Zion Solutions Group partners with Lakeshore Learning to launch State-Of-The-Art distribution center
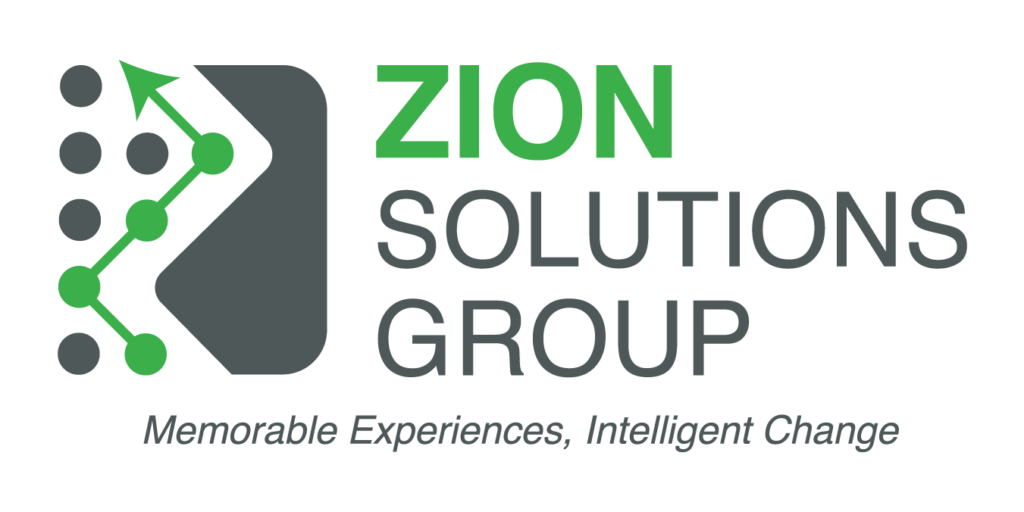
In a significant step toward redefining supply chain efficiency and boosting the local economy, Lakeshore Learning hired Zion Solutions Group, a trailblazer in advanced supply chain integration, to help implement a cutting-edge 1.2 million square foot distribution center in Garland, Utah. This collaboration is set to create over 500 jobs, showcasing an unparalleled commitment to innovation and community development. “Our relationship with Lakeshore Learning, beginning in 2015, has been a testament to what visionary collaboration can achieve,” stated Jim Shaw, president of Zion Solutions Group. “This is not just a collaboration; it’s a leap toward the future of supply chain management. By combining Lakeshore Learning’s vision with our technological expertise, we are set to introduce a distribution hub that exemplifies efficiency, sustainability, and economic growth for Garland.” Artin Ghazarian, Lakeshore Learning’s Chief Supply Chain Officer, highlighted the project’s ambition: “Our journey with Zion Solutions Group has been marked by a shared drive for excellence. This distribution center goes beyond expanding our logistical capabilities—it’s a testament to our dedication to setting new industry standards for efficiency and environmental stewardship in supply chain management.” Jordan Frank, EVP & Co-Founder of Zion Solutions Group, emphasized the collaborative synergy: Our relationship with Lakeshore Learning is more than a partnership; it’s a melding of minds aimed at redefining the future of our industry. We’re not just optimizing logistics; we’re crafting a model of innovation that leverages technology for smarter, more sustainable operations. We aim to inspire the sector by demonstrating how collaboration and technology can create impactful solutions.” The facility will harness the latest in automation and robotics to optimize both efficiency and scalability. Zion Solutions Group will play a crucial role in this evolution, meticulously shaping the project from its conceptual stages to its final form. This includes value-added engineering to support Lakeshore Learning’s specific needs, overseeing the procurement and engineering processes to ensure precision, and integrating advanced software solutions—including Zion Apex (WES)—for peak functionality. Beyond the project’s completion, Zion’s Customer Experience team will continue to support the operations team and provide optimization opportunities, ensuring the facility operates smoothly and evolves with technological advancements. With an operational goal set for 2025, Lakeshore Learning’s Garland distribution center represents a major milestone in the region’s job creation and economic growth. This initiative aligns with Zion’s mission to drive sustainable innovation and cement its market leadership.
Steele Solutions set to move into Tech Center in West Allis, WI
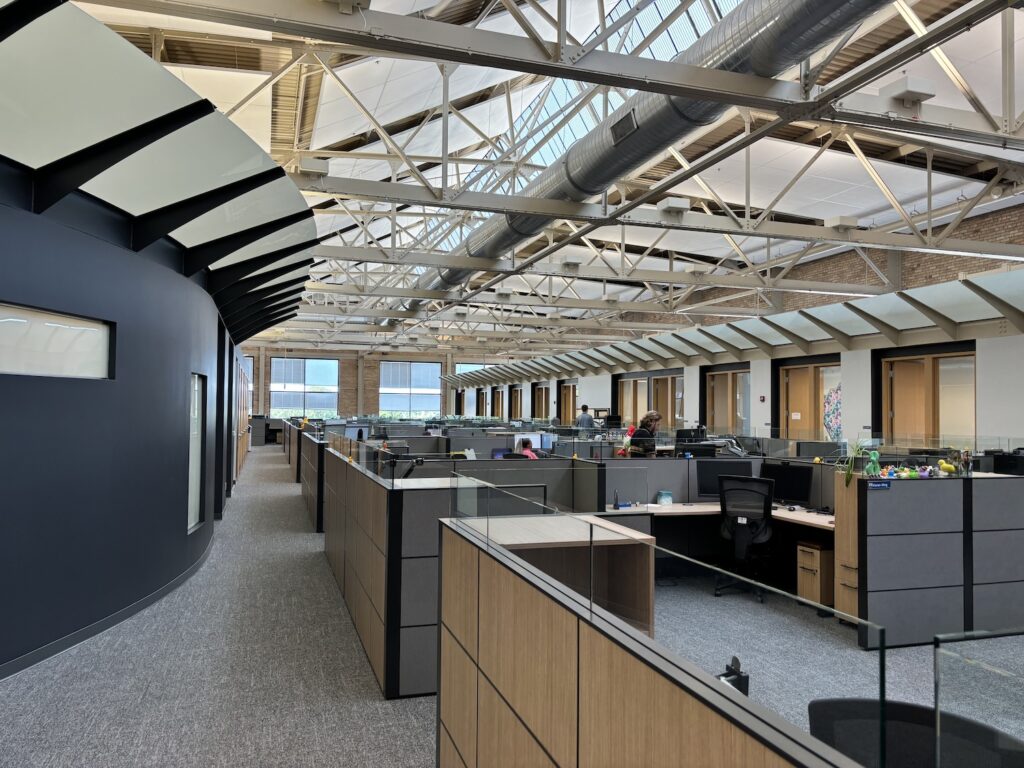
The new location as an anchor of Summit Place in West Allis signifies growth and enhanced collaboration while maintaining strong manufacturing roots in South Milwaukee Steele Solutions Inc., a manufacturer of structural steel work/equipment platforms, material handling chutes, and public safety security lockers, announces the opening of its new Tech Center at Summit Place, located at 6737 West Washington Street, West Allis. This significant move highlights the company’s commitment to growth, innovation, and enhanced operational efficiency. “Our new Tech Center, situated in the heart of West Allis, is a perfect blend of historic charm and modern functionality,” said Steele Solutions, president Matthew McBurney. “The 40,000-square-foot space, housed in the renovated and historic Allis-Chalmers building, embodies our vision of fostering collaboration and driving innovation.” The new building will feature: A state-of-the-art Technical Innovation Center Complete design and project management teams Departments for Finance, HR, Supply Chain, Quality, Sales, and Marketing An expansive training center and an outside patio This move brings all office functions under one roof, promoting seamless communication and idea-sharing. The location, developed by Whitnall-Summit Development Company, is part of an urban adaptive reuse project on the former Allis-Chalmers Campus, which historically produced some of the world’s largest machinery. “We chose this central city location to attract top technical talent and to ensure easy accessibility,” added McBurney. “Being right off the highway and walkable to local amenities like the farmers market and restaurants makes it an ideal spot for our team. Our larger office space not only provides room to grow but also enhances our ability to collaborate and innovate.” Steele Solutions will be an anchor tenant in the building, sharing the space with notable entities such as Children’s Hospital of Wisconsin and Goodwill’s Mission Programs. The building’s exposed brick beams, big windows, and convenient amenities provide a unique and inspiring work environment. The corporate headquarters will remain in South Milwaukee, ensuring continuity and stability in production operations. Steele Solutions is currently hiring and looking to expand its team. The new building provides the necessary space for this growth and additional features to attract top talent to the vibrant and innovative workplace.
