GRI expands footprint in South America
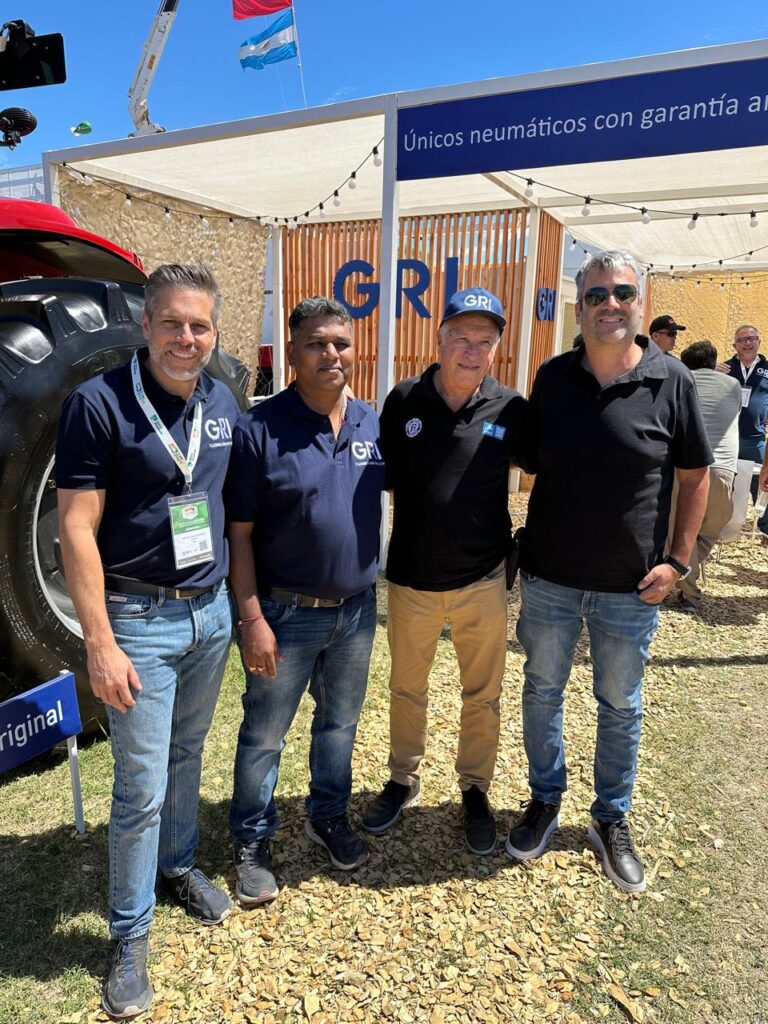
GRI has reached a significant milestone with its successful entry into the South American market, marking a new chapter of growth and innovation for the company in this vibrant region. This expansion highlights GRI’s commitment to global growth in the Specialty Tires sector, supported by a strong sales team and a customer-centric approach. Hernan Acosta, GRI’s partner and head of the South American business, emphasized the strategic initiatives driving the company’s rapid progress and customer satisfaction. “Our entry into South America was a strategic move to establish GRI as a leader in Specialty Tires. We began by assembling a dedicated local team and forming strong partnerships with reputable dealers across 11 countries in the region. This allowed us to establish a robust distribution network and lay the groundwork for market penetration. Our goal is not just to sell Specialty Tires, but to contribute to the region's growth through our focus on sustainability and innovation.” Key initiatives such as comprehensive training programs for dealers, facilitating dealer visits to end-users, and rigorous field tests in critical operational environments have been instrumental in driving GRI’s business growth in both the Agricultural (AG) and Material Handling (MH) sectors. Barry Guildford, Global Commercial Director of GRI, stated, “Our commitment to superior customer service, technical expertise, and high-grade products has enabled us to meet the increasing demand for reliable products capable of withstanding challenging operational conditions across the region. By emphasizing superior value through product quality and exceptional service, we have positioned GRI as a trusted choice for Specialty Tires in South America.”
Diversified Fall Protection appoints Kynan Wynne as company’s Chief People Officer
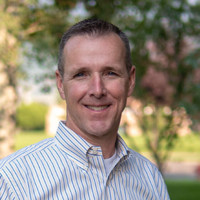
Diversified Fall Protection (DFP) has named Kynan Wynne as Chief People Officer. This marks the first time in the company’s history that an executive has been appointed to this role, a reflection of the company’s commitment to the ongoing support of its employees and dedication to building an empowering culture. “We fondly refer to Kynan as our culture crusader,” said Travis Nelson, CEO of DFP. “We are so fortunate to have someone with Kynan’s experience and people skills to fill this role. This is an uncommon position for a company in our industry, but our people are the most important input to our success, and we know we cannot grow without investing in them. The customer experience is a direct reflection of the employee experience.” Wynne is a well-established industry veteran with nearly 40 years of experience. He most recently served as Chief Sales and Marketing Officer for DFP, a position he has held since late 2021 when he formally became part of the organization as a result of DFP’s acquisition of his company, Rooftop Anchor, Inc. Wynne had founded Rooftop Anchor in 2009 and was CEO before the company became a DFP brand. In his newly created position at DFP, Wynne will be responsible for creating the overall employee experience, guiding career growth, and building upon an existing employee-oriented culture. Wynne will report directly to the CEO with the full Human Resources team reporting to him. “All the business success I’ve enjoyed in my life is a direct result of being surrounded by amazing people,” said Wynne. “When a company is devoted to providing a workplace culture that allows people to grow and thrive, the best version of that person appears. As an employer, it’s our duty to help that along. A Core Value of ours is ‘to take people to higher ground,’ and our goal is to do just that, starting with our own team members.” Established in 1994, DFP currently employs more than 300 professionals across six U.S. locations, serving all 50 states. The company has experienced exponential growth, quadrupling in size since 2019, propelled in part by four strategic acquisitions between late 2019 and 2021 (PEAK Fall Protection, Fall Protection Systems (FPS), Rooftop Anchor, and Versatile Systems, Inc.). Since 2021, DFP has achieved a remarkable 30% growth rate. DFP specializes in partnering with strategic clients as their trusted advisor, assessing fall protection concerns with their fully integrated model, and providing “Fall Protection Partnership for Life” through the servicing of fall protection systems and workforce training. DFP also fabricates and distributes a range of distribution-ready fall protection products under their SafePro brand.
U.S. rail traffic for May and the Week ending June 1, 2024
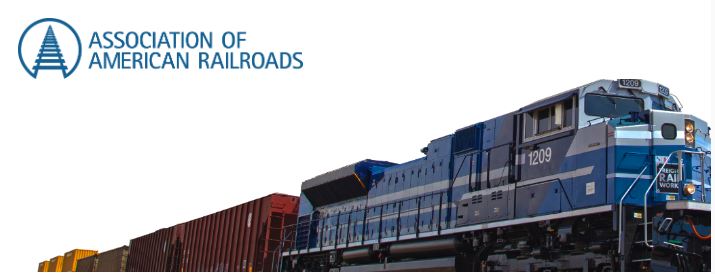
The Association of American Railroads (AAR) reported U.S. rail traffic for the week ending June 1, 2024, as well as volumes for May 2024. U.S. railroads originated 1,060,801 carloads in May 2024, down 6.0 percent, or 67,145 carloads, from May 2023. U.S. railroads also originated 1,281,248 containers and trailers in May 2024, up 7.6 percent, or 90,744 units, from the same month last year. Combined U.S. carload and intermodal originations in May 2024 were 2,342,049, up 1.0 percent, or 23,599 carloads and intermodal units from May 2023. In May 2024, 12 of the 20 carload commodity categories tracked by the AAR each month saw carload gains compared with May 2023. These included: petroleum & petroleum products, up 7,123 carloads or 15.4 percent; chemicals, up 5,023 carloads or 3.2 percent; and grain, up 4,418 carloads or 4.7 percent. Commodities that saw declines in May 2024 from May 2023 included: coal, down 69,404 carloads or 22.0 percent; crushed stone, sand & gravel, down 12,569 carloads or 11.4 percent; and primary metal products, down 3,016 carloads or 7.2 percent. “At first glance, rail traffic in May seems to display mixed signals,” stated Rand Ghayad, Chief Economist of the Association of American Railroads. “While coal’s continued decline has led to a decrease in total carloads, a closer examination reveals that carloads (excluding coal) increased for the fourth consecutive month. Although it is unlikely that we will witness a reversal in coal’s trend, other commodities—such as intermodal traffic and petroleum—hold greater growth potential and will likely be more important strategically for railroads in the future. In May, intermodal traffic spiked, maintaining its upward trajectory over several months. This surge reflects both increased port activity and intensified efforts by railroads to compete in a fiercely competitive market. Additionally, solid volume gains were observed for petroleum products, chemicals, and grain.” Excluding coal, carloads were up 2,259 carloads, or 0.3 percent, in May 2024 from May 2023. Excluding coal and grain, carloads were down 2,159 carloads, or 0.3 percent. Total U.S. carload traffic for the first five months of 2024 was 4,683,510 carloads, down 5.0 percent, or 247,984 carloads, from the same period last year; and 5,568,464 intermodal units, up 8.7 percent, or 443,453 containers and trailers, from last year. Total combined