MAHLE aftermarket achieves milestone in Operational Efficiency with AutoStore empowered by Kardex
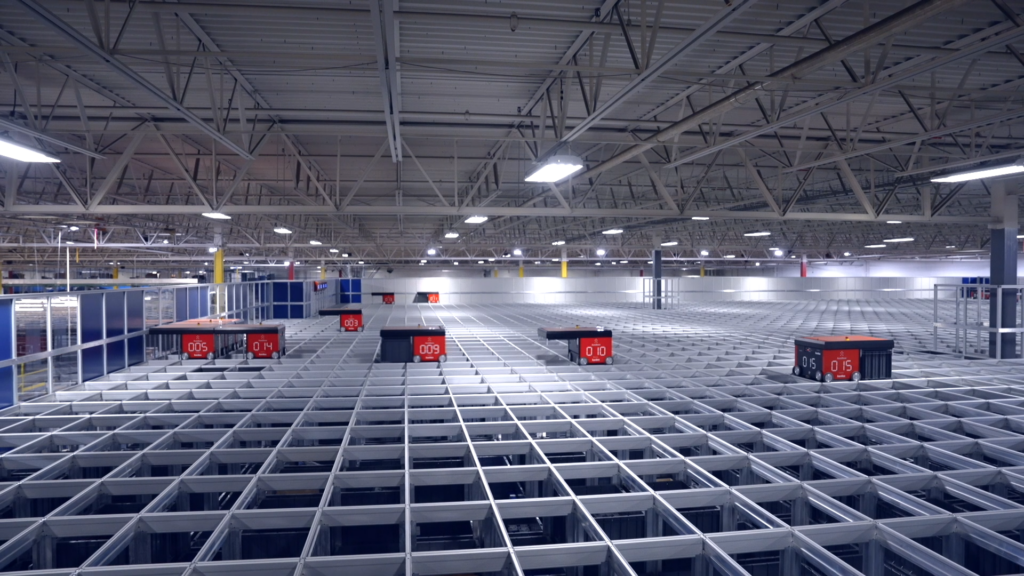
MAHLE Aftermarket turned to Kardex for an automated storage and retrieval solution following a shift in orders from large pallets to mixed-SKU single cartons and storage constraints at its Olive Branch, Mississippi fulfillment center, with the global parts and solutions provider ultimately selecting AutoStore empowered by Kardex Having witnessed a trend towards more small package orders and less frequent large stock pallet orders, MAHLE Aftermarket selected a highly efficient AutoStore empowered by the Kardex robotic cube storage system to increase capacity and throughput. A global parts and solutions provider to the independent aftermarket was also experiencing storage capacity constraints at its Olive Branch, Mississippi distribution center. MAHLE looked for a high-density storage solution that would enable it to adapt to the shift in customer order profiles and is scalable for future growth. Having examined various options, MAHLE Aftermarket invested in the AutoStore empowered by the Kardex solution. The project has been hailed a success by MAHLE, helping the company store more products in less space and ship small orders more efficiently. Working together proves successful for MAHLE and Kardex MAHLE chose Kardex to implement the intelligent goods-to-person automated storage and retrieval system (ASRS) tailored to MAHLE Aftermarket’s material flow, with market-leading inventory storage density and processing. The complete AutoStore solution at the Mississippi facility comprises 42,000 bins, seven ports, and 18 robots, in addition to a connected conveyor solution with 18 gravity lanes used for consolidation. Designed and planned by the experts at Kardex, the AutoStore solution was built and commissioned on schedule and ramped up quickly and smoothly. Kardex FulfillX maximizes the capabilities of AutoStore robotic cube systems to optimize resources and processes, delivering the fastest order fulfillment solution per square foot on the market. It increases storage capacity by up to 4 times and enhances performance by up to 10 times compared with traditional methods without additional workforce. MAHLE praises density, scalability, and hands-on support MAHLE Aftermarket has hailed the support Kardex provided throughout the project. Lorraine Hinderer, MAHLE Aftermarket Head of Business Innovation and Excellence, says, “One of the reasons we chose Kardex is because compared to the other integrators, they were able to provide an end-to-end solution tailored to our material flow, whereas the others were focused on selling their solution and not a holistic approach. I would recommend Kardex to other companies – and have actually – just due to the way that they support in the whole initial design and sizing… but also in actually implementing the system on-site.” Rhiannon Fisher, MAHLE Aftermarket Head of Business Excellence for the North America region, adds, “The support provided by Kardex exceeded expectations. During the design process, they were very hands-on. They provided support on-site during the entire process and ultimately delivered a turnkey solution.” Fred Fox, Director of Project Success for the Kardex Solutions AutoStore team, explains that Kardex offers clients the flexibility to either leverage Kardex FulfillX, the purpose-built software package designed specifically for AutoStore end-user solutions, integrate other warehouse management systems (WMS), or utilize their own software. In the case of MAHLE Aftermarket, it chose to integrate with its existing SAP Warehouse Management System. “Together, we got a really good solution in place, and that’s just part of who we are and what we want to do,” Fox states. MAHLE Aftermarket prepares for the future with AutoStore empowered by Kardex Following the success of the Olive Branch project, MAHLE Aftermarket automated a second operation in Décines-Charpieu (Lyon), France, including 22,440 storage bins, seven robots, and two workstations. MAHLE continues to evaluate its other locations worldwide to assess if AutoStore, empowered by Kardex, can enhance customer service, increase efficiencies, and standardize its operations. Kardex delivers a wide range of potential solutions for both logistics and manufacturing operations.
MAXXDRIVE gear units deliver powerful performance for demanding applications
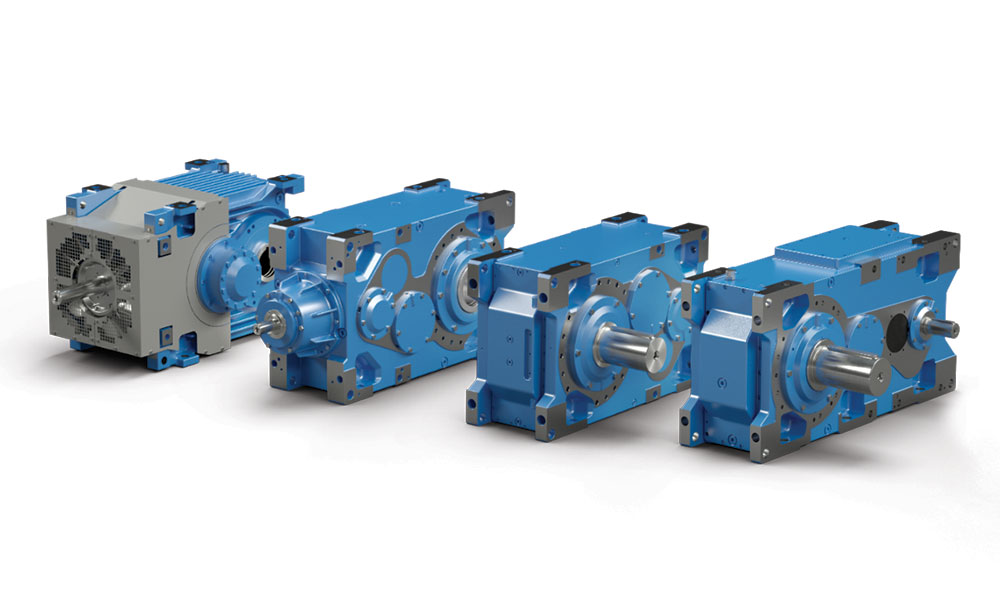
MAXXDRIVE industrial gear units from NORD DRIVESYSTEMS deliver significant output torques, quiet operation, and long service life for heavy-duty industrial applications. NORD’s MAXXDRIVE product family includes both parallel shaft and right-angle designs for adaptability to a wide range of heavy industrial applications. MAXXDRIVE industrial gear units from NORD DRIVESYSTEMS are designed to handle heavy-duty applications such as bucket elevators, agitators, conveyor belt drives, mixers, mills, drums, crushers, and more. The product family is available in a parallel shaft design as well as a right-angle design. Constructed according to the UNICASETM housing principle in which all bearings and seals are contained within a single casting, the robust gear units are optimized to ensure excellent load capacity, long service life, long bearing life, quiet operation, and are lower in weight than jointed housing gear units. The industrial gear units additionally offer many modules, input options, and output options for high versatility and adaptability to a wide range of applications. MAXXDRIVE industrial gear units offer a unique combination of flexibility and durability. They feature mounting surfaces on six sides of the drive for versatile mounting configurations and flexible integration into installation spaces. As a standard, the gear units are equipped with an efficient NBR or FKM sealing system that is suitable for many environments. For specific ambient conditions, optimized sealing systems incorporating gamma-ring, labyrinth, and Taconite seals are also available. Standard compact MAXXDRIVE industrial gear units include MAXXDRIVE parallel industrial gear units and MAXXDRIVE right-angle industrial gear units. MAXXDRIVE parallel industrial gear units have 11 case sizes to choose from and offer a torque range up to 2,495,900 lb-in, performance up to 8,075 hp, and 2-stage or 3- stage gearing options. MAXXDRIVE right-angle industrial gear units also have 11 case sizes available but in 3-stage and 4-stage gear reductions with output torque up to 2,301,200 lb-in and performance up to 2,850 hp. Both designs are extremely durable thanks to UNICASE housings and high precision bevel gearing. High quality, low friction bearings and large center distances ensure significant load capacity and reliable automation. Reinforced output bearings with a spread bearing design and dry cavity are also available for applications requiring increased bearing load capacities and additional oil leak protective measures such as agitators or mixers. MAXXDRIVE XD parallel gear units have 10 case sizes available in 3-stage or 4-stage reductions and like the MAXXDRIVE parallel gear units, deliver output torque up to 2,495,900 lb-in and performance up to 8,075 hp. These industrial gear units are engineered to meet the special requirements of crane and hoist applications, featuring a center distance increased by 35% compared to the compact MAXXDRIVE series. This extended distance enables maximum space for the motor and rope drum to be on the same side of the gearbox in a unique U-shaped arrangement ideal for lifting gear drives. The housings are FEA-optimized for overhung load, especially downwards forces, and include an inspection cover on top of the unit for easy maintenance and service access. Both 3-stage and 4-stage versions feature the same overall unit dimensions and center distances for a standardized design that reduces system variants and lowers the Total Cost of Ownership (TCO). MAXXDRIVE XT industrial gear units have been designed especially for applications requiring high speed ratios in combination with high powers. They offer a 2-stage, right-angle gear unit with a unique housing geometry optimized to achieve maximum thermal capacity. An efficient cooling fin design helps dissipate heat faster while an axial fan and air guide covers enhance airflow to prevent the unit from overheating at maximum power. Thanks to their effective cooling abilities, these drives provide a robust solution in environments with demanding ambient conditions and large temperature fluctuations. The right-angle design additionally enables a symmetrical configuration for mirror image installations where space is limited and can also be mounted on a swing base depending on the application. In addition to standard MAXXDRIVE options, NORD also offers an Endurance Package combining several protective measures that ensure drives will withstand challenging environments, such as those within the Grain industry. The five main components of the package include a drying agent filter, oil sampling point, quick fit filter trolley connection, oil inspection glass, and an additional quick fit filter trolley connection with an oil drain cock.
