SupplyOne receives prestigious Pregis Inspyre and Preserve awards
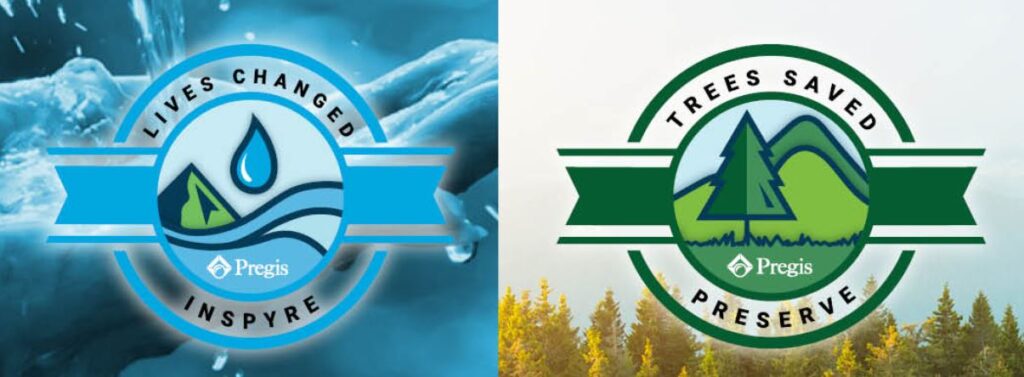
SupplyOne, Inc., the largest independent supplier of corrugated and other value-added packaging products, equipment, and services in North America, just announced it has been honored with the Pregis Inspyre and Preserve awards. These awards highlight SupplyOne’s commitment to sustainability and dedicated efforts to improve lives worldwide. Pregis’s Inspyre Award honors customers who are changing lives through their commitments to a better world. As a member of the ‘1% for the Planet’ initiative, 1% of all Pregis’s Inspyre sales go directly to Uzima, a non-profit that provides life-changing water filters to communities in need. SupplyOne’s Packaging Specialists objectively assess each unique customer’s application and, drawing from the broadest range of packaging products available, provide unbiased guidance on the optimal packaging solution to address their objectives. Through this process and subsequent recommendation of Pregis’ Inspyre packaging, SupplyOne directly contributes to global clean water access. Through the Inspyre initiative, SupplyOne has made a significant difference, impacting over 6,900 lives. It’s a stark reality that one in nine people worldwide experiences water insecurity. This often leads to waterborne illnesses and contributes to a cyclical trap of poverty. Each Uzima filter can provide clean water to a family of 6-10 people, reducing medical expenses, improving school attendance, and empowering better lives. The Pregis Preserve Award recognizes efforts to promote sustainable Easypack paper solutions. Pregis’s Easypack paper is 100% recycled, 100% recyclable, and 100% biodegradable. This chain of custody-certified product has tangible benefits for the world’s forests. Each ton of Easypack paper used equates to 17 trees saved from harvest. Healthy forests are vital in reducing carbon dioxide levels, providing cleaner air and water, and offering sanctuary for vulnerable species. By helping manufacturers and processors implement Easypack paper solutions, SupplyOne has helped save over 13,000 trees from harvest, further demonstrating its commitment to a greener planet. These accolades underscore SupplyOne’s dedication to sustainability and social responsibility. We are grateful to Pregis for the recognition and will continue to work towards positively impacting our shared environment.
AAR reports Rail Traffic for the week ending July 27, 2024
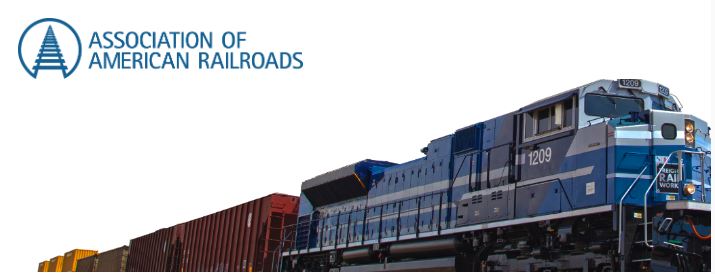
The Association of American Railroads (AAR) has reported U.S. rail traffic for the week ending July 27, 2024. This week, the total U.S. weekly rail traffic was 508,496 carloads and intermodal units, up 5.3 percent from the same week last year. Total carloads for the week ending July 27 were 228,845, down 0.5 percent from the same week in 2023, while U.S. weekly intermodal volume was 279,651 containers and trailers, up 10.5 percent from 2023. Four of the ten carload commodity groups posted an increase compared with the same week in 2023. They included grain, up 5,676 carloads, to 20,665; farm products excl. grain, and food, up 1,461 carloads, to 16,811; and forest products, up 418 carloads, to 8,360. Commodity groups that posted decreases compared with the same week in 2023 included coal, down 6,142 carloads, to 61,382; nonmetallic minerals, down 1,316 carloads, to 33,264; and metallic ores and metals, down 602 carloads, to 21,455. For the first 30 weeks of 2024, U.S. railroads reported a cumulative volume of 6,422,997 carloads, down 4.2 percent from the same point last year, and 7,683,689 intermodal units, up 8.5 percent from last year. Total combined U.S. traffic for the first 30 weeks of 2024 was 14,106,686 carloads and intermodal units, an increase of 2.3 percent compared to last year. North American rail volume for the week ending July 27, 2024, on ten reporting U.S., Canadian, and Mexican railroads totaled 329,218 carloads, down 2.4 percent compared with the same week last year, and 356,464 intermodal units, up 6.6 percent compared with last year. Total combined weekly rail traffic in North America was 685,682 carloads and intermodal units, up 2.0 percent. North American rail volume for the first 30 weeks of 2024 was 19,797,795 carloads and intermodal units, up 2.3 percent compared with 2023. Canadian railroads reported 84,556 carloads for the week, down 4.0 percent, and 64,306 intermodal units, down 6.2 percent compared with the same week in 2023. For the first 30 weeks of 2024, Canadian railroads reported a cumulative rail traffic volume of 4,803,839 carloads, containers, and trailers, up 1.6 percent. Mexican railroads reported 15,817 carloads for the week, down 18.3 percent compared with the same week last year, and 12,507 intermodal units, down 3.8 percent. Cumulative volume on Mexican railroads for the first 30 weeks of 2024 was 887,270 carloads and intermodal containers and trailers, up 4.8 percent from the same point last year. To view the weekly rail charts, click here.
KION significantly increases profitability in the first half of 2024 driven by improvements in both operating segments
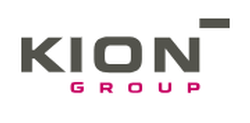
Revenue up by 2 percent to € 5.736 billion (H1 2023: € 5.617 billion) Adj. EBIT improves 28 percent to € 447 million (H1 2023: € 348 million) Adj. EBIT margin of 7.8 percent (H1 2023: 6.2 percent) Free cash flow of € 202 million (H1 2023: € 229 million) Outlook for 2024 confirmed with narrowed bandwidths The KION Group continued to deliver strong earnings and margins in the first half of 2024. With revenues of € 5.736 billion (H1 2023: € 5.617 billion) and a 28 percent higher adjusted EBIT of € 447.0 million (H1 2023: € 348.3 million), the adjusted EBIT margin went up by 160 basis points to 7.8 percent (H1 2023: 6.2 percent). “Significant year-on-year profitability improvements in both operating segments led to a 28 percent increase of our adjusted EBIT in the first half of the year,” says Rob Smith, Chief Executive Officer of KION GROUP AG. “Despite a slower market recovery in the current financial year, we are well on track to achieve our outlook. Our clear strategy, our broad range of products and solutions for customers and our presence in all key markets position KION very well for the future.” The Industrial Trucks & Services segment increased total revenues by 4.1 percent to € 4.306 billion (H1 2023: € 4.135 billion), supported by a higher number of products delivered and previous price increases. The revenue in the service business grew by 2.3 percent across all key categories. Despite a slight increase in the second quarter, total revenue in the Supply Chain Solutions segment declined to € 1.451 billion (H1 2023: € 1.497 billion) in the first half of 2024 – mainly due to lower order intake in the project business in previous quarters. The service business revenue increased by 11.9 percent compared to the first half of 2023. Adjusted EBIT for the Industrial Trucks & Services segment improved substantially to € 470.7 million (H1 2023: € 378.9 million). Revenue growth combined with stable material purchase prices led to a significantly higher gross margin. The adjusted EBIT margin increased to 10.9 percent (H1 2023: 9.2 percent). At € 42.1 million, adjusted EBIT in the Supply Chain Solutions segment almost tripled compared to the previous year (€ 14.8 million). Improved project implementation, efficiency measures and, in particular, the growth in the service business contributed to the improvement in earnings and margins. The adjusted EBIT margin rose to 2.9 percent (H1 2023: 1.0 percent). KION Group net income improved to € 181.7 million in the first half of 2024 (H1 2023: € 146.3 million). This corresponds to undiluted earnings per share of € 1.35 (H1 2023: € 1.09). Free cash flow was € 202.2 million (H1 2023: € 228.8 million) in the first six months of 2024 reflecting the high operating result. Outlook confirmed and narrowed The KION Group expects the global industrial trucks market (in units) to remain on the prior year level in 2024 compared to earlier expectations of slight growth. In the market for supply chain solutions, the KION Group now expects the global market volume in 2024 (measured in terms of revenue) to decline slightly compared with the previous expectation of a slight growth. Based on the business performance in the first half of the year and the updated market expectations, the Executive Board of KION GROUP AG has confirmed its outlook and narrowed its guidance ranges for the 2024 financial year as follows: Outlook 2024 KION Group Industrial Trucks & Services Supply Chain Solutions in € million Outlook 2024 Outlook 2024 adjusted Outlook 2024 Outlook 2024 adjusted Outlook 2024 Outlook 2024 adjusted Revenue1 11,200 – 12,000 11,300 – 11,700 8,500 – 9,000 8,500 – 8,700 2,700 – 3,000 2,800 – 3,000 Adjusted EBIT1 790 – 940 830 – 920 850 – 950 870 – 930 60 – 120 80 – 120 Free cash flow 550 – 670 550 – 670 – – – – ROCE 7.4% – 8.8% 7.7% – 8.7% – – – – 1 Disclosures for the Industrial Trucks & Services and Supply Chain Solutions segments also include intra-group cross-segment revenue and effects on EBIT. Key performance indicators for the KION Group and its two operating segments for the first half-year of 2024 and for the second quarter ending June 30, 2024 in € million Q2/2024 Q2/2023 Diff. H1/2024 H1/2023 Diff. Revenue Industrial Trucks & Services Supply Chain Solutions 2,877 2,153 732 2,836 2,130 714 1.4% 1.1% 2.5% 5,736 4,306 1,451 5,617 4,135 1,497 2.1% 4.1% -3.1% Adjusted EBIT [1] Industrial Trucks & Services Supply Chain Solutions 220.3 231.0 23.7 192.3 202.3 7.7 14.5% 14.2% > 100% 447.0 470.7 42.1 348.3 378.9 14.8 28.3% 24.2% > 100% Adjusted EBIT margin [1] Industrial Trucks & Services Supply Chain Solutions 7.7% 10.7% 3.2% 6.8% 9.5% 1.1% – – – 7.8% 10.9% 2.9% 6.2% 9.2% 1.0% – – – Net income 70.7 72.8 -2.9% 181.7 146.3 24.1% Basic earnings per share (in €) (undiluted) [2] 0.52 0.54 -4.1% 1.35 1.09 23.6% Free cash flow [3] 136.5 123.9 12.7 202.2 228.8 -26.5 Order intake [4] Industrial Trucks & Services Supply Chain Solutions 2,640 1,966 677 2,872 2,001 881 -232 -35 -204 5,079 3,770 1,318 5,273 3,957 1,335 –194 -188 -17 Order book [4], [5] Industrial Trucks & Services Supply Chain Solutions 5,272 2,602 2,732 6,045 3,197 2,921 -773 -595 -189 Employees [6] 42,303 42,325 -22 [1] Adjusted for effects of purchase price allocations as well as non-recurring items. [2] Net income attributable to shareholders of KION GROUP AG: € 177.0 million (H1/2023: € 143.3 million). EPS calculation is based on average number of shares of 131.1 million. [3] Free cash flow is defined as cash flow from ongoing business plus cash flow from investment activity. [4] Prior-year figures for order intake and order book have been definition-related adjusted in the SCS segment. [5] Figures as of June 30, 2024, compared to balance sheet date Dec. 31, 2023. [6] Number of full-time equivalents incl. apprentices and
Episode 507: Live from WERC 2024: Rapyuta Robotics
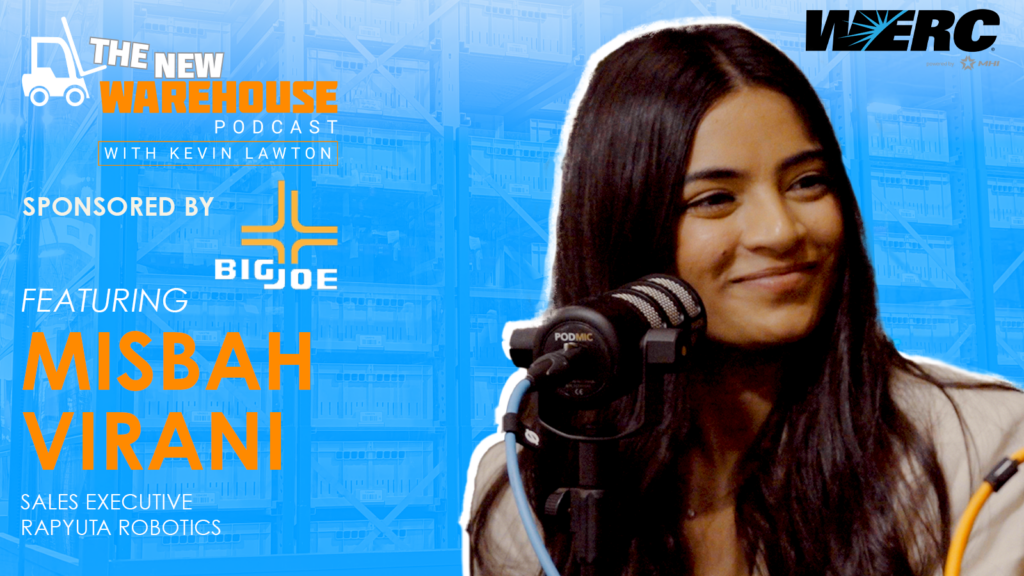
Today, we’re diving into a fascinating discussion from the New Warehouse Podcast, recorded live at the WERC 2024 conference in the vibrant city of Dallas, Texas. Kevin sat down with the dynamic Misbah Virani from Rapyuta Robotics, who handles partnerships in North America. Here’s a rundown of their engaging conversation on Rapyuta Robotics’ foray into the North American market and their innovative automation solutions. Entering the North American Market Rapyuta Robotics, originally based in Tokyo, Japan, has made significant strides since entering the North American market about a year ago. Misbah shared that the company has firmly established its presence in the Japanese market, boasting a 70 percent market share with their pick-assist robots. This success has emboldened their expansion into North America, with new offices set up in Schaumburg, Illinois. Misbah pointed out that both the Japanese and North American markets are eager for automation, largely driven by labor shortages. What’s fascinating is the quick impact on productivity levels, evidenced by their data showcasing a twofold increase in productivity where these robots are deployed. Pick-Assist Robots: Enhancing Productivity For those unfamiliar with their offerings, Misbah elaborated on the pick-assist robots. Designed to work alongside humans, these robots optimize tasks like picking items by minimizing travel time for employees and reducing errors. Instead of employees running around, the robots guide them efficiently through the warehouse, increasing overall productivity. Misbah emphasized that Rapyuta Robotics’ solutions are scalable. Businesses can add more robots as their operations grow, ensuring they meet productivity goals even during peak seasons. What sets them apart is their dedication to support. Rapyuta Robotics offers 24/7 on-call support and onsite engineers to ensure seamless integration, with robots designed to work in narrow aisles ranging from 3 to 5 feet, showcasing extraordinary agility. Tailored Automation Solutions One crucial takeaway from Mizba’s insights is that automation doesn’t have to be an all-or-nothing approach. Rapyuta Robotics offers a unique simulator to help businesses understand the ROI and the number of robots they might need. This consultative approach is a hit among potential clients, as it provides a clear picture without upfront costs. If you’re intrigued by these innovations, Rapyuta Robotics offers several ways to see their robots in action. From virtual and onsite demos to live demonstrations at client facilities, they ensure potential customers get a comprehensive look at their solutions. The New Warehouse Podcast Live from WERC 2024: Rapyuta Robotics
Kito Crosby announced significant investment in Peerless chain manufacturing equipment
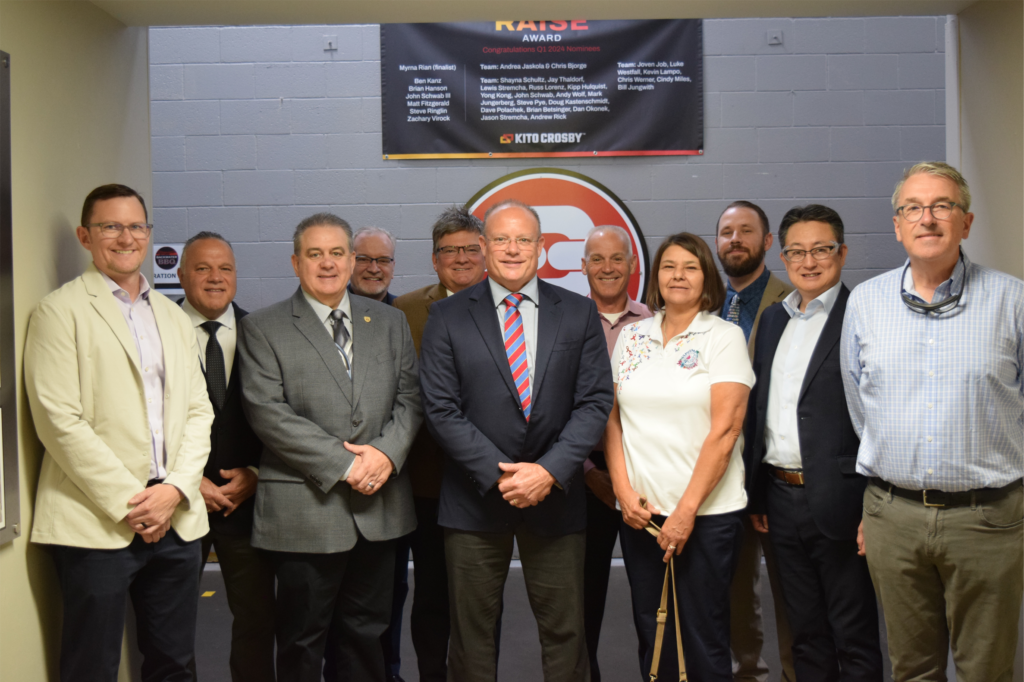
Kito Crosby, a global leader in the lifting and securement industry, proudly announces the completion of a major investment at its flagship manufacturing site of Peerless branded products in Winona, Minnesota. The multi-year, multi-million-dollar, project involved the design, installation, and startup of an advanced continuous plating system utilized in chain production. This state-of-the-art system adds a unique and proprietary coating to a chain that prevents rust and corrosion to our already world-class product. Designed to further enhance product quality and employee safety, the new plating system incorporates new features, such as automated monitoring and increased air handling systems. “This line was designed with our customers and team members in mind,” said George Kosidowski, President of Peerless. “The investment will enhance our internal processes, which will improve our service levels to customers and scale our operations for increased demand.” The Winona plant, like all Kito Crosby manufacturing facilities worldwide, is heavily vertically integrated, with a Peerless chain manufactured in the United States from raw material to finished product on site. A special ribbon-cutting ceremony was held in July with Winona team members and Kito Crosby leaders, local dignitaries, and the International Association of Machinists & Aerospace Workers (IAMAW) leadership. Continuous plated chains are used across multiple industries, including food processing, cargo control, trailer safety, and hardware.
