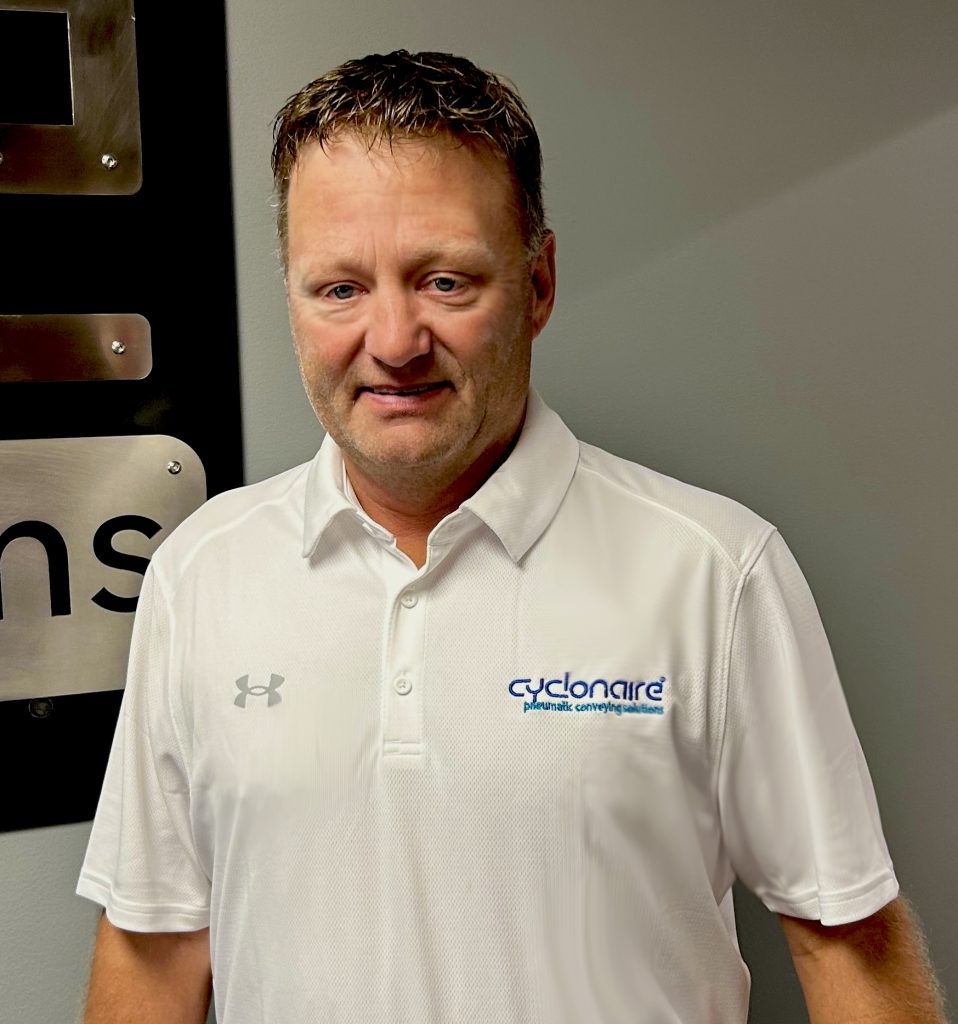
Cyclonaire has announced the appointment of Scott Berner as Channel Sales Manager. In this newly established role, Scott will lead our commercial relationships with Manufacturer Representatives and drive initiatives to enhance year-over-year sales of Cyclonaire systems. Scott brings a robust background to this position, with six years of experience at Cyclonaire and over 15 years in the bulk material handling industry. His previous roles at ASI, CST Storage, and STT Enviro Corp have equipped him with a deep understanding of the industry and a network of valuable connections. Scott’s return to Cyclonaire is marked by his extensive expertise and strong relationships with our Manufacturer’s Rep Network and key accounts. In addition to his new role, Scott will also take on the responsibilities of Business Development Manager for Cyclonaire’s Rail Sanding sector. His strategic vision and industry expertise make him an excellent choice for advancing our rail sanding initiatives. “Scott’s comprehensive understanding of the rail industry and his proven ability to drive results make him an outstanding addition to our team,” said Jay Anzelmo, Vice President of Sales and Marketing. “We are confident that his leadership will propel us to new achievements in the Rail Sanding sector and enhance the value we deliver to our clients.” Scott holds a degree from the University of Nebraska and is enthusiastic about contributing to Cyclonaire’s continued success. Please join us in welcoming Scott Berner to the team. We are excited about his leadership’s positive impact on our sales efforts and market presence.
Swisslog’s SynQ powered AutoStore solution to automate parts distribution for Komatsu’s Tennessee distribution center
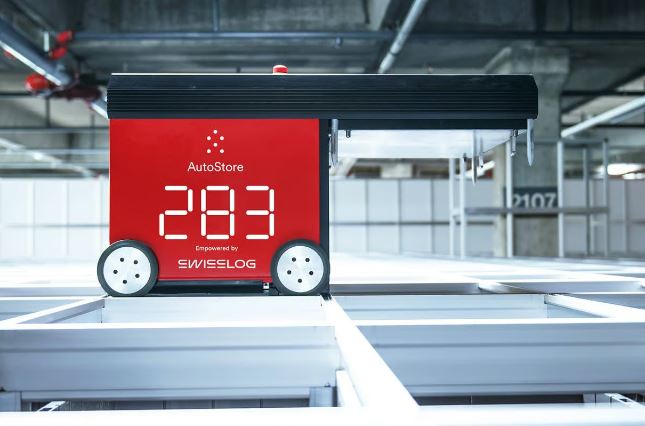
Swisslog, a provider of best-in-class warehouse automation and software, has announced that Komatsu will install a Swisslog automation solution within its Ripley, Tennessee, distribution center to meet its growing omnichannel distribution needs. Designed by Swisslog experts, the solution features the AutoStore system optimized by Swisslog’s SynQ software. It is expected to be operational by January 2025. The automation solution from Swisslog supports Komatsu’s emphasis on innovation and will enable its state-of-the-art parts and service program in the USA. It will be the second system globally with Swisslog’s integration of AutoStore and SynQ, with the first system being installed in Australia in 2024. The existing 685,00 square-foot Ripley, Tennessee distribution center is a critical hub for parts and equipment, containing parts needed for Komatsu’s heavy construction equipment. The automation solution, which comprises 16,000 bins and nine robots, is designed to help ensure timely delivery for its dealers and end customers. Swisslog automation experts worked with Komatsu to integrate the system into the existing facility and operations so that it would not interrupt existing operations. The automation solution to be deployed in the facility operates on Swisslog’s SynQ software. This software provides warehouse execution, material flow, and automation control system functionality in a single, modular platform. It can integrate seamlessly with existing warehouse management systems (WMS) to orchestrate the material flow. “We are thrilled to partner with Komatsu to automate its second distribution center globally with AutoStore and our SynQ software to help ensure fast turnaround times for parts delivery,” said Sean Wallingford, president and CEO of Swisslog Americas. “We designed the automation solution to easily grow as the need for capacity is expected to increase. The system helps ensure continuous operation as Komatsu expands capacity to handle more parts.” As an experienced integrator of AutoStore, Swisslog currently has over 400 AutoStore projects in over 26 countries.
