ASSP and SafetyCulture offer new training on mobile devices
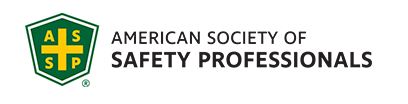
The American Society of Safety Professionals (ASSP) has joined with SafetyCulture, a global technology company, to help frontline workers stay up-to-date on federal safety and health standards. A new series of bite-sized refresher training courses are now accessible on any mobile device and can be completed on-site in just 15 minutes. “Essential safety and health courses are literally being put into the pockets of workers across the country,” said Mary Goranson, ASSP’s vice president of workforce development. “It’s a user-friendly experience that helps employers provide refresher training while enabling our Society to reach more workers with important safety information that can reduce injuries, illnesses and fatalities on the job.” The 27 new courses are designed around standards set by the Occupational Safety and Health Administration (OSHA). The mobile training aims to shake up the notion of traditional compliance training, making it widely accessible and highly interactive, even in remote locations. The courses are free with a SafetyCulture account. The series of educational courses covers topics that include fall protection, machine guarding, heat stress, hazard communication, and respiratory protection, ensuring that workers stay current on safety and health protocols in the same brief time it takes to conduct a toolbox talk. The annual OSHA refresher training is geared toward workers in industries that face greater risks, such as construction and manufacturing, where federal regulations make a bigger impact in sending workers home safe at the end of the day. “OSHA regulations play a key role in safeguarding worker safety and health,” Goranson said. “At a minimum, organizations must stay compliant and workers need to understand what is expected of them from a safety perspective.” The new courses are particularly helpful to safety professionals and workers who have received their OSHA DOL Card or last completed OSHA training more than one year ago. This group includes carpenters, electricians, plumbers, welders, masons, and other workers who require a higher level of workplace safety knowledge. “Making training more impactful and accessible is something we are really passionate about,” said Mike Welch, managing director of SafetyCulture Training. “By teaming up with ASSP, we are more broadly using our mobile technology to provide the high-quality courses that frontline workers need to navigate common job-site hazards.” The new material is now available on SafetyCulture’s online platform for organizations to deliver the refresher training courses directly to their team’s mobile devices to ensure compliance with OSHA standards.
The Movu atlas pallet shuttle offers Westhof BIO automated high performance in deep-freeze storage
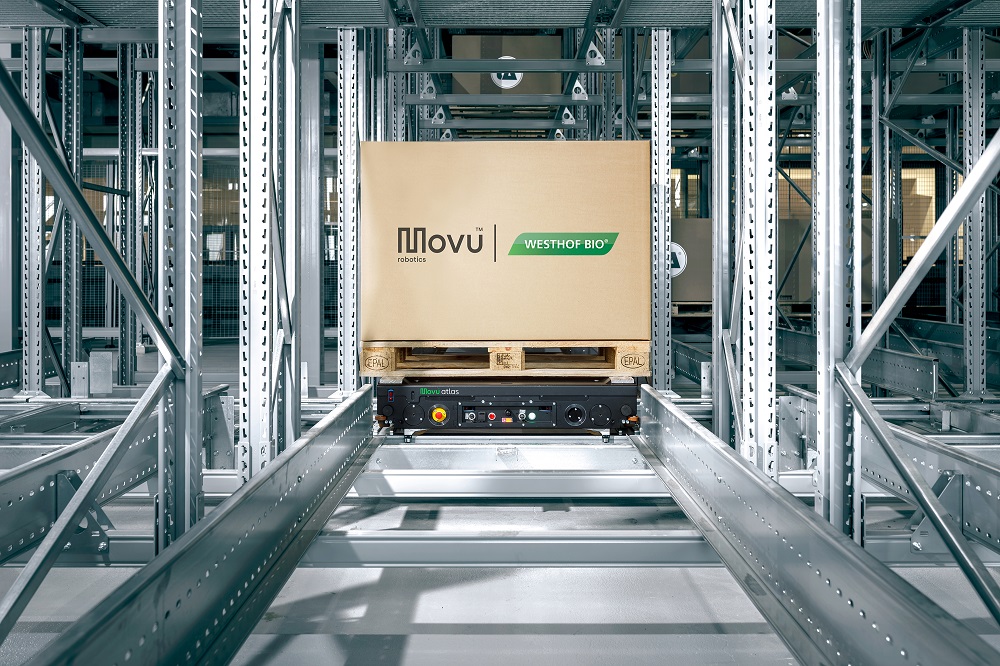
German Organic vegetable freezing company Westhof BIO has selected easily accessible, plug-and-play automation in the form of a stow Racking silo served by Movu atlas 2D pallet shuttles. Part of an integrated intralogistics solution from systems integrator Körber, the silo and shuttles play a key intralogistics role in Westhof BIO’s brand new, highly automated production facility, located near Hamburg in Germany. Due to go live in June 2024, the Movu system provides a reliable and efficient automated flow of goods and high-density storage in a six-level silo to hold over 5000 pallets of frozen vegetables in the cold store. Westhof BIO processes around 10,000 tonnes of fresh produce annually providing an organic frozen range. Its new climate- and resource-saving organic freezing plant gives the company room to expand and represents a major step forward for the company. The ultra-modern and automated freezer warehouse stores frozen vegetables to allow their delivery on pallets to manufacturers of organic food and baby food all year round. The company looked for a high-density storage solution for the vegetables in its minus 24 degrees centigrade cold store that offers reliability and scalability as well as an efficient and accurate flow of goods. The automation solution consists of six Movu atlas shuttles, one of which transports the pallets on each of the six levels of the stow silo, which measures 60 m long x 31 m wide x 17 m high. Providing deep, multi-pallet channel storage, the silo maximizes space by minimizing the number and width of driving aisles – this installation has just one. Efficient and quick to set up, the plug-and-play Movu atlas system fits all buildings to ensure no warehouse is left behind when it comes to automation. Even if a shuttle goes down or requires maintenance, it can be easily removed and replaced with a new shuttle within a day, with Westhof BIO’s WMS directing goods to one of the other silo levels. The easily scalable atlas system allows the addition of shuttles to increase throughput and store greater quantities of vegetables during harvest peak. Stefan Pieters, CEO of Movu Robotics said: “We are delighted to have successfully handed over another Movu project to our customer. With the combination of the stow silo and the Movu atlas 2D shuttle, Westhof BIO could trust on consistent high engineering and Project Management standards with a reliable project lead time. The Movu atlas 2D Shuttle is a true example of simple and easily accessible plug and play automation in challenging cold storage environment. It´s scalability provides Westhof BIO with automation that handles peaks and adapts easily to future requirements.” Berit Carstens-Lask, Managing Director of Westhof BIO, adds: ”We are extremely satisfied with the automation solution that has been realized and with both the engineering and execution of the project. We hope that when we start running it, the automation solution from Movu will make a significant contribution to optimising our entire production and warehouse processes, making them much more efficient and flexible.”
Bobcat breaks ground for Mexico manufacturing facility
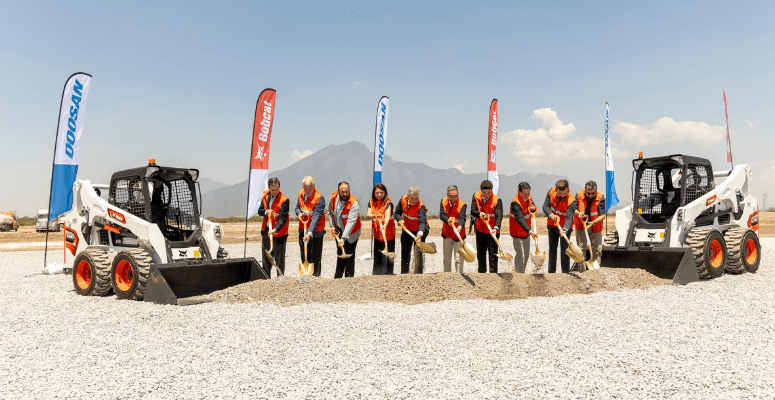
Bobcat Company, a global equipment, innovation, and worksite solutions brand, held a ceremonial groundbreaking on June 13 for its new, $300-million manufacturing facility in Mexico. Located in the Salinas Victoria municipality, outside of Monterrey in the state of Nuevo Leon, Mexico, the 700,000-square-foot facility is expected to be operational in 2026. The groundbreaking ceremony was attended by Bobcat representatives, elected officials, and area business leaders. The new location, which was announced in 2023, will expand Bobcat’s existing global footprint to create additional production capacity and manufacturing capabilities for select compact track and skid-steer loader models. Bobcat’s compact loaders are also produced in the U.S. and the Czech Republic where production will remain following the new facility opening. “We have seen tremendous growth across our business, and this new facility will support our long-range plans for increased production to meet customer demand,” said Scott Park, Doosan Bobcat CEO and vice chairman. “This groundbreaking represents our commitment to our customers—present and future—who are ready to accomplish more with our equipment.” The manufacturing facility will seek LEED Silver certification and feature state-of-the-art technology with an emphasis on quality, precision and energy efficiency. “We look forward to growing our manufacturing footprint in the Salinas Victoria community for its excellent industrial sector, skilled workforce and strong business environment,” said Mike Ballweber, Doosan Bobcat North America president. “Our investment here demonstrates our confidence in this manufacturing environment and thriving local economy.” The design team includes U.S.-based Shultz + Associates Architects and Mexico-based GP Construcción, a division of Grupo GP, as the construction manager. Shultz + Associates Architects has partnered with Bobcat on the design and architecture of many of its North American locations. GP Construcción specializes in industrial parks and facilities across Mexico. The new factory is expected to create 600 to 800 jobs in the region. Career opportunities can be found at bobcat.com/carreras.
