H&E opens New Branch in Amarillo, TX
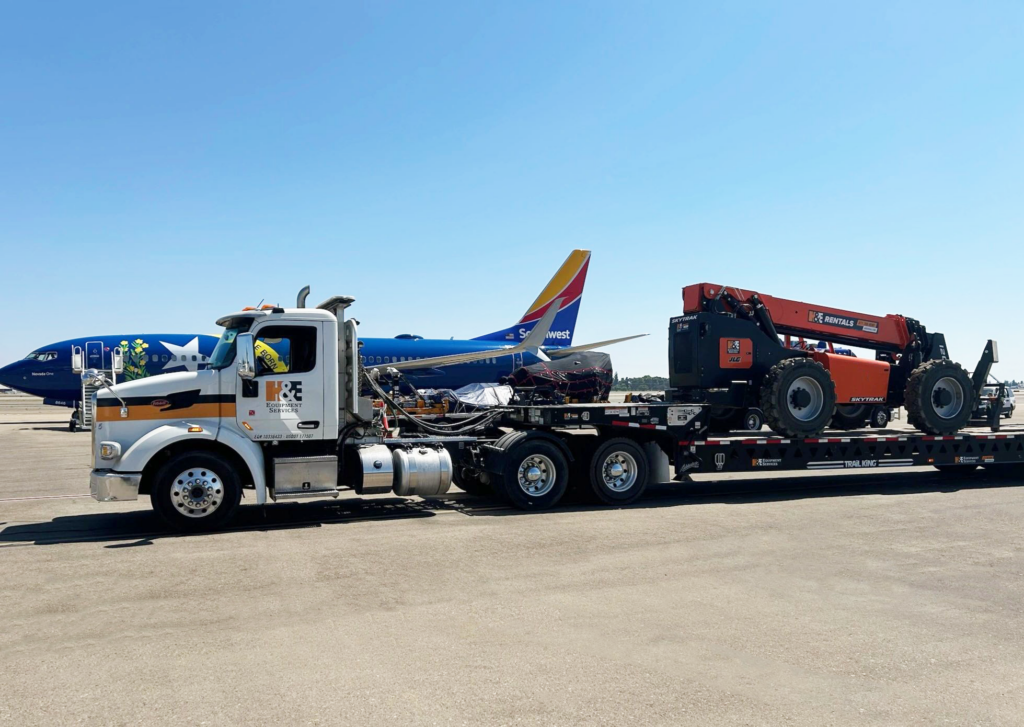
H&E Rentals has announced the opening of its Amarillo branch, the company’s 30th location in the state of Texas. H&E has opened 25 new branches across the country and acquired nine others since the second quarter of last year, and it has operations in 32 states. The facility is located at 12828 I-27, Amarillo, TX 79119-2507, phone 806-718-7900. It includes a fully fenced yard area, offices, and a repair shop and carries a variety of construction and general industrial equipment. “The positioning of a new branch in Amarillo gives H&E complete coverage of the Texas Panhandle that stretches across the New Mexico state line. We now have greater reach above our existing Lubbock branch, which allows H&E to better serve the West Texas market, and we’ve reduced the distance between our Albuquerque and Oklahoma City locations,” says Branch Manager Nick Ohman. “Our facility is directly on the I-27 frontage road and just a short drive from I-40. That strategic location allows us to efficiently move equipment from an expanded local fleet to job sites stretching from the Oklahoma state lines and down across State Highway 86. We’re in a great place to help customers across the entire panhandle.” The Amarillo branch specializes in the rental of aerial lifts, earthmoving equipment, telescopic forklifts, compaction equipment, generators, light towers, compressors, and more and represents the following manufacturers: Allmand, Atlas Copco, Bomag, Case, Club Car, Cushman, Doosan, Gehl, Generac Mobile, Genie, Hamm, Hilti, Husqvarna, JCB, JLG, John Deere, Kobelco, Kubota, LayMor, Ledwell, Lincoln Electric, Link-Belt Excavators, MEC, Miller, Multiquip, Polaris, Sany, Skyjack, SkyTrak, Sullair, Sullivan-Palatek, Tag, Towmaster, Unicarriers, Wacker Neuson, Yanmar, and others. Founded in 1961, H&E is one of the largest equipment rental companies in the nation, providing the higher standard in equipment rentals. Branches are located throughout the Pacific Northwest, West Coast, Intermountain, Southwest, Gulf Coast, Southeast, Midwest, and Mid-Atlantic regions.
Bobcat celebrates $3.26M renovation at Buford facility
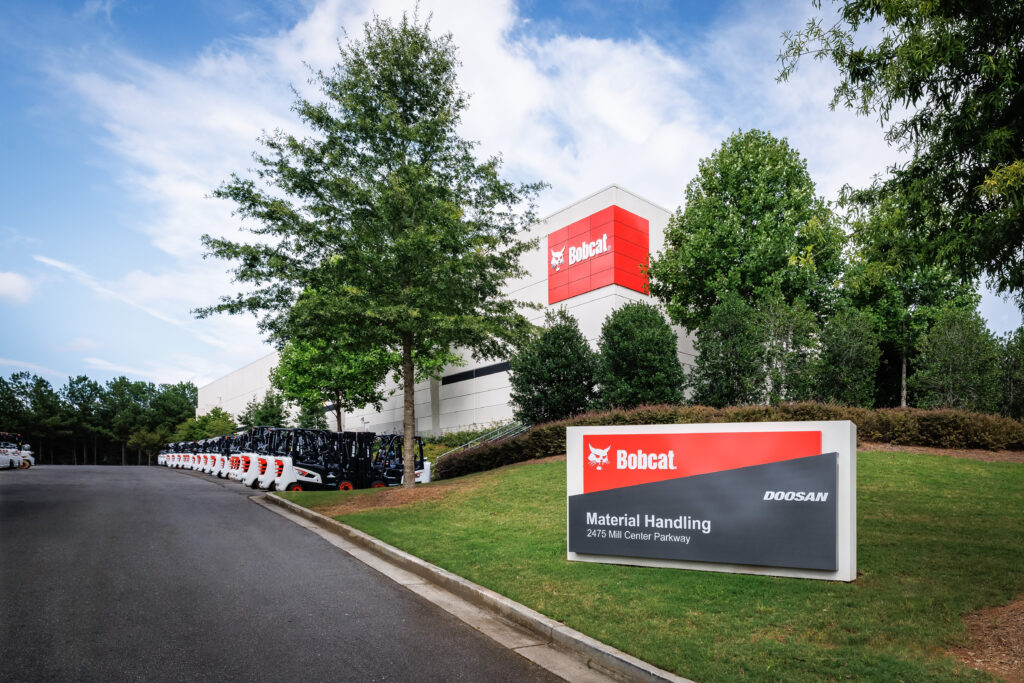
Bobcat Company recently brought material handling into the Bobcat brand, transitioning from Doosan Industrial Vehicle to Bobcat in early 2024. The investment in the Buford facility modernized conference rooms, break rooms and office spaces, improved the interior design, finishing and furnishing to align with other Bobcat locations, and updated exterior signage. Featuring open seating and no cubicles, the enhanced spaces support cross-functional teamwork and engagement. “Investing in our facilities and operations to create collaborative, inspiring workplaces is one of many ways that Bobcat supports our employees,” said Mike Ballweber, president, Doosan Bobcat North America. “Fostering our company’s success alongside the dedicated team in Buford is a priority for us. We are thrilled to provide them with a work environment that encourages collaboration and drives innovation.” The 200,000-square-foot Buford facility houses a state-of-the-art parts operation which supplies over 30,000 line items to support its affiliate groups. Additionally, the material handling product line includes 179 separate models with a full range of diesel, gas, liquid propane gas and electric forklifts, with capacities ranging from 3,000 to 55,000 pounds. “The growth of the Bobcat brand into the material handling industry allows us to provide even more solutions to help our customers accomplish more,” said Jarrod Steck, Bobcat vice president of material handling products. “Our Buford team has grown by 40 percent in the last year and is still growing. Bobcat’s investment in both people and facility illustrate our level of commitment to growing Bobcat’s presence in this important market.” More than 180 employees work at the Buford location – a significant increase since 2022. Employment opportunities are available in product support, sales administration and product and parts areas. Shultz + Associates Architects supported the architecture plans, while Omega Construction served as the general contractor of the facility renovations. In addition to its operations in Buford, Bobcat has an extensive presence throughout the U.S., as well as globally.
Manufacturing Technology Orders Grow 4.3% in June 2024 as Year-Over-Year Order Gap Narrows
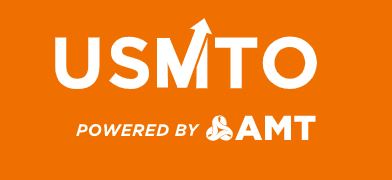
Orders of manufacturing technology, measured by the U.S. Manufacturing Technology Orders Report published by AMT – The Association For Manufacturing Technology, totaled $386.7 million in May 2024. Orders of manufacturing technology, measured by the U.S. Manufacturing Technology Orders (USMTO) report published by AMT – The Association For Manufacturing Technology, totaled $402.3 million in June 2024. New orders of metalworking machinery were up 4.3% from May 2024 but down 1.6% from June 2023. Year-to-date orders reached $2.2 billion, down 10.7% compared to the first half of 2023. While the value of orders maintained momentum in June 2024, with the average value increasing significantly, the number of units ordered for the month dropped to 1,471 units, the lowest since July 2023. This divergence indicates manufacturers are generally investing in more automated, task-specific solutions. This trend is further confirmed, as inflation among machine tools, measured by the producer price index, has stayed relatively flat for the last several months. June 2024 orders from contract machine shops dropped over 10% from May 2024 in both the number of units ordered and the total order value. Through the first half of the year, the value of these orders was the lowest since the first half of 2020, but the number of units ordered fell further, reaching its lowest level since the first half of 2010. Primary metal manufacturers have also pulled back machinery orders in 2024, dropping to the lowest levels in both unit count and value since the first half of 2010. Demand for machinery in this sector has been waning, as the World Steel Association reports that global steel production in the first half of 2024 was flat compared to the first half of 2023. One notable exception to this recent trend is the aerospace sector, which has increased orders in the first half of 2024 to the highest number of units since the first half of 2018, yet the value of orders remains about 2% below orders placed in the first half of 2022. With capacity utilization in the aerospace sector reaching post-COVID peaks, this confirms that these manufacturers are in need of additional machinery to meet growing demand. Orders of manufacturing technology are down nearly 11% in the first half of 2024 compared to 2023, but that difference has narrowed in the past several months after the beginning of the year failed to meet the optimistic expectations formed from anticipated interest rate cuts and strengthened consumer and business sentiment. Despite the lingering uncertainty around the Federal Reserve’s interest rate policy, the pending election, and escalating geopolitical tensions, the remainder of 2024 seems ready for a rebound in demand for manufacturing technology – perhaps even more so with the opening of IMTS 2024 – The International Manufacturing Technology Show in September at Chicago’s McCormick Place.
