The NASA 2024 Space App Challenges have been released
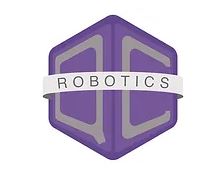
Join Queen City Robotics Alliance and NASA as We Discover “The Sun Touches Everything” As we announced last month, Queen City Robotics Alliance is the Charlotte host for the 2024 NASA Space Apps Challenge. NASA recently released the 20 challenges for this year’s theme “The Sun Touches Everything.” Which challenge will you tackle? The NASA International Space Apps Challenge is the world’s largest global hackathon. This two-day event on October 5-6 allows participants of all ages to use NASA’s free and open data sources and its Space Agency Partners’ space-based data to address real-world issues on Earth and in space. During the event, participating teams gather at designated sites all over the world in person and virtually to address challenges submitted by NASA experts. The 2024 challenges were announced on August 22. Here are a few of this year’s challenges* and each one can be adapted to fit different education levels from beginner, intermediate, advanced, and professional. (*Information from the NASA 2024 Space Apps website.) Beyond Sunlight: An Aquatic Chemosynthetic World – Earth’s ecosystems heavily rely on sunlight, but imagine an ocean world where chemosynthesis, not photosynthesis, sustains life. Your challenge is to design such a world and its diverse ecosystem, pushing the boundaries of astrobiology beyond traditional Earth-like conditions. PACE in the Classroom – The Plankton Aerosol Cloud ocean Ecosystem (PACE) satellite launched and has begun returning data about Earth’s oceans and atmosphere. NASA’s open science policy allows for all the PACE data to be accessed by the public, but it can be difficult to understand if you are not already familiar with these types of data. Your challenge is to create a digestible set of materials that can be used in classrooms across the world to help students understand the data and information that PACE is gathering and improve ocean literacy worldwide. Tell Us a Climate Story – Over the last several decades, a huge amount of climate data from numerous sources has been collected. This data is freely available to the public, but making sense of this vast amount of data is not easy! Your challenge is to use the open-source data on the U.S. Greenhouse Gas Center website to tell a compelling story about climate change. These challenges are designed to incorporate a variety of skills, not just math and science, but art, research, software design, graphic design, creative writing, photography, and even music. This allows participants from diverse backgrounds and skill sets to contribute to NASA’s understanding of both our world and beyond. TWO (2) SPECIAL ANNOUNCEMENTS: 1) QCRA sponsor Sullenberger Aviation Museum will provide one (1) family four-pack day pass to every participant who completes a NASA Space Apps Challenge at The Zone. 2) Thanks to our sponsors Infosys and Bosch Rexroth, QCRA will offer local awards to Charlotte teams participating at The Zone. QCRA CEO Kaiwen Cheng is excited the organization has this unique opportunity to host this singular event because it will bring more recognition, interest, and outreach for QCRA’s STEM (Science, Technology, Engineering, and Math) programs in the Charlotte community. “This is an opportunity for students to use NASA to explore ideas,” said Cheng. “Space technology is a leading technology. It’s using space to inspire and impact our daily lives. Things like GPS and memory foam mattresses. We wouldn’t have those things today without NASA technology.” “This is also an exciting opportunity for our students,” he continued, “because it is an interesting and tangible way for them to explore STEM education and find out what their talents are through NASA and the wonders of space.”
KION Group supports Endowed Professorship for AI Solutions at TU Dortmund University
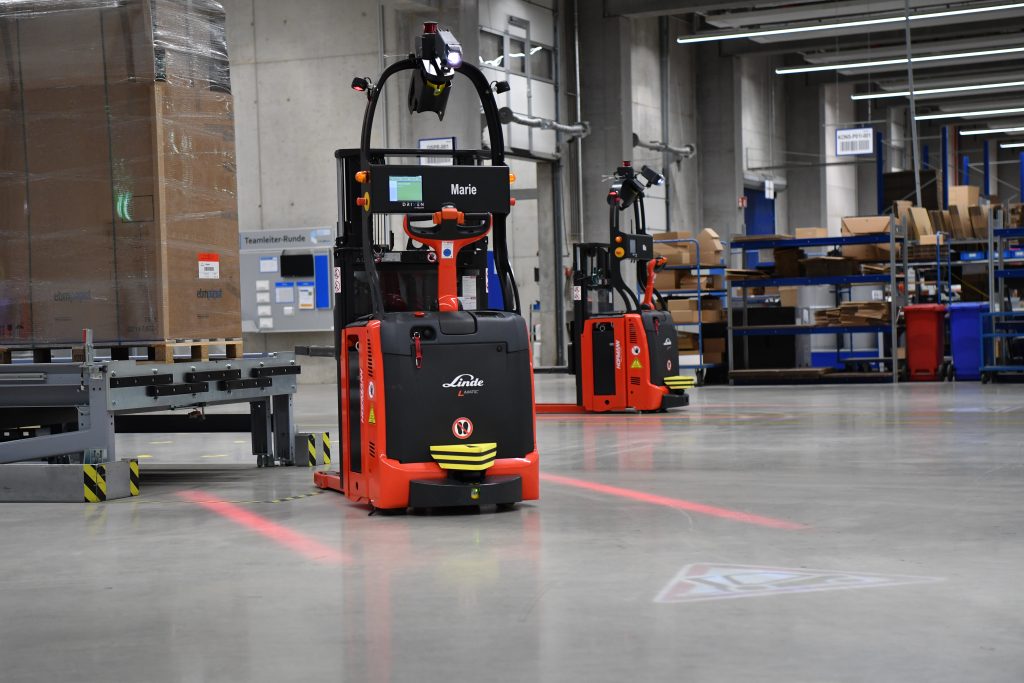
KION Group establishes a research hub for AI-assisted intralogistics solutions Sebastian Peitz was appointed professor at the Department of Computer Science at TU Dortmund University Ching Pong Quek, CTO of KION Group: “Planned collaboration underlines our pioneering role in the promising technological field of Artificial Intelligence (AI)” The KION Group is funding an Endowed Professorship for Safe Autonomous Systems at TU Dortmund University. Sebastian Peitz will be responsible for this field. He has been appointed professor at the Department of Computer Science and will begin his research and teaching activities at the university in the winter semester 2024/2025. His work will focus on developing autonomous systems that operate intelligently and safely for all parties involved. This applies, in particular, to autonomous mobile robots, forklift trucks, and AI-based systems used in logistics and production environments. The objective of the endowed professorship is to advance the field of research at the highest international level. The professorship will form a hub for digital and intelligent logistics in close collaboration with research networks and cooperation partners within and outside TU Dortmund University, such as the Fraunhofer Institute for Material Flow and Logistics IML and the KION Group. “The planned collaboration with TU Dortmund University and Professor Peitz will lead to relevant milestones in the field of artificial intelligence,” says Ching Pong Quek, Chief Technology Officer of the KION Group. He adds that the endowed professorship will complement the KION Group’s internal research and development activities in the fields of AI and machine learning and underline its pioneering role in one of the most promising technological fields for the future. “The KION endowed professorship will help autonomous industrial trucks and other machines in the storage and logistics industry to work more safely and efficiently,” emphasizes Quek. After completing his PhD in 2017, Sebastian Peitz worked at the University of Paderborn as a postdoc at the Institute for Industrial Mathematics before moving to the Institute for Computer Science as a junior professor in 2021. He has extensive experience in artificial intelligence, machine learning, and robotics. Since 2022, he has led an AI junior research group to develop multi-criteria training algorithms for deep learning. At the beginning of September, the European Research Council granted him a Starting Grant for secure and data-efficient reinforcement learning for complex technical systems. TU Dortmund University offers a unique environment that enables a combination of fundamental and application-oriented research and also combines logistics and computer science. The Department of Computer Science is one of the leading faculties in artificial intelligence and machine learning. The KION Group will finance the endowed professorship with one million euros over five years.
ALAN Tropical Storm Francine Situation Report: September 13, 2024
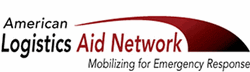
ALAN has been improving logistics response to disasters for 19 years, and the need is greater now than ever. Please donate today to help us continue our work for many more years to come. American Logistics Aid Network is mobilized for Hurricane/Tropical Storm Francine. As part of our response efforts, we are committed to providing you with the latest information and updates on supply chain impacts via our periodic Situation Reports, which can be found below in this email and on our website. In the wake of Tropical Storm/Hurricane Francine’s landfall along the Gulf coast, the American Logistics Aid Network (ALAN) is urging area residents to heed safety advisories – and reminding members of the logistics community that their post-storm help could be needed soon. In addition to working closely with the non-profit and emergency response communities, ALAN is providing real-time visibility on the storm’s supply chain impacts—including damages to roads, ports, and airports—via its Supply Chain Intelligence Center, which individuals and businesses can access free of charge. ALAN has also updated its Disaster Micro-Site with helpful Tropical Storm/Hurricane Francine resources. That site is where ALAN will post requests for donated logistics assistance, most of which will arrive within 24 to 72 hours after the storm’s initial landfall. Logistics businesses that wish to make a financial donation to ALAN instead can do so by visiting https://www.alanaid.org/donate/ EMERGENCY DECLARATIONS President Biden approved an Emergency Declaration for Louisiana on September 10, 2024, in preparation for impacts from Tropical Storm Francine beginning on September 10, 2024 and continuing. STATE