Bringing dead customers back to life
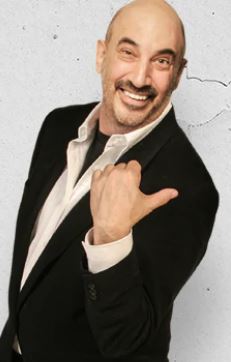
You lost a customer. You’ve probably lost lots of customers. You don’t want to think about them. It’s painful. In fact, you’re reading this and have already had a few instant thoughts about this one or that one. Makes you mad, doesn’t it? They’re dead and buried in that great customer graveyard in the sky. A graveyard full of unfulfilled promises, screwed up deliveries, missed deadlines, wrong billing, crappy service… want me to keep going? Two more thoughts: lost revenues and lost profits. More? One more thought: lost commissions. That one hurts. Especially the ones “you were counting on.” The ones you “already spent.” It makes you madder, doesn’t it? Well, I have great news. Keep thinking about them. They’re gone but not forgotten. Dead, but not buried. I challenge you to reconnect with them as soon as possible. They have money waiting for you. TRUE STORY: A newly hired sales regional manager for a Fortune 100 company noticed two file drawers marked Code 99. When she inquired about the meaning, a rep told her, “Those are the customers who hate our guts. They have sued us, left our machines on the curb, bad-mouthed us, and said they never wanted to see us again.” She emptied the drawers and divided the files among the sales team with the directive to visit each customer, meet with the decision-maker, and find out what happened. That’s all—no sales pitch. RESULT: The results were staggering. More sales per lead than any program they had run in the past five years. Many of the old (angry) people were not there anymore, making the initial conversation much less painful and the bad memories dim or lost. From there, they discovered that there were opportunities. Sales opportunities. And the customers appreciated the straightforward courage. NOTE WELL: All customers are not lost from screwups. Often, someone came in and stole them either by lower price, or just by a better salesperson. NOTE REAL WELL: I am NOT recommending you go in with price concessions. Bad precedent for a new beginning. Bring something to the table beside “low price,” and you’ll walk away with a profit. There’s a thought. Want a customer zombie approach process that will wake up the dead? Here’s the plan: Start now. It takes courage, it takes planning, it’s a grim dose of reality, but let me assure you, it works. Get out the files and make a list of EVERY ONE OF THEM. Adopt a fun approach: Have a lost and found (customer) day. Have a lost and still fond of (customer) day. Have a lost customer appreciation day. Have a we screwed up day. IDEA: Send a dart board with your company logo in the center and a few darts and ask them to “get it out of their system” and to please let you back in their office on the condition that they keep the darts in the drawer while you’re there. Fun. Uncomfortable with fun? OK, OK… Adopt a professional approach: Send a letter with a peace offering. Send a card. Whether you use a fun or professional approach, you must also do the following: The game plan: Arrange a meeting to find out why. Find out what happened as a result of your screw-up, lack of attention, or lost order. Ask for another chance with conditions that you both set and agree to (sometimes in writing). Golden Lessons: Document the “whys” and you will be amazed to find that every reason is fixable. In fact, some have already been fixed. If corrected properly, these are the most valuable resources you have for making your business better. Pay for victories:Offer ultra rewards to salespeople, ransoms and bounties. Pay double commission or some kind of bonus for a resurrected customer. The Goal: You will win sales, profits, and a new understanding of how to improve your business from a customer’s perspective the only one that matters. The Bonus: Good will lost, and recovered. If you win the customer back, you will have re-created a story, eliminated the bad one, and replaced it with new-found testimony. Huge value. You know the old saying, “Every obstacle presents an opportunity.” Some salespeople may see this idea as “uncomfortable” or too much of an obstacle. But I promise if you can get beyond the reluctance or skepticism, you will win. You get to steal back the business and learn the “why you lost them” lessons. You get answers and sales. You get a win, while the competition gets a loss. You regain lost pride while they get a shot in the wallet. You get a commission while they get jack squat. What could be better? About the Author: Jeffrey Gitomer is the author of twelve best-selling books, including The Sales Bible, The Little Red Book of Selling, and The Little Gold Book of Yes! Attitude. His real-world ideas and content are also available as online courses at www.GitomerLearningAcademy.com. For information about training and seminars, visit www.Gitomer.com, email Jeffrey at salesman@gitomer.com, or call him at 704 333-1112.
NORD Powers Automation with modular solutions for over 100 diverse industries
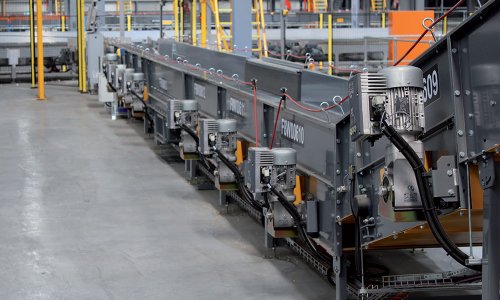
NORD offers a wide selection of gear units, electric motors, and drive electronics that work in unison to deliver efficient, reliable automation. NORD DRIVESYSTEMS delivers reliable, high efficiency automation solutions to a wide range of industries. Their modular product portfolio of over 20,000,000 standard components includes gear units, electric motors, and electronic control products that offer versatility and flexibility for easy adaptation to application requirements. NORD supports the post and parcel industry with high-efficiency drive solutions optimized for reliable, low-maintenance operation. Standardized LogiDrive complete drive solutions are often selected for these applications as they provide a gear unit, motor, and variable frequency drive that can be configured to meet precise specifications. Their modular design incorporates Plug-and-Play technology for easy installation and enables all components of the drive to be individually serviced, minimizing maintenance, downtime, and repair costs. Sorters, belt conveyors, curved conveyors, and lifters employ two-stage NORDBLOC.1 helical bevel gear units paired with IE4 or IE5+ permanent magnet synchronous motors and NORDAC LINK variable frequency drives, while merger applications use UNICASE helical inline gear units to accommodate their particularly high dynamics and speeds. Both compact solutions provide high-efficiency, fast ramp times, smooth automation, long service life, and quiet operation. Baggage handling systems often incorporate hundreds of gear motors that work together to efficiently move baggage from one end of the airport to the other. They must be precise, reliable, and customizable with sophisticated electronic controls to ensure the highest level of performance and energy efficiency. With high quality drive systems that combine gear motors with integrated distributed controls, NORD DRIVESYSTEMS provides both a reliable and cost-effective solution that meets the special requirements of the industry. These solutions typically consist of UNICASE helical bevel gear units or two-stage NORDBLOC.1 helical bevel gear units paired with high efficiency IE3 or IE5+ motors and NORDAC FLEX variable frequency drives. The decentralized modular design is beneficial for maintenance while M12 quick disconnect receptables simplify the installation process and cut down on complicated wiring systems. Each NORD motor frame size has several available brake sizes, a multitude of options, and integrated dynamic brake control for rapid starting and stopping of the conveyors as baggage travels through the system. Additionally, their brake motors with distributed control AC drives have the brake rectifier integrated directly into the drive, eliminating the need for standard brake rectifiers and associated brake control relay circuits. When it comes to the packaging industry, continuous running of automation systems is a high priority. All technology and drives must be well-balanced and have a high level of stability to meet production goals. For bottling plants that require multiple systems for preparation, filling, and packaging, NORD offers UNICASE worm gear units, UNIVERSAL SI worm gear units, and UNIVERSAL SMI worm gear units paired with NORDAC PRO SK 500P variable frequency drives. These centralized VFDs enable precise adjustment of speeds to avoid faults from bottles falling over during conveyance. They also deliver the high speeds and precision control required during the sealing process. An integrated multi-protocol Ethernet interface allows for remote maintenance tools, control, and online inspection of the entire system to check for faults and evaluate data from all drives in the plant. The food and beverage industry has a wide range of machines that perform specific automated tasks such as food separators, belt coating systems, and pipes that pump liquid pastes into mixers. NORD delivers robust drive technology for these specialized systems and adheres to strict hygiene standards with options including food-grade lubrication, stainless steel shafts, IP69K-rated washdown protection, and more. Their UNICASE helical bevel gear motors deliver efficient, reliable automation for separators and belt systems with durable, wear-free gear teeth, high axial and radial load capacities, and low maintenance for reduced downtime. NORDBLOC.1 helical inline gear units are an ideal solution when it comes to pump applications thanks to their large bearings that provide exceptional strength, durability, and minimal wear from radial and axial forces. For food and beverage applications that require electronic controls, NORD offers NORDAC ON/ON+ variable frequency drives with integrated multi-protocol Ethernet interface for easy integration into modern automation systems. Their housings are made from robust aluminum alloy with an IP protection class up to IP66, making it suitable for harsh environmental conditions. These drives can additionally be operated in temperature ranges from -22°F (-30°C) to +104°F (+40°C), making them ideal for both deep-freeze and high-heat applications. With their widespread industry knowledge, application expertise, and global sales and technical support, NORD DRIVESYSTEMS delivers complete drive solutions from a single source configured to meet the most specialized of automation system needs.