U.S. traffic for the first 22 weeks of 2024 was 10,251,974 carloads and intermodal units, an increase of 1.9 percent compared to last year. Week Ending June 1,2024 Total U.S. weekly rail traffic was 450,077 carloads and intermodal units, up 2.4 percent compared with the same week last year. Total carloads for the week ending June 1 were 206,236 carloads, down 5.9 percent compared with the same week in 2023, while U.S. weekly intermodal volume was 243,841 containers and trailers, up 10.7 percent compared to 2023. Six of the 10 carload commodity groups posted an increase compared with the same week in 2023. They included grain, up 2,947 carloads, to 19,049; farm products excl. grain, and food, up 1,010 carloads, to 16,075; and petroleum and petroleum products, up 927 carloads, to 10,006. Commodity groups that posted decreases compared with the same week in 2023 included coal, down 12,514 carloads, to 51,817; nonmetallic minerals, down 4,514 carloads, to 27,128; and miscellaneous carloads, down 1,306 carloads, to 7,996. North American rail volume for the week ending June 1, 2024, on 10 reporting U.S., Canadian, and Mexican railroads totaled 310,890 carloads, down 2.6 percent compared with the same week last year, and 327,199 intermodal units, up 8.2 percent compared with last year. Total combined weekly rail traffic in North America was 638,089 carloads and intermodal units, up 2.7 percent. North American rail volume for the first 22 weeks of 2024 was 14,459,420 carloads and intermodal units, up 2.0 percent compared with 2023. Canadian railroads reported 88,149 carloads for the week, up 3.3 percent, and 71,065 intermodal units, down 2.0 percent compared with the same week in 2023. For the first 22 weeks of 2024, Canadian railroads reported a cumulative rail traffic volume of 3,544,980 carloads, containers, and trailers, up 0.7 percent. Mexican railroads reported 16,505 carloads for the week, up 13.2 percent compared with the same week last year, and 12,293 intermodal units, up 29.8 percent. Cumulative volume on Mexican railroads for the first 22 weeks of 2024 was 662,466 carloads and intermodal containers and trailers, up 11.6 percent from the same point last year. View reports here
Wauseon Machine to showcase precision machining and fabrication capabilities at Design 2Part Shows (D2P)
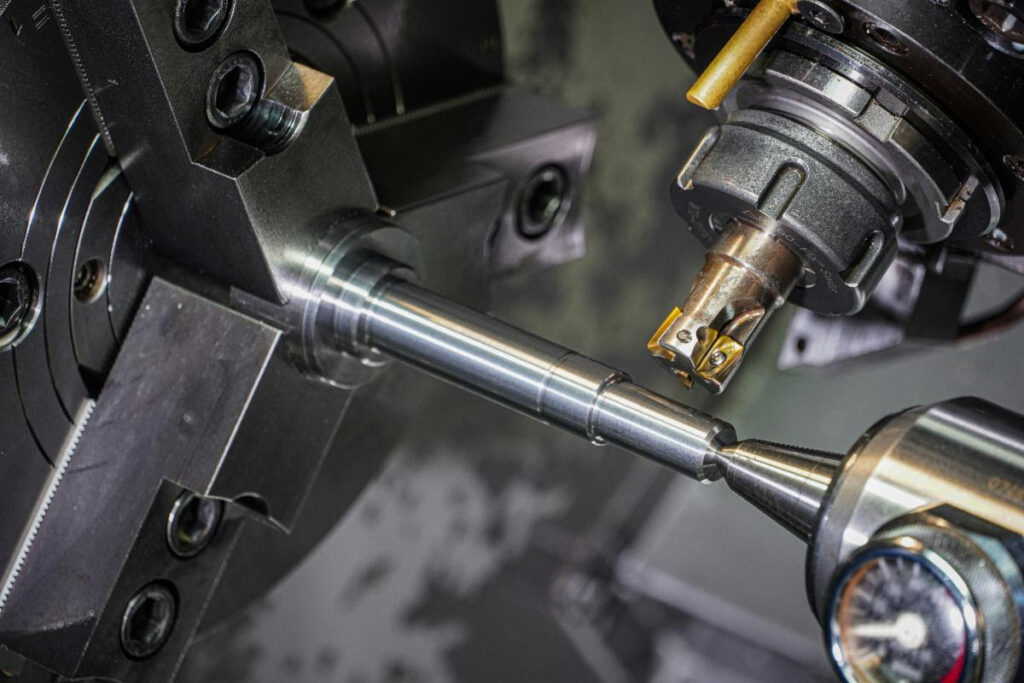
Visit Booth #215 to connect with a Wauseon expert and find your next manufacturing solution Wauseon Machine, Inc. (WM) announced its participation in the upcoming Design 2Part Shows (D2P) in Novi, MI from June 19 – 20. D2P is renowned for providing immediate business opportunities. Moreover, as the only trade show in the region exclusively featuring exhibitors specializing in design and contract manufacturing services, D2P offers a unique platform for networking and collaboration. At the event, Wauseon Machine will highlight its robust precision machining and fabrication capabilities. With over 100 CNC machines and a network of preferred partners specializing in metal fabrication, Wauseon Machine delivers unparalleled value to its customers. Services include laser and die cutting, bending, forming, welding, coating, and assembly, catering to both low and high-volume production needs. Located in the central business hub of Irving, the Irving Convention Center offers easy access and is equipped with state-of-the-art facilities, ensuring a conducive environment for fruitful networking among industry experts. “We are thrilled to participate in the D2P conference and showcase our cutting-edge capabilities in precision machining and fabrication,” says William Johnson, VP of Operations at Wauseon Machine. “Our team looks forward to connecting with other attendees and demonstrating how our expertise can drive success for their future projects.”
New SolarShield™ HMI Clear Cover maximizes visibility even when closed and locked
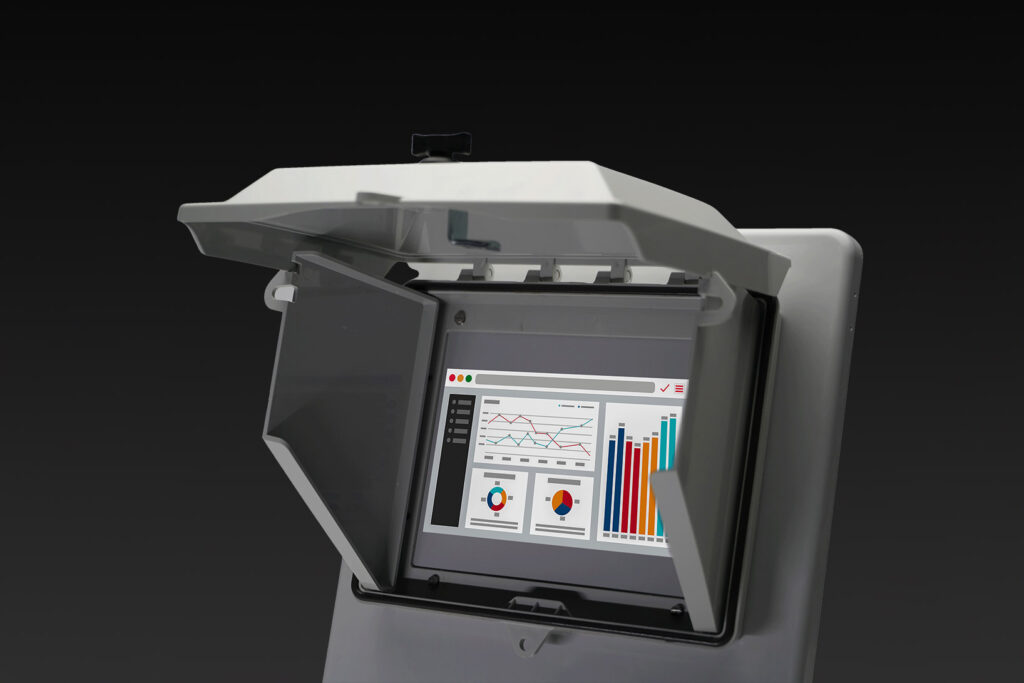
AttaBox® Enclosures has introduced AttaBox SolarShield™ HMI Covers, providing the ultimate HMI screen protection in the harshest of environments. Now, AttaBox is offering the option of a clear cover configuration that maximizes the visibility of the HMI screen while the cover is closed and locked providing the convenience of hands-free viewing. The new AttaBox SolarShield Clear and Opaque HMI Covers offer the most innovative, durable, non-metallic HMI Covers for use with all enclosure material types. The covers are ideal for protecting HMI Screens from UV and harsh environmental conditions and are the industry’s only non-metallic HMI covers with side shields. AttaBox SolarShield HMI Clear and Opaque Covers are designed for reliable performance in non-hazardous industrial and commercial markets including industries such as oil and gas, equipment manufacturing, industrial machines, water/wastewater, marine, and food and beverage. Extremely tough and durable, AttaBox SolarShield HMI Covers can be used in both outdoor and indoor applications. They provide superior protection of the Human Machine Interface (HMI) screens from the sun, dust, water (rain, sleet, snow), sand, flames, oils, chemicals, grease, dirt, foreign objects, and other environmental conditions that cause corrosion and damage. AttaBox SolarShield HMI Clear and Opaque Covers fit standard 8” and smaller HMI screens and maintain a NEMA 4X rating of enclosure when paired with a NEMA 4X HMI device. These universal covers can be used with either non-metallic or metallic enclosures. Among the many performance benefits of AttaBox SolarShield HMI Clear and Opaque Covers: Simple and functional: they are easy to use. A hinged design includes supporting inner doors for hands-free use and better visibility of the opaque HMI screen in the sun. Superior Protection: Maintains NEMA 4 and 4X rating when paired with a NEMA 4 or 4X HMI device. AttaBox SolarShield HMI Covers protect HMI screens and electrical equipment from corrosion and damage due to UV, oils, dirt, and sand and greatly reduce equipment replacement cost. Strength: Impact-resistant but light-weight opaque polycarbonate cover and base construction with UV inhibitors provides long life in harsh conditions. Reliable sealing featuring a robotically applied foam-in-place seamless polyurethane gasket. AttaBox SolarShield HMI Covers come with a stainless steel hardware kit included and are padlock-able for increased security. Installation is simple and easy with the use of common tools. AttaBox SolarShield HMI Covers maintain UL’s best rating: an “f1” per UL 746C (polycarbonate material has passed tests for UV exposure and water immersion). They also conform to the following standards: cURus Listed, UL50e, UL508A, Type 1, 3R, 4, 4X, 12. They provide an Operating Temperature Rating of -40°F to +248°F (-40°C to +120°C). AttaBox Enclosures, a Robroy Industries® brand and manufacturer of high-performing non-metallic electrical and industrial enclosures, has delivered nearly seven decades of reliable service to diverse industries and leads the way in providing application-specific solutions for installations within continuously demanding environments.