Atlantic Forklift Services recognized as one of the fastest growing companies in North Carolina
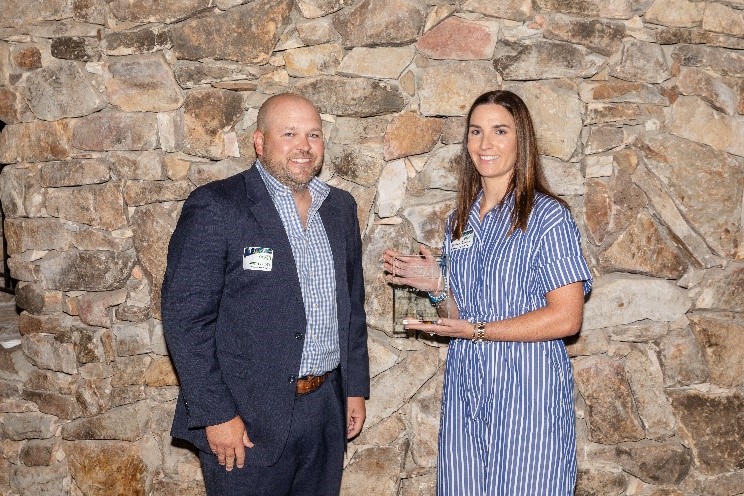
Atlantic Forklift Services was recently included on the 2024 North Carolina Mid-Market Fast 40 list. This is the fourth year in a row that they have been mentioned on this exclusive list. In addition, they were listed as #10, making it the highest ranking they have received since being included. This list recognizes middle-market companies in North Carolina for their entrepreneurial spirit and strong revenue growth. Cherry Bekaert verified that the Fast 40 companies were selected based on revenue and employment growth over the past three years. The companies’ annual revenue ranges between $10 million and $500 million. In recognition of this award, Keith Driscoll, President of Atlantic Forklift Services, said, “We are incredibly honored to receive this award for our growth. This recognition is a testament to the dedication and hard work of our entire team, whose commitment to excellence drives our success. Additionally, this achievement would not have been possible without the trust and support of our valued customers, who inspire us to continually improve and innovate. We are excited about the future and remain focused on delivering outstanding value to our customers and stakeholders.”
London Packaging Week unveils pioneering Innovation Award winners
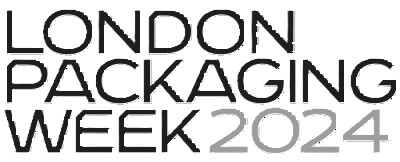
London Packaging Week’s Innovation Awards honour groundbreaking designs, including Bowmore ARC-52 Mokume, Highland Park’s 54-year-old decanter, Coca-Cola’s label-free Sprite Naked, and Altra’s groundbreaking Altra Box. London Packaging Week is thrilled to unveil the winners of its inaugural Innovation Awards, sponsored by Fedrigoni, celebrating groundbreaking advancements in packaging across various categories. This year’s awards recognize exceptional design, creativity, and sustainability in packaging solutions. In the Premium and Luxury Drinks categories, two exceptional winners have set new standards in packaging innovation. Bowmore ARC-52 Mokume triumphed in the Luxury category, while Highland Park’s 54-year-old decanter stood out in the Premium Drinks category. Both designs exemplify luxury and craftsmanship, reflecting the rich heritage and natural elements of their origins. These innovations push the boundaries of creativity and sustainability in their respective sectors, making them outstanding examples of premium drink packaging. In a collaboration with Aston Martin, Bowmore has crafted a decanter that is as much a work of art as it is a vessel for this exceptional whisky. The design takes inspiration from the Japanese metalworking technique ‘Mokume-Gane,’ known for its unique layered patterns. This technique has been reimagined through layered carbon fibre sheets, creating the decanter’s distinctive Mokume lid. The result is a lid that evokes a futuristic aesthetic and mirrors the natural black rocks of Loch Indaal, the home of the Bowmore Distillery. The Bowmore ARC-52 Mokume decanter, housing a rare 52-year-old Bowmore whisky, fetched an impressive £225,000 at a Sotheby’s auction, with proceeds directed to a fund bolstering Islay’s distilling industry. Bowmore was represented on the day by Malcolm Swindell, Strategic Innovation Lead at Suntory Global Spirits, who said: “As custodians of Bowmore, it’s so special to be recognized by the judges of London Packaging Week. Firstly, we’d like to thank our partners at Aston Martin. The two teams shared a vision to bring together the very best in technical expertise and creative thinking – to push boundaries and develop something truly special.” Highland Park’s 54-year-old single malt Scotch whisky exemplifies the pinnacle of artistry in premium and luxury drinks, blending rich history with cutting-edge design. The decanter, created by Senior Glass Designer Michael Rudak of Stoelzle Flaconnage, is a work of art. Crafted from heavy flint glass, the decanter features a conical punt at its base, a nod to the distillery’s mash tuns where the whisky-making process begins. The bottle’s surface is adorned with textural embossing that mimics the weathered strata of the Yesnaby cliffs, bringing the essence of Orkney’s landscape to life. This tactile design is not just visual but also a tribute to molten lava gradually forming the Orkney Islands, capturing the raw, untamed beauty of the natural world in glass. Complementing this exquisite decanter is the wooden coffret, designed and handmade by Glasgow-based craftsman John Galvin. Galvin sculpted the presentation box using Scottish oak to mirror the contours of Orkney’s cliffs, particularly the Yesnaby formations. Each box is unique, and colour variations are achieved through meticulous hand-blasting and fuming. Andrew Dietz, Packaging Technologist at Edrington, said: “Thank you to everyone. Thanks for honoring us with this award. I want to thank three suppliers that we collaborated with for this award. It’s John Galvin and John Galvin Designs, Michael Rudak, who was the bottle designer, and Stoelzle Flaconnage, who was the bottle supplier. I can’t forget JC Ribero, the closure manufacturer.” Coca-Cola Services NV’s Sprite Naked won the Food, Beverages, and Personal Care category for its innovative label-free bottle design. This groundbreaking approach leverages fibre laser technology to directly engrave product information