Port of Long Beach sees busiest July on record
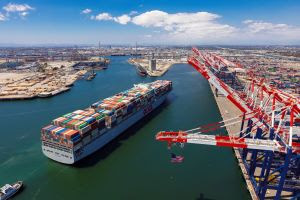
Cargo surge driven by back-to-school, potential tariff increases Surging cargo volumes lifted the Port of Long Beach to its most active July on record – and the third-busiest month in its 113-year history – as retailers stocked up on goods headed into the peak shipping season. Dockworkers and terminal operators moved 882,376 twenty-foot equivalent units in July, up 52.6% from the same month last year and surpassing the previous record set in July 2022 by 12.4%. Imports soared 60.5% to 435,081 TEUs, exports grew 16.3% to 104,834 TEUs, and empty containers moved through the Port jumped 57.8% to 342,462 TEUs. “We’re in a strong position heading into the peak shipping season as consumers purchase back-to-school supplies and shippers move goods ahead of potential tariff increases,” said Port of Long Beach CEO Mario Cordero. “We have plenty of capacity across our terminals and cargo continues to move efficiently and sustainably at this premier gateway for trans-Pacific trade.” “Our waterfront workforce continues to move trade through the Port at a record-setting pace,” said Long Beach Harbor Commission President Bonnie Lowenthal. “Our strong partnerships with labor and industry continue to help us meet the evolving needs of our customers.” The Port has moved 5,174,002 TEUs during the first seven months of 2024, up 20% from the same period last year.
U.S. Rail Traffic for the Week Ending August 10, 2024
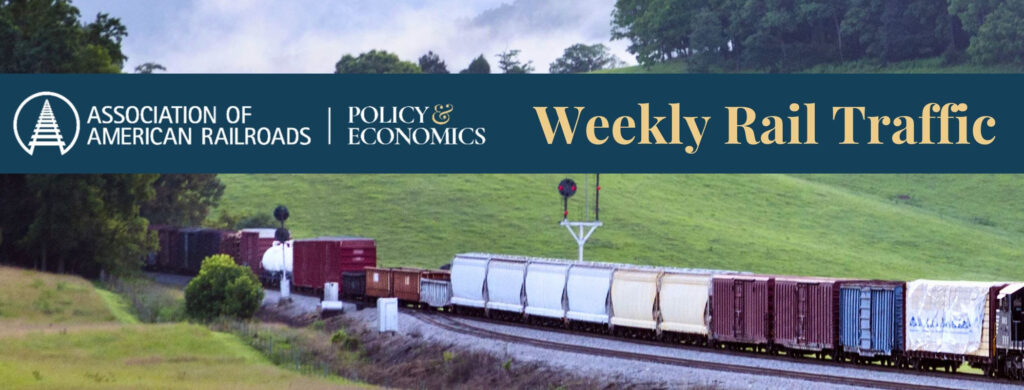
The Association of American Railroads (AAR) has reported U.S. rail traffic for the week ending August 10, 2024. This week’s total U.S. weekly rail traffic was 496,509 carloads and intermodal units, up 5.2 percent compared with the same week last year. Total carloads for the week ending August 10 were 222,039 carloads, down 0.9 percent compared with the same week in 2023, while U.S. weekly intermodal volume was 274,470 containers and trailers, up 10.6 percent compared to 2023. Six of the 10 carload commodity groups posted an increase compared with the same week in 2023. They included grain, up 3,866 carloads, to 18,402; chemicals, up 2,969 carloads, to 32,959; and farm products excl. grain, and food, up 546 carloads, to 16,193. Commodity groups that posted decreases compared with the same week in 2023 included coal, down 7,633 carloads, to 61,031; nonmetallic minerals, down 1,295 carloads, to 31,849; and metallic ores and metals, down 906 carloads, to 19,432. For the first 32 weeks of 2024, U.S. railroads reported a cumulative volume of 6,864,604 carloads, down 4.0 percent from the same point last year; and 8,237,398 intermodal units, up 8.7 percent from last year. Total combined U.S. traffic for the first 32 weeks of 2024 was 15,102,002 carloads and intermodal units, an increase of 2.5 percent compared to last year. North American rail volume for the week ending August 10, 2024, on 10 reporting U.S., Canadian, and Mexican railroads totaled 326,804 carloads, down 0.2 percent compared with the same week last year, and 353,768 intermodal units, up 7.7 percent compared with last year. Total combined weekly rail traffic in North America was 680,572 carloads and intermodal units, up 3.7 percent. North American rail volume for the first 32 weeks of 2024 was 21,143,021 carloads and intermodal units, up 2.3 percent compared with 2023. Canadian railroads reported 89,620 carloads for the week, up 2.5 percent, and 66,976 intermodal units, down 5.5 percent compared with the same week in 2023. For the first 32 weeks of 2024, Canadian railroads reported a cumulative rail traffic volume of 5,114,967 carloads, containers, and trailers, up 1.4 percent. Mexican railroads reported 15,145 carloads for the week, down 6.2 percent compared with the same week last year, and 12,322 intermodal units, up 27.9 percent. Cumulative volume on Mexican railroads for the first 32 weeks of 2024 was 926,052 carloads and intermodal containers and trailers, up 3.3 percent from the same point last year. View charts
Episode 512: Transparency in freight management with CargoShot
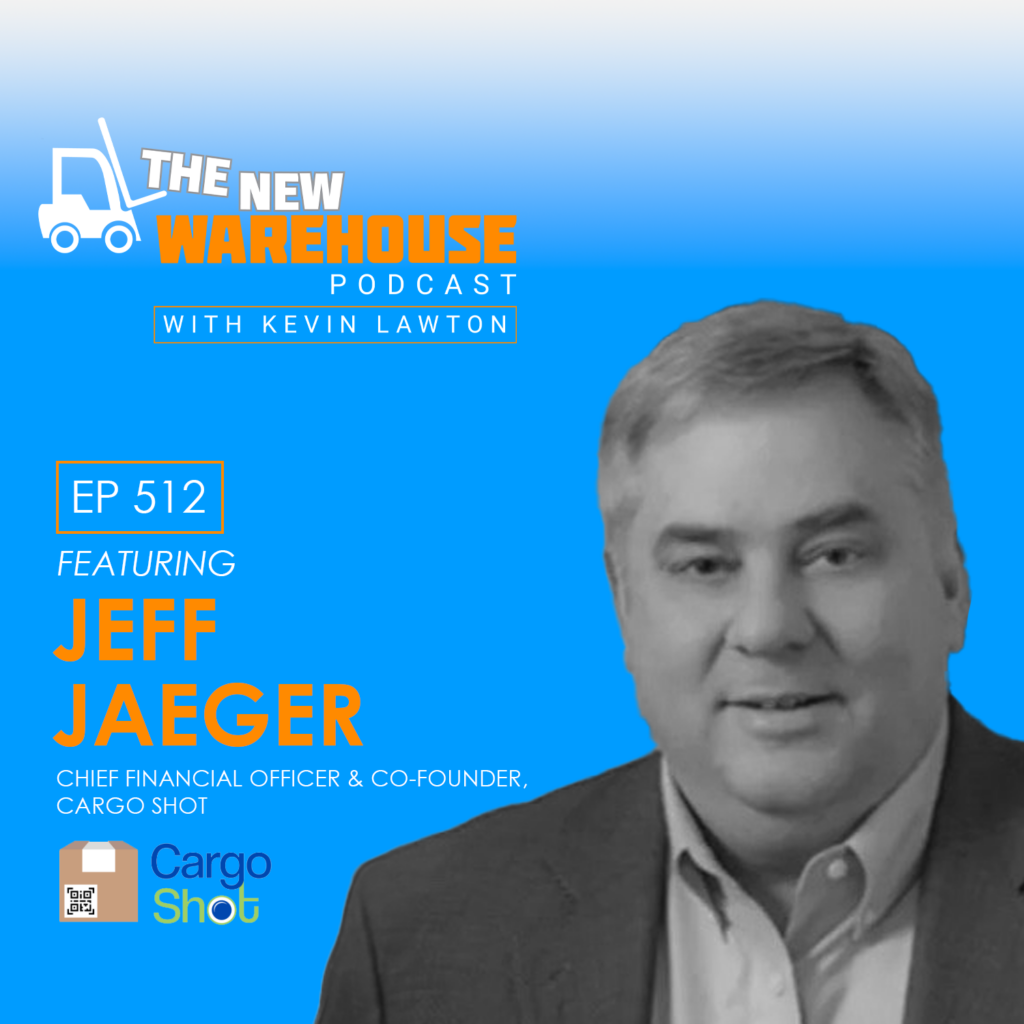
On today’s episode of The New Warehouse Podcast featuring Jeff Jaeger, we tackle the subject of transparency in freight. Jeff, the co-founder of CargoShot, shares how his company is enhancing supply chain accountability through its innovative proof-of-condition solutions. Jeff shares his journey from moving heavy equipment worldwide for the Marine Corps to spearheading a startup that tackles the costly issues of freight claims and chargebacks. Dive into this insightful conversation to discover how CargoShot is revolutionizing the logistics industry by providing product condition transparency throughout the supply chain. The High Cost of Freight Claims Jeff outlines the significant pain point in the logistics industry: excessive freight claims and penalties. He recounts feeling helpless against fines and penalties assessed by big box retailers, “I didn’t think we were as bad as what we were getting penalized for, so I started taking photos, and I started sending them with the time and date stamp so they could clearly see the product.” Jeff saw significant relief from fines and penalties by proving they had done the work correctly. This issue propelled him to create a scalable solution that reduces erroneous charges by providing clear, irrefutable evidence of freight conditions upon shipment. Ensuring Freight Claim Accountability CargoShot addresses these challenges with its innovative mobile app, which allows users to capture and store real-time photographic evidence of freight conditions. Jeff explains the app’s functionality: “You can take that information to prove that you did your job right, or in the cases that if you didn’t, use it as a coaching/training session for your team, and speed up resolution time with the client.” By automating and simplifying the proof-of-condition process, CargoShot drastically reduces the likelihood of unwarranted penalties, fostering greater accountability and efficiency. Optimizing Transparency in Freight Management Looking forward, Jeff is excited about the potential for new technologies to mitigate freight claim issues further. He shares insights into upcoming features, “We’re working on technology using computer vision, machine learning, and artificial intelligence to be proactive.” These developments aim to preemptively identify potential issues before they result in fines, setting a new standard for proactive management in logistics. CargoShot aims to establish a seamless chain of custody from the initial warehouse receipt to the final delivery, involving every stakeholder along the way. The goal is to ensure that if an issue arises, accountability is accurately assigned, not merely defaulted. Key Takeaways CargoShot drives unnecessary costs out of the supply chain by streamlining freight claims, damage, fines, and penalties. The mobile app is hardware-agnostic and offers scalable solutions across multiple locations. Enhanced data capturing leads to improved supply chain accountability and efficiency. The New Warehouse Podcast Episode 512: Transparency in Freight Management with CargoShot
ARA’s US & Canada third-quarter economic forecast released
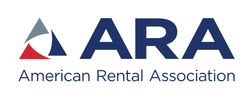