Episode 510: Addressing lost and stolen packages with Deliverlitics
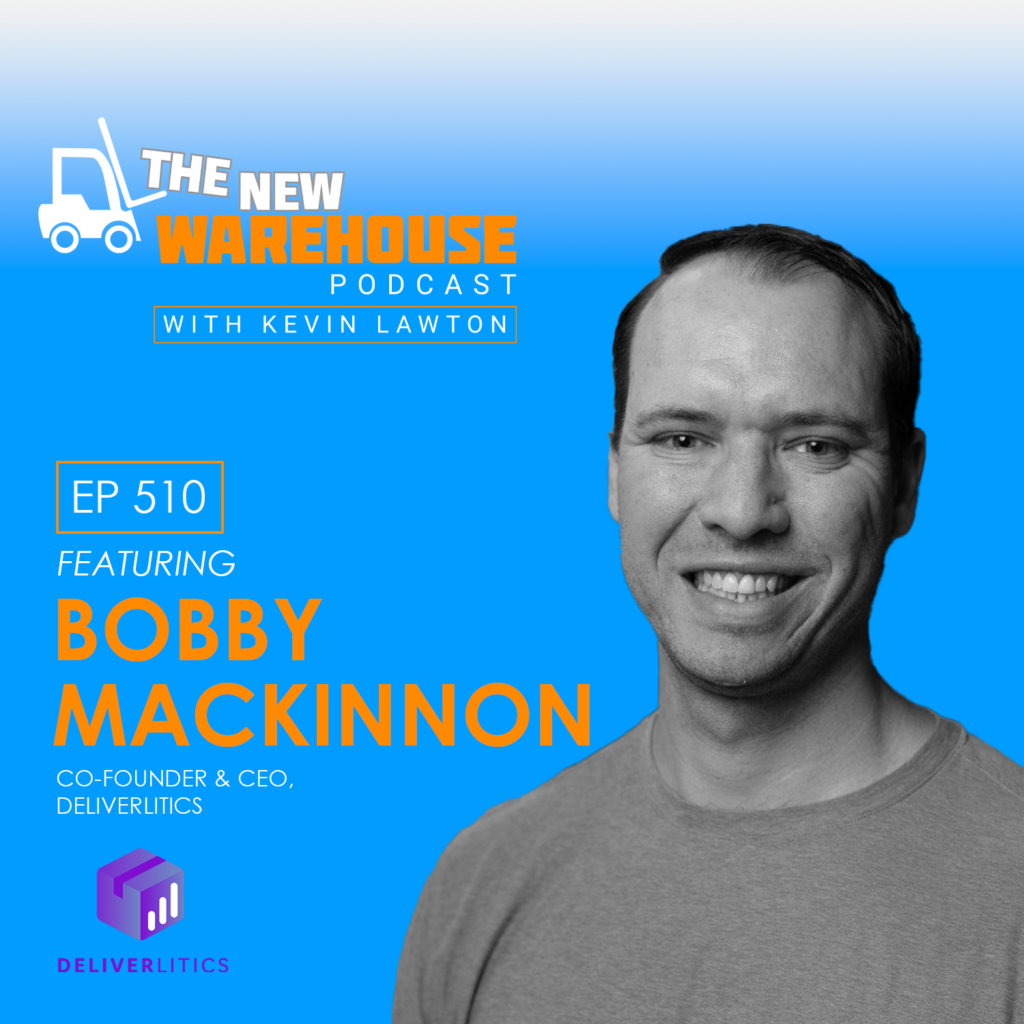
Today’s episode of The New Warehouse Podcast features Bobby McKinnon, Co-Founder and CEO of Deliverlitics. Deliverlitics is dedicated to solving a significant issue in the delivery and e-commerce industry: lost and stolen packages. With increased e-commerce activities, this problem has become more prevalent, impacting consumers and businesses. Bobby shares insights on how Deliverlitics leverages AI to tackle this challenge effectively. Bobby McKinnon’s Journey to Deliverlitics Bobby McKinnon’s background is diverse and impressive. After spending half a decade as an Army logistics and supply chain officer, he transitioned to the corporate world, gaining experience at Nike and a blockchain data analytics startup. His military experience, particularly in high-pressure logistics environments, equipped him with the skills to lead and innovate in the supply chain sector. “The military gave me a set of tools and passions for leading organizations that have pushed me to where I am today,” Bobby explains. His journey culminated in co-founding Deliverlitics, driven by a desire to address the pervasive issue of lost and stolen packages. The Problem of Lost and Stolen Packages The rise in e-commerce has exacerbated the issue of lost and stolen packages, creating significant challenges for retailers and consumers alike. Bobby categorizes the problem into three main areas: misplaced items, package theft, and first-party fraud. “Somewhere in the neighborhood of $15 to $20 billion is what it’ll end up being lost or stolen this year across all of e-commerce,” he notes. Examples like the man dressed as a trash bag stealing packages highlight the creativity of thieves. Moreover, first-party fraud, where customers falsely claim packages are missing, adds to the financial burden on businesses. Deliverlitics’ AI-Driven Solution Deliverlitics addresses these challenges through innovative AI solutions. By analyzing vast amounts of data, they predict and mitigate the risk of package loss and theft. This analysis allows them to provide specific recommendations to mitigate the identified risks. Bobby elaborates, “AI allows us to sift through these things, find the points of correlation, find the things that are causing these events to occur or contributing to their propensity to happen. And then we can predict them.” Their Shopify plugin, for example, assesses the risk of each order in real-time, providing recommendations like adding signature verification or redirecting to a secure location. This proactive approach protects businesses and enhances the consumer experience by reducing friction and maintaining trust. Key Takeaways Innovative AI Solutions: Deliverlitics uses AI to analyze data and predict risks associated with package delivery. Significant Financial Impact: The e-commerce industry loses billions annually due to lost and stolen packages. Proactive Recommendations: Their system provides real-time recommendations to mitigate risks, improving both business operations and customer satisfaction. The New Warehouse Podcast Episode 510: Addressing Lost and Stolen Packages with Deliverlitics
Register For SuperCorrExpo® Today!
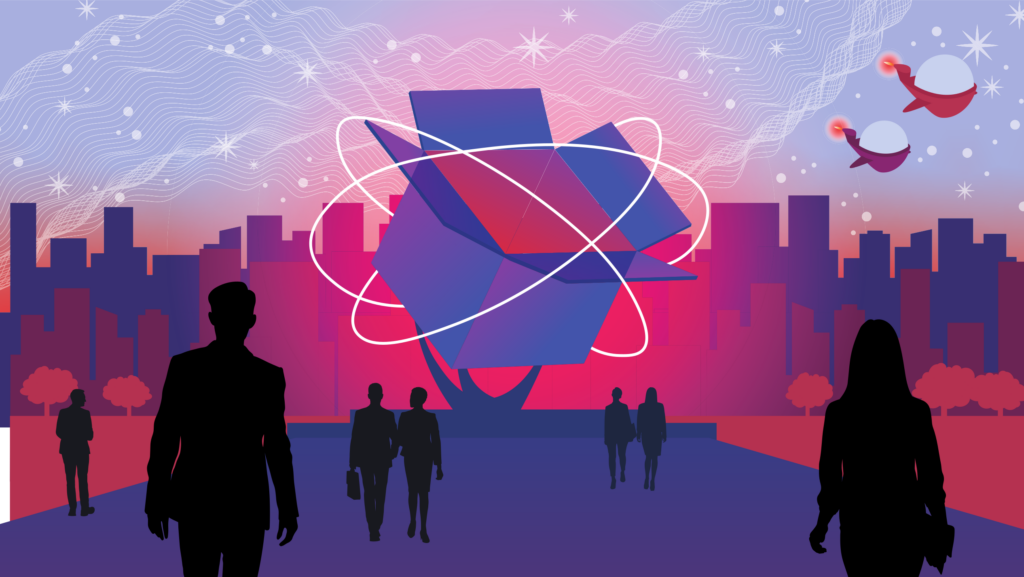
SuperCorrExpo®, taking place September 8-12 in sunny Orlando, Florida, will feature North America’s largest display of working equipment for the corrugated and folding carton industries. With the rare opportunity to see, touch and demo working equipment right on the show floor, attendees can gain firsthand experience and insights into the latest technological advancements and innovations driving the industry forward. Over 300 companies will be exhibiting at SuperCorrExpo®. Industry leaders from across the globe will be showcasing working machinery, including: A.G. Stacker, Baysek Machines, EAM-Mosca, Eco Paper Machinery, Engineered Recycling Systems, Fosber America, Geo. M. Martin, Global Boxmachine, Haire Group, Innoveyance, Kolbus America, Mainline Conveyor Systems, Samuel Packaging Systems Group, Shenzhen HanGlory Digital Printing Group, Signode, Solema USA, Stitching and Gluing Solutions, SUN Automation Group, TCY, TISCO/ HARPER/ ALLTEK, and WSA USA. Thousands will be attending to take advantage of the unparalleled educational and networking opportunities available as SuperCorrExpo®. The world’s leading box plants are looking to gain the tools and expertise to equip their businesses for the future. The list of attendees is available here. Don’t get boxed out! Register today to join the world’s professionals in paving the way for the future of the corrugated industry.