H&E Equipment Services, Inc. reports second quarter 2024 results
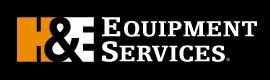
H&E Equipment Services, Inc. reported financial results for the second quarter that ended June 30, 2024, including further expansion of its branch network which now extends to 31 states. SECOND QUARTER 2024 SUMMARY WITH A COMPARISON TO SECOND QUARTER 2023 Revenues increased 4.5% to $376.3 million compared to $360.2 million. Net income was $33.3 million compared to $41.2 million. The effective income tax rate was 27.8% compared to 26.3%. Adjusted EBITDA totaled $173.2 million, an increase of 2.8% compared to $168.6 million. Adjusted EBITDA margins were 46.0% of revenues compared to 46.8%. Total equipment rental revenues were $312.4 million, an increase of $20.9 million, or 7.2%, compared to $291.5 million. Rental revenues were $275.5 million, an increase of $16.8 million, or 6.5%, compared to $258.7 million. Sales of rental equipment decreased 11.9% to $34.9 million compared to $39.7 million. Gross margin declined to 45.5% compared to 46.7%. Total equipment rental gross margins were 45.5% compared to 46.8%. Rental gross margins were 51.0% compared to 51.8%. Average time utilization (based on original equipment cost) was 66.4% compared to 69.3%. The Company’s rental fleet, based on original acquisition cost, closed the second quarter of 2024 at $2.9 billion, an increase of $279.0 million, or 10.7%. Average rental rates increased 1.9% compared to the second quarter of 2023, and declined 0.1% compared to the first quarter of 2024. Dollar utilization of 38.6% compared to 40.6% in the second quarter of 2023 and 37.0% in the first quarter of 2024. Average rental fleet age on June 30, 2024, was 40.0 months compared to an industry average age of 48.1 months. Paid regular quarterly cash dividend of $0.275 per share of common stock. Reviewing the Company’s second quarter performance, Brad Barber, chief executive officer of H&E noted, “Rental revenues increased 6.5% compared to the year-ago quarter, with the increase led primarily by the ongoing expansion of our branch network. A total of 23 new locations, including acquisitions, were opened over the last twelve months ending June 30, 2024, providing important access to new markets with expanding opportunities. Also, we received support from rental rates, which improved 1.9% compared to the year-ago level. On a sequential quarterly basis, rental rates in the second quarter declined 0.1%. The improvement in revenues was partially offset by lower average physical utilization, which closed the quarter at 66.4%, or a decline of 290 basis points compared to the year-ago result. Average physical utilization in the second quarter recorded a sequential quarterly improvement of 280 basis points. Finally, we closed the quarter with an original equipment cost (OEC) of $2.9 billion, a 10.7% increase from the year-ago quarter, including a gross fleet investment of $122.1 million in the second quarter and $196.5 million through the first six months of 2024. Our 2024 expected gross fleet expenditures remain in a range of $350 million to $400 million.” Mr. Barber described the Company’s sustained focus on expansion into key U.S. markets, stating, “We opened six new branch locations during the second quarter that enhance our presence in the Southeast, Gulf Coast and Mid-Atlantic regions of the U.S., representing attractive geographies with increasing construction activity and excellent long-term potential. Also, the completion of our latest acquisition in May 2024 resulted in the addition of four branches in northern and central Montana, increasing our presence in that state to six locations while maximizing our exposure to a diverse set of project opportunities. This long-term strategic commitment to expanding our market presence provides greater scale and advantageously positions the Company for future opportunities and improved financial performance. We concluded the second quarter of 2024 with 149 branches across 31 states, representing growth of approximately 45% over the last 36 months ending June 30, 2024.” Commenting on the outlook for the equipment rental industry, Mr. Barber said, “We reiterate our view of a more moderate level of spending and project starts as the construction industry continues to transition to a lower level of activity compared to levels in 2022 and 2023. Higher project financing costs and more stringent lending standards have led to curtailed spending, especially among smaller contractors. Conversely, we are encouraged by the continued growth in mega projects and increased infrastructure project funding. H&E’s participation in these projects continues to rise as the Company fully leverages its increased scale in the U.S. Mega projects are a meaningful growth opportunity for H&E and our industry, and given their size and long duration, they provide a more stable base of demand in support of key industry fundamentals.” FINANCIAL DISCUSSION FOR SECOND QUARTER 2024 Revenue Total revenues improved to $376.3 million, or 4.5%, in the second quarter of 2024 from $360.2 million in the second quarter of 2023. Total equipment rental revenues of $312.4 million improved 7.2% compared to $291.5 million in the second quarter of 2023. Rental revenues of $275.5 million increased 6.5% compared to $258.7 million in the second quarter of 2023. Sales of rental equipment totaled $34.9 million, a decrease of 11.9% compared to $39.7 million in the second quarter of 2023. Sales of new equipment of $10.7 million increased 20.5% compared to $8.9 million in the same quarter of 2023. Gross Profit Gross profit totaled $171.3 million in the second quarter of 2024, increasing 1.7% compared to $168.4 million in the second quarter of 2023. Gross margin declined to 45.5% for the second quarter of 2024 compared to 46.7% for the same quarter in 2023. On a segment basis, gross margin on total equipment rentals was 45.5% in the second quarter of 2024 compared to 46.8% in the second quarter of 2023. Rental margins were 51.0% compared to 51.8% over the same period of comparison. Rental rates in the second quarter of 2024 were 1.9% better than rates in the second quarter of 2023. Time utilization (based on original equipment cost) was 66.4% in the second quarter of 2024 compared to 69.3% in the second quarter of 2023. Gross margins on sales of rental equipment improved to 62.4% in the second quarter of 2024 compared to 59.1% in second quarter of 2023. Gross margins on sales of new equipment were 16.9% in the second quarter of 2024 compared to 14.9% over the same period of comparison. Rental Fleet The original equipment cost of the Company’s rental fleet as of June 30, 2024, was approximately $2.9 billion, representing an increase of $279.0 million, or 10.7%, from the end of the second quarter of 2023. Dollar utilization in
Moderna Products quadruples its capacity for plastic pet supplies with an automated warehouse from Mecalux
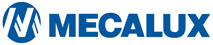
The sustainable accessories manufacturer expects to double its sales amidst the expansion of an industry set to reach $500 billion by 2030. Its facilities in Izegem (Belgium) manage over 1,500 pallets daily, producing, storing, and distributing feeders, water bowls, and beds to more than 79 countries. logo. With the pet industry growing rapidly — projected to reach a value of $500 billion by 2030, according to Bloomberg — Moderna Products aims to double its sales in the next five years. The company will continue providing litter boxes, beds, carriers, feeders, and water dispensers for pets in over 79 countries worldwide. “We manufacture plastic injection molded products in two large centers in Izegem and South Carolina. We’re proud to say we manage the entire supply chain, spanning product development, production, storage, and distribution,” says Bart Bonte, owner and CEO of Moderna Products. The third-generation family business invests in “the most advanced technologies to remain competitive.Our priority is to use highly energy-efficient storage and production systems while maintaining our return on investment,” says Bonte. Moderna Products is committed to eco-friendly practices, signing a Green Pact and equipping its headquarters with solar panels. The manufacturer of sustainable plastic pet products has automated the movements of 1,500 pallets a day with an energy-efficient rack-supported building. Measuring 131′ high by 328′ long, the facility constructed by Mecalux accommodates 12,560 pallets. Additionally, Moderna Products manages all operations with Easy WMS. This software solution monitors every step — from order receipt to shipping — providing complete control over the company’s pet supplies. Moderna Products has also installed the WMS for Manufacturing module to integrate the warehouse with the production lines and gain end-to-end traceability of its raw materials. “Automation was the logical step. Our logistics processes had to align with the robotic advancements already underway in our production operations. We opted for automation to expand our space, enhance safety, and make our processes more environmentally friendly. As a result, we no longer require traditional lighting,” says Bonte. Automation, the backbone of the facility, ensures the uninterrupted flow of goods between the center’s various zones. Five twin-mast stacker cranes handle pallet movements inside the storage aisles. Meanwhile, a conveyor system transports pet products to the manufacturing and picking areas. With these upgrades in place, Moderna Products looks forward to continuing its commitment to caring for dogs and cats, which it has done since 1980.
Stoecklin Logistics expands North American team
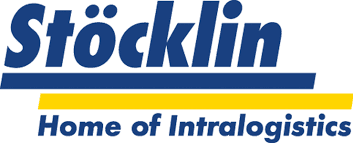
With over seven decades of combined experience in the sales and service industry, new hires Albert Trail, Dejan Ockerl, and James Wright will help expand Stoecklin’s customer support and maintenance capabilities Stoecklin Logistics, Inc., has announced three new experts to its North American team. Strategically located near Stoecklin Logistics’ US office in Georgia, each new hire comes with an extensive background in automated equipment systems and will leverage their combined experience to foster new and existing relationships with key accounts to support Stoecklin Logistics’ growth strategy across the U.S. and Canada. Albert Trail, Sales Manager, Stoecklin Logistics, comes to Stoecklin Logistics with decades of experience in helping companies automate and improve their supply chains. His experience extends to many industries including automotive, pharmaceutical, cosmetic, food, and confectionery. As sales manager, Trail will apply his expertise in automation to help Stoecklin build its network and future-proof customers’ supply chains. Dejan Ockerl, Service Manager, Stoecklin Logistics, has a versatile skill set combining technical, commercial, and managerial expertise. His background includes experience in preventative maintenance, field service, and electrical troubleshooting for large organizations throughout Europe and North America. In his new role as service manager, Ockerl will lead Stoecklin’s service team in analyzing and improving the performance of its solutions. Among Ockerl’s team is new hire James Wright, Service Technician. Wright joins Stoecklin Logistics with an extensive background in field service engineering and maintenance and will be responsible for preventative maintenance, repairs, and on-site support for the company’s North American customers. “Businesses in all sectors are seeking reliable, professional services, support, and solutions. At Stoecklin, we strive to be more than just an automated systems provider—We’re a technology and business partner that helps its customers accelerate operations and improve their supply chains through speed, agility, and safety. The expansion of our sales and service teams in North America only deepens our commitment to providing unparalleled customer service and supporting long-term growth,” said Juerg Frefel, CEO, Stoecklin Logistics. Last month, Stoecklin Logistics was named the overall winner of the 2024 Top 3PL & Cold Storage Providers Award for its dedication in helping distributors improve sustainability efforts and supply chain efficiency with its solutions.