DECLARATIONS Mississippi Governor Reeves issued a State of Emergency Proclamation for Tropical Storm Francine on September 10, 2024. Louisiana Governor Landry issued Executive Order Number JML 24-142 State of Emergency for Tropical Storm Francine on September 9, 2024. Louisiana Department of Transportation Secretary Donahue issued a Secretary’s Emergency Order on September 9, 2024, in preparation for the impacts of Tropical Storm Francine. ACTIVE TRANSPORTATION WAIVERS Title: Mississippi Governor Reeves issued Executive Order No 1582 for Tropical Storm Francine. Effective: 09/10/24| Expires on: 09/24/24 Description: The Governor issued a Proclamation declaring a State of Emergency for Tropical Storm/Hurricane Francine on September 9, 2024. Executive Order waives specific provisions of Parts 390 through 399 of Title 49, CFR, including relief from Title 49, Part 395.3 and 395.5 for motor carriers providing direct assistance to disaster relief efforts. Title: Louisiana Department of Public Safety Deputy Secretary declared a regional emergency Effective: 09/10/24| Expires on: 09/23/24 Description: The Department of Public Safety Deputy Secretary declared a regional emergency providing exemption pursuant to Title 49, CFR, Part 390.23 and LA R.S. 32:1501 ET SEC, 1 and certain exemptions from Parts 390 through 399 of Title 49, FMCSR. Title: Louisiana Department of Transportation Secretary Donahue issued Secretary’s Emergency Order Effective: 09/09/24| Expires on until rescinded Description: The Department of Transportation Secretary issued a Secretary’s Order with respect to commercial motor carriers traveling for the purpose of emergency preparedness and disaster relief efforts; provisions of Louisiana Revised Statue 32:386(1) are suspended, and the size and weight restrictions for vehicles. STATE BUSINESS AND INDUSTRY RESOURCES State of Louisiana Virtual Louisiana Hurricane Francine Resources Department of Transportation LaGeaux Oversize / Overweight Truck Permitting Louisiana Business Emergency Operations Center Tropical Storm Francine Operation Emergency Louisiana Get a Game Plan Business Resources Louisiana DOTD Evacuation Map Application State of Mississippi Mississippi Business Emergency Operations Center State of Texas Texas Economic Development & Tourism Business Resources Texas Workforce Commission Resources for Employers ROAD CONDITIONS Louisiana 511 Mississippi MDOT Traffic Drive Texas CURFEWS (as of September 13, 2024) Amite (6 pm to 6 am until further notice) Berwick (lifted) Iberia Parish (lifted) Independence (lifted) Jeanerette (lifted) Lafourche Parish (lifted Friday morning) Morgan City (lifted) St. Helena Parish (Wednesday until further notice) St. Mary Parish east of Calumet Cut (Thursday until further notice) Tangipahoa village (lifted) Terrebonne Parish (8 am Wednesday until further notice) Washington Parish (lifted) EVACUATION STATUS (as of September 13, 2024) State of Louisiana Assumption Parrish (voluntary) Cameron Parish (mandatory) Iberia Parish (voluntary) Jefferson Parish (mandatory outside flood protection levee) Lafayette Parish (voluntary) Lafourche Parish (mandatory) Plaquemines (lifted as of 9/12 12:30 pm) Port Fourchon (mandatory) St. Martin Parish (voluntary) St. Mary Parish (voluntary) Terrebonne Parish (mandatory, zone 1) State of Mississippi Bay St. Louis (mandatory, all boats) Diamondhead (voluntary) Waveland (voluntary) State of Texas Galveston County (voluntary) PORT CONDITIONS (as of September 13, 2024), per USCG Home Port) State of Louisiana Amelia (closed) Atchafalaya River (open) Bayou Boeuf Lock (closed) Bayou Chene (closed) Bayou Lafourche (closed) Bayou Sorrel Lock (open) Berwick (closed) Cameron (open) Charenton Canal (closed) Houma Navigation Canal (closed) Intercoastal City (closed) Lake Charles (open) Leland Bowman Locks (open) Mississippi River (open) Morgan City (closed) Orange (open with restrictions) Old River Lock (open) Port Allen (open) Port of Greater Baton Rouge (open) Port Fourchon (open) Port of New Iberia (closed) Port of New Orleans (open) Port of Plaquemines (open) Port of South Louisiana (open) Port of St. Bernard (open) Port of West St. Mary (closed) Sabine (open) State of Texas Beaumont (open) Calhoun Port Authority (open) Freeport (open) Galveston (open with restrictions) Harlingen (open) Houston (open) Port Arthur (open) Port of Brownsville (open) Port of Corpus Christi (open) Port of Isabel (open) Port of Mansfield (open) Port of Palacious (open) Port of Victoria (open) Texas City (open) AIRPORT CONDITIONS (as of September 13, 2024) Baton Rouge Metropolitan Airport (open with delays) Jackson International Airport (open, general delays) Louis Armstrong New Orleans International Airport (open, general delays) UTILITIES (as of September 13, 2024) State of Alabama As of 12 pm CDT there are 3,322 reported power outages in Alabama Alabama Power Outage Map State of Louisiana 12pm CDT, there are 114,493 reported power outages in Louisiana Louisiana Entergy Power Outage Map New Orleans Entergy Power Outage Map CLECO Power Outage Map Washington-St. Tammany Electric’s Outage Map Louisiana Public Service Commission Utility Outage Resources Louisiana Power Outages State of Mississippi As of 12 pm CDT there are 724 reported power outages in Mississippi Entergy Power Outage Map Mississippi Public Service Commission Storm Information State of Mississippi Power Outages State of Texas Public Utility Commission of Texas Outage Viewer STATE / CITY EMERGENCY MANAGEMENT AGENCY Louisiana Governor’s Office of
GEODIS to Hire 3,700 Seasonal Workers for Peak Season
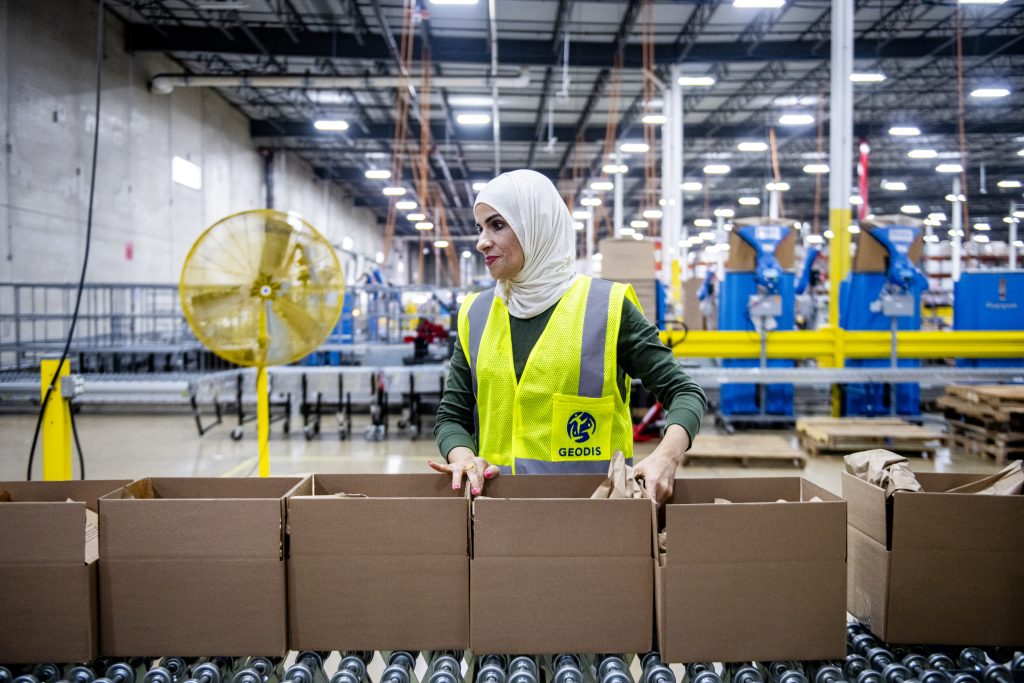
GEODIS has announced plans to hire 3,700 seasonal workers across its campuses in the U.S. and Canada to help manage the expected rise in volumes during peak season. This hiring initiative will bolster the company’s operational capacities in its warehouses and distribution centers in preparation for the holiday season, a time when consumer demand surges. Emarketer noted U.S. holiday sales in 2023 increased 3.9% year-over-year as consumer spending grew even amidst uncertain economic times, and a similar pattern is projected for this year. Emarketer expects a substantial 4.8% increase in holiday retail sales for 2024, signifying continued growth despite factors such as inflation and consumer price sensitivity. In anticipation of this demand, GEODIS is seeking seasonal employees to join its nearly 17,000 teammates who power its operations across North America. GEODIS is recruiting material handlers and equipment operators across 13 regions in the U.S. and Canada this peak season. The company offers competitive wages, peak premium pay incentives, peak and referral bonuses, and an expedited payment option that allows workers to receive up to 50% of their paycheck before payday through an on-demand program. Additionally, GEODIS provides flexible schedules with weekend opportunities and multiple shift options daily, allowing teammates to choose times that best suit their lives. Both part-time (under 30 hours a week) and full-time (over 30 hours a week) seasonal positions are available. Prospective teammates can also use GEODIS’ virtual recruiting assistant, Sophie, to find the right role, easily navigate the application process and receive fast answers to questions before being connected to a recruiter for next steps. “We acknowledge the immense responsibility we have to our customers to deliver exceptional service every day, and this is especially true during peak season,” said Anthony Jordan, GEODIS in Americas Executive Vice President and Chief Operating Officer. “Because peak season is the most business-critical sales period of the year for many of our retail clients, expanding our workforce is vital to ensure we have a flexible, dynamic team that can handle anticipated surges in demand.” GEODIS’ culture puts teammates at the forefront by offering opportunities for employees to provide feedback and suggestions through surveys, personal check-ins and group meetings. The company also prioritizes teammate safety and ensures optimal work conditions in modern facilities with state-of-the-art technology. GEODIS invests in its teammates with paid safety-focused training, allowing them to gain hands-on experience so they can feel confident from day one of employment. “GEODIS is committed to creating a diverse and supportive work environment where employee well-being is our top priority,” said Jordan. “Whether looking for extra income during the holidays or wanting to explore a long-term path at GEODIS, our teammates have the opportunity to make a difference and receive the training and support they need to move their careers forward.”
