Seegrid terminates Product and Distribution Agreements with Raymond Corporation
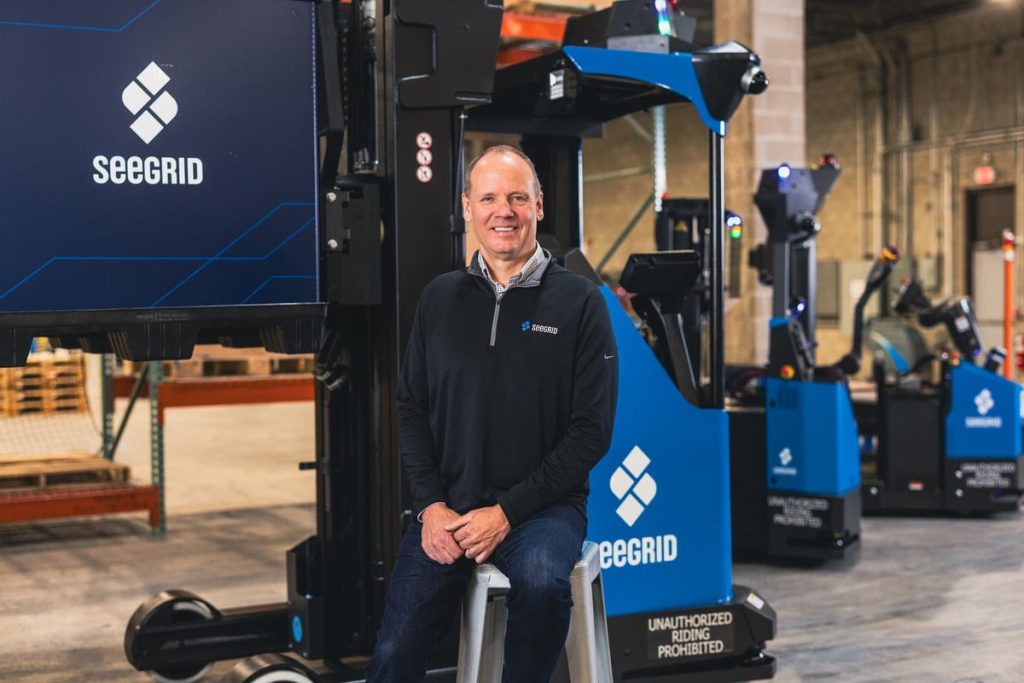
Seegrid Corporation, a manufacturer of autonomous mobile robot (AMR) solutions for palletized material handling, today announced its decision to terminate its product and distribution agreements with Raymond Corporation (a division of Toyota), effective upon the conclusion of a ninety-day notice period. “This move will allow us to sell and service the full Seegrid-branded product line across all market segments rather than serving a large portion of the market through Raymond,” said Joe Pajer, Chief Executive Officer of Seegrid. “We are seeing more customers desire a direct relationship with Seegrid as we roll out our new lift truck products and release innovative technology enhancements across our product line.” The decision emphasizes Seegrid’s commitment to fostering lasting customer relationships throughout their automation journeys. With this change, Seegrid can guide all customers from initial consultation through implementation to operational excellence, ensuring a seamless experience backed by Seegrid’s best practices and experienced post-support teams. “We appreciate Raymond’s partnership in our earlier years,” added Pajer. “At the same time, we have carefully studied our business relationship with Raymond and concluded that we are in a better position to deliver the benefits of our innovative technology to all customers if we do so directly and with Seegrid-branded products only. We are very excited to make our full product line available to all customers. This shift in go-to-market strategy follows a year marked by record-breaking end-user sales, with particularly high demand for our advanced autonomous lift truck solutions” Pajer concluded.
Cimcorp appointed Pekka Natri as Head of Region
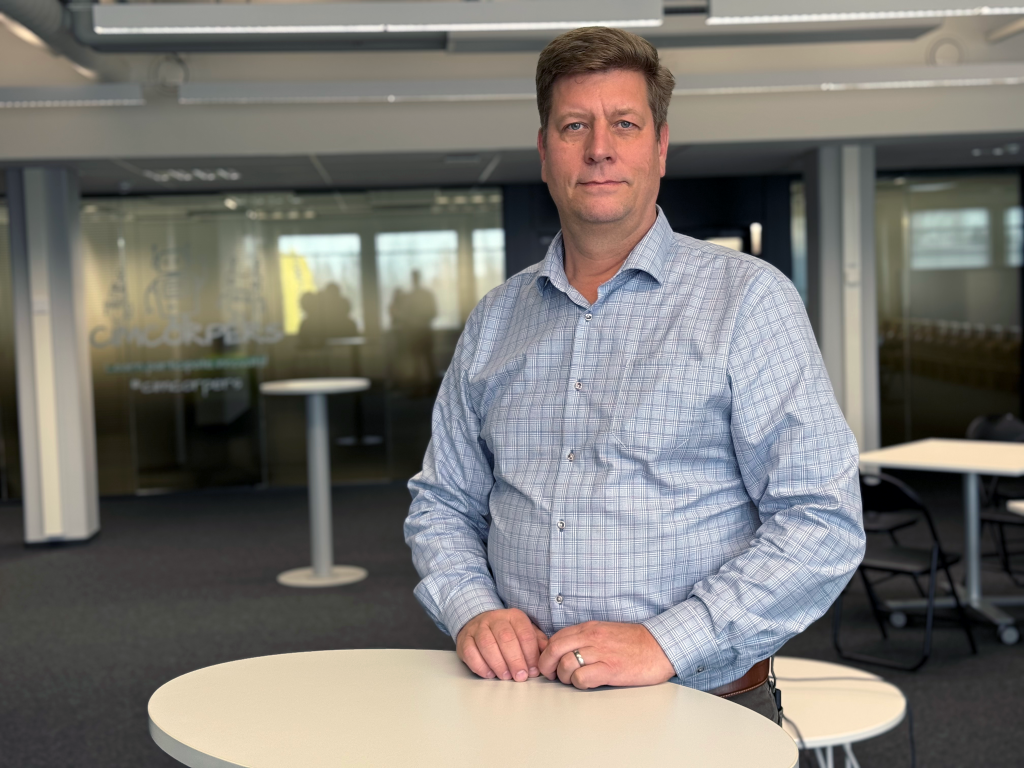
With nearly 30 years of experience leading diverse international teams, Natri will streamline all North American operations and align regional goals with global strategy Cimcorp has announced the appointment of Pekka Natri to Head of Region for North America. Natri has been a key member of the Cimcorp team since 2018, formerly serving as Head of Region for SEAP and India. With a successful track record of establishing and growing local entities for international businesses, Natri will now be responsible for streamlining all North American operations, driving collaboration with partners, and aligning regional goals with Cimcorp Group’s global strategy. “I am thrilled to take on this new opportunity to strengthen Cimcorp’s position as a leader in the North American market,” said Natri. “As head of region, my goal is to make an immediate, positive impact for customers and employees today, as well as to set the groundwork for ultimately shaping the future of automation in our core sectors—grocery retail and tire manufacturing.” With a background in biotechnical engineering and nearly 30 years of experience in the technology space, Natri has led teams in many different parts of the world, including China, India, Africa, Southeast Asia, Australia, and Finland. His breadth of expertise spans business development, management, sales, solution development, and project delivery, and he has successfully implemented strategic growth plans for complex international businesses at the market area level and on a global scale. After joining Cimcorp in 2018, Natri spearheaded the company’s efforts to expand its presence and customer service capabilities in India. Nartri established a new office in Chennai, where he managed everything from location selection to recruitment and training. In 2023, Natri led the startup of a new office in Sydney, Australia, helping Cimcorp achieve a stronger position in the Australian market. In his new role, Natri will focus on aligning North American teams, functions, and partners to best serve customers locally while also supporting global growth. “Through working in various countries with diverse teams, I’ve developed a deep understanding and appreciation of different perspectives and ways of thinking. As a manager, I give people the freedom to approach ideas and issues in new ways—which enables our team to collaborate and solve challenges with open minds,” said Natri. “I’ve also gained the ability to see things from a regional perspective, without missing the big picture. I’ve been on both sides of the coin, working with employees at local sites and with executives at company headquarters. This will help me not only improve North American operations, but also support our company’s overall strategy.” As an experienced leader, Natri prioritizes building a workplace based on trust, transparency, and open communication. He is a major proponent of employee development and will ensure Cimcorp supports its staff in exploring ongoing educational and career opportunities. Natri said, “I believe great leadership is based on transparency, mutual trust, and setting clear targets. I want to create an open environment where everyone feels comfortable sharing their ideas. Working as a team, we can create synergies and deliver greater value than what we could achieve alone. My role in it all is to motivate employees to focus on the right goals, ensuring that they succeed as individuals and that we succeed as a company.”
