PAC Machinery introduces a new motorized adjustable height stand for tabletop baggers
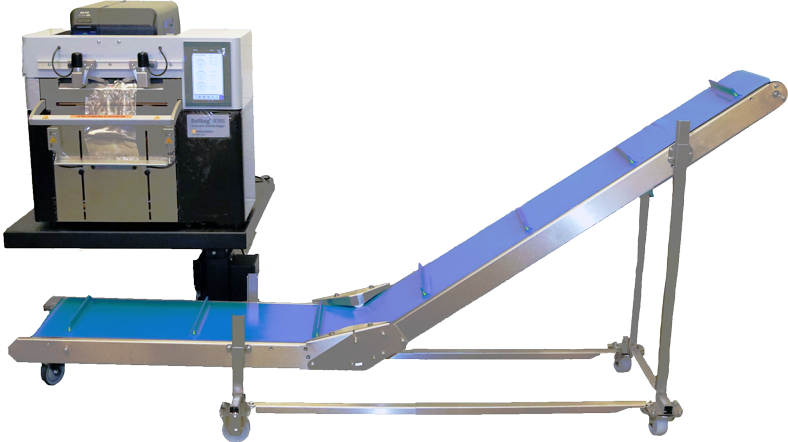
PAC Machinery, a provider of packaging for more than 60 years, has introduced new bagger accessories and resources that make bagging with tabletop automatic baggers even better! They have announced a new Motorized Adjustable Height Stand for automatic tabletop-style bagging machines. This new motorized stand adjusts the bagger height from 22 to 34 inches. This allows the operator to adjust the bagger’s seal height/loading height to best suit the operator and is more ergonomic than PAC’s fixed height stand. Effortlessly adjust the tabletop bagger’s height with the push of a button. Place it anywhere in a facility near an electrical outlet. This stand is ideal for PAC Machinery models Rollbag R785, R1275, and R1285. Using the new motorized adjustable height stand, allows the user to also add PAC’s Motorized Conveyor (see options section). Bags drop down from the bagger onto the stainless conveyor that gets placed in front of the bagger. Products travel up the adjustable incline section which has a height of approximately 35”. Conveyor is available in 10″ & 16″ widths. The new Motorized Adjustable Height Stand also allows the operator to use the Weigh Count Sorting Table to count and bag specific item quantities or weights – that is ideal for small parts packaging. Two New downloadable resources are now available on our website. Download our NEW bags brochure to see our wide selection of custom bags for your bagger and our NEW Stock Bags download is also a great resource!
National Forklift Safety Day: Yale Reliant operator assistance technology reaches 14 million hours of real-world run time

Yale Lift Truck Technologies announces a major milestone for its Yale Reliant™ operator assistance technology to mark the 11th edition of National Forklift Safety Day. Since its launch as a first-of-its-kind solution in 2021, Yale Reliant has since accumulated over 14 million run-time hours across over 6,000 commercially deployed lift truck units. The award-winning technology reinforces lift truck operating best practices and supports operator awareness to help reduce the risk of accidents and close calls like a pedestrian unexpectedly walking in front of a lift truck or an operator traveling too quickly around turns. “Warehouses are pushed to the limit trying to keep up with productivity targets, but they can’t take their focus off safety, especially with a shrinking, transient labor pool that brings an influx of inexperienced lift truck operators,” says Brad Long, Brand Manager, Yale Lift Truck Technologies. “National Forklift Safety Day is an annual reminder of the everyday, year-round importance of operator training and best practices, and the proven track record of Yale Reliant is a testament to technology’s real-world value for warehouses as they seek tools to help protect their employees, inventory and bottom line.” Yale Reliant automatically applies interventions in response to compromised stability, when obstacles are detected in the path of travel or in close proximity, and even based on rules customers specify for certain areas of their warehouse. Adjustments, such as a reduction in travel speed or a smoothing of forklift or tilt movement, are carefully measured to avoid abrupt shifts or jerks that can upset stability. Yale Reliant keeps the operator in ultimate control of the lift truck, but the changes remain noticeable enough for operators to feel. The system also communicates the cause through a display screen, providing an additional layer of feedback to help reinforce proper operation established during training. The growth of warehousing and distribution in the past decade has led to an increased focus on safety in the industry from the U.S. Department of Labor. In July 2023, the Occupational Safety and Health Administration (OSHA) announced a national emphasis program (NEP) to reduce and prevent workplace hazards in warehousing and distribution center operations, and powered industrial truck (PIT) operations are part of the program’s focus. To help warehouse managers understand how the NEP affects them and how to establish a safety culture, Yale offers on-demand events featuring input from state-level occupational safety and health leaders and in-house experts.
PFlow Industries named a Southeast Wisconsin Top Workplace
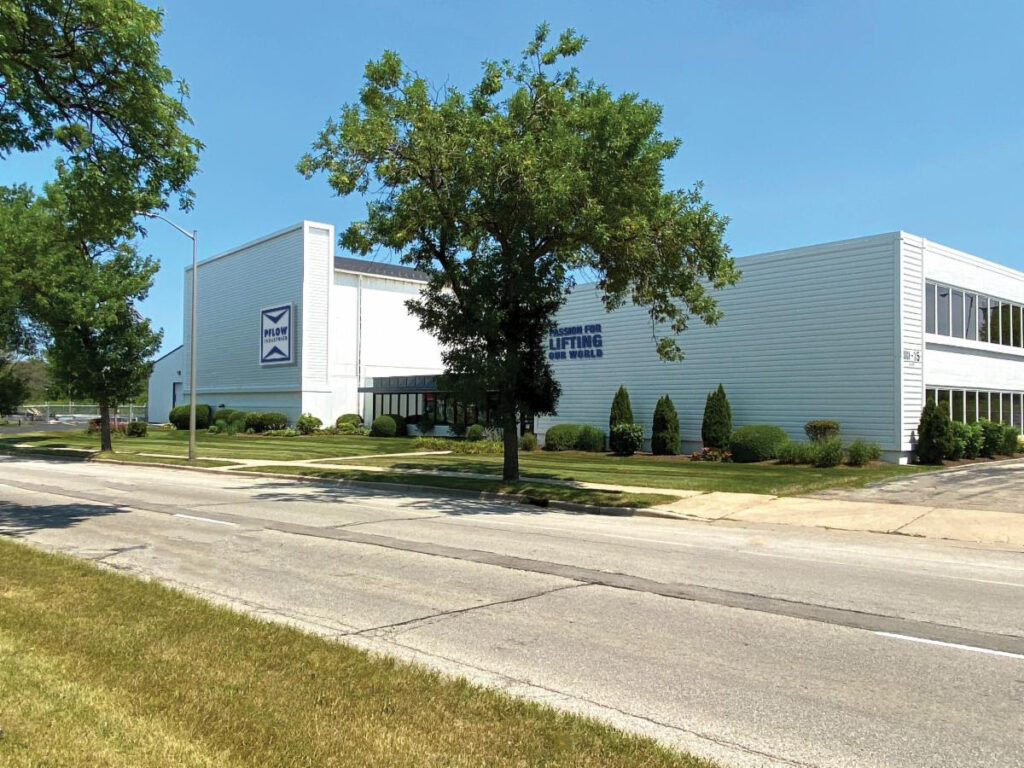
Award dedicated to rewarding people-first culture excellence PFlow Industries, the pioneer in vertical reciprocating conveyor (VRC) technology, announces that it has been named a 2024 Top Workplace winner by the Milwaukee Journal Sentinel, which recognized 169 Milwaukee and Southeast Wisconsin companies and organizations as winners. PFlow won a Southeast Wisconsin “Top Workplaces” award, placing #37 in a group of 61 mid-sized companies. Top Workplaces award winners are determined entirely by employee survey feedback gathered by the Energage Platform’s Workplace Survey, a research-backed employee engagement survey that measures the workplace experience to drive award-winning, people-first cultures. The program uses a proprietary approach that combines a wealth of data and industry-leading benchmarks to ensure winners represent cultural greatness. “Being a 100 percent employee-owned company is advantageous for both employees and customers, and I am extremely proud that PFlow has been recognized as a Top Workplace,” said Pat Koppa, President at PFlow Industries. “PFlow is focused on delivering innovative, robust, and reliable vertical material lifting solutions that are built to last. We are dedicated to encouraging a supportive work culture, providing best-in-class products and service for our customers, and improving the lives of those in our community through volunteer service and community giving efforts – “lifting our world” by putting people first.” The Workplace Survey qualifies each winning company for Top Workplaces employer recognition throughout the year, including regional, national, cultural excellence, and industry awards.
