Kito Crosby has launched a self indicating dynamometer
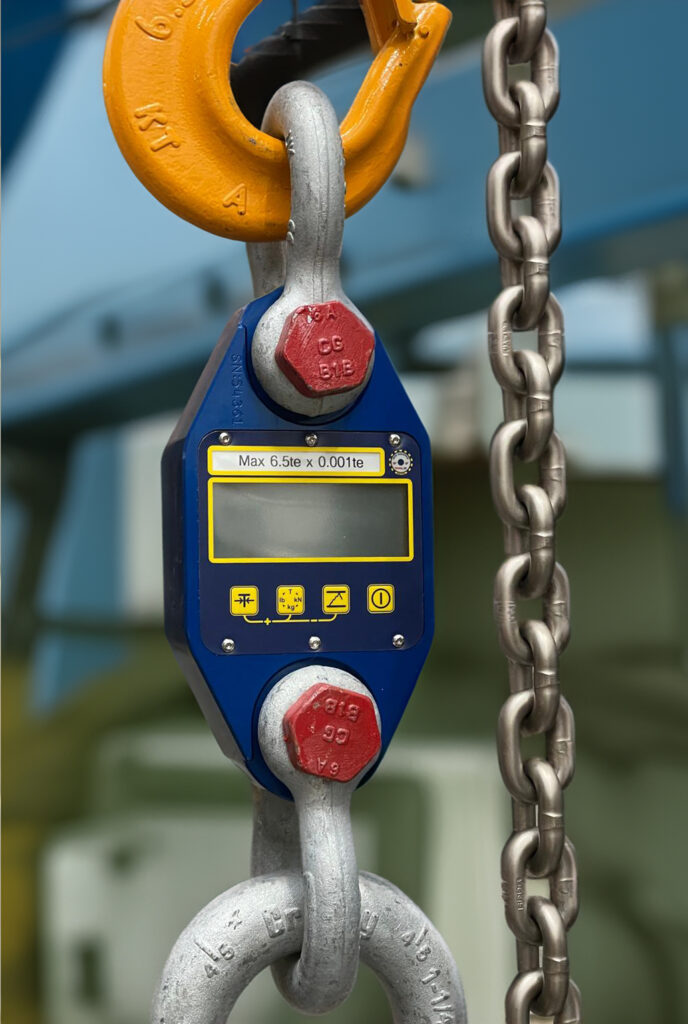
Kito Crosby announces the launch of the Crosby Straightpoint Self-Indicating Dynamometer (SID) – designed to replace outdated mechanical products. The Crosby Straightpoint Self-Indicating Dynamometer (SID) is a dynamic self-indicating version of the well-known Crosby Straightpoint product ‘Bluelink.’ The SID is available in a 6.5t capacity with advanced features and benefits, providing solutions where proximity load monitoring is required, such as when operating lever or chain hoists at height or lifting vehicle motors. Providing accurate load measurement and incident prevention, this dynamometer is rigged using industry-standard shackles such as Crosby G2130 shackles with a compact design to minimize headroom loss (6.14” or 156mm from eye to eye). Constructed with high-grade aircraft-quality aluminum and with a safety factor of 6:1, its lightweight design does not sacrifice on strength. The Crosby Straightpoint link style dynamometers are on average 30% lighter than those of other suppliers. The easy-to-read 6-digit LCD screen provides a fast and accurate readout, and features: Tare and preset tare Selectable measurement units (lbs, kg, kN and tonnes) 100Hz high-speed peak hold Audible set-point alarm Overload counter Additional features include a battery life of 80 hours of continuous use and an optional connection to a hand-held readout device with the ability to connect to four dynamometers simultaneously. The Crosby Straightpoint SID is a smart lightweight solution for measuring the load in a variety of applications including aircraft engine installation and maintenance, gantry cranes, steel beam fabrication, general weighing, tie downs, towing and linesman tensioning. Peter Hird, Commercial Director for Crosby Straightpoint and Crosby BlokCam said, “This is a natural progression from the Bluelink which is our popular entry-level wireless loadcell. Many applications are close-up and hands-on such as operating a lever hoist and the ability to view the load on the load cell while the operator is in close proximity is imperative in many applications. This entry-level dynamometer will allow more users to measure and know the load, furthering job site safety and productivity.”
Semi-automated pallet shuttle technology optimizes material handling storage
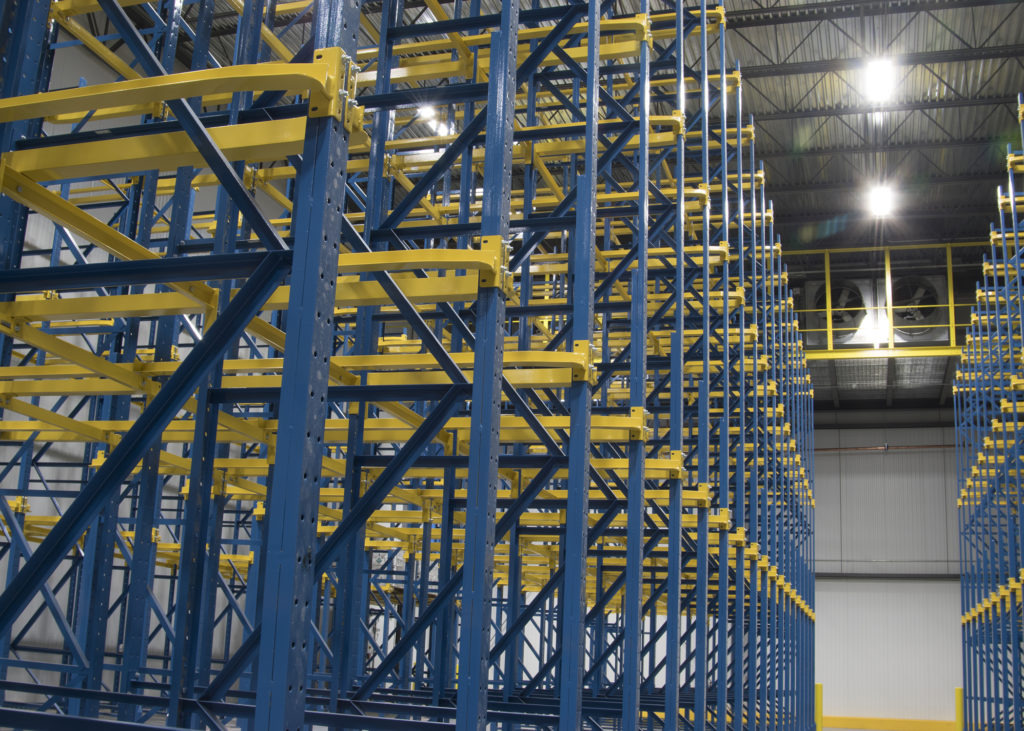
For businesses seeking optimal warehouse logistics management, Steel King Industries, an OEM with extensive expertise in designing and manufacturing high-quality pallet rack systems, offers a new semi-automated technology as a turnkey solution. The pallet shuttle is a lithium-ion powered Pallet Runner™ deep lane storage system from partner Automha Americas, a pioneering pallet shuttle provider, that efficiently moves pallets in and out of high-density storage lanes, creating increased storage density in an existing space. The system is particularly suited to applications with high-volume SKUs, as pallets are loaded into the system by lift truck and transported into deep lanes by the Pallet Runner cart. Once the load is positioned, the cart returns to the front of the system to receive the next pallet. The lift truck operator travels only between load source and lane entry, and the cart does the rest. This maximizes productivity and minimizes travel distance for both product loading and unloading. The Pallet Runner is a cost-effective option for companies looking to streamline their storage processes, reduce operational costs, and ensure a competitive edge in the rapidly evolving market. The deep lanes of the system increase storage density by reducing aisles and utilizing depth space, maximizing storage capacity within the same footprint. The system moves quickly and seamlessly, enhancing efficiency, expediting pallet loading/unloading, and reducing wait time for trucks at loading docks compared to traditional forklift operations. The system can be scaled up or reconfigured with relative ease to accommodate growth or changes in product lines. With less need for forklift drivers to enter storage lanes, the Pallet Runner system reduces labor requirements and associated expenses while improving safety. “The seamless integration of the pallet shuttle technology with the pallet rack systems will offer warehouses and distribution centers increased automation, efficiency, flexibility, productivity, and safety,” said Don Heemstra, VP of Sales and Marketing for Steel King. About the Author: Del Williams is a technical writer based in Torrance, California.