Welch backs the Blue with winning bid
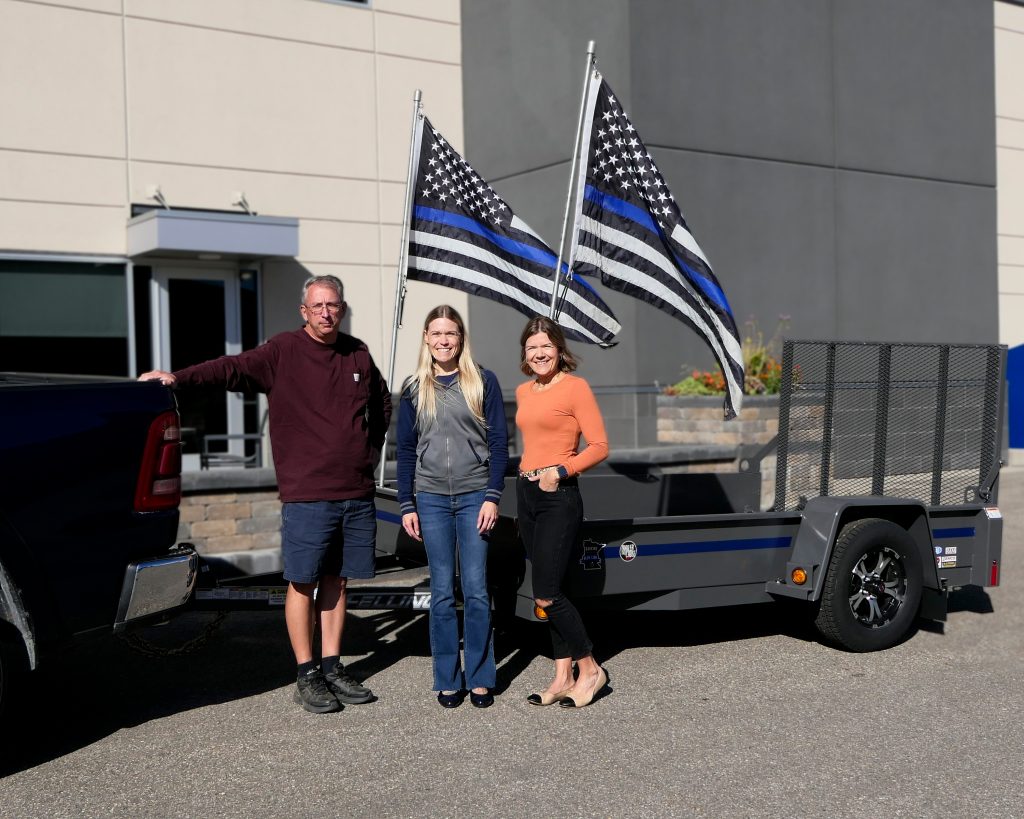
Felling Trailers, Inc. conducted its twelfth annual online auction of an FT-3 drop deck utility trailer to benefit a non-profit organization: Backing the Blue Line. A winning bid of $6,650.00 won the auction that ended the evening of Patriots Day, Sept. 11th. The bid winner is a follower and dedicated supporter of the annual Trailer for a Cause auctions, Joe Welch of Caledonia, MN. Joe, a construction and farm equipment dealer, has followed Felling Trailers’ Trailer for a Cause auctions for several years and was the bid winner in the 2022 auction that benefitted Eagle’s Healing Nest. “I have followed the Trailer for a Cause auctions for about five years. The organizations the auctions benefit are very good ones. The Felling employees have chosen very good causes to support,” said Joe. “Being able to help with this support is very rewarding for me. We need these guys (law enforcement) out there; anyone that has to go to work with a bulletproof vest needs our support and respect.” A few weeks after the auction closed, arrangements were made for Joe to come and pick up his new trailer. It will be used a bit for business and pleasure. “I am very appreciative of the work law enforcement does for us, the sacrifices they make, and the fact that they never know what the next call will bring,” said Welch. The 2024 Trailer for a Cause FT-3 utility trailer was painted a custom grey with a blue line and the Backing the Blue Line emblem. Suppliers of Felling Trailers had joined in to support Backing the Blue Line by sponsoring the construction of the trailer, from lighting to tires to decking. The 2024 Trailer for a Cause sponsors are Trans-Texas, PPG, Dexter, Sealco, Peterson, Industrial Wood (Blackwood), Demco, and Pacific Rim. Felling Trailers wants to help generate awareness about the valuable work that Backing the Blue Line does for officers and their families through their various programs and support services. The online auction ran for nine days, from Monday, Sept. 2nd at noon CST through Wednesday, Sept. 11th at noon CST, ending with Joe’s winning bid. One hundred percent of the $6,650 benefited Backing the Blue Line! Two weeks after Joe had picked up the 2024 Trailer for a Cause, Backing the Blue Lines’ Gretchen Gifford, VP/Executive Board of Directors, accompanied by her husband, Officer Gifford, and son, made the trip to Sauk Centre to accept the donation check. The Giffords met with Felling Trailers’ Owners Brenda Jennissen and Bonnie Radjenovich to present them with the check for $6,650. “There are a lot of great organizations out there. It is truly humbling to be the recipient of your fundraiser this year,” said Gretchen. “It’s been a tough couple of years for the law enforcement community; we’ve had five fallen officers in the last thirteen months. We (Backing the Blue Line) provided blue memorial roses that had been requested for the funeral of an officer who died in the line of duty this past weekend.” “Speaking with a Minnesota National Guardsman and State Law Enforcement officer’s widow, it was evident the significant support Backing the Blue Line provided her and their son. She said BtBL has been there since day one and continues to provide emotional support, cards on holidays, and gifts for their son just to show they care,” said Brenda Jennissen, Felling Trailers CEO/President. “It’s nice to be remembered. We are blessed and fortunate to be able to support them meaningfully. We are there for all the moments we can be, providing injury baskets when officers are hurt in the line of duty and sending cards on holidays and important dates. We celebrate the good moments too, onesies for members with new babies and events that allow for the meeting and socializing among wives who live and understand our lives, as well as encourage continued relationships and friendships,” said Gifford.
Brian Short honored with PTDA Warren Pike Award
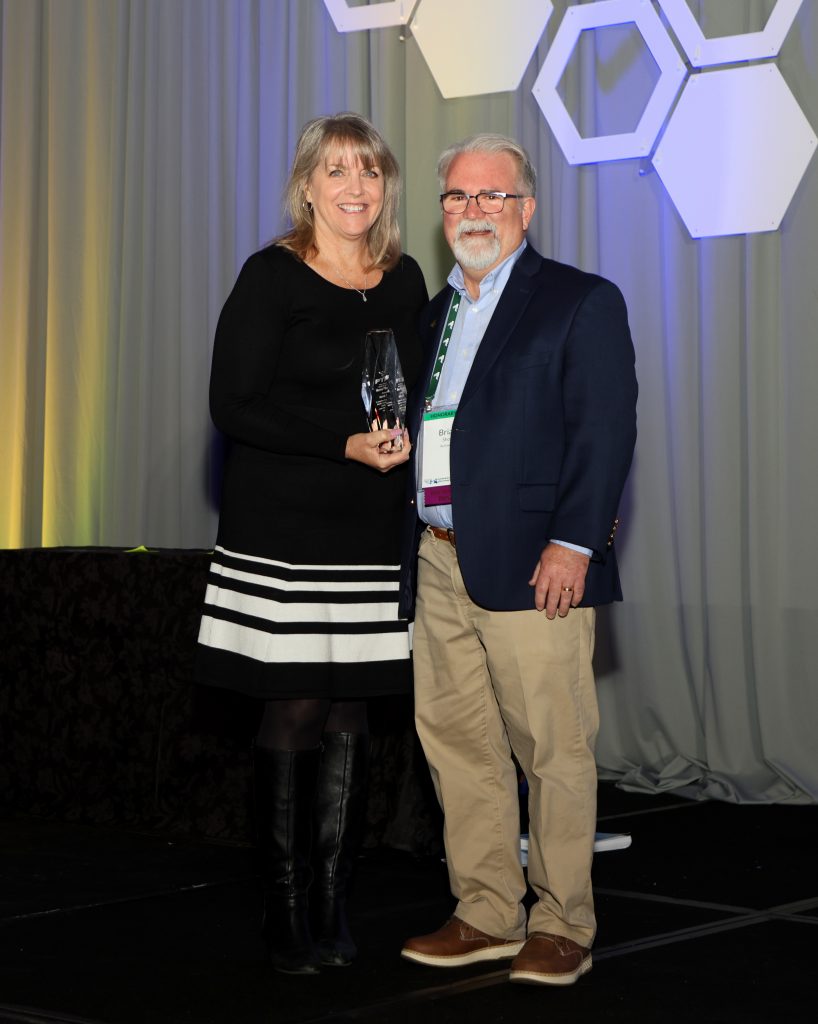
The Power Transmission Distributors Association (PTDA) has named Brian Short the 33rd recipient of its Warren Pike Award for lifetime achievement in the power transmission/motion control (PT/MC) industry. The award was bestowed upon Short during the PTDA 2024 Industry Summit on October 25 in Colorado Springs, Colo. Established in 1984, the Warren Pike Award honors individuals who have demonstrated outstanding, continuous, long-term support of PTDA and the PT/MC industry and is only presented when an individual’s achievements merit this prestigious recognition. Warren Pike Award recipients are selected by the PTDA Board of Directors. Revered as an industry expert, Short began his 40-plus-year career with Bruening Bearing and advanced through a number of roles before retiring from Pfannenberg USA. As an advocate for the industry, he shared his knowledge as a member of several PTDA committees and served as PTDA Foundation President in 2018 and 2019. “I served on committees with so many great people, many of whom are Warren Pike Award winners…” shared Short in his acceptance remarks. “We developed many tools to help distributors be more efficient and effective, and the strong relationships I built helped me throughout the balance of my career. You could say that PTDA helped me broaden my horizons and be lucky enough to actively participate in elevating excellence.”