AutoScheduler.AI wins NextGen Solution Provider Award in Artificial Intelligence Category
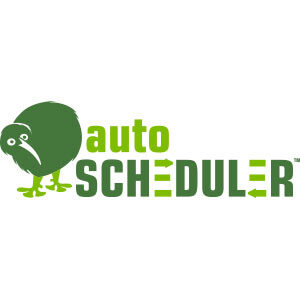
NextGen Supply Chain Conference Awards Recognize Companies Shaping Tomorrow’s Supply Chains AutoScheduler.AI, an innovative Warehouse Orchestration Platform and WMS accelerator, has announced the company is named a winner in the Artificial Intelligence category of the NextGen Solution Provider Awards. The NextGen Solution Provider Awards honor up to four solution providers that have utilized NextGen supply chain technologies in a project implemented for a customer in the following categories: Robotics, Digital Transformation, Artificial Intelligence, and Predictive Analytics. “We are proud to win this prestigious award for our AI-enabled technology that takes disparate data and converges supply chain activities to create plans that orchestrate campus operations for optimized efficiency prescriptively,” says Keith Moore, CEO of AutoScheduler.AI. “Our clients’ warehouses operate at peak performance.” The NextGen Supply Chain Conference Awards recognize the companies shaping tomorrow’s supply chains with advances that are helping organizations navigate the complexities of the modern supply chain while also preparing them for success in the future. Winners will be presented their award at the conference which takes place in Chicago, October 21-23, 2024, at the Chicago Athletic Association. Moore adds, “Our technology smooths warehouse operations by orchestrating and planning all activities in real-time on top of an existing WMS. It considers space, time, labor, dock doors, and more constraints to ensure that orders are fulfilled on time and in full. Clients gain efficiencies and value in their supply chains through optimized labor, schedules, touches, and inventory.” AutoScheduler’s AutoPilot converges disparate data to orchestrate supply chain activities and optimize campus operations. By integrating data from WMS, yard management systems, ERP, visibility systems, and production schedules, it creates a unified view of operations. Utilizing operational twin technology, AutoPilot predicts future states by analyzing current conditions and planned activities across systems. It employs complex mathematics, AI, and optimization techniques to determine the most efficient use of capacity. This approach optimizes activity systems, prescribes event sequences, and creates a feasible operational schedule, minimizing touches and labor while maximizing service levels.
Dematic has announced 2024 STEM Scholarship Winners
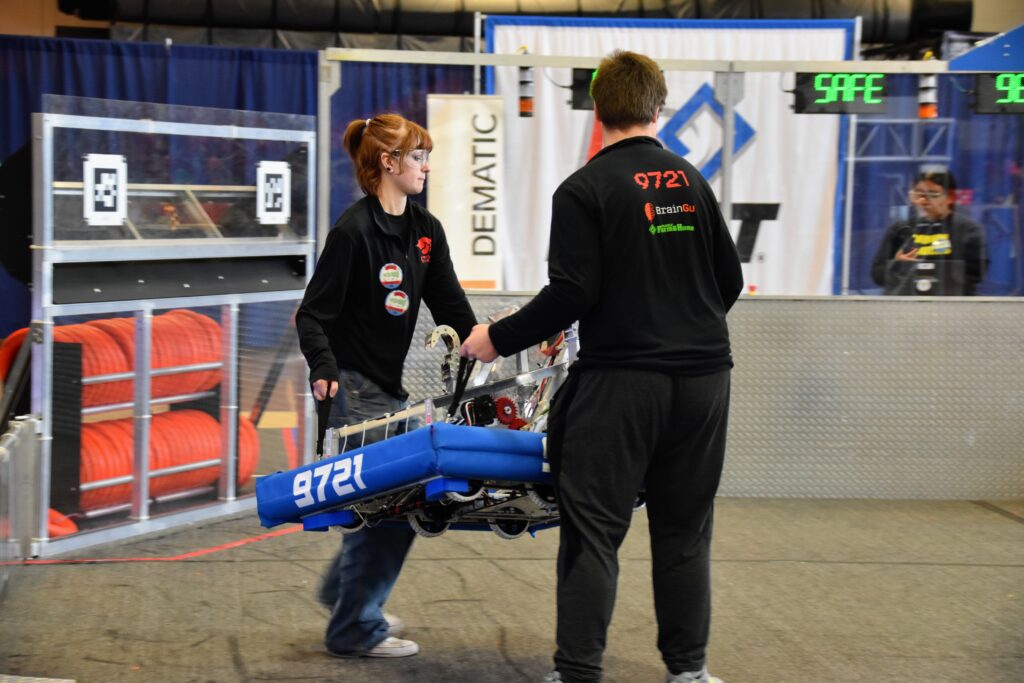
12 Students Awarded Dematic FIRST® Scholarships to Pursue STEM Education Dematic has announced the winners of the 2024 Dematic FIRST® Scholarship program, which recognizes students dedicated to pursuing careers in STEM (science, technology, engineering, and mathematics). In partnership with the corporate nonprofit FIRST (For Inspiration and Recognition of Science and Technology), this scholarship program underscores Dematic’s commitment to nurturing the next generation of leaders and innovators in the supply chain and logistics industry. This year’s scholarship recipients include students Aman Amjad from Brookfield, Wisconsin, and Lily Hoopes from Bonney Lake, Washington, who were both awarded $5,000 to support their post-secondary education or technical certification. Dematic also awarded $1,000 scholarships to 10 additional students: Blake Bollow, Noelle Bryan, Casey Bushey, Allie Cadenhead, Rafael Calderon, Adriana Cruz, Jason Elisei, Bill Giang, Hendrik Sorensen, and Adam Thai. “This year’s Dematic FIRST scholarship winners are truly exceptional,” says Mike Larsson, President of Dematic and Executive Board Member of KION Group. “The skills and experiences they’ve gained through the FIRST program will propel them not only to successful careers in STEM but also to becoming future leaders. The high caliber of this year’s applicants highlights our need for continued investment in STEM education. By empowering these future leaders, we’re paving the way for the next generation.” Now in its fourth year, the Dematic FIRST scholarship program attracted applications from students across 28 states, Washington, D.C., and Canada. Dematic executives reviewed all applications, selecting honorees based on their academic excellence and commitment to pursuing a future in STEM. The program requires applicants to provide their transcripts, a one-page essay discussing a future where humans and machines interact in the warehouse, and a letter of recommendation. In addition, they must have previously competed in a FIRST Robotics Competition or FIRST Tech Challenge. “Being awarded the Dematic FIRST Scholarship is an incredible honor as I advance my education at Georgia Tech and embark on my career,” says Amjad. “Participating in FIRST during high school ignited my passion for STEM, and I’m grateful to Dematic for supporting my studies. FIRST and Dematic encourage students to explore real-world careers through teamwork, education, and robotics. Thank you for opening doors to opportunities, including early workforce exposure and access to advanced technology.” Dematic is dedicated to supporting FIRST and its mission to engage youth to become skilled professionals, creative thinkers, and well-rounded citizens. Dematic employees actively contribute to FIRST teams by providing mentorship and guidance to students helping to foster their development. Last year, Dematic sponsored 18 FIRST teams and donated $68,000 to support students as they prepared for competitions and careers in STEM. Since 2008, Dematic has sponsored teams participating in FIRST robotics competitions and invested more than $310,000 in local teams, events, and student scholarships, demonstrating an unwavering commitment to nurturing the next generation of STEM professionals. To learn more, visit dematic.com. Scholarship Winners:
IDEC ez-Wheel Assist Wheel Drive Boosts material handling operations
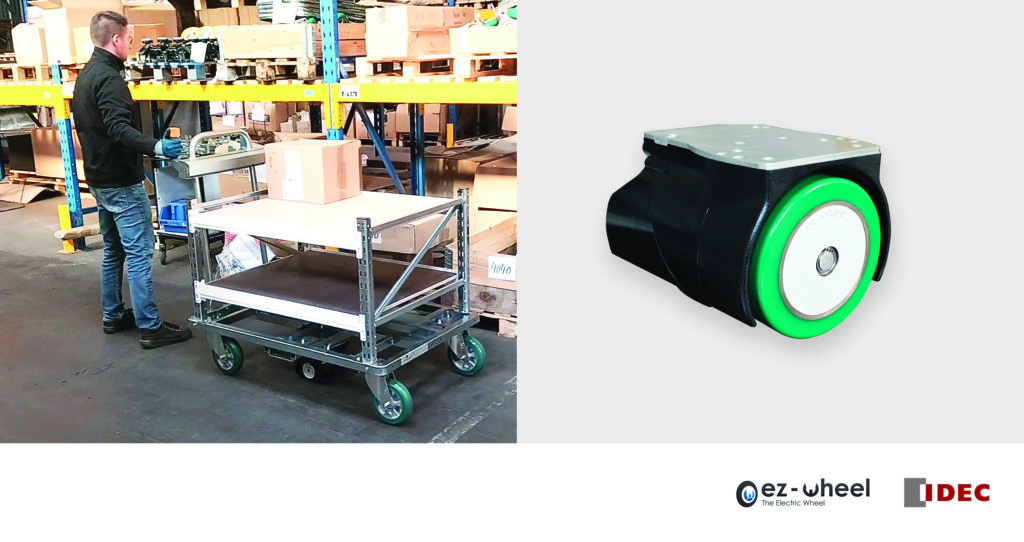
The modular all-in-one wheel, gearbox, drive, battery, and control solution is easily integrated into new or existing equipment to help workers safely transport heavy payloads. IDEC Corporation announced the new ez-Wheel Assist Wheel Drive (AWD) EW1A Series, providing electrical motion assistance for industrial manual material handling equipment. With the help of an EW1A, workers can easily and safely move heavy loads, increasing productivity and efficiency. Even in highly automated facilities, there remain many operations requiring personnel to exert manual force to move trolleys, carts, and other mobile equipment. Besides the physical challenge, workers could also be susceptible to injuries or other musculoskeletal issues while performing these tasks. The EW1A addresses this and other issues with an integrated electric motorized wheel solution that is easily retrofitted onto existing trollies or designed into new equipment. Power and control options The EW1A system consists of a few modular components, with many options to satisfy new equipment designs, or aftermarket retrofits by maintenance personnel. The main drive unit is available with 150mm or 160mm resilient polyurethane wheels, and the ability to support a vertical working load up to 400kg, and to transfer loads up to 1000kg. A suspension bracket provides an adaptable way to add the main drive unit to upgrade any equipment. All models can accept internal batteries, which are recharged with a specific cable and charger. However, for greater capacity designers can alternately choose to use an external battery pack using an adapter cable. Batteries operate at a nominal 24V DC, with capacities ranging from 3Ah to 15Ah, depending on the model. The wheels operate at about 0 to 5km/hr (0 to 3mph) in both directions and are available with adjustable braking modes and an option parking brake. The wheels are rated for indoor use, in non-freezing temperatures and up to 40°C. Two controller options are available. The standard controller is a compact panel, much like a pendant control but fixed-mounted, with an on/off button, forward/reverse speed control thumbwheel, and a lighted or unlighted emergency stop button. A two-handle-type controller is also available with the same functionality implemented into a pair of handles, which can be oriented vertically or horizontally as needed for the best user experience. The handle-type controller is available with or without a battery charge status LED indicator. Convenient ez-Config software running on a PC and connected using a standard USB cable lets users easily configure operating parameters, such as forward/reverse speed, acceleration time, deceleration mode, assist time limit, time to sleep mode, and more. Progressive safety and efficiency Companies everywhere need solutions for improving the safety and efficiency of their workers, helping them comply with standards like ISO 11228-2 for ergonomics, and potentially reducing insurance costs. The IDEC ez-Wheel Assist Wheel Drive EW1A Series meets these needs as the world’s first 100% integrated industrial autonomous wheel, combining the wheel, gearbox, drive, battery, and control solution in a compact and modular form factor. It is easily retrofitted on any existing moving equipment as an aftermarket solution, to upgrade and update working capabilities. Applications abound anywhere equipment or payloads are manually moved, in warehouse and material handling facilities, automotive plants, logistics/retail, manufacturing, construction, food and beverage, and more. With an attractive price/performance ratio, end users of all types can deploy the EW1A to improve worker health while increasing productivity and efficiency, often realizing a return on investment of less than one year.