Port of Long Beach achieves busiest month on record
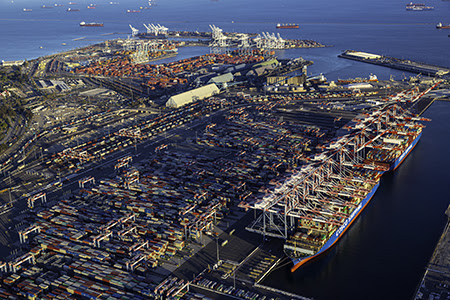
Potential tariff increases, labor negotiations contribute to peak shipping season The peak shipping season boosted the Port of Long Beach in August to its strongest month in its 113-year history as retailers moved cargo ahead of potential tariff increases and labor negotiations continued at seaports on the East and Gulf coasts. Dockworkers and terminal operators in Long Beach moved 913,873 twenty-foot equivalent units in August, up 33.9% from the same month last year and surpassing the Port’s previous all-time one-month record set in May 2021 by 6,657 TEUs. Imports jumped 40.4% from August 2023 to 456,868 TEUs, exports rose 12% to 104,646 TEUs and empty containers moved through the Port increased 33.7% to 352,360 TEUs. In addition to being the Port’s third consecutive monthly year-over-year increase, August also marked only the second time the Port has exceeded 900,000 TEUs in a single month. “Cargo diversions and concerns about upcoming tariffs are creating a busy peak season for us,” said Port of Long Beach CEO Mario Cordero. “We’re prepared for the uptick in shipments and continued growth through the rest of the year with a dedicated waterfront workforce, modern infrastructure and plenty of capacity across our terminals.” “The docks are bustling with record-setting activity as we continue to move cargo quickly, reliably and sustainably,” said Long Beach Harbor Commission President Bonnie Lowenthal. “As the premier gateway for trans-Pacific trade, the Port of Long Beach is delivering on its promise of outstanding service and facilitating the most efficient movement of goods across the supply chain.” The Port has moved 6,087,875 TEUs during the first eight months of 2024, up 21.9% from the same period last year. Click for complete cargo numbers
Manufacturing Technology orders look to rebound as IMTS 2024 opens, rate cuts loom
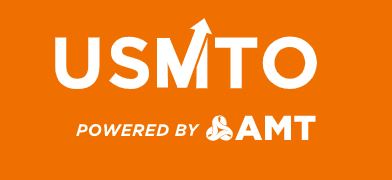
Orders of manufacturing technology, measured by the U.S. Manufacturing Technology Orders report published by AMT, totaled $321.7 million in July 2024, showing declines of 19.3% from June 2024 and 7.8% compared to July 2023. Orders of manufacturing technology, measured by the U.S. Manufacturing Technology Orders (USMTO) report published by AMT – The Association For Manufacturing Technology, totaled $321.7 million in July 2024. Orders declined 19.3% from June 2024 and declined 7.8% compared to July 2023. Year-to-date orders reached $2.53 billion, a decline of 10.5% from the first seven months of 2023. July is typically one of the slower months of the year for manufacturing technology orders. Despite that, July 2024 is 3.8% above the pre-2020 average for the month. Cancellations were the highest since July 2023, and the ratio of cancellations to new orders remained above the historical average in all but two months of this year. Despite these mixed messages, there are signs that the industry may be at the beginning of the anticipated rebound. While the value of orders declined from June to July 2024, the number of units ordered in July 2024 increased by 1.9% over June 2024. Contract machine shops, the largest customer of manufacturing technology, outperformed the market for the first time in several months. The value of manufacturing technology orders contracted less than 5%, while the number of units ordered increased nearly 10% from June to July. This indicates that shops are beginning to expand capacity in anticipation of their customers placing additional orders for parts. Conversely, medical equipment manufacturers increased the value of their orders from June to July 2024 while decreasing the number of units. With a manufacturing process that requires high precision, traceability, and customization, the medical industry typically places orders for more sophisticated machinery. Some estimates predict this industry will grow by 50% between now and 2029, so this sector is poised to become a reliable customer of manufacturing technology. Orders from manufacturers of electrical generation and distribution equipment were flat from June to July 2024. However, because July was a down month, they comprised a larger share of the total orders. This sector has pulled back orders from their peak in early 2023 but remain on an upward trend. Increased power demand from data centers as well as a larger focus on grid modernization has made this a very important sector for manufacturing technology. After Federal Reserve Chair Jerome Powell’s speech at the Jackson Hole Economic Symposium and the weak August jobs report, a rate cut at the Fed’s September meeting is all but certain, according to market reactions. Assuming the Fed has managed to guide the economy to a soft landing, predicting how machine tool orders will react is difficult due to the lack of historical examples of soft landings – especially compared to the many examples of recessions. Still, with the anticipated rate cut expected to begin alleviating some concerns of households and businesses, renewed demand up and down the supply chain may be on the doorstep as manufacturers converge on # # # The United States Manufacturing Technology Orders (USMTO) Report is based on the totals of actual data reported by companies participating in the USMTO program. This report, compiled by AMT – The Association For Manufacturing Technology, provides regional and national U.S. orders data of domestic and imported machine tools and related equipment. Analysis of manufacturing technology orders provides a reliable leading economic indicator as manufacturing industries invest in capital metalworking equipment to increase capacity and improve productivity. USMTO.com. AMT – The Association For Manufacturing Technology represents U.S.-based providers of manufacturing technology – the advanced machinery, devices, and digital equipment that U.S. manufacturing relies on to be productive, innovative, and competitive. Located in McLean, Virginia, near the nation’s capital, AMT acts as the industry’s voice to speed the pace of innovation, increase global competitiveness, and develop manufacturing’s advanced workforce of tomorrow. With extensive expertise in industry data and intelligence, as well as a full complement of international business operations, AMT offers its members an unparalleled level of support. AMT also produces IMTS – The International Manufacturing Technology Show, the premier manufacturing technology event in North America. AMTonline.org. IMTS – The International Manufacturing Technology Show is where the creators, builders, sellers, and drivers of manufacturing technology come to connect and be inspired. Attendees discover advanced manufacturing solutions that include innovations in CNC machining, automation, robotics, additive, software, inspection, and transformative digital technologies that drive our future forward. Powered by AMT – The Association For Manufacturing Technology, IMTS is the largest manufacturing technology show and marketplace in the Western Hemisphere. With more than 1.2 million square feet of exhibit space, the show attracts visitors from more than 110 countries. IMTS 2022 had 86,307 registrants, featured 1,816 exhibiting companies, saw over 7,600 people attend educational events, and included a Student Summit that introduced the next generation to manufacturing. Be the change at IMTS 2024, Sept. 9-14, 2024. Inspiring the Extraordinary. IMTS.com. AuthorChristopher Chidzik
Combilift secures double win at UK Engineering & Manufacturing Awards 2024
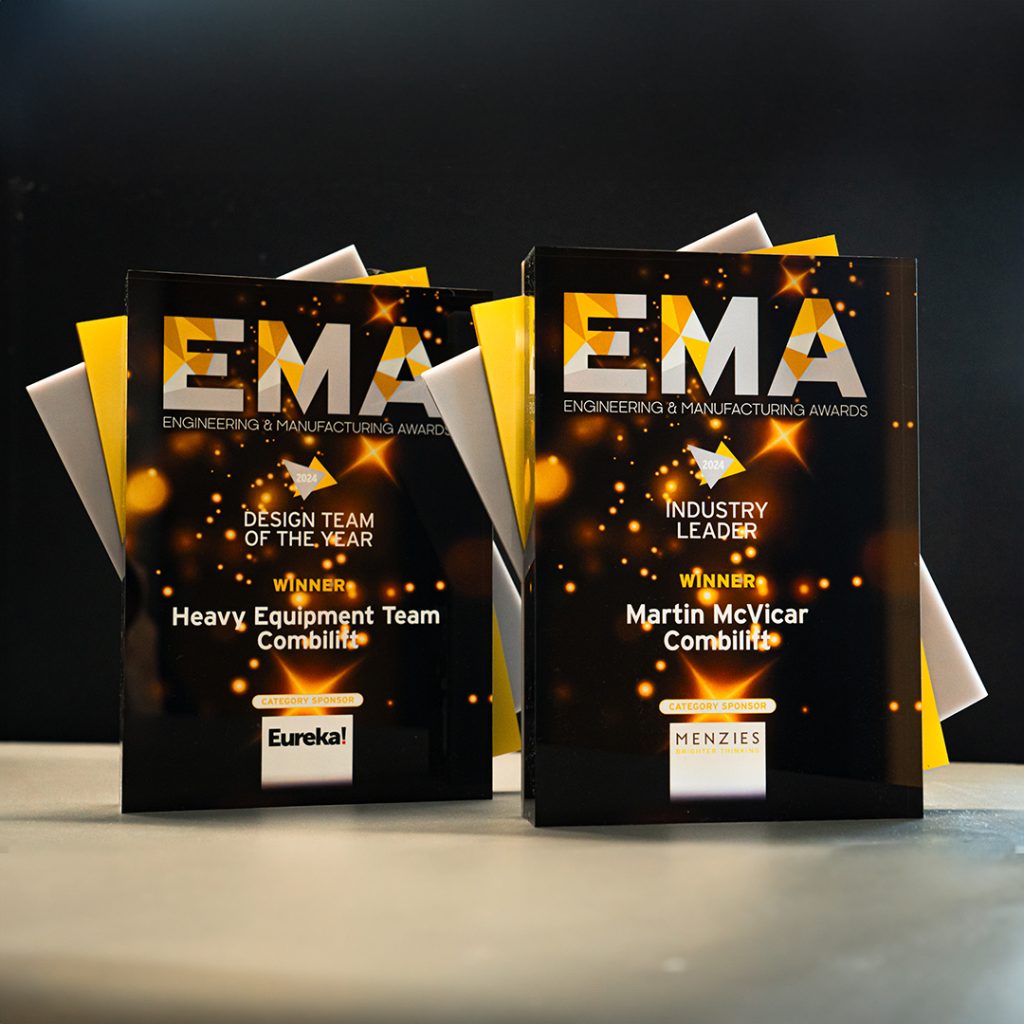
Combilift, a global innovator in material handling solutions, has achieved dual recognition at this year’s UK Engineering & Manufacturing Awards 2024, securing two highly prestigious awards. Design Team of the Year The ‘Design Team of the Year’ award was presented to Combilift’s Heavy Equipment Team for their exceptional work on the groundbreaking 12-wheel “Combi-LC Blade.” This cutting-edge machine has been specifically engineered to handle offshore wind turbine blades, reaching up to 115 meters in length and weighing as much as 70 tonnes. The design significantly enhances the ability to transport these large, non-uniform loads safely and efficiently from manufacturing sites to storage and deployment locations. This innovative solution addresses the growing needs of the renewable energy sector, where the demand for efficient logistics systems is increasing as the size and scale of offshore wind turbines continue to grow. Before the development of the Combi-LC Blade, existing transportation methods were often inadequate and posed logistical challenges. Combilift’s Heavy Equipment Design Team drew upon their extensive experience in engineering complex transport systems, previously creating the renowned Combi-SC Straddle Carrier and Combi-MG Mobile Gantry ranges. In collaboration with Siemens Gamesa, one of the world’s largest offshore wind turbine technology suppliers, Combilift designed a transport system that offers unparalleled stability and safety when moving these massive turbine blades. The Combi-LC Blade has now been successfully deployed at manufacturing sites across the globe, demonstrating its effectiveness and transforming how wind turbine blades are handled and transported. Combilift is renowned for its customer-centric approach and ability to develop customized material handling solutions tailored to meet customers’ needs. This award, sponsored by *Eureka Magazine*, recognizes the team’s exceptional skill, collaboration, and dedication to solving one of the most pressing challenges in renewable energy logistics but also highlights the company’s commitment to providing innovative customer-led solutions. Industry Leader Award In addition to this remarkable team achievement, Combilift’s co-founder and CEO, Martin McVicar, received the coveted ‘Industry Leader Award’, sponsored by *Menzies*. This accolade honors McVicar’s visionary leadership and unwavering commitment to innovation, which have played a pivotal role in transforming Combilift from a small Irish manufacturer into a global leader in the material handling sector. Martin McVicar’s leadership has been instrumental in Combilift’s success. Since co-founding the company, McVicar has overseen its rapid growth, transforming it into one of Ireland’s top exporters, with a projected turnover of €500 million this year. His approach to leadership combines technical expertise with a hands-on, inclusive management style. Known for his engineering prowess, McVicar has a background as Chief Engineer at Moffett Engineering, a role he held at 19. Under his guidance, Combilift has become synonymous with innovative problem-solving in material handling, consistently delivering tailored solutions for complex logistical challenges. The judges highlighted McVicar’s ability to navigate the company through a range of external challenges, from the impacts of the pandemic to global supply chain disruptions, while maintaining a forward-thinking approach that identifies opportunities for growth and transformation. Beyond business success, McVicar is deeply committed to fostering a strong corporate culture. Combilift’s headquarters, the largest factory under one roof in Ireland, serves as a manufacturing hub and an ambassador for corporate social responsibility. The company regularly hosts apprenticeship schemes, charity events, family days, and educational visits, further solidifying its role within the local community. Combilift also sponsors the local Ladies GAA team, demonstrating McVicar’s commitment to supporting gender equality in sports. Combilift’s double win at the UK Engineering & Manufacturing Awards 2024 is a testament to its innovative spirit and visionary leadership, reinforcing its position as a global leader in the material handling industry.