Episode 518: Finding Your Perfect 3PL Partner with Matt Hertz
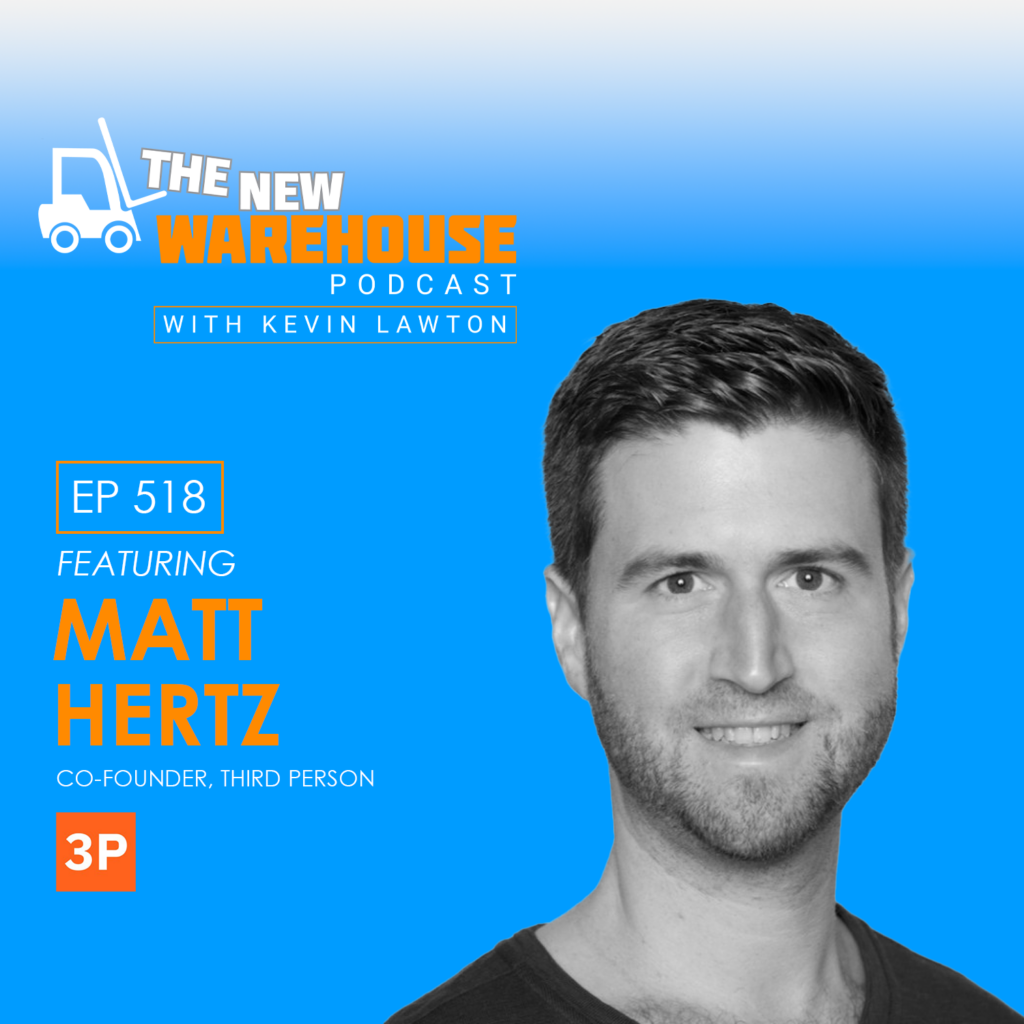
The New Warehouse Podcast welcomes Matt Hertz, the co-founder of Third Person and Second Marathon. Matt’s journey through the e-commerce landscape, from selling sports cards online in the late ’90s to becoming a pivotal figure in the logistics and fulfillment sectors, provides valuable insights. His experience working with major e-commerce brands laid the groundwork for his current ventures, which focus on helping emerging e-commerce brands navigate the complex world of third-party logistics. This conversation delves into the challenges of rapid growth, the importance of finding the right 3PL partners, and the evolving landscape of e-commerce fulfillment. From Sports Cards to E-Commerce Giant Matt’s entrepreneurial journey began in Toronto, Canada, where he started buying and selling sports cards online in 1999. This early exposure to e-commerce and logistics provided invaluable lessons. “I started selling on Yahoo auctions, and it was all about fulfilling orders out of my home,” Matt recalls. His passion for e-commerce continued as he moved on to larger ventures, such as being an early employee at Rent the Runway and Birchbox. At Birchbox, Matt played a crucial role in scaling operations from 500 monthly orders to over a million. “We knocked down a lot of walls,” Matt says, reflecting on how their efforts helped pave the way for other subscription-based businesses. The Perfect 3PL Partner Can Scale As e-commerce brands scale, finding the right 3PL partner becomes critical. Matt shares how Birchbox’s rapid growth posed challenges not only for the internal team but also for their 3PL partners. “They didn’t believe us when we said we were going to grow 200% month over month,” he explains. This disbelief was common among partners who were unprepared for such explosive growth. The lesson here? Choose a 3PL capable of handling your current needs but also rapid scaling. Matt emphasizes that this relationship is “like a marriage,” where both parties must be aligned in their goals and expectations. Building a Better 3PL Experience with Third Person Matt’s 3PL matchmaking experience led to the launch of Third Person, a platform designed to help e-commerce brands find the right 3PL partners. He realized that many brands struggled with this process, often relying on Google searches or referrals. Matt notes, likening it to a haphazard approach to dating. Third Person aims to streamline this process by understanding each brand’s unique needs and matching them with the most suitable 3PLs. This service is precious for brands that may not have the resources to engage in a full consultancy but still need expert guidance. Key Takeaways Early e-commerce experience can lay the foundation for success in logistics and fulfillment. Rapid growth requires 3PL partners who can adapt quickly and scale with the business. The relationship between a brand and its 3PL is crucial and should be treated with the same care as a long-term partnership. Third Person offers a tailored solution to help e-commerce brands find the right 3PL, moving beyond simple Google searches to a more informed matching process. The New Warehouse Podcast Episode 518: Finding Your Perfect 3PL Partner with Matt Hertz
BSL Battery to exhibit at Logis-Tech Tokyo 2024
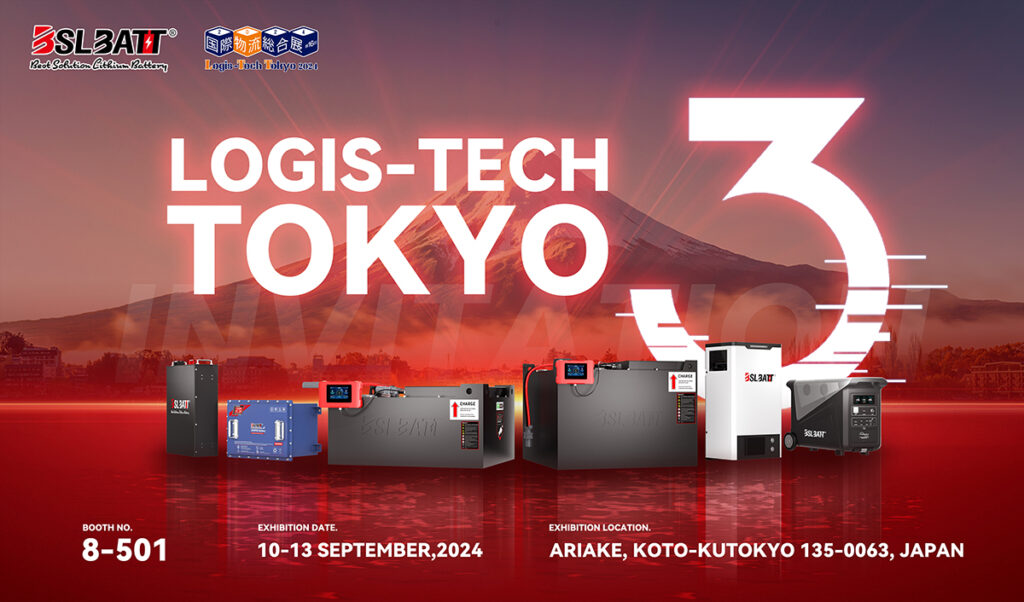
BSL Battery – Industrial will exhibit its integrated and enhanced lithium portfolio at Logis-Tech Tokyo 2024, held at Aricke 135-oo63, Koto-ku, Tokyo, Japan, from September 10 to 13. The booth will showcase a complete and rich lithium portfolio, focusing on the unique and innovative approach to lithium batteries taken by BSL Battery – Industrial to cover the entire battery value chain – a vital aspect of the energy transition to an all-electric future and address the various needs and challenges of customers and providing value to customers, demonstrating how their comprehensive energy storage lithium solutions work together efficiently and reliably to bring more benefits to customers. The booth will guide visitors through a seamless end-to-end journey, covering everything from batteries and chargers to energy management software and comprehensive solutions. The booth will feature the following product-themed areas: Complete energy solutions, including lithium-ion batteries, chargers, and innovative peak load management “BSL cloud,” – are now also available for integration with wall boxes and our industrial energy storage systems BSLBATT® insert batteries are designed to fit most electric pallet trucks, stackers, and order pickers. They are a ready-to-go replacement for most walk-behind pallet trucks, including Caterpillar, Clark, Crown, Big Joe, and Toyota. Thanks to opportunity charging and an integrated charger, they increase uptime and provide greater charging convenience. BSLBATT’s 80 V lithium-ion batteries are designed to accommodate various ground support equipment through its modular design and integral battery management system. As a vehicle