ProGlove appoints industry veteran Charles Jackson to lead North America market expansion
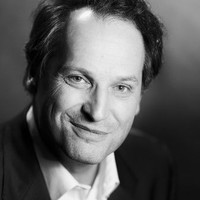
The firm will triple the size of its Chicago office in response to strong market demand, as it eyes continued double-digit annual growth in the North American market ProGlove has appointed Charles Jackson to the role Head of North America to execute on the company’s growth strategy in the North American market. Jackson was selected to run the North American market due to his deep sector expertise and proven track record in driving strategic market development. In his new role, he will lead the charge in expanding ProGlove’s North American footprint, with a focus on commercializing ProGlove’s data capabilities and a roadmap to drive customer productivity, safety and health use cases. Jackson, who has relocated from Atlanta to Chicago to take up the role, has previously held various leadership roles, and successfully established footholds in the US market and the broader Americas region for organizations. He was most recently at Pricer Inc. where he grew the business’s sales from $3 million to over $100 million annually, serving retail, manufacturing, and logistics with scalable high-speed wireless displays. He also specializes in complex sales that integrate cutting-edge hardware, cloud-based management SaaS, and scaled deployments. The Americas, with its vast geographic size, thriving logistics and supply chain ripe for modernization, offers significant growth potential for industrial wearables. According to a recent survey by ProGlove, 46% of US warehouse and logistics executives plan to invest in industrial wearables in the next five years, compared to 40% in the rest of the world. ProGlove is well-positioned to capitalize on this momentum, having already established partnerships with major American automakers including The Big Three, and leading industry players including Staples Inc., GAP, and DHL. Stefan Lampa, CEO of ProGlove, said: “Charles has demonstrated exceptional leadership throughout his career and an outstanding ability to drive significant growth. With a notable track record, deep logistics and warehouse sector expertise, and extensive experience leading teams to success, Charles is well-prepared to help us expand our reach and enhance our impact in the Americas. His commitment to team building and strategic innovation aligns perfectly with our goals at ProGlove. “We are looking forward to the new perspective and energy Charles will bring to the team, as well as to our collective efforts of putting people first to provide healthier, safer, and hyper-efficient workplaces.” Charles Jackson, Head of North America at ProGlove, added: “ProGlove has single-handedly changed the face of warehousing and logistics with its technology. It has already experienced impressive growth in the Americas and has, as a company, evolved far beyond a sophisticated scan device. Today, the organization encompasses an extensive suite of hardware and software solutions, delivering critical actionable insights for businesses across sectors. “We’ve only scratched the surface of what’s possible here and with rapid industry evolution, the future will extend far beyond wearables. I’m excited to be joining ProGlove as we embark on this journey to solidify our dominance in the North American market, and to unveil more groundbreaking innovation in the year ahead.”
ORBIS hosted a 2024 Community Giving Reception
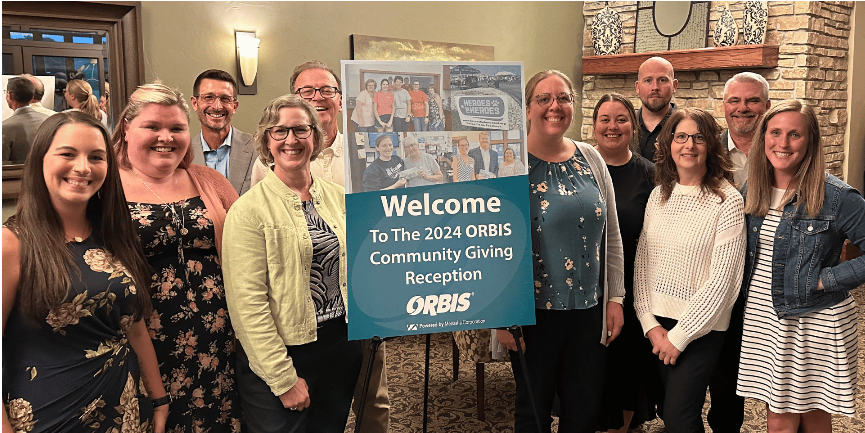
ORBIS® Corporation held its annual Community Giving Reception on August 22 to celebrate and honor the services that nonprofit organizations provide to area communities. The event brought together 80 attendees representing charitable organizations from across southeast Wisconsin to receive their charitable donations. Menasha Corporation, ORBIS’ parent company, was founded by Elisha D. Smith in 1849. He was a tremendous philanthropist in the Menasha, Wis. area. Today, the Menasha Corporation Foundation proudly carries on the tradition of Elisha Smith’s giving. Funding is made available by Menasha Corporation Foundation, the charitable entity of ORBIS’ parent company. ORBIS has community teams across the enterprise to serve the local, geographic communities in which its employees live. These teams identify and support local groups, agencies and causes in need of financial support, time or volunteers. The Community Action Team at ORBIS’ headquarters, located in Oconomowoc, has built partnerships with many nonprofits in southeast Wisconsin and celebrates these partnerships at the Community Giving Reception. “The Giving Reception shines a light on the positive impact nonprofit organizations make in the communities where our employees live and work,” said Jo Anne Behling, leader of the ORBIS Community Action Team. “In addition to the donations we make, we collaborate with our nonprofit partners to provide volunteers to help support their great work to make the world a better place for citizens and animals in need and advance the health and wellbeing of the community. This is a special year for us, as Menasha Corporation celebrates its 175th anniversary.” Strength and Service through Local Partnerships ORBIS demonstrates a strong commitment to the communities where their employees reside, regularly partnering with local entities and businesses to enhance community growth. In addition to community giving efforts, one other example of this partnership is how ORBIS achieved a significant fundraising milestone of $1 million for Children’s Wisconsin during their fourth annual Good Day for Kids golf outing. The event was held in June at the Grand Geneva golf course in Lake Geneva, Wisconsin. This year’s outing collected over $370,000 for pediatric critical care, supporting the Pediatric Simulation and Resuscitation Program. The partnership aims to improve care for children facing life-threatening conditions. To date, the event has raised $1 million for the program, offering realistic simulation-based training for healthcare professionals nationwide. “We are incredibly proud of our employees’ dedication to volunteerism and community service,” said ORBIS President Norm Kukuk. “Neighborhood involvement and improvement is a crucial part of our mission, and I’m thrilled to celebrate their collective efforts in partnering with organizations to support and uplift the communities we serve. It’s all part of honoring the spirit of service that has set us apart for the last 175 years.” 2024 Menasha Foundation fund recipients: Alzheimer’s Association of Wisconsin Angelman Syndrome Foundation Big Bob & Bob Van Wie Tournament – UW Carbone Blessings in a Backpack (Waukesha Chapter) Brewers Community Foundation Bryon Riesch Paralysis Foundation CCLS – Creative Community Living Services Downs Syndrome Association of WI Educational Foundation of Watertown HAWS (Humane Animal Welfare Society in Waukesha) Hebron House Heroes for Heroes Hope Center Humane Society of Jefferson County Imagine a Day Foundation Johnson Creek Helping Hands Food Pantry Johnson Creek Police Department Journey21 Kisses From Keegan & Friends Lake Area Free Clinic Lake Country DockHounds Lake Country Shop with Cops Lake Mills Food Pantry Lake Mills Police Department LifeStriders Madison Starlings Make-A-Wish Foundation Milwaukee Bucks Foundation National Alliance on Mental Illness – Southeastern WI Oconomowoc Festival of the Arts Oconomowoc Police Department Oconomowoc Regional Cancer Center Oconomowoc Scholarship Foundation PAVE Personal Essentials Pantry Pets Helping People Prohealthcare Foundation (Angelsgrace Hospice) Rainbow Hospice Care Shorehaven ST. Katharine Drexel Shelter Summit Police Department The Cure Starts Now – WI Chapter – Brayleighville Watertown Food Pantry Watertown Humane Society Watertown Police Department Waukesha Country Green Team Western Lakes Fire Department Women & Girls Fund of Waukesha County
AAR reports Rail Traffic for the week ending August 24, 2024
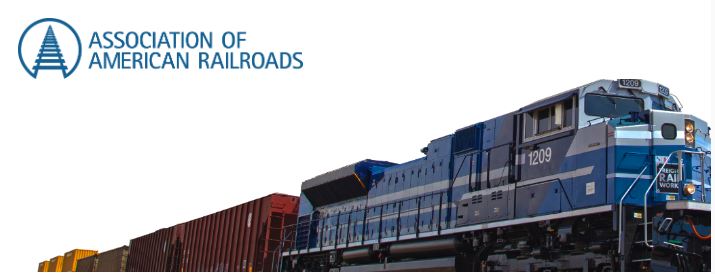
The Association of American Railroads (AAR) has reported U.S. rail traffic for the week ending August 24, 2024. This week’s total U.S. weekly rail traffic was 516,807 carloads and intermodal units, up 9.5 percent compared with the same week last year. Total carloads for the week ending August 24 were 228,858 carloads, up 1.2 percent compared with the same week in 2023, while U.S. weekly intermodal volume was 287,949 containers and trailers, up 17.1 percent compared to 2023. Seven of the ten carload commodity groups posted an increase compared with the same week in 2023. They included grain, up 5,519 carloads, to 18,914; petroleum and petroleum products, up 951 carloads, to 10,867; and miscellaneous carloads, up 602 carloads, to 9,360. Commodity groups that posted decreases compared with the same week in 2023 were coal, down 5,785 carloads, to 62,543; nonmetallic minerals, down 329 carloads, to 32,891; and metallic ores and metals, down 212 carloads, to 21,812. For the first 34 weeks of 2024, U.S. railroads reported a cumulative volume of 7,324,543 carloads, down 3.7 percent from last year, and 8,811,085 intermodal units, up 9.1 percent from last year. Total combined U.S. traffic for the first 34 weeks of 2024 was 16,135,628 carloads and intermodal units, an increase of 2.9 percent compared to last year. North American rail volume for the week ending August 24, 2024, on nine reporting U.S., Canadian, and Mexican railroads totaled 310,429 carloads, down 4.5 percent compared with the same week last year, and 350,204 intermodal units, up 7.1 percent compared with last year. Total combined weekly rail traffic in North America was 660,633 carloads and intermodal units, up 1.3 percent. North American rail volume for the first 34 weeks of 2024 was 22,504,112 carloads and intermodal units, up 2.3 percent compared with 2023. Canadian railroads reported 65,550 carloads for the week, down 22.0 percent, and 49,890 intermodal units, down 28.0 percent compared with the same week in 2023. For the first 34 weeks of 2024, Canadian railroads reported a cumulative rail traffic volume of 5,385,867 carloads, containers, and trailers, up 0.5 percent. Mexican railroads reported 16,021 carloads for the week, up 6.8 percent compared with the same week last year, and 12,365 intermodal units, up 5.7 percent. Cumulative volume on Mexican railroads for the first 34 weeks of 2024 was 982,617 carloads and intermodal containers and trailers, up 3.8 percent from the same point last year. To view the railroad traffic charts, click here.