U.S. Rail Traffic for the week ending September 07, 2024
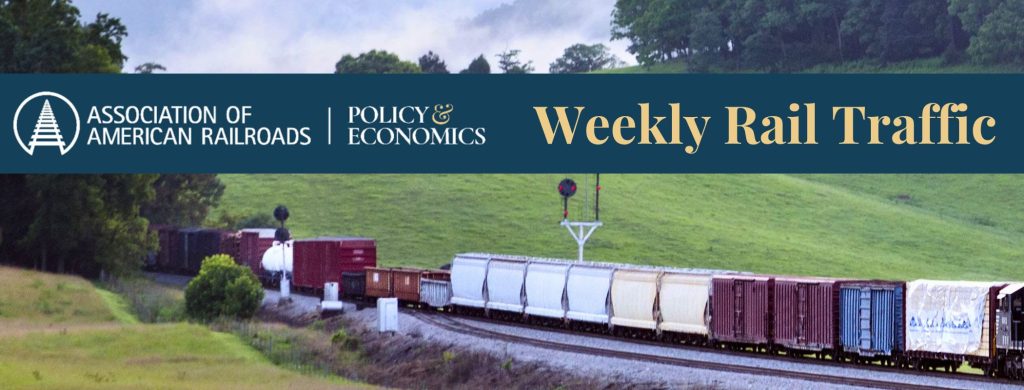
The Association of American Railroads (AAR) has reported U.S. rail traffic for the week ending September 7, 2024. For this week, total U.S. weekly rail traffic was 479,179 carloads and intermodal units, up 7.3 percent compared with the same week last year. Total carloads for the week ending September 7 were 222,201 carloads, up 2.2 percent compared with the same week in 2023, while U.S. weekly intermodal volume was 256,978 containers and trailers, up 12.1 percent compared to 2023. Five of the 10 carload commodity groups posted an increase compared with the same week in 2023. They included grain, up 4,920 carloads, to 19,552; chemicals, up 3,269 carloads, to 32,669; and petroleum and petroleum products, up 1,033 carloads, to 10,778. Commodity groups that posted decreases compared with the same week in 2023 included coal, down 4,024 carloads, to 63,754; motor vehicles and parts, down 1,248 carloads, to 13,663; and forest products, down 338 carloads, to 7,511. For the first 36 weeks of 2024, U.S. railroads reported a cumulative volume of 7,780,022 carloads, down 3.4 percent from the same point last year; and 9,351,417 intermodal units, up 9.4 percent from last year. Total combined U.S. traffic for the first 36 weeks of 2024 was 17,131,439 carloads and intermodal units, an increase of 3.2 percent compared to last year. North American rail volume for the week ending September 7, 2024, on 9 reporting U.S., Canadian, and Mexican railroads totaled 323,723 carloads, down 0.1 percent compared with the same week last year, and 334,792 intermodal units, up 9.2 percent compared with last year. Total combined weekly rail traffic in North America was 658,515 carloads and intermodal units, up 4.4 percent. North American rail volume for the first 36 weeks of 2024 was 23,874,410 carloads and intermodal units, up 2.5 percent compared with 2023. Canadian railroads reported 87,045 carloads for the week, down 2.9 percent, and 65,938 intermodal units, up 1.7 percent compared with the same week in 2023. For the first 36 weeks of 2024, Canadian railroads reported a cumulative rail traffic volume of 5,691,447 carloads, containers and trailers, up 0.3 percent. Mexican railroads reported 14,477 carloads for the week, down 13.8 percent compared with the same week last year, and 11,876 intermodal units, down 6.0 percent. Cumulative volume on Mexican railroads for the first 36 weeks of 2024 was 1,051,524 carloads and intermodal containers and trailers, up 5.1 percent from the same point last year. Download charts here
Yale wins green award for continued expansion of lithium-ion lift truck options
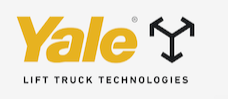
Yale Lift Truck Technologies has announced its recognition as a Green Supply Chain Partner by Inbound Logistics magazine for the 13th year running. This year’s award recognizes the company for bringing the benefits of lithium-ion powered lift trucks to a broader range of operations. The two newest models in the company’s UX lift truck line, the three-wheel ERP32-40UXTL and the four-wheel ERP30-70UXL, are lithium-ion counterbalanced lift trucks engineered for retail stores, warehouses, and home centers where occasional to average duty cycle applications are the norm. These value-driven lift trucks provide businesses that might not previously have been able to justify the investment in lithium-ion with an approachable alternative to lift trucks powered by lead-acid batteries. “Warehouses that use electric lift trucks understand the advantages of lithium-ion batteries but, because of the investment involved, some operations with lighter runtimes considered them out of reach. We’ve continually expanded our UX line to make this technology more accessible,” says Brad Long, North America Brand Marketing and Global Activation Manager, Yale. “By having a budget-friendly option to incorporate lithium-ion lift trucks into their operation, warehouses can make real progress toward their sustainability goals and maximize productivity with faster charging times and less maintenance. It’s a win-win.” Lithium-ion batteries generate zero harmful emissions and can last over four times longer than a lead-acid battery, helping reduce recycling waste. Both the ERP32-40UXTL and the ERP30-70UXL are simple, affordable, adaptable lift trucks for both indoor and outdoor operations. The integrated lithium-ion batteries are available in different sizes and charge rates that can be scaled to fit the requirements of particular operations.
Antares Vision Group to debut versatile, high-speed serialization station at Pack Expo 2024
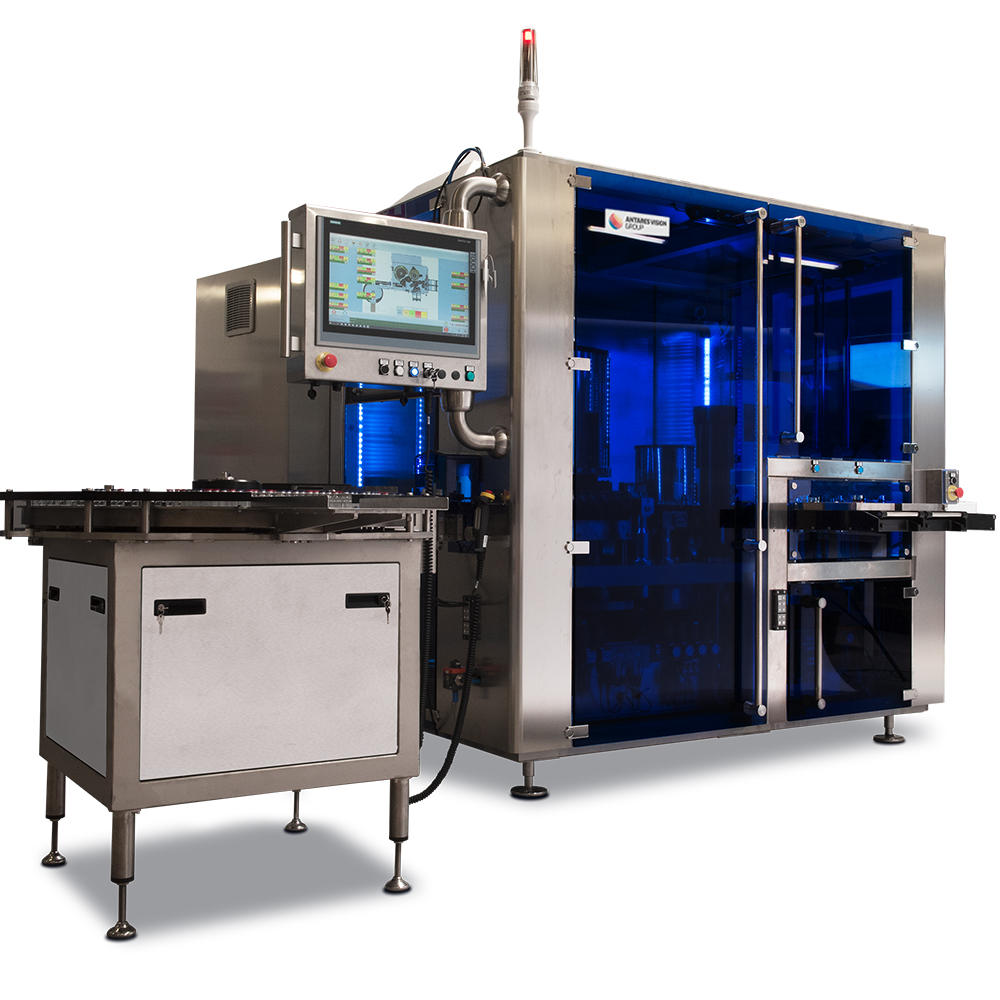
For pharma bottles of various shapes & sizes and will introduce a serialization module for flat cartons, and demonstrate a high-speed automated visual inspection unit for liquid-filled vials. Antares Vision Group will introduce a sophisticated new traceability solution for pharmaceutical bottles at Pack Expo, November 3-6 in Chicago. At its Booth S-3754, the company will debut the Omnivision Bottle Serialization Station for round, square or rectangular bottles commonly used in healthcare applications. Other solutions that Antares Vision Group will showcase include the debut of a standalone module for the offline serialization of flat cartons and a high-speed inspection unit for liquid-filled vials. Across Antares Vision Group’s core strengths of traceability and inspection, the solutions showcased at Pack Expo share several commonalities. Perhaps most prominently, all three solutions – and in fact, the vast majority of the company’s overall portfolio – can be deployed as integrated modules into existing production environments. This inherent agnosticism amounts to a key compatibility element that substantially simplifies incorporation. Concerning traceability specifically, the company’s ultra-secure cloud-based systems enable end-to-end “full stack” connection of the physical and digital worlds. The holistic, fully validated, preconfigured, automated platforms span serialization Levels 1 through 5, ensuring compliance and connectivity with partners and regulatory authorities. Versatile Automated Serialization Solution for Bottles Capable of handling a wide range of bottle sizes at speeds up to 300 per minute, the Omnivision Bottle Serialization Station can print unique helper codes on the top or bottom of each bottle, then perform a 360-degree reading of the unoriented bottle surface for recognition of printed serialized data and code association. This helper code is then used for subsequent manual or automatic aggregation phases, such as bundling or case packing. The system's seamless product handling ensures superior printing quality and a lateral belt system provides bottle separation. Optional topsert inspection is available. Serialization Module for Flat Cartons Also at Pack Expo, Antares Vision Group will premiere a standalone semi-automatic serialization module specifically designed to handle flat, empty cartons and boxes. The Print & Check FT performs traceability functions including marking, recording, and serialization data verification. Flat cartons are loaded into a collector, which precisely feeds the conveyor belt. Cartons are then printed, with a high-resolution camera confirming data correctness and an end-of-belt reject system removing any erroneous ones. The Print & Check FT can achieve line speeds up to 30 meters per minute, and incorporate up to four thermal inkjet printing heads. Other features include an 18.5-inch touchscreen for intuitive operation, a manual code reader for product identification and re-aggregation, adjustable rubber grips to accommodate various carton sizes, and a signaling column that monitors overall machine status. High-speed Visual Inspection & Leak Detection of Liquids in Glass Containers Antares Vision Group is also a market leader in automatic inspection solutions. At Pack Expo, the company will demonstrate an automatic Visual Rotating Inspection (VRI) system capable of inspecting up to 400 liquid-filled glass containers per minute. The machine combines sophisticated particle & cosmetic detection able to integrate with high voltage, vacuum, and headspace gas analysis (HSGA) technology-driven closure integrity verification at an exceptionally rapid production pace. The machine allows for the precise detection of cosmetic defects and particles and checks fill levels. The VRI unit can inspect liquids in a wide variety of viscosities, including water-like, oily, suspension, gel, emulsion, lyophilized, and powder products. Vials are also inspected for cosmetic defects such as crimping quality, flip-off color, neck-shoulder sidewalls, and stopper position. Molded glass and plastic containers also can be inspected for particles and cosmetic defects. Optional add-on features include code verification, optical character recognition (OCR)-optical character verification (OCR-OCV), and serialization incorporation. A split-infeed screw setup provides smooth and reliable operation, preventing undesired stops and restarts. A main floating carousel with a torque motor-driven inspection platform allows ideal cleanability and single-point product handling (from the neck), providing a constraint-free optical setup and improving detection capabilities through enhanced Field of View (FOV) and Depth of Field (DOF). Guideless conveying utilizes vacuum-operated star wheels, minimizing container breakage risks and false rejects. Changeover for star wheels and grippers is approximately 30 minutes, thanks to a guided operations sequence that does not require mechanical adjustments. Inspection reconfiguration occurs intuitively according to recipe selection.