Episode 492: Driving innovation in supply chains with PepsiCo Labs
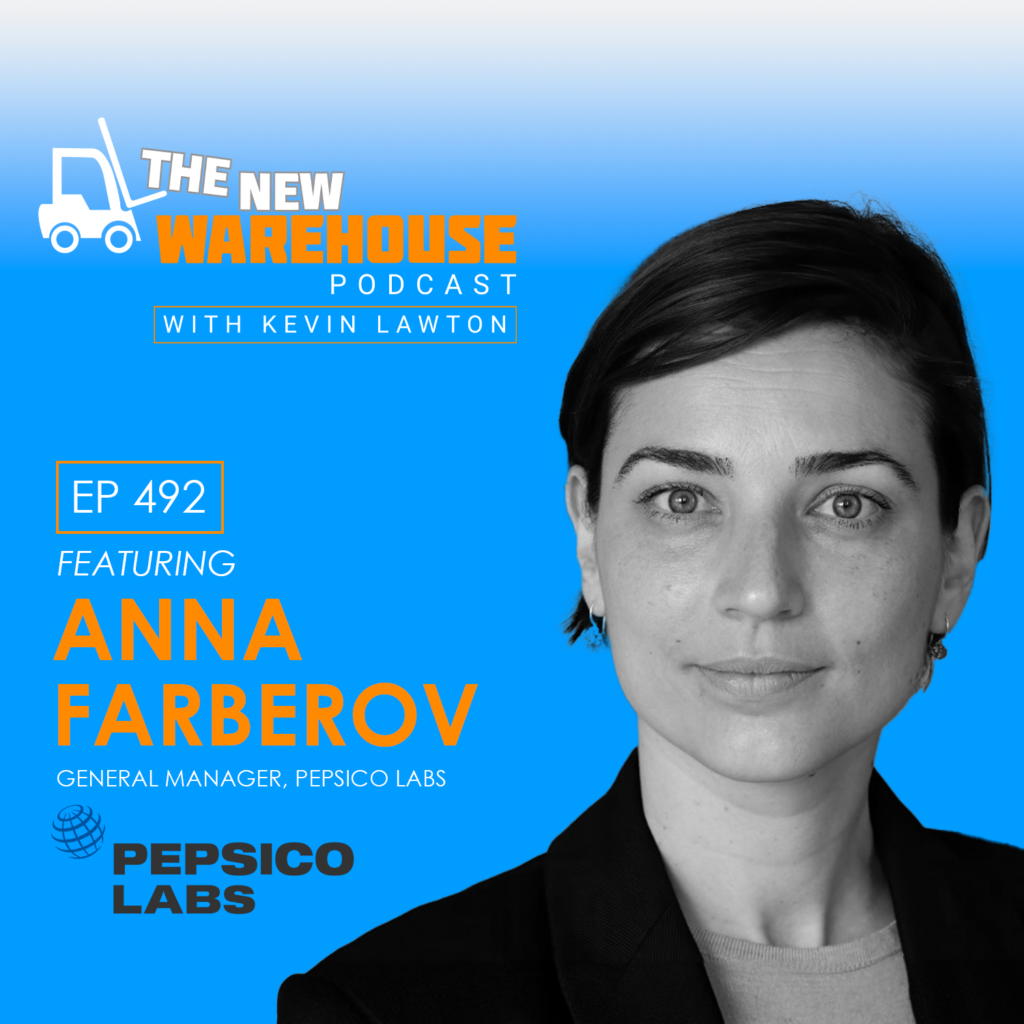
Today’s episode of The New Warehouse Podcast features Anna Farberov, the General Manager at PepsiCo Labs. Anna is at the forefront of technological innovation at PepsiCo, exploring and implementing cutting-edge solutions to enhance efficiency across their supply chain. In this episode, Anna delves into the inner workings of PepsiCo Labs, their approach to innovation, and world-changing technologies that are revolutionizing their operations from seed to shelf. The Integrated Value Chain of PepsiCo PepsiCo’s operations span the entire supply chain, making their approach to supply chain innovation uniquely comprehensive. Anna explains, “We start with what we call ‘seed to shelf.’ We own the seed, we grow the potatoes, and we use our own trucks to ship them.” This vertical integration means that PepsiCo controls every step, from agriculture to direct store delivery, ensuring quality and efficiency throughout. Anna highlights the sheer scale of their operations, noting that small changes can lead to significant impacts. “Imagine if we find a way to grow potatoes better or use less water in our irrigation. Even improving the throughput of our warehouses can have a huge impact,” she says. This comprehensive control allows PepsiCo Labs to target innovations that can deliver substantial benefits across various touchpoints in their supply chain. Taking a Pragmatic Approach to Innovation in Supply Chains PepsiCo Labs takes a pragmatic approach to innovation in supply chains, focusing on solving specific business problems rather than chasing the latest tech trends. “We look at what are the biggest problems in the business, go to the business experts, and ask them what we can solve,” Anna explains. This problem-first strategy ensures that the innovations they adopt are both relevant and impactful. One example Anna shares is their approach to eCommerce warehousing. “We needed a solution for eCommerce that required a large number of SKUs moving fast in a small footprint. This led us to micro-fulfillment centers with automated storage and retrieval systems,” she explains. By focusing on the specific needs of their eCommerce operations, PepsiCo Labs was able to implement solutions that improved efficiency without compromising product availability. Balancing Technology with Human Elements While automation and technology are crucial, Anna emphasizes the importance of centering supply chain innovations around the human element. “You can’t just throw a lot of tech or robotics at a warehouse and expect it to happen. You need to center it around the human element and bring the people with you on the journey,” she states. This approach ensures that technological advancements enhance rather than disrupt the work environment for PepsiCo employees. Anna shares a practical example: “We’ve implemented a scanning solution that can capture multiple labels in one photo, reducing the repetitive task of scanning labels individually.” This not only improves efficiency but also enhances the work experience for employees by eliminating tedious tasks. Key Takeaways PepsiCo controls its supply chain from “seed to shelf,” allowing targeted innovations with significant impacts. Focusing on solving specific business problems ensures relevant and impactful technological adoption. Centering innovations around employees enhances efficiency while improving the work environment. The New Warehouse Podcast EP 492: Driving Innovation in Supply Chains with PepsiCo Labs
Bobcat expands Tractor lineup with introduction of utility tractors
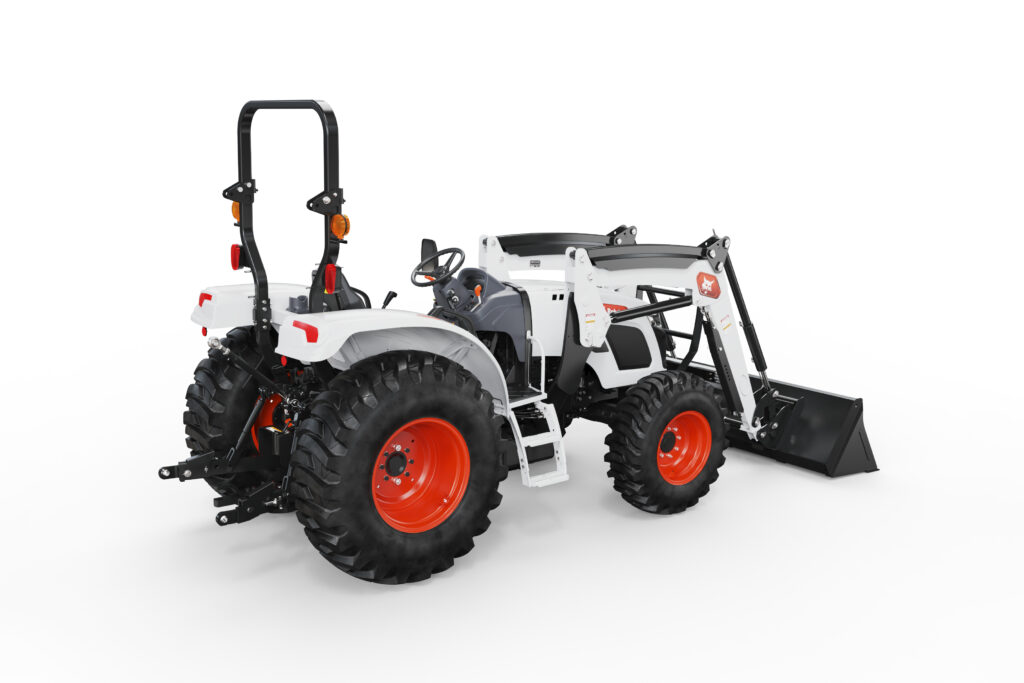
Bobcat Company is expanding its tractor lineup with the launch of three utility tractors: the Bobcat UT6066, UT6566, and UT6573. Bobcat utility tractors are built for heavy-duty work while making it easier for operators of all experience levels to accomplish more on their acreage. “Designed with intuitive, operator-friendly controls, Bobcat utility tractors are dependable, easy to operate, and highly versatile machines that maximize performance and productivity,” said Jonathan Widmer, Bobcat senior product specialist. “There’s less demand on operators so they can focus more on leaving behind great results, whether they’re putting an implement to work or moving material with the tractor’s loader.” Bobcat utility tractors feature 12×12 power shuttle transmissions that deliver smooth, easy shifting without stepping into a clutch pedal. Powered by turbocharged, Tier 4 diesel engines, these versatile workhorses offer robust, high-power performance with impressive low-end torque, plus an efficient fuel system. The tractors offer reliable starts, swift travel speeds, long component life, easy service access, and simple maintenance, as well as reduced noise and vibration for comfortable workdays behind the wheel. The climate-controlled cab, which comes standard on the UT6566 and UT6573, provides year-round comfort no matter the weather conditions. The utility tractors also feature wide glass panels, convenient visibility to the 3-pt hitch, power and tilt steering, and ergonomic controls that are thoughtfully laid out to enhance operator performance and minimize fatigue. Implement and Attachment Versatility The optional Bobcat front-end loader is easy to attach and disconnect, with free-standing capability when removed. The loader delivers impressive lift and reach capabilities for maximum productivity. It comes with the Bobcat Bob-Tach® attachment mounting system for quick and easy attachment changes and an integrated hydraulic valve for powered attachment operations. The mechanical, self-leveling loader keeps pallet forks level throughout the full range of motion and minimizes bucket spillage. Bobcat utility tractors feature a rear power take-off (PTO) that achieves 540 rpm at engine speeds of either 1,800 rpm or 2,500 rpm for maximum power. The Category 2, 3-point hitch is key to Bobcat utility tractors’ versatility, allowing operators to take on tasks that require both non-powered and PTO-powered implements. The telescopic lower links and stabilizers support easy implement connections and removals without the need for tools. Rear-remote hydraulics further enhance these tractors’ implement versatility. Operators can engage the PTO with just the push and turn of a button. Other performance-enhancing features include: PTO Cruise enables operators to maintain consistent PTO power when the engine’s load conditions change. Draft Control helps maintain the desired implement height, raising the implement only when required to prevent tire slippage or engine stall. Four-Wheel Drive engages at the push of a button. Rear-Remote Hydraulics offer operators greater versatility by enabling hydraulic functions for many implements. Power and Tilt Steering supports operator comfort and minimizes fatigue. Mechanical Self-leveling keeps the loader bucket or pallet forks level and minimizes bucket spillage. Loader Floatation allows the loader attachment to follow the ground contour. Bobcat Bob-Tach supports quick and easy loader attachment changes. “Whether you need a dependable tractor for cutting hay, clearing snow, feeding livestock, seeding food plots, handling materials or a multitude of other tasks, there’s a versatile Bobcat utility tractor to help you do more with one machine,” Widmer said. Bobcat currently offers several tractor options as part of its existing product portfolio, including sub-compact tractors, compact tractors and articulating tractors. The new utility tractors will be available at select Bobcat dealerships this summer.