Women In Trucking Association names 2024 Top Woman-Owned Businesses in Transportation
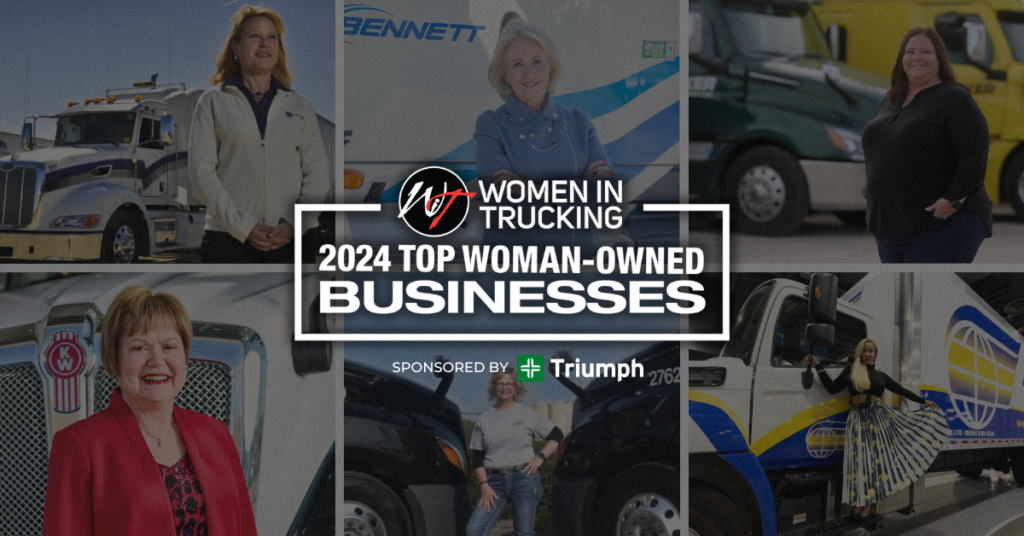
Redefining the Road magazine, the official magazine of the Women In Trucking Association (WIT), announced the recipients of the 2024 “Top Woman-Owned Businesses in Transportation.” “There is a significant economic impact of woman-owned businesses,” said Brian Everett, group publisher and editorial director of Redefining the Road magazine. “In fact, in the United States alone, there are nearly 14 million woman-owned businesses, accounting for nearly 40% of all small businesses. These businesses are thriving due to the entrepreneurial strengths and skill sets of these driven women owners. Woman-owned businesses employ millions of people and generate some $2.7 trillion in annual revenue.” Criteria used to identify qualified applicants include majority ownership by a woman, financial stability and growth, innovation, and entrepreneurial spirit, according to Everett. Each company was nominated and chosen based on business success and accomplishments, including those related to gender diversity. “It’s a privilege for the Women In Trucking Association to honor the 2024 Top Woman-Owned Businesses in Transportation,” said Jennifer Hedrick, president and CEO of WIT. “These 15 companies exemplify outstanding business practices and innovation and are led by female pioneers in this industry.” There is a broad range of company sizes named to the 2024 “Top Woman-Owned Businesses in Transportation” list, which is sponsored by Triumph, but all must generate a minimum of $5 million in gross annual sales. Companies named to the 2024 “Top Woman-Owned Businesses in Transportation” list and the primary female business owners are: AGT Global Logistics (Angela Eliacostas, founder & president) Andy Transport (Andreea Crisan, president & CEO) Aria Logistics (Arelis Bonilla, founder & president) Bennett Cartage Consultants, Inc., Evans Delivery Jacksonville (Tammy Bennett, president) Bennett Family of Companies (Marcia G. Taylor, CEO) Brenny Transportation, Inc. (Joyce Brenny, founder & CEO) Garner Trucking, Inc. (Sherri Garner Brumbaugh, president & CEO) Hassett Logistics (Michelle Halkerston, president & CEO) HTR Logistics (Lindsey Haught, founder & president) Kirsch Transportation Services, Inc. (Camilla Moore-Kirsch, founder & CEO) Partners Funding, Inc. (Sherri DeJong, vice president, co-founder & co-owner) Powersource Transportation (Barb Bakos, owner & president) Rihm Family Companies (Kari Rihm, president & CEO) S-2international LLC (Jennifer Mead, CEO) Tucker Freight Lines (Sauny Tucker, CEO) The 2024 “Top Woman-Owned Businesses in Transportation” will be recognized during a special program at the upcoming Women In Trucking Accelerate! Conference & Expo, which takes place Nov. 10-13 in Dallas, TX. For more information, visit www.womenintrucking.org.
Episode 506: Automated Storage and Retrieval Systems (ASRS) with Element Logic
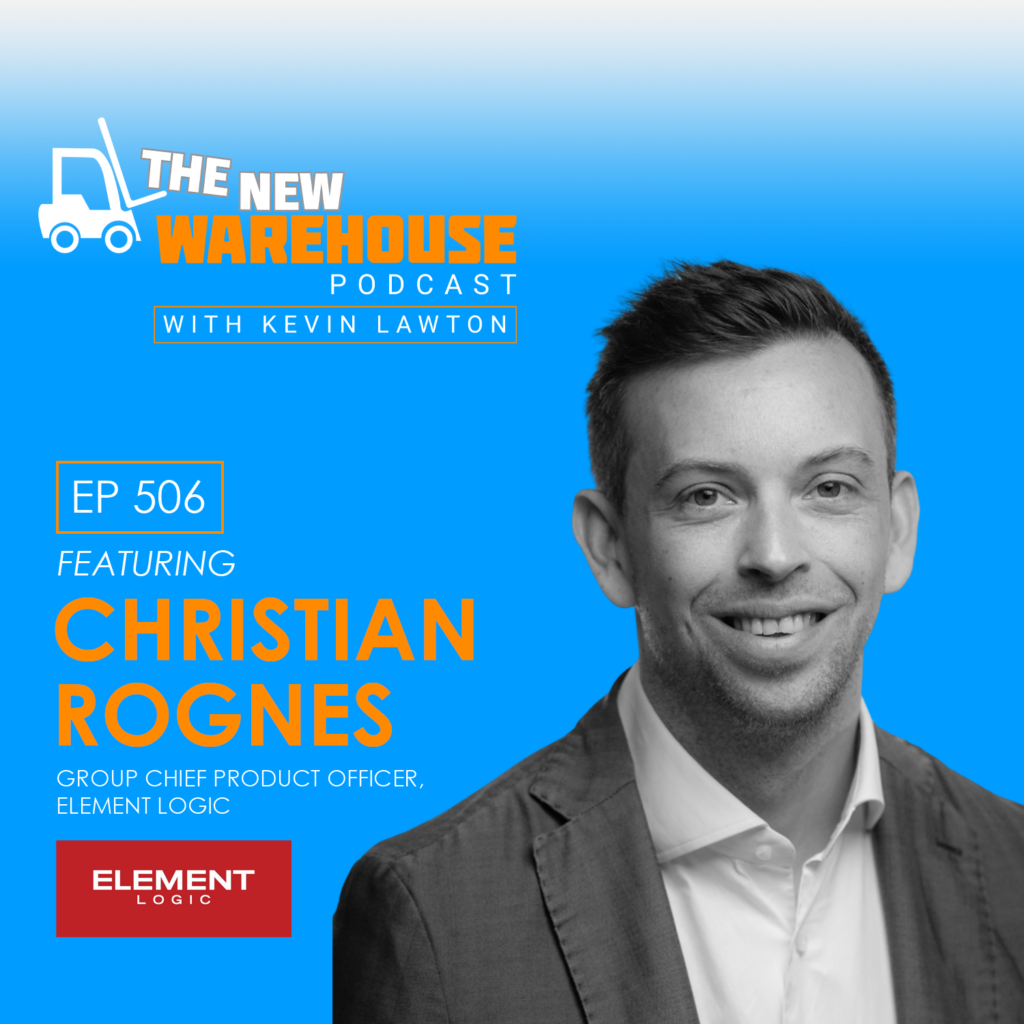
The New Warehouse Podcast episode features Christian Rognes, the Chief Product Officer at Element Logic. Element Logic is the first and largest AutoStore partner, specializing in automated storage and retrieval systems (ASRS). In this episode, we delve into the evolution of ASRS, Element Logic’s journey, and its innovative approach to warehouse automation. The Evolution of ASRS Systems Element Logic has pioneered the ASRS market, and Christian Rognes shares insights into the journey from manual to automated systems. He emphasizes, “The first battle that we had to fight was between manual and automation.” Over the years, ASRS technology has rapidly evolved, driven by the need for efficiency and precision in e-commerce. Christian highlights that Europe has been a front-runner in adopting these systems, noting, “We have approximately 30 to 40 percent of the install base worldwide.” While most of Element Logic’s install base resides in Europe, Christian sees huge growth potential in the U.S. Differentiating in a Crowded Market Christian explains that with many companies offering similar technologies, Element Logic stands out by focusing on user-centric solutions. “It’s really about finding what’s unique with Element Logic and how we can play on those competitive assets.” By integrating AutoStore with other technologies and optimizing its software, Element Logic ensures seamless warehouse operations. The holistic approach to warehouse management is crucial, especially in complex markets like the U.S., where customized solutions are necessary to meet diverse needs. Enhancing the Warehouse User Experience A major focus for Element Logic is improving the user experience in warehouses. Christian discusses the importance of understanding the needs of warehouse workers, saying, “We really have to flip this around and talk to the users.” By developing products that address the specific pain points of warehouse operations, Element Logic aims to enhance productivity and worker satisfaction. This user-centric approach improves efficiency and contributes to better working conditions, which is a significant aspect of their mission. Key Takeaways on Automated Storage and Retrieval Systems Element Logic holds 30-40% of the global AutoStore install base. The shift from manual to automated systems is crucial for modern warehousing. Differentiation through user-centric solutions is key in a competitive market. Improving user experience in warehouses enhances productivity and worker satisfaction. The New Warehouse Podcast Episode 506: Automated Storage and Retrieval Systems (ASRS) with Element Logic
BSLBATT® relocates to new factory and triples production space to accelerate customer expansion
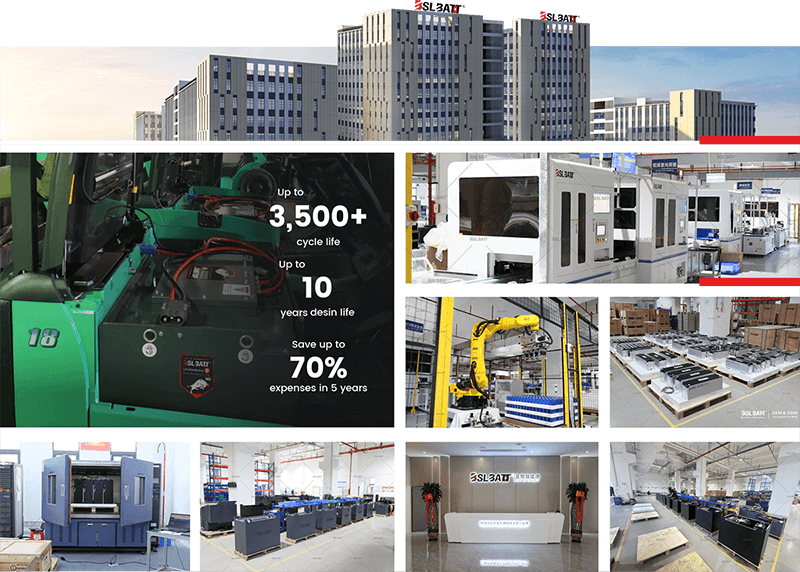