that can operate in multiple environments, with locations worldwide, the battery has a temperature range from – 30°. BSLBATT lithium battery charger connected to lithium-ion products. BSLBATT Portable Battery Power Station has a wide range of applications. Whether you are looking for a reliable home backup power supply during a power outage, a camping battery that can maintain your leisurely outdoor off-grid life or an emergency power supply for emergency rescue, the BSLBATT portable power station can meet your needs. Why attend? Explore innovative solutions for clean energy in material handling Connect with industry leaders and experts Get hands-on with our third-generation forklift lithium battery, GSE lithium battery, and portable lithium battery products Don’t miss your chance to be part of the clean energy future! Register now and secure your spot at this must-attend event. https://www.logistech-online.com/en/registration.php Dates: September 10-13 Location: Aricke, Koto-ku, Tokyo 135-oo63, Japan Booth: 8 Booth 501
Darren Hawkins assumes executive position at NACPC
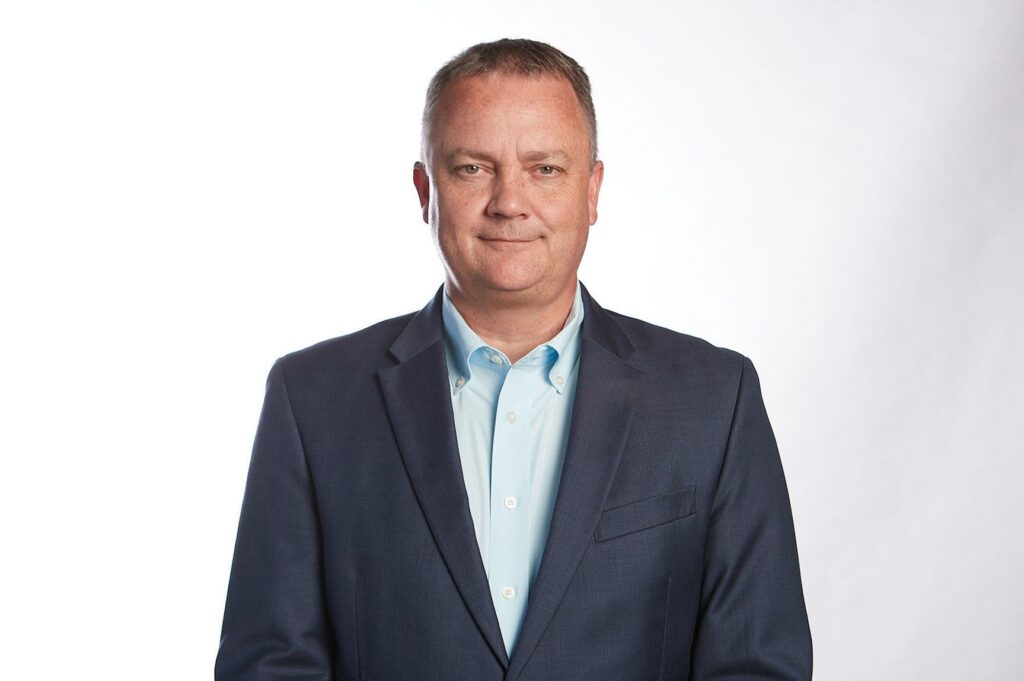
Darren Hawkins announced as president and incoming CEO, Dave Manning to serve as Chairman of the Executive Board The North American Chassis Pool Cooperative (NACPC) announces Darren Hawkins as president and incoming Chief Executive Officer. Before this appointment, he served as CEO of Yellow and had 35 years of experience in transportation logistics service with three large motor carriers. “Darren is serving as president now and will add the CEO designation on January 1, 2025. I will transition to Chairman of the Executive Board, allowing me to stay involved with this great company and take advantage of many personal interests outside of work,” said Dave Manning, CEO of NACPC. “I’ve known Darren for many years and am excited to have him guiding NACPC into the future. He is the perfect person to lead NACPC to achieve the ambitious growth goals established by our Board.” “I’m honored to work with the NACPC team to continue providing a modern fleet of chassis to the U.S. intermodal container network with first-class service, expansion in our domestic services, and continued heavy investment in our international services to benefit US motor carriers with chassis choice and competitive pricing,” said Darren Hawkins.
Iowa vs. Iowa State rivalry Bobblehead unveiled to celebrate Saturday’s Game
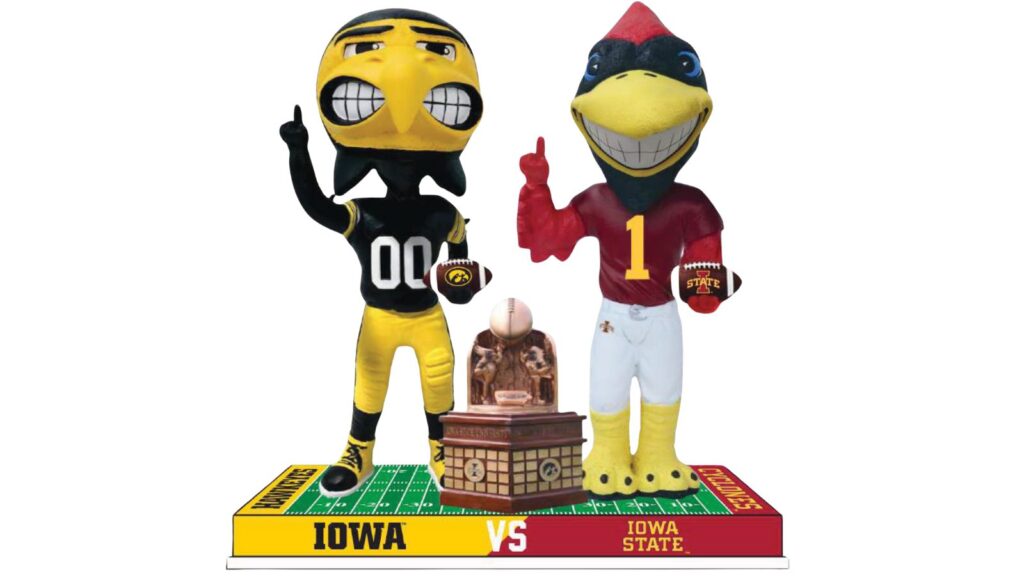
This morning, the National Bobblehead Hall of Fame and Museum unveiled a limited-edition Iowa Hawkeyes vs. Iowa State Cyclones Rivalry Bobblehead ahead of Saturday’s game between the two rivals in Iowa City. The bobblehead features Iowa’s mascot, Herky the Hawk, and Iowa State’s mascot, Cy the Cardinal, with a replica Cy-Hawk Trophy. The bobblehead commemorates the longtime football rivalry, which has awarded the Cy-Hawk Trophy to the winning team since 1977. The special edition bobblehead, numbered up to 2,024, will be released in conjunction with the 71st meeting between the Hawkeyes and Cyclones on Saturday, September 7th, at Kinnick Stadium in Iowa City, Iowa. It is available exclusively from the National Bobblehead Hall of Fame and Museum, an official licensee of the University of Iowa and Iowa State University. Standing side-by-side on a football field base that reads “HAWKEYES” in one end zone and “CYCLONES” in the other end zone, Iowa mascot Herky the Hawk and Iowa State mascot Cy the Cardinal are wearing their respective uniforms while giving the No. 1 signal. Positioned in between Herky and Cy is a replica of the Cy-Hawk Trophy. The front of the base features the logos for each team. With a combined enrollment of nearly 70,000 students, Iowa and Iowa State compete with each other in the Iowa Corn Cy-Hawk Series, which awards points for athletic victories over the different universities. The schools also compete for the Cy-Hawk Trophy in football. The teams first met on the gridiron in 1894, and Iowa has won seven of the last eight matchups to increase its lead in the all-time series to 47-23. The Hawkeyes won last year’s meeting in Ames, 20-13, giving longtime Iowa coach Kirk Ferentz his 200th career victory. “We’re excited to unveil this limited-edition Iowa vs. Iowa State Rivalry Bobblehead ahead of tomorrow’s game in Iowa City,” National Bobblehead Hall of Fame and Museum co-founder and CEO Phil Sklar said. “This bobblehead will be the perfect way for Iowa and Iowa State fans, alumni, students, faculty, and staff to show off their school and state pride!” The National Bobblehead Hall of Fame and Museum, located at 170 S. 1st. St. in Milwaukee, Wisconsin, opened to the public on February 1st, 2019. The HOF and Museum also produce high-quality, customized bobbleheads for retail sales and organizations, individuals, and teams nationwide. The bobbleheads are now available at this link in the National Bobblehead Hall of Fame and Museum’s Online Store. The bobbleheads, expected to ship in January, are $50 each, plus a flat-rate shipping charge of $8 per order.