AAR reports Rail Traffic for the week ending August 31, 2024
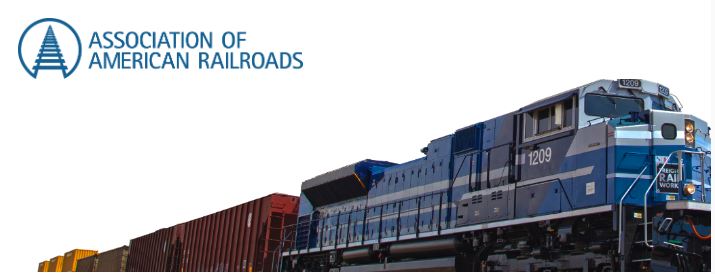
Today, the Association of American Railroads (AAR) reported U.S. rail traffic for the week ending August 31, 2024. This week’s total U.S. weekly rail traffic was 516,632 carloads and intermodal units, up 8.4 percent compared with the same week last year. Total carloads for the week ending August 31 were 233,278, up 1.0 percent from the same week in 2023, while the U.S. weekly intermodal volume was 283,354 containers and trailers, up 15.3 percent from 2023. Seven of the ten carload commodity groups posted an increase compared with the same week in 2023. They included grain, up 5,492 carloads, to 20,494; petroleum and petroleum products, up 1,365 carloads, to 11,412; and motor vehicles and parts, up 1,144 carloads, to 17,221. Commodity groups that posted decreases compared with the same week in 2023 were coal, down 5,495 carloads, to 62,624; metallic ores and metals, down 1,487 carloads, to 21,616; and nonmetallic minerals, down 166 carloads, to 32,156. For the first 35 weeks of 2024, U.S. railroads reported a cumulative volume of 7,557,821 carloads, down 3.6 percent from last year, and 9,094,439 intermodal units, up 9.3 percent. Total combined U.S. traffic for the first 35 weeks of 2024 was 16,652,260 carloads and intermodal units, an increase of 3.1 percent compared to last year. North American rail volume for the week ending August 31, 2024, on nine reporting U.S., Canadian, and Mexican railroads totaled 343,419 carloads, up 2.3 percent compared with the same week last year, and 354,117 intermodal units, up 8.1 percent compared with last year. Total combined weekly rail traffic in North America was 697,536 carloads and intermodal units, up 5.2 percent. North American rail volume for the first 35 weeks of 2024 was 23,201,648 carloads and intermodal units, up 2.4 percent compared with 2023. Canadian railroads reported 94,106 carloads for the week, up 4.7 percent, and 58,491 intermodal units, down 18.8 percent compared with the same week in 2023. For the first 35 weeks of 2024, Canadian railroads reported a cumulative rail traffic volume of 5,538,464 carloads, containers, and trailers, up 0.3 percent. Mexican railroads reported 16,035 carloads for the week, up 8.9 percent compared with the same week last year, and 12,272 intermodal units, up 24.8 percent. Cumulative volume on Mexican railroads for the first 35 weeks of 2024 was 1,010,924 carloads and intermodal containers and trailers, up 4.1 percent from the same point last year. To view the rail charts, click here.
August 2024 Logistics Manager’s Index Report® LMI® at 56.4
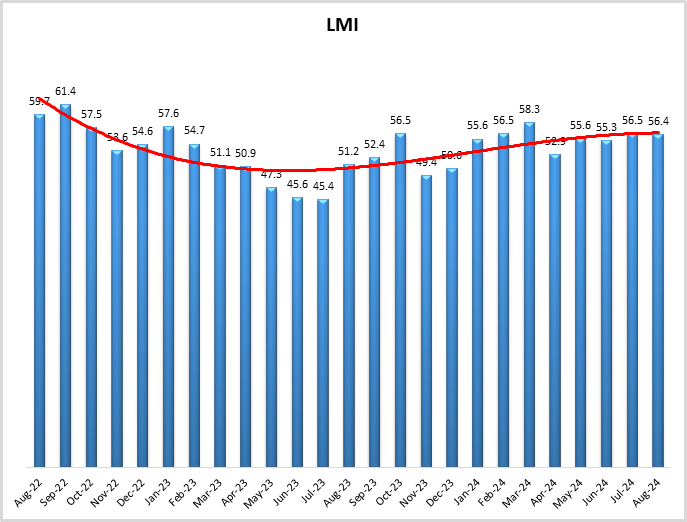
Growth is INCREASING AT AN INCREASING RATE for Inventory Levels, Inventory Costs, Warehousing Capacity, Warehousing Prices, Transportation Capacity, and Transportation Utilization. Growth is INCREASING AT A DECREASING RATE for Warehousing Utilization and Transportation Prices The Logistics Manager’s Index reads in at 56.4, down slightly (-0.1) from July’s reading of 56.5. The overall index has now increased for nine consecutive months. The index has been remarkably consistent, reading in at 55.6, 55.3, 56.5, and 56.4 over the last four months (for a standard deviation of 0.5) as the logistics industry has continued its slow, steady expansion. The major move of the August report are Inventory Levels, which are up (+6.1) to 55.7, breaking the streak of contraction that we had observed over the previous three months. This suggests that after running inventories down, firms are building them back up again in anticipation of Q4. This suggests a return to traditional patterns of seasonality that we have not seen since pre-COVID. This buildup of inventories is somewhat tempered by increases in both Warehousing Capacity (+5.0) and Transportation Capacity (+5.8). While it may seem somewhat incongruous for there to be more available capacity when inventories are up, there are some reasonable explanations when we dig into the details. The expansion of Transportation Capacity could be some smaller carriers or owner-operators “getting off the sidelines”. Transportation Prices read in at 61.6. This means that prices have increased consecutively in seven of the last eight months as well as in the last four. The prices are still nowhere near the highs of 2020-2021, but it is a marked shift from the 18 consecutive months of contraction from July 2022 to December 2023. The signs of new life in the freight market, along with anticipation of the traditional jump in demand that follows the Labor Day holiday, are likely causing some of the capacity that had been sidelined over the past two years to re-enter the market, accounting for the mild increase in available capacity. Warehousing Capacity increased at least partly because Downstream Inventory Levels are still decreasing at 46.3 (although this is a notably slower rate than July’s 40.0). As a result, downstream capacity is increasing significantly faster than upstream (67.6 to 56.8). We would expect this to shift as inventories matriculate downstream to retailers. If this does not happen, it may mark a slower-than-expected peak season. That being said, Warehousing Prices are still up (+2.8) to 63.1, with more of the cost increase coming from Downstream respondents who reported a growth rate of 67.6. Researchers at Arizona State University, Colorado State University, Florida Atlantic University, Rutgers University, and the University of Nevada, Reno, and in conjunction with the Council of Supply Chain Management Professionals (CSCMP) issued this report today. Results Overview The LMI score combines eight unique components that comprise the logistics industry, including inventory levels and costs, warehousing capacity, utilization, and prices, as well as transportation capacity, utilization, and prices. The LMI is calculated using a diffusion index, in which any reading above 50.0 indicates that logistics is expanding; a reading below 50.0 indicates a shrinking logistics industry. The latest results of the LMI summarize the responses of supply chain professionals collected in August 2024. The LMI read in at 56.4 in August, nearly unchanged (-0.1) from July’s reading of 56.5. This continues the run of moderate expansion that we have observed throughout 2024. It is interesting that the rate of expansion in the overall index has plateaued between 55.0 and 56.5 throughout most of the year (with March’s 58.3 and April’s 52.9 being the only exceptions). This is a modest growth rate below the all-time average of 61.8. The overall index has been below the all-time average every month since June 2022, when it read in at 65.0. In their future predictions, respondents predict that within the year, the overall index will reach 62.4, which is consistent with their forecasts throughout the summer and will bring us back in line with that all-time average. The logistics industry is a leading indicator and barometer for economic activity. It will be interesting to continue monitoring these movements over the next year and to see whether or not we see any acceleration past the slow, steady growth that has characterized the logistics industry throughout 2024 (which, it should be pointed out, has been a relief relative to the contraction or anemic growth we saw throughout 2023). The slow, steady growth of the LMI, in many ways, mirrors the overall U.S. economy. U.S. GDP for Q2 was revised up to 3.0% growth, which is up 0.2% from the initial estimate of 2.8%. Morgan Stanley’s current estimate for Q3 growth is 2.3% (up from the previous estimate of 2.1%)[1]. The PCE price index also came in slightly lower, moving down from 2.6% to 2.5%, providing another data point for the normalization of inflation[2]. This spending comes despite revisions showing that 818,000 fewer jobs were created between April 2023 and March 2024 than were initially reported[3]. This mix of strong spending with a softening labor market significantly increases the chances that the Fed will cut interest rates by at least a quarter point at their September meeting, something that would begin the process of loosening up spending for both the Downstream and Upstream supply chain. Despite the dip in PCE, Americans increased their spending at retailers in July, with sales up 1% from June’s reading. This is the largest month-to-month increase in consumer spending since January 2023[4]. Spending was spurred by the continued cooling of prices, which rose by only 0.2% from June to July – a far cry from the 2.5% increase from the same period in 2023[5]. There is also a seasonality element; the National Retail Federation (NRF) estimates that U.S. consumers spent $38.8 billion ($875 per household) on back-to-school shopping. This is down slightly from last year’s $41.5 billion spent but still represents the second-highest back-to-school season on record[6]. Despite this, the U.S. economy continues to be tougher on lower-income individuals. This is evidenced by
IDENTCO’s high-performance DuraChem Labels suitable for a variety of industries
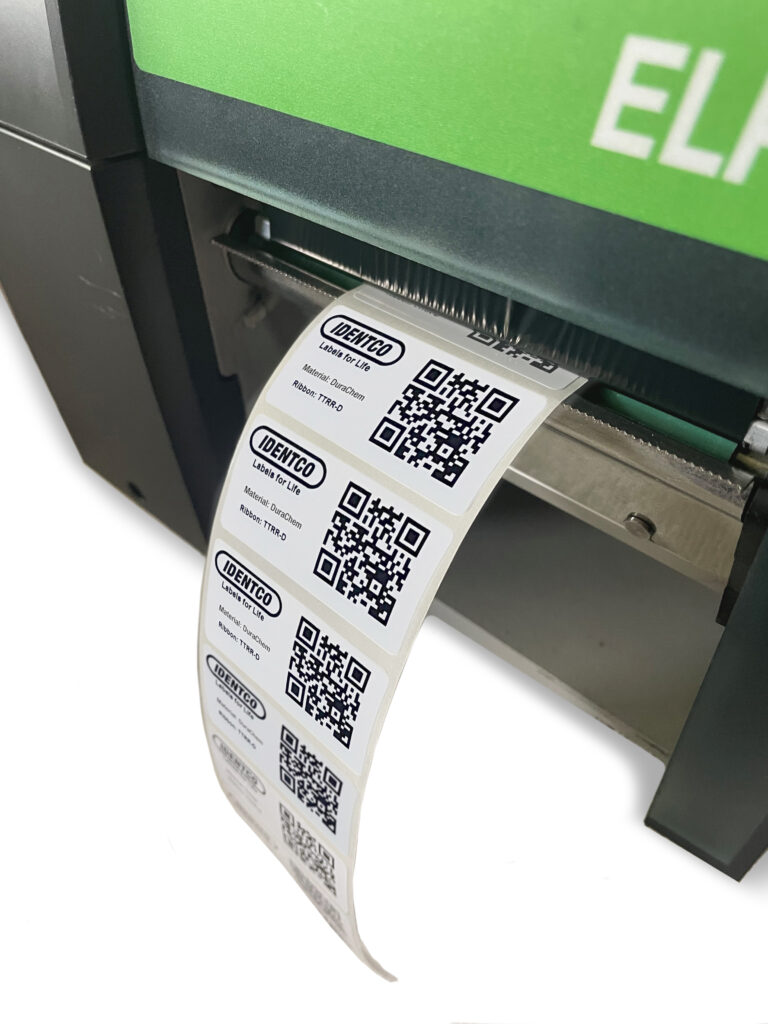
Previously known as the TTL®700 Series, DuraChem labels offer chemical, solvent, abrasion, and smudge resistance for both indoor and outdoor use IDENTCO, a manufacturer of high-performance labeling solutions for the power equipment, electronics, transportation, and general industrial sectors – has renamed its stock TTL® 700 Series. Now called DuraChem, this highly durable series of labels is constructed from white gloss polyester, a versatile material that can adhere to various standard smooth surfaces. Featuring a solvent adhesive and gloss topcoat that offers excellent chemical, solvent, abrasion, and smudge resistance, DuraChem has 2-year UL, CUL, and CSA ratings for both indoor and outdoor use. Additionally, this series can withstand temperatures of up to 150 degrees Celsius. These attributes make DuraChem labels an ideal choice for various medical, industrial, electronics, military, and automotive industries. The DuraChem series offers an assortment of face stock, adhesive, and liner combinations that allow for UV flexographic, digital pre-printing, and on-demand thermal transfer printing of variable information. This label series offers flexibility in terms of application. Depending on the circumstance, it can be hand-applied or auto-applied. DuraChem labels can be supplied blank or pre-printed, with the option of variable printing conveniently done at a customer’s location. When combined with the recommended IDENTCO ribbon, DuraChem labels meet the most demanding requirements for durability.