Toyota Material Handling auctions pink forklift to dealer network, Raising $65,000 for Breast Cancer Awareness
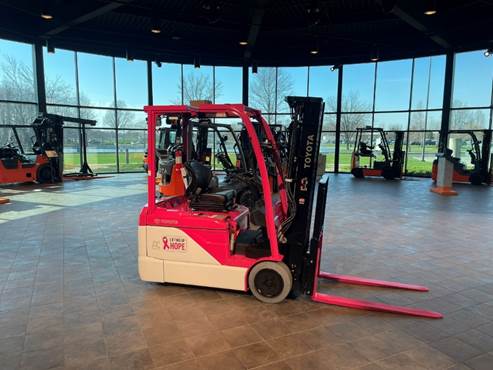
Toyota Material Handling showcased its steadfast commitment to supporting breast cancer research and treatment by auctioning off a custom pink forklift to its industry-leading dealer network at the company’s annual dealer meeting earlier this year. Toyota donated the entire winning bid of $65,000 to the Susan G. Komen Foundation. The initiative was driven by the Toyota Women’s Impact Network (T-WIN), a women-led group dedicated to fostering Toyota’s success and inclusivity for women in the workplace. Recognizing the immense potential within Toyota’s female workforce, T-WIN spearheaded the creation of the distinctive pink forklift, leveraging the talent and creativity of its members while honoring the women who participated in building the truck. This year’s auction coincided with Women’s History Month, concluding a series of initiatives led by Toyota women throughout March. The pink forklift auction has become a catalyst for Toyota’s ongoing philanthropic efforts since the first successful auction in 2022. Once again, each female Toyota associate who contributed to building the forklift added their signature to the truck, symbolizing their support for finding a cure for breast cancer. “Hosting this auction in conjunction with our Women’s History Month initiatives was a wonderful opportunity for Toyota Material Handling to make an impact on breast cancer research and awareness while honoring all those who have been affected,” said Lea Ann King, Vice President of Legal and General Counsel of Toyota Material Handling. “We are so thankful for our incredible dealer network whose participation and support made this auction successful.” During Toyota’s annual dealer meeting in Scottsdale, Arizona, leaders from Toyota’s more than 60 North American dealers were presented with the opportunity to bid on the one-of-a-kind 3-Wheel Electric Forklift. After a competitive auction, Shoppa’s Material Handling, a Toyota dealership in Dallas, Texas, made the winning bid of $65,000, nearly doubling the amount raised from the previous auction. “We are thrilled to have secured the iconic pink breast cancer awareness forklift from Toyota Material Handling’s auction and donate the proceeds to Susan G. Komen foundation,” said Jimmy Shoppa, President of Shoppa’s Material Handling. “Shoppa’s stands in solidarity with those affected by breast cancer and is committed to contributing to a brighter, healthier future for all. We are proud to play our part in this meaningful endeavor.” The pink forklift will find its home in Shoppa’s Material Handling’s dealership, where it will serve as a symbol of hope and inspiration for the entire company. In honor of National Breast Cancer Awareness Month in October, Shoppa’s Material Handling will host an event showcasing the pink forklift, further spreading awareness, support for the cause, and their partnership with the Komen Foundation. This initiative reaffirms Toyota’s ongoing dedication to positively impacting the community by staying true to its core purpose of ‘helping people carry the load’. Through initiatives like these, Toyota continues to demonstrate its commitment to corporate social responsibility by making a difference in the lives of others. Learn more about Toyota Material Handling’s philanthropic efforts here.
Port of Long Beach sets $760 million annual budget
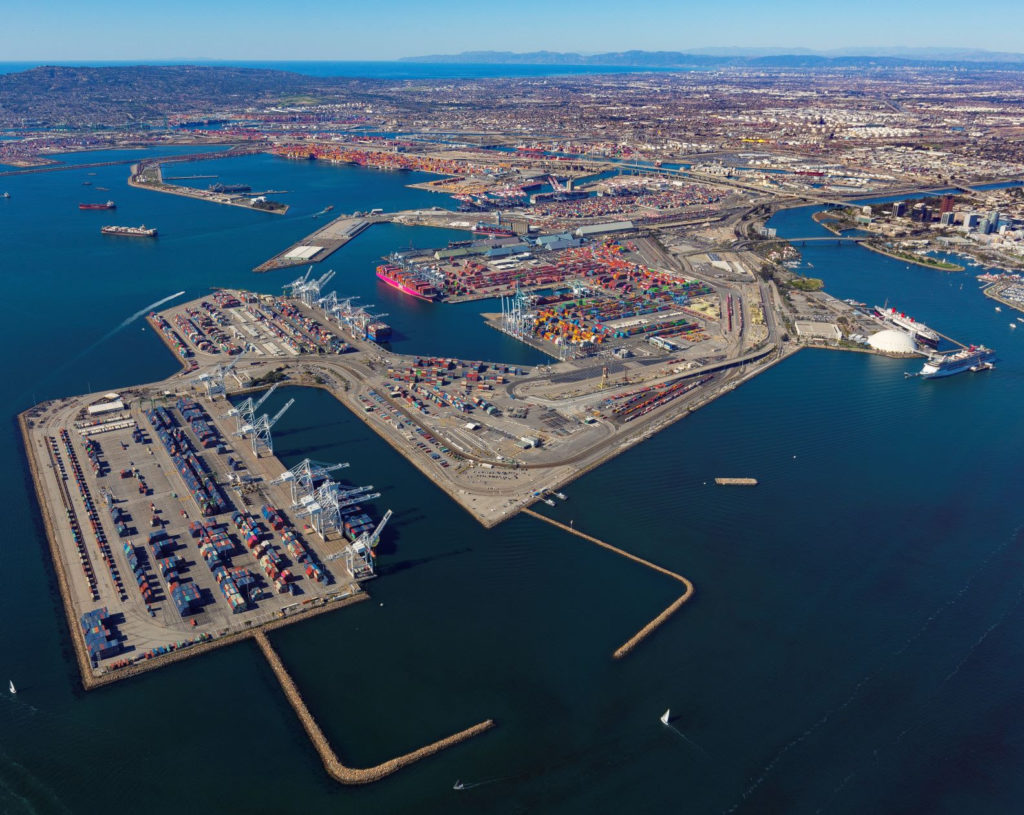
The Long Beach Board of Harbor Commissioners has approved a $760 million budget for the Port of Long Beach for the 2025 fiscal year, establishing a plan to fund new capital improvements in rail, zero-emissions, and other infrastructure. Later this year, the budget will be sent for approval to the Long Beach City Council. It includes a record $25.8 million transfer to the City’s Tidelands Operating Fund, which supports quality-of-life projects along Long Beach’s 7-mile coastline that have improved shoreline safety, cleanliness, water quality, facilities, and other amenities. The Port’s budgeted spending for the 2025 fiscal year, which begins Oct. 1, is 19.5% higher than the budget adopted last year. The increase is largely due to infrastructure projects like the Pier B On-Dock Rail Support Facility, which breaks ground this year, and the proposed Pier Wind. If approved, Pier Wind would be the nation’s largest facility specifically designed to assemble offshore wind turbines. Operating revenue is estimated to be 6.8% higher than last year’s budget. “This budget reflects our values, balancing serving as an economic engine for our city and region and growing responsibly while limiting environmental impacts,” said Port of Long Beach CEO Mario Cordero. “We are optimistic about the year ahead and this spending plan builds our competitive advantages for the green future.” “Because trade, construction and tourism support 51,000 jobs in Long Beach – or one in five jobs – it’s important we stay focused on attracting business, building for the future and moving cargo sustainably,” said Harbor Commission President Bobby Olvera Jr. “This budget advances these goals by leveraging our stable financial strength as a top gateway for global commerce.” Next year’s proposed capital budget totals $368.3 million, 47.2% higher than the prior year. Of the sum, $204.9 million is for the Pier B project, which will break ground this summer. Pier B will shift more cargo to “on-dock rail,” where containers are taken to and from marine terminals by trains. Moving cargo by on-dock rail is cleaner and more efficient, as it reduces truck traffic. No cargo trucks would visit the facility. The Port of Long Beach maintains one of the most comprehensive seaport infrastructure programs in the nation. Also included in the budget is approximately $25 million in Clean Truck Fund subsidies to support the transition of the heavy-duty truck fleet to zero emissions. The Port of Long Beach has twin goals of a zero-emissions cargo-handling fleet by 2030 and zero-emissions trucking by 2035. Additionally, during the Board’s action, the amount allocated for the Community Sponsorship Program was increased from $2 million to $3 million. The sponsorship program helps the Port of Long Beach engage with and inform local community members about Port operations and initiatives. As the City’s Harbor Department, the Port of Long Beach does not use tax revenue to support operations.