CLARK Material Handling Company announced the New WSTX30 and WSTX35 Pallet Stackers
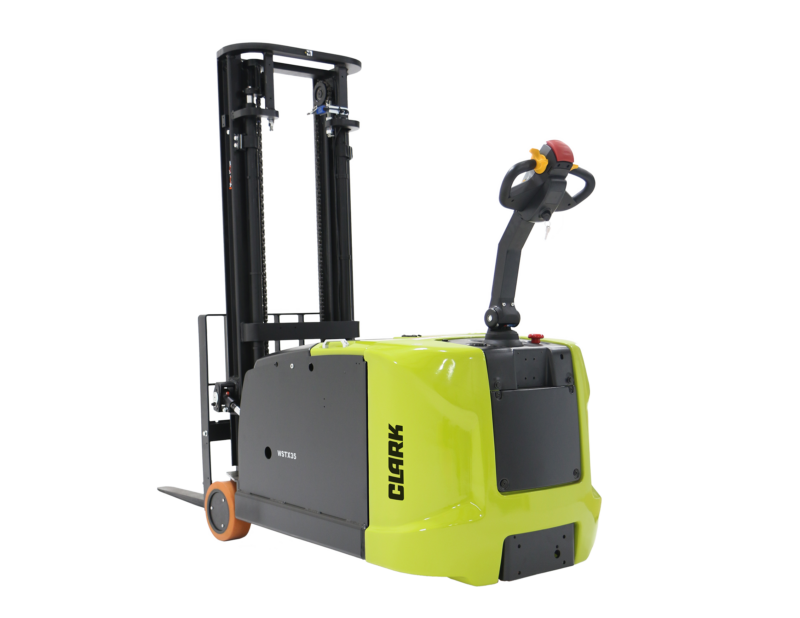
Built to Last and designed to transport up to 3,000 and 3,500 pounds, the WSTX is a compact alternative to sit-down forklifts CLARK Material Handling Company has announced the launches of the WSTX30 and WSTX35. Built to Last and designed to transport up to 3,000 and 3,500 pounds, the WSTX is a compact alternative to sit-down forklifts. This pallet stacker features power steering, a durable I-beam mast, and constant travel speed regardless of the truckload. Designed for use in logistics, manufacturing, and warehousing, key features of this new product include: 3,000 & 3,500 – pound lift capacity – for moving heavy cargo with ease Regenerative braking and brushless AC motor – minimizes downtime and maintenance Emergency Power Disconnect – shuts off system power to protect operator Ergonomic handle – with convenient access to all controls without lifting your hand Vertically-mounted motor and transmission – reduces downtime and noise while improving efficiency and performance Available for ordering through CLARK dealers, the WSTX30 and WSTX35 represent another “CLARK solution” for end-users to manage all their material handling needs. “The WSTX 30 & 35 pallet stackers are exceptional replacements to sit-down forklifts. These trucks are compact, durable, and can handle substantial loads while focused on operator comfort and reducing downtime,” said Brandon Bullard, Vice President of Sales.
Episode 535: The Power of Proximity
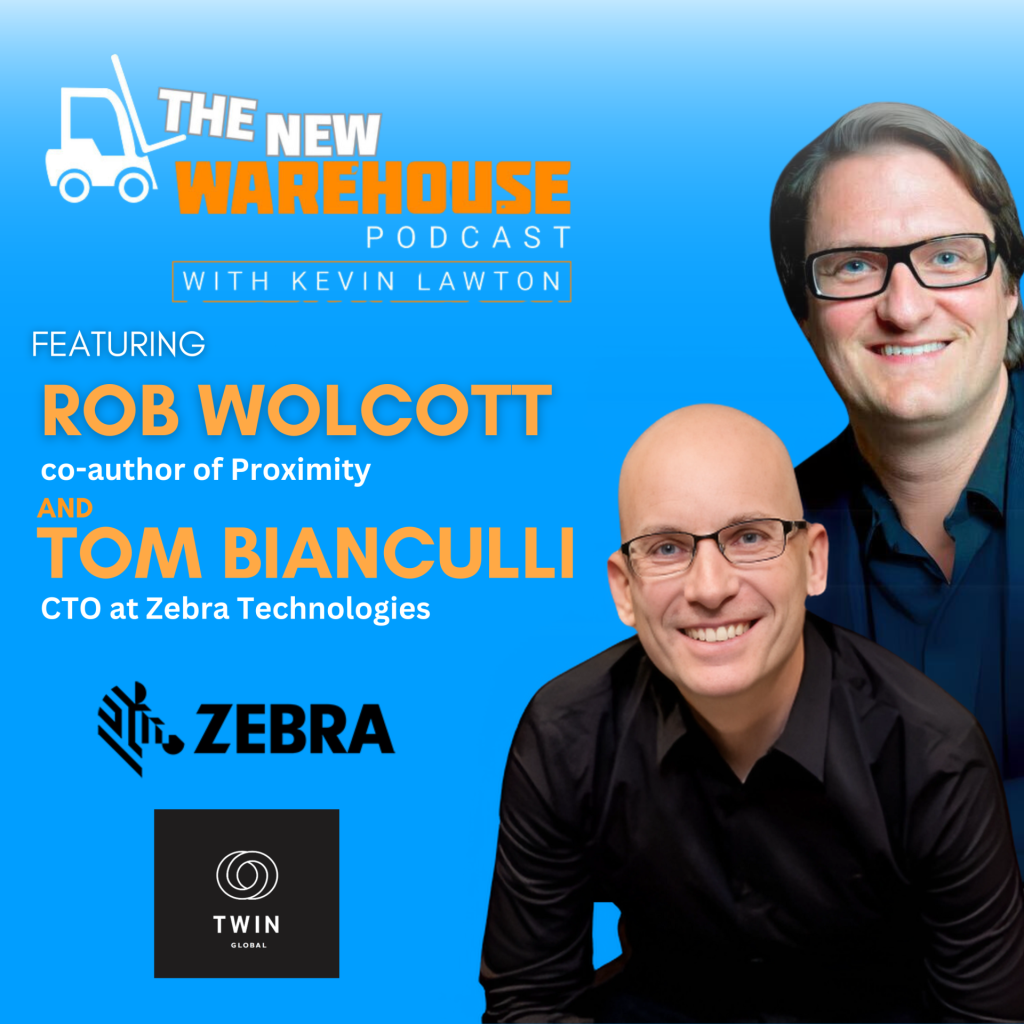
In this episode of The New Warehouse Podcast, Kevin welcomes Rob Wolcott, co-founder of TWIN Global and author, and Tom Bianculli, CTO of Zebra Technologies, for a discussion on the transformative concept of proximity as outlined in Wolcott’s book, Proximity. This concept—envisioning an “anything, anywhere, anytime” world—is about bringing resources closer to the point of demand. With Zebra’s innovations in visibility and data, the discussion dives into how proximity influences supply chain efficiencies, warehouse operations, and future possibilities in technology. Redefining Proximity in the Digital Age The proximity concept, as Wolcott describes, envisions a world where goods, data, and services are available “anywhere, anywhere, anytime.” This shift challenges traditional supply chains, creating opportunities to respond to demand in real time rather than stockpiling goods. “Digital compels the production and provision of value ever closer to the moment of actual demand,” notes Wolcott. An early example includes large language models that operate at the “far edge,” processing data directly on devices, and reducing dependency on central servers and cloud systems. By optimizing resources to meet immediate needs, industries can create a future where every operation is faster, smarter, and more efficient. The Warehouse as a Microcosm of Proximity The warehouse, explains Bianculli, serves as an ideal testing ground for proximity, as real-time data guides optimal workflows. Zebra’s “Sense, Analyze, Act” framework illustrates this by enabling forklifts and robots to function at high efficiency, moving inventory only when necessary. “If you know where every pallet and fork truck is, you can optimize every movement,” he adds, demonstrating how proximity improves utilization and reduces waste. Bianculli shares examples where advanced algorithms reroute forklifts to achieve 80% utilization—significantly more than traditional systems. As “microcosms of the future,” warehouses highlight how proximity can transform logistics by optimizing each action to deliver quicker, seamless service. Proximity’s Broad Impact on B2B and B2C Expectations As consumers demand rapid and tailored services, businesses must adopt proximity thinking to stay competitive. “Your customers don’t care about your constraints,” emphasizes Wolcott. This sentiment extends beyond retail, affecting B2B relationships where timely, accurate order fulfillment is critical. Hospitals, for example, expect quick, on-demand deliveries of medical supplies—a trend driven by Zebra’s technology solutions. Similarly, innovations like Interstellar Lab’s on-site pods redefine production by growing ingredients precisely where and when they’re needed, avoiding lengthy supply chains. “It’s an example of pretty far-edged stuff that brings proximity right to where it matters most for businesses. The yields on these plants in interstellar pods are 1000, 2000, and in some cases 3000 percent higher than in the wild.” Key Takeaways on Proximity Proximity envisions an “anything, anywhere, anytime” approach, transforming industries. Warehouses embody proximity by dynamically optimizing workflows and reducing waste. B2B and B2C sectors are increasingly turning to proximity strategies to keep up with rising consumer expectations and mitigate risks. The New Warehouse Podcast Episode 535: The Power of Proximity
Seegrid’s Lift RS1 AMR is the Future of Autonomous material handling
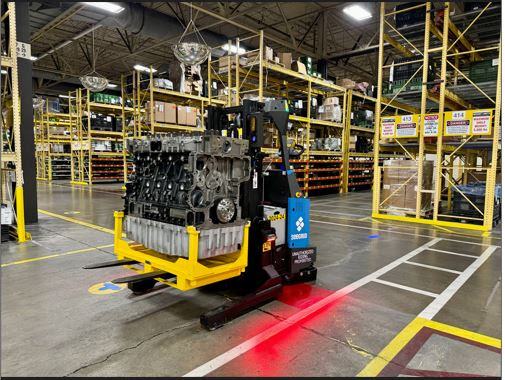