Every Step Matters … and So Does Every Sponsor
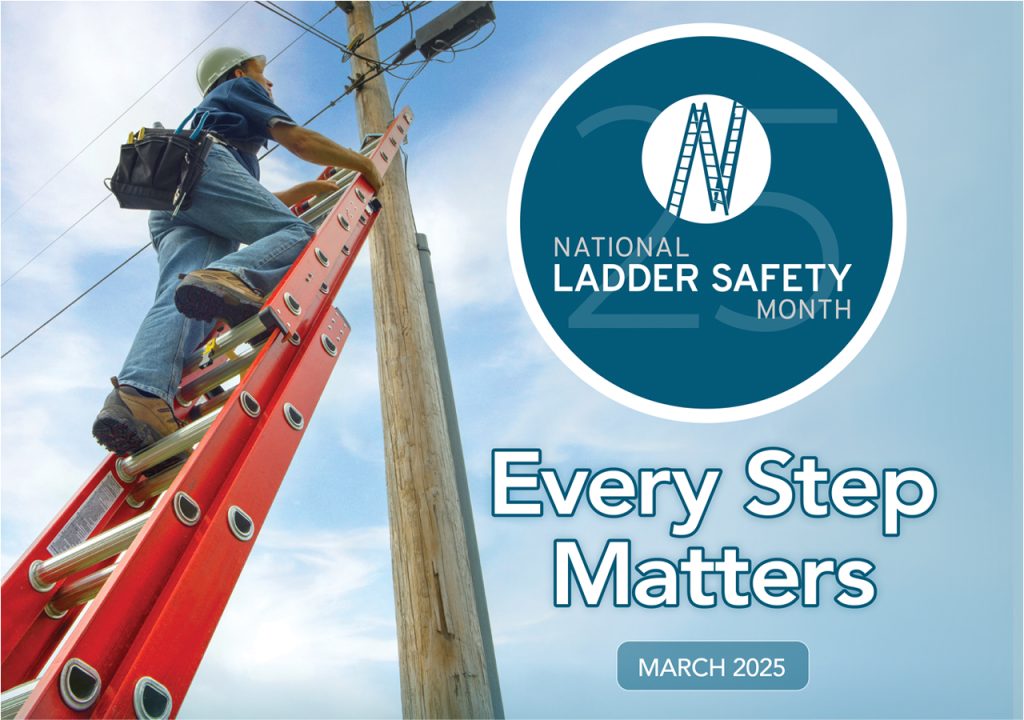
Ladder Safety Month: American Ladder Institute offers sponsorships for 2025 campaign This past March, the message of National Ladder Safety Month reached millions of people. Now, the American Ladder Institute (ALI) is seeking sponsors for the 2025 campaign, so it can reach even more. The sponsorship is a valuable brand extension for any company invested in the manufacture of ladders OR in their safe use. Companies with employees working at heights understand the value of emphasizing safety and its impact on accident prevention and saving lives. Observed every March, National Ladder Safety Month is the only program dedicated exclusively to promoting ladder safety at home and work. Each year, tens of thousands are injured and hundreds die in accidents caused by improper ladder usage. The reach of National Ladder Safety Month only expands with the support of its sponsors. They are the driving force behind helping to raise awareness on safe use and decreasing these tragic numbers. ALI, the only approved developer of safety standards for the U.S. ladder industry, is the present sponsor for National Ladder Safety Month. Other major sponsorship opportunities are also available and can be found by reading the 2025 prospectus. Sponsorship packages are available at a variety of participation levels, each with a slate of promotional benefits for sponsors, including logo appearance on materials, tagged recognition in social media posts, social media mentions, listings in press releases, dedicated email blasts to ALI’s database of more than 23,500, web banner ads, and more. The 2024 campaign delivered to sponsors more than 900,000 social media impressions, more than 264 million press release impressions, and an email open-rate of 38%, which is 13% higher than the industry average. The Top Cap sponsor (limited to one) earns the most benefits, for a participation level of $25,000. There are also opportunities for Middle Rung Sponsors, First Rung Sponsors, Supporting Partners, Associates, and more, with participation levels starting at just $500. The theme of National Ladder Safety Month 2025 is “Every Step Matters.” It serves as a reminder of the necessity to be present and mindful at all times on a ladder, as well as the importance of making ladder safety part of regular safety training. The goals of the campaign are to raise awareness of ladder safety, decrease injuries and fatalities caused by ladder misuse, and increase the number of people certified in Ladder Safety Training.
Power Adhesives launches first-to-market biodegradable hot melt for carton and corrugated packaging industry
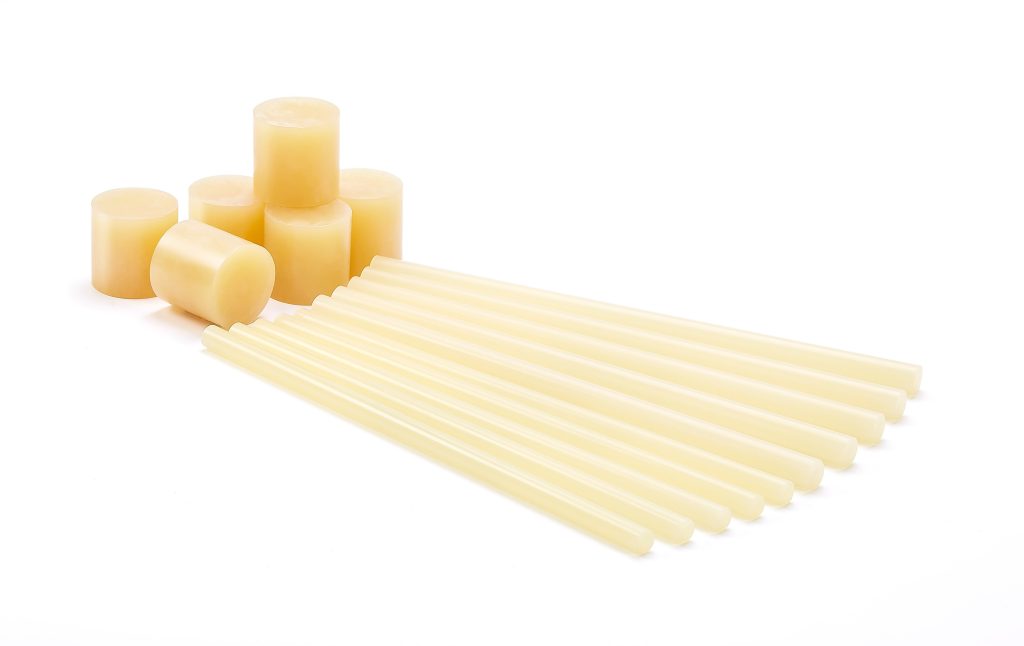
Brands, converters & packers can support the circular economy with latest adhesive innovation Marking a world-first, UK-headquartered Power Adhesives has announced the launch of its fully certified, biodegradable, shaped hot melt adhesive designed for use by carton, corrugated packaging & POS converters, as well as contract packers. Certified to completely break down in the presence of oxygen, leaving behind only non-harmful products and no microplastics, Tecbond 214B is manufactured with 44% bio-based materials and certified to ASTM D6400 and EN13432; the EU standard that sets out the requirements for compostable and biodegradable products. Brendan Colgan, Power Adhesives Chief Executive Officer, said: “This is an exciting time for the packaging industry. All players in the supply chain are working hard to drive sustainable products and processes into the market to support brands and consumers, and this is truly a groundbreaking moment for the packaging adhesives sector. “Brands and their packaging partners often expect new sustainable solutions to come at a premium cost. With Tecbond 214B, we’re delivering the adhesive quality and performance our customers have come to rely on combined with the same competitive pricing – no compromise. We recognise that the climate emergency is driving entire industries to step up and become more sustainable. While we’re working on our sustainability journey, we hope this innovation will lead the way for the packaging adhesives industry.” Available globally, Tecbond 214B offers the same performance characteristics as standard tecbond, with a high level of tack and fast setting speed providing an almost instant bond once applied and compressed. This enables companies to drive efficiency into packing procedures, improving workflow and output. Tecbond 214B is also an indirect food contact approved, enabling it to be used in all areas of the food packaging process, from wrap-around cartons and boxes to shipping packaging.
Toyota Material Handling and Raymond Corporation celebrates grand opening
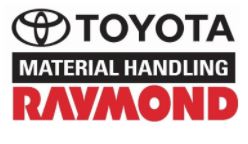
Expansion brings new workforce, economic opportunities to New York’s Southern Tier The Raymond Corporation and Toyota Material Handling, two companies within Toyota Material Handling North America (TMHNA), announce the official opening of the Energy Solutions Manufacturing Center of Excellence in Broome County, New York. The facility, managed by The Raymond Corporation, will manufacture lithium-ion batteries, as well as thin plate pure lead battery technology for both Toyota® and Raymond® products. The culmination of many years of hard work, this facility significantly advances Raymond’s manufacturing capabilities and provides expanded workforce opportunities in the Binghamton, New York, area and beyond. Additionally, as a supporter of the New Energy New York initiative, this project builds on the state’s efforts to support next-generation energy resources. “This grand opening marks a significant milestone in our company’s journey,” said Michael Field, president and CEO, The Raymond Corporation. “But more important, it represents our commitment to the future by bringing jobs, growth and opportunity to advance the community and the material handling industry and by offering our customers superior energy solutions to fit their unique needs.” “This facility is a testament to our long, rich history of innovation and developing advanced technologies,” said Jennifer Lupo, vice president of energy solutions, supply chain and leasing, The Raymond Corporation. “With the growing range of solutions available to support electric-powered equipment in facilities, we’re excited to continue driving industry advancement through our latest innovations and offerings.” “Binghamton’s battery hub keeps sparking new growth,” said Sen. Chuck Schumer. “I am thrilled The Raymond Corporation and Toyota Material Handling have picked Broome County as the home for their new Energy Solutions Manufacturing Center of Excellence which will help manufacture lithium-ion batteries and other critical battery technology. For years, I have worked to craft and lead legislation to bring battery manufacturing back to America, and this investment today shows how the Binghamton area continues to prove it is ready to lead America’s battery future. Now forklifts and other electric-powered equipment that keep our country’s factories running smoothly will be powered by technology developed and made right here in the Southern Tier. From my CHIPS and Science law to the American Rescue Plan, I have helped deliver over $100 million in federal and other public investment to help the Binghamton area and upstate New York be prepared for opportunities like this one. With investments like this, we are securing Broome County and the Southern Tier region’s spot as the next loop on America’s battery belt.” Empire State Development (ESD) President, CEO and Commissioner Hope Knight said, “Expanding New York state’s green economy is a top priority for Gov. Kathy Hochul and for ESD. We’re proud to support The Raymond Corporation’s commitment to driving alternative energy applications in the lift truck manufacturing industry and thrilled that this century-old Southern Tier company is continuing to create economic opportunities and quality jobs throughout the region.” Lithium-ion batteries offer significant benefits, such as avoiding removal from the lift truck, opportunity charging and less intensive maintenance compared with lead-acid batteries. This leads to increased labor efficiency and reduced downtime. The Energy Solutions Manufacturing Center of Excellence will enable TMHNA to develop a more diverse portfolio of energy solutions as industry demand for electric products continues to grow. “We are dedicated to powering a greener future, and this strategic investment will help us on that mission,” said Josh Linnemann, vice president of engineering, Toyota Material Handling. “Most important, we are committed to doing whatever it takes to solve our customers’ evolving problems. The Energy Solutions Manufacturing Center of Excellence will allow us to create so much value for our customers by developing and producing solutions to meet each customer’s unique needs.”