Episode 494: Supply Chain orchestration with Brian Gaunt of DHL
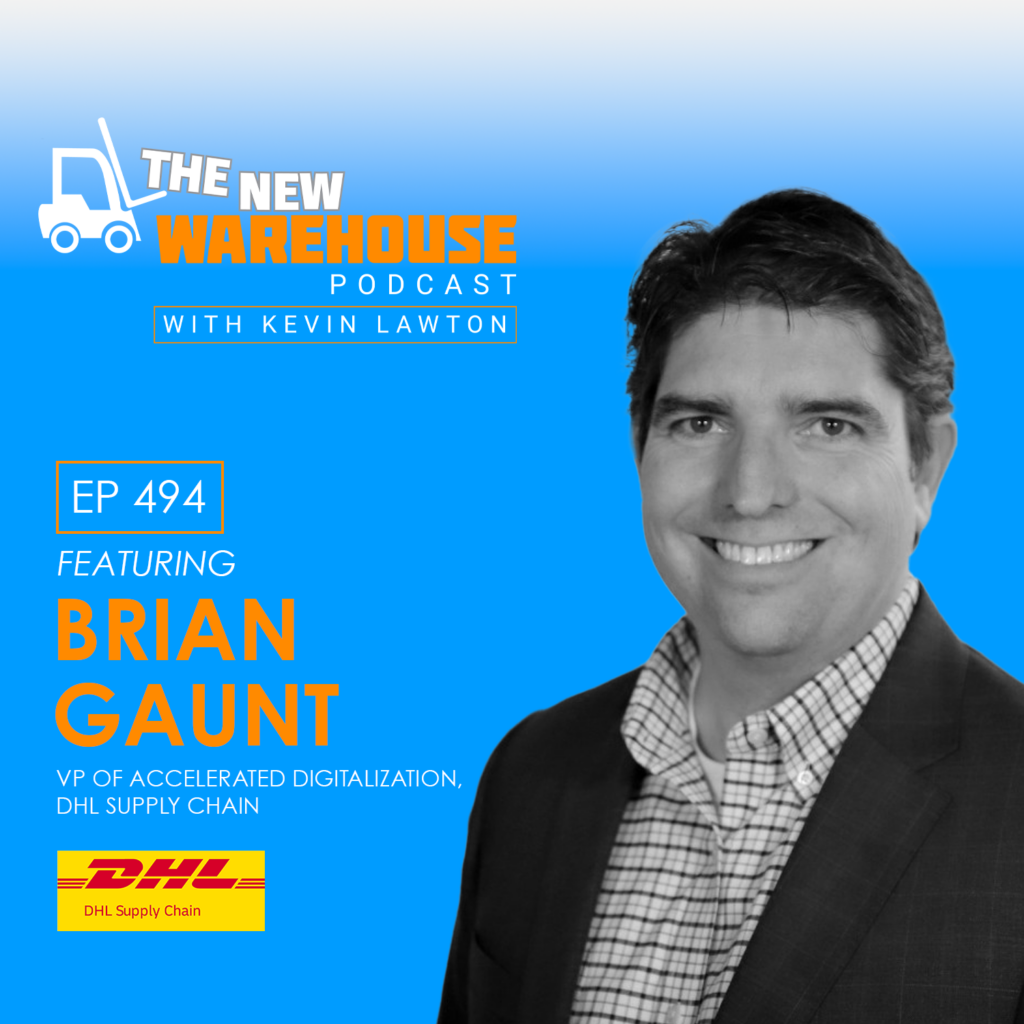
Supply chain orchestration is today’s topic on The New Warehouse Podcast. Recorded live at Manifest, Kevin sits down with Brian Gaunt, the VP of Accelerated Digitalization at DHL Supply Chain. In addition to discussing supply chain orchestration, the conversation delves into emerging trends in automation and AI and the critical role of data analytics in optimizing warehouse operations. Brian shares valuable insights on how DHL navigates these advancements and what the future holds for the logistics giant. The Power of Data in Orchestrating Supply Chains Brian Gaunt emphasizes the pivotal role of data in supply chain orchestration. “Everything we touch generates output,” he explains, highlighting the importance of effectively capturing and utilizing this data. “One of the great things about automation is it’s really good at tracking what it does. So, we can get very predictable productivity results coming out of those types of solutions.” DHL leverages data from both manual processes and automated systems to optimize warehouse operations, enabling better forecasting and resource allocation. DHL can perform predictive analysis by integrating machine learning solutions, enhancing overall efficiency and productivity. Warehouse Orchestration Warehouse orchestration at DHL involves harmonizing both automated and manual processes to create a seamless workflow. Brian discusses how advanced robotics and data analytics contribute to this orchestration. “Orchestration overall or supply chain orchestration, as we look at it, is really optimizing that full end-to-end visibility from the point of manufacture to those raw materials or finished products arriving from the manufacturer into the warehouse.” Providing visibility into every aspect of the supply chain improves productivity and enhances associates’ working conditions by automating strenuous tasks. The Future of Supply Chain Orchestration Brian says DHL will focus on refining data utilization and incorporating new automation solutions to enhance supply chain orchestration further. Brian notes that staying on top of technological advancements is crucial for maintaining efficiency and improving worker satisfaction. “Robotics solutions do a lot of the tasks that the person really doesn’t want to do. Nobody wants to unload a box in a hot trailer or cold trailer.” This strategy can create more appealing and safer working environments by continually integrating innovative solutions, ultimately driving better performance and customer satisfaction. “If we’re able to put a piece of equipment in there to do that and allow that person to do something else, it’s a much better fit.” Key Takeaways on Supply Chain Orchestration Data Utilization: Effective data capture and analysis are essential for optimizing supply chain operations. Automation and Robotics: Integrating advanced automation solutions improves productivity and working conditions. Continuous Innovation: Staying updated with technological advancements ensures efficiency and enhances employee satisfaction. The New Warehouse Podcast Episode 494: Supply Chain Orchestration with Brian Gaunt of DHL
H&E opens new branch in the Myrtle Beach area
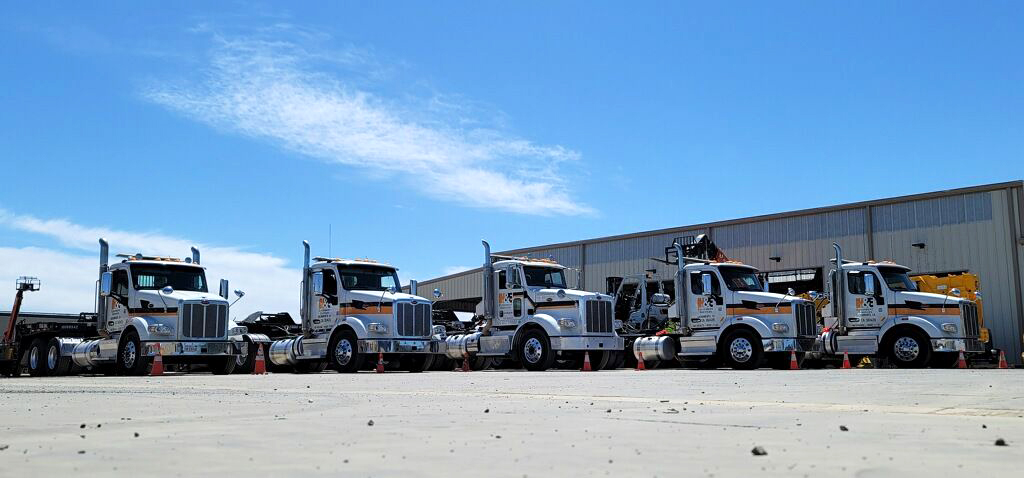
Effective June 17, 2024, H&E Rentals (H&E) has announced the opening of its Myrtle Beach branch, the fourth general rental equipment location in the state of South Carolina. Since the second quarter of 2023, H&E has opened 19 new branches across the country and acquired nine others. The facility is located at 695 Century Circle, Conway, SC 29526-8278, phone 843 733-4800. It includes a fully fenced yard area, offices, and a repair shop and carries a variety of construction and general industrial equipment. “H&E has extended its coverage along the South Carolina coast, from Georgetown up to the North Carolina state line, and then inland to I-95 from Dillon to Manning. We can easily reach all points in between with close proximity to state highways 501, 701, and 368 and to major roadways that branch off in all directions,” says Branch Manager Joe Pannunzio. “Our location strategically bridges the gap between our existing Charleston, South Carolina, and Wilmington, North Carolina, branches, so we are able to help both new and existing customers secure the right equipment for their projects.” The Myrtle Beach branch specializes in the rental of aerial lifts, earthmoving equipment, telescopic forklifts, compaction equipment, generators, light towers, compressors, and more and represents the following manufacturers: Allmand, Atlas Copco, Bomag, Case, Club Car, Cushman, Doosan, Gehl, Generac Mobile, Genie, Hamm, Hilti, Husqvarna, JCB, JLG, John Deere, Kobelco, Kubota, LayMor, Ledwell, Lincoln Electric, Link-Belt Excavators, MEC, Miller, Multiquip, Polaris, Sany, Skyjack, SkyTrak, Sullair, Sullivan-Palatek, Tag, Towmaster, Unicarriers, Wacker Neuson, Yanmar, and others.
Women In Trucking Association announces continued Gold Partnership with Bridgestone Americas
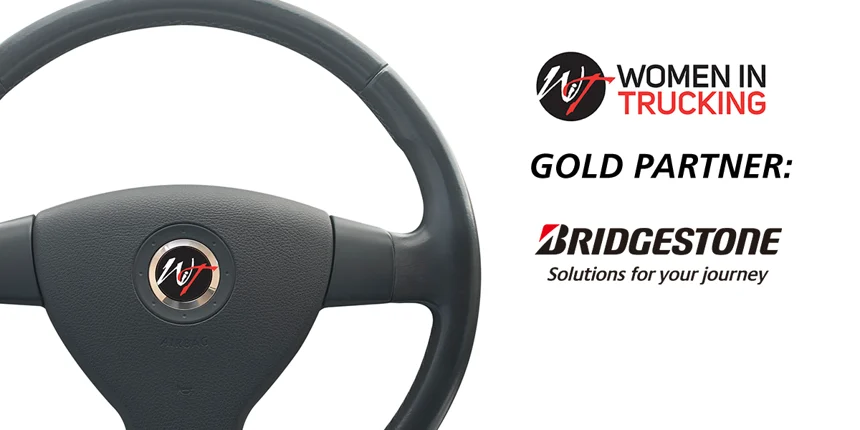
The Women In Trucking Association (WIT) has announced that Bridgestone Americas (Bridgestone) has renewed its Gold Level Partnership strengthening its mission to encourage the employment of women in the industry, promote their accomplishments, and minimize obstacles faced by women working in trucking. In 2022 and 2023, the company was a Platinum Sponsor of WIT’s Accelerate! Conference & Expo held in Dallas, TX. LaTres Jarrett, Executive Director of Customer Loyalty and Retention Marketing for Bridgestone Americas, serves on the WIT board of directors. Samantha McCracken, Strategic Account Leader for Bridgestone Americas, is additionally a member of the WIT Content Committee. “Bridgestone is committed to making positive and lasting impacts in our communities and industries to help build a better future,” said Jarrett. “What really matters is fostering an inclusive environment where women’s achievements are recognized and their potential is fully realized. Continuing our partnership with Women In Trucking reaffirms our commitment to empowering and celebrating diverse talent – especially women – in our industry.” “We’re grateful for Bridgestone’s commitment to creating a more gender-diverse culture in transportation,” said Jennifer Hedrick, WIT president and CEO. WIT’s valuable partnerships with companies such as Bridgestone allow us to enhance engagement and opportunity within the trucking profession.”