Seegrid manufactures autonomous mobile robot (AMR) solutions for palletized material handling, highlighting its Lift RS1 AMR. This autonomous lift truck is designed to transform material handling workflows, providing unmatched productivity, efficiency, and safety to manufacturing, warehousing, and logistics operations. Seegrid’s Lift RS1 AMR is capable of a 6-foot lift height, making it ideal for low-lift processes across the most prevalent industrial facility applications. A payload capacity of 3,500 pounds enables facilities to handle heavy loads more efficiently, boosting overall operational productivity. The RS1 demonstrates exceptional reliability, consistently performing tasks with precision and minimal downtime, ensuring seamless material handling operations. The RS1 has been built with the same proven technology stack, enabling Seegrid AMRs to log over 15 million autonomous production miles in customer facilities. With its vision-guided technology, Seegrid’s Lift RS1 can safely and reliably navigate even the most dynamic environments without requiring infrastructure such as magnets or reflectors. Moreover, the RS1 helps simultaneously address staffing shortages and respond to customer demands by providing facilities with a dependable autonomous solution. The RS1 features Seegrid’s pioneering Sliding Scale Autonomy, a unique-to-Seegrid innovation that blends the agility of autonomous mobile robots (AMRs) and the predictability of automated guided vehicles (AGVs). This allows the truck to navigate differently based on what is best suited for the specific customer application. Whether performing long-haul routes or dynamically executing picks and drops, the RS1 excels by providing both the predictability and agility required by modern manufacturing, warehousing, and logistics environments. Equipped with LiDAR-based SLAM technology, the RS1 plans dynamic routes based on real-time perception feedback, ensuring reliable picks and drops without explicit training. Sliding Scale Autonomy offers a capability unmatched by competitors, empowering customers to optimize their material handling workflows in ways traditional AMRs and AGVs cannot. Safety is a top priority for Seegrid, and the Lift RS1 offers 360° safety coverage. The truck has primary and secondary safety sensing capabilities, which is a standout feature in the industry. While many systems rely solely on primary obstruction detection, which can only sense objects within 6 inches of the ground, Seegrid’s secondary obstruction detection technology precisely scans the drop area before payload release. This guarantees an extra layer of safety, ensuring accurate pallet drops and reducing the risk of errors. Seegrid continues to deploy its proven and trusted AMRs in live customer environments—with hundreds of successful deployments and thousands of AMRs—all transforming how customer facilities operate without a single reportable or recordable safety incident. Beyond offering pioneering autonomous solutions, Seegrid prides itself on its ongoing service and support, proven implementations, and industry-leading ROI. Supporting more than 50 global brands, Seegrid continues revolutionizing how facilities operate. As seen in one customer manufacturing facility, more than a hundred Seegrid AMRs are responsible for nearly 80% of their non-conveyed material moves, cutting inventory levels by up to 30% and expected to deliver positive ROI in less than 18 months. With fast deployment times of weeks, not months, the RS1 can be fully integrated into facility operations without disrupting existing workflows, allowing its benefits to be experienced almost instantly. The Lift RSI AMR is designed to meet and exceed the ever-increasing demands of today’s modern manufacturing, warehousing, and logistics industries, which rely heavily on palletized material handling. Seegrid’s pioneering autonomous lift trucks continue to bring real value to customers today. As industry innovators, they will continue developing new technology to enable their customers to automate their material handling workflows more than ever before.
AAR reports Rail Traffic for the week ending November 02, 2024
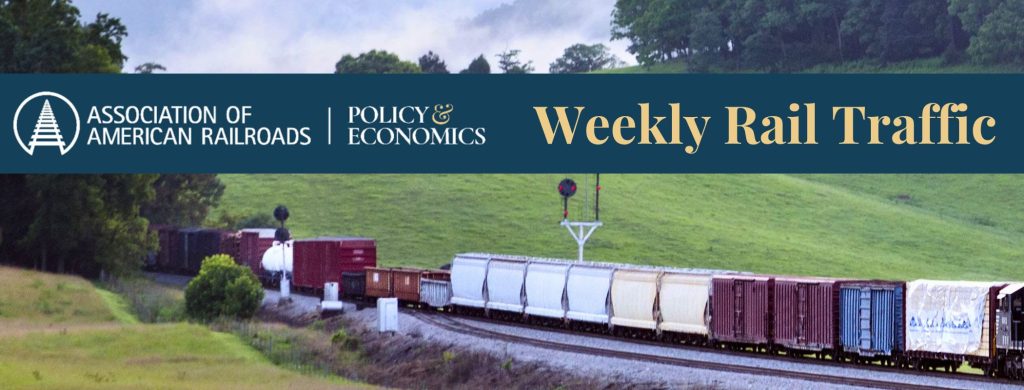
Today, the Association of American Railroads (AAR) reported U.S. rail traffic for the week ending November 2, 2024. This week’s total U.S. weekly rail traffic was 516,743 carloads and intermodal units, up 6.6 percent compared with the same week last year. Total carloads for the week ending November 2 were 228,635, up 1.9 percent from the same week in 2023, while U.S. weekly intermodal volume was 288,108 containers and trailers, up 10.7 percent from 2023. Nine of the ten carload commodity groups posted an increase compared with the same week in 2023. They included chemicals, up 2,326 carloads, to 32,425; grain, up 2,229 carloads, to 23,656; and nonmetallic minerals, up 1,911 carloads, to 33,124. One commodity group posted a decrease compared with the same week in 2023: coal, down 7,949 carloads to 57,314. For the first 44 weeks of 2024, U.S. railroads reported a cumulative volume of 9,600,065 carloads, down 3.0 percent from the same point last year, and 11,621,688 intermodal units, up 9.0 percent from last year. Total combined U.S. traffic for the first 44 weeks of 2024 was 21,221,753 carloads and intermodal units, an increase of 3.2 percent compared to last year. North American rail volume for the week ending November 2, 2024, on nine reporting U.S., Canadian, and Mexican railroads totaled 340,572 carloads, up 1.8 percent compared with the same week last year, and 371,537 intermodal units, up 9.9 percent compared to the previous year. Total combined weekly rail traffic in North America was 712,109 carloads and intermodal units, up 5.9 percent. North American rail volume for the first 44 weeks of 2024 was 29,507,054 carloads and intermodal units, up 2.4 percent compared with 2023. Canadian railroads reported 96,792 carloads for the week, down 0.8 percent, and 70,113 intermodal units, up 4.2 percent compared with the same week in 2023. For the first 44 weeks of 2024, Canadian railroads reported a cumulative rail traffic volume of 7,013,025 carloads, containers, and trailers, up 0.0 percent. Mexican railroads reported 15,145 carloads for the week, up 20.3 percent compared to last year, and 13,316 intermodal units, up 27.2 percent. Cumulative volume on Mexican railroads for the first 44 weeks of 2024 was 1,272,276 carloads and intermodal containers and trailers, up 3.0 percent from the same point last year. To view the weekly rail traffic charts, click here.