Developing behavioral principles to support your corporate strategy
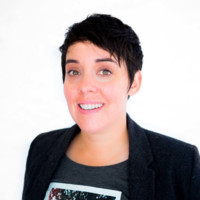
When strategy development is complete, most executives start the rollout process. But communicating the strategy isn’t activating the strategy. Activation requires establishing guidance on how to shed old mindsets and embrace new ways of thinking. This necessitates shifting from telling to illustrating. Change always begins with identifying specific behaviors that impact outcomes. Yet things like company values are typically too subjective, abstract, or generic to drive a distinct strategy. For instance, “product excellence” is a common organizational value, and no one would argue against it. But what does that mean for daily decision-making? How does that value help those teams with conflicting opinions find common ground? This is why behavioral principles are needed. In this example, translating “product excellence” into a behavioral principle would be, “We won’t release a product until we would use it ourselves.” When facing multiple courses of action, this provides teams with a clear edict. Rather than having various interpretations of what product excellence means – which can fuel relentless internal debate and conflict – the behavioral principle becomes the decision-making tool. Your behavioral principles should be designed in a way that makes them: a) embody your unique orientation and position, b) shine a clear light on how employees should make decisions, and c) be free of buzzwords. There are two parts to writing a behavioral principle. First, specify the what, and second, explain the how. With one of our clients, we began by asking, “What behaviors and mindsets reinforce and express your unique orientation and brand position?” and crafted the following four behavioral principles: 1. We create experiences that connect emotionally with customers, by knowing who they are, caring, and genuinely engaging. 2. We develop helpful, practical, and beneficial solutions to real-world problems by understanding customers’ real-life challenges. 3. We positively impact the customer experience through every conversation, every interaction, every point of contact, every message, and every piece of content. 4. We focus on making things easier for customers by helping simplify decisions and removing complexity. Depending on your circumstances, you may benefit from developing additional principles but do not exceed more than what would be considered practical and reasonable. Too many can create the potential for inconsistencies and contradictions. If necessary, consolidate similar principles into a single concept. The goal is to ensure the organization has a straightforward framework for making aligned decisions.
Port’s small business spending surpasses $55 Million
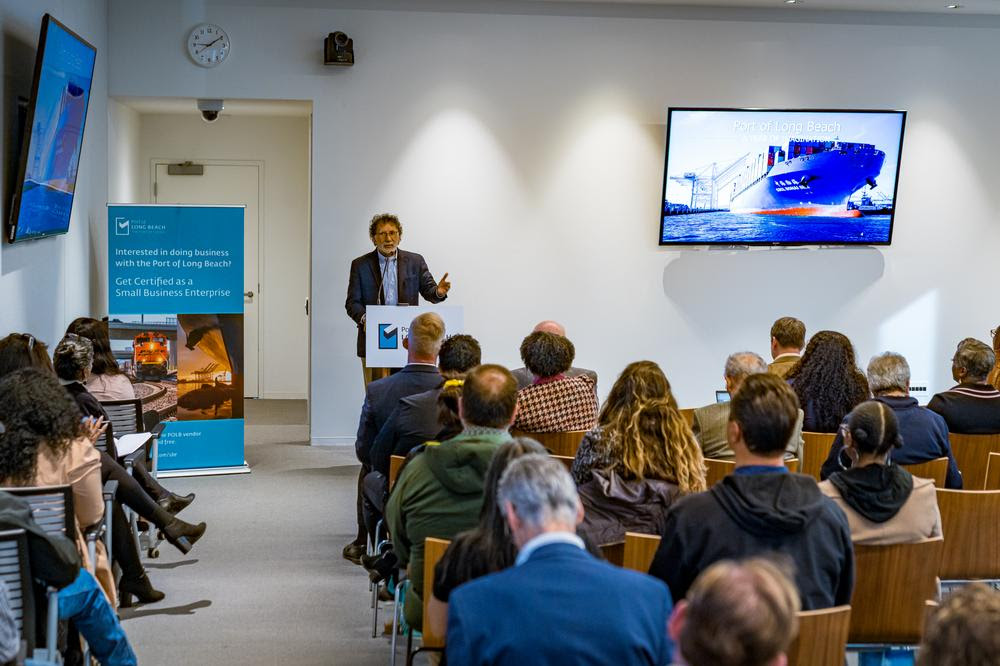
Effort to broaden opportunities to more firms exceeds goal by 15% A commitment by the Port of Long Beach to include more small businesses among its vendors and contractors continues to be extraordinarily successful, broadening access to port-related construction and professional services contracts. Last fiscal year, almost 42% of Port funds spent on eligible contracts through the Port’s Small Business Enterprise Program went to purchase needed services and materials from companies defined as “small business enterprises” and “very small business enterprises.” The 41.8% participation by small and very small businesses in contracting in fiscal year 2023 is the second-highest since the program was started in 2004, behind only 48.9% in 2022. The amount of applicable spending on construction projects, consulting services, event planning, and other supplies and services, rose year-over-year from $54.2 million to $55.7 million. The goal set for small business enterprise participation at the Port, which is the Harbor Department of the City of Long Beach, is 27%, higher than many peer agencies. “The SBE program provides opportunities to a wider, more diverse range of local contractors, suppliers and other businesses, which strengthens the local economy,” said Port of Long Beach CEO Mario Cordero. “As an additional benefit, we believe this practice also increases competition for tens of millions of dollars in public contracts each year, resulting in better outcomes and even more value.” “The Port of Long Beach is a job creator for our community and beyond, but we recognize it’s not enough to merely serve as an economic engine,” said Long Beach Harbor Commission President Bonnie Lowenthal. “This program was created to ensure there’s a place for smaller companies to benefit from the economic opportunities.” The thresholds of annual receipts and number of employees for classification as a small business vary widely by industry, as determined by the U.S. Small Business Administration. The very small business eligibility is equivalent to the state of California’s microbusiness designation – businesses with $5 million or less in annual gross sales, averaged over the last three fiscal years, or manufacturers with 25 or fewer employees. Aspiring contractors for the Port apply for posted contracts on the Port’s “Planet Bids” online system, where the business owners can pre-register their companies and check back for posted bids. The Port of Long Beach is a global leader in green port initiatives and top-notch customer service, moving cargo with reliability, speed and efficiency. As the premier U.S. gateway for trans-Pacific trade, the Port handles trade valued at $200 billion annually and supports 2.6 million jobs across the United States, including 575,000 in Southern California. In 2024, industry leaders named it “The Best West Coast Seaport in North America” for the sixth consecutive year. During the next 10 years, the Port is planning $2.3 billion in capital improvements aimed at enhancing capacity, competitiveness and sustainability.
SUN Automation Groups® new SUN625 heavy duty die cutter
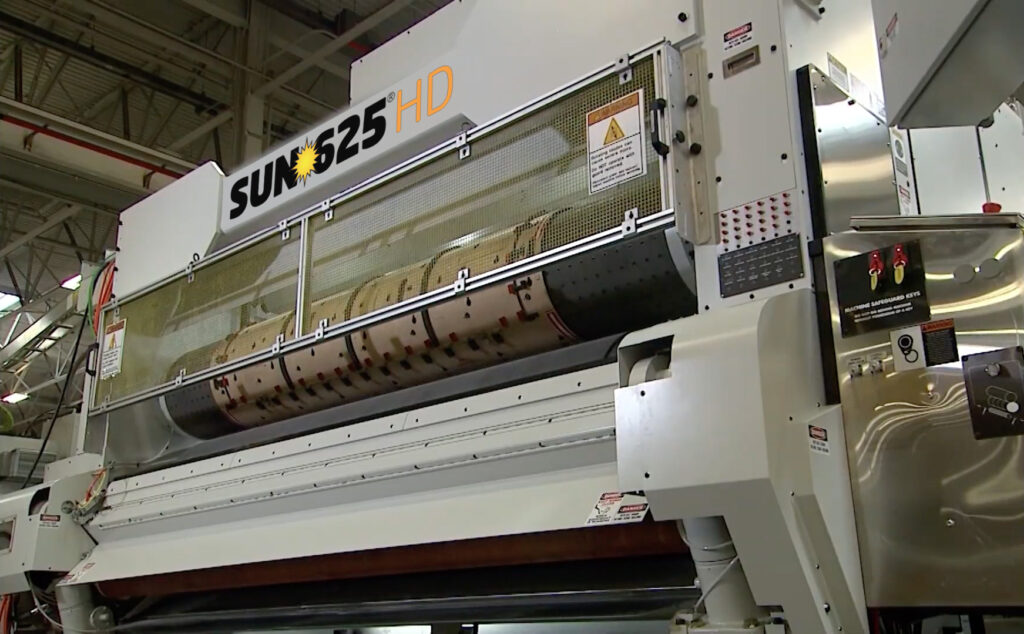
SUN Automation Group (SUN) has announced the introduction and application of the SUN625® HD Rotary Die Cutter. The first of its kind, the market-proving SUN625 RDC has been reimagined with many improvements to compete in the most demanding conditions in the Corrugated Board Rotary Die-Cutting market. The SUN625 RDC has been a stalwart in the industry for over a decade, renowned for its reliability and performance. Building on this legacy, SUN has relentlessly pursued perfection, culminating in the development of the SUN625HD. With multiple installations throughout North America, this machine is set to redefine high-speed, high-volume production. Boasting increased load capacity, larger journals, enhanced fatigue resistance, and reduced deflection under load, this iteration reveals a complete reimagining aimed at elevating die-cutting operations. “We are thrilled to introduce the SUN625 Heavy Duty Die Cutter, a significant leap forward in advancing our customers’ die-cutting operations,” says Eric Aulton, Product Manager for the SUN625. “Over the years, we have made small improvements to our design, such as improved forged journal design, register drive re-location, and structural rigidity, but the new iteration of our heavy-duty die cutter is poised to elevate our customers’ capabilities to much greater heights.” The SUN625HD offers the most robust die-cut nip assembly, unparalleled in the marketplace today. With a 300% improvement in load capacity over previous models, the new design delivers a significant increase in production efficiency. Fatigue resistance sees a monumental 500% improvement and a 60% reduction in deflection under load, ensuring precision and quality in every cut. Additionally, journal sizing has more than doubled any other offering in the 66” machine category. SUN’s patent-pending nip position and larger diameter anvil cylinder allow for the smoothest operation of Corrugated Board Die Cutting on the toughest of conditions, such as heavy-weight paper and double wall, and for full-width multi-up/out applications such as Protein and Agriculture packaging. “With these innovations to our esteemed rotary die cutter, SUN is not just meeting the needs of today’s market but also preparing for the challenges of tomorrow,” says Greg Jones, Executive Vice President at SUN. “As we embark on a new era in the corrugated industry, SUN Automation Group remains dedicated to excellence, innovation, and, above all, the success of our customers.” These new innovations and continuous efforts to refine SUN’s corrugated machinery align with SUN’s commitment to best serve its customers. SUN strives to understand the distinct needs and considerations of all operations. With the increased challenges within the die-cutting market, SUN is devoted to staying ahead of the curve in providing customers with the tools to advance their operations and meet their customer needs.