IFOY Award 2024 winners announced
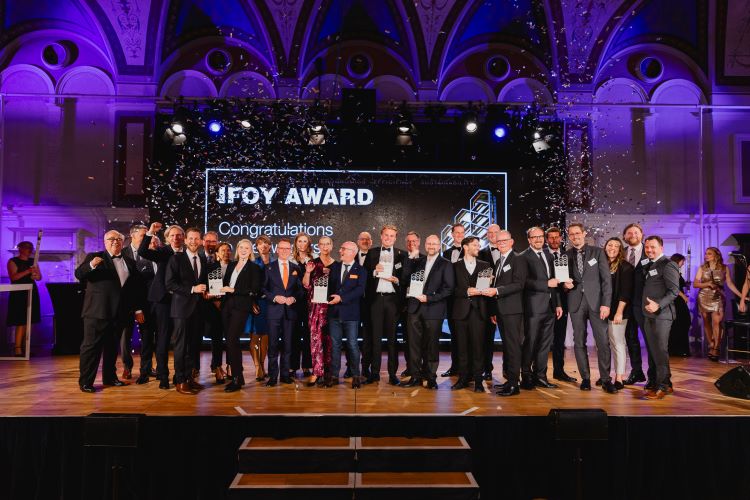
Jungheinrich, RAVAS EUROPE, SAFELOG with Mercedes, SSI Schäfer, and STILL have been announced as winners of the IFOY Award 2024. The International Intralogistics and Forklift Truck of the Year (IFOY) Award recognizes the year’s best intralogistics products and solutions. The international jury of the 2024 global intralogistics competition nominated a total of 16 products and solutions from 15 companies in seven categories and voted on the winners following a three-stage audit. Brightpick, Brightpick Autopicker – Start-up of the Year The IFOY Spin-off Award “Start-up of the Year” goes to Brightpick for the autonomous, mobile picking robot Brightpick Autopicker. The international jury selected the AI-based 2-in-1 robot as the best new development in this market segment. The Autopicker from Brightpick, a start-up founded in Bratislava in 2021, is the world’s first autonomous mobile picking robot. Brightpick worked closely with its sister company Photoneo on its development. Same founders, similar technology: 3D vision, robotics, AI, and software for a functioning warehouse execution system. Autopicker installations with a total of 70 devices can now be found in the USA (headquarters), Germany, Slovakia, and the Czech Republic. What’s new about this type of picking: the Autopicker pulls the source tote from the standard rack, which does not require rollers or rails. As the robot moves to the next storage location, it picks the target tote like a human picker, taking the picked tote to the next storage location. There must therefore always be an empty space available in which the bin can be placed. The autopicker works with a trolley that independently picks and consolidates orders–without human intervention. In technical terms, Autopicker uses a patented design with two bins for this process to pull storage bins (storage tote) from the shelf, pick the items using a robotic gripper arm and place them in an order tote. The big difference to other fulfillment robots is that the autopicker does not have to go to central picking stations. Another advantage is its versatility, as it can be used not only for picking in the rack aisle, but also for other tasks such as pallet picking, warehouse replenishment, dynamic storage, order consolidation, temporary storage and shipping. And if human dexterity is required for picking, for example, the autopicker can also be used for normal goods-to-person picking. The robots can also reliably pick a wide range of products, including chilled and non-chilled food, pharmaceuticals, medical devices, packaged goods, cosmetics, electronics and textiles in plastic packaging. The entire autopicker fleet and the fulfilment process in the warehouse are orchestrated and optimised by the Brightpick intuition software. IFOY Verdict The fact that picking takes place while a robot is moving from one location to another without the robot having to return to a “base station” is new and revolutionary. Although an exact measurement during the live assessment at Test Days was not possible, a higher throughput rate and thus a considerable time saving could be confirmed. This leads to a reduction in the number of robots required, which has a positive effect on the return on investment and noticeably reduces picking costs. According to Brightpick, the savings in labour costs are significantly higher than with traditional goods-to-person stations, with higher throughput, easier installation and lower costs. The company claims that picking costs have been halved. Click here for the original test report, IFOY Innovation Check and pictures Jungheinrich, EJC 112i – Warehouse Truck Highlifter of the Year The IFOY Award 2024 in the “Warehouse Truck Highlifter” category goes to the EJC 112i from Jungheinrich. The international jury voted the compact highlifter the best new product in this category. With its compact design and outstanding performance, the EJC 112i sets a new standard in the entry-level segment and clearly stands out from the competition. Especially in small warehouses with narrow aisles, the high residual capacity enables optimum space utilisation. Together with the small turning radius and user-friendly operation, it is clear why the EJC 112i makes day-to-day work easier for every operator. The EJC 112i is more than just a further development of its predecessor, but offers an even more compact and manoeuvrable solution thanks to the integrated lithium-ion battery. When designing the truck, Jungheinrich paid particular attention to the high energy density of lithium-ion technology, which stores the same amount of energy in significantly smaller modules. This not only saves space, but also opens up new possibilities in terms of truck size. The result is immediately apparent: the EJC 112i has a smaller L2 size, offers a good view of the fork and has a low overall height. The impressively small turning circle makes manoeuvring effortless, even in tight spaces. To compensate for the shorter length and lower weight of the lithium-ion battery, the truck has been completely redesigned. The mast profiles have been widened in the side view and the steering arms have been reinforced. The entire chassis is balanced to ensure optimum force equalisation. The result is immediately noticeable when the load is lifted. At the maximum 1,200 kg, the EJC 112i does not move and effortlessly lifts up to 2,900 mm. Up to 3,800 mm, the truck picks up 830 kg and at the maximum lift height of 4,700 mm, 650 kg still remains, all with a load distance of 600 mm. The increased residual capacity of the EJC 112i optimises space utilisation and minimises floor space requirements, as heavier loads can be stored in higher racks. The IFOY test confirms that the EJC 112i offers the best performance in its class, with exceptionally high lifting and lowering speeds and efficient performance. Thanks to the more powerful pump motor and a better balance between pump power and lift cylinder, the new truck lifts significantly faster than its predecessor and well above the average in this class. The driving and acceleration speeds have remained almost the same. In the most powerful setting, P3, the EJC 112i achieves a comfortable, even speed of 6.05 km/h with and without a load. The battery capacity and the power of the charger
Episode 493: Automation & Mobility at Momentum 2024 with Agility Robotics & Manhattan Associates
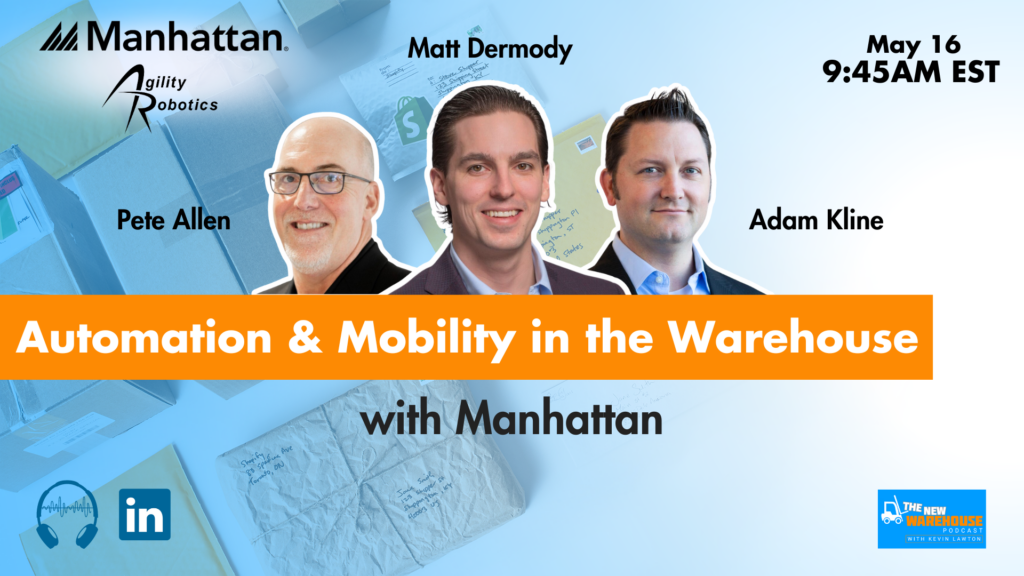
In this engaging session from Momentum 2024, I was joined by a panel consisting of Adam Kline and Matt Dermody from Manhattan Associates and Pete Allen from Agility Robotics to discuss the current state of automation and mobility in the warehouse industry. The discussion highlights advancements in robot technology, particularly focused on humanoid robots, their practical applications, user experience considerations in warehousing, and the future landscape of automation. The Current State of Automation There has been a huge uptick in automation solutions coming to market in the warehouse space and the panel agrees that labor challenges and finding ways to augment labor are one of the biggest driving factors for this uptick. Adam even mentions how just 5 or 6 years ago at Momentum you would not see robotic solutions at the show but this year there was a presence and most notably the presence of Digit from Agility Robotics, a humanoid robot. As we look at the many options that are on the market, Matt points out how there is a variation in form factors that are allowing for different processes to now be automated and how AI is allowing for more to be done as well. Humanoids in the Warehouse When it comes