onto 100% recycled PET (rPET) bottles, eliminating the need for traditional labels. By integrating rPET and removing labels, Sprite Naked simplifies the recycling process, making it more efficient and reducing packaging waste. The environmental impact of Sprite Naked is impressive, with Coca-Cola achieving a 98% reduction in the carbon footprint associated with the labeling process. This substantial decrease is attributed to the elimination of label production and adhesive use, which typically contribute to higher emissions. “It was quite a brave piece of work,” said Lisa Meade, Head of Structural Packaging at Kingfisher. “Here you have a very large company taking what I believe was a fairly bold step by removing all the color signals from the packaging. For the consumer, at the shelf and at the moment of purchase decision, they removed the labels and instead used embossing and debossing on the blow-molded bottle. I really like this pack for several reasons, but what stands out to me is that it was a really brave decision for them to do that and move away from the traditional design.” Winning the Beauty, Cosmetics, and Perfume Category, Altra’s The Altra Box continues to garner praise for its innovative and more sustainable approach to luxury packaging. This groundbreaking design is constructed from a single sheet of 100% recycled UK paper, replacing traditional packaging methods with a biodegradable, sturdy alternative. The box’s design features a pentagonal outer sleeve with specialized compartments for an empty glass flacon and a perfume refill, promoting sustainable home refills. This thoughtful design encourages consumers to opt for refills rather than discarding entire packages, significantly reducing waste and supporting a circular economy. Premium Drinks – 1 certificate and 1 winner: Certificate: Black Shuck Pineapple & Coconut Schnapps from Black Shuck LTD Winner: Highland Park 54-year-old from Erdington Luxury – 1 winner Winner: Bowmore ARC-52 Mokume from Bowmore Food, Beverages and Personal Care Category – 3 certificates and 1 winner Certificate: Indian Spice Tin with 9 Spices and Silk Sari Wrap from Spice Kitchen Certificate: Victoria Chocolate Creations from McVities Certificate: Club Zero Refillable Milk Bottles from Abel & Cole Winner: Sprite Naked from Coca-Cola Company Beauty, Cosmetics and Perfume Category – 3 certificates and 1 winner Certificate: All Weather Styling Gel & Soft Leave-in Cream Certificate: Skin Accumax from Advances Nutrition Programme Certificate: Skin Ultimate from Advances Nutrition Programme Winner: The Altra Box by Altra
US East Coast ports strike customer advisory, Container xChange
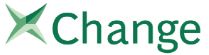
Implications of Looming labor strikes on U.S. container trade and supply chains Issued by Container xChange September is traditionally one of the busiest months for U.S. containerized imports, driven by the peak shipping season as businesses prepare for the holiday rush. However, this year presents an unprecedented combination of challenges that could heavily impact supply chains. Potential labor strikes, natural disasters, and tariff uncertainties are converging, creating a highly volatile environment for global trade. This also led to the pulling forward of orders by retailers, which led to strong inventories in the US. In August 2024, U.S. container cargo imports surged by 12.9% year-over-year, with major ports handling nearly 2.5 million TEUs. While this reflects strong freight demand, it also intensifies concerns as labor strikes loom on October 1st. “The possibility of strikes in US East Coast and Gulf Coast Port adds uncertainty for container shipping professionals doing business in the US,” shared Christian Roeloffs, co-founder and CEO of Container xChange. For container trading and leasing companies, these disruptions could lead to significant delays and port congestion, impacting equipment turnaround times. “Companies should anticipate short-term spikes in demand for leased containers as retailers rush to secure goods ahead of potential disruptions, particularly for seasonal inventory and industrial shipments,” Roeloffs further added. “While the threat of strikes looms large, it’s important to note that U.S. inventories are currently strong due to the pulling forward of orders earlier this year to avoid existing disruptions. This stockpile will act as an essential buffer, mitigating the risk of container rates spiking dramatically due to the strikes. Additionally, with no significant signs of peak season demand strengthening, these strikes might not have as intense an impact as historically seen. However, the overall impact will largely depend on the duration of the strikes, with prolonged disruptions having the potential to intensify the implications for supply chains, leading to more pronounced bottlenecks and greater challenges in container availability.” Shared Roeloffs. Potential U.S. Strikes on October 1st The International Longshoremen’s Association (ILA), representing more than 85,000 dockworkers on the East and Gulf Coasts of the U.S., faces a contract expiration on September 30, 2024. As negotiations with the United States Maritime Alliance Ltd. (USMX) show signs of breaking down, a strike now appears increasingly likely, threatening to disrupt nearly half of the nation's ocean trade. Maersk has already warned of severe disruptions, noting that even a