In its updated forecast, the American Rental Association (ARA) indicates that the United States equipment rental industry’s 2024 growth projection indicates softening. The most current projections indicate an 8.9% revenue increase in 2024, totaling $78.7 billion in construction and general tool rental revenue, and a 5.3% growth in 2025. This is a decrease from last quarter’s projected 9.7% increase, totaling $79.2 billion. Broken down by segment, construction and industrial rental revenue (CIE) is projected to be $62.3 billion, and general tool rental revenue is expected to total $16.4 billion. “While the rental industry and opportunities continue to expand, we are experiencing softer growth,” states Tom Doyle, ARA vice president of program development. “The ARA quarterly survey results confirm this softening.” “The forecast for construction and industrial has not changed much since last quarter, perhaps a few tenths of basis points, but there has been more change to general tool,” says Scott Hazelton, managing director at S&P Global. “The market is still doing well but slowing. Next year’s GDP growth is lower than trend at 1.6% growth, the trend is around 2.1%. The overall view of rental is positive moving forward, but there is uncertainty out there.” Kurt Barney, president of Vandalia Rental, Vandalia, Ohio, adds, “Largely what we’re seeing is softening growth as well. We’re seeing pricing elasticity. It’s no longer, ‘Do you have it?’ We’re back to doing business like 2019 when we have to really communicate the value proposition of working with us.” Barney also says, “We’re balancing rate pressures, supply chain, and mix of the fleet in a softening environment, especially on the earthmoving side. As interest rates begin to decline, I think it will take some of the projects off the sidelines. The quarter and half points have a huge impact on those projects. The rental model and proposition has never been stronger. It’s a good place to be.” The updated Canadian equipment rental revenue forecast shows a 6.6% growth, totaling $5.75 billion, compared to last quarter’s projection of 7.2% growth, totaling $5.79 billion. Broken down by segment, general tool and construction and industrial equipment (CIE) are expected to grow. Canadian general tool revenue this year is projected to be 6.8%, $1.08 billion, and Canadian CIE revenue in 2024 is projected to be $4.67 billion. Rob Wilson, chief operating officer of Stephenson’s Rental Services, Mississauga, Ontario, says, “What we’re seeing across our markets is pretty slow, but Stephenson’s is still growing. It’s a mixed bag. Residential activity represents 60% to 65% of those markets, and that activity is down.” Wilson is optimistic that the latter half of 2025 will be very strong. The 2025 projection for Canada’s combined rental revenue is $6.14 billion, a 6.7% year-over-year growth. Broken down by segment that equals $1.14 billion in general tool rental revenue and $5 billion in CIE rental revenue. “I wouldn’t characterize Canada’s economy as robust, but CIE is one of the strongest investments in particular,” says Hazelton. “We do expect the economy to get stronger as a whole by 2027.” What’s driving this forecast? S&P Global believes that interest rates will not come down until December, despite the chair of the Federal Reserve, Jerome Powell’s most recent testimony. Powell wants to see inflation stay under control before any moves are made. Hazelton also believes that when the cuts come, they will come slowly. “We [S&P Global] also see a downshift in GDP from 2.4% growth this year to 1.6% growth next year,” says Hazelton.
Episode 511: Harnessing AI for Warehouse Optimization
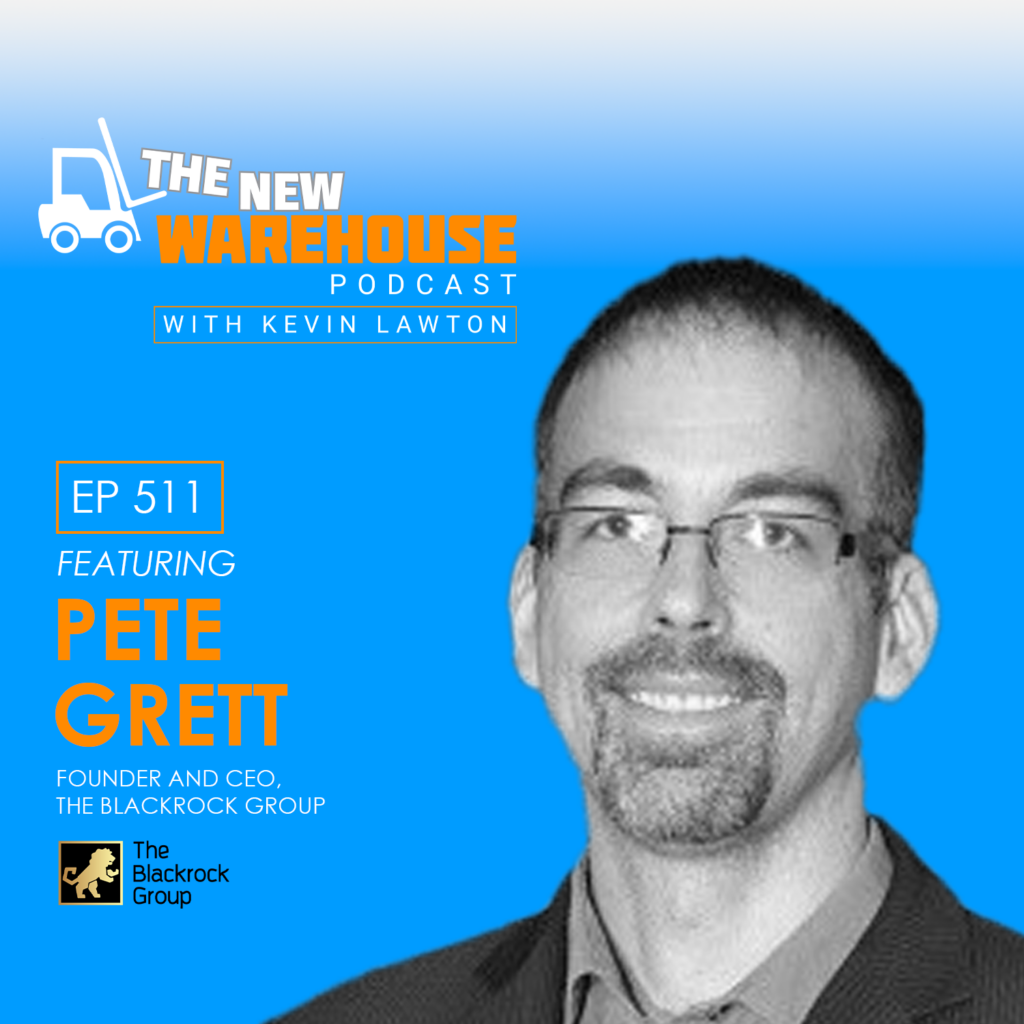
Today’s episode of The New Warehouse Podcast delves into the topic of AI for warehouse optimization with Pete Grett, founder and CEO of The Black Rock Group. Pete, an AI evangelist with a deep background in tech and supply chain management, shares his journey from a 19-year-old temp worker in a warehouse to leading a consulting firm. Today, we explore how AI is revolutionizing warehouse operations, the myths and realities of AI, and actionable strategies to leverage this technology for better decision-making and efficiency. From Warehouse Floor to Tech Leadership Pete’s journey began humbly as a temp worker, driven by ambition and a desire to climb the operations ladder. He transitioned into IT while implementing a new warehouse management system, which set the stage for founding The Blackrock Group. “One of the things we really focus on is having people who have been operators. We want to be practitioners of what we preach,” Pete emphasizes. This experience helps bridge the gap between IT and business, ensuring that technological investments can deliver maximum ROI. Using AI for Warehouse Optimization AI is rapidly transforming various aspects of warehouse operations, offering significant benefits in efficiency and productivity. Pete notes, “Our tagline that I really believe in is, make better decisions, solve problems faster.” AI can enhance tasks like labor management, quality checks, and warehouse slotting by providing swift and accurate analysis. For instance, AI can quickly crunch data to identify inefficiencies and suggest improvements, a task that previously required sophisticated software and extensive time. Pete explains the value of using AI for warehouse optimization, “How can we improve an individual’s job and make them more efficient and productive? The warehouse is a great example. Are you over-counting or over-auditing? With analysis from AI, you can focus your attention on where labor drives value.” This capability allows for more focused and meaningful use of resources, making AI an invaluable tool in the modern warehouse. Preparing for AI Integration Integrating AI into warehouse operations requires preparation, particularly regarding data quality and accessibility. Pete advises, “Having access to your data, having as good a data as you can have, understanding where it comes from, what it means—those are essential pieces.” Companies should invest in their data infrastructure and consider affordable AI services to start small and scale up as they see benefits. For example, Pete believes even a simple $20 monthly subscription to ChatGPT can provide substantial analytical power. He explains The Blackrock Group’s approach to integration, “We try to make it affordable enough so that these are OPEX expenses that don’t take a lot of authorization. It’s just so low cost that the customer will earn the investment back pretty quickly.” Key Takeaways on AI for Warehouse Optimization Experience on the warehouse floor is crucial for implementing tech solutions that work seamlessly in real-world scenarios. AI can transform warehouse operations by improving decision-making and efficiency through rapid data analysis and actionable insights. Ensuring high quality is essential for successful AI integration. Affordable AI services can help businesses start small and scale as needed. AI can optimize labor management, quality checks, and warehouse slotting, leading to significant productivity gains. The New Warehouse Podcast Episode 511: Harnessing AI for Warehouse Optimization
SupplyOne expands Nationally and Internationally
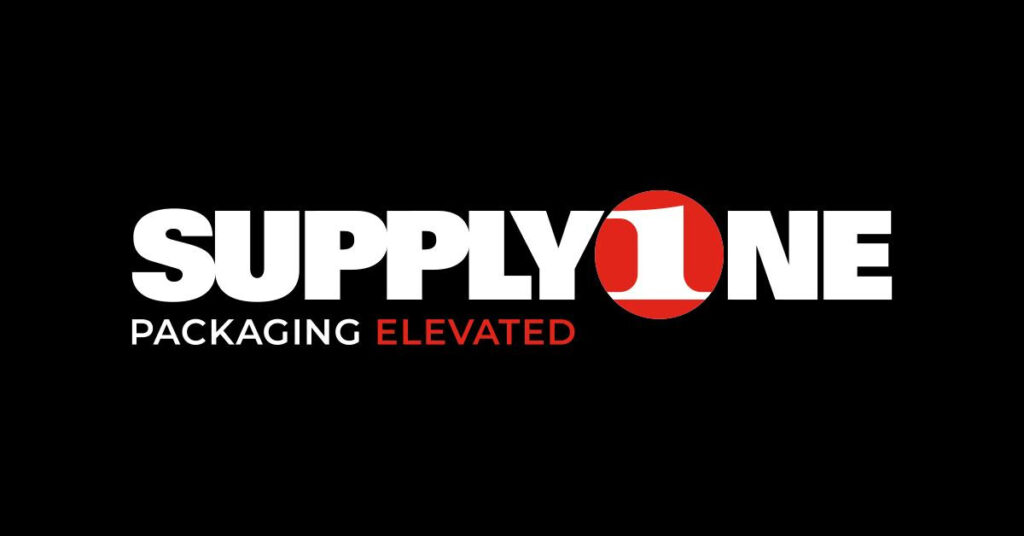
The company has completed three acquisitions in 2024 alone, bringing its overall count to forty-one acquisitions over its 25 years in business. SupplyOne is accelerating its growth across the U.S. and now into Canada. With new locations in Portland, Seattle, and Toronto, the company continues to enhance its services to meet the unique needs of its customers and attract like-minded businesses interested in joining its expanding footprint. “Our focus is on growth, and we’re actively seeking companies that are customer-focused and ready to scale,” said Todd Renehan, President & CEO of SupplyOne. “We value partners who align with our decentralized business model and our core principles: putting people first, fostering growth, staying agile, and delivering innovative packaging solutions.” SupplyOne has already completed three acquisitions in 2024, bringing its total to forty-one since its founding 25 years ago, with more in the pipeline. The recent acquisitions of Crownhill Packaging in Toronto, Bacon & Graham in New Jersey, and Columbia Corrugated Box on the West Coast highlight SupplyOne’s commitment to offering superior packaging solutions with both national reach and local expertise. “Our expansion reflects our dedication to our core values and solidifies our position as the acquirer of choice in North America,” said Nathan Barton, Senior Vice President, Corporate Development & Acquisitions at SupplyOne. “We’re excited about the opportunities ahead and look forward to welcoming more exceptional businesses into the SupplyOne family.”