E Tech Group acquired Automation Group

E Tech Group announces the immediate renaming of Automation Group to E Tech Group, following the strategic acquisition of Automation Group on October 3, 2023. E Tech Group has announced that the brand formerly known as Automation Group has been renamed as E Tech Group. E Tech Group’s acquisition of Automation Group was finalized on October 3, 2023. Effective immediately, the brand formerly known as Automation Group will operate under the name E Tech Group, unifying the two entities under one market-leading brand. The transition to the new name will be seamless for clients and partners. All existing commitments remain in place, ensuring continuity and stability. “The strategic direction and growth mindset of E Tech Group aligned seamlessly with that of Automation Group. Our company has always placed a strong emphasis on taking care of our people, both internally and externally,” explained Randy Ruano, former President of Automation Group. “Our first core value is being people-focused. During discussions with E Tech Group’s leadership, we identified a shared commitment to prioritizing people, which made the decision to move forward with buyout simple.” The acquisition helped deepen E Tech Group’s reach into the food and beverage as well as data center industries. The brand formerly known as Automation Group has helped E Tech Group expand its capabilities within virtualization, cybersecurity, automation design, networking, and big data. In addition, the acquisition brought 12 locations spread throughout northern and southern California, as well as Denver, Dallas-Fort Worth, Indianapolis and Williamsburg, Virginia. This brand merger is positioned to assist E Tech Group’s offering of ‘main automation partner.’ “This investment marks a significant milestone in our journey as a Main Automation Partner. By integrating the expertise and resources of Automation Group, we’re expanding our portfolio of solutions and services to meet the evolving needs of our clients. This move strengthens our presence in key industries like food and beverage and data centers and enhances E Tech’s automation solutions that our clients know and trust,” said Matt Wise, Chief Executive Officer of E Tech Group. “For our clients, this means access to a broader range of solutions and a seamless experience. For our employees, it opens new avenues for collaboration, growth, and professional development within a larger, more dynamic organization. And for our stakeholders, it positions a bright future filled with innovation, growth, and shared success.”
TerraSource Global announces the acquisition of Peninsula Iron Works
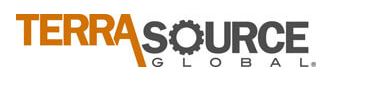
TerraSource Global has announced the acquisition of Peninsula Iron Works (PIW) as of May 31, 2024. Kevin Hambrice, CEO at TerraSource Global, said, “Peninsula Iron Works has a long history of success providing high-quality, US-based manufacturing that complements TerraSource Global’s industrial processing equipment. PIW handles heavy fabrication, machine build, and rebuild work for steel mills, aggregate processing operations, sheet mills, lumber mills, aluminum plants, scrap yards, and more. With one of the largest machining part envelopes, PIW is able to offer unique solutions that other companies cannot. We look forward to working with PIW’s management team as we integrate our areas of expertise into more complete solutions for customers and expand our aftermarket offerings for the aggregates, mining, and forest products industries.” James Johnson, President of Peninsula Iron Works, said, “There is a natural complement between TerraSource Global’s proven, high-quality material handling equipment and PIW’s expertise in large, complex equipment design builds, fabrications, and rebuilds. We are excited to become part of TerraSource Global and partner with their team to serve customers in all corners of the world.”
Episode 491 Embracing Human-Centric Supply Chains with Alcott Global
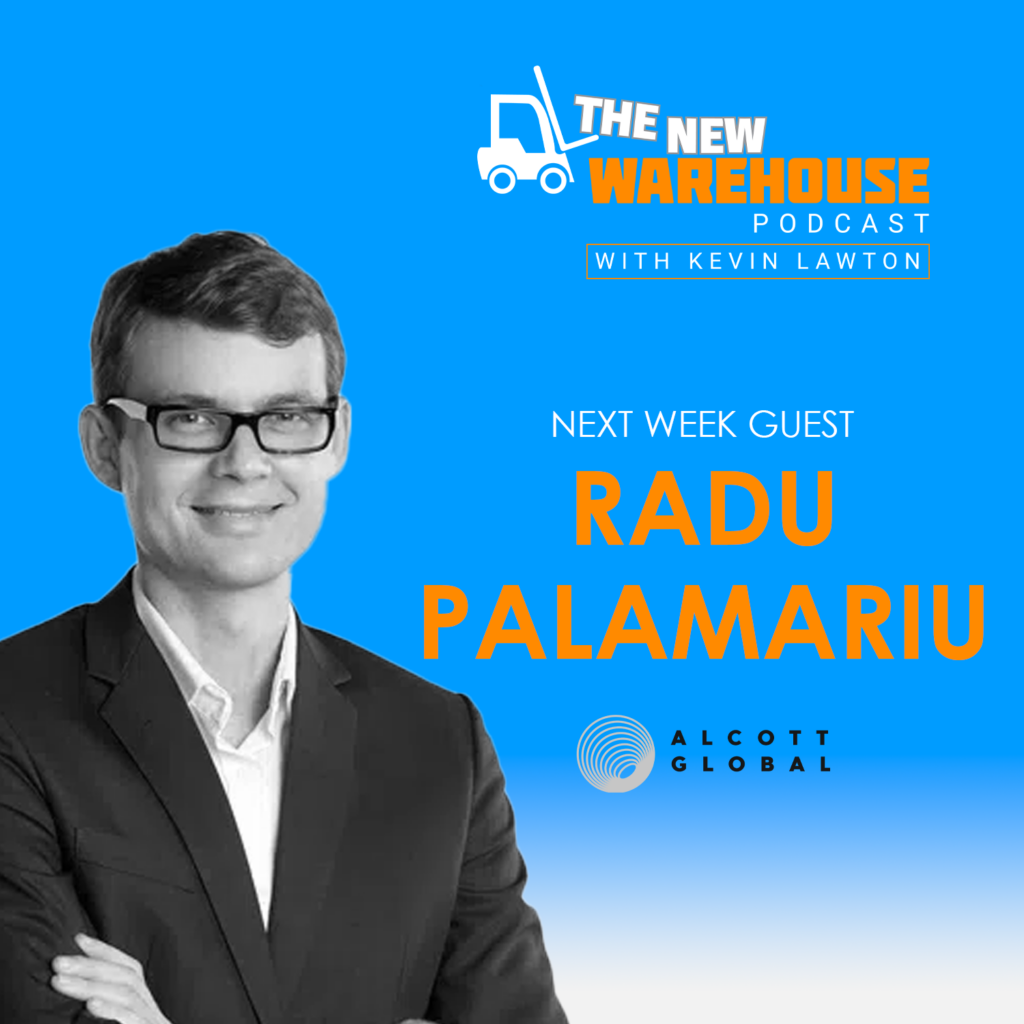
In the latest episode of The New Warehouse Podcast, Kevin sits down with Radu Palamariu, the Managing Director of Alcott Global for Europe and Asia Pacific. Palamariu is an influential figure in the supply chain industry. He is known for his work in executive recruitment, his role as the host of the Leaders in Supply Chain Podcast, and for co-authoring the book From Source to Sold. During the episode, they discuss the vital role of human elements in supply chains, the impact of technology, and the importance of storytelling and soft skills in leadership. The Human Element in Supply Chains Radu Palamariu emphasizes that technology alone cannot drive success in supply chains; it is the people behind the technology who make a difference. He argues, “Technology doesn’t make or break businesses, people do.”This perspective highlights the essential role of human expertise and judgment in leveraging technology effectively. Palamariu’s insights draw from his extensive experience in executive search, where he has seen firsthand the importance of leadership and human capital in operational success. Palamariu points out that while automation and AI are transforming the industry, they do not replace the need for skilled professionals. “The people that are able to make change happen, that are digital savvy, and that have a good understanding of how to combine all of this are more important than ever,” he states. This underscores the need for continuous learning and adaptation among supply chain professionals. The Power of Storytelling in Leadership One of the key themes discussed is the significance of storytelling and soft skills in effective leadership. Palamariu notes, “The best leaders are the best storytellers, able to tell narratives that inspire people and get stuff done.” He explains that successful leaders can connect their technical achievements to broader business goals, such as increasing profitability or enhancing customer service. This ability to communicate and inspire is crucial for advancing leadership roles within the supply chain sector. Palamariu also reflects on his journey and the value of curiosity and learning. His podcast, initially a tool for his education, has become a platform for sharing industry knowledge. He encourages professionals to develop their storytelling skills better to articulate their value and impact within their organizations. Technology as a Tool, Not a Solution While technology is a significant focus in modern supply chains, Palamariu cautions against adopting new technologies without clear objectives. He explains, “Tech is a tool, not the ultimate solution. Unless you have a problem, get very clear on what’s your problem first.” He shares examples of companies implementing AI and other technologies without fully understanding their needs, leading to ineffective solutions. Palamariu advises starting with the problem and then seeking the most appropriate technological tools to address it. He also mentions the importance of data quality, noting that even the most advanced AI cannot compensate for poor data. This pragmatic approach ensures that technology investments are aligned with business goals and deliver tangible benefits. Key Takeaways on Human-Centric Supply Chains Human expertise and leadership are crucial in leveraging technology effectively. Effective communication and storytelling are critical skills for supply chain leaders. The capability to drive change in both large and small to mid-sized companies within a digital-first environment is invaluable. The New Warehouse Podcast 491: Embracing Human-Centric Supply Chains with Alcott Global
