Toyota Material Handling lifts communities Nationwide
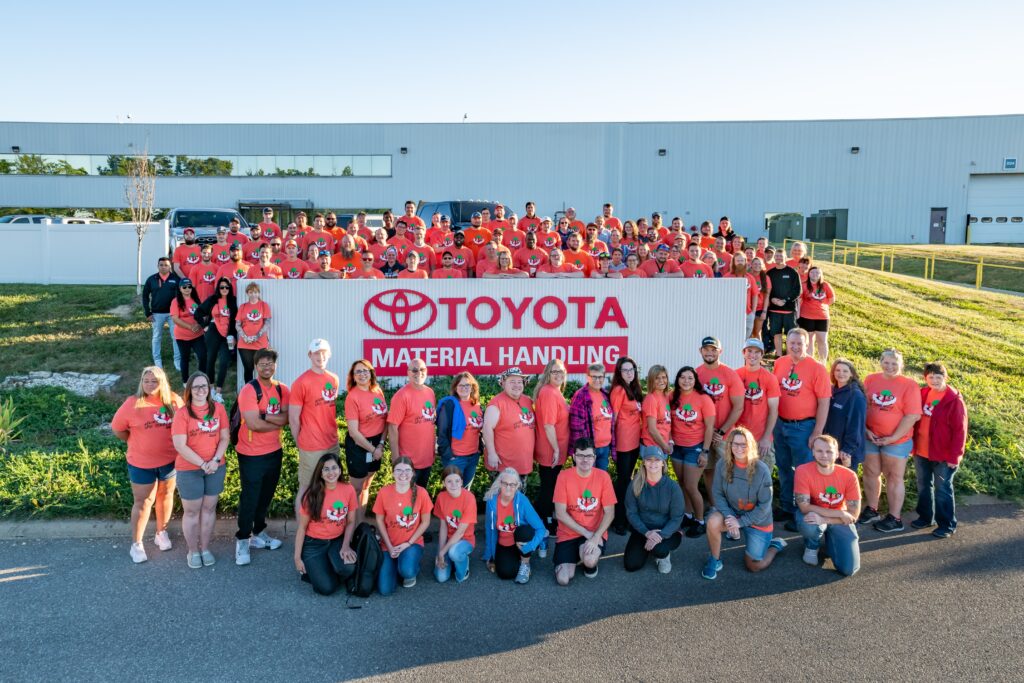
Toyota Material Handling and its nationwide network of dealers showcased its commitment to improving their local communities during the company’s annual ‘Lift the Community Day.’ Since 2021, Toyota associates have participated in an annual day-long philanthropic event near Toyota’s Columbus, Indiana, headquarters. This year, the initiative expanded to include participation from Toyota’s dealers, increasing the impact on communities throughout the U.S. On July 1, 324 Toyota associates completed 2,300 volunteer hours during the event. In addition to impacting the Columbus community, associates from 10 dealerships and Toyota’s Heavy Duty division participated in their volunteer efforts, making this a nationwide philanthropic event. “Participating in ‘Lift the Community Day’ is important to our associates and to upholding Toyota’s core values,” said Tracy Stachniak, Toyota Material Handling Vice President of Human Resources. “Our business has the resources and compassion to be a philanthropic leader and make a significant impact not only in our local community but throughout North America. We were eager to expand this event to dealers and look forward to driving further change throughout our communities.” ‘Lift the Community Day’ exemplifies Toyota’s founding principle of contributing to society and ‘helping people carry the load’ by promoting a compassionate environment. This year, associates and dealers supported more than 30 local non-profit organizations and programs throughout five Indiana counties and 11 states across the country. These efforts resulted in an economic impact exceeding $84,685. Corporate social responsibility is central to Toyota’s culture, reflecting the company’s core values: be faithful to duties and create a home-like atmosphere. Toyota fosters numerous community-focused relationships, including corporate partnerships with the American Red Cross, United Way, and Anchor House, an Indiana nonprofit providing housing initiatives, employment resources, and nutritional assistance. “We are incredibly grateful for the unwavering support and dedication of the volunteers from Toyota,” said Grace Kestler, Executive Director of The Arc of Bartholomew County. “Their commitment to our cause has been invaluable, and their contributions have made a significant impact on our efforts. With their expertise and hard work, they played a crucial role in our renovation project. We deeply appreciate the partnership with Toyota and thank them for being an essential part of our mission to support individuals with disabilities, helping us create a more inclusive and brighter future for our community.” Toyota provides each associate with paid community service hours to volunteer with various organizations. Throughout the year, Toyota sponsors and organizes volunteer activities on and off campus. In 2023, Toyota associates donated 11,765 hours to support local organizations, contributing to a total economic impact of $745,721. Learn more about Toyota’s commitment to volunteerism and corporate social responsibility here.
Longtime Hyster-Yale technology leader honored as distinguished supply chain professional
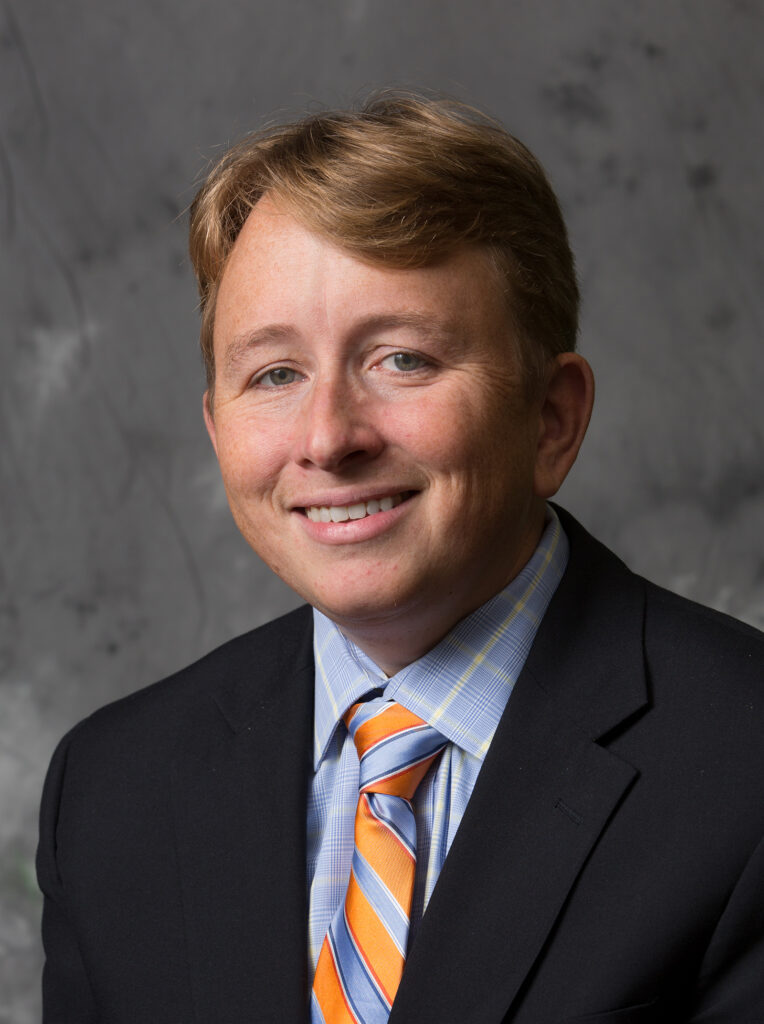
Hyster-Yale Materials Handling announces that Steven LaFevers, Vice President of Global Emerging Technology, has been named a 2024 Rainmaker by DC Velocity, a supply chain and logistics trade publication. This recognition honors LaFevers’ for his accomplishments at Hyster-Yale, most notably building the company’s Emerging Technology division from the ground up. “I’ve worn a lot of different hats in my 24-plus years with Hyster-Yale, but the most rewarding has been developing and leading our Emerging Technology team,” said LaFevers. “I’m honored by this recognition, but want to acknowledge that it doesn’t solely belong to me – it belongs to every member of the team. Without their hard work and ingenuity, we wouldn’t be able to develop and launch technologies that bring our company and our industry into the future.” LaFevers’ division embodies the technology innovation capabilities of a startup while leveraging the company’s resources as a mature materials handling manufacturer. The Emerging Technology team has grown significantly, from 25 employees to more than 150 in the last few years alone, and has introduced groundbreaking technology solutions to the market. LaFevers held a pivotal role in developing and launching a first-of-its-kind operator assistance technology suite, marketed through the Yale® and Hyster® brands as Yale Reliant™ and Hyster Reaction™. Since its commercial launch in 2021, Hyster Reaction and Yale Reliant have been deployed on more than 6,000 lift trucks and accumulated more than 14 million hours of real-world run time. In response to customer demand, the company has rapidly expanded the availability of the solution from an original lineup of five lift truck models at launch to a total of 59 models. LaFevers also spearheaded the adoption of the company’s lift truck telematics solution. They oversaw the commercialization of the company’s automated lift trucks, which have grown to a commercially installed base of over 500 units and counting. Through his years of experience, LaFevers has also become a go-to source for media outlets covering the space on materials handling trends and technology. He has participated in interviews and written bylined articles for publications, including Robotics 24/7, Workplace Material Handling & Safety, Food Logistics, and more. Additionally, LaFevers is one of the founding members of the Board of Directors for the East Carolina University (ECU) Innovation Foundation.