brief strike could result in weeks of recovery due to accumulated backlogs. The uncertainty is compounded by the fact that the duration of these strikes is unclear—it could be resolved within weeks or drag on for months, as seen with the West Coast strike last year. “Leasing rates may rise sharply as importers seek to secure containers amid potential delays. In this environment, traders will need to diversify their partner networks, and sourcing strategies, and explore alternative ports to mitigate container shortages,” shared Roeloffs. A Volatile Market for Container Traders “September is usually crucial for U.S. containerized imports due to the approaching holiday season. However, this year presents compounded uncertainties,” Roeloffs commented. Beyond U.S. port strikes, other challenges such as geopolitical instability, Houthi attacks in the Middle East, and the restructuring of global shipping alliances are contributing to market volatility. Supply Chain Disruptions and Port Congestion In the event of labor strikes, East and Gulf Coast ports will experience congestion, delaying container turnarounds. Traders could face increased demurrage and detention fees as containers remain stuck at the port. The backlog of cargo could create equipment shortages, raising leasing rates as demand spikes. Some businesses may be forced to reroute shipments through alternative ports, adding logistical complexities and costs. These uncertainties will fuel market volatility for container trading companies, with unpredictable container prices and availability. Traders may have to adjust their sourcing strategies while maintaining flexibility to adapt to changing market conditions. Potential Impact on Customers Container Trading Companies: Expect fluctuating demand and availability of containers as trade routes realign and U.S. port operations face potential delays. Having alternative strategies for equipment sourcing will prove essential to mitigate bottlenecks. Container Leasing Companies: The expected surge in demand for container equipment during the peak season could drive leasing rates upward, especially in the event of prolonged labor strikes or storm-related disruptions. Planning for repositioning and anticipating changes in demand across regions will be key to maintaining business continuity. Preparing for Disruptions As U.S. container trading and leasing companies navigate these disruptions, we encourage close monitoring of the evolving labor negotiations, weather risks, and global shipping alliance restructuring. We anticipate short-term demand spikes, potential container shortages, and fluctuating leasing rates as the market reacts to these external pressures.
Cimcorp VP of Operations Anne Happonen recognized as a 2024 Women in Supply Chain Winner
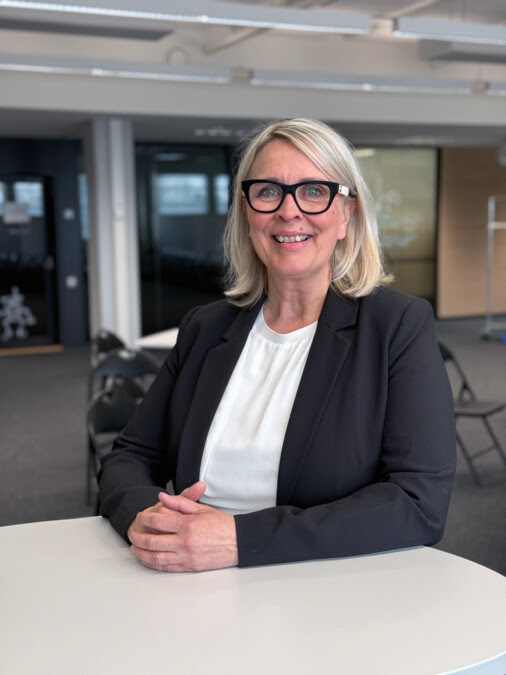
Cimcorp has announced its VP of Operations, Anne Happonen, has been named to the “2024 Women in Supply Chain” list by Food Logistics and Supply & Demand Chain Executive. The annual award honors female supply chain leaders and executives whose accomplishments and mentorship set a foundation for women at all levels of a company’s supply chain network. Anne earned the award for her extensive background in helping global organizations navigate the intricate landscape of international business. Over the last three decades, Anne has built a successful track record of leading and managing multicultural teams focused on delivering promises to customers and creating innovative new solutions. As VP of Operations at Cimcorp, Anne works with global clients in the fresh food distribution and tire manufacturing industries. She ensures that every automation project delivers customized automated solutions that help each customer optimize material flow, increase operational efficiencies, generate rapid ROI, and achieve long-term business success. “I’m truly honored to be included in the 2024 Women in Supply Chain list,” said Anne. “My approach to leadership is rooted in transparency, collaboration, and adaptability—key elements for cultivating a culture of openness and trust. I believe that active listening, engaging in meaningful discussions, and seeking common ground are vital skills for any leader. What drives me is building these relationships and seeing people take pride in their work.” Aligned with Cimcorp’s core company values, Anne’s “people-first” approach also helps foster a culture where safety is paramount. This approach to safety not only prevents accidents but also builds trust and satisfaction among employees and customers alike. “Every year, this award continues to amaze me. But this year especially, it’s all about the quality of the submissions. These women are doing remarkable things for their communities, organizations, and teams and are paving the way for future young female leaders to be a part of an industry that’s making a difference,” says Marina Mayer, Editor-in-Chief of Food Logistics and Supply & Demand Chain Executive and Co-Founder of the Women in Supply Chain Forum. “New this year, the award was broken down into Rising Stars, Trailblazers, DEI Pioneer and Workforce Innovator. From there, we named an overall winner per category and then four honorable mentions per category. This year’s applications were superb and made it next to impossible to just pick one winner. I’m so proud of these women and their achievements. We’re just getting started.”