Caster Concepts new line of Casters for demanding applications
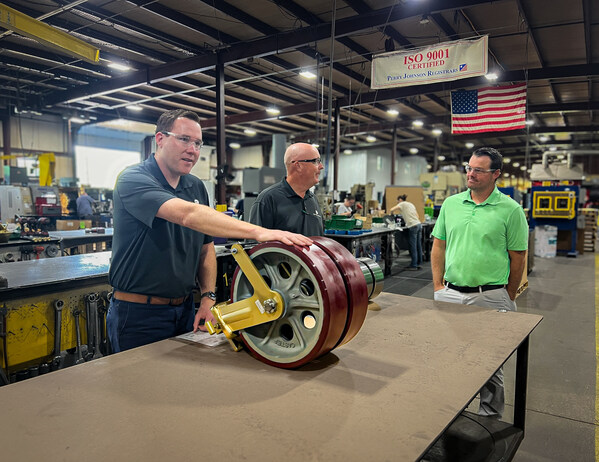
Caster Concepts has introduced multiple casters designed for heavy-duty, extra-duty, and super-duty applications. With real-world capacities exceeding 100 tons, these casters are custom-designed to provide optimal solutions when massive loads need to be moved safely and efficiently. “These products offer engineered solutions designed to improve productivity and safety in demanding applications such as moving equipment or heavy materials,” Doug Backinger, Vice President of Sales at Caster Concepts, said. “We are working with customers to offer the solution that best matches their material handling and work environment needs.” Designed and produced completely in the US, these products can be quickly manufactured and shipped – and can meet the most stringent industry standards. They are currently used in the manufacturing of heavy machinery spanning multiple industries, including agriculture, marine, aerospace, automotive, asphalt, and more. Product grades include: Heavy Duty (80 series, 81 series, 85 series, 87 series, 90 series, 91 series) Extra Heavy-Duty Category (95 series, 97 series, 99 Series) Super Heavy Duty – 2-99 (82 series and up Kingpin and 2-81 KingPinless and up) Includes Dual Wheel casters
Hikvision offers unmatched prices on leading ColorVu Cameras through September
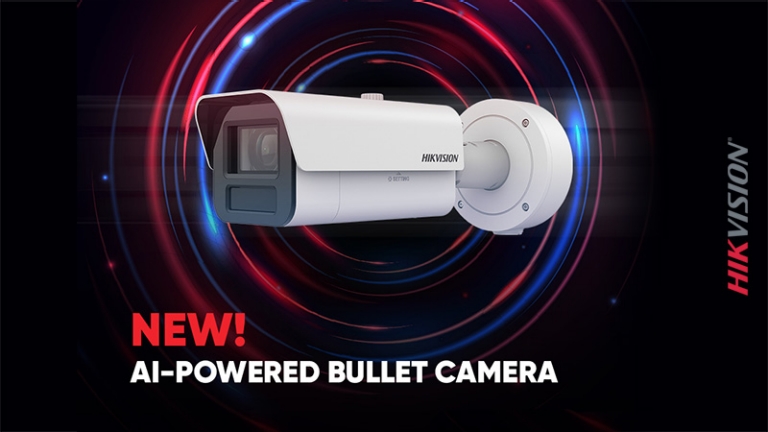
Hikvision, a world-leading manufacturer and supplier of security products and solutions that deliver the ideal combination of high performance and extreme value, is excited to announce an exclusive, limited-time offer on its cutting-edge ColorVu cameras, recognized as the industry standard for 24/7 full-color surveillance. Through September 30, security professionals can get Hikvision’s ColorVu cameras at the most competitive price-performance ratio ever offered. “As the pioneering force behind ColorVu technology, Hikvision has consistently set the standard for 24/7 full-color imaging. This special offer underscores our dedication to empowering security professionals and end users with our groundbreaking innovations,” said John Xiao, Vice President of Marketing, Hikvision USA. “With an unrivaled range of form factors and cutting-edge full-color capabilities, ColorVu cameras are indispensable for modernizing any security system.” With prices starting as low as $120,* Hikvision’s ColorVu cameras provide unparalleled image clarity, even in the most challenging lighting conditions. Hikvision’s extensive lineup of ColorVu cameras feature 4 MP resolution, true Wide Dynamic Range (WDR), and advanced analytics, including human and vehicle detection. With its array of features, these aren’t simply a camera; they’re a versatile and powerful security investment. Promotional models include: 4 MP ColorVu Mini Dome Camera: Available in black or white housing with deep learning human and vehicle classification. 4 MP ColorVu Mini Bullet Camera: Get real-time audio security with its built-in microphone and deep learning human and vehicle classification. 4 MP ColorVu Dome Camera: Built-in microphone for real-time audio security, audio and alarm interface available, plus deep learning analytics. 4 MP ColorVu Turret Camera: Real time audio security with the built-in microphone and deep learning capabilities. 4 MP Panoramic ColorVu Fixed Turret Network Camera: One image that presents all the scenes covered by the camera. 4 MP 12X ColorVu PTZ Camera Expansive night view up to 164 feet (50 m) IR distance and 328 feet (100 m) white light. Upgrade your security with ColorVu—the industry leader in 24/7 full-color surveillance. Don’t miss this limited time opportunity to experience unparalleled image quality at an exceptional price.
Henkel presents pressure-sensitive adhesives at LabelExpo
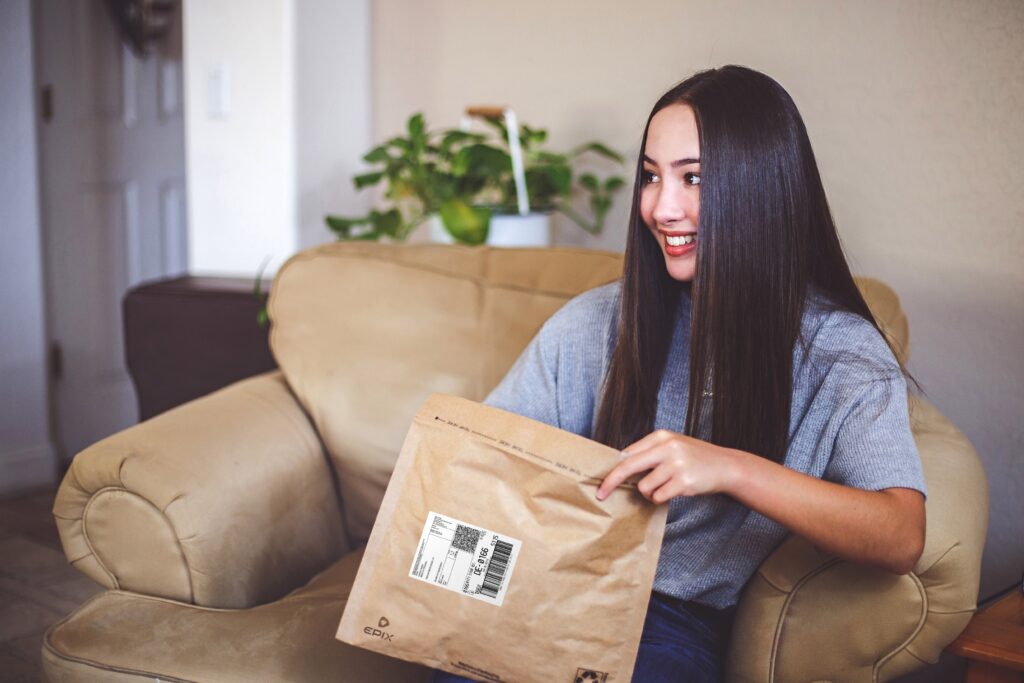
This year’s LabelExpo, September 10-12 in Chicago, is all about sustainability. Visitors will have the opportunity to network with industry experts at North America’s largest label and packaging printing trade show. As one of the leading suppliers of sustainable solutions for the packaging industry, Henkel Adhesive Technologies will present its portfolio of pressure-sensitive adhesives certified as compatible with post-consumer recycling processes according to the test protocol of the Tag and Label Manufacturers Institute (TLMI). At the trade fair, the manufacturer of adhesives, sealants and functional coatings is highlighting how it plays an instrumental role in driving sustainability in the packaging industry. Henkel will be demonstrating how the manufacture of sustainable products can be put into practice with its portfolio of pressure-sensitive adhesives (PSA). Henkel’s selection of hotmelt, water-based, UV and solvent-based acrylic adhesives offers high-quality bonding solutions for PSA tapes, labels, and graphics that are compliant with TLMI test protocol RCA LRP-2 for post-consumer recycling processes. Among the products featured are two label adhesives, Technomelt 4144 RE and PS 9625 RE. These well-established solutions are a part of the RE product range, which encompasses adhesives and coatings that are designed for recycling. Technomelt 4144 RE is used for general purpose labels and tapes. It shows good adhesion to a wide range of substrates, including recycled corrugated board and low-density polyethylene, as well as curved surfaces. For removable and linerless labels, Technomelt PS 9625 RE is suitable due to its repositionability and low viscosity. Both adhesives are approved for use in food packaging in accordance with U.S. Food and Drug Administration (FDA) Directive 175.105. “Our approach to sustainability is to create more value in the industry while reducing our environmental footprint. As well as helping our customers to become more sustainable, we aim to continuously improve our own product portfolio. Our goal is to use our technologies to help solve current and future global environmental and social challenges,” says Ky Flamini, Commercial Business & Sales Director Tapes & Labels North America at Henkel.