H&E opens new branch near Idaho Falls, SD
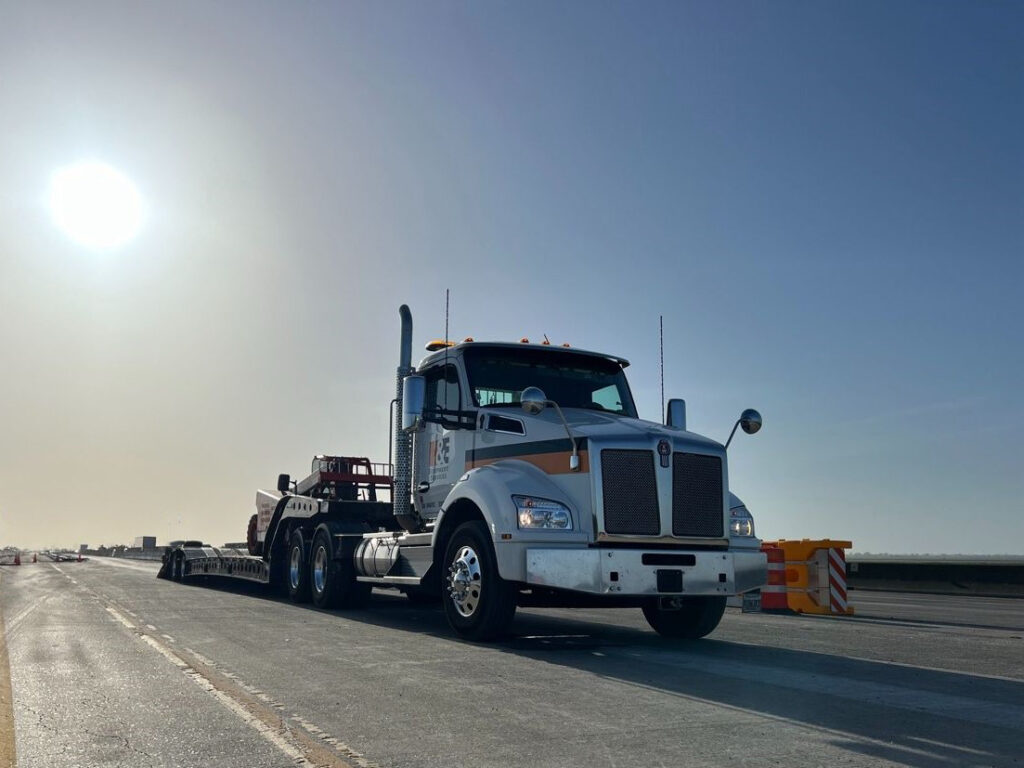
Effective July 15, 2024, H&E Rentals (H&E) announces the opening of its Idaho Falls branch, the third general rental equipment location in the state of Idaho. H&E has opened 22 new branches across the country and acquired nine others in just over a year, and it has operations in 31 states. The facility is located at 2727 East 14th North, Ammon, ID 83401-6232, phone 208-977-0900. It includes a fully fenced yard area, offices, and a repair shop and carries a variety of construction and general industrial equipment. “H&E has extended its coverage in Idaho and across the Wyoming state line to easily service projects that are a farther reach for our branches in Boise, Belgrade, Montana, and Ogden, Utah. Our Idaho Falls branch has filled in those gaps between our other H&E facilities in the region, and we can now work in tandem to take care of our customers across several states,” says Branch Manager Josh Criddle. “We’ve added greater fleet availability to the area, and the location of our new facility has quick access to I-15 and roadways that branch off in all directions, so we can get equipment moving to job sites without delay.” The Idaho Falls branch specializes in the rental of aerial lifts, earthmoving equipment, telescopic forklifts, compaction equipment, generators, light towers, compressors, and more and represents the following manufacturers: Allmand, Atlas Copco, Bomag, Case, Club Car, Cushman, Doosan, Gehl, Generac Mobile, Genie, Hamm, Hilti, Husqvarna, JCB, JLG, John Deere, Kobelco, Kubota, LayMor, Ledwell, Lincoln Electric, Link-Belt Excavators, MEC, Miller, Multiquip, Polaris, Sany, Skyjack, SkyTrak, Sullair, Sullivan-Palatek, Tag, Towmaster, Unicarriers, Wacker Neuson, Yanmar, and others.
Episode 502: Warehousing and freight with AFS Logistics
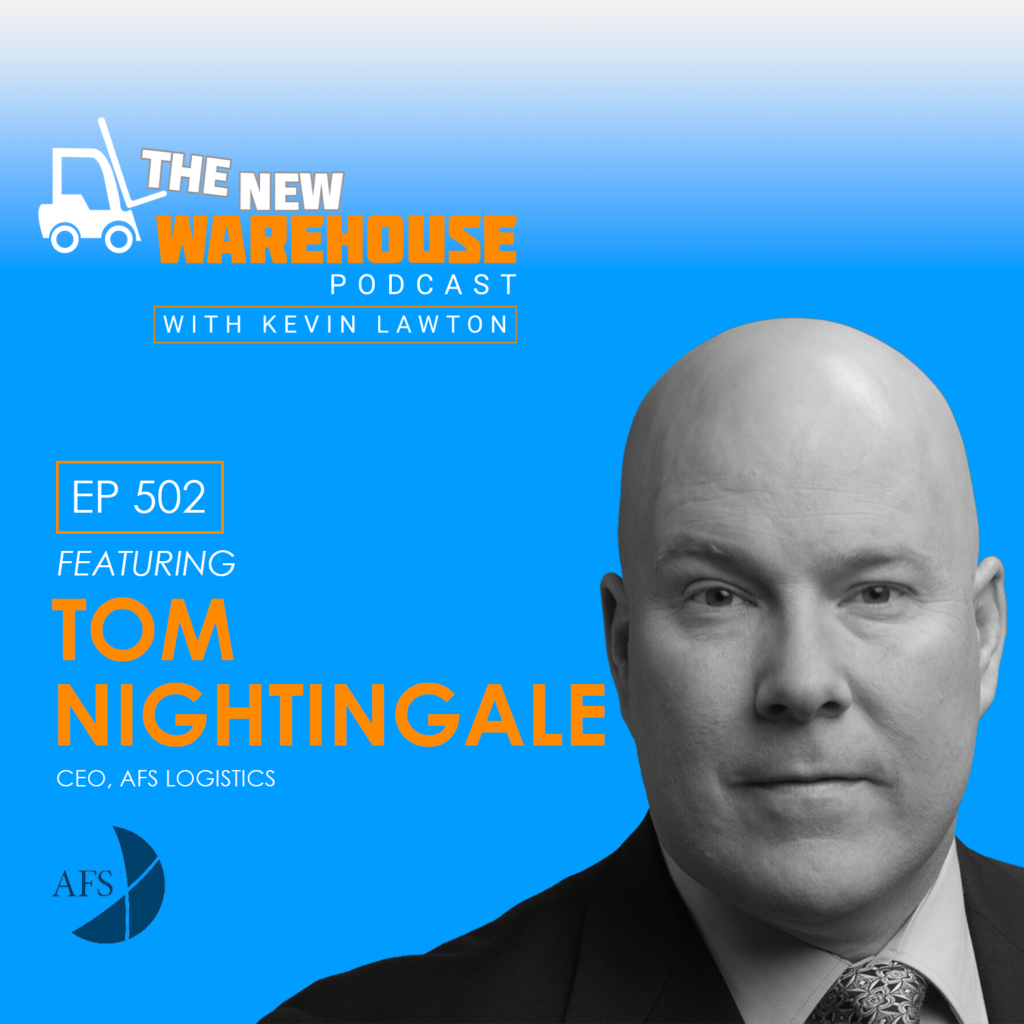
Welcome to The New Warehouse Podcast! Today, we are thrilled to have Tom Nightingale, the CEO of AFS Logistics, join us. AFS Logistics is a non-asset-based third-party logistics (3PL) provider with over 40 years of experience. Tom shares his take on warehousing and freight, highlighting the essential relationship between these two elements in the supply chain. Join us for a deep dive into the freight industry’s latest trends. Discover how AFS tailors specialized services to meet the evolving demands of consumer behavior and technological progress. The Critical Role of Warehousing in Transportation Tom emphasizes the pivotal role of warehouses, “Warehouses really serve as the critical components of the entire supply chain.” He shares how the role is evolving rapidly due to changes in consumer behavior, necessitating more diverse transportation modes and advanced automation within warehouses. For instance, a warehouse that once handled rail inbound and truckload outbound may now also manage LTL, parcel, and courier services, requiring flexible infrastructure and labor management. Balancing Transportation Asset Ownership Owning transportation assets can be a double-edged sword for 3PLs. Tom advises caution: “Transportation asset ownership is pretty expensive… those assets can become an albatross around your neck.” The inherent imbalance in transportation can lead to financial strain when market conditions shift. Tom recommends warehouse operators focus on their core competencies and partner with expert transportation providers rather than investing in their own assets. This approach helps mitigate risks and allows for greater operational flexibility. Freight Industry Insights Tom explains how TD Cowen/AFS Freight Index leverages AI and machine learning to provide detailed and predictive insights into various freight market segments. This index provides visibility into the freight market by processing data from the $11 billion worth of freight that AFS Logistics audits and pays annually. This extensive data provides a comprehensive view of various market segments, including parcel, truckload, and less-than-truckload (LTL) shipments. He shares his Key Observations: Parcel Market Sagging: The index shows that the parcel market demand remains lower than during the pandemic’s peak. Cost Management: Parcel providers are reducing costs to manage increased integration and labor expenses. Surcharges: An increase in fuel and delivery area surcharges affects a broad population. Pricing Environment: Despite decreasing volumes, the parcel express segment continues to see pricing improvements due to strategic cost reductions. Flat LTL Market: The index indicates a relatively flat rate trend, with only a slight increase observed from Q1 to Q2. Truckload Capacity: The truckload segment shows capacity additions that offset market fluctuations, with large carriers absorbing more business as smaller ones exit. Companies can leverage warehousing and freight market insights to help them plan and optimize supply chain strategies, manage costs, improve operational efficiency, and stay ahead of market trends. Key Takeaways on Warehousing and Freight Warehouses and freight are critical to the supply chain ecosystem, adapting to diverse modes and consumer demands. Owning transportation assets can be risky; focus on core strengths and partner with experts. Leveraging external expertise for non-core services enhances operational efficiency and value. The New Warehouse Podcast 502: Warehousing and Freight with AFS Logistics
Shoppa’s adds Will Dusek to executive team
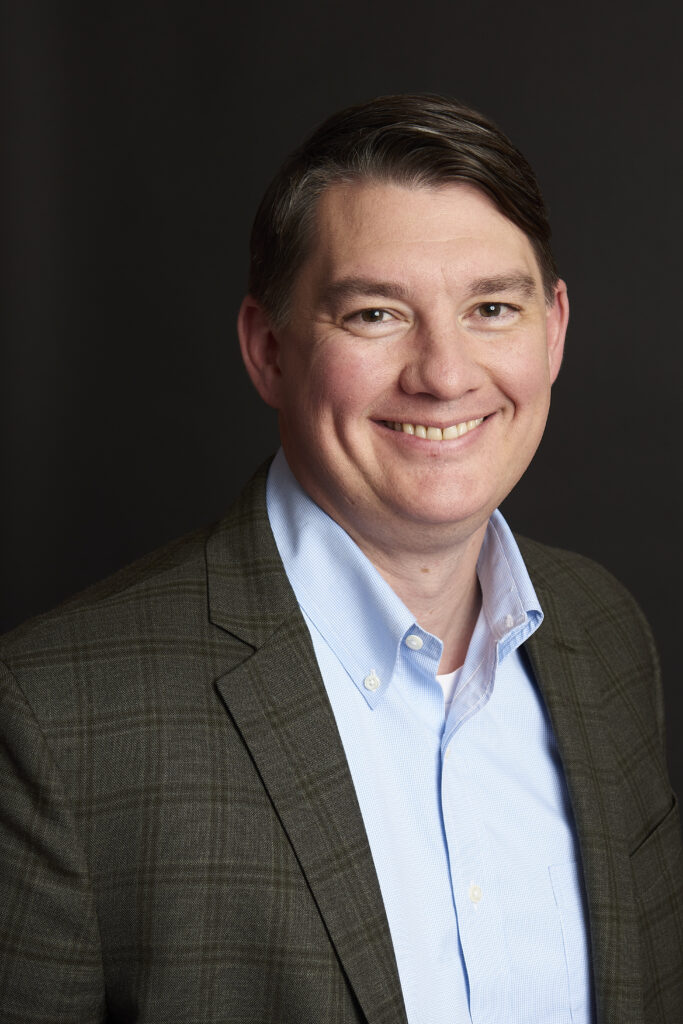
Shoppa’s Material Handling has announced the appointment of Will Dusek as Chief Strategy and Transformation Officer. Will joins Shoppa’s with over 20 years of experience in developing data-driven strategies that enhance performance and drive value. Will Dusek is a seasoned executive with a proven track record of leading highly collaborative teams to develop creative and innovative solutions and achieve operational excellence? His extensive background and forward-thinking approach to business ensure that decisions are informed by comprehensive analysis, leading to optimal outcomes. “We are thrilled to welcome Will to the Shoppa’s family,” said Jimmy Shoppa, President of Shoppa’s. “His strategic vision and ability to drive performance improvements will be invaluable as we continue to pursue our growth objectives. Will’s experience and commitment to excellence aligns perfectly with our mission to deliver an exceptional customer experience in everything we do.” Throughout his career, Will has demonstrated a unique talent for aligning strategic initiatives with business goals, ensuring sustainable success. His leadership will play a pivotal role in guiding Shoppa’s through its next phase of innovation and expansion. “I am excited to join Shoppa’s and contribute to its dynamic growth trajectory,” said Will Dusek. “I look forward to working with the talented team at Shoppa’s to drive strategic initiatives that will further enhance our performance and deliver exceptional value to our customers.” Will Dusek’s appointment underscores Shoppa’s dedication to attracting top talent to lead its strategic initiatives. With his expertise, Shoppa’s is well-positioned to achieve new heights and continue its legacy of delivering unparalleled value to its customers.