Emerson to help drive greater industrial edge interoperability
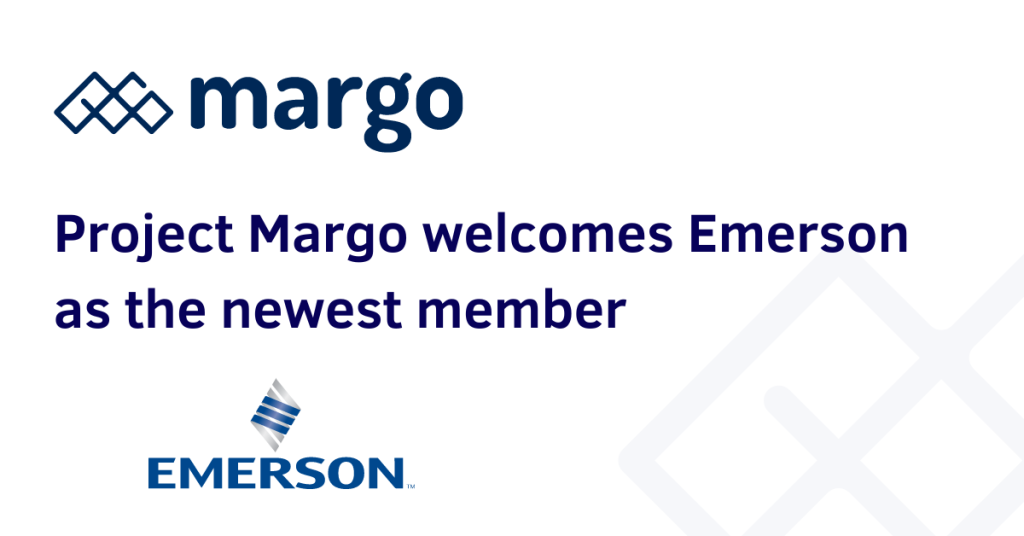
The company brings a deep legacy of driving industry standards to the Margo initiative, enabling more flexible, scalable automation for customers Global automation and technology provider Emerson joins the Linux Foundation’s Margo, a new open-standard initiative designed to make edge applications, devices, and orchestration software work seamlessly across multi-vendor industrial automation environments. As process and discrete manufacturers implement enhanced digitalization, they encounter challenges at the edge due to multi-vendor and multi-technology devices, apps, and orchestration environments that do not easily integrate. The Margo initiative addresses these challenges through the creation of practical reference implementations, open standards, and testing toolkits. This approach will help remove obstacles and simplify the process of building, deploying, scaling, and operating complex, multi-vendor industrial edge environments, helping manufacturers of all sizes build new and better digital operations or modernize existing ones. “The modern OT edge is the backbone of our next-generation automation architecture, enabling the availability of data and computing closest to where it is needed,” said Peter Zornio, Emerson’s chief technology officer. “Successful implementation will require open edge standards that will enable scalable, simplified, and seamless interoperability among applications, edge devices, and orchestration software – no matter the vendor technology. “Emerson is pleased to join the Margo initiative to help create a unified and cohesive edge management ecosystem. Our collective progress will make it easier, faster, and less costly for our customers to develop digital transformation programs that realize the full potential of AI, machine learning, and analytics at the edge.” The Margo initiative complements Emerson’s Boundless Automation™ vision for a next-generation, modern automation architecture designed to break down data silos and enable computing power where it is best suited, whether that’s in the field, edge, or cloud. Drawing its name from the Latin word for edge, Margo is supported by some of the largest automation providers globally. Emerson joins Margo as a steering member along with industry peers to develop open and secure edge interoperability standards for industrial automation ecosystems. The Margo project represents a significant industry collaboration to define mechanisms for interoperable orchestration of edge applications, workloads, and devices. It will deliver the promise of interoperability through an open standard, reference implementation, and comprehensive compliance testing toolkit. More details on the project can be found at margo.org.
KPI Solutions appoints Dean Starovasnik as Vice President Consulting Solutions
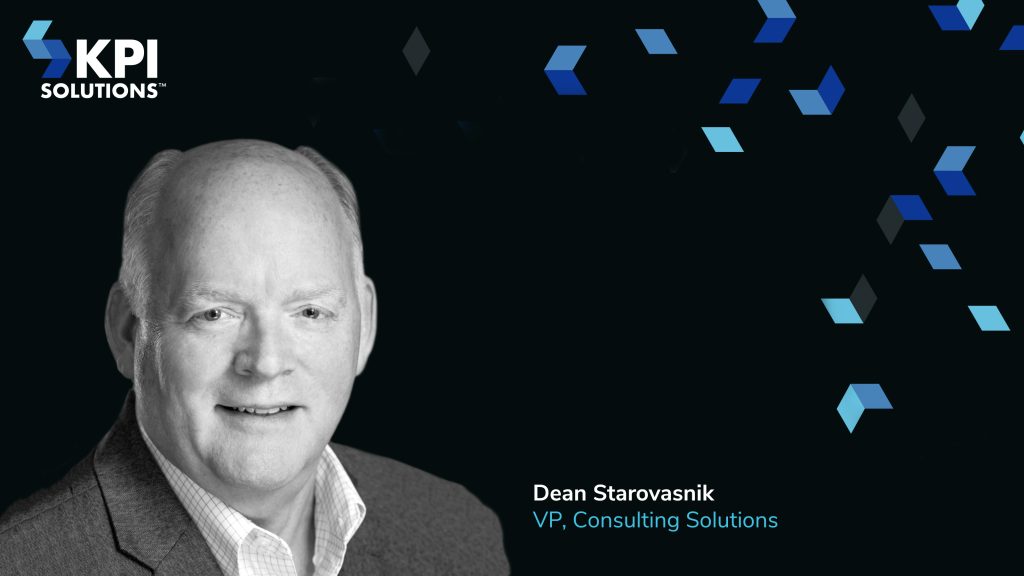
With 30 years of experience in the supply chain industry, he specializes in designing and implementing innovative and cost-justified distribution solutions KPI Solutions has announced that Dean Starovasnik has joined the company as Vice President, Consulting Solutions. In this role, Dean will partner with clients to understand their distribution objectives, and then create and deliver value-based strategic initiatives that enhance productivity and build resilience. He brings deep experience in a variety of industries including wholesale, retail, and eCommerce. “I’m happy to join KPI Solutions and help our clients solve complex supply chain challenges and navigate the many alternatives for warehouse design and automation,“ said Dean. “My background in end-to-end distribution projects allows me to bring a fresh perspective as we evaluate the best way to leverage a client’s investment in people, technology, and space to boost productivity and enable agility.” “Dean’s experience in transformative supply chain design and business case rationalization will bring value to our clients as we orchestrate innovative engineering with world-class automation technologies,” said Ron Adams, Chief Commercial Officer. “KPI’s clients will benefit from his broad yet analytical perspective that provides innovative and forward-thinking designs to achieve a company’s goals for efficiency, flexibility and scalability.” Dean joins KPI Solutions from enVista, where he was a Client Partner. Prior experience includes working in supply chain consulting and engineering at Bastian Solutions and Peach State Integrated Technologies. He earned his Bachelor of Science degree in aerospace engineering from the Massachusetts Institute of Technology and his Master of Science in space systems operations from the Naval Postgraduate School. He is a Professional Certified in Material Handling by MHI.