Serpa puts versatility back into packaging at PACK EXPO 2024
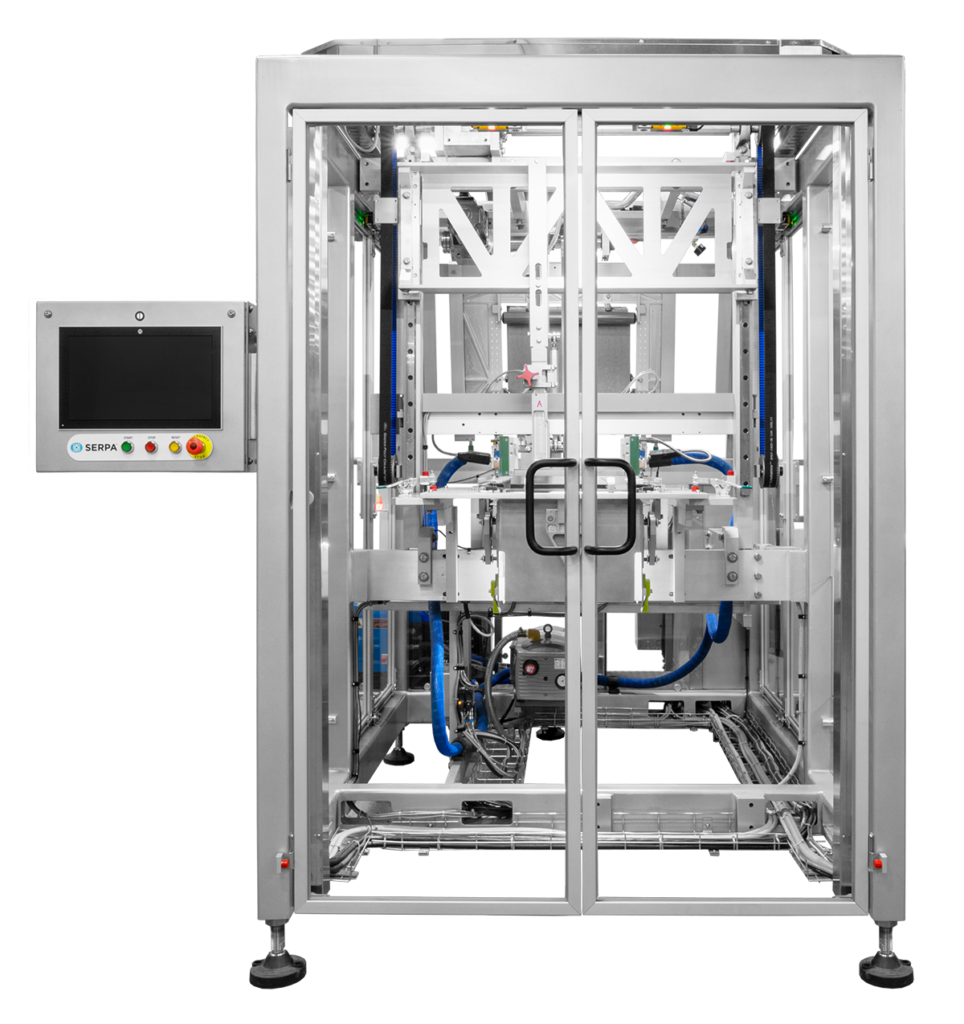
Visit Serpa in booth S-3650 to learn how its versatile FG1 Top Load Carton/Tray/Case Former, and other solutions can add efficiency to your next packaging application. If versatility is what you need in your next tray-forming machine, then you need to see Serpa and its FG1 Top Load Carton/Tray/Case Former, which will be demonstrating its capabilities in booth S-3650 at PACK EXPO 2024, Nov. 3-6, at McCormick Place in Chicago. Serpa, a ProMach brand, is a manufacturer of cartoners, sleevers, case and tray packers, robotic palletizers, and auxiliary packaging equipment for numerous industries including pharmaceutical, medical device and nutraceutical, food, personal care, and commercial goods. The FG1 Top Load Carton/Tray/Case Former is one of Serpa’s most versatile machines. It can form cartons, cases, or trays using corrugated or chipboard materials, making the FG1 an ideal all-in-one solution for customers needing a higher level of flexibility in their packaging operations. But versatility is not only restricted to different tray styles and materials. The FG1 is designed for ultra-fast toolless changeovers in less than 2 minutes. Simply remove and replace the lightweight, ergonomic forming head and you are back in business. As applications and product runs change throughout the day, the FG1 is built to change with you, providing the highest level of uptime to keep your operations running with minimal disruptions. The FG1 also boasts the best operator and maintenance access in the industry. The standalone FG1 can be integrated into any existing packaging line and is available in single (up to 75 cartons per minute) or dual head (up to 400 cartons per minute) configuration. The machine comes with a small footprint to fit into tight spaces, and has ample walk-in access for easy maintenance. In addition to the FG1, PACK EXPO attendees will see five other Serpa machines in action, including: P100 Horizontal Continuous Motion Cartoner is a state-of-the-art machine featuring a balcony design that provides maximum access to all the drive components from one side of the machine, while maintaining a compact footprint. P200 Side Load Case Packer is a machine that runs both cases and trays; tape closure on cases and glue sealing of trays is accomplished with a simple changeover. TEL10 Tamper Evident Labeler can be easily integrated with existing or new packaging lines to add another level of security to secondary-packaging operations. RF450/TL450 High Speed Insert Feeding and Tray Unloading System features a patented design that largely eliminates common insert feeding issues. FM150 Intermittent Motion Beverage Cartoner uses Serpa’s proven orbital carton erector with prebreak feature to operate at speeds of more than 80 cartons per minute. Plan to visit Serpa in booth S-3650 at PACK EXPO 2024 to learn how its technologies can add speed and efficiency to your next packaging application.
Orchestrating the Future: PepsiCo/FLNA’s Warehouse Transformation with AutoScheduler.AI’s AutoPilot
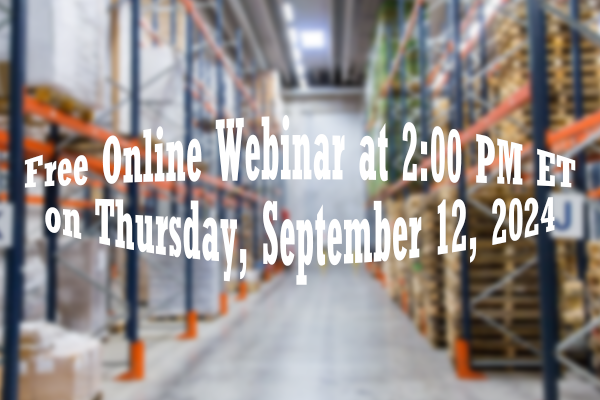
Free Online Webinar at 2:00 PM ET on Thursday, September 12, 2024 AutoScheduler.AI has announced the company is sponsoring a webinar hosted by DC Velocity magazine to discuss PepsiCo/FLNA’s (Frito Lay North America) warehouse transformation using AutoScheduler.AI’s AutoPilot. Keith Moore, CEO of AutoScheduler.AI, and Peter Hanna, a leader at PepsiCo, will share how AutoPilot is revolutionizing operations at PepsiCo/FLNA. Faced with rising demand, shrinking margins, and complex operations, PepsiCo turned to AutoScheduler.AI’s cloud-based AutoPilot platform to optimize warehouse operations and improve efficiency, including a 30% increase in product picks per hour. “PepsiCo has been focused on driving value for customers through innovative supply chain processes that improve fulfillment times, reduce operating costs, and maximize productivity,” says Keith Moore, CEO of AutoScheduler.AI. “Our AI algorithms can prioritize customer orders based on predefined rules and criteria while considering warehouse constraints, which helps to improve customer satisfaction and overall profitability.” At the free webinar on September 12, 2024, at 2:00 PM ET, attendees will: Learn how AutoPilot unifies data across systems for better visibility. Discover how advanced algorithms maximize productivity and minimize costs. See how AutoPilot provides comprehensive, real-time insights for informed decision-making. Hear about the impressive gains at PepsiCo/FLNA, including a 30% increase in picks per hour. AutoScheduler.AI AutoPilot smooths warehouse operations by orchestrating and planning all activities in real-time on top of an existing WMS. It considers space, time, labor, dock doors, and more constraints to ensure that orders are fulfilled on time and in full. Clients gain efficiencies and value in their supply chains through optimized labor, schedules, touches, and inventory. Register here
Kito Crosby announces Lifting for the Troops campaign for 2024
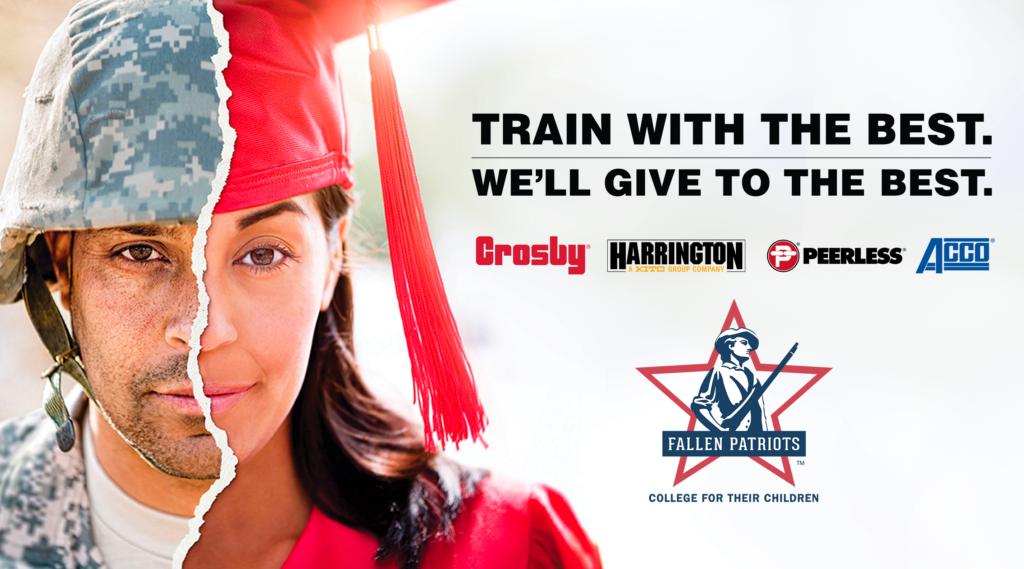
Kito Crosby has announced its Lifting for the Troops campaign for 2024, supporting the Children of Fallen Patriots Foundation. Fallen Patriots provides college scholarships and educational counseling to military children who have lost a parent in the line of duty. After government programs, the average shortfall in college funding for a student to earn a four-year degree is $25,000. Supported by its loyal channel partners and end users throughout the United States, Kito Crosby looks to raise $75,000 this fall for the Fallen Patriots. From September 1 through October 31, 2024, Kito Crosby will donate $500 for every Crosby, Harrington, Peerless, or Acco training event the company hosts in the US. In addition, all proceeds from the popular Crosby User’s Guide for Lifting online training course during this time will be donated to this honorable cause. Company named sponsorships and private donations are also welcome. 100% of the proceeds from sponsorships and private donations go directly to Fallen Patriots and help Kito Crosby reach its goal. Approximately 25,000 children have lost an active-duty parent in the military over the last 35 years. Of those, 96% of casualties are men, leaving behind single mothers to care for their families, and 60% report having trouble making ends meet. The foundation said that $625 million is needed nationwide to cover the gap between government assistance and the actual cost of a degree. Since 2002, Fallen Patriots has provided nearly $66 million in college scholarships to more than 3,400 students, including more than 1,500 graduates. Kito Crosby has trained more than 600,000 people in a wide range of industries since 1991. Every time a worker attends a Crosby, Harrington, Peerless, or Acco training event, or completes Crosby’s online training course this fall, they can know that they are playing an important part to help secure a better future for military children who have lost a parent. With a US manufacturing footprint that includes plants in Texas, Oklahoma, Arkansas, Pennsylvania, South Dakota, Alabama, and Minnesota, Kito Crosby’s involvement with the country’s military stretches back to its earliest days, supplying lifting hardware for military equipment. Today, more than 50 Veterans work in the company’s facilities designing, manufacturing, and distributing the best lifting and securement solutions in the world. “We are honored to partner with the Children of Fallen Patriots Foundation again for now the fifth year,” said Melissa Ruths, Kito Crosby Chief Marketing Officer. “Together, with our channel partners and end users, we are proud to support such an important cause and help raise enough this year to cover the cost of three college scholarships for young people who have been affected by military casualties.”