Bobcat expands product lineup with Backhoe Loader introduction
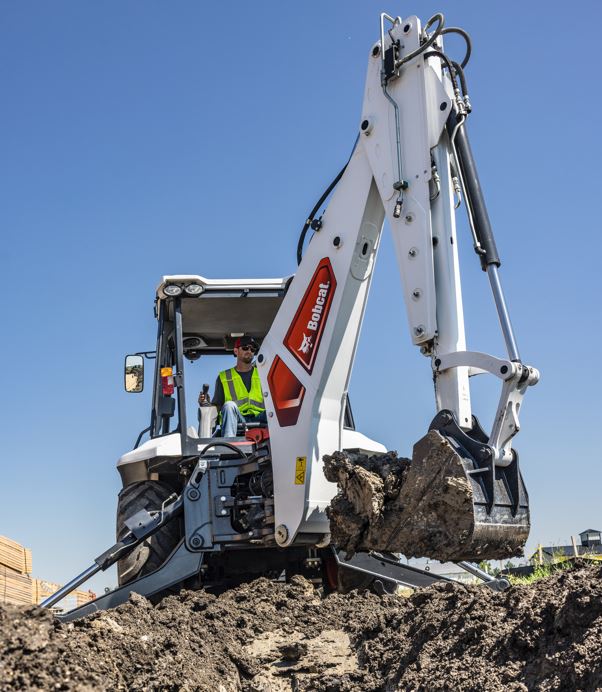
Bobcat Company, a global equipment, innovation, and worksite solutions brand, has expanded its North American product lineup by introducing the B760 backhoe loader. Designed with legendary Bobcat performance and versatility, the B760 offers the most digging depth in its size class. With a wide range of job site solutions built into one tough machine, the backhoe loader features an impressive lift capacity of more than 2,200 pounds at full reach, a digging depth of 18 feet, 5 inches, and nearly 180 degrees of backhoe swing for less repositioning and fast cycle times. The backhoe loader comes with a standard-equipped extendable arm that provides up to 8 inches of additional dig depth compared to other machines of the same size. The B760’s performance and versatility extend throughout the machine, with the front-end loader providing a lift capacity of 7,985 pounds with its standard, general-purpose bucket. “The new B760 helps operators accomplish more on the job site with its dig, load, and carry versatility,” said Jamison Wood, Bobcat product development specialist. “The backhoe loader is designed for durability, easy operation, simple maintenance, and incredible performance. Its size keeps it accessible on sites with limited space, while its impressive travel speeds keep operators productive across large job sites.” Powered by a turbocharged 3.4-liter Bobcat engine, the B760 delivers powerful, high-torque performance and efficiency. It achieves emissions compliance without a diesel particulate filter (DPF). With powerful backhoe and loader breakout forces, operators can confidently dig in and conquer some of the most challenging job site tasks, such as excavation, site preparation, material handling, trenching, snow removal, and more. The power shift transmission provides quick direction changes, while the backhoe loader’s swift travel speeds allow operators to minimize the need for a trailer. With thoughtfully laid out and easy-to-use controls, new operators can reach maximum productivity in less time. The easy-to-read 5-inch color display panel provides full-featured machine interaction and monitoring capabilities for efficient and productive operation. The operator station and optional cab are designed for all-day comfort, with controls designed for easy use and minimal operator fatigue. Additional standard features that enhance operator productivity include: Ride control for reduced bucket spillage and enhanced operator comfort Automatic return-to-dig positioning to maximize cycle time efficiency Eight work lights for long days of loader and backhoe operations A 1.4-cubic-yard general-purpose loader bucket for greater job site versatility The pilot controls for smooth, fast, and precise backhoe workgroup operations Auxiliary hydraulics to power attachments from the front and rear The B760 backhoe loader will be available at Bobcat dealerships across North America in late 2024/early 2025. Visit bobcat.com/dealer to find a local dealer. The B760 will be displayed at the American Public Works Association PWX Conference Sept. 8-11.
Cyclonaire appoints Jay Anzelmo as Vice President Sales and Marketing
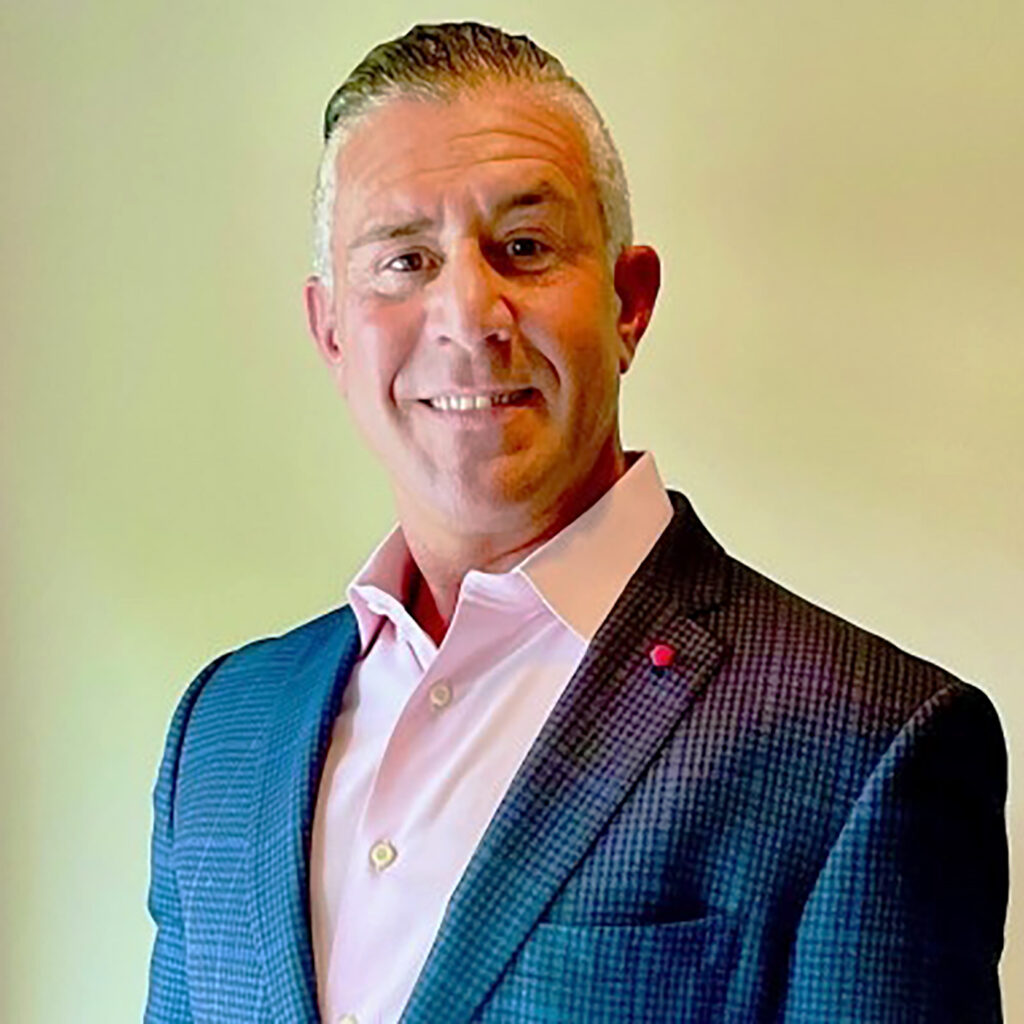
Cyclonaire Corporation, a provider of pneumatic conveying solutions, announces the appointment of Jay Anzelmo as Vice President of Sales and Marketing. Mr. Anzelmo will assume this pivotal leadership role following the retirement of Mike Colella later this year, who has served as Vice President for the past seven years. Mr. Anzelmo brings a wealth of expertise in Sales and Marketing and has a proven track record of delivering results and fostering collaborative relationships to achieve organizational goals. “We are delighted to welcome Jay Anzelmo to the Cyclonaire team as our new Vice President,” said Scott Schmid, president at Cyclonaire Corporation. “His extensive experience and strategic vision will be invaluable as we continue to expand our market presence and deliver unparalleled solutions to our customers.”In his role, Mr. Anzelmo will be responsible for driving continued growth strategies across multiple business sectors, and his leadership will play a pivotal role in advancing Cyclonaire’s commitment to excellence and innovation in pneumatic conveying technology. “I am honored to join Cyclonaire at such an exciting time in the company’s journey,” said Jay Anzelmo. “I look forward to collaborating with the talented team at Cyclonaire to drive growth, foster innovation, and exceed customer expectations.” Mr. Anzelmo assumes the role of Vice President following Mike Colella’s retirement. Mike Colella has made significant contributions to Cyclonaire’s success over the years. “We extend our heartfelt appreciation to Mike for his dedicated service, and the entire organization wishes him all the best in his well-deserved retirement,” added Scott Schmid. Mr. Anzelmo holds a Bachelor of Science degree from Missouri State University. Prior to joining Cyclonaire, he held key leadership roles at Wilson Manufacturing, CST Industries, and Universal Dynamics.