Fortifi acquires assets and intellectual property of BANSS
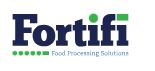
Frontmatec by Fortifi to manage the transition and provide systems, equipment, and aftermarket customer service and support Fortifi Food Processing Solutions (“Fortifi”) announced today that it has acquired the intellectual property and customer relationships as well as select inventories and fixed assets of JWE-BANSS GmbH (“BANSS”). Formerly based in Biedenkopf, Germany, BANSS was a manufacturer and provider of primary protein processing systems, equipment, and related parts. The company filed for insolvency during the summer of 2024. Through the asset acquisition, Fortifi becomes the sole legal provider of BANSS aftermarket parts and the exclusive owner of the company’s library of engineered designs and part drawings. BANSS has served customers in 94 countries and shipped more than 1,100 machines in the past two decades. Fortifi’s Frontmatec team will manage the transition and integrate the business’s assets. “I am pleased to welcome BANSS customers into the Fortifi fold,” said Massimo Bizzi, CEO of Fortifi. “We recognize the vital role that responsive customer service, innovation, high-quality solutions, and consistent on-time delivery play in our customers’ operations. Through Frontmatec, the Fortifi team is ready to ensure a smooth transition with enhanced service quality.” “Frontmatec is dedicated to revitalizing relationships with BANSS customers and earning their trust through the delivery of exceptional service and support,” said Dennis Gallagher, president of Frontmatec. “In addition to being their sole authorized source of aftermarket parts, we’re ready to provide cutting-edge food processing solutions to help drive these customers’ business growth and success.” Frontmatec, part of the Fortifi group of companies since 2022, develops world-leading customized solutions for automation across the entire protein industry value chain. Its manufacturing facility and offices in Beckum, Germany, will provide customer service, equipment and system support, and spare parts to BANSS customers.
BSL Battery-Industrial is officially listed on the ECOTEC (Micropower) Charger Compatibility list
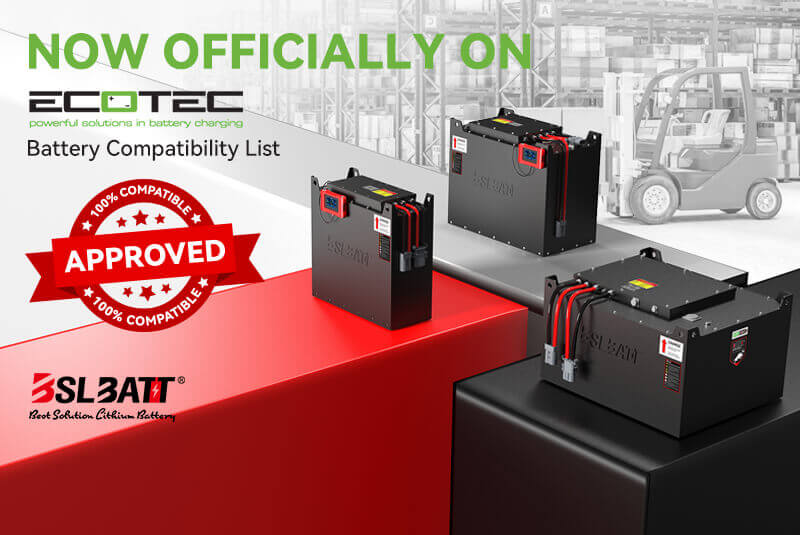
BSL Battery Industrial announced that it had joined the ECOTEC (Micropower) Charger Compatibility List. This program qualifies California customers for financing under California Edison’s “Charge Ready to Transport” program when their fleets transition to lithium-ion electric forklift infrastructure! As an ECOTEC (Micropower) partner, BSL Battery – Industrial can showcase its integration with ECOTEC (Micropower) in a curated network of tested and compatible battery and charging solutions. These are the main criteria for program eligibility: applicants must: Be within the SCE service territory Purchase or lease two or more electric forklifts within 18 months of signing the agreement The easement will be required to procure, own, install, and operate the charging stations for 10 years These are the zero-emission voucher incentive benchmarks for clean off-road equipment projects Forklift lbs. Lift Cap Funding 8,001 – 12,000 $15,000 12,001 – 20,000 $20,000 20,001 – 33,000 $50,000 >33,000 $150,000 This program will increase BSLBATT’s visibility among leading OEMs seeking warehouse lithium solutions that offer electric forklift products with best-in-class performance, extended battery life, and maximum uptime. Through this program, OEMs can view optimized BSLBATT battery algorithms with ECOTEC (Micropower), such as the one developed for the forklift lithium battery product shown below with BSLBATT installed in a Yale forklift. Haley Ning, Director of Marketing Center at BSL Battery—Industrial, said: “We are delighted to be included in the ECOTEC (Micropower) charger compatibility list. We appreciate the help provided by ECOTEC (Micropower) engineers. We work with many well-known companies that we admire, and we hope that cooperating with ECOTEC (Micropower) chargers will take our relationship with OEMs to the next level.”
Episode 534: Mastering Analytics in logistics with Milo’s Tea Company
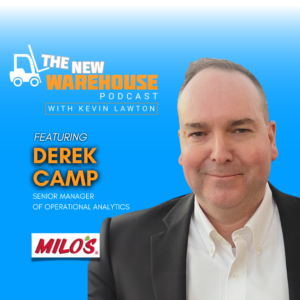
Today’s episode of The New Warehouse Podcast dives into the topic of analytics in logistics with Derek Camp, Senior Manager of Operational Analytics at Milo’s Tea Company. We cover the fascinating intersection of analytics and operations within the logistics industry, highlighting how Milo’s Tea leverages data to streamline processes and enhance efficiency. Derek shares his unique journey in the field and the innovative strategies employed at Milo’s Tea to drive success. From Replenishment to Analytics Derek Camp’s career at Milo’s began in replenishment, evolving over 11 years through roles increasingly focused on analytics. Initially managing replenishment for the company’s largest customer, Derek transitioned into sales analytics and operations. “I had never really worked in an analytics job… but reading the job description, I thought I could do a good job with it,” Derek explains. His story illustrates the power of adaptability and growth within a logistics role, emphasizing the impact of analytics across different company operations. Operational Analytics at Milo’s Tea At Milo’s Tea, operational analytics isn’t just about data collection; it’s about driving real change and efficiency across various departments. Derek discusses key metrics such as OTIF (On-Time In-Full) and OEE (Overall Equipment Effectiveness), which are crucial for assessing and enhancing production and logistics efficiency. “The higher OEE you have, the more product you can make in less time,” he notes, underlining the direct correlation between analytical insights and operational success. Analytics in Logistics: Key Performance Indicators (KPI) Milo’s Tea utilizes a strategic array of KPIs within its logistics and production operations. Derek explains how specific KPIs like Consumer Complaints Per Million (CCPM), On Time In Full (OTIF), and Overall Equipment Effectiveness (OEE) play a crucial role in their operations. Consumer Complaints Per Million (CCPM): Assesses the number of consumer complaints per million units sold. “CCPM is a quality metric that tells you how often our consumers call in with complaints about our product, whether it’s taste or, you know, packaging or whatever.” On Time In Full (OTIF): measures the percentage of deliveries that are both on time and complete, reflecting the effectiveness of the logistics operations. “OTIF is the overarching customer service metric for us. That’s what our customers look at first when you talk to them in a line review. And if your OTIF is high, then it starts the conversation off in a good way.” Overall Equipment Effectiveness (OEE): is a standard for measuring manufacturing productivity by comparing the actual output against the potential output if operations were optimal. “In production, you know, and this sort of falls into CI and production, but when we look at OEE, that is a metric that tells you how efficient you’re running your plant. And so, if you, the higher OEE you have, the more product you can make, and less time and the lower OEE you have, you’re not being efficient in making your product.” Key Takeaways on Analytics in Logistics Embracing change and new opportunities can lead to significant career advancements in logistics and operations. Key performance metrics like OTIF and OEE are integral in measuring and improving operational efficiency. Effective analytics requires a blend of accurate data, comprehensive understanding, and strategic application to foster operational success. The New Warehouse Podcast Episode 534: Mastering Analytics in Logistics with Milo’s Tea Company