H&E Opens New Branch in Victoria, TX
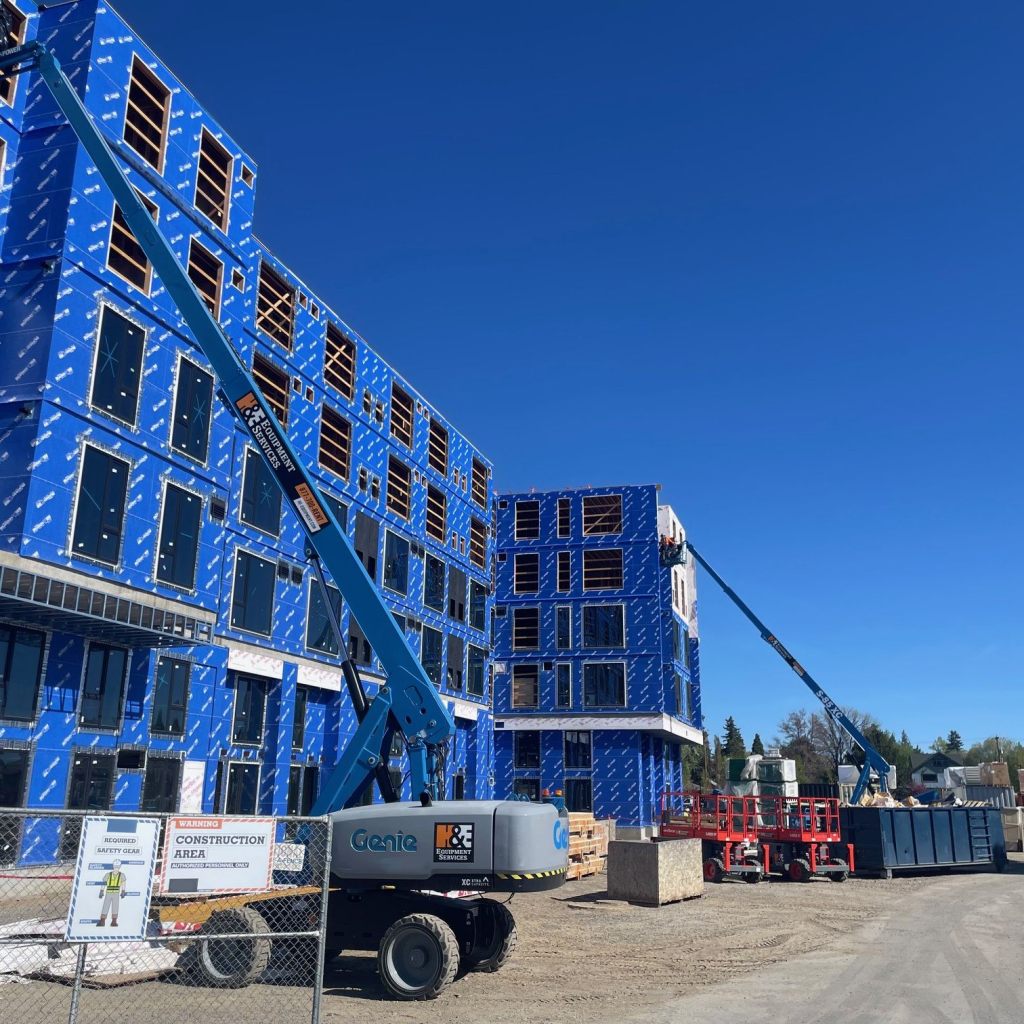
H&E Rentals announced the opening of its Victoria branch, the company’s 32nd location in the Lone Star State. It is also the 10th Texas branch added in the past two years. The facility is located at 159 Enterprise Drive, Victoria, TX 77905-3273, phone 361-412-4700. It includes a fully fenced yard area, offices, and a repair shop and carries a variety of construction and general industrial equipment. “The addition of a new branch in Victoria gives H&E total coverage of the Texas coast, and especially the growing market of Port Lavaca. We reach from lower Texas up toward our San Antonio branch, east toward our Freeport location, and west toward our Corpus Christi facility. Having several other H&E locations within reach allows us to source equipment from an expanded area fleet and provide whatever our customers need for their jobs,” says Branch Manager Brad Nicks. “Our facility is directly off Hwy 77 with quick access to highways 59 and 87 and I-69E, so we’re ready to deliver out to El Campo, Hallettsville, Cuero, Goliad, Refugio, and down to the Gulf.” The Victoria branch specializes in the rental of aerial lifts, earthmoving equipment, forklifts, telehandlers, compaction equipment, generators, light towers, compressors, and more. The fleet represents the following manufacturers: Allmand, Atlas Copco, Blue Diamond Attachments, BOMAG, Case, Club Car, Connect Work Tools, Cushman, Gehl, Generac Mobile, Genie, Hamm, Haulotte, Husqvarna, JCB, JLG, John Deere, Kobelco, Kubota, LayMor, Ledwell, Lincoln Electric, Link-Belt Excavators, Manitou, MEC, Miller, Multiquip, Okada, Polaris, Sany, Skyjack, SkyTrak, Sullair, Sullivan-Palatek, Tag, Towmaster, UniCarriers, Vacuworx, Virnig, Wacker Neuson, Yanmar, and others. Founded in 1961, H&E is one of the largest equipment rental companies in the nation, providing a higher standard in equipment rentals. Branches are located throughout the Pacific Northwest, West Coast, Intermountain, Southwest, Gulf Coast, Southeast, Midwest, and Mid-Atlantic regions.