Bobcat to debut Several New Machines at Equip Expo 2024
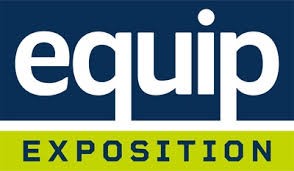
Bobcat invites the media to see and experience some of its latest products for grounds maintenance, turf renovation and landscaping professionals across several indoor and outdoor booth spaces at Equip Expo 2024: Indoor booth #3052 Outdoor booth demo areas #7506D and #7700D Outdoor UTV Driving Experience First Time Ever – Attendees Can Experience the World’s First All-Electric Compact Track Loader Equip Expo attendees will have the unique opportunity to experience the Bobcat T7X, the world’s first all-electric compact track loader. While the machine has been on display at prior trade shows, this will be the first time attendees can operate the loader as part of Bobcat’s exhibit. The T7X is commercially available at select Bobcat dealerships and available to rent through certain Sunbelt Rental locations. New Utility Tractors on Display Introduced in June 2024, Bobcat’s utility tractor lineup (UT6066, UT6566, UT6573) offers a competitive advantage for hauling, digging, raking, scraping, and more. Bobcat will display its UT6573 at this year’s show. Bobcat utility tractors feature 12×12 power shuttle transmissions that deliver smooth shifting without stepping on a clutch pedal. Powered by turbocharged, Tier 4 diesel engines, these tractors offer robust performance, low-end torque, and an efficient fuel system. The tractors offer easy service access, simple maintenance, and reduced noise and vibration for more comfortable driving. The climate-controlled cab, which comes standard on the UT6566 and UT6573, provides year-round comfort. The utility tractors also feature wide glass panels on models with cabs, convenient visibility to the 3-point hitch, power and tilt steering, and ergonomic controls that enhance operator performance and minimize fatigue. Bobcat Turf Renovation Equipment Bobcat turf renovation equipment includes aerators, sod cutters, dethatchers and overseeders that serve landscaping and grounds care professionals across a variety of industries including golf, sports turf, landscaping and rental. These turf renovation products officially joined the Bobcat brand in early 2024 following a brand transition from RYAN. The SC18H sod cutter, AE19 aerator, AE30S aerator, DT18 walk-behind dethatcher and verticutter will be on display at Bobcat’s indoor booth. ZT5000 Zero-Turn Mower The Bobcat ZT5000 is a high-performing, turf-taming machine designed to tackle challenging mowing tasks with precision and ease. It is equipped with an AirFX™ cutting system with a deep, bullnose-deck design that increases vacuum, lifting grass to the blade for a superior cut while the bolt-on, air-gap baffle technology accelerates under deck airflow for a professional finish. The ZT5000 is available with two cutting deck sizes: a 52-inch or 61-inch deck. AT450 Articulating Tractor The Bobcat AT450 articulating tractor is a four-season machine that excels at material handling, turf maintenance, slope mowing and snow removal, and is an ideal solution for landscapers, hobby farmers, golf course groundskeepers and sports facility professionals. The tractor’s articulating and oscillating frame keeps all four wheels in contact with the ground—even on rough, uneven terrain—helping with stability and limiting turf disturbance. The Bobcat booths will highlight an array of other products including compact tractors; light compaction; small articulated loaders; compact track loaders; compact excavators; portable power equipment; utility vehicles; and walk-behind, stand-on and zero-turn mowers. Bobcat will also show its ZT6000e electric zero-turn mower and its ZT6200 autonomous mower prototype. Equipment on display will also feature optional accessories and innovative attachment offerings like the disc mulcher and Brushcat™ rotary cutter. Additional Equip Expo Experiences with Bobcat Bobcat is returning for the fourth year in a row with its zero-turn mower giveaway at 1:30 p.m. on Oct. 17 in its indoor booth (3052). Show attendees can enter to win a brand new ZT7000 zero-turn mower by bringing their entry ticket included on their attendee badge to the Bobcat indoor booth. Must be present to win. Bobcat is also co-sponsoring the Equip Expo arena concert featuring Trace Adkins with an opening performance by Clayton Q., at 7 p.m. on Oct. 17 at the KFC Yum! Center.
Episode 519: Cold Chain visibility with Coldcart
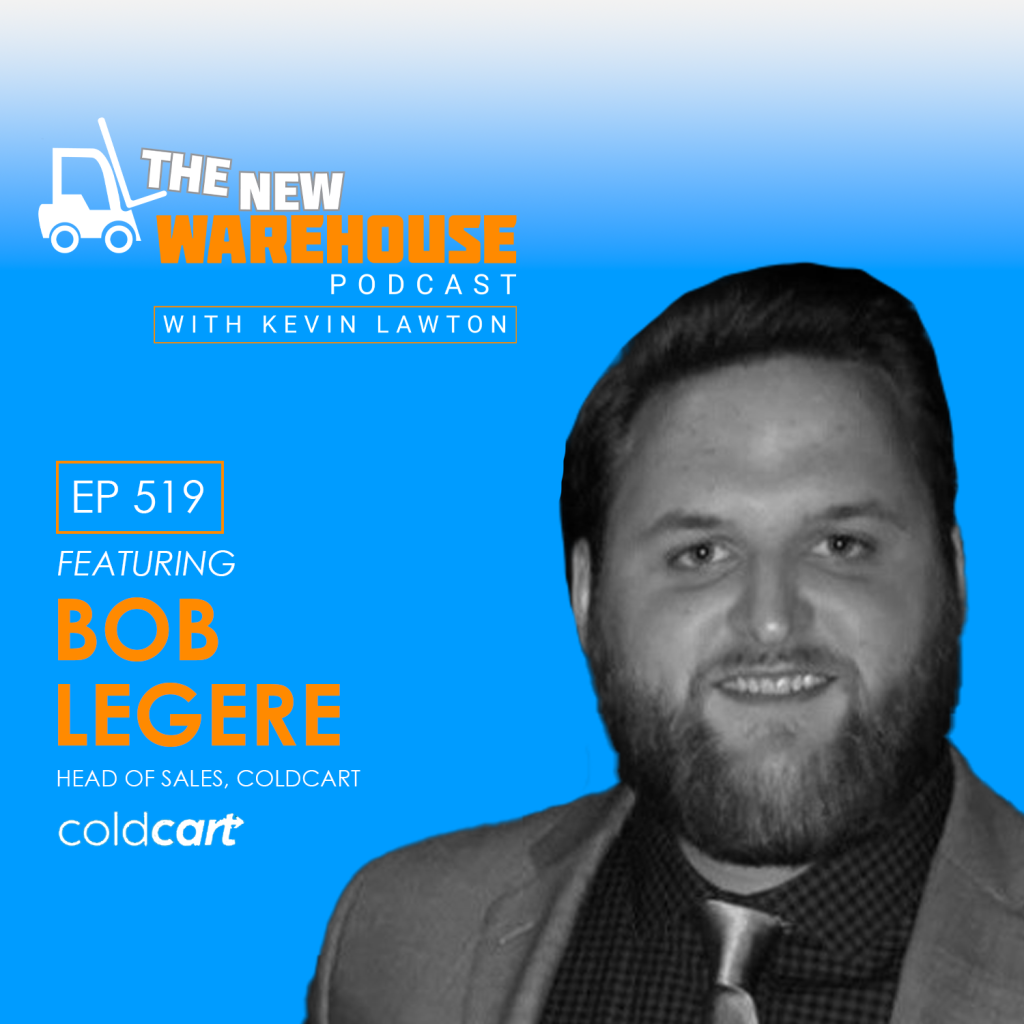
In this episode of The New Warehouse Podcast, Bob LeGere, Head of Sales at Coldcart, joins us to share insights into the world of cold chain fulfillment. Bob shares valuable insights into how Coldcart is revolutionizing the cold chain space by offering enhanced cold chain visibility and customized solutions for managing perishable goods. We explore the differences between fulfilling cold chain versus dry goods and discuss the unique challenges and opportunities when dealing with temperature-sensitive products. The Cost of Cold Chain Logistics When transitioning from dry goods to cold chain logistics, companies often face significantly different cost structures. Bob emphasizes, “The name of the game is always cutting costs, but that’s not necessarily the case with perishables.” Unlike non-perishable goods, where cost reduction is paramount, in cold chain logistics, the focus shifts towards minimizing risk and ensuring timely deliveries. For example, Coldcart’s system tracks weather patterns to decide whether it’s safe to ship orders, reducing the risk of spoilage and costly reshipments. Cold Chain Visibility and Customization One of the differentiators of Coldcart is its advanced system that provides unparalleled cold chain visibility and customization options. Bob explains, “It’s all about visibility and tracking. If you can find someone that will give you more visibility, customization, and flexibility—that’s what you should be looking for.” Coldcart’s platform not only allows businesses to adapt to real-time conditions, such as unexpected temperature spikes, but it also offers the ability to create rules based on these variables, ensuring that perishable goods are always shipped under optimal conditions. Partnering for Growth in the Perishable Space Bob discusses the importance of building partnerships with brands early on and growing alongside them. He notes, “There’s more value in partnering with brands early on and growing alongside them than just trying to steal the biggest volume shippers.” This approach allows Coldcart to tailor their services to the specific needs of smaller brands, helping them scale while maintaining the quality and integrity of their perishable products. Bob parallels his experience at ShipBob, where he witnessed the evolution of non-perishable e-commerce, which he believes is now happening in the perishable space. Key Takeaways Cost Management: In cold chain logistics, the focus shifts from cost-cutting to risk management, particularly regarding timely deliveries and avoiding spoilage. Visibility and Flexibility: Coldcart’s platform offers real-time tracking and customizable rules that help businesses optimize the shipping process for perishable goods. Growth Partnerships: Building early brand partnerships is crucial for long-term success in the perishable space. The New Warehouse Podcast Episode 519: Cold Chain Visibility with Coldcart
Superior Tire & Rubber Corp. celebrates 60 years
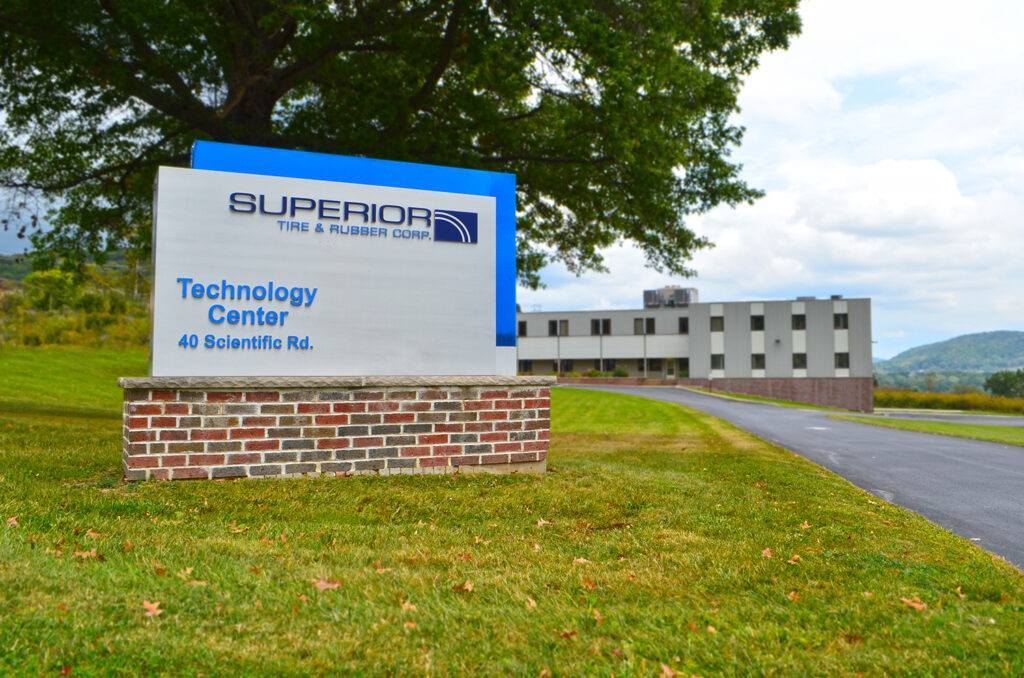