Bioelements and Multi X join forces to transform fresh steak packaging with biodegradable packaging
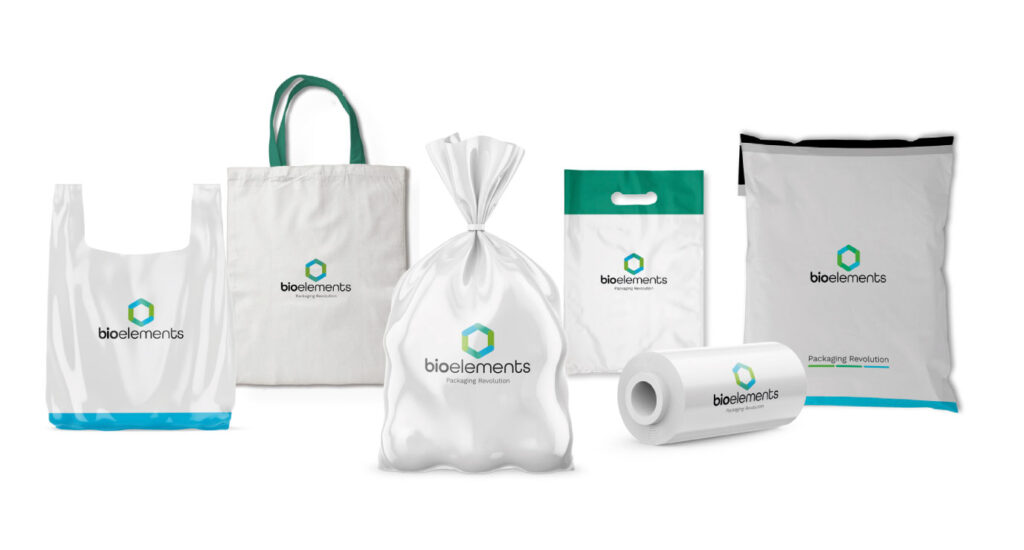
Latin American Salmon Supplier Introduces Products with Biodegradable Packing Bioelements Group has announced that Bioelements will be supplying biobased, biodegradable, and compostable packaging to Multi X. This leading salmon products supplier was founded 34 years ago as a sea farmer in Southern Chile and now produces and exports salmon exclusively. The salmon farming company will replace all of the bags it uses for packaging fresh fillets with bioplastic containers produced by Bioelements. As part of its sustainability strategy, Multi X is working to reduce the impact of plastics on the planet by replacing all the bags that Multi X uses with biodegradable packaging. This equates to 35% of Multi X’s annual production and positively impacts the United States, the salmon farming company’s main export destination. The technology behind Bioelements’ biodegradable packaging has been developed by the company’s science team in collaboration with academia, achieving innovative formulations that allow its packaging to biodegrade under the action of fungi and microorganisms. This approach is ideal for Mult X and its goal of reducing its reliance on traditional carbon-based plastic technology for packaging. “It is a biodegradable alternative that will positively impact the environment. Bioelements bags maintain the same mechanical, barrier, and performance characteristics as conventional materials,” highlighted Ignacio Parada, CEO of Bioelements. “This alternative will allow Multi X to offer its clients an alternative that helps stop pollution due to waste accumulation. People are increasingly demanding that companies take charge of environmental challenges and this project will undoubtedly add value to the brand within the industry and open the doors to continue developing joint projects.” According to Daniel Santa Cruz, supply manager of Multi X evaluating the Bioelements packaging, the Bioelements packaging performed very well throughout the useful life of the product, then biodegraded successfully within the timeframe Bioelements has promoted. “We were pleased with our test results of the Bioelements technology and they concluded successfully,” he said. “We are excited about implementing the new packaging and working with Bioelements for additional solutions to address the plastic packaging issue.” This alliance adds to the list of milestones that Bioelements has experienced in recent times, along with the opening of its laboratory in Santiago and the recognition by the Financial Times as one of the fastest-growing companies in the Americas. It continues to make great strides in Latin America markets as well as the newly entered U.S. market, including with such customers as Adidas, Chile-Peru, Australis Seafoods, Justo, Privalia, Walmart Mexico, among others.
NGen awards Nano One and Worley $2.8 Million
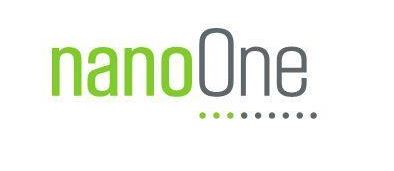
Next Generation Manufacturing Canada (NGen) awards Nano One and Worley Chemetics C$2.8 million in non-dilutive non-repayable funding through the Electric Vehicle Manufacturing Program (EVMP). The award supports the joint development of reactors and kiln components for the One-Pot process, Nano One’s patented, scalable, and efficient method for producing lithium-ion batteries. The NGen award supports cathode active materials production and fosters equipment manufacturing and technology development capabilities in Canada by Nano One and Worley Chemetics. Nano One® Materials Corp and Worley Chemetics® (“Chemetics”) are pleased to announce that they have been awarded $2.8 million CAD in non-dilutive and non-repayable funding by Next Generation Manufacturing Canada (NGen) through its Electric Vehicle Manufacturing Program (EVMP), to aid in the development of the Canadian Electric Vehicle supply chain and manufacturing ecosystem. NGen is an industry-led, non-profit organization that supports development of world-leading advanced manufacturing capabilities in Canada. The funding will advance a new project to help both companies develop, market and sell CAM facility packages that incorporate Nano One’s proprietary One-Pot process into a process engineering design package. “NGen backing Worley Chemetics’ collaboration with Nano One will accelerate the commercial trajectory of the distinctive One-Pot process,” said Laura Leonard, Worley’s Group President of Technology Solutions. “The fastest path to net zero is to standardize or as we are doing with Nano One, design one, build many.” Nano One formed a strategic alliance on May 2, 2024 with Worley, a global professional services company of energy, chemicals and resources experts, with a commitment to sustainability, and specialization in the design and delivery of battery materials facilities, including first-of-a-kind technology scale-up and deployment. The companies will jointly develop, market and sell CAM facility packages that incorporate the One-Pot process into a process engineering design package. The package will include intellectual property rights, flow sheets, detailed engineering, the operational know-how of both parties and proprietary equipment including reactors and kiln components being supported by NGen. The One-Pot process combines precursor CAM (pCAM), CAM and CAM coating processes into one holistic process using secure and resilient supply chains while reducing cost, complexity, energy use and environmental footprint. The elimination of wastewater and harmful by-products has the potential to reduce the cost, time and risk of permitting CAM facilities, to enable designs that can be constructed on a wide range of sites and expedite financial decisions and growth potential. Drawing on its specialized capabilities, experience and knowledgeable team, Chemetics will support Nano One in identifying the best materials of construction, and fabrication methods for key equipment required for the One-Pot process, and in engineering and delivering the technology and its associated equipment. The project’s goal is to integrate both companies’ advanced process and equipment knowledge into the CAM manufacturing ecosystem, enabling the joint marketing and sale of equipment in Canada and around the world. Design specifications will be determined through rigorous reactor studies, analysis and selection of appropriate materials of construction, ensuring compatibility with feedstocks and reagents, as well as operating conditions. The collaboration between Nano One and Chemetics will add valuable layers of intellectual property protection to the CAM package offering, providing potential customers with greater reliability on equipment performance and competitive differentiation. Dan Blondal, CEO of Nano One, said “The capital provided by NGen enables companies such as Nano One and Worley to accelerate technology development, commercialization and deployment. We want to thank NGen for their confidence, for their valuable support and for recognizing Nano One’s accomplishments, partners and business objectives.”