American Logistics Aid Network activates for Hurricane Beryl
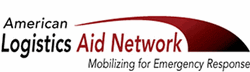
On Monday, July 8, 2024, Beryl made landfall in Texas as a category one hurricane, bringing heavy winds, flash flooding, and state-wide power outages. ALAN (American Logistics Aid Network) mobilized its network and works with non-profit and business partners to aid response efforts. On Tuesday, July 9, ALAN hosted a Logistics Coordination Call with responding non-profit partner organizations. During the call, partners shared their current response capabilities and identified potential logistics gaps. ALAN’s response coordination efforts – which include fielding and filling specific requests for logistics help – will continue this week as additional needs are identified. “Most of our requests for assistance arrive after a hurricane or tropical storm has hit, sometimes weeks, months, or even years into recovery,” said ALAN’s Operations Coordinator, Alexia Nobles. “That’s because each storm winds up having very different outcomes and pain points. And you can’t predict what those will be – and where relief organizations will require supply chain assistance the most – until after the storm has moved through.” ALAN’s Disaster Micro-Site is the best resource for viewing open logistics needs for response efforts. It’s also where we post critical resources and information in the form of Situation Reports as we receive new updates. “We are likely to witness supply chain impacts given parts of the Caribbean, Mexico, and U.S. Gulf Coast were all affected,” said Kathy Fulton, ALAN’s Executive Director. “ALAN will continue to convene its public and private sector networks to provide visibility, smart logistics solutions, and compassionate humanitarian response as relief efforts demand.”
Port of Long Beach Data Project receives $7.875 Million to speed goods delivery
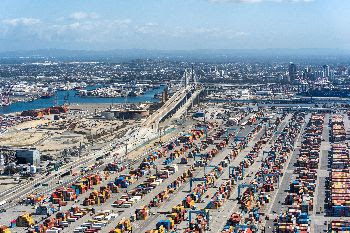
A comprehensive Port of Long Beach digital platform being designed to help speed cargo deliveries across the nation, the Supply Chain Information Highway, is getting an infusion of funding from Gov. Gavin Newsom’s administration. The Governor’s Office of Business and Economic Development (GO-Biz) announced a $7.875 million grant for the Port’s data system today. The funding is expected to help build out a variety of functions, including export and rail cargo visibility, user authentication and data security, the exchange of data between foreign ports, truck appointments, and a number of future project enhancements that will enhance operational efficiency and customer service. The Supply Chain Information Highway will enable stakeholders to make scheduling, planning, and operational decisions prior to cargo arrival, making the delivery of goods more efficient and cost-effective. The cloud-based system is anticipated to be compatible with similar data-sharing platforms across the maritime logistics industry, including at major California ports, supporting improved supply chain resilience, goods movement efficiency, emissions reductions, and economic competitiveness. “With six marine terminals at the Port of Long Beach now connecting to a beta version of the Supply Chain Information Highway, we’ve entered a crucial phase of development,” said Port of Long Beach CEO Mario Cordero. “We are grateful to the State of California and GO-Biz for their continued leadership in supporting data modernization to bolster goods movement. This funding will be important as we roll out these new enhancements to increase cargo velocity and tighten coordination across modes of transportation.” “We’re very excited with how this product – free to registered users – will help the more than 200,000 shippers who use the Port of Long Beach better plan and move cargo,” said Long Beach Harbor Commission President Bobby Olvera Jr. “Thank you to Governor Newsom for his continued recognition of the role the state’s seaports play in enhancing the economy and creating good-paying jobs.” “California’s ports are an essential link in the global supply chain, and this first-of-its-kind, collaborative data system will help ensure they remain so,” said GO-Biz Director and Senior Advisor to Governor Gavin Newsom, Dee Dee Myers. “I want to thank Port of Long Beach CEO Mario Cordero and the rest of his team for their leadership and ongoing participation in this effort.” “As Chair of the Senate Select Committee on Ports and Goods Movement, I believe it is important to strive for innovative enhancements that will support jobs and help ensure the efficient movement of goods in California,” said Sen. Lena Gonzalez, D-Long Beach. “I am pleased to see the Governor’s Office of Business and Economic Development allocating over $7 million in state funding for the Supply Chain Information Highway digital platform. Given that the Port of Long Beach is part of the ninth-busiest port complex in the world, contributing to 1 in 20 jobs in Southern California and over 2.6 million jobs nationwide, this funding will not only improve goods access for Californians but also support our communities by strengthening our economic landscape.” “This is a win for both the port and the surrounding communities,” said Assemblymember Josh Lowenthal, D-Long Beach. “Data is power. With this investment from GO-Biz we can ensure stakeholders are connecting and coordinating like never before. I’m confident that this will lead to fewer and more efficient trips and reduce unnecessary idling.” “The Port of Long Beach supports 1 in 5 jobs in this city and millions across the country,” said Long Beach Mayor Rex Richardson. “This grant from the Governor’s Office of Business and Economic Development will improve access to cargo information and help speed the movement of goods to American homes and businesses even faster and more efficiently, strengthening the economy not only here in Long Beach and California, but coast-to-coast.” The Port of Long Beach has partnered with a leading tech firm, St. Louis-based UNCOMN, to create the Supply Chain Information Highway. UNCOMN is collaborating with Amazon Web Services to provide cloud services and cloud hosting for the data. Development is focusing on three operational platforms in 2024: A Container Track and Trace feature to access up-to-date information about the status of containers moving through the Port of Long Beach. The Port Operations Dashboard, where users can review Port of Long Beach operational metrics. The dashboard can be viewed at www.polb.com/operations. The Beneficial Cargo Owner Dashboard, where BCOs can access more detailed information about their containers, including if they have arrived or departed and which Port terminal they are at.