April 2024 Manufacturing Technology Orders slow decline and remain above historical average
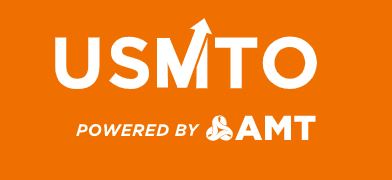
Orders of manufacturing technology, measured by the U.S. Manufacturing Technology Orders Report published by AMT – The Association For Manufacturing Technology, reached $317.9 million in April 2024. This is a 25.6% decrease from March 2024 but only 5.4% behind orders in April 2023. Orders in 2024 totaled $1.43 billion through April, 16.2% behind orders placed in the first four months of 2023. Machinery orders have been steadily declining since hitting a peak in the fourth quarter of 2021, according to the USMTO data. Although 2024 has had the weakest start to the year since 2020, orders through April are nearly 5% above the average order volume through the first four months of a year since USMTO began tracking orders in 1998. Contract machine shops, the largest customer of manufacturing technology, decreased orders significantly in April compared to March 2024 – but by less than the overall market. Still, contract machine shops experienced the slowest start to the year since the first few months of 2020, when COVID shutdowns caused orders to crater. After two strong years of orders, the automotive industry has begun to pare back investment in manufacturing technology. Consumer demand for electric vehicles has not met expectations despite significant investment from major automakers. Additionally, demand for internal combustion engines has lagged behind expectations as inflation persists and heightened interest rates give pause to consumers looking to purchase and finance a new vehicle. The aerospace industry has continued its elevated level of investment into 2024. Order activity from this sector is particularly strong in the Southeast region, leading it to the strongest growth of any region. Driven by a pool of talented workers, aerospace companies have been opening and expanding manufacturing operations in the Southeast over the last several years, particularly in North Carolina. In the longer-term trend, the decline in orders appears to be stabilizing. At AMT’s Spring Economic Webinar, Oxford Economics revised their forecast to predict 2024 will end flat or slightly down compared to 2023, anticipating a pickup in order activity through the remainder of the year. Through April, new orders of durable goods were nearly flat compared to the beginning of 2023, and industrial production fell 7.6% from its post-COVID peak. Oxford Economics further predicted that industrial production had reached its lowest point of the current business cycle in most advanced economies. On average, orders in the second half of a year exceed the first by nearly 10%. Should industrial production and new orders pick up through the remainder of 2024, manufacturers will begin to need additional capacity right around the time the doors to IMTS 2024 open in Chicago.
SupplyOne establishes West Coast Production and Distribution Presence with Columbia Corrugated Box
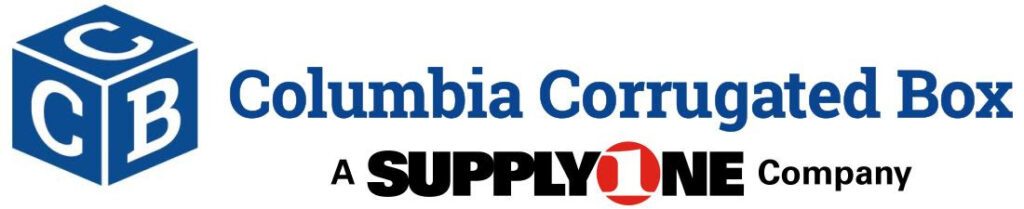
SupplyOne, Inc., just announced that it has expanded its footprint to the West Coast with the acquisition of Columbia Corrugated Box Company, Inc (CCB). CCB manufactures custom corrugated solutions, protective packaging, and high-resolution printed packaging solutions in the Pacific Northwest. Founded in 1967, CCB is comprised of two divisions, Columbia Corrugated Box and Packaging Resources Company (PRC). The Company primarily operates within Washington, Oregon, and Northern California, with facilities in the Portland and Seattle metro areas as well as Medford, OR, and Eugene, OR. In addition to offering traditional corrugated packaging solutions, CCB offers specialty custom corrugated services, retail point-of-purchase displays, and high-color graphics through litho lamination and digital printing capabilities. The PRC division primarily operates in the protective packaging solution field. Products provided consist of items such as custom cushioned crates, thermoformed pick-and-place build pallets, and value-added foam products. “Adding a SupplyOne presence to the West Coast further enhances our ability to service customers nationwide, in addition to the ongoing expansion of our North American coverage,” said Todd Renehan, President and CEO of SupplyOne. “From our first conversations with CCB, we aligned strongly on approaching each customer with custom solutions and superior service.” “As a family-owned business for over 50 years, it was extremely important to find the right partner that continues our legacy of fast, high-quality packaging solutions, embraces a customer-first attitude, and treats employees like family. SupplyOne fits the bill on all fronts while offering an expansive North American footprint to serve our customers even more broadly,” said Steve Tanner, Owner of CCB. “The management team and loyal employees of CCB have built one of the best corrugated and protective packaging businesses in the country over the last 50+ years, of which we are very proud. As part of SupplyOne, we are looking forward to taking the business to the next level with international scale, while maintaining the high-touch service our customers expect. We are very excited for the future growth this partnership will help drive,” said Roggy Pflug, COO of CCB. This acquisition represents the 41st addition to the SupplyOne portfolio in its 25 years in business.
CLARK Material Handling Company appoints Vice President of Manufacturing and Vice President of Finance
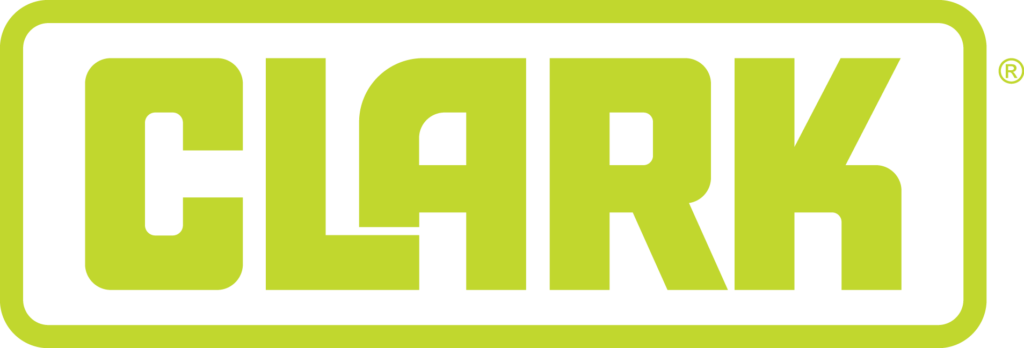
CLARK Material Handling Company has announced the promotion of Anthony Nash and Dan Kaiser to Vice President level positions as part of the strategic vision for the company’s organizational structure, to further support and enhance CLARK’s global operations and to serve the CLARK dealer network better. These promotions reflect the company’s ongoing commitment to providing its dealers and customers with high-quality innovative products and world-class service and support to meet their unique needs and challenges. Anthony Nash has been promoted to Vice President of Manufacturing. In his new role, Mr. Nash will be pivotal in driving success across quality, production, purchasing, operations planning, facilities, and safety areas of the business. With 30 years of proven leadership experience in manufacturing, Mr. Nash brings a strong focus on quality, continuous improvement, and operations. Mr. Nash will continue to drive SIOP (Sales, Inventory, and Operations Planning) as well as collaborating with international factories. Dan Kaiser has been promoted to Vice President of Finance. A 24-year veteran in the industry and in finance, Mr. Kaiser will lead all of the accounting and finance functions for CLARK North America, and in his new capacity will also oversee the internal IT team. Mr. Kaiser will continue to provide financial governance and strategy to CLARK as well. The promotion of Mr. Nash and Mr. Kaiser will allow CLARK to leverage their combined talents and skills to pursue the company’s vision for the benefit of CLARK dealers and CLARK customers.