Plastics Machinery Shipments decline in Q2 2024, growth prospects remain

The Plastics Industry Association’s Committee on Equipment Statistics (CES) released Q2 2024 shipment data for primary plastics machinery in North America, covering injection molding and extrusion. The shipment value is estimated at $224.8 million, marking a 15.4% decrease from the previous quarter and a 36.2% year-over-year (Y/Y) decline. In the primary plastics machinery sector, single-screw extrusion saw a 3.4% quarter-over-quarter (Q/Q) increase but a 28.6% Y/Y decrease. Twin-screw extrusion experienced a 23.5% Q/Q decrease and a 25.3% Y/Y decline. Injection molding shipments fell by 16.3% Q/Q and faced a 37.7% Y/Y decline. “The second consecutive quarter of decline in shipments is not due to a pullback in plastics demand. In fact, based on monthly Plastics Demand Estimate,∗ there has been growth in demand recently. There is no indication that the baseline demand for plastic products has deteriorated,” commented PLASTICS’ Chief Economist, Perc Pineda, PhD. Manufacturers’ finished goods inventories of plastics and rubber products were estimated at $15.0 billion in June this year, compared to $15.2 billion in June last year, indicating slow inventory adjustments. Results from the latest CES quarterly survey showed that a high percentage (79.9%) of respondents anticipate steady or improved market conditions over the next twelve months. However, 40.0% reported an increase in quoting activity, which was lower than the 48.9% in the previous quarter’s survey citing an increase in quoting activity. In Q2 2024, U.S. total exports of plastics equipment declined by 14.7% to $341.0 million compared to the previous quarter, while imports decreased by 3.8% to $856.8 million during the same period. Slightly more than half (53.4%) of exports went to Mexico and Canada, jointly accounting for $182.3 million of U.S. plastics machinery exports globally. Pineda remarked, “While the rate of decline in the second quarter was significantly less than in the first quarter, the industry continues to deal with higher interest rates, and that’s weighing on capital expenditure plans.” The economy is currently not operating at maximum capacity in plastics processing; capacity utilization is below potential, leaving room for growth.
Mitsubishi Logisnext Americas and Family of Brands join efforts to Sponsor the 2024 FedEx St. Jude Championship
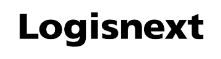
Mitsubishi Logisnext Americas Inc. (Logisnext) has announced its return as a sponsor for the 2024 FedEx St. Jude Championship. This year, Logisnext is joined by its entire family of brands – Cat® lift trucks, Jungheinrich®, Mitsubishi Forklift Trucks, UniCarriers® Forklift and Rocla AGV Solutions – showcasing a unified front in support of the St. Jude Children’s Research Hospital. From Aug. 14 to 18 at the TPC Southwind in Memphis, Tennessee, the tournament will feature the top 70 players on the PGA Tour competing in an exhilarating battle for the FedExCup. Since the tour’s initial partnership with St. Jude in 1970, the Memphis tournament has raised more than $60 million, significantly advancing the hospital’s lifesaving mission of ending childhood cancer. This longstanding tradition underscores that golf has always been more than just a game in Memphis; it’s been and continues to be a powerful force for good. “We are immensely proud to sponsor the PGA Tour’s FedExCup Playoffs and to be part of this prestigious event for another year,”said Stu Jacover, General Manager of National Accounts, Logisnext. “This year is particularly special as we bring together all our family of brands, reinforcing our collective commitment to charitable initiatives and the communities we serve. This sponsorship highlights our dedication to social responsibility and demonstrates our unified strength and broad capabilities in the material handling industry.” Logisnext and its family of brands extend a warm invitation to their valued Dealers and Dealer customers to join this unique golf experience. The FedEx St. Jude Championship continues to be a hallmark event in the world of golf, demonstrating the profound connection between sports and philanthropy. The event offers an exclusive opportunity to support a noble cause while engaging in meaningful conversations and fostering relationships.
Electric hoist leaves large distillery in high spirits
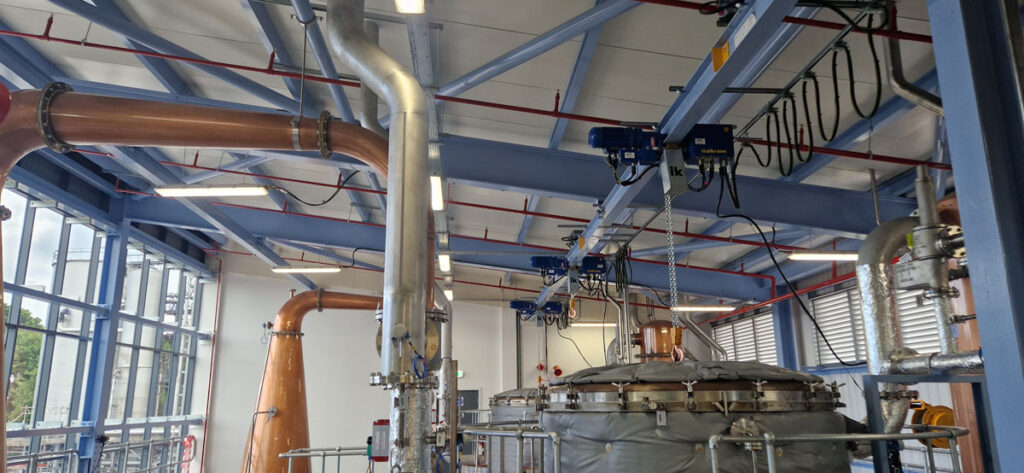
The world’s largest producer of spirits is now benefiting from a turnkey package of three Italkrane ATEX-rated electric chain hoists supplied by Hoist & Winch Ltd. Operational within a new extension of the Scotland-based distillery, the 2-ton swl (safe working load) hoists raise and lower sealed vessel lids and baskets containing raw materials used in the production of gin. Among the challenges of this demanding project was a restriction in the overall height of the new building due to local planning laws. In turn, only limited headroom is available for lifting operations over the vessels. Critical for the application, therefore, was the specification by Hoist & Winch of Italkrane YY series electric chain hoists featuring a low-headroom design. The ATEX specification of the hoists is necessary due to the vapours and fumes produced in the manufacture of alcohol-based products. Italkrane YY series electric chain hoists feature an Ex d electrical enclosure design to contain any explosions and stop flames, sparks and hot gases from escaping. Full anti-spark features are in place for all components subject to sliding friction, including the brass trolley wheels. Also present is a non-sparking load hook, brass anti-tip device and polycarbonate pendant control ensuring explosion protection up to Zone 1 II B T4 classification. The power supply to each hoist unit is via a festoon cable track system complete with sliding trolleys and support arms clipped to the top flange of the hoist runway beam. Each hoist unit also features an Italkrane heavy-duty geared top/bottom limit switch and friction-type slipping clutch overload protection device. “Although we provide a full spectrum of lifting equipment services, Hoist & Winch is particularly at home supplying equipment for demanding industries, including the distillery sector,” explains Hoist & Winch Director Andy Allen. “We have extensive knowledge of this industry, where our quality of service and flexible approach ensure the highest levels of customer satisfaction.” Due to the critical nature of the project and the risk of explosion throughout the high-risk site, it was clear that very stringent planning and close monitoring of working practices would be necessary at all times. In addition, the site work was subject to Construction Design and Management (CDM) Regulations, supported by a requirement for all site engineers to hold a valid CCNSG Safety Passport/CSCS competency certification. Installation took place over seven days, with a Hoist & Winch CompEX-certified electrical installation engineer completing all connection work. The load testing of each hoist unit and complete runway beam took place using a dynamic test load of 2t + 125% proof load. Additional functional testing using the vessel lids and raw material baskets proved system functionality in line with customer requirements. Following the issue of a LOLER (Lifting Operations and Lifting Equipment Regulations) Thorough Examination Report for all installation work, Hoist & Winch provided on-site training for the distillery’s operating personnel. Although providing the optimal solution for this large distillery, Italkrane ATEX-rated electric chain hoists are also suitable for many other applications requiring safe lifting operations in explosion risk environments. In addition, Hoist & Winch can offer ATEX wire rope hoists for longer lifting tasks, heavier loads up to 50t swl and higher duty applications.