to form factors of robotic solutions, humanoids are certainly garnering a lot of attention. The combination of the humanoid form factor and AI allows for rapid training opportunities that can make a humanoid robot more flexible in what processes it can utilize. Agility Robotics is pushing warehouse automation forward with its humanoid option, Digit, and has firmly put its flag in the sand on being the warehouse humanoid robot. This has been further solidified through their partnership with Manhattan which allows them to integrate with the Manhattan Active Warehouse Management platform and help Manhattan’s users easily bring humanoid robots into their workflows. As of right now, these robots are just moving totes in different ways but Pete discusses the evolution of them and their pursuit to make them into collaborative robots that can work right beside you. The Future of Automation Without a doubt, automation is here to stay and will continue to evolve in the coming years. Manhattan is positioning themselves to be able to support these advancements and make utilizing these solutions easier for their end users. The most interesting concept from this conversation came from Matt who describes the future of robotics having a virtual gym where AI based robotics can easily go in to learn a new task. In this virtual gym the robot will be able to replicate the processes at a rapid rate allowing for new tasks to quickly be learned. Through these advancements, robots will be able to become more flexible and adaptable to new environments or tasks. Key Takeaways Undoubtedly, labor challenges are driving the uptick in automation solutions hitting the market and giving reason for these solutions to continue to be present in our industry. Humanoids are a fairly new form factor to the robotics space and Agility Robotics is focusing on the warehouse specifically by positioning themselves with partnerships like the one with Manhattan Associates, Zion Solutions Group and GXO. To help advance the development of robots, AI is playing a large part in how quickly these robots can and will be able to adapt to their environment and have additional flexibility to focus on more than one task. The New Warehouse Podcast EP 493: Automation & Mobility at Momentum 2024 with Agility Robotics & Manhattan Associates
Port of Long Beach trade slows in May
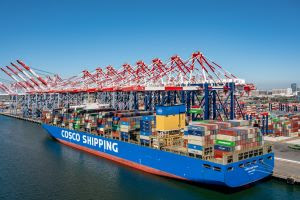
Cargo declines amid canceled voyages, shifting trade routes Shifting trade routes and canceled voyages led to a decline in cargo at the Port of Long Beach in May. Dockworkers and terminal operators moved 695,937 twenty-foot equivalent units last month, down 8.2% from May 2023. Imports slid 4.5% to 345,271 TEUs and exports decreased 21.1% to 100,885 TEUs. Empty containers moving through the Port declined 7% to 249,782 TEUs. The Port has moved 3,449,181 TEUs through the first five months of 2024 and is still up 10% from the same period in 2023. “I am confident we will see additional cargo as we work with industry partners to rebuild our market share in this increasingly competitive environment,” said Port of Long Beach CEO Mario Cordero. “Looking ahead, I anticipate a moderate increase in cargo as we move into summer and we recapture business by delivering the top-notch customer service that makes us the Port of Choice.” “Our longshore labor, facilities, and industry partners are ready for cargo growth as we head into the shipping season for back-to-school and beyond, thanks to our ability to move goods reliably, quickly, and sustainably.” said Long Beach Harbor Commission President Bobby Olvera Jr. “Over the long term, the San Pedro Bay ports complex will continue to be a strategic and sustainable gateway for trans-Pacific trade.” For complete cargo numbers, visit polb.com/statistics.
PLASTICS releases new Recycling is Real Video featuring Printpack in Atlanta, GA

The Plastics Industry Association (PLASTICS) has unveiled a new video as part of the Recycling is Real advocacy campaign, dedicated to promoting and defending plastic recycling in America. This video highlights the efforts taking place at Printpack’s facility in Atlanta, Georgia where recycled materials, created through advanced recycling technologies, are remade into packaging used for everyday products. PLASTICS’ Recycling is Real campaign, which began in September of 2023, has featured Ultra-Poly, Placon, Novolex, MAAG, Niagara Bottling, Epsilyte, Amcor, Envision Plastics, PolyQuest, Nexus Circular , and an advanced recycling partnership among TenCate, Cyclyx International and ExxonMobil. “Plastic recycling is very real, and Printpack uses materials through advanced recycling to make packaging for products consumers can find right on the grocery store shelf,” said PLASTICS’ President and CEO Matt Seaholm. “The Recycling is Real campaign highlights the people of our industry across America who work to recycle valuable materials every single day. We will continue to show the public and lawmakers that recycling is undeniable, and a feasible and economical way to achieve a more circular economy.” “At Printpack, we are committed to advancing a circular economy through the use of recycled and recyclable plastic materials in our packaging solutions,” said Tom Seidel, Director of Sustainability at Printpack. “Our collaboration with advanced recycling partners allows us to give new life to plastic waste by transforming it back into high-quality packaging that meets the needs of our customers and consumers. We are proud to be featured in the Recycling is Real campaign to showcase how recycling and sustainability are at the core of Printpack’s mission.” Click here to view Recycling is Real featuring Printpack The Recycling is Real campaign provides content to help elected officials and policymakers understand that recycling is a vital link of the sustainability and circularity chain, enabling them to make more well-informed decisions about recycling resources for their constituents. The Recycling is Real campaign was also created in an effort to put an end to false narratives claiming that recycling doesn’t happen or is a “myth.” Recycling has come under attack from those who wish to reduce or eliminate the production of plastic altogether. Recycling is Real shows how recycling happens, where it happens and introduces the people who make it happen. Printpack is a leading manufacturer of sustainable flexible and specialty rigid packaging with over 60 years of experience helping brands improve retail visibility, heighten brand awareness, and capture market share. Printpack combines unique insights into consumer preference with advanced technological capabilities to convert packaging concepts into reality. Headquartered in Atlanta, GA, Printpack is a privately held company that believes cooperation and integrity result in innovation. To learn more, call 404 460-7000 or visit printpack.com.
Bridgestone laying off 118 workers in Iowa
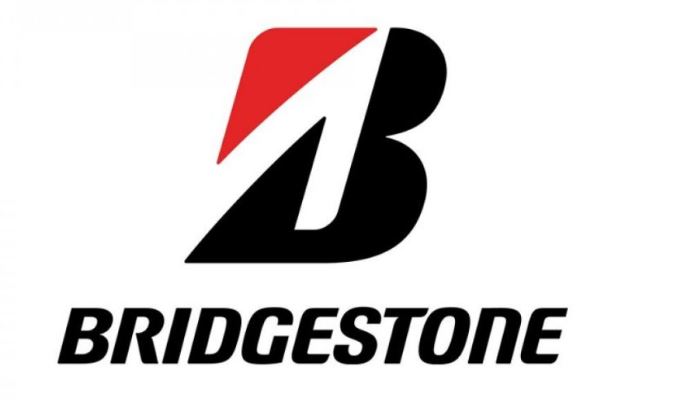
Bridgestone contends with falling demand across multiple continents Bridgestone Americas will be laying off 118 workers at its Des Moines, Iowa plant as demand for their agricultural tire business according to a company statement. This is due to farmers cutting back on equipment and other discretionary spending as they delay planting due to weather concerns. According to an Iowa Worker Adjustment and Retraining Notification Act note, Bridgestone’s layoff will be taking effect on July 5th. The United Steelworkers Union Local 310L confirmed this and said it will impact those who have two years or less of seniority at the factory. The factory opened in 1945 and produces tires for agriculture, construction, forestry, and off-road uses.