ORBIS earns recognition as a John Deere “Partner-level Supplier”
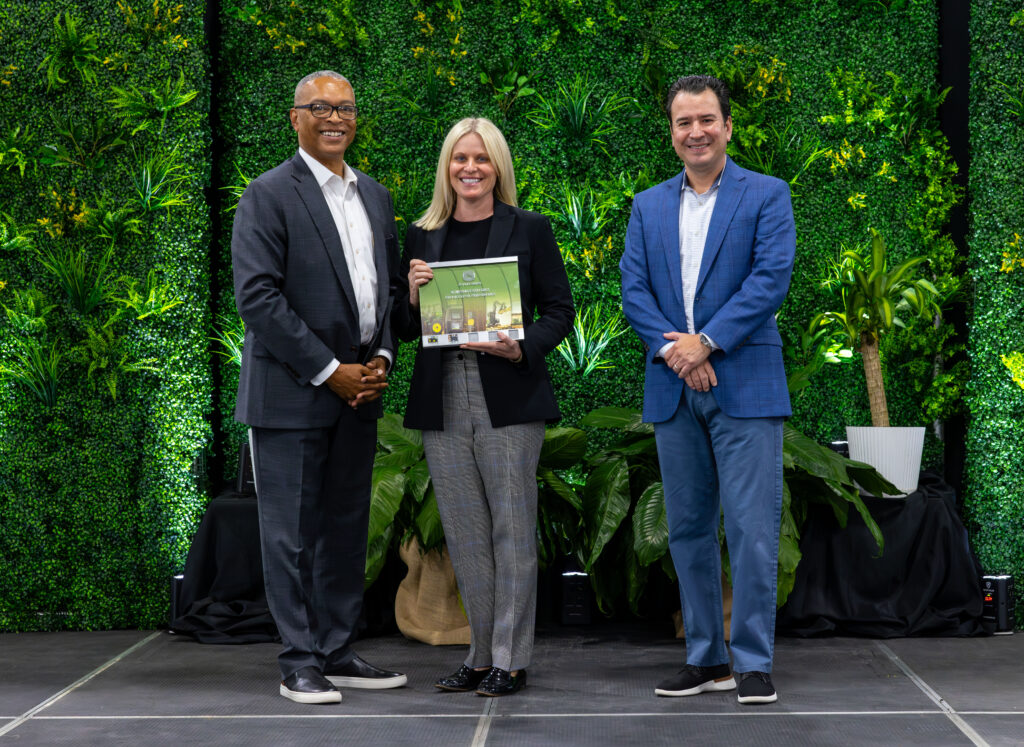
ORBIS ® Corporation has earned recognition as a Partner-level supplier for 2023 in the John Deere Achieving Excellence Program. The Partner-level status is Deere & Company’s highest supplier rating. The Oconomowoc, Wis.-based company was selected for the honor in recognition of its dedication to providing products and services of outstanding quality as well as its commitment to continuous improvement. Company employees accepted the recognition during formal ceremonies held on April 11 in Moline, Illinois. ORBIS supports John Deere’s network of reusable containers to deliver parts to their facilities. Suppliers who participate in the Achieving Excellence program are evaluated annually in several key performance categories, including quality, delivery, process alignments, value creation, and relationship. John Deere Supply Management created the program in 1991 to provide a supplier evaluation and feedback process that promotes continuous improvement.
SupplyOne establishes West Coast Production and Distribution presence with Columbia Corrugated Box
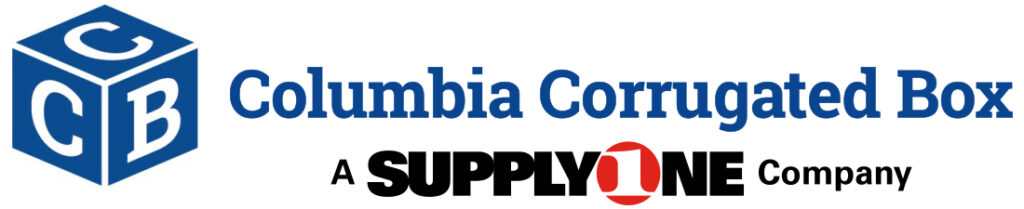
SupplyOne, Inc., the largest independent supplier of corrugated and value-added packaging products, equipment, and services in North America, announced that it has expanded its footprint to the West Coast by acquiring Columbia Corrugated Box Company, Inc (CCB). CCB manufactures custom corrugated solutions, protective packaging, and high-resolution printed packaging solutions in the Pacific Northwest. Founded in 1967, CCB is comprised of two divisions, Columbia Corrugated Box and Packaging Resources Company (PRC). The Company primarily operates within Washington, Oregon, and Northern California, with facilities in the Portland and Seattle metro areas as well as Medford, OR, and Eugene, OR. In addition to offering traditional corrugated packaging solutions, CCB offers specialty custom corrugated services, retail point-of-purchase displays, and high-color graphics through litho lamination and digital printing capabilities. The PRC division primarily operates in the protective packaging solution field. Products provided include custom cushioned crates, thermoformed pick-and-place build pallets, and value-added foam products. “Adding a SupplyOne presence to the West Coast further enhances our ability to service customers nationwide, in addition to the ongoing expansion of our North American coverage,” said Todd Renehan, President and CEO of SupplyOne. “From our first conversations with CCB, we strongly aligned with approaching each customer with custom solutions and superior service.” “As a family-owned business for over 50 years, it was extremely important to find the right partner that continues our legacy of fast, high-quality packaging solutions, embraces a customer-first attitude, and treats employees like family. SupplyOne fits the bill on all fronts while offering an expansive North American footprint to serve our customers even more broadly,” said Steve Tanner, Owner of CCB. “The management team and loyal employees of CCB have built one of the best corrugated and protective packaging businesses in the country over the last 50+ years, of which we are very proud. As part of SupplyOne, we are looking forward to taking the business to the next level with international scale, while maintaining the high-touch service our customers expect. We are very excited for the future growth this partnership will help drive,” said Roggy Pflug, COO of CCB. This acquisition represents the 41st addition to the SupplyOne portfolio in its 25 years in business.
Industry consultant George Keen publishes new book for equipment dealers
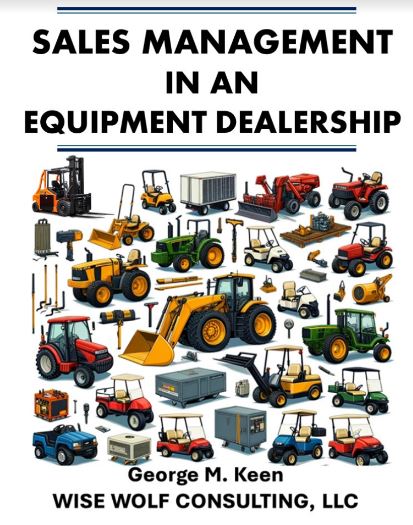
Conquer Your Equipment Dealership’s Sales with Powerful Strategies! Industry consultant George Keen has released his new paperback book to maximize the dealership’s potential with strategic sales management. The book is called Sales Management in an Equipment Dealership. It unlocks the full potential of your dealership with expert sales management strategies. “Sales Management in an Equipment Dealership” equips you with the tools and knowledge to build a high-performing sales team and maximize profits. This comprehensive guide dives deep into crucial sales management techniques specifically tailored for the equipment dealership environment. Master the Art of Market Segmentation: Learn how to identify your ideal customers and tailor sales strategies to their unique needs. Forge Unbreakable Customer Relationships: Discover proven methods to boost customer satisfaction and cultivate long-term loyalty. Build a Winning Sales Force: Explore effective recruitment and training techniques to assemble a team of top-performing salespeople. Harness the Power of CRM: Implement Customer Relationship Management systems to streamline communication and boost sales efficiency. Cultivate a Thriving Sales Culture: Foster a positive and results-oriented environment that motivates your team to achieve peak performance. “Sales Management in an Equipment Dealership” is your one-stop shop for taking your dealership’s sales to the next level. Whether you’re a seasoned sales manager or just starting out, this book provides the practical guidance you need to succeed. The book is available now on Amazon in paperback, eBook, and possibly in Spanish later this year. George Keen is offering a special discounted price to Wholesaler’s readers by using this QR code or this link. George Keen advises companies on strategic questions and productivity challenges related to technology and innovation, with a focus on financial performance transformation and the development of profitable business models. George has more than 45 years of consulting experience—including Western Europe and South America—and brings in-depth knowledge of the equipment dealer/distributor facets. George serves a variety of dealers and distributors and a wide range of machinery dealer organizations. Industries include forklifts, construction, agriculture, generators, air compressors, retread tires, heavy trucks, and golf cars, to mention a few.