BSL New Energy Technology Co.. Ltd. (Brand: BSLBATT® ), an innovative high-tech company that designs and manufactures smart lithium-ion batteries (50% more efficient than similar products on the market) for industrial forklifts used in the warehousing and distribution industries, announced that it opened a new factory in Zhongkai, Huizhou on July 18, 2024 to complement its BSLBATT Global Fortune 500 and Top 100 customers with faster delivery capabilities and respond to the growth of lithium-ion battery pack sales worldwide. The new building has three times the production area of the original company. One building will now house all internal manufacturing operations, assembly, logistics, service center, and corporate headquarters. This move aligns with our growth strategy and responds to the growing market demand for BSLBATT® lithium batteries. President of BSLBATT®, Eric Yi, said, “The company is growing, and this move is part of the business plan. We didn’t expect that adding manufacturing space and increasing production in 2024 would become urgent. We saw the growing market share of lithium batteries in the material handling power market combined with the delayed demand last year in the first six months of 2024. We saw a perfect storm of orders!” “Our new building has three times the production area of the original company, which gives us plenty of room to grow,” said Mr. Lin Peng, Chief Technology Officer of BSLBATT®. “Having all elements of our internal manufacturing processes, service center, and corporate headquarters under one roof will make BSLBATT® more efficient. Our customers know we are ready to go the extra mile to ensure our batteries perform as they should, and we are committed to increasing battery reliability while accelerating battery production!” Bella Chen, Sales Director at BSLBATT®, emphasized the significance of this move, saying, “This new facility significantly increases our workforce, improves production efficiency, enhances production capacity, and more.” Haley Ning, COO at BSLBATT®, said, “We have achieved high double-digit growth each year for the past four years, which has driven our need to expand to supplement our product support and production infrastructure. The investment in the new Huizhou Zhongkai facility expands our production infrastructure to provide comprehensive and responsive delivery services to customers from global regions while, more importantly, reducing production and transportation costs for our company.” With more than 14,000 battery packs, BSLBATT® is a manufacturer in lithium battery applications, as reflected in its thought leadership and technology platform to lead customers toward clean, safe, and sustainable industrial and commercial energy solutions. The company is committed to delivering superior product performance, value, and support services, allowing customers to take their business to the next level while achieving greater profitability. For more information about BSLBATT, visit lithiumforkliftbattery.com.
Queen City Robotics Alliance is Charlotte’s official host for the 2024 NASA Space Apps Challenge
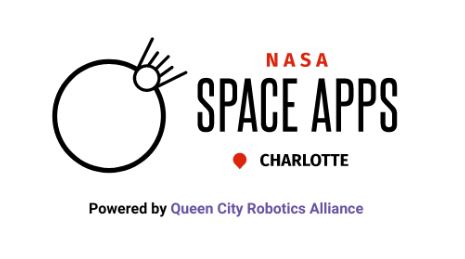
This global event happens at The Zone October 5-6 Queen City Robotics Alliance announced that it has been selected as the Charlotte host for the 2024 NASA Space Apps Challenge in October. The event will take place at QCRA’s facility, The Zone, the weekend of October 5-6. The NASA International Space Apps Challenge is the world’s largest global hackathon. This two-day event on October 5-6 allows participants of all ages to use NASA’s free and open data sources and its Space Agency Partners’ space-based data to address real-world Earth and space problems. The 2024 theme is “The Sun Touches Everything.” During the event, participants (individuals and teams) gather at designated sites worldwide in person and virtually to address challenges submitted by NASA experts. Also known as a Hackathon, this event began in 2012 and primarily focused on technology in space but has evolved to include challenges here on Earth. Today, the NASA Space Apps Challenge features arts and humanities challenges alongside the technology challenges, thus building a more inclusive program. The challenges will also have different difficulty levels from elementary age to college students to industry professionals, so everyone is welcome to participate. These challenges range in complexity and subject, tasking participants to create everything from artistic visualizations of NASA data to conceptualizing and developing informational apps and software programs. NASA’s goal is to “promote innovation through international collaboration.” The format for the event is called a hackathon, which is an event set up by a company or organization that brings people together in a collaborative environment to find high-quality solutions for current issues. This event is free and open to all ages; however, anyone 18 and under must be registered and accompanied by a parent or other adult. To learn more about NASA’s program, use this link: https://www.spaceappschallenge.org/nasa-space-apps-2024/ QCRA CEO Kaiwen Cheng is excited that the organization has this unique opportunity to host this singular event because it will bring more recognition, interest, and outreach to QCRA’s STEM (Science, Technology, Engineering, and Math) programs in the Charlotte community. “This is an opportunity for students to use NASA to explore ideas,” said Cheng. “Space technology is a leading technology. It’s using space to inspire and impact our daily lives. Things like GPS and memory foam mattresses. We wouldn’t have those things today without NASA technology.” “This is also an exciting opportunity for our students,” he continued, “because it is an interesting and tangible way for them to explore STEM education and discover their talents through NASA and the wonders of space.” To receive Charlotte event updates, visit QCRA’s particular event website – Space Apps – Charlotte (google.com) – or follow QCRA’s social media outlets.
Emerson announced changes in Global Sales Leadership
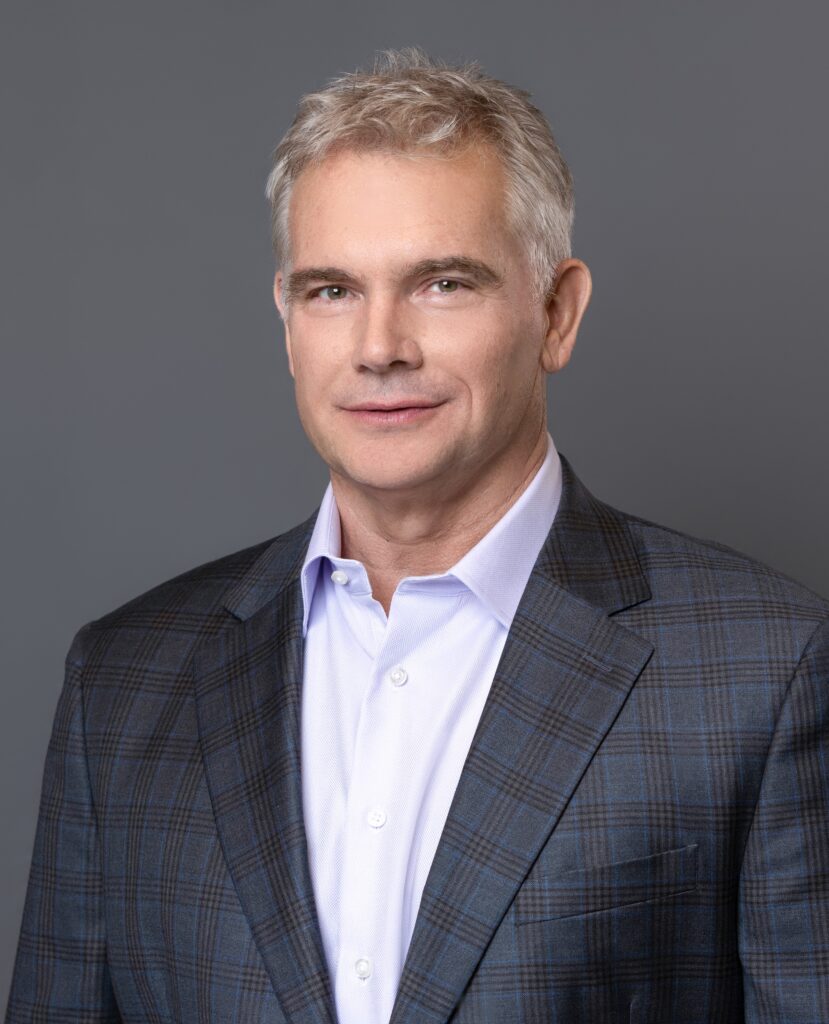
Worldwide sales management to be consolidated under newly-appointed Vice President of Global Sales Andy Schwege Emerson has announced a key executive change at its Appleton Group division with the promotion of 35-year electrical industry veteran Andy Schwegel to the newly created position of Vice President of Global Sales, effective immediately, overseeing domestic and international sales organizations. He will report directly to Anthony Hartman, President of Appleton Group. Previously Vice President of International Operations & Industrial and Commercial Sales, Mr. Schwegel will be responsible for continuing to drive growth and top-line revenue expansion for Appleton Group brands Appleton™, O-Z/Gedney™, EasyHeat™ and Nelson™ across a global sales network that encompasses over 2,500 distributor partners. “Andy has a long-standing record of bolstering sales and delivering on strategic business opportunities,” said Hartman. “His deep understanding of the harsh and hazardous location electrical markets, combined with a wealth of executive experience, makes him the ideal leader for our entire global sales operation. His ability to continuously accelerate sales growth and navigate complex market landscapes will be pivotal as we expand the Appleton footprint worldwide to meet the demand for safe, reliable and efficient electrical solutions.” In his 22-year tenure with Emerson, Mr. Schwegel has held increasingly responsible positions, primarily in marketing, business development and sales management. Before joining Emerson, Schwegel gained industry experience working for Eaton and Grainger.