JCB breaks ground on a new $500 million North American factory
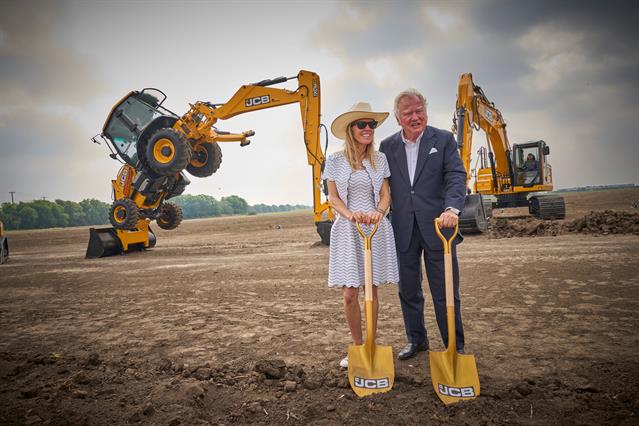
On June 4th, JCB began work on a new $500 million factory in San Antonio, Texas – the biggest investment in the company’s history. An official groundbreaking ceremony at the site marked the beginning of construction, where The Hon. Alice Bamford, the daughter of company Chairman Anthony Bamford, as she turned the first shovelful of dirt on the property. Work on the 720,000 sq. ft. (67,000m²) factory is underway on the 400-acre site. It will be the company’s second-largest plant, rivaled only by JCB’s world headquarters in Rocester, Staffordshire, England, and create 1,500 new jobs over five years. The factory will make Loadall telescopic handlers and aerial access equipment, with production scheduled to start in 2026. The factory will also have the capacity to expand and build other products in the future. Chairman Lord Bamford said: “Construction equipment manufacturers sell more than 300,000 machines every year in North America, making it the single largest market in the world. JCB has been growing its share of this important market steadily over the past few years and the time is now right to invest in our manufacturing capacity in North America, where we already have one factory.” “JCB really has come a considerable way since we sold our first machine here 60 years ago and it gives me immense pleasure to see how our business has grown in North America. Today really is a milestone day in the history of our family company,” Bamford says. “Texas was this year named as The Best State for Business for a record-breaking 20th year, and I am proud to welcome JCB as the newest business to call our great state home,” said Governor Greg Abbott. “Today’s groundbreaking marks a major milestone in JCB’s journey that will create 1,500 good-paying jobs for hardworking Texans in Bexar County and bring hundreds of millions of new capital investment to San Antonio and beyond. ‘Made in Texas’ is truly a powerful global brand, and I look forward to celebrating JCB’s continuing success as we work together to build a bigger, better Texas for decades to come.” JCB CEO Graeme Macdonald said: “JCB’s business in North America has made tremendous progress in the past few years and the opportunity for growth here is vast. This record investment gives us a fantastic opportunity to build on our success and we look forward to the completion of this great new facility.” Richard Fox-Marrs, President & CEO of JCB North America, said: “The Loadall telescopic handler is JCB’s biggest selling product in North America and it is also the single largest market for aerial access equipment worldwide, and therefore, it makes great sense to build these two ranges here.” “Texas is an obvious choice for our new North American manufacturing facility, not least because the state is the largest consumer of construction equipment in the USA. San Antonio is also the logical choice as a location for our new factory because of its central location, proximity to the supply chain and great local labor force. We are really excited about JCB’s new San Antonio factory and for the future of our business in North America,” says Fox-Marrs. JCB sold its first machine in North America in 1964 and opened its first US manufacturing plant in 2001 in Savannah, Georgia, which employs 1,000 people. The new facility will manufacture machines for customers specifically in North America. JCB employs 19,000 people globally and has 22 factories around the world, including 11 in the UK, seven in India, and others in Brazil and China. The company will mark its 80th anniversary in 2025.
Keeping sustainability on track: it needs the right tire
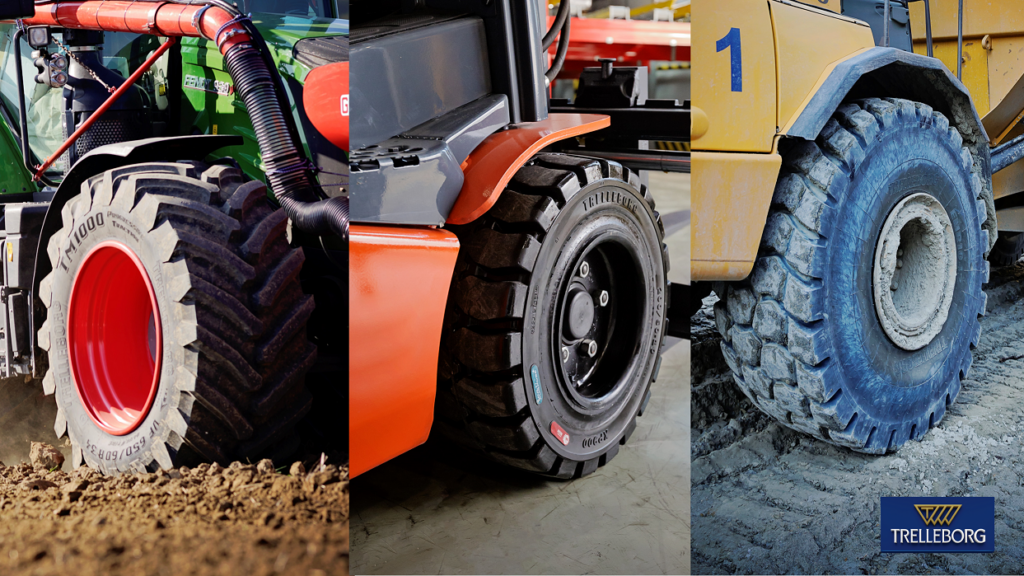
It’s time to rethink the way we make tires, and the off-highway segment is no exception to this global imperative, driven by sustainability in the first place. The escalating costs of petroleum-based rubber, coupled with manufacturers’ demand for materials that boost operational efficiency and cut long-term expenses, have emerged as potent motivators, while regulatory bodies have also entered the fray, underlining the necessity for eco-friendly solutions in tire production and recycling processes. New ranges of innovative products, engineered to optimize performance while minimizing environmental footprints, are consequently making their debut in the market, shining as beacons of sustainability; and, among them, Trelleborg Tires stands out as a compelling story to be shared. Cutting-edge tire technology as a sustainability engine While the sustainable impact of tires has been frequently overlooked, Trelleborg Tires has been making a name for itself through a revolutionary approach to materials sourcing and manufacturing processes. By harnessing renewable resources and employing advanced production techniques, Trelleborg Tires is nowadays capable of delivering tire solutions that not only perform exceptionally but also reduce carbon emissions and environmental footprint significantly. For instance, the TM1 ECO POWER tire, engineered for both electric and fuel-powered tractors, incorporates 65% bio-based and recycled materials, offering superior performance at the highest environmental standards, and ultimately promoting responsible sourcing and manufacturing practices. Similarly, the XP1000 advanced treads for material handling equipment are crafted from high-performance compounds made with recycled materials, ensuring longevity and significant emissions reduction, also thanks to an exclusive Pit Stop Line that minimizes waste. These unique features contribute to a reduction in carbon emissions on the order of 110 tons of CO2, equivalent to the pollution generated by nearly 800,000 kilometers of driving. Eventually in the construction segment, the EMR range is specifically designed for loader, dumper, and grader applications, with a robust carcass to support eventual retreading. Tires that keep you going, durable and efficient design for maximized performances Beyond the tire composition, Trelleborg Tires has prioritized fuel and energetic efficiency as a key feature of its sustainable tire offerings, providing solutions that enable vehicle operators to not only save money, but also increase productivity and contribute to a greener and more sustainable future. Design is key: thanks to its tread central rib, the TM1 ECO POWER has proven extremely low rolling resistance which enables low fuel consumption and extended battery usage, proving an astounding 47% improvement versus a premium standard tire. In the same way, the advanced construction and compound formula of the XP1000 provides for extra battery power for electric forklifts and reduces fuel consumption for internal combustion truck; and the strong radial carcass and state of the art compound of the EMR1030 tire assure a long operational life made of low fuel consumption and equal load distribution. The man behind the wheel comes first A comfortable driving experience is paramount for operators’ safety and efficiency. By reducing accidents, it becomes a key sustainable feature for tires as well as sustainable asset for companies. Trelleborg Tires has recognized this. For example, the TM1 ECO POWER offers from 5% to 10% less deflection compared to the premium standard agricultural tire, leading to reduced deformation under load, and offering improved stability during both transportation and daily farm operations, while the XP1000 middle cushion layer absorbs road roughness, minimizing vibrations while maximizing operator comfort and safety. Ultimately, the multi surface tread design of the EMR series delivers control and perfect grip when it’s needed the most, whether on sand, rock, gravel, or soil. Through all these examples, Trelleborg’s sustainable tire innovations represent a paradigm shift in the off-highway tire industry, where green design and performance converge to shape the future of the segment. By championing sustainability at every stage of the tire lifecycle, Trelleborg Tires is not only redefining industry standards but also reaffirming its commitment to creating a more sustainable world for generations to come.
AAR reports Weekly Rail Traffic for the week ending June 8, 2024
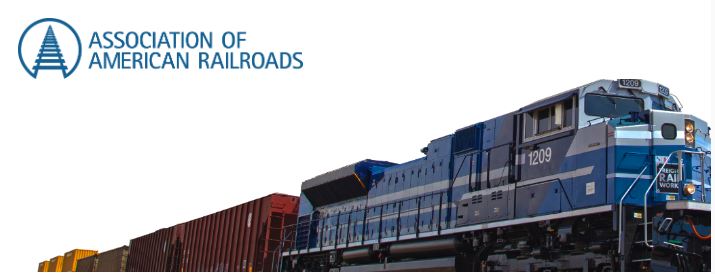
The Association of American Railroads (AAR) has reported U.S. rail traffic for the week ending June 8, 2024. For this week, total U.S. weekly rail traffic was 489,916 carloads and intermodal units, up 4.1 percent compared with the same week last year. Total carloads for the week ending June 8 were 218,234 carloads, down 4.4 percent compared with the same week in 2023, while U.S. weekly intermodal volume was 271,682 containers and trailers, up 12.2 percent compared to 2023. Six of the 10 carload commodity groups posted an increase compared with the same week in 2023. They included grain, up 2,350 carloads, to 18,912; petroleum and petroleum products, up 1,836 carloads, to 11,102; and farm products excl. grain, and food, up 1,556 carloads, to 17,436. Commodity groups that posted decreases compared with the same week in 2023 included coal, down 10,298 carloads, to 54,797; nonmetallic minerals, down 3,999 carloads, to 30,879; and metallic ores and metals, down 1,903 carloads, to 19,224. For the first 23 weeks of 2024, U.S. railroads reported a cumulative volume of 4,901,744 carloads, down 5.0 percent from the same point last year; and 5,840,146 intermodal units, up 8.8 percent from last year. Total combined U.S. traffic for the first 23 weeks of 2024 was 10,741,890 carloads and intermodal units, an increase of 2.0 percent compared to last year. North American rail volume for the week ending June 8, 2024, on 10 reporting U.S., Canadian, and Mexican railroads totaled 325,376 carloads, down 2.6 percent compared with the same week last year, and 354,865 intermodal units, up 8.3 percent compared with last year. Total combined weekly rail traffic in North America was 680,241 carloads and intermodal units, up 2.8 percent. North American rail volume for the first 23 weeks of 2024 was 15,127,364 carloads and intermodal units, up 2.0 percent compared with 2023. Canadian railroads reported 89,664 carloads for the week, up 3.7 percent, and 70,833 intermodal units, down 2.2 percent compared with the same week in 2023. For the first 23 weeks of 2024, Canadian railroads reported a cumulative rail traffic volume of 3,705,477 carloads, containers, and trailers, up 0.7 percent. Mexican railroads reported 17,478 carloads for the week, down 10.0 percent compared with the same week last year, and 12,350 intermodal units, down 4.7 percent. Cumulative volume on Mexican railroads for the first 23 weeks of 2024 was 679,997 carloads and intermodal containers and trailers, up 8.6 percent from the same point last year. To view the weekly US rail traffic chart, click here.