Forklift Battery Safety Tips & Safety Practices for Forklift Safety Day 2024
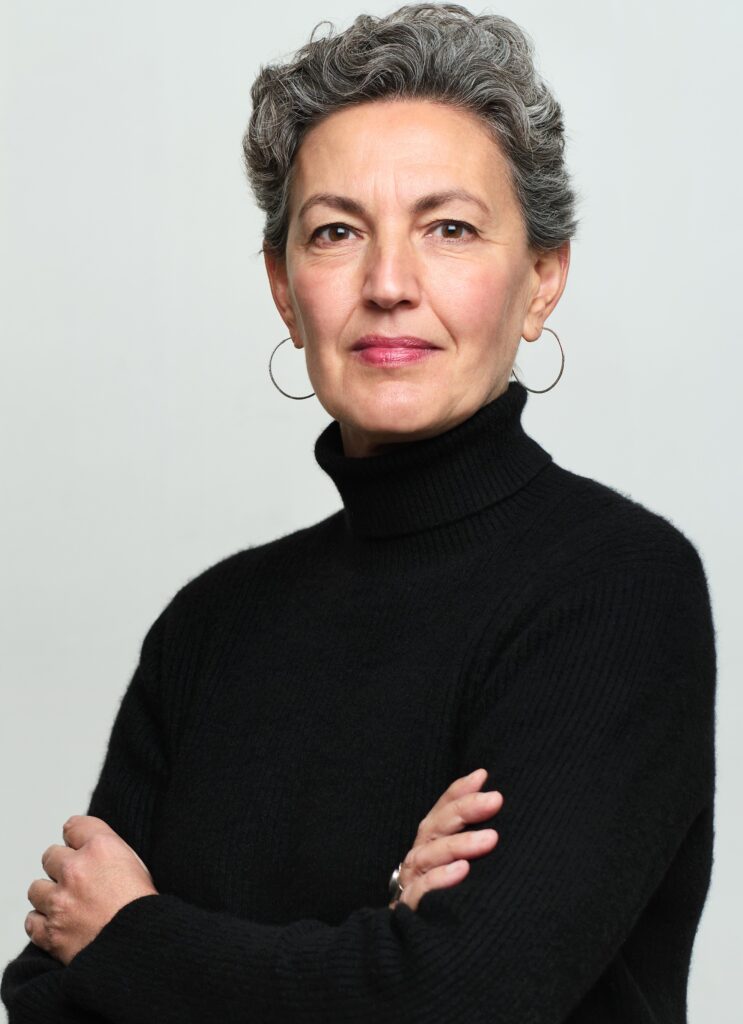
Forklifts are essential workplace vehicles that offer immense utility and productivity boosts. However, they are also associated with significant safety risks, as many workplace transport-related accidents involve forklifts. This underscores the importance of adhering to forklift safety practices. National Forklift Safety Day, promoted by the Industrial Truck Association, is dedicated to ensuring the safety of those who manufacture, operate, and work around forklifts. June 11, 2024, marks the eleventh annual event. To support this event, ROYPOW will guide you through essential forklift battery safety tips and practices. A Quick Guide to Forklift Battery Safety In the world of material handling, modern forklift trucks have gradually shifted from internal combustion power solutions to battery power solutions. Therefore, forklift battery safety has become an integral part of overall forklift safety. Which is Safer: Lithium or Lead Acid? Electric-powered forklift trucks typically utilize two types of batteries: lithium forklift batteries and lead-acid forklift batteries. Each type has its advantages. However, from a safety perspective, lithium forklift batteries have clear benefits. Lead-acid forklift batteries are made of lead and sulfuric acid, and if improperly handled, the fluid can spill. Additionally, they require specific vented charging stations as charging can produce harmful fumes. Lead-acid batteries also need to be swapped during shift changes, which can be hazardous due to their heavy weight and the risk of falling and causing operator injuries. In contrast, lithium-powered forklift operators do not have to handle these hazardous materials. They can be charged directly in the forklift without swapping, which reduces related accidents. Moreover, all lithium-ion forklift batteries are equipped with a Battery Management System (BMS) that provides comprehensive protection and ensures overall safety. How to Choose a Safe Lithium Forklift Battery? Many lithium forklift battery manufacturers incorporate advanced technologies to enhance safety. For instance, as the industrial Li-ion battery leader and a member of the Industrial Truck Association, ROYPOW, with a commitment to quality and safety as the top priority, constantly strives to develop reliable, efficient, and safe lithium power solutions that not only meet but exceed safety standards to deliver optimal performance and reliability in any material handling application. ROYPOW adopts LiFePO4 technology for its forklift batteries, which has been proven the safest type of lithium chemistry, offering superior thermal and chemical stability. This means they’re not prone to overheating; even if punctured, they won’t catch fire. The automotive-grade reliability withstands tough uses. The self-developed BMS offers real-time monitoring and intelligently prevents overcharging, over-discharge, short circuits, etc. Moreover, the batteries feature a built-in fire extinguishing system while all materials used in the system are fireproof for thermal runaway prevention and added safety. To guarantee ultimate safety, ROYPOW forklift batteries are certified to meet rigorous standards such as UL 1642, UL 2580, UL 9540A, UN 38.3, and IEC 62619, while our chargers adhere to UL 1564, FCC, KC, and CE standards, incorporating multiple protective measures. Different brands may offer varying safety features. Therefore, it’s essential to understand all the different aspects of safety in order to make an informed decision. By investing in reliable lithium forklift batteries, businesses can enhance workplace safety and productivity. Safety Tips for Handling Lithium Forklift Batteries Having a safe battery from a trusted supplier is a great place to start, but the safety practices of operating the forklift battery are also important. Some tips are as follows: Always follow the instructions and steps for installation, charging, and storage given by the battery manufacturers. Do not expose your forklift battery to extreme environmental conditions such as excessive heat and cold could affect its performance and lifespan. Always turn off the charger before disconnecting the battery to prevent arcing. Regularly check electrical cords and other parts for signs of fraying and damage. If there are any battery failures, maintenance and repairs need to be carried out by an authorized well-trained, and experienced professional. A Quick Guide to Operation Safety Practices In addition to the battery safety practices, there are more that forklift operators need to practice for the best forklift safety: Forklift operators should be in full PPE, including safety equipment, high-visibility jackets, safety shoes, and hard hats, as required by environmental factors and company policies. Inspect your forklift before each shift through the daily safety checklist. Never load a forklift exceeding its rated capacity. Slow down and sound the forklift’s horn at blind corners and when backing up. Never leave an operating forklift unattended or even leave keys unattended in a forklift. Follow the designated roadways outlined at your worksite when operating a forklift. Never exceed speed limits and stay alert and attentive to your surroundings when operating a forklift. To avoid hazards and/or injury, only those who have been trained and licensed should operate forklifts. Never allow anyone under the age of 18 to operate a forklift in non-agricultural settings. According to the Occupational Safety and Health Administration (OSHA), over 70% of these forklift accidents were preventable. With effective training, the accident rate may be reduced by 25 to 30%. Follow the forklift safety policies, standards, and guidelines and participate in thorough training, and you can significantly enhance forklift safety. Make Every Day Forklift Safety Day Forklift safety is not a one-time task; it’s a continuous commitment. By fostering a culture of safety, staying updated on best practices, and prioritizing safety every day, businesses can achieve better equipment safety, operator and pedestrian safety, and a more productive and secure workplace.
Brown joins OTR as Global VP Sales & Marketing OEM
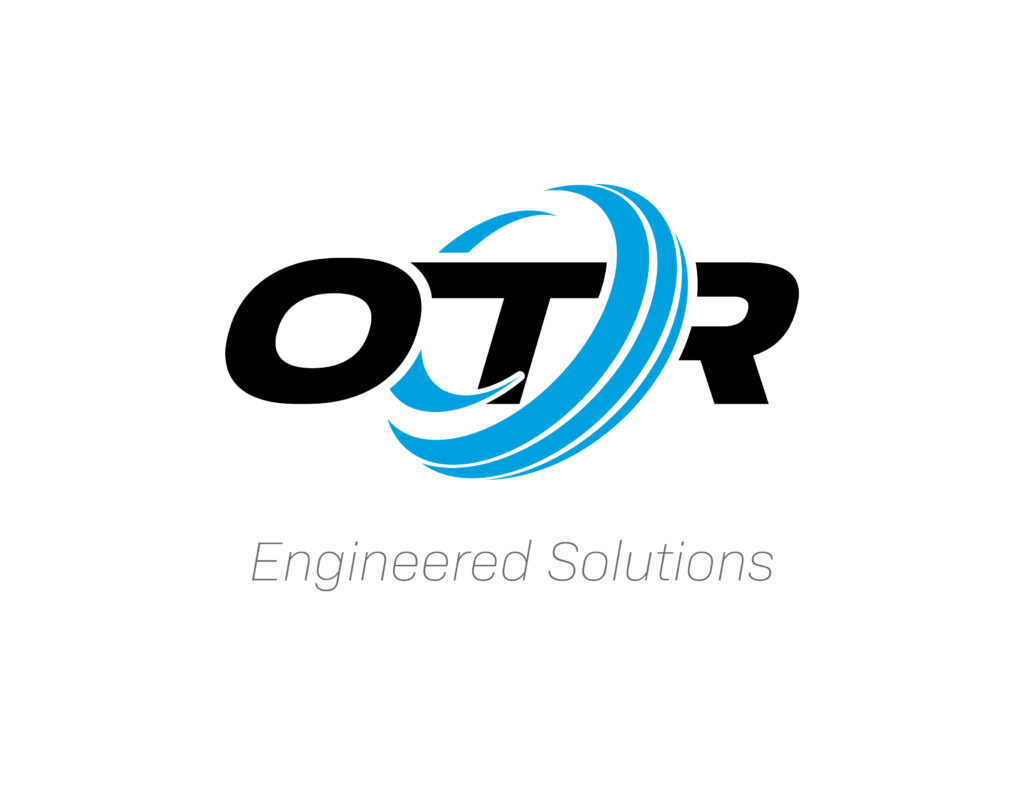
OTR Engineered Solutions (OTR) has named Ben Brown as its new Global VP Sales & Marketing OEM. He will be a part of OTR’s executive team, reporting directly to President and CEO, Tom Rizzi, and will serve an integral role in developing the company’s strategic OEM partnerships. In his new position, Brown will be responsible for growing the company’s OEM business globally across various markets, including construction, lawn and garden, powersports, agriculture, forestry, mining, material handling, and specialty vehicles. To achieve this goal, he will leverage OTR’s 32 facilities worldwide, which offer a range of value-added services such as warehousing, tire mounting, and sequencing. Additionally, he will build brand recognition through the execution of a detailed marketing plan. Brown’s extensive experience includes senior leadership and executive positions in the automotive and commercial vehicle industry. His accomplishments include growing revenue, driving new business, and successfully managing teams for his past employers, among other responsibilities. “Our OEM partners are extremely important to OTR, and Ben is a great fit to help grow this area of our business,” said Tom Rizzi, President and CEO. “We’re proud of the unmatched value we offer OEMs through custom engineering, global distribution, subassembly, and many other services. We’re excited for Ben to enhance this offering to our customers and to help drive OTR’s purpose of making our customers’ lives easier.” OTR Engineered Solutions is a market-leading global enterprise specializing in off-the-road tire, wheel, and track solutions for original equipment manufacturers (OEMs) and aftermarkets. Known for being an innovator in multiple off-the-road applications, OTR differentiates itself by providing value-added services such as warehousing, tire mounting, and sequencing, among other things. The firm has long established strategic partnerships with OEMs covering Construction, Lawn & Garden, Powersports, Agriculture, Forestry, Mining, Material Handling, and Specialty Vehicle markets. OTR’s infrastructure comprises 32 facilities and warehouse locations throughout the U.S., Canada, Europe, and Asia, serving customers globally.