Peak Technologies listed as Top Solution Provider in annual industry ranking
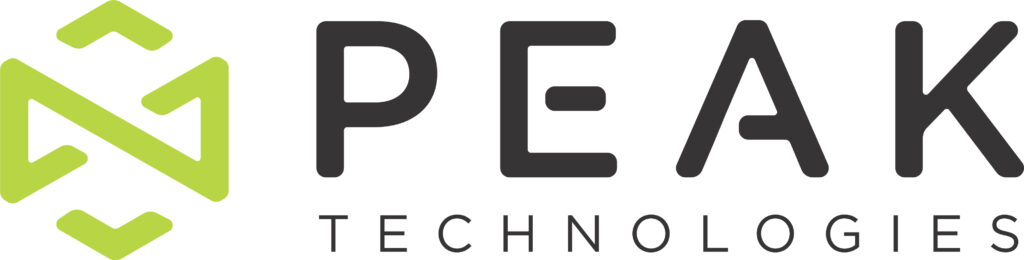
Peak Technologies ranked 65th on The Channel Company’s CRN Solution Provider 500 list, the annual ranking of the largest solution providers with operations in North America. Peak Technologies, a provider of digital supply chain and mobile workforce solutions, has been named to The Channel Company’s CRN Solution Provider 500 list, the annual ranking of the largest solution providers by revenue with operations in North America. Peak Technologies is ranked 65th in the 2024 list, the third straight year the company is listed among the top 70 out of 500 companies. Each year, the CRN Solution Provider 500 list is published by The Channel Company to rank the top integrators, service providers and IT consultants in the industry and recognize the critical ways these companies help businesses and organizations adopt and get the most value from leading-edge technologies. This year’s list emphasized the rapidly growing role and impact that artificial intelligence (AI) and generative AI technologies is having across multiple industry segments. “We are pleased and honored that we have once again been listed among the top companies in our field on the CRN Solution Provider 500 list,” said Tony Rivers, President and CEO, Peak Technologies. “It recognizes the continuing success we have had in both developing innovative, high-impact, smart technologies solutions for our customers and expanding our ability to help them solve their digital supply chain and mobile workforce challenges.” From manufacturing, warehousing, transportation and logistics operations to retail, healthcare and field service applications, Peak Technologies has become one of the industry’s largest providers of end-to-end automation solutions that modernize the factory, optimize the warehouse, revolutionize the retail experience and reimagine field services and last-mile delivery. “We recognize the need to continuously invest in new smart technologies and AI-driven solutions to help our customers navigate the seismic shifts in the IT industry,” said Alexander Price, Senior Vice President, Smart Technologies at Peak Technologies. “Our recent investments include new offerings in machine vision, autonomous mobile robots (AMRs), RFID/RTLS platforms and advanced analytics solutions, all developed to help our customers leverage cutting-edge technology to achieve their critical operational and productivity goals.” Technology solutions recently launched by Peak Technologies include: Peak Analytics, a powerful supply chain AI and image recognition solution that lets logistics operations capture key information about package quality by harnessing the power of image recognition and AI. Using advanced machine vision cameras placed within scan tunnels on conveyor lines, Peak Analytics advanced software delivers real-time data about the condition of every package, allowing companies to identify problem inventory at the source. Autonomous Mobile Robots (AMRs) provide mobility solutions to help automate and streamline labor-intensive logistics tasks such as picking, receiving, loading replenishment and put away, saving time and helping increase daily output while allowing skilled workers to focus on high-value tasks. Advanced Machine Vision (MV) solutions automate manufacturing inspection using advanced 2D, 3D and deep learning solutions. Sensors, cameras, frame grabbers and advanced software quickly and accurately detect objects for instant inspection, sorting, traceability or high-speed production. By capturing high-quality digital images of items moving at very high speeds, MV systems can gauge whether the data or objects meet certain parameters and provide AI-driven analytics for real-time visibility and decision making. RFID (Radio Frequency Identification) and RTLS (Real-Time Location Systems) solutions provide precise location data of high-value assets, assisting in loss-prevention and enhancing supply chain visibility. Track the receipt and movement of goods within a warehouse, facility or yard, or use dynamic, real-time locationing to immediately track and locate items and verify inventory. Both technologies improve asset visibility across warehousing and logistics operations, helping automate and improve asset use and processes. In recent years, Peak Technologies has also made growth investments through 15 strategic mergers and acquisitions. These include the 2023 acquisition of North Coast Technical, a leading provider of machine vision hardware and image processing software for Fortune 500 companies, and the 2022 merger with Supply Chain Services, a leading full life-cycle system integrator and provider of digital supply chain, retail and mobile workforce solutions.
Pfannenberg announced the ultimate signaling solutions for light duty applications
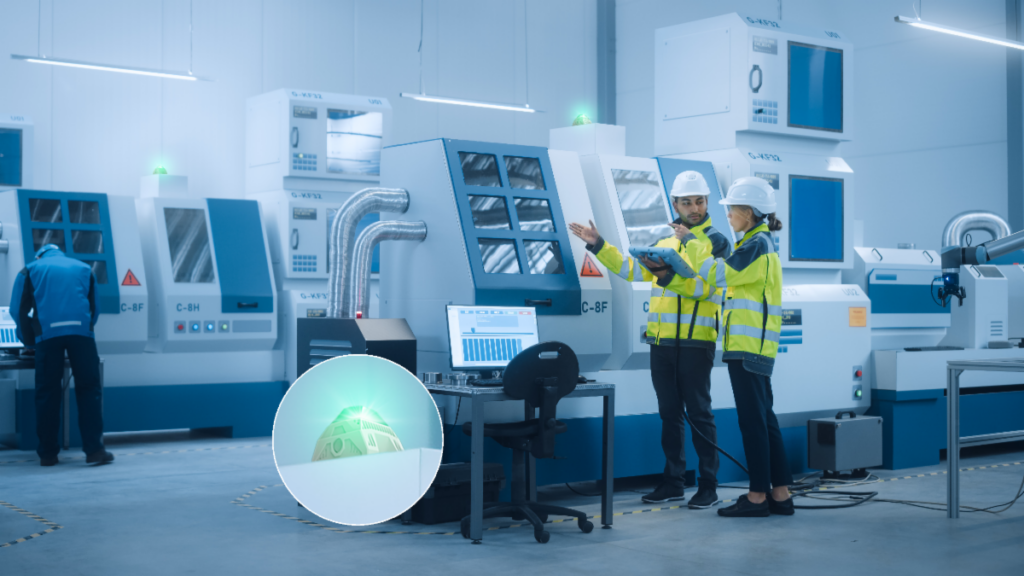
Customizable Signal Fits a Range of Applications from Control Cabinets to Autonomous Vehicles Pfannenberg, a manufacturer of thermal management and signaling technologies, launches the PA1-R and PA L1-R, the ultimate signaling solutions for light-duty applications. These products deliver high performance in an economical package, ensuring a safe and reliable signaling solution for audible (PA1-R) and combined audible, and visual (PA L1-R) needs. The PA 1-R and the PA L1-R are the go-to choices for automation, material handling, and machine-building applications where status and indication lights and sounds are critical safety measures needed to notify staff about current or imminent events. The PA1-R features just sound while the PA L1-R is highly customizable, providing independent control of light and sound, allowing users to signal with sound only or a combination of light and sound. For the audible alarm in both products, users can choose from 70 tones and reduce the volume to meet application needs, selecting from 85dB, 92dB, 98dB, and 105dB to fit a range of environments. The PA L1-R also allows users to select the perfect color light signal to fit their intended application with the RGB version of the product, including green, yellow, amber, blue, purple, red, white, and magenta. To best suit the environment of the application, users can also choose between continuous, blinking, flashing, and rotating LED lights. Rotating LED lights offer an ideal alternative in contexts where blinking features may have limited visibility. On top of this, the signal’s top-mounted installation ensures excellent 360-degree perceptibility with its radial design. Both versions feature a multi-voltage-power supply of 10-60 V DC and 95-265 V AC, making them one-size-fits-all all options for the needs of your application. They are also available with an optional M12 connection, allowing for quick connection without wiring or the need for an electrician. This versatility and ease of connection allow the signals to be versatile and adapt to any application, saving time and money.