US Cutting Tool Orders totaled $214.7 Million in April 2024, Raising Year-to-Date total nearly 5% over 2023
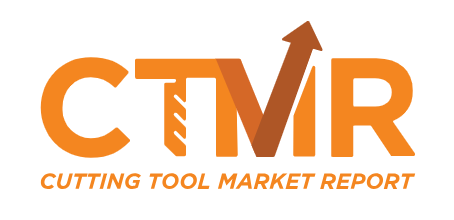
Shipments of cutting tools, measured by the Cutting Tool Market Report compiled in a collaboration between AMT – The Association For Manufacturing Technology and the U.S. Cutting Tool Institute (USCTI), reached $214.7 million in April 2024. Orders increased by 1.1% over March 2024 and grew by 13% over April 2023. Year-to-date shipments totaled $846.1 million, nearly 5% above shipments made in the first four months of 2023. “While April 2024 shipping numbers do show an increase from those of 2023, caution continues due to many uncertainties ahead for the remainder of 2024,” said Steve Boyer, president of USCTI. “Uneven growth and turbulence have continued to impact cutting tool orders through the first quarter of 2024, and there have been some downgrades in expected needs from the aerospace sector, leading to stagnation in new orders.” Costikyan Jarvis, president of Jarvis Cutting Tools, expanded on Boyer’s analysis, saying, “The industrial sector of the economy continues to move sideways. While the value of cutting tool shipments is up about 5% over last year, the flatter growth rate in units shows that inflationary pressures are still present.” Looking forward, Jarvis said: “There are two big ‘ifs’ that could result in improved demand during the second half of the year. The first is that the overall production remains consistent. The second is if Boeing can start ramping up production of the 737 to the FAA limit of 38 per month. If those two things can happen, the cutting tool industry might be positioned for growth in both revenue and volumes.” The Cutting Tool Market Report is jointly compiled by AMT and USCTI, two trade associations representing the development, production, and distribution of cutting tool technology and products. It provides a monthly statement on U.S. manufacturers’ consumption of the primary consumable in manufacturing – the cutting tool. Analysis of cutting tool consumption is a leading indicator of both upturns and downturns in U.S. manufacturing activity, as it is a true measure of actual production levels. Historical data for the Cutting Tool Market Report is available dating back to January 2012. This collaboration of AMT and USCTI is the first step in the two associations working together to promote and support U.S.-based manufacturers of cutting tool technology. The graph below includes the 12-month moving average for the durable goods shipments and cutting tool orders. These values are calculated by taking the average of the most recent 12 months and plotting them over time. AMT – The Association For Manufacturing Technology represents and promotes U.S.-based manufacturing technology and its members – those who design, build, sell, and service the continuously evolving technology that lies at the heart of manufacturing. Founded in 1902 and based in Virginia, the association specializes in providing targeted business assistance, extensive global support, and business intelligence systems and analysis. AMT is the voice that communicates the importance of policies and programs that encourage research and innovation, and the development of educational initiatives to create tomorrow’s Smartforce. AMT owns and manages IMTS – The International Manufacturing Technology Show, which is the premier manufacturing technology event in North America. The United States Cutting Tool Institute (USCTI) was formed in 1988 and resulted from a merger of the two national associations representing the cutting tool manufacturing industry. USCTI works to represent, promote, and expand the U.S. cutting tool industry and to promote the benefits of buying American-made cutting tools manufactured by its members. The Institute recently expanded its by-laws to include any North American manufacturer and/or remanufacturer of cutting tools, as well as post-fabrication tool surface treatment providers. Members, which number over 80, belong to seven product divisions: Carbide Tooling, Drill & Reamer, Milling Cutter, PCD & PCBN, Tap & Die, Tool Holder and All Other Tooling. A wide range of activities includes a comprehensive statistics program, human resources surveys and forums, development of product specifications and standards, and semi-annual meetings to share ideas and receive information on key industry trends.
Matrix appoints Chris Shay as South-Central Regional Sales Manager
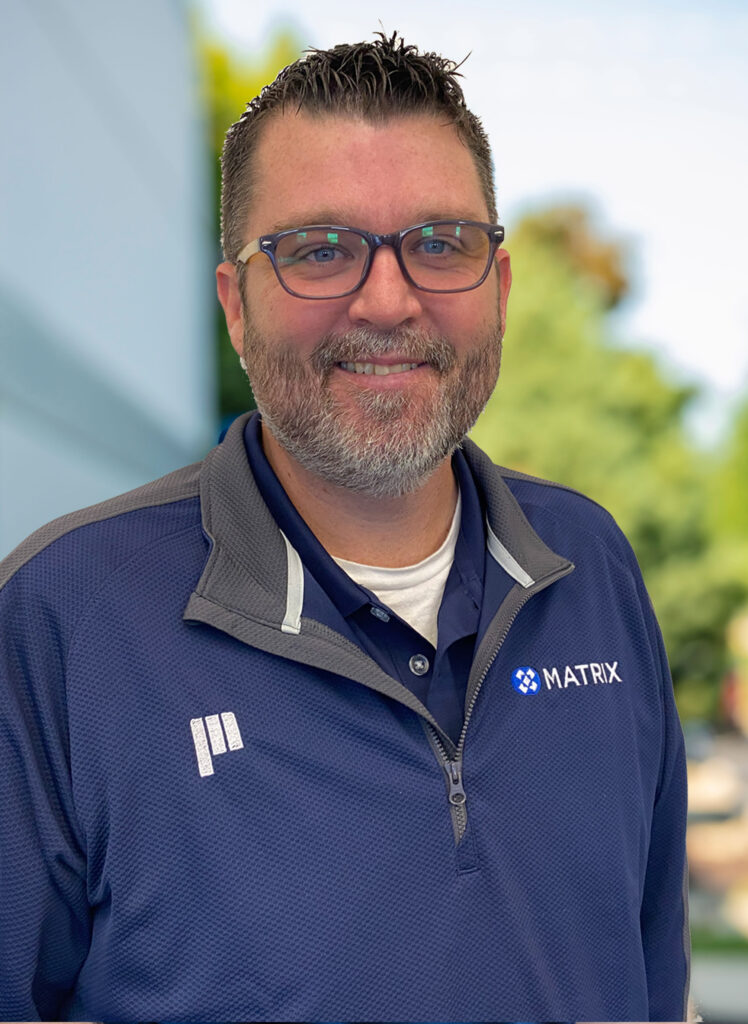
Chris Shay is their point of contact for Matrix vertical form fill and seal packaging customers in the South-Central region of the United States. In his role, Shay will be working with integrators, copackers, and end-user customers to expand the company’s growing vertical form-fill-seal packaging business. Matrix is a provider in vertical form fill seal packaging equipment producing a variety of flexible bag styles, including pillow, gusseted, flat bottom, and modified doy. Shay comes to Matrix after a 10-year career holding engineering and sales positions at Formers International, a manufacturer of hand-crafted form fill and seal bag forming assemblies. Shay’s background gives him distinct insight into packaging industry design and customer needs, enabling him to recommend the best vertical form-fill-seal packaging solution to maximize ROI for customers’ specific applications. “I’m excited to apply my experience to help guide customers toward the right packaging system to meet or exceed their sales and production goals,” Shay said. “Matrix is a progressive company that’s become the foremost leader in vertical form fill seal technology, and I’m very happy to be joining their team of talented professionals.” Shay is based in Houston, Texas. Matrix’s South-Central region encompasses eight states from Montana south to Texas. He can be reached at Chris.shay@promachbuilt.com.