Superior Tire & Rubber Corp. celebrates its 60th anniversary, commemorating six decades of dedication, innovation, and leadership in the polyurethane and rubber industry. Founded on September 15, 1964, as an automotive retailer and tire recapping business in Warren, Pennsylvania, Superior Tire has evolved into a major player in the polyurethane and rubber markets. Superior Tire’s products (still manufactured in Warren, PA) have a global reach in five focused business areas that help drive material handling solutions, build roads and buildings, plant and harvest the food we eat, and keep a variety of specialized industrial equipment up and running in a 24/7 world. During its growth, Superior Tire has never forgotten its roots and, as a result, has become a respected local enterprise known for its commitment to community, quality, and industry advancements. “This is a proud moment for Superior Tire,” said Hank LeMeur Jr., president and CEO. “We have faced many challenges and exciting wins over the years, and I have no doubt we’re set up to execute strongly in the next 60 years.” A Legacy of Innovation Superior Tire’s vision is to be the vendor of choice by offering its customers a technical advantage, providing those customers with a significant lead in their market. This bold vision could not be achieved without a first-class Engineering department delivering innovative products that stand the test of time. Led today by Joseph Peterson, PhD, VP of Engineering & Quality, his team is staffed with ten passionate engineers who hold nine granted patents with an additional four patents pending. “Our team of experienced individuals is focused on improving design and advancing solutions in the markets we serve,” said Joe. “As we continue to grow, we will need additional talent to join our team to continue creating the technical advantage that our customers expect.” While focusing on new product developments, the Superior Engineering team emphasizes quality and continuous improvement within the manufacturing process and has a talented team of in-house mold designers. Manufacturing Philosophy – The Superior Way Today, Superior Tire has over 375 employees (300 in production) who produce nearly 1.3 million parts annually at its three manufacturing plants in Warren, PA. As the company has grown, it needs to adapt to new manufacturing philosophies, first-class safety standards, and sustainable processes (ISO-9001) to ensure the highest quality possible. In 2018, Superior Tire adopted the Superior Production System, which mimics the Toyota Production System. This system helped bring a shared vision and language to the production floor as demand and growth soared. In addition to process and production systems, Superior Tire has implemented four Universal robot cobots, three Fuji robotic machining centers, four high-speed rotary molding lines, and six auto-feed trimming machines over the last five years. “Innovation in manufacturing processes is fundamental to sustaining our continued growth,” said Beau Kibby, VP of Manufacturing & Warehousing. “Each day, we challenge ourselves to develop new processes that improve our output while sustaining our quality standards.” Safety is core to everything at Superior Tire, and they celebrate safety by recognizing employees who achieve 1,000,000 minutes of work safety. Over the years, Superior Tire has recognized 54 teammates who have achieved and exceeded this safety milestone and one teammate who achieved the coveted 5,000,000 minutes, equating to 40+ years of work safety! Celebrating the Superior Family Over the last 60 years, many employees and teammates have helped make Superior Tire & Rubber Corp. what it is today. Although there are too many to mention in this article, we want to take a moment to thank each employee (past and present) for their dedication, effort, perseverance, vision, and teamwork! As a small tribute of our appreciation to our employees and the community, Superior Tire is hosting an open house at 1818 Pennsylvania Ave in Warren, PA, on Saturday, September 14 (10:00 AM to 1:00 PM) for employees and their families to participate in celebrating our 60th anniversary. The public is welcome to join our celebration! Calynne Neff, HR Manager for Superior Tire, added, “We are proud of all our current and past teammates and look forward to a fun day together. Superior continues to add to our workforce, and we hold open interviews each Wednesday at our plant on Penn Ave. If you’re looking for a new career challenge with a path to grow, come and talk to us!” Looking Ahead Superior Tire is deeply rooted in its history and is spreading its wings as it looks excitedly to the next 60 years. “In my view, we are just getting warmed up!” said Jared Steier, VP of Sales and Marketing for Superior Tire. “There are so many exciting partnerships and products that will sustain our market share and growth in the years to come. By offering innovative, performance-delivering products in the material handling, construction, agricultural, and industrial markets, we have nowhere to go but up! We are investing in the right markets, manufacturing strategies, and engineering excellence to ensure we can meet the needs of today’s and tomorrow’s partners.” He concluded, “It truly is an exciting moment in our 60-year history.”
American Logistics Aid Network calls on industry businesses to help with Tropical Storm/Hurricane Francine relief
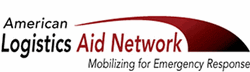
As Tropical Storm/Hurricane Francine intensifies and approaches the Gulf coast, the American Logistics Aid Network (ALAN) is urging area residents to heed safety advisories – and reminding members of the logistics community that their post-storm help could be needed soon. “All signs point to Tropical Storm/Hurricane Francine making landfall as a Category 2 hurricane, and because the area has experienced so much rain in the past two weeks, officials are expecting lots of downed trees, significant power outages, and water systems disruptions that could last several days. Inland flooding is likely across Louisiana and parts of Mississippi and Texas,” said Kathy Fulton, ALAN’s Executive Director. “As a result, we have already begun receiving requests for assistance – and we are mobilizing accordingly.” In addition to working closely with the non-profit and emergency response community, ALAN is monitoring the storm’s real-time path and supply chain impacts—including damages to roads, ports, and airports—via its Supply Chain Intelligence Center, which individuals and businesses can access free of charge. ALAN has also updated its Disaster Micro-Site with helpful Tropical Storm/Hurricane Francine resources. That site is where ALAN will post requests for donated logistics assistance, most of which will start arriving within 24 to 72 hours after the storm’s initial landfall. Logistics businesses that wish to make a financial donation to ALAN instead can do so by visiting https://www.alanaid.org/donate/. “On a final note, we encourage businesses to give their employees who live on the Gulf Coast ample time to prepare or evacuate, even if it means closing down early or temporarily suspending operations,” she said. “Staying safe should always be priority number one. “We hope that these efforts and our advisories will prove to be merely precautionary and that Tropical Storm/Hurricane Francine’s effects won’t be as significant as predicted. Meanwhile, please join us in holding good thoughts for the residents of the Gulf Coast.”
EP North America debuts new Lithium-Ion Battery Powered Forklifts
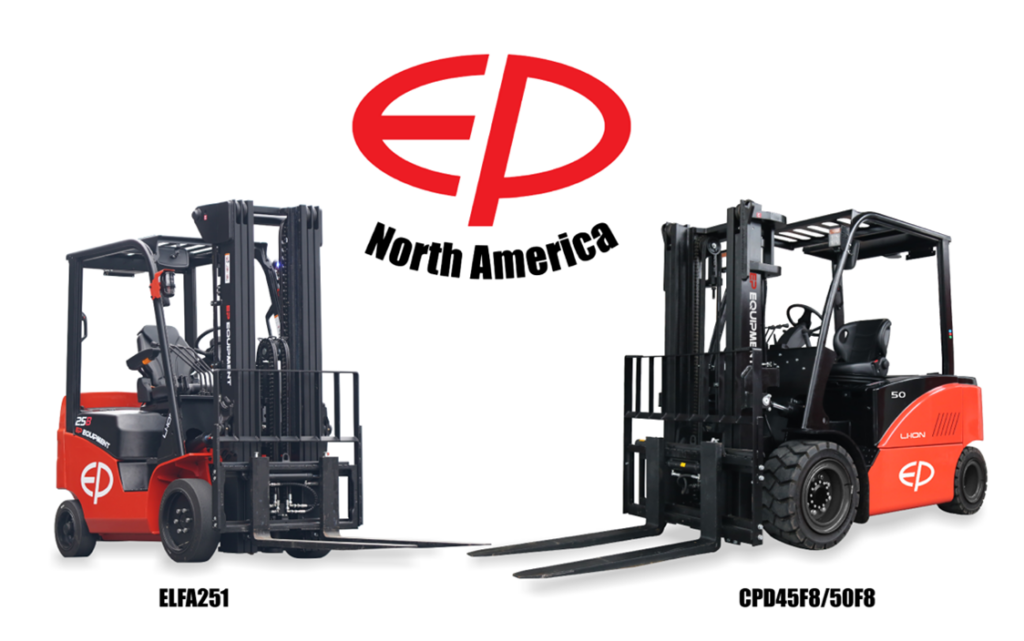
With innovation and ease of use in mind, these forklifts can upgrade operations for success EP North America, a fast-growing, lithium-ion-focused material handling equipment provider offering innovative and competitive options to the market, today debuted two new forklifts. The CPD45F8/50F8 and EFLA251 help warehouse and DC managers provide robust lithium-ion solutions to upgrade any diesel and LPG warehouse vehicle fleet. They are available today via EP North America’s dealer network. “EP North America continues to expand its portfolio to solve a wider range of material handling applications, leveraging our unparalleled strength in lithium-powered solutions,” said Jason Bratton, general manager of EP North America. “Whether leading occasional or multi-shift operations, these lithium-ion powered solutions provide exceptional value, quality, and dependability that we believe our dealer network and their customers have been looking for.” The CPD45F8/50F8 is an IPX4-rated, pneumatic forklift designed for outdoor use to suit applications up to 10,000 lbs. The CPD45F8/50F8 utilizes an integrated EP Energy 80V lithium-ion battery, requiring zero maintenance and eliminating ongoing fuel costs associated with diesel/LPG units. Removing the internal combustion engine reduces fatigue by eliminating vibration, heat, noise, and exhaust, creating a more comfortable and productive work environment. The EFLA251 is a Class I forklift engineered to provide a direct alternative in both utilization and cost to the Class IV LP equivalent. Featuring a lifting capacity of 5,000 lbs., the EFLA251 is powered by an EP Energy 80V Lithium-ion battery with onboard charging as a standard feature and can empty to full in just over two hours, eliminating all dependencies on LPG. EP controls cost and supply through a vertical integration strategy that ensures readily available stock and consistently short lead times on factory orders. EP has loaded dedicated demo units to its fleet to make available through the remainder of 2024, supporting its efforts in driving conversion adoption from IC to E.