IFS launches industrial AI capabilities in latest release of IFS Cloud
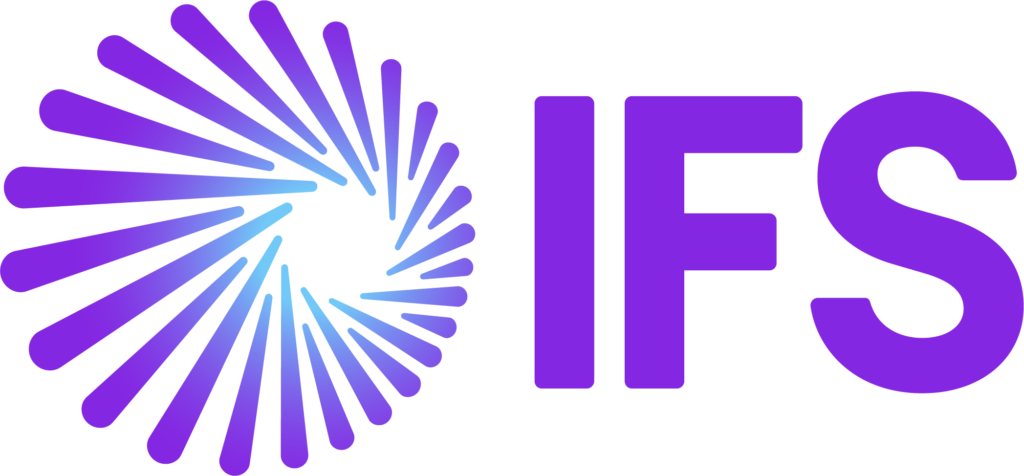
IFS has announced the general availability of its latest IFS Cloud release. As the only vendor focused on helping asset- and service-focused companies leverage the power of Industrial AI, IFS is releasing new AI-powered functionality that enables customers to improve operational effectiveness and profitability. This May release focuses on three strategic themes, which are supported by a powerful IFS.ai Copilot that helps users better understand and use data from across a company’s supply chain and operations. Powering Potential: Humans and Technology in Harmony The power of IFS Cloud extends beyond human potential to asset potential; assets operate optimally, minimizing downtime and extending lifespans, resource utilization is optimized, and operations are streamlined. Key features and capabilities include: IFS.ai Copilot: improve decision-making and enhance user experience and engagement through our AI-powered assistant. The first data source target for this release is IFS Cloud help and support information. Boost productivity through timely knowledge and guidance. Analytics as a Service: gain accelerated time to value and valuable insights while reducing capital expenditure and operating costs. Transport Loading: improve the shipment process, supporting greater capacity utilization, and faster goods loading. Task Bundling for Service: increase technician utilization and efficiency and reduce travel costs and emissions while improving service margins Maintenance Planning and Scheduling new Lobbies: improve visibility, drive efficient asset maintenance operations, and drive asset compliance. Driving Profitability: Winning in a Volatile Landscape Business success hinges not just on potential, but on measurable profitability. This release equips customers to fine-tune global operations, lower costs, reduce waste, and empower the organization to consider new business models. Key features and capabilities include: Supply Chain Customer Scheduling: handle multiple open schedules from the same plant simultaneously, increasing productivity and time savings. Advanced SLA Management: increase margins, SLA adherence, and compliance. Incomplete & Follow-on Process: service management is enhanced with an intuitively guided technician process for reporting to achieve SLA compliance, avoid penalties, and improve customer satisfaction. Business to Business Portal: let contractors record multi-site work, for greater control and visibility while streamlining the communication process between contract and asset owners. Sustainability as a Competitive Edge IFS Cloud empowers businesses to not only achieve sustainability goals but also emerge as champions of environmental stewardship, which will resonate with stakeholders from consumers to investors. Optimizing resource utilization, minimizing waste, and tracking environmental impact lets customers reduce their carbon footprint. Key features and capabilities include: Emissions Tracker: enhancements to accurately track progress against sustainability through easy emissions data collection. Gain a more complete view with the addition of select Scope 3 emissions categories. Also, input kilowatt consumption data from utility supplier invoices. ESG Lobbies: now underpinned by Power BI for easier real-time access to focused insights. Support for Circular Manufacturing: enhancements cut production costs by supporting the planning of the remanufacturing process. This enables the introduction of new revenue streams and lower carbon footprint. Packing Material Management: enable more sustainable operations by handling unit accessories as inventory increasing the use of reusable packaging. Christian Pedersen, Chief Product Officer, at IFS commented: “With this latest release of IFS Cloud, customers will benefit from a new level of meaningful AI capabilities and innovation that is truly relevant to their industry and impactful to their business. The IFS.ai Copilot is the natural next step for IFS Cloud users to engage with and benefit from the AI capabilities we have embedded into IFS Cloud. We’re offering so much more than generic AI—our industrial AI approach means customer can effectively manage supply chains and improve their operations. We’re creating an environment where technology and human ingenuity come together.” Pedersen added: “At a time where regulation in Europe and the U.S. is making companies take action in how they set and manage their Sustainability commitments, we are offering new AI-powered capabilities that both help companies improve their operations and report progress. As we look ahead, it’s clear that IFS.ai will continue to be a catalyst for change, driving businesses forward with purpose and passion within the industrial setting. The future is not just bright; it’s AI-powered, composable, and cloud-enabled, and it’s here now.” IFS.ai applied The new capabilities in 24R1 provide powerful industrial AI functionality, but also packed into the release is new industry-specific tooling. Take for example Aerospace and Defense. New Aircraft Release to Service functionality automatically detects and flags missing mandatory components and overdue maintenance tasks for compliance and risk reduction, and Aircraft Airworthiness Status Insights provides visibility and control of fleet status and aircraft in maintenance to enable aviation operators with additional efficiency and productivity gains. The new release offers similar benefits to customers in other asset and service focused industries.
Seeq selected for Enterprise-Wide Analytics
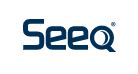
The Seeq platform will be leveraged to maximize production and enhance efficiency across Equinor’s global assets. Seeq and Equinor have announced a multi-year commercial agreement for the Seeq Industrial Analytics and AI platform to be leveraged across Equinor’s global assets to further accelerate digital transformation outcomes. Through the agreement, Equinor will implement Seeq to empower its engineering teams to optimize production and improve energy performance across a variety of assets. Initially, the company plans to leverage Seeq to monitor well and process behavior, thereby gaining a deeper understanding of daily operations to maximize production, enhance workforce collaboration and increase efficiency. “Innovative energy organizations like Equinor want to leverage interoperable systems that utilize collective knowledge to accelerate value,” said Dr. Lisa Graham, CEO at Seeq. “Seeq is honored to provide our open, industrial analytics and AI SaaS platform to Equinor to drive rapid, enterprise-wide digital transformation outcomes.” Seeq delivers a self-service, industrial analytics and AI platform that accesses and leverages vast amounts of historically underused data. By incorporating leading-edge technologies, including AI, machine learning and other capabilities, into its platform and leveraging its global partner network, Seeq powers a range of use cases for employees across the enterprise to accelerate digital transformation outcomes such as operational excellence and profitability, workforce upskilling, and sustainability.