BarTender intelligent templates™ simplify and streamline SAP label printing
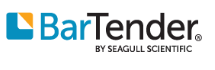
Seagull Scientific, LLC, (“Seagull”) maker of BarTender®, the global leader in software to print, mark, and code labels, RFID tags, products, and packaging, has partnered with BCC Distribution to makes it easy to design and print barcode labels from SAP . Using BarTender Intelligent Templates , companies can produce a wide variety of flexible label designs without having to create and maintain hundreds of separate documents. This allows users to use dynamic data, images, colors, object positions, and text on each label that is printed. BarTender leverages conditional printing to specify exactly when different objects, layers, or templates in your document are printed. For example, you can configure a graphic to be printed if the data given includes a specific numeric or text value and the graphic will not print outside of these conditions. Or you can choose to print a template based on the specified parameters from within your database. BarTender partners with SAP ISV specialists like BCC Distribution, a leading provider of SAP certified software solutions, for mobile RF scanning, barcode label printing, mobile device management and more. BCC Distribution’s QuickPrint is a comprehensive enterprise printing solution that makes it easy to design and print barcode labels directly from SAP software, leveraging BarTender on the backend. BarTender Intelligent Templates are used by businesses of all sizes across many industries, including the world’s largest and most dynamic supply chains. To learn more about using dynamic design techniques, visit Creating Intelligent Templates™ . BCC Distribution is exhibiting at the SAP Saphire Conference in Orlando, Florida this week. Stop by booth #526 to learn more about SAP barcode and label printing or visit QuickPrint – BCC Distribution.
ARI Phoenix, Inc. appoints Christopher Jones as its President/Chief Operating Officer
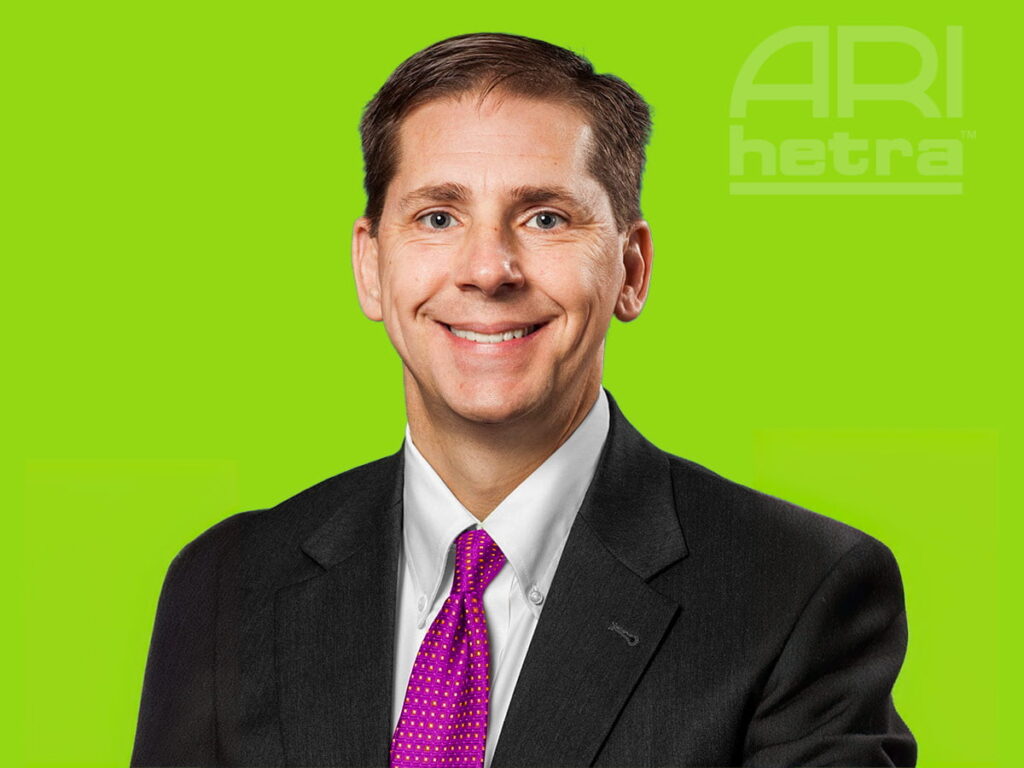
Seasoned Sales Executive takes the helm to drive next level growth. ARI Phoenix, Inc. (ARI) is pleased to announce that Christopher Jones of Liberty Township Ohio joins the company as President and Chief Operating Officer. Mr. Jones most recently served as the President of GF Machining Solutions, the US operation of a Swiss leader in machining and automation. His 30-year career has been marked by excellence in sales development and general corporate leadership. Mr. Jones remarked “I’m thrilled to bring my skills to bear at such a great local company.” ARI is an industry leader in shop equipment for the heavy-duty truck maintenance industry across North America. The company’s flagship product is the ARI-HETRA mobile column lift (MCL) which is sold in ARI’s trademarked “safety green.” The MCL is the preferred solution to safely lift trucks weighing as much as 150,000 lbs with any wheelbase or width. As the name implies, mobile column lifts are easily moved between service bays and are purchased at a fraction of comparable fixed solutions. Gary Hudson, Chairman and CEO of ARI-HETRA notes “We are so excited to join forces with Chris and are confident that he will take us to the next level!”
Toshiba social media leader Robert Catalano wins gold
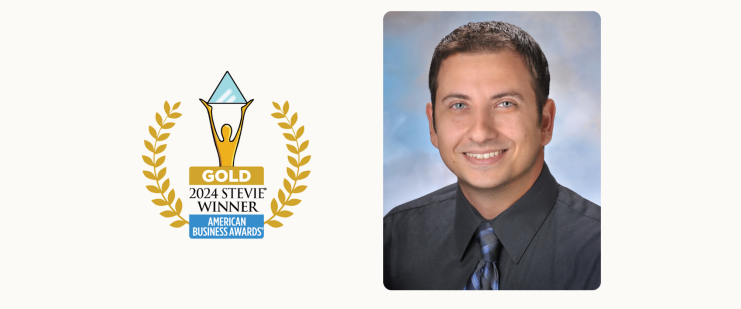
Catalano earns Gold Stevie for Best Business Influencer of the Year Toshiba America Business Solutions’ social media leader Robert Catalano secures the Gold Stevie® Award in The 2024 American Business Awards® for Best Business Influencer of the Year. This Gold Stevie is presented to the individual demonstrating innovation in social media content creation and moderation, management, and marketing. The American Business Awards are the premier business awards program in the United States. All organizations operating in the U.S.A. are eligible to submit nominations – public and private, for-profit and non-profit, large and small. More than 300 professionals worldwide participated in the judging process to select this year’s Stevie Award winners. “Decision-making and relationship building occur more and more online, which makes a strong social media presence a key part of our U.S. market economy,” Stevie Awards president Maggie Miller says. “This year’s Stevie Awards judges recognized Robert Catalano’s pivotal role in Toshiba’s social media innovation and his marketing acumen.” Catalano particularly won the prestigious national honor by bolstering Toshiba’s social media presence through his original approach and strategic vision. Catalano’s keen understanding of audience preferences and trends enables him to lead compelling campaigns that resonate with Toshiba stakeholders resulting in an 84% year-to-year (from April 1, 2022 to April 1, 2023) increase in social media engagement. “Team Toshiba is proud of Robert for earning the 2024 Gold Stevie for Best Business Influencer of the Year,” states Toshiba America Business Solutions Director of Field Marketing and Events Salley Thornton. “By consistently elevating our organization’s social media presence at an elite level day-in-and-day-out, he is truly deserving of this significant honor.” Catalano is a Rutgers University alumnus (2010) who holds a Bachelor of Arts in communications from the New Brunswick, N.J. university. He is also a baseball enthusiast and New York Yankees fanatic who enjoys spending free time with his wife and two children, which includes occasional visits to Yankee Stadium.