Kenco to install AutoStore at Jeffersonville, Indiana Distribution Center
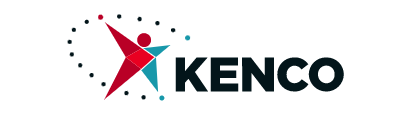
With systems integration partner KPI Solutions, Kenco’s new automated storage and retrieval system will shorten click-to-delivery times for the 3PL’s eCommerce customers starting this summer Kenco has announced the implementation of AutoStore™ at the company’s Jeffersonville, Ind. distribution center. Set to go live in summer 2024, the AutoStore system – designed and implemented by KPI Solutions – will service Kenco’s eCommerce customers and open the door for businesses of all sizes to access a technology typically only available to larger companies. Once complete, the AutoStore system will include 49,000 bins, 130 grid robots, 10 picking ports and four replenishment ports. Kenco estimates 15 million units will travel through the system per year. The announcement reinforces Kenco’s dedication to automation and warehouse transformation, coming on the heels of Kenco’s introduction of Automation Guidance. A part of their comprehensive Material Handling Solutions offering, this consultative offering will help clients upgrade existing facilities with automated material handling equipment assets to meet today’s warehouse needs. “At Kenco, we’re dedicated to continuously improving our operations,” said Jason Minghini, Senior Vice President of Operations at Kenco. “By implementing AutoStore’s proven solution, not only are we optimizing our space and workforce, we’re taking our eCommerce fulfillment solutions to the next level by providing even shorter click-to-delivery times for all customers in this market.” Jeffersonville is Kenco’s second AutoStore installation. While the first serves a single client, the newest installation is larger and will efficiently process orders from multiple customers for an optimized operation. “The system and reserve storage will take up about one-fourth of one of the facilities on our campus,“ said Jeffersonville Senior Director of Site Logistics, Bill Dragoo. “Installation is going smoothly, and we’re excited to see the full benefits of the solution come to life this summer.” As an ASRS, AutoStore harnesses the power of warehouse robots for 24/7 order fulfillment within a cubic layout up to quadruple the storage capacity of traditional warehouse racking. The goods-to-person (G2P) system maximizes existing labor and space, reinforcing supply chain dependability. “We are proud and happy to partner with Kenco to manage their warehouse space innovatively and efficiently, empowering their customers to achieve incredible results,” said Mike Harding, Account Executive at KPI Solutions. “This AutoStore system will boost labor productivity and enable scalability while improving delivery times for consumers across North America.”
Olvi Brewery expands with second automated warehouse from Cimcorp
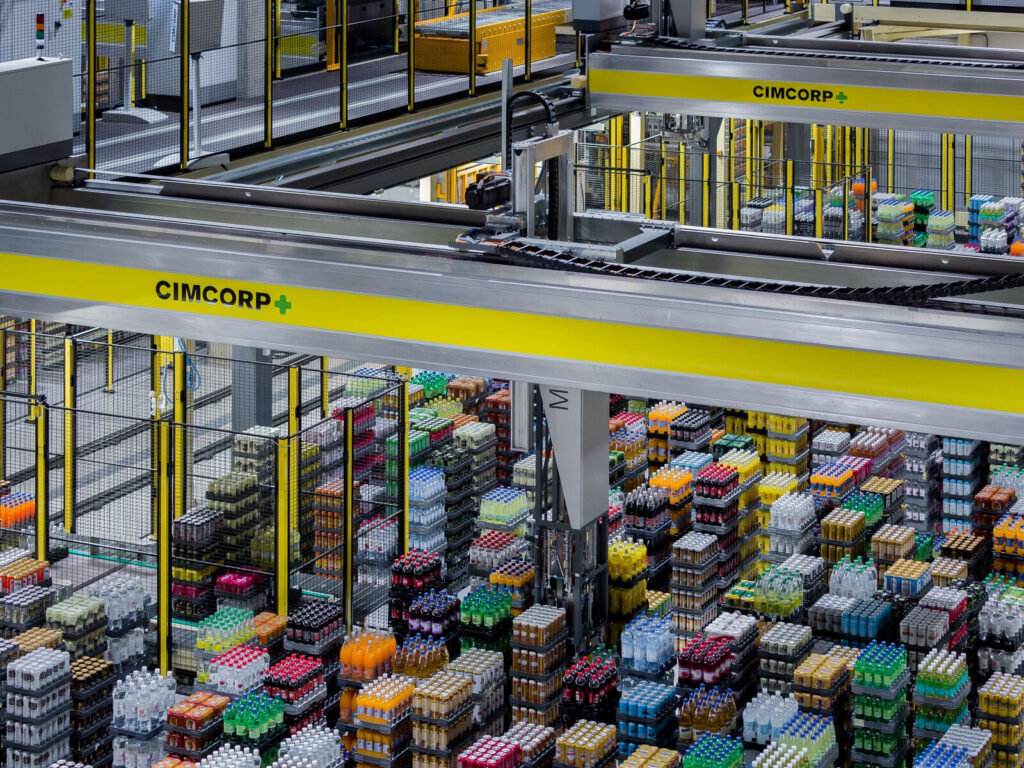
Cimcorp’s automation boosts storage capacity and enhances operational efficiency, helping the Finnish brewery handle growing production volumes and seasonal demands Cimcorp has announced it has supplied a new high-bay automated warehouse to its longtime customer Olvi , one of the leading beverage producers in Finland and the Baltic region. This is the second automated warehouse Cimcorp has implemented at Olvi’s headquarters in Iisalmi, Finland, cementing a strong partnership spanning nearly two decades. By providing more storage capacity, the new automated warehouse supports Olvi’s growing production volumes and levels out the seasonal demands of the brewing industry. In the beverage industry, demand swings dramatically between seasons, with the potential to cause bottlenecks in production and distribution on peak days. At Olvi, Cimcorp’s automation mitigates these risks and enhances operational capabilities, ensuring the brewery can better manage inventory and ultimately provide superior service to its customers. Benefits of Cimcorp’s high-bay automated warehouse include: Increased efficiency and throughput: Automated storage and retrieval systems (AS/RS) quickly and accurately move products in and out of storage, speeding up the picking process. The warehouse can also operate 24/7 without the need for breaks. Improved customer satisfaction: Increased speed and accuracy in order picking lead to faster fulfillment times, complete order accuracy, less product damage, and enhanced customer satisfaction. Space optimization: The high-bay warehouse utilizes vertical space, allowing for greater storage capacity within a smaller footprint. This enables a wider product range. “Our existing high-bay warehouse was implemented with Cimcorp in 2014. This second warehouse enables us to increase storage capacity and secure the reliability of deliveries for our customers, especially during seasonal peaks. We need to be agile and respond to the fast order-delivery rhythm whenever the sun starts shining,” said Ilkka Heikkilä, Logistics Supervisor at Olvi. “We appreciate Cimcorp’s reliability and technical solutions that are tailored to our needs. Having a local partner who understands our ways of working and production needs—without compromising the daily output—is invaluable.” The partnership between Cimcorp and Olvi began in 2005 when Cimcorp installed an automated order-picking system featuring gantry robots for the brewery. Collaboration between the companies has continued over the years, including installing the original high-bay warehouse with a Warehouse Control System (WCS), an innovative keg-picking solution, and a robotic dolly-picking system. To support its automation, Olvi utilizes Cimcorp’s 24/7 helpdesk service, benefiting from support in Finnish and in the same time zone. Cimcorp’s helpdesk team is knowledgeable and familiar with Olvi’s systems and processes, allowing them to provide the exceptional service and proactive maintenance needed to ensure reliability throughout the system’s entire lifecycle. “Our fruitful collaboration with Olvi spans nearly 20 years,” said Riku Puska, Sales Manager, Warehouse & Distribution, Cimcorp Group. “Designing future development and innovating together have been the cornerstones of this partnership. Being available for our customers 24/7 and responding quickly to any requests are very important to us. Delivering peace of mind is part of our DNA.”