Emerson released first adjustable Jelly Jar LED Luminaire for hazardous locations
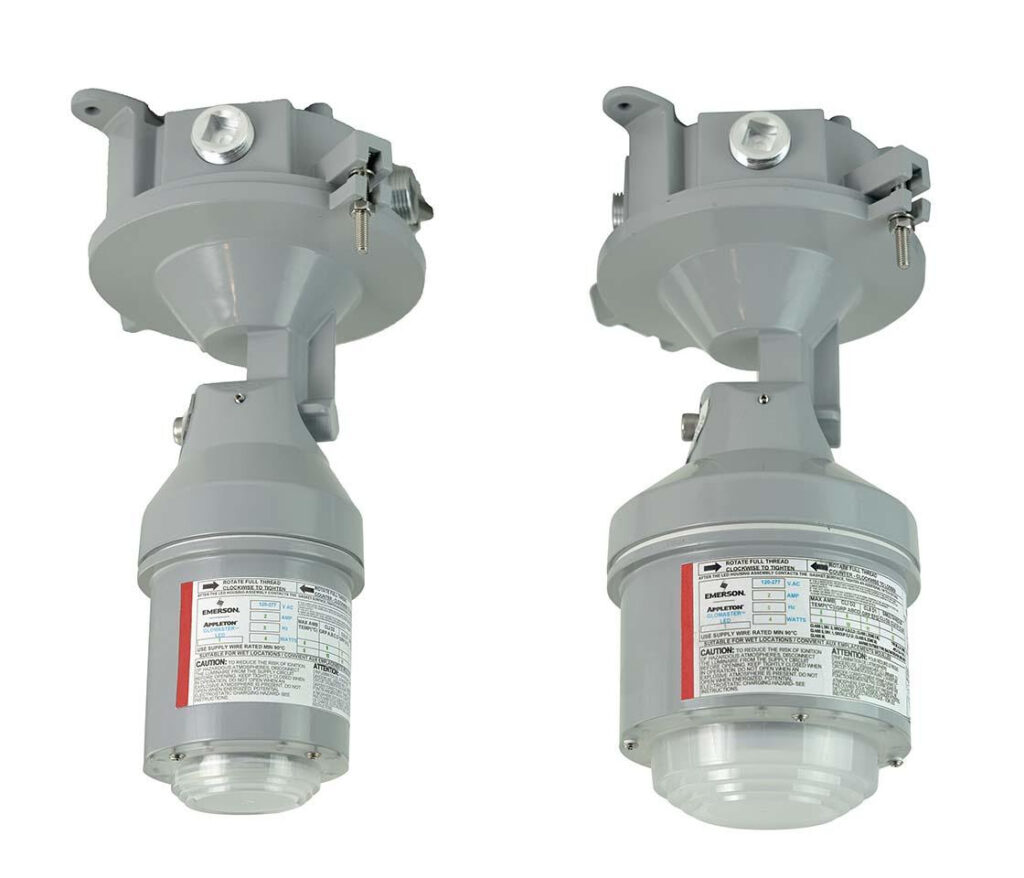
Versatile Appleton™ Glomaster™ LED fixtures streamline set-up with field selectable lumen output and CRT levels for safer, more productive work environments Positioning itself as the innovation leader in the explosion-proof lighting market, Emerson has introduced the world’s first hazardous location Jelly Jar vapor tight luminaire to feature field-selectable lumen output and Correlated Color Temperatures (CCT) settings: the Appleton Glomaster™ LED Series. Depending on the model, Appleton Glomaster LED luminaires are available with either 1000/2000 nominal lumens or 3500/5000 nominal lumens and come paired with a choice of 3000K/4000K/5000K CCT. Changing lumen output and CCT settings in the field only takes a few seconds, significantly reducing installation costs while helping users achieve optimal lighting for safety and productivity. High precision optics, including 360° uplighting, ensure adequate light levels in stairwells, docks, walkways, exits, and emergency call stations, among other close proximity areas. Alongside the flexibility of field-selectable controls, Appleton Glomaster LED luminaires offer the versatility to be pendant, wall, or ceiling mounted, or on virtually any flat surface. An adjustable knuckle lets users rotate it from 0° to 90° in precise 10° increments, regardless of mounting orientation to accommodate site requirements. Appleton Glomaster LED luminaires can be further customized by optional accessories. Colored globes are available to indicate critical areas, such as eyewash stations, together with stainless steel globe guards, and visors to reduce glare. Rugged and Reliable Appleton Glomaster LED luminaires are ruggedly built to endure prolonged exposure to extremely harsh environments, indoors or outdoors. Salt spray, high-pressure water jets, corrosive chemicals, and ambient temperatures from -40° F to 131° F are no match to the luminaire’s cast copper-free aluminum construction, silicone rubber gaskets, stainless steel hardware, polycarbonate globe, and gray epoxy powder coat paint finish. Integrated 6KV surge protection safeguards the luminaires against the most prevalent types of power quality issues found in many industrial facilities. Thanks to their industrial-grade design the luminaires boast a service life of over 100,000 hours or twice that of competitive models. Once the fixture portion is at the end of its life it is user-replaceable. Energy Efficiency Appleton Glomaster LED luminaires were introduced as part of Emerson’s mission to advance sustainability, serving as energy-efficient substitutes for CFL, HID or incandescent lights. Compared with these sources, Appleton Glomaster LED luminaires consume 75% less energy and require far less maintenance. Certified for Hazardous Locations The Appleton Glomaster LED Series is certified for NEC Class I, Div 2, and Class II locations where flammable liquids, gases or dust may be present, such as petrochemical plants, wastewater centers, and underground mining. Additionally, the Appleton Glomaster LED is IP66 waterproof and rated for NEMA 4X wet environments including marinas.
Staffing index rebounds back to 90 in August
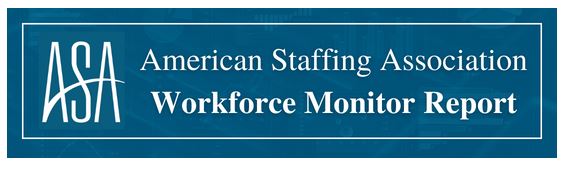
The year-to-year gap narrows, new starts down from the previous week Staffing employment increased during the week of Aug. 12-18, with the ASA Staffing Index edging up by 0.4% to return a rounded value of 90. The index declined as usual over the July Fourth holiday and has seen a slower recovery when compared with previous years. Staffing jobs were down 11.1% compared with the same week last year, narrowing the gap by around one percentage point from the previous week. Staffing companies listed no primary factor that prevented further growth. New starts, however, saw a decrease in the 33rd week of the year, down by 7.2% from the prior week. More than three in 10 staffing companies (35%) reported gains in new assignments week-to-week—below the average of 42% per week so far this year. The ASA Staffing Index’s four-week moving average increased from the prior week to hold at a rounded value of 89, and temporary and contract staffing employment for the four weeks ending Aug. 18 was 12.2% lower than the same period in 2023. “The index has finally recovered from its seasonal, midyear dip, and has returned to a steady-state value of 90 for 2024. This year, it took seven weeks for the index to recover from the July Fourth dip, compared with just three weeks in the previous two years. Cooling labor market activity and subdued labor churn likely extended this year’s recovery time for the index, but these conditions are anomalies that will begin to ease once interest rates are lowered next month as expected,” said Noah Yosif, chief economist at ASA. This week will be used in the August monthly employment situation report scheduled to be issued by the U.S. Bureau of Labor Statistics on Sept. 6. The ASA Staffing Index is reported nine days after each workweek, making it a near real-time measure of staffing employment trends. ASA Staffing Starts are the number of temporary and contract employees placed in new assignments during the reporting week. ASA research shows that staffing employment has historically been a coincident economic indicator.
Episode 515: Mujin tackles warehouse industry challenges
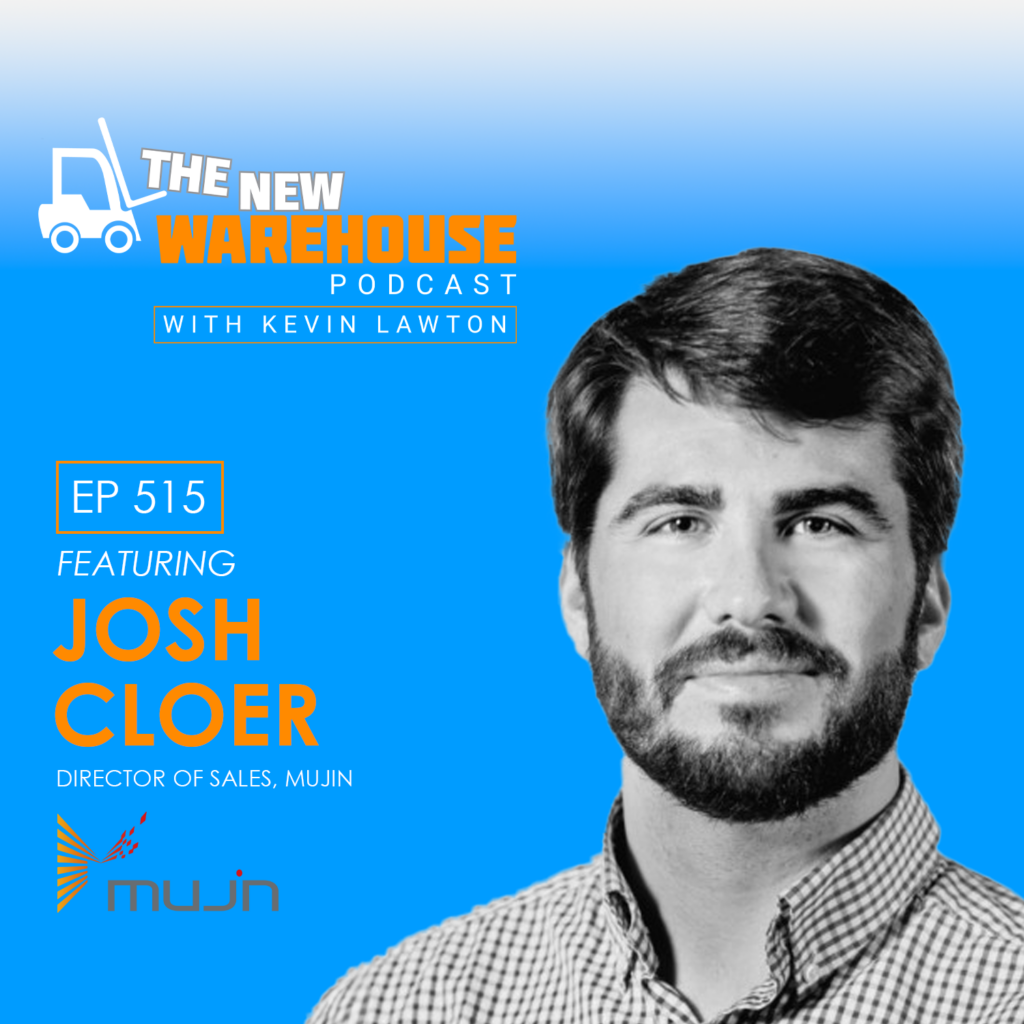
In this episode of The New Warehouse Podcast, Kevin sits down with Josh Cloer, the Director of Sales at Mujin. Mujin, a robotics technology company initially founded in Tokyo, has been at the forefront of developing cutting-edge solutions that address some of the most pressing challenges in warehouse operations. From the company’s revolutionary MujinController to their groundbreaking TruckBot, Josh delves into the advancements shaping the future of warehousing, emphasizing the importance of integrating intelligent control systems to maximize efficiency and reduce manual labor. The Mujin Controller Enables Smart Automation At the heart of Mujin’s technology is the Mujin Controller, a sophisticated brain that powers their robotic solutions. Josh highlights how this controller has transformed how the industry approaches warehouse automation. “The concept behind the Mujin controller is really that you no longer have to very directly describe how to move the things as the person that’s programming the system. It’s really a digital twin. Once the Mujin controller has an understanding of the surroundings, there are these real-time motion planning aspects. So there’s no predetermined route that the robot’s going to take to move from point A to point B.” he explains. Unlike traditional systems that require explicit programming, the controller operates through real-time motion planning, allowing robots to adapt on the fly to their environment. For robots like Mujin’s TruckBot, this means they can autonomously determine the best way to accomplish tasks such as unloading containers or mixed palletizing. The controller’s ability to “know itself and its surroundings” marks a significant leap towards fully autonomous warehouse operations. Tackling Warehouse Industry Challenges Mujin’s Truckbot has gained significant attention for its ability to automate one of the most challenging jobs in warehousing—unloading floor-loaded containers. Josh shares that customer feedback has been overwhelmingly positive, with the Truckbot effectively addressing the “back-breaking work” of case handling. By pairing the Truckbot with robotic palletizers, Mujin offers a comprehensive solution that not only unloads containers but also palletizes goods, significantly reducing the need for manual labor. “It’s solving the challenges it’s meant to solve, and we also get a lot of folks asking can you do this and that” Josh notes, emphasizing the importance of integrating robotics across the warehouse workflow to achieve maximum efficiency.” Flexible Automation for the Warehouse Industry Looking ahead, Josh discusses Mujin’s focus on making automation more accessible to small and medium-sized warehouses. Historically, only large warehouses with substantial budgets could afford advanced robotic systems. However, with the introduction of flexible and modular solutions like Mujin’s robotic case-picking system, smaller warehouses can now adopt automation without significant upfront investment. “I think you’re going to see more and more flexible automation to enable small to medium-sized warehouses to do much more and closer to lights out with the caveat that you always have maintenance,” Josh says, pointing out that this shift will enable more warehouses to move towards lights-out operations while still accommodating human oversight for maintenance and handling exceptions. Key Takeaways Mujin Controller: Powers real-time motion planning, enabling robots to adapt to their environment autonomously. Truckbot: Automates the challenging task of unloading containers and can be paired with robotic palletizers for a complete end-to-end solution. Flexible Automation: Mujin makes automation accessible to small and medium-sized warehouses, allowing them to adopt advanced robotic solutions without significant upfront costs. The New Warehouse Podcast Episode 515: Mujin Tackles Warehouse Industry Challenges