StayLinked’s research identifies average warehouse loses $400,000 per year due to hidden productivity killer
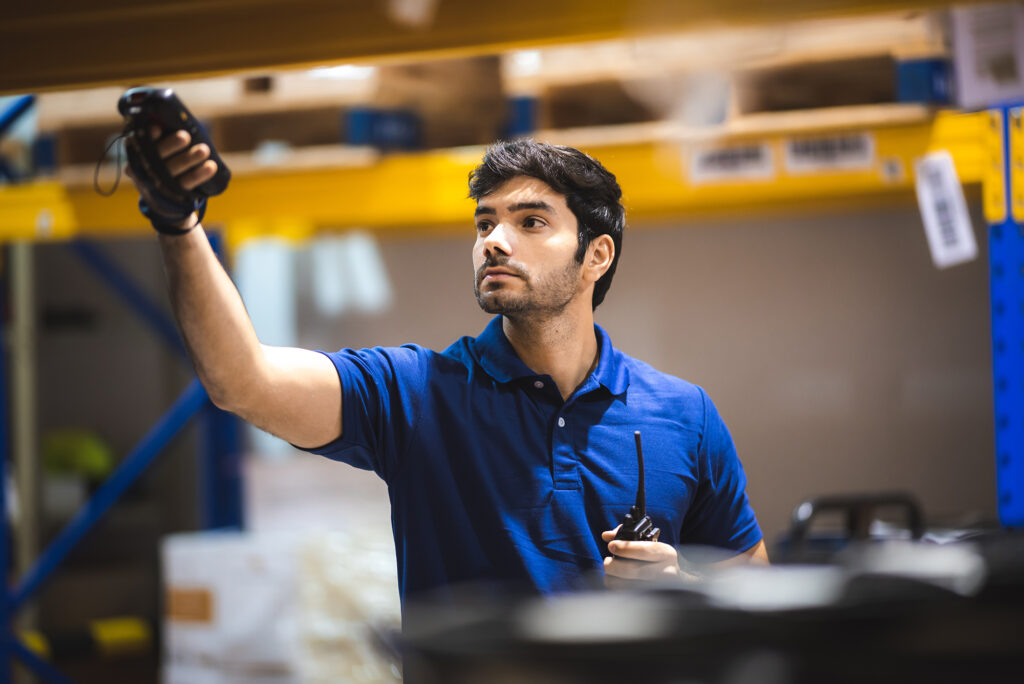
First-of-its-kind research shows productivity and profitability loss caused by ‘dropped sessions’ StayLinked’s research report, titled ‘Dropped Sessions – The Hidden Productivity Killer’, is the first to explore the impact of dropped sessions with those directly involved in warehouse operations: the warehouse worker. Dropped sessions occur when the connection is lost between a worker’s mobile device and the warehouse management system (WMS). The report reveals that over 30% of workers experience a dropped session at least once per hour. Each worker incurs an average of 50 minutes of lost productivity per day resolving dropped sessions. The average cost of dropped sessions per worker, per day is $29.23. For a warehouse with 50 workers, this equates to $1,461.67 a day and over $400,000 a year. In the majority of warehouses, dropped sessions are deemed to be a standard occurrence that workers simply endure. However, the impact goes further than simply productivity. Workers often lose all access to the workflow task they were in the process of completing, which can include the associated data. Resolving the issue often requires them to log in again and repeat the task – or even swap their device for a new one – increasing the risk of missed service level agreements (SLAs) and financial penalties. “Dropped sessions cost warehouses significant amounts in lost profitability. That’s what this report, which is the first look at the impact of dropped sessions from a warehouse worker’s perspective, tells the market,” said Justin Griffith, chief technology officer, StayLinked. “It also reveals that warehouse operations managers are not fully aware that dropped sessions are a single identifiable problem that is impacting efficiency, driving up hidden costs, and eating away at the bottom line.” These hidden costs around dropped sessions don’t just affect warehouse workers. For example, StayLinked’s report reveals that 33% of warehouse workers said they need to enlist the help of costly and valuable IT support to regain connectivity. “Warehouse managers may have overlooked dropped sessions as being a prolific productivity killer because ‘dropped sessions’ is not a term used by warehouse workers when experiencing connection issues,” continued Griffith. “Workers refer to program crash, black screen, system crash, power failure, glitch, mobile device outage, and many other descriptions, which makes it challenging for warehouse managers to identify dropped sessions as being the major cause of workflow disruptions.” The report also revealed that warehouse managers and workers alike often regard dropped sessions as ‘inevitable’, ‘part of the job’ and ‘that’s just how terminal emulation (TE) software works’ – terminal emulation software is used by over half of warehouses around the world. Worryingly, for mobile device manufacturers, 47% of respondents believe that dropped sessions are caused by the hardware. “Our report shows the importance of raising awareness among warehouse operations managers that dropped sessions shouldn’t be a regular daily disruption to worker productivity, and are not caused by the mobile device hardware,” added Griffith. “The deployment of the right TE software delivers session persistence by enabling the worker’s workflow session to reside on a resident server and not on the worker’s mobile device. This ensures that if connectivity issues arise, connectivity to the WMS and the resulting data is not lost, even in 5G and private-5G network environments,” explained Griffith. “I don’t think any supply chain organization or warehouse operator can afford not to address dropped sessions. For the average warehouse employing 50 workers, their bottom line could be boosted by up to $400,000,” stated Griffith. “From our calculations, if dropped sessions were eliminated throughout the entire industry, up to $3.2 billion could be saved.” A copy of the report: ‘Dropped Sessions – The Hidden Productivity Killer’, can be downloaded here: https://info.staylinked.com/session-persistence-report2024
Thermal Runaway: Counterfeit or knockoff Lithium-Ion Battery Warning: Proper handling of overheating Lithium-Ion Batteries
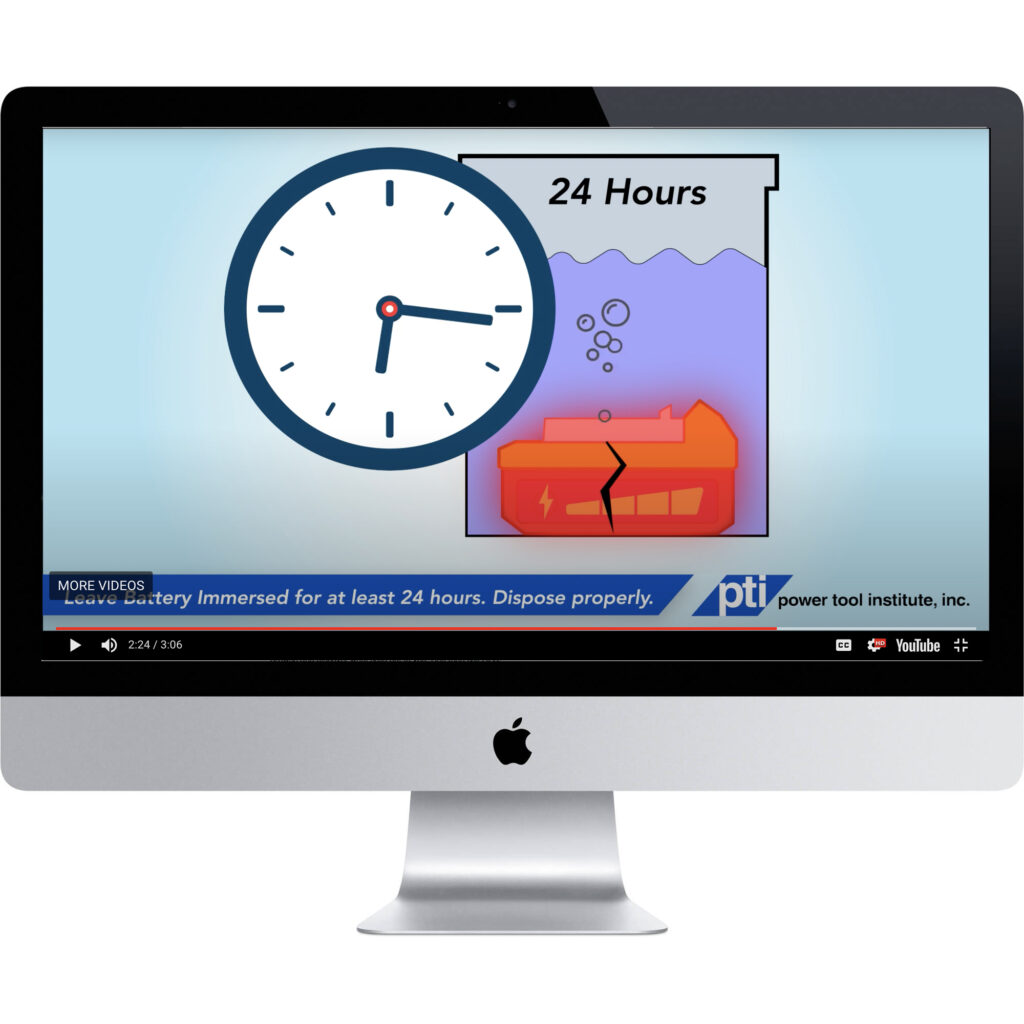
Video from Power Tool Institute details correct procedures The Power Tool Institute, an organization for power tool safety resources, information, and education, has released a new video demonstrating how to properly handle a battery that’s in thermal runaway. A lithium-ion battery that is too hot to touch, melting, smoking, or on fire may be in thermal runaway, which can be caused by misusing or abusing the battery, such as by dropping, puncturing, damaging, or exposing the battery to liquids. Lithium-ion batteries, when purchased by an OEM for their respective tools, are safe. More and more counterfeit and knockoff batteries have appeared on the market and can cause serious issues, including fires. As detailed in the video, the quickest way to cool down and stop an overheating lithium-ion battery is to immerse the battery in a sturdy container filled with water and keep it there for 24 hours. The new video can be viewed at https://www.takechargeofyourbattery.com/videos/safe-handling-of-overheated-lithium-ion-batteries/. Before immersing a battery, there are some things to keep in mind: Don’t physically touch the battery to move it; instead, use something like a long-handled shovel. Wear PPE to protect eyes and skin. Move the battery at least 15 feet away from combustible materials. If the battery is connected to a tool or charger, don’t try to disconnect it. It’s better to sacrifice those items than risk being injured. Put them in the water as well. Be sure to first unplug the charger from the wall outlet. It’s important to leave the battery immersed for at least 24 hours so additional cells within the battery don’t re-ignite. Even if you don’t see flames, the thermal runaway may not be over. While one cell is cooling down, a different cell might be heating up. Once it is safe to dispose the battery, never throw it into the trash or a municipal recycling bin. Instead, take it to a local recycling center or place it in a receptacle specifically designed for recycling batteries. In general, when you take care of your batteries, they will take care of you. However, it’s still important to be aware of proper safety procedures in the event of an emergency like thermal runaway. For more information and helpful power tool safety tips, visit https://www.powertoolinstitute.com/.