MHEDA announced Parts & Service Management Conference Registration open
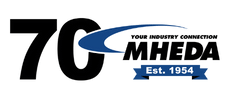
The Material Handling Equipment Distributors Association (MHEDA) is excited to announce its upcoming Parts & Service Management Conference, set for September 12, 2024, at Atlas Toyota Material Handling in Elk Grove Village, Illinois. This one-day event is designed to empower professionals in the material handling industry with actionable insights and best practices to elevate department performance and profitability. The conference will feature sessions on monitoring key performance indicators, strategies to reduce the impact of parts backorders, and sales growth through e-commerce. Attendees will have the opportunity to engage with industry peers through roundtable discussions, an optional networking dinner at Gibson’s Steakhouse, and more. Registration for the event is now open, with early bird rates available until August 23, 2024.
KEEN Utility athletic-level work sneaker
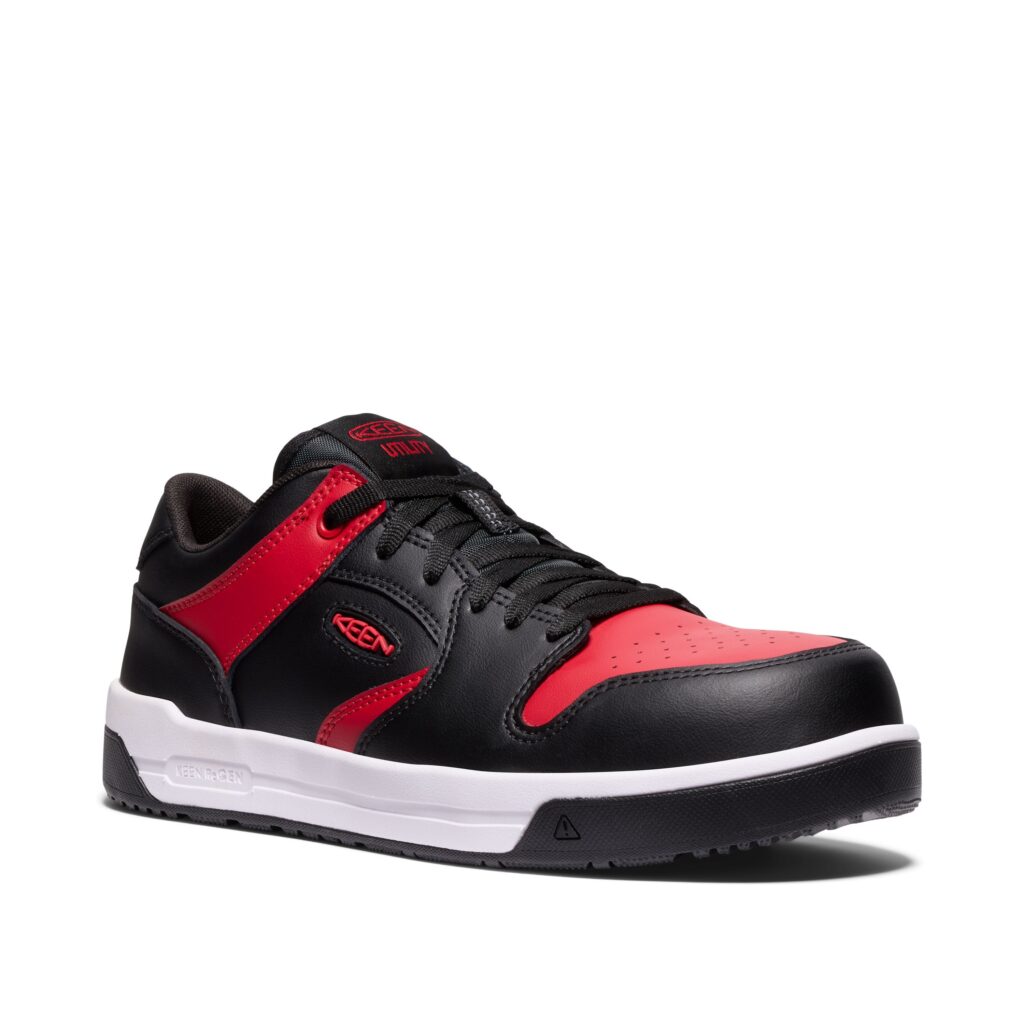
New for Fall ‘24, KEEN Utility’s Overton is a modern work sneaker built with a wide toe and snug heel for a workday-enhancing fit. The Overton boasts an athletic-level KEEN.ReGEN cushioning provides up to 50% energy return with every step, lightweight carbon-fiber safety toes to protect without holding you back, and a slip-resistant, EH-rated rubber outsole for dependable footing on hard surfaces. A versatile, throwback-inspired work shoe, the Overton is available in several collar heights and colorways for men and women.
Hyster-Yale participates in US Department of Defense SkillBridge program
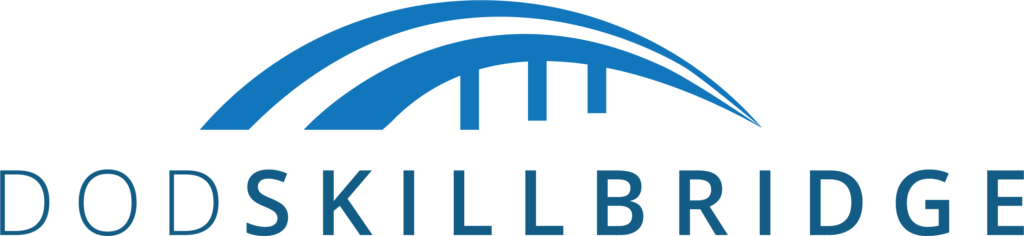
Program advances Hyster-Yale’s commitment to veterans, enables manufacturer to recruit talent from the world’s most highly trained and motivated workforce. Hyster-Yale Materials Handling announces its participation in the United States Department of Defense (DOD) SkillBridge program, offering training and career opportunities to service members and their spouses as they transition to civilian life. DOD SkillBridge connects service members in their final 180 days of service with companies that provide civilian work experience at no cost to the company while the service member continues receiving military compensation and benefits. “Our service members dedicate their lives to serving our country, and this program is our opportunity to reward that service while also adding skilled, dedicated talent to the Hyster-Yale team and our dealer partners,” says Anthony Salgado, Chief Operating Officer, Hyster-Yale Materials Handling. “The SkillBridge program provides hands-on experience that helps service members explore career interests and develop job skills in the private sector. As a proud veteran of the U.S. Navy, I know how important resources and support are to a successful transition to the civilian workforce.” SkillBridge enables Hyster-Yale and its independently owned dealer partners to recruit and retain top-notch talent nationwide with a particular emphasis on the dealer network’s initiative to hire skilled technicians. Specifically tailored for technician apprenticeships, this program immerses participants in targeted training that equips them with the necessary skills and expertise for a successful career in materials handling. “We’re proud to work with SkillBridge to give back to our military veterans for the bravery and sacrifices they’ve made for all of us,” says Troy Pederson, Director of Training & Development at LiftOne, a Hyster-Yale dealer and established SkillBridge employer. “In the last year, we’ve helped 10 SkillBridge interns transition from military to civilian life, and the value and positive impact of the program can’t be overstated. At LiftOne, we’ve gained so much from the experience and diverse mix of technical and leadership skills of our SkillBridge candidates.” “Our participation demonstrates our long-standing commitment to employing men and women who have served our country, and the value we place on their strong work ethic, discipline, loyalty and leadership qualities,” says Jessica Mason, Talent Acquisition Manager at Eastern Lift Truck Co. “Veterans enhance our workforce and make a positive impact on our entire organization.”