Women In Trucking Association has announced continued Gold Partnership with Great Dane
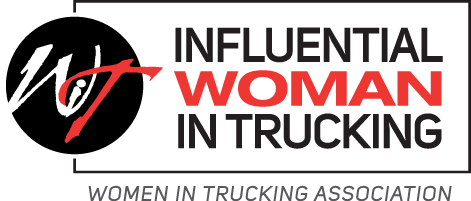
The Women In Trucking Association (WIT) has announced that Great Dane has renewed its Gold Level Partnership. This partnership is vital to the advancement of the non-profit organization’s mission to encourage the employment of women in transportation and logistics, celebrate their success and minimize the obstacles they face. This is the tenth consecutive year that Great Dane has supported WIT as a gold level partner. In addition to providing financial support, the company actively participates in the association. Laura Roan Hays, Sales Enablement Manager at Great Dane, serves on the WIT board of directors. “We’re proud to partner with Women in Trucking and support women who are making significant strides in the trucking industry, contributing their skills and dedication to the field, and ultimately changing it for the better,” said Roan Hays. “Additionally, the professional relationships formed through WIT membership provide encouragement and support, playing a crucial role in helping women in trucking excel in their careers.” “We’re grateful for Great Dane’s involvement and dedication to creating more gender diversity in the transportation industry,” said Jennifer Hedrick, WIT president and CEO. “It’s with supportive partnerships like this WIT can truly make a significant difference in the industry.” With a history dating back to 1900, Great Dane has established itself as a transportation solutions leader – delivering innovative products and exceptional services that help move America forward. Great Dane not only engineers durable and high-quality trailers and truck bodies but also fosters relationships with customers and industry partners that last the long haul. Founded in 2007, the Women In Trucking Association is a resource for more than 8,000 corporate and individual members located in the United States, Canada and Mexico, as well as Japan, Australia, Sweden, South Africa and New Zealand. Recent accomplishments include: releasing the 2023 WIT Index, the official barometer to benchmark and measure the percentage of women who make up critical roles in transportation each year, which had more than 300 company participants; awarding a deserving member a 2018 Volvo VNL670 in collaboration with Arrow Truck Sales, Inc.; honoring 300-plus leaders in transportation through several programs; and more than 1,900 registered attendees at the 2023 Accelerate! Conference and Exhibition.
Port of Long Beach presents $300k in scholarships
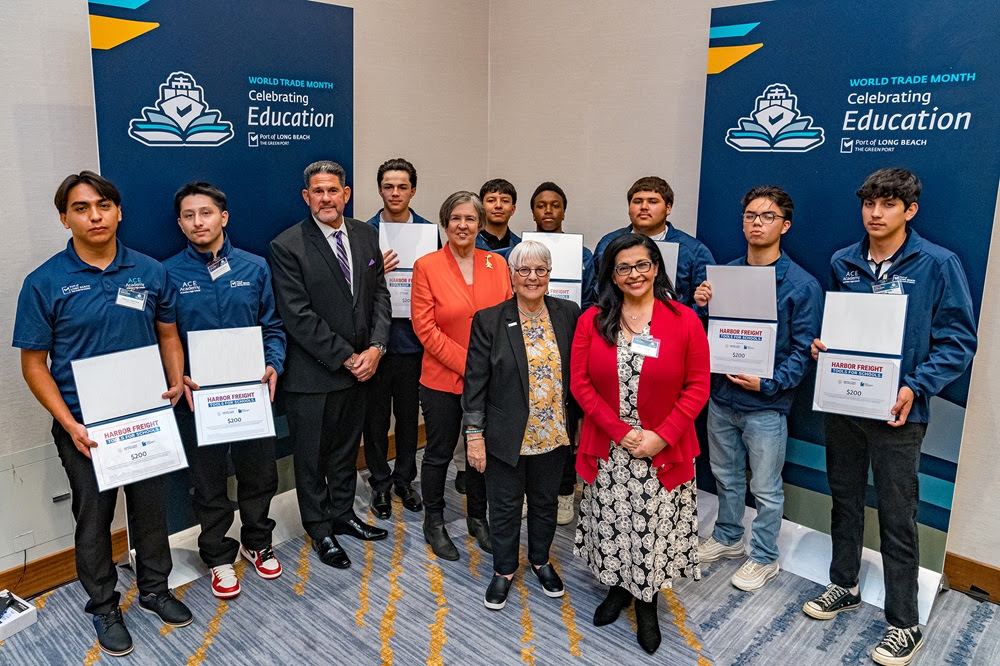
136 local students receive assistance to study in trade-related fields The Port of Long Beach this week awarded $300,000 in scholarships to 136 high school and local college students to assist in their pursuit of education and training in port-related fields including engineering, environmental science, maritime law and technical trades. The scholarships were announced at the annual Celebrating Education event, which brings together students, educators, public officials and business leaders to highlight the Port’s education outreach programs and recognize the accomplishments of students involved. “It’s important to invest in the future workforce of the goods movement industry, right here in the city,” said Long Beach Harbor Commission President Bobby Olvera Jr. “Scholarships are an important way to nurture a labor pool with the talents and skills to keep cargo moving efficiently through our trade gateway.” “We’re building the future of our industry at the Port of Long Beach with new ideas and innovative technologies,” said Port of Long Beach CEO Mario Cordero. “Developing a skilled workforce through our comprehensive education program is a big part of making that happen.” Since 2014, the Port has awarded more than $1.4 million in scholarships to students pursuing careers in international trade and goods movement. This year’s scholarships went to students from local high schools, Long Beach City College and Cal State Long Beach. This year’s budget for scholarships was $300,000, up from the previous year’s $250,000. In an expansion of its commitment to supporting education outreach and workforce development, Olvera also announced Wednesday the Port is creating a new Tools Scholarship designed to assist new and aspiring tradespeople in launching their careers. The scholarship will help new Long Beach City College trades program students and graduates buy their first set of tools. At the Celebrating Education event, Olvera also awarded 10 students from the ACE Academy of Jordan High School with $200 Harbor Freight Tools gift cards. The gift cards were donated by the Harbor Freight Tools for Schools program to the Mayor’s Fund for Long Beach, which facilitated the gift cards free of charge.
Nucor acquired manufacturer of high-performance commercial doors
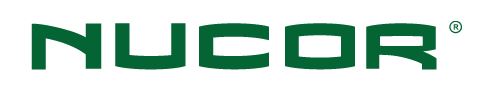
Nucor Corporation announced it has agreed to acquire Rytec Corporation, a manufacturer and seller of high-speed, high-performance commercial doors. The all-cash transaction is valued at $565 million, which represents approximately 12.5x Rytec’s estimated 2024 EBITDA. With over 300 teammates operating out of two manufacturing facilities in Wisconsin, Rytec is widely considered to be the pre-eminent brand for high-performance commercial doors. “Rytec is a leader in high-performance commercial doors and serves several growing end-user markets. This acquisition further executes our strategy to expand beyond our core steelmaking businesses into related downstream businesses. Adding high-performance doors will create cross-selling opportunities with other Nucor businesses and greatly expand Nucor’s product portfolio serving the commercial arena,” said Leon Topalian, Chair, President and Chief Executive Officer of Nucor. “Rytec has a strong cultural fit with Nucor, and we are excited to welcome the Rytec teammates to the Nucor family.” Rytec produces high-speed Spiral® rigid rolling doors for warehouses, manufacturing facilities, auto dealerships, and parking garages, as well as durable fabric doors for cold storage/food and beverage, manufacturing, and clean room applications. The company has a strong focus on product development and has invested significantly in technology and automation to improve quality, increase efficiency, and enhance safety. “We are excited to work with the incredible team at Rytec. Their products are a natural platform for expanding Nucor’s overhead door product suite. Rytec has established itself as the premier brand in high-performance commercial doors, with a strong reputation for quality and best-in-class customer service. The combination of Rytec with C.H.I. Overhead Doors will create an overhead door platform that will deliver superior product breadth and solutions to Nucor’s commercial customers,” said Chad Utermark, Executive Vice President of New Markets and Innovation for Nucor.
Women In Trucking Association announced its June 2024 Member of the Month
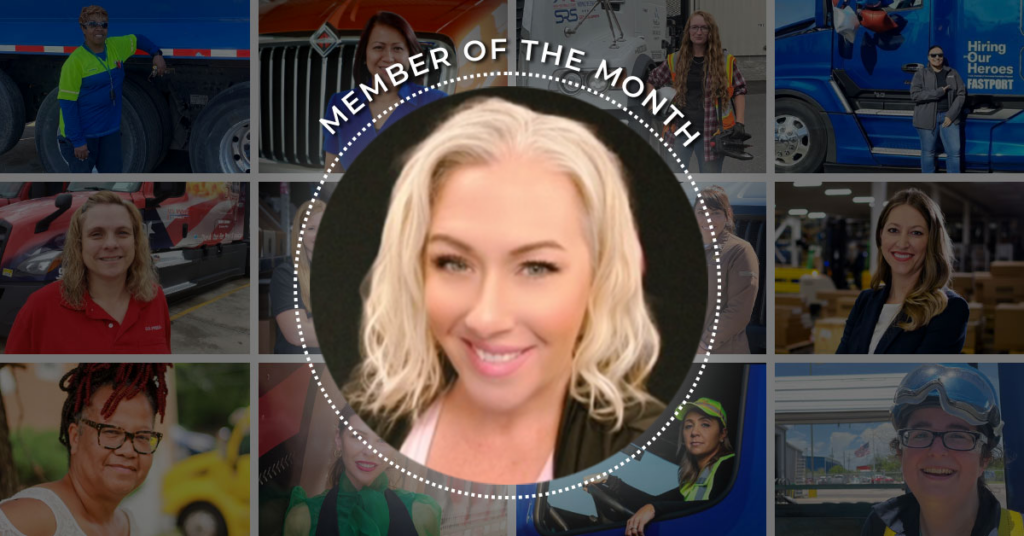
The Women In Trucking Association (WIT) has announced Christina Parrillo as its June 2024 Member of the Month. Parrillo is the Field Services Midwest Branch Manager at Clean Harbors. Growing up, Parrillo desired to be a pediatrician and began the pre-med track at the University of Michigan. However, about two and a half years in, she had a change of heart. Being what she believes is a “science nerd,” she took interest in a class on hazardous waste management. The course was only offered at certain times because the professor who taught it actively worked in the industry. She eventually took an internship with that professor, and they hired her at the end of the internship. At that time, the only position open was for Rodman and she took it, beginning her career in the industry which ultimately led her to Clean Harbors. Parrillo’s journey is a testament to her resilience and gratitude. In a world where adversity often tests one’s resolve, she has risen above life’s challenges, leaving an indelible mark on society. Her story is about determination and a profound gratitude for her accomplishments. As a female leader at Clean Harbors, she has overcome adversities and significantly impacted her career, embodying the essence of gratitude in all aspects of her life. As an inspiring female leader, Parrillo has embarked on a path of professional excellence. With unwavering determination, she has continued to climb the corporate ladder at Clean Harbors while significantly impacting the employees she is surrounded by. For Parrillo, the hazardous waste industry is a dirty job, especially in field services and she believes it can be draining not only mentally but physically at times. Parrillo has channeled her experiences into a driving force, propelling her and her team, which she cares deeply for, towards success. Parrillo was the first female in the Great Lakes division to be promoted to branch manager overseeing the field services line of business. With more than 15 years of experience in multiple leadership roles, Parrillo leads one of seven employee resource groups, WAVES (Women Advancing Our Values in Environmental Services), across an organization of 22,000 employees. She has been a pivotal leader in significantly impacting the females of Clean Harbors by implementing female-fitted uniforms while cultivating a culture of psychological safety for the WAVES members she serves within the workplace. Aside from her everyday role as a branch manager, Parrillo also manages multiple drivers while ensuring her customers are receiving the highest level of service from her team. The two things she loves about her job are working for an environmental company that makes a difference and that no two days are ever the same. Parrillo appreciates the sense of sisterhood between women in the industry, as it fosters a sense of unity, support, and understanding that can enhance productivity and collaboration. While women often face unique challenges and barriers in the workplace, she believes having a strong network of supportive women can make all the difference. “As a woman, I have learned from others through their experiences, challenges, and skills, gaining great respect and knowledge for what we do in this industry,” said Parrillo. Parrillo would like women interested in the trucking industry to know that it is great industry, but sometimes you might need to have thick skin saying, “get the lay of the land and know when to pick your battles. You have several sources you can pull from to get any help or information you might need.”