Unipipe Solutions highlights UnipipeHP Aluminum Piping Systems
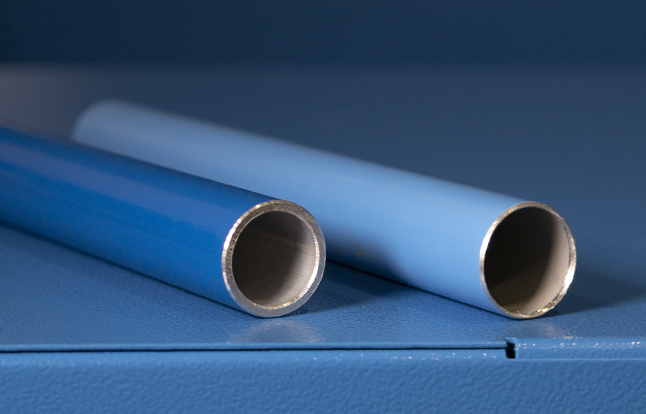
The Most Robust, Cost-Effective, and Easy-to-Install Piping System Available, for Pressures up to 1015 PSI Unipipe Solutions, an industrial piping sector, highlights the UnipipeHP Aluminum Piping System for High-Pressure Compressed Air Applications. The UnipipeHP is an advanced aluminum piping system specifically engineered for the highest-pressure applications. Featuring a robust design and superior performance, the UnipipeHP system is rated for up to 1015 PSI (70 BAR). It is cost-effective and easy to install and maintain, making it ideal for various demanding applications, including multi-fluid systems, high-pressure compressed air, and nitrogen systems. UnipipeHP sets itself apart with its heavy wall tubing and rigorous inspection standards, ensuring reliability and safety. The fittings for UnipipeHP are identical in design to those of the standard UnipipeAIR system, rated for 232 PSI (15 BAR), maintaining consistency while offering enhanced pressure capabilities. The UnipipeHP system is available in sizes up to 2-½” (63mm), while the UnipipeAIR system is available in sizes up to 10” (250mm). This flexibility allows for the completion of even the largest projects without the need for specialized tools or skilled labor. One of the standout features of the Unipipe system, including UnipipeHP, is its unique stainless steel gripping ring. This innovative design ensures quick and secure installation without the need for special tools, crimping, or grooving. The installation process takes half the time of traditional piping options and is significantly faster than copper piping. The system’s lightweight nature—75% lighter than iron pipe—allows for single-person installation of systems up to 6 inches in diameter. Unipipe systems boast the most secure fittings in the market. The proprietary stainless steel clamp ring in every fitting bites into the aluminum pipe, creating a connection rated for over five times the pressure of other systems. This clamp ring ensures 100% contact around the pipe, tightening further as pressure increases. Additionally, a plastic ring identifies the fluid and working pressure for each system, enhancing usability and safety. In terms of cost-effectiveness, Unipipe systems provide the lowest cost of ownership. When considering both material and labor costs, Unipipe proves to be the most economical choice, saving 30% to 40% over traditional piping methods. Unipipe systems are suitable for ultra-clean environments and outperform traditional piping methods such as black iron pipe and copper. Black iron pipe is heavy, prone to internal rusting, and labor-intensive to install, while copper is both expensive and slow to install. In contrast, Unipipe systems are faster, easier to install, lighter in weight, and ideally suited for compressed air applications. Unipipe systems are ideal for ultra-clean environments and Unipipe fittings are universally compatible with most other aluminum systems currently on the market, ensuring a seamless integration process. All Unipipe pipe and fittings come with a 20-year guarantee against manufacturer’s defects, provided they are installed and supported according to the Unipipe installation instructions.
OZ Lifting launches hoist clamp
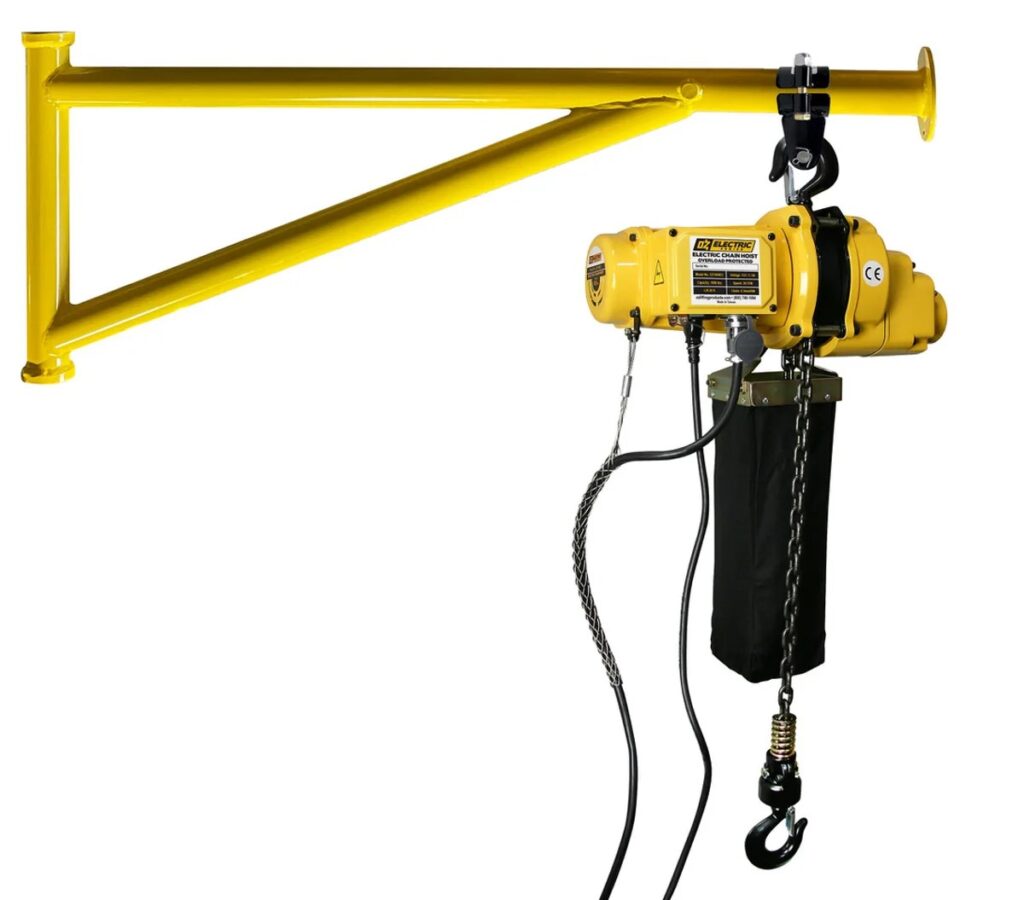
The hoist clamp presents a quick, easy, and safe way to hang any of the company’s electric chain or manual hoists, under 0.5-ton capacity, to its pipe- and wall-mounted arms with the required hardware. The user can mount the hoist clamp anywhere along the mounting arm at a full-rated capacity of 1,000 lbs. The clamps are sold separately if users already have a mounting arm, but they can be sourced with the pipe- (model OBH230) or wall-mounted (OBH230-WALL) arms. The OBH230 was originally developed for the construction industry, mainly on job sites with scaffolding; it is sized for scaffolding pipe diameter. The OBH230-WALL, meanwhile, has wider application uses. Richard Miller, sales manager at OZ Lifting, said: “Our mounting arm is very popular, and we have received feedback on options to mount a hoist with a traditional top hook. This led to the development of the hoist clamp, so once again it is an example of product innovation being driven by the point of use. “It opens the door to a variety of applications,” he continued. “Most users prefer to use a complete solution from a manufacturer, versus trying to piece the equipment together with a sling, chain, rope, etc. They get the benefit of a solution that has been load-tested and approved at the source. We provide the customer the option to order as they choose; we often build to suit and can accommodate the different styles and configurations that are available.” The mounting arm — tested to a minimum safety factor of 3:1 — is essentially a mini jib crane and can be installed in either ‘upright’ or ‘reversed’ orientation, depending on the needs of the customer and application. When the mounting arm is in the upright position, the hoist clamp may be attached to the outermost horizontal pipe; when the arm is in the reversed position, the clamp may be attached anywhere along the horizontal pipe. End-use applications will be varied and widespread; the mounting arm is already utilized in many industries and environments. Miller reiterated its suitability in the construction and manufacturing sectors but pointed to growing market share in many other vertical markets. The OZ Lifting hoist clamp features steel construction and a long-lasting powder coat finish for added durability. It is in stock and ready for distribution to the manufacturer’s extensive dealer network.