Episode 520: 4PL Solutions from CBIP Logistics
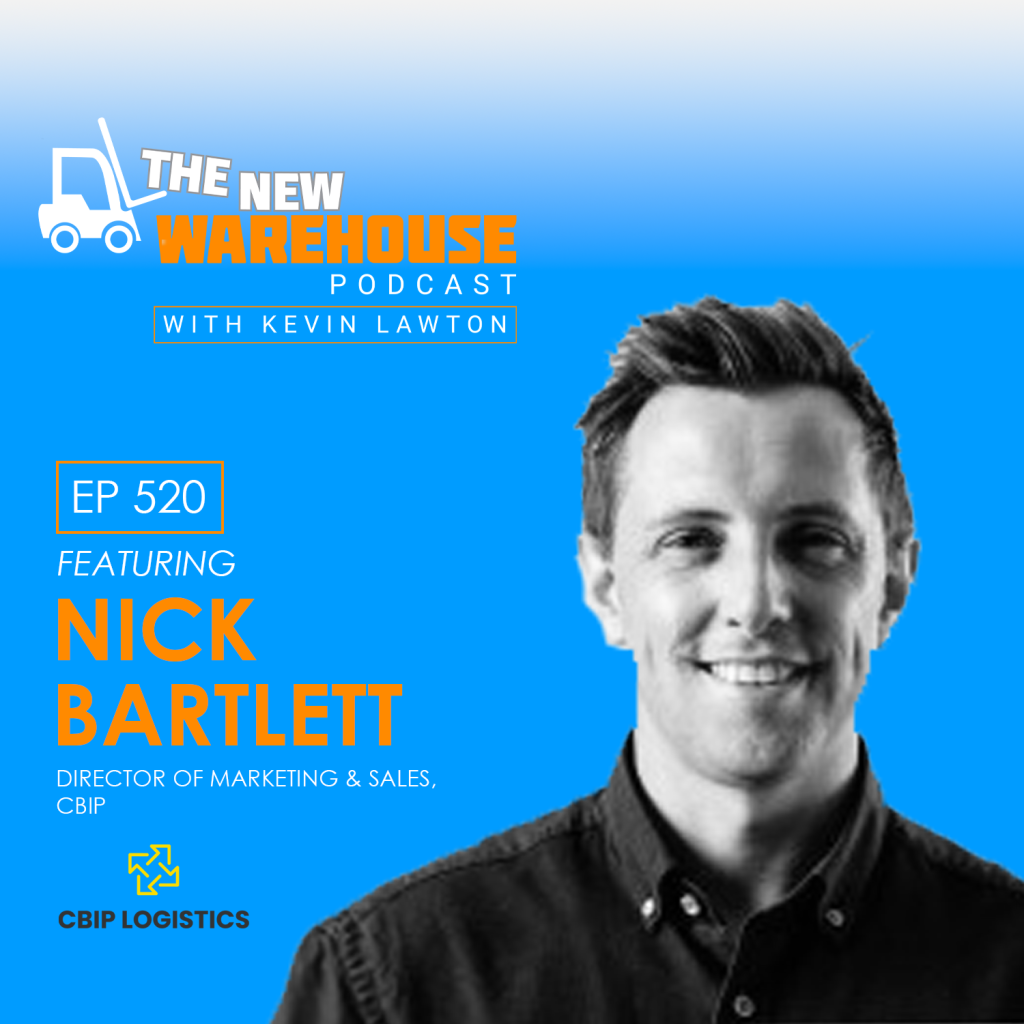
In this episode of The New Warehouse Podcast, Kevin chats with Nick Bartlett, Director at CBIP Logistics, a leading fourth-party logistics (4PL) provider based in Hong Kong. Nick shares insights into CBIP’s innovative approach to bridging the gap between brands and global logistics solutions, particularly in Asia-Pacific. The conversation covers CBIP’s journey towards carbon neutrality, its in-house tech platform launch, and the evolving direct-to-consumer (DTC) market in Asia. 4PL Solutions for Global Expansion CBIP Logistics connects brands with leading logistics solutions worldwide. CBIP’s business model emphasizes flexibility and brand representation, allowing companies to expand internationally without being tied to a single logistics partner. “We represent the brand’s promises. We don’t represent the 3PLs’ profitability line,” says Nick Bartlett. This approach has enabled CBIP to support over 100 brands, shipping across 160 countries focusing on providing tailored logistics solutions that align with each brand’s specific needs. Nick highlights that CBIP’s role is more than just matchmaking between brands and logistics providers. The company takes full operational responsibility from start to finish, ensuring the brand’s promise is delivered consistently across all markets. This unique 4PL model can help brands looking to expand into regions like Asia. The Evolving DTC Market in Asia Asia’s direct-to-consumer (DTC) market is rapidly evolving, driven by increasing e-commerce adoption and technological advancements. However, Nick points out that Asia’s logistics infrastructure is still catching up with Western markets. “The infrastructure inside the logistics industry has progressed but is just not as fast as what you see in the U.S.,” Nick notes. Despite these challenges, the region is witnessing significant growth, particularly in markets like Vietnam, the Philippines, and Thailand. Nick also discusses the importance of trust in the Asian market, which is a critical factor in the success of DTC brands. However, while speed of delivery is essential, building trust with consumers is paramount. “Trust in an Asian culture is of the highest qualities, one of the highest values positioned,” says Nick. This trust is built through localization, understanding consumer preferences, and adapting brand strategies to fit local markets. CBIP’s Commitment to Sustainability and Innovation In 2022, CBIP Logistics achieved carbon neutrality, marking a significant milestone in the company’s commitment to sustainability. The journey to carbon neutrality was rigorous, involving a comprehensive audit of CBIP’s operations and supply chain. “We wanted it to be credible, fair, and transparent,” says Nick. Additionally, CBIP is developing an in-house tech platform, currently in beta, designed to streamline operations and enhance customer experience. The platform, called “Bundle,” aims to consolidate the operations of CBIP’s customers, offering a more integrated and efficient solution. Nick explains, “The power of what we’re building is in the ability to automate and allocate tasks across our extensive network of suppliers.”This approach improves operational efficiency for CBIP’s customers. Key Takeaways CBIP Logistics offers a unique 4PL model that provides brands with flexible, brand-centric logistics solutions essential for global expansion. The DTC market in Asia is increasing, with significant opportunities for brands prioritizing trust and localization. CBIP Logistics achieved carbon neutrality in 2022, demonstrating a solid commitment to sustainability. The company’s in-house tech platform, “Bundle,” enhances operational efficiency and provides valuable data-driven insights for customers. The New Warehouse Podcast Episode 520: 4PL Solutions from CBIP Logistics
Kito Crosby launches new wide body shackle