Cyngn reports Second Quarter 2024 financial results
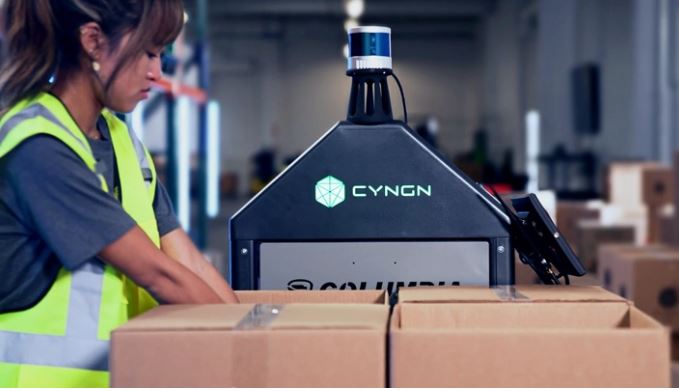
Recent Operating Highlights: Joined John Deere supply base Rolled out a partnership with RobotLAB, adding the autonomous DriveMod Tugger vehicles to its portfolio of 200+ robots Received a notice of allowance for a 20th U.S. patent and 21st U.S. patent for its AI-powered autonomous vehicle solutions Highlighted its proprietary computer vision advancements with NVIDIA accelerated computing Expanded the Cyngn Dealer Network to include Alta Equipment Group, with more than $1 billion in annual sales Cyngn, developer of industrial autonomous vehicles, today announced financial results for its second quarter, which ended Jun 30, 2024. “During the second quarter, we continued the momentum we made in Q1, marked by rapid strides toward broad commercialization,” said Cyngn CEO Lior Tal. “In addition to the progress we made with John Deere, another key priority has been to expand our sales channels to access more opportunities via established dealers and partners. We are well on our way toward bringing Cyngn’s autonomous industrial vehicle products to even more facilities by partnering with experienced material handling and automation leaders like Motrec, Alta, and RobotLAB. “Our expanding dealer network yields channels that consistently deliver commercial opportunities. On the advertising side, we doubled the number of marketing-sourced leads and decreased the acquisition cost of these opportunities by 67%. “Overall, our pipeline is very healthy. We continue to make progress with automotive manufacturers and their tier-1 suppliers, defense contractors, and heavy equipment manufacturers. We are largely engaging with known brands in the Fortune 500, and we will continue to work closely with our customers to share these exciting logos with the public when we can.” “Autonomous vehicle deployments have a long sales cycle,” said Ben Landen, VP of Business Development. Vehicles need to be put through their paces at customer facilities to ensure they will operate as reliably and safely as a well-trained human driver. Cyngn passes this test easily, but it takes time. These big organizations with well-established workflows need to see for themselves that Cyngn vehicles are the best employees they’ve ever had. “By all accounts, this process is working. Our pipeline is growing, we keep adding industry veterans with extensive experience to our sales team, and we have the resolve and partners to stay the course in our pursuit of the significant industrial automation market in front of us. “We look forward to providing additional updates and continuing to increase momentum.” “Regaining compliance with Nasdaq’s minimum bid price was a significant priority,” added Don Alvarez, Cyngn’s CFO. “Our balance sheet remains clean with no debt, and these factors underscore our financial health and position us favorably as we move forward. Our solid foundation and strategic direction are positioning us for a successful future.” When reviewing the financial information below, note that all share and per share information, Common stock, and Additional paid-in capital have been restated to reflect the 1-for-100 reverse stock split effected on July 3, 2024. Q2 2024 Three-Month Financial Review: The second quarter’s revenue was $8.7 thousand compared to $550.9 thousand in the second quarter of 2023. In the second quarter of 2024, revenue consisted of EAS software subscriptions from DriveMod Stockchaser vehicle deployments, whereas prior year revenue resulted from NRE contracts. Total costs and expenses in the second quarter were $5.8 million, down from $7.0 million in the second quarter of 2023. This decrease was primarily due to a $447.7 thousand decrease in cost of revenue, a $239.1 thousand reduction in G&A expenses, and a decrease in R&D expenses of $538.7 thousand. The decrease in the cost of revenue is driven by the lower costs associated with EAS revenue compared to the NRE contracts in 2023. The decrease in G&A expenses is due to a decrease in personnel costs, reduced premiums for Director and Office Liability Insurance, and spending improvements on general office expenses. The decrease in R&D expense was primarily driven by capitalizing costs for specific customers and capitalizing costs related to the development of software. The headcount at the end of the second quarter of 2024 was 85 versus 75 at the end of the second quarter of 2023. Net loss for the second quarter was $(5.8) million, compared to $(6.4) million in the corresponding quarter of 2023. The second quarter of 2024 net loss per share was $(4.11), based on basic and diluted weighted average shares outstanding of approximately 1,416.8 thousand. This compares to a net loss per share of $(12.97) in the second quarter of 2023, based on approximately 489.9 thousand basic and diluted weighted average shares outstanding. Q2 2024 Six-Month Financial Review: Year-to-date second-quarter revenue was $14.2 thousand, compared to $1.4 million in the second quarter of 2023. Second-quarter 2024 revenue consisted of EAS software subscriptions from DriveMod Stock chaser vehicle deployments, whereas prior-year revenue was the result of NRE contracts. Total costs and expenses in the second quarter were $11.8 million, down from $13.8 million in the second quarter of 2023. This decrease was primarily due to a $950.6 thousand decrease in cost of revenue, a $606.6 thousand reduction in G&A expenses, and a decrease in R&D expenses of $414.1 thousand. The decrease in the cost of revenue is driven by the lower costs associated with EAS revenue compared to the NRE contracts in 2023. The decrease in G&A expenses is due to a decrease in personnel costs, reduced premiums for Director and Office Liability Insurance, and spending improvements on general office expenses. The decrease in R&D expense was primarily driven by capitalizing costs for specific customers and capitalizing costs related to the development of software. Net loss for the second quarter was $(11.8) million, compared to $(12.0) million in the corresponding quarter of 2023. The second quarter of 2024 net loss per share was $(12.15), based on basic and diluted weighted average shares outstanding of approximately 970.3 thousand. This compares to a net loss per share of $(24.48) for the first six months of 2023, based on approximately 489.4 thousand basic and diluted weighted average shares outstanding during the period. Balance Sheet Highlights*: Cyngn’s cash and short-term investments at June 30, 2024, total
The Manitowoc Company reports Second-Quarter 2024 financial results with net sales down 6.8% year-over-year

Today, the Manitowoc Company, Inc. reported a second-quarter net income of $1.6 million, or $0.04 per diluted share. Second-quarter adjusted net income (1) was $8.8 million, or $0.25 per diluted share. Net sales in the second quarter decreased 6.8% year-over-year to $562.1 million and were unfavorably impacted by $2.7 million from changes in foreign currency exchange rates. In the second quarter, adjusted EBITDA (1) was $36.0 million, a decrease of $24.4 million or 40.4% from the prior year. Orders in the second quarter were $428.4 million, a 22.2% decrease from the prior year. This resulted in a backlog of $836.3 million at the end of the second quarter. Orders were unfavorably impacted by $2.0 million from changes in foreign currency exchange rates. “During the second quarter, we faced a variety of operational issues which led to lower-than-anticipated results. In addition, the Tower Crane business in Europe remained a headwind to our results. Order intake was sluggish for mobile cranes in Europe and North America. Mobile customers have been slow to commit to new cranes in the face of the uncertainties associated with the upcoming U.S. election and the continued higher interest rate environment. Looking at the balance of the year, we expect weaker demand to continue. As a result, and with a focus on inventory reductions to generate free cash flow, we took actions to adjust our build schedules in the second half. We have updated our full year guidance accordingly,” commented Aaron H. Ravenscroft, President and Chief Executive Officer of The Manitowoc Company, Inc. “CRANES+50 is the driving force in our transformation as a stand-alone crane company. Since its launch, our non-new machine sales have grown 34%, expanding our higher margin, recurring revenue streams. We remain focused on continuous improvement through The Manitowoc Way and growing our aftermarket through CRANES+50 to drive long-term shareholder value,” added Ravenscroft. Updated Full-Year 2024 Guidance Manitowoc is updating its full-year 2024 guidance as follows: Net sales – $2.175 billion to $2.225 billion (previously $2.275 billion to $2.375 billion) Adjusted EBITDA – $125 million to $140 million (previously $150 million to $180 million) Depreciation and amortization – $60 million to $63 million (previously $63 million to $67 million) Interest expense – $36 million to $38 million (previously $32 million to $34 million) Provision for income taxes – $9 million to $13 million (previously $18 million to $22 million) Adjusted diluted earnings per share – $0.45 to $0.90 (previously $0.95 to $1.55) Capital expenditures – $60 million, of which approximately $25 million is for the rental fleet Free cash flows – $30 million to $50 million (previously $30 million to $60 million) (1) Other non-recurring items – net for the three months ended June 30, 2024, relate to $5.3 million of costs associated with a legal matter with the U.S. EPA and $0.1 million of one-time costs. Other non-recurring items – net for the six months ended June 30, 2024, relate to $5.3 million of costs associated with a legal matter with the U.S. EPA and $0.2 million of one-time costs. Other non-recurring items – net for the three and six months ended June 30, 2023, relate to $10.8 million of costs associated with a legal matter with the U.S. EPA. Other non-recurring items – net for the trailing twelve months relate to $15.7 million of costs associated with a legal matter with the U.S. EPA and $0.8 million of one-time costs. (2) Other (income) expense – net includes net foreign currency gains (losses), other components of net periodic pension costs, and other items in the three and trailing twelve months ended June 30, 2024, and the three months ended June 30, 2023. Other expenses – net for the three and six months ended June 30, 2023, include a $9.3 million write-off of non-cash foreign currency translation adjustments from the curtailment of operations in Russia.