Tele Radio handhelds for lifting applications
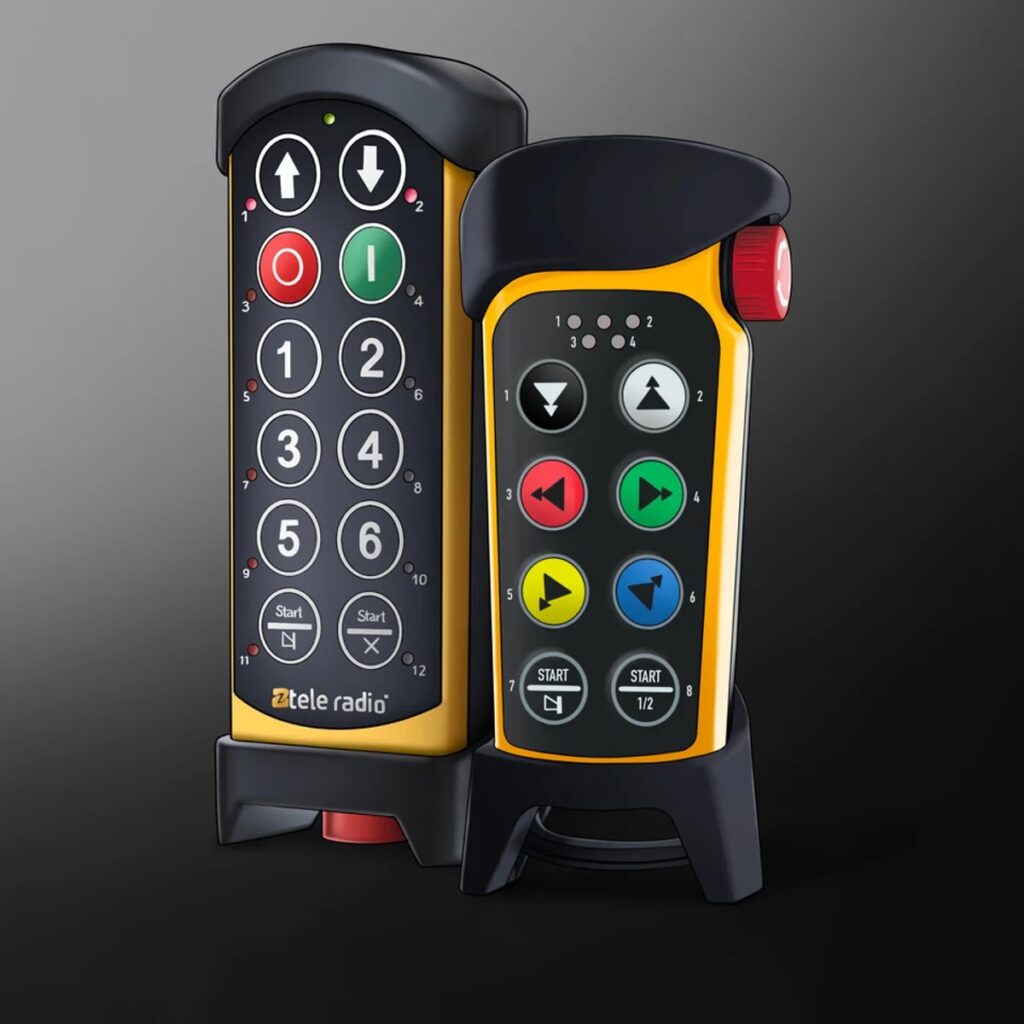
Tele Radio has reminded the industry of the benefits of two handheld radio remote controls specifically for the demands of lifting and hoisting applications. The T19-2 and T29-12 joined the company’s Panther line of products, which all meet Performance Level d (PLd), Category 3, equivalent to Safety Integrity Level (SIL) 2. This makes them suitable for use in high-risk areas such as those with moving and heavy loads. Tele Radio, part of Sweden’s Allgon Group, offers a wide variety of handheld transmitters and larger-size waist belt transmitters for all kinds of industrial applications. However, the T19-2 and T29-12 present a variety of benefits to end users operating cranes and hoists, largely because of their conformity to relevant standards and certifications, and the fact that they are lightweight, easy to handle, and cost-effective. KeesJan van der Elst, Market Manager at Tele Radio, said: “Both transmitters are popular in the marketplace due to their high safety and quality at a competitive price. They are easy to set up for specific applications, and are widely used to control jib cranes, overhead cranes, loader cranes, and other overhead lifting equipment.” The T19-2 has eight buttons, while the T29-12 is a 12-button version; the latter can control up to 24 different functions, but this can become 4 x 24, through the ‘layer selection’ option. The additional buttons mean the T29-12 can even be used for the safe control of more advanced machinery, like recovery vehicles and excavators. These buttons have three steps: off, half, and full. A broad offering of accessories and a 500m wireless range, depending on the surrounding environment, means the applications for each transmitter are limitless. Both transmitters work on rechargeable lithium-ion batteries and are equipped with robust housing with a protective bumper and are water resistant according to IP65. They work on the worldwide accepted 2.4 GHz frequency and, thanks to advanced technology, interference is minimal. It is also possible to create a group code, through which multiple transmitters can control a single receiver. Van der Elst said: “The Panther systems include several three relay crane controls and can be fitted with standard harnesses and connectors for various types of cranes and lifting equipment. In addition to the standard settings, advanced setups are possible through a USB connection with a personal computer. A separate programming kit is available [from Tele Radio] to set up the Panther PLd to a user’s specific needs.” Another standout feature of the Panther is the ability to pair the transmitter and receiver high in a crane from the ground. In other words, a transmitter, connected to a receiver that is mounted high in a crane, can be replaced and paired easily without climbing to the receiver and without opening it. It can be completed from the ground floor. This configuration is another example of the flexibility and user-friendliness of the products. While the transmitters are water resistant according to IP65, the receivers are protected by IP66, providing resistance to dust and water. Van der Elst added: “The Panther PLd systems are the clear choice for certified hoisting and lifting, where high performance is a requirement. Consider the accessories — holders, chargeable batteries, charging cables, straps, and covers — and it’s evident that both the T19-2 and T29-12 are perfect for the demands of lifting and hoisting applications in a multitude of end-user applications.”
Essential measures for minimizing disruption amid Ningbo Port closure
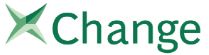
Container xChange is alerting the global container trading and leasing community to the serious repercussions of the recent explosion aboard the Yang Ming vessel YM Mobility at Ningbo Port, China. This incident, which has led to the closure of one of the world’s busiest container terminals, is expected to have significant ripple effects across global supply chains, especially on the main trade lanes out of Asia. On August 9, 2024, a container loaded with hazardous materials exploded aboard the YM Mobility while it was berthed at Ningbo Beilun’s Phase III Terminal. The explosion, which involved organic peroxide materials, has led to the terminal’s closure until further notice. “With this closure, Ningbo Port is no longer operational, compounding existing supply chain disruptions exacerbated by Typhoon Gaemi in July.” shared Christian Roeloffs, cofounder and CEO of Container xChange. “For container trading companies and those involved in container leasing, this incident presents some straightforward challenges worth accounting for. The disruption at the Ningbo Port, combined with pre-existing congestion at major Asian ports, will lead to a deterioration of ocean schedules and further delays in container availability. Companies must brace for increased dwell times, potential rerouting of shipments, and a tightening of available container supplies, especially for hazardous and dangerous goods.” shared Roeloffs. Recommended Actions: Rerouting Shipping Routes: Companies are exploring and evaluating alternative shipping routes through less congested ports to avoid delays. The closure of Ningbo will likely increase congestion at neighboring ports, so proactive planning is crucial. Increase Safety Protocols: Rigorous inspections and adherence to safety protocols, particularly for hazardous goods, must be prioritized to prevent similar incidents. Stay Informed: Regular updates from shipping partners and port authorities will be crucial in adjusting operations in real-time. Companies should maintain open lines of communication to adjust operations in real-time. Plan for Extended Dwell Times: With delays expected to increase, companies should anticipate longer dwell times at major ports and adjust their inventory and delivery schedules accordingly. Companies should plan for extended delays and consider increasing inventory levels to avoid disruptions.
SUN Automation Group highlights latest Innovations and Key Partnerships
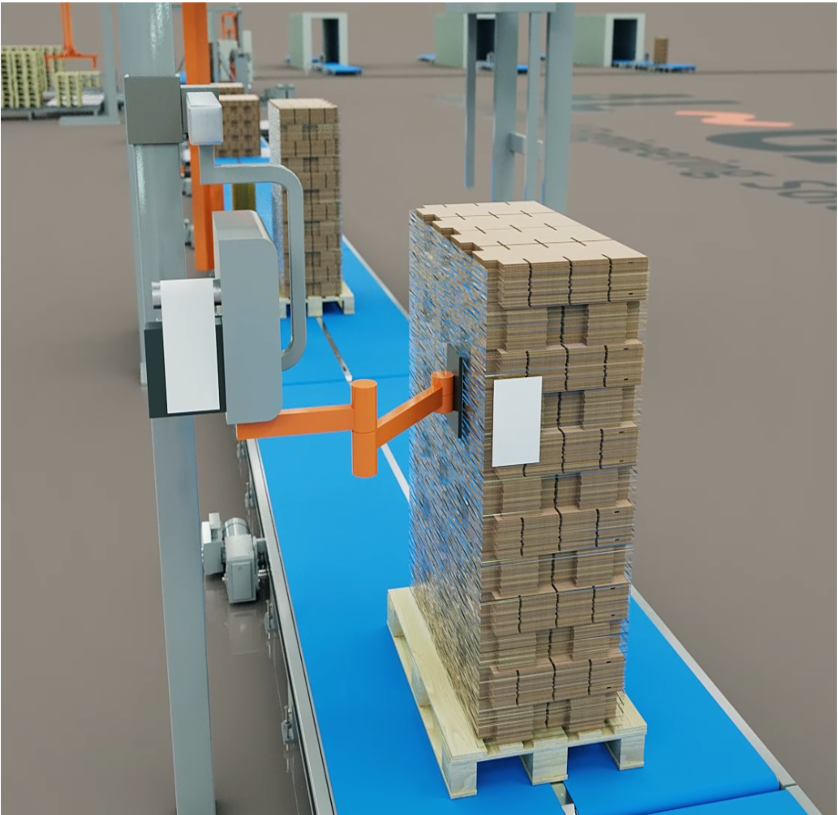
SUN Automation Group (SUN) will attend SuperCorrExpo at Booth 1731 at the Orange County Convention Center in Orlando, Florida from September 8-12. Visitors can learn more about the SUN625® HD Rotary Die Cutter, SUN’s next-level solution for corrugated manufacturing. With comprehensive feeding, printing, and converting capabilities, the SUN fixed-frame RDC offers more production volume than two traditional RDC machines while producing superior container quality. “We’re incredibly excited to share the SUN625® HD at SuperCorrExpo,” said Eric Aulton, Product Manager – RDC. “This new technology, specifically, a new engineered approach to Rotary Die Cutting, embodies our commitment to innovation and productivity and offers our customers unprecedented machine reliability, product throughput, and product accuracy. It’s setting new standards in efficiency and versatility, and we look forward to discussing its transformative capabilities in September.” SUN will also highlight Helios, the company’s machine learning and IIoT platform. The SaaS solution quantifies and analyzes key elements of the corrugated manufacturing process. With this data, box plant leaders are empowered to make more efficient and informed decisions about when to schedule downtime and order parts to prevent machine failure. “Helios saves box plants time and money by enabling their equipment to work smarter, not harder,” said Gokul Gopakumar, Vice President of Technology and Business Development. “Its machine learning capabilities enable predictive maintenance, and its real-time remote monitoring allows for quick identification and resolution of issues. Helios is the 21st-century solution for optimizing the manufacturing process.” In addition, SUN will feature its breadth of strategic global partnerships at SuperCorrExpo. By combining industry leaders’ experience, equipment, service, and technology worldwide, SUN can provide the right solution for any operation and accommodate even the most unique needs. “Our strategic partnerships allow us to expand as a total solutions provider for the corrugated industry,” said Greg Jones, Executive Vice President. “We can capitalize on our all-encompassing resources to provide individualized solutions for our customers. We look forward to demonstrating how our current knowledge, experience, and global presence can serve the corrugated community.” SUN is proud to maintain key partnerships to provide solutions for increasing production, efficiency, and profitability. When SuperCorrExpo attendees visit SUN’s booth this year, they will also have the opportunity to meet and learn more about these strategic partners. Al-Gar Al-Gar is a global leader in corrugated engineering solutions. Based in Barcelona, Spain, the company provides expertise and resources to optimize manufacturing processes with customizable solutions for design, control systems, retrofits, and maintenance. Al-Gar bolsters its comprehensive services with top-of-line product offerings that enhance corrugated, paper, and converting operations. SUN will display the Al-Gar Load Tag Inserter, showcasing the latest innovative corrugated solutions. New Partner: Versor Versor, a leading innovator in Specialty Folder Gluers, joins SUN’s lineup of strategic partners. Their advanced technology enhances the capabilities of corrugated manufacturing operations, ensuring efficient and high-quality output. Versor has proudly installed over 300 machines in Europe alone. Other Key Partners: Latitude Machinery Group (LMC) Since August 2019, SUN Automation Group has been the exclusive representative for Latitude Machinery Corp. (LMC) in North and Central America. As a world-class Rotary Die Cutters and Flexo Folder Gluers manufacturer with over 100 machine installations in North America, LMC has an outstanding reputation for reliability and throughput. PARA Srl Machinery and Material Handling for Corrugated Board As a globally integrated Italian material handling company and partner to SUN since 2021, PARA boasts a wide variety of material handling solutions for the corrugated industry, with 30 plant installations in the U.S. and over 15,000 products installed worldwide. PARA’s extensive product range includes pre-feeders, palletizers, RDC stackers, bundle breakers, pallet inserters, vertical storage solutions, paper mill roll transports, and unit conveyor systems. Highcon SUN and Highcon have been cultivating a growing relationship since 2021. Highcon represents the digital arm of corrugated converting solutions, bringing patented digital cutting and creasing for post-print processes in the folding carton and corrugated carton industries. ePS ePS leverages its extensive product range and global reach to deliver expertise across all aspects of plant operations, from scheduling and MES to ERP solutions. Much like Helios, ePS’ solutions are specifically tailored for corrugated box plants to address both current and future software needs. SUN is committed to delivering excellence to the corrugated industry.