Caster Concepts adds specialized engineering area at Michigan facility
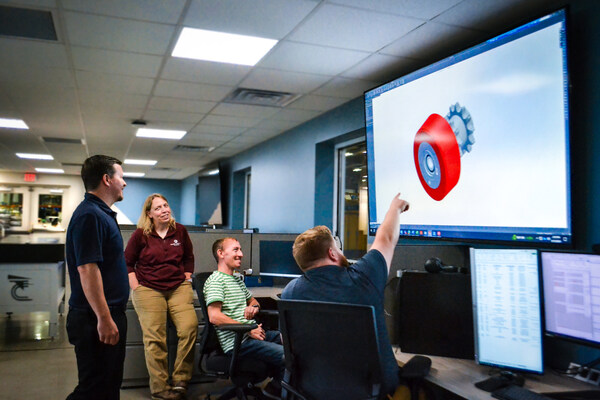
Caster Concepts has further expanded operations at their West Michigan Ave facility in Albion, Michigan to include a 3,000 square foot advanced engineering area. This follows a 16,000 square foot manufacturing expansion in 2023. “This expansion is all about attracting new engineering talent to the Caster Concepts team,” said Bill Dobbins, President, Caster Concepts. “Our engineers will have even more advanced precision machinery and the newest tools needed to meet the unique challenges our customers bring to us every day.” The new area will focus on designing tailored solutions to unique material handling challenges faced by Caster Concepts customers. It will include the space and tools needed to explore solutions using 3D solid modeling, EA Analysis, rapid prototyping, and quality assurance testing, such as dynamometer and static load testing) and design review and collaboration. The facility in Albion focuses on the production of the company’s core products and includes customized polyurethane fabrication capabilities, as well as other equipment and resources needed to match the right product to specific applications. Used properly, advanced caster technology – developed for the specific material handling challenge – provides up to 3X longer life and reduces push force by more than 70%, addressing major ergonomic and operational challenges.
Seegrid announces closing of $50M Series D investment
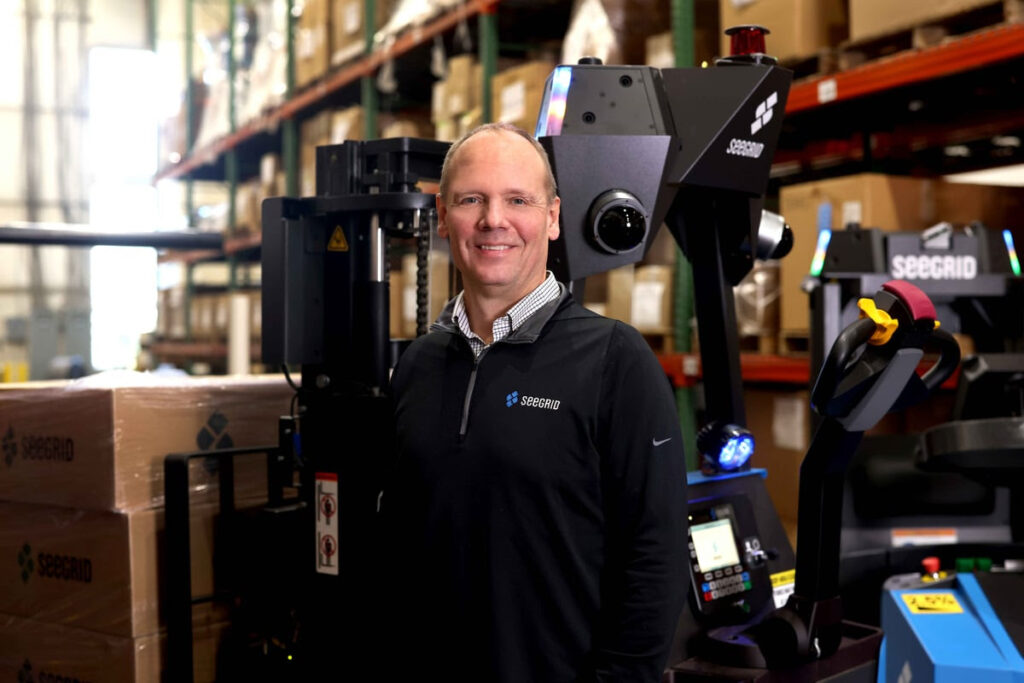
Seegrid Corporation, a provider of autonomous mobile robots (AMRs) for pallet material handling, today announced the successful closure of its $50M Series D investment round, funded by its existing lead investors Giant Eagle Incorporated and G2 Venture Partners, as well as smaller investments from other existing shareholders. The investment allows Seegrid to accelerate its autonomous lift truck market initiatives, generating more growth than expected in a market projected to reach nearly $3.5B by 2027 (Interact Analysis, Mobile Robots – 2023). “We are thrilled to have secured this additional funding from our investors. It enables us to drive our innovative AMR technology and solutions into the market faster, delivering even more value to our customers sooner,” said Seegrid’s CEO and President, Joe Pajer. “In addition, this investment is a testament to our investors’ confidence in our vision, the strength of our leading-edge AMR technology and solutions, and the accelerating market traction we are achieving. Seegrid pioneered and remains the leader in the autonomous tow tractor market. We are revolutionizing the industry again as we successfully develop, manufacture, and deploy innovative new autonomous lift truck solutions.” “Unrelenting labor shortages and wage inflation, accompanied by increasing consumer demand, are driving rapid market adoption of autonomous technologies in manufacturing, warehousing, and logistics,” continued Pajer. “This is particularly true in the area of palletized material flows, which are addressed by Seegrid’s autonomous tow tractors and lift trucks. This market segment is just now ‘coming into its own,’ and Seegrid is a clear leader. “Seegrid is leading this market in part because of innovative technologies we have introduced in the last six months, including Sliding Scale Autonomy, which provides high levels of both flexibility and predictability in autonomous navigation and manipulation, and Enhanced Pallet and Payload Detection, which enables reliable recognition and manipulation of the broad range of payloads required by world-class manufacturers. In addition, Seegrid is on track to introduce its second autonomous lift truck later this year. The CR1 will lift even heavier payloads to heights of up to 15 feet. When these unique-to-Seegrid technologies are combined with decades of industry-leading deployment experience acquired from our leadership in the autonomous tow tractor market, we are chosen again and again by blue-chip customers who seek autonomous solutions that work in the real world.” This recent funding marks a significant milestone for Seegrid, underscoring its leadership in the AMR space and setting the stage for continued success and innovation in the future of material handling automation.