PneuTech highlights the RK Fixed speed air compressors
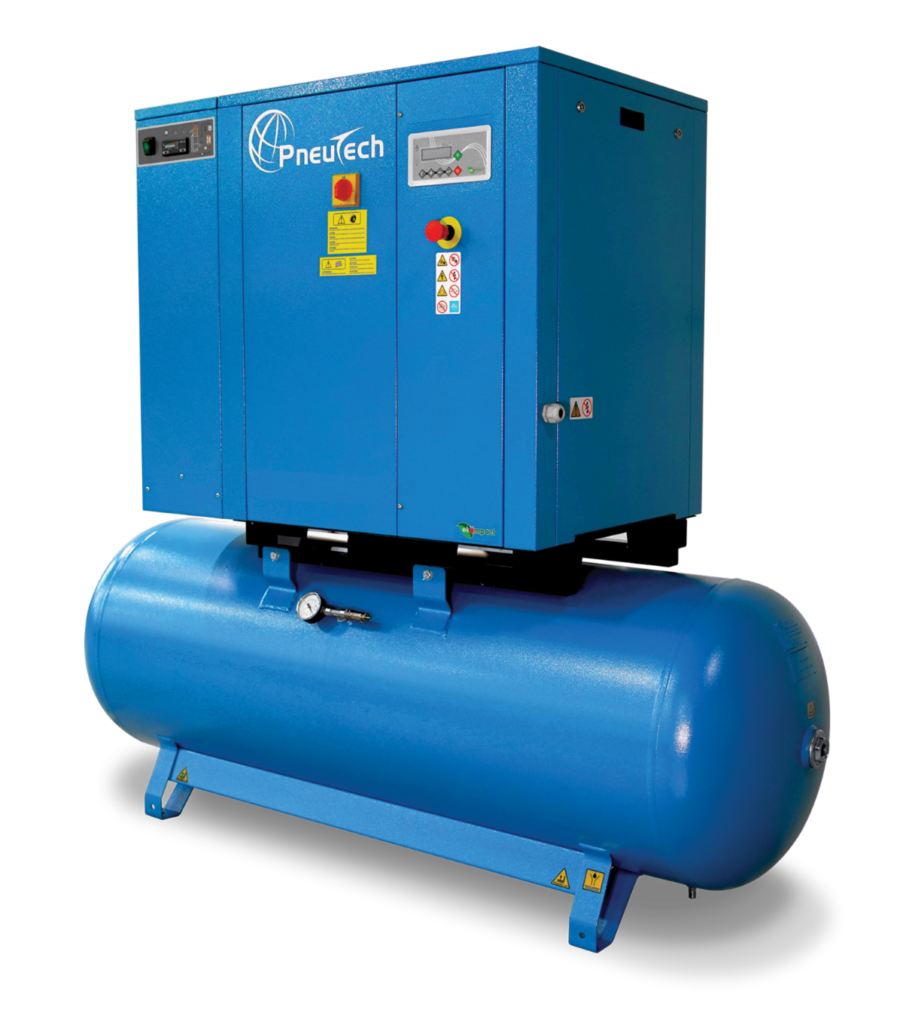
Integrated dryer package ensures consistent, dry, clean air in a compact, economical design PneuTech highlights the RK Rotary Screw Air Compressor Fixed Speed Series with Integrated Dryer, which delivers consistent, dry, clean air while optimizing both cost and floor space. This innovative and streamlined design provides a dependable and easy-to-maintain solution for industries such as metalworking that depend on high-quality compressed air. The integrated design minimizes the need for extensive piping and electrical connections typically required for standalone dryers, significantly conserving valuable floor space and reducing installation costs. These compact models, available in models ranging from 5-20 hp (19.9–73.8 CFM), are designed for straightforward operation. Each unit comes equipped with a digital dewpoint indicator and an electronic dryer controller, which monitors the compressed air’s dewpoint and manages the condensate drain. The design prioritizes serviceability and safety, featuring an easily removable panel allowing quick access to all key dryer components. This simplifies maintenance tasks, such as cleaning condenser coils and performing repairs. Additionally, every model has a service valve between the receiver tank and the dryer module, ensuring safety during maintenance or repair activities. The single-point condensate drain simplifies connections to the condensate management system using a 1⁄4” line. Additionally, a conveniently accessible cabinet filter, standard on all RK Series air compressors, is washable and promotes prolonged filter life, reducing overall maintenance requirements. RK Fixed Speed Rotary Screw Air Compressors also feature an oversized air-oil separator tank and element to facilitate effective three-stage separation, achieving less than 3 ppm oil carryover and a pressure drop of less than 0.02 bar. The highest air quality is assured with renowned Mann filtration. PneuTech offers a 5-Year Warranty on major components, including the air end, oil sump tank, electric motor(s), air cooler, and oil cooler, along with a 1-Year Warranty on the entire unit (regular maintenance not included).
Seven deadly sins of manufacturing
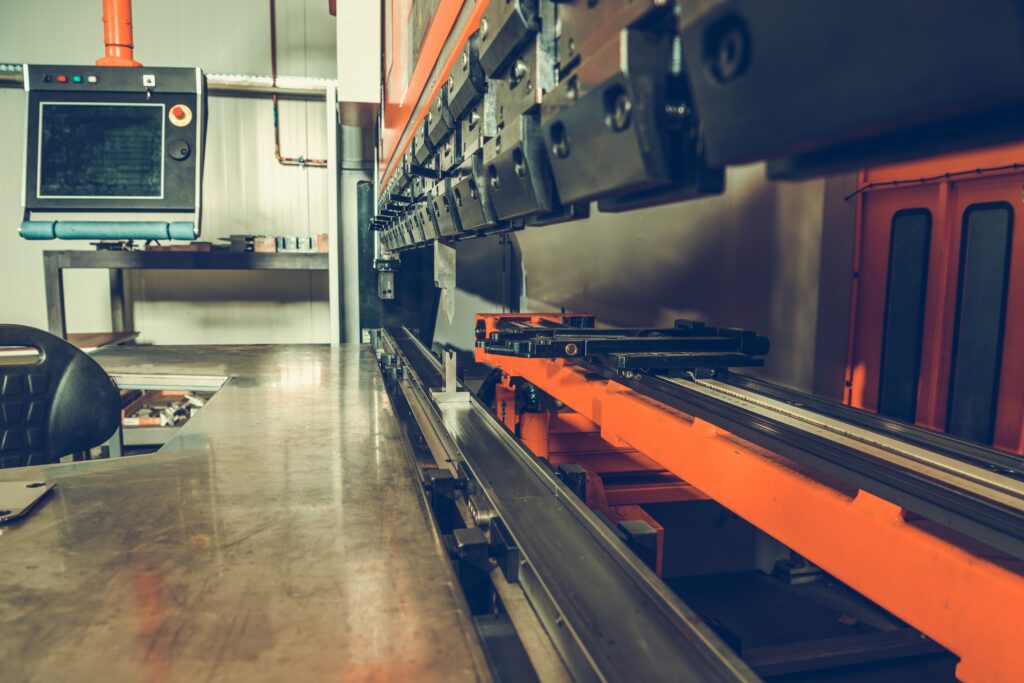
Learning how to identify and prevent these sins will reduce or eliminate unnecessary waste, improve efficiency and productivity, protect profitability and cash flow, and uphold your company’s reputation. If any of these sins are lurking within your business, here’s how to identify and rectify them. Transportation Delivering products on time to manufacturing customers is essential for building vendor loyalty. However, waste created by unnecessary movement of raw materials, finished goods, or work in process (WIP) can make it difficult to meet expected shipping dates, leading to increased costs and dissatisfied customers. In addition to wasting fuel and energy costs, excess transportation can also trigger other wastes such as waiting and motion. Transportation waste often results from poor plant design, such as large distances between operations. It can also be generated by large batch sizes, poorly designed production systems, and multiple storage facilities, as well as inefficient material flows during storage, retrieval, and transfer. To prevent this kind of waste, design a sequential flow from raw materials to finished goods, don’t store WIP in inventory, and maintain consistency and continuity when assigning job priorities. Value stream mapping (VSM), a lean manufacturing technique for analyzing, designing, and managing the flow of materials through the shop floor, can be very effective in identifying transportation waste. It involves full documentation of all aspects of your production flow rather than just mapping specific production processes. The voice of the customer (VOC) can be used in conjunction with VSM to add important information. If your VOC has information critical to success that is not supported in your VSM, (e.g. customer says they want delivery in X days, your VSM says the process takes more than X days) the two documents together can guide the improvement efforts. Inventory Excess inventory is a form of waste related to the holding costs of raw materials, WIP and finished goods. In addition to driving up inventory costs, this deadly sin ties up capital, takes up space, and allows for inventory to age and obsolete. Excess inventory is a good indicator of other issues within the production process. Excess material purchasing resulting from poor forecasting and production planning is often caused by a poorly designed link between the procurement department and the manufacturing and scheduling departments of an organization. Due to a lack of visibility and an unknown future, procurement is forced to err on the side of ordering too much material. Purchasing raw materials only when needed and reducing the need for safety stock will minimize this waste. ERP Inventory software simplifies this process by tracking inventory counts with remarkable accuracy to facilitate the reduction of over- or under-purchasing. Mobile barcode scanning for inventory receiving and movement can reduce this type of waste by providing high levels of inventory visibility and control. It reduces the need for manual inventory and cycle counts, increasing the accuracy of stock on hand. Real-time inventory data improves the performance of forecasting software so purchasers know when to order more stock. Motion This deadly sin consists of unnecessary movements by employees or machines that don’t add value to the product or service. Common sources of motion waste include poor workstation layout and negligent production planning and process design. Shared equipment and machines, siloed operations, and lack of production standards can be added to this list. Motion on the shop floor can include reaching for raw materials, walking to get tools or materials, or moving finished goods out of the work area. Redesigning your shop floor to simplify the work will help reduce excess motion. In the office, wasted motion can include searching for files, sifting through spreadsheets or multiple folders to find what is needed, excess mouse clicks, and double data entry. ERP software can jettison a lot of this waste by automating processes to eliminate manual data entry, reduce paper, and simplify purchasing and receiving. Implementing 5S, a five-step methodology that creates a more organized and productive workspace can also play a role in minimizing motion waste: Sort – Keep only what you need Set in Order – Keep it organized Shine – Keep it clean Standardize – Keep it the same across workstations Sustain – Keep it consistent over a long-time horizon Waiting Wasting time waiting for materials, information, equipment, or people is considered a sin because it slows production, increases costs, and adds no value. Furthermore, it can prevent finished goods from being delivered on time – a bigger sin in the minds of customers. A major source of waiting occurs when production employees don’t know which job to be working on now and what comes up next or have not been provided with the necessary raw materials. ERP software can solve that problem by making the information directly available to machinists without leaving their workcenters and providing the warehouse with a dispatch list of jobs slated to start. To reduce this waste, use VSM to analyze the total time spent working on jobs from order to shipment and summarize the amount of time where value is not added to your product. Make the process flow as seamless as possible by creating buffers between production steps and create standardized instructions to provide consistency in the method and time required for each step. Four rules to minimize waiting waste: Automate scheduling so workers always know what to do and when. Design processes to ensure continuous or single-piece flow. Have standardized work instructions. Develop multi-skilled workers who can quickly adjust to unexpected work demands. Overproduction Overproduction occurs when manufacturing the product is required or before it is asked for. Often referred to as the “just in case” sin, manufacturers tend to use overproduction as a backup in the event of unexpected increases in demand. However, it can lead to a rash of problems, from preventing smooth workflow and increased storage costs to hidden defects within WIP. All of which require additional capital to fund excessive lead times and the production process. Strategies for terminating overproduction include: Use a pull system to control manufacturing