Bonus Episode: Gen AI in the Warehouse at Momentum 2024
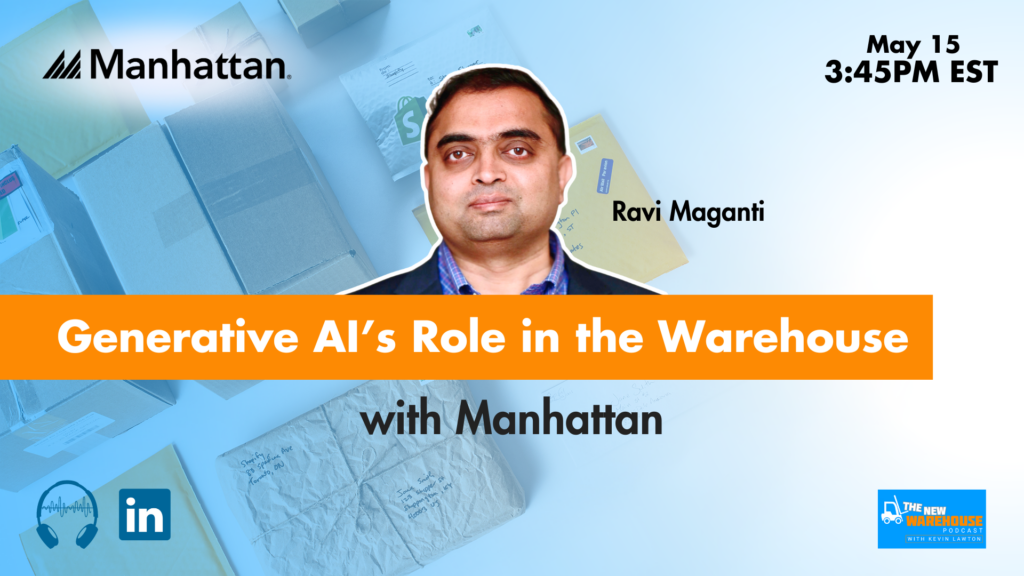
On this bonus episode of the podcast, we are talking AI in the warehouse with Ravi Maganti from Manhattan Associates. This conversation was originally broadcast live at Momentum 2024 where AI was certainly a large topic of conversation with Manhattan announcing their generative AI approach to the warehouse called Manhattan Assist. One of the top questions I get from people both in the industry and outside the industry is “how is AI coming into the warehouse?” so I was very excited to have this conversation and get the answer. What is Generative AI? With AI or artificial intelligence becoming so prevalent in our world, not just a specific industry, there is a lot of talk about what AI can do and what AI even is. There are multiple different types of AI and applications that Ravi gives us definitions of and examples of in the conversation, however, we are focused on generative AI in this use case. The easiest way to think of generative AI is ChatGPT, which is a generative AI platform and what Ravi compares to “the mobile phone revolution” with its prevalence in today’s society. The true definition is where multiple sets of existing data are taken and can then be used to generate new content whether it is text, images, video or other examples. This is very similar to what you might see from a chat interface where you ask a question and the generative AI platform will return information to you based on what you have asked. How Generative AI is Coming Into the Warehouse Now, how is generative AI coming into the warehouse itself? With Manhattan’s recent launch of Manhattan Assist, which has been in development for over a decade and was teased last year at Momentum, generative AI has now found a home in the warehouse. Through their first launch of Assist to their Manhattan Active users they are giving access to Assist on every part of the Active platform allowing users to dig into configurations on any screen. This takes away multiple different points at which interaction would be needed from a support level. Now that configurations can be dissected to the level the user needs right in an easy-to-access chat system they can get on with their work and not run into potential roadblocks. One of the benefits of Manhattan Active is being able to have access to new features every 90 days without any updates or implementations. With so many features coming on line at a frequent pace, a user can now easily understand them and how to put them into place for themselves with Manhattan Assist. Starting at this higher level and foundational system configuration level is a big win for those operating on Manhattan Active and will be a big foundation for what’s to come from Manhattan Assist. Key Takeaways Generative AI is what most think of when they think of AI (like ChatGPT) and Ravi explains how Manhattan has developed their large language models (LLMs) over time to deliver Manhattan Assist. Manhattan Assist is Manhattan Active’s newest feature that brings Generative AI into the warehouse and helps to breakdown configurations on any aspect of the platform in easy to digest ways. Manhattan Assist is just the start of what Generative AI can do in the warehouse and the continued learning and evolution of the platform will increase the ability of the user to be better informed and make better decisions. The New Warehouse Podcast Gen AI in the Warehouse at Momentum 2024
Combilift launches National Forklift Safety campaign
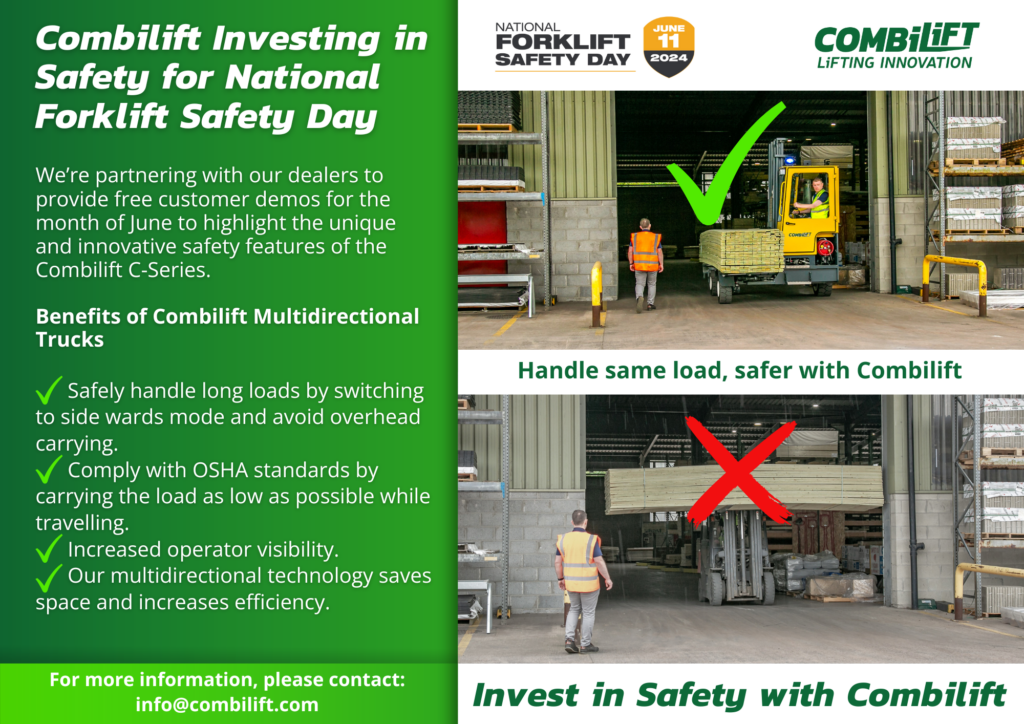
“Lift Your Standards by Lowering Your Load” Combilift has announced the launch of its new National Forklift Safety campaign, “Lift Your Standards by Lowering Your Load.” This initiative aims to enhance awareness and promote best practices in forklift safety across industries. Forklift safety is of paramount importance to Combilift, and every year, we are committed to using National Forklift Safety Day (NFSD) as a reminder of how forklift operations can and should be safer than ever. This year, the NFSD falls on the 11th of June and in line with this, we are taking the opportunity to make June a safety-focused month. Throughout June, we are partnering with our dealer network to provide free demonstrations to our customers to highlight the safety benefits of the multidirectional Combilift C-Series. To maximize the campaign’s impact, Combilift is reaching out to media outlets and industry partners to help spread the word. We are excited to share our campaign flyer and video, which provides essential safety tips and guidelines for forklift operators and employers. Key Points of the Campaign: Safety First: Emphasizing the importance of maintaining a lower load height while traveling to improve visibility, stability and reduce accidents. (In compliance with OSHA standards, which mandate keeping the load as close to the ground as possible during travel) Training and Education: Offering comprehensive training programs to ensure that forklift operators are well-equipped with the knowledge to perform their duties safely. Industry Standards: Advocating for adherence to national and international safety standards in material handling operations. We kindly request your support in sharing this flyer through your platforms, newsletters, and social media channels. By doing so, you will be contributing to a safer working environment for forklift operators and helping to prevent workplace accidents.