Equity company invests in Martins as a major shareholder
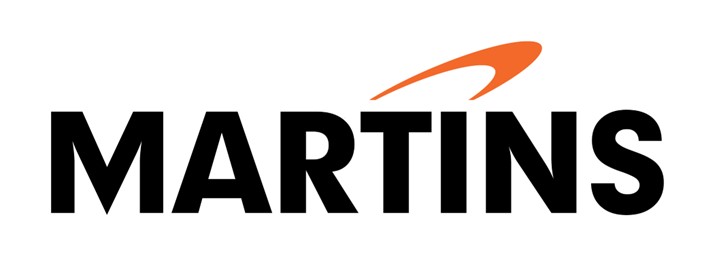
MARTINS Industries, a global provider of equipment and supplies for tires and wheels based in Farnham, Quebec, has announced that Walter Capital Partners is now a major shareholder. This transaction is intended to support MARTINS as it implements its acquisition-based growth strategy to consolidate its position as a leader in its industry. “With Walter Capital Partners, we can count on a remarkable partner to help us fast-track the implementation of our acquisition-based growth plan, mainly in the United States and Europe,” says Martin Dépelteau, president of MARTINS Industries. “As many companies are facing succession issues these days, we’ll be in a great position to explore and capitalize on acquisition opportunities.” “We were impressed by the management team’s energy, ambition, and motivation,” says Eric Doyon, Managing Partner at Walter Capital Partners. “All members of the executive committee are shareholders who are just as eager as we are to keep MARTINS moving forward. With its extensive global distribution network, its track record of successfully integrating previous acquisitions, combined with our arrival as a strategic partner, everything is in place for MARTINS Industries to broaden its product range and continue its international expansion.” Since its 2002 founding, MARTINS has experienced nonstop growth, first organically and then through strategic acquisitions, including Canada’s Magnum+ in 2019 and England’s Checkpoint in 2022. The company is an excellent platform for acquisitions. It offers opportunities to key people in such acquisitions to keep growing with it, as it did, for instance, with Checkpoint as a senior manager, became a shareholder, and a member of MARTINS’ executive committee. MARTINS is known worldwide for its distribution network, which extends from Canada to the United States, the United Kingdom, Australia, the Middle East, and Europe. Its employees are located on both sides of the Atlantic.
AUSA acquisition complete and is now part of JLG

JLG Industries, Inc., an Oshkosh Corporation business and a global manufacturer of mobile elevating work platforms (MEWPs) and telehandlers, announces that Oshkosh has completed the acquisition of AUSACORP S.L. (AUSA), adding the market-leading brand’s compact all-terrain machines for the transportation and material handling to the company’s Access segment. Following the acquisition of Hinowa in 2023, the AUSA acquisition further supports the Oshkosh accelerated growth strategy and strengthens the JLG® equipment portfolio. Established in 1956, AUSA specializes in designing, manufacturing, and selling wheeled dumpers, rough terrain forklifts, and compact telehandlers for the residential, civil, and road construction industries and the transportation and handling of industrial and agricultural materials. The acquisition included AUSA’s 250,000-sq.-ft. manufacturing facility in Barcelona, Spain, with approximately 350 team members and access to 200 equipment dealers worldwide. “AUSA’s culture of innovation and quality matches the same standards we hold,” says Mahesh Narang, president of JLG, “and our shared core values around safety, productivity, and sustainability position us well for the future. Together, we will work diligently, as both companies always have, to meet the needs of our customers.” JLG and AUSA have collaborated since 2020, bringing the SkyTrak® 3013 to market together. With the acquisition, AUSA products will enhance JLG’s line of telehandlers and complement Hinowa’s tracked dumpers and forklifts. Both acquisitions help accelerate JLG’s growth into the specialty equipment, agriculture, and landscaping markets while providing its construction and materials handling customers with an even broader array of products — all backed by JLG’s robust training, support, and service infrastructure. “Our combined capabilities, market leadership positions, and complementary product offerings provide a more comprehensive solution to address market needs, expand our operational footprint, and unlock growth opportunities worldwide,” finishes Narang. “The acquisitions of AUSA and Hinowa help JLG create an organization that can better serve customers globally.”
Alta Equipment Group elects Colin Wilson as Director

On September 1, 2024, the Board of Directors of Alta Equipment Group Inc. elected Colin Wilson to fill a vacancy on the Board, effective immediately. Mr. Wilson was elected to the class of directors whose term expires at the Company’s annual shareholders meeting in 2026. Mr. Wilson, age 70, has over 40 years of experience in the materials handling industry. He began his career in 1970 with Coles Cranes in Sunderland, England, where he worked in production engineering, marketing, product management, and overseas licensing. After time with a compressor company and a European lift truck competitor, Mr. Wilson joined Hyster-Yale Group (formerly NACCO Materials Handling Group), a global company whose primary business is lift trucks with annual revenues over $4 billion, in 1988 as European Sales and Marketing Director for the Yale brand. He had roles of increasing responsibility, culminating in his role as the President and Chief Executive Officer in September 2014. Mr. Wilson held the President and Chief Executive Officer role at Hyster-Yale Group until January 2020, when he retired. Mr. Wilson graduated with a Bachelor of Science Degree in Mechanical Engineering from Sunderland Polytechnic (now the University of Sunderland). Mr. Wilson served on the Executive Committee and Board of Directors of the Industrial Truck Association of America (ITA), is the past chairman and board member of the Materials Handling Institute of America (MHI), and has also served as a member of the Material Handling Equipment Distributors Association’s Board of Advisors (MHEDA) and as President of the British Industrial Truck Association (BITA). “Colin is a proven leader in the material handling business, and he possesses unmatched industry knowledge and insights into our unique strategy,” said Ryan Greenawalt, Chief Executive Officer and Chairman. “His experience will benefit as we expand this strategic business segment. We welcome Colin to the Alta family.” “I am excited to join the Board of Alta and contribute to the Company’s impressive growth strategy,” said Mr. Wilson. “Alta has a leading position in the material handling market, and significant opportunities exist to expand this stable and profitable business segment further.”
Wolter Inc. expands into Atlanta, GA with acquisition of Dedicated Material Handling Solutions
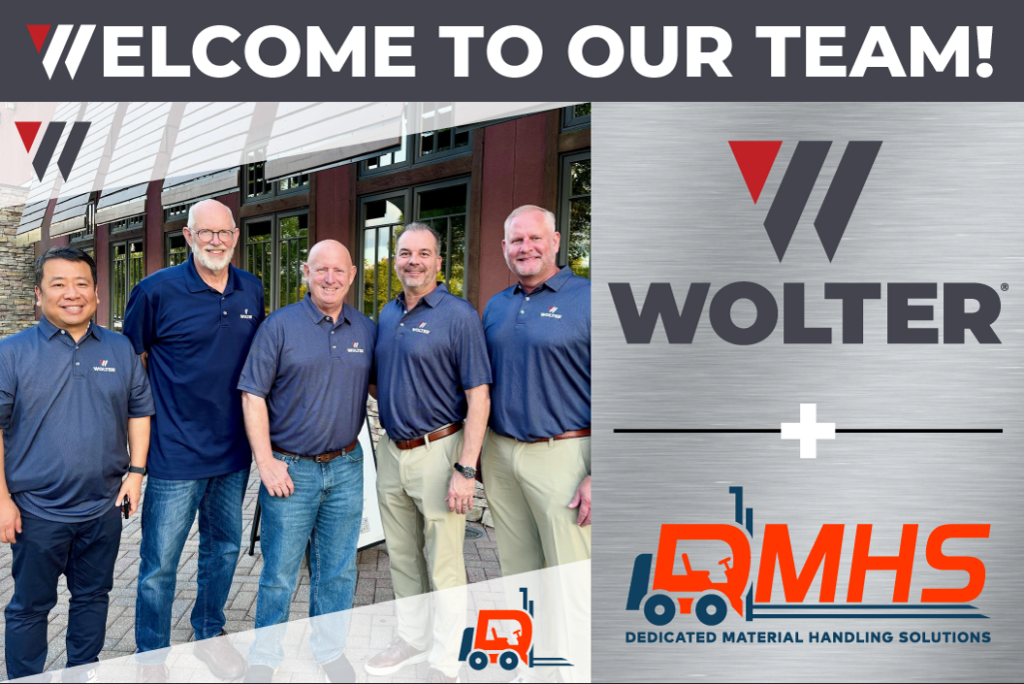
Wolter Inc., a provider of material handling solutions in seven Midwest states, has strategically expanded its footprint by acquiring Dedicated Material Handling Solutions (DMHS). With two established locations in Buford and Atlanta, GA, DMHS has a strong presence in the Atlanta metro market, positioning Wolter Inc. for significant growth in the Southeastern United States. This acquisition enables Wolter Inc. to bring its industry-leading services and extensive product offerings to the Atlanta Metro area’s thriving industrial and logistics hub. It aligns with Wolter Inc.’s vision of becoming a national material handling leader while strongly emphasizing local service excellence. Key Benefits: Expanded Product Line: DMHS customers will now have access to Wolter Inc.’s comprehensive range of material handling solutions, including forklifts, automation & robotic technologies, and more. Enhanced Service: Wolter Inc.’s renowned technician training program and robust tech support system will extend to the Southeast, providing Atlanta businesses with top-tier service and support. Local Expertise, National Strength: DMHS’s deep local market knowledge combined with Wolter Inc.’s national resources ensures that customers in the region receive unparalleled support. Jerry Weidmann, CEO of Wolter Inc., remarked, “Acquiring Dedicated Material Handling Solutions is a natural extension of our growth strategy and a significant expansion into the Southeastern U.S. The Atlanta Metro area is a dynamic market, and we’re excited to deliver our comprehensive solutions here. Together with the DMHS team, we are committed to driving success for our customers and reinforcing our commitment to exceptional material handling solutions nationwide.”