Toyota Material Handling Celebrates 25th Anniversary of SAS during National Forklift Safety Day
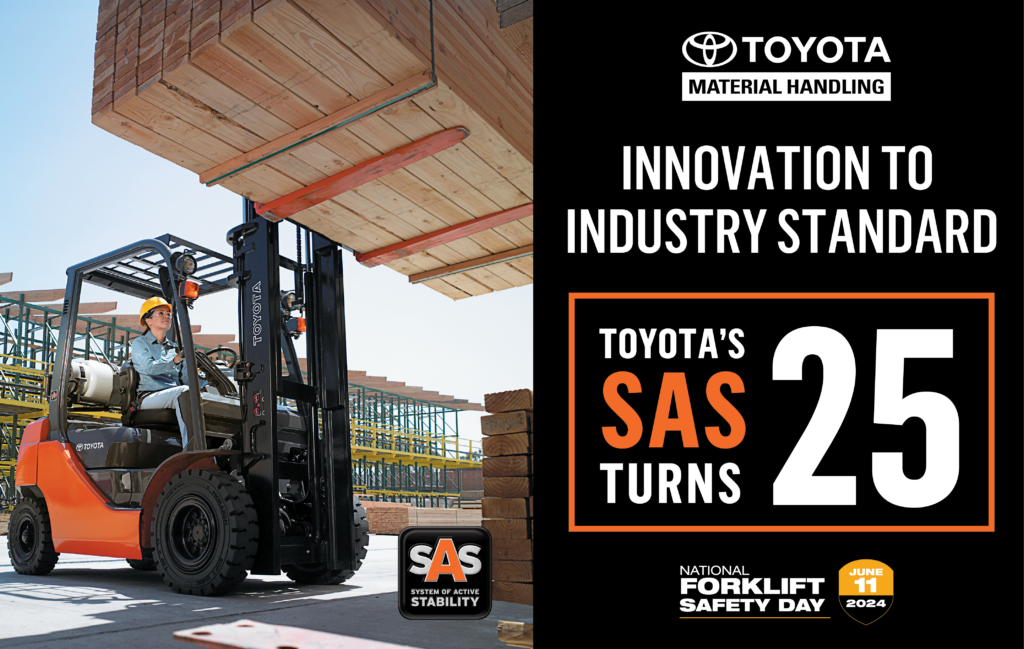
Toyota Material Handling is celebrating the 25th anniversary of its System of Active Stability™ (SAS), which revolutionized the material handling industry by reducing the likelihood of forklift tip over. Commemorated on the 11th annual National Forklift Safety Day, this milestone calls attention to Toyota’s emphasis on empowering customers to foster a culture of safety. As part of this year’s event, Toyota is sharing educational resources with dealers and forklift operators on innovative technology and forklift safety best practices. National Forklift Safety Day, sponsored by the Industrial Truck Association (ITA), is an annual event that educates customers, policymakers, and government officials about safe forklift use and proper operator training. With approximately 4.5 million forklift operators in the workforce, Toyota continues to emphasize the importance of continual safety education. “Since its inception 11 years ago, National Forklift Safety Day has helped drive more discussion about making and keeping forklift safety a core part of every organization’s culture,” said Cesar Jimenez, Toyota Material Handling Vice President of Regulatory Affairs, Product Planning, and Product Assurance. “National Forklift Safety Day helps us reinforce our industry mission and message to provide new and ongoing safety training to forklift operators in all industries.” In addition to SAS, Toyota’s Smart Environment Sensor Plus™ (SEnS+) can assist operators in identifying pedestrians or objects in their path. SEnS+ includes industry-first capabilities, including dynamic zoning, adjustable truck slowdown and backward movement prevention features. These innovative technologies are part of Toyota Assist, a suite of advanced features designed to enhance forklift operability, productivity and situational awareness that are a testament to Toyota’s commitment to promoting safety within the industry. Toyota’s Jimenez and Brett Wood, President & CEO of Toyota Material Handling North America, will play key roles in Tuesday’s event. Wood, currently serving his second term as ITA chair, participated on the committee that established the first National Forklift Safety Day. During his initial tenure, Wood was instrumental in developing the ITA’s economic impact report, Lifting America: The Economic Impact of Industrial Truck Manufacturers, Distributors and Dealers. This report provided the industry with quantifiable statistics, offering valuable insights and emphasizing the importance of safety within the material handling industry. Jimenez, who also has nearly three decades of experience in the industry, has followed in Wood’s footsteps with his appointment as the chair for this year’s National Forklift Safety Day. Jimenez and Wood have been steadfast in their leadership to raise awareness and increase safety standards within the material handling industry. Toyota Material Handling also cultivates a safety-focused culture by offering site surveys, consultations and operator training. By embodying Toyota’s culture of Kaizen – or continuous improvement – and upholding Toyota’s core values, Toyota Material Handling is integral in promoting the vital role industrial trucks perform in manufacturing, warehousing, logistics and distribution. For more resources, visit Toyota Material Handling’s National Forklift Safety Day page at ToyotaForklift.com.
Hyundai Material Handling supports National Forklift Safety Day
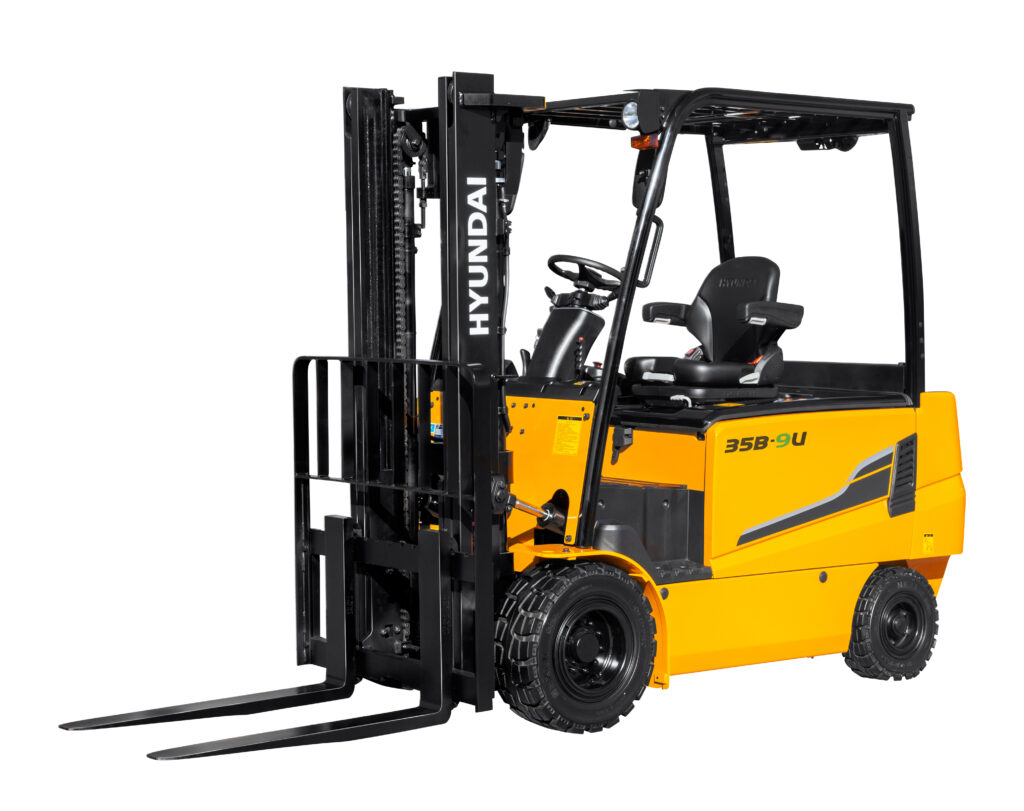
To demonstrate its support of National Forklift Safety Day, June 11, and its commitment to creating safe working environments, Hyundai Material Handling has announced a special offer to purchasers of select, new Hyundai electric forklifts and reach trucks. When purchased between June 11 and July 5, these new Hyundai models will include a free Pedestrian Detection System (PDS). The Hyundai PDS includes both front- and rear-view cameras, an alert voice siren, and a 2-channel monitor. While a $1,500 value, its true value is immeasurable when placed against the possible accidents and injuries it can help prevent. According to the Occupational Safety and Health Administration (OSHA), each year there are between 35,000 and 62,000 forklift related injuries. Many involving bystanders and pedestrians. OSHA estimates that over 70% of these accidents are preventable. “At Hyundai, the safety of operators, pedestrians, everyone in the workplace, is priority #1,” said Lewis Byers, Executive Vice President/COO, Hyundai Material Handling. “Our equipment includes the latest in Operator Presence Safety Systems and the industry’s most innovative safety features. Our free Pedestrian Detection System offer is just one more way we want to help our customers and their employees remain safe on the job.” National Forklift Safety Day was created by the Industrial Truck Association (ITA) in 2014 to advocate safety training and practices and carry that message to government, industry, the media, and the public. “We’re proud to be a member of the ITA.” noted Lewis Byers, “We share its commitment to our industry and the safety of the men and women who operate and work around our equipment. We’re glad to do our part to raise awareness of the importance of workplace safety, while promoting safe forklift operation.”