Carolina Handling supports hunger relief organizations with equipment giveaway
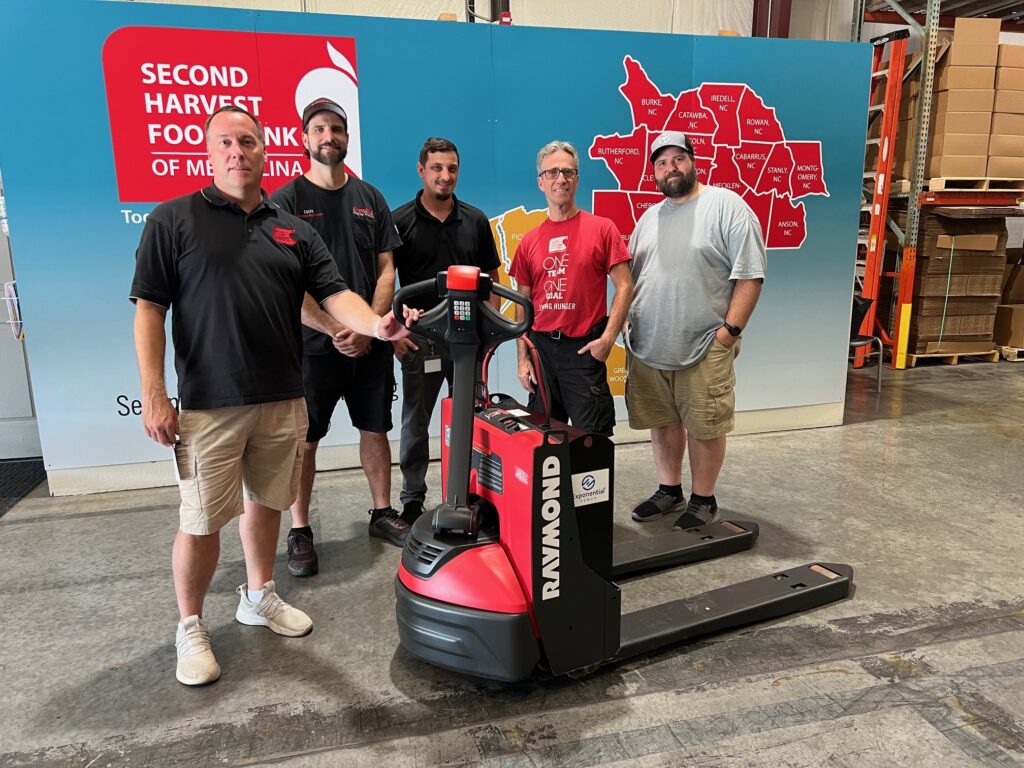
In celebration of Carolina Handling’s 58 years in business in 2024, the Charlotte, North Carolina-based intralogistics company has awarded 58 motorized pallet jacks to hunger relief organizations throughout the Carolinas, Georgia, and Alabama. Carolina Handling launched its 58 for 58 pallet jack giveaway on May 1 with a new fiscal year philanthropic focus called “Handling Hunger Together.” Equipment was awarded to qualifying organizations on a first-requested basis. “There are numerous organizations throughout our territory that receive, store, and distribute thousands of pounds of food each year to feed the hungry,” said Carolina Handling President & CEO Brent Hillabrand. “The need for reliable equipment to move pallets of donated food at food banks and pantries is even greater than we realized. We’re honored to partner with so many of the nonprofits that are addressing food insecurity in their communities.” The organizations receiving a motorized pallet jack combine to serve 11.2 million individuals each year throughout the Carolinas, Georgia, Alabama and the panhandle of Florida. Together, they distribute an average of 290 million pounds of food annually. “The safety of our volunteers will be greatly improved by the efficiency and multiple uses of this new asset,” said Allen G. Triebel, executive director of Gilmer Community Food Pantry in Ellijay, Georgia. “We will be able to maneuver large pallets inside our panel truck, and our petite pet pantry team leader will now be able to move pallets loaded with 500 lbs. of pet food safely and with ease.” Sarah Ann Bannister, director of resource development at AIM in Anderson, South Carolina, agrees. “We’re a small nonprofit, so having the resources to purchase something like new equipment is very rare,” Bannister said. “We’re so excited for the motorized pallet jack. We’re able to unload trucks and get things moved around the pantry so much easier.” According to Feeding America, more than 44 million people in the U.S. face hunger each year, including 1 in 5 children. About two billion pounds of food is rescued by food banks of the Feeding America network each year, with more than 49 million people turning to these charitable organizations in 2023 to help feed their families. “Fighting food insecurity is a challenge, and since the pandemic that challenge has taken on a new look,” said Donal Dickens, regional branch coordinator at Second Harvest Food Bank in Williamston, South Carolina. “One constant throughout it all is the need for resources to put food in our communities. Any donation of time, food, money or equipment is extremely welcomed and goes a long way.” The following organizations were awarded a Raymond motorized pallet jack in Carolina Handling’s 58 for 58 giveaway: ACTS, Aiken, SC AIM, Anderson, SC Anderson Emergency Kitchen, Anderson, SC Another Chance of Atlanta, Inc., Atlanta, GA Appalachian Ministries of The Carolinas, Pelzer, SC Backpack Buddies of Metro Atlanta, Dunwoody, GA Bags of Hope, Cornelius, NC Blessings Working Together, Douglasville, GA Bountiful Blessings Food Ministry, Jacksonville, NC Bountiful Blessings Food Pantry, Gastonia, NC Bremen Food & Clothing Bank, Inc., Breman, GA Calvary Community Care, Navassa, NC Church Community Services of Scotland County, Laurinburg, NC City Bridges, Inc., Fairburn, GA Community Food Bank of Central Alabama, Birmingham, AL Community Ministry of North Augusta, North Augusta, SC Decision Point Ministries, Atlanta, GA Favor House, Atlanta, GA Feeding & Helping Georgians, Atlanta, GA Feeding GA Families Inc., Atlanta, GA Food Bank of North Alabama, Huntsville, AL Food2Life – Rescue Food Foundation, Decatur, GA Gillsville Baptist Church GEM Missions Program, Gillsville, GA Gilmer Community Food Pantry, Ellijay, GA Gleaning House Food Pantry, Pickens, SC Good News Buenas Nuevas International Ministries, Pine Level, NC Ignite Resource Center, College Park, GA Juniper Level Missionary Baptist Church, Raleigh, NC Klonnie Lewis Food Pantry, Gordon, GA Loaves & Fishes Greenville, SC Love In Action International Ministries, Dothan, AL Making A Way Housing, Inc., Atlanta, GA Martha’s Mission Cupboard, Morehead City, NC Middle Georgia Community Food Bank, Macon, GA Midwest Food Bank – Georgia, Peachtree City, GA Miracle Hill Ministries, Greenville, SC Ms. Linda’s Legacy, Inc., Lithonia, GA Nicole’s House of Hope, Atlanta, GA Northeast Georgia Food Bank, Athens, GA Open Door Food Bank, Jacksonville, NC Our Daily Bread Christian Food Ministry, Inc., Rockingham, NC Providence Ministries Inc., Dalton, GA Rainbow Pantry, Royston, GA Recovery Ventures, Rutherfordton, NC Second Harvest Food Bank, Spartanburg, SC Second Harvest Food Bank of Metrolina, Charlotte, NC Second Harvest Food Bank of Metrolina, Williamston, SC Shiloh McDonough Community Outreach, McDonough, GA Ship Outreach and Community Center, Raleigh, NC The Clay House Inc., Riverdale, GA The LOT Project, Inc., Anderson, SC The Salvation Army, Raleigh, NC The Salvation Army of Greenville, Oconee and Pickens, Greenville, SC The Storehouse Pickens County, Easley, SC The Villages at Carver Family YMCA, Atlanta, GA There’s Hope for the Hungry, Cumming, GA United Christian Ministries, Easley, SC United Food Force Inc., McDonough, GA Urban Recipe, Atlanta, GA Vass Community Food Pantry, Vass, NC Wade Walker Park Family YMCA, Stone Mountain, GA West Alabama Food Bank, Tuscaloosa, AL
Charting a sustainable path: How innovations in the material world are shaping packaging’s future
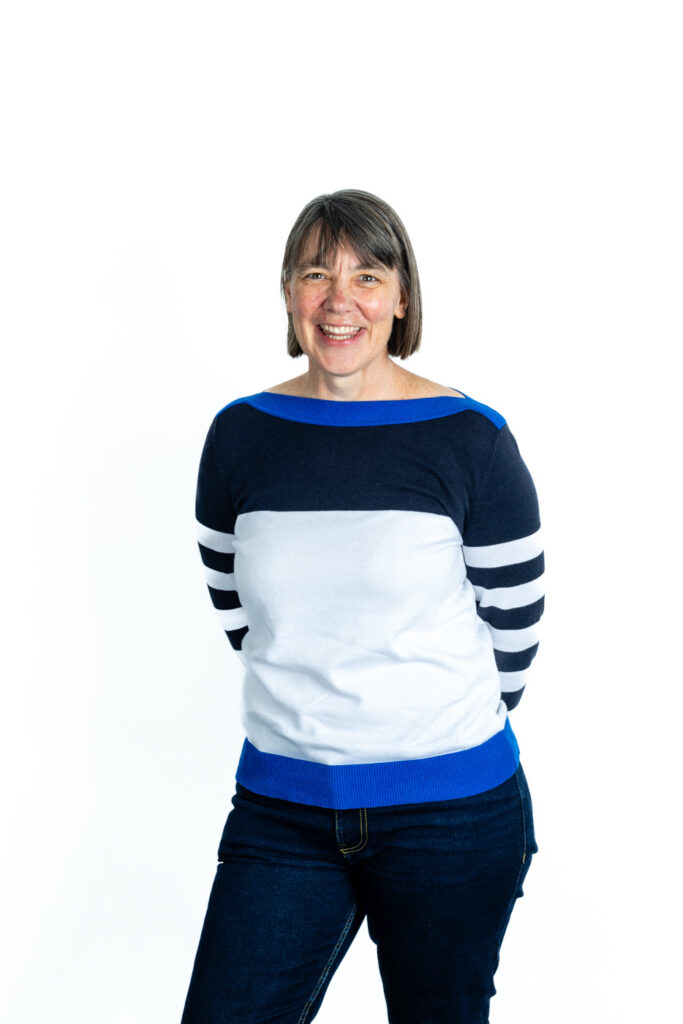
Jude Allan, Chair of IOM3 Packaging Society and interim Managing Director of OPRL, discusses how the evolving landscape of material science fosters a new era of sustainable packaging. The packaging industry is at a critical juncture, driven by significant strides in material science and an urgent need for sustainable solutions. With the impending implementation of extended producer responsibility (EPR) in April 2027, the industry’s attention is laser-focused on ensuring all packaging is recyclable and accurately labeled. This pivotal shift underscores the vital role of material science in crafting innovative solutions that meet functional needs while reducing environmental impact. Material science is at the vanguard of this revolution, propelling the exploration of alternative materials that retain the protective qualities of traditional options with significantly reduced environmental harm. Pioneering materials are now engineered to be lightweight, durable, and sustainable, addressing the critical issue of waste generated by conventional packaging. Creating biodegradable and compostable materials that decompose naturally without leaving detrimental residues is a testament to the transformative potential of material science in revolutionizing the packaging sector. At the core of this transformation is Jude Allan, a key figure leading the industry through this period of change. In her dual roles as Chair of the IOM3 Packaging Society and interim Managing Director of OPRL, Allan is not just playing a role but a crucial one in shaping the sector’s response to these changes. The Future of Labelling According to Allan, the future of labeling is upon us, marking a pivotal moment for businesses as they take full responsibility for their packaging lifecycle. This transition aims to boost recycling rates and increase the use of recyclable materials. At the highly anticipated London Packaging Week, a key event in the industry, on Thursday, September 12, from 10:45 AM to 11:15 AM, Allan will present a compelling session titled “The Future of Labelling: Be Informed and Be Responsible.” This session will delve into the impact of new legislation and mandatory labeling on recycling awareness, offering valuable insights into how businesses can navigate these regulatory changes and harness innovative labeling solutions to engage consumers effectively. According to Allan, companies can educate supply chains, enhance environmental responsibility, and drive a more sustainable future by leveraging data and adopting advanced labeling strategies. “I would like people to think about the fact that we are just about to enter the implementation phase of packaging extended producer responsibility,” she told London Packaging Week. “Assuming that the legislation goes through, then mandatory labeling is coming our way very quickly. The deadline for everything is only two-and-a-half years away because it is April 2027, and there’s a lot to be done to get to that point. “So, the first thing I would like people to take away is that even if you hadn’t realized that you were liable to put mandatory labeling on your packaging, you would be, so it’s time to get ready. It’s time to be, ‘Oh, OK, we will need to do that. We need to include it.’ Therefore, we need to think about what our packaging is. Is it recyclable? Just be ready to make that move. “The second thing is that we’ve all been aware of the legislation coming and extended producer responsibility happening. People have been engaged with it, depending on what’s been going on in their agenda and how it affects their business, but that’s not the only thing happening. The other thing I want to discuss and ensure people take away is that there are many interesting challenges around the future of labeling itself from a technological perspective. “That’s the two halves of what I want to talk about: the mandatory actions we need to take and the exciting possibilities for the future. How can we use technology to our advantage? What will help to improve communication with consumers in the future? We want a simple message so people know exactly what to do with stuff, but some consumers are already more interested in more details. How do we do that? There’s dynamic labelling and QR codes. Even the humble barcode, which has been around for so long, will change. I almost feel oddly nostalgic about that, but it’s quite an interesting change in how we interact with our shopping and learn more about the products we buy. “A whole lot is happening. Some of it is stuff we need to do, and some we want to do because it’s interesting, exciting, and will make a difference for our customers.” Embracing a Materials-Agnostic Philosophy Allan champions a materials-agnostic philosophy, emphasising that the value of packaging lies not in competing materials but in selecting the right one for each specific application. Her vision reflects a broader shift towards collaboration over competition, driven by a collective goal to enhance functionality and environmental responsibility. This approach underscores the importance of using materials that protect products, facilitate recycling, and support sustainability. Allan’s perspective highlights a critical evolution in packaging—moving from a mindset of material superiority to one focused on the effective use and reclamation of materials. By fostering understanding and confidence in recycling practices, Allan advocates for a more nuanced and responsible approach to material selection, ensuring that packaging contributes positively to consumer experience and environmental stewardship. “It’s always been about the right material, in the right format, at the right time,” she added. “If you get those things right, there shouldn’t be competitiveness between materials; each tries to see the other fall down. That used to happen, but I don’t see it much anymore, and I’m very happy to see that change. “A lot of the work around legislation has helped. If we all work together rather than protecting our territory, we will make a better future for everybody. Collaboration has been a really important part of that. I wear both hats – the OPRL hat and the IOM3 Packaging Group hat. Both of those are about being materials agnostic. It doesn’t matter what the material is if it is the best for packaging that product to protect it
Safety 2024 attendance in Denver soars above previous record
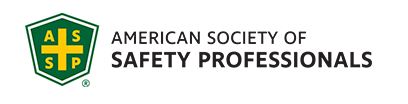
The signature event of the American Society of Safety Professionals (ASSP) attracted 6,758 workplace safety and health professionals this month to set a new attendance record for the global event. An additional 217 people joined a livestream session while 4,360 exhibitor representatives populated the expo hall, ultimately involving more than 11,000 people at the sold-out Safety 2024 Professional Development Conference and Exposition in Denver. “We saw an overwhelming desire from safety professionals to network with colleagues and stay current on best practices, industry trends and the latest product innovations,” said ASSP President Pam Walaski, CSP, FASSP. “The turnout was beyond our wildest dreams. Safety 2024 was an incredible success.” The registered attendance at the Colorado Convention Center from Aug. 7-9 far surpassed ASSP’s previous record of 5,937 attendees from Safety 2023 in San Antonio. It is one of America’s largest annual conferences for the advancement of workplace safety and health that began in Chicago in 1962. Boosting Safety 2024’s popularity was a dynamic expo with more than 650 vendor booths that covered nearly 120,000 square feet. The extensive product showcase was a key element of the overall experience, incorporating new and expanded elements such as tech talks, flash sessions and a career advancement center. “Our expo is so engaging that we get some safety and health professionals coming only for that,” Walaski said. Safety 2024 welcomed more than 3,500 first-time attendees, making up more than half of the total attendance. About one-third of the record crowd was non-members. Those who had never been an ASSP member received a free year of membership. The extraordinary results signal future growth for ASSP and the occupational safety and health profession. “We’re proud to be a global leader in providing professional development for the workplace safety and health community,” Walaski said. “Our event shares case studies and new safety approaches along with vast networking opportunities that help practitioners solve safety challenges and advance their careers.” The conference surpassed its $25,000 fundraising goal as participants donated nearly $27,000 to the ASSP Foundation, including a $10,000 match from Liberty Mutual. The ASSP Foundation promotes occupational safety and health as a career choice and works to build a sustainable talent pipeline in the profession that will help make all industries safer worldwide. Looking ahead to next year, ASSP’s Safety 2025 will take place July 22-24 in Orlando at the Orange County Convention Center, the second-largest convention facility in the nation. Orlando is known for its sunny weather and world-famous theme parks. The city is also home to The Orlando Eye, a stunning 400-foot Ferris wheel at Icon Park that ranks among the 10 largest in the world. The attraction is only 1 mile from the convention center.
Bobcat announces winners at North Dakota professional and local golf
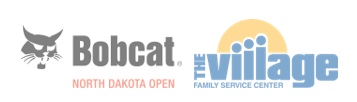
Proceeds benefit Fargo-area community with more than $1.291 million raised since 1984 The 60th annual Bobcat North Dakota Open again brought exciting professional and amateur golf to the Fargo Country Club, August 23-25, while also supporting The Village Family Service Center. Brady Calkins of La Quinta, Calif., won the tournament. Calkins has played in this tournament several times; this was his first Bobcat North Dakota Open win. Coming in second place, behind Calkins, was Caleb Vanarragon of Blaine, Minn. Will Grevios of Sioux Falls, S.D., came in third behind Vanarragon. Jacob Skarperud of Fargo, N.D., topped the amateur division of the tournament. Ian Simonich was the amateur division runner-up, coming in a close second to Skarperud following a playoff to settle a tie. Skarperud made a birdie on hole #13 for the win. Skarperud was also the 2020 Bobcat North Dakota Open Amateur Champion. This year’s event marked the 40th year that Bobcat Company has served as the lead corporate sponsor for the tournament, which has resulted in raising more than $1.291 million in support of The Village’s community outreach services. “Bobcat Company is proud to again support this annual tournament, which has become a favorite tradition in the Fargo community,” said Mike Ballweber, president of Doosan Bobcat North America. “For decades, the Bobcat North Dakota Open has been a great way to showcase pro and amateur golf talent, while also giving back to our community by helping The Village build brighter futures for area kids and families who need our support.” A large field of amateur golfers were paired with pros during Friday’s and Saturday’s rounds. The tournament’s events also included a kick-off celebration, barbeque and a Big Brothers Big Sisters program golf clinic for children who each received a set of junior golf clubs courtesy of the North Dakota Golf Association. The three-day, pro-am golf tournament concluded Sunday with an awards presentation during which Bobcat representatives presented a check to representatives of The Village representing Bobcat’s total donations while serving as the annual tournament’s title sponsor. “We are incredibly grateful for the support of Bobcat Company and other generous sponsors,” said Kelly Olson, president and CEO of The Village Family Service Center. “The generosity of our sponsors and the community is truly making a difference in the lives of the people we serve, and we look forward to continuing this important partnership in the years to come.” In addition to Bobcat Company serving as the tournament’s title sponsor, other major sponsors this year included Bell Bank, Bremer Bank, D-S Beverages, J & M Printing, Lapham-Hickey Steel Corp and Swanston Equipment Corporation. The 60th annual Bobcat North Dakota Open is a part of the Dakotas Tour, a 20-event, professional golf tour played in Minnesota, Iowa, North Dakota and South Dakota.