AutoScheduler secures $6.5M funding from Noro-Moseley Partners
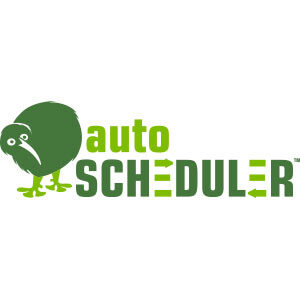
Investment to speed technology advancement and accelerate growth AutoScheduler.AI, an innovative Warehouse Orchestration Platform, and WMS accelerator announces a $6.5M first round of funding from Noro-Moseley Partners, an early growth equity firm based in Atlanta, GA, to continue growing and expanding the company and its technologies. Before this round, AutoScheduler was privately funded, growing rapidly and profitably. “We believe that now is the time for AutoScheduler to stake its claim as the leader of the warehouse orchestration space,” says Vasant Kamath, General Partner, Noro-Moseley. “Warehouses are undergoing a seismic shift in the industry and are at the forefront of supply chain transformation. With the right innovative tools in place, warehouses and supply chain leaders can unlock major efficiencies and improve customer satisfaction. AutoScheduler’s AutoPilot and AutoPilot Central are the tools to do just that.” Mr. Kamath will join the Board of AutoScheduler as part of the transaction. “Warehouse environments are constantly changing with fluctuating inventory levels, customer demands, and workforce availability, needing meticulous orchestration to meet customer service levels,” says Keith Moore, CEO of AutoScheduler.AI. “We believe the industry is at the cusp of innovation with our warehouse orchestration solutions, and we plan to expand on these technologies to deliver unparalleled results for customers’ bottom lines.” AutoScheduler intends to use the funds to enhance its AI-enabled warehouse orchestration solutions, which sit on top of a WMS, to optimize decision-making and deliver on time and in full fulfillment. In addition, AutoScheduler will expand its reach through strategic marketing and partnerships. It plans to grow the team, enhance the leadership team, and bring more products to market that leverage AI to enhance clients’ success. Recently, AutoScheduler introduced AutoPilot Central, which provides a bird’s-eye view of multi-site data for centralized command and control of an entire distributed warehouse network. Executives can better identify potential issues within the network, determine which shipments are at risk, and act before an issue occurs. AutoScheduler’s solutions benefit food, beverage, retail, and CPG firms by: Offering Dynamic Operations: AutoScheduler’s solutions offer real-time, dynamic warehouse orchestration that continuously optimizes operations, setting it apart from traditional, static WMS (Warehouse Management System) solutions. The platform adapts to changing conditions within the warehouse, ensuring the optimal use of labor, resources, and space. Planning for Tomorrow: AutoScheduler’s solutions go beyond managing the current execution window to predict future bottlenecks and issues, allowing businesses to take proactive measures to ensure smooth operations and prevent disruptions. Offering Full-Scale Visibility: AutoScheduler’s products provide detailed, real-time operational visibility and data streams that consolidate all necessary information into a single view for a clearer, comprehensive overview of all warehouse activities. Excelling in complex environments: The platform handles dynamic and chaotic environments, making it perfect for businesses with fluctuating demands and high operational complexity. “Companies that use AutoScheduler to orchestrate warehouse operations, such as PepsiCo, will be viewed as innovators and will help to shape the future of how we manage the distribution landscape,” adds Moore.
AAR reports Rail Traffic for the week ending July 6, 2024
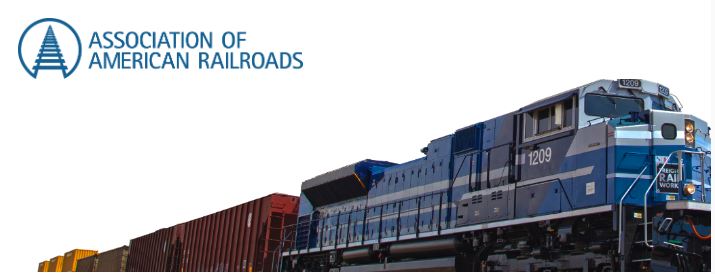
Today, the Association of American Railroads (AAR) reported U.S. rail traffic for the week ending July 6, 2024. This week’s total U.S. weekly rail traffic was 421,817 carloads and intermodal units, up 3.3 percent compared with the same week last year. Total carloads for the week ending July 6 were 195,030, down 1.2 percent from the same week in 2023, while the U.S. weekly intermodal volume was 226,787 containers and trailers, up 7.6 percent from 2023. Seven of the ten carload commodity groups posted an increase compared with the same week in 2023. They included grain, up 4,702 carloads, to 17,486; chemicals, up 2,017 carloads, to 30,552; and forest products, up 803 carloads, to 7,955. Commodity groups that posted decreases compared with the same week in 2023 were coal, down 7,804 carloads, to 50,700; nonmetallic minerals, down 3,326 carloads, to 26,710; and motor vehicles and parts, down 214 carloads, to 10,646. For the first 27 weeks of 2024, U.S. railroads reported a cumulative volume of 5,764,404 carloads, down 4.4 percent from last year, and 6,869,897 intermodal units, up 8.6 percent. Total combined U.S. traffic for the first 27 weeks of 2024 was 12,634,301 carloads and intermodal units, an increase of 2.3 percent compared to last year. North American rail volume for the week ending July 6, 2024, on ten reporting U.S., Canadian, and Mexican railroads totaled 299,444 carloads, up 0.4 percent compared with the same week last year, and 304,920 intermodal units, up 16.7 percent compared with last year. Total weekly rail traffic in North America was 604,364 carloads and intermodal units, up 8.0 percent. North American rail volume for the first 27 weeks of 2024 was 17,781,131 carloads and intermodal units, up 2.3 percent compared with 2023. Canadian railroads reported 89,296 carloads for the week, up 6.8 percent, and 66,515 intermodal units, up 71.5 percent compared with the same week in 2023. For the first 27 weeks of 2024, Canadian railroads reported a cumulative rail traffic volume of 4,344,255 carloads, containers, and trailers, up 1.6 percent. Mexican railroads reported 15,118 carloads for the week, down 11.6 percent compared to last year, and 11,618 intermodal units, down 0.4 percent. Cumulative volume on Mexican railroads for the first 27 weeks of 2024 was 802,575 carloads and intermodal containers and trailers, up 7.0 percent from last year. To view rail charts, click here.