Safety 2024 in Denver will feature Society’s largest ever expo
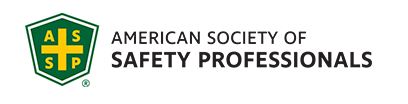
The American Society of Safety Professionals (ASSP) continues its planning for this summer’s Safety 2024 Professional Development Conference and Expo, which will feature a dynamic expo that is expected to be the Society’s largest ever. ASSP’s signature workplace safety education event will take place at the Colorado Convention Center in Denver from Aug. 7-9. “Our expo is so engaging and illuminating that some safety and health professionals just come to the conference for that,” said ASSP President Jim Thornton, CSP, CIH, FASSP, FAIHA. “It’s a remarkable space that showcases the latest personal protective equipment, product innovations and professional services that can advance occupational safety and health.” ASSP’s largest expo to date was at Safety 2019 in New Orleans that involved more than 600 vendors and covered nearly 120,000 square feet. Safety 2024 is already approaching those record numbers with more than two months of preparation remaining. The largest Safety 2024 exhibitors by floor space are Ergodyne, ERGOMAT, Milwaukee Tool, SureWerx, Bulwark Protection, Applications International Corporation, GlenGuard and Protective Industrial Products. Other prominent exhibitors include Airgas, Grainger, Red Wing Brands of America, Superior Glove and VelocityEHS. The expo floor will include an expanded ASSP Career Advancement Center that has something for all attendees, not just those looking for a new position. There also will be a “Leaders in Safety Tech” area where exhibitors on the forefront of safety innovation demonstrate their advancements. Three locations on the expo floor will feature fast-paced “flash sessions” that tackle safety challenges with research, best practices and audience participation. “Our interactive expo has always been a key element of the overall in-person experience,” Thornton said. “I truly believe it’s a can’t-miss opportunity for anyone whose responsibilities include worker safety and health.” Thousands of safety and health professionals from around the world look to ASSP’s annual conference – now in its 63rd year – to advance their careers and take advantage of networking opportunities that can help elevate safety at their companies. Attendees will also be inspired, entertained and informed by popular general sessions. Safety professionals can register online and earn 1.5 continuing education units (CEUs) for career advancement. Groups from the same company can save even more on registration by contacting ASSP’s Nancy O’Toole at 847.768.3466
Toyota Material Handling adds to its North American Headquarters with $100M expansion project
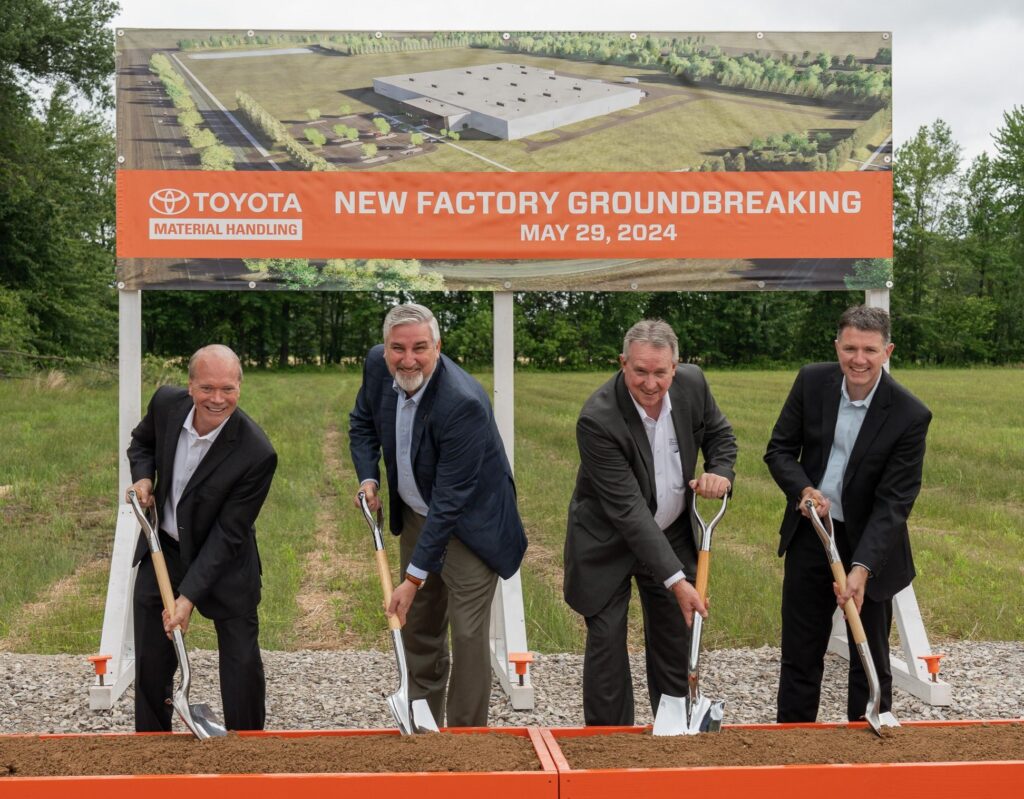
Company officially breaks ground on new factory, which will be used for electric forklift production Toyota Material Handling, the North American leader in material handling solutions, proudly announced a significant expansion to its Columbus, Indiana headquarters during a groundbreaking ceremony on Wednesday. The company – which first began building forklifts in Columbus in 1990 – is investing nearly $100M for a new 295,000 square-foot manufacturing facility dedicated to producing electric products. This expansion marks another milestone in Toyota’s growth as a company and its longstanding partnership with the state of Indiana, and highlights the organization’s commitment to innovation, sustainability, and solving customer problems. “We are excited about this significant strategic expansion to our Columbus campus,” said Tony Miller, Toyota Material Handling Senior Vice President for Engineering, Operations & Strategic Planning. “At Toyota, we will always be driven by what is best for our customers. Electric products are more popular than ever, and we are committed to doing whatever it takes to keep up with increased demand. This new factory will allow us to deliver those electric units to customers faster than we can today.” The project will allow Toyota Material Handling to add 85 new jobs by the start of production in June 2026. “Indiana has made it a strategic priority to cultivate the economy of the future, and we continue to see impact of our work thanks to the partnership of great companies like Toyota,” said Indiana Governor Eric J. Holcomb, who attended the groundbreaking event on Wednesday. “We’re so grateful to see Toyota continuing to invest heavily in southern Indiana. Toyota’s been a cherished partner and career cultivator to the State for the last 35 years, and we look forward to strengthening our bond even more in the decades to come in and around the Columbus region. Today’s remarkable announcement shows yet again just how important our state’s business friendly environment – focus on long-term success and access to a skilled workforce – is to companies seeking to expand and grow far into the future.” The decision to invest an additional $100 million in a new factory underscores Toyota Material Handling’s dedication to advancing sustainable technologies and meeting the evolving needs of its customers. The facility will allow Toyota to leverage cutting-edge manufacturing processes to produce electric products much more quickly than it can today, while meeting the high standard of quality customers expect from Toyota. “Electric forklifts make up 65% of the North American market and this trend towards electrification in the material handling industry will continue to grow,” said Brett Wood, President & CEO of Toyota Material Handling North America and Senior Executive Officer for Toyota Industries Corporation (TICO). “We hope this announcement shows our industry-leading dealer network and our customers that we are a proactive company, not a reactive one. We do not just plan for next week or next year – we’re preparing for the next decade, and this new initiative perfectly represents our commitment to that strategy. This investment is one of the largest in our history and signifies TICO’s commitment to the North American market, the state of Indiana, the city of Columbus, and most importantly, our dealers and our customers.” This is far from the first time Toyota Material Handling has reinvested in its North American headquarters. Since first establishing its presence in Columbus in 1990, Toyota has been a cornerstone of the local community and an integral part of Indiana’s manufacturing landscape. At the time, Toyota Material Handling was split into two separate companies. The sales and marketing arm of the company – formerly Toyota Material Handling U.S.A. (TMHU) – was headquartered in Irvine, California, from 2002 until 2012, when it relocated to Columbus as part of a $4.6M expansion. In 2015, Toyota completed a $16M expansion to add more than 50,000 square feet to its facility, including a two-story office building, a new cafeteria, storm shelter and locker rooms. In 2017, the company opened a state-of-the-art wellness center – the Toyota Recreational Complex (T+Rex) – to provide its employees with more easily accessible health and wellness opportunities right on the Toyota campus. The 35,000 square-foot facility features two basketball courts, an indoor track, an exercise room, a recreation room, and more. The T+Rex facility offers all of the amenities of a modern fitness center including a yoga room, free weights, treadmills and other fitness equipment. It also includes a medical center to provide primary health care, wellness coaching, physical therapy and a pharmacy at no cost to Toyota associates and their families. Later in 2017, Toyota invested another $17.5M to add more than 150,000 square feet to improve internal and external logistics at the facility by consolidating external warehouses to internal storage and distribution on site. The same year, the company also invested $7.3M to acquire the neighboring property and expand its footprint by 200,000 square feet. The acquisition allowed the company to relocate and renovate its aftermarket parts distribution center to provide customers the parts they need more quickly. Including the newest project, Toyota has completed more than 15 total expansions in 34 years, with over $400M in total investments. When the new factory is complete, Toyota’s Columbus footprint will grow to nearly 1.8M square feet – more than six times larger than the 280,000 square-foot facility it opened in 1990. “I’m very pleased to see Toyota continue to grow in the Columbus community”, said Columbus Mayor Mary Ferdon. “Beginning in 1990 when Toyota built their initial plant in Columbus, we’ve seen the impact the company has had on the area through the high-quality careers they provide, and through the work they’ve done for Columbus and Bartholomew County. Toyota is a wonderful community partner providing financial resources and volunteers to organizations throughout the community. We look forward to this expansion and our continued relationship and partnership with Toyota as we build a prosperous community for all.”