Laner Conveyor for bottle and can variety case pack
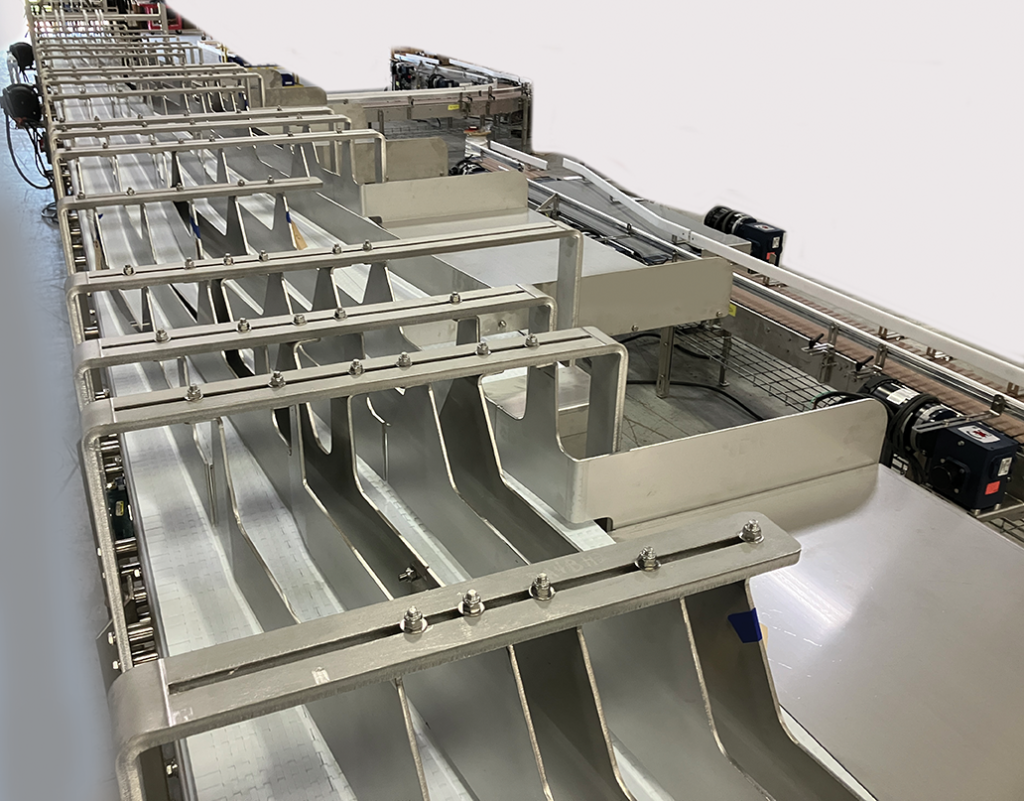
Multiple lanes, multiple flavors. Wow. Multi-Conveyor recently built a series of stainless steel-constructed conveyors to transport cans or bottles to feed a case packer. In this embedded video, we focus on the manual loading of flavor varieties that transport through an adjustable multi-laner to create multi-flavor beverage case packs. An initial conveyor (not shown) will assist the operators to load the already filled and labeled bottles or cans onto tables of three operator positions each. Multi-Conveyor employees demonstrate how operators feed the product from operator positions onto the multi-lane conveyor. Each operator loading station is responsible for a specific flavor or variety of product. The individual products travel through 6 separate lanes with adjustable guide rails up to nearly 40 feet of multi-lane travel, coming together at a common discharge end to feed the case packer The lanes combine product making a now mixed variety of can or bottle favors that create a multi-flavor case pack. Of course, this technology can also transport individual flavors as required. Lane conveyors are often fed by diverts and can be used as a means of accumulation to assist downstream processes. Laners can be equipped with a variety of devices including gates, guides, fishtails and sweeps that can be controlled manually or fully automated with programmable logic controls or PLC.
Swisslog opens new office in Canada to support growth opportunities in the region
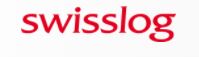
Located in Mississauga, Ontario, the new Swisslog office is the latest step in the company’s accelerated growth in the Americas region. In June, Swisslog opened a new Americas region headquarters in Atlanta. Over the past year, the company has also strengthened its sales and execution teams to support the Canadian market. “Canada’s supply chain continues to see strong growth, partly driven by an increase in imports and exports and the private sector’s commitment to increase overall supply chain efficiency,” said Sean Wallingford, president and CEO of Swisslog Logistics, Inc. “The new office will help us continue to provide automation solutions that deliver even greater support for customers, while also bringing further innovation to the region with operational efficiency.” Swisslog’s entire portfolio of automation solutions and software is available in the Canadian market, with special focus on general merchandise, food and beverage, industrial manufacturing, electronics and healthcare industries. This portfolio features fully automated end-to-end integrated solutions, including ASRS applications for unit loads and eaches, all orchestrated by Swisslog’s intelligent SynQ software. Swisslog automation experts work closely with customers to determine which solution best fits their operational needs and business objectives. Swisslog also continues to grow its 24/7 customer support network available to its North American customers. This includes over 50 field resources and over 100 full-time help desk resources, as well as an expanding group of service technicians strategically located across the region to help ensure the automation solutions help customers meet their business objectives. The company will be exhibiting at this year’s Advanced Design & Manufacturing Expo (November 13-14) at the Palais des congrès de Montréal in Montréal, Québec. Show attendees can visit the Swisslog booth (#1815) to experience the latest advancements in state-of-the-art automation solutions for storage and retrieval of pallets, cases, and totes. With more than 2,500 installations of automation solutions around the globe, Swisslog has invaluable experience in multiple flexible, scalable, and modular automation technologies. The company is also one of the leading integrators of the AutoStore system, with more than 400 AutoStore projects in over 25 countries.
ORBIS acquires Creative Techniques and expands packaging
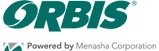
ORBIS Corporation has announced that it has acquired substantially all the assets of Creative Techniques, Inc. (CTI), which is headquartered in Orion Township, Mich. ORBIS is a subsidiary of Menasha Corporation. Terms of the transaction were not disclosed. Founded in 1984, CTI’s business focuses on designing and manufacturing custom packaging, including stand-alone trays, container dunnage, precision rack dunnage, seat pallets, and kitting trays. It offers state-of-the-art high-pressure injection molding, structural foam molding, and prototyping capabilities. ORBIS also acquired CTI’s facilities, including 60,000 square feet of manufacturing space and 22,000 square feet of warehousing space. Approximately 110 employees are joining the ORBIS team in connection with the transaction. “What excites me about this acquisition is the engineering excellence and solutions-focused approach CTI brings to its customers,” said ORBIS President Norm Kukuk. “They create tremendous value in their front-end processes, tooling development, rapid prototyping capabilities, and ultimately the high-quality packaging they deliver to customers. We look forward to welcoming their talented team to ORBIS and expanding our capabilities in these areas.” CTI serves the automotive industry and has a proven track record in delivering value to its customers with innovative products and service levels. President and CEO of Menasha Corporation Chris Drees lauded CTI’s track record of delivering value to its customers in the automotive industry with innovative products and service levels, noting that “CTI is strongly aligned with ORBIS in its focus on sustainability, customer relationships, innovation, and supply chain expertise.” ORBIS is a market leader in reusable packaging solutions for the automotive and retail supply chain markets. It produces plastic returnable totes, bulk containers, pallets, dunnage, and metal racks in twelve manufacturing sites and operates more than thirty service centers across North America and Europe.
Cyngn completes initial deployment of DriveMod Tugger with a major defense contractor
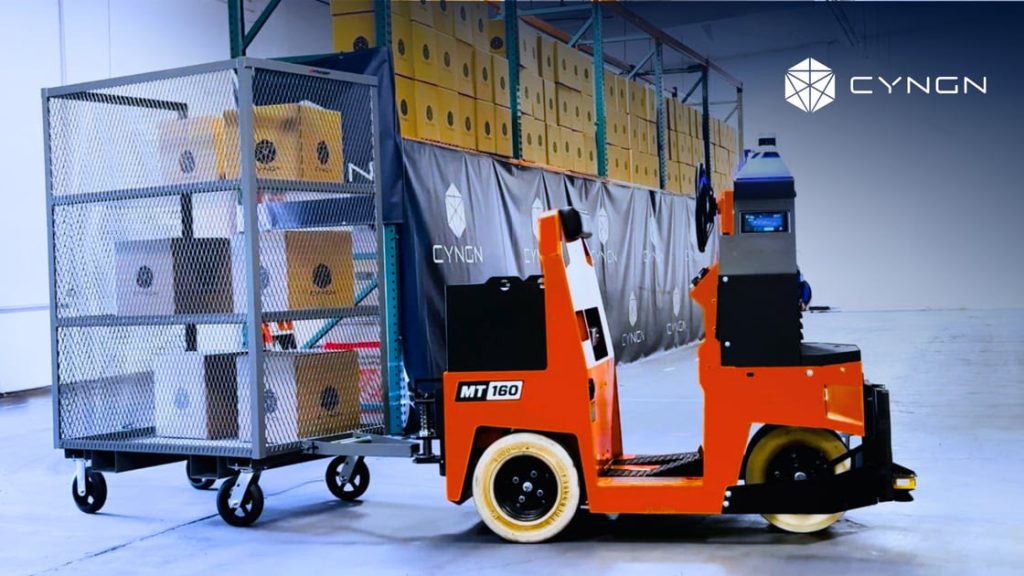
Cyngn Inc. announced that it successfully deployed its DriveMod Tugger at a defense contractor’s facility. While details are not being disclosed for security reasons, the engagement highlights the applicability of Cyngn’s autonomous vehicle technology to address the rigorous operational needs of defense industry manufacturing applications, which can be particularly stringent work environments with high associated costs. The aerospace and defense industry continues to be a significant economic force in the United States. In 2023, the industry generated an impressive $955 billion in total business output, showcasing its substantial economic impact. The sector employs over 2.2 million people, representing about 1.4% of the nation’s total employment base.