Crown TSP 1000/1500 Series Turret Truck with Gena® Operating System reinforces safety and performance
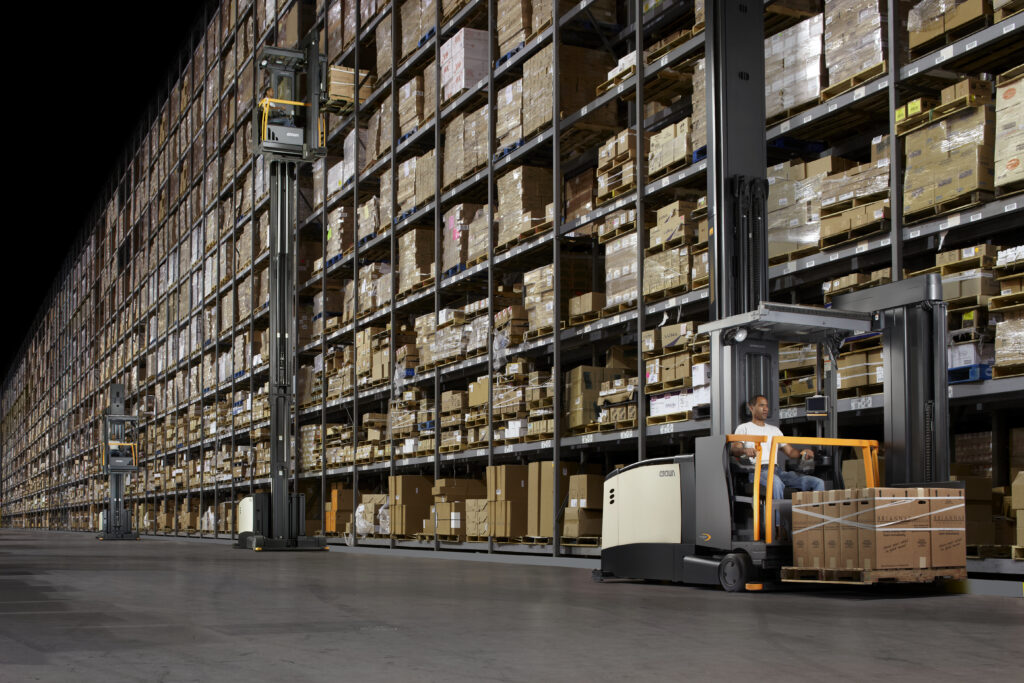
Crown Equipment Corporation has announced the availability of the new generation Crown TSP 1000/1500 Series very narrow-aisle turret truck. The lift truck features the Gena® operating system, which reinforces operator safety and enhances lift truck performance. It also simplifies truck-to-operator communication and provides real-time actionable data. The intuitive and innovative Gena operating system delivers a customizable, interactive experience to enhance supply chain performance. The transformational lift truck operating system provides users with real-time, actionable data, including safety reminders, illustrations, and customizable widgets that display key operating metrics like battery state of charge, hour meter, and height indicator. The TSP Series turret trucks deliver exceptional travel, lift, and lower speeds, all supported by the heavy-duty Crown MonoLift® mast, which delivers greater stability up to 675 inches. The mast allows operators to lift more weight to greater heights. The new turret truck also has the added ability to blend main mast hydraulic and auxiliary mast hydraulic functions, allowing operators to raise/lower the main platform and the auxiliary forks simultaneously to boost efficiency and enhance productivity. “At Crown, we understand that to achieve the desired business objectives, our customers need their systems, processes, and equipment to work together. That’s why we take a consultative approach and build each turret truck to fit the unique specifications and requirements of their applications and operational needs,” said Chris Grote, senior product manager of Crown Equipment. “We have developed technology-based tools to help us explore very narrow aisle configurations and benefits that will increase returns. For instance, our exclusive, very narrow aisle TSP SureSpec software gives you a fast, accurate way to spec turret trucks for our customers that help optimize their warehouse space.” To ensure the turret truck fits the application and meets operational goals, Crown consultants focus on three main factors as they relate to each customer: 1. The facility includes understanding aisle strategy, rack and ceiling heights, and floor surface specifications. It also includes specific performance needs for challenging environments like cold storage. 2. Load handling includes the size, weight, shape, and consistency of the pallet loads, along with racking configurations. 3. Performance potential involves using simulation software to define possible scenarios and analyze their costs and benefits to help ensure desired results are achieved. TSP Series turret trucks can be equipped with operator-assist technology options that enable more efficient operation and enhance operator confidence and performance. For example, the Auto Positioning System blends travel and lift functions to allow the turret truck to take the most effective route to a designated rack location, increasing productivity by up to 25%. Auto Fence slows or stops travel and can limit lift height within the guided very narrow aisle based on the location of the turret truck. The Crown TSP 1000/1500 Series turret truck includes Crown’s patented OnTrac® anti-slip traction control system, which reduces slippage or wheelspin whenever the lift truck accelerates, plugs, or brakes on wet or dusty floors. Customized energy solutions for the turret truck are available based on a range of V-Force® lead-acid or lithium-ion batteries and chargers to meet customer application and infrastructure requirements.
3M announces departure of Chief Financial Officer
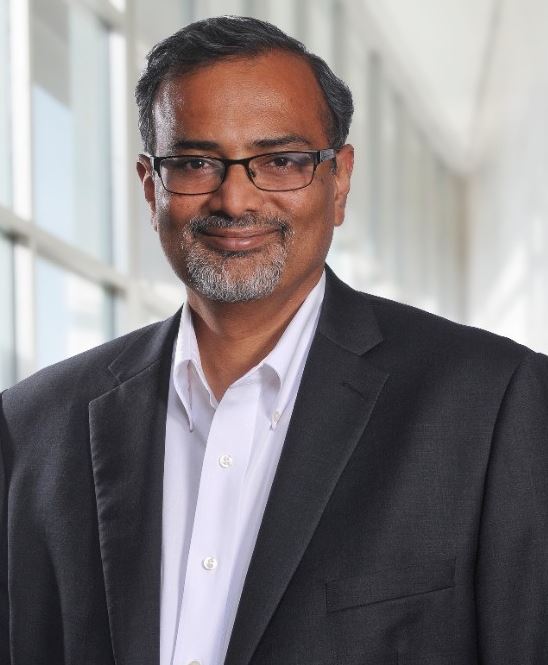
3M announced today that Monish Patolawala, President and Chief Financial Officer, will resign effective July 31, 2024, to pursue another opportunity. Mr. Patolawala will stay on through July 31, 2024, to ensure an orderly transition. “On behalf of all 3Mers, I thank Monish for his leadership and contributions to 3M over the past four years,” said William Brown, 3M Chief Executive Officer. “We wish him continued success in his future endeavors.” “It has been a privilege to work as part of 3M’s leadership team, and I am proud of our accomplishments,” said Mr. Patolawala. “3M is well positioned for success, and this is the right time for me to transition to a new opportunity.” 3M has initiated a CFO succession process and will provide updates as appropriate.
Episode 501: Solving the truck parking crisis with Truck Parking Club
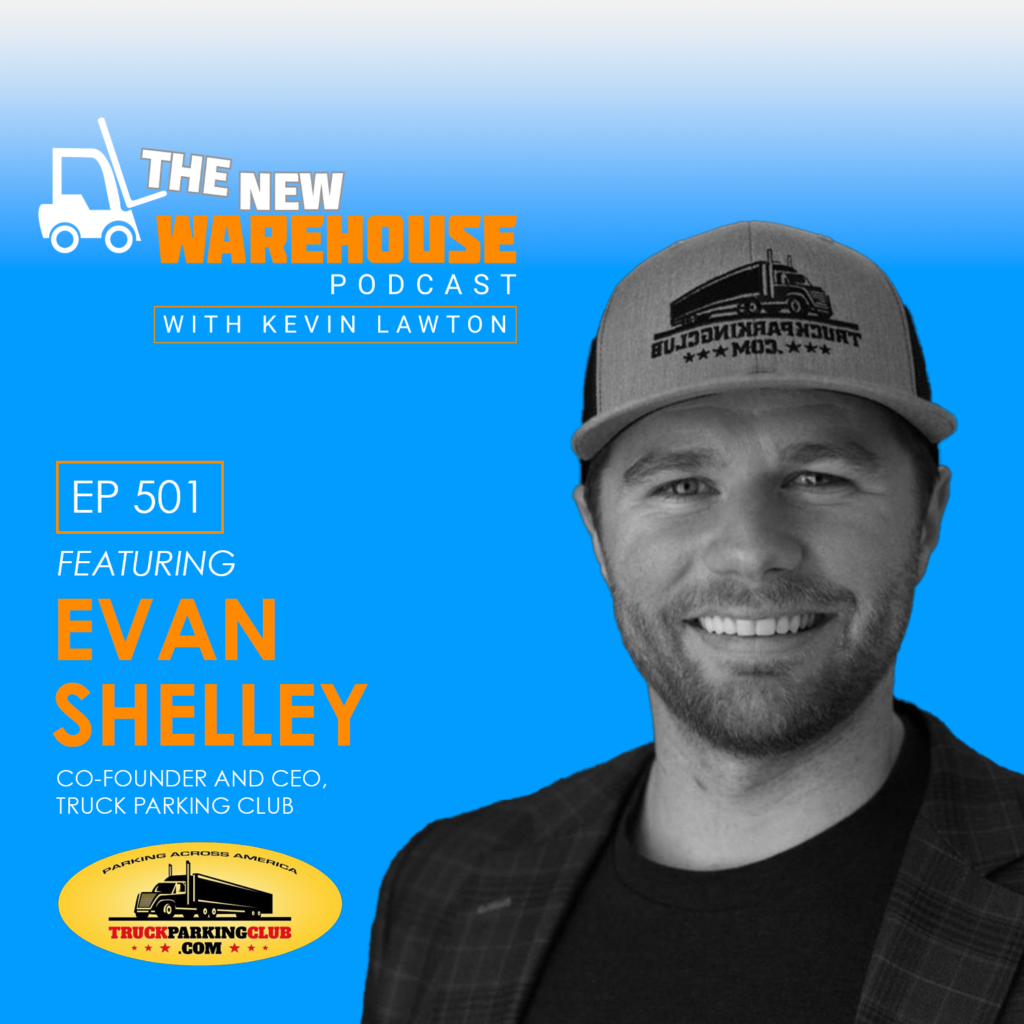
Welcome to this episode of The New Warehouse Podcast. Today, we are joined by Evan Shelley, the co-founder and CEO of Truck Parking Club. This innovative company addresses the widespread truck parking shortage in the United States. Truck Parking Club provides a platform that connects truck drivers with available parking spaces using a two-sided marketplace model. The company leverages technology to solve both the parking shortage and awareness issues, making it easier for truckers to find and reserve parking spots. Evan shares insights into the genesis of Truck Parking Club, its operations, and its impact on the warehousing and logistics industry. Tackling the Truck Parking Shortage Evan highlights the critical need for truck parking across the U.S. and how the Truck Parking Club emerged from his civil engineering and real estate background. Evan recognized a significant gap, “There’s a huge need for more truck parking. Municipalities wouldn’t support it, but people in the industry understood the severity of the issue.” The Truck Parking Club addresses this shortage using a self-service model, where property owners list their spaces for truckers to reserve. Evan adds, “We don’t just take existing trucking and put it in the marketplace. It’s also trucking companies, yards, repair shops, CDL schools, and locations currently suitable for truck parking. The easiest way to explain it is that we are the Airbnb for truck parking.” This alleviates parking stress for truckers and monetizes unused spaces for property owners. Bringing Awareness to the Shortage of Truck Parking Beyond just a shortage of spaces, Evan emphasized the problem of awareness. Truckers often waste valuable time searching for parking. “If you don’t know there’s available space two miles down the road, you’re not going to find it until you drive past it,” Evan noted. Truck Parking Club’s platform aims to bridge this gap by providing real-time information on available parking spaces. The technology ensures truckers can easily find and reserve spots, reducing the time spent searching and increasing efficiency. This dual approach of increasing supply and improving awareness is central to the company’s mission. The Truck Parking Shortage Impacts Warehousing and Logistics The truck parking shortage also significantly affects the warehousing and logistics industry. Evan pointed out, “It costs everyone money if drivers don’t have an adequate place to park and are spending a lot of time looking for parking.” Warehouses often face constraints due to a lack of parking, leading to delays and increased operational costs. By integrating Truck Parking Club’s solution, warehouses can offer parking spaces to truckers, reducing these constraints and fostering better relationships with drivers. Evan shared, “Ultimately, they make money, and there’s less stress, especially in situations where drivers can’t leave due to lack of hours or other constraints.” Key Takeaways Truck Parking Club provides a two-sided marketplace connecting truckers with available parking spaces. The platform enhances awareness of parking availability, saving truckers time and reducing stress. Leveraging existing spaces, warehouses, and logistics companies can reduce constraints and operational costs. Property owners can monetize unused spaces, adding value to their assets. The New Warehouse Podcast 501: Solving the Truck Parking Crisis with Truck Parking Club