Revised employment statistics and the policy implications on plastics
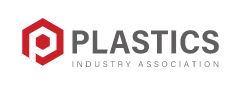
The Bureau of Labor Statistics (BLS) recently released the 2024 Preliminary Benchmark Revision of the Current Employment Statistics (CES), revealing that total nonfarm jobs were 818,000 fewer than previously estimated for the twelve months ending in March 2024. While CES survey employment estimates are benchmarked annually against comprehensive March employment counts, the magnitude of this downward revision has raised concerns. Upward and Downward Revisions Professional and business services employment saw the largest downward jobs revision of 358,000. Manufacturing employment was also revised down by 115,000 over the same period. Conversely, there were upward revisions: private education and health services employment increased by 87,000, and transportation and other services were revised upward by 56,400 and 21,000, respectively. While specific industries did not break down the manufacturing revisions, these revisions will eventually be reflected in the monthly industry workforce statistics. Why Is this Important to the Plastics Industry? Employment is a key economic indicator of economic growth. The labor market continues to reflect changes in the economy’s aggregate demand and supply dynamics. Therefore, revisions to employment data are neither surprising nor trivial, as they can be valuable in assessing the business landscape. First, the manufacturing sector, a primary customer of the plastics industry, is particularly important. The lower employment rate in manufacturing suggests reduced manufacturing activity, which can have both upstream and downstream ripple effects. For plastics and rubber product manufacturing, the preliminary employment estimate for July was 724,000, nearly matching the monthly average of 725,300 in 2021. Secondly, PLASTICS releases its Annual Size and Impact Report each year, which quantifies the plastics industry across the supply chain and its contribution to the broader economy.* A decrease in manufacturing employment might be offset by increased service employment. Based on 2022 data, total jobs related to the plastics industry numbered 209,000 in manufacturing and 483,000 in services. Third, changes in government data have far-reaching policy implications. Institutions, including the Federal Reserve, have publicly acknowledged that their policy actions have been and will continue to be data-dependent, and rightfully so. Still, data quality and reliability are crucial. The U.S. policy shift to support a global goal of reducing plastic production as part of a global plastics treaty is shortsighted. The effect of such a policy on the U.S. labor market is net negative, considering the interlinkages of plastics production throughout the economy’s value chain—whether in manufacturing or services. Unfortunately, with lower employment numbers than previously estimated, policies are being deliberately considered to further reduce the ability of industries to generate employment throughout the broader economy. Based on the Economic Policy Institute’s estimates, 100 direct jobs in durable goods manufacturing create a total of 744.1 jobs, while 100 direct jobs in nondurable goods manufacturing create 514.3 jobs.* The revisions in manufacturing employment by industry are yet to be released. According to the BLS, the CES will be updated when the final benchmark revision and monthly employment estimates in January 2025 are issued. *The 2024 edition of Plastics Size and Impact Report will be release at a virtual Executive Briefing to PLASTICS members and Press on September 19, 2024, at 2:00 PM. For additional information and to register visit: https://events.plasticsindustry.org/SIZEnIMPACT24 *Bivens, J. Updated employment multipliers for the U.S. economy. Economic Policy Institute, Washington, DC. January 23, 2019. https://www.epi.org/publication/updated-employment-multipliers-for-the-u-s-economy/
Episode 517: Leveraging podcasting to Fuel 3PL growth
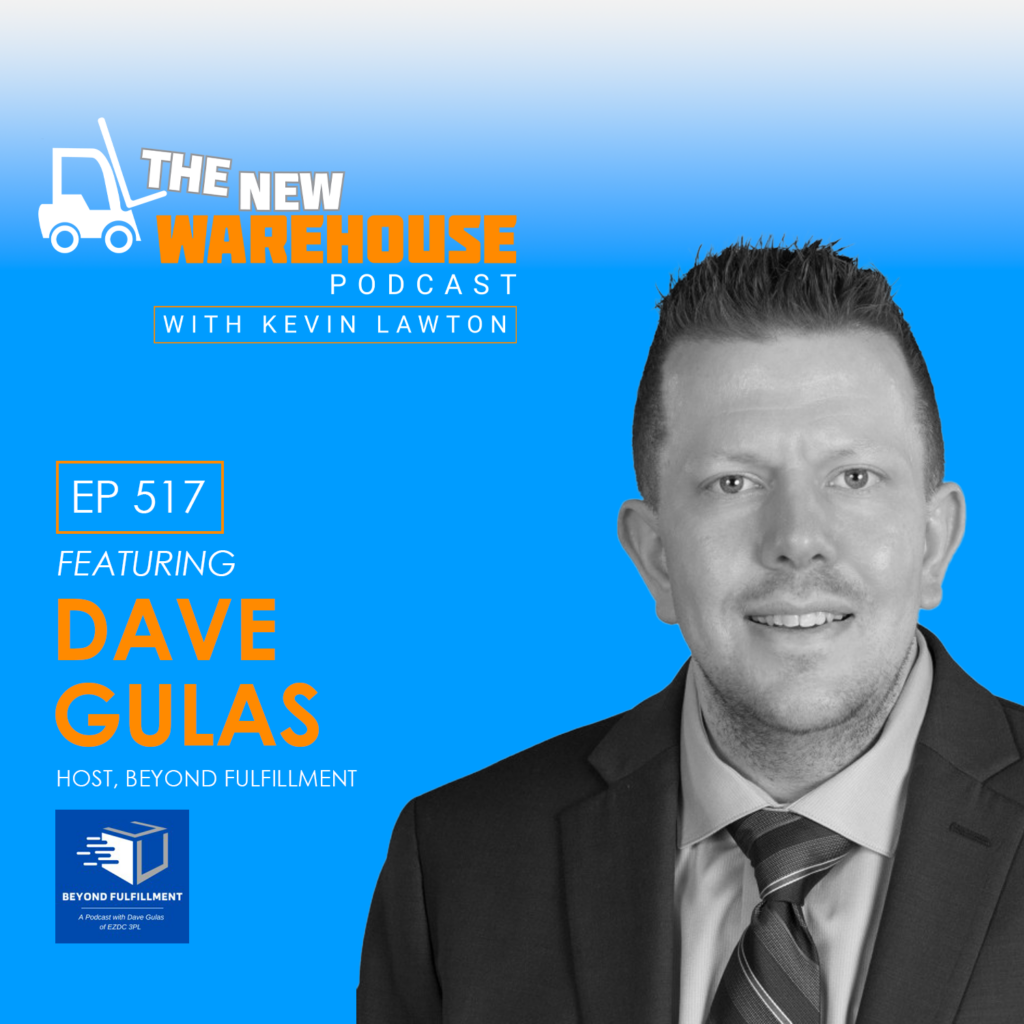
In this episode of The New Warehouse Podcast, Kevin welcomes back Dave Gulas, founder of EZDC 3PL and host of the Beyond Fulfillment Podcast. Dave’s transition from the pharmaceutical industry to the 3PL space showcases a remarkable growth trajectory. His strategic use of podcasting to build a personal brand and expand his business network has been a critical driver of this success. In their conversation, Dave shares insights into how podcasting has opened doors, increased lead generation, and contributed to the overall growth of his 3PL business. The Power of Consistency in Content Creation One of the standout themes in this conversation is the importance of consistency in content creation. Dave emphasized that starting his podcast was pivotal in growing his business. He noted, “When I started, I had no experience, but I just kept going. The more you do it, the better you get.” His discipline in regularly producing content has improved his podcasting skills and significantly boosted his company’s online presence. “You don’t have to get it right; you just have to get it going and continue to improve and adjust along the way.” This consistency has led to a steady stream of leads, which has been crucial in a highly competitive industry like logistics. Navigating the Challenges of 3PL Growth As Dave’s 3PL business expanded, he encountered the typical challenges of rapid growth, particularly in identifying the right customers. Early on, Dave admitted to chasing after every deal. He shared, “We brought in accounts that really weren’t the right fit for us, and we’re now transitioning away from some of those.” This experience has taught him the value of refining his company’s focus and only taking on clients that align with their strengths, leading to better service and more satisfied customers. Expanding Services Through Strategic Partnerships Dave also discussed the strategic decision to add freight brokerage to his service offerings. This move helps provide a more comprehensive service to his clients, who often require help with freight services in addition to fulfillment. Partnering with SPI Logistics allowed Dave to manage sales while efficiently leveraging SPI’s robust back-office support. “Becoming an agent with SPI has been great,” Dave said, highlighting how this partnership has enabled him to serve his clients better and offer a more complete logistics solution. Key Takeaways Consistency is Key: Regularly producing content, even without initial experience, can significantly boost business visibility and lead generation. Focus on the Right Clients: Identifying and sticking to your company’s strengths leads to more successful client relationships and better overall business outcomes. Strategic Partnerships Enhance Service: Expanding service offerings through partnerships can help provide clients with a more comprehensive solution, improving satisfaction and retention. The New Warehouse Podcast Episode 517: Leveraging podcasting to Fuel 3PL growth