Alta Equipment Group announces Second Quarter 2024 Financial Results

Total revenues increased $19.7 million year over year to $488.1 million Construction Equipment and Material Handling revenues of $294.9 million and $175.6 million, respectively Product support revenues increased 10.1% year over year, with Parts sales increasing to $78.0 million and Service revenues increasing to $66.2 million New and used equipment sales decreased 1.2% year over year to $251.5 million Net loss available to common stockholders of $(12.6) million Basic and diluted net loss per share of $(0.38) Adjusted basic and diluted net income per share* of $0.01 Adjusted EBITDA* of $50.3 million Alta Equipment Group Inc., a provider of premium material handling, construction, and environmental processing equipment and related services, today announced financial results for the second quarter that ended June 30, 2024. Ryan Greenawalt, Chief Executive Officer of Alta, said, “Our business rebounded well this quarter from the seasonally-challenged first quarter and in the face of a moderating market environment for new equipment sales. Notably, our product support business performed well in this moderating environment as we continued to achieve organic growth on an increased field population, with revenues increasing to a record of $144.2 million, an increase of $13.2 million from a year ago. Additionally, our Material Handling segment continued its steady path of profitable growth as we progressively executed a solid sales backlog and gained market share in strategic regions and product categories throughout our footprint. We also saw a rebound in our Master Distribution segment, as revenue in the quarter was $16.7 million versus $12.8 million in the first quarter. While we benefited from a return to normal seasonality and a strong quarter from our Material Handling segment and our product support business lines, market unit volumes in our Construction Equipment segment remain under pressure due to uncertainty regarding interest rates and the election outcome, especially affecting small to mid-size contractors. Additionally, our construction equipment sales margins continued to be impacted by the oversupply of competitive new equipment on the market in the quarter.” Mr. Greenawalt continued, “In the second quarter, we gained further traction in our eMobility segment, which expands the Alta dealership model into the over-the-road commercial vehicle industry with a focus on commercial electric vehicles and fueling and charging infrastructure. To that end, we are excited about our new partnership with Harbinger Motors, a new manufacturer of best-in-class commercial electric vehicles in the medium-duty truck space. With the inclusion of Harbinger to our portfolio and the traction gained with new customers in the quarter, we now have approximately $25 million of sales backlog in the eMobility business that we expect the majority to convert to revenues in the second half of 2024.” In conclusion, Mr. Greenawalt commented, “As we head into the second half of 2024 and into 2025, cost and fleet optimization and other initiatives to streamline our business will be high priorities as we calibrate to the transitioning environment. Despite what we believe to be potentially transitory headwinds for new equipment sales, our long-term outlook for our Construction Equipment segment remains positive. Infrastructure-related project pipelines are significant. We expect state DOT budgets to remain elevated in 2025 and spending on federal infrastructure programs is still in the early innings. In the Material Handling segment, we’re proud to be a world-class partner of Hyster-Yale Materials Handling and believe that their product portfolio and commitment to advanced technologies combined with our diversified end-markets will allow us to gain market share in key regions in the years to come, regardless of the volatility in the macro environment. I sincerely want to thank all of our 3,000 dedicated employees for their hard work and commitment to our business and to one another through the first half of the year.” Full Year 2024 Financial Guidance and Other Financial Notes: The Company updates our guidance range and now expects to report Adjusted EBITDA between $190.0 million and $200.0 million for the 2024 fiscal year. On June 5, 2024, the Company sold $500.0 million of Senior Secured Second Lien Notes at the rate of 9.000% per annum, which are due on June 1, 2029 (“2029 Notes”). With the proceeds, the Company extinguished our $315.0 million of Senior Secured Second Lien Notes due April 2026. The Company recorded a loss on debt extinguishment of $6.7 million. Concurrently with the 2029 Notes, the Company amended our ABL First Lien Credit Agreement to extend the maturity date to 2029 and increase the facility size to $520.0 million. Concurrently with the 2029 Notes, the Company amended our ABL First Lien Credit Agreement to increase the floor plan facility to $90.0 million. During the second quarter, the Company repurchased 231,334 shares for $2.0 million. We have a remaining repurchase authorization of $10.5 million.
Raymond West and Toyota Lift Northwest join forces

Raymond West Intralogistics Solutions and Toyota Lift Northwest announced that effective immediately, they have joined forces, marking the formal integration of the Pacific Northwest’s two material handling equipment companies into a unified entity. This strategic alliance aims to leverage the strengths of both organizations to deliver comprehensive, cutting-edge solutions for their existing and future clients. James Wilcox, CEO of Raymond West, will spearhead this initiative, while Dr. Ashwini Wankhede will remain President and Chief Operating Officer of Toyota Lift Northwest. “The joining of Raymond West and Toyota Lift Northwest brings together the expertise, resources, and market presence of two iconic material handling brands,” said James Wilcox. “Our combined efforts will enhance our capacity to deliver an unparalleled value proposition and set the standard for our clients in that whatever they need, the problem or challenge they have in their facility with material handling, we have the solution to Store, Move, and Optimize their operations.” “Our core values are completely aligned with those of Raymond West, and providing customers with integrated material handling solutions remains at the forefront,” said Dr. Ashwini Wankhede. “By leveraging strengths from both organizations, we are confident to dominate the market and provide customers with consistent services along the entire Northwest corridor.” Raymond West, with 75 years of history, and Toyota Lift, with 57 years, are poised to create a formidable market presence, projected to exceed $1 billion in revenue. With a combined workforce of more than 1,600 employees and an extensive network of 29 service locations across the West Coast, the newly unified entity is primed to exceed client needs and expectations.
Mallard Mfg unveils new Slim-Fit Full-Length Carton Flow Divider
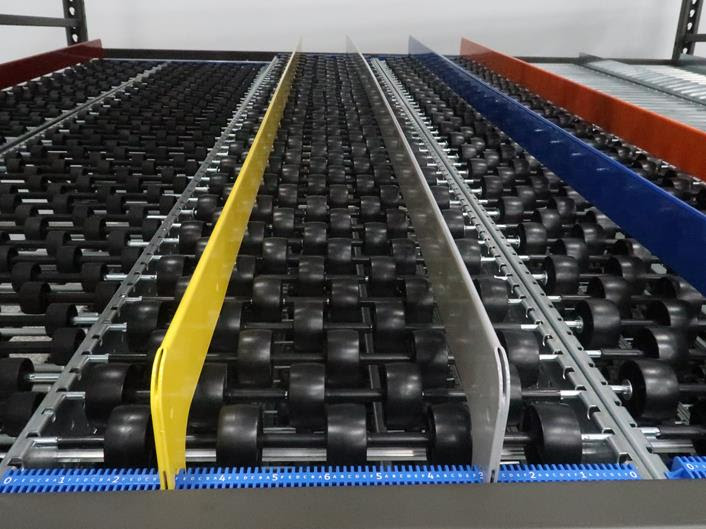
The patent-pending solution enhances order-picking speed and accuracy by easily segregating SKU lanes across multiple carton flow types Mallard Manufacturing, a gravity flow storage solutions provider, introduces new Slim-Fit (patent-pending) full-length dividers for wheeled carton flow systems. This custom-engineered product redefines efficiency and flexibility in carton and tote storage and picking applications. The full-length dividers click into specially designed holders, creating SKU slots of any width and maximizing shelf space for edge-to-edge storage. “We are thrilled to introduce the new Slim-Fit divider for our wheeled carton flow products,” said Kevin Risch, President of Mallard Manufacturing. “This innovation reflects our commitment to addressing customer needs with advanced gravity flow solutions that enhance efficiency and help control operational costs.” Product Features: A thin profile allows more SKU lanes Adjustable in 0.17” increments, eliminating wasted space Mirrored image divider brackets speed accurate slotting & reslotting Five color choices – mix and match Secure fit double-action locking – won’t dislodge The Slim-Fit full-length carton flow divider offers several key advantages over other lane segmenting accessories: Enhanced SKU Capacity: The narrow divider profile and adjustability within 0.17-inch increments ensure optimized shelf use to accommodate more SKU lanes. Innovative Bracket Design: Mirrored image divider brackets on the load and pick ends of the flow tracks facilitate faster, accurate slotting and reslotting, streamlining warehouse processes. Secure and Durable: The divider’s double-action locking mechanism ensures a secure fit, preventing accidental dislodging. Color-Coding Options: Available in five colors—blue, yellow, red, orange, and grey—the dividers enable easy color-coding of picking applications, further improving accuracy and speed. Worker Safety: The rounded-edge design and protective powder-coated finish prioritize worker safety by minimizing the risk of cuts and injuries. Despite their durability, the dividers remain lightweight, facilitating easy lifting and repositioning for swift and effortless reprofiling. Compatibility: The dividers are compatible with Mallard’s entire range of wheeled carton flow rack products, Dyna-Flo, Dyna-Flo HD (heavy-duty), and Dyna-Deck replacement tracks. Positive ROI: Depending on the application, pick rates typically range from 50 to 150 pick lines per hour, with an average of approximately 70. Saving 2 seconds per pick may not initially seem significant. Still, when extrapolated across each worker, hour, day, week, and year, it results in not only a highly efficient picking operation but also a favorable ROI. Industries that benefit from the efficiencies of carton flow rack include Retail, Grocery, Medical, Pharmaceutical, Health & Beauty, Auto, Electronics, and E-commerceFull-length lane dividers enhance carton flow function for popular applications such as: Order Picking Parts Storage Assembly/Kitting
Sexton joins OTR as Global VP of Engineering and Innovation
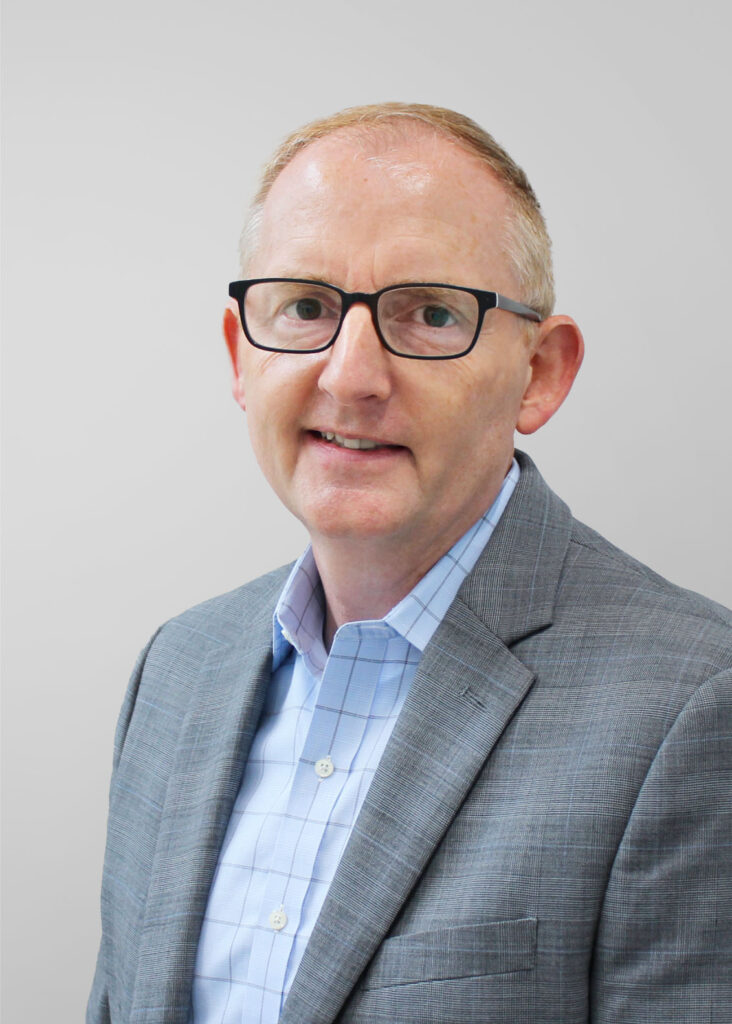
Patrick Sexton has joined OTR Engineered Solutions (OTR) as the company’s new Global Vice President of Engineering and Innovation. In this role he will oversee OTR’s engineering team worldwide, ensuring all activities align with strategic goals. “It’s an exciting time at OTR, as we’re not only investing heavily in product development but also advancing technology and building global infrastructure,” said Tom Rizzi, President and CEO. “Patrick will be a great addition to OTR’s executive team, and he’ll help us continue to innovate and grow.” Sexton offers vast experience in energy, electrification, automotive, and similar industries. He has led the development of various products and solutions for leading technology companies, serving in both engineering and executive-level positions. He also has a background in providing technical and strategic consulting. Throughout his career, he has been awarded 10 patents, with others currently in process. “OTR has a proud history of innovation in off-the-road tire, wheel, and track technologies, dating back to 1987,” said Rizzi. “With 32 facilities and more than 1,400 employees worldwide, we’re only getting started. Sexton will be instrumental in further developing our premium solutions for OEM and aftermarket customers in numerous industries, leading to future growth globally.” A native of Ireland, Sexton earned a degree in mechanical and manufacturing engineering from Munster Technical University in Cork, Ireland. After spending some of his career in the United Kingdom, he moved to the United States, where he recently became a citizen. OTR Engineered Solutions is a market-leading global enterprise specializing in off-the-road tire, wheel, and track solutions for original equipment manufacturers (OEMs) and aftermarkets. Known for being an innovator in multiple off-the-road applications, OTR differentiates itself by providing value-added services such as warehousing, tire mounting, and sequencing, among other things. The firm has long established strategic partnerships with OEMs covering Construction, Lawn & Garden, Powersports, Agriculture, Forestry, Mining, Material Handling, and Specialty Vehicle markets. OTR’s infrastructure comprises 32 facilities and warehouse locations throughout the U.S., Canada, Europe, and Asia, serving customers globally.