Omnicon achieves fifth consecutive CSIA Certification
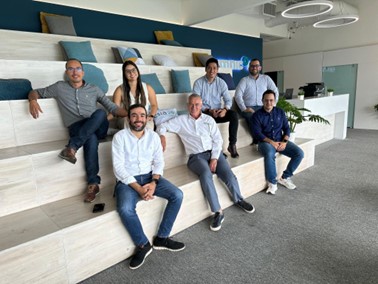
Omnicon has announced its successful recertification by the Control System Integrators Association (CSIA). This achievement marks the fifth consecutive time Omnicon has met the high standards required for CSIA certification, underscoring the company’s commitment to providing innovative industrial automation and data integration services. “Maintaining our CSIA certification demonstrates our commitment to delivering high-quality and reliable service to our clients,” said Eduardo Acosta, CEO of Omnicon. “This recertification reflects the hard work and dedication of our entire team, ensuring our clients that we operate with integrity and professionalism.” Omnicon has been a CSIA member since 2006 and achieved its first certification in 2009. In addition to maintaining CSIA certification, Omnicon has received notable accolades; in 2021, the company was honored as the CSIA Integrator Member of the Year, recognizing its industry leadership and excellence. In 2020, CEO Eduardo Acosta received the prestigious Charlie Bergman Award, honoring individuals who have shown outstanding leadership in the control systems integration industry, mirroring the values of CSIA founder Charlie Bergman. Additionally, Omnicon has been recognized as one of Deloitte’s Best Managed Companies for the past three consecutive years. “Selecting a CSIA Certified system integrator is a strategic choice to work with a fully vetted professionally managed control system integration business,” says Jose Rivera, CEO of CSIA. “The certification process involves a substantial investment of resources to meet the Best Practice’s stringent performance standards, demonstrating the company’s commitment to excellence. By choosing an SI that has embraced the CSIA’s Best Practices and successfully achieving Certification, you’re choosing a partner dedicated to implementing industry-leading standards in your facility.” CSIA certification involves a comprehensive audit encompassing ten key areas, including general management, human resources management, marketing, business development, sales management, financial management, project management, and cybersecurity, among others. This thorough evaluation ensures that companies adhere to the highest standards of quality and performance. “Being CSIA certified means we are recognized as a top-tier system integrator capable of working with any company and delivering quality solutions,” said Daniel Gomez, COO. “Our certification not only validates our team’s expertise but also assures our clients that we have solid processes in place to deliver consistent results.” CSIA, a global trade association, is committed to advancing the control system integration industry by focusing on the management of integration businesses. To achieve CSIA certification, a company must meet a certain number of the guidelines outlined in the CSIA Best Practices & Benchmarks manual. Maintaining certification requires successfully passing an audit every three years. “We owe our success to the dedication of our incredible team, loyal customers, and trusted partners,” said Acosta. “I extend my heartfelt gratitude to each member of our team for their contributions in helping us achieve this milestone. Their support and commitment have been instrumental in our journey.”
Episode 514: AI-Driven Workforce Optimization with INFORM
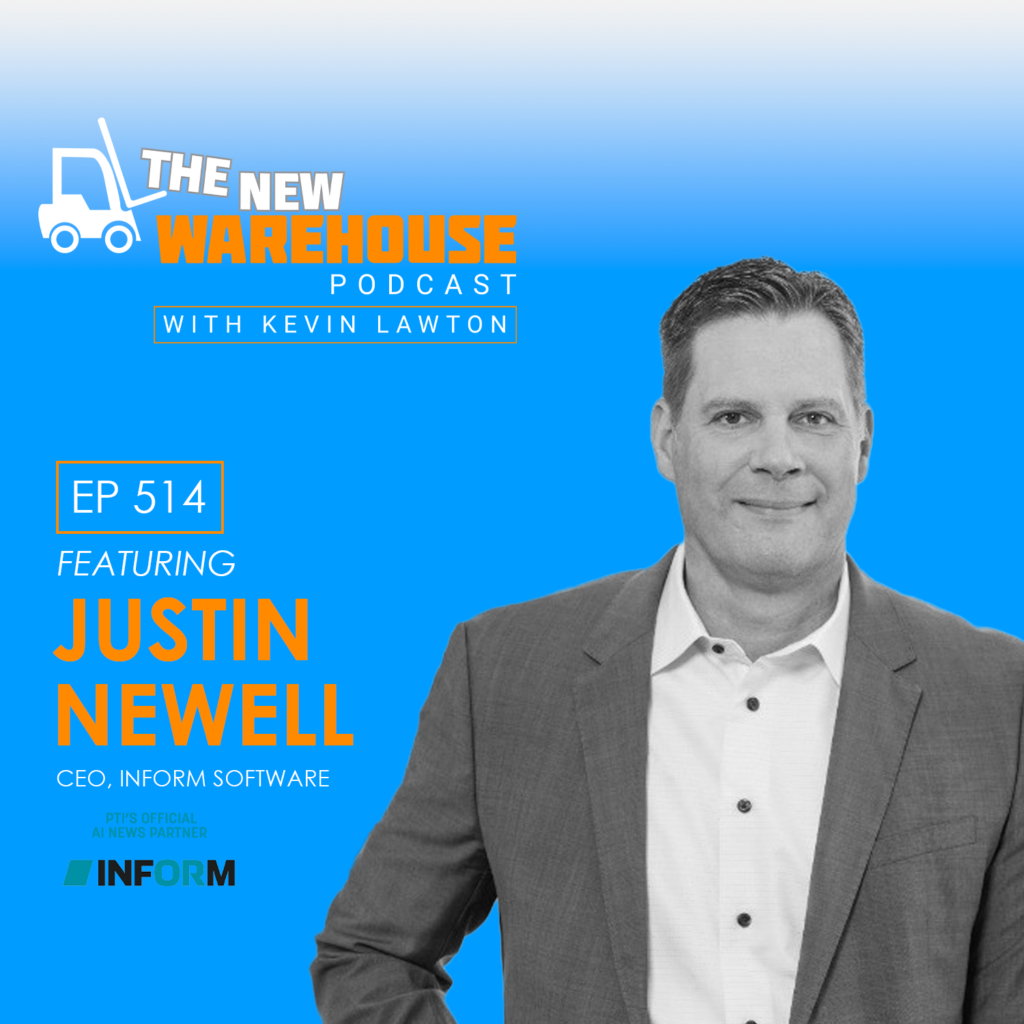
In this episode of The New Warehouse Podcast, Kevin welcomes Justin Newell, CEO of INFORM, a company with over 55 years of expertise in operations research and specializing in AI-based solutions. INFORM specializes in optimizing business operations across various industries, including logistics, aviation, and manufacturing. The conversation dives into the challenges of increased capacity demands in warehouses and how INFORM’s innovative solutions, like WorkforcePlus, are helping businesses maximize their existing workforce while navigating the complexities of today’s labor market. Addressing Labor Shortages with AI-Driven Workforce Optimization Labor shortages have become a significant hurdle in warehouse operations, impacting everything from stock put-away to inventory management. Justin Newell explains, “With the retiring population of the baby boomers and fewer people entering the workforce, labor shortages are causing major disruptions.” INFORM’s WorkforcePlus solution leverages AI to tackle these challenges by optimizing staff scheduling and real-time task allocation. This technology ensures that warehouses adapt quickly to disruptions, making the most out of their current workforce. Enhancing Operational Efficiency Through Process Mapping and AI The key to improving operational efficiency is understanding and mapping current processes. Newell shares that when engaging with customers, INFORM conducts detailed process mapping to identify inefficiencies. “It’s eye-opening for the customer when they realize how outdated their assumptions are about their operations,” he says. By integrating AI-driven solutions, INFORM helps businesses re-evaluate and optimize their workflows, resulting in significant efficiency gains. For companies that haven’t yet embraced these improvements, INFORM has seen efficiency gains of up to 40%. Embracing Technology to Maximize Workforce Utilization Looking ahead, Newell envisions a more engaged and empowered workforce through technology. “The younger generation expects technology; they want to be more involved in the process,” he notes. INFORM’s AI solutions enhance job satisfaction by automating mundane tasks and providing employees with real-time feedback and decision-making tools. This approach improves productivity and makes jobs safer and more attractive. “If you can make a job better through technology, you’re going to see a huge amount of change,” Newell concludes, pointing to a future where technology and human labor work hand in hand for optimal results. Key Takeaways on AI-Driven Workforce Optimization INFORM’s WorkforcePlus optimizes labor utilization, addressing workforce shortages through advanced scheduling and task allocation. Detailed analysis of existing workflows can reveal significant efficiency improvements, with potential gains of up to 40%. Technology is imperative to engage the modern workforce, enhancing job satisfaction and improving safety. The New Warehouse Podcast Episode 514: AI-Driven Workforce Optimization with INFORM
Orbital Stretch Wrapper secures long products that extend pallet edges
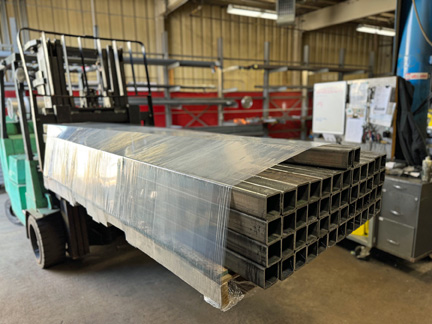
TAB Wrapper Tornado Permits Delivery Without Custom Pallets, Crates The TAB Wrapper Tornado from orbital wrapper manufacturer TAB Industries, LLC, allows long and oddly shaped metal parts and products extending beyond the pallet’s edges to be secured and safely delivered using stretch wrap alone. Eliminating the need to build custom pallets or stock uncommon pallet sizes, the patented orbital wrapping machine wraps stretch wrap 360 degrees around and under the entire length of the pallet and the load to ensure the proper amount of compression is applied at the center of gravity. Load shifting on the lift truck, in storage racks, and/or in transit is eliminated, along with the need for cumbersome crates, boxes, and banding. Proven effective for stretch wrapping rods and profiles, pipes and fittings, and a diverse range of finished machinery and fully assembled products and equipment, the TAB Wrapper Tornado is available in semi-automated and automated models with 115-inch, 100-inch, and 80-inch wrapping ring diameters as standard. Tall pallet loads reaching up to 95 inches in height or width and long pallet loads of any length may be safely wrapped into a stable, unitized load. The versatile orbital stretch wrappers are designed and manufactured at the company’s Reading, Pa. headquarters and delivered ready for operation with a warranty. A companion line of stretch wrap is also stocked in the facility and available for nearly any orbital stretch wrapping machine.