Kito Crosby introduces the newly engineered Crosby G-2160 Wide Body Shackle. From the manufacturer that introduced the original wide body shackle, the new ergonomic design delivers industry-leading safety and efficiency and provides superior performance and versatility in demanding heavy lift applications. The new design comes in eight capacities ranging from 400t to 2000t. The new Crosby G-2160 provides: The widest bow on the market allows higher sling efficiency and capacity, with smaller sling sizes Three lifting points, including a recessed and removable center lifting point that reduces the risk of snags and provides balanced handling Bow-to-bow compatibility for all sizes, unlike any other brand Anti-rotation bolt head to prevent unwanted turning during installation Easy-Loc™ bolt securement option available for 400t, 500t, and 600t Optional Crosby Straightpoint load monitoring – the only wide body shackle on the market ready to ship directly from the factory with this industry-leading technology Fernanda Zamorano, Global Product Manager, Kito Crosby, said: “The Crosby G-2160 Wide Body Shackle is a game changer for those working in heavy lifting environments. We are excited to bring this innovative product to market and look forward to helping improve safety on job sites, while saving end users both time and investment on slings.” The Crosby G-2160, the world’s first wide body shackle, was introduced in 1978 and has since become an integral component in industrial, construction, and oil and gas lifting projects around the world. Whether used for offshore lifting, construction projects, or other heavy-duty applications, the Crosby G-2160 Wide Body Shackle delivers the strength, reliability, and safety for which Crosby products are known.
TAB Industries to showcase two Orbital Stretch Wrapper models at FABTECH Booth #S-11128
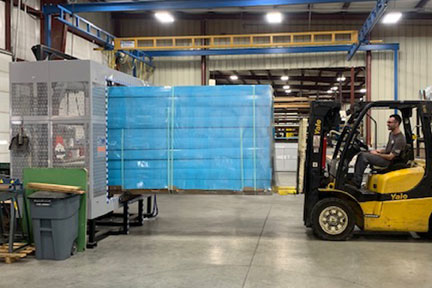
Automated TAB Wrapper Tornado smart controls to be shown in two sizes At FABTECH Orlando booth #S-11128, orbital stretch wrapper manufacturer TAB Industries, LLC, plans to showcase its patented TAB Wrapper Tornado pallet wrapping machine with two different machines. To be shown with 100-inch and 80-inch wrapping rings, the two orbital stretch wrappers feature the company’s Smart Controls automation technology with wireless remote control operation and automated cut and wrap capabilities, plus a new LED safety light tower. This best-selling configuration option enables one worker to automatically stretch and wrap a pallet load in 30 seconds or less without leaving the seat of a forklift. Ideal for metal shops offering fabrication, stamping, powder coating, cutting, welding, and other metalworking services, the TAB Wrapper Tornado automatically applies stretch wrap 360 degrees around and under the pallet and load to create a secure, stable, unitized load. The need for boxes, banding, and crates is eliminated along with shifting in transit and storage. In addition to the automated 100-inch and 80-inch units to be shown at the booth, the orbital stretch wrapping machine is also available with a 115-inch wrapping and in semi-automated models as standard. The orbital stretch wrappers are designed and manufactured at the company’s Reading, Pa. headquarters and delivered ready for operation with a warranty. A companion line of stretch wrap is available for nearly any orbital stretch wrapping machine.
Siemens new high torque 1FK7 servomotors
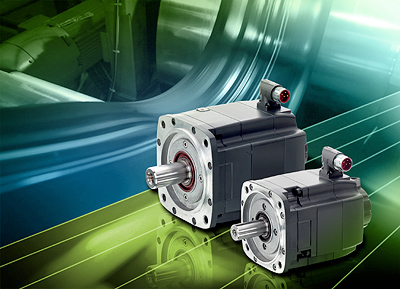
Siemens Industry, Inc. has announced expanding its popular 1FK7 servomotor family, introducing a new high-inertia style. The higher rotor inertia of this design makes the control response of the new 1FK7-HI servomotors highly robust and suitable for high and variable load inertia applications, including the feed and auxiliary axes on machine tools, as well as winders and unwinders on converting packaging, and printing equipment. These self-cooled 1FK7-HI servomotors provide stall torque in the 3 Nm to 20 Nm range and are offered in IP64 or IP65 with IP67 flange degree of protection, with selectable options for plain or keyed shaft, holding brake, 22-bit incremental or absolute encoders, as well as 18 color options. A mechanical decoupler between the motor and encoder shaft protects the encoder from mechanical vibrations, providing a long service life. In cases where the encoder needs to be exchanged, the device automatically aligns the encoder signal to the rotor pole position, enabling feedbacks to be changed in the field in less than five minutes. These new Siemens 1FK7-HI servomotors also feature the unique Drive-Cliq® serial bus and electronic nameplate recognition, allowing virtual plug-n-play operation when paired to the Sinamics® S drive platform. All servomotors in this new line are also configured to interface with Siemens Sinumerik® CNC technology for machine tool applications and the motion controller Simotion® for general motion control use. Selecting the proper motor to suit the application is facilitated by the Siemens Sizer® toolbox and compatible 3D CAD model-generating CAD-Creator package.