Port of Long Beach Harbor Commission names Director of Project Controls
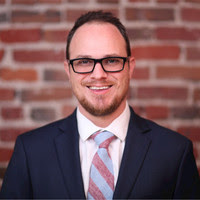
On Monday, the Long Beach Board of Harbor Commissioners approved the selection of Ashley Morteboy to lead the Project Controls Division at Port of Long Beach, the nation’s second-busiest seaport. The Director of Project Controls is responsible for establishing and tracking schedules, budgets, and costs for the timely delivery of the Port’s infrastructure projects to the Engineering Services Bureau. Morteboy comes to the Port of Long Beach after working two years as director of project controls at UC Davis Health, where he similarly oversaw the planning and design of the agency’s capital improvement program. He previously served as a senior manager at Procter & Gamble for two years and brings over 18 years of project controls experience working nationally and internationally throughout his career, spanning a wide range of capital investment ventures for many sectors and industries. Morteboy holds a bachelor’s degree in mechanical engineering from Manchester Metropolitan University in the United Kingdom. Morteboy’s appointment is effective July 29.
Manufacturing Technology Orders grow in May 2024 despite sustained high interest rates
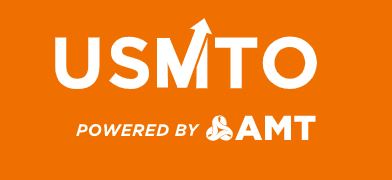
Manufacturing technology orders, measured by the U.S. Manufacturing Technology Orders Report published by AMT – The Association For Manufacturing Technology, totaled $386.7 million in May 2024. New machinery orders were up nearly 22% from April 2024 and 6.5% over May 2023. This is the first month in 2024 where the value of orders placed exceeded those of the same month the previous year. Through the first five months of 2024, orders totaled $1.8 billion, a 12.2% decrease compared to 2023. Manufacturers have realized they can no longer outwait the Fed’s “higher for longer” interest rate strategy. As a result, they are beginning to increase capital equipment purchases to meet the sustained demand for goods and machinery from consumers and businesses, even as high interest rates persist. Despite 2024’s mild slump in machinery orders compared to the beginning of 2023, cutting tool orders, as measured by the Cutting Tool Market Report, a collaboration between AMT and the U.S. Cutting Tool Institute (USCTI), show 2024 consumption holding steady at record levels. This indicates that despite reported hesitation to invest in additional machinery, production levels remain elevated, which is confirmed by the measure of industrial production from the Federal Reserve. Contract machine shops, the largest consumer of manufacturing technology, increased their orders from April to May 2024 but significantly less than the industry’s overall growth. While some OEMs have made additional investments despite heightened interest rates, contract machine shops have consistently failed to keep pace with the overall market throughout 2024. Electrical equipment manufacturers are having the best start to the year since the record-setting start of 2022. Similarly, power generation and transmission equipment manufacturers are investing at the second-highest year-to-date rate since 2008. These industries undoubtedly benefit from the government investment authorized by the CHIPS and Infrastructure Acts and are, therefore, less sensitive to interest rates than others. As previously reported, the Biden administration is in a rush to spend the remaining money allocated by Congress under these bills in case President Joe Biden does not win reelection in November. That spending could accelerate, given the public’s response to Biden’s debate performance at the end of June. The automotive sector continued to purchase machinery but at a much slower pace than the previous two years. Vehicle assemblies increased in May 2024 and remained above the monthly average this year. Like manufacturers awaiting lower interest rates before investing in machinery, consumers may have grown tired of waiting out the Fed, as new vehicle sales increased in April and May. The Fed’s interest rate path has thrown a wrench in many economic forecasts since the beginning of the year. The outlook for manufacturing technology orders was no different. The beginning of the year fell well short of expectations, but the lag behind 2023 has narrowed in recent months. Whatever course the Federal Reserve eventually takes with interest rates, the USMTO data shows the appetite for additional manufacturing capacity growing as we approach September’s IMTS 2024 – The International Manufacturing Technology Show, the largest manufacturing trade show in the Western Hemisphere.
Eagle Mark 4 celebrates milestone with grand opening of new headquarters building
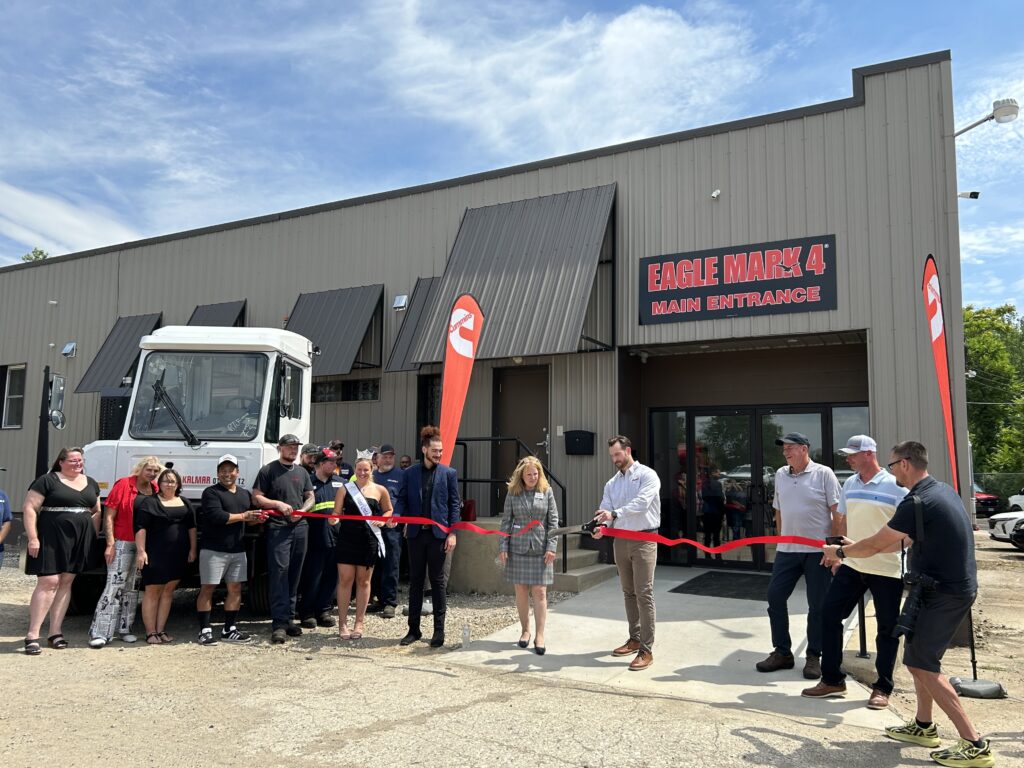
Eagle Mark 4, a Kalmar Ottawa Premier Partner, celebrated the grand opening of its newly renovated headquarters on July 3, 2024, with a ribbon-cutting ceremony and open house event. To commemorate the company’s significant milestone, Eagle Mark 4 welcomed the Richland Area Chamber of Commerce, government officials, customers, employees, Scout Construction, and local media to the new building for a ribbon-cutting ceremony followed by a lunch. “Thank you to our community partners and the Richland Area Chamber of Commerce,” said Eagle Mark 4 president Mike Tozzi. “This building has a long-standing history, and we are proud to be able to give it a new purpose with the help of Scout Construction. Thank you to all our employees who have worked so hard over the past year and our customers who have allowed us to reach this point. This new facility presents new opportunities to grow within the Mansfield community and on a national scale.” Ellen Heinz, President and CEO of Richland Area of Commerce, led the ribbon-cutting ceremony. “We are so thankful for Eagle Mark 4’s additional investment!” Heinz said. “They are a leader in the yard truck industry, and we are thrilled the area is home to their U.S. headquarters! This expansion not only retains and creates new jobs but has transformed the property and their footprint in our area. We are so fortunate to have them as a valued member of our business community and to see them growing in our area!” Located at 95 Ohio Brass Road, Mansfield, OH 44902, the 40,000-square-foot facility serves as Eagle Mark 4’s national headquarters to its satellite locations in North Carolina and New Mexico with a fully stocked parts warehouse and dedicated space designed for its Cummins-certified, skilled technicians to service yard trucks. Key features of the new headquarters include: 15-bay shop space with full-service wash bay 10-acre lot State-of-the-art parts warehouse Updated employee offices with three conference rooms Safety and training conference room