Women In Trucking Association announces its November 2024 Member of the Month
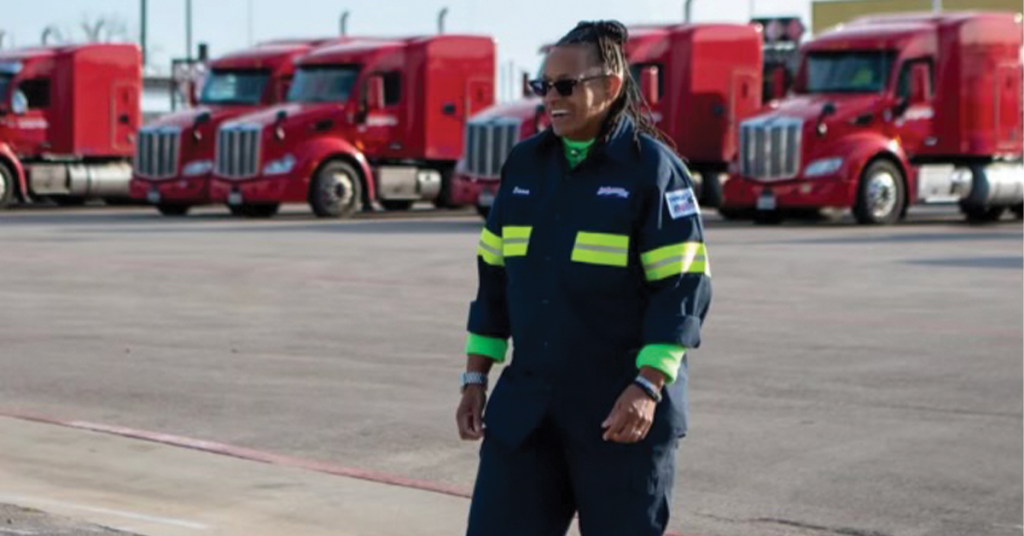
The Women In Trucking Association (WIT) has announced Dana Tarver as its November 2024 Member of the Month. Tarver is a fuel hauler for Kenan Advantage Group (KAG), a specialized transportation and logistics provider across a range of diversified end markets in the United States and Canada. In 1995, driven by tenacity and a willingness to embrace challenges head-on, Tarver began her career in the trucking industry at the age of 25. Today, she consistently demonstrates thoroughness and punctuality, adheres to all company policies and is guided by her personal motto – do it right the first time. Tarver serves as an exemplary illustration of the valuable contributions a successful driver can make, as her pride in herself, her role, and her company shines through her daily trips. With a passion for safety, Tarver meticulously maintains her equipment, takes all necessary precautions, and values mentoring others on the subject. She takes great pride in fellow professional drivers calling her for advice and guidance on the road. Through trucking, Tarver has carved out a fulfilling career that provides job security and allows her to enjoy time with family and friends without stress or exhaustion, knowing she is well taken care of. She encourages other women not to be intimidated by the male-populated industry and to recognize the opportunities for growth and success available within it. Tarver is a champion for other women navigating a career path in the trucking industry, saying, “Never be intimidated to do this job. What’s for you will be for you if you always put safety first. When in doubt, stop and ask somebody!”
Omnicon exhibits at 2024 Pack Expo and Automation Fair
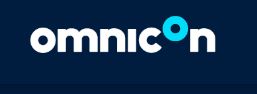
Omnicon has expanded its U.S. presence by establishing operations across several states, allowing for closer client support in the region. The company will showcase its expertise at two major industry events: Pack Expo in Chicago, Illinois, from November 3-6, 2024 at booth #LL10514, and Automation Fair in Anaheim, California, from November 18-21, 2024 at booth #1014. Omnicon has announced the expansion of its U.S. presence with new operations based in Houston, Texas, adding to the company’s established presence across the nation. With COO Daniel Gomez now located in Houston, this strategic move allows Omnicon to provide in-person support to clients across the region. “We are thrilled about our expansion within the U.S., a move that reflects our commitment to staying connected with our clients nationwide and ensuring we can offer more responsive support,” said Daniel Gomez, COO of Omnicon. “With local resources in place, we’re able to provide faster, dedicated service to meet the needs of each customer across the country.” In addition to expanding its U.S. footprint, Omnicon will showcase its expertise at two major industry events: Pack Expo, taking place November 3-6, 2024 in Chicago, Illinois, and Automation Fair, from November 18-21, 2024 in Anaheim, California. “Omnicon’s expansion of our presence in the U.S., along with our involvement in these major industry events, highlights our ongoing commitment to staying close to our customers and leading the way in industry innovation,” said Eduardo Acosta, CEO of Omnicon. “By strengthening our presence in the U.S. and taking part in key gatherings like Automation Fair and Pack Expo, we’re not only ensuring that we’re at the forefront of the latest tech developments but also reinforcing our partnerships.” At Pack Expo booth #LL10514, Omnicon will showcase its smart manufacturing solutions, including workflow orchestration, OEE performance monitoring, and MOM integration. Attendees can explore how Omnicon’s advanced automation technologies are helping manufacturers optimize production efficiency and streamline operations. Pack Expo, hosted by The Association for Packaging and Processing Technologies (PMMI), is the largest packaging and processing show in the U.S., featuring over 1,000 manufacturers and suppliers presenting the latest innovations in the industry. Omnicon, recently recognized again as one of Deloitte’s Best Managed Companies, will also be exhibiting at booth #1014 during Rockwell Automation’s Automation Fair. Known for its focus on industrial automation and digital transformation, Omnicon will showcase innovations tailored for the energy industry, highlighting solutions designed to enhance efficiency and connectivity. In a presentation during Automation Fair, in Room 201C of the Anaheim Convention Center, COO Daniel Gomez will join energy industry leader Celsia to present a success case in industrial automation and smart manufacturing. The session, titled “Pioneering Hydroelectric Industrial Automation and Remote Supervisory Revolution,” will offer insights into advanced applications of automation in the energy sector. The presentation will take place on November 20th, at 1pm PST. Automation Fair, which attracts over 15,000 attendees annually, is a premier event for exploring the latest in automation, control, and information technologies. Attendees are encouraged to visit Omnicon’s booth to discover more about the company’s industry-leading solutions.
Mallard Manufacturing hires new National Accounts Manager
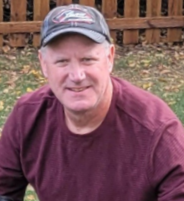
Mallard Manufacturing, a provider of gravity flow solutions, has announced the appointment of Brian Meyer as National Accounts Manager. With over 30 years of experience in the material handling industry, Brian has held pivotal roles in manufacturing and integrator/dealer sectors, making him uniquely qualified to strengthen Mallard’s national account relationships across Indiana, Missouri, Arkansas, Oklahoma, Texas, and Louisiana. Meyer will play a critical role in assessing customer needs, specifying applications, preparing project quotes, and designing solutions in his new position. His responsibilities include close collaboration with the manufacturing team and direct engagement with customers and end-users to deliver tailored solutions that enhance operational efficiencies. Kevin Risch, president of Mallard Manufacturing, commented: “Brian’s wealth of experience and deep understanding of customer needs make him an invaluable addition to our team. His leadership will further strengthen our ability to deliver customized solutions that optimize material flow and enhance operational efficiencies for our clients.” “At Mallard Manufacturing, I see an unparalleled commitment to customer-focused support and innovation,” said Meyer. “The new Innovation Lab and Testing Center exemplifies our dedication to ensuring our solutions not only meet but exceed customer expectations. This facility allows us to conduct comprehensive live-feed and interactive simulation testing, addressing potential challenges before finalizing pallet flow and carton flow solutions.” The Innovation Lab and Testing Center features state-of-the-art equipment designed to validate the performance of gravity flow products in real-world conditions. From optimizing inventory flow to troubleshooting loading and unloading processes, this facility enables Mallard Manufacturing to deliver reliable and efficient solutions tailored to specific customer needs. Brian Meyer’s addition to the team strengthens Mallard’s commitment to delivering exceptional customer value and driving innovation in the material handling industry.