Brushless DC hypoid gearmotors
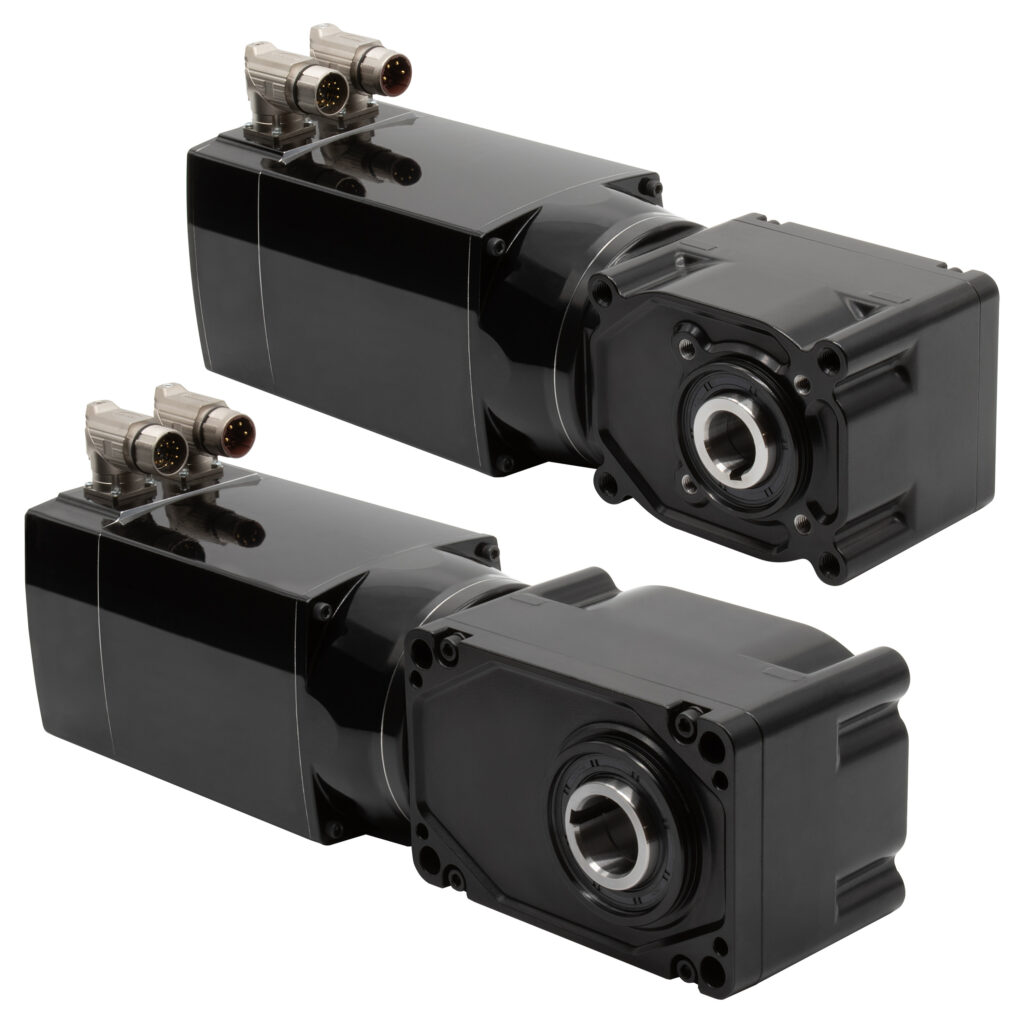
Maintenance-Free. Compact. Efficient. Bodine Electric Company introduced 12 new brushless DC hollow shaft gearmotors with hypoid gearing. These type 42B-25H2 and 42B-30H3 geared motors combine a new brushless DC, 130 VDC motor with two hypoid gearheads. When used with a brushless DC speed control, these gear motors deliver maintenance-free performance with high starting torque and linear speed-torque characteristics. They are ideal for industrial automation equipment that demands quiet operation, high-torque density, and a wide speed range. Quiet, Efficient Performance These new BLDC (electronically commutated) hypoid gearmotors are designed to be high-performance, maintenance-free alternatives to gearmotors with standard worm gearing. The gearmotors are available with gear ratios from 5:1 to 240:1, provide up to 2,370 lb-in (268 Nm) of continuous torque, and speeds of up to 400 rpm. The unique hypoid gearheads are permanently lubricated and feature hardened steel gears for long life and quiet operation. They can be face-mounted in any orientation via four-tapped holes or through bolts. Driven by a maintenance-free, totally enclosed non-ventilated (TENV), 1/2 HP (368 Watts), brushless DC (130 VDC) motor, the type 42B-25H2 and 42B-30H3 gearmotors are ideal for applications that require continuous operation and minimal downtime. These new brushless DC motors feature a built-in 256 PPR, magnetic encoder with commutation track, and are rated IP-66 for protection from dust and water. They are terminated with two built-in watertight connectors (power and signals). Hollow Shaft Design The new type 42B-25H2 (1-inch bore) and 42B-30H3 (1.25-inch bore) hollow shaft gearmotors optimize mounting space, simplify installation, and reduce the number of required parts. They can be connected directly to the driven load eliminating costly shaft couplings and mounting hardware that can be unsafe, bulky, and present alignment issues. These hollow shaft gearmotors offer left- or right-hand face mounts for maximum application flexibility. Gearmotor/Motor Accessories Bodine offers various accessories including a base/foot mounting bracket for each gearhead, shaft kits, and a shaft cover kit for the non-extension shaft side of the gearhead.
Hyster expands forklift operator assist lineup
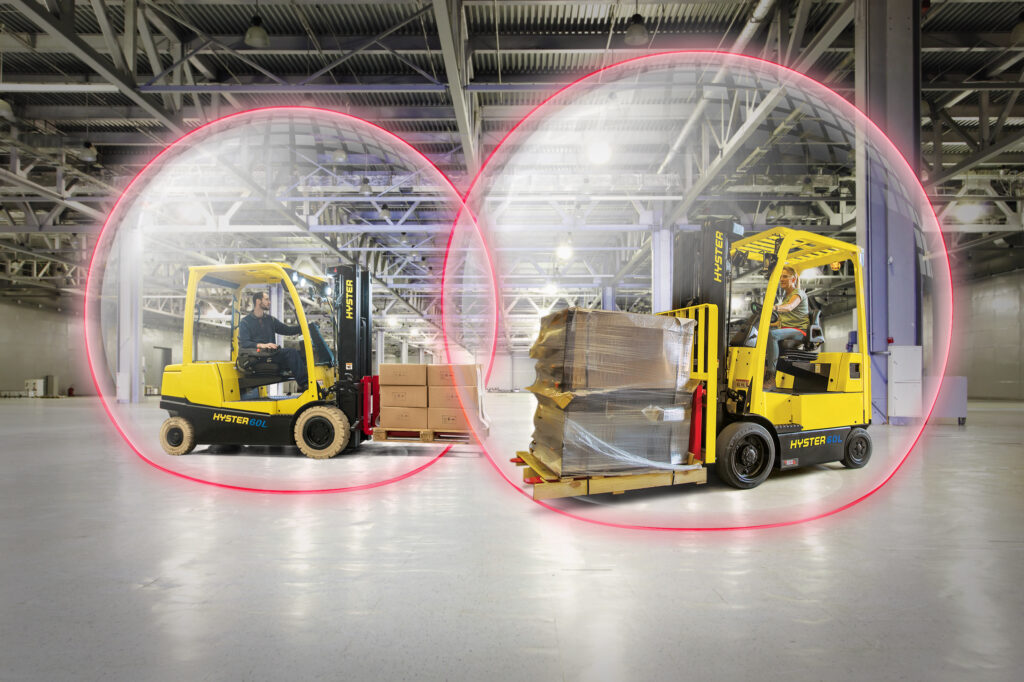
Helping to support safety initiatives in broader range of demanding material handling environments Hyster Company announced two major updates to its operator assist solutions for forklifts, designed to help operators maintain equipment stability and best practices for safe operation. Hyster Reaction™, the company’s operator assist solution, is now available on 59 lift truck models. This selection includes a wide range of electric counterbalanced forklifts with load capacities up to 12,000 pounds designed for the most demanding indoor applications. Not only that, Advanced Dynamic Stability (ADS), one of the foundational technologies in Hyster Reaction, is now available as a standalone option, giving operations the utmost choice to equip their fleets with the technology that best matches their needs. ADS continuously monitors forklift and load status, and automatically applies interventions in response to compromised stability. Previously, ADS was available only when packaged with other technologies as part of Hyster Reaction solutions. The standalone availability provides a more affordable, accessible option for applications that may not warrant investment in the detection technology or infrastructure required for other Hyster Reaction technologies. Since launch, customer deployments of Hyster Reaction technology have accumulated 14 million hours of run time in the field. The full Hyster Reaction suite includes ADS on its own or packaged with one or more technologies, including object detection, proximity detection and real-time location sensing. Hyster Reaction keeps the operator in ultimate control of the lift truck, but depending on the package selected automatically applies interventions in response to compromised stability, obstacles detected in the path of travel or close, and even based on rules specified for certain areas of the facility. Those performance interventions, such as a reduction to travel speed or a smoothing of fork lift or tilt movement, are carefully measured to avoid abrupt shifts or jerks that can upset stability. The changes remain noticeable enough for operators to feel, and the system also communicates the cause through a display screen, providing an additional layer of feedback to help reinforce proper operation established during training. “This month we recognize the 11th annual observance of National Forklift Safety Day, which helps underscore the critical importance of forklift operator training and best practices. As our industry continues to evolve, advanced technology is now capable of complementing those critical, foundational elements of forklift safety,” says Darrell Hinnant, Commercial Director, Emerging Technologies, Hyster. “Tools like ADS and Hyster Reaction are designed according to forklift operator best practices and can help reinforce what operators learned in training with real-time performance interventions on the shop floor.”