Hangcha Forklift Canada offers new material handling solutions to the Canadian market
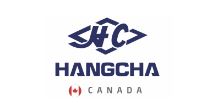
A subsidiary of the esteemed Hangcha Group welcomes new equipment following success in Australia and the U.S Hangcha Forklift Canada (“Hangcha Canada”) has introduced an innovative lineup of new material-handling equipment to the Canadian market. These new products are designed to enhance productivity across multiple industries in both indoor and outdoor operational environments. They will be available across Canada starting October 1, 2024, following their official unveiling to Hangcha Canada’s dealers on September 25, 2024. With a majority of the equipment already proven in the Australian and U.S. markets, this marks a significant milestone for Hangcha Canada as it continues to expand its product offerings and reinforce its position as a leader in the material handling industry. Hangcha Canada’s newest material handling solutions: 0.2T A Series Storage Assist Vehicle: This vehicle has a lithium battery and a maintenance-free brushless AC motor. It is designed for narrow, low-clearance environments like small warehouses, supermarkets, and labs. Operators will appreciate the ergonomic design, featuring multi-layer pads to reduce fatigue and user-friendly controls, including an integrated charger and multi-function instruments for enhanced comfort and ease of use. XC Series Electric Lithium-ion Personal Carrier: This versatile personal carrier offers efficient and sustainable transportation solutions and is equipped with a lithium battery for extended operation and minimal maintenance. It can carry up to 350kg and tow up to 2,200kg. The spacious operator compartment, suspended rear drive axle, and dual-function brake pedal ensure a comfortable and intuitive driving experience. 3.5-5.5 T X Series 4-Wheel Cushion Tire Forklift Truck with Lithium Power: A safe and reliable solution for demanding environments. Built on an eco-friendly lithium battery platform, it ensures a low center of gravity and excellent stability. The forklift’s compact and sturdy design, combined with accessible maintenance features like movable panels and a roller-equipped battery compartment, make it both efficient and user-friendly. 2.5-3.5T High-Voltage Lithium Battery Rough Terrain Forklift: Representing a new generation of rough terrain forklifts, Hangcha has merged the durability of internal combustion models with the efficiency and comfort of electric forklifts. Equipped with dual-motor high-voltage drive systems and a new energy vehicle platform, these forklifts deliver exceptional performance in challenging environments. Rough Terrain Scissor Lifts: Designed for efficiency and productivity in demanding outdoor jobs, the two-way extension platform supports a load of up to 680kg, with built-in overload protection to ensure safety during operation. Powered by an 80V lithium battery system and permanent magnet synchronous motor, the lifts are energy-efficient, reducing consumption by 8-10% compared to traditional motors. HS Series Electric Crawler Scissor Lifts: Ideal for indoor and outdoor use on uneven terrain, the lifts have a maximum working height ranging from 6.5m to 13.8m. Driven by a permanent magnet synchronous motor, these lifts provide high efficiency, strong power, and fast movement. With a 0.9m extension platform and high-strength anti-slip flooring, operators enjoy expanded workspace and enhanced safety. “To ensure seamless integration and maximum benefit from these new products, Hangcha Canada is offering detailed training sessions for our dealers, led by our technical trainer, Richard Sinclair,” shared John Sedlacek, National Sales Director at Hangcha Canada. “We are delivering the kind of innovation that truly makes a difference for both the growth of our dealers and the success of our customers.” Hangcha Canada’s training sessions will cover theoretical and practical aspects, ensuring dealers are well-equipped to support customers with these advanced tools. “I’ve seen firsthand how the Storage Assist and Personal Carrier have performed in the U.S., and the results have been nothing short of impressive,” said Frank Russo, VP of Sales and Business Development at Hangcha Forklift America. “Our global sales operation is supported by Hangcha Group’s 11 million sq. ft. manufacturing facility and its leadership in lithium-ion technology. Rest assured, there’s much more innovation on the way to make handling easier.” Hangcha Canada remains committed to delivering cutting-edge solutions to the Canadian market. Its warehouses in Mississauga, Ontario, Vancouver, British Columbia, and Vaudreuil-Dorion, Quebec, hold an inventory of more than 550 forklifts at any given time.
RSS Raises Profile at LiftEx 2024
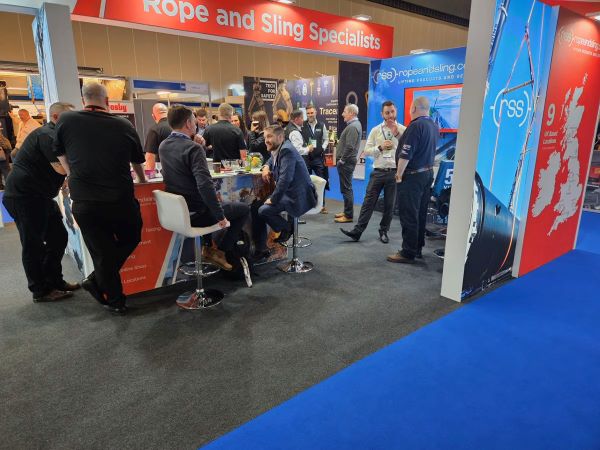
Rope and Sling Specialists Ltd. (RSS) will return as a lead sponsor and take a new exhibit to LiftEx 2024, which takes place 16-17 October at London’s Olympia. See RSS at Stand 40. Having steadily grown its presence at the Lifting Equipment Engineers Association’s (LEEA) flagship event, RSS will again sponsor the water bottles and lanyards, while a larger hospitality area will be at the center of a new-look stand. The exhibit will be the same overall size as last year’s display, which was the focal point for many attendees at the Exhibition Centre Liverpool, but the concept has been revamped and built around a longer bar set against a backdrop of enhanced graphics. Lifting and lashing products will be among those given greater prominence in Olympia’s West Hall. Alan Varney, engineering services director at RSS, said: “We had a successful show in Liverpool last year, but we want to build on that this time. Visitors can expect a more immersive experience, with interesting visuals, supported by an expert team and the usual company hospitality. The jury is still out on the relocation to a less central [UK] venue, but we’re not participating in any negativity; we want to drive a crowd to our stand and give them a flavor of the best the industry has to offer in terms of lifting and rigging products, and the personalities that support it all.” Last year, at the center of the exhibit was a map, detailing all of the company’s national facilities, including the Gemmak Engineering fabrication site. Since then, RSS has recently opened a new depot in Glasgow, Scotland, fronted by Tony McAtee, operations manager, expanding a footprint north of the border created by its Grangemouth site. An additional location in Netherton, West Midlands, will be opened later this year, under Paul Smith, while another depot on the South Coast is also in the pipeline, likely to be unveiled in early 2025. That will take the total to 14 national facilities. Varney said: “We continue to be strategic in where we open our premises, steadfast in our plan to position product and expertise as close to the point of use as possible. We have wanted to expand in Scotland for a while, and putting ourselves in the city of Glasgow will enable us to more efficiently deliver services to the region. “The Midlands site is more focussed on equipment hire and serves as a hub for specialist lifting products in the middle of the country. The southern regions are generating work for our services all the time, and our existing depots are finding it a challenge to cope with that ongoing demand. All of these locations will require engineers, drivers, and hire / sales representatives.” RSS will be represented at LiftEx 2024 by Steve Hutin, managing director; Alan Varney; Paul Glover, national director of operations; and Mark Barnard, operations manager, Swansea; they will be joined by representatives of its Heathrow and Aylesford, Kent operations. The company’s LiftEx carnival will also include a presence at the LEEA Awards, which will be presented on 16 October at London’s famous Dorchester Hotel. See RSS at LiftEx Stand 40.