Garvey Corporation Teams with Morrison Container Handling Solutions and Garrdio US to Showcase Packaging Capabilities at Pack EXPO
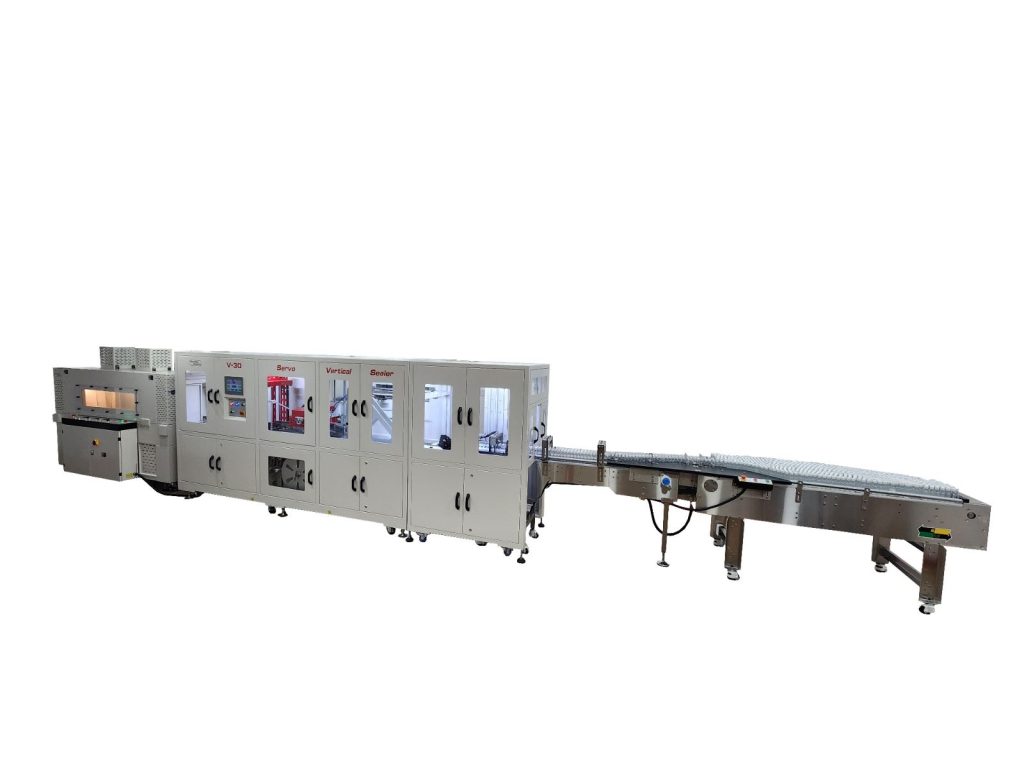
Garvey Corporation, Morrison Container Handling Solutions, and Garrido USA, and are excited to debut a new collaboration at PACK EXPO International this November. Garvey’s Bi-Flo Accumulation Conveyor acts as a critical aspect in this model showcasing its ability to have product continuously moving in lanes with precision timing to interact with the technology V-30 technology of Morrison and the T-61 DB of Garrdio. Morrison’s V-30 produces a top seal and a vertical cross seal on multi-packs, and the version on display at the show features a Garvey Bi-Flo Accumulation conveyor to create two lanes of product that feed into a Morrison timing screw drive unit that counts the containers and groups them into the assigned pack pattern. The grouped containers proceed to then continue into the inverting head which for a top seal. Next, a closing conveyor ensures the transfer within the cross-seal area is smooth while the product is being sealed. Once sealed, the packaged product transfers to Garrido’s T-61 DB tunnel for a final shrink. Upgrade options include print registration and top-flight bar infeeds for higher speed applications. “Accumulating product and single filling them, comes second nature to Garvey Corporation — accumulators are what we make.” Michael Earling, Business Development Director for Garvey Corporation (a CMCO Company) said. “What we do, is help our customer increase productivity on their production lines by up to 25%. When we can work with other OEMs, like Morrison and Garrido USA, to make a system that can solve a customer’s problem, it’s a great feeling.” The Garrido system brings a versatile, easy-to-use machine to its customers, all with a cost-effective price tag. “Our high-speed continuous motion machines with vertical cross seal have been extremely successful and well received in the industry,” Nicolas Garrido, Vice President and General Manager at Garrido, said. “Due to this, we have had request for multi-packing solutions such as this one. We are excited on growing our offering for similar solutions in partnership with Garvey and Morrison!” “Creating pack patterns and groups of containers is a very common application at Morrison Container Handling Solutions,” Vice President of Sales Dustin Lee said. “We’re really excited to provide this proven infeed method to Garrido with the help of Garvey to help make an even more efficient machine and reach more customers in our industry.” This particular system is mainly used for products that are taller than wide. The Morrison timing screw system makes it adaptable for multiple container sizes. “Morrison and Garvey are known for providing proven systems that work,” Garrido said. “The teams from both companies are extremely easy to work with and efficient in communicating through the entire project, from sales to engineering to shipment.” All three companies are known for providing expertise in their particular niche of the packaging industry, and by working together, customers will receive one machine with high quality equipment from three established OEMs. View this machine video here. To see this machine in action in person, visit Garrido’s Booth S-2576. Visit Booth N-5623 to learn more about Garvey Corporation’s offerings. You can learn more about Morrison Container Handling Solutions by visiting Booth N-4906. You can add these companies to your show planner for the best user experience.
Hamilton Caster unveils the ultimate field installable toe guard
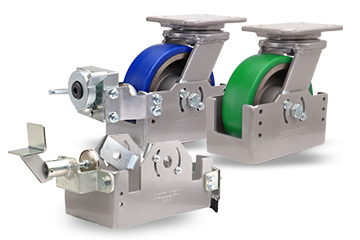
Hamilton Caster has introduced its latest innovation to enhance workplace safety —the Field Installable Toe Guard. Affectionately known as the Swiss Army knife of toe guards, this versatile solution not only enhances workplace safety by protecting feet from injury but also offers support for two brake styles—heavy-duty contact brakes and ergonomic brakes—and floor brushes, all of which are field-installable. Heavy-duty contact brakes ensure steady support for larger loads, while ergonomic brakes minimize operator strain and fatigue. Optional floor brushes sweep away foreign objects and debris during operation, protecting casters from damage and keeping pathways clear. These features enhance operational efficiency and contribute to a safer work environment, making this an essential upgrade for safeguarding employees across various environments. Constructed from robust 3/16” steel and finished in a sleek platinum gray, this toe guard ensures long-lasting durability and protection. With an industry-standard 1/2” clearance from the floor, the toe guard integrates seamlessly with existing casters, eliminating the need for drilling or modifications. Customers can opt to have the toe guard assembled onto a new caster or order it separately for easy installation on existing casters. This multi-purpose toe guard replaces Hamilton’s previous model, providing a more adaptable and customizable option available for wheel diameters 4” – 12”. “Our field installable toe guard is designed to significantly enhance safety without the need for replacing entire caster assemblies,” said Mark Lippert, president of Hamilton Caster. “Its customizable features allow users to modify protection levels to specific needs, ensuring comprehensive safety in various operational settings.” What truly distinguishes this toe guard is its versatility, offering a range of options to suit different safety needs. Key features include: Enhanced Safety: Made from 3/16” steel and designed with a standard 1/2” floor clearance to prevent costly injuries and protect workers Comprehensive Kit: Includes a replacement axle, 2 lock clips, and 4 nuts for a complete and hassle-free installation. Compatibility: Available in 8 different caster sizes, accommodating 4” – 8” diameter wheels with 2” tread widths and 6” – 12” diameter wheels with 3” tread widths. Customizable Options: Enhance functionality with 2 heavy duty brake styles that can be mounted on the front or back, and floor brushes “Staying true to Hamilton’s legacy of quality, our field installable toe guards are manufactured in-house, ensuring exceptional durability and faster delivery,” Lippert added. “This streamlined production process reduces lead times and enhances customer satisfaction.” For additional customization, upon request we offer a unique height-adjustable skirt, allowing adjustments up to 1” off the floor, tailoring the level of protection in special cases, such as up-slope travel of casters. Whether you’re seeking a straightforward safety upgrade or a highly customizable solution, Hamilton’s field installable toe guard is the ultimate tool for workplace safety. For complete specs and product details check out the all-new Field Installable Toe Guard Landing Page or contact our team to learn how the Field Installable Toe Guard can elevate safety in your facility.