Newcastle Systems Worker Satisfaction Survey just released
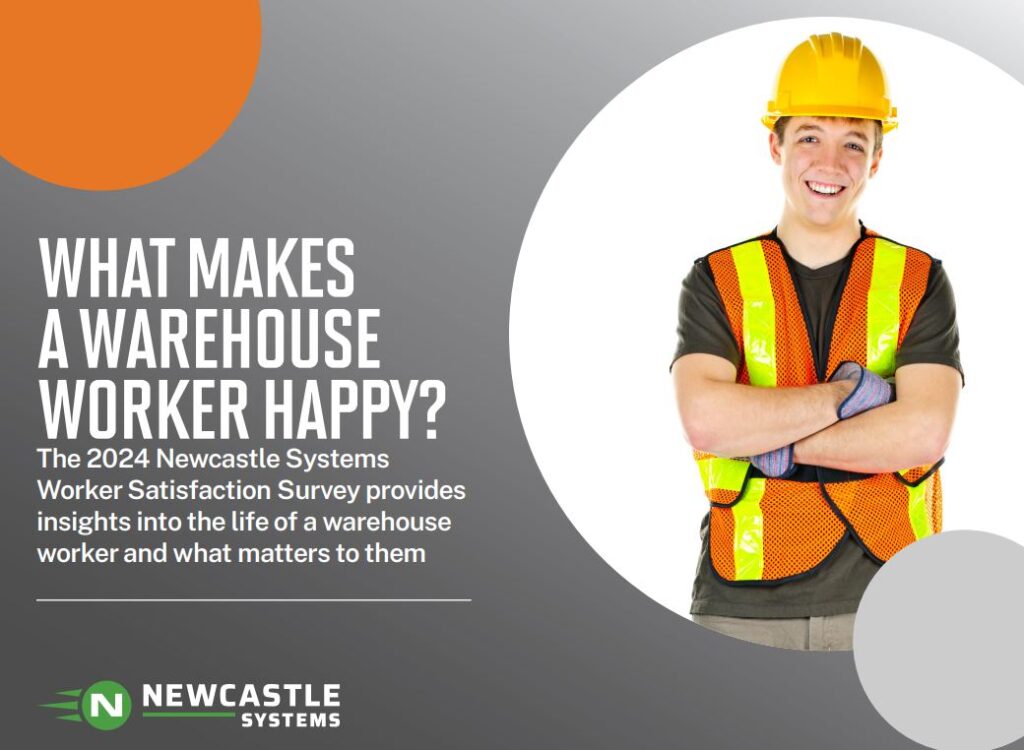
The 2024 Newcastle Systems Worker Satisfaction Survey provides a comprehensive look into warehouse workers’ daily experiences and satisfaction levels across the United States. Conducted by Newcastle Systems, a leader in ergonomic mobile-powered workstations, this first-of-its-kind survey draws insights from more than 200 warehouse workers, revealing their challenges, what makes them happy, and the steps employers can take to improve their working conditions and satisfaction. Key Findings Warehouse Worker Challenges Warehouse work is physically demanding, with many workers experiencing significant fatigue due to long hours, repetitive tasks, and fluctuating warehouse temperatures. The survey found that 22.5% of respondents identified the physicality of their job as the greatest source of fatigue, while 21% cited long workdays. Despite these challenges, the warehousing sector remains a critical part of the U.S. economy, employing approximately 1.851 million people as of late 2023. Worker Satisfaction The survey highlighted that employee satisfaction is closely tied to how valued workers feel by their employers. While 39% of respondents felt “somewhat valued,” a concerning 5% felt “not valued at all.” The number one factor contributing to job satisfaction, as reported by 33% of workers, is fair and competitive pay. This finding underscores the importance of equitable compensation and supportive working conditions in retaining a dedicated workforce, especially in the face of labor shortages and increasing eCommerce demands. Investing in the Workforce The survey revealed shared concerns across generations of warehouse workers, particularly regarding inadequate tools and outdated equipment. About 10% of respondents, translating to nearly 200,000 workers nationwide, reported lacking the tools needed to complete their jobs effectively. The top three concerns among workers were the need for better safety measures, equipment upgrades to enhance efficiency, and improvements to warehouse cooling and heating systems. Addressing these issues is critical for employers aiming to boost employee morale, productivity, and satisfaction. The Role of Technology and Ergonomics Technology and ergonomics play a crucial role in modern warehouse operations. The survey found that most respondents were moderately comfortable integrating robotics and other automated solutions into their work environment. Ergonomic tools, such as mobile-powered workstations, wearable barcode scanners, and cobots, were particularly favored by workers, with 20% reporting that these tools make their jobs more enjoyable. These findings suggest that a hybrid approach, combining manual labor with automated solutions, can optimize workflow and enhance job satisfaction. Regional Differences The survey also revealed regional differences in worker perceptions. The South had the highest number of respondents (39.6%), followed by the Midwest (28%), the West (20%), and the Northeast (12%). Interestingly, the greatest source of fatigue varied by region, with workers in the Northeast and West most affected by the physicality of the job and long hours. At the same time, those in the South and Midwest were more concerned with inadequate breaks. Maximizing ROI To maximize their employee’s return on investment (ROI), employers must improve workplace conditions, offer fair compensation, and enhance communication with workers. Proactive measures, such as updating safety protocols, providing ergonomic tools, and improving HVAC systems, can significantly enhance employee satisfaction and productivity. As warehouse workers are integral to the growing eCommerce sector, investing in their well-being is crucial for long-term success. Conclusion The 2024 Newcastle Systems Worker Satisfaction Survey offers valuable insights into the challenges and needs of warehouse workers across the U.S. By addressing the issues highlighted in the report—such as the need for better pay, improved working conditions, and the integration of ergonomic and technological solutions—employers can create a more positive and productive work environment, ultimately driving success in the evolving landscape of warehouse operations. To view the survey, click here.
Cold Storage Power Supply BSLBATT forklift lithium batteries support refrigerated applications for Crown forklifts
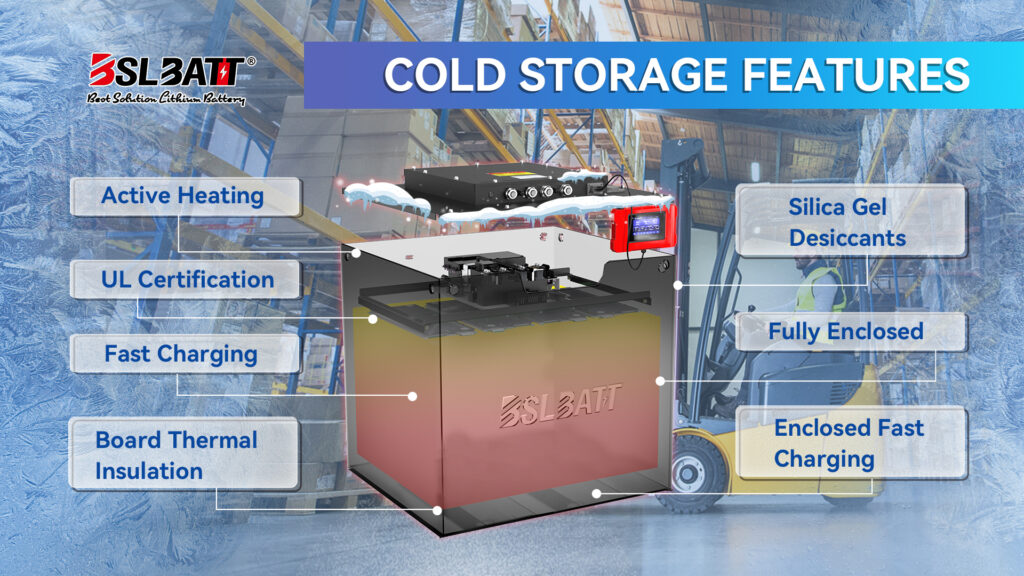
BSL New Energy Technology Co., Ltd. (Brand: BSLBATT® ), an innovative high-tech company that designs and manufactures smart lithium-ion batteries (50% more efficient than similar products on the market) for industrial forklifts used in the warehousing and distribution industries, has partnered with PF, a major European cold storage customer, to launch the largest fleet of lithium-battery-powered Crown forklift in the cold storage industry, with a deployed capacity of approximately 6.6 megawatt-hours (MWh). Lithium-battery systems eliminate time-consuming and expensive maintenance and provide longer life at extreme temperatures, especially in cold environments. As the company converts all existing and future material handling equipment to lithium batteries, the fleet will run better, longer, and consume less power. As one of the largest public cold storage companies in the world, PF has 30 facilities in Italy, France, and Spain. Many upcoming facilities are under construction. The company’s warehouses are below -30 degrees Celsius and face unique challenges that lead-acid batteries cannot solve. Specifically, lead-acid battery systems lose power and operating efficiency over a shorter cycle life, increasing operating costs and performance degradation by up to 60%. Tracy Shen, Sales Manager of the Power Division at BSL Battery – Industrial, said: “PF customers have seen immediate benefits from switching from lead-acid battery systems to lithium-ion systems. Lithium-ion systems eliminate time-consuming and expensive maintenance and maintain a longer service life at extreme temperatures, especially in cold environments. As the company strives to convert all existing and future material handling equipment to lithium-ion batteries, the fleet will operate better, longer, and consume less power.” This heightened reality is challenging for cold storage facility operators who can’t meet demand. Doing more with less is imperative; lithium-ion batteries are a proven way to optimize equipment utilization. Why do BSLBATT Lithium-Ion batteries perform so well in cold storage operations? BSL Battery—Industrial batteries were designed and tested to withstand the toughest environments. They have added features to prioritize safety and performance in the cold. Active Heating: Our batteries have an individual heater on each module to provide continuous heating at temperatures up to -40°C UL Certification: This certification proves our commitment to providing safe products and ensures performance in the most demanding conditions Board Thermal Insulation: Prevent battery energy loss during charging/discharging, and maintain a constant temperature! Silica Gel Desiccant: Silicone desiccant is added to each battery pack to prevent condensation from affecting the battery. Fully Enclosed: BSLBATT batteries achieve an IP67 rating due to their fully enclosed design. This element protects the battery from condensation, ice, and other liquids. Fast Charging: The battery can be charged faster, contributing to decreased downtime for heavy-use cold storage businesses. It can also be charged within blast freezers and refrigerated warehouses. PF customer said the company chose BSL Battery – Industrial because the company has more than ten years of experience in developing innovative lithium systems for various applications, including the power industry. It can provide local services to customers in the Netherlands, Italy, Spain, and France in Europe. In addition, PF customer executives also sought a partner that could provide more sustainable products, allowing customers to seamlessly and cost-effectively transition to lithium battery systems and plans to make 100% of fleet operations powered by lithium batteries.