Dorner appoints Mark Schmid as new Regional Sales Manager
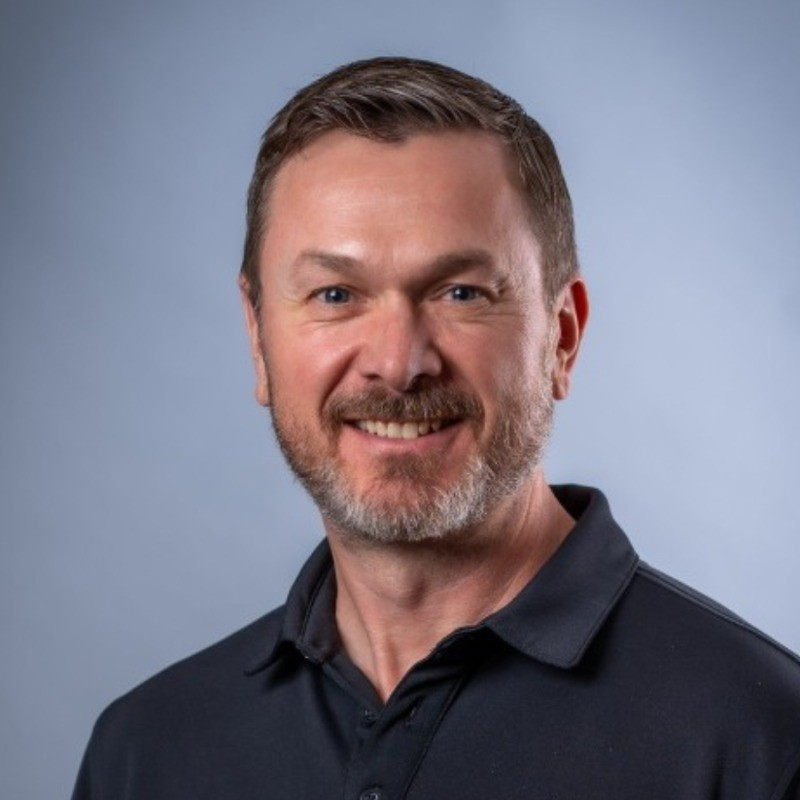
Mark Schmid has been appointed Regional Sales Manager, covering the upper Midwest portions of the U.S. for Dorner. Schmid will be working with sales channel partners and key accounts to grow the company’s automation, industrial, and sanitary conveyor business within his region. Schmid comes to Dorner with more than 20 years of automation and controls-focused experience. Most recently, he was Director of Business Development at Cybertrol, a Minneapolis-based control and information systems company. “The exciting part of the automation industry is that there are so many facets to it. Everything you come across is unique, and you must draw from experience and use creativity to develop solutions,” Schmid said. “The material handling space is a very attractive part of automation. There’s high demand for Dorner products, and I’m excited to be on board and be part of that push to promote the Dorner brand to customers in my region.” Schmid’s region includes Wisconsin, Minnesota, Iowa, Nebraska and both North and South Dakota. “Being able to bring someone onboard with Mark’s diverse background in automation, material handling and HMI and PLC controls is certainly going to benefit our customers in the Upper Midwest,” said John Kuhnz, Vice President of Sales, Precision Conveyance at Dorner. “I have no doubt that Mark will be a great asset to Dorner.”
Frontier Forklifts joins Donkey Forklifts as Southeast Texas dealer
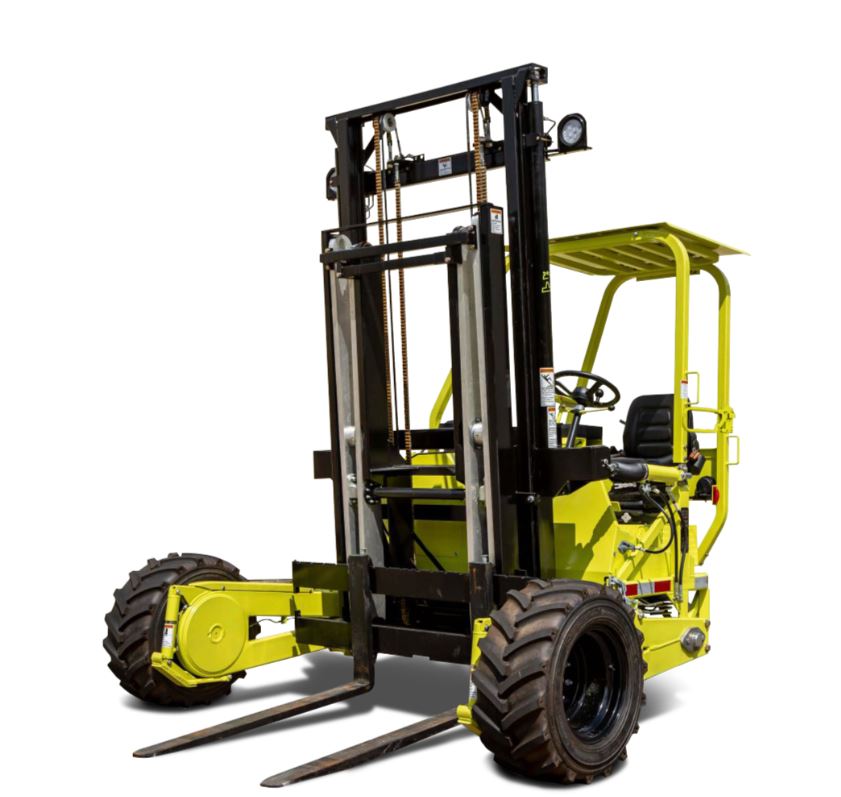
Donkey Forklifts®, an American-made forklift manufacturer known for its versatile and reliable equipment, has announced a new partnership with Frontier Forklifts, a trusted dealer with over 20 years of experience in material handling solutions in Southeast Texas. “We are excited to welcome Frontier as our newest dealer for Southeast Texas and look forward to supporting their success in the region,” said Bradley Holder, Director of Sales for Donkey Forklifts. As an authorized dealer for Donkey Forklifts, Frontier will now offer customers direct access to Donkey’s full range of forklift solutions, backed by the unparalleled service and support that both companies are known for. This collaboration aims to meet the growing demand for high-quality material handling equipment in Southern Texas. “After years of partnership in Donkey service and parts, Frontier Forklifts is proud to say we are now the factory-authorized dealer for Donkey equipment sales in the South Texas area,” General Manager Brian Harris said. “We are very familiar with the quality of the product line and the courteous and professional support offered by the factory staff. We look forward to helping South Texas with the Donkey product!” Donkey and Frontier Forklifts are eager to combine their expertise to enhance material handling standards in Southeast Texas. For more information about Donkey’s products and Frontier Forklifts’ services, visit Frontier Forklifts’ website at frontierforklifts.com, contact Brian Harris at 281 482-4500, or email sales@frontierforklifts.com.
NRF urges ILA-USMX to resume negotiations and avoid port strike
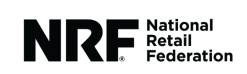
The National Retail Federation released the following statement from NRF President and CEO Matthew Shay regarding concerns about a potential labor strike at U.S. ports on the East and Gulf Coasts. The International Longshoremen’s Association and the United States Maritime Alliance have until Sept. 30 to reach a new contract. “NRF continues to call upon the International Longshoremen’s Association and the United States Maritime Alliance to return to the bargaining table to resume negotiations in order to reach a new deal before the contract expires on Sept. 30. The threat of a strike during the peak shipping season has many retailers already implementing costly mitigation strategies. “At a time when inflation is on the downward trend, a strike or other disruption would significantly impact retailers, consumers, and the economy. The administration needs to offer any and all support to get the parties back to the table to negotiate a new contract.” In June, NRF led a coalition of 158 state and federal trade associations in a letter to President Biden urging the administration to work with the negotiating parties to reach a new agreement. Earlier this year, NRF sent a letter to ILA and USMX calling for the resumption of port labor negotiations. As the leading authority and voice for retail, NRF will continue to advocate for policies that ensure supply chain resiliency.
Research into AI adoption finds U.S. service companies held back by lack of skills, security concerns, and legacy systems
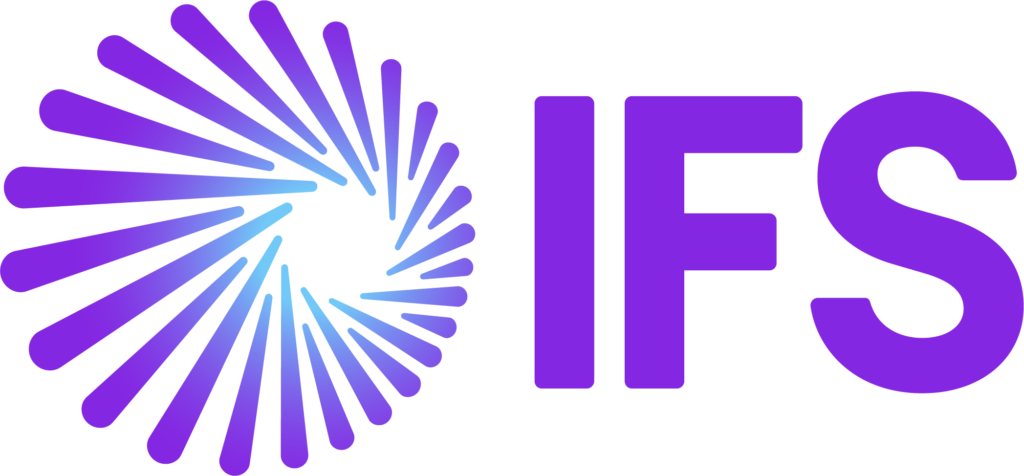
However, there is optimism that Industrial AI will improve quality control and bring new sustainability gains Research from IFS, a technology provider of enterprise cloud and industrial AI software, shows despite high levels of AI optimism among service companies, hurdles still stand in the way of successful AI adoption and deployment. Limited skills & expertise (38%), ethical/safety/security concerns (36%), and a legacy-based technology landscape (36%) were identified as the top service factors slowing adoption progress. What’s more, only 58% of respondents working in the service industry felt their industry was adopting AI faster than others—the lowest score out of all industries surveyed. However, there is optimism about the benefits of AI. Cost reductions/margin gains (31%) and mitigating risk (31%) are the two areas where service companies expect AI to make large differences. Sustainability planning also correlates directly with overall AI optimism. The less wide-ranging an industry’s sustainability strategy was regarding AI, the less likely they were to be optimistic about AI in general. Interestingly, most service respondents with an AI strategy for sustainability believe it can have the biggest impact through quality control and reducing product discarded (22%), alongside regular simulation and optimization of the business targeted to meeting sustainability goals (22%). Christian Pedersen, Chief Product Officer, IFS, commented: “At the surface level, the lack of optimism across some respondents may suggest we are at the edge of a trough of disillusionment, particularly following the all-encompassing hype that AI enjoyed for much of the last 18 months. “The lofty expectations for AI bely a fundamental misunderstanding of how it is supposed to drive value. The real power lies in Industrial AI, where data flows through every part of your business, combining structured, interlinked datasets to uncover insights, optimize every process, and marry the digital with the physical world. If a business doesn’t have a strategy to reach that point, then they need a partner who can guide them on that journey,” concluded Pedersen. There are more insights and actions in the Industrial AI: the new frontier for productivity, innovation and competition Executive Report. The IFS Global AI Optimism League Table by Country Research Methodology Censuswide surveyed 1,709 C-level/President/SVP/Directors who work in Services, Manufacturing, Telecommunications, A&D, Construction & Engineering, or Energy & resources in organizations with $50m+ annual revenue (Aged 18+) across the U.S., Canada, UK, Germany, France, UAE, Norway, Japan, Australia, Sweden, Denmark and Finland.