Episode 509: The Eighth Notch is streamlining last-mile delivery
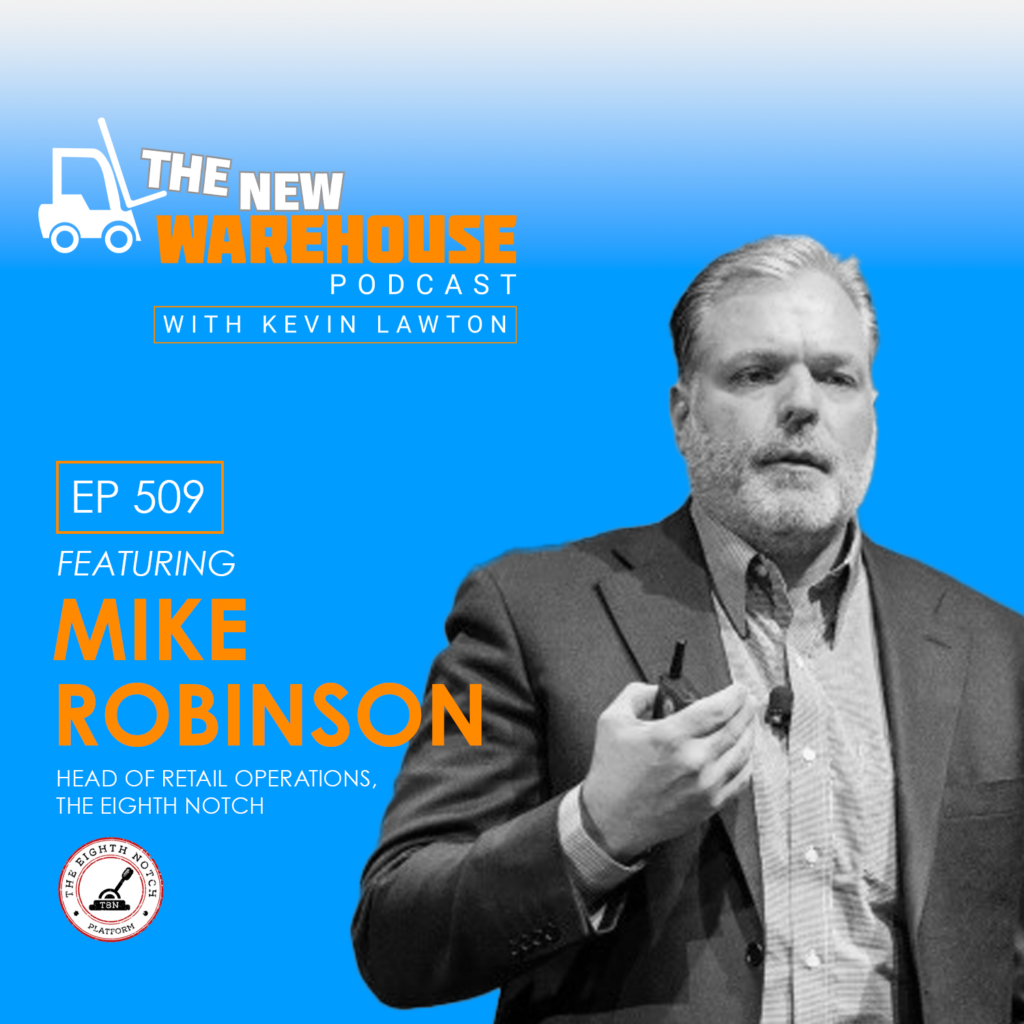
Today, Mike Robinson, the Head of Retail Solutions and a founding member of The Eighth Notch, joins the show to discuss how The Eighth Notch is streamlining last-mile delivery. In this episode, we explore The Eighth Notch’s unique approach to addressing delivery coordination challenges, particularly in the last mile of e-commerce deliveries. Mike shares insights into their innovative solutions that aim to improve sustainability and efficiency in the delivery process. The Origin and Mission of The Eighth Notch Mike provides an intriguing background story, describing himself as an “accidental retailer” and sharing how his career trajectory led him to become a founding member of The Eighth Notch. He recounts his experiences at major retailers like Gap and Macy’s, where he witnessed the exponential growth of e-commerce and the consequent logistical challenges. This experience sparked his desire to focus on improving rather than just expanding e-commerce operations. The name “The Eighth Notch” itself is a tribute to the founder’s father, a railroad engineer. The term signifies the highest power setting on a locomotive, symbolizing their commitment to peak performance in delivery logistics. Tackling Delivery Coordination Issues The Eighth Notch’s primary goal is to reduce the frequency and inefficiency of delivery trucks by better coordinating deliveries. Mike explains that the current state is unsustainable economically and environmentally and that it is“done in an unsynchronized, uncoordinated manner.” The Eighth Notch aims to optimize delivery schedules, ensuring multiple packages arrive simultaneously. Mike illustrates how the company created a three-way gain-share model where the carrier gets their share, the retailer gets an incentive for changing their behavior, and they get a component of the savings. Enhancing Consumer Experience and Sustainability A key aspect of The Eighth Notch’s strategy is consumer education and engagement. While the end consumer might not be directly aware of the behind-the-scenes coordination, The Eighth Notch is providing consumers with the benefit of fewer, more consolidated deliveries, which reduces carbon emissions and enhances convenience. The company is also looking into offering consumers choices at checkout, similar to Amazon’s sustainable delivery options. This shift towards consumer-enlisted sustainability aligns with growing environmental consciousness among shoppers. Key Takeaways from The Eighth Notch Efficiency through Coordination: The Eighth Notch focuses on synchronizing deliveries to reduce frequency and enhance efficiency. Economic and Environmental Benefits: Their model saves costs and reduces carbon emissions, benefiting carriers, retailers, and the environment. Consumer Engagement: Offering sustainable delivery options at checkout can drive consumer engagement and loyalty. The New Warehouse Podcast Episode 509: The Eighth Notch is Streamlining Last-Mile Delivery
2024 Generative AI Product of the Year Awards accepting nominations now
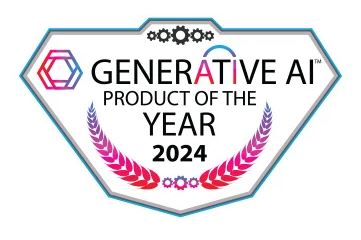
Generative AI Expo and TMCnet are accepting applications for the 2024 Generative AI Product of the Year Awards. Suppose your organization has developed applications, platforms, models, devices, servers, sensors, or any other solution that harnesses the potential of Generative AI to elevate performance within any vertical market segment. In that case, we encourage you to apply for the 2024 Generative AI Product of the Year Awards. This is your opportunity to establish leadership in a rapidly emerging market, showcase your achievements, and drive new business for your innovative AI and automation solutions. This award is for solutions providers to prove that they have demonstrated excellence in leveraging Generative AI to help users: Enhance customer experiences Streamline operations Increase efficiency Improve quality Drive business success TMCnet and Generative AI Expo’s team of editors and judges encourage submissions from all market segments that have successfully deployed/implemented Generative AI solutions. Here are some of the applications we expect to be included in the winner’s list: Conversational Agents Content Creation and Automation Image Generation Video Generation Music Composition Natural Language Processing Chatbots and Virtual Assistants Style Transfer Data Augmentation Video Game Design Art Generation Code Generation Storytelling Speech Synthesis Character and Avatar Creation Video Captioning Product Design Recommendation Systems Language Translation These are some of the diverse applications where Generative AI technologies are being used to create content, solve problems, and enhance various fields. Your solutions in these areas should be rewarded for their excellence. Generative AI Product of the Year Award Winners Earn All of These Benefits: Independent Validation from Highly-Respected 3rd Party Source Highlighted as an award winner in TMCnet and Generative AI Expo feature story Announced as an award winner via press release Measurable Publicity Boost for Your Solution and Brand Featured in extensive social media campaign across all Generative AI Expo, TMC, and TMCnet platforms – reaching in excess of 100,000 followers Provided award press kit to inform clients, prospects, and media of your achievement Unlimited License to Award Logos^ Adds Year-Round, Impressive Boost to Marketing Campaigns Add Award logo to: Website home page, product pages, and About Us Social Media platforms, profiles, and posts Marketing brochures Digital and print ad campaigns Sales presentations E-mail signatures Trade show booth Webinars and other video content Annual report Business cards Promotional items Customer newsletters White papers and case studies Internal employee communications Increased Inbound Inquiries for Your Sales Team Your presence on the list of winners could be just what you need to land on more high-value RFPs Instant Morale Boost for Your Hard-working Team Show appreciation to all team members who build and bring your solutions to market Awards are not given in specific categories. All tools, platforms, and applications contributing to generating Generative AI solutions are considered. While Generative AI is primarily associated with software applications and models, hardware and technology products also enable and enhance Generative AI capabilities. GPU Accelerators AI-Optimized Servers AI Cameras and Sensors Smart Assistants and Devices Robotic Process Automation (RPA) 3D Printers Generative Art Installations Any of your hardware and technology products designed to support and leverage Generative AI are also eligible to earn the award. To be considered for a 2024 Generative AI Product of the Year Award, please complete the online form detailing why your solution(s) should be considered. Include product information and other relevant documentation to support your nomination. The judging panel may reach out to you seeking additional information. TMCnet and Generative AI Expo editors and judges will carefully evaluate all award submissions. These judges assess each entry based on its own merits rather than against other submissions. All worthy solutions will be selected for awards. Early Bird Deadline: Monday, August 12. Save $100 off the processing fee. Only nominated solutions are considered. Winners are to be announced in October 2024.