Generix named in the 2024 Gartner® Magic Quadrant™ for Warehouse Management Systems (WMS)
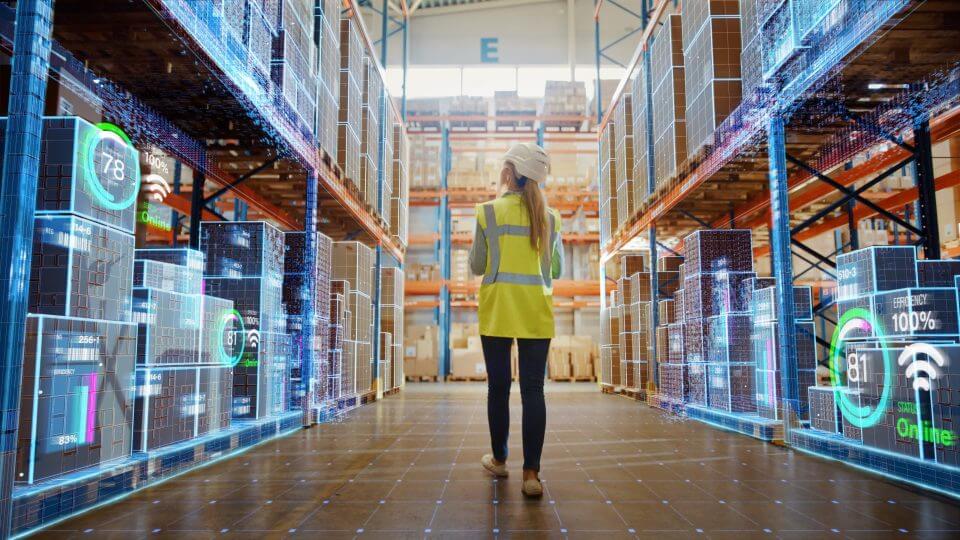
For the sixth consecutive year. In a dynamic market where AI and the Cloud reign supreme, Generix reaffirms its commitment to innovation, bolstering its SaaS solutions to maintain leadership in the supply chain execution domain and cater to its 500+ WMS customers globally. With approximately 2,000 warehouses operating daily with its two distinct WMSs, Generix WMS and SOLOCHAIN, the company remains dedicated to maximizing warehouse efficiency and performance. With a broad and deep functional scope coupled with standardized processes, Generix WMS solution covers the needs of companies across a wide spectrum of industries, often dealing with complex operations. In addition, SOLOCHAIN WMS solution offers complete flexibility and is designed to simplify business process integration with powerful visual tools. The synergy between Generix WMS and SOLOCHAIN offers comprehensive solutions tailored to diverse industry needs, including stored, cross-dock, e-commerce, and multi-customer flows. Generix’s commitment to innovation and sustainable growth remains unwavering. The strategic investments in research and development (R&D) have started to generate results. These investments reinforce Generix’s mission to digitally connect all businesses together across global value chains. “We are honored to be recognized in the Magic Quadrant™ for the six consecutive year. We believe this underscores our relentless commitment and efforts to empowering companies across industries to continuously innovate their warehouse operations, digitize their key business processes and continuously optimize their overall performance. From our perspective, the analysis of our two WMSs is a strong marker of our technological shift and the acceleration of better data exploitation with AI to best serve our customers.” comments Si-Mohamed Saïd, Chief Marketing & Product Officer.
Hangcha Forklift Canada partners with EMU for Circuit Gilles Villeneuve Race
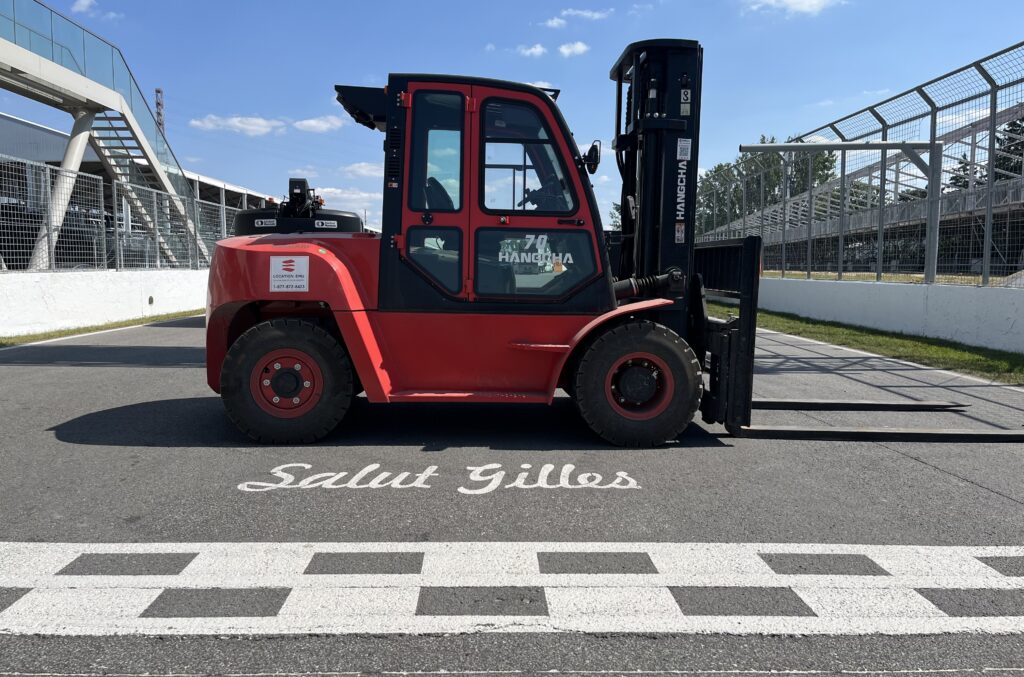
Subsidiary of the esteemed Hangcha Group and its exclusive Québec dealer prepare for June event Hangcha Forklift Canada has announced its partnership with Équipements EMU as the forklift service provider for the Circuit Gilles Villeneuve Race, scheduled for June 7-9, 2024. This marks the second consecutive year the companies will be collaborating for the Montréal-based event deploying several dozen forklifts on-site to ensure seamless operations for both the set-up and post-race disassembly. The race held at Circuit Gilles Villeneuve is an annual motor racing event established in 1961. Located on a man-made island in the St. Lawrence River, Circuit Gilles Villeneuve is renowned for its iconic venue. In 2023, a staggering 345,000 race fans attended the event over three days, solidifying its status as a cornerstone in the motorsport calendar. Hangcha Canada and EMU, both based in Québec, are ideally positioned to support the event’s logistics. “We’re thrilled to return for another year as the race’s forklift service provider. Last year, the team brought over 35 Hangcha forklifts that worked in the paddocks serving all race teams,” says Louanne Rioux, Sales and Marketing Director at Hangcha Canada. “It sweetens the deal to do it alongside EMU, our exclusive Québec dealer since 2021. EMU has been honored and recognized as a top-performing dealer for Hangcha Canada and we look forward to delivering another year of exceptional service to the racing community.” Hangcha forklifts, to be delivered between May 21 and May 31, 2024, will be strategically positioned in the paddocks, guaranteeing readiness for the race. The Hangcha Canada on-site representative will be Louanne Rioux, Sales and Marketing Director, alongside Jean-Sebastien Demers, General Manager at EMU. “As we gear up for June, we’re excited to deploy a range of Hangcha pneumatic forklifts ranging from capacities of 6,000 lbs to the high capacity forklifts of 22,000 lbs and more,” expresses Jean-Sebastien Demers. “We’re extremely grateful for the opportunity to once again support this race, which holds a special place in the hearts of the Québécois, with new, reliable, and efficient equipment. The record-breaking attendance at the 2023 event speaks volumes about its significance and the passion it ignites among locals, visitors, and racing enthusiasts.” Headquartered in Vaudreuil-Dorion, Québec, Hangcha Canada proudly stands as the only forklift manufacturer with a head office and distribution center located within Canada, showcasing its commitment to the Canadian market.