Queen City Robotics Alliance announces two new board members
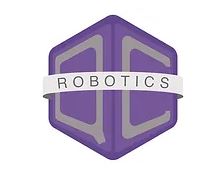
Queen City Robotics Alliance has announced the addition of two new board members – Robert Hillman and Brian Keiger. Robert Hillman is the founder and managing partner of RLH Consulting. Founded in 2008, the company handles business development, structured credit, financial advisor/strategist, strategic advisory, and campaign management for corporations and individuals. He is also on the City of Charlotte’s Business Advisory Committee (BAC). This committee provides recommendations and advice to the City Council on ways Charlotte can improve business development, emphasizing small businesses while providing a forum to raise issues, discuss issues, and have input into City policy responses. Mr. Hillman received his Bachelor of Science in Electrical Engineering from the Massachusetts Institute of Technology and has an MBA from the Stern School of Business at New York University. Mr. Hillman joined the board earlier this year and looks forward to growing QCRA’s outreach into Charlotte’s underserved communities. Brian Keiger is Vice President for Conveyco Technologies, a leading system integrator in warehouse automation, and has been involved in the supply chain industry for over 34 years. Mr. Keiger is also active in MHI, North America’s leading material handling trade association, holding a seat on several committees, and is the chair of the Mobile Automation Group. He also holds seats on the Industry Advisory Panel for the National Center of Supply Chain Technology Education (NCSCTE) and on the Systems Engineering and Engineering Management (SEEM) Advisory Board at the University of North Carolina Charlotte. He received his bachelor’s degree in mechanical engineering from North Carolina State University. Mr. Keiger joined the board last month because “STEM education is important, and these kids are important.” He believes STEM education goes beyond imparting knowledge to nurture critical thinking skills, enhances scientific literacy, and cultivates the next generation of trailblazers and problem solvers. “At QCRA we’re building more than a STEM education program, we’re building kids,” Mr. Keiger says. “We’re preparing the next generation’s workforce. As a businessman in an ever-evolving supply chain industry, this is crucial. The talent is right here, already being developed. All we have to do is invest.”
Advance Lifts highlights its Industrial Powered Turntables (TPH &TPL)
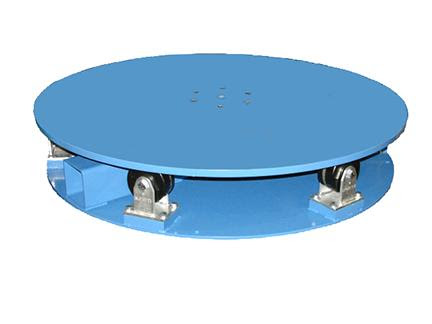
Motorized turntables allow products to be rotated safely and more accurately Advance Lifts, a North American manufacturer of industrial scissor lift tables and dock lifts, highlights its Industrial-Powered Turntables (TPH &TPL), designed to provide unparalleled efficiency, safety, and durability when rotating heavy loads in the material handling industry. Turntables are used in positioning jobs where loads are regularly rotated. There are two basic types of standard-duty turntables: non-powered and powered. Industrial-powered turntables are used when the rotational effort of a job is too high for a manual turntable. Powered turntables are available in both low-profile and high-profile configurations. Low-profile powered turntables (TPL) are used for power applications where low platform height is essential. There are 16 models with edge load maximums ranging from 50 to 1,400 lbs. Load capacities range from 2,000lbs to 10,000lbs with platform diameters ranging from min 24”/max 48” to 85”/max 96”. Circular platforms are required for this configuration because the drive motor is located at the platform’s edge and projects above the platform. The platforms are supported by lifetime lubricated roller-bearing cam followers. High-profile powered turntables (TPH) are used for power applications where low platform height is less important or the loads are square. There are 16 models with edge load maximums ranging from 100 lbs to 1,200 lbs. Load capacities range from 2,000 lbs to 10,000 lbs, and platform sizes range from 24×24” to 96×96”. Standard rectangular and round platforms are available. These heavy-duty rotating platforms have a drive motor under the platform. Inverted casters with tapered roller bearings or cam followers support them.
How Self-Nurturing Therapy can make you a better leader Seven steps to practice now
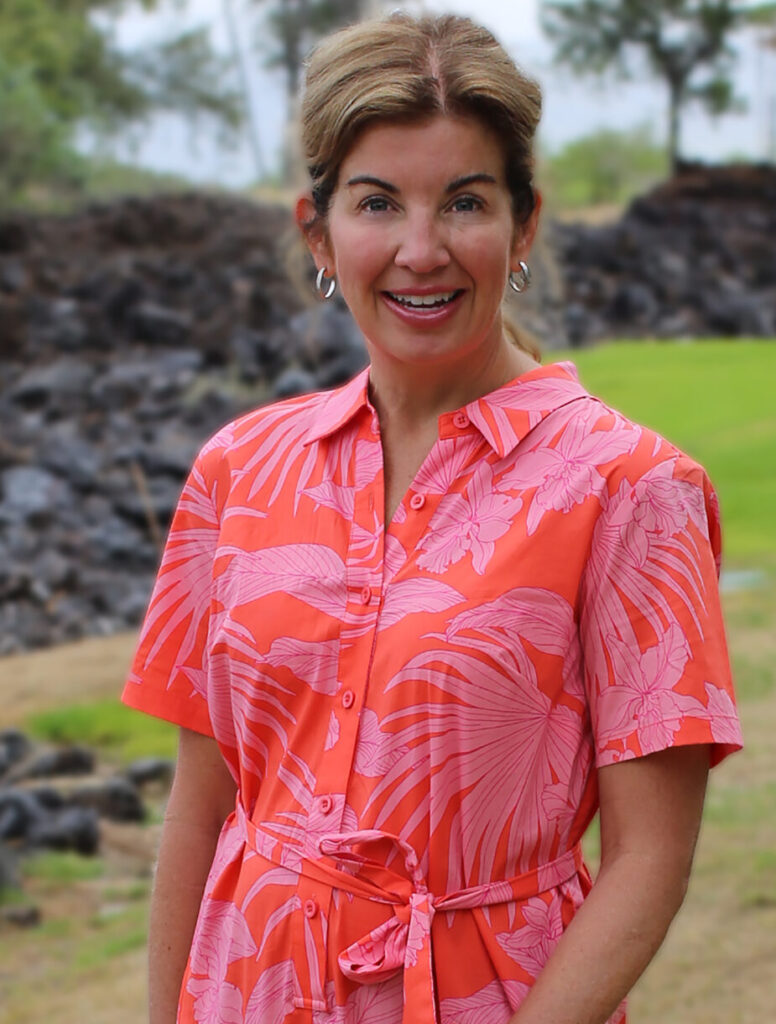
Navigating leadership brings a unique set of challenges and opportunities. A young executive, Sarah, faced complaints from her team, who described her as dismissive and devaluing. She was initially blindsided and defensive, yet, as do excellent leaders, she focused on improvement–learning that how leaders make people feel is essential to retention, culture, and ultimately profit. As frontrunners in your field, you know strategies to build your team, yet something is preventing the desired outcome. What is getting in your way? Failure to emotionally connect with your team members makes “lonely at the top” inevitable and creates a culture vulnerable to disconnection, dissatisfaction, and lack of cohesiveness. On the other hand, a positive connection with your team brings an entirely new level of positive, productive, and happy relationships. Rather than focusing solely on strategies to improve interactions, a new approach called Self-Nurturing Therapy (SNT) targets the part within you that carries the fear of vulnerability and acts as a gatekeeper to allowing meaningful emotional connection with others. How SNT Enhances Leadership Leaders learn to change their relationship with vulnerability rather than attempting to eliminate it. SNT encourages leaders to engage with their emotions, building resilience and capability. This emotional strength translates into better communication, sharing of creativity, and a more effective leadership style. Self-nurturing therapy is a process that teaches how to soothe your vulnerable part–specifically your inner child–and learn to thrive in relationships. Here are seven steps that leaders can practice now to enhance their performance: Get to Know Your Inner Child: Give your young self the attention she deserves. By acknowledging and soothing early wounds, leaders can reduce reactive response styles. Sarah, for example, discovered that her reaction to dismissiveness was a self-protective reaction rooted in a childhood of bullying. Sarah’s inner child was so anxious that the corporate strategies she had learned to communicate with team members were interrupted by her emotional state. To reduce reactivity, create a timeline