AAR reports Rail Traffic for the week ending August 03, 2024
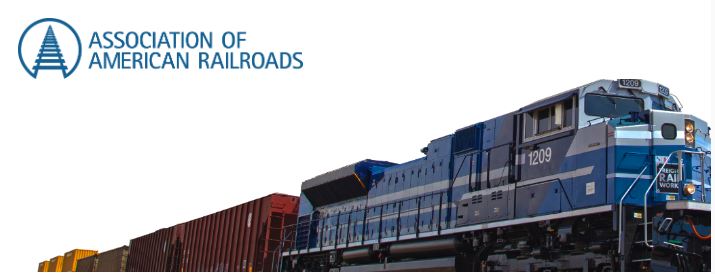
The Association of American Railroads (AAR) has reported U.S. rail traffic for the week ending August 3, 2024, and July 2024 volumes. U.S. railroads originated 1,073,191 carloads in July 2024, down 2.1 percent, or 23,353 carloads, from July 2023. U.S. railroads also originated 1,319,818 containers and trailers in July 2024, up 8.4 percent, or 102,549 units, from the same month last year. Combined U.S. carload and intermodal originations in July 2024 were 2,393,009, up 3.4 percent, or 79,196 carloads and intermodal units from July 2023. In July 2024, 12 of the 20 carload commodity categories tracked by the AAR each month saw carload gains compared with July 2023. These included grain, up 19,690 carloads or 26.5 percent; chemicals, up 4,797 carloads or 3.1 percent; and petroleum & petroleum products, up 4,048 carloads or 8.5 percent. Commodities that saw declines in July 2024 from July 2023 included coal, down 35,167 carloads or 11.0 percent; crushed stone, sand & gravel, down 11,563 carloads or 10.6 percent; and motor vehicles & parts, down 6,436 carloads or 9.1 percent. Excluding coal, carloads were up 11,814 carloads, or 1.5 percent, in July 2024 compared to July 2023. Excluding coal and grain, carloads were down 7,876 carloads or 1.1 percent. Total U.S. carload traffic for the first seven months of 2024 was 6,642,565 carloads, down 4.1 percent, or 286,356 carloads, from the same period last year, and 7,962,928 intermodal units, up 8.6 percent, or 631,898 containers and trailers, from last year. Total combined U.S. traffic for the first 31 weeks of 2024 was 14,605,493 carloads and intermodal units, an increase of 2.4 percent compared to last year. Week ending August 3, 2024 Total U.S. weekly rail traffic was 498,807 carloads and intermodal units, up 5.7 percent compared to last year. Total carloads for the week ending August 3 were 219,568, down 1.2 percent from the same week in 2023, while the U.S. weekly intermodal volume was 279,239 containers and trailers, up 11.8 percent from 2023. Six of the ten carload commodity groups posted an increase compared with the same week in 2023. They included chemicals, up 2,971 carloads, to 33,218; petroleum and petroleum products, up 1,629 carloads, to 11,016; and grain, up 1,368 carloads, to 17,022. Commodity groups that posted decreases compared with the same week in 2023 included coal, down 5,528 carloads, to 58,978; nonmetallic minerals, down 2,052 carloads, to 31,312; and metallic ores and metals, down 1,357 carloads, to 20,721. North American rail volume for the week ending August 3, 2024, on ten reporting U.S., Canadian, and Mexican railroads totaled 322,520 carloads, down 1.2 percent compared with the same week last year, and 351,513 intermodal units, up 6.1 percent compared with last year. Total combined weekly rail traffic in North America was 674,033 carloads and intermodal units, up 2.5 percent. North American rail volume for the first 31 weeks of 2024 was 20,471,828 carloads and intermodal units, up 2.3 percent compared with 2023. Canadian railroads reported 90,465 carloads for the week, up 1.6 percent, and 64,067 intermodal units, down 10.6 percent compared with the same week in 2023. For the first 31 weeks of 2024, Canadian railroads reported a cumulative rail traffic volume of 4,958,371 carloads, containers, and trailers, up 1.5 percent. Mexican railroads reported 12,487 carloads for the week, down 17.3 percent compared to last year, and 8,207 intermodal units, down 15.8 percent. Cumulative volume on Mexican railroads for the first 31 weeks of 2024 was 907,964 carloads and intermodal containers and trailers, up 4.2 percent from the same point last year. To view the rail traffic reports, click here.
US Container Shipping braces for headwinds as peak season approaches
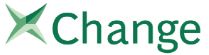
Majority of US container traders surveyed anticipate further container price hikes in August, 92% expect volatility China to US and China to Europe Container leasing rates surge in July The US container shipping sector is cautiously approaching the peak season, with the upcoming US elections and labor negotiations poised to bring their own set of implications for the container logistics industry, as indicated in the August Container Market Forecaster by Container xChange. The sector has already been witnessing its own set of challenges like overestimation of demand, pulling forward of orders which caused inflationary trends in the freight and container rates and resultantly, the wait and watch strategy by container sellers and container buyers. The election year brings an element of uncertainty, as many US container traders are concerned about potential changes in trade and regulatory policies, as well as economic policies that could impact consumer sentiment and their spending patterns. “While our customers anticipate these headwinds impacting their business, they also remain hopeful that business activity will pick up in September as companies prepare for the holiday season.” shared Angelo Marino, Americas Account manager, Container xChange. “The upcoming labor negotiations on the US East Coast in Q3 add another layer of potential volatility. Retailers have been preparing for the peak season since early 2024, aiming to avoid stock shortages, and now that we’re entering this busy period, the focus will be on understanding the true demand dynamics. The anticipation of these events is critical for navigating the complexities of the market in the coming crucial months.” shared Christian Roeloffs, cofounder and CEO of Container xChange. “The hot container leasing market isn’t solely due to the Suez Canal issue; it also ties into expectations surrounding potential changes in US administration and international trade policies. Additionally, retailers are anticipating the peak season and aiming to ensure their stock is secured well before November to avoid any kind of disruptions. While we expect container imports in Europe and the US, along with Asian exports, to remain strong as we approach the peak season, this momentum is likely to cool off by the end of the year. This is because the current stock recovery from retailers will have been largely completed. There is a possibility that the market could stay hot a little longer if retailers decide to stock up ahead of the Chinese New Year, but we don’t anticipate that the current market conditions, influenced in part by the Suez Canal crisis, will persist indefinitely into the future,” shared Andrea Monti, Managing Director and CEO of Sogese SRL, a trading and leasing company based in Italy and a customer of Container xChange. “Our customers in the US are facing challenges with inventory liquidation due to mismatched expectations between container buyers and container sellers. In this context, it may not be a prosperous time for container traders, the logistics market, or retailers who have stockpiled inventories to avoid delays in the peak season.” added Roeloffs. Container Price Sentiment Survey Results A survey of around 1,000 US-based container traders reveals that 78% expect container prices to continue rising in the coming weeks, driven by election uncertainty and potential labor strikes. Only 14% foresee a decline, while 8% expect prices to remain stable. This indicates a broad expectation of continued volatility in the US container trading environment. However, the global Container Price Sentiment Index (xCPSI) by Container xChange dropped from 63 to 39 points in July, suggesting waning sentiment towards rising container prices in the near term. Roeloffs added, “The overestimation of strong consumer demand has resulted in overstocked retail inventories. We’ve observed for some time now that actual consumer demand hasn’t experienced a significant spike, thereby allowing retailers and importers ample time to restock before their next cycle. This situation could challenge the container shipping industry, as the recent spike in freight rates and container prices may not be sustainable further in the rest of the year. It’s only a matter of time before we see a downward trend in container and freight rates.” Market Outlook “As we approach the peak season of 2024, we’re observing a couple of pivotal shifts expected to impact the container shipping industry. First, there’s a gradual correction in supply and demand on the cards that should stabilize rates in the latter half of the year, owing to a lack of solid demand surge. In a longer term, the more profound change is the ongoing trend toward regionalization and smaller trade networks, which became mainstream in 2021. This shift has gained even more importance today, especially as geopolitical conflicts become a regular consideration in risk resilience strategies. Intra-Asia trade boom is a significant factor that indicates that smaller, more complex trade networks are developing and flourishing.” shared Christian Roeloffs, cofounder and CEO of Container xChange, the online container trading and leasing marketplace, based in Hamburg, Germany.