Gordon Report: Will the U.S. Labor economy avoid brain death?
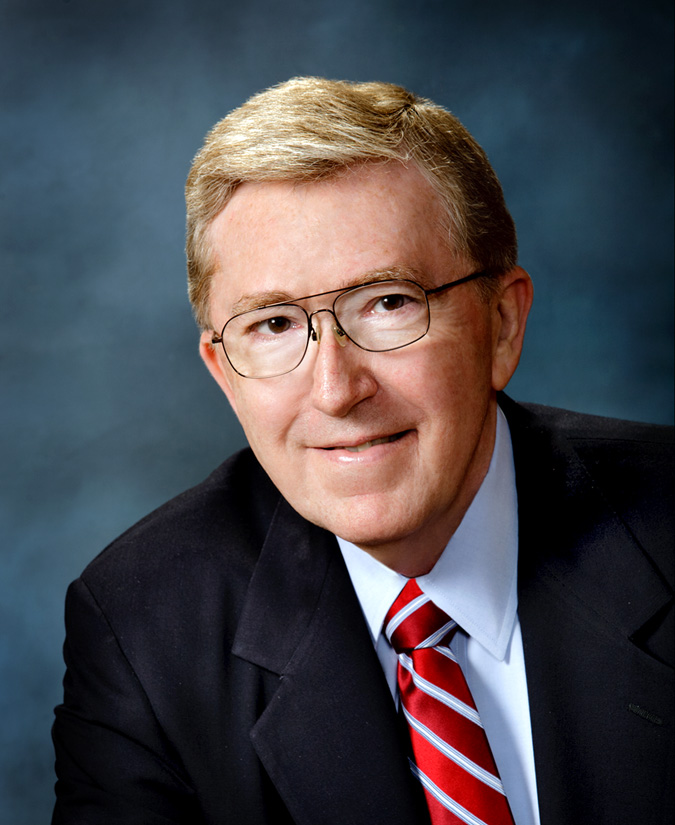
The Gordon Reports are based on over 30 years of research on the causes, effects, and solutions for continuing worldwide skills-jobs disconnects. For your convenience, here are the major publications that have reported on a burgeoning talent-deficit question: Closing the Literacy Gap in American Business, 1991 (adult reading) FutureWork, 1994, and Enhancing Learning in Training and Adult Education, 1998 (higher performing employer training and development programs) Skill Wars: Winning the Battle for Productivity and Profit, 2000 (training return-on-investment) The 2010 Meltdown: Solving the Impending Jobs Crisis, 2005 (impact of baby-boomer retirements on workforce skill levels 2010-2030) Winning the Global Talent Showdown, 2009 (skilled worker challenges in 25 nations and their solutions) The Talent Hunters, 2012, (China, India, and the United States vie to attract skilled workers) Future Jobs: Solving the Employment and Skills Crisis, 2013, 2018 (preparing solutions for skilled talent deficits) Job Shock, 2022 (Building a new skilled workforce in the wake of COVID-19) These publications feature case studies of businesses and communities rising to the challenge of fixing skill deficits. Many have established Regional Talent Innovation Networks (RETAINs), not one-off partnerships but collaborative hubs focusing on systemic change. Coast to coast, under local brand names, RETAINs connects schools and businesses to educate and train students and incumbent workers for today’s jobs and careers. The Fourth Industrial Revolution continues to raise the education and skills required to develop and use advanced technologies, with AI now the focus of attention. Yet the skill levels of too many Americans stalled out during the last decades of the 20th century. High levels of vacant jobs persist across all business sectors. Wages continue to rise as businesses seek to mine the inadequate supply of knowledge workers. We are nearing a state of collapse in such people’s current and future availability. The critical mass of educated Americans is inadequate to support and grow the U.S. economy. Why has this happened? It begins with education National Assessment of Educational Progress (NAEP) test scores show a steep post-COVID decline in American elementary school students’ reading and mathematics performance. In 2022, only about one-third of 4th- and 8th-grade public and private school students scored in reading at grade level or above. In mathematics, 37 percent of 4th-graders scored at grade level or above, but only 27 percent of 8th-grade students did. All the testing results showed a significant growth in students scoring well below their grade level in both mathematics and reading. International testing also showed sharp drops in reading and mathematics results. The 2022 PISA exam of 15-year-old students in 81 OECD member countries saw mean performance fall 10 points in reading and 15 points in mathematics compared to 2018 results. The results of the 2024 ACT exams confirm another confirmation of educational declines. American high-school seniors take this achievement test to assess readiness for college-level studies. The 2024 average ACT score was the lowest in thirty years. This year, the Georgetown University Center on Education and the Workforce issued a report on post-secondary job requirements. It indicates that 75 percent of all jobs by 2031 will require post-secondary education: two—or four-year degrees, technical certificates, or apprenticeships. These post-secondary options will need students to have achieved 12th-grade reading comprehension. In 2024, only 33 to 37 percent of public and private high school graduates read at this comprehension level. This is a major factor behind the sad statistic that only half of students who start a post-secondary degree complete it. Looking to the future Demand for more advanced IT skills will continue to grow across the job market. Higher cognitive skills, critical thinking, and creativity are essential for innovation. They all involve achieving higher reading comprehension. Business executives report skill shortages and expect them to continue. A 2024 Experis survey of IT employers in over 40 countries found that 76 percent reported difficulty finding the skilled talent they need. The World Economic Forum predicts up to 90 million skilled job vacancies worldwide by 2030, with up to 30 million in the United States. U.S. high schools are now graduating a significant number of functionally illiterate young adults. The 21st-century reality is that the world has moved into a new era of occupational transitions and employment qualifications. What actions need to be taken to stave off the brain death of the U.S. labor force? A 2024 McKinsey Global Institute Report, “A New Future of Work,” found that the surveyed executives expect greater skill demands by 2030. Companies are considering retraining their current workers, hiring contractors, and using them to fill these growing skills deficits. Success with these strategies depends on widening talent pools. Due to inadequate elementary and high school preparation, too many young Americans do not have the educational foundation needed to succeed in today’s high-tech jobs and careers. Reform needs to begin at these early educational levels. Businesses need to develop career information programs in elementary schools that highlight the new jobs created by the Fourth Industrial Revolution and how to prepare for them. They also need to expand partnership programs with secondary and post-secondary educational institutions. Career academy high schools can allow local businesses to help students explore how well their interests and skills fit employment opportunities. Apprenticeship, internship, and work-study programs must be implemented in more industry sectors. Business leaders must deploy these and other strategies prioritizing human capital development. To make this succeed, Regional Talent Innovation Networks can help business leaders collaborate with other community sectors to reinvent local and regional education-to-employment systems. RETAINs provide the framework for long-term systemic transformation that sustains talent growth that benefits individuals, businesses, and U.S. economic competitiveness. About the Author: Edward E. Gordon is the founder and president of Imperial Consulting Corporation in Chicago. His firm’s clients have included companies of all sizes, from small businesses to Fortune 500 corporations, U.S. government agencies, state governments, and professional/trade associations. He taught in higher education for 20 years and is the Author of numerous books and articles. More information on his background can be found at www.imperialcorp.com. As a professional speaker, he is available to