Lift Tables for production line integration
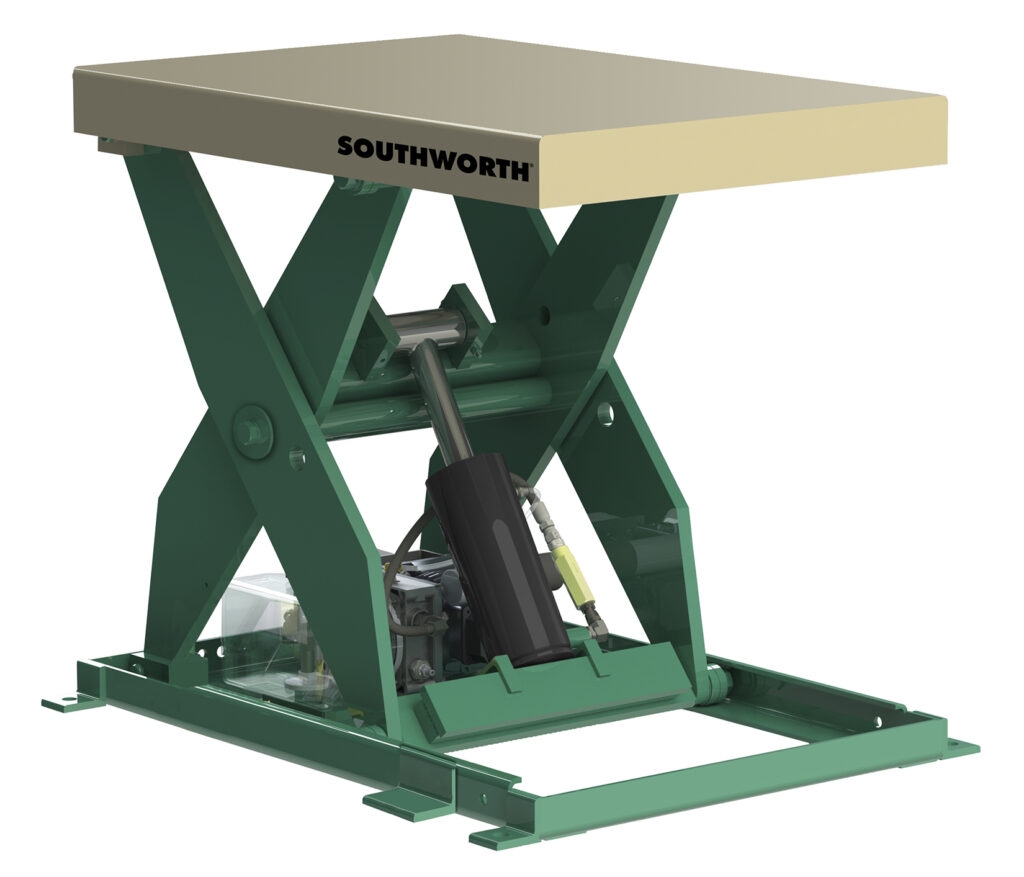
The performance requirements of lift tables in a production process are far greater than those of stand-alone lifts. To ensure maximum reliability and uptime in these production environments, Southworth has introduced a Production Ready package for many of their most popular models. By incorporating a series of options, upgrades and heavy-duty features, the Production Ready package minimizes unplanned maintenance and costly production interruptions. With regular PM service, the interval before major maintenance and replacement of renewable parts is extended from 50,000 up to 200,000 cycles or more. Southworth LS, LSH and DL Series lifts can be furnished with the Production Ready package so there are literally thousands of configurations to choose from. Southworth Production Ready lifts feature oversized cylinder rods, high-strength alloy shafts and pins, thicker composite bushings for increased strength and durability, regreasable needle-bearing cam followers, reinforced roller tracks with wear strips, upper limit switches, and soft connectivity for electrical connections. Southworth also recommends the Production Ready package for dynamic load handling on lifts with conveyor tops, pneumatic ball transfers or turntables, or where the lifts travel under load such as on AGVs or towed carts. It is also ideal for non-uniform loads that consistently place more weight on one end or side of the platform. Because the maintenance interval of these lifts is greatly extended, they are also ideal for use in areas with limited access for maintenance.
China Container market update – July 2024
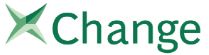
Mixed signals from China’s shipping container trading and leasing markets Average container prices in China stabilize for the first time in 2024 Leasing rates from China to the US and Europe continue to surge in July Shanghai, China – July 23, 2024 Container xChange released its latest monthly China market update, revealing that the average container prices in China have held steady in July for the first time in 2024. Chart 1: Average prices for 40 ft high cube cargo-worthy containers, July 2023 to July 2024 While the average container prices (for container trading) in China stabilized this month, the average leasing rates from China to the US and China to Europe continued to surge in July. Table 1: Month-on-month comparison of average leasing rates for 40 ft HC containers “The recent volume increase and subsequent container price hikes was primarily driven by the pulling forward of orders, raising questions about the strength of underlying demand. If this demand proves to be weak in the H2 of 2024, we could see container prices and freight rates momentum decline.” shared Christian Roeloffs, cofounder and CEO of Container xChange, the global online marketplace for container trading and leasing. In the short term, Container xChange reports that average leasing rates for westbound trade from China have continued to surge throughout July. Muhammad Farhan Khan, CEO at Sourcing Riders Ltd (Import & Export Company in China), shared that, China’s container demand is surging, particularly for shipments to the US, driven by increased consumer spending. However, capacity constraints and disruptions in major shipping routes have led to significant spikes in leasing rates. Despite these challenges, container prices have not significantly increased in July 2024, indicating a more balanced market. The overall situation remains dynamic and volatile.” According to Farhan, the updated Ocean freight rates for August’s 1st half on the China to US West Coast have reached $8,800 (August 1-15, 2024) from $8,200 (for July1-15 2024) and for China to US East Coast have also increased to $9,700 (August 1-15, 2024) from $9,100 (for July1-15 2024) China to Europe average container leasing rates rise at a slower pace Average container leasing rates on the China to Europe route continue to rise but at a slower pace this month. Month-to-month increases from June to July 2024 show a continuing trend of rising costs. Looking at the longer duration, the year-over-year increases highlight the impact of the Red Sea crisis, which caused container prices to inflate throughout this year. Chart 2: Shanghai to Europe average leasing rates for 40ft HC, July 2023 to July 2024 Chart 3: Monthly Average container leasing prices across major China-to-Europe routes, July 2023 to July 2024 Higher average leasing rates from China to US West Coast compared to East Coast Container leasing rates continue to climb on the China to US route, with significant month-to-month increases from June to July 2024, reflecting ongoing congestion and supply chain disruptions impacting this route. According to the data, average container leasing rates are generally higher on China to US West Coast (Long Beach, Los Angeles) routes compared to the US east coast. From the data, the average container leasing rates from China to the US West Coast in July 2024 are higher compared to those to the US East Coast. Table 2: Average container leasing rates from China to the U.S. East and West Coast in June and July 2024 Labor negotiations at U.S. East Coast and Gulf of Mexico ports pose a significant risk for shippers already dealing with extended transit times and increased costs. The International Longshoremen’s Association (ILA) contract, covering 45,000 dockworkers from Maine to Texas, expires on September 30. Canadian routes also witness a substantial increase but tend to be slightly lower than their U.S. counterparts. Market Outlook While the current data indicates a potential stabilization in container prices, the market remains sensitive to global economic conditions and trade dynamics. “The macroeconomic indicators from China reveal a mixed picture. House prices have dropped more sharply than anticipated, declining by 4.5% year-on-year compared to the forecasted 4.1%. GDP growth also fell short of expectations at 4.7% versus the predicted 5.0%, and retail sales increased by only 2% year-on-year against a forecast of 3.2%. On the other hand, June exports showed a positive trend, rising by 3.6% year-on-year for the first six months of 2024. Carriers and leasing companies are optimistic about a further upswing in trade activity. However, we believe that the current surge in demand is primarily driven by large retailers preemptively managing inventories for the peak season, rather than a robust demand recovery. Consequently, the likelihood of container prices sliding and stabilizing at a lower level is high. The recent stabilization of container prices in China aligns with our earlier forecast, suggesting that the peak of price hikes may have been reached or is nearing soon.” Shared Christian Roeloffs, cofounder and CEO of Container xChange.
AAR reports Rail Traffic for the week ending July 20, 2024
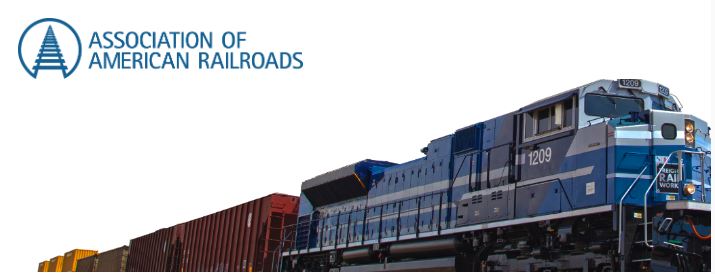
The Association of American Railroads (AAR) reported U.S. rail traffic for July 20, 2024. This week’s total U.S. weekly rail traffic was 480,083 carloads and intermodal units, up 1.4 percent compared with the same week last year. Total carloads for the week ending July 20 were 214,348, down 3.4 percent from the same week in 2023, while the U.S. weekly intermodal volume was 265,735 containers and trailers, up 5.8 percent from 2023. Five of the ten carload commodity groups posted an increase compared with the same week in 2023. They included grain, up 2,387 carloads, to 17,300; petroleum and petroleum products, up 1,591 carloads, to 10,745; and farm products, excluding grain, and food, up 1,413 carloads, to 16,880. Commodity groups that posted decreases compared with the same week in 2023 included coal, down 6,278 carloads, to 57,906; nonmetallic minerals, down 3,825 carloads, to 30,758; and motor vehicles and parts, down 2,175 carloads, to 12,466. For the first 29 weeks of 2024, U.S. railroads reported a cumulative volume of 6,194,152 carloads, down 4.4 percent from last year, and 7,404,038 intermodal units, up 8.4 percent from last year. Total combined U.S. traffic for the first 29 weeks of 2024 was 13,598,190 carloads and intermodal units, an increase of 2.2 percent compared to the previous year. North American rail volume for the week ending July 20, 2024, on ten reporting U.S., Canadian, and Mexican railroads totaled 317,607 carloads, down 4.1 percent compared with the same week last year, and 346,231 intermodal units, up 3.9 percent compared to the previous year. Total combined weekly rail traffic in North America was 663,838 carloads and intermodal units, down 0.1 percent. North American rail volume for the first 29 weeks of 2024 was 19,112,113 carloads and intermodal units, up 2.3 percent compared with 2023. Canadian railroads reported 86,987 carloads for the week, down 3.3 percent, and 68,443 intermodal units, down 0.6 percent compared with the same week in 2023. For the first 29 weeks of 2024, Canadian railroads reported a cumulative rail traffic volume of 4,654,977 carloads, containers, and trailers, up 1.9 percent. Mexican railroads reported 16,272 carloads for the week, down 15.9 percent compared to last year, and 12,053 intermodal units, down 7.0 percent. Cumulative volume on Mexican railroads for the first 29 weeks of 2024 was 858,946 carloads and intermodal containers and trailers, up 5.5 percent from last year. To view the traffic charts, click here.