Women In Trucking Association announces its September 2024 Member of the Month
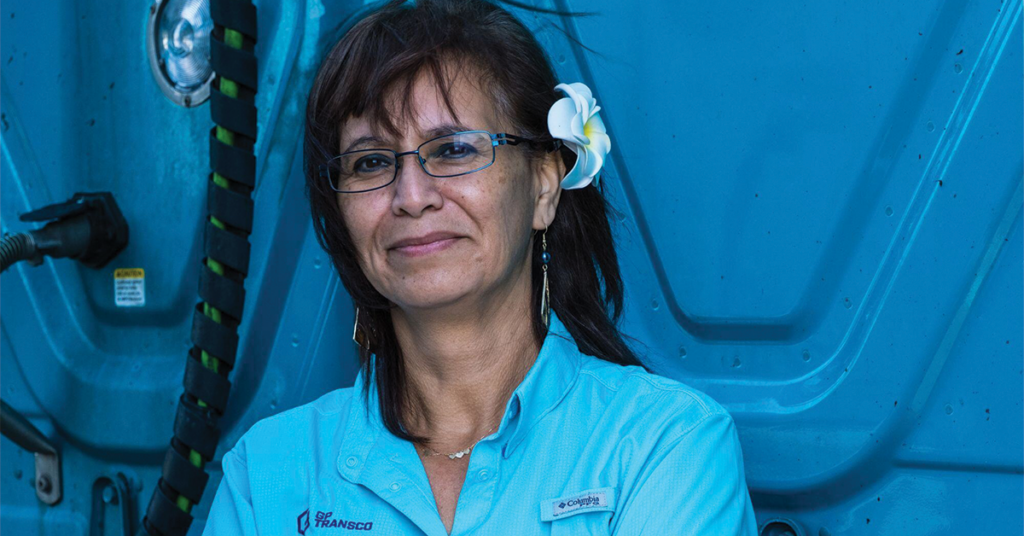
The Women In Trucking Association (WIT) has announced Lehua Anderson as its September 2024 Member of the Month. Anderson is a professional driver for GP Transco, a trusted leader in transportation that delivers excellence and innovative solutions for the trucking and logistics industry. Originally from Moloka’i, a tiny island in Hawaii, Anderson relocated and was raised in rural Alaska, where much of the population survived on fishing, farming, and hunting. This upbringing, surrounded by a family of towering Polynesian men, showed her that challenges are meant to be conquered, regardless of gender norms. “Men don’t scare me,” says Anderson. Once Anderson’s children moved out, she and her husband decided they wanted to travel and began pursuing professional truck driving careers. Now, with a staggering 25 years of overall experience, she enjoys the freedom of driving, saying, “I don’t have to manage or supervise anyone, and I have the freedom to make my own choices about when my day is going to start and where I want to go.” For Anderson, trucking isn’t just a profession; it’s a passion forged through years of dedication and a deep-seated love for the open road. Anderson stresses the importance of researching and finding a company that prioritizes the safety of its drivers, especially as a woman in a male-dominated industry. As an example, while at her first company, she recalls a time she got stuck in a blizzard with no heat in her truck. Anderson relied on her ten years of living in Alaska to survive, showcasing her ability to navigate any roadblock with finesse and confidence. Anderson is a beacon of strength and resilience in the trucking world, where grit and determination pave the way. Her journey with GP Transco is about miles driven and overcoming obstacles with unwavering courage. As Anderson continues to drive forward with GP Transco, she embodies the perseverance that defines the Women in Trucking community. Her story inspires admiration and a profound respect for those who dare to break barriers and pave new paths in the trucking world.
Vacuum Barrier Corporation demonstrates high-speed Liquid Nitrogen Dosing System at Pack Expo
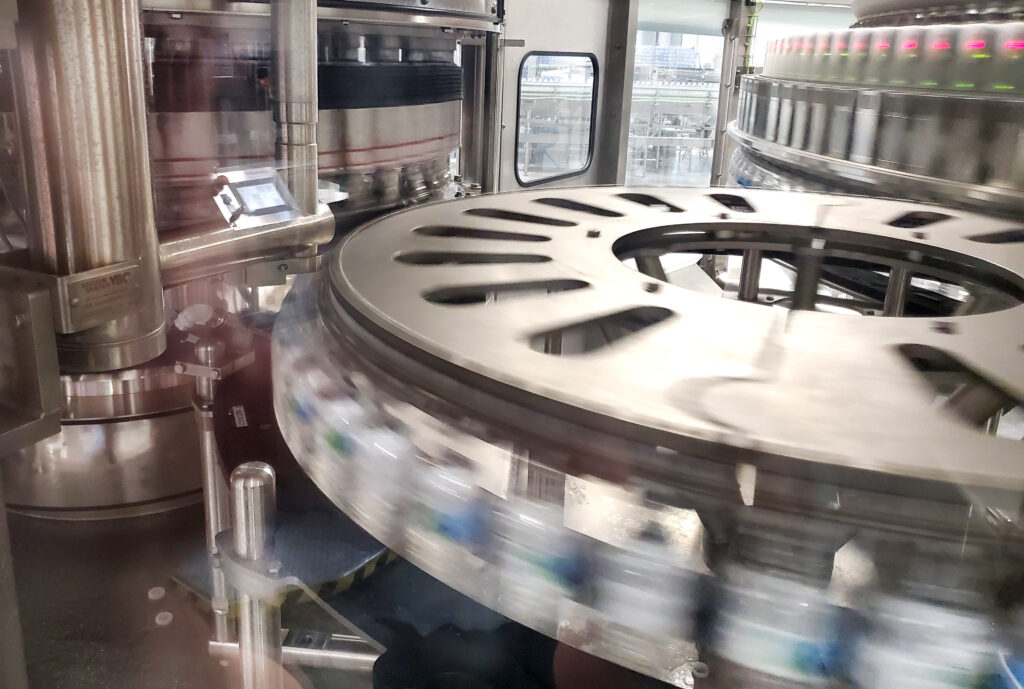
Among other benefits, the company’s new NITRODOSE® G3 SERVODOSER® can adjust liquid nitrogen flow rate without nozzle changeover Vacuum Barrier Corporation will demonstrate its newest high-speed liquid nitrogen dosing system at Pack Expo, November 3-6 in Chicago. At Booth C-2516, the company will display its NITRODOSE® G3 SERVODOSER®, whose differentiators include adjusting the flow rate during discrete and continuous dispensing without changing nozzles. An advanced dosing system designed for fast, precise delivery of low-pressure liquid nitrogen in beverage applications, the NITRODOSE® G3 SERVODOSER® allows manufacturers to adapt to their production needs without downtime. The seamlessly integrated system can handle up to 2,000 containers per minute (CPM) while offering exemplary dosing control. The NITRODOSE® system is used for non-carbonated beverages in plastic bottles or aluminum cans, where it adds rigidity to enhance structural integrity and durability. Equipped with a seven-inch color touchscreen for intuitive operation, the NITRODOSE® G3 SERVODOSER® can deliver dosing durations as brief as four milliseconds and offers an accuracy of approximately +/-1% of dose weight. The system also offers Clean in Place (CIP) protection, with an automatic cover that prevents moisture from entering the dosing head during the process, eliminating potential freeze-ups. The nozzle is designed to withstand high-pressure washdowns or harsh chemical cleanups. “The NITRODOSE® G3 SERVODOSER® represents a significant advancement in liquid nitrogen dosing technology,” said Jim Fallon, International Sales Manager at Vacuum Barrier Corporation. “This system not only meets the high demands of beverage production but also offers unparalleled flexibility and efficiency.