of your life, identifying experiences where you felt shame or vulnerability. Knowing where your self-protection emerged reduces reactivity in interactions with others. Create Emotional Awareness. Leaders are taught the importance of communication, but without understanding your emotions, interactions will fall flat. To resolve this, reflect on what earlier experiences taught you about others. Do you see others as trustworthy and safe or risky and uncertain? Did safe people support you when bad things happened, or could you only count on yourself? Sarah identified that years of suffering from bullying left her feeling alone in her journey. She realized that interactions elicited fear that they would disappoint and an immediate internal reaction to keep conversations short and direct so they would end quickly. Create a Soothing Mantra. Negative early life experiences that are left unprocessed don’t evaporate. Instead, the inner child holds them tight, a reminder to never put yourself at physical or emotional risk again. Some things would have been helpful to you as a child that you never received. Practice acknowledging and accepting emotions from your early years. Start by asking yourself, “What does my inner child need to hear when she is worried?” You’ve got this, or That was then, this is now, offer reassurance and empower a secure response. Think of Your Inner Child as Your Gatekeeper. Excellent leaders have a business gatekeeper to ensure they are insulated from the risk of overscheduling or losing focus. Your inner child is the gatekeeper to how much you allow yourself to care for and invest in relationships emotionally. As a competent adult, you hold the capability to assess those trustworthy enough to be part of your inner circle. Write a list of people who have shown integrity and take a moment to acknowledge them. Notice how your interaction improves when you assure your gatekeeper that you are safe, secure, and confident in your ability to assess others. Purposefully Value Your Feelings. What did your child-self need to cope during difficult times but was denied? For some, like Sarah, it was knowing they were safe, while for others, it was hearing, “You’re loved”. Good parents value what their children need and feel. As an adult, you can self-deliver what you need. Rewire negative thought patterns rooted in your early experiences with positive messaging. Were you taught to believe that other people’s wants and desires were more important than your feelings? Tell yourself, “You matter.” Were you taught to believe harmony was more important than caring for yourself? Know, “You. Matter”. Thrive Emotionally at Work. See team members as worthy of having a meaningful relationship with you. While your inner child tries to protect you from caring too much, it disrupts the soft skills that make good leaders great. Communication without empathy and understanding is risky for leaders. Instead, practice curiosity about what people are experiencing and, equally as important, what emotional response these interactions evoke within you. Use open-ended questions: “How was your weekend?” rather than “Hope you had a good weekend.” Leaders who know their people receive increased investment from them and a willingness to go the distance when asked. Learning to Tolerate Emotions Requires Practice. If you have a loud inner child determined to protect you from vulnerability, showing them that you’re taking the lead requires practice. Avoid becoming frustrated with yourself and instead respond with self-kindness. It’s been a journey to achieve your leadership goals, and you are constantly growing. Mastering comfortability with emotions leads to joy for self and high-performance teams and requires practice. Integrate reflective journals, conversations with trusted friends, and meditation or yoga to support you through this rewarding process. Celebrate the moments when you notice emotions, feel the discomfort, and remind yourself, “Hey, I’m okay!” In summary, leaders who engage in SNT experience numerous benefits that enhance their effectiveness and happiness in their role. Leaders can create a positive, empowering environment that drives organizational success by healing past traumas and fostering present-moment awareness. About the Author: Julie Gowthorpe, PhD, RSW, is a public speaker and author. In addition to her private practice, Gowthorpe contributes her expertise
Farrukh Ghani joins Hyundai Material Handling as Director of Dealer Development & National Accounts
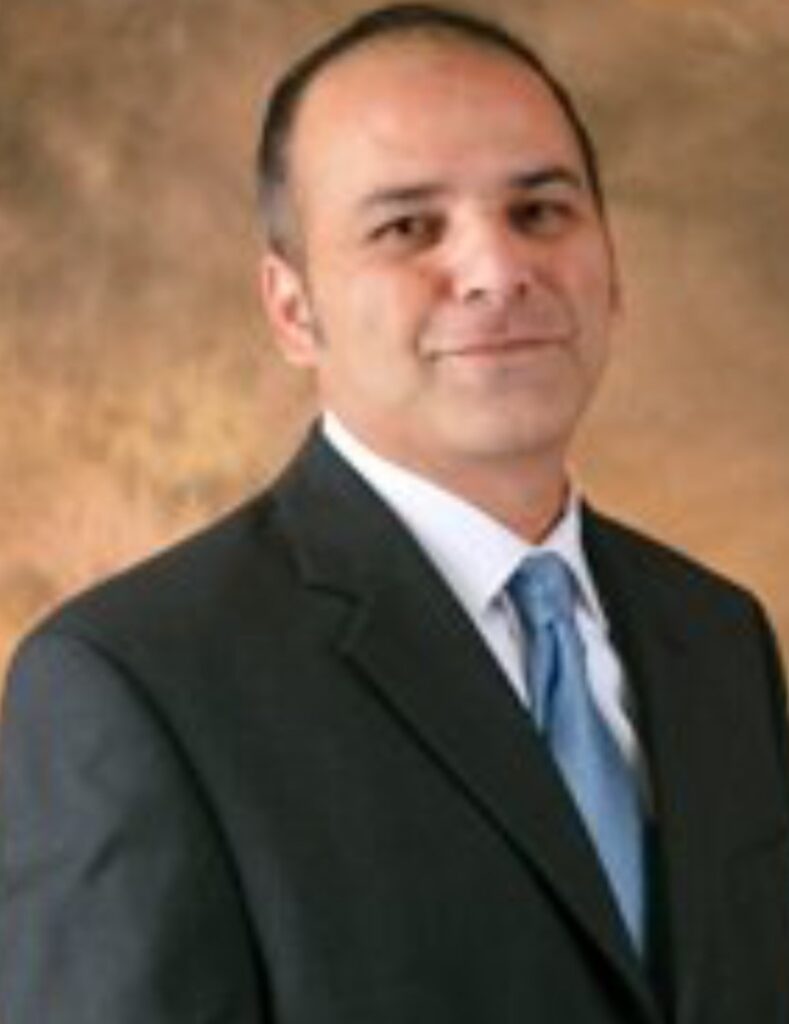
Hyundai Material Handling hired Farrukh Ghani as the new Director of Dealer Development and National Accounts. Mr. Ghani brings more than 25 years of industry experience to the company. His areas of responsibility will include leading the company’s efforts to strengthen its dealer network, add to its growing list of national accounts, and continue its more aggressive approach to sales and marketing. Mr. Ghani has held key leadership positions in the material handling industry. Previously, he served as Director of Channel Development for Doosan Industrial Vehicle America, helping the company achieve record growth and market share year-over-year from 2016 to 2023. Before that, he served as vice president and chief financial officer for Clark Material Handling Company, overseeing and enhancing diverse departments such as finance, sales, IT, order management, and logistics. “I’m very excited to bring my years of experience to Hyundai, its leadership team, and an incredible lineup of dealers,” said Mr. Ghani. “My goal is to help continue the company’s impressive growth and its position of excellence and innovation in the material handling industry.” His wealth of experience also includes creating and implementing successful programs in Sales and Marketing, Strategic Planning, and Global Operations. His proven record of success covers a wide range of business sectors, including manufacturing, supply chains, logistics, engineering, and finance. “We’re extremely proud to bring on someone of Farrukh’s experience and years of success,” said Lewis Byers, Executive Vice President/COO of Hyundai Material Handling. “We believe he’s going to make a tremendous difference in our organization and with our dealers and national accounts. As an organization, we’re committed to growth, building stronger relationships with both our dealer partners and customers, and increasing our North American market share. Farukh will play a key role in all of this.”
The New Warehouse goes LIVE on LinkedIn today discussing The Warehouse Revolution
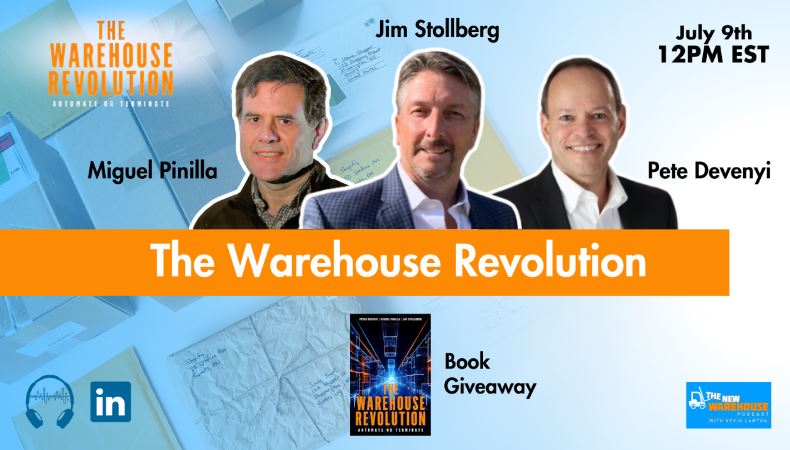
The New Warehouse, with host Kevin Lawton, will host a special LIVE LinkedIn podcast with the authors of The Warehouse Revolution—Automate or Terminate at noon EST. Kevin will be joined by authors Miquel Pinilla, Jim Stollberg, and Pete Devenyi. To join, click this link or the image below to take you to the LinkedIn event. We will go live at noon EST, so just hit the join button, and you can listen in. Have questions? Please reply to this email address or raise your hand in the event and ask them yourself.