Hamilton enhances legacy casters with V-Style Seal and launches new Dual Wheel Series
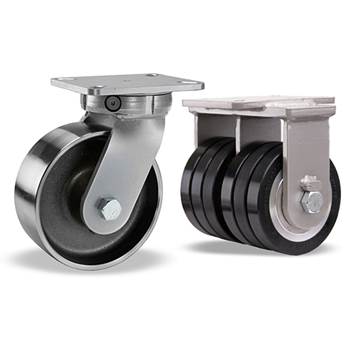
Hamilton Caster & Mfg. Co., a 117-year-old industry leader in heavy-duty industrial casters, has announced enhancing its legacy Super Endurance Caster (SEC) series, now rebranded as the Spinfinity® Super Endurance Caster (ZFSEC) series. In addition, Hamilton is introducing the all-new Spinfinity® Super Endurance Dual Caster (ZFSEC2) series, both of which feature a new heavy-duty ‘V-Style’ seal designed to elevate performance in the most demanding environments. The Spinfinity® Super Endurance Caster (ZFSEC) series replaces Hamilton’s legacy SEC series, setting a new benchmark for kingpinless caster design in extra heavy-duty applications. The heavy-duty ‘V-Style’ seal is central to this upgrade, which offers protection against dirt, debris, and moisture. This advanced sealing technology ensures consistent performance and extends the caster’s life, making it the ideal choice for environments where reliability is critical. “With the introduction of the V-Style seal, the ZFSEC series is engineered to withstand the harshest conditions while providing zero-fix, 100% maintenance-free operation,” said Mark Lippert, president of Hamilton Caster. “This enhancement allows our customers to minimize maintenance costs and downtime, further solidifying Hamilton’s reputation for durability and dependability.” The ZFSEC series retains the robust construction that Hamilton is known for, including a swivel top plate and inner raceway made from forged steel, providing superior strength for shock conditions. Sealed precision ball bearings are also now standard in all wheels, contributing to the maintenance-free performance of the series. Notably, the zerk fittings have been eliminated, as the new design makes them unnecessary. Complementing the ZFSEC series, Hamilton introduces the all-new Spinfinity® Super Endurance Dual Wheel Caster (ZFSEC2) series. This dual-wheel series is engineered for extra heavy-duty applications where stability, durability, and maintenance-free operation are paramount. Like its counterpart, the ZFSEC2 series leverages the new ‘V-Style’ seal, ensuring that each caster is fully protected against contaminants that could compromise performance. Combined with sealed precision ball wheel bearings, this caster series ensures zero-fix, 100% maintenance-free performance. The dual-wheel configuration enhances stability and allows for a lower overall height, offering a perfect blend of strength and maneuverability. Casters in both series are finished in a durable HAA polyester platinum powder coat. They are available in a wide variety of wheel types, allowing for customization based on application needs. For complete wheel specs and product details, check out the Spinfinity® Super Endurance Caster Landing Page and the Spinfinity® Dual Caster Landing Page.
Episode 516: Transforming plastic waste in warehouses into durable products with Trex
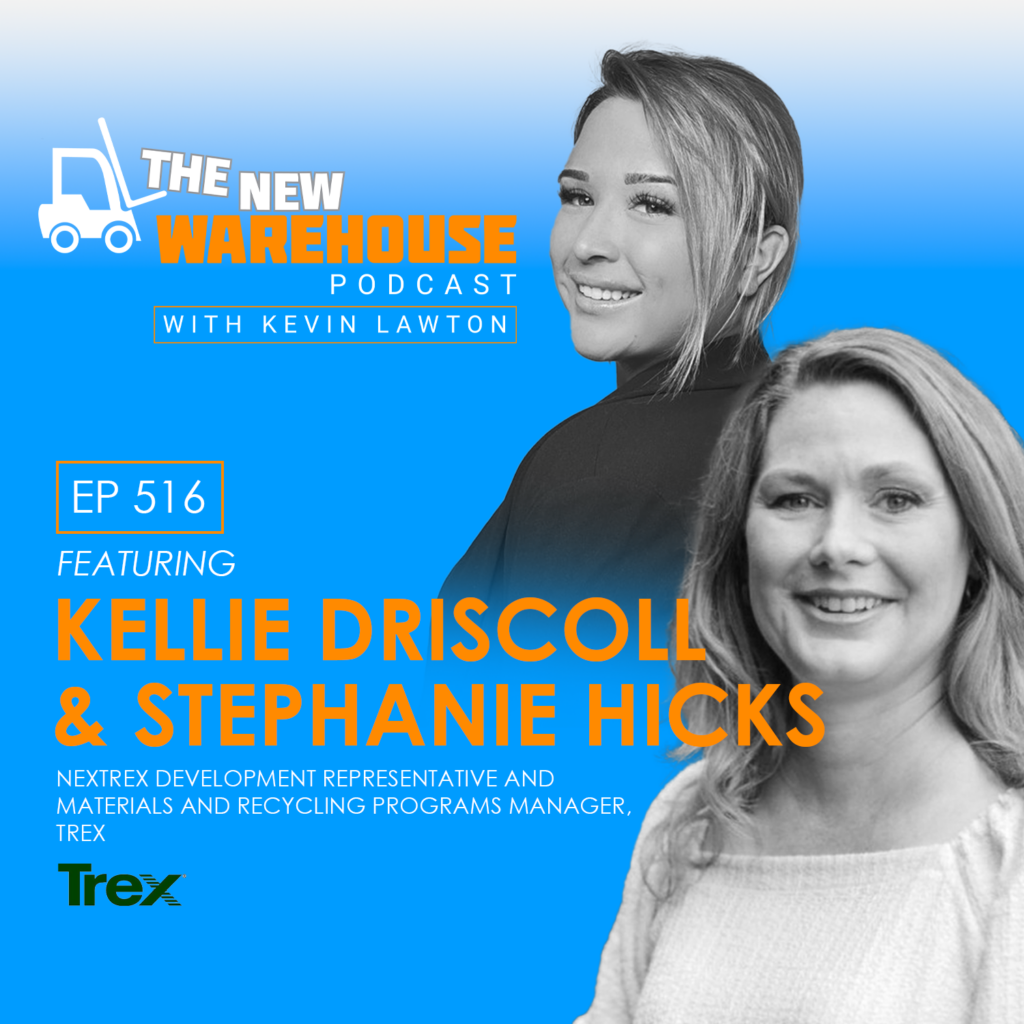
Today, we are joined by Kellie Driscoll, the NexTrex Development Representative, and Stephanie Hicks, the Materials and Recycling Programs Manager, both from Trex. Trex is widely known for manufacturing composite deck boards using recycled materials. In this episode, Kellie and Stephanie discuss Trex’s unique recycling initiatives, particularly their work with warehouses to recycle polyethylene film into durable decking materials. Recycling Plastic Waste in Warehouses Trex has become a pioneer in sustainable manufacturing, largely thanks to its NexTrex program. The program utilizes polyethylene film, a common byproduct in warehouses, and transforms it into the core material for Trex decking. Kellie Driscoll explains, “Our bread and butter when it comes to getting polyethylene film is working with distribution centers and warehouses.” By partnering with these facilities, Trex helps reduce landfill waste and provides warehouses with a sustainable outlet for their plastic film, offering them both environmental and financial benefits. How NexTrex Works: From Waste to Wonder NexTrex operates by establishing a systematic recycling process within warehouses. Trex works closely with these facilities to ensure the efficient collection, bailing, and storage of polyethylene film. “We have a team of about 20 reps that cover the country… it’s a lot of cold calling and networking,” says Stephanie, highlighting Trex’s approach to engaging warehouses. Once the plastic film is collected and baled, Trex arranges its transportation to their plants to process it into decking materials. “If they don’t have a bailer, we have a bailer financing program where we purchase it for them, and instead of rebating for the film, it goes towards paying off the bailer,” adds Stephanie. The commercial recycling program provides a second life for plastic waste and supports the increasing demand for sustainable building products. The Future of NexTrex The NexTrex program continues to evolve, addressing the challenges of plastic waste recycling through education and creative problem-solving. For instance, Kellie notes the importance of community involvement in expanding recycling efforts: “It’s continuous education…we have a program, we’re willing to help.” Trex is also committed to assisting warehouses with the necessary infrastructure to ensure the success of their recycling initiatives. “We provide a good solution to get the plastic out and get it recycled and we are creative at removing obstacles to help people meet their goals,” says Stephanie. As more distribution centers join the program, NexTrex can significantly impact both sustainability and the bottom line for the businesses involved. Key Takeaways NexTrex Program: A pioneering initiative by Trex to recycle polyethylene film from warehouses into composite decking. Sustainability and Savings: Warehouses benefit both environmentally and financially by partnering with Trex for plastic recycling. Ongoing Growth: Trex is expanding the NexTrex program through education and infrastructure support, aiming to increase its impact in the warehousing industry. The New Warehouse Podcast Episode 516: Transforming Plastic Waste in Warehouses into Durable Products with Trex
MHIA to celebrate EVOL Milestones and introduce latest innovations at SuperCorrExpo 2024
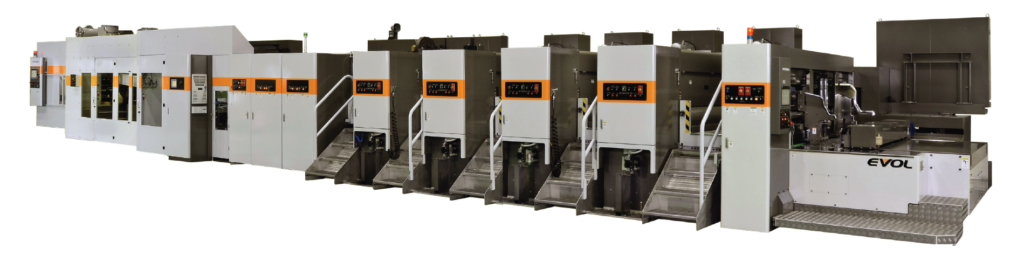
Mitsubishi Heavy Industries America (MHIA) Corrugating Machinery Division, a corrugating and box-making machinery supplier, announced its participation in SuperCorrExpo® 2024. Visit us at Booth #2357 in Orlando, Florida, from September 8 to 12 to discover how MHIA is teaming up with box makers worldwide. “It’s been an exciting year for MHIA, and we look forward to celebrating with our customers and teams worldwide,” said Hiroyuki Kikumoto, president of MHIA Corrugating Machinery Division. In celebration of EVOL’s latest global milestones—over 235 EVOLs sold in North America and over 670 worldwide—MHIA will honor its customers and team with an Ice Cream Social on Tuesday, September 10th, from 2:00 to 4:00 p.m. at Booth #2357. Attendees are invited to cool off and learn why many box plants choose EVOL. “We could have bought any machine we wanted, but it was EVOL all the way,” said the General Manager of Rand Whitney. Enhanced EVOL Digital Services: In addition to highlighting its renowned equipment, representatives will also be on hand to discuss the significant enhancements to the EVOL Digital Services program, including the expansion of the EVOL AR Library and its integration with Maintenance Agreement Visits (MAVs). The EVOL AR Library now features a comprehensive collection of augmented reality-enhanced procedures for the EVOL 100, offering step-by-step guidance for machine maintenance. Future developments will include tailored procedures for the EVOL 115, ensuring up-to-date instructions for all users. “At MHIA, innovation is our driving force,” said Christine Little, Director of Sales for MHIA Corrugating Machinery Division. “These advancements in our EVOL Digital Services are part of our ongoing commitment to revolutionizing service operations and empowering our customers with cutting-edge tools for success.” Production Improvement Program (PIP): Learn about our new Production Improvement Program (PIP), designed to help maintain EVOL machines to original equipment manufacturer (OEM) specifications. This four-month program includes eight visits from an MHI consultant, offering training, analysis, and continuous support to keep operations running smoothly. MC-100 Flexo Folder Gluer (FFG): Not to be missed, MHIA is also highlighting its MC-100, a state-of-the-art Flexo Folder Gluer that delivers speeds of 300 boxes per minute and can double feed for 500 boxes per minute. The innovative stop-and-start wheel feeder ensures 100% alignment and quality control, while elevated platforms provide easy operator access to minimize downtime. MPF Prefeeder: Discover our latest Prefeeder (MPF), designed for maximum efficiency and reliability. The MPF delivers sheets to top printing flexo folder gluers (FFG) at speeds of 400 boxes per minute without interruption. It handles both single-wall and double-wall sheets with precision, ensuring continuous operation and high-speed stable stacking. Gold Star Service Team and Support: “Whether in-house or online, MHIA’s Gold Star Service Team sets the standard for customer support. During SuperCorrExpo 2024 and beyond, our team is dedicated to evolving with our customers’ needs and is ready to provide unparalleled assistance throughout their journey with MHIA,” said Christine Little, Director of Sales for MHIA Corrugating Machinery Division. Join MHIA at SuperCorrExpo 2024 to explore the benefits of these new offerings, engage with our sales, service, and technical team members, and discuss collaboration opportunities. Learn more about how MHIA continues pushing innovation boundaries in the corrugated industry.
Vital and Advanced: Access Control Group’s Fleet Management Solutions
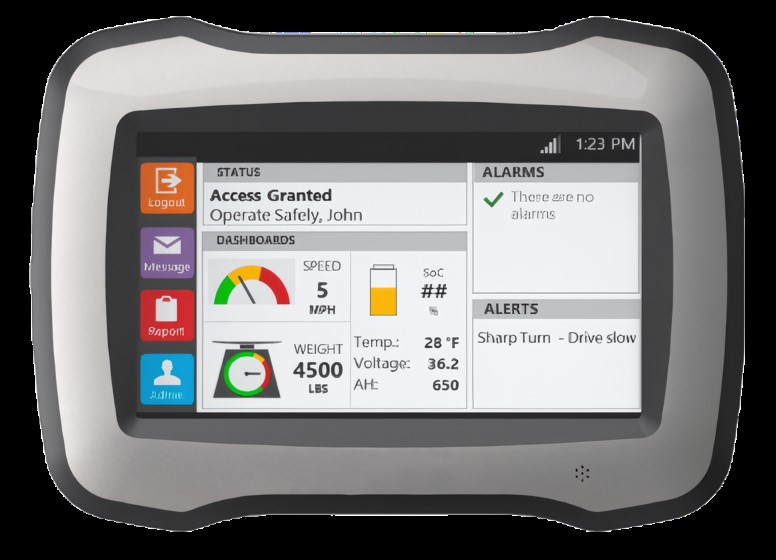
Access Control Group, a provider of industrial asset management solutions, continues to revolutionize the industry with its flagship products, Vital and Advanced. Since their introduction, these innovative fleet management systems have transformed how businesses monitor and optimize their powered equipment fleets. Vital, the company’s entry-level solution, offers a versatile and cost-effective approach to asset tracking. It features precision hour meter readings, impact detection, and real-time GPS tracking. Vital’s harness-based system connects to vehicle inputs through an SSI, making it ideal for businesses of all sizes looking to improve their operational efficiency. Building on Vital’s capabilities, Advanced offers a more comprehensive fleet management solution. It includes features such as operator RFID authentication, certification tracking, and OSHA-compliant safety checklists. Advanced also provides fleet usage monitoring and productivity metrics, making it a powerful tool for businesses looking to maximize their fleet’s productivity and safety. Both Vital and Advanced integrate seamlessly with Access Control Group’s AssetPro 360 platform, allowing for detailed analytics and reporting. This integration enables businesses to make data-driven decisions about their fleet management strategies, potentially leading to significant cost savings and efficiency improvements. The continued success of Vital and Advanced underscores Access Control Group’s commitment to innovation in the fleet management sector. As businesses increasingly seek ways to optimize their operations and reduce costs, these products continue to play a crucial role in shaping the future of industrial asset management.
PFlow highlights F Series Vertical Reciprocating Conveyor for stadiums and arenas
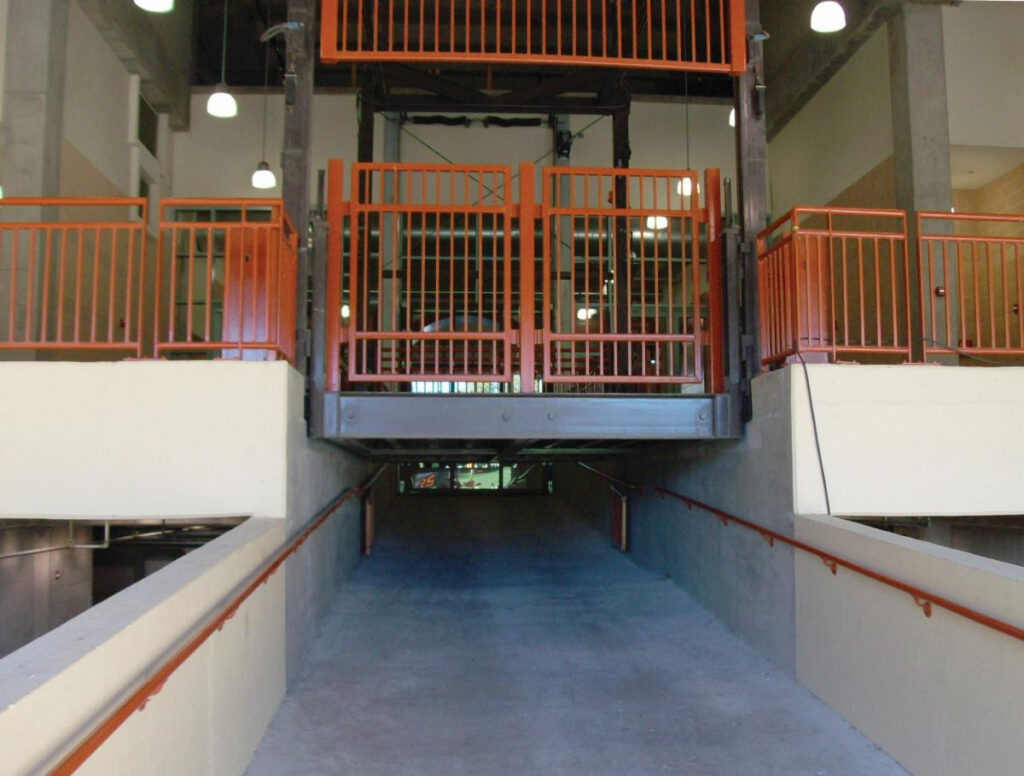
Easily handles loads of up to 50,000 pounds or more PFlow Industries, the pioneer in vertical reciprocating conveyor (VRC) technology, highlights the F Series VRC. This 4-post mechanical vertical lift can easily handle loads of up to 50,000 pounds or more in a wide range of material handling applications. The lift can also be customized to handle lift material loads up to 200,000 pounds. The F Series is ideal for lifting multiple pallets, oversized materials, large carts, or heavy machinery between two or more levels, indoors or outdoors. PFlow develops custom-made solutions using F Series technology to meet the unique needs of stadiums and arenas. For example, PFlow partnered with Dallas-based material handling provider Cisco-Eagle to create a VRC capable of lifting a 10×19-foot section of the University of Texas stadium concourse to create enough clearance in the field-level entrance below for Big Bertha to make it into the stadium. The VRC lifts the 12,000-lb section within 30 seconds, allowing Big Bertha, the world’s largest bass drum, to enter and exit the arena seamlessly. The F Series 4-post mechanical VRC offers maximum flexibility in carriage size, capacity, and traffic patterns, allowing loading and unloading from all four sides. Featuring an unlimited carriage size, with a minimum length of 6 feet wide and 6 feet 6 inches long, the F Series can lift large and bulky loads that cannot be accommodated by other lifting means. Its ability to reach any floor level maximizes facility use and provides greater material handling operational flexibility. The F Series has a standard travel speed of 18 feet per minute (FPM). It can be customized to accommodate speeds of up to 400 FPM, making it an essential part of automated, high-speed/high-cycle material handling applications used in continuous cycle operations – 24/7/365. The F Series is backed by a lifetime structural warranty and is crafted with quality construction that offers reliable, long-term performance, ensuring less downtime. It can be hot-dipped, galvanized, or epoxy-finished to withstand extreme weather conditions and temperature fluctuations while enhancing corrosion resistance in harsh outdoor or wash-down environments. To ensure worker safety and protect material payloads, the F Series features numerous built-in advanced safety features, including limit switches that shut down the motor and engage the brake when the switch is tripped, or power is lost; motor overload protection; chain sensors that prevent the slack chain from jumping the sprockets; and safety cams that prevent unintended carriage descent. The units conform to ASME B20.1 Safety Standards.